机械加工质量
机械加工质量及控制

机械加工质量及控制引言机械加工是一种常见的制造方法,用于将原始材料加工成所需形状和尺寸的零件。
机械加工质量的好坏直接影响着零件的性能和使用寿命。
对机械加工质量进行严格的控制是非常重要的。
机械加工质量的要求1. 尺寸精度:机械加工零件的尺寸精度是保证其装配性能和工作稳定性的关键。
通常使用公差来描述尺寸精度的要求,公差越小,零件的尺寸精度要求就越高。
2. 表面质量:机械加工零件的表面质量对摩擦、磨损和腐蚀等性能有着重要的影响。
表面粗糙度是评价表面质量的重要指标,粗糙度越小,表面质量越好。
3. 几何形状:机械加工零件的几何形状要求直接决定了其与其他零件的配合性能。
例如,孔的圆度和直线度要求可以直接影响轴承的配合质量和旋转性能。
机械加工质量控制方法1. 加工设备的选择:选择适合加工要求的设备是保证机械加工质量的关键。
不同加工设备的精度、刚度和稳定性存在差异,需要根据具体的加工要求进行选择。
2. 切削工艺的优化:切削工艺的合理优化可以提高机械加工零件的表面质量和尺寸精度。
通过选择合适的刀具、切削参数和切削液等,可以减小切削力和热变形,降低表面粗糙度。
3. 机床调试和维护:机床的准确定位和运动稳定性是保证机械加工质量的基础。
需要定期检查和维护机床,保持其精度和稳定性。
4. 检测和测量:通过使用合适的测量工具和设备,对机械加工零件的尺寸、形状和表面质量进行检测和测量。
及时发现问题并进行调整和纠正,以确保机械加工质量的有效控制。
机械加工质量控制的挑战1. 加工材料的变化:不同材料的加工特性有所不同,对机械加工工艺和控制要求也存在差异。
需要根据不同材料的特点进行合理的工艺选择和优化。
2. 加工过程的变动:在机械加工过程中,由于刀具磨损、切削力变化等原因,加工过程可能会出现变动。
及时对加工过程进行调整和控制,以确保一致的加工质量。
3. 人为因素的干扰:机械加工过程中,操作人员的技能水平和责任意识也会对加工质量产生影响。
机械加工质量控制
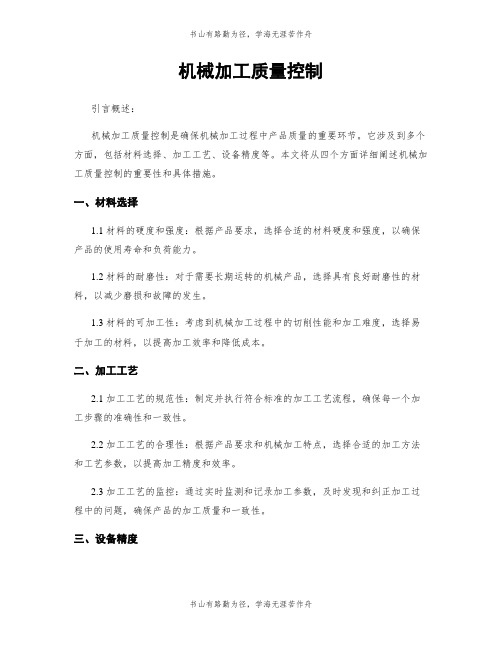
机械加工质量控制引言概述:机械加工质量控制是确保机械加工过程中产品质量的重要环节。
它涉及到多个方面,包括材料选择、加工工艺、设备精度等。
本文将从四个方面详细阐述机械加工质量控制的重要性和具体措施。
一、材料选择1.1 材料的硬度和强度:根据产品要求,选择合适的材料硬度和强度,以确保产品的使用寿命和负荷能力。
1.2 材料的耐磨性:对于需要长期运转的机械产品,选择具有良好耐磨性的材料,以减少磨损和故障的发生。
1.3 材料的可加工性:考虑到机械加工过程中的切削性能和加工难度,选择易于加工的材料,以提高加工效率和降低成本。
二、加工工艺2.1 加工工艺的规范性:制定并执行符合标准的加工工艺流程,确保每一个加工步骤的准确性和一致性。
2.2 加工工艺的合理性:根据产品要求和机械加工特点,选择合适的加工方法和工艺参数,以提高加工精度和效率。
2.3 加工工艺的监控:通过实时监测和记录加工参数,及时发现和纠正加工过程中的问题,确保产品的加工质量和一致性。
三、设备精度3.1 设备的选型和调试:根据产品要求和加工工艺的特点,选择适合的机床和刀具,并进行调试和校准,以确保设备的准确性和稳定性。
3.2 设备的维护和保养:定期对设备进行维护和保养,包括清洁、润滑和紧固等,以保持设备的正常运转和精度。
3.3 设备的监控和改进:通过设备的监控和数据分析,及时发现设备故障和性能下降的问题,并采取相应的改进措施,以提高设备的可靠性和加工精度。
四、质量检验4.1 检验方法的选择:根据产品特点和加工要求,选择合适的检验方法,包括尺寸测量、表面质量检查等,以确保产品的准确性和一致性。
4.2 检验设备的校准:定期对检验设备进行校准和验证,以确保检验结果的准确性和可靠性。
4.3 检验结果的记录和分析:对检验结果进行记录和分析,及时发现和解决质量问题,并采取相应的改进措施,以提高产品的质量和客户满意度。
结论:机械加工质量控制是确保产品质量的关键环节。
机械加工质量保证措施

机械加工质量保证措施在机械加工的世界里,质量就像是那根神奇的线,拉得越紧,成品越完美。
说到质量保证,咱们可得好好唠唠,这可不是随便说说的事儿。
咱们总是希望买到的东西既好看又好用,对吧?质量保证措施就是为这事儿而生的。
可以说,它就是咱们的“守护神”,让每一个零件都能发挥出应有的作用。
得说说材料的选择。
这可不是随便拿个东西就能搞定的。
优质的原材料就像是做饭的好食材,味道全靠它。
假设你用的是劣质的钢材,那可就麻烦了,强度不够,耐磨性差,简直是给自己挖坑!所以,材料的来源、检验、储存,每一步都得小心翼翼,像对待自己心爱的宠物一样,生怕出一点差错。
咱们得聊聊加工工艺。
这个就像是个大厨的拿手好菜,得讲究火候。
每个工序都得严格把控,从切割到打磨,再到表面处理,不能马虎。
这过程就像是在舞台上表演,台上一分钟,台下十年功,每一步都得精准到位。
使用合适的设备也是关键,设备老化了,那可真是“老牛拉破车”,根本无法满足高质量的需求。
工人的技术水平也至关重要。
一个熟练的工人,就像一位艺术家,能把每个零件都打磨得光滑如新。
培训和考核可不能少,这就像是学校的期末考试,考的就是你平时的积累。
谁都知道,一个不熟练的工人做出来的活儿,真是“心有余而力不足”。
所以,定期进行技能培训,保持工人的热情与专业,才能保证加工质量。
检测环节也是不可忽视的。
就像是吃饭前的味道检查,得确保每一口都是鲜美的。
无论是尺寸、形状还是表面质量,咱们都得严谨地检查。
引入现代化的检测设备,就像是给加工车间装上了“火眼金睛”,能一眼看出问题所在。
每一个小小的偏差,都可能导致大问题,谁都不想在关键时刻出个岔子。
生产过程中的环境也有讲究。
一个干净整洁的车间,能提高工人的工作效率,就像是清爽的空气让人心情舒畅。
相反,杂乱无章的环境只会让人心烦意乱,根本无法专心工作。
定期的清理和维护,保持设备的良好状态,这样才能让加工过程顺畅如行云流水。
还得说说沟通,尤其是在团队内部。
机械加工质量保障措施有哪些
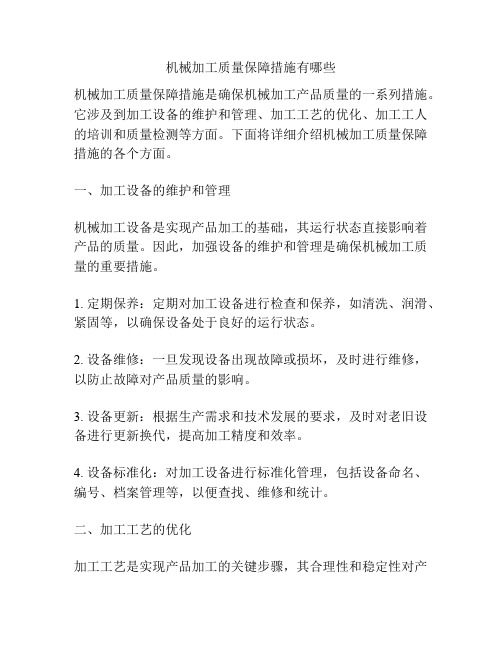
机械加工质量保障措施有哪些机械加工质量保障措施是确保机械加工产品质量的一系列措施。
它涉及到加工设备的维护和管理、加工工艺的优化、加工工人的培训和质量检测等方面。
下面将详细介绍机械加工质量保障措施的各个方面。
一、加工设备的维护和管理机械加工设备是实现产品加工的基础,其运行状态直接影响着产品的质量。
因此,加强设备的维护和管理是确保机械加工质量的重要措施。
1. 定期保养:定期对加工设备进行检查和保养,如清洗、润滑、紧固等,以确保设备处于良好的运行状态。
2. 设备维修:一旦发现设备出现故障或损坏,及时进行维修,以防止故障对产品质量的影响。
3. 设备更新:根据生产需求和技术发展的要求,及时对老旧设备进行更新换代,提高加工精度和效率。
4. 设备标准化:对加工设备进行标准化管理,包括设备命名、编号、档案管理等,以便查找、维修和统计。
二、加工工艺的优化加工工艺是实现产品加工的关键步骤,其合理性和稳定性对产品质量有着重要的影响。
因此,优化加工工艺是确保机械加工质量的核心措施。
1. 工艺流程优化:分析产品的加工特点,制定合理的加工工艺流程,避免加工中出现不必要的工序,提高加工效率和质量。
2. 工艺参数控制:根据产品的要求,合理设定加工参数,如加工速度、刀具进给量、切削液的使用等,以实现加工的精度和质量要求。
3. 工艺指导书编制:制定工艺指导书,详细记录每个工序的操作要点和加工参数,以便操作人员按照规定操作,确保稳定的产品质量。
4. 工艺改进:定期开展工艺改进活动,通过引进新技术、改进工艺路线等方式,不断提高加工工艺的可靠性和稳定性。
三、加工工人的培训和管理加工工人是机械加工质量的直接执行者,他们的技能水平和工作态度直接影响着产品的质量。
因此,加强加工工人的培训和管理是确保机械加工质量的重要措施。
1. 技能培训:加强加工工人的技能培训,包括理论知识的学习和实践操作的训练,提高加工工人的技术水平和操作能力。
2. 质量意识培养:加强加工工人的质量意识培养,强调产品质量的重要性,培养他们的责任感和主动性,以确保工作的认真和细致。
机械加工质量及控制
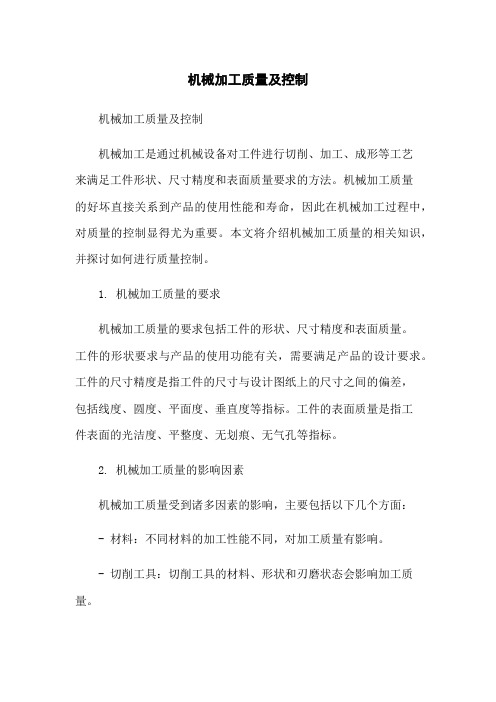
机械加工质量及控制机械加工质量及控制机械加工是通过机械设备对工件进行切削、加工、成形等工艺来满足工件形状、尺寸精度和表面质量要求的方法。
机械加工质量的好坏直接关系到产品的使用性能和寿命,因此在机械加工过程中,对质量的控制显得尤为重要。
本文将介绍机械加工质量的相关知识,并探讨如何进行质量控制。
1. 机械加工质量的要求机械加工质量的要求包括工件的形状、尺寸精度和表面质量。
工件的形状要求与产品的使用功能有关,需要满足产品的设计要求。
工件的尺寸精度是指工件的尺寸与设计图纸上的尺寸之间的偏差,包括线度、圆度、平面度、垂直度等指标。
工件的表面质量是指工件表面的光洁度、平整度、无划痕、无气孔等指标。
2. 机械加工质量的影响因素机械加工质量受到诸多因素的影响,主要包括以下几个方面:- 材料:不同材料的加工性能不同,对加工质量有影响。
- 切削工具:切削工具的材料、形状和刃磨状态会影响加工质量。
- 加工工艺:包括切削速度、进给量、切屑清除等,对加工质量有重要影响。
- 加工设备:加工设备的精度、刚性和稳定性对加工质量有直接影响。
- 操作技术:操作人员的技术水平和经验对加工质量有很大的影响。
3. 机械加工质量的控制方法为了保证机械加工质量,需要采取一系列的控制方法。
3.1 设计合理性控制这是机械加工质量控制的首要环节。
设计时需要考虑工件的功能和使用要求,并根据不同材料的加工性能确定合适的工艺参数。
3.2 切削工具的选择和维护切削工具的选择应根据加工工件的材料和形状来确定,同时需要定期进行刃磨和维护,确保切削工具的良好状态。
3.3 加工工艺的控制合理的加工工艺参数包括切削速度、进给量、冷却液的使用等。
在加工过程中需要严格控制这些参数,以保证工件的尺寸精度和表面质量。
3.4 加工设备的维护和调整加工设备的精度、刚性和稳定性对加工质量有直接影响。
定期对设备进行维护和调整,保持其良好状态。
3.5 操作人员的培训和管理操作人员的技术水平和经验对加工质量至关重要。
机械加工质量控制标准

机械加工质量控制标准在机械制造领域中,机械零部件的质量是至关重要的。
为了确保机械零部件的加工质量,我们需要遵守一定的标准和规范。
本文将介绍机械加工质量控制标准。
一、加工质量要求机械零部件的加工质量要求包括尺寸精度、形位公差、表面质量等方面的要求。
在进行加工之前,需要明确零部件的加工质量要求,并在加工过程中严格控制,以保证最终产品的质量。
1. 尺寸精度尺寸精度是衡量机械零部件加工质量的重要指标之一。
尺寸精度一般分为公差等级,根据零部件的实际要求选择适当的公差等级。
加工过程中需采用合适的加工工艺和设备,保证尺寸精度的达到要求。
2. 形位公差形位公差是衡量机械零部件几何形状和位置精度的指标。
对于要求较高的零部件,需要在制定工艺方案和选择设备时考虑形位公差的控制。
在加工过程中,应严格按照设计要求进行加工,保证形位公差的控制。
3. 表面质量零部件的表面质量对于产品的整体外观和性能有较大的影响。
在机械加工过程中,应注重工艺操作的细节,控制好加工参数和刀具状况,保证零部件的表面光洁度和无明显缺陷。
二、加工工艺要求机械加工工艺是保证零部件加工质量的重要环节。
在加工过程中,应根据零部件的具体要求和材料特性,合理选择加工工艺和设备,并制定相应的操作规程。
1. 工艺路线在制定加工工艺时,需要明确每道工序的加工内容和顺序。
合理的工艺路线可以最大程度地减少加工扭曲和变形,提高零部件的加工精度。
2. 加工方法不同的零部件可能采用不同的加工方法,如车削、铣削、钻削、磨削等。
选择合适的加工方法需要考虑加工效率和加工质量的平衡,确保加工过程中的稳定性和准确性。
3. 刀具选择刀具是机械加工中不可或缺的工具,合适的刀具选择能够有效地提高加工质量。
在选择刀具时,需要考虑加工材料的硬度、表面光洁度等因素,并结合具体的加工操作进行选用。
三、设备要求机械加工设备对于加工质量的控制至关重要。
高精度、稳定性好的设备能够提供良好的加工基础,保证零部件加工质量的稳定性和可靠性。
机械加工质量分析及控制

机械加工质量分析及控制机械加工质量分析及控制一、引言二、机械加工质量分析机械加工质量的分析主要包括以下几个方面:1.表面粗糙度分析机械加工的表面粗糙度对于产品的外观和性能有着重要影响。
通过使用表面粗糙度测量仪器,可以对机械加工的表面粗糙度进行评估。
常用的表面粗糙度参数包括Ra、Rz等。
2.尺寸精度分析机械加工的尺寸精度是指产品的实际尺寸和设计图纸上的尺寸之间的偏差。
通过使用测量工具和仪器,可以对机械加工的尺寸精度进行评估。
常用的尺寸精度参数包括公差、尺寸偏差等。
3.形状偏差分析机械加工的形状偏差是指产品的实际形状和设计图纸上的形状之间的偏差。
通过使用形状测量仪器,可以对机械加工的形状偏差进行评估。
常用的形状偏差参数包括圆度误差、平面度误差等。
三、机械加工质量控制为了确保机械加工的质量,需要进行相应的控制措施。
以下是几个常用的机械加工质量控制方法:1.工艺参数控制调整机械加工的工艺参数,可以对机械加工的质量进行控制。
例如,通过调整切削速度、进给速度和切削深度等参数,可以控制机械加工的表面粗糙度和尺寸精度。
2.设备状态监控对机械加工设备的状态进行监控,可以及时发现并修复设备故障,避免对产品质量的影响。
常用的设备状态监控方法包括振动监测、温度监测等。
3.质量检验与统计分析对机械加工的产品进行质量检验,并进行统计分析,可以及时发现并纠正加工过程中的问题。
常用的质量检验方法包括外观检查、尺寸测量等。
四、机械加工质量的分析和控制是确保产品质量的重要手段。
通过对表面粗糙度、尺寸精度和形状偏差等进行分析,可以找出问题所在。
通过工艺参数控制、设备状态监控和质量检验与统计分析等控制措施,可以提高机械加工的质量水平。
机械加工质量

在现代制造业中,机械加工质量是至关重要的。它不仅关系到产品的性能和 可靠性,还对企业的声誉和客户满意度具有重大影响。
常见的机械加工缺陷
1 尺寸偏差
尺寸与设计要求不一致,可能导致产品功能不正常。
2 表面质量问题
划痕、气泡、裂纹等表面不良会影响产品的外观和性能。
3 材料选择错误
选择不适合的材料可能导致产品强度不够或易损坏。
问题分析
通过仔细观察和数据施
采取合适的措施,如调整工艺参数、改进设备 等,以解决质量问题。
经验分享:案例研究
1
案例一
通过优化工艺流程和控制参数,将零件尺寸偏差降低至设计要求范围内。
2
案例二
引入新的表面处理技术,提高产品外观质量和抗腐蚀能力。
3
案例三
建立完善的质量管理体系,有效控制生产过程中的质量问题。
提高机械加工质量的方法
精密设备
投资先进的机械设备和工具, 以确保高精度和高效率。
合理工艺
优化加工方案、制定详细的 工艺流程和操作规范。
质量控制
引入严格的质量管理体系, 确保每一道工序都符合质量 标准。
机械加工质量的检测与控制
质量检测
使用先进的检测设备和技术,如三坐标测量仪、 光谱分析仪等。
过程控制
通过实时监控和数据分析,及时发现和解决潜在 问题。
相关的机械加工质量标准
ISO 9001 ISO 14001 ASM E B16.5
国际质量管理体系认证标准,注重各个环节的 质量控制。
环境管理体系认证标准,强调资源的节约和环 境的保护。
美国机械工程师标准,用于管道和法兰连接的 质量要求。
机械加工质量问题的解决方法
机械加工质量预测

基于统计分析的方法
回归分析
通过分析机械加工数据,建立加工参数与质量指标之 间的回归关系,预测加工质量。
方差分析
研究加工参数对质量指标的影响,确定各参数对质量 的影响程度。
聚类分析
将相似的加工参数进行聚类,根据聚类结果预测加工 质量。
基于机器学习的方法
支持向量机
通过构建支持向量机模型,根据加工参数预测 加工质量。
高质量的加工可以减少产品故障,提高客户满意度。
生产效率
02
优质的机械加工可以减少返工和维修,从而提高生产效率,降
低生产成本。
企业竞争力
03
在激烈的市场竞争中,提高机械加工质量可以增强企业的竞争
力。
机械加工质量的定义与评估标准
定义
机械加工质量是指零件加工后符合技术要求和设计意图的程 度。
评估标准
主要包括尺寸精度、形状精度、表面粗糙度、材料性能等。
1 2
选用高性能刀具
使用具有良好耐磨性和抗冲击性的刀具,提高刀 具寿命和加工精度。
选择合适的材料
针对不同的加工需求,选择合适的刀具材料,提 高切削效率和加工质量。
3
及时更换刀具
定期检查刀具磨损情况,及时更换新刀具,保证 加工质量。
引入智能化检测与监控系统
在线检测技术
采用机器视觉、激光扫描等技术,实时检测加工表面的质量和尺寸 精度。
影响机械加工质量的因素
设备因素
机床、刀具、夹具等设备的性能和精度对加 工质量有直接的影响。
人员因素
操作人员的技能水平、工作态度和责任心对 加工质量有重要影响。
工艺因素
加工方法、工艺参数、冷却液等工艺条件的 选择对加工质量至关重要。
机械加工质量的概念

机械加工质量的概念
机械加工质量通常包括两个方面: 几何方面的质量和材料性能方面的质量。
几何方面的质量--指机械加工后最外层表面与四周环境间界面的几何外形误差。
它分为宏观几何外形误差和微观几何外形误差。
1)宏观几何外形误差(如圆度误差,平面度误差等)。
宏观几何外形误差的波长(测量长度或取样长度)与波高(误差值)的比值一般大于1000。
2)微观几何外形误差(微观几何外形的不平度,或称表面粗糙度)。
其波长与波高比值一般小于50。
3)介于宏观几何外形误差与微观表面粗糙度之间的周期性几何外形误差,常用波度来表示,其波长λ与波高Hλ比值等于50~1000。
波度主要是由加工系统的振动所引起的。
材料性能方面的质量--指机械加工后,零件肯定深度表面层的物理力学性能等方面的质量与基体相比发生了变化,故称加工变质层。
主要表现在以下几方面:
1)表面层加工硬化机械加工过程中产生的塑性变形,使晶格扭曲、崎变,晶粒间产生滑移,晶粒被拉长等,这些都会使表面层金属硬度增加,通称为加工硬化(或冷作硬化)。
加工硬化的评定指标通常有3项:
① 表面层金属硬度HV;
② 硬化层深度h;
③ 硬化程度N:
式中HV0 --工件内部金属原来的硬度。
2)表面层金相组织变化机械加工过程中由于切削热的作用,有可能表面层金属的金相组织发生变化。
例如,磨削淬火钢时,磨削热的作用会引起淬火钢中马式体的分解,或消失回火组织等。
3)表面层残余应力由于切削力和切削热的综合作用,表面层金属晶格的变形或金相组织变化,会造成表面层残余应力。
机械加工成品质量技术指标或者标准

机械加工成品质量技术指标或者标准机械加工成品的质量技术指标或标准是指用于评估和衡量机械加工成品质量的各种要素和要求。
这些指标或标准可以帮助制造商和用户确定成品是否符合预期的要求,并确保其质量以满足用户需求。
以下是一些常见的机械加工成品质量技术指标或标准。
1.尺寸精度:尺寸精度是机械加工成品中最重要的指标之一。
它指的是成品与设计尺寸之间的差异。
常见的尺寸精度标准包括公差和尺寸偏差。
对于某些关键零部件,如发动机配件或航空航天部件,尺寸精度可能非常高,因为它们的功能和性能可能受到微小尺寸差异的影响。
2.表面粗糙度:表面粗糙度是指机械加工成品表面的纹理和光洁度。
高品质的机械加工成品应具有平滑、均匀的表面,以确保其与其他部件的贴合和运动的顺畅。
表面粗糙度可以通过测量平均粗糙度、峰值高度等参数来评估。
3.功能性能:机械加工成品的功能性能指其在特定工作条件下执行所需功能的能力。
这取决于成品的材料、设计和加工质量等因素。
功能性能测试可能包括强度测试、疲劳寿命测试、耐腐蚀性测试等,以确保成品能够在预期的使用环境下可靠地工作。
4.材料性能:材料性能是机械加工成品质量的关键要素之一。
它指的是成品所使用材料的物理、化学和力学性能。
常见的材料性能指标包括强度、硬度、韧性、耐磨性、耐腐蚀性等。
制造商必须选择具有适当材料性能的材料以满足成品的需求,并确保最终产品的质量。
5.安全性能:对于某些机械加工成品,如汽车零部件或医疗设备,安全性能是至关重要的。
安全性能指成品在使用时对人、设备或环境造成的潜在危险程度。
制造商必须遵守相关的安全标准和法规,以确保成品的安全性能达到要求。
6.可靠性:可靠性是指机械加工成品在一定时间内保持稳定和无故障运行的能力。
可靠性工程是通过使用可靠性分析和测试方法来评估和改进成品的可靠性。
对于一些关键应用领域,如航空航天、医疗和能源等,可靠性要求非常高,因为成品的故障可能导致严重的后果。
综上所述,机械加工成品的质量技术指标或标准涉及尺寸精度、表面粗糙度、功能性能、材料性能、安全性能和可靠性等多个方面。
机械加工质量分析及控制
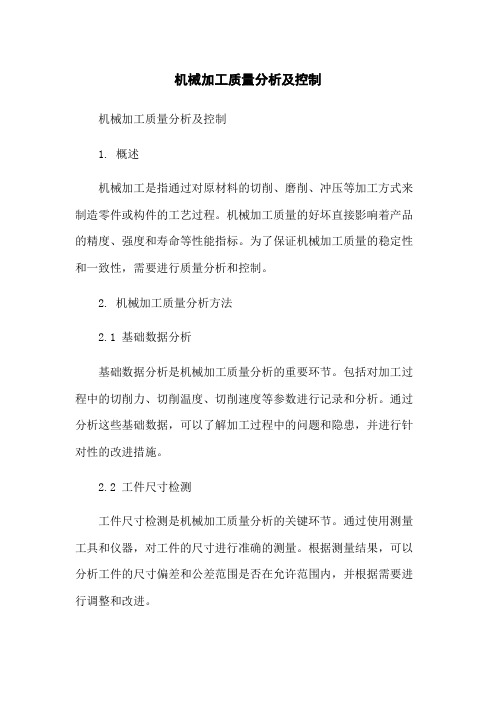
机械加工质量分析及控制机械加工质量分析及控制1. 概述机械加工是指通过对原材料的切削、磨削、冲压等加工方式来制造零件或构件的工艺过程。
机械加工质量的好坏直接影响着产品的精度、强度和寿命等性能指标。
为了保证机械加工质量的稳定性和一致性,需要进行质量分析和控制。
2. 机械加工质量分析方法2.1 基础数据分析基础数据分析是机械加工质量分析的重要环节。
包括对加工过程中的切削力、切削温度、切削速度等参数进行记录和分析。
通过分析这些基础数据,可以了解加工过程中的问题和隐患,并进行针对性的改进措施。
2.2 工件尺寸检测工件尺寸检测是机械加工质量分析的关键环节。
通过使用测量工具和仪器,对工件的尺寸进行准确的测量。
根据测量结果,可以分析工件的尺寸偏差和公差范围是否在允许范围内,并根据需要进行调整和改进。
2.3 表面质量检测表面质量检测是机械加工质量分析的另一个重要环节。
通过使用光学显微镜、电镜等仪器,对工件的表面质量进行检测和评估。
根据检测结果,可以分析工件的表面光洁度、粗糙度等指标是否符合要求,并采取相应的措施进行改进。
3. 机械加工质量控制方法3.1 设备维护与管理机械加工设备的维护和管理对于保证加工质量非常重要。
定期对设备进行保养和检修,确保设备的正常运行和准确性。
,使用合适的刀具和夹具,并正确地安装和调整,可以有效地控制加工质量。
3.2 加工工艺优化加工工艺的优化也是机械加工质量控制的重要手段之一。
通过对工艺参数的调整和优化,可以实现加工质量的提高和降低加工成本。
例如,通过合理地选择切削速度、进给速度和切削深度等参数,可以控制加工过程中的热变形和切削力,提高加工质量。
3.3 质量管理体系建立建立质量管理体系是机械加工质量控制的基础。
通过制定加工工艺规范和质量控制标准,并进行员工培训和绩效评估,可以确保加工质量的稳定性和一致性。
,定期进行质量审核和改进,提高质量管理水平。
4. 结论机械加工质量的分析和控制是保证产品质量的重要环节。
机械加工质量控制标准及规范

机械加工质量控制标准及规范
一、引言
机械加工质量控制是确保制造过程中产品达到预期质量的关键要素。
本文档旨在介绍机械加工质量控制的标准及规范,并提供相关指导。
二、质量控制标准
1. 尺寸控制:确保零件尺寸与设计要求相符合,并符合国家相关标准。
2. 几何形状控制:确保零件的几何形状达到设计要求,如平面度、圆度、直线度等。
3. 表面质量控制:确保零件表面光洁度、粗糙度等符合要求,采用适当的表面处理方法。
4. 材料控制:确保使用的材料符合产品要求,包括材料的物理性能、化学成分等。
5. 装配控制:确保零件的装配质量达到要求,包括零件之间的间隙、配合、误差等。
三、质量控制规范
1. 加工工艺规范:明确机械加工过程中的具体工艺要求,包括
机床的选用、切削参数的设定、工件固定方式等。
2. 检测方法规范:规定机械零部件在加工过程中的检测方法,
包括使用的检测工具、检测标准等。
3. 质量记录规范:要求对机械加工过程中的关键节点进行记录,包括尺寸、几何形状、表面质量、材料等的检测结果。
4. 不合格品处理规范:明确不合格品的处理流程,包括原因分析、责任追究、修整或重新加工的方式等。
四、总结
机械加工质量控制的标准及规范对于保障产品质量至关重要。
本文档提供了一个基本的指导框架,但具体的标准和规范应根据实
际情况制定,并在实践中不断改进。
以上为《机械加工质量控制标准及规范》的文档内容。
---
注:本文档中的内容仅供参考,不做任何法律解释和依据。
机械加工质量及其检测

先进制造技术
装配工艺的另一种说法是装配方法。
装配方法说明书(或者是作业指导书)必须清楚地描述对象、操作顺序以及使用的工具和物料。
装配说明书应能简单易学,同时还能很方便的制作、复制、分发和变更。
装配工艺还应包括工艺大纲或者是工艺路线,每一工序的详细操作指导书、物料清单、加工过程草图或者直观教具以及每个工序的加工位置。
必须针对质量特征和不同精度等级的要求,合理选择适用的测量工具或仪表,并在规程中标明它们的型号.规格和编号,说明其使用方法;
编制检验规程的要求
编制检验规程
C.当采用抽样检验时,应正确选择并说明抽样方案。根据具体情况及不合格严重性分级确定AQL值(AQL值表示为可接受的水准),正确选择检查水平,根据产品抽样检验的目的.性质.特点选用适用的抽样方案。 检验规程的主要目的是使检验人员按检验规程规定的内容.方法及程序进行检验,保证检验工作的质量.有效地防止错检.漏检等现象发生。
机械加工时,每种机床上所达到的精度越高,则所耗费的工时越多,成本越高。
每种机床在正常条件下能经济地达到的加工精度是有一定范围的,这个精度范围就是这种加工方法的经济精度。
正常生产条件:设备完好、工夹量具适应、工人技术水平相当、工时定额合理。
经济加工精度
在制造工艺过程中采用的基准称为工艺基准
装配基准:是产品装配时用来确定零件或部件在机器中的相对位置所用的基准。
长度:包括轴径、孔径
角度:包括锥度
形状和位置误差:包括直线度、平面度、圆度、圆柱度和表面粗糙度等的基本测量方法。
机械加工质量检测
卡尺、千分尺、指示表千分尺、杠杆千分尺、杠杆齿轮传动测微仪、扭簧测微仪、电感测微仪、电容测微仪、立式光学计、卧式光学计、立式测长仪、万能测长仪、
机械加工质量及控制简洁范本

机械加工质量及控制
机械加工质量及控制
1. 引言
机械加工是一种常见的制造工艺,广泛应用于各个行业。
机械加工质量直接影响着产品的性能和可靠性,控制机械加工质量至关重要。
2. 机械加工质量的重要性
机械加工质量的好坏直接关系到产品的使用寿命和性能。
优质的机械加工能够提高产品的稳定性和精度,降低故障率,延长使用寿命,提高产品的市场竞争力。
3. 机械加工质量的评估指标
一般来说,评估机械加工质量可以从以下几个方面进行考虑:尺寸精度:包括几何尺寸的偏差和公差范围。
表面质量:表面光洁度、表面硬度、表面无划伤等。
加工精度:加工误差和加工精度的偏差。
机械性能:材料的硬度、韧性等。
4. 机械加工质量控制的方法
为了确保机械加工的质量,我们可以采用以下几种方法进行控制:
工艺控制:通过合理设计和选取适当的加工工艺,以达到所需的加工精度和表面质量。
机械设备控制:选择高精度的机床和工具,提高机械设备的性能和稳定性,以保证加工的质量和精度。
检测与测量控制:使用先进的检测设备和测量工具,对加工过程进行实时监测和测量,并及时调整工艺参数,以保证加工质量的稳定性。
过程控制:对加工过程中的各个环节进行监控和控制,确保每个环节都符合要求,并及时发现和排除问题。
5.
机械加工质量的好坏直接关系到产品的性能和可靠性。
通过合理的工艺控制、优质的机械设备、精准的检测测量和科学的过程控制,可以有效地提高机械加工的质量,从而提高产品的市场竞争力。
在实际应用中,需要根据具体情况选择适当的控制方法,以达到最佳的加工质量。
机械加工质量
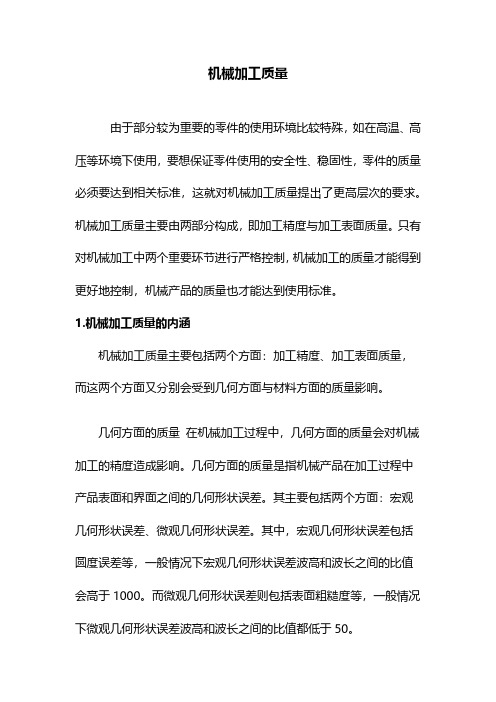
机械加工质量由于部分较为重要的零件的使用环境比较特殊,如在高温、高压等环境下使用,要想保证零件使用的安全性、稳固性,零件的质量必须要达到相关标准,这就对机械加工质量提出了更高层次的要求。
机械加工质量主要由两部分构成,即加工精度与加工表面质量。
只有对机械加工中两个重要环节进行严格控制,机械加工的质量才能得到更好地控制,机械产品的质量也才能达到使用标准。
1.机械加工质量的内涵机械加工质量主要包括两个方面:加工精度、加工表面质量,而这两个方面又分别会受到几何方面与材料方面的质量影响。
几何方面的质量在机械加工过程中,几何方面的质量会对机械加工的精度造成影响。
几何方面的质量是指机械产品在加工过程中产品表面和界面之间的几何形状误差。
其主要包括两个方面:宏观几何形状误差、微观几何形状误差。
其中,宏观几何形状误差包括圆度误差等,一般情况下宏观几何形状误差波高和波长之间的比值会高于1000。
而微观几何形状误差则包括表面粗糙度等,一般情况下微观几何形状误差波高和波长之间的比值都低于50。
材料方面的质量在机械加工中,材料方面的质量是指机械产品表面层所涉及的物理学性能的质量和基体之间产生的变化,也被称为加工变质层。
在机械加工过程中,材料方面的质量会对加工表面质量造成影响,这主要表现在表面层加工硬化和表面层金相组织变化两个方面。
其中,表面层加工硬化是指机械加工时所产生的塑性变形、晶粒间产生滑移等导致机械产品表面层金属的硬度被增强。
一般对机械产品加工硬度进行评定需要考虑三个方面,即表面层金属硬度、硬化深度与硬化程度。
表面层金相组织变化是指在机械加工中因切削热的作用,导致机械产品表面金属的金相组织产生变化。
2.机械加工质量的影响因素在机械加工过程中,机械加工质量问题主要包括切削加工表面粗糙度、磨削加工表面粗糙度。
一般影响机械加工质量的因素可以分为两个方面,即几何因素和物理学因素。
切削加工表面粗糙度在机械加工中,切削加工表面粗糙度这一质量问题的产生原因主要包括几何因素和物理学因素两个方面。
机械加工质量分析及控制

机械加工质量分析及控制引言在机械制造过程中,机械加工是一项重要的工艺。
机械加工质量的好坏直接影响到制造产品的性能和可靠性。
因此,对于机械加工质量进行分析和控制是非常重要的。
本文将介绍机械加工质量的分析方法和控制措施。
机械加工质量分析1. 加工表面粗糙度分析加工表面粗糙度是评估机械加工质量的重要指标之一。
常见的评估方法包括:Ra值、Rz值、Rq值等。
通过测量和分析加工表面的粗糙度指标,可以了解加工质量是否符合设计要求,从而评估加工过程的稳定性和精度。
2. 尺寸测量与分析机械加工过程中,尺寸的精度是衡量加工质量的重要指标之一。
通过尺寸测量,可以评估加工件的尺寸精度是否满足设计要求,并分析加工误差的来源。
常用的尺寸测量方法有:千分尺、游标卡尺、三坐标测量等。
3. 加工变形分析在机械加工过程中,加工件的压力、温度等因素会引起加工变形。
加工变形会直接影响加工件的质量和尺寸精度。
通过对加工变形进行分析,可以了解加工过程中的变形规律,并采取相应的控制措施,如合理选用加工工艺和工件固定方式等,以减小加工变形。
4. 刀具磨损分析刀具磨损是机械加工过程中不可避免的问题。
刀具的磨损程度直接影响到加工表面的质量和尺寸精度。
通过对刀具磨损进行分析,可以判断刀具的使用寿命和更换时机,以保证加工质量和效率。
机械加工质量控制1. 加工工艺优化机械加工的工艺参数对加工质量有重要影响。
通过优化加工工艺参数,可以提高加工质量和效率。
优化加工工艺的方法包括:合理选择切削速度、进给量和切削深度等参数,以最大限度地提高表面质量和尺寸精度。
2. 刀具管理刀具的选择和管理对于机械加工质量至关重要。
合理选用刀具材料和几何形状,可以提高切削效率和加工质量。
此外,定期检查和维护刀具,及时更换磨损严重的刀具,能够保持加工质量的稳定。
3. 加工设备维护加工设备的维护对机械加工质量的控制也非常重要。
定期对加工设备进行检查和维护,确保设备的工作状态良好,可以保证加工质量的稳定。
机械加工质量分析及控制
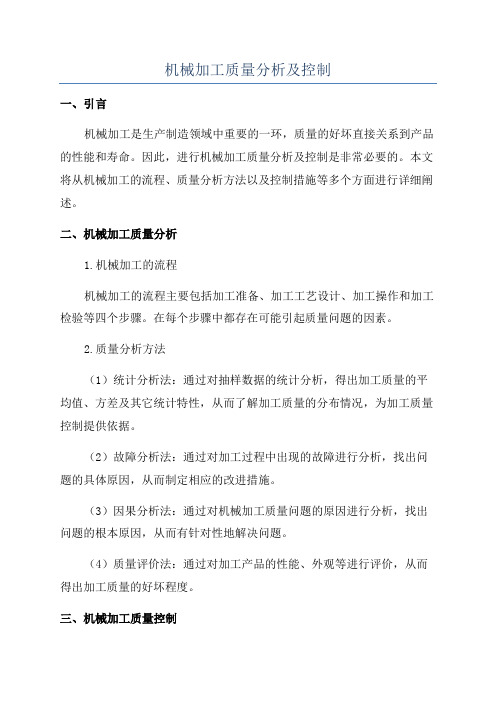
机械加工质量分析及控制一、引言机械加工是生产制造领域中重要的一环,质量的好坏直接关系到产品的性能和寿命。
因此,进行机械加工质量分析及控制是非常必要的。
本文将从机械加工的流程、质量分析方法以及控制措施等多个方面进行详细阐述。
二、机械加工质量分析1.机械加工的流程机械加工的流程主要包括加工准备、加工工艺设计、加工操作和加工检验等四个步骤。
在每个步骤中都存在可能引起质量问题的因素。
2.质量分析方法(1)统计分析法:通过对抽样数据的统计分析,得出加工质量的平均值、方差及其它统计特性,从而了解加工质量的分布情况,为加工质量控制提供依据。
(2)故障分析法:通过对加工过程中出现的故障进行分析,找出问题的具体原因,从而制定相应的改进措施。
(3)因果分析法:通过对机械加工质量问题的原因进行分析,找出问题的根本原因,从而有针对性地解决问题。
(4)质量评价法:通过对加工产品的性能、外观等进行评价,从而得出加工质量的好坏程度。
三、机械加工质量控制1.加工工艺的控制加工工艺的合理设计对机械加工的质量控制起着重要作用。
在工艺设计中,要充分考虑原材料及刀具的选择,确定合适的切削参数、冷却液的使用等,避免加工过程中产生过大的切削热,从而影响加工质量。
2.加工操作的控制加工操作是机械加工中最直接的环节,其质量直接决定了产品的质量。
在加工操作中,操作人员应严格按照操作规程进行操作,保持良好的操作习惯,例如保持正确的加工速度、切削深度等。
同时,操作人员还需要具备一定的机械加工技能和经验,能及时发现问题并进行调整。
3.检验控制的措施(1)首件检验:对于新开工的产品,首件检验是必要的,确认加工工艺和操作是否符合要求,以保证后续产品的质量。
(2)过程检验:在加工过程中,对关键工序进行检验,及时发现和纠正问题,避免不良品的产生。
(3)末件检验:对于加工完成的产品,在出厂前进行末件检验,确保产品达到客户的要求。
四、结论机械加工质量的分析和控制是必不可少的。
- 1、下载文档前请自行甄别文档内容的完整性,平台不提供额外的编辑、内容补充、找答案等附加服务。
- 2、"仅部分预览"的文档,不可在线预览部分如存在完整性等问题,可反馈申请退款(可完整预览的文档不适用该条件!)。
- 3、如文档侵犯您的权益,请联系客服反馈,我们会尽快为您处理(人工客服工作时间:9:00-18:30)。
(4)调整误差 机械加工过程中的每一道工序都要进行各种各样 的调整工作,由于调整不可能绝对准确,因此必 然会产生误差,这些误差称为调整误差。
2、工艺系统的受力变形 (1)工艺系统的刚度 机械加工过程中,工艺系统在切削力、传动力、惯
性力、夹紧力、重力等外力的作用下,各环节将 产生相应的变形,使刀具和工件间已调整好的正 确位置关系遭到破坏而造成加工误差。例如,在 车床上车削细长轴时,工件在切削力的作用下会 发生变形,使加工出的工件出现两头细中间粗的 腰鼓形
第七章 机械加工质量
尺寸精度
机械加工精度
形状精度
加 工 质 量
表面质量
位置精度 表面粗糙度
表面层的物理、力学性能
第一节 概述 一、机械加工精度 1、机械加工精度的概念
所谓机械加工精度,是指零件在加工后的几何 参数(尺寸大小、几何形状、表面间的相互位 置)的实际值与理论值相符合的程度。符合程 度高,加工精度也高;反之则加工精度低。机 械加工精度包括尺寸精度、形状精度、位置精 度三项内容,三者有联系,也有区别。
3)定尺寸刀具法 用具有一定形状和尺寸精度的刀 具进行加工,使加工表面达到要求的形状和尺寸的 加工方法。如用钻头、铰刀、键槽铣刀等刀具的加 工即为定尺寸刀具法。定尺寸刀具法生产率较高, 加工精度较稳定,广泛的应用于各种生产类型。 4)自动控制法 把测量装置、进给装置和控制机构 组成一个自动加工系统,使加工过程中的尺寸测量、 刀具的补偿和切削加工一系列工作自动完成,从而 自动获得所要求的尺寸精度的加工方法。该方法生 产率高,加工精度稳定,劳动强度低,适应于批量 生产。
原始误差主要来自两方面:一方面是在加工前就存 在的工艺系统本身的误差(几何误差),包括加 工原理误差,机床、夹具、刀具的制造误差,工 件的安装误差,工艺系统的调整误差等;另一方 面是加工过程中工艺系统的受力变形、受热变形、 工件残余应力引起的变形和刀具的磨损等引起的 误差,以及加工后因内应力引起的变形和测量引 起的误差等。
(2)获得形状精度的方法 1)轨迹法 依靠刀尖运动轨迹来获得形状精度的
方法。刀尖的运动轨迹取决于刀具和工件的相对成 形运动,因而所获得的形状精度取决成形运动的精 度。普通车削、铣削、刨削和磨削等均为刀尖轨迹 法。 2)成形法 利用成形刀具对工件进行加工的方法。 成形法所获得的形状精度取决于成形刀具的形状精 度和其他成形运动精度。用成形刀具或砂轮进行车、 铣、刨 、磨、拉等加工的均为成形法。
2、表面质量对零件使用性能的影响 (1)对零件耐磨性的影响
① 表面粗糙度对耐磨性的影响 一般情况下,表面粗糙度越小,零件表面越光滑,
耐磨性越好。但当零件表面的粗糙度小于最佳值 后,摩擦面之间的润滑油会被挤出而形成干摩擦, 反而使磨损加快。
② 冷作硬化对耐磨性的影响 一定的冷作硬化可以提高表面硬度,增加耐磨性。
6)合理设计系统结构 在设计机床夹具时,应尽量 减少组成零件数,以减少总的接触变形量;选择 合理的结构和截面形状;并注意刚度的匹配,防 止出现局部环节刚度低。
7)提高夹具、刀具刚度;改善材料性能。 8)控制负载及其变化 适当减少进给量和背吃刀量,
常只考虑此方向上的切削分力Fy和变形位移量y
K Fy (N / mm ) y
式中: Fy:切削力在Y方向的分力;
y:系统在切削力Fx、Fy、Fz共同作用下在Y方向上的变形;
y系 y机床 y夹具 y刀架 y工件
而工K系艺系yF系y统, K刚机床度算yF机式y床 , K夹具
Fy y夹具
K刀架
Fy y刀架
, K工件
Fy y刀架
所以工艺系统刚度为: K系
K机床 K夹具 K刀架 K工件
(2)工艺系统受力变形引起的误差及改善措施 工艺系统受力变形会引起工件的尺寸误差和形
状误差。减少工艺系统受力变形是保证加工精度的 有效途径之一。生产实际中常采取如下措施: 1)提高接触刚度 所谓接触刚度就是互相接触的两表 面抵抗变形的能力。提高接触刚度是提高工艺系统 刚度的关键。常用的方法是改善工艺系统主要零件 接触面的配合质量,使配合面的表面粗糙度和形状 精度得到改善和提高,实际接触面积增加,微观表 面和局部区域的弹性、塑性变形减少,从而有效地 提高接触刚度。
导轨误差可分为直线度误差、扭曲度误差、相互 位置误差三种形式。
3)机床传动链误差 传动链始末两端的联系是通过一系列的传动元件来实
现的,当这些传动元件存在加工误差、装配误差和
磨损时,就会破坏正确的运动关系,使工件产生加
工误差,这些误差即传动链误差。 1)尽量减少传动元件数量,缩短传动链,以缩小误
差的来源。
主轴的回转误差的三种
基本形式
径向跳动--瞬时回转轴 线沿平均回转轴线的径 向跳动运动。
轴向窜动--瞬时回转轴 线沿平均回转轴线方向 的轴向运动。
角度摆动--瞬时回转轴 线与平均回转轴线成一 倾斜角,但其交点位置 是固定不变的运动。
2)导轨误差
床身导轨既是装配机床各部件的基准件,又是保 证刀具与工件之间导向精度的导向件,因此 导轨误差对加工精度有直接的影响。
2)采用误差校正装置来提高传动精度。 3)提高传动链中各元件,尤其是末端元件的加工和
装配精度,以保证传动精度。
4)设法消除传动链中齿轮间的间隙,以提高传动精 度。
(3)刀、夹具制造误差 1)刀具的误差 刀具的制造误差对加工精度的影响,根据刀具种类
不同而异。当采用定尺寸刀具如钻头、铰刀、拉 刀、键槽铣刀等加工时,刀具的尺寸精度将直接 影响到工件的尺寸精度;当采用成形刀具如成形 车刀、成形铣刀等加工时,刀具的形状精度将直 接影响工件的形状精度;当采用一般刀具如车刀 、镗刀、铣刀等的制造误差对零件的加工精度并 无直接影响,但其磨损对加工精度、表面粗糙度 有直接的影响。
4)合理装夹工件,减少夹紧变形 当工件本身薄弱、 刚性差时,夹紧时应特别注意选择适当的夹紧方 法,尤其是在加工薄壁零件时,为了减少加工误 差,应使夹紧力均匀分布。缩短切削力作用点和 支承点的距离,提高工件刚度。
5)对相关部件预加载荷 例如,机床主轴部件在装 配时通过预紧主轴后端面的螺母给主轴滚动轴承 以预加载荷,这样不仅能消除轴承的配合间隙, 而且在加工开始阶段就使主轴与轴承有较大的实 际接触面积,从而提高了配合面间的接触刚度。
3)展成法 又称为范成法,它是依据零件曲面的成 形原理、通过刀具和工件的展成切削运动进行加工 的方法。展成法所得的被加工表面是刀刃和工件在 展成运动过程中所形成的包络面,刀刃必须是被加 工表面的共轭曲线。所获得的精度取决于刀刃的形 状和展成运动的精度。滚齿、插齿等均为展成法。 (3)获得位置精度的方法
1、工艺系统的几何误差
包括加工方法的原理误差、机床的几何误差、刀夹 具制造误差和调整误差等。
(1)原理误差
加工原理误差是指采用了近似的成形运动或近似的 刀刃轮廓进行加工而产生的误差。
如:1、滚齿,由于滚刀的刀刃数有限,加工出来的齿轮齿
形是有限个刀刃切成的折线;另,由于滚刀制造困难, 采用阿基米德基本蜗杆代替渐开线基本蜗杆,由此产生 的加工误差,则属于原理误差。
但过度时,脆性会增大,表面易剥落。 ③ 残余应力对耐磨性的影响 表面为压应力时,耐磨性高。
(2)对零件疲劳强度的影响
表面缺陷会引起应力集中,降低疲劳强度。若
表面存在一定的冷作硬化或残余压应力,疲劳强度 将会提高。
(3)对零件配合精度的影响 表面比较粗糙时,轮廓峰在工作中被逐渐磨掉, 零件尺寸发生变化,进而影响到配合性质。 一般来说,表面粗糙度应与加工精度相适应。
工件的位置精度取决于工件的安装(定位和夹 紧)方式及其精度。
1) 找正安装法 找正是用工具和仪表根据工件上有 关基准,找出工件有关几何要素相对于机床的正确 位置的过程。 2)夹具安装法 夹具是用以安装工件和引导刀具的 装置。在机床上安装好夹具,工件放在夹具中定位, 能使工件迅速获得正确位置,并使其固定在夹具和 机床上。因此,工件定位方便,定位精度高且稳定, 装夹效率也高。 3)机床控制法 利用机床本身所设置的保证相对位 置精度的机构保证工件位置精度的安装方法。如坐 标镗床、数控机床等。
成形法铣齿,由于铣刀分
八个刀号,每一个刀号 在相应组内齿数最少的 可获得精确地齿形,其 它齿数只能获得近似的 齿形。因此,铣齿产生 的加工误差也属于原理 误差。
(2)机床误差
机床几何误差包括机床本身各部件的制造误差、安装误差和 使用过程中的磨损引起的误差。这里着重分析对加工影响 较大的主轴回转误差、机床导轨误差以及传动链误差。
二、获得加工精度的方法 (1)获得尺寸精度的方法 1)试切法 通过试切─测量─调整─再试切,反复
进行到被加工尺寸达到要求的精度为止的加工方法。 试切法不需要复杂的装备,加工精度取决于工人的 技术水平和量具的精度,常用于单件小批生产。 2)调整法 按零件规定的尺寸预先调整机床、夹具、 刀具和工件的相互位置,并在加工一批零件的过程 中保持这个位置不变,以保证零件加工尺寸精度的 加工方法。调整法生产效率高,对调整工的要求高, 对操作工的要求不高,常用于成批及大量生产。
2)提高工件定位基面的精度和表面质量 工件的定位 基面如存在较大的尺寸、形位误差和表面质量差, 在承受切削力和夹紧力时可能产生较大的接触变形, 因此精密零件加工用的基准面需要随着工艺过程的 进行逐步提高精度。
3)设置辅助支承,提高工件刚度,减小受力变形 切 削力引起的加工误差往往是因为工件本身刚度不足 或工件各个部位刚度不均匀而产生的。当工件材料 和直径一定时,工件长度和切削分力是影响变形的 决定性因素。为了减少工件的受力变形,常采用中 心架或跟刀架,以提高工件的刚度,减小受力变形。
工艺系统受力变形是加工中一项很重要的原始误差 ,它严重的影响工件的加工精度。工艺系统的受 力变形通常是弹性变形,一般来说,工艺系统抵 抗弹性变形的能力越强,加工精度越高。工艺系 统抵抗外力使其变形的能力称为工艺系统的刚度 。工艺系统的刚度用切削力和在该力方向上所引 起的刀具和工件间相对变形位移的比值表示的。 由于切削力有三个分力,在切削加工中对加工精 度影响最大的是刀刃沿加工表面的法线方向(Y 方向上)的分力,因此计算工艺系统刚度时,通