7航空发动机叶片
航空发动机叶片关键技术发展现状分析
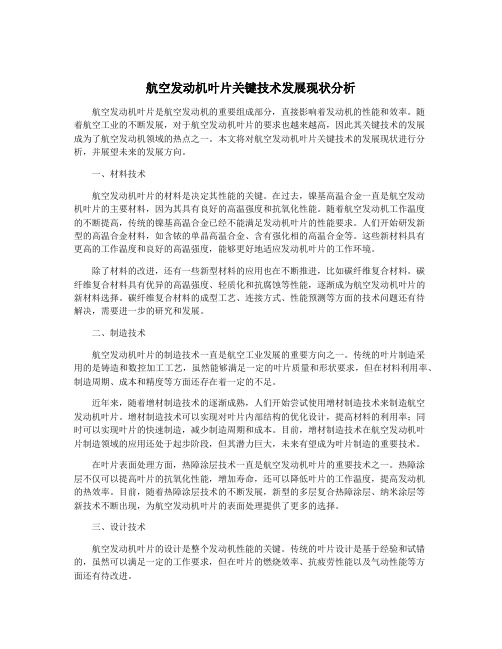
航空发动机叶片关键技术发展现状分析航空发动机叶片是航空发动机的重要组成部分,直接影响着发动机的性能和效率。
随着航空工业的不断发展,对于航空发动机叶片的要求也越来越高,因此其关键技术的发展成为了航空发动机领域的热点之一。
本文将对航空发动机叶片关键技术的发展现状进行分析,并展望未来的发展方向。
一、材料技术航空发动机叶片的材料是决定其性能的关键。
在过去,镍基高温合金一直是航空发动机叶片的主要材料,因为其具有良好的高温强度和抗氧化性能。
随着航空发动机工作温度的不断提高,传统的镍基高温合金已经不能满足发动机叶片的性能要求。
人们开始研发新型的高温合金材料,如含铱的单晶高温合金、含有强化相的高温合金等。
这些新材料具有更高的工作温度和良好的高温强度,能够更好地适应发动机叶片的工作环境。
除了材料的改进,还有一些新型材料的应用也在不断推进,比如碳纤维复合材料。
碳纤维复合材料具有优异的高温强度、轻质化和抗腐蚀等性能,逐渐成为航空发动机叶片的新材料选择。
碳纤维复合材料的成型工艺、连接方式、性能预测等方面的技术问题还有待解决,需要进一步的研究和发展。
二、制造技术航空发动机叶片的制造技术一直是航空工业发展的重要方向之一。
传统的叶片制造采用的是铸造和数控加工工艺,虽然能够满足一定的叶片质量和形状要求,但在材料利用率、制造周期、成本和精度等方面还存在着一定的不足。
近年来,随着增材制造技术的逐渐成熟,人们开始尝试使用增材制造技术来制造航空发动机叶片。
增材制造技术可以实现对叶片内部结构的优化设计,提高材料的利用率;同时可以实现叶片的快速制造,减少制造周期和成本。
目前,增材制造技术在航空发动机叶片制造领域的应用还处于起步阶段,但其潜力巨大,未来有望成为叶片制造的重要技术。
在叶片表面处理方面,热障涂层技术一直是航空发动机叶片的重要技术之一。
热障涂层不仅可以提高叶片的抗氧化性能,增加寿命,还可以降低叶片的工作温度,提高发动机的热效率。
目前,随着热障涂层技术的不断发展,新型的多层复合热障涂层、纳米涂层等新技术不断出现,为航空发动机叶片的表面处理提供了更多的选择。
航空发动机叶片关键技术发展现状分析
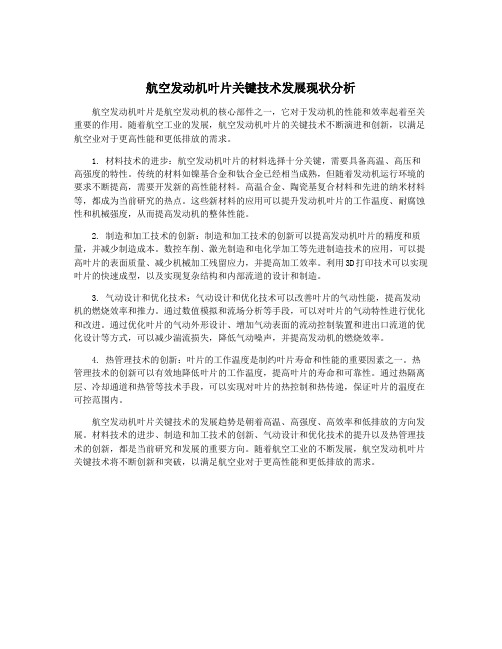
航空发动机叶片关键技术发展现状分析航空发动机叶片是航空发动机的核心部件之一,它对于发动机的性能和效率起着至关重要的作用。
随着航空工业的发展,航空发动机叶片的关键技术不断演进和创新,以满足航空业对于更高性能和更低排放的需求。
1. 材料技术的进步:航空发动机叶片的材料选择十分关键,需要具备高温、高压和高强度的特性。
传统的材料如镍基合金和钛合金已经相当成熟,但随着发动机运行环境的要求不断提高,需要开发新的高性能材料。
高温合金、陶瓷基复合材料和先进的纳米材料等,都成为当前研究的热点。
这些新材料的应用可以提升发动机叶片的工作温度、耐腐蚀性和机械强度,从而提高发动机的整体性能。
2. 制造和加工技术的创新:制造和加工技术的创新可以提高发动机叶片的精度和质量,并减少制造成本。
数控车削、激光制造和电化学加工等先进制造技术的应用,可以提高叶片的表面质量、减少机械加工残留应力,并提高加工效率。
利用3D打印技术可以实现叶片的快速成型,以及实现复杂结构和内部流道的设计和制造。
3. 气动设计和优化技术:气动设计和优化技术可以改善叶片的气动性能,提高发动机的燃烧效率和推力。
通过数值模拟和流场分析等手段,可以对叶片的气动特性进行优化和改进。
通过优化叶片的气动外形设计、增加气动表面的流动控制装置和进出口流道的优化设计等方式,可以减少湍流损失,降低气动噪声,并提高发动机的燃烧效率。
4. 热管理技术的创新:叶片的工作温度是制约叶片寿命和性能的重要因素之一。
热管理技术的创新可以有效地降低叶片的工作温度,提高叶片的寿命和可靠性。
通过热隔离层、冷却通道和热管等技术手段,可以实现对叶片的热控制和热传递,保证叶片的温度在可控范围内。
航空发动机叶片关键技术的发展趋势是朝着高温、高强度、高效率和低排放的方向发展。
材料技术的进步、制造和加工技术的创新、气动设计和优化技术的提升以及热管理技术的创新,都是当前研究和发展的重要方向。
随着航空工业的不断发展,航空发动机叶片关键技术将不断创新和突破,以满足航空业对于更高性能和更低排放的需求。
航空发动机叶片知多少(一)——风扇叶片简介

航空发动机叶⽚知多少(⼀)——风扇叶⽚简介如果经常坐飞机,那肯定都知道,飞机发动机前⾯有⼀圈很⼤很⼤的叶⽚。
没错,通常通过发动机外观我们只能看到发动机的风扇叶⽚(涡扇发动机)或者涡桨叶⽚(涡桨发动机),也就是我们通常在飞机前⾯能看到的很⾼很⼤的叶⽚。
那飞机发动机上究竟是不是只有我们看到的风扇叶⽚啊?如果你只见树⽊,不见森林,那就错了,风扇叶⽚论数量只占到发动机中叶⽚总数的2%左右,还有很多叶⽚是什么呢?下⾯跟着⼩编⼀起来看看发动机上的叶⽚类型,以及每种叶⽚不同的⼯作原理。
今天我们先来说说——修长的风扇叶⽚!就风扇叶⽚⽽⾔,⽬前世界上⽬前最⼤风扇叶⽚是GE9X的风扇叶⽚它的叶尖直径为3.4m,采⽤GE公司的第4代碳纤维复合材料制成。
3.4m是什么概念,也就是说单个叶⽚安在发动机上,它的半径⼏乎相当于成年⼈的⾝⾼。
GE9X叶⽚钛合⾦风扇叶⽚风扇叶⽚是最容易观察到的叶⽚。
风扇叶⽚的直径⼀般⽐较⼤,从⼀⽶到三⽶多不等。
风扇叶⽚的主要作⽤是把进⼊发动机的空⽓进⾏初步压缩,压缩后的⽓体分两路,⼀路进⼊内涵道进⾏继续压缩,⼀路流进外涵道直接⾼速排出,产⽣巨⼤的推⼒。
可能觉得不可思议,其实涡扇发动机80%以上的推⼒都是由直接排出外涵道的⽓体提供的。
风扇叶⽚⼀般是由钛合⾦以及复合材料制成。
其中,GE的风扇叶⽚⼀般都是碳纤维复合材料。
复合材料的⽐强度很⾼,所以发动机转速,⽐较⾼的复合材料是不存在强度问题。
GE90发动机复合材料风扇叶⽚:直径达3.124m.叶⾝与叶根⽤IM7中长碳纤维与韧性好的8511-7环氧树脂组成的被称为”⼤⼒神”的8511-7/IM7复合材料制成⼀整体。
在叶⾝的压⼒⾯上喷涂聚胺酯防腐涂层,在叶背上涂有聚胺酯漆。
为提⾼叶⽚抗⼤鸟撞击的能⼒,叶⽚前缘从上⾄下包有钛合⾦薄⽚,在叶盆尾缘位于叶尖1/3的⾯积上也包有钛合⾦薄⽚。
钛合⾦薄⽚是⽤3MAF191胶粘到复合材料的叶⾝上的。
为防⽌叶⽚在叶尖与尾缘处材料脱层,⽤Kevlar材料制成的线在叶尖与尾缘处进⾏了缝合。
航空发动机叶片技术指标
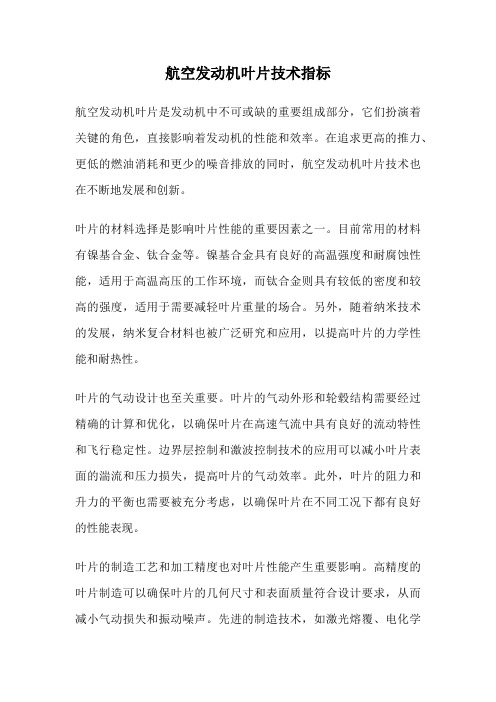
航空发动机叶片技术指标航空发动机叶片是发动机中不可或缺的重要组成部分,它们扮演着关键的角色,直接影响着发动机的性能和效率。
在追求更高的推力、更低的燃油消耗和更少的噪音排放的同时,航空发动机叶片技术也在不断地发展和创新。
叶片的材料选择是影响叶片性能的重要因素之一。
目前常用的材料有镍基合金、钛合金等。
镍基合金具有良好的高温强度和耐腐蚀性能,适用于高温高压的工作环境,而钛合金则具有较低的密度和较高的强度,适用于需要减轻叶片重量的场合。
另外,随着纳米技术的发展,纳米复合材料也被广泛研究和应用,以提高叶片的力学性能和耐热性。
叶片的气动设计也至关重要。
叶片的气动外形和轮毂结构需要经过精确的计算和优化,以确保叶片在高速气流中具有良好的流动特性和飞行稳定性。
边界层控制和激波控制技术的应用可以减小叶片表面的湍流和压力损失,提高叶片的气动效率。
此外,叶片的阻力和升力的平衡也需要被充分考虑,以确保叶片在不同工况下都有良好的性能表现。
叶片的制造工艺和加工精度也对叶片性能产生重要影响。
高精度的叶片制造可以确保叶片的几何尺寸和表面质量符合设计要求,从而减小气动损失和振动噪声。
先进的制造技术,如激光熔覆、电化学加工等,可以提高叶片的表面质量和耐热性,延长叶片的使用寿命。
叶片的结构强度和振动特性也需要被充分考虑。
叶片在高速旋转和高温环境下会承受巨大的离心力和热应力,因此需要具有足够的强度和刚度来抵御这些力的作用。
同时,叶片的振动特性也需要被控制在一定范围内,以防止共振或失稳现象的发生。
航空发动机叶片技术指标包括材料选择、气动设计、制造工艺、结构强度和振动特性等多个方面。
在不断追求发动机性能和效率提升的同时,航空发动机叶片技术也在不断创新和改进,以满足航空工业的需求。
航空发动机叶片关键技术发展现状分析
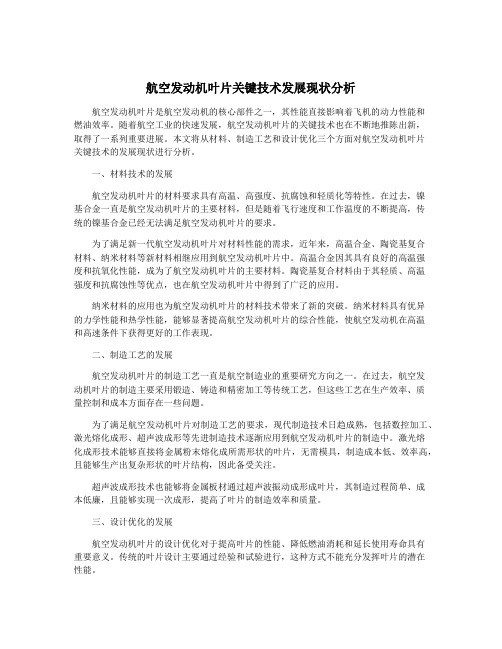
航空发动机叶片关键技术发展现状分析航空发动机叶片是航空发动机的核心部件之一,其性能直接影响着飞机的动力性能和燃油效率。
随着航空工业的快速发展,航空发动机叶片的关键技术也在不断地推陈出新,取得了一系列重要进展。
本文将从材料、制造工艺和设计优化三个方面对航空发动机叶片关键技术的发展现状进行分析。
一、材料技术的发展航空发动机叶片的材料要求具有高温、高强度、抗腐蚀和轻质化等特性。
在过去,镍基合金一直是航空发动机叶片的主要材料,但是随着飞行速度和工作温度的不断提高,传统的镍基合金已经无法满足航空发动机叶片的要求。
为了满足新一代航空发动机叶片对材料性能的需求,近年来,高温合金、陶瓷基复合材料、纳米材料等新材料相继应用到航空发动机叶片中。
高温合金因其具有良好的高温强度和抗氧化性能,成为了航空发动机叶片的主要材料。
陶瓷基复合材料由于其轻质、高温强度和抗腐蚀性等优点,也在航空发动机叶片中得到了广泛的应用。
纳米材料的应用也为航空发动机叶片的材料技术带来了新的突破。
纳米材料具有优异的力学性能和热学性能,能够显著提高航空发动机叶片的综合性能,使航空发动机在高温和高速条件下获得更好的工作表现。
二、制造工艺的发展航空发动机叶片的制造工艺一直是航空制造业的重要研究方向之一。
在过去,航空发动机叶片的制造主要采用锻造、铸造和精密加工等传统工艺,但这些工艺在生产效率、质量控制和成本方面存在一些问题。
为了满足航空发动机叶片对制造工艺的要求,现代制造技术日趋成熟,包括数控加工、激光熔化成形、超声波成形等先进制造技术逐渐应用到航空发动机叶片的制造中。
激光熔化成形技术能够直接将金属粉末熔化成所需形状的叶片,无需模具,制造成本低、效率高,且能够生产出复杂形状的叶片结构,因此备受关注。
超声波成形技术也能够将金属板材通过超声波振动成形成叶片,其制造过程简单、成本低廉,且能够实现一次成形,提高了叶片的制造效率和质量。
三、设计优化的发展航空发动机叶片的设计优化对于提高叶片的性能、降低燃油消耗和延长使用寿命具有重要意义。
航空发动机叶片材料及制造技术现状

航空发动机叶片材料及制造技术现状
摘要:
航空发动机叶片是航空发动机的关键组件之一,其材料性能和制造技术直接影响发动机的性能和可靠性。
本文对航空发动机叶片的材料和制造技术进行了详细介绍,并分析了目前的发展趋势和面临的挑战。
主要内容包括叶片材料的分类和性能要求、叶片制造的工艺流程、先进材料与制造技术的应用以及未来的发展方向。
第一部分:引言
1.1研究背景
1.2研究目的
第二部分:叶片材料的分类和性能要求
2.1叶片材料的分类
2.2叶片材料的性能要求
2.3典型叶片材料探讨
第三部分:叶片制造的工艺流程
3.1制造流程的概述
3.2锻造工艺
3.3喷涂工艺
3.4焊接工艺
3.5其他制造工艺的研究进展
第四部分:先进材料与制造技术的应用
4.1高温合金材料
4.2复合材料的应用
4.3多材料结构的发展
4.4先进制造技术的应用
第五部分:未来的发展方向
5.1合金材料的进一步发展
5.2复合材料的应用前景
5.3先进制造技术的创新
5.4综合应用与跨学科研究
第六部分:结论
6.1发动机叶片材料和制造技术的现状
6.2发展趋势和挑战
6.3未来研究的重点与方向
本文以航空发动机叶片材料和制造技术为研究对象,从材料的分类和
性能要求、制造工艺流程、先进材料与制造技术的应用以及未来的发展方
向等方面进行了全面深入的探讨。
通过分析现有材料和技术的优势和缺陷,提出了未来研究的重点与方向,并指出了面临的挑战。
本文对航空发动机
叶片的材料和制造技术的研究具有指导意义,也为相关领域的进一步研究
提供了参考。
(整理)(7)航空发动机叶片.

发动机叶片一、 发动机与飞机 1. 发动机种类 1) 涡轮喷气发动机(WP )WP5、WP6、WP7、……WP13 2) 涡轮螺桨发动机(WJ )WJ5、WJ6、WJ7 3) 涡轮风扇发动机(WS )WS9、WS10、WS11 4) 涡轮轴发动机(WZ )WZ5、WZ6、WZ8、WZ9 5)活塞发动机(HS )HS5、HS6、HS92. 发动机的结构与组成燃气涡轮发动机主要由压气机、燃烧室和涡轮三大部件以及燃油系统、滑油系统、空气系统、电器系统、进排气边系统及轴承传力系统等组成。
(发动机的整体构造如下图1)三大部件中除燃烧外的压气机与涡轮都是由转子和静子构成,静子由内、外机匣和导向(整流)叶片构成;转子由叶片盘、轴及轴承构成,其中叶片数量最多(见表1~5)3. 发动机工作原理及热处理过程风扇高压压气机燃烧室高压涡轮 低压涡轮加力燃烧室喷管发动机的整体结构工作原理:发动机将大量的燃料燃烧产生的热能,势能给涡轮导向器斜切口膨胀产生大量的动能,其一部分转换成机械功驱动压气机和附件,剩余能由尾喷管膨胀加速产生推力。
热力过程:用p-υ或T-S 图来表示发动机的热力过程:4. 飞机与发动机发动机是飞机的动力,也是飞机的心脏,不同用途的飞机配备不同种类的发动机。
如: 1)军民用运输机、轰炸机、客机、装用WJ 、WS 、WP 类发动机。
2)强击机、歼击机、教练机、侦察机、装用WP 、WS 、HS类发动机。
3)军民用直升机装用WZ 类发动机。
二、 叶片在燃气涡轮发动机中叶片无论是压气机叶片还是涡轮叶片,它们的数量最多,而发动机就是依靠这众多的叶片完成对气体的压缩和膨胀以及以最高的效率产生强大的动力来推动飞机前进的工作。
叶片是一种特殊的零件,它的数量多,形状复杂,要求高,加工难度大,而且是故障多发的零件,一直以来各发动机厂的生产的关键,因此对其投入的人力、物力、财力都是比较大的,而且国内外发动机厂家正以最大的努力来提高叶片的性能,生产能力及质量满足需要。
航空发动机叶片结构材料疲劳寿命

航空发动机叶片结构材料疲劳寿命航空发动机是飞机的心脏,而叶片是发动机中最重要的零部件之一。
发动机叶片的结构材料和疲劳寿命对于发动机的性能和可靠性至关重要。
本文将深入探讨航空发动机叶片结构材料的选择以及疲劳寿命的问题。
一、航空发动机叶片的结构材料选择航空发动机叶片需要具备优异的力学性能、耐高温性能和抗腐蚀性能。
通常情况下,航空发动机叶片的结构材料主要选择高温合金材料。
这种材料具有高强度、高硬度和良好的耐热性能,能够承受高温高压的工作环境。
航空发动机叶片的结构材料需要具备以下几个方面的性能:1. 高温强度:航空发动机叶片在工作过程中需要承受高温和高速气流的冲击,因此材料需要具备出色的高温强度,保证叶片在高温环境下不会出现塑性变形或失效。
2. 耐腐蚀性:航空发动机叶片在工作过程中会受到酸性气体和高速气流的腐蚀,因此材料需要具备良好的耐腐蚀性能,以延长叶片的使用寿命。
3. 抗疲劳性:航空发动机叶片在运行中会受到循环载荷的作用,因此材料需要具备良好的抗疲劳性能,以保证叶片在循环载荷作用下不会出现疲劳断裂。
目前,航空发动机叶片常用的高温合金材料有镍基合金和钛基合金。
镍基合金具有良好的高温强度和抗腐蚀性能,广泛应用于航空发动机叶片的制造。
钛基合金则具有较低的密度和优秀的热膨胀性能,适用于一些特定的工作环境。
二、航空发动机叶片疲劳寿命的影响因素航空发动机叶片的疲劳寿命受到多种因素的影响:1. 材料的特性:航空发动机叶片的结构材料应具备良好的抗疲劳性能,以延长叶片的使用寿命。
2. 工作环境的影响:航空发动机叶片在高温、高速气流的环境中工作,这些工作环境对叶片的疲劳寿命有着直接的影响。
高温环境会加快材料的疲劳破坏速度,而高速气流则会加剧叶片的振动和疲劳载荷。
3. 加工和制造工艺:航空发动机叶片的制造过程中可能存在缺陷,如裂纹、凹陷等。
这些缺陷会对叶片的疲劳寿命产生负面影响。
4. 维护和保养:航空发动机叶片的维护和保养对于延长叶片的疲劳寿命至关重要。
航空发动机叶片关键技术发展现状分析
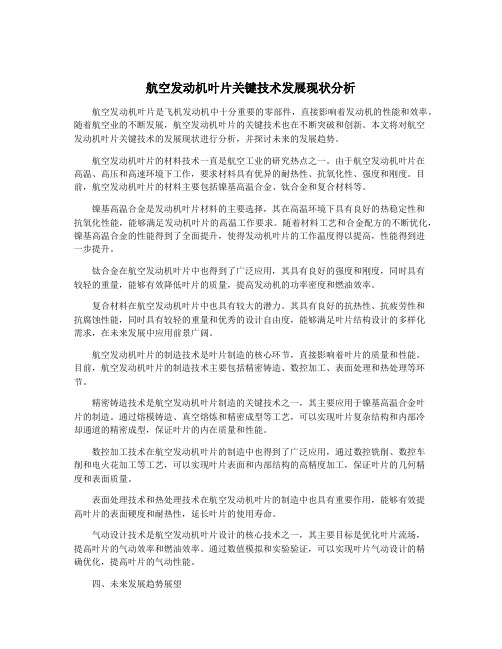
航空发动机叶片关键技术发展现状分析航空发动机叶片是飞机发动机中十分重要的零部件,直接影响着发动机的性能和效率。
随着航空业的不断发展,航空发动机叶片的关键技术也在不断突破和创新。
本文将对航空发动机叶片关键技术的发展现状进行分析,并探讨未来的发展趋势。
航空发动机叶片的材料技术一直是航空工业的研究热点之一。
由于航空发动机叶片在高温、高压和高速环境下工作,要求材料具有优异的耐热性、抗氧化性、强度和刚度。
目前,航空发动机叶片的材料主要包括镍基高温合金、钛合金和复合材料等。
镍基高温合金是发动机叶片材料的主要选择,其在高温环境下具有良好的热稳定性和抗氧化性能,能够满足发动机叶片的高温工作要求。
随着材料工艺和合金配方的不断优化,镍基高温合金的性能得到了全面提升,使得发动机叶片的工作温度得以提高,性能得到进一步提升。
钛合金在航空发动机叶片中也得到了广泛应用,其具有良好的强度和刚度,同时具有较轻的重量,能够有效降低叶片的质量,提高发动机的功率密度和燃油效率。
复合材料在航空发动机叶片中也具有较大的潜力。
其具有良好的抗热性、抗疲劳性和抗腐蚀性能,同时具有较轻的重量和优秀的设计自由度,能够满足叶片结构设计的多样化需求,在未来发展中应用前景广阔。
航空发动机叶片的制造技术是叶片制造的核心环节,直接影响着叶片的质量和性能。
目前,航空发动机叶片的制造技术主要包括精密铸造、数控加工、表面处理和热处理等环节。
精密铸造技术是航空发动机叶片制造的关键技术之一,其主要应用于镍基高温合金叶片的制造。
通过熔模铸造、真空熔炼和精密成型等工艺,可以实现叶片复杂结构和内部冷却通道的精密成型,保证叶片的内在质量和性能。
数控加工技术在航空发动机叶片的制造中也得到了广泛应用,通过数控铣削、数控车削和电火花加工等工艺,可以实现叶片表面和内部结构的高精度加工,保证叶片的几何精度和表面质量。
表面处理技术和热处理技术在航空发动机叶片的制造中也具有重要作用,能够有效提高叶片的表面硬度和耐热性,延长叶片的使用寿命。
航空发动机叶片的生产制造技术

航空发动机叶片的生产制造技术航空发动机叶片是航空发动机的重要组成部分,它在整个发动机运行过程中承受着极高的温度、压力和振动等力载荷。
因此,航空发动机叶片的生产制造技术对航空发动机的性能、可靠性和寿命都有着重要影响。
在这篇文章中,我们将详细介绍航空发动机叶片的生产制造技术。
1.材料选择与预处理在进行叶片制造之前,需要对材料进行预处理,以去除杂质、提高材料的均匀性和晶粒细化。
预处理方法包括热处理、化学处理和表面处理等。
2.叶片造型与设计叶片的造型与设计是叶片制造的关键环节。
叶片的形状、结构和轮毂之间的连接方式直接影响着叶片的性能和寿命。
通常情况下,叶片的内部结构是由空腔、腔板和护腔等组成的。
这些结构可以提高叶片的强度和刚度,在高速旋转过程中减小振动和压力损失。
叶片的形状通常采用空气动力学原理和结构力学原理进行设计,以提高发动机的效率和推力。
同时,还需要考虑到叶片的制造可行性和工艺性,确保叶片可以顺利制造出来。
3.叶片制造工艺铸造是叶片制造的主要工艺,通常采用真空熔模铸造或单晶铸造等方法。
真空熔模铸造是指将预熔的合金材料注入到陶瓷模具中,然后进行冷却凝固,最后得到具有复杂形状和精密尺寸的叶片。
单晶铸造则是通过在模具中形成单一晶体结构,去除晶界和晶粒边界,提高叶片的高温性能和抗腐蚀性能。
锻造是叶片制造的另一种常见工艺,通过对金属材料进行加热和塑性变形,使其达到所需的形状和尺寸。
复合材料制造是使用纤维增强树脂基体材料制造叶片的工艺。
这种工艺具有良好的抗腐蚀性和高温性能,适用于制造大型和复杂形状的叶片。
机加工是对叶片进行最后加工和整形的工艺。
这包括数控机床加工、电火花加工、冲压和磨削等方法,以保证叶片的几何尺寸和表面质量。
热处理是对叶片进行热处理,以改善材料的组织结构和性能。
常见的热处理方法包括固溶处理、时效处理和表面处理等。
4.质量控制与检测质量控制主要通过严格的制造工艺和生产流程来实现,确保叶片的尺寸和形状的精确性。
航空发动机事故“第1杀手”——叶片

航空发动机事故“第1杀手”——叶片2018年4月17日,西南航空1380号航班(Southwest Airlines Flight 1380)的一架波音737型客机在巡航状态时,突然发生发动机爆炸事故,事故导致1人遇难,148人生还。
初步的调查结果:这次事故是由于发动机发生了非包容性故障。
航空事故历史中,发动机叶片损坏而引发的飞机事故还真不少见2014年,我国南航CZ3739航班飞机引擎空中着火,事后调查显示发生故障的发动机进口处,压气机风扇的叶片有断裂。
据推测,有可能是叶片断掉后进入发动机内,损伤发动机进气流场,导致后者发生“畸变”,进而形成“喘振”。
所幸的是这次事故没有造成人员伤亡。
2016年8月27日,一架西南航空的波音737-700型客机在执飞新奥尔良飞奥兰多的航班时,同样发生CFM56-7B型发动机的风扇叶片非包容性故障,所幸此次事故中客机安全降落,并无更为严重事故发生。
其实据不完全统计,我国空军现役飞行的发动机事故中,80%都跟发动机叶片断裂失效有关。
而这么娇贵的部分一旦发生断裂失效,对发动机乃至整个飞机的损害往往是致命性的。
可见,发动机叶片断裂不容小觑,那么今天小编就带领大家全方位认识一下发动机叶片的断裂,看看它为啥有这么惊人的破坏力。
从理论上看,涡轮叶片断裂的故障机理有疲劳、超应力、蠕变、腐蚀、磨损等。
疲劳发动机工作时,由于经常起动、加速、减速、停车以及其他条件的影响,会使涡轮各部件承受复杂的循环载荷作用,使得叶片经受大量弹性应力循环,最终引起高周疲劳、低周疲劳或热疲劳,使得涡轮叶片断裂。
涡轮发动机叶片根部疲劳裂纹扩展超应力涡轮叶片由于其形状的不规则,叶片中存在应力集中部位。
尽管在设计中往往会采取一系列措施加以避免,但实际上,超应力仍然是造成涡轮叶片断裂的一个原因。
发动机叶片中应力分布建模蠕变高温环境下,蠕变断裂是涡轮叶片主要的失效形式之一。
随着涡轮后燃气温度从20世纪50年代的1150K增加到现在的2000K,蠕变将导致叶片的塑性变形过大甚至产生蠕变断裂。
航空发动机叶片关键制造技术

航空发动机叶片关键制造技术首先,航空发动机叶片的材料选择是制造过程中的一个重要考虑因素。
一般来说,叶片需要具备高温和高压力环境下的稳定性和强度。
因此,钛合金和镍基合金是常用的叶片材料。
钛合金具有良好的耐高温性能和强度,但是制造难度较大;而镍基合金则具有较高的强度和抗蠕变能力。
其次,航空发动机叶片的制造通常采用铸造和锻造两种工艺。
铸造是制造大型和复杂形状叶片的常用方法。
树脂砂铸造和单晶铸造是两种常见的铸造工艺。
树脂砂铸造可以制造出较大规模的叶片,而单晶铸造可以制造出无晶粒界的单晶叶片,提高了叶片的耐高温性能。
锻造是制造高强度和复杂形状叶片的一种有效方法。
采用锻造工艺可以提高叶片的综合机械性能和抗蠕变能力。
另外,表面处理也是航空发动机叶片制造中的一个重要环节。
表面处理可以改善叶片的表面质量和适应性。
例如,机械抛光和电解抛光可以提高叶片的光洁度和表面平整度。
化学镀和阳极氧化等技术可以提高叶片的耐腐蚀性和抗氧化性。
此外,还可以通过表面涂覆特殊涂层来提高叶片的热防护能力和抗磨损性能。
最后,航空发动机叶片的质量控制也是制造过程中的一项重要任务。
叶片的尺寸、形状和材料性能需要进行严格的检测和测试。
通常采用的方法包括非破坏性检测、尺寸测量和材料性能测试。
非破坏性检测可以通过超声波检测、X射线检测和磁粉检测等方法来检测叶片内部的隐性缺陷。
尺寸测量可以通过光学投影仪、三坐标测量机和激光扫描仪等设备来进行。
材料性能测试通常包括拉伸、硬度和金相显微组织分析等。
总之,航空发动机叶片的关键制造技术涉及材料选择、工艺选择、表面处理和质量控制等方面。
通过不断提升制造技术,可以制造出更高质量、更高性能的航空发动机叶片,提升整个航空发动机的性能和可靠性。
航空发动机叶片关键技术发展现状分析

航空发动机叶片关键技术发展现状分析
航空发动机叶片是航空发动机中至关重要的部件之一,直接关乎整个发动机的性能和使用寿命。
随着航空工业的发展和航空市场的需求增加,对于航空发动机叶片的要求也越来越高,不断地提升着相关的技术水平和研究层面。
一、材料技术的创新
航空发动机叶片作为汽机、燃气轮机等发动机的核心部件,材料选择的优劣直接影响整个发动机的性能。
传统的金属叶片材料的弊端在于重量大,使得整个发动机的重量也增加了很多,因此航空领域开始对高性能陶瓷材料、复合材料以及高温合金材料进行研究和应用,使得发动机叶片具有更高的耐腐蚀性、更好的强韧性和高温性能,保证了整个发动机在高温和高压的环境下也能够正常工作。
二、精密处理技术的发展
航空发动机叶片的形状和尺寸非常精密,特别是在叶尖区域的加工精度要求非常高。
因此,越来越多的碳纤维复合材料叶片在生产过程中采用了精密数控加工技术,使得发动机叶片具有更高的几何精度和表面粗糙度,同时也保证了叶片在高温下不会发生变形。
三、减重技术的突破
随着航空市场逐渐趋向轻量化发展,航空发动机叶片在减轻重量方面也取得了许多突破。
早期采用的金属材料叶片通常会在叶片表面采用钛合金涂层,以降低热膨胀系数和增加叶片的寿命,但是涂层的开销也很大。
现在,航空叶片在材料上采用的是复合材料或高温合金材料,不仅重量大幅降低了,可以更好地承受高温高压环境的影响,而且还可以采用空心的设计,进一步减轻叶片的重量。
B737-300飞机发动机风扇叶片检查标准
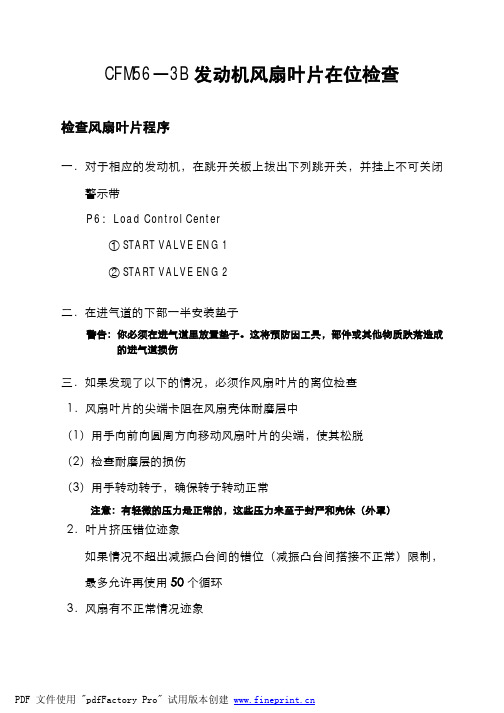
图2
8.叶尖 (1)叶尖前缘的卷曲在叶片的数量上是没有限制的,只要
a.与叶尖交叉的卷曲,延伸不超过 0.5 英寸(12.7 毫米) b.叶尖前缘向下的卷曲,延伸不超过 0.5 英寸(12.7 毫米)
PDF 文件使用 "pdfFactory Pro" 试用版本创建
c.与最初轮廓线的最大偏斜不超过 0.25 英寸(6.3 毫米) d.偏转的角度不超过 60 度 (2)最多有 6 个叶片在叶尖前缘出现卷曲是允许的,但限制是: a.与叶尖交叉的卷曲,延伸不超过 1.3 英寸(33 毫米)(和值) b.叶尖前缘向下的卷曲,延伸不超过 2.0 英寸(51 毫米)(和值) c.与最初轮廓线的最大偏斜不超过 0.6 英寸(15 毫米)(和值) d.偏斜的角度不超过 60 度 e.在这样的指定条件下,不能有多于 3 个相邻的叶片有卷曲 (3)当 1 个叶片的叶尖前缘出现卷曲是允许的,但限制是: a.与叶尖交叉的卷曲,延伸不超过 2.0 英寸(51 毫米) b.叶尖前缘向下的卷曲,延伸不超过 2.0 英寸(51 毫米) c.与最初轮廓线的最大偏斜不超过 1.0 英寸(25 毫米) d.偏斜的角度不超过 45 度 (4)叶尖后缘的卷曲在数量上是没有限制的,只要 a.与叶尖交叉的卷曲,延伸不超过 0.5 英寸(12.7 毫米) b.叶尖前缘向下的卷曲,延伸不超过 0.5 英寸(12.7 毫米) c.与最初轮廓线的最大偏斜不超过 0.25 英寸(6.3 毫米) d.偏斜的角度不超过 60 度 (5)最多有 6 个叶片在叶尖后缘出现卷曲是允许的,但限制是: a.与叶尖交叉的卷曲,延伸不超过 1.0 英寸(25 毫米)(和值) b.叶尖前缘向下的卷曲,延伸不超过 1.0 英寸(25 毫米)(和值) c.与最初轮廓线的最大偏斜不超过 0.3 英寸(7.6 毫米)
航空发动机叶片的设计与优化研究

航空发动机叶片的设计与优化研究随着航空业的高速发展,航空发动机成为了飞机性能的核心。
发动机的性能与效率直接影响到机身的推进力以及燃料的消耗情况。
而发动机叶片作为发动机的关键部件之一,其设计和优化研究则成为了航空工程师们关注的焦点。
一、叶片的基本原理与功能叶片是组成航空发动机的关键组件,相当于人体的肺。
它们的设计和优化关乎到飞机的性能和安全。
首先,叶片的主要功能是通过产生推力将飞机的动力传递给气流,实现机身的推进。
其次,叶片还需要具备良好的强度和耐热性能,能够在高温工况下保持正常运转。
最后,叶片的设计还需要考虑到气动和机械方面的因素,确保在飞行过程中叶片的性能和稳定性。
二、叶片设计的基本原则在航空发动机叶片的设计过程中,航空工程师需要遵循一些基本原则来确保叶片的性能和效率。
首先,叶片的设计需要通过数值模拟和实验验证来获得最优的气动性能。
这包括减小阻力、提高升力和降低噪音。
其次,叶片的形状设计要考虑到最大限度地减小气动加载和振动,以提高叶片的耐久性和可靠性。
此外,通过降低材料的重量来减小叶片的质量,进而提高发动机的功率和效率成为了研究的重点。
三、叶片设计的优化方法为了实现叶片设计的优化,航空工程师们采用了多种方法和技术。
其中,计算流体力学(CFD)是一种常用的数值模拟工具,可以对叶片的气动性能进行详细的分析和预测。
通过建立准确的数值模型,在计算机上模拟风洞试验,可以大大减少实验成本和时间,并有效地提高设计效率。
此外,还有一些优化算法,如遗传算法、粒子群算法和模拟退火算法等,可以用于叶片形状的参数优化。
这些算法通过迭代计算和比较,逐渐找到全局最优解,从而改进叶片的性能和效率。
四、叶片材料的选择与优化除了叶片的形状设计,材料的选择和优化也对叶片的性能和效率起着至关重要的作用。
目前,航空工程师们普遍使用高温合金和复合材料来制造叶片。
高温合金具有良好的耐热性和刚性,可以在高温环境下保持较好的稳定性。
而复合材料则具有较低的密度和较高的强度,可以减轻叶片的质量,进而提高发动机的性能和效率。
航空发动机叶片材料及制造技术现状
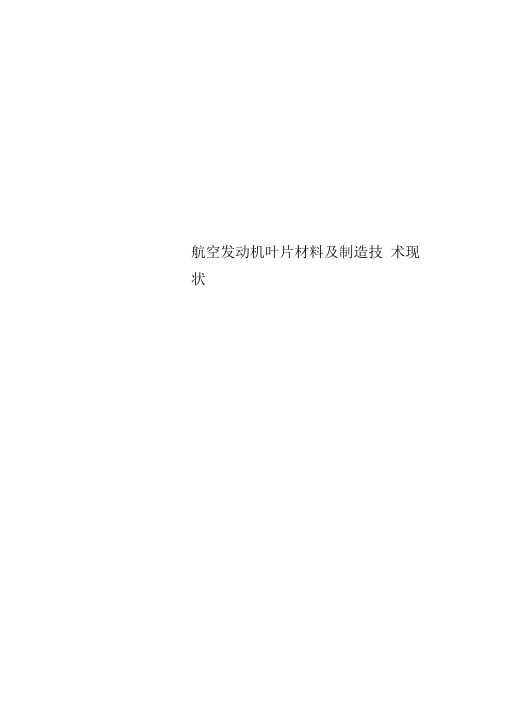
航空发动机叶片材料及制造技术现状Thrust航空发动机叶片材料及制造技术现状在航空发动机中,涡轮叶片由于处于温度最高、应力最复杂、环境最恶劣 的部位而被列为第一关键件,并被誉为“王冠上的明珠”.涡轮叶片的性能水 平,特别是承温能力,成为一种型号发动机先进程度的重要标志,在一定意义 上,也是一个国家航空工业水平的显著标志【007】。
航空发动机不断追求髙推重比,使得变形高温合金和铸造髙温合金难以满 足其越来越高的温度及性能要求,因而国外自70年代以来纷纷开始研制新型高 溫合金*先后研制了定向凝固高温合金"单晶高温合金等具有优异高温性能的 新材料;单晶高温合金已经发展到了第3代° 80年代,又开始研制了陶瓷叶片材 料,在叶片上开始采用防腐、隔热涂层等技术。
1航空发动机原理简介航空发动机主要分民用和军用两种。
图】是普惠公司民用涡轮发动机主要构 件;图2是军用发动机的工作原理示意图:图3是飞机涡轮发动机内的温度、气 流速度和压力分布乍图4是罗尔斯■罗伊斯喷气发动机内温度和材料分布;图5为 航空发动机用不同材料用量的发展变化情况。
Twn Spool Sha^l la Tum ,the Fan and I he CfflnpmBoraTurbrne 漳 Tiim Oycer Sh»fl.Low PressureTurbtne ta Turn Inner ShadLow PflHb&u 帕 CwimswrFin Air Bypassing U IA Jal Engm*图1普惠公司民用涡轮发动机主要构件k>itin-rlw oih'Hb-Mwt图2 EJ200军用飞机涡轮发动机的工作原理LIANG• riWfdvbu 麗虹r* f ■ 出 K in piwJuiA- th«ih*-inwwKHi ■■ ihv1vrferinR«i'■L・LMiv M Ann o4 tHp^-vki-d U«a |I H 』lunj wikncid thmu^ IwliripwkdirwtT IK 。
航空发动机叶片高温失效机制探讨

航空发动机叶片高温失效机制探讨一、航空发动机叶片概述航空发动机叶片是航空发动机中的关键部件之一,它们负责将燃料燃烧产生的能量转换为机械能,进而推动飞机前进。
由于航空发动机在运行过程中需要承受极高的温度和压力,因此叶片的材料和设计必须能够承受这些极端条件。
叶片的高温失效不仅会影响发动机的性能,还可能导致严重的安全事故。
因此,研究航空发动机叶片的高温失效机制对于提高发动机的可靠性和安全性至关重要。
1.1 航空发动机叶片的功能与结构航空发动机叶片通常分为压气机叶片和涡轮叶片两种。
压气机叶片的主要作用是压缩进入发动机的空气,而涡轮叶片则利用燃烧产生的高温高压气体推动发动机转动。
叶片通常由金属合金制成,这些合金必须具备良好的高温强度、抗蠕变性和抗氧化性。
1.2 航空发动机叶片的材料选择为了满足高温环境下的工作要求,航空发动机叶片的材料选择至关重要。
常用的材料包括镍基超合金、钴基超合金和钛合金等。
这些材料在高温下具有优异的机械性能和抗腐蚀性能,能够保证叶片在极端条件下的稳定性和耐久性。
二、航空发动机叶片的高温失效机制航空发动机叶片在高温环境下工作时,可能会因为多种原因发生失效。
这些失效机制包括热疲劳、热腐蚀、热冲击、氧化和蠕变等。
了解这些失效机制对于设计更可靠的叶片材料和结构至关重要。
2.1 热疲劳失效热疲劳是指叶片在反复的热循环作用下,由于温度变化引起的热应力超过材料的疲劳极限而导致的失效。
热疲劳通常发生在叶片的根部和边缘,这些区域的应力集中较大。
为了提高叶片的热疲劳寿命,可以通过优化材料的微观结构和表面处理来提高其抗疲劳性能。
2.2 热腐蚀失效热腐蚀是指在高温和腐蚀性环境中,叶片材料表面发生化学反应,导致材料性能下降的现象。
热腐蚀通常发生在燃烧室和涡轮部分,这些区域的高温和腐蚀性气体会加速材料的腐蚀过程。
为了防止热腐蚀,可以采用涂层技术在叶片表面形成保护层,以隔离腐蚀性气体和材料的直接接触。
2.3 热冲击失效热冲击是指叶片在极短时间内经历剧烈的温度变化,导致材料内部产生热应力,进而引发裂纹和断裂的现象。
航空发动机叶片分类
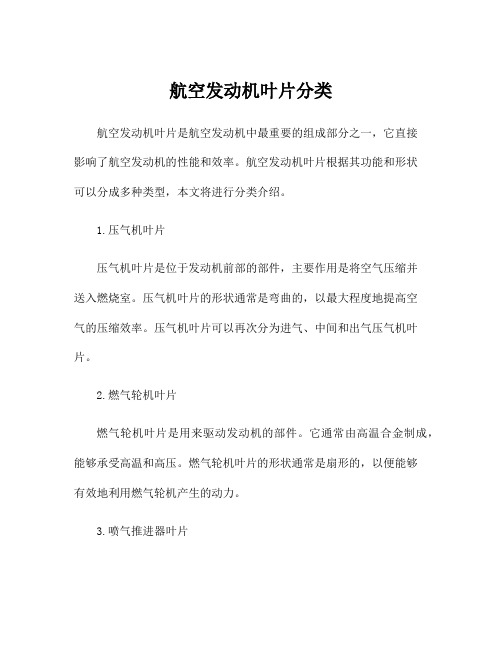
航空发动机叶片分类航空发动机叶片是航空发动机中最重要的组成部分之一,它直接影响了航空发动机的性能和效率。
航空发动机叶片根据其功能和形状可以分成多种类型,本文将进行分类介绍。
1.压气机叶片压气机叶片是位于发动机前部的部件,主要作用是将空气压缩并送入燃烧室。
压气机叶片的形状通常是弯曲的,以最大程度地提高空气的压缩效率。
压气机叶片可以再次分为进气、中间和出气压气机叶片。
2.燃气轮机叶片燃气轮机叶片是用来驱动发动机的部件。
它通常由高温合金制成,能够承受高温和高压。
燃气轮机叶片的形状通常是扇形的,以便能够有效地利用燃气轮机产生的动力。
3.喷气推进器叶片喷气推进器叶片是用来驱动航空器的部件。
它通常由轻质金属制成,可以在高空中承受极端的温度和压力。
喷气推进器叶片的形状通常是锥形或扇形的,以便能够更好地将推力传递给空气。
4.内置安装叶片内置安装叶片是一种特殊类型的叶片,它被安装在发动机内部,用于调节空气流量和燃料混合。
内置安装叶片的形状取决于其功能和位置。
5.噪音减缓叶片噪音减缓叶片是一种专门设计的叶片,用于减少航空发动机产生的噪音。
噪音减缓叶片的形状和结构通常比普通叶片要复杂,以最大程度地减少噪音污染。
6.涡轮增压器叶片涡轮增压器叶片被用于控制航空发动机的气流和压力。
涡轮增压器叶片的形状和数量取决于具体的应用场景。
总的来说,航空发动机叶片按照其功能和形状不同,可以分成多种类型。
随着航空技术的不断发展和创新,航空发动机叶片的形状和材料也在不断改进和升级,以满足不同的航空需求。
航空发动机中叶片的一般工艺流程
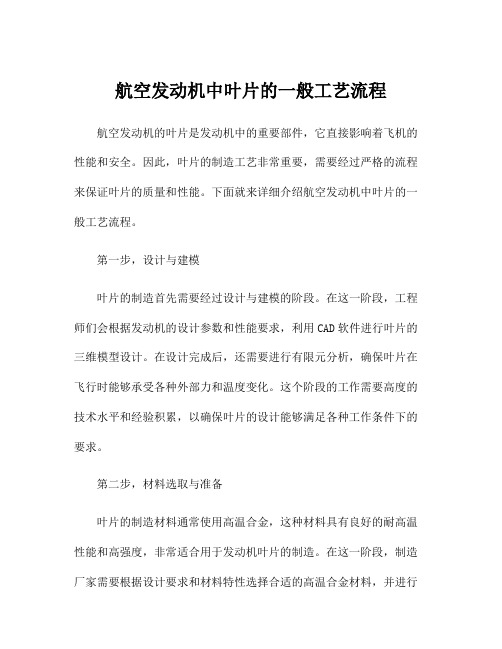
航空发动机中叶片的一般工艺流程航空发动机的叶片是发动机中的重要部件,它直接影响着飞机的性能和安全。
因此,叶片的制造工艺非常重要,需要经过严格的流程来保证叶片的质量和性能。
下面就来详细介绍航空发动机中叶片的一般工艺流程。
第一步,设计与建模叶片的制造首先需要经过设计与建模的阶段。
在这一阶段,工程师们会根据发动机的设计参数和性能要求,利用CAD软件进行叶片的三维模型设计。
在设计完成后,还需要进行有限元分析,确保叶片在飞行时能够承受各种外部力和温度变化。
这个阶段的工作需要高度的技术水平和经验积累,以确保叶片的设计能够满足各种工作条件下的要求。
第二步,材料选取与准备叶片的制造材料通常使用高温合金,这种材料具有良好的耐高温性能和高强度,非常适合用于发动机叶片的制造。
在这一阶段,制造厂家需要根据设计要求和材料特性选择合适的高温合金材料,并进行原材料的采购和准备工作。
由于高温合金材料的成本较高,制造厂家需要确保原材料的质量和规格符合要求。
第三步,精密铸造叶片的制造通常采用精密铸造的工艺。
在这一阶段,制造厂家将选取好的高温合金材料进行加热熔融,然后通过精密铸造工艺将熔融金属注入到预先制作好的叶片模具中。
精密铸造能够保证叶片的内部结构和外部形状的精度,确保叶片在空气动力学性能和稳定性上具有较好的表现。
第四步,热处理与表面处理在精密铸造完成后,叶片还需要经过热处理和表面处理的工艺。
热处理能够调整叶片的微观组织和提高其强度和硬度,以确保在高温和高速飞行状态下仍能保持稳定的性能。
同时,叶片的表面还需要进行特殊的涂层处理,以提高其抗氧化和抗腐蚀能力,延长叶片的使用寿命。
第五步,精密加工与组装在经过热处理和表面处理后,叶片还需要进行精密加工工艺。
这一阶段主要包括CNC加工、抛光和平衡等工序,以确保叶片的精度和平衡性。
同时,叶片还需要与其他部件进行组装,形成完整的叶片装配组件。
第六步,质量检测与试验叶片的制造流程完成后,还需要经过严格的质量检测与试验。
7航空发动机叶片

发动机叶片一、 发动机与飞机 1. 发动机种类 1) 涡轮喷气发动机(WP )WP5、WP6、WP7、……WP13 2) 涡轮螺桨发动机(WJ )WJ5、WJ6、WJ7 3) 涡轮风扇发动机(WS )WS9、WS10、WS11 4) 涡轮轴发动机(WZ )WZ5、WZ6、WZ8、WZ9 5)活塞发动机(HS )HS5、HS6、HS92. 发动机的结构与组成燃气涡轮发动机主要由压气机、燃烧室和涡轮三大部件以及燃油系统、滑油系统、空气系统、电器系统、进排气边系统及轴承传力系统等组成。
(发动机的整体构造如下图1)三大部件中除燃烧外的压气机与涡轮都是由转子和静子构成,静子由内、外机匣和导向(整流)叶片构成;转子由叶片盘、轴及轴承构成,其中叶片数量最多(见表1~5)3. 发动机工作原理及热处理过程工作原理:发动机将大量的燃料燃烧产生的热能,势能给涡轮导向器斜切口膨胀产生大量的动能,其一部分转换成机械功驱动压气机和附件,剩余能由尾喷管膨胀加速产生推力。
热力过程:用p-υ或T-S 图来表示发动机的热力过程:4. 飞机与发动机发动机是飞机的动力,也是飞机的心脏,不同用途的飞机配备不同种类的发动机。
如: 1)军民用运输机、轰炸机、客机、装用WJ 、WS 、WP 类发动机。
2)强击机、歼击机、教练机、侦察机、装用WP 、WS 、HS类发动机。
3)军民用直升机装用WZ 类发动机。
二、 叶片在燃气涡轮发动机中叶片无论是压气机叶片还是涡轮叶片,它们的数量最多,而发动机就是依靠这众多的叶片完成对气体的压缩和膨胀以及以最高的效率产生强大的动力来推动飞机前进的工作。
叶片是一种特殊的零件,它的数量多,形状复杂,要求高,加工难度大,而且是故障多发的零件,一直以来各发动机厂的生产的关键,因此对其投入的人力、物力、财力都是比较大的,而且国内外发动机厂家正以最大的努力来提高叶片的性能,生产能力及质量满足需要。
1.叶片为什么一定要扭在流道中,由于在不同的半径上,圆周速度是不同的,因此在不同的半径基元级中,气流的攻角相差极大,在叶尖、由于圆周速度最大,造成很大的正攻角,结果使叶型叶背产生严重的气流分离;在叶根,由于圆周速度最小,造成很大的负攻角,结果使叶型的叶盆产生严重的气流分离。
- 1、下载文档前请自行甄别文档内容的完整性,平台不提供额外的编辑、内容补充、找答案等附加服务。
- 2、"仅部分预览"的文档,不可在线预览部分如存在完整性等问题,可反馈申请退款(可完整预览的文档不适用该条件!)。
- 3、如文档侵犯您的权益,请联系客服反馈,我们会尽快为您处理(人工客服工作时间:9:00-18:30)。
发动机叶片一、 发动机与飞机 1. 发动机种类 1) 涡轮喷气发动机(WP )WP5、WP6、WP7、……WP13 2) 涡轮螺桨发动机(WJ )WJ5、WJ6、WJ7 3) 涡轮风扇发动机(WS )WS9、WS10、WS11 4) 涡轮轴发动机(WZ )WZ5、WZ6、WZ8、WZ9 5)活塞发动机(HS )HS5、HS6、HS92. 发动机的结构与组成燃气涡轮发动机主要由压气机、燃烧室和涡轮三大部件以及燃油系统、滑油系统、空气系统、电器系统、进排气边系统及轴承传力系统等组成。
(发动机的整体构造如下图1)三大部件中除燃烧外的压气机与涡轮都是由转子和静子构成,静子由内、外机匣和导向(整流)叶片构成;转子由叶片盘、轴及轴承构成,其中叶片数量最多(见表1~5)3. 发动机工作原理及热处理过程工作原理:发动机将大量的燃料燃烧产生的热能,势能给涡轮导向器斜切口膨胀产生大量的动能,其一部分转换成机械功驱动压气机和附件,剩余能由尾喷管膨胀加速产生推力。
热力过程:用p-υ或T-S 图来表示发动机的热力过程:4. 飞机与发动机发动机是飞机的动力,也是飞机的心脏,不同用途的飞机配备不同种类的发动机。
如: 1)军民用运输机、轰炸机、客机、装用WJ 、WS 、WP 类发动机。
2)强击机、歼击机、教练机、侦察机、装用WP 、WS 、HS类发动机。
3)军民用直升机装用WZ 类发动机。
二、 叶片在燃气涡轮发动机中叶片无论是压气机叶片还是涡轮叶片,它们的数量最多,而发动机就是依靠这众多的叶片完成对气体的压缩和膨胀以及以最高的效率产生强大的动力来推动飞机前进的工作。
叶片是一种特殊的零件,它的数量多,形状复杂,要求高,加工难度大,而且是故障多发的零件,一直以来各发动机厂的生产的关键,因此对其投入的人力、物力、财力都是比较大的,而且国内外发动机厂家正以最大的努力来提高叶片的性能,生产能力及质量满足需要。
1.叶片为什么一定要扭在流道中,由于在不同的半径上,圆周速度是不同的,因此在不同的半径基元级中,气流的攻角相差极大,在叶尖、由于圆周速度最大,造成很大的正攻角,结果使叶型叶背产生严重的气流分离;在叶根,由于圆周速度最小,造成很大的负攻角,结果使叶型的叶盆产生严重的气流分离。
因此,对于直叶片来说。
除了最近中径处的一部分还能工作之外,其余部分都会产生严重的气流分离,也就是说,用直叶片工作的压气机或涡轮,其效率极其低劣的,甚至会达到根本无法运转的地步。
发动机叶片数量统计如下(以WJ6、WS11为例)表:1.WJ6压气机叶片数量见表1 表1涡轮叶片数量见表2 表2发动机叶片总数1078+424=15021502×500=751000按平均价格500元/片,总产值3.755亿2.WS11压气机叶片总数见表3表3风扇叶片数量见表4表4涡轮叶片数量见表5表5叶片总数1297+192+507=1996按300台计2000×300=600000片按500元/片计价共计产值3亿元。
2. 叶片的工作原理1) 压气机叶片顾名思义,压气机是用来“压气”地,把进口大气压P H=1的压力压到出口处的所需要的压力.我们下图来分析其压缩的原理:气体在图2中的流道内由于其容积越来越小而将气体的压力“憋”得越来越高。
在图2中由于叶栅通道内的相对运动中截面积扩大,引起速度下降,ω1>ω2,气流的动能减少,减少的动能大部分转化为气流的压力能,从而使气流的压力提高P1>P2。
工作轮的任务不仅要提高压力,而且要不断给气流假如轮缘功L u使气流不断的被压缩。
压气机叶片中有工作叶片和整流叶片之分,工作叶片是随着转子旋转的,而整流叶片是静止不动,给工作叶片进口或出口紊乱的气流进行整理使气流有序的流动减少流动损失。
气流在整流叶片中同样是增压过程。
压气机的级数往往有很多级,这是因为它的级增压比不高,一般在1.2左右,要将气流压力提高到很高,则需很多级来完成。
总压比与级压比的关系是πn*=πnIπKIIπKIII……πKn压气机级数一般都是8级以上。
2)涡轮叶片通过涡轮的流程通道和基元级叶片叶栅通道的结构型式来分析涡轮叶片的工作原理从图3和图2可看出其气流进出口的状态正好相反。
气流流过图3的流道时由于面积越来越大而压力越来越低。
这是由于气流流过叶栅通道F 1CA 和F 2PK 膨胀过程中的压力下降很快所需要的容积。
其原理为:由于涡轮叶片进口面积F Z 大于出口面积,同样工作叶片也是如此。
从燃烧室中流出的燃气速度不高,约100m/s ,进入涡轮叶片后由于叶栅通道是收敛的,燃气在出口处(F 1CA )膨胀,使气流的温度、压力大弧度下降,使出口速度C 1(ω2)大弧度上升可过600m/s ,接近音速,从而走到和完成热能、压力能转换为动能,又由动能转换为机械能。
涡轮总落压比与落压比的关系如下式:π*T =πT ⅠπT Ⅱ……πTn涡轮级数比压气机少,有单级、双级,大发到6级 3.叶片的几何尺寸图6压气机叶片叶栅集合参数示意图(1).压气机叶片i—进气攻角(β1K—β1)v—安装角β1K—进气构造角t—栅距β1—进气气流角C max—最大厚度β2K—排气构造角R q—前缘圆半径β2—排气气流角R n—后缘圆半径δ—落后角θ—叶片弯角S—轴向宽度b/t—叶片稠度b—弦长在设计中需重点控制的参数如下:(a).C max应控制在叶尖为C max/b=0.04~0.06;而叶根则为:C max/b=0.1~0.12。
(b).i应控制前几级0~-2°,后几级为1~2°。
(c).R q、R n可按下曲线计算得出:方法:根据C max及b查出R q/b、R n/b然后计算出R q、R n。
(2)涡轮叶片涡轮叶栅平面参数分压气机叶片相同。
注:压气机工作叶片、整流叶片、涡轮工作叶片、导向叶片的叶片平面叶栅构造参数相同。
4.叶片的连接方式无论是压气机叶片还是涡轮叶片,是工作叶片还是导向叶片都必须安装在发动机上使其能工作而且还要牢固,所有发动机的叶片安装方法大致有以下几种:4)压气机工作叶片压气机工作叶片的下部带有燕尾榫头安装在带有燕尾榫槽的轮盘上,如图示:另一种用圆柱销联接如图示5)压气机的整流叶片整流叶片是静止不动的,因此它将叶片焊在内、外环中如图:6) 涡轮工作叶片涡轮工作叶片都带有榫头装在带有榫槽的涡轮盘上,如图示:7) 涡轮导向叶片涡轮导向叶片大多用挂钩涡轮导向叶片大多用挂钩的形式与机匣联接如图12所示:5.叶片的工作条件压气机叶片含风扇叶片属于冷端部件的零件,除最后几级由于高压下与气体的摩擦产生熵增而使温度升高到约600K(327°C),其余温度不高,进口处在高空还需防结冰。
工作前面几级由于叶片长以离心负荷为主,后面几级由于温度以热负荷为主。
总之压气机叶片使用寿命较长。
叶片的使用的材料一般为铝合金、钛合金、铁基不锈钢等材料。
涡轮是在燃烧室后面的一个高温部件,燃烧室排出的高温高压燃气流经流道流过涡轮,所有叶片恰好都是暴露在流道中必须承受约1000°C的高温1Mpa的以上高压燃气的冲刷下能正常工作。
因此叶片应有足够的耐高温和高压的强度。
涡轮叶片的使用寿命远低于压气机叶片约2500h。
叶片的最大应力点如图13示,其应力分布为C>A>B;C、A的应力为拉伸应力,B为压应力,压气机叶片与其相同。
这是转子叶片,静子叶片只承受热应力及弯曲应力,没有离心应力。
叶片使用的材料一般为高温铸造合金如K403、K424等、和高温合金如GH4133等,温下高强度材料。
三、叶片加工与控制1.加工叶片的加工分两大部分:一部分为叶片型面加工,一部分为榫头加工及缘板加工:压气机工作叶片的型面是用高能高速热挤压成型后经抛光而成;整流叶片是由冷轧成型经抛光而成。
涡轮叶片的叶型,无论是工作叶片还是导向叶片均为铸件者都是型面没有余量精密铸造件都是大余量经数铣、抛光而成。
压气机叶片和涡轮叶片的榫头及上、下缘板尺寸为机械加工而成。
前面讲过在燃气涡轮发动机的所有零件中唯有叶片的故障率是最高的,造成机毁人亡的事故也时有发生。
这是因为叶片的数量多,工序多、周期长、要求高,加工难度大,加工过程中的形状、位置、烧伤、缺陷、碰伤、材质转工等过程控制中,难免会出现失控的时候,给叶片(尤其是工作叶片)造成伤害,使其带病工作所致。
因此,对叶片生产的全过程控制十分重要。
2.叶片的质量控制我们说控制叶片的质量,主要是三个方面:a.确保叶片设计强度不降低b.确保发动机性能不降低c.确保装配性能好下面分别对造成上面三个方面的因素进行分析:1).造成叶片强度下降的因素有如下几点:a..叶片用材不当b.叶片疏松超标3级以上c.叶片剖面晶粒粗大3级以上d.有垂直于进排气边的柱状晶e.根部叶型变薄f.榫齿经处以下到根部有细颈g.进排气边也有碰缺,严重的垂直进排气边的严重划伤,造成应力集中h.根部截面叶型厚度,设计过薄不成比例i.叶片受到严重腐蚀而未能加工掉j.加工中烧伤k.叶片重量偏大l.叶片渗层成形及厚度不合理2).由于叶片加工不当使发动机性能下降的因素有如下几点:a.叶型表面粗糙度过低b.叶片安装角偏离设计值过大c.叶片进排气边圆半径偏大不圆滑d.进气攻角偏离设计值过大e.叶片高度偏小f.叶片重量偏大3.)影响装配的主要因素:a. 使用夹具不当加大了加工误差b. 尺寸测量方法不正确造成测量误差c. 加工部位的形状没有保证如直线度、平面度等d. 加工应力过大造成加工后变形e. 尺寸加工不到位,符合性差4). 强度、性能、装配含义的定义强度是指叶片在工作中由于上述因素(11个方面的因素)降低了叶片的疲劳强度造成叶片裂纹、变形、折断而导致故障,这就是我们常说叶片的疲劳强度不足。
性能是指发动机工作中出现燃油消耗高,排气温度高,输出功率低和喘振等故障,这就是我们所说发动机性能差,这就是说以我们生产的叶片工作不匹配,原因只有两个不足:设计水平低,就是加工符合性差,也就是我们前面所说叶片平面叶栅几何参数不合适,主要原因就是上面6个方面因素所致。
装配是指工作叶片安装到轮盘上的联接发生了困难,榫头安装不进榫槽或间隙过大,叶片摆动量过大,或过小,轴向、径向凹凸不平;导向叶片的挂钩插不进机匣的环形钩槽,或者过紧,或过松。
周向、轴向、径向、凹凸不平差别很大。
这就是我们所说装配性能差。
造成原因就是上面所述5个方面的因素所致。
3.加工1).叶片型面加工目前国内各发动机厂的叶片型面加工方法大体相同:压气机工作叶片:高能高速锤热挤压成形,手工抛光而成。
见图压气机整流叶片:板材冷轧,手工抛光而成。
见图涡轮导向叶片:大多数为型面无余量精铸而不需抛光,有小部分型面有小余量,需经抛光而成。
见图涡轮工作叶片:工作叶片温度在600°C以上,大多数为型面无余量精铸而成而不需抛光。