压铸机工艺参数现场检验记录表
压铸机工艺参数分析

∙压铸工艺参数分析(一)∙∙为了便于分析压铸工艺参数,下面示出如图5-1和图5-2所示的卧式冷室压铸机压射过程图以及压射曲线图。
压射过程按三个阶段进行分析。
第一阶段(图5-1b):由0 -Ⅰ和Ⅰ-Ⅱ两段组成。
0 -Ⅰ段是压射冲头以低速运动,封住浇料口,推动金属液在压射室内平稳上升,使压射室内空气慢慢排出,并防止金属液从浇口溅出;Ⅰ-Ⅱ段是压射冲头以较快的速度运动,使金属液充满压射室前端并堆聚在内浇口前沿。
第二阶段(图5-1c):Ⅱ-Ⅲ段,压射冲头快速运动阶段,使金属液充满整个型腔与浇注系统。
第三阶段(图5-1d):Ⅲ-Ⅳ段,压射冲头终压阶段,压射冲头运动基本停止,速度逐渐降为0。
a)图5-1 卧式冷室压铸机压射过程图图5-2 卧式冷室压铸机压射曲线图s--冲头位移曲线P0--压力曲线v--速度曲线1、压力参数(1)压射力压射冲头在0-Ⅰ段,压射力是为了克服压射室与压射冲头和液压缸与活塞之间的摩擦阻力;Ⅰ-Ⅱ段,压射力上升,产生第一个压力峰,足以能达到突破内浇口阻力为止;Ⅱ-Ⅲ段,压射力继续上升,产生第二个压力峰;Ⅲ-Ⅳ段,压射力作用于正在凝固的金属液上,使之压实,此阶段有增压机构才能实现,此阶段压射力也叫增压压射力。
(2)比压比压可分为压射比压和增压比压。
在压射运动过程中0-Ⅲ段,压射室内金属液单位面积上所受的压射力称为压射比压;在Ⅲ-Ⅳ段,压射室内金属液单位面积上所受的增压压射力称为增压比压。
比压是确保铸件质量的重要参数之一,推荐选用的增压比压如表5-1所示。
表5-1 增压比压选用值(单位:MPa)(3)胀型力压铸过程中,充填型腔的金属液将压射活塞的比压传递至型(模)具型腔壁面上的力称为胀型力。
主胀型力的大小等于铸件在分型面上的投影面积(多腔模则为各腔投影面积之和),浇注系统、溢流、排气系统的面积(一般取总面积的30%)乘以比压,其计算公式如下F主=APb/10式中F主-主胀型力(KN);A-铸件在分型面上的投影面积(cm2);Pb-压射比压(MPa)。
IPQC生产现场稽核表

44 检查作业员有没有对老化箱温度进行点检。
注:针对不良项,IPQC需要在IPQC巡检记录表上记录,并交由相关责任人分析原因并答复改善措施。本检查表内容由IPQC每日进行首件检验 和每2小时抽检以外的时间进行工艺纪律检查。
QR-01-63(REV:A0)
攻 39 要加工的产品对应所选的丝攻(钻头)是否正确。
牙
40
丝攻(钻头)是否制定有使用寿命管控,是否仍在使用超过使用寿命的钻头。检查有无钻头使用时间记录,是否有超过规定寿 命的钻头仍在被使用
41 检查老化箱温度是否达到规定要求。
老 42 检查老化记录表是否按要求填写,有无漏填错填。 化 43 检查有无老化过和未老化产品以及不同型号之间的混料现象。
25 机器有没有调整确认后生产。
26 砂纸的使用寿命是否有明确的要求。是否仍在使用过期的砂纸。
IPQC生产现场稽核表
工序 序号
检查重点
27 操作员是否经过培训、了解冲光口的作业方法。是否有上岗证?
冲光 口
28 检查作业员作业前是否有对设备进行做点检。 29 检查作业员作业前是否对对冲床检查是否平整、有没有松动等异常。 30 冲头是否有进行保养,冲头有没有磨损现象。
6 产线有无新的工艺和夹具及机台的导入,如有,验证,培训和控制,效果的确认
7 产线转线的点检及监控,清拉!返工料的控制
8 各岗位,各工序有无连续3个不合品的情形发生,如有,停岗位,停工序
9 各岗位,各工序有无新的不良现象出现,如有,立即报告QE
10 检查生产线有无员工在座位上打电话玩手机饮食等。
11 检查员工是否带手指套作业。
18 检查员工做完产品之后是否按照作业指导书要求用手捧产品进行装盒。
19 作业员使用的工具是否按照作业指导书要求使用。
一体化压铸机工艺参数表
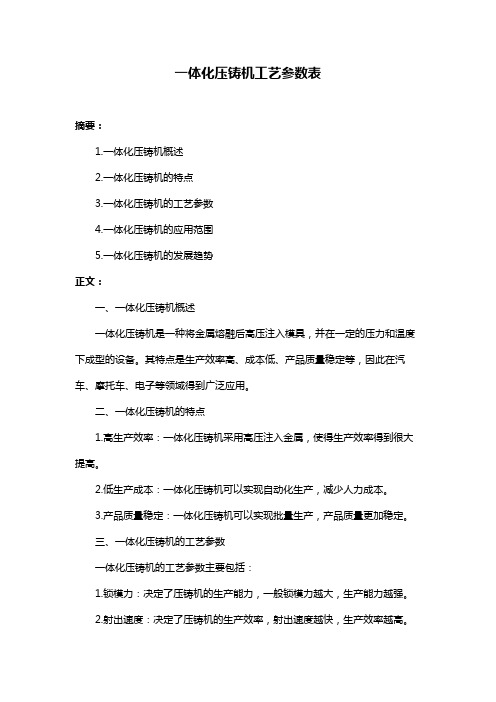
一体化压铸机工艺参数表
摘要:
1.一体化压铸机概述
2.一体化压铸机的特点
3.一体化压铸机的工艺参数
4.一体化压铸机的应用范围
5.一体化压铸机的发展趋势
正文:
一、一体化压铸机概述
一体化压铸机是一种将金属熔融后高压注入模具,并在一定的压力和温度下成型的设备。
其特点是生产效率高、成本低、产品质量稳定等,因此在汽车、摩托车、电子等领域得到广泛应用。
二、一体化压铸机的特点
1.高生产效率:一体化压铸机采用高压注入金属,使得生产效率得到很大提高。
2.低生产成本:一体化压铸机可以实现自动化生产,减少人力成本。
3.产品质量稳定:一体化压铸机可以实现批量生产,产品质量更加稳定。
三、一体化压铸机的工艺参数
一体化压铸机的工艺参数主要包括:
1.锁模力:决定了压铸机的生产能力,一般锁模力越大,生产能力越强。
2.射出速度:决定了压铸机的生产效率,射出速度越快,生产效率越高。
3.模具温度:影响了压铸件的质量,模具温度过高或过低都会影响压铸件的质量。
4.金属液温度:决定了压铸件的结晶组织,金属液温度过高或过低都会影响压铸件的质量。
四、一体化压铸机的应用范围
一体化压铸机广泛应用于汽车、摩托车、电子等领域,主要用于生产发动机壳体、变速器壳体、汽车车身等部件。
五、一体化压铸机的发展趋势
随着汽车、摩托车、电子等领域的发展,一体化压铸机的需求越来越大,未来一体化压铸机的发展趋势主要有以下几点:
1.生产效率更高:随着技术的发展,一体化压铸机的生产效率将得到进一步提高。
2.应用范围更广:随着一体化压铸技术的发展,一体化压铸机将在更多的领域得到应用。
压铸工序质量审核表

压铸工序质量审核表表号:QR-8.2.3-01NO:序号审核项目涉及部门审核内容对照标准质量特性分级审核结果不符合项记录工艺因素管理因素一质量控制计划1质量控制点流程图生产部查(2-3个)管理文件,看是否有管理点流程图,质量控制点选择是否合适质量点控制程序2控制文件生产部文件是否齐全;压铸件工艺卡,工序质量表,作业指导书质量点控制程序生产部压铸机“日检维修卡”,“设备定检卡”品控室检查作业指导书二工序因素(一)人1熔化工压铸车间办公室持证上岗,查有无操作合格证人员培训控制程序压铸车间到生产部查(3个月)“工艺纪律检查表”看该岗贯彻率工艺纪律检查控制程序生产部询问熔化工:工艺规程是否便于操作工艺技术文件控制程序压铸车间询问熔化工:工艺规程是否便于操作工艺技术文件控制程序询问熔化工:该合金的最高熔化温度,出炉温度合金熔化工艺流程询问熔化工:炉控柜仪表(电压表、电流表、功率因素表、温度表)的作用及控制范围,查当月合金成份记录图表的记录情况,查(半个月)“熔化工艺日记录”是否认真填写设备操作规程;压铸合金及炉料管理2压铸工办公室压铸车间持证上岗,查有无操作合格证人员培训控制程序压铸车间查控制点压铸工,是否由专人生产到生产部查(3个月)“工艺纪律检查表”看该岗位贯彻率工艺纪律检查控制程序;质量控制点控制程序查“控制点”文件是否齐全(压铸工艺卡,作业指导书)质量控制点控制程序生产部询问压铸工:按工艺卡及作业指导书操作有无困难,工艺参数的选择是否正确、完善工艺技术文件控制程序压铸车间询问压铸工:所生产的铸件应控制的主要工艺参数值,压射压力、慢压射行程、余料饼厚、留模时间、浇注温度压铸工艺卡;作业指导书压铸车间抽查(1份)质量控制点的“压铸工艺参数记录表”,看记录状况是否在控制范围作业指导书压铸车间抽查(2个)质量控制点压铸工,讲述“压铸机日检维修卡”几项内容设备日检点控制程序压铸车间抽查(2名)压铸工询问“压铸模巡检记录卡”的部份内容压铸模控制程序(三)设备1压铸模压铸模库(模具车间)看(3份)“压铸模调试传票”,查是否有相应的“产品鉴定表”压铸模控制程序查(2份)模具使用工作传票的填写情况看(2份)“质量问题通知单”,并查“模具传票”上相应的处理意见模具车间查(2套)库存现生产模具,看是否带“尾件”及“尾件检查表”模具车间维修工询问(2个)维修工“压铸模巡检记录卡”上的部份内容压铸模控制程序看库存模具状况:是否有合金、涂料等杂物及锈钝现象看现场模具使用状况、各活动部分是否活动自如压铸车间压铸工查模具使用维护状况;分型面、溢流槽、排气槽、滑块槽有无合金、夹杂物等压铸模控制程序查“导柱、导套”,斜杆、孔及“滑块、滑块槽”接合面的润滑状况2压铸机生产部查(2份)压铸机“日检维修卡”档案,看“日检”是否认真设备使用与维护管理查(2份)压铸机“定检表”,看是否按期定检查(3份)近期“日检维修卡”的停机工时,看设备能力压铸车间压铸工查(3台)压铸机的液压系统是否漏油,看维修状况设备日点检管理机电维修工看(3台)压铸机压射系统的建压时间是否正确,查维修状况设备日点检管理看(3台)压铸机的压射系统的持压状况,查设备维护效果压铸车间压铸工查(3台)压铸机储能器压力是否合适,看设备工作状况设备日点检管理查(3台)压铸机活塞是否发卡,看设备点检状况品控室查(3台)压铸机各压力表是否完好,查这些压力表是否有合格证计量器具使用维护和保养管理(三)材料1原材料(金属炉料)(1)采购单供销部查铝锭、锌锭、电解铜的采购单各1份,看其规格是否与规定相符金属炉料消耗定额汇总表查(2-3种)原材料供方名单,看是否有质量保证能力认可采购物资控制程序(2)材质证明书品控室查(2种)炉料(铝、锌锭)近半年的材质证明书,看是否有检查员签字认可进货检验与试验控制程序品控室及保管员查(2种)批炉号的锌(或铝)锭,看是否有材质证明书或化验报告单原材料质量检验管理供销部查(2-3种)材料代用单(炉料),看审批手续是否齐全原材料质量检验管理(3)原材料储存炉料库看库房原材料是否分类堆放,有无明显标识,是否防潮原材料质量检验管理2回炉料压铸车间回炉料库到库房看回炉料是否分类堆放,有无标识,是否防潮,看回炉料中是否有混料现象及其他杂物压铸合金及炉料管理压铸车间查压铸机旁回炉料箱内是否有混料现象压铸车间带镶件回炉料是否单独存放品控室看合金检查员“保温炉”抽查“化验报告单”所查不合格料是否签署了“处理意见”3合金铸锭压铸车间炉料库询问保管员,合金锭入库的依据,并查看近2天的铝(或铜)合金的“化验报告单”再核定实物合金熔化工艺规程查库房合金锭是否按炉号分类存放压铸车间熔化工段看合金锭箱上是否有明显的合金炉号标识合金熔化工艺规程4镶件品控室看车间内存放镶件是否有检查员确认的合格单配套件质量检查管理品控室看车间内存放镶件是否有锈钝现象5辅助材料(1)精炼剂供销部、车间查熔化炉台上精炼覆盖剂是否过期,受潮变质合金熔化工艺规程(2)型腔涂料(脱模剂)供销部看现场使用的型腔涂料是否有沉淀现象型腔涂料配制工艺规程(四)工艺方法1熔化过程炉料准备压铸车间查(2-3种)炉料的破碎粒粒度是否符合要求(Si,Cu),查破碎或炉料剪切现场是否有混料现象。
压铸工艺参数(一)

(1)快压射速度的作用和影响 a、快压射速度对铸件力学性能的影响 提高压射速度,则动能转化为热能,可提高合金熔液的流动性,这有利于 消除流痕、冷隔等缺陷,也可提高力学性能和表面质量。但速度过快时,合金 熔液呈雾状与气体混合,产生严重涡流包气,使力学性能下降。 图3-12是AM60B,在浇注温度680℃,模具180℃下试验,压射速度对力学 性能的关系。
任务三 压铸工艺参数(二)
任务四 涂料及压铸件清理
1
压力
教学 内容
3
2
胀型力
速度
教学要求:
掌握压力、速度的表示形式; 熟悉压射力、比压及胀型力的计算方法; 了解比压的选择、压射速度和内浇口速度对铸件力学 性能的影响。
压铸工艺是把压铸合金、压铸模和压铸机这三大生产要素有机组合 和运用的过程。
压铸时,影响金属液充填成型的因素很多, 正确选择和调整压铸 工艺参数,是保证压铸件质量、发挥压铸机的最大生产率和正确设计压 铸模的依据。 压铸工艺参数主要有压射压力、压射速度、充填时间和压铸模温度 等。
d FS 4
2
3、比压的选择
表3-5 各种压铸合金的计算压射比压
MPa
二、胀型力
压铸过程中,填充结束并转为增压阶段时,作用在凝固的金属上的比压(增压 比压)通过金属(铸件浇注系统、排溢系统)传递于型腔壁面,此压力称为胀型力(又 称为反压力)。 胀型力可用下式表示:
F z P bzA
式中: Fz——胀型力,N; Pbz——增压比压,Pa; A——承受胀型力的投影面积,m2。 当胀型力作用在分型面上时,便为分型面胀型力,而作用在型腔各个侧壁方 向时,则称为侧壁胀型力。 分型面胀型力公式:
压射力计算: P
y
P g
标准铝压铸工艺参数表

标准铝压铸工艺参数表1. 压铸温度。
铝合金的压铸温度是影响产品质量的重要参数之一。
通常情况下,铝合金的压铸温度在650°C至750°C之间。
过高的温度会导致产品熔融不均匀,而过低的温度则会造成产品表面粗糙。
因此,在实际生产中,需要根据具体的铝合金材料选择合适的压铸温度。
2. 压射速度。
压射速度是指铝合金液态金属进入模腔的速度。
适当的压射速度可以确保产品充填充分,避免气孔和夹杂物的产生。
一般来说,压射速度应根据产品的形状和尺寸进行调整,以保证产品的成型质量。
3. 模具温度。
模具温度对铝合金压铸产品的表面质量和尺寸精度有着重要影响。
过高或过低的模具温度都会导致产品的缺陷,因此需要根据具体的铝合金材料和产品要求来确定合适的模具温度。
4. 注射压力。
注射压力是指压铸机对铝合金液态金属施加的压力。
适当的注射压力可以确保产品充填充分,避免产品内部产生气孔和夹杂物。
在实际生产中,需要根据产品的形状和尺寸来确定合适的注射压力。
5. 冷却时间。
冷却时间是指产品在模具中冷却的时间。
适当的冷却时间可以确保产品的尺寸精度和表面质量。
通常情况下,冷却时间需要根据产品的厚度和材料来确定,以确保产品达到理想的硬度和强度。
6. 顶杆力。
顶杆力是指顶出铝合金产品的力量。
适当的顶杆力可以确保产品顺利脱模,避免产品变形和损坏。
在实际生产中,需要根据产品的形状和尺寸来确定合适的顶杆力。
7. 模具开合力。
模具开合力是指模具在开合过程中所受的力量。
适当的模具开合力可以确保模具的正常运行,避免模具损坏和产品缺陷。
在实际生产中,需要根据模具的结构和尺寸来确定合适的模具开合力。
总结:以上是标准铝压铸工艺参数表的相关内容,希望能对大家在铝合金压铸加工过程中有所帮助。
在实际生产中,需要根据具体的产品要求和铝合金材料来确定合适的工艺参数,以确保产品质量和生产效率。
同时,也需要不断优化和调整工艺参数,以适应市场和客户需求的变化。
希望大家能够加强学习和实践,不断提升铝合金压铸加工的技术水平和质量管理水平。
压铸工艺检验记录表

压铸机编号 零件编号 零件名称 模具编号 点检人 点检项目 一快位置 一快流量 二快位置 二快流量/圈数 增压位置 增压流量/圈数 增压触发压力 压射时间 冷却时间 增压延时 回锤延时 压射压力表 料柄厚度 喷涂液浓度 铝液温度 喷涂工艺点检 模具冷却水是否畅通 说明:点检人按压铸工艺内容进行工艺点检记录,符合工艺卡的为√,不符合填写数值并在交接班里注明不符合原因,没有特殊情况必须严格按照规定工艺执行,没有工艺参数的为/。 备注:如有工艺不能指导生产,或生产不稳定,请及时反馈。
压铸机型号
设备是否完好
文件编号
年/月
版本号
1
2
3
4
5
6
7
89Biblioteka 101112
13
14
15
16
17
18
19
20
21
22
23
24
25
26
27
28
29
30
31
压铸工艺记录单范文

压铸工艺记录单范文日期:_________工序:_________产品型号:_________一、准备工作:1.检查模具,确保模具无损坏、磨损等问题,并进行必要的维护和保养。
2.准备压铸机及相关设备,检查机器故障及工作状态,确保正常运转。
3.准备合适的合金材料,检查材料质量,并确保充足供应。
4.清洁工作区域,确保无尘、无异物及其他杂质。
二、铸件参数设置:1.铸件尺寸:记录所需铸件的长度、宽度、高度及其它尺寸参数。
2.产品材料:填写产品所采用的材料类型及其化学成分。
3.铸件形式:选择合适的铸造形式,如冷锭铸造、热锭铸造等。
4.注入温度:确定铸造合金的注入温度,以保证合金在模具中充分流动。
5.注入速度:确定注入合金的速度,以避免产生冷焦、砂眼等缺陷。
6.注入压力:确定注入合金的压力,以保证合金填充模具中的每个部位。
三、铸件工艺操作:1.清洁模具:使用合适的清洁剂清洁模具表面,确保模腔无异物。
2.涂抹模具:使用维护剂或润滑剂涂抹模具,以减少铸件与模具的摩擦。
3.加热模具:将模具加热至合适温度,以提高铸件表面质量。
4.取出铸件:当合金冷却固化后,将铸件从模具中取出,并进行必要的修整和去毛刺处理。
5.检测铸件:对铸件进行外观检测、尺寸检测及力学性能等相关测试。
6.包装和储存:将铸件进行包装,并储存在适当的环境中,以保证其质量和保存时间。
四、问题记录和处理:1.记录铸件过程中出现的问题和异常情况,如气孔、缩松、砂眼等缺陷。
2.分析问题产生的原因,并进行相应的对策和改进措施。
3.记录改进措施的效果并进行总结,以便今后参考和应用。
五、安全操作及环保:1.操作人员必须佩戴符合安全要求的个人防护装备,包括安全帽、眼镜、手套等。
2.严格按照操作规程进行操作,确保人员和设备的安全。
3.对废弃材料、废水等进行合理处理,减少对环境的污染。
4.定期进行设备维护和检修,确保设备的正常运行和工艺参数的准确。
以上为压铸工艺记录单的大致内容,可以根据实际情况进行具体调整和补充。
压铸工艺参数分析(一)
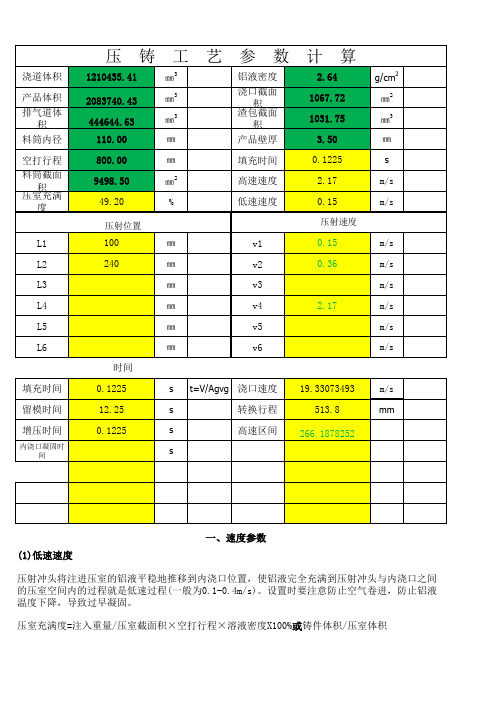
积 料筒内径 空打行程 料筒截面
积 压室充满
度
L1 L2 L3 L4 L5 L6
填充时间 留模时间 增压时间
内浇口凝固时 间
压铸工艺参数计算
1210435.41
㎜3
2083740.43
㎜3
444644.63
㎜3
110.00
㎜
铝液密度
浇口截面 积
渣包截面 积
产品壁厚
2.64 1067.72 1031.75
135
126
126
126
520-2200 750-2600 840-2900 1033-3286 1322-4004 1400-4100 顶出部分
150
180
180
200
200
200
250
360
360
500
500
500
其他
14
14
14
14
14
16
37
37
37
37+37 37+37 37+37
38000
留模时间=产品壁厚X产品壁厚 (3)增压时间
压铸件进一步得到致密的最终压力所使用的时间,增压压力的时间要比内浇口凝固的时间短,否 则内浇口凝固,压力无法传递到铸件上。
增压时间=0.01X产品壁厚X产品壁厚
(4)内浇口凝固时间 内浇口凝固的时间关系到压力是否能够传递到铸件上,铸件的内部质量是否能达到合格状态。 内浇口凝固时间=2X0.01X产品壁厚X产品壁厚
压室充满度=注入重量/压室截面积×空打行程×溶液密度X100%或铸件体积/压室体积
(压室充满度的标准一般为20-50%)或压室的充满度在60%-80%之间较为适宜 低速速度=0.7X√压室直径/压室充满度
压铸工艺参数表

压铸工艺参数表
摘要:
1.压铸工艺参数表的定义与作用
2.压铸工艺参数表的主要内容
3.压铸工艺参数表的实际应用
正文:
压铸工艺参数表是压铸生产过程中必不可少的一种文档,主要用于记录和指导压铸工艺的各项参数,以确保生产出的铸件质量达到要求。
压铸工艺参数表不仅为生产工人提供了操作依据,也为质量检测人员提供了检验标准,同时还是生产过程优化和改进的重要参考依据。
压铸工艺参数表的主要内容包括以下几个方面:
1.压铸机型号和规格:记录使用的压铸机型号和规格,以便针对不同型号和规格的压铸机采取相应的工艺措施。
2.合金材料:记录使用的合金材料种类和牌号,以便根据合金材料的特性调整工艺参数。
3.压铸压力:记录压铸过程的压力参数,包括高压力、低压力等,以保证铸件的填充和密实。
4.速度:记录压铸过程的速度参数,包括高速、中速、低速等,以保证铸件的质量和生产效率。
5.温度:记录压铸过程中的温度参数,包括熔融温度、压射温度、模具温度等,以保证铸件的凝固和成型质量。
6.充型时间:记录压铸过程中的充型时间,以保证铸件的充型饱满。
7.喷涂时间:记录喷涂时间,以保证涂层的质量和均匀性。
8.铸件的缺陷和质量检测:记录铸件的缺陷和质量检测结果,以便分析和改进工艺。
在实际生产过程中,压铸工艺参数表需要根据实际情况进行调整。
例如,当生产不同结构的铸件时,需要调整压铸压力、速度和充型时间等参数;当使用不同牌号的合金材料时,需要调整熔融温度和模具温度等参数。
通过不断优化和调整压铸工艺参数,可以有效提高铸件的质量和生产效率。
总之,压铸工艺参数表在压铸生产过程中起着举足轻重的作用。
压铸工艺卡

名 称距 离速 度阀开度处数XX机械有限公司编制/日期会签/日期审核/日期批准/日期客户代码操作车间设备编号产能(件/班)页 码产品名称产品图号工序编号材料牌号表单编号/版本工艺路线熔炼→压铸→锯料头→打砂→去毛刺→抛丸→喷塑→机加一序→机加二序→机加三序→机加四序→超声波清洗→检验、包装→入库→发运铸造图示压铸机压铸机型号力劲900T 材料牌号LM6压室直径∅100压射位置下档模具模具编号法兰尺寸Φ200X20液压抽芯有顶杆先复位有涂料冲头油牌号/脱模剂牌号花野935冲头油类型颗粒脱模剂配比1:100镶嵌件/工艺活块名称活块材质H13图号数量1料柄厚度(mm )25±5顶回延时(s )4铝液温度/C°670±20压射时间(s )6模具温度/C°220±20冷却时间(s )取件方式自动熔炼温度/C°800±20喷雾方式自动新、旧料配比7:3顶出延时(s)310压机工作流程图快压流量2圈顶出时间(s )3增压流量7圈吹气时间(s )6热模时间10-15min增压预热模数10pcs产品要点常规要求快压压力(bar )140喷雾时间(s )8增压压力(bar )130冷模预热模数20pcs 1.操作人员上岗前必须穿戴好劳保用品;2.日期章按照周期更换并符合当前年月;3.产品各项尺寸检验符合检验规定;4.熔炼参数在控制范围内;(熔炼工艺点检记录表)5.压铸参数在控制范围内;(压铸工艺点检记录表)6.确保设备状态稳定;(设备点检记录表);7.作业按工艺流程模块化运作;(流程图);8.作业场地整洁,干净,安全;(5S 要求);参数压射0位快压启动点增压启动点料头保压点冲头跟踪位置0mm 340mm 关键点编号12345———压铸工艺参数增压选择420mm 480mm 550mm 0.5m/s2.5m/s 3m/s 3m/s 0.5m/s1.外观:不允许有开裂或严重冷隔、拉模、缺料、变形等缺陷;2.气孔:按照ASTM-E505 5/8 3级执行;锯床剖切或X-ray 探伤;3.重量:毛坯重量3.16Kg±0.02Kg ,整模重量6.148Kg±0.02Kg4.拉模:检查孔内不允许严重拉模,注意喷雾位置;5.印痕:不允许有严重流痕或阶梯痕迹;6.合模:确保每次合模到位,每4小时全面清理1次模具分型面的杂物;7.产品整齐摆放在托盘上,层与层之间用隔板隔开;8.填写生产流程卡,标明生产信息;签名/日期异常处理管理流程更改标记更改内容样件试生产量产工艺参数异常停机报告压铸主管领班按要求执行压铸主管判定参数正确继续生产是否压铸工艺卡用木榔头把料柄(黄色标识)敲掉,内浇口残留要求凸出≥0.3mm ,凹进≤0.3mm,不允许缺料;敲完后注意查看是否严重变形,检查进料部位是否冲浇口严重。
压铸过程工艺参数记录表

1of1
压力设定
锁模压力(Mpa) 调模压力(Mpa)
顶针压力(Mpa)
低压压力(Mpa)
熔炉设定
合金保温温度℃ 新料:回炉料
脱模剂
Model 型号 Ratio 配比(%)
调机人员 :
压铸车间主任:
首次
记录编码: YZ-2015
生产数量 模具编号 调机时间及参数
备注
` 生产部长签字:
远博生产部
表格编号/版本:XXX/AO
压铸过程工艺参
压铸材料
零件名称 出模数
压铸参数
标准参数值
压铸机
Models机型 ID编号
冲头尺寸
射出位置
二速位置 增压位置
增压选择
顶出延时 顶回延时
时间设定
冲头润滑 开模
射料
射出压力
储能 二速压力手轮 (圈) 增压压力手轮 (圈) 总压力(Mpa)
开模压力(Mpa)