高炉生产工艺流程
高炉工艺流程

高炉工艺流程高炉是冶金工业中最重要的设备之一,用于生产炼铁。
高炉工艺流程的主要目标是将铁矿石转化为可用于生产钢铁的铁液。
下面是一个典型的高炉工艺流程:1. 高炉的装料:首先,将适量的炼铁生料(铁矿石,焦炭和石灰石)按照一定比例混合,并通过送料系统连续地装入高炉的上部,即炉缸。
2. 预热和干燥:装料进入高炉后,通过炉顶和鼓风机将燃烧的热风引入高炉。
热风在高炉内升温,并将装料预热和干燥,以使其更容易熔化。
3. 还原反应:高炉内的燃烧和还原反应同时进行。
燃烧产生的热能和还原剂(主要是一氧化碳)使铁矿石发生还原反应,将氧气从铁矿石中脱去,生成铁和一氧化碳。
4. 熔化和铸渣:随着高炉内温度的升高,铁矿石开始融化,并与燃烧产生的一氧化碳反应生成液态的铁液。
在融化的过程中,石灰石被加入以吸收并结合炉渣中的杂质,形成铸渣。
5. 铸渣处理:铸渣是高炉中产生的主要副产品之一。
在高炉底部,温度较低的区域,通过铁口将铁液和铸渣分离。
铁液通过铁口流出,而铸渣则被收集并送入渣铁处理设备进一步处理。
6. 倾吐:当高炉达到预定的操作周期后,铁液将被倾吐到铁水箱中,并通过连铸技术进一步加工成钢坯。
7. 渣铁处理:铸渣中包含着一定量的铁和有价值的金属元素,因此需要对铸渣进行处理。
渣铁处理设备通常包括磁选机、重介质分选机和焦炉等,以回收其中的金属。
8. 炉后处理:通过高炉后处理操作,可以对炼铁过程中产生的废气和废液进行处理。
例如,废气可以通过脱硫和除尘设备进行净化,废液可以通过沉淀和过滤等方法进行处理。
这是一个典型的高炉工艺流程,每个钢铁生产厂商都可能有些许差异。
此外,高炉的操作也需要高度的技术和经验,以确保生产的效率和质量。
高炉的工艺流程是复杂而多变的,需要不断的优化和改进,以降低能耗、提高产量和质量。
高炉炼铁工艺流程简介
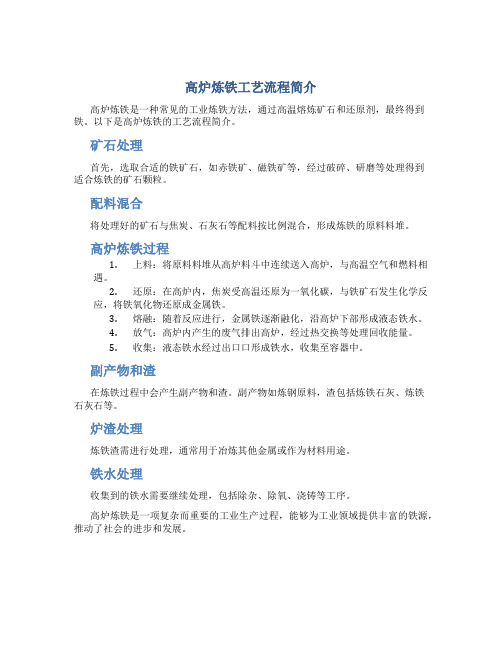
高炉炼铁工艺流程简介
高炉炼铁是一种常见的工业炼铁方法,通过高温熔炼矿石和还原剂,最终得到铁。
以下是高炉炼铁的工艺流程简介。
矿石处理
首先,选取合适的铁矿石,如赤铁矿、磁铁矿等,经过破碎、研磨等处理得到
适合炼铁的矿石颗粒。
配料混合
将处理好的矿石与焦炭、石灰石等配料按比例混合,形成炼铁的原料料堆。
高炉炼铁过程
1.上料:将原料料堆从高炉料斗中连续送入高炉,与高温空气和燃料相
遇。
2.还原:在高炉内,焦炭受高温还原为一氧化碳,与铁矿石发生化学反
应,将铁氧化物还原成金属铁。
3.熔融:随着反应进行,金属铁逐渐融化,沿高炉下部形成液态铁水。
4.放气:高炉内产生的废气排出高炉,经过热交换等处理回收能量。
5.收集:液态铁水经过出口口形成铁水,收集至容器中。
副产物和渣
在炼铁过程中会产生副产物和渣。
副产物如炼钢原料,渣包括炼铁石灰、炼铁
石灰石等。
炉渣处理
炼铁渣需进行处理,通常用于冶炼其他金属或作为材料用途。
铁水处理
收集到的铁水需要继续处理,包括除杂、除氧、浇铸等工序。
高炉炼铁是一项复杂而重要的工业生产过程,能够为工业领域提供丰富的铁源,推动了社会的进步和发展。
高炉炼铁的主要工艺流程

高炉炼铁的主要工艺流程
《高炉炼铁的主要工艺流程》
高炉是钢铁企业中用于炼铁的主要设备,其工艺流程是将铁矿石和焦炭加入高炉内,经过一系列的化学和物理反应,最终得到熔融的生铁。
下面将介绍高炉炼铁的主要工艺流程。
1. 搅拌坩埚法:将原铁矿石和焦炭按一定的比例混合,放入高炉的上部,即炉料层。
在高炉内,炉料层受到高温和高压的影响,发生一系列的物理和化学反应。
2. 燃烧:通过给炉料层加入空气或者氧气,点燃炉料层的顶部,使其燃烧。
燃烧产生的热量使炉料层内的焦炭燃烧,并提供高温条件,促进各种反应的进行。
3. 还原反应:当焦炭燃烧释放出一定量的一氧化碳时,与高炉内的铁矿石发生还原反应,使氧化铁还原为生铁。
4. 精炼:在高温下,生铁中的杂质和一些有害元素(如硫、磷等)会被氧化成气体,并通过炉顶排出。
这一过程称为精炼,是炉料中杂质清除的重要环节。
5. 收得生铁:经过一定时间的冶炼,高炉内的炉料最终产生了熔融的生铁。
生铁通过炉口排除,并进入铁水槽中,成为炼铁的产物。
通过上述简单介绍,可以看出高炉炼铁的主要工艺流程是一个
复杂的过程,包括搅拌坩埚法、燃烧、还原反应、精炼和收得生铁等环节。
这一流程不仅需要科学合理的原料比例和控制方法,还需要高炉操作者的丰富经验和技巧。
只有合理的工艺流程和专业的操作技术,才能保证高炉炼铁的顺利进行和生产出优质的生铁产品。
炼铁高炉工艺流程
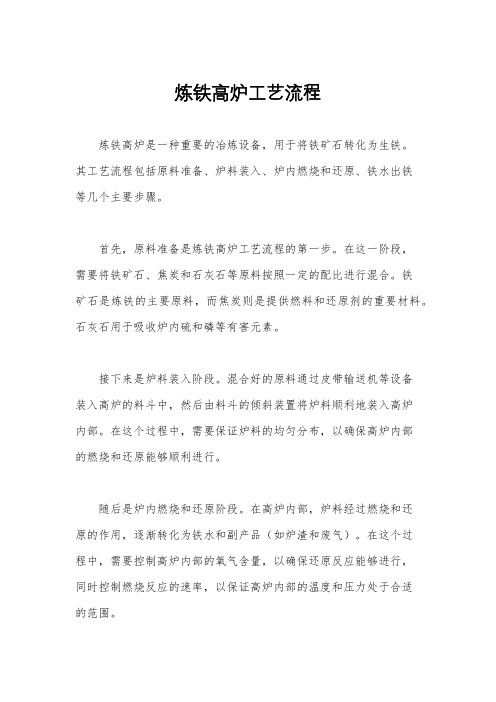
炼铁高炉工艺流程
炼铁高炉是一种重要的冶炼设备,用于将铁矿石转化为生铁。
其工艺流程包括原料准备、炉料装入、炉内燃烧和还原、铁水出铁
等几个主要步骤。
首先,原料准备是炼铁高炉工艺流程的第一步。
在这一阶段,
需要将铁矿石、焦炭和石灰石等原料按照一定的配比进行混合。
铁
矿石是炼铁的主要原料,而焦炭则是提供燃料和还原剂的重要材料。
石灰石用于吸收炉内硫和磷等有害元素。
接下来是炉料装入阶段。
混合好的原料通过皮带输送机等设备
装入高炉的料斗中,然后由料斗的倾斜装置将炉料顺利地装入高炉
内部。
在这个过程中,需要保证炉料的均匀分布,以确保高炉内部
的燃烧和还原能够顺利进行。
随后是炉内燃烧和还原阶段。
在高炉内部,炉料经过燃烧和还
原的作用,逐渐转化为铁水和副产品(如炉渣和废气)。
在这个过
程中,需要控制高炉内部的氧气含量,以确保还原反应能够进行,
同时控制燃烧反应的速率,以保证高炉内部的温度和压力处于合适
的范围。
最后是铁水出铁阶段。
经过一定时间的冶炼,高炉内部的铁水和炉渣逐渐达到一定的容量,此时需要开启高炉的出铁口,将铁水和炉渣分离出来。
铁水用于生产钢铁,而炉渣则可以用于建筑材料等领域。
总的来说,炼铁高炉工艺流程是一个复杂的系统工程,需要各个环节紧密配合,才能够顺利进行。
通过对每个环节的精细控制,可以提高炼铁高炉的冶炼效率和产品质量,从而为钢铁工业的发展做出贡献。
高炉生产工艺流程

接下来是炉气处理阶段,高炉冶炼过程中产生的炉气中含有一氧化碳、二氧化碳、氮气等物质。这些气体需要被净化和处理,以达到排放标准。常用的方法包括干法除尘、湿法除尘、除硫和除氮等。
最后是余热回收阶段,高炉生产过程中产生了大量的余热,包括炉渣的冷却余热和炉气的余热。这些余热可以通过余热回收系统进行收集和利用,从而提高能源利用效率。
接下来是炉内反应阶段,当炉缸中的炉料逐渐下降时,炉缸内的温度会迅速上升。炉料在高温下被还原成铁,同时产生大量的炉渣。在这个过程中,还会产生大量的一氧化碳和水蒸气。
然后是铁水出炉阶段,当足够的铁被还原出来时,可以通过倾炉孔将铁水从高炉中排出。铁水会流入铁罐中,并冷却凝固成铁块。
之后是炉渣处理阶段,高炉炉渣是由炉料ห้องสมุดไป่ตู้的铁氧化物、石灰石和其他杂质组成的。处理炉渣主要有两个目的:一是回收其中的铁,二是确保炉渣中的有害物质被安全处理。一般会通过氧枪在炉渣中吹氧气,使其中的铁氧化物氧化成铁,并进一步回收。
高炉生产工艺流程
高炉是一种用于冶炼铁的设备,它能够将铁矿石中的铁氧化物还原成纯铁。高炉生产工艺流程包括六个主要步骤:入炉、炉内反应、铁水出炉、炉渣处理、炉气处理和余热回收。
首先是入炉阶段,这个阶段主要是将铁矿石和焦炭按一定比例装入高炉的上料斗中,然后通过料斗控制系统将料物顺次送入炉缸内。在这个过程中,还会加入一定量的石灰石和焦粉,以调节炉料的碱度和流动性。
高炉生产工艺流程

高炉生产工艺流程
《高炉生产工艺流程》
高炉是冶炼铁的主要设备之一,其生产工艺流程复杂而精密。
下面我们就来简要介绍一下高炉生产工艺流程。
首先是原料的准备。
在高炉冶炼过程中,主要原料包括铁矿石、焦炭和石灰石。
这些原料需要进行粉碎和预处理,以便于在高炉中的正常使用。
接下来是原料的投入。
在高炉的顶部,将热风和原料同时注入,而在炉底则通过鼓风机将空气送入,这样可以形成高炉内部的燃烧和还原环境。
然后是炉内反应的进行。
在高炉内部,焦炭先被加热分解形成一定数量的一氧化碳和氢气,然后这些还原气体与熔化的铁矿石发生反应,最终生成液态铁和副产物(例如石灰石渣和炉渣)。
最后是产物的采集和处理。
产生的液态铁会通过出口流出,而炉渣则会流出高炉底部。
这些产物需要进一步加工,例如炉渣用于筑路或者水泥生产,而液态铁则用于钢铁的生产。
总的来说,高炉生产工艺流程是一个复杂而有序的过程,需要严格的管理和运行。
只有良好的生产工艺流程,才能确保高炉的正常生产,同时也能减少资源的浪费和环境的污染。
钢铁生产高炉操作工作流程

钢铁生产高炉操作工作流程钢铁生产过程是一个复杂而精细的工艺过程,其中高炉操作是整个生产流程中至关重要的一环。
本文将详细介绍钢铁生产高炉操作的工作流程,从原料准备、炉缸布料、点火预热、风温控制、出铁、停炉等环节进行阐述。
一、原料准备钢铁生产的原料主要包括铁矿石、焦炭、石灰石和回收废铁等。
在高炉操作前,首先需要对这些原料进行准备工作。
铁矿石需要破碎、分级、洗选,以确保矿石的质量和粒度符合生产要求。
焦炭则需要经过碳化、煅烧和混合等处理,以提高燃烧效率和炉内温度。
二、炉缸布料炉缸布料是指将预先准备好的原料按一定的比例投入到高炉炉腔内。
在高炉操作中,需要考虑各种原料的配比和进料方式,以达到最佳的冶炼效果。
通常情况下,铁矿石和焦炭按一定比例混合后装入高炉上部的料斗,然后通过布料装置均匀分布到炉缸内。
三、点火预热炉缸布料完成后,需要进行点火预热操作。
点火预热是指将炉内的原料进行燃烧,以使炉内温度逐渐升高到冶炼所需的温度。
点火预热过程通常包括初次点火、次发点火和正常点火等阶段。
在高炉操作中,要注意控制点火的氧气和燃料的配比,以保证点火正常进行。
四、风温控制点火预热完成后,需要进行风温控制。
高炉内需要通过燃烧来提供能量,而风是提供燃烧所需氧气的关键。
在高炉操作过程中,需要根据冶炼条件的要求,控制风温的高低。
通常情况下,风的温度越高,炉内温度也会相应提高。
通过调节风温,可以控制高炉内的温度和冶炼反应的速率。
五、出铁高炉操作的最终目的是生产出高质量的钢铁产品。
在生产过程中,需要定期进行出铁操作,将炉内的铁水抽取出来,并进行冷却和净化处理。
出铁操作需要考虑铁水的温度、速度和清洁度等因素,以确保生产出符合要求的钢铁产品。
六、停炉高炉操作周期结束或需要进行维护时,需要进行停炉操作。
停炉是指将高炉的冶炼过程暂停,进行冷却、清洗和维护等工作。
在停炉期间,需要对高炉进行检查、保养和维修,以保证高炉的正常运行和延长使用寿命。
综上所述,钢铁生产高炉操作是一个复杂而关键的工作环节。
高炉炼铁生产工艺流程

高炉炼铁生产工艺流程
高炉炼铁生产工艺流程是指利用高炉将铁矿石还原为铁的整个过程,下面以700字左右简要介绍高炉炼铁生产工艺流程。
高炉炼铁生产工艺流程主要包括原料准备、炉料制备、高炉的运行和操作以及产物处理等环节。
在高炉炼铁生产中,原料准备是首要环节,主要包括铁矿石的选矿、破碎、磁选等工序。
选矿和磁选可将铁矿石中的杂质去除,提高铁矿石的品位。
破碎则是将大块的铁矿石破碎成适合高炉入炉的大小。
炉料制备是指将铁矿石与其他辅料按一定比例混合烧结而成的固体料块,主要包括铁矿石、焦炭和石灰石等。
混合烧结的目的是提高炉料的强度和透气性,保证高炉正常运行。
高炉的运行和操作是指高炉内矿料的还原和产物的处理过程。
高炉内的还原过程是指将铁矿石中的氧化铁还原为金属铁的过程。
高炉内温度较高,铁矿石中的氧化铁在还原剂(主要为焦炭)的作用下被还原为CO和H2,并最终在高炉底部还原为铁。
高炉产物的处理主
要包括炉渣处理和收集炉气中的有价金属。
炉渣是高炉还原过程中由炉料和矿石中的杂质形成的。
通过适当的操作,可以将炉渣中的有价金属(如铜、锌等)回收利用。
炉气是高炉过程中产生的气体,在高炉炼铁生产中,通常以废气发电的方式将炉气利用起来,不仅能减少能源的消耗,还可以降低对环境的污染。
总的来说,高炉炼铁生产工艺流程主要包括原料准备、炉料制备、高炉的运行和操作以及产物处理等环节。
通过合理的工艺流程,可以高效地将铁矿石还原为金属铁,实现铁的生产和利
用。
高炉炼铁工艺流程在全球范围内得到广泛应用,对推动经济的发展和保障国家的资源安全起到了重要作用。
高炉生产的工艺流程
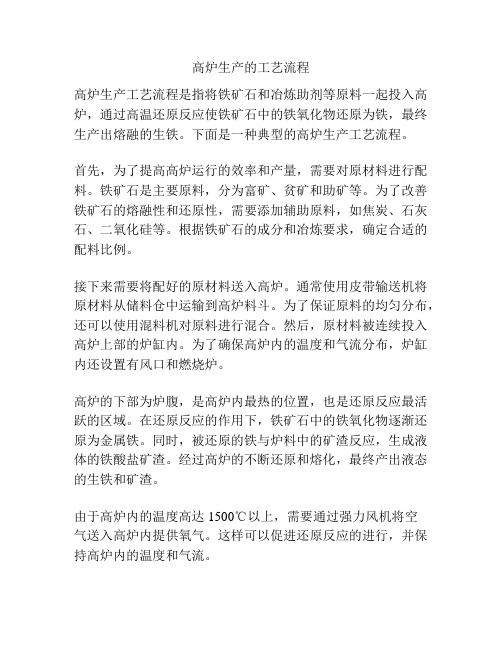
高炉生产的工艺流程高炉生产工艺流程是指将铁矿石和冶炼助剂等原料一起投入高炉,通过高温还原反应使铁矿石中的铁氧化物还原为铁,最终生产出熔融的生铁。
下面是一种典型的高炉生产工艺流程。
首先,为了提高高炉运行的效率和产量,需要对原材料进行配料。
铁矿石是主要原料,分为富矿、贫矿和助矿等。
为了改善铁矿石的熔融性和还原性,需要添加辅助原料,如焦炭、石灰石、二氧化硅等。
根据铁矿石的成分和冶炼要求,确定合适的配料比例。
接下来需要将配好的原材料送入高炉。
通常使用皮带输送机将原材料从储料仓中运输到高炉料斗。
为了保证原料的均匀分布,还可以使用混料机对原料进行混合。
然后,原材料被连续投入高炉上部的炉缸内。
为了确保高炉内的温度和气流分布,炉缸内还设置有风口和燃烧炉。
高炉的下部为炉腹,是高炉内最热的位置,也是还原反应最活跃的区域。
在还原反应的作用下,铁矿石中的铁氧化物逐渐还原为金属铁。
同时,被还原的铁与炉料中的矿渣反应,生成液体的铁酸盐矿渣。
经过高炉的不断还原和熔化,最终产出液态的生铁和矿渣。
由于高炉内的温度高达1500℃以上,需要通过强力风机将空气送入高炉内提供氧气。
这样可以促进还原反应的进行,并保持高炉内的温度和气流。
生铁和矿渣分布在高炉的下部,通过高炉的出铁口和高炉炉底进行采集。
生铁经过处理后可以用于制造钢铁产品,矿渣则会进行冷却和处理,用于生产水泥等建筑材料。
在高炉生产过程中,为保证高炉的正常运行,还需要注意高炉内的铁液流动性、温度和气体分布的均匀性。
此外,高炉还需要定期检修和清理,以保持设备的正常运转。
总的来说,高炉生产工艺流程是一个复杂的化学反应过程。
通过合理的原料配比和控制温度、气流等因素,可以实现高效、稳定的铁矿石冶炼,生产出高质量的生铁和矿渣,为钢铁产业提供坚实的基础。
高炉炼铁工艺流程
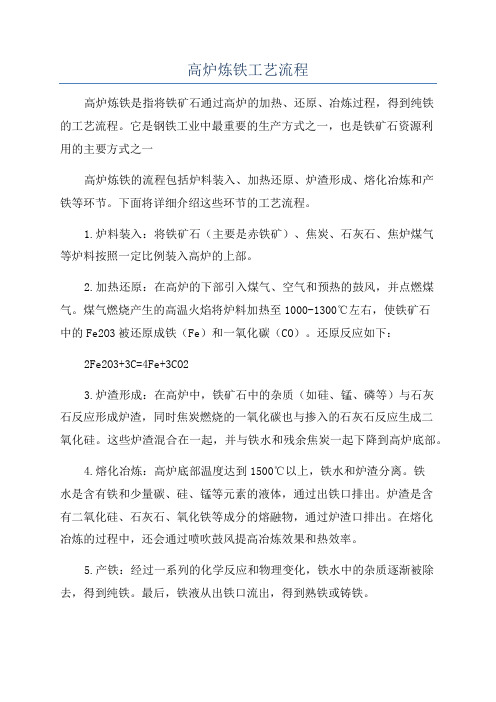
高炉炼铁工艺流程
高炉炼铁是指将铁矿石通过高炉的加热、还原、冶炼过程,得到纯铁
的工艺流程。
它是钢铁工业中最重要的生产方式之一,也是铁矿石资源利
用的主要方式之一
高炉炼铁的流程包括炉料装入、加热还原、炉渣形成、熔化冶炼和产
铁等环节。
下面将详细介绍这些环节的工艺流程。
1.炉料装入:将铁矿石(主要是赤铁矿)、焦炭、石灰石、焦炉煤气
等炉料按照一定比例装入高炉的上部。
2.加热还原:在高炉的下部引入煤气、空气和预热的鼓风,并点燃煤气。
煤气燃烧产生的高温火焰将炉料加热至1000-1300℃左右,使铁矿石
中的Fe2O3被还原成铁(Fe)和一氧化碳(CO)。
还原反应如下:2Fe2O3+3C=4Fe+3CO2
3.炉渣形成:在高炉中,铁矿石中的杂质(如硅、锰、磷等)与石灰
石反应形成炉渣,同时焦炭燃烧的一氧化碳也与掺入的石灰石反应生成二
氧化硅。
这些炉渣混合在一起,并与铁水和残余焦炭一起下降到高炉底部。
4.熔化冶炼:高炉底部温度达到1500℃以上,铁水和炉渣分离。
铁
水是含有铁和少量碳、硅、锰等元素的液体,通过出铁口排出。
炉渣是含
有二氧化硅、石灰石、氧化铁等成分的熔融物,通过炉渣口排出。
在熔化
冶炼的过程中,还会通过喷吹鼓风提高冶炼效果和热效率。
5.产铁:经过一系列的化学反应和物理变化,铁水中的杂质逐渐被除去,得到纯铁。
最后,铁液从出铁口流出,得到熟铁或铸铁。
高炉生产工艺流程

高炉生产工艺流程高炉是冶金工业中常用的设备,用于将铁矿石转化为熔融铁的冶炼装置。
它是钢铁工业的重要环节,具有高温、高压、复杂的生产工艺流程。
以下是一个典型的高炉生产工艺流程。
首先,在高炉生产中,需要准备原料。
原料主要包括铁矿石、冶金焦、石灰石等。
其中,铁矿石是高炉的主要原料,通常选择含铁量较高的矿石。
冶金焦是用于提供燃料和还原剂的原材料,而石灰石则是用于调节高炉内矿渣的成分。
接下来,将原料送入高炉。
一般情况下,原料会通过皮带输送机、提升机等设备送入高炉顶部的料斗中。
然后,原料被均匀地分布在高炉内,保证了冶炼的均匀性。
在高炉内,原料经历一系列的物理、化学反应过程,最终转化为熔融铁。
首先,原料在高温下发生燃烧反应,冶金焦中的碳和空气中的氧气反应产生高温燃烧气体。
这个过程叫做炉外还原。
在高温燃烧气体的作用下,铁矿石中的氧气被还原成元素铁,并和冶炼焦发生反应生成熔融铁。
这个过程叫做炉内还原。
此外,石灰石的主要作用是与矿石中的杂质反应形成矿渣,从而提高了熔点,方便后续的分离。
熔融铁以液态形式沉积在高炉底部的铁口中,而矿渣则会浮在熔融铁上方。
为了保证高炉正常运行,定期需要排除矿渣。
这个过程叫做铁水的出铁和矿渣的出渣。
最后,在高炉冶炼完毕后,需要对铁口进行装备维护。
同时,高炉底部会有积存的铁渣和矿下砂,需要清理干净,为下一次冶炼做准备。
总的来说,高炉生产工艺流程包括原料准备、送料、炉外还原、炉内还原、铁水的出铁和矿渣的出渣以及设备维修等环节。
这个流程涵盖了高炉冶炼中的主要过程,确保了高炉正常运行和高质量的铁产品的生产。
高炉工艺流程

高炉工艺流程
高炉是冶炼铁的主要设备,其工艺流程包括原料准备、炉料装入、炉内燃烧、还原、熔融和出铁等环节。
下面将详细介绍高炉工艺流程。
首先是原料准备。
高炉的主要原料有焦炭、铁矿石和石灰石。
焦炭是炼铁的燃料,铁矿石是生铁的主要原料,石灰石是用来消耗炉渣中的硅酸和硫。
这些原料需要经过破碎、筛分和配比等工序,确保其化学成分和粒度符合高炉冶炼的要求。
接下来是炉料装入。
在高炉顶部设有料斗,将原料按一定的配比顺序装入料斗,然后通过料斗的开闭装入到高炉内。
炉料的装入顺序和层次对高炉的冶炼过程有着重要的影响,需要根据炉料的性质和冶炼要求进行合理的设计。
然后是炉内燃烧和还原。
在高炉内,焦炭燃烧产生的热量使炉料逐渐升温,矿石中的铁氧化物被还原成金属铁。
同时,燃烧产生的一氧化碳还与矿石中的氧化物发生化学反应,生成二氧化碳和金属铁。
接着是熔融。
随着高炉内温度的升高,金属铁逐渐熔化,与炉渣分离。
炉渣是炼铁过程中产生的一种碱性物质,它能够与矿石中的杂质发生化学反应,形成易于分离的渣滓。
最后是出铁。
经过一系列的冶炼过程,炉内的金属铁和炉渣分离,金属铁在高炉底部聚集,通过出铁口流出。
而炉渣则通过炉渣口排出高炉。
总的来说,高炉工艺流程是一个复杂的物理化学过程,需要严格控制各个环节的操作参数,确保冶炼过程稳定、高效。
同时,高炉的自动化技术和智能化控制也在不断发展,为提高生产效率和降低能耗提供了重要的技术支持。
通过对高炉工艺流程的深入了解,可以更好地指导生产实践,提高炼铁工艺的技术水平,推动炼铁行业的可持续发展。
高炉炼铁工艺流程

炼铁基本概论一、高炉炼铁生产工艺流程在高炉炼铁生产中,高炉是工艺流程的主体,从其上部装入的铁矿石、燃料和熔剂向下运动,下部鼓入空气燃烧燃料,产生大量的还原性气体向上运动,炉料经过加热、还原、熔化、造渣、渗碳、脱硫等一系列物理化学过程,最后生成液态炉渣和生铁。
高炉是一竖式圆筒形冶炼炉,由炉基、炉壳、炉衬及冷却设备、支柱或框架组成。
用耐火砖或其他材料砌筑成的炉衬形成的高炉内部空间形状称为炉型,一般由上至下分为炉喉、炉身、炉腰、炉腹和炉缸五部分。
如图所示。
炉喉炉身炉腰炉腹炉缸以高炉本体为核心,高炉生产还包括以下几个系统:1. 上料系统:包括贮矿场,贮矿槽,焦炭滚筛,称量漏斗,料坑,料车、斜桥和卷扬机等,大型高炉采用皮带机上料。
本系统的任务是将原、燃料运到炉顶装入受料漏斗。
2. 装料系统:包括上料罐,下料罐,上密封阀,下密封阀,料流调节阀,布料溜槽,气密箱等。
高压操作的高炉还有均压阀和放散阀。
本系统的任务是均匀地按工艺要求将上料系统运来的炉料装入炉内。
3. 送风系统:包括鼓风机,热风炉,热风总管,热风围管、送风装置等。
本系统的任务是把从鼓风机房送出的冷风加热并送入高炉。
4. 煤气回收及除尘系统:包括煤气上升管,煤气下降管,重力除尘器,布袋除尘等。
高压高炉还有高压阀组。
本系统的任务是将炉顶引出的含尘量很高的荒煤气净化成合乎要求的气体燃料。
5. 渣铁处理系统:包括出铁场,泥炮,开口机,炉前吊车,铁水罐,摆动流槽,铸铁机,堵渣口机,嘉恒炉渣处理设施等。
本系统的任务是定期将炉内的渣、铁出净,保证高炉连续生产。
6. 喷吹系统:喷吹系统目前以喷煤为主。
喷煤系统有制粉机,收集罐,贮存罐,喷吹罐,混合器和喷枪。
喷油系统有卸油泵,贮油罐,过滤器,送油泵,稳压罐,调整装置及喷枪。
本系统的任务是磨制、收存和计量后把煤粉或重油从风口喷入高炉。
7. 动力系统:该系统包括水、电、压缩空气、氮气、蒸汽等生产供应部门。
本系统的任务是为高炉各生产系统提供保障服务。
高炉生产的工艺流程

高炉生产的工艺流程
《高炉生产工艺流程》
高炉是一种生产铁的设备,通常用来从铁矿石中提取铁的过程。
下面是高炉生产的工艺流程。
首先,取得原料。
原料包括铁矿石、焦炭和石灰石。
铁矿石是高炉的主要原料,通常是由含铁量较高的矿石制成。
焦炭是一种煤炭制品,用来加热高炉,使铁矿石中的铁得以提取。
石灰石用来帮助将非铁性杂质从铁矿石中剥离出来。
其次,原料预处理。
铁矿石首先需要经过破碎和磨粉的过程,以便在高炉中更容易被加热。
焦炭也需要进行预处理,以去除其中的杂质和硫。
接下来,原料进入高炉。
铁矿石、焦炭和石灰石被混合在一起,然后送入高炉的顶部。
高炉内部温度达到1500°C以上,原料
在高温下逐渐熔化并产生还原气体。
然后,铁的提取。
在高炉内,还原气体和熔融铁矿石反应,将铁从矿石中提取出来。
非铁性杂质则形成渣,浮在熔融的铁上方。
这样,铁和渣就可以分离了。
最后,产出铁和渣。
经过一系列的处理,从高炉中得到的铁和渣分别被收集起来。
铁经过冷却和成形后,成为各种钢材的生产原料。
而渣通常被用作道路材料或建筑材料。
在整个高炉生产的工艺流程中,需要高温、还原气体和适当的原料配比。
这样才能确保高炉生产出优质的铁和渣。
高炉炼铁生产工艺流程
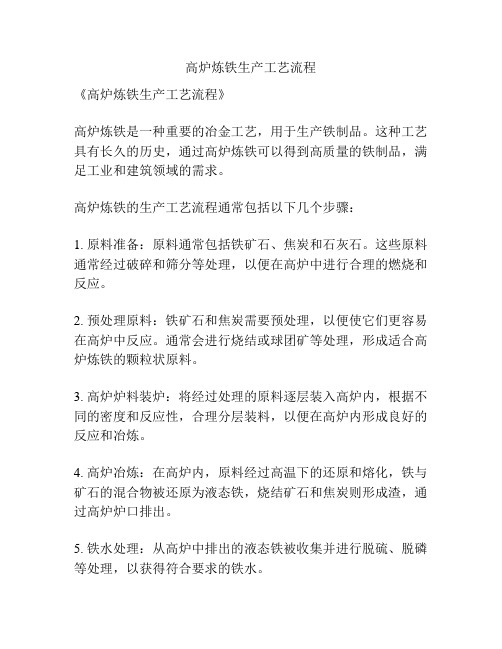
高炉炼铁生产工艺流程
《高炉炼铁生产工艺流程》
高炉炼铁是一种重要的冶金工艺,用于生产铁制品。
这种工艺具有长久的历史,通过高炉炼铁可以得到高质量的铁制品,满足工业和建筑领域的需求。
高炉炼铁的生产工艺流程通常包括以下几个步骤:
1. 原料准备:原料通常包括铁矿石、焦炭和石灰石。
这些原料通常经过破碎和筛分等处理,以便在高炉中进行合理的燃烧和反应。
2. 预处理原料:铁矿石和焦炭需要预处理,以便使它们更容易在高炉中反应。
通常会进行烧结或球团矿等处理,形成适合高炉炼铁的颗粒状原料。
3. 高炉炉料装炉:将经过处理的原料逐层装入高炉内,根据不同的密度和反应性,合理分层装料,以便在高炉内形成良好的反应和冶炼。
4. 高炉冶炼:在高炉内,原料经过高温下的还原和熔化,铁与矿石的混合物被还原为液态铁,烧结矿石和焦炭则形成渣,通过高炉炉口排出。
5. 铁水处理:从高炉中排出的液态铁被收集并进行脱硫、脱磷等处理,以获得符合要求的铁水。
6. 铁水浇铸:经过处理的铁水被注入铸模,冷却后形成铁制品。
高炉炼铁生产工艺流程通过一系列复杂的物理化学反应,将铁矿石转化为高质量的铁制品。
这种工艺是钢铁工业的基础,为各种行业提供了重要的原材料和零部件。
高炉生产工艺流程
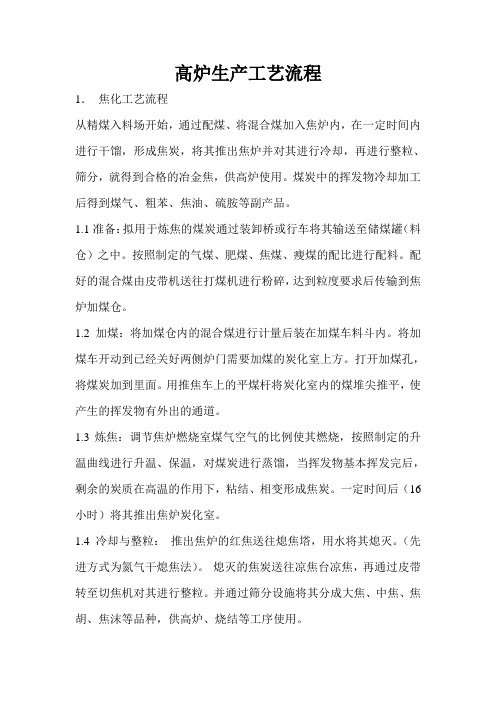
高炉生产工艺流程1.焦化工艺流程从精煤入料场开始,通过配煤、将混合煤加入焦炉内,在一定时间内进行干馏,形成焦炭,将其推出焦炉并对其进行冷却,再进行整粒、筛分,就得到合格的冶金焦,供高炉使用。
煤炭中的挥发物冷却加工后得到煤气、粗苯、焦油、硫胺等副产品。
1.1准备:拟用于炼焦的煤炭通过装卸桥或行车将其输送至储煤罐(料仓)之中。
按照制定的气煤、肥煤、焦煤、瘦煤的配比进行配料。
配好的混合煤由皮带机送往打煤机进行粉碎,达到粒度要求后传输到焦炉加煤仓。
1.2 加煤:将加煤仓内的混合煤进行计量后装在加煤车料斗内。
将加煤车开动到已经关好两侧炉门需要加煤的炭化室上方。
打开加煤孔,将煤炭加到里面。
用推焦车上的平煤杆将炭化室内的煤堆尖推平,使产生的挥发物有外出的通道。
1.3炼焦:调节焦炉燃烧室煤气空气的比例使其燃烧,按照制定的升温曲线进行升温、保温,对煤炭进行蒸馏,当挥发物基本挥发完后,剩余的炭质在高温的作用下,粘结、相变形成焦炭。
一定时间后(16小时)将其推出焦炉炭化室。
1.4 冷却与整粒:推出焦炉的红焦送往熄焦塔,用水将其熄灭。
(先进方式为氮气干熄焦法)。
熄灭的焦炭送往凉焦台凉焦,再通过皮带转至切焦机对其进行整粒。
并通过筛分设施将其分成大焦、中焦、焦胡、焦沫等品种,供高炉、烧结等工序使用。
1.5 化产回收:焦炉炭化室内炼焦蒸馏出的挥发物通过积气罐收集后送往化产回收系统,在其冷却过程中,会析出焦油、粗苯、氨等物质,采用不同工艺将其回收处理。
作为副产品销售。
冷却的煤气供铸管退火炉、烧结点火炉等处使用。
2.烧结工艺流程从原料进入料场开始,通过配料将各种矿粉按比例进行混合,通过胶带输送机将其送到烧结机上进行布料进行烧结,烧成的烧结矿经过破碎、筛分、冷却等工序形成成品烧结矿,成品烧结矿通过皮带输送至高炉料仓这一过程。
它包括原料储存、燃料加工、整粒、配料、一次混合、二次混合、烧结、冷却、整粒的全部工艺过程。
2.1 准备:精矿粉、富矿粉、高炉返矿、云粉等由汽车从原料场转运至烧结配料库。
炼铁高炉工艺流程
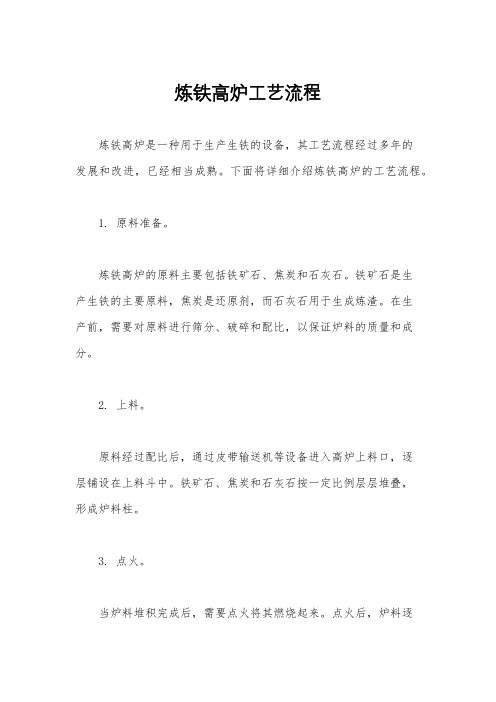
炼铁高炉工艺流程炼铁高炉是一种用于生产生铁的设备,其工艺流程经过多年的发展和改进,已经相当成熟。
下面将详细介绍炼铁高炉的工艺流程。
1. 原料准备。
炼铁高炉的原料主要包括铁矿石、焦炭和石灰石。
铁矿石是生产生铁的主要原料,焦炭是还原剂,而石灰石用于生成炼渣。
在生产前,需要对原料进行筛分、破碎和配比,以保证炉料的质量和成分。
2. 上料。
原料经过配比后,通过皮带输送机等设备进入高炉上料口,逐层铺设在上料斗中。
铁矿石、焦炭和石灰石按一定比例层层堆叠,形成炉料柱。
3. 点火。
当炉料堆积完成后,需要点火将其燃烧起来。
点火后,炉料逐渐升温,煤气和炉渣开始产生,高炉内部温度逐渐升高。
4. 还原。
在高温下,焦炭开始发生还原反应,将铁矿石中的氧化铁还原为金属铁。
还原反应释放出大量的热量,使高炉内部温度进一步升高。
5. 碳氧化反应。
随着温度的升高,炼炉石灰石开始分解,释放出二氧化碳,与铁矿石中的残余氧化物发生碳氧化反应,生成炼渣。
6. 放铁。
当高炉内部温度达到一定程度,炼铁开始熔化,熔化的铁从高炉底部的出铁口流出,经过冷却成型,得到初生铁。
7. 放渣。
除了炼铁外,高炉中还会生成炼渣。
炼渣是一种含有氧化物和矿石杂质的物质,需要定期从高炉炉嘴排出,以保证高炉正常运行。
8. 检修。
高炉在生产过程中需要进行定期检修和维护,以保证设备的正常运行和安全生产。
检修包括炉体、炉缸、炉喉等部位的维护和更换。
总结,炼铁高炉工艺流程经过多年的发展和改进,已经相当成熟。
从原料准备到炉料上料、点火、还原、碳氧化反应、放铁、放渣和检修,每个环节都需要严格控制,以保证高炉的正常运行和生产效率。
炼铁高炉是钢铁行业的重要设备,其工艺流程对于钢铁生产具有重要的意义。
高炉炼铁生产工艺流程简介
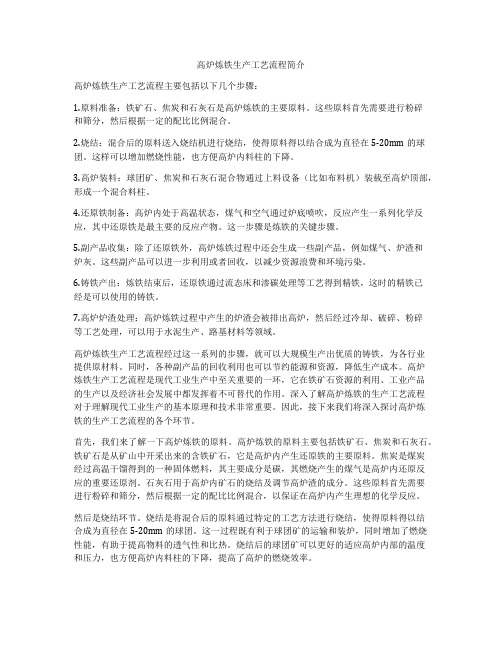
高炉炼铁生产工艺流程简介高炉炼铁生产工艺流程主要包括以下几个步骤:1.原料准备:铁矿石、焦炭和石灰石是高炉炼铁的主要原料。
这些原料首先需要进行粉碎和筛分,然后根据一定的配比比例混合。
2.烧结:混合后的原料送入烧结机进行烧结,使得原料得以结合成为直径在5-20mm的球团。
这样可以增加燃烧性能,也方便高炉内料柱的下降。
3.高炉装料:球团矿、焦炭和石灰石混合物通过上料设备(比如布料机)装载至高炉顶部,形成一个混合料柱。
4.还原铁制备:高炉内处于高温状态,煤气和空气通过炉底喷吹,反应产生一系列化学反应,其中还原铁是最主要的反应产物。
这一步骤是炼铁的关键步骤。
5.副产品收集:除了还原铁外,高炉炼铁过程中还会生成一些副产品,例如煤气、炉渣和炉灰。
这些副产品可以进一步利用或者回收,以减少资源浪费和环境污染。
6.铸铁产出:炼铁结束后,还原铁通过流态床和渗碳处理等工艺得到精铁,这时的精铁已经是可以使用的铸铁。
7.高炉炉渣处理:高炉炼铁过程中产生的炉渣会被排出高炉,然后经过冷却、破碎、粉碎等工艺处理,可以用于水泥生产、路基材料等领域。
高炉炼铁生产工艺流程经过这一系列的步骤,就可以大规模生产出优质的铸铁,为各行业提供原材料。
同时,各种副产品的回收利用也可以节约能源和资源,降低生产成本。
高炉炼铁生产工艺流程是现代工业生产中至关重要的一环,它在铁矿石资源的利用、工业产品的生产以及经济社会发展中都发挥着不可替代的作用。
深入了解高炉炼铁的生产工艺流程对于理解现代工业生产的基本原理和技术非常重要。
因此,接下来我们将深入探讨高炉炼铁的生产工艺流程的各个环节。
首先,我们来了解一下高炉炼铁的原料。
高炉炼铁的原料主要包括铁矿石、焦炭和石灰石。
铁矿石是从矿山中开采出来的含铁矿石,它是高炉内产生还原铁的主要原料。
焦炭是煤炭经过高温干馏得到的一种固体燃料,其主要成分是碳,其燃烧产生的煤气是高炉内还原反应的重要还原剂。
石灰石用于高炉内矿石的烧结及调节高炉渣的成分。
高炉生产工艺流程

放大
高炉生产工艺,流程简介
高炉炼铁简单的说就是,将铁矿石(烧结矿、球团矿、 块矿)焦炭按比例分层从高炉炉顶装入。从高炉下部风口 处吹入高温鼓风(1100~1200℃)。在高炉炉内进行预热 还原反应,生成渣铁,渣铁从高炉下部铁口流出,在炉外 铁钩内利用渣铁本身比重不同(渣2.0铁7.8)进行分离。 渣进入渣沟,冲水渣或放入干渣坑。铁水通过铁钩摆动流 嘴放入鱼雷罐送往炼钢或铸铁机。高炉本身就是一种竖炉 型逆流式反应器。在炉内堆积成料柱状的炉料,受逆流而 上的高温还原煤气流的作用,不断地被加热、分解、还原、 软化、熔融、滴落,并最终形成渣铁融体而分离。高炉解 剖分析证明,冶炼过程中,炉内料柱基本上是整体下降, 称为层状下降或活塞流。高炉煤气经过除尘进入煤气管网, 完成整个冶炼过程。
65
1
36
7
200
1
120
35.6
65
1
124
7
200
1
378
16.4
1#高炉槽下原料参数及振动筛技术参数
项目
型号
装机数量
品种
处
理
粒度组成㎜
物 料 物料比重t/m3
温度、湿度℃
单机处理量t /h
筛面倾角
双振幅(㎜)
设 备
振动频率 (r/min)
参 分级粒度㎜
数 及
筛面规格(mm)
要 求
电机功率
安装方式
烧结矿 ≤150 ------常温 200 2-4 0-5°可调 1200×800 TZD-41-4C 2×0.75KW 1450 吊挂形式 振动电机 间断性 380V
Hale Waihona Puke 焦炭振动给料机TZG-95-150F 4
- 1、下载文档前请自行甄别文档内容的完整性,平台不提供额外的编辑、内容补充、找答案等附加服务。
- 2、"仅部分预览"的文档,不可在线预览部分如存在完整性等问题,可反馈申请退款(可完整预览的文档不适用该条件!)。
- 3、如文档侵犯您的权益,请联系客服反馈,我们会尽快为您处理(人工客服工作时间:9:00-18:30)。
一、运上料系统:
矿焦槽及槽下上料设备性能及参数
矿、焦槽工艺性能
料仓 烧结矿槽 焦炭槽 球团矿槽 单槽有效容积 (m3) 415 415 415 数量 (个) 5 4 3 总贮存量 ( t) 3631 830 2739 贮存时间 (h) 15.3 12.3 29.2
块杂矿槽
焦丁仓 粉焦仓 3-5mm小烧结矿 仓 粉矿仓
高炉生产工艺简介
放大
高炉生产工艺,流程简介
高炉炼铁简单的说就是,将铁矿石(烧结矿、球团矿、 块矿)焦炭按比例分层从高炉炉顶装入。从高炉下部风口 处吹入高温鼓风(1100~1200℃)。在高炉炉内进行预热 还原反应,生成渣铁,渣铁从高炉下部铁口流出,在炉外 铁钩内利用渣铁本身比重不同(渣2.0铁7.8)进行分离。 渣进入渣沟,冲水渣或放入干渣坑。铁水通过铁钩摆动流 嘴放入鱼雷罐送往炼钢或铸铁机。高炉本身就是一种竖炉 型逆流式反应器。在炉内堆积成料柱状的炉料,受逆流而 上的高温还原煤气流的作用,不断地被加热、分解、还原、 软化、熔融、滴落,并最终形成渣铁融体而分离。高炉解 剖分析证明,冶炼过程中,炉内料柱基本上是整体下降, 称为层状下降或活塞流。高炉煤气经过除尘进入煤气管网, 完成整个冶炼过程。
三、送风系统: 热风炉、鼓风机。
热风炉可分为四种类型。即:内燃、外燃、顶燃、球式。 内燃:又分为传统和改进型,下部燃烧室上不蓄热室,火井易短路烧穿。 外燃:大高炉多用外燃,占地大、投资高,炉壳因 晶体间应力腐蚀而引起开裂。 顶燃:利用炉顶空间进行燃烧,取消了侧燃烧室或外燃室,结构对称、 温度分明、占地少、效率高、投资少节能型热风炉。俄罗斯卡鲁金型,82 年在塔吉尔冶金公司1513M3首用。1150~1220℃工作。4、10、16年三次凉 炉观察拱顶,燃烧装置格子砖完好可工作30年。 球式:属于顶燃式烧球。 吉钢三座顶燃式热风炉,烧炉采用低热值高炉煤气掺烧焦炉煤气,采用 空气煤气双预热。单位蓄热面积106M2/m3,配二台助燃风机,1用1备,风 量15万m3/h,风压12kpa。二烧一送工作制,全高42.34米。热风阀、冷风 阀、混风阀、倒流阀、冷风放风阀、煤气1、煤气2、空气切断阀、烟道、 废气。 鼓风系统包括两台130t锅炉,两台汽轮机、一台电动鼓风机 汽轮机通过膜片式联轴器带动高炉鼓风机,汽轮机尾中温中压反动凝气式 汽轮机。鼓风机风量(额定)4500m3/h ,正常4000m3/h,下限2700m3/h、 出口压力 0.4MPa、转速4550转、全部静叶都可调的轴流式压缩机。
二、高炉本体及冷却系统
本体:炉底炉钢采用炭块+陶瓷砌体水冷炉底。 炉底总厚度2800mm,一层400mm高导热石墨碳砖+三层1200mm 半导热石墨碳砖+400mm国产微孔碳砖+800mm陶瓷砌体。 给排水:高炉采用砖壁合一全冷却壁,薄内衬,共14段冷却壁,其中 1~4段位低鉻铸铁。5、6、7段为国产铜冷却壁,其余各段为球墨铸铁, 采用全软水闭路循环冷却壁系统,冷却壁和炉底水冷管为一级冷却回路 系统,风口、中套、直吹管和热风阀组成第二级冷却回路系统。 全系统总循环水量:3500m3/h、一级回路2900+600 m3/h、 二级回路900 m3/h风口+650 m3/h二套、78 m3/h直吹管、 600 m3/h热风阀。二级合计2238 m3/h。 软水站:主要设备-电动离心泵3台(2用1备)、事故柴油泵1台、 电机泵1台、中压增压泵2台、高压增压泵3台(1用2备)
Y160M-6 2×5.5KW
坐式 激振器 间断性 380V
Y160M-6 2×5.5KW
坐式 激振器 间断性 380V
Y160M-6 2×5.5KW
坐式 激振器 间断性 380V
Y160M-6 2×5.5KW
坐式 激振器 间断性 380V
Y160M-6 2×5.5KW
坐式 激振器 间断性 380V
高炉可按工艺流程分为几个系统:
一、运上料系统:包括皮带运输、槽下筛分、称量、炉顶布料;
二、高炉本体、冷却系统:包括高炉本体耐材、炉形、软水闭路;
三、送风系统:包括风机、热风炉; 四、炉前出渣、铁系统:包括渣处理、铁水运输、铸铁机; 五、煤气处理系统:包括重力除尘、干法除尘、加压阀组、放散塔; 六、煤粉喷吹系统:包括制粉、喷吹; 七、环保除尘系统:包括矿槽除尘、出铁场除尘、铸铁机除尘。
外运
吉林钢铁高炉设计原则是: 1.坚持技术进步的原则,采用国内外成熟的先进技术及设备。 2.采用精料、高温、高压、富氧、及喷吹的先进冶炼工艺及 相关的技术。 3.设计主要经济技术指标: 一座高炉有效容积1800M3、 利用系数2.38吨铁/M3h 焦比≤340kg/TFe、煤比180 kg/TFe、 炉顶压力0.2MPa、热风温度1200℃、 渣比≤360 kg/TFe、入炉品位≥57%、 年产铁量150万吨、年产水渣62万吨(含水率15%)
设 备 参 数 及 要 求
槽体宽度(mm) 电机功率 振动频率(r/min) 安装方式
振动源
间断连续工作 工作电压
振动电机
间断性 380V
振动电机
间断性 380V
振动电机
间断性 380V
振动电机
间断性 380V
槽上大小皮带10条 槽下上料主皮带:B=1400 mm、v=2m/s,矿=2100 t/h、焦=550t/h、 L=368m 槽下供料GJ1皮带:B=1400 mm、v=2m/s,矿=2100 t/h、焦=550t/h、 a=80 L =171m 槽上皮带都是B=1200 mm、v=2m/s,烧结矿=800 t/h、球团矿=1200 t/h、焦=300t/h 皮带长短不同电机功率不同(37×2)(45×4)(160×2) (185×1)(75×1) 槽上从槽前转运站,来三条皮带,分别为焦、矿、球、块矿。 焦炭:可从焦化直付或通过原料厂皮带外进。 烧结来料:成品槽来料或原料厂外进。 球团:现阶段原料厂外进。 块矿:原料厂外进。 矿槽布置:14个槽一列布置,有效容积415M3,矿3600 t/15h、焦 830 t/12h、球2700 t/29h、杂1900 t/h 槽上1高炉,8条,槽下反焦、矿5条,主供料皮带各一条,总计15条。
炉顶部分:
吉林钢铁高炉炉顶为串罐式无钟装置,串罐与并罐的 优缺点: 上罐有旋转和不转,上罐入口分料板,下罐内有上密上料 闸,一次均压二次均压,二次均压高于炉内 0.001~0.002MPa,均压放散,下罐下面连接阀箱,眼睛阀, 齿轮阀。阀箱内下密、下料闸、料流调节。
无料钟炉顶均压制度两种:
正常工作制度,料线到后一均——开二均——开下密—— 开料流调节阀——空点来后——关料流调节阀—— 关下密同时关二均——开放散——开上密——开上料闸漏斗 ——漏完料关上料闸——关上密及均压放散——开一均 除往炉内布料外,下罐总是不充压,即料线到来后关放 散阀,开一均。 高压操作顶压大于0.03MPa的叫高压操作。 提高炉顶压力降焦、提高0.01MPa, 炉喉煤气速度降低5.6%,从而发展高炉边缘煤气流。
提高煤气利用率:①增加煤气停留时间
②有利下料有利顺行 ③减少除尘量
料线: 炉喉钢砖上沿为料线0米。正常料线1~2.5米。 料线越降低越加重边缘。无料钟炉顶溜槽可调节下料流的抛物线角度, 可以自动调节,4米以内影响不大。 下料旋转溜槽:分定点、单环、多环旋转布料。每批料分11圈布料。 γ角以12~50度旋转启动角度为60度步进,可反正转,正常为多环布料。 有问题时可单环38度同大钟角度相同布料。
四、炉前出渣铁系统:渣铁处理、铁水运输、铸铁机
炉渣可用为水渣、干渣。 干渣:可用干渣坑和放渣罐 水渣:可用水渣池,高炉直接冲渣,冲渣可冲渣池,因芭渣、嘉恒渣、 拉萨渣、轮法渣粒化装置,就是嘉桓渣。 嘉恒渣:1.炉渣粒化,粒化器125~1250转/min。2.脱水,随着脱水器旋 转,筛网中的渣渣缓慢上升达到顶部时翻落下来进入受料斗,斗斜面出 口落到皮带机。 因芭渣:转鼓脱水,皮带在转鼓中。 炉前出铁采用液压矮式泥炮及全液压开口机。开口机最大开口深度 3.4m,钻头直径50~65mm,铁口角度10±5℃,摆动流槽,电动主铁钩为半 贮铁式固定主沟。 吉林钢铁高炉,一台套嘉恒渣处理,日处理最大1680吨/日、最大渣 量8吨/min、峰值10吨/min。皮带B=1200mm、V=2m、输送能力=700t/h, 提升高度22米、长度=385米。3台粒化供水泵(两用一备),循环水量 2400m3/h,补水量180m3/h,干渣坑循环水量400m3/h,补水量100m3/h。
吉林钢铁高炉工艺流程简介
吉林建龙钢铁设计建两座1800M3高炉, 其主要工艺设备从原料起分为;皮带上 料,无料钟串罐炉顶。高炉冷却用全软水 闭路循环,复合炉底。炉前用液压矮炮、 全液压开口机、摆动溜槽、鱼雷罐受铁等 先进工艺设备。
1#转运站(分级筛)
槽前转运站
运外
煤气放散塔
运外 调压阀组
重力除尘器 焦矿槽 粉(焦矿筛分) 炉顶装料
生产实践中,高炉炼铁是一项非常复杂的系统工程, 整个冶炼过程可变因素多,物理、化学反应基本上看不见、 摸不着。高炉操作者要根据原燃料变化去调节冶炼过程中 的热量平衡、碱度平衡。调节方法多为原燃料装入顺序、 装入方法、配比及风量、风温、喷煤量、氧气等手段去完 成整个冶炼过程。 高炉冶炼主要就是一个氧化还原的过程,还原剂主要有三 种:CO、H2和固体C,试验证明,无论是何种还原剂,还原 铁氧化物,都是由高级向低级氧化物逐级变化,并以570℃ 为界。 >570℃ Fe2O3 → Fe3O4 → FeO → Fe <570℃ Fe2O3 → Fe3O4 → Fe 高炉内H2的还原能力在高于810℃时大于CO的还原能力, 高炉内H2的主要来源是风口喷吹燃料中的碳氢化合物分解、 焦炭中有机氢和鼓风湿分分解产生的。
Y132S-6 2×3KW
坐式 激振器 间断性 380V
Y132M2-6 2×5.5KW
坐式 激振器 间断性 380V