列管式换热器
列管式换热器原理

列管式换热器原理列管式换热器是一种常见的换热设备,它通过管道内的流体与外部介质的热交换来实现热量的传递。
在工业生产和生活中,列管式换热器被广泛应用于加热、冷却和热回收等领域。
本文将介绍列管式换热器的原理及其工作过程。
列管式换热器的原理基本上是利用了流体在管道内的流动和外部介质之间的热传导来实现热量的传递。
在列管式换热器中,流体通过管道流动,而外部介质则围绕着管道进行热交换。
当流体在管道内流动时,它会与管壁接触,通过管壁与外部介质进行热交换,从而实现热量的传递。
列管式换热器通常由管束、管板、壳体和管束固定装置等部件组成。
管束是由许多管子组成的,它们通常是平行排列的,形成了一个整体。
管板则用于固定管束,使其保持在一定的位置。
壳体则是管束和管板的外部保护结构,起到保护和支撑的作用。
而管束固定装置则用于固定管束,防止在使用过程中发生移动或振动。
列管式换热器的工作过程通常分为两个流体之间的热交换。
当热流体进入换热器时,它会通过管道流动,并与管道内的冷流体进行热交换。
在这个过程中,热流体会释放热量,使得冷流体温度升高。
而热流体则会冷却下来,完成了热量的传递。
这样,通过不同流体之间的热交换,实现了热能的传递和利用。
列管式换热器的原理简单清晰,工作效率高,因此在工业生产和生活中得到了广泛的应用。
它不仅可以用于加热和冷却,还可以用于热回收和能量利用。
在化工、电力、食品等行业中,列管式换热器都扮演着重要的角色,为生产和生活提供了便利。
总的来说,列管式换热器的原理是基于流体之间的热交换,通过管道内的流动和管壁与外部介质之间的热传导来实现热量的传递。
它的工作过程简单高效,被广泛应用于工业生产和生活中。
随着科技的不断进步,列管式换热器的性能和效率将会得到进一步提升,为人们的生产和生活带来更多的便利和效益。
列管式换热器原理

列管式换热器原理
列管式换热器是一种常见的热交换设备,它通过管道内的流体与管外的流体进行热交换,广泛应用于化工、电力、石油、制药等领域。
本文将介绍列管式换热器的原理及其工作过程。
首先,列管式换热器的原理是基于热传导和对流传热的基本原理。
当两种不同温度的流体通过换热器内外的管道时,热量会通过管壁传导到另一种流体中,从而使两种流体的温度发生变化,实现热量的传递。
其次,列管式换热器的工作过程可以分为对流传热和传导传热两个阶段。
在对流传热阶段,流体在管内外表面形成对流层,通过对流传热来实现热量的传递;而在传导传热阶段,热量则通过管壁的传导来传递到另一种流体中。
列管式换热器的设计和选型需要考虑多种因素,包括流体的性质、流量、温度、压力等参数。
在实际应用中,需要根据具体的工艺要求和环境条件来选择合适的换热器型号和材质,以确保其正常运行和长期稳定性。
此外,列管式换热器的热效率也是一个重要的考量因素。
通过合理的设计和优化换热器结构,可以提高换热器的热效率,降低能耗,从而达到节能减排的目的。
总的来说,列管式换热器是一种高效、可靠的热交换设备,其原理和工作过程相对简单清晰,但在实际应用中需要综合考虑多种因素,以确保其正常运行并发挥最佳的换热效果。
希望本文能对您对列管式换热器有一个更深入的了解。
列管式换热器的传热效率

列管式换热器的传热效率引言换热器作为热工学中的重要设备,广泛应用于许多领域中,其中列管式换热器是常见的一种类型。
本文将重点讨论列管式换热器的传热效率,并着重探讨其中的关键因素。
1.列管式换热器概述列管式换热器是一种将两个流体通过一系列管道进行热交换的设备。
其基本原理是利用管道中的流体与外部流体接触,通过传导、对流和辐射等方式,实现热量的传递。
列管式换热器通常由管束和外壳两部分组成,其中管束中的管道为热交换的主要区域。
2.传热效率的定义传热效率是指换热器实际传递的热量与理论上最大可能传递的热量之比。
传热效率一般用ϵ表示,其计算公式如下:ϵ=(Q实际传递的热量)/(Q理论上最大可能传递的热量)3.影响传热效率的因素3.1温度差温度差是影响传热效率的重要因素之一。
传热速率与温度差成正比,当温度差增大时,传热速率也随之增加,从而提高传热效率。
3.2流体性质流体的性质,如热导率、比热容等,对传热效率也有显著影响。
热导率越大、比热容越小的流体,其传热效率通常较高。
3.3流体流速流体流速是影响传热效率的关键因素之一。
较高的流速可以增加传热面与流体的接触频率,提高传热效率。
3.4换热面积换热面积是列管式换热器传热效率的重要影响因素。
换热面积越大,传热面与流体的接触面积就越大,传热效率也就提高。
3.5温差分布温差分布是影响传热效率的难点之一。
由于流体在管道内的流速和温度分布不均匀,导致热量无法完全传递,从而影响传热效率。
4.提高传热效率的方法4.1优化设计在列管式换热器的设计过程中,可以通过合理选择换热面积、优化管道布局等方式,提高传热效率。
4.2流体流速控制通过控制流体的流速,可以增加传热面与流体的接触频率,提高传热效率。
4.3温度分布均匀合理调整流体流速和温度分布,可以减小温差分布,提高传热效率。
4.4清洁维护定期对列管式换热器进行清洗和维护,保持换热面的清洁,可以减少污垢对传热的影响,提高传热效率。
结论通过对列管式换热器的传热效率进行分析,我们可以得出以下结论:传热效率受多个因素的共同影响,包括温度差、流体性质、流体流速、换热面积和温差分布等。
化工设备课件列管式换热器PPT课件

材料选择
高温材料
对于高温工况,选择耐高温、抗氧化、抗腐 蚀的材料,如不锈钢、镍基合金等。
腐蚀性介质
对于腐蚀性介质,选择耐腐蚀、防腐蚀的材 料,如钛合金、聚四氟乙烯等。
低温材料
对于低温工况,选择耐低温、抗脆化的材料, 如铝合金、铜合金等。
压力容器材料
根据压力需求,选择具有足够强度和稳定性 的材料,如碳钢、低合金钢等。
建立设备维修与保养记录,便于追踪设备运行状况和及时发现潜在问题。
05
列管式换热器的故障诊断与处理
常见故障及原因
列管堵塞
由于列管内壁结垢、腐蚀或异物堵塞 等原因,导致传热效率下降。
列管破裂
由于列管材质缺陷、焊接质量差或使 用过程中受到过大的压力或温度波动, 导致列管破裂。
热效率低
由于传热面积不足、传热介质流量不 足或传热温差过小等原因,导致换热 器热效率低下。
特点
结构紧凑、传热效率高、适应性 强、操作定、可处理高热量和 腐蚀性介质等。
工作原理
01
热流体通过列管内部,被加热或 冷却的流体在列管外部流动,通 过列管壁进行热量交换。
02
热量通过列管壁从热流体传递到 被加热或冷却的流体,实现热量 交换。
类型与结构
固定管板式
管板与壳体焊接在一起,结构 简单,适用于壳程压力不高、
03
列管式换热器设计
设计参数
传热面积
根据工艺要求,计算所需的传热面积,确保 热量交换的效率和效果。
传热效率
选择合适的传热方式,如导热、对流、辐射 等,以提高传热效率。
压力等级
根据工艺压力需求,选择合适的压力等级和 耐压材料,确保设备安全。
温度范围
根据工艺温度需求,选择耐温材料和结构, 确保设备在规定的温度范围内工作。
列管式换热器原理

列管式换热器原理
列管式换热器是一种常见的热交换设备,其主要原理是通过流体在管
内和管外之间传递热量,实现两种介质之间的热能转移。
该设备通常
由多个管子组成,每个管子内部都有一条螺旋形或直线形的金属导管,导管内部通常充满了冷却液或者加热液等介质。
当需要进行换热时,将需要加热或者冷却的流体通过导管内部流动,
同时将另一种介质通过导管外部流动。
由于两种介质之间存在温度差
异和压力差异,因此会产生自然对流或强制对流的效应,在这个过程中,两种介质之间会进行热能交换。
在列管式换热器中,导管内部和外部的介质可以是气体、水、蒸汽等。
同时,在不同的应用场景下,可以采用不同材料制造导管和壳体。
例如,在化工行业中,通常使用耐腐蚀性能较好的不锈钢材料来制造列
管式换热器。
列管式换热器具有许多优点。
首先,它可以实现高效的热能转移,从
而节约能源。
其次,该设备结构紧凑,占用空间较小,易于安装和维护。
此外,在不同的介质之间进行换热时,可以实现相对较高的温度
控制精度。
然而,在使用列管式换热器时也需要注意一些问题。
首先,由于该设
备内部存在许多导管和壳体等组件,因此容易产生阻塞和污垢等问题。
如果不及时清洗和维护,则可能会影响设备的正常运行。
其次,在使
用不同介质进行换热时需要注意介质之间的兼容性问题,避免产生化
学反应或者腐蚀等情况。
总之,列管式换热器是一种高效、紧凑、易于安装和维护的热交换设备。
它通过流体在管内和管外之间传递热量的方式实现两种介质之间
的热能转移,并在许多工业领域中得到广泛应用。
列管式换热器的工作原理

列管式换热器的工作原理
列管式换热器工作原理:
列管式换热器是一种常见的换热设备,通过在列管内流动的两种不同温度的流体之间进行热传递。
它由一组管子(通常为圆柱形)组成,这些管子被安装在一个容器内。
其中一个流体进入管子(通常称为管束)的一侧,另一个流体则从管子的外部流过。
两个流体之间的热传递是通过管子的壁面完成的。
列管式换热器的工作原理可以分为平行流和逆流两种情况:
1. 平行流:在平行流情况下,两个流体的流动方向是相同的,即它们在整个换热器中的流动方向都是一致的。
这种情况下,热量从热源流体通过管壁传递给冷源流体。
由于两个流体之间有较大的温度差异,热量可以通过管壁迅速传递,使得冷源流体的温度迅速升高,而热源流体的温度迅速降低。
2. 逆流:在逆流情况下,两个流体的流动方向相反,即它们分别从两个不同的端口进入换热器,并在另一端口排出。
这种情况下,热量从热源流体通过管壁传递给冷源流体,同时也有部分热量从冷源流体传递给热源流体。
逆流情况下,热量传递效率较高,因为两个流体在整个换热器中都以最大的温差进行热传递。
无论是平行流还是逆流,列管式换热器通过增大交换管的数量和表面积,增加热交换效果。
此外,还可以通过改变流体的流
速、调整管束的排列方式等方式来优化列管式换热器的工作性能。
列管式换热器结构特点

列管式换热器结构特点以下是 8 条关于列管式换热器结构特点的内容:1. 列管式换热器那管子可真是密密麻麻的呀,就像一片管子的森林!你想想看,在工厂里,它就像个勤劳的小蜜蜂,默默地工作着,让热交换高效进行。
比如化工厂里,各种液体就在这些管子里穿梭,进行着温度的传递呢!2. 它的结构紧凑啊,简直就是个空间利用大师!不占多少地方,却能发挥大作用。
这不就像一个小巧玲珑的魔法师,能在小小的地方变出大大的奇迹嘛!像在一些空间有限的车间,它就能很好地施展自己的本领。
3. 列管式换热器的管束,那可是它的核心力量啊!就如同勇敢的战士在战斗中冲锋陷阵一样。
你看,热水和冷水在管束里交汇,实现热量的转移,多厉害呀!比如说空调系统里,它就让我们能享受舒适的温度呢!4. 它的坚固耐用特性真的超棒!感觉就像一个坚强的堡垒,风吹雨打都不怕。
就算长时间工作,也不会轻易出问题。
就像家里的老冰箱,用了好多年依然可靠,这列管式换热器也是这样可靠啊!5. 列管式换热器的换热效率很高哇,这可太重要了!简直可以比作是速度超快的赛车,一下子就冲到终点。
在能源利用方面,它真的是一把好手。
像热电厂里,它为发电提供了高效的支持呢!6. 它的适应性很强啊,不管啥样的环境都能应对自如!这不就是个全能选手嘛!无论是高温还是低温,它都能稳稳当当工作。
就好比运动员无论在啥场地都能发挥出色一样。
7. 列管式换热器那设计多巧妙呀,每个部分都配合得那么好!就像一个完美的团队,成员们各司其职,共同完成任务。
想想看在工业生产中,它默默地为生产的顺利进行贡献力量,多了不起啊!8. 它的维护也相对简单呢,不像有些设备那样麻烦!这多贴心呀!就像养了一只好照顾的宠物,不用太费心。
在实际使用中,只要定期看看,就能保证它正常工作啦。
总之,列管式换热器真的是工业领域中不可或缺的重要设备呀!。
列管式换热器原理
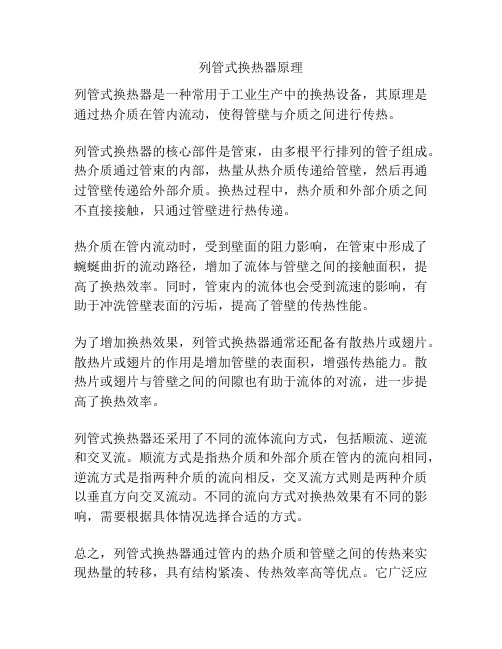
列管式换热器原理
列管式换热器是一种常用于工业生产中的换热设备,其原理是通过热介质在管内流动,使得管壁与介质之间进行传热。
列管式换热器的核心部件是管束,由多根平行排列的管子组成。
热介质通过管束的内部,热量从热介质传递给管壁,然后再通过管壁传递给外部介质。
换热过程中,热介质和外部介质之间不直接接触,只通过管壁进行热传递。
热介质在管内流动时,受到壁面的阻力影响,在管束中形成了蜿蜒曲折的流动路径,增加了流体与管壁之间的接触面积,提高了换热效率。
同时,管束内的流体也会受到流速的影响,有助于冲洗管壁表面的污垢,提高了管壁的传热性能。
为了增加换热效果,列管式换热器通常还配备有散热片或翅片。
散热片或翅片的作用是增加管壁的表面积,增强传热能力。
散热片或翅片与管壁之间的间隙也有助于流体的对流,进一步提高了换热效率。
列管式换热器还采用了不同的流体流向方式,包括顺流、逆流和交叉流。
顺流方式是指热介质和外部介质在管内的流向相同,逆流方式是指两种介质的流向相反,交叉流方式则是两种介质以垂直方向交叉流动。
不同的流向方式对换热效果有不同的影响,需要根据具体情况选择合适的方式。
总之,列管式换热器通过管内的热介质和管壁之间的传热来实现热量的转移,具有结构紧凑、传热效率高等优点。
它广泛应
用于石化、化工、制药等行业,在工业生产中发挥着重要的作用。
列管式换热器

列管式换热器列管式换热器是一种常见的换热设备,通常用于多种工业领域,如化工、石油、电力、制药等。
它的工作原理是通过将一个或多个管道(称为管子)插入一个外壳中,并使热交换流体通过管子和壳体之间流动,以实现热量的传递。
设计举例:化工厂中的列管式换热器。
工艺要求:1.热源介质为低温烟气(300℃,2000Nm³/h)。
2.冷却介质为水(20℃,1000L/h)。
3.需要达到的换热效果:烟气温度降低到200℃以下。
设计步骤:1.确定换热面积:根据热负荷计算,烟气的热负荷(Q)为:Q = mcΔT其中,m为烟气质量流量,c为烟气比热容,ΔT为烟气温度差。
在本例中,m为2000Nm³/h,c取1000J/(kg·℃),ΔT为300℃。
另外,换热器的换热系数(U)可以根据实际情况选择一个合适的数值。
假设U为1000W/(m²·℃)。
根据换热方程,换热面积(A)可由以下公式计算:Q = UAΔTlm其中,ΔTlm为对数平均温差,可根据进出口温度计算得到。
综上所述,可以计算得到所需的换热面积。
2.确定管子数量和布局:根据换热面积和设计要求,可以确定所需管子的数量和布局。
通常情况下,管子的数量选择为偶数,并且可以采用等间距布置。
3.材料选择:根据介质的性质和工艺要求,选择合适的材料用于制作管子和壳体。
常用的材料有不锈钢、镍合金、铜等。
4.热力设计:根据所需传热量、管子数量和进出口温度等参数,计算出每根管子的传热量。
同时,根据流体的流动参数,确定管子的直径和管道内流速。
一般情况下,可以保持流速在1-3m/s之间。
5.结构设计:根据换热器的实际需求和工艺要求,设计并确定壳体内部的分隔板、支撑杆等结构。
这些结构可以增强换热效果和传热效率,并帮助流体均匀分布。
6.安全设计:在列管式换热器的设计中,需要考虑各种安全因素,如压力、温度和泄漏等。
可以通过安全阀、温度控制器和泄漏检测器等装置来保障设备的安全运行。
什么是列管式换热器

什么是列管式换热器?列管式换热器主要由壳体、管束、管板(又称花板)和顶盖(又称封头)等部件构成。
管束安装在壳体内,两端用胀接或焊接方式固定在管板上,两种流体分别流经管内外进行换热。
水流经管内的称为管程水冷却器,流经管外的称壳程水冷却器。
为提高流体的流速常在壳程设折流挡板。
常用挡板有两种:圆缺形(也称弓形)和交替排列的环形及圆盘形。
目前广泛使用的列管式换热器主要有以下几种。
(1)固定管板列管式换热器见图5-1-17及图5-1-18。
两端管板是和壳体连为一体的。
其特点是结构简单,适用于管内外温差小、管外物料较清洁、不易结垢的情况。
管内外温差大于50℃时,因壳体和管束的热膨胀程度不同,可能将管子拉弯或拉松,损坏换热器。
这时如壳体承受压力不太高,则可采用在壳体上具有补偿圈(或称膨胀节)的固定管板式换热器。
管内流体通过一程管束就流出的称单程换热器,如图5-1-17。
有时为提高管内流体的流速,可设计成双程、四程或六程换热器。
如图5-1-18为双程换热器,流体通过第一程后,再折回,流过第二程管束后才流出。
(2)浮头列管式换热器见图5-1-19。
该种换热器一端的管板不与壳体相连,便于自由伸缩。
适用于管内外温差较大、需常拆卸清洗的情况。
其结构较复杂。
(3)U形列管式换热器见图5-1-20。
该种换热器只有一端设管板,U形管的两端分别装在管板两侧,封头用隔板隔成两室,管子可以自由伸缩。
其结构比浮头式简单,化工厂中常见。
列管式水冷却器几乎是最常见的型式。
与前几种型式相比,其单位体积所能提供的传热面积要大得多,传热效率高,结构紧凑、坚固、能选用多种材质,可以用于高温、高压的大型装置。
列管式换热器的结构
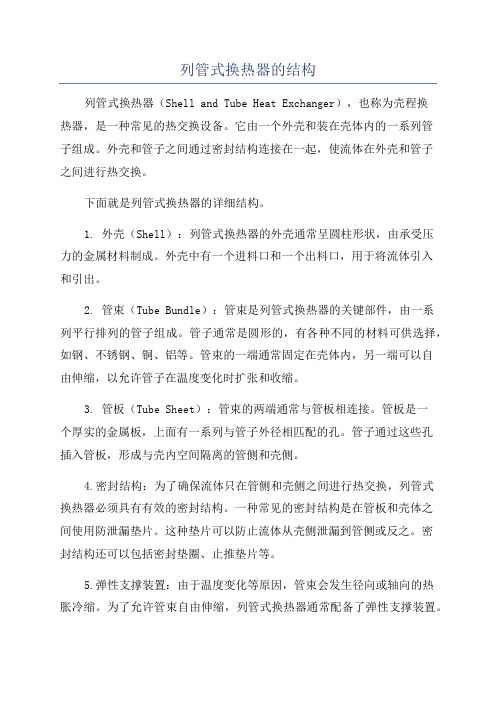
列管式换热器的结构列管式换热器(Shell and Tube Heat Exchanger),也称为壳程换热器,是一种常见的热交换设备。
它由一个外壳和装在壳体内的一系列管子组成。
外壳和管子之间通过密封结构连接在一起,使流体在外壳和管子之间进行热交换。
下面就是列管式换热器的详细结构。
1. 外壳(Shell):列管式换热器的外壳通常呈圆柱形状,由承受压力的金属材料制成。
外壳中有一个进料口和一个出料口,用于将流体引入和引出。
2. 管束(Tube Bundle):管束是列管式换热器的关键部件,由一系列平行排列的管子组成。
管子通常是圆形的,有各种不同的材料可供选择,如钢、不锈钢、铜、铝等。
管束的一端通常固定在壳体内,另一端可以自由伸缩,以允许管子在温度变化时扩张和收缩。
3. 管板(Tube Sheet):管束的两端通常与管板相连接。
管板是一个厚实的金属板,上面有一系列与管子外径相匹配的孔。
管子通过这些孔插入管板,形成与壳内空间隔离的管侧和壳侧。
4.密封结构:为了确保流体只在管侧和壳侧之间进行热交换,列管式换热器必须具有有效的密封结构。
一种常见的密封结构是在管板和壳体之间使用防泄漏垫片。
这种垫片可以防止流体从壳侧泄漏到管侧或反之。
密封结构还可以包括密封垫圈、止推垫片等。
5.弹性支撑装置:由于温度变化等原因,管束会发生径向或轴向的热胀冷缩。
为了允许管束自由伸缩,列管式换热器通常配备了弹性支撑装置。
这些装置可以是弹簧、法兰或其他形式的支撑装置,以保证管束在应力范围内自由伸缩。
6.管侧流体通道:当流体通过管侧流通时,流体会在管子内部进行热交换。
管侧流体通道由一系列管子组成,管子通常是平行排列的。
流体进入管侧流道后,在管子内部形成一种交叉流或平行流形式,与壳侧的流体进行热交换。
7.壳侧流体通道:当流体通过壳侧流通时,流体会在管束外部进行热交换。
壳侧流体通道由管束外壳内的空间组成,流体在该空间内流动。
壳侧流体可以是单相流体,也可以是多相流体(如汽液两相流),流体通常以横向或纵向的方式流动。
列管式换热器
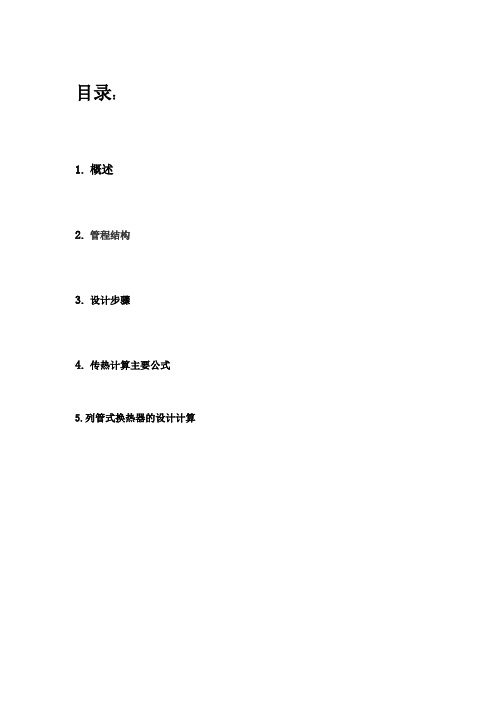
目录:1.概述2.管程结构3.设计步骤4.传热计算主要公式5.列管式换热器的设计计算【概述】换热器是将热流体的部分热量传递给冷流体的设备,又称热交换器。
英语翻译:heat exchanger换热器是实现化工生产过程中热量交换和传递不可缺少的设备。
在热量交换中常有一些腐蚀性、氧化性很强的物料,因此,要求制造换热器的材料具有抗强腐蚀性能。
换热器的分类比较广泛:反应釜压力容器冷凝器反应锅螺旋板式换热器波纹管换热器列管换热器板式换热器螺旋板换热器管壳式换热器容积式换热器浮头式换热器管式换热器热管换热器汽水换热器换热机组石墨换热器空气换热器钛换热器换热设备,要求制造换热器的材料具有抗强腐蚀性能。
它可以用石墨、陶瓷、玻璃等非金属材料以及不锈钢、钛、钽、锆等金属材料制成。
但是用石墨、陶瓷、玻璃等材料制成的有易碎、体积大、导热差等缺点,用钛、钽、锆等稀有金属制成的换热器价格过于昂贵,不锈钢则难耐许多腐蚀性介质,并产生晶间腐蚀。
在石油、化工、轻工、制药、能源等工业生产中,常常需要把低温流体加热或者把高温流体冷却,把液体汽化成蒸汽或者把蒸汽冷凝成液体。
这些过程均和热量传递有着密切联系,因而均可以通过换热器来完成。
随着经济的发展,各种不同型式和种类的换热器发展很快,新结构、新材料的换热器不断涌现。
为了适应发展的需要,我国对某些种类的换热器已经建立了标准,形成了系列。
完善的换热器在设计或选型时应满足以下基本要求:(1)合理地实现所规定的工艺条件;(2)结构安全可靠;(3)便于制造、安装、操作和维修;(4)经济上合理。
换热器不得在超过铭牌规定的条件下运行。
应经常对管,壳程介质的温度及压降进行监督,分析换热管的泄漏和结垢情况。
管壳式换热器就是利用管子使其内外的物料进行热交换、冷却、冷凝、加热及蒸发等过程,与其他设备相比较,其余腐蚀介质接触的表面积就显得非常大,发生腐蚀穿孔结合处松弛泄漏的危险性很高,因此对换热器的防腐蚀和防泄漏的方法也比其他设备要多加考虑,当换热器用蒸汽来加热或用水来冷却时,水中的溶解物在加热后,大部分溶解度都会有所提高,而硫酸钙类型的物质则几乎没有变化。
列管式换热器的计算

列管式换热器的计算列管式换热器是一种常见的热交换设备,用于将热量从一个流体传递给另一个流体。
它由一组管子和外壳组成,热量通过管壁传递。
在设计或计算列管式换热器时,需要考虑各种参数和因素。
下面将详细介绍列管式换热器的计算方法。
首先,需要确定列管式换热器的传热面积。
传热面积影响热量传递的效率,可以通过以下公式计算:A=n×π×D×L其中:A表示传热面积(m2)n表示管子数量D表示管子外径(m)L表示管子长度(m)然后,需要计算每个管子的传热系数。
传热系数表示单位面积上的传热量,可以通过以下公式计算:U=(1/(1/h_i+δ_i/k_i+1/h_o))其中:U表示总传热系数(W/(m2·K))h_i表示内壁对流传热系数(W/(m2·K))δ_i表示管壁导热系数(W/(m·K))k_i表示管壁导热系数(W/(m·K))h_o表示外壁对流传热系数(W/(m2·K))对流传热系数可以通过经验公式、实验或计算获得。
管壁导热系数可以根据管材的材料及厚度获得。
接下来,需要计算传热器的热负荷。
热负荷表示单位时间内流体传递的热量,可以通过以下公式计算:Q=m×Cp×ΔT其中:Q表示热负荷(W)m 表示流体的质量流量(kg/s)Cp 表示流体的定压比热容(J / (kg·K))ΔT表示流体进出口温度的温差(K)最后,需要计算传热器的温度差。
温度差表示流体进出口温度之间的差距,可以通过以下公式计算:ΔT = (T_i - T_o) / ln(T_i / T_o)其中:ΔT表示温度差(K)T_i表示进口温度(K)T_o表示出口温度(K)根据以上公式,可以计算出列管式换热器的传热面积、传热系数、热负荷和温度差。
这些参数和结果对于合理设计和选择列管式换热器非常重要。
列管式换热器原理

列管式换热器原理列管式换热器是一种常见的换热设备,它通过管道内流体的传热来实现热量的交换。
其原理主要包括传热传质原理和换热器的结构原理。
首先,我们来看传热传质原理。
列管式换热器的传热传质原理是基于热量的传导、对流和辐射三种方式。
在换热器中,热源和冷却介质通过管道内流动,热源的热量通过管壁传导给冷却介质,同时在管道内部也会发生对流传热。
此外,还会有一部分热量通过辐射的方式传递。
这些传热方式共同作用,实现了热量的传递和交换。
其次,我们来看换热器的结构原理。
列管式换热器通常由管束、管板、壳体、支撑、密封件等部件组成。
管束是换热器中最重要的部件,它由多根管子组成,管子之间通过管板连接固定。
壳体是管束的外部保护结构,用于固定管束和冷却介质的流动。
支撑和密封件则起到固定和密封的作用,确保换热器的正常运行。
在列管式换热器的工作过程中,热源和冷却介质分别经过管道内流动,热源的热量通过管壁传导给冷却介质,同时在管道内部也会发生对流传热。
冷却介质吸收热源的热量后,温度升高,然后流出换热器,而热源则失去热量,温度下降,流出换热器。
通过这样的热量交换过程,实现了热源和冷却介质之间的热量传递和温度调节。
列管式换热器广泛应用于化工、石油、电力、冶金、食品等工业领域,其原理简单、结构紧凑、传热效果好,因此受到了广泛的青睐。
在实际应用中,我们需要根据具体的工艺要求和介质特性选择合适的列管式换热器,同时合理设计和运行换热器,确保其安全、高效地运行。
总之,列管式换热器的原理主要包括传热传质原理和换热器的结构原理,通过管道内流体的传热来实现热量的交换。
在实际应用中,我们需要充分理解其工作原理,合理选择和设计换热器,确保其安全、高效地运行,为工业生产提供可靠的热能支持。
列管式换热器计算

列管式换热器计算列管式换热器(shell and tube heat exchanger)是广泛应用于工业生产过程中的一种热能传递设备。
它主要由壳体、管束和传热介质组成,通过将两个介质分别流经壳体和管束,实现热能传递的目的。
在进行列管式换热器的计算之前,需要了解一些基本的参数和公式。
1.热传导功率计算公式:热传导功率(Q)可以通过以下公式计算:Q=U×A×ΔTm其中,U为传热系数(W/(m²·K)),A为传热面积(m²),ΔTm为平均温差(K)。
2.传热系数的计算:传热系数的计算是列管式换热器计算中的关键步骤。
传热系数(U)可以通过以下公式计算:1/U = 1/hi + Σ(δ/ki) + 1/ho其中,hi为管内传热系数(W/(m²·K)),δ为管壁厚度(m),ki为管材的导热系数(W/(m·K)),ho为壳体侧传热系数(W/(m²·K))。
3.管内传热系数的计算:管内传热系数(hi)可以通过经验公式获得。
常用的经验公式有Dittus-Boelter公式和Sieder-Tate公式。
4.壳体侧传热系数的计算:壳体侧传热系数(ho)通常需要经验或试验数据来确定,也可以通过计算软件进行估算。
5.平均温差的计算:平均温差(ΔTm)可以通过以下公式计算:ΔTm = (Ts – Tf) / ln((Ts – Tf) / (Tg – Tf))其中,Ts为传出介质的温度(K),Tf为传入介质的温度(K),Tg为壳体侧介质的温度(K)。
通过以上的基本参数和公式,可以进行列管式换热器的计算。
首先,需要确定换热器的设计要求和工艺参数,例如需求的传热功率、传入介质和传出介质的温度、壳体侧介质的温度等。
其次,选择适当的管材和壳体材料,确定管径、管程数和管束类型。
根据设计要求,计算所需的传热面积,并选择管程数和管长。
然后,通过管内传热系数的计算公式,确定管内传热系数。
化工原理课程设计列管式换热器

可用旳场合:
1)管程走清洁流体;
2)管程压力尤其高;
3)管壳程金属温差很大,固定管板换热器连设置膨胀节都无法 满足要求旳场合.
2、流动空间旳选择
3、流速旳拟定
4、流动方式旳选择
除逆流和并流之外,在列管式换热器中冷、 热流体还能够作多种多管程多壳程旳复杂 流动。当流量一定时,管程或壳程越多, 表面传热系数越大,对传热过程越有利。 但是,采用多管程或多壳程必造成流体阻 力损失,即输送流体旳动力费用增长。所 以,在决定换热器旳程数时,需权衡传热 和流体输送两方面旳损失。
5、流体出口温度旳拟定
若换热器中冷、热流体旳温度都由工艺条件所要求,则不存在 拟定流体两端温度旳问题。若其中一流体仅已知进口温度,则 出口温度应由设计者来拟定。例如用冷水冷却一热流体,冷水 旳进口温度可根据本地旳气温条件作出估计,而其出口温度则 可根据经济核实来拟定:为了节省冷水量,可使出口温度提升 某些,但是传热面积就需要增长;为了减小传热面积,则需要 增长冷水量。两者是相互矛盾旳。一般来说,水源丰富旳地域 选用较小旳温差,缺水地域选用较大旳温差。但是,工业冷却 用水旳出口温度一般不宜高于45℃,因为工业用水中所含旳部 分盐类(如CaCO3、CaSO4、 MgCO3和MgSO4等)旳溶解度 随温度升高而减小,如出口温度过高,盐类析出,将形成传热 性能很差旳污垢,而使传热过程恶化。假如是用加热介质加热 冷流体,可按一样旳原则选择加热介质旳出口温度。
取管长应根据出厂旳钢管长度合理截用。 我国生产系列原则中管长有1.5m,2m, 3m,4.5m,6m和9m六种,其中以3m和 6m更为普遍。同步,管子旳长度又应与管 径相适应,一般管长与管径之比,即L/D约 为4~6
列管式换热器原理

列管式换热器原理
列管式换热器是一种常见的换热设备,它通过管道内的流体与外部介质进行热
量交换,实现了能量的传递。
其原理主要包括传热方式、传热系数和传热面积等方面。
下面将详细介绍列管式换热器的原理。
首先,列管式换热器的传热方式主要有对流传热和传导传热两种。
对流传热是
通过流体在管内外的对流运动,将热量从热源传递到冷却介质。
而传导传热则是通过管壁的传导作用,将热量从管内传递到管外,再通过对流传热的方式传递给介质。
这两种传热方式共同作用,使得列管式换热器能够高效地完成热量交换。
其次,传热系数是影响列管式换热器传热效果的重要因素之一。
传热系数取决
于流体的性质、流速、管道材质等因素。
流体的性质包括其导热系数、黏度等,流速则决定了流体与管壁之间的传热程度,而管道材质的热导率则直接影响了传热效果。
通过合理选择流体和管道材质,可以有效提高传热系数,从而提高列管式换热器的传热效率。
最后,传热面积也是影响列管式换热器传热效果的关键因素之一。
传热面积越大,热量交换的效率就越高。
因此,在设计列管式换热器时,需要充分考虑传热面积的大小和布局方式,以确保热量能够充分交换。
总的来说,列管式换热器的原理主要包括传热方式、传热系数和传热面积三个
方面。
通过合理设计和选择,可以提高列管式换热器的传热效率,满足不同工况下的换热需求。
希望本文对您理解列管式换热器的原理有所帮助。
列管式换热器工作原理
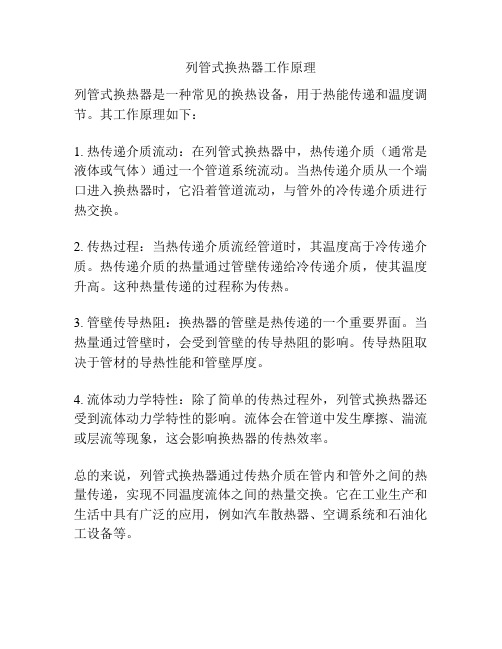
列管式换热器工作原理
列管式换热器是一种常见的换热设备,用于热能传递和温度调节。
其工作原理如下:
1. 热传递介质流动:在列管式换热器中,热传递介质(通常是液体或气体)通过一个管道系统流动。
当热传递介质从一个端口进入换热器时,它沿着管道流动,与管外的冷传递介质进行热交换。
2. 传热过程:当热传递介质流经管道时,其温度高于冷传递介质。
热传递介质的热量通过管壁传递给冷传递介质,使其温度升高。
这种热量传递的过程称为传热。
3. 管壁传导热阻:换热器的管壁是热传递的一个重要界面。
当热量通过管壁时,会受到管壁的传导热阻的影响。
传导热阻取决于管材的导热性能和管壁厚度。
4. 流体动力学特性:除了简单的传热过程外,列管式换热器还受到流体动力学特性的影响。
流体会在管道中发生摩擦、湍流或层流等现象,这会影响换热器的传热效率。
总的来说,列管式换热器通过传热介质在管内和管外之间的热量传递,实现不同温度流体之间的热量交换。
它在工业生产和生活中具有广泛的应用,例如汽车散热器、空调系统和石油化工设备等。
列管式换热器设备工艺原理

列管式换热器设备工艺原理一、概述列管式换热器是一种常用的换热设备,广泛应用于化工、医药、食品、能源等领域。
该设备的工艺原理是利用壁面上的传热孔道将流体中的热量传递给另外一侧的流体,以实现两侧流体温度的变化。
本文将介绍列管式换热器的基本概念、工艺原理以及常见应用。
二、列管式换热器的基本结构列管式换热器由管束、弹板箱和固定管板等组成。
其中管束是由多根金属管子组成的,可以分成U型管、臂式管等几种形式。
弹板箱是指用弹性材料制作的箱子,由弹性材料的自身弹性质量能够使管束与箱体之间处于一定的紧密接触状态。
此外,固定管板用来固定管束,也可以使流体在管束内的传热均匀分布,从而提高传热效率。
三、列管式换热器的工艺原理列管式换热器的工艺原理基于摩尔爵士定律,即两种流体之间的热量传递与其热容量、温度差和传热面积有关。
在列管式换热器中,两种流体通过管束内外流动,而管壁则成为两种流体之间的传热面积。
热量从高温流体向低温流体流动,高温流体温度降低,低温流体温度升高,直到达到热平衡。
此过程中,两种流体之间的换热量可以通过如下公式核算:Q=U×ΔT×S 其中Q表示换热量,U表示总传热系数,ΔT表示两种流体之间的温差,S表示传热面积。
总传热系数U包括内壁传热系数hi、壁的热传递系数λ和外壁传热系数ho三部分,在列管式换热器中,由于管材是金属材料,散热性能足够好,因此λ很小,可以忽略不计。
此外,U值的计算还需要考虑流体的性质、流量、管道材质以及管间距等多种因素。
四、列管式换热器的应用列管式换热器被广泛应用于化工、医药、食品、能源等行业中,常见的应用场景包括:1. 快速冷却定向快速冷却可以提高产品的效率、提升产品的质量。
列管式换热器可以快速将产品内部的热量散发出来,同时保证温度的均匀分布,因此常用于温度敏感的产品冷却。
2. 温度回收列管式换热器还可以用来回收高温流体的热量,将其用于低温流体的加热,以减少能源浪费,提高节能效率。
列管式换热器原理

列管式换热器原理
列管式换热器是一种常用的换热设备,其基本原理是在圆柱形管子内部流动的流体与管外壁之间进行传热。
通过流体在管内壁与管外壁之间的传热,实现了热量的传递和交换。
列管式换热器的主要构成部分包括管壳、管束和管板。
管壳作为容器,将工作流体引入换热器,并将其导入管束中,然后将冷却介质或加热介质引入管壳,通过管束与工作流体进行热量交换。
管板则将管束连接在一起,形成一个整体。
在列管式换热器内部,热量传递主要发生在管外壁和管内壁之间。
工作流体从管束进入管内,流经管内壁,与管内壁接触并传递热量。
同时,冷却介质或加热介质从管壳中进入,包围着管内壁,与管外壁接触并吸收或释放热量。
通过管内壁和管外壁的热量交换,实现了工作流体和冷却介质或加热介质之间的热量传递。
为了增强列管式换热器的热量传递效果,通常在管束内安装一种称为增强片的结构。
增强片具有扰动流体流动的作用,可以增加流体与管内壁的接触面积,提高传热效率。
除了增强片,还可以在管束内设置折流板或分流器等辅助结构。
折流板可以引导流体沿着规定的路径流动,增加流体与管内壁的接触次数,提高传热效果。
分流器则可以将流体分成多个通道,使流体能够均匀地与管内壁进行热量交换。
总的来说,列管式换热器通过工作流体与冷却介质或加热介质
之间的热量交换,实现了热量的传递和交换。
通过增强片、折流板和分流器等辅助结构的应用,可以进一步提高换热效率。
- 1、下载文档前请自行甄别文档内容的完整性,平台不提供额外的编辑、内容补充、找答案等附加服务。
- 2、"仅部分预览"的文档,不可在线预览部分如存在完整性等问题,可反馈申请退款(可完整预览的文档不适用该条件!)。
- 3、如文档侵犯您的权益,请联系客服反馈,我们会尽快为您处理(人工客服工作时间:9:00-18:30)。
江西科技师范大学食品科学与工程专业《化工原理课程设计》说明书题目名称列管式换热器的设计专业班级11级食品科学与工程学号20111912 20111878 20111911 学生姓名胡利君吕亚琼钟翠指导教师常军博士2012 年11月06日目录1.概述 (1)1.1设计方案 (1)1.1.1设计条件 (1)1.1.2选择换热器类型 (1)1.1.3传热器管程安排 (2)1.2设计换热器的要求 (2)2.衡算 (2)2.1传热面积的计算 (2)2.1.1定性温度的确定 (3)2.1.2计算平均传热温差 (3)2.1.3初算传热面积 (3)2.2工艺结构尺寸 (3)2.2.1管径和管内流速 (3)2.2.2管程数和传热数管数 (3)2.2.3平均传热温差校正及壳程数 (4)2.2.4传热管排列和分程方法 (4)2.2.5壳体直径 (4)2.2.6折流板 (4)2.2.7接管 (5)2.3换热器核算 (5)2.3.1传热面积校正 (5)2.3.2壳程传热膜系数 (6)2.3.3污垢热阻和壁管热阻 (6)2.3.4换热器内压降得核算 (7)3.总结 (8)4.附录 (9)4.1计算总表 (9)4.2设备选型表 (10)5.图纸 (11)6.参考文献及资料 (12)1.概述1.1设计方案换热器是化工、石油、食品及其他许多部门的通用设备,在生产中常用的一种换热机械装置。
按用途它可分为加热器、冷却器、冷凝器、蒸发皿和再沸器等。
根据冷、热流体热量交换的原理和方式可分为三大类:混合式、蓄热式、间璧式。
本设计以列管式换热器为模型,以进口温度5℃、出口温度70℃、流量为30m3/h为设计条件,针对列管式换热器生产过程中最主要的设备部件进行模拟设计和选型,本论文进行工艺设计、主要设备及附件尺寸的设计。
1.1.1设计条件两流体的温度变化情况:热流体进口温度160℃,出口温度105℃;流体进口温度5℃,出口温度70℃。
冷流体的流量为30m3/h。
1.1.2 选择换热器的类型列管式换热器可分为固定管板式换热器、浮头式换热器和U型管式换热器。
该换热器用饱和水蒸气加热,冬季操作时,其进口温度会降低,故而会加大管壁温度和壳体温度之差,所以温差较大。
同时,在清洗和检修时,整个管束可以从壳体中抽出,因此应选用浮头式换热器。
1.1.3传热管管程安排由于水较易结垢,如果流速太低,将会加快污垢增长速度,使换热器的热流量下降;因此,饱和水蒸汽应走壳程,水走管程。
1.2设计换热器的要求(1)合理的实现所规定的工艺条件传热量流体的物热力学参数与物理化学性质是工艺过程所规定的条件。
设计者应根据这些条件进行热力学和流体力学的计算,经过反复比较,使所设计的换热器具有尽可能小的传热面积,在单位时间内传递尽可能多的热量,其具体做法如下。
①增大传热系数?在综合考虑流体阻力及不发生流体诱发振动的前提下,尽量选择高的流速。
②提高平均温差?对于无相变的流体,尽量采用接近逆流的传热方式。
因为这样不仅可以提高平均温差,还有助于减少结构中的温差应力,在允许的条件下,可提高热流体的进口温度或降低冷流体的进口温度。
③妥善布置传热面?例如在管壳式换热器中,采用合适的管间距和排列方式,不仅可以加大单位空间内的传热面积,还可以改善流体的流动性质,错列管束的传热方式比并列管束的好。
如果换热器中的一侧有相变,另一侧流体为气相,可在气相一侧的传热面上加翅片,以增大传热面积,更有利于热量的传递(2)安全可靠换热器是压力容器,在进行强度,刚度,温差应力以及疲劳寿命计算时,应遵循我国《钢制石油化工压力容器设计规定》与《钢制管壳式换热器设计规定》等有关规定与标准。
这对保证设备的安全可靠起着重要作用(3)有利于安装,操作与维修直立设备的安全费往往低于水平或倾斜的设备。
设备与部件应便于运输与装拆,在厂房移动时不会受到楼梯,梁柱的妨碍,根据需要可添置气,液排放口,检查孔与敷设保温层(4)经济合理评价换热器的最终指标是:在一定的时间内固定费用(设置的购置费和安装费等)与操作费(动力费,清洗费,维修费等)的总和为最小。
在设计或选型时如果有几种换热器都能完成生产任务的需要,这一指标尤为重要。
传热面上垢层的产生和增厚,使传热系数不断降低,传热量随之减少,故有必要停止操作进行清洗。
在清洗时不仅无法传递热量,还要支付清洗费,这部分费用必须从清洗后传热条件的改善得到补偿,因此存在一最适宜的运行周期严格的讲,如果孤立的从换热器本身来进行经济核算已确定适宜的操作条件与适宜的尺寸是不够全面的,应以整个设备为对象进行经济核算或设备的优化。
但要解决这样的问题难度很大,当影响换热器的各项因素改变后对整个系统的效益关系影响不大时,按照上述观点单独地对换热器进行经济核算仍然是可行的选择换热器时,要遵循经济,传热效果优,方便清洗,符合实际需要等原则2.衡算2.1传热面积的计算2.1.1定性温度的确定冷流体的定性温度:1257037.522t t T C ++∆===︒ 热流体的定性温度:12160105132.522T T T C ++∆===︒ 水在平均温度37.5C ︒下的有关物性数据由()1⎡⎤⎣⎦附录三可得()3, 4.17410/.p c C J kg K =⨯,3992.2/kg m ρ=,6653.310.pa s μ-=⨯0.635/(.)W m K λ=饱和水蒸汽在平均温度132.5C ︒的有关物性数据由()1⎡⎤⎣⎦附录三可得3, 4.26610/(.)p h C J kg K =⨯,31.650/kg m ρ=,6217.810.pa s μ-=⨯0.686/(.)W m K λ=热负荷(忽略热损失):36,,2130992.2() 4.17410(705) 2.24103600T m c p c Q q c t t W ⨯=-=⨯⨯⨯-=⨯ 饱和水蒸汽用量(忽略热损失):6,3, 2.24109.55/4.2661055T m h p h Q q kg s c t ⨯===∆⨯⨯2.1.2计算平均传热温差1111055100t T t C ∆=-=-=︒2221607090t T t C ∆=-=-=︒ 因为12100290t t ∆=<∆,所以 1210090=9522m t t t C ∆+∆+∆==︒逆2.1.3初算传热面积由于壳程气体的压力较大,故可选较大的K 值。
假设2610/(.)K W m C =︒,则可估算传热面积为:622.2410=38.6561095T m Q S m K t ⨯==∆⨯估2.2工艺结构和尺寸2.2.1管径和管内流速取管内流速 1.8/u m s =,传热数管数10n =0.024d m === 由()2⎡⎤⎣⎦附录二十一查阅可选用33.5 3.25mm φ⨯规格的钢管得0.027d m =根据224430/3600 1.4/0.027vq u m s d ππ⨯===⨯2.2.2管程数和传热管数224430/3600110.027 1.4v s q N d u ππ⨯==≈⨯⨯ 按单程管设计,所需的传热管长度为:038.6533.4340.033511S S L d N ππ===≈⨯⨯估按单程管设计,传热管过长,宜采用多管程结构。
根据本设计实际情况采用非标准设计,先去传热管长度8.5l m =,则该换热管的管程数为:3448.5p L N l === 传热管总数:11444n =⨯=2.2.3平均传热温差校正及壳程数平均温差校正系数如下:21117050.421605t t p T t --===-- 12211601050.85705T T R t t --===-- 按单壳程,双管程结构,查()1参考文献图4-25得0.943t ϕ∆=平均传热温差:=0.94395=89.585m t m t t C ϕ∆∆=∆⨯︒逆由于平均传热温差校正系数大于0.8,同时壳程流体流量较小,故取双壳程合适。
2.2.4传热管排列和分程方法采用组合排列法,即每程内均按正三角形排列,隔板两侧采用正方形排列。
取管心距01.25t p d =,则 1.2533.541.87542t p mm =⨯=≈隔板中心到离其最近一排管中心距离:6272t P Z mm =+= 各程相邻管的管心距为54mm 。
2.2.5壳体直径采用多管程结构,壳体直径可按()2参考文献式(4-15)估算。
取管板利用率,则壳体直径为:1.05 1.05337.78D mm ==⨯=按卷制壳体的进级档,可取400D mm =。
2.2.6折流板采用弓形折流板,取弓形折流板园缺高度为壳体内径的25%,则切去的圆缺高度为0.25400100h mm =⨯= 可取100h mm =。
取折流板间距0.3(0.2)B D D B D =<<,则0.3400120B mm =⨯= 可取B 为120mm 。
折流板数目8500-1=-1=69.870120B N =≈传热管长折流板间距 2.2.7接管壳程流体进出口接管:取接管内流体流速 2.5/i u m s =,则接管内径为:0.0698D m === 圆整后可取管内径为70mm 。
管程流体进出口接管,取接管内流体流速27/u m s =,则接管内径为:0.389D m ==2.3换热器核算2.3.1传热面积校正 管程传热膜系数0.80.40.023Re i pr d λα=管程流体流通截面积2220.027441/80.0125842i n S d m ππ==⨯⨯⨯= 管程流体流速和雷诺数分别为:30/36000.6624/0.01258v i i q u m s S === 60.0270.6624992.2Re /27162653.310i d u ρμ-⨯⨯===⨯ 普朗特数:364.17410653.310Pr 4.290.635p C μλ-⨯⨯⨯=== 0.80.40.80.420.6350.023Re Pr 0.02327162 4.293414/(.)0.027i i W m C d λα==⨯⨯⨯=︒2.3.2壳程传热膜系数10.550.143000.36Re Pr (/)'i w d e λαμμ=⨯ 管子按正三角形排列,传热当量直径为:2222020)40.042-0.0335)2424'==0.0250.0335Pt d d e m d ππππ-⨯⨯=⨯ 壳程流通截面积:-320033.5=BD(1-)=120400(1-)=9.7141042d s m pt ⨯⨯⨯ 壳程流体流速及其雷诺数分别为:09.55/1.65==60/0.009714u m s 50-60.027595.8 1.65Re ==1.2210217.810⨯⨯⨯⨯ 普朗特数:3-60-24.26610217.810Pr ==1.36268.210⨯⨯⨯⨯ 粘度校正:0.14(/)=1.05w μμ152300.682=0.36(1.2210) 1.362 1.05=7171/.0.025W m C α⨯⨯⨯⨯⨯︒2.3.3污垢热阻和管壁热阻查()1参考文献表4-6, 管外侧污垢热阻00R =,管内侧污垢热阻2=0.0002(m .)/W i R C ︒,根据我们的清洗方式估计管内污垢热阻变化大概是在 10%-20%已知管壁厚度=0.0335b m ,碳钢在该条件下的热导率为50/(.)W m C ︒。