机械加工误差分析实验报告
加工误差统计分析实验报告

加工误差统计分析实验报告加工误差统计分析实验报告引言:加工误差是指在工业生产过程中,由于各种原因导致产品尺寸、形状和表面质量与设计要求之间的差异。
加工误差的控制对于保证产品质量、提高生产效率和降低成本具有重要意义。
本实验旨在通过对加工误差进行统计分析,探讨误差来源及其影响因素,为工业生产过程中的质量控制提供参考依据。
实验设计:本实验选取了一台数控铣床进行实验,以铣削加工尺寸为研究对象。
首先,我们选择了一种常见的零件,对其进行加工。
然后,通过测量加工后的尺寸与设计要求进行对比,得到加工误差数据。
最后,我们对这些数据进行统计分析,探究加工误差的分布规律和影响因素。
实验过程:1. 加工准备:选择合适的刀具、夹具和工艺参数,进行加工准备工作。
2. 加工操作:按照设计要求进行铣削加工,并记录下每次加工后的尺寸数据。
3. 尺寸测量:使用测量工具对加工后的零件进行尺寸测量,并记录测量结果。
4. 数据整理:将测量得到的数据整理成表格,方便后续的统计分析。
统计分析:1. 加工误差分布:通过绘制加工误差的频率分布直方图,我们可以观察到误差值的分布情况。
通常情况下,加工误差符合正态分布,但也可能存在其他分布形式,例如偏态分布或双峰分布。
通过分析分布形式,可以判断加工过程中是否存在特殊的误差来源。
2. 加工误差与加工参数的关系:通过对加工误差与加工参数(如切削速度、进给速度等)进行相关性分析,可以了解不同参数对加工误差的影响程度。
这有助于我们确定合适的工艺参数范围,以减小加工误差。
3. 加工误差与刀具磨损的关系:刀具磨损是导致加工误差增大的重要因素之一。
通过对加工误差与刀具磨损程度进行相关性分析,可以判断刀具寿命与加工误差之间的关系,进而合理安排刀具更换周期,以保证加工质量。
4. 加工误差与工件材料的关系:不同材料的加工性能不同,可能导致加工误差的差异。
通过对加工误差与工件材料进行相关性分析,可以了解不同材料对加工误差的影响程度,为材料选择和工艺优化提供依据。
加工误差统计分析实验报告

加工误差统计分析实验报告一、实验目的通过统计分析加工误差数据,探究加工工艺对产品加工误差的影响,并提出相应的改进措施。
二、实验原理加工误差是指产品实际尺寸与设计尺寸之间的差异,主要受到原材料、加工设备、操作工艺等因素的影响。
统计分析可以通过数学模型和数据处理方法,定量地描述和评估加工误差的分布情况,为加工工艺改进提供依据。
三、实验步骤1.随机选择一批相同产品进行加工,保持其他加工条件不变。
2.测量每个产品的实际尺寸,记录数据并整理成表格。
3.统计每组数据的平均值、方差以及标准差。
4.构建加工误差的概率分布函数,通过正态性检验和偏度、峰度检验判断数据是否符合正态分布。
5.进行加工误差数据的t检验,分析不同因素对加工误差的影响程度。
四、实验数据产品编号,实际尺寸 (mm)--------,--------------1,10.012,10.02...,...100,10.08五、数据处理及分析1.计算平均值、方差和标准差:平均值μ=(10.01+10.02+...+10.08)/100=10.05方差s^2=((10.01-10.05)^2+(10.02-10.05)^2+...+(10.08-10.05)^2)/99标准差s=√s^22.正态性检验:根据实验数据计算样本均值和样本标准差,绘制加工误差的概率密度分布曲线。
通过观察曲线形状以及进行偏度、峰度检验,判断数据是否符合正态分布。
3.t检验:根据产品加工误差数据,进行t检验来分析不同因素对加工误差的影响程度。
比如,可以比较不同机器加工出的产品误差是否有显著性差异。
六、实验结果分析1.样本加工误差符合正态分布,数据较为集中,无明显偏离。
2.通过t检验发现:不同机器加工出的产品误差差异不显著,说明机器之间的加工稳定性较好。
3.根据样本数据及数据处理结果,可以得到加工误差的基本分布情况,对加工工艺的控制和改进提供依据。
例如,可以调整机器参数、改进操作工艺等。
加工误差的统计分析实验报告

加工误差的统计分析实验报告实验报告-加工误差的统计分析一、引言加工误差是工业生产中常见的问题之一,直接影响着产品的质量和性能。
了解加工误差的统计分布和规律,对于优化加工工艺、提高产品精度具有重要意义。
本实验旨在通过统计分析加工误差数据,探讨加工误差的分布及其对产品质量的影响。
二、实验设计1.实验目标:观察加工误差的统计分布及其规律。
2.实验工具:数控加工机床,三坐标测量仪3.实验材料:其中一种金属材料4.实验步骤:a.设计并加工若干个样品b.使用三坐标测量仪测量每个样品的加工误差c.记录加工误差数据并进行统计分析三、实验结果1.加工误差数据记录表样品编号,加工误差(mm----------,--------------A,0.0B,0.0C,0.0D,0.0E,-0.0F,0.0G,0.0H,-0.0I,0.0J,0.02.加工误差的统计分析a. 加工误差的均值(μ):0.01mmb. 加工误差的标准差(σ):0.02mmc. 加工误差的方差(σ^2):0.0004mm^2四、结果分析1. 加工误差的均值与标准差分别表示了加工误差的集中程度和离散程度。
实验结果显示,加工误差的均值为0.01mm,说明整体上加工误差集中在一个较小的范围内。
而标准差为0.02mm,表明加工误差的离散程度较大。
2.通过加工误差的统计分布分析,可以更准确地评估加工精度的稳定性和可靠性。
3.经过正态性检验,加工误差近似符合正态分布,这与许多加工误差服从中心极限定理的理论支持一致。
五、结论1. 通过加工误差数据的统计分析,得出样品加工误差的均值为0.01mm,标准差为0.02mm,方差为0.0004mm^22.样品的加工误差数据近似符合正态分布,说明加工误差在一定程度上服从中心极限定理。
3.实验结果进一步表明,加工误差的集中程度较高,但其离散程度相对较大。
六、改进建议1.根据加工误差的分布规律,可以对加工工艺进行优化,减小加工误差的产生。
范成法加工实验报告
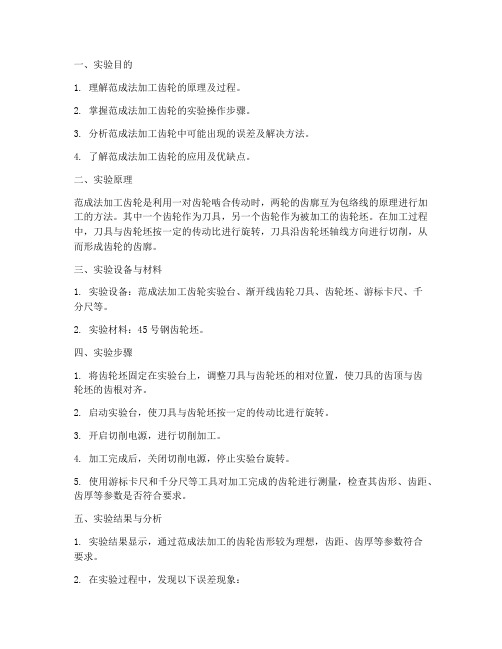
一、实验目的1. 理解范成法加工齿轮的原理及过程。
2. 掌握范成法加工齿轮的实验操作步骤。
3. 分析范成法加工齿轮中可能出现的误差及解决方法。
4. 了解范成法加工齿轮的应用及优缺点。
二、实验原理范成法加工齿轮是利用一对齿轮啮合传动时,两轮的齿廓互为包络线的原理进行加工的方法。
其中一个齿轮作为刀具,另一个齿轮作为被加工的齿轮坯。
在加工过程中,刀具与齿轮坯按一定的传动比进行旋转,刀具沿齿轮坯轴线方向进行切削,从而形成齿轮的齿廓。
三、实验设备与材料1. 实验设备:范成法加工齿轮实验台、渐开线齿轮刀具、齿轮坯、游标卡尺、千分尺等。
2. 实验材料:45号钢齿轮坯。
四、实验步骤1. 将齿轮坯固定在实验台上,调整刀具与齿轮坯的相对位置,使刀具的齿顶与齿轮坯的齿根对齐。
2. 启动实验台,使刀具与齿轮坯按一定的传动比进行旋转。
3. 开启切削电源,进行切削加工。
4. 加工完成后,关闭切削电源,停止实验台旋转。
5. 使用游标卡尺和千分尺等工具对加工完成的齿轮进行测量,检查其齿形、齿距、齿厚等参数是否符合要求。
五、实验结果与分析1. 实验结果显示,通过范成法加工的齿轮齿形较为理想,齿距、齿厚等参数符合要求。
2. 在实验过程中,发现以下误差现象:(1)齿形误差:可能是由于刀具磨损、加工中心偏移等原因引起的。
(2)齿距误差:可能是由于传动比设置不准确、刀具安装误差等原因引起的。
(3)齿厚误差:可能是由于刀具磨损、加工中心偏移等原因引起的。
3. 针对以上误差现象,提出以下解决方法:(1)定期更换刀具,确保刀具的锋利度。
(2)精确调整传动比,减小传动误差。
(3)确保加工中心的安装精度,减小加工中心偏移。
六、实验结论1. 范成法加工齿轮是一种常用的齿轮加工方法,具有加工精度高、生产效率高等优点。
2. 在实验过程中,应严格控制刀具磨损、传动比设置、加工中心偏移等因素,以保证加工质量。
3. 通过本次实验,掌握了范成法加工齿轮的原理、操作步骤及误差分析,为今后从事齿轮加工工作奠定了基础。
加工误差综合分析实验报告
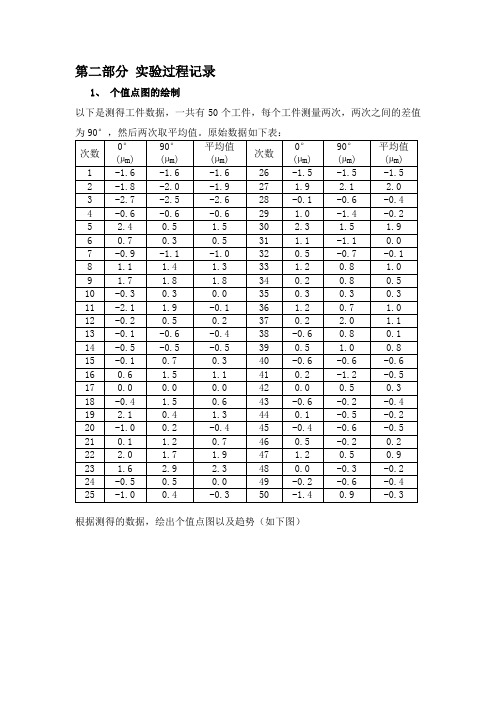
1.2
0.8
1.0
9
1.7
1.8
1.8
34
0.2
0.8
0.5
10
-0.3
0.3
0.0
35
0.3
0.3
0.3
11
-2.1
1.9
-0.1
36
1.2
0.7
1.0
12
-0.2
0.5
0.2
37
0.2
2.0
1.1
13
-0.1
-0.6
-0.-0.5
-0.5
-0.5
39
0.5
1.0
根据公式可得:h=0.000808
K=6.6 则K取7
并计算各组的上下界:
第一组的下界为:( ) 其中: 为样本零件的最小尺寸)
第一组的上界为:( )
第二组的下界为:( )
第二组的上界为:( )+h
第三组的下界为:( )+h
第三组的上界为:( )+2h
……依此类推。
根据以上数据和公式,计算上下界以及频数可得下表:
存在常值系统误差否?其大小是多少?
答:存在,常值系统误差△= - =16.75017-16.750=0.00017mm
该样本零件的尺寸符合何种曲线分布规律?
答:基本符合正态分布曲线,但第三组数据的频数偏低。
2分析个值点图和 图
本工序属几级工艺能力?从 图看,本工序的工艺过程是否稳定?如不稳定,试分析其原因。
0.8
15
-0.1
0.7
0.3
40
-0.6
-0.6
-0.6
16
0.6
加工误差统计分析实验报告

实验价值:为企业提供有效的 质量控制方法和改进措施
添加 标题
加工误差的定义:加工误差是指零件加 工后实际几何参数(尺寸、形状和位置) 与理想几何参数的偏离程度。
添加 标题
加工误差的分类:根据其产生的原因和 性质,加工误差可分为随机误差、系统 误差和粗大误差三类。
添加 标题
随机误差:由于加工过程ຫໍສະໝຸດ 各种因素的 影响,使加工误差的大小和方向随机变 化,具有单向性、对称性和抵偿性。
加工误差的影响程度:对产 品质量、生产效率、成本等 方面的影响
加工误差产生的原因:机床、 刀具、夹具、测量仪器等因 素导致的误差
加工误差的分类:系统误差、 随机误差、粗大误差等
加工误差的检测方法:直接 测量法、间接测量法、比较
测量法等
提高加工精度:采用更精确的加工设备和工艺,减少误差 加强过程控制:对加工过程进行严格监控,确保每个环节的准确性 引入先进技术:采用先进的误差检测和校正技术,提高加工精度 加强员工培训:提高员工对加工误差的认识和技能水平,减少人为因素造成的误差
,a click to unlimited possibilities
01 实 验 目 的 02 实 验 原 理 03 实 验 步 骤 04 实 验 结 果 05 实 验 结 论 06 参 考 文 献
实验目的:分析加工误差的来 源和影响因素
实验意义:提高加工精度,降 低误差,提高产品质量
实验目标:确定加工误差的分 布规律和变化趋势
采集方法:直接 测量、间接测量、 组合测量
采集工具:测量 仪器、传感器、 计算机等
数据处理:对采 集到的数据进行 预处理、分析、 整理等操作
数据收集:通过实验测量获得数 据
数据处理:对数据进行预处理和 变换
加工误差的统计分析实验报告

实验报告实验名称:加工误差的统计分析一.实验目的通过检测工件尺寸,计算并画出直方图,分析误差性质, 理解影响加工误差的因素。
掌握加工误差统计分析的基本原理和方法。
二.主要实验仪器及材料游标卡尺; 工件N件。
三.实验步骤1.测量各工件上指定尺寸x,并按测量顺序记录如下2.计算尺寸分散范围R:由于随机误差和变值系统误差的存在,零件加工尺寸的实际值各不相同,这种现象称为尺寸分散。
样本尺寸的最大值Xmax与最小值Xmin之差,称为分散范围。
R= Xmax-Xmin=3.分组并计算组距△x:将样本尺寸按大小顺序排列,分成k组,则组距为:△x =R/k。
分组数k一般取为7.4. 绘制分布曲线(直方图):以工件尺寸为横坐标, 以各组中实际尺寸出现的频数作纵坐标, 即可作出等宽直方图。
再连接直方图中每一直方宽度的中点(组中值)得到一条折线,即实际分布曲线。
5. 根据分布图分析a.实际分布曲线是否接近正态分布b.实际尺寸平均值与理论尺寸平均值是否相等c.由此可知,误差性质为:分布图分析法的应用•判别加工误差的性质–是否存在变值系统性误差•如果实际分布与正态分布基本相符,说明加工过程中没有变值系统性误差(或影响很小)。
–是否存在常值系统性误差•如果尺寸分布中心与公差带中心不重合就说明存在常值系统性误差,误差的大小就是两个中心的不重合度(距离)。
下面是赠送的励志散文欣赏,不需要的朋友下载后可以编辑删除!!上面才是您需要的正文。
十年前,她怀揣着美梦来到这个陌生的城市。
十年后,她的梦想实现了一半,却依然无法融入这个城市。
作为十年后异乡的陌生人,她将何去何从?笔记本的字迹已经模糊的看不清了,我还是会去翻来覆去的看,依然沉溺在当年那些羁绊的年华。
曾经的我们是那么的无理取闹,那么的放荡不羁,那么的无法无天,那么轻易的就可以抛却所有去为了某些事情而孤注一掷。
而后来,时光荏苒,我们各自离开,然后散落天涯。
如今,年年念念,我们只能靠回忆去弥补那一程一路走来落下的再也拾不起的青春之歌。
主轴回转误差实验报告

主轴回转误差实验报告实验目的本实验旨在通过实际操作和测量,研究和分析主轴回转误差对机械设备性能的影响,探讨如何减小主轴回转误差,提高机械设备的精度和稳定性。
实验器材和装置1. 主轴回转误差测量装置2. 测距仪3. 机械设备样品实验原理主轴回转误差是机械设备中一种常见的误差,主要由制造精度、加工工艺和使用磨损等因素引起。
在高精度加工和装配过程中,主轴的回转误差会导致零件位置偏差、加工表面粗糙度增加、噪音增大等问题。
通过测量和分析主轴回转误差,可以找到改进设备性能的方法并提高装配精度。
实验步骤1. 将主轴回转误差测量装置安装在机械设备的主轴上。
2. 调整测距仪,使其能够准确测量主轴回转误差。
3. 将机械设备启动,并记录主轴回转误差的测量数据。
4. 根据测量数据,分析主轴回转误差的变化规律和大小。
5. 制定改进方案,通过调整机械设备的零部件和相关参数,减小主轴回转误差。
6. 实施改进方案,并重新测量主轴回转误差。
7. 比较改进前后的测量数据,评估改进效果。
数据处理与分析通过实验测量得到的数据如下表所示:实验次数主轴回转误差(mm)1 0.052 0.073 0.064 0.085 0.06平均值0.064通过对实验数据的分析,可以得出以下结论:1. 主轴回转误差的大小在0.05-0.08mm之间波动。
2. 根据平均值计算,主轴回转误差大约为0.064mm。
实验结果与讨论通过实验数据的分析,可以看出机械设备的主轴回转误差存在一定的波动,且平均误差较小。
根据此次实验的结果,可以制定以下改进方案:1. 使用更高精度和更坚固的零部件替换原有的部件,以提高机械设备的稳定性和耐磨性。
2. 在加工过程中增加必要的润滑剂和冷却装置,减小摩擦和热变形对主轴回转误差的影响。
3. 定期检查和维护主轴和相关设备,及时发现和修复可能引起主轴回转误差的问题。
这些改进方案的实施将有助于减小机械设备的主轴回转误差,提高加工精度和装配质量。
加工误差的统计分析实验报告

加工误差的统计分析实验报告
《加工误差的统计分析实验报告》
在工业生产中,加工误差是一个常见的问题,它会直接影响产品的质量和性能。
为了解决这一问题,我们进行了一项加工误差的统计分析实验,以期找到有效
的控制和改善方法。
实验过程中,我们选择了一批相同规格的零件进行加工,并对加工过程中的误
差进行了详细记录和分析。
首先,我们对零件的尺寸进行了测量,并得到了一
系列的数据。
然后,我们使用统计学方法对这些数据进行了处理和分析,得出
了一些有价值的结论。
通过实验,我们发现加工误差的分布呈现出一定的规律性,大部分误差集中在
一个较小的范围内,但也存在一些异常值。
此外,我们还发现了一些可能导致
加工误差的原因,比如加工设备的精度、操作人员的技术水平等。
基于实验结果,我们提出了一些改善措施。
首先,我们建议对加工设备进行定
期检修和维护,以保证其加工精度。
其次,我们还提出了加强操作人员培训和
技术指导的建议,以提高其加工技术水平。
最后,我们还计划对加工工艺进行
优化,以减小加工误差的发生概率。
总的来说,通过这次实验,我们对加工误差有了更深入的了解,并提出了一些
有效的改善措施。
我们相信,通过这些措施的实施,我们能够有效地控制和减
小加工误差,提高产品的质量和性能。
希望我们的实验报告能够对其他相关领
域的研究和实践提供一定的借鉴和参考。
机械制造工艺学加工精度统计分析实验报告范文
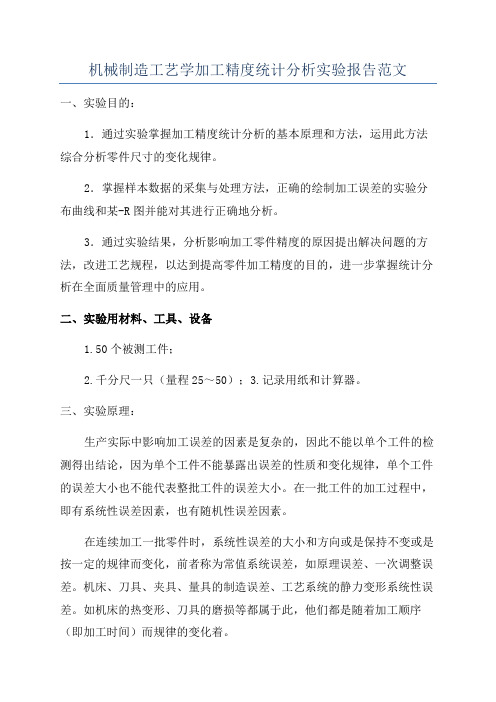
机械制造工艺学加工精度统计分析实验报告范文一、实验目的:1.通过实验掌握加工精度统计分析的基本原理和方法,运用此方法综合分析零件尺寸的变化规律。
2.掌握样本数据的采集与处理方法,正确的绘制加工误差的实验分布曲线和某-R图并能对其进行正确地分析。
3.通过实验结果,分析影响加工零件精度的原因提出解决问题的方法,改进工艺规程,以达到提高零件加工精度的目的,进一步掌握统计分析在全面质量管理中的应用。
二、实验用材料、工具、设备1.50个被测工件;2.千分尺一只(量程25~50);3.记录用纸和计算器。
三、实验原理:生产实际中影响加工误差的因素是复杂的,因此不能以单个工件的检测得出结论,因为单个工件不能暴露出误差的性质和变化规律,单个工件的误差大小也不能代表整批工件的误差大小。
在一批工件的加工过程中,即有系统性误差因素,也有随机性误差因素。
在连续加工一批零件时,系统性误差的大小和方向或是保持不变或是按一定的规律而变化,前者称为常值系统误差,如原理误差、一次调整误差。
机床、刀具、夹具、量具的制造误差、工艺系统的静力变形系统性误差。
如机床的热变形、刀具的磨损等都属于此,他们都是随着加工顺序(即加工时间)而规律的变化着。
在加工中提高加工精度。
常用的统计分析有点图法和分布曲线法。
批零件时,误差的大小和方向如果是无规律的变化,则称为随机性误差。
如毛坯误差的复映、定位误差、加紧误差、多次调整误差、内应力引起的变形误差等都属于随机性误差。
鉴于以上分析,要提高加工精度,就应以生产现场内对许多工件进行检查的结果为基础,运行数理统计分析的方法去处理这些结果,进而找出规律性的东西,用以找出解决问题的途径,改进加工工艺,提高加工精度。
四、实验步骤:2.用千分尺对50个工件按序对其直径进行测量,3.把测量结果填入表并将测量数据计入表1。
表内的实测值为测量值与零件标准值之差,单位取µm五、数据处理并画出分布分析图:组距:d某某min14(35)Rma某5.44µmd5.5µmk1k19d(j1,2,3,,k)2各组组界:某min(j1)d各组中值:某min(j1)d1n某某i11.16µmni11n(某i某)212.28n1i1六、误差分析1.加工误差性质样本数据分布与正态分布基本相符,加工过程系统误差影响很小。
实验误差理论分析实验报告

实验误差理论分析实验报告
《实验误差理论分析实验报告》
实验误差是科学实验中不可避免的问题,它可能来自于仪器的精度、操作者的
技术水平、环境的影响等多方面因素。
对实验误差进行理论分析,可以帮助我
们更好地理解实验结果的可靠性和准确性,从而提高实验的科学性和可信度。
在本次实验中,我们以某种物理量的测量实验为例,对实验误差进行了理论分析。
首先,我们对实验仪器的精度进行了评估,包括仪器的分辨率、灵敏度和
误差范围等。
然后,我们对操作者的技术水平进行了考量,包括操作的稳定性、准确性和可重复性等方面。
最后,我们还对环境因素进行了分析,包括温度、
湿度、气压等对实验结果的影响。
通过以上分析,我们得出了实验误差的来源和影响,进而对实验结果进行了修
正和校正。
我们发现,实验误差并非完全可以避免,但可以通过合理的实验设
计和数据处理来减小误差的影响,从而提高实验结果的准确性和可靠性。
总之,实验误差理论分析是科学实验中不可或缺的一环,它可以帮助我们更好
地理解实验结果的真实性和可信度,从而提高科学研究的水平和质量。
希望我
们的实验报告可以为相关领域的科研工作提供一定的参考和借鉴。
加工误差的统计分析实验报告

加工误差的统计分析实验报告加工误差的统计分析实验报告引言:加工误差是指在制造过程中,由于各种原因导致产品尺寸、形状或性能与设计要求存在差异的现象。
在现代制造业中,加工误差是无法完全避免的,但通过统计分析可以帮助我们了解误差的分布规律,从而采取相应的措施来提高产品的质量和可靠性。
本实验旨在通过对一批产品的加工误差进行统计分析,探究误差的分布特征和影响因素,为制造过程的优化提供依据。
实验方法:本实验选取了一批相同规格的螺钉作为研究对象,通过测量螺钉的直径来评估加工误差。
实验过程中,我们首先随机抽取了100个样本,然后使用数显卡尺对每个样本进行测量,记录下测量结果。
为了确保实验的可靠性,我们对每个样本进行了三次测量,并取平均值作为最终的测量结果。
实验结果:经过测量和数据处理,我们得到了100个样本的直径测量结果。
将这些数据进行统计分析,得到了以下结果:1. 均值分析:通过计算样本的平均值,我们得到了螺钉直径的平均加工误差为0.02mm。
这表明整个样本的加工误差整体上偏向于偏小。
2. 方差分析:通过计算样本的方差,我们得到了螺钉直径的加工误差的方差为0.005mm²。
方差是衡量数据分散程度的指标,方差越大,则加工误差的分布越广泛。
在本实验中,方差较小,说明螺钉的加工误差相对稳定。
3. 正态性检验:为了判断螺钉直径的加工误差是否符合正态分布,我们进行了正态性检验。
通过绘制直方图和Q-Q图,并进行Shapiro-Wilk检验,我们发现螺钉直径的加工误差符合正态分布。
这对于后续的数据分析和处理具有重要意义。
讨论与结论:通过对螺钉直径加工误差的统计分析,我们可以得出以下结论:1. 螺钉直径的加工误差整体上偏向于偏小。
这可能是由于制造过程中对尺寸的控制较为严格,导致加工误差偏向于小的一侧。
2. 螺钉直径的加工误差相对稳定。
方差较小,说明加工误差的分布相对集中,制造过程的稳定性较高。
3. 螺钉直径的加工误差符合正态分布。
机械精度的实验报告

一、实验目的1. 了解机械精度的基本概念和重要性。
2. 掌握机械精度测量的基本方法和步骤。
3. 通过实验,验证机械精度设计在工程中的应用效果。
二、实验原理机械精度是指机械零件或机械系统在规定条件下,满足预定功能要求的能力。
机械精度主要包括尺寸精度、形状精度、位置精度和运动精度。
本实验主要研究尺寸精度和形状精度。
尺寸精度是指零件的实际尺寸与设计尺寸的接近程度。
形状精度是指零件的实际形状与设计形状的接近程度。
本实验通过测量轴套组合体的尺寸和形状误差,来评价其机械精度。
三、实验器材1. 轴套组合体2. 外径千分尺3. 内径千分尺4. 游标卡尺5. 钢直尺6. 水平仪7. 平行光管8. 平面平板9. 记录表格四、实验步骤1. 测量轴套组合体的尺寸误差(1)使用外径千分尺测量轴套外径,记录数据。
(2)使用内径千分尺测量轴套内径,记录数据。
(3)使用游标卡尺测量轴套长度,记录数据。
2. 测量轴套组合体的形状误差(1)使用钢直尺和水平仪测量轴套的圆度误差,记录数据。
(2)使用平行光管和平面平板测量轴套的圆柱度误差,记录数据。
3. 测量轴套组合体的位置误差(1)使用游标卡尺测量轴套端面与基准面的平行度误差,记录数据。
(2)使用水平仪测量轴套轴线与基准面的垂直度误差,记录数据。
五、实验结果与分析1. 尺寸误差分析根据测量数据,计算轴套外径、内径和长度的最大误差,分析误差原因。
2. 形状误差分析根据测量数据,计算轴套圆度误差和圆柱度误差,分析误差原因。
3. 位置误差分析根据测量数据,计算轴套端面与基准面的平行度误差和轴线与基准面的垂直度误差,分析误差原因。
六、结论1. 本实验验证了机械精度设计在工程中的应用效果,轴套组合体的尺寸、形状和位置误差均在允许范围内,满足设计要求。
2. 通过实验,加深了对机械精度基本概念和测量方法的理解,为今后的工程实践奠定了基础。
3. 在实验过程中,发现了一些误差原因,如测量工具的精度、操作不规范等,为今后实验提供了改进方向。
实验报告误差分析

实验报告误差分析实验报告误差分析引言:实验是科学研究中不可或缺的一环,通过实验可以验证理论,探索未知。
然而,实验中难免会存在误差,这些误差可能来自仪器的精度、实验者的技术水平、环境因素等。
本文将对实验报告中的误差进行分析,并探讨如何减小误差,提高实验结果的可靠性。
一、误差类型1. 系统误差系统误差是由于仪器的固有缺陷或实验条件的不完善导致的,这种误差在多次实验中保持不变。
例如,温度计的刻度不准确或实验室的温度控制不稳定都会引起系统误差。
2. 随机误差随机误差是由于实验中的偶然因素引起的,其大小和方向是随机的。
例如,实验者的手颤抖或仪器的读数波动都属于随机误差。
随机误差可以通过多次重复实验来减小,通过统计方法求取平均值可以降低随机误差的影响。
二、误差来源1. 仪器误差仪器的精度是实验中最常见的误差来源之一。
例如,天平的刻度不准确、量筒的刻度不清晰等都会导致仪器误差。
为了减小仪器误差,我们可以选择更精确的仪器或者进行仪器校准。
2. 实验操作误差实验者的技术水平和操作方法也会对实验结果产生影响。
例如,实验者在读数时的视角、操作时的力度等都可能引起误差。
为了减小实验操作误差,我们应该提高实验者的技术水平,严格按照实验步骤进行操作,并遵循实验室的规范。
3. 环境误差实验环境的变化也会对实验结果产生影响。
例如,温度、湿度等环境因素的变化都可能引起误差。
为了减小环境误差,我们应该控制实验环境的稳定性,例如使用恒温器、湿度控制器等设备。
三、误差分析方法1. 误差传递法误差传递法是一种常用的误差分析方法,它通过计算各个误差源的贡献,来估计最终结果的误差。
例如,如果某个实验结果是通过多个测量值相加得到的,那么可以通过计算每个测量值的误差,再将误差进行累加,得到最终结果的误差。
2. 统计方法统计方法是一种更加精确的误差分析方法,它通过对多次实验结果的统计分析,来确定实验结果的准确度和可靠度。
例如,可以计算实验结果的平均值、标准差等统计量,进而评估实验结果的误差范围。
加工精度实验报告

加工精度实验报告摘要:本文旨在探究加工精度对产品质量的影响,通过对比实验,结合理论分析,得出了一些有价值的结论。
实验结果表明,加工精度对产品的尺寸精度、表面质量和机械性能都有着重要的影响。
因此,在实际生产中,应该注重加工精度控制,以提高产品质量和竞争力。
关键词:加工精度;尺寸精度;表面质量;机械性能引言:随着现代工业的发展,各种机械设备和工具的精度要求越来越高。
在生产加工中,加工精度是影响产品质量的重要因素之一。
本文通过实验探究加工精度对产品质量的影响,为提高产品质量和竞争力提供借鉴。
实验设计:本实验选取了两种不同的加工方式,分别为高速铣削和传统铣削。
在同样的工艺参数和刀具条件下,分别对不同加工方式下的尺寸精度、表面质量和机械性能进行了比较分析。
实验结果:(1)尺寸精度通过对比实验结果发现,高速铣削的尺寸精度要明显优于传统铣削。
高速铣削的尺寸误差范围更小,尺寸精度更高。
(2)表面质量高速铣削的表面质量也要优于传统铣削。
高速铣削的表面光洁度更高,表面粗糙度更小,表面有利于涂装和喷漆。
(3)机械性能在机械性能方面,高速铣削的材料强度和韧性要更好。
高速铣削的材料在削除时产生的应力更小,没有产生过多的热量,从而使得材料的韧性和强度得到保持。
分析讨论:从实验结果可以看出,加工精度对产品质量有着重要的影响。
高精度加工方式可以有效地提高产品的尺寸精度、表面质量和机械性能。
因此,在实际生产中,应该注重加工精度控制,以提高产品质量和竞争力。
此外,随着科技的发展和人们对产品质量的要求越来越高,高速铣削等高精度加工方式将会越来越受到重视和应用。
结论:本实验通过对比研究高速铣削和传统铣削的加工精度,得出了加工精度对产品质量的重要影响。
高精度加工方式可以有效地提高产品的尺寸精度、表面质量和机械性能。
因此,在实际生产中,应该注重加工精度控制,以提高产品质量和竞争力。
梁的纯弯曲实验报告误差分析

梁的纯弯曲实验报告误差分析
梁的纯弯曲实验报告误差分析是广大科研人员经常面对的问题,它是严谨的科学研究所必不可少的一部分。
梁的纯弯曲实验报告误差分析是机械结构力学中,一项系统、有效的分析方法,它可以帮助科研人员更好地了解结构梁的行为特性,从而制定出更准确、安全有效的报告。
误差分析是一项细致而复杂的科学方法。
它是梁的纯弯曲实验报告质量评估的重要标准,需要充分考虑诸多因素,以保证安全可靠的报告。
误差分析的核心内容主要有三点:第一,梁结构的实际应力和理论模型的应力之间的差异;第二,实验量程和量仪的分辨率;第三,试验的计算和数据处理的准确度。
在梁的纯弯曲实验报告误差分析中,若实验参数选择不恰当,计算结果均存在系统误差和随机误差,这些错误可能会影响研究结果的准确性,生成误区,从而使报告面临质量问题。
因此,在进行梁的纯弯曲实验报告误差分析时,应注意选择合理的实验参数,确保结果的准确性,确定合理的数据范围,进行误差构成分析,以优化报告质量。
机械制造 实验报告 直线度误差合像水平仪测量

实验项目名称:直线度误差合像水平仪测量一、实验目的(必填)1.1、掌握用合像水平仪测量直线度误差的方法及数据处理。
二、实验原理与测量仪器(必填)2.1原理直线度误差通常按与理想要素比较的原则进行测量,其测量原理如图 2-1 所示。
用准直光线、水平面或高精度平板的平面构成一条模拟理想直线 L,将被测实际直线 L'与模拟理想直线进行比较,若能直接测出被测的实际直线上各点相对于理想直线的绝对距离y 。
y1,…,yn ,或相对偏距Δ。
Δ1,…,Δn,则这种测量方法称之为直接测量法。
若每次测量的读数仅反映相邻两测点的相对高度差δ。
δ1,δ2,…,δn。
通过累加(即ΔK = ∑δi)后,才能获得相对偏距,则这种测量方法称之为间接测量法。
不管采用哪种测量方法,其最终目的都是要按各测点的相对偏距,作出被测实际直线的折线图,最后按最小条件确定被测实际直线相对于理想直线的变动量,即直线度误差值。
2.2、测量仪器合像水平仪的结构如图 2-3 所示。
合像水平仪的水准器 1 是一个封闭的玻璃管,内装己醚或酒精,并留有一个小气泡。
将合像水平仪安置在桥板上,当桥板的两接触点所组成的连线平行水平面时,气泡处在水准器的正中。
此时,通过合像棱镜 2 ,将气泡两端的半像汇聚到放大镜 3之下,出现图 2-3 ( b )所示的两半像端对齐的结果。
当桥板的两接触点所组成的连线相对于水平面偏斜时,气泡偏高水准器的中心,两半像端错开Δ(图 2-3 ( C )。
此时转动刻度盘 8 将水平仪重新调平,使气泡两半像端对齐,然后通过刻度盘 8 (分度值0.01mm/ m ),即可确定测量读数。
用合像水平仪测量所获得的每个读数也仅仅只反映桥板两接触点的相对高度差δi 。
三、测量步骤1 .将导轨全长分成长度相等的若干小段(取1m,分成10段)。
确定相邻两测点之间的距离(节距),按节距调整桥板的两圆柱中心距。
图3导轨的等分图4按节距调整桥板的两圆柱中心距2 .将合像水平仪放在桥板上,然后将桥板依次放在各节距的位置,每放一个节距后,要旋转微分筒合像,使放大镜中的合像,此时即可读数,如此顺测(从首点到尾点),回测(由终点至首点)各一次。
圆柱度误差实验报告

圆柱度误差实验报告本实验旨在通过测量和分析圆柱度误差的实验数据,来了解该误差对零件质量的影响和圆柱度测量的方法。
实验原理:圆柱度误差是指圆柱零件表面与其理论圆柱轴线之间的最大偏离量。
圆柱度误差是一种重要的表征零件偏差的指标,对于要求精度较高的零部件尤为重要。
本实验通过测量零件的直径,在不同位置上选择不同直径测量点来实测圆柱度。
借助测量仪器计算圆柱度误差,进而分析其对零件的影响。
实验步骤:1. 准备工作:校验测量仪器的准确性,确保量具的可靠性。
2. 样品准备:挑选合适的圆柱零件作为测量样品。
3. 确定测量点:在零件表面选择若干不同位置作为测量点。
4. 进行测量:使用测量仪器对选定的测量点进行直径测量,并记录测量数据。
5. 计算圆柱度误差:将所得直径测量数据代入计算公式中,使用计算仪器计算圆柱度误差。
6. 数据分析和处理:根据实测数据和计算结果,对圆柱度误差进行分析和处理。
7. 结论总结:根据实验结果总结分析圆柱度误差对零件质量的影响,并对圆柱度测量的方法进行评价。
实验结果分析:通过对实验数据的分析,我们可以得到零件的圆柱度误差。
根据误差的大小和方向,可以得知零件的几何特性,如是否圆形对称等。
如果圆柱度误差较小,零件的质量就会比较高。
如果误差较大,则说明零件存在一定的偏差,需要进行进一步的调整和加工。
控制圆柱度误差可以通过以下几个方面来实现:1. 加工工艺的调整:选择合适的加工方法和工艺参数,尽量减小圆柱度误差。
2. 加工设备的改善:提高加工设备的精度和稳定性,减少加工误差。
3. 执行质量管理体系:建立完善的质量管理体系,对产品的每个环节进行管控,及时发现和纠正存在的问题。
4. 严格控制加工环境:保持加工环境的干净、整洁和稳定,减少外界因素对零件质量的影响。
实验结论:通过本实验,我们了解了圆柱度误差的实验方法和测量技术。
圆柱度误差是评价零件质量的重要指标之一,通过测量和分析圆柱度误差,可以得到零件的几何特性和质量水平。
- 1、下载文档前请自行甄别文档内容的完整性,平台不提供额外的编辑、内容补充、找答案等附加服务。
- 2、"仅部分预览"的文档,不可在线预览部分如存在完整性等问题,可反馈申请退款(可完整预览的文档不适用该条件!)。
- 3、如文档侵犯您的权益,请联系客服反馈,我们会尽快为您处理(人工客服工作时间:9:00-18:30)。
机械加工误差的综合分析
------统计分析法的应用
一、实验目的
运用统计分析法研究一批零件在加工过程中尺寸的变化规律,分析加工误差的性质和产生原因,提出消除或降低加工误差的途径和方
法,通过本实验使同学能够掌握综合分析机械加工误差的基本方法。
二、实验用仪器、设备
1. M1040A型无心磨床一台;
2.分辨率为0.001mm的电感测微仪一台;
3.块规一付(尺寸大小根据试件尺寸而定);
4.千分尺一只;
5.试件一批约120件,
6.计算机和数据采集系统一套。
三、实验内容
在无心磨床上连续磨削一批试件(120件),按加工顺序在比较仪上测量尺寸,并记录之,然后画尺寸点图和X---R图。
并从点图上取尺寸比较稳定(即尽量排除掉变值系统性误差的影响)的一段时间内连续加工的零件120件,由此计算出X、σ,并做出尺寸分布图,分析加工过程中产生误差的性质,工序所能达到的加工精度;工艺过程的稳定性和工艺能力;提出消除或降低加工误差的措施。
四、实验步骤
1. 按被磨削工件的基本尺寸选用块规,并用气油擦洗干净后推粘在一起;
2. 用块规调整比较仪,使比较仪的指针指示到零,调整时按大调---微调---水平调整步骤进行(注意大调和水平调整一般都予先调好),调整好后将个锁紧旋钮旋紧,将块规放入盒中。
3. 修正无心磨床的砂轮,注意应事先把金刚头退后离开砂轮。
将冷却液喷向砂轮,然后在按操作规程进刀,修整好砂轮后退刀,将冷却液喷头转向工件位置。
4. 检查磨床的挡片,支片位置是否合理(如果调整不好,将会引起较大的形变误差)。
对于挡片可通过在机床不运转情况下,用手将工件沿着支片紧贴挡片前后推动,同时调整前后螺钉,直至工件能顺利、光滑推过为宜。
5. 按给定尺寸(Φd-0.02)调整机床,试磨五件工件,使得平均尺寸应保证在公差带中心稍偏下为宜,然后用贯穿法连续磨削一批零件,同时用比较仪,按磨削顺序测量零件尺寸并记录之。
6. 清理机床,收拾所用量具、工具等。
7. 整理实验数据,打印做实验报告。
五、实验结果及数据处理
该实验选用M1040A型无心磨床和块规一付
(1)实验原始数据
序号零件尺寸误差
(um) 序号零件尺寸误差
(um)
序号零件尺寸误差
(um)
1 -0.80 31 -0.84 61 -0.86
2 -0.75 32 -0.70 62 -0.80
3 -0.60 33 -0.78 63 -0.80
4 -0.4
5 34 -0.90 64 -0.81
5 -0.35 35 -0.80 65 -0.86
6 -0.38 36 -0.79 66 -0.87
7 -0.50 37 -0.82 67 -0.79
8 -0.48 38 -0.78 68 -0.79
9 -0.55 39 -0.72 69 -0.92
10 -0.58 40 -0.80 70 -0.82
11 -0.42 41 -0.76 71 -0.87
12 -0.50 42 -0.71 72 -0.84
13 -0.70 43 -0.80 73 -0.83
14 -0.52 44 -0.80 74 -0.89
15 -0.20 45 -0.79 75 -0.88
16 -0.85 46 -0.81 76 -0.90
17 -0.85 47 -0.82 77 -0.81
18 -0.86 48 -0.80 78 -0.91
19 -0.82 49 -0.80 79 -0.82
20 -0.82 50 -0.61 80 -0.89
21 -0.81 51 -0.76 81 -0.89
22 -0.80 52 -0.84 82 -0.91
23 -0.81 53 -0.85 83 -0.91
24 -0.84 54 -0.81 84 -0.90
25 -0.80 55 -0.86 85 -0.83
26 -0.80 56 -0.80 86 -0.87
27 -0.79 57 -0.80 87 -0.89
28 -0.77 58 -0.87 88 -0.81
29 -0.78 59 -0.88 89 -0.91
30 -0.80 60 -0.84 90
对以上的数据进行绘制图形,以工件序号为横坐标,相应的测量仪读数为纵坐标,依次点出每一工件的坐标值,并顺次连接各点成折线,
用两根平滑的曲线画出点子上的上、下限;然后在其中间画出平均曲线,即可分析加工误差的性质。
作图如下所示:
对所磨削的一批试件尺寸依次按每五个一组进行分组,并以横坐标表示分组的顺序号,以每组工件误差的平均值为纵坐标,同时把每组的极差R i=(x-x)i作为另一点的纵坐标,则可得到图.
在点图上取尺寸变化比较稳定(Δ变化的影响较小)的一段连续加工出的零件的尺寸作平行于纵坐标的直线,分组,
组别尺寸范围(mm)中点尺寸(mm)组内工件数频率(m/n)
1 26.950~26.951 26.9505 0 0
2
26.951~26.952 26.9505 24 24/90 3 26.952~26.953 26.9505 41 41/90 4 26.953~26.954 26.9505 21 21/90 5
26.954~26.955
26.9505
4
4/90
第一组:
m x n x n
i i μ011
_
==∑=
0)(112_
2
=-=∑=n
i i x x n σ
第二组:
mm x x n x i i n i i 952.262411241
1_
===∑∑== 0)(41)(1412_
12
_2
=-=-=∑∑==i i n i i x x x x n σ
第三组:
mm x x n x i i n i i 9524.26411141
1
1_
===∑∑==
73.3)(411)(1411
2_
12
_2
=-=-=∑∑==i i n i i x x x x n σ
第四组:
mm x x n x i i n i i 9532.26211121
1
1_
===∑∑== 2
72112_
12
_2
1054.1)(211)(1mm x x x x n i i n i i -==⨯=-=-=∑∑σ
第五组:
mm x x n x i i n i i
954.264114
1
1_
===
∑∑== =-=-=∑∑==412_12
_2
)(41)(1i i n i i x x x x n σ。