常压塔冷凝器设计
冷凝器设计
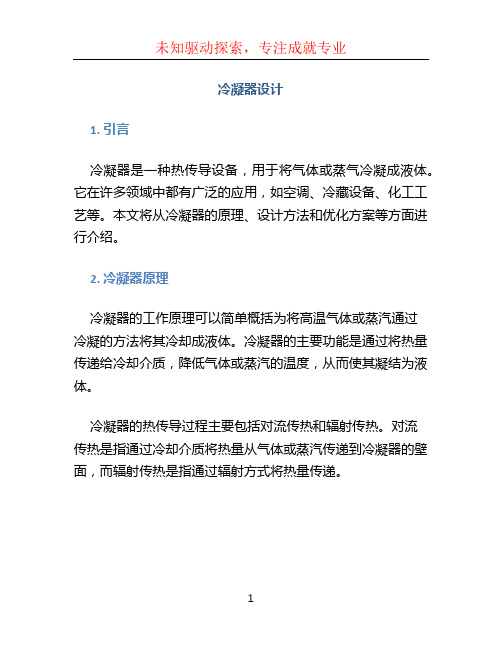
冷凝器设计1. 引言冷凝器是一种热传导设备,用于将气体或蒸气冷凝成液体。
它在许多领域中都有广泛的应用,如空调、冷藏设备、化工工艺等。
本文将从冷凝器的原理、设计方法和优化方案等方面进行介绍。
2. 冷凝器原理冷凝器的工作原理可以简单概括为将高温气体或蒸汽通过冷凝的方法将其冷却成液体。
冷凝器的主要功能是通过将热量传递给冷却介质,降低气体或蒸汽的温度,从而使其凝结为液体。
冷凝器的热传导过程主要包括对流传热和辐射传热。
对流传热是指通过冷却介质将热量从气体或蒸汽传递到冷凝器的壁面,而辐射传热是指通过辐射方式将热量传递。
3. 冷凝器设计方法3.1 冷凝器的类型常见的冷凝器类型主要包括管壳式冷凝器、管外冷凝器和冷凝器簇。
•管壳式冷凝器是将冷却介质和气体或蒸汽分开的一种结构,主要由壳体、管束和冷却介质组成。
•管外冷凝器是将冷却介质直接接触到气体或蒸汽的一种结构。
•冷凝器簇是多个冷凝器并联或串联连接在一起的一种结构。
3.2 冷凝器的设计参数冷凝器的设计参数包括冷凝器的换热面积、冷却介质的流速、冷凝温度差等。
根据不同的工况和要求,可以选择不同的设计参数。
3.3 冷凝器的换热计算换热计算是冷凝器设计的重要环节,主要包括冷却介质的传热系数和冷凝传热的计算。
•冷却介质的传热系数可以通过实验或流体力学计算得到。
•冷凝传热的计算可以通过传热方程和换热器表面积来进行。
4. 冷凝器优化方案在冷凝器设计过程中,为了提高冷凝效果和减小体积,可以采取一些优化措施。
4.1 改变冷凝器的结构通过改变冷凝器的结构,可以提高其换热效率。
例如采用多管道、螺旋管和多级蒸发器等结构。
4.2 优化冷却介质流动通过优化冷却介质的流动,如增加冷却介质的流速和改变流动方式,可以提高冷凝器的传热效果。
4.3 使用先进的材料选择合适的材料可以提高冷凝器的耐腐蚀性和传热性能。
5. 总结本文介绍了冷凝器的原理、设计方法和优化方案。
冷凝器设计涉及到多个方面的知识,需要综合考虑工况和要求,并根据实际情况进行优化。
大庆原油常压塔工艺的设计

大庆原油常压塔工艺的设计摘要本次设计主要是针对大庆原油常压塔的工艺设计。
中国加入WTO 后,石化市场日趋受到国外的严重冲击已是当今不争的事实,石化工业如何适应未来这种新的生产局面和参与市场竞争已经成为极为严重的问题;降低加工成本、提高经济效益、提高产品质量和开发高附加值的精细化工产品已成为当今中国石化工业所面临的紧要工作。
塔设备又是石油化工行业的重要设备,所以塔设备的质量至关重要。
如何扩能增效、节能降耗;如何改善塔的结构,提高塔效率,提高操作弹性。
这些都是塔设计人员所面临的新的研究和开发热点。
为了更好地提高原油的生产能力,本着投资少、能耗低、效益高的思想来对大庆原油进行常压塔工艺设计。
通过查阅相关文献,最终决定采用两段汽化流程。
此流程主要由一个脱盐脱水装置、一个初馏塔、一台常压炉、一个常压塔及若干台换热器、冷凝冷却器和机泵等组成。
原油首先进入脱盐脱水装置进行预处理,经预处理的原油再经换热升温至一定温度后即进入预设的初馏塔,在初馏塔中分馏出原油中最轻的馏分,初馏塔只取出一个塔顶产物作为重整原料;由初馏塔塔底抽出的液相部分再经进一步换热和在加热炉中加热至规定的温度,再进入常压塔,常压塔采取两侧线,塔顶生产汽油,两个侧线分别生产煤油和柴油,塔底馏出常压重油,可作为钢铁或其它工业的燃料,在某些特定的情况下也可以作为催化裂化或加氢裂化装置的原料。
本次设计主要着重对常压塔进行了设计,塔板采用浮阀塔板。
除此之外,此次设计还对常压塔进行了较为细致的分析。
本设计对工业生产也有一定的参考价值。
本设计采用1次中段回流,计算得到塔径为3.6米,塔板为25层,开孔率为23.61%,浮阀个数为2010个,热量利用率为63.55%。
关键词: 原油; 初馏塔; 常压塔; 浮阀塔板; 重整原料目录前言 (1)第一章、绪论 (3)1.1选题的依据 (3)1.2本课题在国内外的研究现状 (3)第二章、常压塔的设计方案 (5)2.1加工方案 (5)2.2塔及塔板的类型 (5)2.3回流方式 (5)2.4换热器 (6)2.5加热炉 (6)2.6工艺参数的确定 (6)第三章、原油的预处理 (7)3.1原油预处理的目的与作用 (7)3.2基本原理 (7)3.3原油预处理的主要途径 (7)第四章、工艺参数的设计计算 (8)4.1原料及产品有关参数的计算 (8)4.1.1基础数据 (8)4.1.2原油的有关数据计算 (10)4.1.3各馏出产品的有关数据计算 (12)4.2物料平衡 (17)4.3汽提水蒸气的用量 (17)4.4塔板数的确定 (17)4.5精馏塔计算草图 (18)4.6操作压力 (18)4.7汽化段温度 (19)4.8塔底温度 (20)4.9塔顶及侧线温度的假设与回流热的分配 (20)4.10侧线温度及塔顶温度的校核 (21)4.10.1柴油抽出板(第18层)温度 (21)4.10.2煤油抽出板(第9层)温度 (22)4.10.3塔顶温度 (24)4.11全塔的气液负荷分布 (25)4.11.1塔顶(第一块板上方)的气液负荷 (25)4.11.2第一层板下方的气液负荷 (25)4.11.3常一线抽出口下方(第9层板下方)的气液负荷 (26)4.11.4中段循环回流入口板上方的气液相负荷 (27)4.11.5中段循环回流抽出板下方的气液相负荷 (28)4.11.6煤油抽出板上方的气液相负荷 (29)4.11.7柴油抽出板上方的气液相负荷 (29)4.11.8各段气液相负荷列表 (30)第五章、塔设备的设计计算 (31)5.1塔径的初算 (31)5.2浮阀数及开孔率的计算 (33)5.2.1浮阀的选取 (33)5.2.2浮阀数及开孔率的计算 (33)5.3溢流堰及降液管的设计 (34)5.3.1液体在塔板上的流动型式 (34)5.3.2溢流堰的设计 (34)5.3.3溢流堰高度及塔板上清液层高度的设计 (34)5.3.4液体在降液管的停留时间及流速 (34)5.3.5降液管底缘距塔板高度 (35)5.4水力学计算 (35)5.4.1塔板压力降 (35)5.4.2雾沫夹带 (35)5.4.3泄漏 (36)5.4.4淹塔情况 (36)5.4.5降液管的负荷 (36)5.5塔板上的适宜操作区和负荷上、下限 (36)5.5.1雾沫夹带线 (36)5.5.2液泛线 (37)5.5.3液相负荷上限线 (37)5.5.4漏液线 (37)5.5.5液相负荷下限线 (38)5.6塔的内部工艺结构 (39)5.6.1塔顶 (39)5.6.2进口 (40)5.6.3抽出盘及出口 (40)5.6.4人孔 (40)5.6.5塔底 (40)5.6.6塔裙 (41)5.6.7封头 (41)5.7塔高 (41)第六章、换热流程 (42)6.1换热流程图 (42)6.2换热流程的计算 (42)6.2.1换热设备 (42)6.2.2中段回流作为热源 (44)6.2.3重油作为热源 (44)6.2.4冷后重油作为热源 (45)6.2.5柴油作为热源 (45)6.2.6塔顶冷凝器的计算 (46)6.2.7中段回流冷却 (46)6.3热量的利用率 (47)6.3.1各组分所提供的热量 (47)6.3.2原油所获得的热量 (47)6.3.3热量利用率 (47)结论 (48)符号表△T —温差,℃△F —实沸点蒸馏参考50%-平衡汽化参考线50%,℃D —温度校正值,℃ g —重力加速度,m 3/h M —分子量,g/mol Q —热量,kJ/h L —内回流,kg/h H i —焓值,kJ/kgL —液相负荷,kmol/h V —气相负荷,kmol/h ρ—密度,g/m 3σ—表面张力,达因/厘米 H t —板间距,mW a —气体操作速度,m/s K s —系统参数 K —安全参数F a —气相空间截面积,㎡V d —计算降液管内液体流速,m/s F d —降液管面积,㎡ D c —塔径,m(W h )C —阀孔临界速度,m/s Ф—开孔率 N —浮阀数,个 L —堰长,m W d —堰宽,m h w —堰高,mh ow —堰上液层高度,m h L —塔板上的清夜高度,mτ—液体在降液管的停留时间,m V d —降液管流速,m/sh b —降液管底缘距塔板高度,m △P d —干板压力降,米液柱ΔP VL —气体通过塔板上液层的压力降,米液柱V μ—蒸汽粘度,k g ·s/m 2V L —液相流量,m 3/s V V —气相流量,m 3/s F 0—阀孔动能因数 V —气速,m/sK —常数,取0.107; D —破沫网直径,m θ—气体流量,m 3/s H b —塔底空间,m H —塔高,m W c —流量,kg/h A —传热面积,㎡ µi —油品物性,cp K —总传热系数(以管外壁表面积为基准),kcal/㎡h ℃h i —管内流体的膜传热系数(以管外壁表面积为基准),kcal/㎡h ℃r i —管内流体的结构热阻(以管外壁表面积为基准),㎡h ℃/kcalr p —管子的热阻(一般金属管子可以忽略不计),㎡h ℃/kcalh 0—管外流体的膜传热系数(以管外壁表面积为基准),㎡h ℃/kcalr 0—管外流体的结垢热阻(以管外壁表面积为基准),㎡h ℃/kcald h —阀孔直径,m前言石油是重要的能源之一,我国的工业生产和经济运行都离不开石油,但是又不能直接作为产品使用,必须经过加工炼制过程,炼制成多种在质量上符合使用要求的石油产品,才能投入使用。
(能源化工行业)化工常压塔毕业设计

(能源化工行业)化工常压塔毕业设计摘要本设计为年产200万吨大庆原油的常压设计。
石油是现代工业的血液,我国的工业生产和经济运行都离不开石油,但是又不能直接作为产品使用,必须经过加工炼制过程,连制成多种在质量上符合使用要求的石油产品,才能投入使用。
原油常减压蒸馏作为原油的一次加工工艺,在原油加工总流程中占有重要作用,在炼厂具有举足轻重的地位,其运行的好坏直接影响到后续的加工过程。
其中重要的分离设备—常压塔的设计,是能否获得高收率、高质量油的关键。
近年来常减压蒸馏技术和管理经验不断创新,装置节能消耗显著,产品质量提高。
但与国外先进水平相比,仍存在较大的差距。
为了更好地提高原油的生产能力,本着投资少,能耗低,效益高的思想对大庆原油进行常压蒸馏设计。
设计的基本方案:设计了一个常压一段汽化蒸馏装置,此装置由一台管式加热炉、一个常压塔以及若干台换热器(完善的换热流程应达到要求:充分利用各种余热;换热器的换热强度较大;原油流动压力降较小。
)、冷凝冷却器、机泵等组成,在常压塔外侧为侧线产品设汽提塔。
流程简单,投资和操作费用较少。
原油通过这样的常压蒸馏,一般可得到350—370℃以前的几个馏分,可用作汽油、煤油(航空或灯用、)柴油等产品,也可分别作为重整化工(如轻油裂解)等装置的原料。
蒸余的塔底重油可作钢铁或其它工业的燃料。
在某些特定的情况下也可以作催化裂化或加氢裂化装置的原料。
关键词:原油;常压设计;换热;常压塔AbstractThis is mainly on the annual production of 2,000,000 tons of crude oil in Daqing atmospheric design.Oil is one important source of energy, China's industrial production and economic operation can not be separated from oil,But as the product can not be directly used, Refining the process must go through processing, and even made a variety of quality in line with the requirements of the use of petroleum products, can be put into use.Atmospheric and vacuum distillation of crude oil as a crude oil processing technology, the total flow of crude oil processed in an important role, In the refinery plays a decisive role in its operation will have a direct impact on the follow-up process.One of the important separation equipment - atmospheric tower design is the availability of high-yield, high-quality oil in the key.In recent years atmospheric and vacuum distillation technology and management experience continuous innovation, significant consumption of energy-savmpared with fing devices, improving product quality. However, cooreign advanced level, there are still large gaps.To better enhance the production capacity of crude oil, in a small investment, low energy consumption and high efficiency ofthe thinking of the Daqing oil for atmospheric distillation design.The basic design of the programme: design a section of vaporizationatmosphericdistillation unit,This device from a furnace official, a Taiwan atmospheric tower and a number of heat exchangers(Improve the heat transfer process should meet the requirements: the best use of waste heat; heat exchanger greater intensity of the heat exchanger; flow of oil pressure drop smaller.) Condensate cooler, Pump and other components, in the atmospheric tower adjacent to the lateral line products based stripper.Simple processes, investment and operational costs less.Crude oil through the atmospheric distillation, 350-370 ℃ before the general availability of several fractions,Can be used as gasoline, kerosene (aviation or lamp), diesel and other products, Also can be re-engineering as a chemical (such as naphtha cracking) of raw materials and other devices. I steamed the bottom of heavy oil for steel or other industrial fuel. In certain circumstances can also be FCC or hydrocracking unit of raw materials.Key words:oil pressure;Atmospheric design;Heat exchanger;Atmospheric tower目录前言 (1)一、物料衡算 (4)1.1 基准数据的处理 (4)1.1.1 基准数据 (4)1.1.2 数据处理 (5)1.1.3 求平衡汽化曲线各点温度 (6)1.2 各种馏出产品的性质 (7)1.2.1 各种馏出产品的基础数据 (7)1.2.2 各馏出产品的性质 (9)1.3 物料衡算 (10)二、塔的工艺参数的选取 (12)2.1 原油精馏塔计算草图求取 (12)2.1.1 确定蒸汽用量 (12)2.1.2 塔板型适合塔板数 (12)2.1.3 精馏塔计算草图: (12)2.1.4 操作压力的确定 (12)2.2 汽化段和塔底温度的确定 (13)2.2.1 汽化段温度 (13)2.2.2 进料在汽化段中的焓 (14)2.2.3.塔底温度 (14)三、塔顶及侧线温度的假设与回流热分配 (15)3.1 全塔回流热 (15)3.1.1 假设塔顶及各侧线温度 (15)3.1.2 全塔回流热 (15)3.1.3 流热分配 (15)3.2 侧线及塔顶温度的校 (16)3.2.1 柴油抽出板(第22层)温度 (16)3.2.2 煤油抽出板(第10层)温度 (17)3.2.3 塔顶温度 (18)四、塔设备的设计计算 (20)4.1 全塔气液负荷的分布计算 (20)4.1.1 塔顶(第一块板上方)的气液负荷 (20)4.1.2 第一层板下方的气液负荷 (20)4.1.3 常一线抽出口下方(即第10层下方)的气液负荷 (21)4.1.4 中段循环回流入口板上方的气液相负荷 (22)4.1.5 中段循环回流抽出板下方的气液相负荷 (23)4.1.6 煤油抽出板上方的气液相负荷 (24)4.1.7 柴油抽出板上方的气液相负荷 (24)4.1.8 汽化段气液相负荷 (25)4.2 各段气液相负荷列表 (26)五、常压塔和塔板主要工艺尺寸计算 (27)5.1 塔径的初算 (27)5.1.2 适宜的气体操作速度Wa (28)5.1.3 气相空间截面积Fa (28)5.1.4 计算降液管内液体流速Vd (28)5.1.5 计算降液管面积Fd (28)5.1.6 计算塔横截面和塔径 (29)5.1.7 采用塔径及相应的设计空塔气速 (29)5.1.8 液相的表面张力:(260.6℃时) (29)5.2 浮阀数及开孔率的计算 (29)5.2.1 浮阀的选取 (30)5.2.2 浮阀数及开孔率的计算 (30)5.3 溢流堰及降液管的决定 (30)5.3.1 决定液体在塔板上的流动型式 (30)5.3.2 决定溢流堰 (30)5.3.3 溢流堰高度及塔板上清夜层高度的决定 (31)5.3.4 液体在降液管的停留时间及流速 (31)5.3.5 降液管底缘距塔板高度 (31)5.4 水力学计算 (31)5.4.1 塔板压力降 (31)5.4.2 雾沫夹带 (31)5.4.3 泄漏 (32)5.4.4 淹塔情况 (32)5.4.5 降液管的负荷 (32)5.5 塔板的负荷性能图 (32)5.5.1 雾沫夹带线 (32)5.5.4 漏液线 (33)5.5.5 液相负荷下限线 (34)六、塔的内部工艺结构 (35)6.1 板式塔的部工艺结构 (35)6.1.1 塔顶 (35)6.1.2 进口 (35)6.1.3 抽出盘及出口 (36)6.1.4 人孔 (36)6.1.5 塔底 (36)6.1.6 塔裙 (37)6.1.7 封头 (37)6.2 塔高H (37)七、换热过程 (38)7.1 换热方案的确定 (38)7.1.1 换热的意义 (38)7.1.2 换热方案 (38)7.2 换热设备的选取和计算 (38)7.2.1 换热设备的计算 (38)7.2.2 中段回流作为热源 (40)7.2.3 重油作热源 (40)7.2.4 冷后重油作为作热源 (40)7.2.5 柴油作为热源 (41)7.2.6 塔顶冷凝器的计算 (41)7.2.7 中段回流冷却 (42)7.2.8各段换热所用的换热器型号列表如下 (42)7.3 热源利用率计算 (43)7.3.1 热源利用率计算: (43)7.3.2 原油提供热量计算 (43)7.3.3 热量利用率计算 (43)八、讨论 (44)致谢 (47)附录 (47)参考文献大庆原油常压设计前言中国炼油工业迅速发展,据美国《油气杂志》世界炼油特别报告统计,2005年中国原油年加工能力达3.12亿吨,超过俄罗斯和日本,成为仅次于美国的世界炼油大国。
冷凝器的设计步骤_解释说明
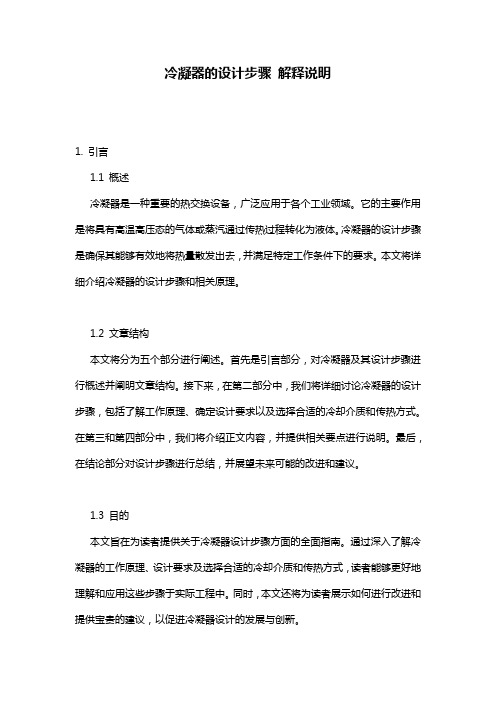
冷凝器的设计步骤解释说明1. 引言1.1 概述冷凝器是一种重要的热交换设备,广泛应用于各个工业领域。
它的主要作用是将具有高温高压态的气体或蒸汽通过传热过程转化为液体。
冷凝器的设计步骤是确保其能够有效地将热量散发出去,并满足特定工作条件下的要求。
本文将详细介绍冷凝器的设计步骤和相关原理。
1.2 文章结构本文将分为五个部分进行阐述。
首先是引言部分,对冷凝器及其设计步骤进行概述并阐明文章结构。
接下来,在第二部分中,我们将详细讨论冷凝器的设计步骤,包括了解工作原理、确定设计要求以及选择合适的冷却介质和传热方式。
在第三和第四部分中,我们将介绍正文内容,并提供相关要点进行说明。
最后,在结论部分对设计步骤进行总结,并展望未来可能的改进和建议。
1.3 目的本文旨在为读者提供关于冷凝器设计步骤方面的全面指南。
通过深入了解冷凝器的工作原理、设计要求及选择合适的冷却介质和传热方式,读者能够更好地理解和应用这些步骤于实际工程中。
同时,本文还将为读者展示如何进行改进和提供宝贵的建议,以促进冷凝器设计的发展与创新。
2. 冷凝器的设计步骤2.1 了解工作原理在进行冷凝器的设计之前,我们首先需要充分了解冷凝器的工作原理。
冷凝器是一种用于将气体或蒸汽转化为液体的热交换设备。
通过冷却和压缩气体或蒸汽,使其内部分子能量降低,从而实现相变为液体,并释放出大量热量。
2.2 确定设计要求确定设计要求是冷凝器设计过程中非常关键的一步。
在这一阶段,我们需要考虑以下因素:- 待处理气体的性质和特点:包括气体流量、温度、压力等参数。
- 冷凝器的使用环境:包括环境温度、环境压力等因素。
- 冷凝液排放方式:确定液态产物的排放方式,例如采用重力排放还是泵送排放等。
- 性能要求:根据应用需求确定效率、能耗等性能指标。
2.3 选择合适的冷却介质和传热方式在设计冷凝器时,我们需要选择合适的冷却介质和传热方式以达到预期效果。
常见的冷却介质包括空气、水和制冷剂等,而传热方式则有对流传热、辐射传热和传导传热等。
化工原理课程设计塔顶冷却器设计
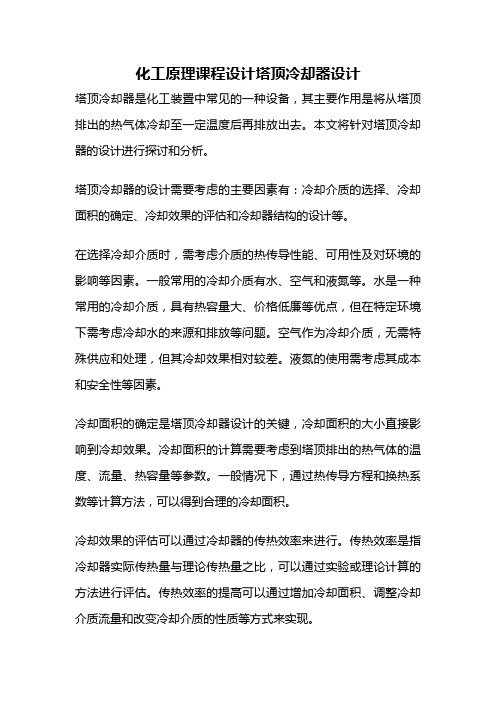
化工原理课程设计塔顶冷却器设计塔顶冷却器是化工装置中常见的一种设备,其主要作用是将从塔顶排出的热气体冷却至一定温度后再排放出去。
本文将针对塔顶冷却器的设计进行探讨和分析。
塔顶冷却器的设计需要考虑的主要因素有:冷却介质的选择、冷却面积的确定、冷却效果的评估和冷却器结构的设计等。
在选择冷却介质时,需考虑介质的热传导性能、可用性及对环境的影响等因素。
一般常用的冷却介质有水、空气和液氮等。
水是一种常用的冷却介质,具有热容量大、价格低廉等优点,但在特定环境下需考虑冷却水的来源和排放等问题。
空气作为冷却介质,无需特殊供应和处理,但其冷却效果相对较差。
液氮的使用需考虑其成本和安全性等因素。
冷却面积的确定是塔顶冷却器设计的关键,冷却面积的大小直接影响到冷却效果。
冷却面积的计算需要考虑到塔顶排出的热气体的温度、流量、热容量等参数。
一般情况下,通过热传导方程和换热系数等计算方法,可以得到合理的冷却面积。
冷却效果的评估可以通过冷却器的传热效率来进行。
传热效率是指冷却器实际传热量与理论传热量之比,可以通过实验或理论计算的方法进行评估。
传热效率的提高可以通过增加冷却面积、调整冷却介质流量和改变冷却介质的性质等方式来实现。
冷却器结构的设计需要考虑到冷却介质的流动方式、传热面积的布置和冷却器的材料选择等因素。
冷却介质的流动方式通常有直流和逆流两种方式,直流方式适用于冷却温度较高的情况,而逆流方式适用于要求更高的冷却效果的情况。
传热面积的布置可以采用管束式、板式或管壳式等结构形式,根据具体的工艺要求来选择。
冷却器的材料选择需考虑到介质的化学性质、温度和压力等因素,一般常用的材料有不锈钢、钛合金和铜等。
在塔顶冷却器的设计过程中还需要考虑到安全性和经济性等因素。
安全性是指冷却器在工作过程中不发生泄漏、爆炸等危险情况,需考虑到冷却介质的选择和处理、冷却器结构的强度和密封性等因素。
经济性是指在满足工艺要求的前提下,尽可能减少投资和运行成本,可以通过优化设计和合理使用资源等方式来实现。
冷凝器设计说明

冷凝器设计说明一、引言冷凝器是一种热交换设备,主要用于将气体或蒸汽冷凝成液体。
在各行各业的生产过程中,冷凝器起到了至关重要的作用。
本文将详细介绍冷凝器的设计原理和注意事项。
二、冷凝器的设计原理冷凝器的设计原理是基于热传导和传热的原理。
当高温气体或蒸汽进入冷凝器时,通过与冷却介质接触,热量会从气体或蒸汽传递到冷却介质中。
在这个过程中,气体或蒸汽会冷却下来,并逐渐凝结成液体。
三、冷凝器的设计要点1. 温度差:冷凝器的设计要考虑冷却介质与气体或蒸汽之间的温度差。
温度差越大,传热效果越好,但也会增加冷凝器的尺寸和成本。
2. 冷却面积:冷凝器的冷却面积需要足够大,以确保热量能够充分传递给冷却介质。
通常采用多管或片状结构来增加冷却面积。
3. 冷却介质:冷凝器的冷却介质可以是水、空气或其他液体。
选择合适的冷却介质需要考虑工艺要求、环境条件和能源消耗等因素。
4. 流速和压降:冷凝器的设计要合理控制流速和压降,以确保冷却介质能够充分流过冷凝器,并保持稳定的工作状态。
5. 材质选择:冷凝器的材质应具有良好的导热性和耐腐蚀性,以确保冷却介质和气体或蒸汽之间的有效传热。
四、冷凝器的类型1. 管壳式冷凝器:管壳式冷凝器由管束和外壳组成,冷却介质流过管束,气体或蒸汽流过管内。
这种冷凝器结构简单,传热效果好,广泛应用于化工、制药等行业。
2. 管板式冷凝器:管板式冷凝器由多个平行管板组成,冷却介质通过管板流过,气体或蒸汽流过管内。
这种冷凝器结构紧凑,适用于占地面积有限的场所。
3. 直接冷凝器:直接冷凝器是将冷凝介质直接喷洒在气体或蒸汽上,通过冷凝介质的蒸发吸收热量,实现冷凝。
这种冷凝器结构简单,传热效果好,适用于高温气体或蒸汽的冷凝。
4. 间接冷凝器:间接冷凝器是通过换热器将冷却介质与气体或蒸汽隔离,使其通过换热器壁传热。
这种冷凝器结构复杂,但可以避免冷却介质与气体或蒸汽直接接触,适用于对冷却介质有特殊要求的场合。
五、冷凝器的设计注意事项1. 设计合理的冷凝温度和冷却介质流量,以满足工艺要求。
化工常压塔毕业设计

化工常压塔毕业设计引言化工常压塔是化工工程中常用的设备之一,广泛应用于化学工艺过程中的物质分离、纯化和反应等操作。
在化工领域,常压塔的设计与优化是一个重要的研究方向,对于提高生产效率、降低能耗和保护环境具有重要意义。
本文将介绍化工常压塔的毕业设计内容,包括设计目的、设计流程、设计参数和实施方案。
设计目的本次毕业设计的目的是设计一个高效、节能的化工常压塔,以满足某化工厂某项特定工艺操作的需求。
该常压塔需要具备较高的分离效果、较低的压降、合理的结构和操作参数。
通过优化设计,实现工艺操作的稳定性和可持续发展。
设计流程1.工艺分析:首先,进行工艺分析,确定化工过程中的物质分离、纯化或反应等操作。
考虑原料特性、产品要求和工艺条件等因素,确定设计的基本要求。
2.塔床设计:根据物质分离的需求和操作条件,选择合适的塔床类型。
根据传质与传质的要求,确定塔床板间距、开孔率和塔板类型。
通过计算和模拟,确定塔床的高度和板间流动参数。
3.填料选择:根据物料特性、传质效果和操作要求,选择适合的填料材料。
考虑填料的表面积、孔隙率和形状等因素,确定填料层的高度和数量。
4.塔壳设计:根据操作压力、温度和塔内操作条件等因素,选择合适的材料和厚度,设计符合安全标准的塔壳结构。
5.流体力学分析:通过计算和模拟,确定塔床和填料层的流体力学性能,包括塔床液体和气体的流量、压降和分布等参数。
6.操作参数确定:根据设计结果和操作要求,确定塔床液体和气体的操作参数,如进料流量、温度、压力和分离效果等。
7.实施方案:根据前面的设计结果和参数,制定实施方案,包括材料采购、设备安装和调试等工作。
设计参数在本次毕业设计中,需要确定以下设计参数:1.塔高:根据分离要求和塔床板间距,确定塔的总高度。
2.塔床类型:根据传质和操作要求,选择塔床的类型。
3.塔床板间距:根据物料特性和传质效果,确定塔床板的间距。
4.塔床液体和气体流量:根据操作要求和塔床板的流体力学性能,确定塔床液体和气体的流量。
冷凝器设计计算范文
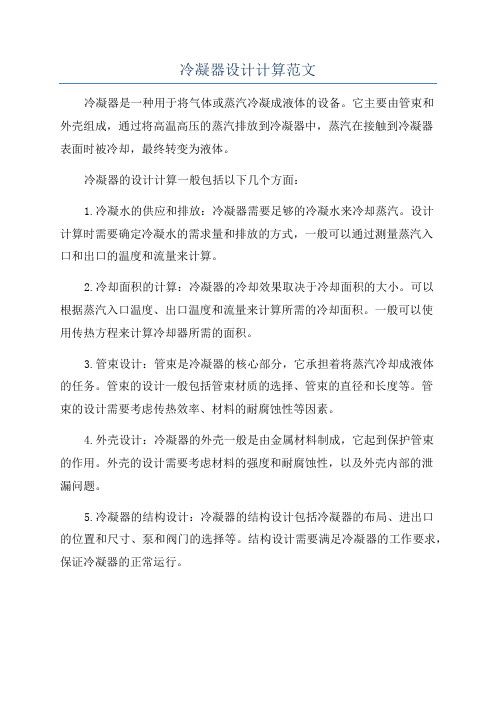
冷凝器设计计算范文
冷凝器是一种用于将气体或蒸汽冷凝成液体的设备。
它主要由管束和
外壳组成,通过将高温高压的蒸汽排放到冷凝器中,蒸汽在接触到冷凝器
表面时被冷却,最终转变为液体。
冷凝器的设计计算一般包括以下几个方面:
1.冷凝水的供应和排放:冷凝器需要足够的冷凝水来冷却蒸汽。
设计
计算时需要确定冷凝水的需求量和排放的方式,一般可以通过测量蒸汽入
口和出口的温度和流量来计算。
2.冷却面积的计算:冷凝器的冷却效果取决于冷却面积的大小。
可以
根据蒸汽入口温度、出口温度和流量来计算所需的冷却面积。
一般可以使
用传热方程来计算冷却器所需的面积。
3.管束设计:管束是冷凝器的核心部分,它承担着将蒸汽冷却成液体
的任务。
管束的设计一般包括管束材质的选择、管束的直径和长度等。
管
束的设计需要考虑传热效率、材料的耐腐蚀性等因素。
4.外壳设计:冷凝器的外壳一般是由金属材料制成,它起到保护管束
的作用。
外壳的设计需要考虑材料的强度和耐腐蚀性,以及外壳内部的泄
漏问题。
5.冷凝器的结构设计:冷凝器的结构设计包括冷凝器的布局、进出口
的位置和尺寸、泵和阀门的选择等。
结构设计需要满足冷凝器的工作要求,保证冷凝器的正常运行。
除了上述的设计计算,冷凝器的安装和维护也是关键的环节。
冷凝器通常需要定期清洗和检查,以保证其正常的工作。
此外,冷凝器的设计和使用也需要考虑环保因素,减少对环境的污染。
塔顶冷凝器的合理化设计
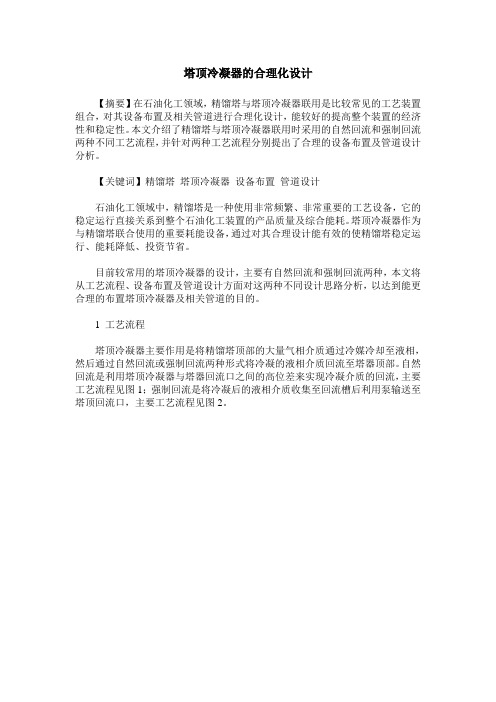
塔顶冷凝器的合理化设计【摘要】在石油化工领域,精馏塔与塔顶冷凝器联用是比较常见的工艺装置组合,对其设备布置及相关管道进行合理化设计,能较好的提高整个装置的经济性和稳定性。
本文介绍了精馏塔与塔顶冷凝器联用时采用的自然回流和强制回流两种不同工艺流程,并针对两种工艺流程分别提出了合理的设备布置及管道设计分析。
【关键词】精馏塔塔顶冷凝器设备布置管道设计石油化工领域中,精馏塔是一种使用非常频繁、非常重要的工艺设备,它的稳定运行直接关系到整个石油化工装置的产品质量及综合能耗。
塔顶冷凝器作为与精馏塔联合使用的重要耗能设备,通过对其合理设计能有效的使精馏塔稳定运行、能耗降低、投资节省。
目前较常用的塔顶冷凝器的设计,主要有自然回流和强制回流两种,本文将从工艺流程、设备布置及管道设计方面对这两种不同设计思路分析,以达到能更合理的布置塔顶冷凝器及相关管道的目的。
1 工艺流程塔顶冷凝器主要作用是将精馏塔顶部的大量气相介质通过冷媒冷却至液相,然后通过自然回流或强制回流两种形式将冷凝的液相介质回流至塔器顶部。
自然回流是利用塔顶冷凝器与塔器回流口之间的高位差来实现冷凝介质的回流,主要工艺流程见图1;强制回流是将冷凝后的液相介质收集至回流槽后利用泵输送至塔顶回流口,主要工艺流程见图2。
比较两种工艺流程不难发现,自然回流因为采用设备本身的位差来推动液相介质回流,不需要增加塔顶回流槽和回流泵设备,在工艺上具有能耗低和节省设备投资的优点。
但是,能否就此下结论说,塔顶冷凝器采用自然回流的设计形式比强制回流更先进实用呢?对此,我们需要对不同回流方式的设备布置进行更进一部的分析。
2 设备布置对于两种不同的工艺流程,我们需要分别采用不同的设备布置形式。
自然回流,由于其利用位差来输送冷凝的液相介质回流,因此塔顶冷凝器的布置标高必然要高于精馏塔顶部标高,否则无法产生足够的输送动力;强制回流,由于其采用泵提供输送动力来使冷凝的液相介质回流,因此塔顶冷凝器的布置标高只需高于塔顶回流罐及回流泵,可以低于精馏塔顶部标高,放置于建构筑物任意位置。
常减压装置常压塔区以及常压冷换构架区管道设计
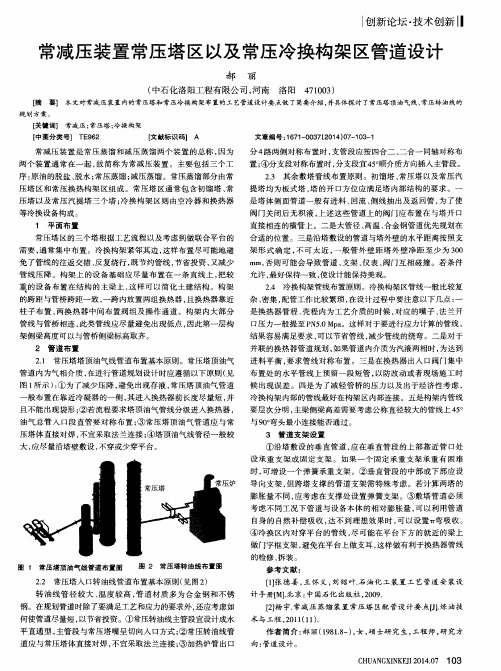
两个装 置通常 在一起 , 故简称 为常减压 装置 。主要 包括 三个工
序: 原油的脱盐 、 脱水; 常压蒸馏 ; 减压蒸馏 。常压蒸馏部分 由常 压塔 区和常压 换热构架 区组成 。常压塔 区通常包含 初馏塔 、 常 压塔 以及 常压 汽提塔 三个塔 ; 冷换构 架区则 由空冷器 和换热器
一
进料平衡 , 要求 管线对称 布置 。三是 在换热器 出入 口阀 门集 中
布置处 的水平 管线上预 留一段短管 , 以防改动或者现场 施工时 候出现误 差。 四是 为了减轻管桥 的压力 以及 出于经济性考 虑 ,
冷 换 构 架 内部 的管 线 最 好 在 构 架 区 内部 连 接 。五 是 构 架 内管 线
柱 子布 置 , 两换 热器 中间布置 阀组及操作 通道 。构 架 内大部分 管线 与管桥相连 , 此 类管线应尽量避免 出现低点 , 因此第一层构 架侧 梁高度可以与管桥侧梁标 高取齐 。
2 管道布置
2 . 1 常压塔塔顶油气线管道布置基本原则 。常压塔顶油气
管道 内为气相介质 为了减少压 降 , 避免 出现存液 , 常压塔顶油气 管道
要层次分明 , 主梁侧梁 高差需要 考虑公称 直径较大 的管线上 4 5 。 与9 0 。 弯 头最小连接能否通过 。 3 管道支架设置 ①沿塔敷 设的垂直 管道 , 应在垂直 管段的上部靠 近管 口处
设 承 重 支 架 或 固 定 支 架 。 如 果 一 个 固 定 承 重 支 架 承 重 有 困难
2 . 2 常压塔入 口转油线管道布置基本原则 ( 见图2 )
塔顶直连冷凝器布置设计

2020,30(5)张传武等 塔顶直连冷凝器布置设计 塔顶直连冷凝器布置设计张传武 肖 桓 华陆工程科技有限责任公司 西安 710065摘要 本文通过工程实例,根据塔顶直连冷凝器工艺介质参数、外形特征、工艺特点等内容,提出设备布置要点;针对不同设备布置结构形式,从设备吊装、检修、操作、应力消除等方面综合考虑,对直连式塔顶冷凝器布置进行优化设计探讨。
关键词 塔 塔顶冷凝器 弹性支撑 热位移张传武:工程师。
2009年毕业于西安交通大学过程装备与控制工程专业。
从事化工设备布置与配管设计工作。
联系电话:13474064568,E-mail:zcw2277@chinahualueng com。
塔与塔顶冷凝器是化工生产过程中的重要生产设备,是产品精制、分离过程中的典型工艺设备组合装置。
直连式塔顶冷凝器在塔顶高回流比、阻力降较敏感系统等特殊工况下,因其布置上的优势而经常被使用。
因此,其优化合理的设备布置非常重要。
1 塔顶直连冷凝器分类塔顶直连冷凝器根据冷凝器的型式不同,一般分为立式和卧式两种类型,见图1、图2。
图1 立式塔顶直连冷凝器图2 卧式塔顶直连冷凝器立式塔顶直连冷凝器因换热面积受塔的直径、塔顶压降等参数的限制,塔顶气相量较小时一般采用立式塔顶直连冷凝器;相比立式塔顶直连冷凝器而言,卧式塔顶直连冷凝器的换热面积不受塔的直径和塔顶压降等参数的影响,因此换热面积相对较大,换热效率会相对较高,塔顶气相量较大时一般采用卧式。
2 塔顶直连式冷凝器布置特点2 1 立式塔顶直连冷凝器布置立式塔顶直连冷凝器与塔顶管口采用法兰连接,整个冷凝器的荷载垂直作用于塔体,布置初期需设备专业提前对塔的壁厚、裙座的受力和地脚螺栓的强度进行核算确认。
一般立式塔顶直连冷凝器更适合独立塔安装布置设计。
2 2 卧式塔顶直连冷凝器布置卧式塔顶直连冷凝器与塔顶管口既可以采用法兰也可以采用焊接型式连接,当采用独立塔安装布置时,整个冷凝器的荷载垂直作用于塔体,布置初期需设备专业提前对塔的壁厚、裙座的受力和地脚螺栓的强度、冷凝器支撑稳定性进行核算确认;当采用框架式塔安装布置设计利用框架来支撑冷凝器时,由于塔的热位移,冷凝器需要使用弹簧或者气缸等弹性支撑。
HTRI设计实例-最实用的初学者入门教材
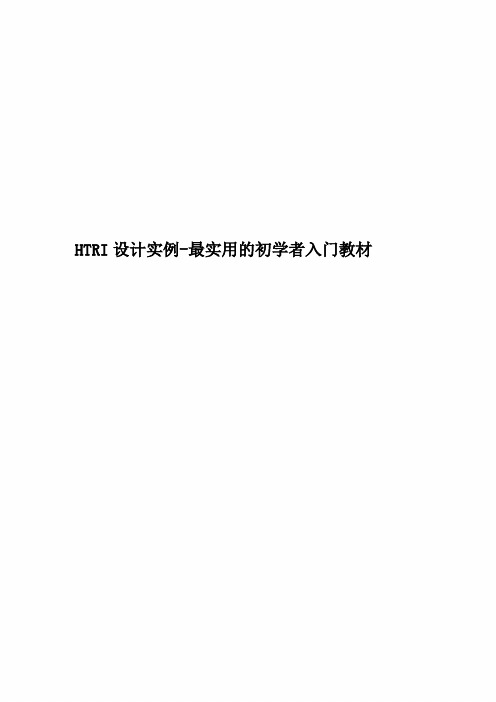
HTRI设计实例-最实用的初学者入门教材HTRI设计实例-最实用的初学者入门教材目录第1章前言 (1)1.1 课题研究背景及意义 (1)1.2 换热器简介 (2)1.2.1 换热器分类 (2)1.2.2 管壳式换热器的结构和使用特点 (3)第2章冷凝器设计 (9)2.1 冷凝器选型 (9)2.1.1 饱和蒸汽冷凝 (9)2.1.2 含不凝气的冷凝冷却过程 (9)2.1.3 安装注意事项 (10)2.2 冷凝器设计依据 (10)2.2.1 管壳式冷凝器类型的选择 (10)2.2.2 换热器合理压降的选择 (11)2.2.3 工艺条件经验温度的选择 (11)2.2.4 管长 (12)2.2.5 管径与管壁 (12)2.2.6 折流板圆缺高度 (12)2.2.7 折流板间距 (13)2.2.8 密封条 (13)2.3 HTRI设计判据 (13)2.3.1 管壳侧流速(velocity) (13)2.3.2 设计余量(overdesign) (14)2.3.3热阻(thermal resistance) (14)2.3.4流型(flow fraction) (14)2.3.5 Window and crossflow (15)2.3.6 常见warning message及解决方法 (15)2.4 HTRI设计实例(HTRI6.0计算) (17)2.4.1 饱和蒸汽的冷凝 (17)2.4.2 含有不凝气的气体冷凝 (34)2.4.3 油气冷凝冷却 (45)第3章结论 (67)3.1 饱和蒸汽冷凝冷凝器数据 (67)3.1.1 饱和蒸汽冷凝器结构数据 (67)3.1.2 饱和蒸汽冷凝器工艺数据 (68)3.2 含不凝气的蒸汽冷凝冷凝器数据 (68)3.2.1 含不凝气的蒸汽冷凝器结构数据 (68)3.2.2 含不凝气的蒸汽冷凝器工艺数据 (69)3.3 油气冷凝冷却冷凝器数据 (70)3.3.1 油气冷凝冷却冷凝器结构数据 (70)3.3.2 油气冷凝冷却冷凝器工艺数据 (71)致谢错误!未定义书签。
冷凝器设计
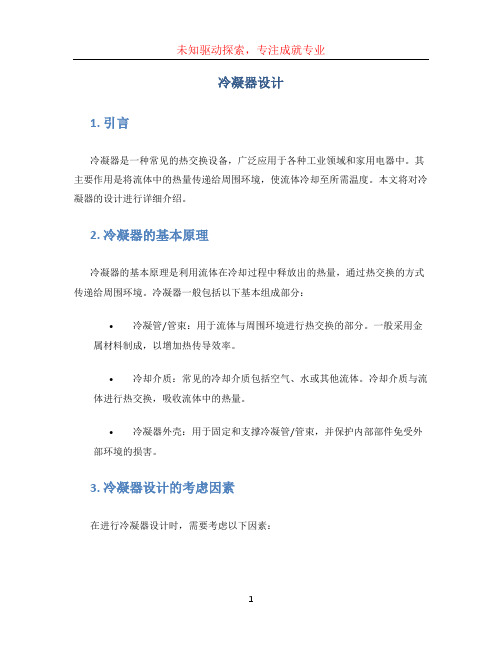
冷凝器设计1. 引言冷凝器是一种常见的热交换设备,广泛应用于各种工业领域和家用电器中。
其主要作用是将流体中的热量传递给周围环境,使流体冷却至所需温度。
本文将对冷凝器的设计进行详细介绍。
2. 冷凝器的基本原理冷凝器的基本原理是利用流体在冷却过程中释放出的热量,通过热交换的方式传递给周围环境。
冷凝器一般包括以下基本组成部分:•冷凝管/管束:用于流体与周围环境进行热交换的部分。
一般采用金属材料制成,以增加热传导效率。
•冷却介质:常见的冷却介质包括空气、水或其他流体。
冷却介质与流体进行热交换,吸收流体中的热量。
•冷凝器外壳:用于固定和支撑冷凝管/管束,并保护内部部件免受外部环境的损害。
3. 冷凝器设计的考虑因素在进行冷凝器设计时,需要考虑以下因素:3.1 热量传递效率冷凝器的热量传递效率直接影响到冷却过程的速度和效果。
为了提高热量传递效率,可以采取以下措施:•增加冷凝管/管束的长度和表面积,增大热交换面积。
•优化冷却介质的流动方式,增加流体与冷却介质的接触面积。
•选择热传导性能较好的材料,提高热传导效率。
3.2 流体特性不同的流体具有不同的物理特性,包括流体的流动性、热导率、热容量等。
在冷凝器设计时,需要考虑流体的特性,以确定合适的流体流动速度和冷却介质的温度。
3.3 冷却介质选择冷却介质的选择取决于具体的应用需求。
常见的冷却介质有空气、水和其他流体。
根据不同的应用环境和要求,选择合适的冷却介质进行冷却。
3.4 设计材料选择冷凝器的设计材料需要具备良好的耐腐蚀性和热传导性能。
常见的冷凝器材料包括铜、铝和不锈钢等。
根据实际应用情况选择合适的设计材料。
4. 冷凝器设计流程冷凝器的设计流程一般包括以下步骤:4.1 确定冷凝器的应用需求根据实际应用需求,确定冷凝器的工作温度范围、流量要求等参数。
了解冷凝器所处的环境条件,以便选择合适的材料和冷却介质。
4.2 确定冷凝器的结构形式根据应用需求和空间限制,确定冷凝器的结构形式,包括冷凝管/管束的布置方式、冷凝器的外形尺寸等。
【优秀毕设】年处理量940万吨常减压装置常压塔工艺设计...

毕业设计(论文)说明书题目常减压装置常压塔工艺设计院别:辽宁石化职业技术学院专业:化学工程与工艺班级:化工102设计人:韩兵兵指导教师:**毕业设计(论文)任务书一、题目:常减压装置常压塔工艺设计二、基础数据1.原料辽河混合原油。
2.处理量: 940 万吨/年。
3.年工作时间:8000小时。
4.原油性质。
见附表。
5.产品方案及产品规格:见附表。
表1 原油实沸点蒸馏馏份油收率及累计收率组分产品切割温度℃收率%(质量) 累积收率%(质量)1 汽油初馏点-130 2.52 2.522 航煤130-230 5.02 7.543 轻柴油230-320 12.3 19.844 重柴油320-350 2.9 22.745 常重油>350 76.96 76.966 损失0.3 0.3合计100表2 原油及直馏产品性质汇总表物料相对密度原油及产品恩式蒸馏数据0% 10% 30% 50% 70& 90% 100% 汽油0.7396 50 82 98 108 117 139 148 航煤0.7784140 153 165 171 187 199 220 轻柴油0.8582 195 231 254 272 301 338 355 重柴油0.9057 279 315 388 413 433 453 465 常重油0.9560原油0.9258256 332 380 415拔头油0.9366说明:1.脱盐后原油含水:0.3%;2.原油含总硫%(质量分数):0.33%;3.原油酸值mg KOH/g:4.144.初馏塔汽油产率为汽油总产率的70%。
5. 原油特性因数K=11.7三、内容要求:1. 说明部分:(1)装置的概括和特点。
(2)生产流程方案的确定。
(3)工艺流程的概述。
(4)主要设备简介。
(5)能耗指标。
(6)设备汇总表。
(7)存在问题与设想。
2. 计算部分:(1)物料衡算。
(2)热量衡算。
(3)确定操作条件。
冷凝器设计说明方案

摘要根据设计条件,依据GB151和GB150及相关规范,对卧式壳程冷凝器进行了工艺计算,结构计算和强度计算。
工艺计算部分主要是根据给定的设计条件估算换热面积,从而进行冷凝器的选型,校核传热系数,计算出实际的换热面积,最后进行压力降和壁温的计算。
结构和强度的设计主要是根据已经选定的冷凝器型式进行设备内各零部件(如接管、折流板、定距管、管箱等)的设计,包括:材料的选择、具体尺寸确定、确定具体位置、管板的计算、法兰的计算、开孔补强计算等。
最后设计结果再通过装配图零件图等表现出来。
关于卧式壳程冷凝器设计的各个环节,设计说明书中都有详细的说明。
关键词:管壳式换热器卧式壳程冷凝器管板法兰AbstractAccording to the design condition, GB151 and GB150 and related norms, design a horizontal shell condenser, which included technology calculate of condenser, the structure and intensity of condenser.The technology calculation process. Mainly, the process of technology calculate is according to the given design conditions to estimate the heat exchanger area, and then, select a suitable condenser to check heat transfer coefficient ,just for the actual heat transfer area .Meanwhile the process above still include the pressure drop and wall temperature calculation . The design is about the structure and intensity of the design. This part is just on the selected type of condenser to design the condenser’s components and parts ,such as vesting ,baffled plates, the distance control tube, tube boxes. This part of design mainly include:the choice of materials,identify specific size, identify specific location, the thickness calculation of tube sheet, the thickness calculation of flange, the opening reinforcement calculation etc. In the end, the final design results through assembly drawing and parts drawing to display.The each aspects of the horizontal shell condenser has detailed instructions in the design manual.Key word: Shell-Tube heat exchanger; Horizontal shell condenser; Tube sheet; Flange.目录摘要 (I)Abstract (II)第1章绪论 (1)1.1 冷凝器概述 (1)1.2 冷凝器类型 (1)1.2.1 卧式壳程冷凝器 (1)1.2.2 卧式管程冷凝器 (2)1.2.3 立式壳程冷凝器 (2)1.2.4 管内向下流动的立式管程冷凝器 (3)1.2.5 向上流动的立式管程冷凝器 (3)第2章工艺计算 (5)2.1 设计条件 (5)2.2 确定物性数据 (5)2.3 冷凝器的类型与流动空间的确定 (5)2.4 未考虑冬季因素 (5)2.4.1 估算传热面积 (5)2.4.2 选工艺尺寸计算 (7)2.4.3 冷凝器核算 (10)2.5 冬季因素考虑 (17)2.6 综合考虑 (18)2.6.1 估算传热面积 (19)2.6.2 选工艺尺寸计算 (19)2.6.3 冷凝器核算 (20)2.7 换热器主要结构尺寸和计算结果 (25)第3章结构设计 (26)3.1 壳体、管箱壳体和封头的设计 (26)3.1.1 壁厚的确定 (26)3.1.2 管箱壳体壁厚的确定 (27)3.1.3 标准椭圆封头的设计 (27)3.2 管板与换热管设计 (28)3.2.1 管板 (28)3.2.2 换热管 (29)3.3 进出口设计 (30)3.3.1 接管的设计 (30)3.3.2 接管外伸长度 (30)3.3.3 排气、排液管 (30)3.3.4 接管最小位置 (31)3.4 折流板或支持板 (32)3.4.1 折流板尺寸 (32)3.4.2 折流板和折流板孔径 (32)3.4.3 折流板的布置 (33)3.5 防冲挡板 (34)3.6 拉杆与定距管 (34)3.6.1 拉杆的结构和尺寸 (34)3.6.2 拉杆的位置 (35)3.6.3 定距管尺寸 (35)3.7 鞍座选用及安装位置确定 (35)第4章强度计算 (36)4.1 壳体、管箱壳体和封头校核 (36)4.1.1 壳体体校核 (36)4.1.2 管箱壳体校核 (36)4.1.3 椭圆封头校核 (37)4.2 接管开孔补强 (37)4.2.1 蒸汽进出口开孔补强 (37)4.2.2 管箱冷却水接管补强的校核 (39)4.3 膨胀节 (40)4.3.1 膨胀节 (41)4.3.2 膨胀节计算 (41)4.4 管板校核 (43)4.4.1 结构尺寸参数 (43)4.4.2 各元件材料及其设计数据 (43)4.4.3 管子许用应力 (44)4.4.4 结构参数计算 (45)4.4.5 法兰力矩 (46)4.4.6 换热管与壳体圆筒的热膨胀应变形差 (46)4.4.7 管箱圆筒与法兰的旋转刚度参数 (46)4.4.8 管子加强系数 (47)4.4.9 旋转刚度无量纲参数 (47)4.4.10 设计条件不同危险组合工况的应力计算 (48)4.4.11 四种危险工况的各种应力计算与校核: (50)4.5 设计值总汇 (52)第5章安装使用及维修 (53)5.1 安装 (53)5.2 维护和检修 (53)结论 (56)参考文献 (57)第1章绪论1.1 冷凝器概述在蒸馏过程中,把蒸气转变成液态的装置称为冷凝器[1]。
冷凝器设计计算步骤
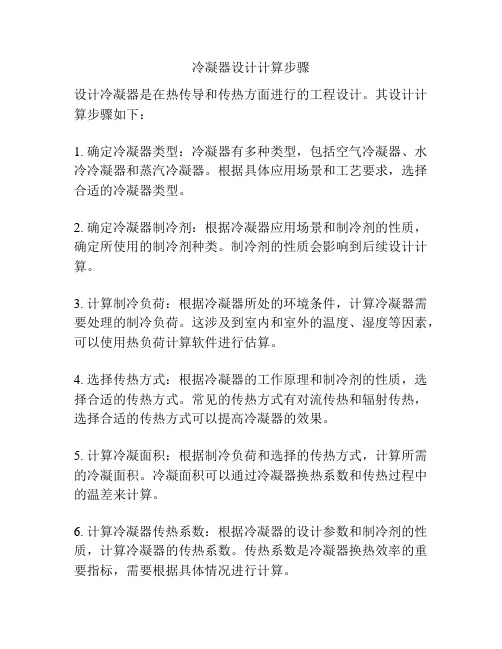
冷凝器设计计算步骤设计冷凝器是在热传导和传热方面进行的工程设计。
其设计计算步骤如下:1. 确定冷凝器类型:冷凝器有多种类型,包括空气冷凝器、水冷冷凝器和蒸汽冷凝器。
根据具体应用场景和工艺要求,选择合适的冷凝器类型。
2. 确定冷凝器制冷剂:根据冷凝器应用场景和制冷剂的性质,确定所使用的制冷剂种类。
制冷剂的性质会影响到后续设计计算。
3. 计算制冷负荷:根据冷凝器所处的环境条件,计算冷凝器需要处理的制冷负荷。
这涉及到室内和室外的温度、湿度等因素,可以使用热负荷计算软件进行估算。
4. 选择传热方式:根据冷凝器的工作原理和制冷剂的性质,选择合适的传热方式。
常见的传热方式有对流传热和辐射传热,选择合适的传热方式可以提高冷凝器的效果。
5. 计算冷凝面积:根据制冷负荷和选择的传热方式,计算所需的冷凝面积。
冷凝面积可以通过冷凝器换热系数和传热过程中的温差来计算。
6. 计算冷凝器传热系数:根据冷凝器的设计参数和制冷剂的性质,计算冷凝器的传热系数。
传热系数是冷凝器换热效率的重要指标,需要根据具体情况进行计算。
7. 选择冷凝水边界条件:根据冷凝器的设计要求,选择合适的冷凝水边界条件。
这包括冷凝水的进口温度、流量和压力等参数,需要保证冷凝水的供给能够满足冷凝器的实际工作需求。
8. 进行热力学计算:根据所选的制冷剂和制冷负荷,进行热力学计算。
这包括冷凝过程中的温度、压力和比焓等参数的计算,可以使用热力学软件进行准确的计算。
9. 进行传热计算:根据冷凝器的设计参数和制冷剂的性质,进行传热计算。
这包括冷凝器的传热面积、传热系数和传热量等参数的计算。
10. 进行流体力学计算:根据冷凝器的设计参数和制冷水的性质,进行流体力学计算。
这包括冷凝器内部的流体流动情况、压力损失和水力不平衡等参数的计算。
以上是设计冷凝器的一般步骤,具体的计算方法和参数选择需要根据具体的应用情况和设计要求进行调整。
对于特定的冷凝器设计,可能还需要考虑其他因素,如材料选择、结构设计和安装要求等。
常压塔冷凝器设计
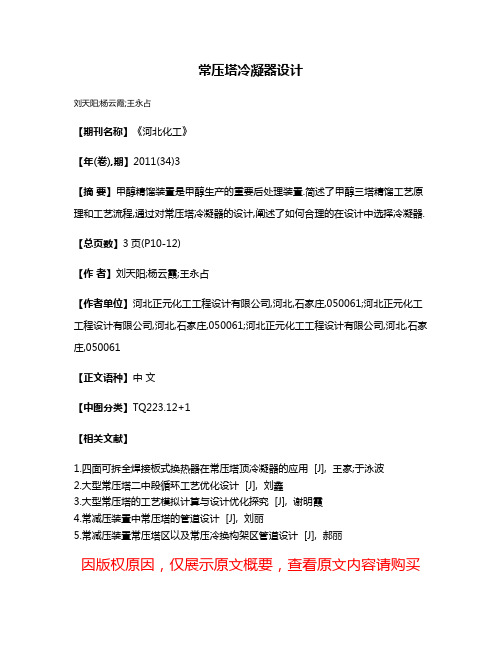
常压塔冷凝器设计
刘天阳;杨云霞;王永占
【期刊名称】《河北化工》
【年(卷),期】2011(34)3
【摘要】甲醇精馏装置是甲醇生产的重要后处理装置.简述了甲醇三塔精馏工艺原理和工艺流程,通过对常压塔冷凝器的设计,阐述了如何合理的在设计中选择冷凝器.【总页数】3页(P10-12)
【作者】刘天阳;杨云霞;王永占
【作者单位】河北正元化工工程设计有限公司,河北,石家庄,050061;河北正元化工工程设计有限公司,河北,石家庄,050061;河北正元化工工程设计有限公司,河北,石家庄,050061
【正文语种】中文
【中图分类】TQ223.12+1
【相关文献】
1.四面可拆全焊接板式换热器在常压塔顶冷凝器的应用 [J], 王家;于泳波
2.大型常压塔二中段循环工艺优化设计 [J], 刘鑫
3.大型常压塔的工艺模拟计算与设计优化探究 [J], 谢明霞
4.常减压装置中常压塔的管道设计 [J], 刘丽
5.常减压装置常压塔区以及常压冷换构架区管道设计 [J], 郝丽
因版权原因,仅展示原文概要,查看原文内容请购买。
(完整版)常压塔毕业设计

摘要常压塔是石油加工中重要的流程之一,这次的设计主要就是对125万吨年处理量的原油常压塔进行设计,其中包括塔板的设计。
常压塔的设计主要是依据所给的原油实沸点蒸馏数据及产品的恩氏蒸馏数据,计算产品的相关物性数据从而确定切割方案、计算产品收率。
参考同类装置确定塔板数,进料及侧线抽出位置,再假设各主要部位的操作温度及操作压力,进行全塔热平衡计算。
采取塔顶二级冷凝冷却和两个中段回流,塔顶取热、第一中段回流取热、第二中段回流取热的比依次为5:2:3。
经过校核各主要部位温度都在允许的误差范围内。
塔板型式选用F型重阀浮阀塔板,依据常压塔内最大气、液相负荷算得塔板外径为3.0m,板间距为0.45m。
这部分最主要的是核算塔板流体力学性能及操作性能,使塔板在适宜的操作范围内操作。
本次设计的结果表明,参数的校核结果与假设值间的误差在允许范围内,其余均在经验值范围内,因此可以确定,该蒸馏塔的设计是符合要求的。
关键词:常压塔,浮阀塔板,流体力学。
AbstractAtmospheric distillation of petroleum processing is one of important processes .A atmosperic distillation column ,which is able to treat crucd oil 125Mt a year ,is designed mainly ,including the design of plate.The design of atmosperic distillation column is based on the datum of true point distillation of the oil and of Engler distilltion of the products. The calculation of products phsical property parameters and the cut conceptual and products yields are also dased on the datum. The tray number ,the feed tray and the side stream withdrawal tray are determined by referring to the same king unit .The following work is to assume the operating temperature and pressure of all the imporant points of the column and to make the energy balance calculation for the whole column. To take the top two cooling and condensing , the two back to the middle and the top the range of allowable error.A type of Fvalve tary is be chosen .Atmospheric tower based on the most gas, liquid external diameter of the load tray can be 3.0m, plate spacing of 0.45m. In this section , The most important work is to calculate the a proper area .The design results show that the results of parameter calibration values and assumptions of the error are in the allowable range, and the remaining values are in the range of experience, so it can be identified that the distillation column designed meets the requirements.Key word :Atmospheric distillating column ,valve tray ,-1—COOH)。
年处理量420万吨常减压装置常压塔工艺设计

年处理量420万吨常减压装置常压塔工艺设计北京化工大学毕业设计(论文)题目:年处理量420万吨常减压蒸馏装置工艺设计院别:专业:化工工艺班级:学生:指导教师:摘要本设计主要是以某石化公司常减压为设计原型,主要计算数据取自生产实际。
所处理的原料为辽河混合原油,经过初馏塔初步分离后再经过常压塔和减压塔的分离得到不同馏程的馏分油。
在采用新工艺、新设备的同时优化了工艺流程,为了节能常压系统采用4台空冷器,为增加处理量,常压炉四路进料四路出料。
为使相当数量的中间馏分得到合理利用,因为它们是很多的二次加工原料,又能从中生产国民经济所需的各种润滑油、蜡、沥青的原料。
因此本设计采用三段汽化蒸馏,即预汽化—常压蒸馏—减压蒸馏。
关键词:常减压蒸馏;常压塔;工艺;设计目录第1章文献综述 (3)1.1 常减压蒸馏意义 (3)1.2 装置的概况和特点 (3)1.3 工艺流程概况 (4)1.4 主要原料、工艺及能耗指标 (7)第2章设计计算 (12)2.1 基础数据的换算 (12)2.1.1平均沸点 (12)2.1.2 确定各馏分相对分子质量和特性因数K (14)2.1.3 确定临界参数 (14)2.1.4 确定焦点参数 (15)2.1.5 确定平衡汽化温度 (15)2.1.6 确定实沸点温度 (19)2.1.7 原料及产品的有关参数汇总 (22)第三章物料衡算 (19)3.1 初馏塔的物料衡算 (23)3.2 常压塔的物料衡算 (20)第四章确定塔的相关参数和条件 (21)4.1 确定塔板数 (21)4.2 确定塔的操作条件 (21)4.2.1 确定塔的操作压力 (21)4.2.2 确定各侧线及塔底的气提蒸汽量 (23)4.2.3 确定过汽化段温度 (23)4.2.4 估算塔底温度 (27)4.2.5 假定塔顶及各侧线温度 (27)4.3 侧线及塔顶温度的校核 (28)4.4 塔经计算 (34)4.4.1 塔经的初算 (34)4.4.2计算出Wmax后再计算适宜的气速Wa (35)4.4.3计算气相空间截面积 (35)4.4.4 降液管内流体流速Vd (35)4.4.5计算降液管面积 (35)4.4.6塔横截面积Ft的计算 (36)4.5 塔高计算 (36)第五章存在的问题和设想 (37)5.1存在问题 (37)5.2设想 (37)5.3三废的处理情况及噪声的消除 (37)总结 (38)参考文献 (39)致谢 (40)北京工大学继续教育学院论文诚信承诺书本人郑重承诺:我所呈交的毕业设计《年处理量420万吨常减压蒸馏装置工艺设计》是在指导教师的指导下,独立开展研究取得的成果,文中引用他人的观点和材料,均在文后按顺序列出其参考文献,设计使用的数据真实可靠。
塔顶冷凝器设计开题报告
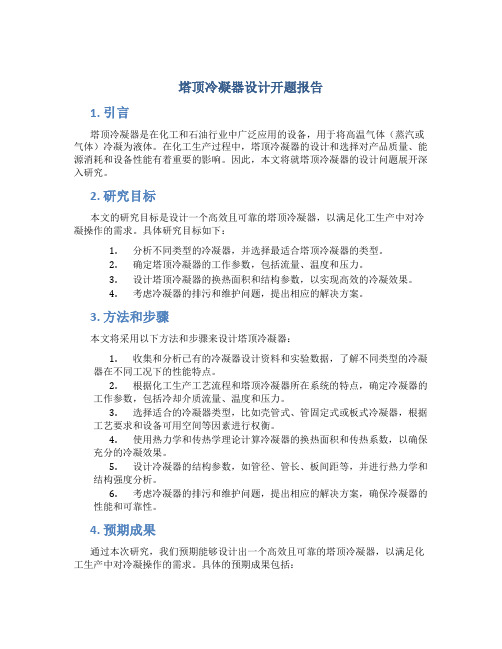
塔顶冷凝器设计开题报告1. 引言塔顶冷凝器是在化工和石油行业中广泛应用的设备,用于将高温气体(蒸汽或气体)冷凝为液体。
在化工生产过程中,塔顶冷凝器的设计和选择对产品质量、能源消耗和设备性能有着重要的影响。
因此,本文将就塔顶冷凝器的设计问题展开深入研究。
2. 研究目标本文的研究目标是设计一个高效且可靠的塔顶冷凝器,以满足化工生产中对冷凝操作的需求。
具体研究目标如下:1.分析不同类型的冷凝器,并选择最适合塔顶冷凝器的类型。
2.确定塔顶冷凝器的工作参数,包括流量、温度和压力。
3.设计塔顶冷凝器的换热面积和结构参数,以实现高效的冷凝效果。
4.考虑冷凝器的排污和维护问题,提出相应的解决方案。
3. 方法和步骤本文将采用以下方法和步骤来设计塔顶冷凝器:1.收集和分析已有的冷凝器设计资料和实验数据,了解不同类型的冷凝器在不同工况下的性能特点。
2.根据化工生产工艺流程和塔顶冷凝器所在系统的特点,确定冷凝器的工作参数,包括冷却介质流量、温度和压力。
3.选择适合的冷凝器类型,比如壳管式、管固定式或板式冷凝器,根据工艺要求和设备可用空间等因素进行权衡。
4.使用热力学和传热学理论计算冷凝器的换热面积和传热系数,以确保充分的冷凝效果。
5.设计冷凝器的结构参数,如管径、管长、板间距等,并进行热力学和结构强度分析。
6.考虑冷凝器的排污和维护问题,提出相应的解决方案,确保冷凝器的性能和可靠性。
4. 预期成果通过本次研究,我们预期能够设计出一个高效且可靠的塔顶冷凝器,以满足化工生产中对冷凝操作的需求。
具体的预期成果包括:1.选择最合适的冷凝器类型,并给出详细的选择理由。
2.给出塔顶冷凝器的工作参数,包括流量、温度和压力的计算结果。
3.设计出满足要求的冷凝器换热面积和结构参数,以及相应的热力学和强度分析结果。
4.提出解决冷凝器排污和维护问题的方案,确保冷凝器的性能和可靠性。
5. 计划进度本研究计划按照以下进度表进行:任务时间安排文献调研第1周参数分析第2周冷凝器类型选择第3周换热面积和结构设计第4-5周排污和维护方案设计第6周结果分析与总结第7周完成论文撰写第8周6. 参考文献1.Smith, J. M., Van Ness, H. C., Abbott, M. M., & Swihart, G. H. (2005).Introduction to Chemical Engineering Thermodynamics. McGraw-HillEducation.2.Incropera, F. P., & DeWitt, D. P. (2002). Fundamentals of Heat andMass Transfer. Wiley.注:以上文档仅为开题报告,详细的研究结果和分析将在后续的研究中逐步完成。
- 1、下载文档前请自行甄别文档内容的完整性,平台不提供额外的编辑、内容补充、找答案等附加服务。
- 2、"仅部分预览"的文档,不可在线预览部分如存在完整性等问题,可反馈申请退款(可完整预览的文档不适用该条件!)。
- 3、如文档侵犯您的权益,请联系客服反馈,我们会尽快为您处理(人工客服工作时间:9:00-18:30)。
正系数 fs=1.15[3] 。
管程压降:
△P1 =λ
L di
ρ水 u2i 2
=0.034×
3 × 994 × (0.89)2 0.02 × 2
=2 007.22(Pa)
△P2 =
3ρ水 u2i 2
=
3
×
994 × (0.89)2 2
=1
180.72(Pa)
△P =(△P1+△P2)FtNp
=(2 007.22+1 180.72)×1.5×4
甲 醇 为 基 本 有 机 化 工 原 料, 用 于 生 产 多 种 产 品。有些产品生产中需要高纯度的甲醇原料,以免 影响产品的纯度和产品的性能,所以粗醇必须提纯。
甲醇精馏就是利用粗醇中各组分挥发能力的 差异,通过液相和气相的回流,使气、液两相逆向多 级接触,在热能驱动和相平衡关系的约束下,使得易 挥发组分不断从液相往气相中转移,而难挥发组分 却由气相向液相中迁移,使混合物得到不断分离的 过程[1]。
× 796
=2
277.53
Pro=
C p甲醇 u甲醇 λ甲醇
=
0.68
×
4.187 × 103 × 0.212
0.65
×
10-3
=8.73
壳程中甲醇被冷却,取(
μ μW
)0.14=0.95,则壳程对
流传热系数αo:
αo=0.36
λ甲醇 de
Re 0.88 o
1
Pr3
(μμW)0.14
=0.36×
0.212
第 34 卷 第 3 期 2011 年 3 月
煤化工
HEBEI HUAGONG
Vol.34, No.3 Mar. 2 0 1 1
常压塔冷凝器设计
刘天阳,杨云霞,王永占
(河北正元化工工程设计有限公司,河北 石家庄 050061)
摘 要:甲醇精馏装置是甲醇生产的重要后处理装置。简述了甲醇三塔精馏工艺原理和工艺流程,通过对常压塔冷
第 34卷
uO=
3
1.07 × 104 600 × 796 × 0.053
=0.070(
m/s)
Reo=
douo ρ甲醇 μ甲醇
=
0.025 × 0.070 × 0.65 × 10-3
796
=2
132.17>500
管外流动摩擦系数:
fo=5.0Reo-0.228=5.0×2 132.17-0.228=0.87
冷凝器热负荷:
Q =W 甲醇[r 甲醇+Cp甲醇(T1-T2)] =1.07×104×[1 101+0.68×4.187×103×(70-65)]/3 600
=3.30×106(W)
循环水量:
W水=
C
Q p水(t2
-
t1)
=
3.30 × 106 × 3 600 4.187 × 103 × (40 - 32)
=
4 × 7 467 3 600 × 10π
=0.383(m)
圆整到 400 mm。
2.5.2 冷凝器液相出口 d2 壳程 1 冷凝量:
ν2=
1.07
×
104 × 796
1.12/2
=7.69
(m3/h)
取 u2=u'2 =0.5 m/s,则
d2=
4 ν2 3 600u2π
=
4 × 7.69 3 600 × 0.5π
ue=
WA甲o'醇 =
3
1.07 × 105 600 × 796 × 0.043
8
=0.085
1(m/s)
4( de=
3 2
t 2)
-
0.0252 4
×
π
0.025π
=
4×(
3 2
× 0.0322
-
0.0252 4
×π)
0.025 × π
=0.020 2 (m)
Reo=
de ue ρ甲醇 μ甲醇
=
0.020 2 × 0.085 1 0.65 × 10-3
精馏设备是精馏工艺运作的载体,选择合适的 设备,对于提高生产率、降低原料的消耗有着重要的 作用。一般来说,根据热量衡算计算冷却剂带走的 热量,同时计算物料和冷却剂的平均温差,然后求出 换热面积并计算冷凝器的尺寸。
以 50 kt/a 三塔精馏的常压塔冷凝器为例来阐述ຫໍສະໝຸດ 置状况。1 三塔精馏工艺简述
进入脱醚塔的粗甲醇与来自脱醚塔再沸器的 气流换热,绝大部分甲醇经脱醚塔冷凝器冷凝后回 流,未冷凝的部分低沸点组分及不凝气进入放空总 管;塔底的甲醇液经过加压塔给料泵加压后进入加 压精馏塔,进塔后与来自加压塔再沸器的气流换热, 气相从塔顶出塔后进入加压塔冷凝器给常压精馏 塔提供热源,冷凝后的甲醇进入加压塔回流槽,一部 分打回流,一部分作为产品采出。塔底液相出塔后 进入常压精馏塔,进塔后与来自加压塔冷凝器的气 流换热,气相出塔顶后经常压塔冷凝器冷却后部分 回流,部分采出,塔底的排出废水送往界外。工艺流 程见附图。
=4.125
初定采用四管程两壳程固定管板式换热器。
查资料得:
φ△t =0.95,△tm =φ△t×△tm′=0.95×31.48=29.90(℃)
假设 K=370 W/(m·2 ℃),则
S=
Q K△tm
=
3.30 × 106 370 × 29.90
=299(m2)
选用管子尺寸为Ф25×2.5,管长 L=3 m,管数
水(40 ℃)→
甲醇气体(70 ℃) ↓
→水(32 ℃)
↓ 甲醇气体(65 ℃)
查表[2]:r 甲醇 =1 101 kJ/kg
Cp甲醇=0.68 kcal(/ kg·℃) Cp水=4.187 kJ(/ kg·℃) ρ甲醇=796 kg/m3,ρ水=994 kg/m3 μ甲醇=0.65 mPa·s μ水=0.727 mPa·s λ甲醇=0.212 W/(m·2 ℃) λ水=0.626 W/(m·2 ℃)
=0.074(m)
圆整到 80 mm。
壳程 2 冷凝量:
ν'2 =
10.68
× (1 - 1.15/2) 796
=5.71(m3/h)
取 u'2 =0.8 m/s,则
d'2 =
4 ν2' 3 600u π
=
4 × 5.71 3 600 × 0.5π
=0.063(m)
2
圆整到 65 mm。
2.5.3 循环水进出口 d3和 d4
收稿日期:2010-12-29 作者简介:刘天阳(1981- ),男,助理工程师,主要从事化工工艺设计工作,E-mail:28205065@。
第3期
刘 天 阳 ,等 :常压塔冷凝器设计
·11·
粗甲醇
放空 冷却水
汽
冷却水 冷却水
汽
污水
冷却水
附图 三塔精馏工艺流程图
1 脱醚塔;2 脱醚塔再沸器;3 脱醚塔冷凝器;4 加压塔给料泵; 5 加压塔再沸器;6 加压精馏塔;7 加压塔冷凝器;8 加压塔回流泵; 9 加压塔回流槽;10 常压精馏塔;11 常压冷凝器;12 常压塔精醇冷 却器;13 加压塔精甲醇冷却器;14 精醇槽
do di
+
do αidi
=
1 519.71
+ 0.000
1 17 + 0.000
2
×
25 20
+
4
25 083.23
× 20
=377.3 [W/(m·2 ℃)]
S 计=
Q Ko△tm
=
3.30 × 106 377.3 × 29.90
=291(m2)
所选换热器的实际换热面积:
S0 = nπdL=1 420×3.141 6×0.025×3=334(m2)
凝器的设计,阐述了如何合理的在设计中选择冷凝器。
关键词:甲醇;精馏;冷凝器;设计
中图分类号:TQ 223.12+1
文献标识码:A
文章编号:1003-5095(2011)03-0010-03
Design on Atmospheric Tower Condenser
LIU Tian-yang,YANG Yun-xia,WANG Yong-zhan (Hebei Zhengyuan Chemical Engineering Design Co., Ltd,Shijiazhuang 050061,China)
=3.55×105(kg/h)
逆流时平均温度差:
△tm'=
△t2 - △t1
ln
△t2 △t1
=
(70
- 40) - (65 -
ln
(70 (65
-
40) 32)
32)
=31.48(℃)
P=
t2 - t1 T1 - t1
=
40 70
-
32 32
=0.21
R=
T1 t2
-
T2 t1
=
70 40
-
65 32
=83.78(
Pa)
△P'=(△P'1 +△P'2 )fs=(369.60+83.78)×1.15
=521.38 Pa< 30(kPa)
取换热器列管的中心距 t =32 mm,则流体通过
管间最大截面积:
Ao'=BD(1-
do t
)=0.2×1.0×(1-
0.025 0.032
)=0.043
8
(m2)
So S计
=
334 291
=1.15,所设计冷凝器合适。
2.5 冷凝器主要尺寸计算
2.5.1 冷凝器气相进口 d1