感应加热表面淬火示意图
合集下载
感应加热表面淬火.

心部具有足够的塑形和韧性。
5
表面淬火后的残余应力
热应力:淬火冷却时体积收缩,表面热应力为拉应力。 组织应力:形成马氏体时体积膨胀,在表面形成压应力。
6
感应加热表面淬火原理 简介:工件在感应线 圈中,在高频交流磁场 的作用下,产生很大的 感应电流(涡流),并 因集肤效应而集中分布 于工件表面,使受热区 迅速加热到钢的相变临 界温度Ac3或Acm之上 (奥氏体化),然后在冷 却介质中快速冷却,使 工件表层获得马氏体。
主要研究的是浅硬化层的疲劳强度以及其 疲劳断裂机制。
12
A:0.13s 0.7mm B:0.30s 1.2mm C: 0.37s 1.5mm D:0.67s 1.8mm E:1.5s
硬化层受加热时间的影响,同时硬化层也影响着残 余压应力的分布。
13
疲劳强度随着硬化层的 深度增加而增加。
表面压应力一般能提高 材料的抗疲劳性能,A, B样品的的残余压应力在 1000Mpa左右,他们的 抗疲劳性能相对于原样 品却没有提高多少!
18
参考文献
[1] Komotori J, Shimizu M, Misaka Y, et al. Fatigue strength and fracture mechanism of steel modified by super-rapid induction heating and quenching[J]. International journal of fatigue, 2001, 23: 225-230. [2] Kristoffersen H, Vomacka P. Influence of process parameters for induction hardening on residual stresses[J]. Materials & Design, 2001, 22(8): 637-644. [3] Coupard D, Palin-luc T, Bristiel P, et al. Residual stresses in surface induction hardening of steels: Comparison between experiment and simulation[J]. Materials Science and Engineering: A, 2008, 487(1): 328339. [4] 刘尚超. 感应深度加热表面淬火工艺与低淬透性钢的应用[J]. 汽 车工艺与材料, 1998 (8): 17-21. [5] 潘邻. 表面改性热处理技术进展[J]. 金属热处理, 2005, 30(C00):23-29. [6] 齐晓华, 魏冠义. 金属零件感应加热表面淬火的应用研究[J]. 漯 河职业技术学院学报, 2011, 10(5): 2感应加热淬火技术特点
表面淬火
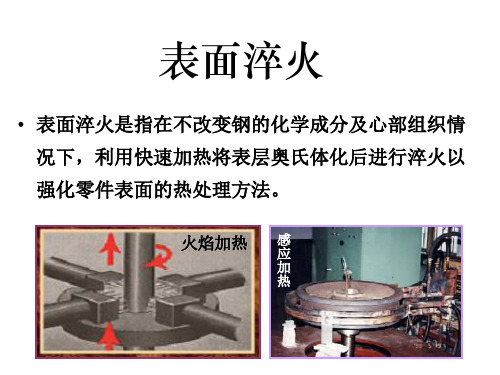
轴 的 感 应 加 热 表 面 淬 火
ቤተ መጻሕፍቲ ባይዱ
• ①表面淬火用材料 • ⑴ 0.4-0.5%C的中碳钢。
• 含碳量过低,则表面硬度、耐磨性下降。
• 含碳量过高,心部韧性下降; • ⑵ 铸铁 提高其表面耐磨性。
机床导轨
表面淬火齿轮
• ②预备热处理
• ⑴工艺: • 对于结构钢为调质或正火。 • 前者性能高,用于要求高的重 要件,后者用于要求不高的普
感应淬火机床
• ⑤表面淬火常用加热方法 • ⑴ 感应加热: 利用交变电流 在工件表面感应巨大涡流,
使工件表面迅速加热的方法。
感应加热 表面淬火 示意图
• 感应加热分为: • 高频感应加热 频 率 为 250-300KHz , 淬 硬层深度0.5-2mm
火传 感动 应轴 器连 续 淬
感应加热表面淬火齿轮的截面图
表面淬火
• 表面淬火是指在不改变钢的化学成分及心部组织情
况下,利用快速加热将表层奥氏体化后进行淬火以
强化零件表面的热处理方法。
火焰加热
感 应 加 热
• 表面淬火目的: • ① 使表面具有高的硬度、耐磨性和疲劳极限; • ② 心部在保持一定的强度、硬度的条件下,具有足够的 塑性和韧性。即表硬里韧。 • 适用于承受弯曲、扭转、摩擦和冲击的零件。
通件。
• ⑵目的: • 为表面淬火作组织准备; • 获得最终心部组织。
回火索氏体
索氏体
• ③表面淬火后的回火 • 采用低温回火,温度不高于200℃。 • 回火目的为降低内应力,保留淬火高硬度、耐磨性。 • ④表面淬火+低温回火后的组织 • 表层组织为M回;心部组织为S回(调质)或F+S(正火)。
感应加热表面淬火
表面淬火

3、高频感应加热表面淬火后的组织和性能
快速加热时钢的相变特点
1)临界温度升高,转变在较宽的温度范围内完成 2)奥氏体晶粒较细 3)奥氏体成分不均匀
ρ—工件电阻率 μ——工件的相对导磁率 f——电流频率 可见: 1)f愈高, δ小,淬硬层深度越浅。 2) ρ愈大, μ愈小,δ越大。
工频:50Hz,功率密度0.1~100W/cm2; 中频:<10kHz,功率密度< 5 W/cm2;
3.3、表面淬火
3.3 、表面淬火 3.3、表面淬火
• 要点:用快速加热法,使零件表面层很快地达到淬火温 度(A化),在热量传至内部之前,立即冷却使表 面层淬硬。 • 材料:中碳钢及中碳合金钢,如40、45、40Cr。 感应加热 • 分类(加热方法) 火焰加热 激光加热
(一)感应加热表面淬火
感应加热表面淬火示意图
下一页 返 回 金属热处理工艺 , SMSE,CUMT 本章首页 上一页
集肤效应示意图
表面淬火的发展
感应淬火原
50300
f
返 回
金属热处理工艺 , SMSE,CUMT
本章首页 上一页
下一页
返
回
金属热处理工艺 , SMSE,CUMT
本章首页 上一页
下一页
50300
f
2、分类(按电源频率)
预处理: 表面淬火前,须对零件进行正火或调质处理,以保证 零件心部具有良好的综合性能。 硬化层深度的确定: 抗磨损:1~6.5mm 抗疲劳:2~12mm 感应加热淬火温度 由于感应加热速度快,但组织转变又具有热滞后,为使组织 转变充分,所以感应加热温度应比常规加热温度提高30~50℃。 后处理: 表面淬火后,一般要对零件进行低温(160~200 ℃)回火 处理,以降低淬火应力和脆性。
感应加热表面淬火示意图
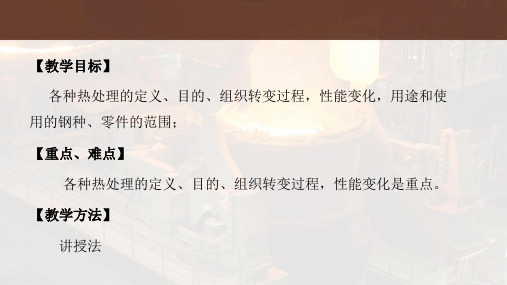
柴油机连杆
高强螺栓
齿轮
6.淬火常见缺陷 (1)淬火裂纹及变形 多种原因引起:工艺、结构、材料等。 (2)氧化、脱碳 (3)过热、过烧 (4)软点与硬度不足 加热温度不匀、存在氧化皮和表面气泡,材料淬透性低、淬 火冷速太小等。
五、钢的回火
回火是指将淬火钢加热到A1以下的某温度保温后冷却的工艺。
1.回火的目的
适用于形状复杂及要求较高的小 型件。
5.钢的淬透性
淬透性是钢的主 要热处理性能。是选 材和制订热处理工艺 的重要依据之一。
(1)淬透性的概念 淬透性是指钢在淬火时获得淬硬层深度的能力。其大小是用规定条件下淬硬层 深度来表示。 淬硬层深度是指由工件表面到半马氏体区(50%M + 50%P)的深度。
讲授法
一、钢的热处理 1.热处理:是指将钢在固态下加热、保温和冷却,以改变钢的组织
结构,获得所需要性能的一种工艺。
为简明表示热处理的 基本工艺过程,通常用温 度—时间坐标绘出热处理 工艺曲线。
热处理是一种重要的加工工艺,在制造业被广泛应用。 在机床制造中约60-70%的零件要经过热处理。 在汽车、拖拉机制造业中需热处理的零件达70-80%。 至于模具、滚动轴承则要100%经过热处理。 总之,重要的零件都要经过适当的热处理才能使用。
优点是冷却理想,缺点是不易掌握。 用于形状复杂的碳钢件及大型合金钢件。
(3)分级淬火法 在Ms附近的盐浴或碱浴中淬火, 待内外温度均匀后再取出缓冷。 可减少内应力 用于小尺寸工件。
(4)等温淬火法 将工件在稍高于Ms的盐浴或碱浴 中保温足够长时间,从而获得下贝氏 体组织的淬火方法。
经等温淬火零件具有良好的综合 力学性能,淬火应力小。
主要用于处理各种工具、模具、轴承及经渗碳和表面淬火的工件。
高强螺栓
齿轮
6.淬火常见缺陷 (1)淬火裂纹及变形 多种原因引起:工艺、结构、材料等。 (2)氧化、脱碳 (3)过热、过烧 (4)软点与硬度不足 加热温度不匀、存在氧化皮和表面气泡,材料淬透性低、淬 火冷速太小等。
五、钢的回火
回火是指将淬火钢加热到A1以下的某温度保温后冷却的工艺。
1.回火的目的
适用于形状复杂及要求较高的小 型件。
5.钢的淬透性
淬透性是钢的主 要热处理性能。是选 材和制订热处理工艺 的重要依据之一。
(1)淬透性的概念 淬透性是指钢在淬火时获得淬硬层深度的能力。其大小是用规定条件下淬硬层 深度来表示。 淬硬层深度是指由工件表面到半马氏体区(50%M + 50%P)的深度。
讲授法
一、钢的热处理 1.热处理:是指将钢在固态下加热、保温和冷却,以改变钢的组织
结构,获得所需要性能的一种工艺。
为简明表示热处理的 基本工艺过程,通常用温 度—时间坐标绘出热处理 工艺曲线。
热处理是一种重要的加工工艺,在制造业被广泛应用。 在机床制造中约60-70%的零件要经过热处理。 在汽车、拖拉机制造业中需热处理的零件达70-80%。 至于模具、滚动轴承则要100%经过热处理。 总之,重要的零件都要经过适当的热处理才能使用。
优点是冷却理想,缺点是不易掌握。 用于形状复杂的碳钢件及大型合金钢件。
(3)分级淬火法 在Ms附近的盐浴或碱浴中淬火, 待内外温度均匀后再取出缓冷。 可减少内应力 用于小尺寸工件。
(4)等温淬火法 将工件在稍高于Ms的盐浴或碱浴 中保温足够长时间,从而获得下贝氏 体组织的淬火方法。
经等温淬火零件具有良好的综合 力学性能,淬火应力小。
主要用于处理各种工具、模具、轴承及经渗碳和表面淬火的工件。
金属热处理工艺学-表面淬火

钢表面淬火后的残余应力
图12. 不同钢材硬化层深度与残余压应力的关系 1----45号钢;2----18Cr2Ni4W; 3----40CrMnMo;4----40CrNiMo
钢表面淬火强化层应与工件负载匹配
x
o
图13. 表面强化与承载应力匹配示意图 1.截面为圆形的工件负载时的应力分布情况 2.表面淬火较浅时,沿表面向内部的应力承载能力曲线 3.表面淬火较深时,沿表面向内部的应力承载能力曲线
特点3.提高加热速度可显著细化奥氏体晶粒。
形核处增加:铁素体与碳化物相界、铁素体亚晶界; 形核时间短、晶粒来不及长大。
特点4.快速加热对过冷奥氏体的转变及马氏体回火有明显影响。
奥氏体成分不均及晶粒细化,减小了过冷奥氏体稳定性,C曲线左移; 成分不均使马氏体转变点和形态都不相同,出现低碳、高碳马氏体。
知识回顾
图 Fe-C相图及其平衡组织
钢表面淬火的金相组织
钢经过表面淬火后的金相组织与钢的成分、淬火前的原始组织以及淬火 加热时截面的温度梯度分布有关。
图3. 共析钢表面淬火沿截面温度分布(a) 及淬火后金相组织(b)
原始材料:退火态共析钢
钢表面淬火的金相组织
图4. 45钢表面淬火沿截面温度分布(a) 及淬火后金相组织(b)
图 感应加热原理示意图
感应加热基本原理
感应电势的瞬时值:
d e d
e
-感应电势的瞬时值,V;
-感应线圈电流回路包围面积内的总磁通,Wb,随交变电流强度 和零件磁导率增加而增加,并于零件与感应器之间的间隙有关;
感应电流(涡流)值: Z
I
e e Z R X
2
2
X
-自感电抗,Ω; -零件材料的电阻,Ω;
钢的表面热处理ppt课件

• 碳素工具钢、渗碳钢、轴承钢、高速工具钢、铸铁、硬质合 金等材料均可进行气相沉积。
完整编辑ppt
19
(2)物理气相沉积(PVD)
• 通过蒸发或辉光放电、弧光放电、溅射等物理方法提供原 子、离子,使之在工件表面沉积形成薄膜的工艺。
• 方法:蒸镀、溅射沉积、磁控溅射、离子束沉积等。
完整编辑ppt
20
• 渗氮前零件须经调质处理,获得回火索氏体组织,以提高 心部的性能。渗氮后不需再热处理。
• 渗氮用于耐磨性和精度要求高的精密零件或承受交变载荷 以及要求耐热、耐蚀、耐磨的零件的重要零件。
完整编辑ppt
15
(3)碳氮共渗技术
• 两种方法:一种是以渗碳为主碳氮共渗,另一种是以渗氮为 主的软氮化。
1)以渗碳为主的碳氮共渗 • 目的:提高工件表面的硬度和耐磨性。 • 碳氮共渗后要进行淬火、低温回火。共渗层表面组织为回火
马氏体、粒状碳氮化合物。渗层深度0.3~0.8 mm。
完整编辑ppt
16
碳氮共渗用钢:低碳或中碳钢、低合金钢及合金钢。
• 特点:具有温度低、时间短、变形小、硬度高、耐磨性好 、生产率高等优点。用于机床和汽车上的各种齿轮、蜗轮 、蜗杆和轴类等零件。
完整编辑ppt
17
(4)渗铝、渗铬、渗硼化学热处理
热处理工艺的应用
热处理技术条件是指对零件采用的热处理方法以及所应达到的
性能要求的技术性的文件。具体应根据零件性能要求,在零件 图样上标出,内容包括最终热处理方法(如调质、淬火、回火、 渗碳等)以及应达到的力学性能判据等,作为热处理生产及检 验时的依据。力学性能通常只标出硬度值,且有一定误差范围, 如弹簧淬火回火硬度45~50HRC。
• 不仅改变了钢表面的组织,而且表面层的化学成分也发生 了变化,因而能更有效地改变零件表层的性能。
完整编辑ppt
19
(2)物理气相沉积(PVD)
• 通过蒸发或辉光放电、弧光放电、溅射等物理方法提供原 子、离子,使之在工件表面沉积形成薄膜的工艺。
• 方法:蒸镀、溅射沉积、磁控溅射、离子束沉积等。
完整编辑ppt
20
• 渗氮前零件须经调质处理,获得回火索氏体组织,以提高 心部的性能。渗氮后不需再热处理。
• 渗氮用于耐磨性和精度要求高的精密零件或承受交变载荷 以及要求耐热、耐蚀、耐磨的零件的重要零件。
完整编辑ppt
15
(3)碳氮共渗技术
• 两种方法:一种是以渗碳为主碳氮共渗,另一种是以渗氮为 主的软氮化。
1)以渗碳为主的碳氮共渗 • 目的:提高工件表面的硬度和耐磨性。 • 碳氮共渗后要进行淬火、低温回火。共渗层表面组织为回火
马氏体、粒状碳氮化合物。渗层深度0.3~0.8 mm。
完整编辑ppt
16
碳氮共渗用钢:低碳或中碳钢、低合金钢及合金钢。
• 特点:具有温度低、时间短、变形小、硬度高、耐磨性好 、生产率高等优点。用于机床和汽车上的各种齿轮、蜗轮 、蜗杆和轴类等零件。
完整编辑ppt
17
(4)渗铝、渗铬、渗硼化学热处理
热处理工艺的应用
热处理技术条件是指对零件采用的热处理方法以及所应达到的
性能要求的技术性的文件。具体应根据零件性能要求,在零件 图样上标出,内容包括最终热处理方法(如调质、淬火、回火、 渗碳等)以及应达到的力学性能判据等,作为热处理生产及检 验时的依据。力学性能通常只标出硬度值,且有一定误差范围, 如弹簧淬火回火硬度45~50HRC。
• 不仅改变了钢表面的组织,而且表面层的化学成分也发生 了变化,因而能更有效地改变零件表层的性能。
四、表面淬火

5、回火工艺
感应加热淬火后一般只进行低温回火。
其目的是为了降低残余应力和脆性,而又不致降低硬度。一般采 用酶回火方式有炉中回火、自回火和感应加热回火.
二、表面淬火的组织与性能 1.表面淬火的金相组织
钢件经表面淬火后的金相组织与 钢种、淬火前的原始组织及淬火加热 时沿截面温度的分布有关。最简单的 是原始组织为退火状态的共析钢。淬 火以后金相组织应分为三区,自表面 向心部分别为马氏体区 (M) (包括残 余奥氏ห้องสมุดไป่ตู้), 马氏体加珠光体 (M十P) 及珠光体 (P)区。 2.表面淬火的性能
3.提高加热速度可显著细化奥氏体晶粒.
快速加热时,过热度很大,奥氏体晶核不仅在铁素体一碳化物 相界面上形成,而且也可能在铁素体的亚晶界上形成,因此使奥 氏体的成核串增大。又由于加热时间极短,奥氏体晶粒来不及长 大.当用超快速加热时,可获得超细化晶粒。
4.快速加热对过冷奥氏体的转变及马氏体回火有明显影响.
感应加热方式:一种称同时加热法,即对工件需淬火表面同时 加热,一般在设备功率足够、生产批量比较大的情况下采用; 另一种称连续加热法,即对工件需淬火部位中的一部分同时加热, 通过感应器与工件之间的相对位移速度来实现。
4、冷却方式和冷却介质的选择
最常用的冷却方式是喷射冷却法和漫液冷却法。
喷射冷却法即当感应加热终了时把工件置于喷射器之中,向工件喷 射淬火介质进行淬火冷却。其冷却速度可以通过调节液体压力、温 度及喷射时间来控制。
漫液淬火法即当工件加热终了时,浸入淬火介质中进行冷却。对 细,薄工件或合金钢齿轮,为减少变形、开裂,可将感应器与工件 同时放入油槽中加热,断电后冷却,也称为埋油淬火法。
5、回火工艺
感应加热淬火后一般只进行低温回火。其目的是为了降低残余应 力和脆性,而又不致降低硬度。一般采用酶回火方式有炉中回火、 自回火和感应加热回火.
感应加热表面淬火

感应加热表面淬火
目 录
Contents
第一章:请第在一此章处:输入您的标 感应加热表题面淬火简介
第二章:请第在二此章处:输入您的标 感应加热表题面淬火技术
第三章:请第在三此章处:输入您的标 感应加热表题面淬火案例
2
感应加热表面淬火简述
Click here to add your title
3
感应加热表面淬火简介
22
工程上规定,当电流强度从
表面向内部降低到表面最大电流
强度的0.368(即I0/e)时,则
该处到表面的距离称为电流透入
深度δ,单位用mm表示。
50300 f
感应电流的基本特性
23
钢的磁导率和电阻率随温度变化 图 钢的磁导率,电阻率与加热
而变化。电阻率随温度升高而增 大,在800-900摄氏度时,各类
感应电流(涡流)值: I e e
Z
R2 X 2
Z -自感电抗,Ω; X -零件材料的电阻,Ω;
R -零件材料的电阻,Ω;
涡流在零件上产生的热量:
Q 0.24I 2R
假设无漏磁条件下,1cm高单匝感应圈中零件表面吸收功率为:
P 1.25103 R I 2 f
a
0
R0 -零件半径,cm; μ -零件磁导率,H/m;
本质区别是热态时钢材是顺
磁体,磁导率极低,因此热态比
冷态透入深度大几十倍。
24
感应加热过程分为三个阶段:冷态、 图 高频加热时零件截面电流密
过渡态和热态。
度与温度变化
感应加热开始时,零件处于室温,
电流透入深度很小(冷态电流分布)。
当表面温度升高到达磁性转变温度,加
热层被分为两层,外层磁性消失,而与
目 录
Contents
第一章:请第在一此章处:输入您的标 感应加热表题面淬火简介
第二章:请第在二此章处:输入您的标 感应加热表题面淬火技术
第三章:请第在三此章处:输入您的标 感应加热表题面淬火案例
2
感应加热表面淬火简述
Click here to add your title
3
感应加热表面淬火简介
22
工程上规定,当电流强度从
表面向内部降低到表面最大电流
强度的0.368(即I0/e)时,则
该处到表面的距离称为电流透入
深度δ,单位用mm表示。
50300 f
感应电流的基本特性
23
钢的磁导率和电阻率随温度变化 图 钢的磁导率,电阻率与加热
而变化。电阻率随温度升高而增 大,在800-900摄氏度时,各类
感应电流(涡流)值: I e e
Z
R2 X 2
Z -自感电抗,Ω; X -零件材料的电阻,Ω;
R -零件材料的电阻,Ω;
涡流在零件上产生的热量:
Q 0.24I 2R
假设无漏磁条件下,1cm高单匝感应圈中零件表面吸收功率为:
P 1.25103 R I 2 f
a
0
R0 -零件半径,cm; μ -零件磁导率,H/m;
本质区别是热态时钢材是顺
磁体,磁导率极低,因此热态比
冷态透入深度大几十倍。
24
感应加热过程分为三个阶段:冷态、 图 高频加热时零件截面电流密
过渡态和热态。
度与温度变化
感应加热开始时,零件处于室温,
电流透入深度很小(冷态电流分布)。
当表面温度升高到达磁性转变温度,加
热层被分为两层,外层磁性消失,而与
机械工程材料新课件

特定条件 930±10℃;保温3~8小时;缓慢冷却; 放大100×;与标准图比较。
钢的晶粒度1~4级,为本质粗晶粒, 随温度升高,晶粒迅速长大。
钢的晶粒度5~8级,为本质细晶粒, 随温度升高长大倾向不明显。
机械工程材料新
1-本质粗晶粒钢2-本质细晶粒钢
加热温度与奥氏体晶粒长大的关系
6
⑵ 奥氏体晶粒长大及其影响因素
机械工程材料新
18
②马氏体的形态
片状(针状)马氏体(M片):连续冷却温度(Ms—Mf);HRC60—65 组织形态:灰片状。C%≥1%
在电镜下,亚结构主要是孪晶,又称孪晶马氏体。 板条状马氏体(M板条):连续冷却温度(Ms—Mf);HRC35—45;
组织形态:灰板条状。C%≤0.3% 在电镜下,板条内的亚结构主要是高密度的位错,又称位错马氏体。
晶粒度—表示晶粒大小的尺度。 起始晶粒度—奥氏体刚刚形成时的晶粒度。(此时晶粒细小) 实际晶粒度—在具体的热加工条件下,得到奥氏体晶粒度。(与热
加工工艺参数有关,一般比起始晶粒度大)
1~4级为粗晶粒
国家标准GB6394-86,金属机械平工均程晶材粒料度新标准评级图
5~8级为细晶粒
5
本质晶粒度—在特定的加热条件下,奥氏体晶粒长大的倾向。
具有高的硬度和强度。 硬度主要取决于含碳量。 塑性和韧性主要取决于组织。
板条马氏体具有较高硬度、较高强度
与较好塑性和韧性相配合的良好的综合力
学性能。
针片状马氏体具有比板条马氏体更高
的硬度,但脆性较大,塑性和韧性较差。
机械工程材料新
马氏体硬度与碳含量的关系
21
3.影响C曲线位置的因素
(1)含碳量的影响
22
4、过冷奥氏体的连续冷却曲线
钢的晶粒度1~4级,为本质粗晶粒, 随温度升高,晶粒迅速长大。
钢的晶粒度5~8级,为本质细晶粒, 随温度升高长大倾向不明显。
机械工程材料新
1-本质粗晶粒钢2-本质细晶粒钢
加热温度与奥氏体晶粒长大的关系
6
⑵ 奥氏体晶粒长大及其影响因素
机械工程材料新
18
②马氏体的形态
片状(针状)马氏体(M片):连续冷却温度(Ms—Mf);HRC60—65 组织形态:灰片状。C%≥1%
在电镜下,亚结构主要是孪晶,又称孪晶马氏体。 板条状马氏体(M板条):连续冷却温度(Ms—Mf);HRC35—45;
组织形态:灰板条状。C%≤0.3% 在电镜下,板条内的亚结构主要是高密度的位错,又称位错马氏体。
晶粒度—表示晶粒大小的尺度。 起始晶粒度—奥氏体刚刚形成时的晶粒度。(此时晶粒细小) 实际晶粒度—在具体的热加工条件下,得到奥氏体晶粒度。(与热
加工工艺参数有关,一般比起始晶粒度大)
1~4级为粗晶粒
国家标准GB6394-86,金属机械平工均程晶材粒料度新标准评级图
5~8级为细晶粒
5
本质晶粒度—在特定的加热条件下,奥氏体晶粒长大的倾向。
具有高的硬度和强度。 硬度主要取决于含碳量。 塑性和韧性主要取决于组织。
板条马氏体具有较高硬度、较高强度
与较好塑性和韧性相配合的良好的综合力
学性能。
针片状马氏体具有比板条马氏体更高
的硬度,但脆性较大,塑性和韧性较差。
机械工程材料新
马氏体硬度与碳含量的关系
21
3.影响C曲线位置的因素
(1)含碳量的影响
22
4、过冷奥氏体的连续冷却曲线
- 1、下载文档前请自行甄别文档内容的完整性,平台不提供额外的编辑、内容补充、找答案等附加服务。
- 2、"仅部分预览"的文档,不可在线预览部分如存在完整性等问题,可反馈申请退款(可完整预览的文档不适用该条件!)。
- 3、如文档侵犯您的权益,请联系客服反馈,我们会尽快为您处理(人工客服工作时间:9:00-18:30)。
熔盐作为淬火介质称盐浴,冷却能力在水和油之间,用于形状复杂件 的分级淬火和等温淬火。
4.淬火方法
采用不同的淬火方法可弥补介质的不足。 (1)单液淬火法 加热工件在一种介质中连续冷却到室温的淬火方法。 操作简单,易实现自动化。
(2)双液淬火法 工件先在一种冷却能力强的介质中 冷却,躲过鼻尖后,再在另一种冷却能 力较弱的介质中发生马氏体转变的方法。 如水淬油冷,油淬空冷。
优点是冷却理想,缺点是不易掌握。 用于形状复杂的碳钢件及大型合金钢件。
(3)分级淬火法 在Ms附近的盐浴或碱浴中淬火, 待内外温度均匀后再取出缓冷。 可减少内应力 用于小尺寸工件。
(4)等温淬火法 将工件在稍高于Ms的盐浴或碱浴 中保温足够长时间,从而获得下贝氏 体组织的淬火方法。
经等温淬火零件具有良好的综合 力学性能,淬火应力小。
淬火是应用最广的热处理工艺之 一。
淬火的目的: 获得马氏体组织,提高钢的性能。
2.淬火温度 (1)碳钢 淬火温度:Ac3+30-50℃。
合金钢 由于多数合金元素(Mn、P除外)对奥氏体晶粒长大有阻碍作用,因而合 金钢淬火温度比碳钢高。 ⑴ 亚共析钢淬火温度 Ac3+50-100℃ ⑵ 共析钢、过共析钢淬火温度 Ac1+50-100℃
主要用于处理各种工具、模具、轴承及经渗碳和表面淬火的工件。
(2)中温回火回火温度:350-500℃
M回火转变为在保持马氏体形态的铁素体基体上分布着细粒状Fe3C的组织,称为 回火托氏体,用T回表示。
柴油机连杆
高强螺栓
齿轮
6.淬火常见缺陷 (1)淬火裂纹及变形 多种原因引起:工艺、结构、材料等。 (2)氧化、脱碳 (3)过热、过烧 (4)软点与硬度不足 加热温度不匀、存在氧化皮和表面气泡,材料淬透性低、淬 火冷速太小等。
五、钢的回火
回火是指将淬火钢加热到A1以下的某温度保温后冷却的工艺。
1.回火的目的
退火 将钢加热至适当温度保温,然后缓慢冷却(炉冷)的热 处理工艺叫做退火。 退火目的 ⑴ 调整硬度,便于切削加工。 ⑵ 消除内应力,防止加工中变形。 ⑶ 细化晶粒,为最终热处理作组织准备。
退火工艺 退火的种类很多,常用的有完全退火、球化退火、去应力退火。
三、钢的正火 2.正火 正火是将亚共析钢加热到Ac3+30-50℃,共析钢加热到Ac1+30-50℃,过 共析钢加热到Accm+30~ 50℃,保温后空冷的工艺。 正火比退火冷却速度大。 (1)正火后的组织: <0.6%C时组织 F+S 0.6%C时组织 S
热处理是一种重要的加工工艺,在制造业被广泛应用。 在机床制造中约60-70%的零件要经过热处理。 在汽车、拖拉机制造业中需热处理的零件达70-80%。 至于模具、滚动轴承则要100%经过热处理。 总之,重要的零件都要经过适当的热处理才能使用。
2.热处理特点:热处理区别于其他加工工艺如铸造、压力加工等的 特点是只通过改变工件的组织来改变性能,而不改变其形状。
3.淬火介质
理想的冷却曲线应只在C曲线鼻尖处快冷,而在Ms附近尽量缓冷,以达到既获 得马氏体组织,又减小内应力的目的。但目前还没有找到理想的淬火介质。
常用淬火介质是水和油。 水的冷却能力强,但低温冷却能 力太大,只用于形状简单的碳钢件。
油在低温区冷却能力较理想,但高温区冷却能力太小,用于合金钢和 小尺寸的碳钢件。
适用于形状复杂及要求较高的小 型件。
5.钢的淬透性
淬透性是钢的主 要热处理性能。是选 材和制订热处理工艺 的重要依据之一。
(1)淬透性的概念 淬透性是指钢在淬火时获得淬硬层深度的能力。其大小是用规定条件下淬硬层 深度来表示。 淬硬层深度是指由工件表面到半马氏体区(50%M + 50%P)的深度。
铸造
轧制
3.热处理适用范围:只适用于固态下发生相变的材料,不发生固 态相变的材料不能用热处理强化。
4.根据加热、冷却方式及钢组织性能变化特点不同,将热处理工艺分 类如下:
二、钢的退火与正火
机械零件的一般加工工艺为:毛坯(铸、锻)→预备热处理→机加工→最 终热处理。
退火与正火工艺主要用于预 备热处理,只有当工件性能要求不 高时才作为最终热处理。
正火温度
正火的目的 ⑴ 对于低、中碳钢(≤0.6C%),目的与退火的相同。 ⑵ 对于过共析钢,用于消除网状二次渗碳体,为球化退火作组织准备。 ⑶ 普通件最终热处理。
合适切削加工硬度 热理与硬度关系
四、钢的淬火 1.钢的淬火
淬火是将钢加热到临界点以上,保温后以大于Vk速度冷却,使奥氏体转 变为马氏体的热处理工艺。
淬硬性是指钢淬火后所能达到 的最高硬度,即硬化能力。
M量和硬度随深度的变化
淬透性的应用
1.对于截面承载均匀的重要件,要全部淬透。如螺栓、连杆、模具等。 2.对于承受弯曲、扭转的零件可不必淬透(淬硬层深度一般为半径的1/2-1/3), 如轴类、齿轮等。 淬硬层深度与工件尺寸有关,设计时应注意尺寸效应。
未经淬火的钢回火无意义,而淬火钢不 回火在放置或使用过程中易变形或开裂。
钢经淬火后应立即进行回火。
2.回火的种类 (1)低温回火回火温度:150-250℃
这种在马氏体基体上分布着细片状碳化物的组织称为回火马氏体,用M回表示。
低温回火的目的是在保留淬火后高硬度、 高耐磨性的同时,降低内 应力,提高韧性。
井式回火炉
(1)减少或消除淬火内应力,防止变形或开裂。
(2)获得所需要的力学性能。淬火钢一般硬度高,脆性大,回火可调整硬度、 韧性。
(3)稳定尺寸。回火可使非平衡M与A’转变为平衡或接近平衡的组 织,防止使用时变形。
(4)高淬透性钢的软化,这类钢空冷即可淬火,如采用回火软化既 能降低硬度,又能缩短软化周期。
【教学目标】 各种热处理的定义、目的、组织转变过程,性能变化,用途和使
用的钢种、零件的范围; 【重点、难点】
各种热处理的定义、目的、组织转变过程,性能变化是重点。 【教学方法】
讲授法
一、钢的热处理 1.热处理:是指将钢在固态下加热、保温和冷却,以改变钢的组织
结构,获得所需要性能的一种工艺。
为简明表示热处理的 基本工艺过程,通常用温 度—时间坐标绘出热处理 工艺曲线。
4.淬火方法
采用不同的淬火方法可弥补介质的不足。 (1)单液淬火法 加热工件在一种介质中连续冷却到室温的淬火方法。 操作简单,易实现自动化。
(2)双液淬火法 工件先在一种冷却能力强的介质中 冷却,躲过鼻尖后,再在另一种冷却能 力较弱的介质中发生马氏体转变的方法。 如水淬油冷,油淬空冷。
优点是冷却理想,缺点是不易掌握。 用于形状复杂的碳钢件及大型合金钢件。
(3)分级淬火法 在Ms附近的盐浴或碱浴中淬火, 待内外温度均匀后再取出缓冷。 可减少内应力 用于小尺寸工件。
(4)等温淬火法 将工件在稍高于Ms的盐浴或碱浴 中保温足够长时间,从而获得下贝氏 体组织的淬火方法。
经等温淬火零件具有良好的综合 力学性能,淬火应力小。
淬火是应用最广的热处理工艺之 一。
淬火的目的: 获得马氏体组织,提高钢的性能。
2.淬火温度 (1)碳钢 淬火温度:Ac3+30-50℃。
合金钢 由于多数合金元素(Mn、P除外)对奥氏体晶粒长大有阻碍作用,因而合 金钢淬火温度比碳钢高。 ⑴ 亚共析钢淬火温度 Ac3+50-100℃ ⑵ 共析钢、过共析钢淬火温度 Ac1+50-100℃
主要用于处理各种工具、模具、轴承及经渗碳和表面淬火的工件。
(2)中温回火回火温度:350-500℃
M回火转变为在保持马氏体形态的铁素体基体上分布着细粒状Fe3C的组织,称为 回火托氏体,用T回表示。
柴油机连杆
高强螺栓
齿轮
6.淬火常见缺陷 (1)淬火裂纹及变形 多种原因引起:工艺、结构、材料等。 (2)氧化、脱碳 (3)过热、过烧 (4)软点与硬度不足 加热温度不匀、存在氧化皮和表面气泡,材料淬透性低、淬 火冷速太小等。
五、钢的回火
回火是指将淬火钢加热到A1以下的某温度保温后冷却的工艺。
1.回火的目的
退火 将钢加热至适当温度保温,然后缓慢冷却(炉冷)的热 处理工艺叫做退火。 退火目的 ⑴ 调整硬度,便于切削加工。 ⑵ 消除内应力,防止加工中变形。 ⑶ 细化晶粒,为最终热处理作组织准备。
退火工艺 退火的种类很多,常用的有完全退火、球化退火、去应力退火。
三、钢的正火 2.正火 正火是将亚共析钢加热到Ac3+30-50℃,共析钢加热到Ac1+30-50℃,过 共析钢加热到Accm+30~ 50℃,保温后空冷的工艺。 正火比退火冷却速度大。 (1)正火后的组织: <0.6%C时组织 F+S 0.6%C时组织 S
热处理是一种重要的加工工艺,在制造业被广泛应用。 在机床制造中约60-70%的零件要经过热处理。 在汽车、拖拉机制造业中需热处理的零件达70-80%。 至于模具、滚动轴承则要100%经过热处理。 总之,重要的零件都要经过适当的热处理才能使用。
2.热处理特点:热处理区别于其他加工工艺如铸造、压力加工等的 特点是只通过改变工件的组织来改变性能,而不改变其形状。
3.淬火介质
理想的冷却曲线应只在C曲线鼻尖处快冷,而在Ms附近尽量缓冷,以达到既获 得马氏体组织,又减小内应力的目的。但目前还没有找到理想的淬火介质。
常用淬火介质是水和油。 水的冷却能力强,但低温冷却能 力太大,只用于形状简单的碳钢件。
油在低温区冷却能力较理想,但高温区冷却能力太小,用于合金钢和 小尺寸的碳钢件。
适用于形状复杂及要求较高的小 型件。
5.钢的淬透性
淬透性是钢的主 要热处理性能。是选 材和制订热处理工艺 的重要依据之一。
(1)淬透性的概念 淬透性是指钢在淬火时获得淬硬层深度的能力。其大小是用规定条件下淬硬层 深度来表示。 淬硬层深度是指由工件表面到半马氏体区(50%M + 50%P)的深度。
铸造
轧制
3.热处理适用范围:只适用于固态下发生相变的材料,不发生固 态相变的材料不能用热处理强化。
4.根据加热、冷却方式及钢组织性能变化特点不同,将热处理工艺分 类如下:
二、钢的退火与正火
机械零件的一般加工工艺为:毛坯(铸、锻)→预备热处理→机加工→最 终热处理。
退火与正火工艺主要用于预 备热处理,只有当工件性能要求不 高时才作为最终热处理。
正火温度
正火的目的 ⑴ 对于低、中碳钢(≤0.6C%),目的与退火的相同。 ⑵ 对于过共析钢,用于消除网状二次渗碳体,为球化退火作组织准备。 ⑶ 普通件最终热处理。
合适切削加工硬度 热理与硬度关系
四、钢的淬火 1.钢的淬火
淬火是将钢加热到临界点以上,保温后以大于Vk速度冷却,使奥氏体转 变为马氏体的热处理工艺。
淬硬性是指钢淬火后所能达到 的最高硬度,即硬化能力。
M量和硬度随深度的变化
淬透性的应用
1.对于截面承载均匀的重要件,要全部淬透。如螺栓、连杆、模具等。 2.对于承受弯曲、扭转的零件可不必淬透(淬硬层深度一般为半径的1/2-1/3), 如轴类、齿轮等。 淬硬层深度与工件尺寸有关,设计时应注意尺寸效应。
未经淬火的钢回火无意义,而淬火钢不 回火在放置或使用过程中易变形或开裂。
钢经淬火后应立即进行回火。
2.回火的种类 (1)低温回火回火温度:150-250℃
这种在马氏体基体上分布着细片状碳化物的组织称为回火马氏体,用M回表示。
低温回火的目的是在保留淬火后高硬度、 高耐磨性的同时,降低内 应力,提高韧性。
井式回火炉
(1)减少或消除淬火内应力,防止变形或开裂。
(2)获得所需要的力学性能。淬火钢一般硬度高,脆性大,回火可调整硬度、 韧性。
(3)稳定尺寸。回火可使非平衡M与A’转变为平衡或接近平衡的组 织,防止使用时变形。
(4)高淬透性钢的软化,这类钢空冷即可淬火,如采用回火软化既 能降低硬度,又能缩短软化周期。
【教学目标】 各种热处理的定义、目的、组织转变过程,性能变化,用途和使
用的钢种、零件的范围; 【重点、难点】
各种热处理的定义、目的、组织转变过程,性能变化是重点。 【教学方法】
讲授法
一、钢的热处理 1.热处理:是指将钢在固态下加热、保温和冷却,以改变钢的组织
结构,获得所需要性能的一种工艺。
为简明表示热处理的 基本工艺过程,通常用温 度—时间坐标绘出热处理 工艺曲线。