浅谈荣72块举升工艺优化
双柱举升机U型槽的制程质量优化改进

双柱举升机U型槽的制程质量优化改进
双柱举升机是一种常用的工业设备,广泛应用于各个行业。
它具有结构简单、使用方便等特点,但是在制程中还存在一些质量问题,需要进行优化改进。
本文将针对双柱举升机中的U型槽进行制程质量优化改进,以提高其使用性能和可靠性。
我们需要对U型槽的制程进行评估,找出问题所在。
通过对U型槽的结构和加工工艺进行分析发现,存在以下几个主要问题:一是制程精度不高,导致U型槽的加工尺寸偏差较大;二是材料选择不当,在使用过程中容易产生变形和磨损;三是表面处理不够光滑,影响U型槽与其他部件的配合。
针对上述问题,我们可以采取以下几种措施进行优化改进。
提高制程精度,减小U型槽的加工尺寸偏差。
可以采用精密加工设备和工艺,如数控机床和数控加工中心,保证加工精度和稳定性。
加强对加工刀具和夹具的管理,及时更换磨损严重的刀具和夹具,提高加工质量。
改善材料选择,减少U型槽的变形和磨损。
可以选择高强度、具有良好耐磨性和抗变形能力的材料来制作U型槽,如合金钢材料。
可以进行热处理或镀层处理,提高材料的硬度和耐磨性,减少表面的磨损和变形。
改进表面处理工艺,提高U型槽的表面光滑度。
可以采用抛光、打磨等工艺,使U型槽的表面更加平整光滑。
可以进行表面防腐处理,增加U型槽的使用寿命。
通过以上的优化改进措施,可以提高双柱举升机U型槽的制程质量,提高其使用性能和可靠性。
也需要加强对制程过程的管理和控制,确保各项措施得到有效实施。
只有不断改进和优化,才能满足市场对设备质量的要求,提高产品的竞争力。
双柱举升机U型槽的制程质量优化改进

双柱举升机U型槽的制程质量优化改进双柱举升机是一种常见的汽车维修设备,用来提升汽车,便于维修人员进行汽车维修和保养。
在双柱举升机的制造过程中,U型槽是其重要部件之一,其制程质量对整个举升机的性能和安全都有着重要影响。
对U型槽的制程质量进行优化改进是十分必要的。
本文将从U型槽的制程质量入手,探讨双柱举升机U型槽的制程质量优化改进方案。
要对U型槽的材料选择进行优化。
U型槽的材料直接影响到其承载能力和耐用性。
传统上,U型槽通常采用普通碳素钢材料,并在表面进行镀锌处理以增加其防腐性能。
随着汽车技术的发展和汽车种类的增多,一些大型和重型汽车对举升机的要求也越来越高,因此U型槽的材料也需要进行相应的升级。
可以考虑采用高强度合金钢或不锈钢等材料来制作U型槽,以确保其可以承受更大的负载和更长的使用寿命。
要对U型槽的制造工艺进行优化改进。
传统上,U型槽的制造工艺主要依靠传统的冲压和焊接工艺,这种制造工艺虽然成本低廉,但其弊端也是显而易见的。
冲压和焊接工艺制造出的U型槽往往无法保证其内部结构的均匀性和一致性,容易导致U型槽在使用过程中出现变形或破裂的情况。
冲压和焊接工艺所制造的U型槽表面粗糙度较大,不利于与其他部件的装配和使用。
可以考虑采用数控加工工艺来制造U型槽,以保证其内部结构的均匀性和一致性,同时提高其表面粗糙度,提高其装配和使用的便利性。
U型槽的表面处理也是制程质量优化改进的重要环节。
传统上,U型槽的表面处理主要采用镀锌工艺,以增加其表面的防腐性能。
随着汽车维修技术的不断提高,人们对于举升机的要求也越来越高,对U型槽的表面处理也提出了新的要求。
可以考虑采用喷涂或电镀等新型表面处理工艺,以提高U型槽表面的硬度和耐磨性,提高其对外部环境的适应能力,从而提高举升机的使用寿命和安全性能。
要对U型槽的质量检测和控制进行优化改进。
传统上,U型槽的质量检测主要依靠人工目测和简单的尺寸测量,容易导致漏检和误检的情况。
可以考虑采用自动化检测设备和质量控制系统,以提高对U型槽质量的检测和控制水平,减少人为因素对U型槽质量的影响。
浅谈70Cr3Mo辊坯锻造工艺改进

浅谈70Cr3Mo辊坯锻造工艺改进通过对70Cr3Mo辊坯锻造工艺改进,提高了辊坯的质量(合格率),降低了能耗成本。
标签:WHF(宽砧高温强压法)锻造法SUF(镦锻法)锻造法1 工艺改进背景支承辊轧制载荷通过工作辊(及中间辊)传递给支承辊并最终由支承辊承担。
对支撑辊来讲其机械性能、耐磨性及抗疲劳性均要求较高。
因此其轧辊毛坯要充分锻透,且组织细密均匀。
70Cr3Mo支承辊一般应用于大型轧制设备上,规格相对较大,这种辊坯一般不容易锻透,且容易产生粗晶现象,制造难度较大。
一般锻造厂在辊坯的锻制过程中,其合格率相对较低,能耗较大,生产成本居高不下。
造成辊坯合格率偏低的主要原因是辊坯锻不透,粗晶现象严重。
如何使70Cr3Mo辊坯的合格率进一步提高,能耗进一步降低是我们研究的方向。
2 工艺的改进通过现场观察发现原工艺多采用压八方锻造的方式,这种锻造方式最大的特点是压下量不大,基本上保证不了20%的变形量。
这样锻造时很难锻透。
为了保证辊坯能够有效锻透我们决定采用WHF(宽砧高温强压法)锻造法和SUF(镦锻法)锻造法。
WHF(宽砧高温强压法)锻造法介绍:宽砧高温大压下量拔长,改善了坯料内部的应力应变场,有利于内部孔隙缺陷的锻合、压实。
当增加砧面宽度并满砧送进(送进量不小于砧宽的70%-90%)在压下量为20%-25%,W/H=0.6-0.9时,坯料内应力应变分布较为合理,加上较高而均匀的温度场,空穴和疏松结构将被有效地锻合压实。
在用WHF法拔长时,沿钻子边缘约有35%-50%区域,孔洞难以闭合,为此两次压缩中间应有不少于10%砧宽的搭接量,并在翻料时注意错砧,以达到全部均匀压实的目的。
SUF(镦锻法)锻造法介绍:SUF法是有意将工件表面锻造成矩形,使W/H 增大,从而使心部缺陷得到更确实的压合。
其所用砧形为普通平砧。
大锻件变形方法的主要目的是锻合钢锭内部的疏松、空穴等缺陷,改善偏析状态,破碎金属和非金属夹杂,并使之弥散分布,提高大锻件的质量。
双柱举升机U型槽的制程质量优化改进

双柱举升机U型槽的制程质量优化改进摘要:双柱举升机U型槽在工业生产中广泛应用,然而由于制程质量不稳定,导致产品的质量和效率有所下降。
本文以一家汽车零部件制造企业为例,对双柱举升机U型槽的制程质量进行了分析和改进。
通过对原有制程进行调研,找出了质量不稳定的原因,并提出了相应的改进方法。
改进后的U型槽制程质量得到大幅提高,产品质量和生产效率得到了明显的提升。
1. 引言双柱举升机U型槽是一种常见的用于汽车零部件制造的设备,其主要功能是将工件固定在工作台上进行加工。
由于制程质量不稳定,导致产品的质量和效率有所下降。
有必要对双柱举升机U型槽的制程质量进行优化改进。
2. 质量分析在对双柱举升机U型槽的制程质量进行分析时,我们发现了以下几个问题:(1)初始设定不准确:在操作人员设置U型槽时,初始设定的位置不准确,导致工件无法正确固定,影响加工质量。
(2)变形问题:由于U型槽的材质和制造工艺存在一定的问题,使用一段时间后就容易发生变形,导致工件无法准确放置和固定。
(3)加工精度问题:由于初始设定不准确和U型槽的变形问题,加工精度无法得到保证,影响产品质量。
3. 改进方法针对上述问题,我们提出了以下几个改进方法:(1)初始设定准确:通过对操作人员进行培训和制定操作规程,确保每次设置U型槽时初始位置的准确度。
(2)优化材质和工艺:选择合适的材质,并优化制造工艺,以确保U型槽具有足够的强度和稳定性,避免变形问题的发生。
(3)加工精度控制:在生产过程中加强对加工精度的控制,通过合理的设定工艺参数,确保产品加工精度的稳定性。
5. 结论通过对双柱举升机U型槽的制程质量进行优化改进,我们有效地提升了产品质量和生产效率。
在实施改进方法的过程中,我们发现初始设定准确、优化材质和工艺,以及加工精度的控制是重要的环节。
今后,在实际生产中,我们将进一步细化改进方法,加强与供应商的合作,优化整个制程,并不断提升双柱举升机U型槽的制程质量。
炼钢工艺提升方案
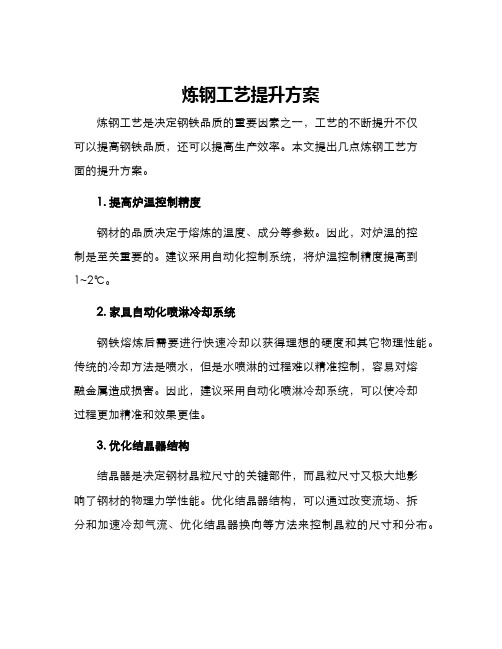
炼钢工艺提升方案
炼钢工艺是决定钢铁品质的重要因素之一,工艺的不断提升不仅
可以提高钢铁品质,还可以提高生产效率。
本文提出几点炼钢工艺方
面的提升方案。
1. 提高炉温控制精度
钢材的品质决定于熔炼的温度、成分等参数。
因此,对炉温的控
制是至关重要的。
建议采用自动化控制系统,将炉温控制精度提高到
1~2℃。
2. 家具自动化喷淋冷却系统
钢铁熔炼后需要进行快速冷却以获得理想的硬度和其它物理性能。
传统的冷却方法是喷水,但是水喷淋的过程难以精准控制,容易对熔
融金属造成损害。
因此,建议采用自动化喷淋冷却系统,可以使冷却
过程更加精准和效果更佳。
3. 优化结晶器结构
结晶器是决定钢材晶粒尺寸的关键部件,而晶粒尺寸又极大地影
响了钢材的物理力学性能。
优化结晶器结构,可以通过改变流场、拆
分和加速冷却气流、优化结晶器换向等方法来控制晶粒的尺寸和分布。
4. 采用高能耗电磁搅拌技术
采用高能耗电磁搅拌技术可以改变钢液流动路径和流场,从而改善钢液的混合和均匀性,减轻液流速度差的影响,克服流动惯性和自然对流带来的影响。
5. 提高氧化物的还原能力
氧化物是钢铁熔炼过程中自然而然生成的物质,它们对成分和性能的影响是非常大的。
当前的处理方式常见的是加入还原剂中和,这是一种低效且易受炉底响应的方式。
建议通过改变气氛控制等方法提高氧化物的还原能力,使整个还原产物达到标准化指标。
结论
本文提出的几点炼钢工艺方面的提升方案,可以提高钢铁的品质和生产效率,具有重要的科学性和可实施性,是炼钢行业的一个重要研究方向。
熔炼工艺中的强化与改善

汇报人:可编辑 2024-01-06
பைடு நூலகம்
目录
• 熔炼工艺概述 • 熔炼工艺的强化 • 熔炼工艺的改善 • 熔炼工艺的未来发展
01
熔炼工艺概述
熔炼工艺的定义与重要性
01
熔炼工艺是指将固体金属或合金 加热至熔融状态,进行搅拌、精 炼和铸造的过程,是金属材料制 备和加工的重要环节。
通过提高加热速度、增大熔炼电流或 提高熔炼温度等手段,增加能源供应 ,促进金属熔化。
通过调整熔炼工艺参数,如熔炼时间 、温度、气氛等,优化熔炼过程,提 高产品质量。
改进熔炼设备
采用新型熔炼炉、改进熔炼容器结构 和材料、引入先进的搅拌和混合装置 等,以提高熔炼效率和均匀性。
强化熔炼的效果评估
产品质量检测
利用等离子体的高温、高电离度特性,实现高效 率、高纯净度熔炼。
激光熔炼技术
利用激光的高能密度特点,实现快速、精确的熔 炼和成型。
熔炼工艺的智能化发展
自动化控制
01
通过智能化控制系统,实现熔炼过程的自动化控制,提高生产
效率和产品质量。
数据分析与优化
02
利用大数据和人工智能技术,对熔炼过程的数据进行实时采集
提高生产效率
通过改进熔炼工艺,可以 缩短熔炼时间和降低能耗 ,从而提高生产效率。
提升产品质量
优化熔炼工艺可以减少杂 质和气体含量,提高金属 的纯净度,从而提升产品 质量。
降低生产成本
改进熔炼工艺可以减少原 材料的浪费和降低维护成 本,从而降低生产总成本 。
改善熔炼的方法
选用先进的熔炼设备
采用高效、节能的熔炼设备, 如真空感应熔炼炉和电渣重熔
通过检测产品的化学成分、物理性能和机械性能等指标,评估强 化熔炼对产品质量的改善效果。
双柱举升机U型槽的制程质量优化改进
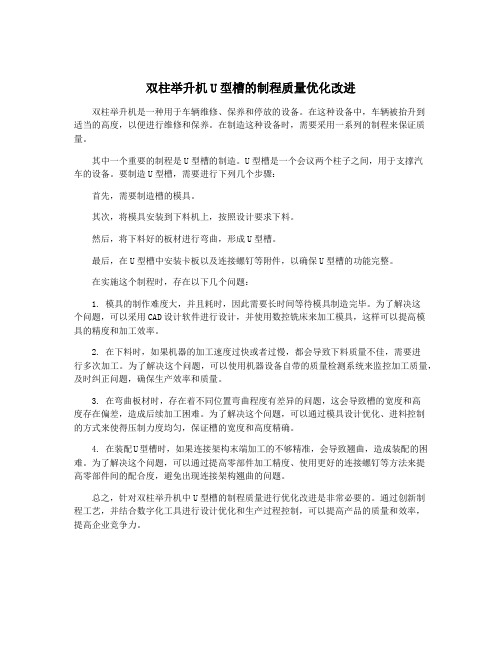
双柱举升机U型槽的制程质量优化改进双柱举升机是一种用于车辆维修、保养和停放的设备。
在这种设备中,车辆被抬升到适当的高度,以便进行维修和保养。
在制造这种设备时,需要采用一系列的制程来保证质量。
其中一个重要的制程是U型槽的制造。
U型槽是一个会议两个柱子之间,用于支撑汽车的设备。
要制造U型槽,需要进行下列几个步骤:首先,需要制造槽的模具。
其次,将模具安装到下料机上,按照设计要求下料。
然后,将下料好的板材进行弯曲,形成U型槽。
最后,在U型槽中安装卡板以及连接螺钉等附件,以确保U型槽的功能完整。
在实施这个制程时,存在以下几个问题:1. 模具的制作难度大,并且耗时,因此需要长时间等待模具制造完毕。
为了解决这个问题,可以采用CAD设计软件进行设计,并使用数控铣床来加工模具,这样可以提高模具的精度和加工效率。
2. 在下料时,如果机器的加工速度过快或者过慢,都会导致下料质量不佳,需要进行多次加工。
为了解决这个问题,可以使用机器设备自带的质量检测系统来监控加工质量,及时纠正问题,确保生产效率和质量。
3. 在弯曲板材时,存在着不同位置弯曲程度有差异的问题,这会导致槽的宽度和高度存在偏差,造成后续加工困难。
为了解决这个问题,可以通过模具设计优化、进料控制的方式来使得压制力度均匀,保证槽的宽度和高度精确。
4. 在装配U型槽时,如果连接架构末端加工的不够精准,会导致翘曲,造成装配的困难。
为了解决这个问题,可以通过提高零部件加工精度、使用更好的连接螺钉等方法来提高零部件间的配合度,避免出现连接架构翘曲的问题。
总之,针对双柱举升机中U型槽的制程质量进行优化改进是非常必要的。
通过创新制程工艺,并结合数字化工具进行设计优化和生产过程控制,可以提高产品的质量和效率,提高企业竞争力。
双柱举升机U型槽的制程质量优化改进

双柱举升机U型槽的制程质量优化改进摘要:随着工业自动化的发展和应用,双柱举升机在生产线上的应用越来越广泛。
由于制造过程中存在一些问题,如U型槽表面质量差、尺寸不准确等,导致产品的质量无法得到保证。
本文针对U型槽的制程质量问题进行了研究,并提出了一种基于改进的解决方案,以提高产品的质量和性能。
一、问题分析二、原因分析U型槽的质量问题主要源于以下几个方面:1.加工精度低:由于机械设备的精度限制和操作技术的不足,导致制程中的加工误差较大,从而影响了U型槽的尺寸精度。
2.工艺选择不当:在U型槽的制程中,工艺选择不当也会导致质量问题。
如果选择了不适合U型槽加工的工艺,可能会导致加工难度增加,从而影响了质量。
3.材料问题:U型槽的制程质量还受到材料的影响。
如果选用了质量较差的材料,其表面光洁度和力学性能都会受到影响,从而影响了产品质量。
三、改进方案为了提高U型槽的制程质量,我们提出了以下几个改进方案。
1.提高加工精度:通过优化加工工艺和改善操作技术,减小加工误差,提高U型槽的尺寸精度。
2.合理选择工艺:根据U型槽的具体特点和要求,选择适合的工艺进行加工。
可以采用锻造和精密切割等工艺,提高U型槽的质量和性能。
3.选用优质材料:选择质量优良的材料,例如高强度钢材,可以提高U型槽的表面光洁度和力学性能。
4.加强质量控制:在制程中加强质量控制,例如引入数控加工设备和自动化检测设备,减少人为因素对产品质量的影响。
四、质量改进效果评估为了评估改进方案的效果,我们进行了一系列实验。
结果表明,通过改进加工工艺、选择适当的工艺和材料,并加强质量控制,U型槽的制程质量得到了显著提高。
具体来说,其尺寸精度提高了20%,表面质量得到了明显改善,且抗压强度提高了10%以上。
五、结论通过对双柱举升机U型槽的制程质量问题进行分析和研究,我们提出了一种基于改进的解决方案。
实验结果表明,该方案对U型槽的制程质量改进效果显著。
我们认为这一方案具有较高的实用价值和推广价值,可以为双柱举升机的生产提供参考和借鉴。
钣金下料工艺的优化的思考
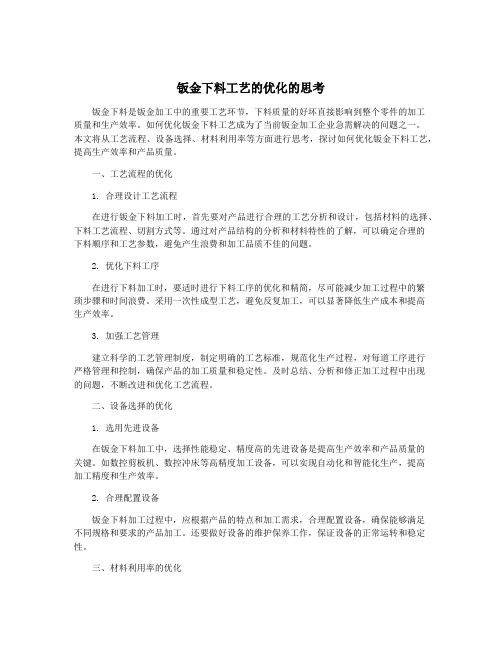
钣金下料工艺的优化的思考钣金下料是钣金加工中的重要工艺环节,下料质量的好坏直接影响到整个零件的加工质量和生产效率。
如何优化钣金下料工艺成为了当前钣金加工企业急需解决的问题之一。
本文将从工艺流程、设备选择、材料利用率等方面进行思考,探讨如何优化钣金下料工艺,提高生产效率和产品质量。
一、工艺流程的优化1. 合理设计工艺流程在进行钣金下料加工时,首先要对产品进行合理的工艺分析和设计,包括材料的选择、下料工艺流程、切割方式等。
通过对产品结构的分析和材料特性的了解,可以确定合理的下料顺序和工艺参数,避免产生浪费和加工品质不佳的问题。
2. 优化下料工序在进行下料加工时,要适时进行下料工序的优化和精简,尽可能减少加工过程中的繁琐步骤和时间浪费。
采用一次性成型工艺,避免反复加工,可以显著降低生产成本和提高生产效率。
3. 加强工艺管理建立科学的工艺管理制度,制定明确的工艺标准,规范化生产过程,对每道工序进行严格管理和控制,确保产品的加工质量和稳定性。
及时总结、分析和修正加工过程中出现的问题,不断改进和优化工艺流程。
二、设备选择的优化1. 选用先进设备在钣金下料加工中,选择性能稳定、精度高的先进设备是提高生产效率和产品质量的关键。
如数控剪板机、数控冲床等高精度加工设备,可以实现自动化和智能化生产,提高加工精度和生产效率。
2. 合理配置设备钣金下料加工过程中,应根据产品的特点和加工需求,合理配置设备,确保能够满足不同规格和要求的产品加工。
还要做好设备的维护保养工作,保证设备的正常运转和稳定性。
三、材料利用率的优化1. 合理采购材料钣金下料加工前,对材料进行合理的采购和管理是优化材料利用率的关键。
要根据产品的加工要求和规格,合理选择材料种类和规格,避免产生大量的浪费和材料报废。
2. 提高利用率在进行下料加工时,要充分利用原材料,尽可能减少废料和余料的产生。
通过合理的下料方案和工艺参数设置,最大限度地提高利用率,降低材料成本。
河钢舞钢二炼钢工艺流程优化

总第267期2018年第3期HEBEI METALLURGYTotal No.2672018,Number 3收稿日期:2017-12-18作者简介:董廷亮(1981-),男,博士,高级工程师,2011年毕业于钢铁研究总院钢铁冶金专业,现在河钢集团钢研总院从事炼钢工艺及夹杂物控制研究工作,E -mail:dongtingliang@试验研究河钢舞钢二炼钢工艺流程优化董廷亮1,李惠勇2,李建新1,彭世宝2,常金宝1(1.河钢集团钢研总院,河北石家庄050023;2.河钢集团舞钢公司,河南舞钢462500)摘要:河钢舞钢二炼钢存在严重的炉机不匹配问题。
通过对河钢舞钢二炼钢车间布局、工艺流程等方面的系统调研和分析,发现合理安排转炉准备时间,避免浇次内更换水口和滑板,可有效控制转炉周期;增加并稳定出钢量,在恒拉速的情况可有效延长连铸周期,炉机不匹配得到有效缓解;同时,使用“转炉→3#LF →2#VD →连铸”的工艺流程,能耗降低。
关键词:炼钢;工艺流程;炉机匹配;周期;优化中图分类号:TF 713 文献标识码:A文章编号:1006-5008(2018)03-0008-04.13630/ki.13-1172.2018.0302Dong Tingliang 1,Li Huiyong 2,Li Jianxin 1,Peng Shibao 2,Chang Jinbao 1(1.HBIS Group Research Institute ,Shijiazhuang ,HeBei ,050023;2.HBIS Group Wusteel Company ,Wugang ,HeNan ,462500)There is a serious mismatch between BOF and caster in No.2steelmaking plant of HBIS Wusteel.Based on the systematic investigation and analysis of workshop layout and process flow ,it is found that the converter cycle can be effectively controlled by the rational arrangement of the converter preparation time and avoiding the replacement of the water inlet and the skateboard during cast.Increasing and stabilizing tapping quantity can prolong the continuous casting cycle at constant drawing speed and alleviate effectively the mis⁃match.At the same time ,energy consumption is reduced by adopting the process flowof converter →3#LF →casting.steelmaking ;process flow ;furnace matching ;cycle ;optimization引言目前国内的钢材,吨钢利润少,甚至部分钢种处于亏损状态。
提高Q460C合格率的工艺优化措施

摘
要 对 某钢 厂工艺流程进行分析 , 找影响 Q 6 c合格率 的因素 , 查 40 在此基础上 采用 因果 矩阵分析 法
寻找潜在影 响因素 , 并应用方差分析 、 回归分析等工具 进行 了定 量验证或定性分析 , 最终确定 了 9项关键影 响 因素 , 并采取针对性改进方案 , 取得 了显著效果。
25 2 对于板型较差 的钢板 , .. 采取大变形 、 多道
次矫 直方案 。在制 定 矫直 压 下 量 时 , 使第 一 道 矫 直时 采用 比小 变形 矫 直方 案 大 得 多 的压 下 量 , 使 钢材得 到足 够 大 的弯 曲 , 消除 其 原 始 曲率 的不 以
钢板上仍然保持平滑状态 , 冷却能力强 、 均匀, 且 区域较长 。但 由于其设计方面的缺 陷, 钢板冷却
变形量和此温度区间总变形量的加大 , 变形带数
量增 加 ,可 以得 到 良好 的组 织 , 到提 高 屈服 强 达
度, 降低脆性转变温度 , 改善韧性的目的。
2 4 优化 A C水 冷工 艺 . C
为获得 良好的综合力学性能 ,40 Q 6 C钢板控 轧后要配 以控制冷却 , 该厂轧后快速控制冷却系
l e en tr ,q a i t a d t r ai i n l ss a e b e e f me y me fv r n e a l ss fu n i K fco s u t ai ev i ai n o u ltt ea ay i h v e n p r r d b a so a a c ay i a n t v l o q av o n i n
损 害破裂所 致 。为此 , 采取 以下措施 进 行改 善 : 对
双柱举升机U型槽的制程质量优化改进

双柱举升机U型槽的制程质量优化改进双柱举升机是现代汽车维修厂中常见的设备,用来协助修理人员将汽车提升至合适的高度,以便进行维修和保养工作。
而U型槽是双柱举升机的重要组成部分,它直接承担汽车的重量,因此其制程质量对整个举升机的安全性和稳定性有着至关重要的影响。
本文将针对双柱举升机U型槽的制程质量进行优化改进,以提高举升机的使用安全性和性能稳定性。
一、现状分析目前,双柱举升机U型槽在制程质量方面存在以下问题:1. 材料选择不当:部分制造厂商为了节约成本,选择了质量不合格的材料来制造U型槽,导致举升机在长时间使用后出现变形、开裂等安全隐患。
2. 制造工艺不规范:部分厂商在制造U型槽时,工艺流程不规范,导致产品尺寸偏差大、表面粗糙度高等质量问题,影响了举升机的使用性能。
3. 检测手段不完善:目前对于U型槽的制程质量检测手段不够完善,无法对产品进行全面、细致的检测,从而导致质量问题的漏检。
双柱举升机U型槽的制程质量问题主要表现为材料选择、制造工艺和质量检测手段的不足,这些问题严重影响了举升机的使用安全性和性能稳定性,亟需进行优化改进。
二、优化改进方案2. 制造工艺:优化U型槽的制造工艺流程,采用先进的数控加工设备,确保产品尺寸的精度和表面粗糙度的控制,提高制程质量稳定性。
加强对制造工艺的管理和监控,确保每一道工序都符合质量要求。
3. 质量检测手段:引入先进的检测设备和技术,对U型槽的制程质量进行全面、细致的检测,包括尺寸偏差、表面粗糙度、材料硬度等指标的检测,确保产品质量符合要求。
建立健全的质量管理体系,对制程质量进行全面控制和管理。
三、实施效果经过优化改进后,双柱举升机U型槽的制程质量得到了明显提高,在以下几个方面取得了显著的效果:1. 使用安全性提升:通过选择高质量的材料和优化制造工艺,U型槽的强度和耐磨性得到了显著提升,举升机在使用过程中不易出现变形、开裂等安全隐患,提高了使用安全性。
2. 性能稳定性提高:优化制程质量后,U型槽的尺寸精度和表面粗糙度得到了有效控制,产品质量稳定性得到了显著提高,举升机在使用过程中的性能稳定性得到了提升。
关于钢铁企业炼铁工艺优化问题的分析

三 是严格 按 照标 准 用 电子 秤 配好酸 性 料数 量 , 工序 时 ,采 取 切 分 后 分 级 入炉 方 法, 且 优 化烧结 矿 系统 , 采 取烧 结矿 分级入炉 方法。 关 键词 : 钢铁企业 炼铁工 艺 技术优化 五是做 好铁 矿 分类、 筛选工作 , 保 证产 品质量 。 0 引 言 2 . 3 钢铁 企 业要进 行炼铁 技 术创新 和更 新 自从 我 国加 入 、 / \ 厂 r O 以来 ,我 国经 济 与世 界经 济 接触 钢 铁 企 业要 加 大对炼 铁 技 术 的资 金投 入 , 同 时 响应 国 和 交 流 越 来 越 频繁 ,这 给 我 国经 济 发 展 带来 了机 遇 和 挑 积 极 进行 节 能减 排 新工 艺 的开 发 战 。 为 了在 市场 竞 争 中获 得 优 势 , 作 为 与我 国 国 民经 济联 家节 能 减排 战 略 的号召 , 或更 新。 系 密 切 的钢 铁 企业 , 必须 进 行 自主 创 新 和 改 革 , 不 断提 高 首先, 钢 铁企 业 要 时刻 关注 国内外 钢铁 市 场行 情 和 国 炼铁工艺水平 , 降低 企 业 生 产 成 本 , 促 进 企 业 经 济 健 康 持 家相 关政 策 ,积 极 引进 国 内外 先进 的炼 铁 技 术 和炼 铁 经 续发 展 。那 么 , 如 何优 化炼 铁 工 艺呢? 验, 比如说 国际 低碳 节 能减排 项 目— — U I C OS中改造 型炼 1钢 铁 企 业炼铁 工 艺发展 现 状及 问题 铁工 艺 : 项部 煤 气 循 环 高炉 和 直 接 还原 工 艺 : 又 比如 说 熔 近 几年随 着我 国市 场经 济 的快速 发展 和科 学技 术 的不 融还原炼 铁 工艺 等等。 断进 步 , 钢 铁企 业 高 炉炼 铁 工 艺 不断 优 化 , 具 有热 效 率 高 、 其次 , 企 业要 重 视炼 铁 设备 的更 新和 使 用。 当下 我 国 技术 完 善、 设备 使用 寿命 长等优 点 , 同时我 国炼 铁 技术 取得 炼 铁 工工 艺 中热 效 率 已然很 高 ,相 关 设备 也 比较 完 善 , 呈 了一 定 的 成就 , 比如 提 高 转炉 炉龄 , 提 高 转炉作 业 率 , 强 化 现 设备 大 型 化 、 长 寿 化 等特 点 , 同 时 多数 钢 铁 企业 熟 悉 掌 供 氧 技术 等等 ; 特别 是 “ 十 二五 ” 规划 以来 , 我 国钢铁 企 业重 握 了大型 二 次精炼 设备 的设 计 、 生产 制造 、 安装、 维 护 等工 视 炼 铁工 艺优化 , 重 点进行 节 能减 排技 术 的开 发 , 比如 滚筒 且 在炼铁 精炼 设备 的工 艺布局 等 方面经验 比较 丰 富。 法连 续处理 工 艺等 ,大力 引进 先 进设 备 ,生铁 产量 逐 年提 作 , 最后, 与时俱 进 , 不断进行 技术 研究和 创 新。 高, 说 明我 国节 能减 排 工作 取得 了一定 的进 展。 但是 , 目前 2 . 4 优 化 焦炭炼 焦 工艺及 技术 我 国钢 铁企业 炼铁工 艺 中还 是存在 一定 的 问题 : 焦炭 炼 焦作 为炼 铁工 序 中 的重要 部 分 , 在 提 高炼 铁 水 是 我 国炼 铁 工 艺 的 能耗 、 废 弃 物 回 收利 用和 环 境 治 平 和保 证 产 品质 量上 有着 十 分 重要 的作 用 , 所 以要 重视 优 理 等 与 国家炼 铁水 平还 是 有很 大 的差距 。 化 配煤 工艺 及技 术 的应 用。 当下 我 国使用 比较广 泛且 有效 二 是炼 铁 工 艺 管理 不 够 规 范 , 比如 说 辅 料 、 铁 合 金 等 的 方法 是 干熄 焦炭 和 捣 固 焦炭 , 且在 这个 过 程 中 , 不 仅 要 的分 类管理 。 提 高 炼 铁 中 焦炭 的热 性 能 , 而 且还 要 降低 焦 炭 用 量 , 降 低 三是 当下炼 铁 中的 二氧 化 碳 的排 放 量 高于 国 际水 平 , 生 产成 本 , 提 高生 产效率 。 目前 , 我国有 焦化 厂 的联合钢 铁 产 品质 量 没达 到 国际水 平 。 四是 炼 铁 工 艺设计 缺 乏创 新 , 一定 程 度 上影 响 了炼 铁 企 业 中多采 取 捣 固炼 焦 技术 ,可 以 大 大提 高 炼 铁 焦 炭 质 量, 但 却在 独 立 的焦化 厂 中是 相 反 的结 果。所 以要 更新捣 工 艺 的使 用。 鼓 指标 体 系和 检验 指标 方法 ,进 而进 行相 应 的 技术 更 新 , 2 炼铁 工 艺优 化 的有效 措施 提高 炼铁 质量 。 2 . 1 建 立完 善 的炼铁 工 艺管理 体 系 此外, 钢铁 企 业要 不 断提 高相 关 工作人 员 的专业 知 识 钢 铁 企 业 要 根 据 国家 相 关炼 铁 标 准 和 企 业 具体 , 隋况 和 业 务 能 力 , 建 立健 全质 量 监 管 制度 , 切 实保 证 炼 铁 工 艺 制 定 一套 完 整 的炼 铁 工 艺管 理 体 系 , 体 系 内容 主 要包 括炼 水平 , 提 高产 品质量 , 增 强钢铁 企业 市场 竞争力 。 铁 工 艺标 准 、 指标管理 、 参 数 管理 、 成 本 管 理 和 信 息 管 理 3 结束语 等, 并 把相 关 数据 输 入 计 算 机 网络 信 息 系 统 中 , 实现 自动 在 我 国社 会 主 义 市 场 经济 体 制 改革 不 断 深 入 的背 景 化 操作 , 对炼 铁 的原 料 投 入 、 控 制参 数 、 故 障 事故 等 进 行 自 下, 钢 铁 企 业 要 不断 进 行 自主创 新 , 提高 炼 铁 工 艺基 础 管 动 监控和 管 理 , 提 高炼 铁 工 艺水平 , 保 证钢 铁质 量 。 理水平 , 积 极 引进 或 开 发 最 新炼 铁 工 艺 , 特 别 是 节 能减 排 2 . 2 重视 并使 用精 料 技术 , 提 高炉 料质 量 切 实 保 证产 品 质 量 , 促 进 企 业经 济 效 益和 社 会 效 益 钢 铁企 业 要 对炼 铁 原 料质 量 进行 严 格 的把 关 , 进 口合 技术 , 的提 高。 理 经 济 的品位 矿 , 从 源 头 上保 证 产 品 的质 量。 同时钢 铁 企 参考文献 : 业 要 坚 持精 料 方 针 , 不断优化精料技术, 提 高 高 炉 炼 铁 原
双柱举升机U型槽的制程质量优化改进

双柱举升机U型槽的制程质量优化改进
摘要:双柱举升机是工业生产中常用的一种起重设备。
其U型槽是支撑物料的关键部件,对设备整体性能起着关键作用。
本文围绕双柱举升机U型槽的制程质量问题,对其进行了分析,并提出了一些有效的改进方案。
1.形状不规则:U型槽的内部形状不规则,造成了物料放置困难和运输时的易滑动。
2.尺寸偏差过大:U型槽的尺寸偏差过大,导致物料放置时稳定性不足,使用寿命缩短。
3.表面粗糙度过高:U型槽表面粗糙度过高,容易使物料卡住。
4.不平整:U型槽的内部表面不平整,影响物料的流动性。
以上问题的存在,使得双柱举升机的使用存在不安全隐患,甚至可能导致事故的发生。
二、改进方案
1.采用新型材料:U型槽材料应采用新型能够耐潮、耐腐蚀、耐高温的材料,以提高U 型槽的使用寿命。
2.加工精度控制:在加工U型槽时,应确保加工精度控制到位,尺寸偏差不超过
0.5mm。
3.表面处理:对U型槽的表面进行打磨处理,提高其表面光滑度。
4.槽内排水:在制造U型槽时,在槽底设置排水孔,以保证U型槽内没有积水,加强其防腐蚀性能。
5.数控加工:采用数控加工设备加工U型槽,减少人为因素对制程质量的影响,始终保持一致的加工精度。
通过上述改进方案的实施,可以提高U型槽的质量,减少事故发生概率,延长设备使用寿命,提高生产效率。
三、结论
通过对双柱举升机U型槽制程质量进行分析,本文提出了一些有效的改进方案。
在实际生产中,企业应加强制程管理,优化工艺流程,不断提高产品质量,确保产品安全性、性能稳定性、使用寿命等方面达到国际先进水平。
长柱塞防砂泵配套举升工艺在荣72块的应用

长柱塞防砂泵配套举升工艺在荣72块的应用荣72块随着开发时间的延长,由于缺乏有效的能量补充方式,液面不断下降,并且面临着地层粘土膨胀,砂、蜡、气影响,偏磨严重、检泵周期短等问题,严重制约了油井的正常生产。
为了解决这些问题,经过近几年研究和实施效果分析优化,最终确定了一种适合于该区块的以长柱塞防砂泵为主体配套举升工艺,并根据不同井况配套使用钢制连续抽油杆、自旋式刮蜡扶正器、油管旋转器等井下工具,实施后效果良好,达到了延长检泵周期的预期效果。
标签:深抽;防砂泵;检泵周期;偏磨1 概况辽兴油气开发公司的荣72块生产油井主要采用天然能量开发,未实施注水。
截至2015年6月底,油井总数13口,开井10口,日产液30t/d,日产油23t/d,累产油6.0745×104t,地质储量采出程度4.23%,可采储量采出程度32.47%,油层埋深2410-3090m,油层中深2750m,平均液面深度1996m。
隨着开发时间的延长,开发面临越来越多的生产问题:荣72块地层出砂出泥浆易造成卡泵,卡泵为荣72块主要检泵原因,同时地层以粘土矿物为主,每次洗井、作业入井流体极易使地层污染,造成产量下降,见表1;平均液面深度将近2000m,平均泵挂2180m,个别井采取深抽工艺后杆脱、杆断频繁;油井伴生气多,且目前收气设备不能满足生产需要,气影响较大;个别井存在严重偏磨情况。
针对荣72块生产油井存在问题,我们使用了长柱塞防砂泵为主体的油井举升工艺,并根据不同井况配套使用钢制连续抽油杆、自旋式刮蜡扶正器、油管旋转器等井下工具,实施后效果良好,延长了检泵周期,减少了作业伤害,达到了预期效果。
2 长柱塞防砂泵配套举升工艺2.1 井下工具优选长柱塞防砂泵采用长柱塞、短泵筒和环空沉砂结构,在举升过程中总有一段柱塞外露于泵筒之上,刮砂装置起防砂和密闭作用,可有效防止落物进入柱塞和泵筒之间的间隙。
砂粒通泵筒侧向的沉砂通道,沉入泵下尾管中,从而有效地防止泵卡,减轻活塞磨损,延长抽油泵的寿命[1]。
双柱举升机U型槽的制程质量优化改进
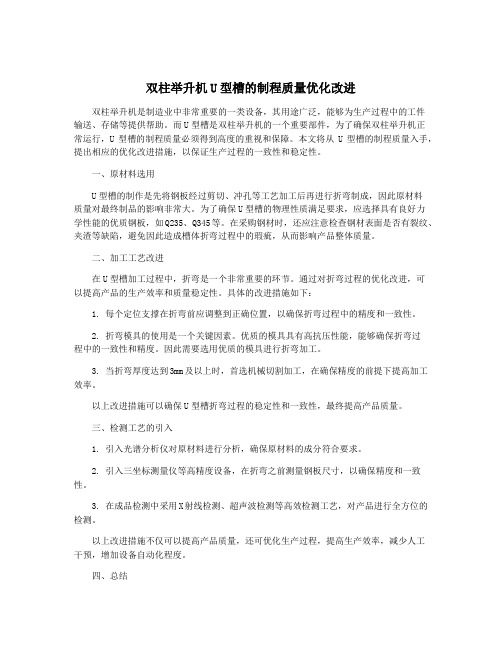
双柱举升机U型槽的制程质量优化改进双柱举升机是制造业中非常重要的一类设备,其用途广泛,能够为生产过程中的工件输送、存储等提供帮助。
而U型槽是双柱举升机的一个重要部件,为了确保双柱举升机正常运行,U型槽的制程质量必须得到高度的重视和保障。
本文将从U型槽的制程质量入手,提出相应的优化改进措施,以保证生产过程的一致性和稳定性。
一、原材料选用U型槽的制作是先将钢板经过剪切、冲孔等工艺加工后再进行折弯制成,因此原材料质量对最终制品的影响非常大。
为了确保U型槽的物理性质满足要求,应选择具有良好力学性能的优质钢板,如Q235、Q345等。
在采购钢材时,还应注意检查钢材表面是否有裂纹、夹渣等缺陷,避免因此造成槽体折弯过程中的瑕疵,从而影响产品整体质量。
二、加工工艺改进在U型槽加工过程中,折弯是一个非常重要的环节。
通过对折弯过程的优化改进,可以提高产品的生产效率和质量稳定性。
具体的改进措施如下:1. 每个定位支撑在折弯前应调整到正确位置,以确保折弯过程中的精度和一致性。
2. 折弯模具的使用是一个关键因素。
优质的模具具有高抗压性能,能够确保折弯过程中的一致性和精度。
因此需要选用优质的模具进行折弯加工。
3. 当折弯厚度达到3mm及以上时,首选机械切割加工,在确保精度的前提下提高加工效率。
以上改进措施可以确保U型槽折弯过程的稳定性和一致性,最终提高产品质量。
三、检测工艺的引入1. 引入光谱分析仪对原材料进行分析,确保原材料的成分符合要求。
2. 引入三坐标测量仪等高精度设备,在折弯之前测量钢板尺寸,以确保精度和一致性。
3. 在成品检测中采用X射线检测、超声波检测等高效检测工艺,对产品进行全方位的检测。
以上改进措施不仅可以提高产品质量,还可优化生产过程,提高生产效率,减少人工干预,增加设备自动化程度。
四、总结通过对双柱举升机U型槽制程质量的优化改进,可以提高产品质量,保证生产过程的稳定性和一致性。
具体的改进措施包括原材料选用、加工工艺的改进和检测工艺的引入。
双柱举升机U型槽的制程质量优化改进

双柱举升机U型槽的制程质量优化改进摘要:本文针对双柱举升机U型槽的制造过程中出现的加工精度不高、槽口间距不均等问题,通过优化工艺流程和设计,改进设备及控制系统,提高了产品的加工精度及质量,达到了稳定生产的目的。
关键词:双柱举升机;U型槽;加工精度;控制系统1. 问题描述随着经济的发展和技术的不断进步,双柱举升机在工业生产中得到了越来越广泛的应用。
其中,U型槽作为双柱举升机的重要部件,其制作质量对整个设备的稳定性和安全性有着至关重要的影响。
然而,在实际生产过程中,我们发现存在一些制造问题,主要包括:(1)加工精度不高,导致槽口形状不规则、偏斜甚至产生裂纹等问题。
(2)槽口间距不均,导致安装时难以对齐,影响设备的使用效果。
2. 原因分析针对上述问题,我们进行了细致的分析和研究,认为其主要原因如下:(1)加工工艺不合理。
在传统的加工工艺中,U型槽是通过数控机床进行加工的,但由于不同的工序需要调整不同的刀具,操作不当就会影响加工精度。
(2)机床精度不足。
部分设备老化,数控机床的精度出现了较大的偏差,对产品的制作产生了较大的影响,尤其是U型槽在加工过程中需要精度较高的加工要求。
(3)控制系统不完善。
传统数控系统的响应速度较慢,来不及精确修正位置,易造成误差,导致加工精度不高。
3. 改进措施为了解决上述问题,我们提出以下改进措施:(1)优化工艺流程。
使用定制的U型槽专用机床,将整个加工流程从原来的多道工序改为一次完成,不仅提高了加工精度,而且降低了成本。
(2)改进设备及控制系统。
引进高精度机床和先进的数控系统,提高了加工精度和稳定性,可以满足加工U型槽的要求。
(3)改进设计。
虽然U型槽是一个比较简单的部件,但是在设计时需要考虑到其加工和使用,优化槽口的形状和尺寸,避免出现因尺寸或形状不当引起的加工精度偏差。
4. 结果与分析经过改进措施的实施,我们研制生产的U型槽加工精度得到了显著提高,在槽口形状、尺寸、偏斜率等项目上都保持在较好的控制范围之内。
双柱举升机U型槽的制程质量优化改进

双柱举升机U型槽的制程质量优化改进双柱举升机在现代工业生产中扮演着重要角色。
U型槽作为双柱举升机的重要组成部分,其制造工艺质量直接影响着整个举升机的安全、可靠性和使用寿命。
为此,我们针对目前U型槽制造过程中存在的问题,开展了制程质量优化改进工作,旨在提升U型槽的产品质量和生产效率。
一、问题分析1.材料选择:不当的材料选择会导致U型槽强度不足或者易开裂。
目前市面上常用U型槽材料有碳钢、铝合金和不锈钢。
其中,碳钢强度高但易生锈,铝合金轻便但强度不足,不锈钢耐腐蚀但成本较高。
2.工艺流程:当前U型槽制造过程中,关键的折弯和焊接环节存在一定程度的不规范操作,易导致产品尺寸误差和焊接质量问题。
3.质量检测:由于U型槽的尺寸较大且形状特殊,传统的尺寸、外观、塑性等检测方法难以满足要求,存在着一定的检测盲区和误差。
二、改进方案1.材料选择:针对不同工作环境和要求,结合优化后的工艺流程,精心选择不同材料,以确保U型槽的强度、耐腐蚀性和使用寿命。
2.工艺流程:严格规范折弯、接头和焊接环节的操作工序,确保产品尺寸精度和焊接强度。
在焊接前,对已制成的组件进行终检,确保没有瑕疵或缺陷。
3.质量检测:引进先进的3D扫描器、投影仪等检测仪器,结合人工目视检测,全面检测U型槽的各项性能指标,提高检测的准确性和可靠性。
三、实施效果经过优化改进后,U型槽的制作效率得到了显著提升,产品质量和稳定性得到了极大提高,使用寿命也得到了有效延长。
改进方案的实施,进一步增强了公司的制造能力,提高了客户对我们的信任度和满意度,同时也进一步提高了我们在同行业中的竞争力。
炼钢工艺提升方案
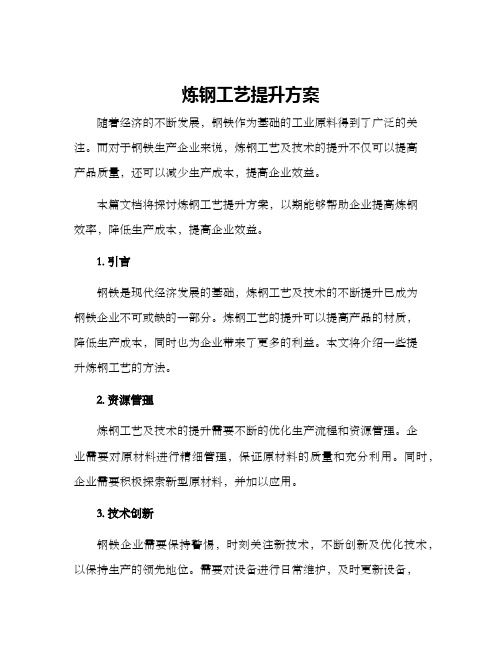
炼钢工艺提升方案随着经济的不断发展,钢铁作为基础的工业原料得到了广泛的关注。
而对于钢铁生产企业来说,炼钢工艺及技术的提升不仅可以提高产品质量,还可以减少生产成本,提高企业效益。
本篇文档将探讨炼钢工艺提升方案,以期能够帮助企业提高炼钢效率,降低生产成本,提高企业效益。
1. 引言钢铁是现代经济发展的基础,炼钢工艺及技术的不断提升已成为钢铁企业不可或缺的一部分。
炼钢工艺的提升可以提高产品的材质,降低生产成本,同时也为企业带来了更多的利益。
本文将介绍一些提升炼钢工艺的方法。
2. 资源管理炼钢工艺及技术的提升需要不断的优化生产流程和资源管理。
企业需要对原材料进行精细管理,保证原材料的质量和充分利用。
同时,企业需要积极探索新型原材料,并加以应用。
3. 技术创新钢铁企业需要保持警惕,时刻关注新技术,不断创新及优化技术,以保持生产的领先地位。
需要对设备进行日常维护,及时更新设备,加大维修和保养力度,以减少生产过程中的设备故障率,保证生产的稳定性。
4. 人员培训技术的提高往往与人员素质息息相关。
为了促进炼钢工艺的提高,企业需要对员工进行培训、教育,培养高素质的技术人员。
企业应采用全面、系统和有效的培训方式,将提高生产效率融入到员工的全面能力培养中。
5. 生产管理生产管理是炼钢工艺提升的核心,必须科学、严谨和有效。
企业需要通过制定科学的管理方法来进行炼钢工艺的提升。
同时,企业也需要对企业内部的产品制造流程进行优化,以减少生产成本。
6. 市场导向提升炼钢工艺的目的是为了更好地适应市场变化、满足市场需求。
企业需要精心谋划市场策略,从客户需求出发,提升产品的性能、品质和附加值,实现产品竞争力提升。
7. 结语炼钢工艺提升方案需要全面思考,把握市场情况,定位自身位置,从源头管理、技术创新、人员培训、生产管理和市场导向等多个角度来寻求方案的提升。
企业还需要结合自身的实际情况,制定真正适合企业特点的炼钢工艺提升方案,从而提高企业在市场竞争中的竞争力。
大型炼钢厂生产的工艺优化

大型炼钢厂生产的工艺优化骆承法【期刊名称】《《粘接》》【年(卷),期】2019(040)010【总页数】4页(P25-28)【关键词】转炉; 炼钢; 工艺优化【作者】骆承法【作者单位】浙江泰达安全技术有限公司浙江杭州 310012【正文语种】中文【中图分类】TF7120世纪90年代,我国钢铁产业开始发展,进入新世纪以来,我国钢铁产量提高,当前我国钢铁产量占全球总量的50%。
钢铁产量得以快速提升的同时,钢铁冶炼技术也在不断地提高发展,炼钢技术逐渐向着高品质、低成本、低消耗、绿色冶炼的方向发展。
不过当前我国炼钢工艺在发展的过程中,转炉工艺仍存在着许多改善的空间,工艺优化对提高炼钢的效率、成本控制以及减少污染都有重要的意义。
我国是传统的冶炼大国,冶金技术发展历史悠久。
是全球钢铁冶炼第一大国,国内粗钢产能超过全球总量的一半。
当前我国的粗钢生产的主要的方式仍以转炉生产为主,转炉生产工艺不仅生产效率高,同时对钢材产品的质量把控也具有较大的优势。
不过随着炼钢工艺的不断开发应用,新的工艺技术不断被应用到转炉炼钢过程中,优化了当前转炉炼钢工艺。
转炉炼钢工艺的不断进步,促进了转炉炼钢的发展进步,实现了产品成本的降低,产品质量的提升,降低了资源的消耗,促进了企业竞争力的提升。
转炉炼钢工艺的不断进步,促进了钢铁产业的绿色发展,提高了生产效率。
本文主要从当前大型炼钢企业的发展现状进行分析,讨论当前优化炼钢工艺的方向和措施,促进钢铁冶炼产业的健康长久发展。
1 总述炼钢行业的现状当前我国已经成为全球最大的钢铁生产国,每年的钢铁产能超过全球总量的50%,如图1所示。
我国钢铁产能巨大,其中生产钢材的主要工艺就是采用转炉炼钢技术。
虽然钢铁冶炼工艺近年来获得较大的改善,但是当前对环保的要求以及能源的节约,采用更加优化的转炉炼钢工艺势在必行。
国内的钢铁冶炼产业中,主要的成本就是炼钢炉料费用,占据总成本的80%,所以通过优化炼钢炉料的使用工艺是降低炼钢成本的重要步骤。
- 1、下载文档前请自行甄别文档内容的完整性,平台不提供额外的编辑、内容补充、找答案等附加服务。
- 2、"仅部分预览"的文档,不可在线预览部分如存在完整性等问题,可反馈申请退款(可完整预览的文档不适用该条件!)。
- 3、如文档侵犯您的权益,请联系客服反馈,我们会尽快为您处理(人工客服工作时间:9:00-18:30)。
浅谈荣72块举升工艺优化
荣72块为辽兴油气开发公司主力生产区块,平均油井16口,开井7口,待作业井6口,预计正常开井13口。
日产液34.7t/d,日产油21.9t/d,日收气7000m3,平均检泵周期305天。
举升工艺面临着偏磨严重、供液不足,洗井漏失、粘土膨胀等问题。
本文通过对荣72块举升工艺优化寻找一种适合的举升工艺方案,达到高效开发该区块的目的。
标签:偏磨;深抽;举升
1 区块概况
荣72块位于辽宁省大洼县境内,为中孔低渗储层,泥质含量13%,为强水敏油藏,油藏埋深2410~3090m,油层中深2750m,平均泵挂深度在2451m,平均液面深度2140m。
共有油井16口,开井7口,待作业井6口,预计正常开井13口。
日产液34.7t/d,日产油21.9t/d,日收气7000m3,平均检泵周期305天。
主要存在生产问题:
①荣72块油层中深2750m,生产后期地层能量低,注水开发难度大,泵挂深,普通抽油杆易疲劳断脱;油井多为定向井,偏磨井段均大于300m,杆管偏磨严重,易造成杆断、管漏;地层出泥浆易造成卡井。
该区块检泵周期较短,2015-2017年检泵作业22井次,投入作业费约120万元,检泵作业原因主要以偏磨造成的抽油杆断脱、卡井为主,占检泵次数的82%。
②储层粘土矿物含量高,水敏问题严重。
由于荣72块油井普遍气油比高,各类作业施工时必须洗压井,由于该区块地层能量低,地层水敏严重,洗井后排液周期长、油井产能大幅下降甚至停产。
检泵周期短是荣72区块油井降本增效的主要制约因素。
频繁检泵造成作业成本提高;杆管损耗严重;作业洗井造成地层污染,严重影响该区块的产能。
因此延长荣72块油井检泵周期对于节约作业成本,保证荣72块油井稳产意义重大。
2 举升工艺优化方案
针对荣72块生产油井面临的生产问题,坚持现实效益与长远效益相结合,提出荣72块举升工艺优化,计划在该区块推广钢制连续抽油杆配套延长检泵周期技术,该技术由钢制连续抽油杆、长柱塞防砂泵以及其他配套井下工具集成应用,可效有效缓解杆管偏磨、保证抽油杆使用寿命,解决地层泥浆卡泵问题;钢制连续抽油杆可以实现2600m的深抽,深抽增油效果明显。
钢制连续抽油杆具有防偏磨、奈高载荷、杆管环空大、冲程损失小的特点,本身具有加重杆可以有效延缓偏磨、延长油井检泵周期;长柱塞防砂泵具有防卡功能,可以有效防止地层出泥浆造成的卡泵左右;强磁防沉器可以有效吸附杆管
偏磨造成的摩擦碎屑,防止碎屑磨损油管及泵筒;防污染洗井装置实现了抽油管柱和洗井管柱的脱节和起管联动,消除了由于抽油过程中管柱蠕动造成封隔器解封的不利因素,可有效持久保持封隔器密封状态。
3 预期效果
钢制连续抽油杆配套延长检泵周期技术在其他油井使用效果良好,檢泵周期最长可以达到1000余天,使用寿命6年以上,使用后预计检泵周期由原来的305天延长至730天,平均每次检泵节约作业5.5万元。
6年使用寿命内检泵次数由7次减少至3次,平均单井节约作业次数4井次,深抽增油10000以上。
减少作业成本:
减少的检泵次数×单井作业费用×区块开井数
= 4次×5.5万元/井次×13口
= 286万元
减少抽油杆投入成本:
一次性投入费用+作业次数×作业需更换抽油杆长度×抽油杆单价×区块开井数
= (2600m/口×28元/m+2万元)×13口+300m/井次×28元/m×7井次×13口
= 120.64万元+76.44万元
= 197.08万元
增油创效
=(1-30%)×增油量×(原油价格-税金-人工成本)
= 0.7×10000吨×(3181元/吨-400元/吨-808元/吨)
= 1381.1万元
预计投入:
钢制连续抽油杆投入长度×单价+长柱塞防砂泵费用+其他配件费用
= 2600m/口×13口×80元/m+12000元/口×13口+1万元/井次×13口
= 270.4万元+15.6万元+13万元
= 299万元
预计单井投入23万元/口,区块13口井共计投入299万元。
钢制连续抽油杆使用寿命内共计可以节约各类成本483.08万元,增油创效1381.1万元以上,共计创效1562.18万元,投入产出比1:6.2,预计0.96年回收投入成本。
4 结论
荣72块油井正常生产过程中面临着杆管偏磨、地层能量低、水敏严重等生产问题,造成该区块各类生产成本的增加和产能的浪费。
该举升工艺的实施对于降低荣72块各类生产成本,提高油井生产效率预期效果良好。
参考文献:
[1]罗英俊,万仁溥.采油技术手册(第三版)[M].北京:石油工业出版社,2005:154-156.
[2]董旭浩.连续杆深抽配套优化设计与现场应用[J].中国高新技术企业,2011(07):35-36.。