废旧塑料的热解-新
常见废塑料回收处置方案
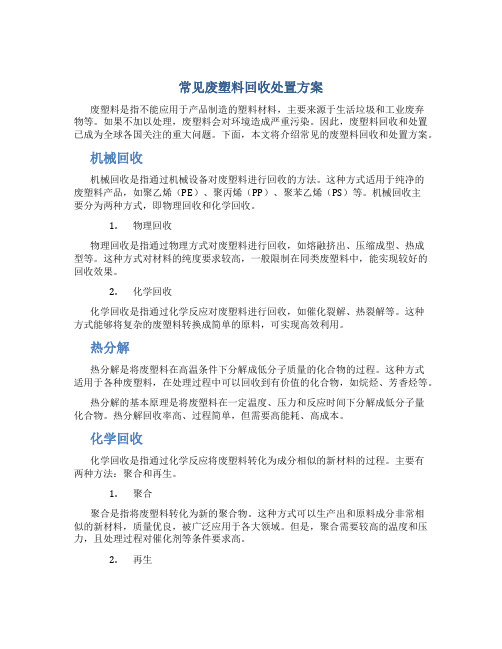
常见废塑料回收处置方案废塑料是指不能应用于产品制造的塑料材料,主要来源于生活垃圾和工业废弃物等。
如果不加以处理,废塑料会对环境造成严重污染。
因此,废塑料回收和处置已成为全球各国关注的重大问题。
下面,本文将介绍常见的废塑料回收和处置方案。
机械回收机械回收是指通过机械设备对废塑料进行回收的方法。
这种方式适用于纯净的废塑料产品,如聚乙烯(PE)、聚丙烯(PP)、聚苯乙烯(PS)等。
机械回收主要分为两种方式,即物理回收和化学回收。
1.物理回收物理回收是指通过物理方式对废塑料进行回收,如熔融挤出、压缩成型、热成型等。
这种方式对材料的纯度要求较高,一般限制在同类废塑料中,能实现较好的回收效果。
2.化学回收化学回收是指通过化学反应对废塑料进行回收,如催化裂解、热裂解等。
这种方式能够将复杂的废塑料转换成简单的原料,可实现高效利用。
热分解热分解是将废塑料在高温条件下分解成低分子质量的化合物的过程。
这种方式适用于各种废塑料,在处理过程中可以回收到有价值的化合物,如烷烃、芳香烃等。
热分解的基本原理是将废塑料在一定温度、压力和反应时间下分解成低分子量化合物。
热分解回收率高、过程简单,但需要高能耗、高成本。
化学回收化学回收是指通过化学反应将废塑料转化为成分相似的新材料的过程。
主要有两种方法:聚合和再生。
1.聚合聚合是指将废塑料转化为新的聚合物。
这种方式可以生产出和原料成分非常相似的新材料,质量优良,被广泛应用于各大领域。
但是,聚合需要较高的温度和压力,且处理过程对催化剂等条件要求高。
2.再生再生是指将废塑料进行物理或化学处理后,再制成经过特殊处理的、性能满足要求的再生塑料。
这种方式可以生产出相对低价的产品,可以用于制造地面材料、建筑材料和轻工业产品等。
生物降解生物降解是指将废塑料在特定的条件下通过微生物降解分解成二氧化碳和水的过程。
生物降解是环保和可持续的处理方式,适用于日用塑料制品和包装等。
但是,生物降解过程时间长,需要高温、高湿等条件,思考成本和效益之间的平衡。
目前废旧塑料处理的主要方法

主要方法塑料包装废弃物的处理基本上可分为填埋、焚烧和回收再生利用。
1.填埋法填埋方法是我国处理固体废弃物最传统的方法,是将固体废弃物放置在空旷的场地上,通过采取防水等措叶甘进行处理。
固体废弃物的填埋不能随便进行,必须合理选择填埋的场地。
目前我国填埋的技术有待发展,很多固体废弃物还是处于堆放的状态4。
填埋的方法具有经济实惠、处理效率高等特点,而且固体废弃物的运输比较方便。
填埋的方法能够及时处理多种废弃物,而且有利于促进我国进行环境保护,实现资源的循环利用。
填埋过程中会产生大量的沼气,可以利用到居民的日常生活中,实现资源的循环利用。
但是,固体废弃物填埋时要注意对渗滤液的控制。
鉴于渗滤液具有高度动态变化特性,因此在对固体废弃物进行填埋时,要对渗滤液进行分解,把硫酸根等硫化物分解掉再进行填埋。
填埋危险的固体,如果事先不进行有效的处理,会对我国的土地资源造成严重危害,因此在填埋时要对固体废弃物进行固化分析,进行稳定化处理,而且对填埋的场地要采取防渗措施。
废弃塑料具有大分子结构,废弃后长期不易分解腐烂。
填埋方法在短期内有一定的效果,但是填埋法简单消极,被填埋的塑料废弃物不见阳光,不经风雨,隔绝空气,难以风化;滞留土壤中会破坏土壤的透气性,降低土壤的蓄水能力,影响农作物生长;而且积累多了会阻碍地下水的疏通与渗透。
塑料密度小,体积大,不易分解,很快占满场地,降低填埋场处理垃圾的能力。
垃圾填埋对资源利用率低,不符合国家可持续发展战略,并不是理想方法。
2.焚烧法焚烧也是处理固体废弃物的有效方法之一,是指让固体废弃物在空气中产生化学反应,其原理为:固体废弃物+氧气=二氧化碳+灰烬+能量。
固体废弃物用焚烧的办法处理后,只剩下原体积的5%左右,可以减少占地面积。
在固体废弃物焚烧的过程中,可以将其中的有毒物质转化成无毒物质,其原理为:酸+碳酸钙=硫酸钙+水。
焚烧的方法可以有效处理那些没有回收价值的固体废弃物。
在固体废弃物焚烧的过程中,产生大量的电力,可以利用到居民的生活和生产中,实现资源的循环利用。
废旧塑料回收再生循环利用的实现途径
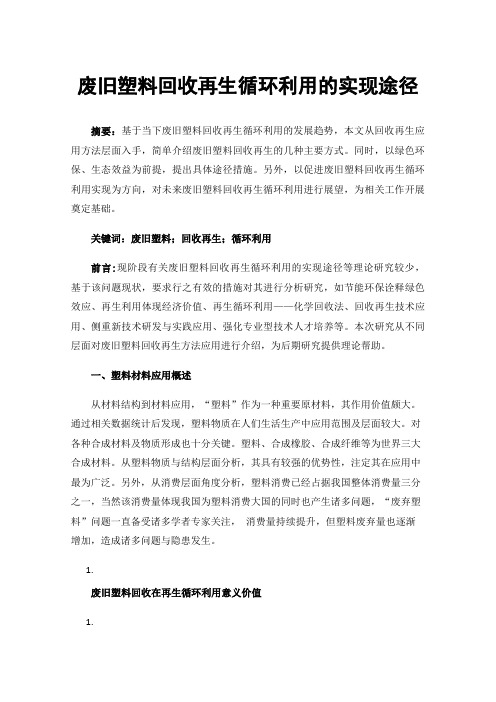
废旧塑料回收再生循环利用的实现途径摘要:基于当下废旧塑料回收再生循环利用的发展趋势,本文从回收再生应用方法层面入手,简单介绍废旧塑料回收再生的几种主要方式。
同时,以绿色环保、生态效益为前提,提出具体途径措施。
另外,以促进废旧塑料回收再生循环利用实现为方向,对未来废旧塑料回收再生循环利用进行展望,为相关工作开展奠定基础。
关键词:废旧塑料;回收再生;循环利用前言:现阶段有关废旧塑料回收再生循环利用的实现途径等理论研究较少,基于该问题现状,要求行之有效的措施对其进行分析研究,如节能环保诠释绿色效应、再生利用体现经济价值、再生循环利用——化学回收法、回收再生技术应用、侧重新技术研发与实践应用、强化专业型技术人才培养等。
本次研究从不同层面对废旧塑料回收再生方法应用进行介绍,为后期研究提供理论帮助。
一、塑料材料应用概述从材料结构到材料应用,“塑料”作为一种重要原材料,其作用价值颇大。
通过相关数据统计后发现,塑料物质在人们生活生产中应用范围及层面较大。
对各种合成材料及物质形成也十分关键。
塑料、合成橡胶、合成纤维等为世界三大合成材料。
从塑料物质与结构层面分析,其具有较强的优势性,注定其在应用中最为广泛。
另外,从消费层面角度分析,塑料消费已经占据我国整体消费量三分之一,当然该消费量体现我国为塑料消费大国的同时也产生诸多问题,“废弃塑料”问题一直备受诸多学者专家关注,消费量持续提升,但塑料废弃量也逐渐增加,造成诸多问题与隐患发生。
1.废旧塑料回收在再生循环利用意义价值1.节能环保诠释绿色效应当下绿色发展已经成为时代主题,如何开展绿色发展与环境保护是当下首要考虑问题,废旧塑料回收的本质在于将塑料污染程度进行最大化降低,经过试验测试后发现,塑料中存在一定污染元素与有害物质,长期废弃会释放出诸多对人类身体有害气体。
同时从生态环境保护层面分析,如废旧塑料出现燃烧会对周边自然环境造成波及,形成土壤或水质污染等。
因此,从多方层面分析考虑,需采用节能环保方式,对废旧塑料进行回收在循环利用,将塑料可能造成的污染进行最大程度降低,避免消费量提升造成大量塑料丢弃与环境污染。
废塑料的回收利用和处理

废塑料的回收利用和处理1 概述塑料具有质量轻、强度高、耐磨性好、化学稳定性好、抗化学药剂能力强、绝缘性能好、经济实惠等优点,因而在生产、生活中得到广泛利用。
废塑料则是在民用、工业等用途中使用过且最终淘汰或替换下来的塑料的统称。
目前,我国废弃塑料主要来源于使用过的农用塑料薄膜、各种塑料包装材料(薄膜、塑料丝及编织品、泡沫塑料、包装箱及容器、各种日用塑料制品、各种各样的塑料袋)、废弃的家用电器、汽车等。
农用薄膜是我国塑料工业中最重要的组成部分,是现代化农业发展中重要的生产资料。
我国的农膜20世纪60年代初期开始自行研制生产,1978年开始从日本引进技术,农膜的生产技术经历了一个从无到有,从普通白膜到功能性农膜的发展过程。
随着科技兴农战略的实施,农用塑料应用技术的推广步伐明显加快,近几十年来我国农膜生产形势发生了举世瞩目的变化。
正是由于农膜的大规模使用,从而也导致了大量的废弃农用塑料薄膜。
据统计,2005年HDPE、PP、PET瓶产量已达120万t,饮料热灌装PET已超过130亿个,塑料包装容器应用市场广阔,碳酸饮料包装中PET瓶占57.4%,大型化工液体包装容器双L环桶和IBC桶、药品和输液塑料包装容器、塑料汽油箱的普及,塑料托盘在仓储、运输中的大量使用都是造成废弃塑料产生的重要来源。
废弃塑料主要以有机固体废物出现,其特点是量大、品种杂,抗腐蚀能力强,不与酸、碱反应,回收、分离、处理、利用难度大,主要分布在农业、商业、工业及日用品领域。
废弃塑料在环境中长期不被降解,造成严重的“白色污染”。
从改善环境、充分利用资源、有利于社会发展的角度考虑,应对废塑料进行回收再利用。
废塑料的回收利用是一个完整的工程,包括收集、分选、加工和再生利用。
2 废塑料管理2.1 源头分类管理从家庭开始分类,居民住宅、社区、公共场所都有分类垃圾箱。
密闭的垃圾分类专用车上门收集垃圾,废纸、废塑料等包装废物送往工厂再生利用,厨房、庭院垃圾用于堆肥。
废塑料热解过程气相成分分析及造粒方法的选择

聚苯乙烯 () 随温度变化情况 2
现象 备注 因空气膨胀和水分蒸发引起, 塑 料未分解。 塑料开始分解并趋于剧烈。 塑料急速分解。 试验残余物* 。 0 % & 1
有少量气泡产生; 酒精灯火焰无变化。 温度开始降至! ) * /, " * & /开始出现少量淡黄色液体, " # * /后气泡 " * * /气泡增加, 逸出较剧烈; 酒精灯火焰逐渐变大。 并且温度降至 % 酒精灯火焰急 % $ * /气泡再次逸出剧烈, ( * /, % " * /气泡逸出剧烈, 剧变大; & ’ * /淡黄色液体增多, & $ * /淡黄色液体变为橙色。
图) ) ( ’ %时 " # 裂解气相分析
* ( *
由此可知, 聚乙烯在! " # $和% " # $热解时放出烷烃和烯烃以及苯等产物。 (’ ) 的热解气相成分分析 % & ! & ! 聚丙烯 ’ 在温度分别为! 聚丙烯的热解气相分析结果如如图( 、 图"所示。 ! # $和% % # $时,
废塑料热解过程气相成分分析及造粒方法的选择
龙世刚 孟庆民 汪志全 冯新华 毛鸣
马鞍山 ! ) " # $ $ ! (安徽工业大学 ・ 安徽省冶金工程与资源综合利用重点实验室
摘 要
本文研究了不同废塑料热解开始温度及其热解过程中气相成分的变化, 并以此为依据分析了热熔水淬造
粒法和微热塑化造粒法对环境和资源回收的影响。结果表明, 微热塑化造粒法是一种既能充分利用资源又无二次 污染的适合高炉喷吹用废塑料造粒方法。
图( ! ! # $时 ’ ’裂解气相分析
! 1 ! % ( " 7 5
废塑料热解的工艺流程

废塑料热解的工艺流程
废塑料热解是一种将废塑料转化为燃料或化工产品的技术过程。
其工艺流程通常包括以下几个步骤:
1. 原料准备,首先需要对废塑料进行分类和处理,去除其中的
杂质和污染物,以确保后续处理过程的顺利进行。
这可能涉及到废
塑料的清洗、破碎和分类等工序。
2. 热解反应,经过原料准备后,废塑料通常被送入热解反应装
置中。
在高温和缺氧的环境下,废塑料会发生热解反应,分解成气体、液体和固体产物。
这一步通常需要在特定的反应器中进行,以
确保反应的高效进行。
3. 气体处理,热解反应产生的气体通常包括烃类气体和其他有
机气体。
这些气体需要进行处理,以去除其中的有害物质和杂质,
同时可以通过冷凝和分离等方法将其中的液体烃类产品分离出来。
4. 液体处理,热解反应还会产生液体产物,通常是液体烃类产
品和其他化工产品。
这些液体产物需要经过进一步的处理和精炼,
以得到符合要求的产品。
5. 固体处理,热解反应产生的固体残渣通常包括焦炭和其他固
体产物。
这些固体残渣可以经过处理,例如焦化和气化等方法,以
得到再生资源或者能源产品。
总的来说,废塑料热解的工艺流程涉及到原料准备、热解反应、气体处理、液体处理和固体处理等多个环节,需要综合考虑原料的
性质、反应条件、产物的处理和利用等多个方面的因素,以实现废
塑料资源化利用的目标。
废旧塑料的回收与利用
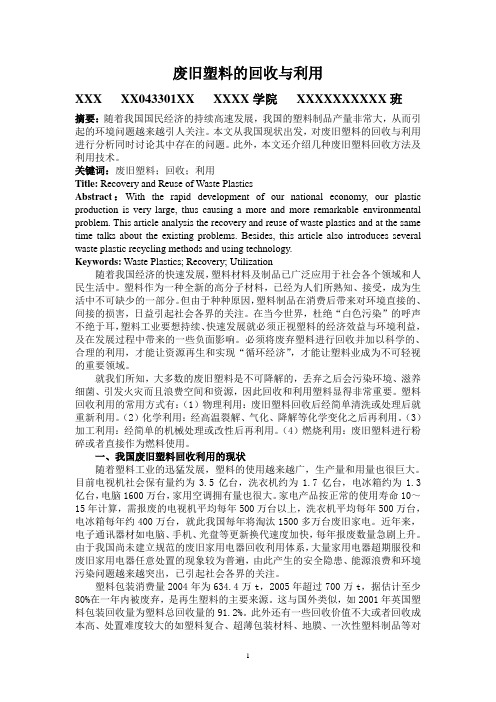
废旧塑料的回收与利用XXX XX043301XX XXXX学院XXXXXXXXXX班摘要:随着我国国民经济的持续高速发展,我国的塑料制品产量非常大,从而引起的环境问题越来越引人关注。
本文从我国现状出发,对废旧塑料的回收与利用进行分析同时讨论其中存在的问题。
此外,本文还介绍几种废旧塑料回收方法及利用技术。
关键词:废旧塑料;回收;利用Title: Recovery and Reuse of Waste PlasticsAbstract:With the rapid development of our national economy, our plastic production is very large, thus causing a more and more remarkable environmental problem. This article analysis the recovery and reuse of waste plastics and at the same time talks about the existing problems. Besides, this article also introduces several waste plastic recycling methods and using technology.Keywords: Waste Plastics; Recovery; Utilization随着我国经济的快速发展,塑料材料及制品已广泛应用于社会各个领域和人民生活中。
塑料作为一种全新的高分子材料,已经为人们所熟知、接受,成为生活中不可缺少的一部分。
但由于种种原因,塑料制品在消费后带来对环境直接的、间接的损害,日益引起社会各界的关注。
在当今世界,杜绝“白色污染”的呼声不绝于耳,塑料工业要想持续、快速发展就必须正视塑料的经济效益与环境利益,及在发展过程中带来的一些负面影响。
废旧塑料的热裂解回收
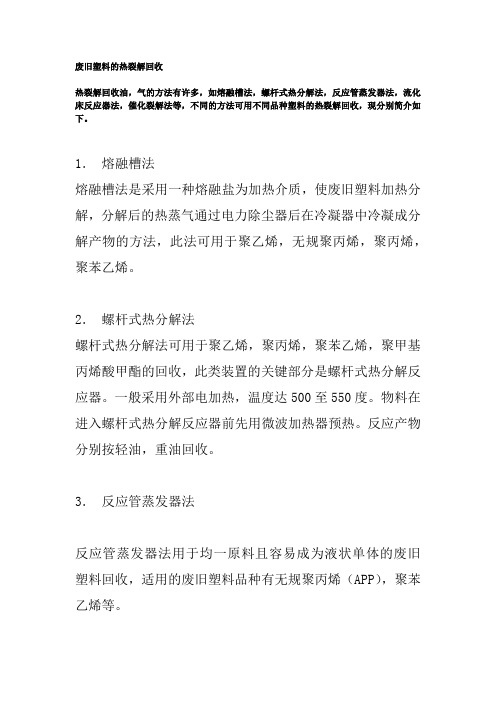
废旧塑料的热裂解回收
热裂解回收油,气的方法有许多,如熔融槽法,螺杆式热分解法,反应管蒸发器法,流化床反应器法,催化裂解法等,不同的方法可用不同品种塑料的热裂解回收,现分别简介如下。
1.熔融槽法
熔融槽法是采用一种熔融盐为加热介质,使废旧塑料加热分解,分解后的热蒸气通过电力除尘器后在冷凝器中冷凝成分解产物的方法,此法可用于聚乙烯,无规聚丙烯,聚丙烯,聚苯乙烯。
2.螺杆式热分解法
螺杆式热分解法可用于聚乙烯,聚丙烯,聚苯乙烯,聚甲基丙烯酸甲酯的回收,此类装置的关键部分是螺杆式热分解反应器。
一般采用外部电加热,温度达500至550度。
物料在进入螺杆式热分解反应器前先用微波加热器预热。
反应产物分别按轻油,重油回收。
3.反应管蒸发器法
反应管蒸发器法用于均一原料且容易成为液状单体的废旧塑料回收,适用的废旧塑料品种有无规聚丙烯(APP),聚苯乙烯等。
4.流化床反应器法
流化床反应器法已有多种装置用于废塑料的油化回收,此法可应用于:聚丙烯,交联聚乙烯,聚丙烯,聚氯乙烯等多种塑料。
5.催化裂解法
催化裂解法是利用合适的催化剂进行低温油化废塑料的方法,一般用于单一品种塑料的油化,适用的塑料有聚乙烯,聚丙烯,聚氯乙烯等。
由于采用低温油化,所以,此法的油分收率较高,另外,催化剂的使用使所得油分较均一,产物的附加价格较高。
塑料废物焚烧能源回收方法

塑料废物焚烧能源回收方法塑料废物焚烧是一种将废弃的塑料物质燃烧为能源的方法。
塑料废物是社会生活中产生量较大的垃圾之一,处理塑料废物成为一项迫切需要解决的问题。
通过焚烧处理废弃塑料,不仅能有效解决废弃物的处理问题,还可以获得一定的能源回收效益。
首先,塑料废物焚烧能够减少废物占地面积。
废弃塑料经过压缩处理后可以通过焚烧方法进行处置。
相对于传统的填埋处理方法而言,塑料废物焚烧不需要大量的占地面积,可以减少对环境的破坏,并且不会造成地下水污染等问题。
其次,塑料废物焚烧还可以转化为电能。
塑料作为一种聚合物材料,具有高热值的特点。
燃烧塑料废物可以产生大量的热能,这些热能可以用于发电。
通过高温燃烧塑料废物产生的热能可以驱动蒸汽轮机,进而产生电能。
再次,塑料废物焚烧还可以进行热能回收。
燃烧废弃塑料产生的烟气中含有大量的热能,通过烟气余热回收技术将烟气中的热能转化为热水或蒸汽,进行加热、供暖等用途。
然而,塑料废物焚烧也存在一定的问题与挑战。
首先,焚烧塑料会产生有害气体和废渣。
塑料中的一些添加剂和化学物质在焚烧过程中会释放出有毒气体,如二恶英等,这对环境和健康造成潜在的风险。
同时,焚烧产生的废渣也需要进行妥善处理,以免对土壤和水源造成污染。
其次,焚烧塑料消耗大量的能源。
虽然焚烧塑料可以获得一定的能源回收效益,但是燃烧过程本身也需要大量的燃料和能源供给。
如果不能有效地控制和利用燃烧过程中的能源,将会导致能源浪费。
对于这些问题和挑战,可以采取一系列的措施进行解决。
首先,可以通过改进焚烧设备和工艺,减少有害气体的排放。
例如,在燃烧过程中加入除尘装置和脱硫装置,有效减少有害物质的排放。
其次,可以加强对废弃塑料的分类和回收。
通过对塑料废物进行分类,可以将可回收的塑料再利用,减少焚烧的数量和能源的消耗。
并且可以对不同种类的塑料废物采取不同的处理方法,以最大程度地减少对环境的影响。
此外,应加大对塑料废物焚烧技术的研发力度,提高能源转化效率。
在流化床中热解废旧塑料的实验研究

第38卷 第10期2006年10月哈 尔 滨 工 业 大 学 学 报JOURNAL OF HARB I N I N STI T UTE OF TECHNOLOGYVol 138No 110Oct .2006在流化床中热解废旧塑料的实验研究董芃,尹水娥,楼黎虹,别如山(哈尔滨工业大学能源科学与工程学院,哈尔滨150001,E 2mail:DongP@hit .edu .cn )摘 要:对高密度聚乙烯(HDPE )、低密度聚乙烯(LDPE )、聚丙烯(PP )、聚苯乙烯(PS )和聚氯乙稀(P VC )等5种单组分废旧塑料在流化床中进行了热解实验,得到了在实验条件下,热解温度对各种单组分废旧塑料热解产物成分和产率的影响规律,为开发废旧塑料热解制油、制气工业装置提供了基本的工艺参数.关键词:废旧塑料;热解;流化床中图分类号:TK224文献标识码:A文章编号:0367-6234(2006)10-1728-04Exper i m en t a l study on the pyrolysis of wa ste pl a sti cs i n flu i d i zed bedDONG Peng,YI N Shui 2e,LOU L i 2hong,B I E Ru 2shan(College of Energy Science and Engineering,Harbin I nstitute of Technol ogy,Harbin 150001,China,E 2mail:DongP@hit .edu .cn )Abstract:The pyr olysis characteristics of five several s orts of the waste p lastics na mely H igh density polyethy 2lene (HDPE ),Low density polyethylene (LDPE ),Polystyrene (PS ),Polyp r opylene (PP ),and Polyvinyl chl oride (P VC )were investigated in fluidized bed .The effect of te mperature on the yield of liquid and gase 2ous fuel p r oducti on and the gas compositi on are analyzed .The essential para meters have been p r ovided f or de 2vel op ing industrial equi pment of p r oducing liquid and gaseous fuel by pyr olysis of waste p lastics .Key words:waste p lastic;pyr olisis;fluidized bed收稿日期:2005-01-06.基金项目:哈尔滨工业大学跨学科交叉性研究基金资助项目.作者简介:董芃(1957—),男,博士,教授. 塑料是以石油、天然气、煤等自然资源为原料合成的,大量塑料废弃物不仅造成了严重的环境污染,而且在自然资源日益匮乏的情况下,导致了社会财富的极大浪费.为了保护环境,实现资源的再利用,把废旧塑料热解制成发热值较高的燃气和液体燃料是很有前途的废旧塑料再利用的处理方法[1-5].在各种热解反应器中,媒体流化床反应器具有热容量大、温度均匀、物料升温速率快、易于实现稳定连续运行等优点[6],非常适用于废旧塑料的热解工艺.因此,研究废旧塑料在媒体流化床热解反应器中的热解规律,对进一步开发废旧塑料热解制油、制气工业装置以及实现废旧塑料的资源化具有重要的意义[7-9].1 实验设备及实验方法111 实验装置与系统实验装置由媒体流化床热解反应器、测量控制系统、进料系统、热解油蒸汽冷却系统、热解气过滤系统、气体测量和取样系统、尾气处理系统、气体分析系统组成,如图1所示.热解反应器用耐高温的碳化硅管制成.在碳化硅管的外表面由上及下缠绕3段电阻丝作为热源,分别采用比例-积分-微分(P I D )调节器来实现对温度的控制,可调范围为0~1600℃,并且通过数字化仪表易于实现P I D 调节参数的设定.热解流化床反应器的内径为Φ89mm ,高度为1450mm ,反应器下部铺设粒径为2~3mm 、高度为600mm 的粗石英砂层,在实际运行中为加热流化的固定床.在粗石英砂层上面有粒径为200~300μm 、高度为500mm 细石英砂作为流化床料,实验时的实际流化风速为0115m /s . 为了准确测定流化床内部的温度,实验装置采用长度为1m 的热电偶从上部插入流化床内的石英砂中,再用一个热电偶测量采样点气流的温度.为了准确计算控制实验原料的给料量,实验装置采用螺旋给料机,给料速度由直流电机调速器控制.针对塑料热稳定性差,遇热容易成粘稠状的特点,在落料管外侧设计有水冷却套管,以保证给料系统的连续稳定运行.实验时的实验原料的给料量为013g/s.1—控制柜;2—空气转子流量计;3—氮气转子流量计;4—直流电机调速器;5—智能温控表;6—压差计;7—气路管道;8—电线;9—热电偶;10—直流电机;11—给料斗;12—螺旋给料装置;13—落料管;14—媒体流化床热解反应器;15—布风系统与残留物排放系统;16—排烟道;17—冷凝管;18—真空弯管;19—锥形接受瓶;20—第一过滤瓶;21—第二过滤瓶;22—烟气分析仪图1 热解装置流程图 实验的热解产物经过热解油蒸汽冷却系统、热解气过滤干燥系统后,用3012H 型自动烟尘气测试仪进行抽取.从测试仪的仪表上可以读取抽气时间、体积、流速和压力等参数.112 实验方法将实验用媒体石英砂床料放入流化床反应器中,将反应器升温到所设定的热解温度,通入作为流化气体的氮气,测量并控制其流量,观察压差计,待流化床反应器内流化稳定后,启动螺旋给料机按照实验方案确定的给料量送入实验原料.通过在线测量,观察到热解产物稳定产出后,打开烟气分析仪,连续抽取热解产物30m in .在抽取热解产物期间的不同的时段进行气体采样,然后将气样用气相色谱仪分析.热解气成分分析采用SP -2000型气相色谱仪.色谱检测器为火焰电离检测器(F I D ).色谱柱是Porapak Q 色谱柱,柱长Φ3mm ×015mm ×2000mm ,最高使用温度250℃,用H 2作载气.进样量为1m l .热解产物中HCl 成分检测分析采用M I A -3型微机化多功能离子分析器,使用微机控制电位,自动滴定测量.2 实验结果与分析211 高密度聚乙烯(HD PE)由图2可以看出,随着热解温度的升高,热解气体的产率增加,冷凝液体产物的产率下降.在540℃时,HDPE 的热解气体产率为6%,冷凝液体产率为94%;在737℃时,HDPE 的热解气体产率为43175%,冷凝液体产物的产率为56125%.图2 热解温度对HDPE 热解产物的影响 由图3可以看出,在热解气体的组成成分中,乙烯的含量要高于甲烷和乙烷.图3 热解温度对HDPE 热解气成分的影响212 低密度聚乙烯(LD PE)由图4可以看出,与HDPE 相似,随着热解温度的升高,LDPE 热解气体的产率增加,冷凝液体・9271・第10期董芃,等:在流化床中热解废旧塑料的实验研究产物的产率下降.在535℃时,LDPE的热解气体产率为817%,冷凝液体产率为9113%;在735℃时,LDPE的热解气体产率为4017%,冷凝液体产物的产率为5913%.图4 热解温度对LDPE热解产物的影响 由图5可以看出,LDPE热解气中也是乙烯的含量高于甲烷和乙烷.图5 热解温度对LDPE热解气成分的影响213 聚苯乙烯(PS)由图6可以看出,随着热解温度的升高,热解气体的产率增加,冷凝液体产物的产率下降.在488℃时,PS的热解气体产率为418%,冷凝液体产率高达9512%;在745℃时,PS的热解气体产率为53148%,冷凝液体产物的产率为46152%.图6 热解温度对PS热解产物的影响 图7描述了热解温度对PS热解气中甲烷和乙烯产率的影响规律.与HDPE和LDPE相比,PS 热解气中乙烷的含量很少,气相色谱图显示PS在热解温度高于650℃时出现乙烷,但含量份额很少,估计是高分子再次裂解的产物.图7 热解温度对PS热解气成分的影响214 聚丙烯(PP)由图8可以看出,PP随着热解温度的升高,热解气体的产率增加,冷凝液体产物的产率下降.在524℃时,PP的热解气体产率为619%,冷凝液体产率为9311%;在738℃时,PP的热解气体产率为8414%,冷凝液体产物的产率为1516%.由图9可以看出,在PP的热解气体中甲烷、乙烯的含量随着温度的升高呈上升趋势,但乙烷却趋于平缓.与HDPE、LDPE、PS不同的是,在PP 的热解气体中甲烷的含量高于乙烯、乙烷.图8 热解温度对PP 热解产物的影响图9 热解温度对PP热解气成分的影响215 聚氯乙稀(PVC)P VC热解产生大量的黑色烟雾,伴随浓烈的刺激性气味,冷凝为黑色的液体.由于冷凝液体里含有碳黑,不容易被回收.并且,采用流化床反应器热解P VC时,热解过程所产生的残渣容易使作为流化媒体的石英砂结块,严重时会导致设备无法正常运行.又由于P VC分解时产生的HCl对设・371・哈 尔 滨 工 业 大 学 学 报 第38卷 备有腐蚀性,因此,工业上通常不会单独裂解废旧P VC 制品,而是将其与PE 、PP 、PS 、PET 等以一定的比例混合,先脱除HCl,再进行裂解.由图10看出,由于P VC 热解会产生固体残渣,因此在同样的热解温度下,P VC 的气体和液体产率比HDPE 、LDPE 、PS PP 都低.由图11可以看出P VC 热解气的甲烷的含量高于乙烯,乙烷.由图12可以看出,随温度上升,P VC 的热解气体中HCl 的含量呈缓慢上升的状态.图10 热解温度对P VC热解产物的影响图11 热解温度对P VC热解气成分的影响图12 P VC 热解气中HCl U 产率与温度的关系曲线3 结 论1)在流化床热解条件下,热解气体产率随着热解温度的升高而增加,冷凝液体产率随着温度的升高而降低.2)热解温度对热解气的产率和组分有着明显的影响.随着温度的升高,热解气产率上升,析出速度快.因此,提高热解温度对提高热解气的产量非常有利.在实验条件下,HDPE 、LDPE 、PS 、PP 、P VC 塑料的热解气成分以甲烷、乙烷、乙烯为主,还有少量的丙烷、丙稀、氢气等.在HDPE 、LDPE 、PS 热解气中,乙烯的产量多于甲烷.在PP 、P VC 热解气中则是甲烷含量高于乙烯.随着热解温度的增加,在实验用所有种类塑料的热解气中,甲烷和乙烯的产量明显增加,但乙烷的增长比较平缓;3)随温度上升,P VC 热解气中HCl 的含量基本保持不变.参考文献:[1]ROS A M ,HOOSHANG P,CHR I STI A N R,et a l .Vacu 2u m pyr olysis of P VC II :Pr oduct analysis [J ].Poly mer Degradati on and Stability,1999,66(1):107-125.[2]KI M S .Pyr olysis kinetics of waste P VC p i pe[J ].W astemanage ment,2001,21(7):609-616.[3]K AM I N SKYW ,SCHLESSE LMANN B.Ther mal degra 2dati on of m ixed p lastic waste t o ar omatics and gas[J ].Poly mer Degradati on and Stability,1996,53(2):189-197.[4]VABA P G .Apparatus for recovery of furl oils fr omwaste foa m p lastics treat m ent [J ].Umwelt,1993,23(5):301-302.[5]罗宁,刘治中,母昭德.废弃塑料裂解油化技术[J ].重庆环境科学,1996,18(3):42-43.[6]黄发容,陈涛,沈学宁.高分子材料的循环利用[M ].北京:化学工业出版社,2000.[7]M I RANDA R,Y ANG J,ROY C,et a l .Vacuu m pyr oly 2sis of comm ingled p lastics containing P VC I .Kinetic study[J ].Poly mer Degradati on and Stability,2001,72(3):469-491.[8]MASTE LLONE M L,PERUGI N I F,et a l .Fluidized bedpyr olysis of a recycled polyethylene[J ].Poly mer Degra 2dati on and Stability,2002,76(3):479-487.[9]CONES A J A,F ONT R F,MARC I L LA A,et a l .Pyrily 2sis of polyethylene in fluidized bed react or[J ].Energy Fuels,1994,8(6):1238-1246.(编辑 杨波)・1371・第10期董芃,等:在流化床中热解废旧塑料的实验研究。
废塑料热裂解技术

第49卷第12期 当 代 化 工 Vol.49,No.122020年12月 Contemporary Chemical Industry December,2020 收稿日期: 2020-04-15 作者简介:时宇(1991-),女,河南省周口市人,助理研究员(博士后),博士,2018年毕业于中国科学院大连化学物理研究所化学工程专业,研究方向:废塑料的资源化转化研究。
E -mail:*********************。
废塑料热裂解技术时 宇1,2(1.清华大学 能源与动力工程系,北京100084; 2.清华大学热科学与动力工程教育部重点实验室,北京100084)摘 要:相比于填埋、焚烧等传统的处理技术,废塑料热裂解技术不仅能降低处理过程中对环境的污染,还能转化成二次燃料和化学品,达到其循环利用的效果。
综述了国内外废塑料热解方法的研究进展,分析了直接热裂解法、催化热解法和共热解法的优缺点,指明了研究开发能适应不同种类原料、活性高、选择性好的催化剂仍是未来废塑料热解技术的重要研究方向。
关 键 词:废塑料;热裂解;催化热解;共热解;分子筛中图分类号:TQ322.2 文献标识码: A 文章编号: 1671-0460(2020)12-2840-04Research Progress of Pyrolysis Technologies of Waste PlasticsSHI Yu 1,2(1. Department of Energy and Power Engineering, Tsinghua University ,Beijing 100084, China; 2. Key Laboratory for Thermal Science and Power Engineering of Ministry of Education, Tsinghua University,Beijing 100084, China )Abstract : Compared with the traditional treatment technologies such as landfill and incineration, the pyrolysis technology of waste plastics can not only reduce the environmental pollution during the treatment process, but also convert waste plastics into secondary fuel and chemicals to achieve its recycling use. In this paper, the research progress of the pyrolysis treatment for waste plastics at home and abroad was reviewed. The advantages and disadvantages of direct pyrolysis, catalytic pyrolysis and co-pyrolysis were analyzed. It was pointed out that the research and development of catalysts suitable for different kinds of raw materials, with high activity and good selectivity are still an important research direction of the pyrolysis technology of waste plastics in the future. Key words : Waste plastics; Thermal cracking; Catalytic pyrolysis; Co-pyrolysis; Molecular sieve石油经过催化裂解能产生乙烯、丙烯、苯乙烯和氯乙烯等单体,同种或异种单体之间通过聚合制备的高分子类材料,统称为塑料。
废塑料资源化利用
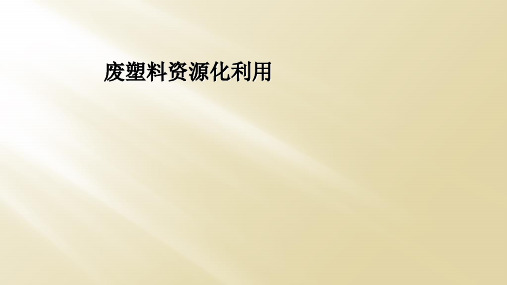
植物纤维织物,含有丰富的纤维素,通过化学加工可以获得许多纤维素衍生产品,如纤维素酯、 纤维素醚等。 ▪ 3.废蛋白质纤维再生毛毡(毯)
废毛织物、丝织物,在没有严重虫蛀的情况下,纤维原本的性质基本上没有发生很大变化。经 过剪断、疏解、脱色、洗涤、干燥等处理,可以重新制成毛绒或丝棉。 ▪ 4.废蛋白质纤维制泡沫剂 ▪ 5.废化学纤维解聚回收化工原料
废塑料资源化利用
固体废物的资源化利用
01 废塑料的综合利用
02 废纸再生及利用
03 废橡胶的再生利用
04 年 才能腐烂的塑料,常常 造成大面积污染。
废塑料的综合利用
1、对生物体的毒害性 在聚氯乙烯(Polyvinyl Chloride, pvc)中,添加剂邻苯二甲酸醋其使用量达到了35%——50% ,随着时
间的推移,PAEs可由塑料中迁移到环境中。研究表明,PAEs具有一般毒性和特殊毒性(如致畸、致突变性 或具有致癌活性),在人体和动物体内发挥着类雌性激素的作用,干扰内分泌,可以造成人体生殖功能异 常、男性精子数量减少。而且其水解和光解速率都非常缓慢,属于难降解有机污染物,在大气、土壤、和 水体中均有残留。全世界每年向海洋和江河中倾倒的塑料垃圾已造成海洋生物的大量死亡。 2、对土壤和大气环境的危害
用 程度分三类。
改性剂
废纸再生及利用
纸张消费
目前我国纸张消费量每年约 3500wt,每年可回收利用的 废纸达1000wt以上,但实际 回收利用率还不到40%,可见 国内废纸回收利用的潜力还 很大。
废纸再生及利用
广泛的再生用途 纸张的原料主要为木材、草、芦苇、竹等植物纤维,废纸又被称为
塑料的热解演讲

一、塑料以及背景介绍
随着石油化工的迅速发展及塑料制品的 大量使用,废旧塑料的废弃量也越来越大。 就我国的塑料而言,总产量从1975年1.4万t增 至1988年的360万t,增加了257倍,预计今后 每年还将以8~ 10%的速度增长。1990年,我 国的废塑料就达到了90万t。一座中等城市年 平均废塑料量就在2000t以上,有的已造成严 重的“白色污染”。
燃性气体; (2) 在常温下为液态的包括乙酸、丙酮、甲醇等化合物在内
的可燃油; (3) 纯碳与玻璃、金属、土砂等混合形成的炭黑的化学分解
过程。
2、热解原理 热解为在一次燃烧室供给不足量之助燃空气,使在
一定温度(650 ℃~850 ℃) 内进行裂解。其中可燃物质于 高温缺氧下分解为短链有机气体及微量氢气,但由于缺 氧,这些有机气体将流入二次燃烧室焚化,而留在一次 炉则为固定碳及灰份。固定碳的氧化速率较慢,故需提 供较长的时间供氧,使之反应成CO 或CO2 ,以达完全 燃烧。一般而言,热解式焚化炉设计的单位炉床负荷较 小,且以底部供气,使固定碳有良好的燃烧反应环境, 故具极佳之灰份品质及减量效果。
作为废旧塑 料的传统处理方 法,大致有掩埋、 再生和焚烧三种 途径。
把废弃塑料再生造粒,作为原材料再利用,虽然有很 高的环境和资源价值,但由于回收过程中分离、清洗成本 太高,经济效益低下,发展受到限制。掩埋法则由于占用 土地量大,而且由于塑料降解能力差,易造成土壤板结焚 烧法则由于焚烧过程中产生二噁英等有害气体,造成二次 污染。废塑料和废轮胎的处理方法大致有掩埋、焚烧、再 生、改性利用及热分解几种,其利弊汇总于表1
表2 热分解产物的组成及其含量
废塑料热解装置[实用新型专利]
![废塑料热解装置[实用新型专利]](https://img.taocdn.com/s3/m/9bf37dc57d1cfad6195f312b3169a4517723e51e.png)
[19]中华人民共和国国家知识产权局[12]实用新型专利说明书[11]授权公告号CN 2876094Y [45]授权公告日2007年3月7日专利号 ZL 200620078207.1[22]申请日2006.01.05[21]申请号200620078207.1[73]专利权人杨克俭地址710086陕西省西安市未央区三桥镇巨家庄红光路西段66号[72]设计人杨克俭 [74]专利代理机构西安永生专利代理有限责任公司代理人申忠才 钟淑云[51]Int.CI.C10G 1/00 (2006.01)C08J 11/10 (2006.01)权利要求书 1 页 说明书 4 页 附图 1 页[54]实用新型名称废塑料热解装置[57]摘要一种废塑料热解装置,包括:炉体,在炉体的顶部设与排烟阀门相联通的排烟管,在炉体的夹层中设保温层,在炉体内设安装有转炉清渣盖的卧式旋转炉,在炉体内卧式旋转炉下设安装有炉排的炉膛,在炉体的侧壁设炉体清渣盖;通过螺旋输送减速器与螺旋输送器电动机联接的螺旋输送器,螺旋输送器与卧式旋转炉之间设密封盖;与转炉电动机相联接的转炉减速器,转炉减速器通过传动机构与卧式旋转炉相联;一端外装有密封套与卧式旋转炉相联通、另一端设置在油水分离器内且设有温度指示器以及压力指示器的冷凝器;它还包括通过导管与油水分离器相联通的盛油桶。
它具有自动化程度高、处理量大、使用寿命长、无环境污染等优点,可用于废旧塑料制备原油。
200620078207.1权 利 要 求 书第1/1页 1、一种废塑料热解装置,其特征在于它包括:炉体[6],在炉体[6]的顶部设置有与排烟阀门[10]相联通的排烟管[9],在炉体[6]的夹层中设置有保温层[7],在炉体[6]内设置安装有转炉清渣盖[24]的卧式旋转炉[8],在炉体[6]内卧式旋转炉[8]下设置安装有炉排[26]的炉膛[25],在炉体[6]的侧壁设置有炉体清渣盖[23];通过螺旋输送减速器[2]与螺旋输送器电动机[1]联接的螺旋输送器[3],螺旋输送器[3]与卧式旋转炉[8]之间设置有密封盖[5];与转炉电动机[19]相联接的转炉减速器[20],转炉减速器[20]通过传动机构与卧式旋转炉[8]相联;一端外装有蜜封套[11]与卧式旋转炉[8]相联通、另一端设置在油水分离器[17]内且设置有温度指示器以及压力指示器的冷凝器[13];它还包括通过导管与油水分离器[17]相联通的盛油桶[18]。
废旧塑料的熔融再生法

废旧塑料的熔融再生法塑料的熔融再生方法包括下述过程:废旧塑料的收集、分拣、清洗、干燥、再生造粒、成型一.废旧塑料的分拣废旧塑料来源复杂,常混入有金属,橡胶,织物,泥纱及其他各种杂质,且不同品种的塑料往往混在一起,这不仅会对用回收废的塑料进行加工造成困难和对生产的制品质量造成影响,而且混入的金属杂质还会损坏加工设备,因此,在用废旧塑料生产制品时,不仅要将废旧塑料中的各类杂质清除掉,而且也要将不同品种的塑料分开,只有这样,才能制得优质再生制品。
废旧塑料的分选方法有手工分选,磁选,密度分选,静电分选,浮选,温差分选和风筛分选等方法。
1.手工分选手工分选步骤如下:(1)除去金属和非金属杂质及剔除严重重量下降的废旧塑料。
(2)先按制品,如薄膜(农用薄膜,本色包装膜),瓶(矿泉水瓶,碳酸饮料瓶),杯和盒类,鞋底,凉鞋,泡沫塑料,边角料等进行分类,再根据上节鉴别法分类不同的塑料品种,如聚乙烯,聚丙烯,聚氯乙烯,聚苯乙烯,聚酯等。
(3)将经上述分类的废旧塑料制品再按颜色深浅和质量分选,颜色可分成如下几类:黑色,红,棕,黄色,蓝,绿和透明无色。
2.磁选磁选的主要目的是除去混入在废旧塑料中的钢铁碎屑杂质,因这些细碎钢铁屑不易用手工分选的方法除去,所以,必须通过磁选的方法清除干净。
3.密度分选密度分选是利用不同塑料具有不同密度这一性质进行分选的方法,通常有溶液分选,水力分选和离心密度分选法等,溶液分选法是将混杂的废旧塑料放进某种具有一定密度的溶液中,然后根据废旧塑料在该溶液中的沉浮状态来进行分选。
溶液分选方法的优点是简易可行,只要选择配制一种或几种溶液就可以进行大批量分选,而避免繁琐的人工分选,其缺点是有些种类的塑料的密度非常接近,因此,要获得高纯度的分离物比较困难。
水力分选常用水力分选器,为提高分选效率,常需先进行清洗,后溶液分选。
离心密度分离采用离心密度分离机。
4.静电分选静电分选是利用各种塑料不同的静电吸力来进行分选的方法。
废塑料热解技术与设备-概述说明以及解释

废塑料热解技术与设备-概述说明以及解释1.引言1.1 概述废塑料热解技术是一种重要的废物处理技术,通过高温处理废塑料可将其分解成低分子化合物,然后再用于生产能源或化工原料。
随着塑料污染愈演愈烈,废塑料热解技术成为了一种重要的解决方案。
本文将重点介绍废塑料热解技术的原理、应用以及相关设备的设计与运行。
通过深入研究和探讨,希望能为促进废塑料资源化利用和环境保护做出贡献。
1.2 文章结构本文将首先介绍废塑料热解技术的基本原理和工作原理,包括热解过程中的反应机制和关键参数。
接着将详细介绍废塑料热解设备的类型、结构和工作原理,比较不同设备的优缺点。
最后将探讨废塑料热解技术在环境保护、资源回收利用等方面的应用,展示其重要性和潜在价值。
通过对技术、设备和应用的全面介绍,旨在为读者提供全面了解和深入认识废塑料热解技术与设备的机会。
文章1.3 目的部分的内容:本文旨在介绍废塑料热解技术与设备的相关知识,探讨其在废塑料资源化利用中的重要性和应用前景。
通过对废塑料热解技术的深入探讨,希望能够加深读者对该技术的理解,促进废塑料资源化利用的推广与应用,推动废塑料处理行业向更加环保、高效的方向发展。
同时,本文旨在为相关领域的研究者和从业者提供参考和借鉴,促进该领域的技术创新和进步。
2.正文2.1 废塑料热解技术废塑料热解技术是一种将废塑料转化为有用化学品或燃料的方法。
通过在高温下将废塑料分解成气体、液体和固体产物,可以实现资源的高效利用和循环利用。
废塑料热解技术主要包括热解过程、热解产物的提取和纯化等步骤。
在废塑料热解过程中,废塑料经过预处理后通入反应器,在缺氧或氮气气氛下加热至高温,通过裂解和反应,废塑料分解生成气体、液体和固体产物。
气体主要是可燃气体,如氢气、甲烷等,可用作化学品合成或燃料;液体产品主要是石油类产品,可用于燃料或化工原料;固体产物主要是焦炭,可用作燃料或原料。
废塑料热解技术相比传统的废塑料处理方法具有许多优势,如高效、环保、资源可回收等。
塑料热解工艺

塑料热解工艺我呀,一直对那些看似平常,实则蕴含着无限可能的东西特别感兴趣。
塑料,这个在我们生活里无处不在的家伙,就像是一个既让人爱又让人恨的朋友。
每天我们都在和各种各样的塑料制品打交道,从塑料袋到塑料瓶,它们方便了我们的生活,可一旦用完了,就成了让人头疼的垃圾。
不过呢,今天我想和大家聊聊一种超级酷的处理塑料垃圾的方法——塑料热解工艺。
你知道吗?塑料热解就像是一场神奇的魔法表演。
想象一下,那些被我们丢弃的塑料垃圾就像是一群不受欢迎的小怪物,堆积在角落里。
而塑料热解工艺就是一个超级魔法师,它能把这些小怪物变成有用的宝贝。
我有个朋友叫小李,他在一家环保科技公司工作。
有一次我去他那儿参观,就亲眼见识到了塑料热解工艺的厉害。
他带我走进他们的实验室,指着那些看起来乱七八糟的塑料垃圾说:“你可别小看这些东西,在热解工艺下,它们会有大变身。
”那这个塑料热解工艺到底是怎么一回事呢?简单来说,就是在高温的环境下,让塑料发生分解反应。
这个高温就像是一把超级热的火,把塑料这个大团体给打散了。
就好比一群紧紧抱在一起的小伙伴,在高温这个厉害的外力下,不得不松开手,各自散开。
在这个过程中,塑料里的大分子会被分解成小分子。
这小分子就像是被解放出来的小精灵,有着各自的新特性。
比如说,有些会变成油类物质。
你能想象吗?那些废旧塑料竟然能变成油!这就像是把石头变成了金子一样神奇。
还有些会变成可燃气体。
我当时就特别惊讶,对小李说:“这简直太不可思议了,就像垃圾变成了宝藏啊!”小李笑着回答我:“这就是科技的力量啊,可别小瞧它。
”不过呢,这个塑料热解工艺可不是随随便便就能做好的。
它就像一道特别复杂的菜,需要精确的火候和合适的配料。
温度要是控制不好,就像做饭时火大了或者火小了一样,整个热解过程就会出问题。
要是温度太高了,可能会产生一些不好的物质,就像炒菜时把菜烧焦了,那可就没法吃了。
而且啊,不同类型的塑料在热解的时候也有不同的要求。
这就好比不同的食材,做的时候得用不同的方法。
塑料制品的生物降解与环保技术
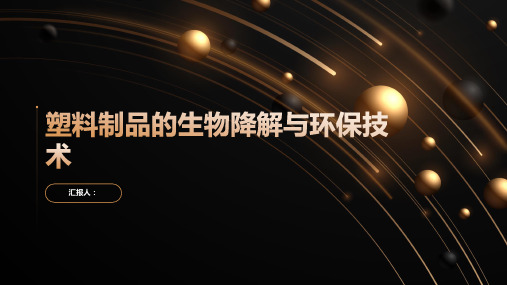
分类:环保技术可以分为污 染防治技术、生态保护技术、 资源循环利用技术等。
污染防治技术:包括废水处 理技术、废气处理技术、固 体废物处理技术等。
生态保护技术:包括生态修 复技术、生物多样性保护技 术等。
资源循环利用技术:包括废 物资源化技术、再生资源利 用技术等。
生物降解塑料:利用微生物将塑料分解为无害物质 光降解塑料:在紫外线作用下分解为无害物质 化学降解塑料:通过化学反应将塑料分解为无害物质 绿色环保技术:采用可再生资源、可降解材料和环保工艺生产塑料制品
酶解:酶将塑料 制品分解为更小 的分子
光解:阳光照射 下,塑料制品分 解为小分子
热解:高温下, 塑料制品分解为 小分子
生物吸收:微生 物吸收分解后的 小分子,用于自 身生长和繁殖
生物转化:微生 物将吸收的小分 子转化为无害物 质,如二氧化碳 和水
光降解塑料:在 光照条件下分解
水降解塑料:在 水中分解
物质
化学降解技术:通 过化学反应将塑料 制品分解为无害物
质
复合降解技术:结 合多种降解技术, 提高降解效率和效
果
光降解技术:利用阳光 将塑料制品分解为无害
物质
环保材料的研发: 研发可降解、可循 环利用的环保材料, 替代传统塑料制品
定义:回收利用 是指将废弃的塑 料制品进行收集、 分类、处理和再 利用的过程。
治理:需要采取 有效措施,如加 强监管、推广环 保技术等
减少使用:减少不必要的塑料制品 使用,选择可重复使用的替代品
生物降解:研发可生物降解的塑料 制品,减少环境污染
添加标题
添加标题
添加标题
添加标题
回收利用:建立完善的塑料制品回 收体系,提高回收率
环保技术:采用环保技术处理塑料 废弃物,如焚烧、填埋等
- 1、下载文档前请自行甄别文档内容的完整性,平台不提供额外的编辑、内容补充、找答案等附加服务。
- 2、"仅部分预览"的文档,不可在线预览部分如存在完整性等问题,可反馈申请退款(可完整预览的文档不适用该条件!)。
- 3、如文档侵犯您的权益,请联系客服反馈,我们会尽快为您处理(人工客服工作时间:9:00-18:30)。
废旧塑料的热解废塑料热解是将已清楚杂质的塑料置于无氧或者低氧的密封容器中加热,使其裂解为低分子化合物。
其基本原理是将塑料制品中的高聚物进行彻底的大分子裂解,使其回到低分子量状态或单体态。
按照大分子内键断裂位置的不同,可将热解分为解聚反应型、随机裂解型和中间型。
解聚反应型塑料受热裂解时聚合物发生解离,生成单体,主要切断了单分子之间的化学键。
这类塑料有α-甲基苯乙烯、聚甲基丙烯酸甲酯等,它们几乎100%地裂解成单体。
随机裂解型塑料受热时分子内化学键的断裂是随机的,产生一定数目的碳原子和氢原子结合的的分子化合物,这类塑料有聚乙烯、聚丙烯等。
大多数塑料的裂解两者兼而有之,属于中间型,但在合适的温度、压力、催化剂条件下,能使其中某些特定数目链长的产物大大增加,从而获得有一定经济价值的产物,如汽油、柴油等。
裂解所要求的温度取决于塑料的种类及回收的目的产物,温度超过600℃,热解的主要产物是混合燃料气,如CH4、C2H4等轻烃。
温度在400~600℃时,主要裂解产物为混合轻烃、石脑油、重油、煤油及蜡状固体,PE、PP的裂解产物主要是燃料气和燃料油,PS热解产物主要是苯乙烯单体。
热解反应主要表现为C-C键的断裂,同时伴有C-H键断裂,热效应为吸热过程。
即外界必须提供大于C-C键能的能量,反应才能顺利进行。
因此,早期的塑料热解方法均为简单的热裂解,即单纯通过加热,使废塑料发生裂解。
但这种方法存在明显的缺陷,即能耗高、效率低、选择性不强。
因此人们迅速开发出了催化裂解法,在热解阶段假如催化剂,不但可以降低反应所需的活化能、提高效率,而且可以提高产物的选择性,相对于高温热解有着明显的优势。
由于催化剂的使用增加了成本,而且催化剂容易积炭失活,而且催化剂本身不易回收。
之后人们又开发出了热裂解-催化改质工艺,使得催化热解工艺得到进一步的完善。
综上所述,废塑料热解主要包括热裂解法、催化热裂解法、热裂解-催化改质法,其中又有不同的工艺形式,如图1-1所示。
一、废塑料热裂解的分类1热裂解热裂解法是最简单的塑料裂解方法,它通过提供热能,克服塑料聚合物裂解所需的活化能,并产生以下三种反应:(1)聚合物通过解聚生成单体;(2)聚合物分子链无规则断裂,产生低分子化合物;(3)通过消除取代基或官能团产生小分子,伴随有不饱和化合物的产生和聚合物交联乃至结焦。
该方法裂解反应温度高,反应时间长,所得汽油辛烷值低,且含有大量烯烃,诱导期短。
所得柴油凝点高,十六烷值低,含蜡量高。
废聚乙烯塑料热裂解的产物多为链烷烃或α-烯烃,生产柴油馏分的反应条件是475℃左右,低压或常压下,反应时间4h左右。
该法投资少、工艺简单,主要设备有热解反应釜、分馏塔、加热控温装置和进料装置。
由于该方法难以得到有经济价值的油品,目前已较少使用。
2催化热解在一定温度、压力、催化剂存在条件下,废塑料发生裂解、氢转移、缩合等特征反应,得到相对分子质量和结构在一定范围内的产物的方法[24]。
通常所用的催化剂有固体硅酸铝、分子筛,它们都属于固体酸催化剂,在反应过程中能够提供质子氢,使反应伴随氢转移过程,从而具有异构化功能。
由于此反应过程中大量焦炭沉积于催化剂表面,使沉积失活,因此催化剂的再生与剩余催化剂的回收比较困难。
由于催化热解法是将催化剂与废塑料混合在一起进行加热,热裂解与催化裂解反应同时进行,所以又称为一段法工艺。
该方法以催化裂解为主,反应速率快、能耗低,油品中异构化、芳烃化产物较多。
该法所需设备主要有塑料切碎机、螺杆挤出机、催化热解釜、分馏塔及控温加热装置。
3热解-催化改质法此法是将废塑料先进行高温热解,产生的高温热解气经过催化剂作用,得到品质较高的油品,类似于石油炼制中的裂解-催化重整过程。
废塑料经过热解后得到的液体燃料是沸点较宽的烃类物质,其中汽油、柴油等轻质馏分含量不高且品质低,若要提高汽油的辛烷值,则需提高异链烷烃、环烷烃和总芳烃含量。
采用催化改质法可以达到改善油品品种的目的。
由于该法是将废塑料热解后,再对热解气进行催化改质,所以又称为二段法工艺。
该方法多用于处理混合废塑料,操作灵活、运行费用较低。
为提高反应速率,缩短反应时间,可在热解阶段加入少量催化剂,从而形成催化热解-催化改质的复合二段法工艺,与一段法工艺相比,二段法中用于催化改质的催化剂可以很好的再生利用。
该方法所用的主要设备有塑料切碎机、螺杆挤出机、热解釜、催化反应器、分馏塔等。
比较上述几种方法有以下特点:(1)从反应温度看,热裂解最高,催化热解最低,热解-催化改质居中;(2)从反应速率看,催化热解最快,热解-催化改质居中,热裂解最慢;(3)从燃料油品种看,热解-催化改质最好,催化热解次之,热裂解最差;(4)从能耗看,催化热解最低,热裂解居中,热解-催化改质最高。
另外,二段法工艺较为成熟,应用广泛。
一段法工艺由于催化剂用量大且不易回收利用,推广应用受到限制。
热裂解处理混合废塑料所得油品蜡含量高、质量差,但若采取此法处理废聚乙烯可得高质量的蜡,经济效益也比较可观。
催化热解如能够解决熔融物的净化及反应残渣与催化剂的分离问题,则将具有很大的发展潜力。
二、废塑料热解催化剂催化是化学工业的支柱。
现代化学工业和炼油工业的生产,百分之八十以上都使用催化过程。
化学工业在综合利用资源、发展新的工业生产过程、工业污染的防治和新能源的开发等方面,都是依靠催化过程作为重要的手段。
近年来,随着大量现代分析测试技术在催化剂研究上的应用和新型催化材料的出现,催化剂工业得到了很大发展。
研究开发新型催化材料催化剂、用新型材料催化某些传统反应过程和开发新的工艺路线,催化新的化学反应的尝试,已成为催化研究的重要分支。
在实用催化剂的开发中,负载型催化剂、配合物催化剂、固体酸碱催化剂、沸石类催化剂、水滑石类催化剂为广大学者所重视。
石油工业的蓬勃发展,对有关反应涉及的催化剂提出了新的要求。
如裂解、重整、氧化、加氢、脱氢、烷基化、聚合等,没有催化剂的存在这些反应都难以行。
其中,金属及其金属氧化物在石油工业中应用最为广泛。
2废塑料热解催化剂分类废塑料热解用到的催化剂主要分为两类[47]:(1)分子筛或改性分子筛,如Y型分子筛与Al2O3形成多层固定床、REY型分子筛等;(2)金属氧化物,如硅铝微球、Al2O3、CuO、ZnO、Fe2O3、Co-Mo氧化物系列。
2.1分子筛或改性分子筛催化剂分子筛是由氧化硅、氧化铝组成的具有特殊立体结构的物质。
20世纪60年代,美国Mobil公司率先将稀土分子筛引入重油催化裂化,大幅增加了汽油产量和质量,提高了装置能力。
稀土分子筛的引入,被誉为“60年代炼油工业的技术革命”。
而我国研究人员[48]合成的磷酸钴铝分子筛和磷酸钴镁分子筛是第三代分子筛。
这两种分子筛拥有B酸酸性和L酸酸性中心,具有良好的热稳定性和良好的裂解性能,在石油化工领域有着良好的应用前景。
翼星等[49]采用自制分子筛催化剂对废聚乙烯塑料进行催化改质,液相产率可达到80%以上,经过催化改质可得到合格的汽油、柴油,测得的汽油辛烷值82。
该催化剂采用硝酸镁、磷酸铵调节Y型分子筛的酸性,与不同比例的铝溶胶和高岭土混合,得到一系列不同型号的催化剂。
以中强酸位、弱酸位为主,平均孔径为25~40nm的改性Y型分子筛催化剂上的裂解反应以重油和柴油的裂解反应为主,可以用于废塑料的热裂解催化改质。
Songip将一些固体酸催化剂,如经稀土金属离子交换的Y型分子筛(REY)、HY、HZSM-5分子筛和硅铝胶(SA)用于催化重整废聚乙烯热裂解产生的重油来生产汽油得到了很好的催化效果。
而单纯使用普通的催化剂,如硅铝胶和HZSM-5分子筛很难将重油转化成汽油。
HY和经稀土金属离子交换的Y型(REY)分子筛因具有较大的孔径,己被证明是催化裂解催化剂有效的分子筛,能将重油转换成汽油。
而且,REY分子筛更适合各种苛刻的条件,生产的汽油辛烷值(RON)达到67,汽油收率到达48%。
相反,高硅或者普通的HZSM-5分子筛生产的汽油辛烷值只有23,汽油收率18%。
中国专利报道了以多次改性的Y型分子筛和高活性的氢氧化铝催化剂,热解废塑料得到的汽油和柴油,总产率85%~87%。
另有使用Ni、Cu、Al等五种金属混合物作催化剂制取油品的报道。
Masuda等采用Ni-REY在水蒸气环境下裂解废塑料,其中Ni的作用是把氢原子从水蒸气转移到碳氢化合物中。
在水蒸气环境下,催化剂的强酸位(经常导致过度裂解)被水蒸气包围,不仅可得到收率较高的液体油品,而且结焦率减少。
与氮气环境下的MFI分子筛的催化作用相比,再生后,Ni-REY的活性保持稳定,而MFI分子筛逐渐失活,而且对汽油的裂解选择性差别较大,液相收率Ni-REY在水蒸气下为78%,MFI在氮气下为35%。
Uemichi等比较了HZSM-5、HY、H-丝光沸石分子筛催化剂、硅铝催化剂裂解废塑料时由于积碳而导致的失活行为。
HZSM-5裂解聚乙烯时,由于积碳较少,催化剂没有失活,而且该催化剂生产轻质油较多,主要由异链烷烃和芳烃构成,但是裂解聚苯乙烯时,催化剂的积碳较多,很容易失活。
硅铝催化剂随着裂解气增多而逐渐失活,而HY,H-丝光沸石分子筛催化剂的失活速度很快。
利用铂催化剂对废塑料的裂解产物中不饱和碳氢化合物进行加氢催化,催化温度390℃,反应时间1.5h,沸点低于360℃的液体产物的产率超过90%。
Zeng等研究了自制的HC-1分子筛催化剂对塑料裂解产物的催化改质作用,并在流化床上进行扩大的工业试验,得到的汽油辛烷值达到93.45。
他们采用经过特殊改性的Y型分子筛和高纯度、高比表面积的氧化铝在特殊条件下加工而成的催化剂(多层固定床),直接催化裂解熔融的PS,反应温度保持在320~390℃,液态产物均为沸点在350℃的轻质产物,苯乙烯产率为62%~65%,乙苯为12%~15%,甲苯为8%~10%,α-甲基苯乙烯为10%~13%。
日本富士公司是采用ZSM-5分子筛催化剂,使产物的碳分布轻质化,裂解产物以煤油、汽油为主。
北京丽坤工厂以沸石为二段位催化剂,在反应温度300~400℃条件下,生产汽油和柴油。
2.2金属氧化物催化剂以金属氧化物为主要催化活性组分的催化剂。
在工业上用得最多的是过渡金属氧化,它们广泛用于氧化还原型机理的催化反应。
主族元素的氧化物多数用于酸碱型机理的催化反应,包括脱氢、加氢、氧化脱氢、氨化氧化、氧氯化等反应。
过渡金属氧化物催化剂,一般为非化学计量化合物,存在着负离子或正离子缺位,形成特定的活性中心。
分子结构中的某些金属-氧键的强度往往不同于正常化合物,能通过电子转移的机理而使反应物活化。
在金属氧化物催化的氧化反应中有多种活化的过渡态氧生成,如O、O、O,它们表现出不同的反应活性,可分两种作用机理,即吸附氧作用机理和晶格氧作用机理。