Thin wafer grinding 超薄晶圆减薄
一种超薄晶圆减薄以及背面金属蒸镀的工艺方法[发明专利]
![一种超薄晶圆减薄以及背面金属蒸镀的工艺方法[发明专利]](https://img.taocdn.com/s3/m/badea38cc67da26925c52cc58bd63186bceb921c.png)
(19)中华人民共和国国家知识产权局(12)发明专利申请(10)申请公布号 (43)申请公布日 (21)申请号 202011336926.X(22)申请日 2020.11.25(71)申请人 绍兴同芯成集成电路有限公司地址 312000 浙江省绍兴市越城区银桥路326号(原永和酒业)1幢1楼113室(72)发明人 严立巍 文锺 符德荣 (74)专利代理机构 北京同辉知识产权代理事务所(普通合伙) 11357代理人 张明利(51)Int.Cl.H01L 21/683(2006.01)(54)发明名称一种超薄晶圆减薄以及背面金属蒸镀的工艺方法(57)摘要本发明公开一种超薄晶圆减薄以及背面金属蒸镀的工艺方法,包括环状保护、键合、薄化减厚、浸泡脱离、支撑保护和转移蒸镀。
本发明利用外围外环支撑保护结合亚膜可以制作超薄晶圆的研磨蚀刻工艺,既能避免破片,亦能提高最边缘部份的良率;可以使得晶圆薄片可在不受应力的情况下脱胶并传送转移;使得薄晶圆在外加圆环的支撑保护下转移至金属膜环治具上,可以进行镀金属膜的工艺;环状支撑保护相对于周边厚度较厚的硅片或是玻璃载板的方法,成本较低且不会造成晶圆周边良率的损失。
解决了现有技术中研磨后晶圆外围厚度较厚,将会损失最少3‑5%的良率,且最后必须切除外围才能进行切割工艺,增加生产成本,影响加工效率。
权利要求书1页 说明书4页 附图2页CN 112466807 A 2021.03.09C N 112466807A1.一种超薄晶圆减薄以及背面金属蒸镀的工艺方法,其特征在于,包括如下步骤:S1、环状保护将研磨胶带(2)的侧端环绕贴合有金属环(1),形成环状保护;S2、键合将晶圆(3)背面向上,正面与研磨胶带(2)键合;S3、薄化减厚对晶圆(3)的背面进行蚀刻,减少晶圆(3)的厚度,然后解除应力,继续减少晶圆(3)的厚度;S4、浸泡脱离将晶圆(3)与研磨胶带(2)浸泡至有机溶剂中,溶剂从边缘逐渐渗入晶圆(3)与研磨胶带(2)的键合面,去除黏着力后,研磨胶带(2)应重力在溶剂浸泡中脱离;S5、支撑保护将晶圆(3)转移至金属环(1)上,使得晶圆(3)得到金属环(1)的支撑和保护;S6、转移蒸镀将受到金属环(1)支撑保护的晶圆(3)转移走,在晶圆(3)背面镀上金属膜(4)。
晶圆减薄技术
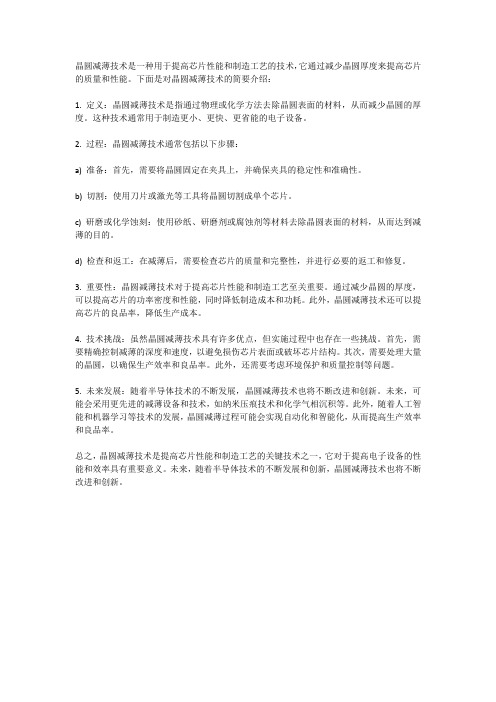
晶圆减薄技术是一种用于提高芯片性能和制造工艺的技术,它通过减少晶圆厚度来提高芯片的质量和性能。
下面是对晶圆减薄技术的简要介绍:1. 定义:晶圆减薄技术是指通过物理或化学方法去除晶圆表面的材料,从而减少晶圆的厚度。
这种技术通常用于制造更小、更快、更省能的电子设备。
2. 过程:晶圆减薄技术通常包括以下步骤:a) 准备:首先,需要将晶圆固定在夹具上,并确保夹具的稳定性和准确性。
b) 切割:使用刀片或激光等工具将晶圆切割成单个芯片。
c) 研磨或化学蚀刻:使用砂纸、研磨剂或腐蚀剂等材料去除晶圆表面的材料,从而达到减薄的目的。
d) 检查和返工:在减薄后,需要检查芯片的质量和完整性,并进行必要的返工和修复。
3. 重要性:晶圆减薄技术对于提高芯片性能和制造工艺至关重要。
通过减少晶圆的厚度,可以提高芯片的功率密度和性能,同时降低制造成本和功耗。
此外,晶圆减薄技术还可以提高芯片的良品率,降低生产成本。
4. 技术挑战:虽然晶圆减薄技术具有许多优点,但实施过程中也存在一些挑战。
首先,需要精确控制减薄的深度和速度,以避免损伤芯片表面或破坏芯片结构。
其次,需要处理大量的晶圆,以确保生产效率和良品率。
此外,还需要考虑环境保护和质量控制等问题。
5. 未来发展:随着半导体技术的不断发展,晶圆减薄技术也将不断改进和创新。
未来,可能会采用更先进的减薄设备和技术,如纳米压痕技术和化学气相沉积等。
此外,随着人工智能和机器学习等技术的发展,晶圆减薄过程可能会实现自动化和智能化,从而提高生产效率和良品率。
总之,晶圆减薄技术是提高芯片性能和制造工艺的关键技术之一,它对于提高电子设备的性能和效率具有重要意义。
未来,随着半导体技术的不断发展和创新,晶圆减薄技术也将不断改进和创新。
晶圆减薄抛光工艺对芯片强度影响的研究

收稿日期:2020-05-09晶圆减薄抛光工艺对芯片强度影响的研究杨生荣1,王海明1,叶乐志2(1.北京中电科电子装备有限公司,北京100176;2.北京工业大学,北京100124)摘要:论述了芯片封装工艺中的减薄、抛光工艺对芯片强度的影响,通过三点弯曲强度测试方法,分析对比减薄工艺以及在减薄后进行化学机械抛光(CMP )和干式抛光(DP )消除应力后芯片强度的分布。
实验表明,晶圆减薄磨削后,对背面磨削面进行去应力抛光,会获得比较高的芯片强度。
关键词:减薄;芯片强度;应力去除;化学机械抛光;干式抛光中图分类号:TN305.2文献标识码:A文章编号:1004-4507(2020)03-0013-04Study on the Influence of Wafer Thinning and PolishingProcess on Chip StrengthYANG Shengrong 1,WANG Haiming 1,YE Lezhi 2(1.CETC Beijing Electronic Equipment Co.,Ltd ,Beijing 100176,China ;2.Beijing University of Technology ,Beijing 100124,China )Abstract:The influence of thinning and polishing process on chip strength in IC packaging process is summarized.By 3-point bending strength test method ,the chip strength distribution after thinning ,CMP(Chemical Mechanical Polishing)and DP (Dry Polishing )stress relief is analyzed and compared.The experiment shows that the chip with high strength can be obtained by stress relief polishing on the back grinding surface after wafer thinning grinding.Key words:Thinning ;Chip strength;Stress relief ;Chemical mechanical polishing (CMP);Dry polishing(DP)随着IC 技术的进步和发展,电子封装需要更薄的芯片来减小封装的体积,并允许多芯片堆叠封装在一个封装体中,这对封装工艺提出了新的挑战。
晶圆减薄研磨工艺
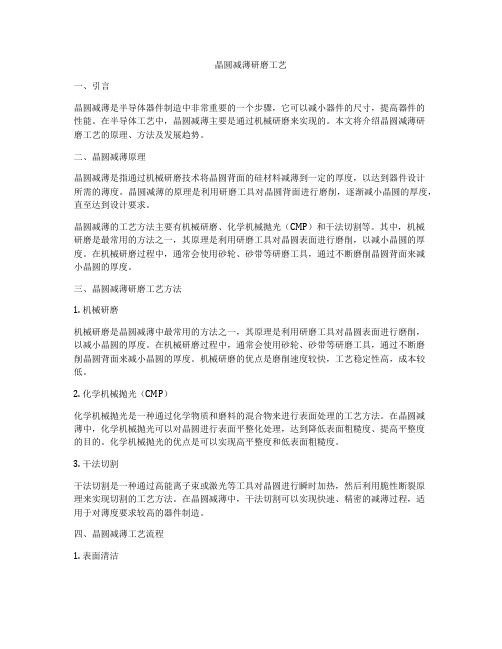
晶圆减薄研磨工艺一、引言晶圆减薄是半导体器件制造中非常重要的一个步骤,它可以减小器件的尺寸,提高器件的性能。
在半导体工艺中,晶圆减薄主要是通过机械研磨来实现的。
本文将介绍晶圆减薄研磨工艺的原理、方法及发展趋势。
二、晶圆减薄原理晶圆减薄是指通过机械研磨技术将晶圆背面的硅材料减薄到一定的厚度,以达到器件设计所需的薄度。
晶圆减薄的原理是利用研磨工具对晶圆背面进行磨削,逐渐减小晶圆的厚度,直至达到设计要求。
晶圆减薄的工艺方法主要有机械研磨、化学机械抛光(CMP)和干法切割等。
其中,机械研磨是最常用的方法之一,其原理是利用研磨工具对晶圆表面进行磨削,以减小晶圆的厚度。
在机械研磨过程中,通常会使用砂轮、砂带等研磨工具,通过不断磨削晶圆背面来减小晶圆的厚度。
三、晶圆减薄研磨工艺方法1. 机械研磨机械研磨是晶圆减薄中最常用的方法之一,其原理是利用研磨工具对晶圆表面进行磨削,以减小晶圆的厚度。
在机械研磨过程中,通常会使用砂轮、砂带等研磨工具,通过不断磨削晶圆背面来减小晶圆的厚度。
机械研磨的优点是磨削速度较快,工艺稳定性高,成本较低。
2. 化学机械抛光(CMP)化学机械抛光是一种通过化学物质和磨料的混合物来进行表面处理的工艺方法。
在晶圆减薄中,化学机械抛光可以对晶圆进行表面平整化处理,达到降低表面粗糙度、提高平整度的目的。
化学机械抛光的优点是可以实现高平整度和低表面粗糙度。
3. 干法切割干法切割是一种通过高能离子束或激光等工具对晶圆进行瞬时加热,然后利用脆性断裂原理来实现切割的工艺方法。
在晶圆减薄中,干法切割可以实现快速、精密的减薄过程,适用于对薄度要求较高的器件制造。
四、晶圆减薄工艺流程1. 表面清洁在进行晶圆减薄之前,首先需要对晶圆表面进行清洁处理,以确保研磨过程中不受到杂质的干扰。
2. 粗磨经过表面清洁处理后,将晶圆放入研磨设备中进行粗磨。
在粗磨过程中,通常会选择适当的研磨工具和磨料,以尽快减小晶圆的厚度。
3. 精磨粗磨完成后,再将晶圆放入研磨设备中进行精磨。
晶圆切割晶圆切割和微加工新技术
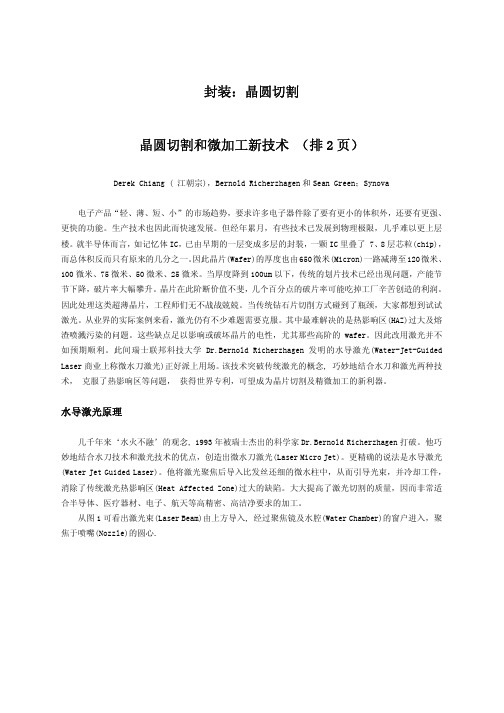
封装:晶圆切割晶圆切割和微加工新技术 (排2页)Derek Chiang ( 江朝宗),Bernold Richerzhagen和Sean Green;Synova电子产品“轻、薄、短、小”的市场趋势,要求许多电子器件除了要有更小的体积外,还要有更强、更快的功能。
生产技术也因此而快速发展。
但经年累月,有些技术已发展到物理极限,几乎难以更上层楼。
就半导体而言,如记忆体IC,已由早期的一层变成多层的封裝,一颗IC里叠了 7、8层芯粒(chip),而总体积反而只有原来的几分之一。
因此晶片(Wafer)的厚度也由650微米(Micron)一路减薄至120微米、100微米、75微米、50微米、25微米。
当厚度降到100um以下,传统的划片技术已经出现问题,产能节节下降,破片率大幅攀升。
晶片在此阶断价值不斐,几个百分点的破片率可能吃掉工厂辛苦创造的利润。
因此处理这类超薄晶片,工程师们无不战战兢兢。
当传统钻石片切削方式碰到了瓶颈,大家都想到试试激光。
从业界的实际案例来看,激光仍有不少难题需要克服。
其中最难解决的是热影响区(HAZ)过大及熔渣喷溅污染的问题。
这些缺点足以影响或破坏晶片的电性,尤其那些高阶的wafer。
因此改用激光并不如预期顺利。
此间瑞士联邦科技大学Dr.Bernold Richerzhagen发明的水导激光(Water-Jet-Guided Laser商业上称微水刀激光)正好派上用场。
该技术突破传统激光的概念, 巧妙地结合水刀和激光两种技术, 克服了热影响区等问题, 获得世界专利,可望成为晶片切割及精微加工的新利器。
水导激光原理几千年来‘水火不融’的观念, 1993年被瑞士杰出的科学家Dr.Bernold Richerzhagen打破。
他巧妙地结合水刀技术和激光技术的优点,创造出微水刀激光(Laser Micro Jet)。
更精确的说法是水导激光(Water Jet Guided Laser)。
半导体封装制程及其设备介绍——【半导体芯片】
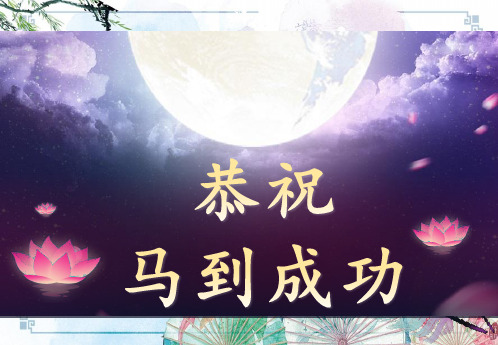
Dual In-line Package
Shape
Typical Features
Material Lead Pitch No of I/O
Ceramic Plastic
2.54 mm (100miles)
8 ~64
SIP
Single In-line Package
Plastic
2.54 mm (100miles) 1 direction
Material Lead Pitch No of I/O
Ceramic
1.27 mm (50miles) j-shape bend 4 direction
lead
18~124
Ceramic
0.5 mm
32~200
SMT (Optional)
Taping (Optional)
Grinding (Optional)
lead
3~25
Through Hole Mount
ZIP
Zigzag In-line Package
S-DIP
Shrink Dual In-line
Package
封裝型式
Shape
Typical Features
Material Lead Pitch No of I/O
Plastic
2.54 mm (100miles) 1 direction
Pack
封裝型式
Shape
Typical Features
Material Lead Pitch No of I/O
Plastic
1.27 mm (50miles) 2 direction
lead
8 ~40
半导体封装制程与设备材料知识简介
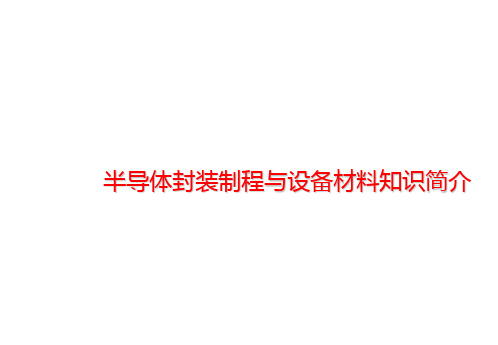
封裝型式
Shape
Typical Features
Materia Lead Pitch No of I/O l
Cerami c
1.27, 0.762 mm
(50, 30miles) 2, 4 direction
lead
20~80
Ceramic
1.27,1.016, 0.762 mm (50, 40, 30
(氧化处理)
Depositio n
(沉积)
WireBondin g
(焊线)
Laser mark (激光印字)
Laser Cut & package saw
(切割成型)
Testin g
(测试)
Lithograp hy
(微影)
Wafer Inspection (晶圆检查) 前段結束
Moldin g
(塑封)
Plastic
1.27 mm (50miles) 2 direction
lead
8 ~40
Plastic
1.0, 0.8, 0.65 mm 4 direction
lead
88~200
Surface Mount
FPG
Flat Package of Glass
LCC
Leadless Chip
Carrier
lead
18~124
Ceramic 0.5 mm
32~200
SMT (Optional)
Taping (Optional)
Assembly Main Process
Grinding (Optional)
Detaping (Optional)
Wafer Mount
晶圆减薄机工作原理
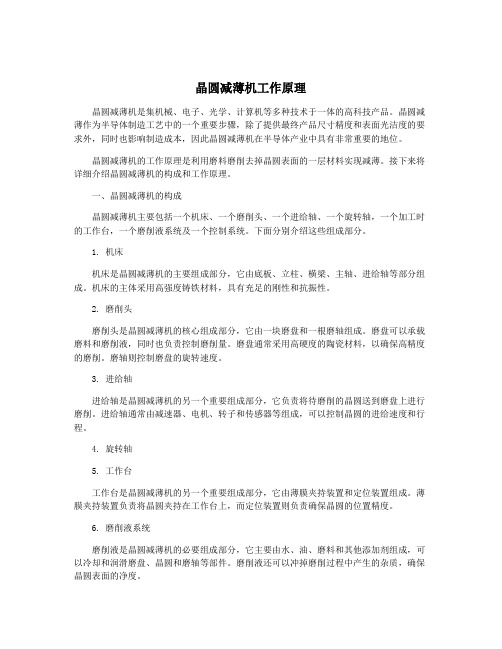
晶圆减薄机工作原理晶圆减薄机是集机械、电子、光学、计算机等多种技术于一体的高科技产品。
晶圆减薄作为半导体制造工艺中的一个重要步骤,除了提供最终产品尺寸精度和表面光洁度的要求外,同时也影响制造成本,因此晶圆减薄机在半导体产业中具有非常重要的地位。
晶圆减薄机的工作原理是利用磨料磨削去掉晶圆表面的一层材料实现减薄。
接下来将详细介绍晶圆减薄机的构成和工作原理。
一、晶圆减薄机的构成晶圆减薄机主要包括一个机床、一个磨削头、一个进给轴、一个旋转轴,一个加工时的工作台,一个磨削液系统及一个控制系统。
下面分别介绍这些组成部分。
1. 机床机床是晶圆减薄机的主要组成部分,它由底板、立柱、横梁、主轴、进给轴等部分组成。
机床的主体采用高强度铸铁材料,具有充足的刚性和抗振性。
2. 磨削头磨削头是晶圆减薄机的核心组成部分,它由一块磨盘和一根磨轴组成。
磨盘可以承载磨料和磨削液,同时也负责控制磨削量。
磨盘通常采用高硬度的陶瓷材料,以确保高精度的磨削。
磨轴则控制磨盘的旋转速度。
3. 进给轴进给轴是晶圆减薄机的另一个重要组成部分,它负责将待磨削的晶圆送到磨盘上进行磨削。
进给轴通常由减速器、电机、转子和传感器等组成,可以控制晶圆的进给速度和行程。
4. 旋转轴5. 工作台工作台是晶圆减薄机的另一个重要组成部分,它由薄膜夹持装置和定位装置组成。
薄膜夹持装置负责将晶圆夹持在工作台上,而定位装置则负责确保晶圆的位置精度。
6. 磨削液系统磨削液是晶圆减薄机的必要组成部分,它主要由水、油、磨料和其他添加剂组成,可以冷却和润滑磨盘、晶圆和磨轴等部件。
磨削液还可以冲掉磨削过程中产生的杂质,确保晶圆表面的净度。
7. 控制系统晶圆减薄机的控制系统负责控制整个机器的运行。
它由一个主控板、外设、传感器和执行器等部分组成。
主控板负责储存和处理代码,控制机器运行;外设可以帮助订单和退出代码;传感器负责检测和反馈磨削过程中的各种参数;执行器则根据控制信号改变机器的运行状态。
半导体封装制程与设备材料知识介绍

24~32
Ceramic Plastic
2.54 mm (100miles)
Surface Mount
SOP Small Outline Package
QFP Quad-Flat
Pack
封裝型式
Shape
Typical Features
Material Lead Pitch No of I/O
Plastic
1.27 mm (50miles) 2 direction
lead
8 ~40
Plastic
1.0, 0.8, 0.65 mm 4 direction
lead
88~200
Surface Mount
FPG
Flat Package of Glass
LCC
Leadless Chip
Carrier
封裝型式
Shape
Tester
Digital
Credence
SC312
Digital
Teradyne
J750
Mix-Signal Credence
Quartet one and one+
Mix-Signal HP
HP93000 P600
Mix-Signal HP
HP93000 C400
Mix-Signal Teradyne
Die Attach (上片)
Deposition (沉积)
WireBonding (焊线)
Wafer Inspection (晶圆检查) 前段結束
Molding (塑封)
Laser mark (激光印字)
Laser Cut & package saw Testing
晶圆减薄过程TTV调整技术研究
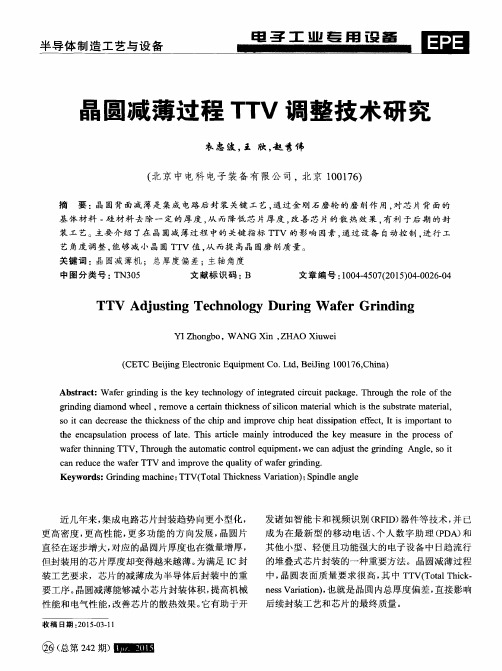
关 键词 :晶 圆减 薄机 ; 总厚度 偏 差 ; 主 轴角 度
中图 分类 号 : T N3 0 5 文 献标 识 码 : B 文 章 编号 : 1 0 0 4 — 4 5 0 7 ( 2 0 1 5 ) 0 4 . 0 0 2 6 . 0 4
T T V Ad j u s t i n g T e c h n o l o g y Du r i n g Wa f e r Gr i n d i n g
S O i t c a n de c r e a s e t h e t hi c k ne s s o f t h e c h i p a nd i mpr ov e c h i p h e a t d i s s i p a t i o n e f f e c t ,I t i s i mpo r t a n t t o t he e nc a p s ul a t i o n p r o c e s s o f l a t e .Th i s a ti r c l e ma i n l y i nt r od uc e d t he k e y me a s u r e i n t h e pr o c e s s o f
Abs t r a c t :W a f e r g r i n di ng i s t h e ke y t e c h no l o g y o f i n t e g r a t e d c i r c ui t pa c k a g e .Th r o ug h t h e r ol e o f t h e
发诸 如智 能 卡和 视 频 识 别 ( R F I D) 器 件 等 技术 , 并 已
成 为在 最 新 型 的移 动 电话 、 个人数字助理 ( P DA) 和 其他 小型 、轻 便且 功 能强大 的 电子 设备 中 日趋 流行 的堆 叠式 芯 片封装 的一种 重要 方法 。晶 圆减薄 过 程 中, 晶 圆表 面质 量 要 求 很 高 , 其中T T V( T o t a l T h i c k . h e s s Va r i a t i o n ) , 也就 是 晶 圆 内总厚度 偏 差 , 直 接影 响 后 续封装 工 艺和 芯 片的最 终质 量 。
封装专业术语集锦

一常用文件、表单、报表中英文名称中文名称 英文名称notice清除通知单 PurgeRequest)Change工程变更申请 ECR(Engineeringplan)improvement持续改善计划 CIP(continuousProject戴尔专案 Dell收据 Receiptsheet数据表 Data核对表 Checklistchecklist文件清单 Documentation设备清单 Equipmentchecklist调查表,问卷 Questionnaireform报名表 Entry追踪记录表 Trackinglogreport日报表 Dailyreport周报表 Weeklyreport月报表 Monthlyreport年报表 Yearlyreport年度报表 Annualreport财务报表 Financialreport品质报表 Qualityreport生产报表 Production不良分析报表FAR(Failure analysis report)首件检查报告First article inspection report初步报告(或预备报告) Preliminaryreport一份更新报告An undated report一份总结报告 A final report纠正与改善措施报告(异常报告单) CAR (Corrective Action Report)出货检验报告Outgoing Inspection ReportofCompliance)符合性报告(材质一致性证明) COC(Certificatereport稽核报告 Audit品质稽核报告Quality audit reportreportaudit制程稽核报告 Process5S稽核报告5S audit report客户稽核报告Customer audit reportreportaudit供应商稽核报告 Supplier年度稽核报告Annual audit reportreportaudit内部稽核报告 Internal外部稽核报告External audit reportcontrolprocessSPC报表(统计制程管制) Statistical工序能力指数(Cpk) Process capability indexlimit(规格)上限 Upperlimit(规格)下限 Lower规格上限Upper Specification Limit(USL)规格下限Lower Specification Limit(LSL)上控制限(或管制上限)Upper Control Limit(UCL)下控制限(或管制下限)Lower Control Limit(LCL)最大值 Maximumvaluevalue平均值 Averagevalue 最小值 Minimum临界值Threshold value / critical valueMRB单(生产异常通知报告) Material Review Board ReportDiagramFlow工艺流程图 Process物料清单(产品结构表/用料结构表)BOM (Bill of Materials )合格供应商名录A VL (Approved Vendor List)异常报告单 CAR工程规范报告通知单(工程变更通知)ECNTECN临时工程规范报告通知单(临时工程变更通知)自主点检表Self Check List随件单(流程卡)Traveling Card (Run Card)压焊图Bonding diagram晶圆管制卡Wafer inspection card晶圆进料品质异常反馈单Feedback Report for Wafer Incoming QualityProblems订购单PO(Purchase Order)出货通知单Advanced Ship Notice送货单/交货单DO(Delivery Order)询价单RFQ(Request for quotation)可靠性实验报告Reliability Monitor Report产品报废单PSB特采控制表CRB退货单返工单PRB委工单委托封装加工确认单异常处理行动措施 OCAP工序关键词中英文对照序号 关键词 英文 备注1 进料检验IQC/IQA (Incoming QC Inspection)2 高倍显微镜 Highpowermicroscope减薄Grinding1 减薄Wafer grind Back grind2 裂纹 Wafercrack3 墨点Ink die / Ink dot4 胶膜(晶圆蓝胶带) Mounting tape / Blue tape5 晶圆 Wafer8 晶圆尺寸 Wafersize9 晶圆厚度Wafer thickness16 开始高度 StartPosition17 粗磨结束高度 Roughspeed细磨高度 Rough/fine18 细磨结束高度 FineSpeed19 清磨时间 SparkOut20 晶圆上胶带 Wafertapping21 晶圆上胶带机Wafer tapping M/C22 晶圆下胶带 Detapping23 晶圆下胶带机 WaferdetappingM/C24 晶圆减薄机 GrindingM/C25 磨头 Grindstone26 晶圆贴片 Wafermount27 晶圆贴片机 Wafermounter28 晶圆传递盒 Wafermagazine29 晶圆装载盒 Wafercassette 30 晶圆管制卡 Waferinspectioncard划片 Sawing1 划片 Wafersaw2 划片机Wafer saw M/C3 贴膜机/绷膜机 TapingM/C4 绷膜环Film Frame (铁环)cleaner5 清洗机 Waferclean6 晶圆清洗 Wafer7 干燥箱 Ovenhandler8 传递框(提篮) Cassettestreet9 划道 Scribe10 划道宽度 Scribewidthstreetblade11 划片刀 Saw12 进刀速Cut speedspeed13 主轴转速 Spindle14 晶粒尺寸 Diesizewater15 冷却水 Coolingwater16 切割水 DI18 刀痕宽度Kerf width & chippingdie20 背崩、缺角 Chipdie21 裂纹、裂片 Crackdie22 掉芯、掉片 MissingWidthStreet29 划道宽度 Saw32 晶粒、芯片 Diesize33 芯片尺寸 Die34 晶圆铁环Wafer film framebubbles35 薄膜气泡 Tape36 划片后目检 PSI 第二次目检上芯 Die Attach / Die Bondbond 装片Die Attach1 上芯 Diebonder2 上芯机 Die3 粘片胶Die attach material epoxy4 导电胶 Epoxy Conducting resin;Conductive adhesive 5 绝缘胶 Non-conductiveepoxy6 点胶头 Dispensernozzle7 吸嘴Rubber tip / Die pick-up toolpin ?8 顶针 Ejector9 墨点片Ink dotted dietape10 兰膜 BlueMagazine11 框架盒 L/Fframe12 引线框架 Lead13 固化 Curing14 干燥箱 Ovenscrap15 晶粒刮伤 Die16 压伤 Dented 凹损Lift-off17 晶粒脱落 Die18 粘偏(上芯歪斜) Skewdiemisorientation19 粘反(上芯反向) Die20 防氧化 OSP Anti-oxidationsqueezedel22 写胶前气压延时 Predelsqueeze写胶后气压延时 Postdelayup23 顶针延迟 Ejectheightup24 顶针高度 Ejectlevel25 粘片高度 Bond26 拣拾芯片高度 Picklevel27 粘接头拾取延迟Head pick delay28 粘接头粘接延时Head bond delay29 捡拾芯片延时 Pickdelaydelay30 粘接芯片延时 Bond31 布进夹转换延时Index clamp delay32 框架步进延时 Indexdelay33 推晶试验Die shear test34 导电胶厚度和覆盖率Epoxy thickness & coverageorientation35 芯片方向 Dievoid36 导电胶空洞 Epoxydamage37 芯片损伤 Chip38 芯片背面损伤Chip backside damagedie39 芯片装斜 Tilted40 芯片粘胶Epoxy on die41 芯片裂缝/晶粒裂痕 Crackdiedie42 翘芯片 Lifteddie43 误置芯片 Misplaced44 空粘No die on L/Fepoxy45 导电胶不足 Insufficientcrack46 多胶 Epoxydiameter47 线径 Wirecuring48 银浆烘烤 Epoxy49 边沿芯片Edge die / Partial diedie50 镜子芯片 Mirrordie51 掉片 Missing52 墨溅Ink splash / splatter53 上芯图 Diediagrambonding54 推片试验Die shear testTester55 推片试验机 Dieshear56 推片头Die shear toolcorrosion57 晶粒腐蚀 Metal58 芯片分级系统 Wafersystemmapping压焊 Wiring Bondingbond)焊丝、打线、球焊(Wire1 压焊 W/Bwire2 金丝 Gold3 焊点、铝垫Bond pad Soldered points4 第一焊点1st Bondsize5 焊点尺寸 Pad6 劈刀(钢嘴) Capillarypitch7 间距 Pad8 延展性 elongationload9 破断力 Breaking10 (焊丝)拉力Wire pull/ ball pull11 (焊丝)推力Wire shear/ ball shear12 超声功率Ultrasonic power13 压力Bonding forcetime14 时间 Bondingtemperature15 温度 Bonding16 超声波压焊Ultrasonic wire bonding17 打火烧球 EFOheight18 弧高 Loop120 第一脚 PIN21 球拉力试验Ball pull test22 球推力试验Ball shear testheight23 球高 Balldiameter24 球径 Ball25 弹坑(KOH腐蚀试验)Cratering (KOH etching test)26 剪切力 Shear(ThermalCompression 27 热压焊 TCBBond)28 助焊剂 Fluxdiagram布线图29 压焊图 Bondingbonding30 布线错误 Wrongsize31 焊点尺寸、铝垫尺寸 Pad32 焊点间距、铝垫间距 Padpitch33 焊不牢 Incompletebondbonding34 无焊 No35 氮气柜N2 box36 实时过程控制 RTPCTray37 产品盘 Handling38 压焊后目检 FBI39 压焊检验机FBI Insp. M/C40 低倍显微镜Low Power Microscope41 前站推车 ASS’YCart42 拉力试验(Wire) pull test43 拉力试验机Wire pull tester44 线钩Wire pull hook45 推球试验Ball shear test46 推球试验机Ball shear tester47 推球头Ball shear tool48 压焊腐蚀试验Bond cratering testdiscolor49 铝条变色 Metaldiscolor50 铝垫变色 BD.Padoxidepad51 铝垫氧化 Bond52 铝垫不粘Nonstick bond on padpeeling53 铝垫脱落 Bondpadpadcratering54 铝垫弹坑 Bond55 超过返工数Over rework limit56 剔球刮伤BD remove & scratch57 金球脱落Ball bond non-stick58 金球过大(小)Ball to large (small)59 金球短路Ball bond short60 引脚脱落Non-stick on lead61 压焊打偏Misplaced bond on LDbroken62 断线 Wirewire63 漏打 Missingconnection64 错打 Wronglooping65 弧度不良 Defectivesagging66 弧度下陷 Looploop67 弧度太低 Lowloop68 弧度太高 Highshort69 弧度短路 Loop70 跨越引线框架Wire overhang on LDresidue71 残线 Wiredistortion72 L/F框架变形 L/Fmismatch73 数量不符 Quantity74 空粘未报废Empty M. not scrap75 金丝受损Gold wire scratch塑封 molding1 塑封 Molding2 塑封料 Moldingcompound5 塑封机Molding M/C ; mold press6 预热机 Pre-heater7 塑封模具 Molddie/chase8 单缸模具Mold9 MGP多缸模具 MGPmold10 自动包封机 Auto11 自动排片机Auto L/F loader12 冲浇口机?13 抓手(机械手) Handler14 点温计 Digimite15 料饼预热温度 Pre-heatTemperature 16 热电偶temperature17 模温 Mold18 预热台 Pre-heaterpressure19 合模压强 Clamppressure20 注塑压强 Transfertime21 固化时间 Curingtemperature22 固化温度 CuringTime23 (料饼)预热时间 Pre-heatspeed24 注塑速度 Transfertime25 注塑时间 Transfer26 后固化时间PMC time (Post Mold Cure Time)28 上料/下料 Load/unloadsweep29 冲丝 Wire30 开路 Open31 短路 Shortunderfilled32 胶体未灌满 Bodymold33 未封满 Incomplete34 崩角Chip package / body chip-out35 胶体麻点 PorosityBody/Blister36 表面气泡 Bubble37 粘污 Smearsurface38 不均匀(表面) Rough39 分层 DelaminatingV oid40 胶体空洞 PKGdeepscratch41 胶体刮痕 Body42 塑封体尺寸Mold PKG Dimension43 X-ray(冲丝和塌丝) X-ray(Wire Sweep & Sagging)44 背面宽/长BTM width / length45 正面宽/长Top width / lengththick46 塑封体厚度 PKG47 包封偏差(胶体错位) Mold Mismatch / PKG mismatch48 偏心(Mold) Offset / PKG misalignment49 后固化PMC(post mold cure)50 模次 Shotstripmolded51 空封 Dummyflash52 废胶 Mold53 注浇口、进浇口Gate (Mold gate) Injection gate54 小脚 GateremainAging 回温过程55 料饼醒料 Compoundblock56 定位块 Locatorpin57 顶针 EjectorDepth58 顶针深度 E-pin59 冷藏库\料饼存放库Cold room/Compound storagegun60 气枪 Air61 芯片涂胶 Diecoating62 芯片涂胶机Auto die coating M/C63 覆晶胶Die coating material64 后站推车ASS’Y B CartTabletLoader65 自动排胶粒机 AutoPreheater66 高频预热机 Compound67 上料架Load / Unload FixtureMagazine68 胶粒盒 Tablet69 塑封料饼 CompoundTablets70 洗模饼Mold Cleaning CompoundMisorientation71 胶体压反 PKG72 塑封溢胶Mold flash on leadcrack73 胶体裂痕 Mold切筋Trim-FormDambarcut 1 切筋 Trimmingdie2 切筋模 Trimdie3 成形模 Form4 分离模singulate5 冲废 De-junk外观检6 检测 InspectionDie7 再成型机模具 Reformsystem8 再成型机 Reformtray9 料盘 Plasticdambar10 连筋 Uncut11 毛刺 burr14 溢料 Junk15 裂纹 Crack16 离层(分层) Delaminating17 管脚反翘 Leadbendtipuncut18 筋未切 Dam-bar19 筋凸出 Dam-barprotrusion20 筋切入Dam-bar cut in打印Marking1 打印 Marking2 印章Marking layout3 激光打印 Lasermarkingmarking(UV)4 油墨打印 Ink5 正印Top side mark6 背印Back side mark7 镜头 Lens8 打印不良\模糊 Illegiblemarkingmarking9 漏打 No10 断字 Brokencharactercharacter11 缺字 Missingmarking12 印字倾斜 Slantmarking13 印记错误 Wrong14 重印 Remark15 印字模糊(褪色) Fademark16 印字粘污 Smear19 电流 current 21 字体(字形) Fontpin22 定位针 Locationprinter23 胶皮打印机 Pad24 激光打印机Laser Marking M/C25 后固化PMC(Post Mold Cure)26 后固化烤箱 PMCOvenstain27 打印污斑 Markingshift28 印记移位 Marking电镀Plating1 电镀 Plating2 来料 Incoming3 冲废 Dejunk4 热煮软化槽 SockingTank7 检验 Inspection外观检8 烘烤 CuringBaking150℃; 60-90ms/9 出料 Unload10 高速线电镀High-speed Plating Line11 统计过程控制 SPC12 搭锡 Solderbridge13 锡丝、锡须Solder flick / Whiskerdefects14 镀层不良 Plating15 发黄 Yellowish16 发黑 Blacken17 变色 Discolor18 露底材(露铜) Exposecopper19 粘污 Smear7-20um 20 镀层厚度 Platingthickness电镀成分, Sn21 镀层成分 Platingcomposition22 外观 Outgoingability23 易焊性 Solder24 无铅化Pb-free / lead freeforce25 结合力 Adhesive26 可靠性 Reliabilitydeflash27 电解 Electrolyticwater28 清洗(自来水) City29 高压清洗High pressure rinse30 脱脂 Descalewater31 清洗(纯水) DI32 活化(合金) Activation33 预镀、预浸 Pre-dip34 电镀 Plating35 吹风 Airblow36 中和 Neutralization37 褪镀 Stripper38 拖出 Dragout39 上料机 Loader40 下料机 Unloader41 纯锡 Tinwater42 纯水(去离子水) DIpressure43 水压 Water44 理化分析Physical and chemical analysisThicknessMeter45 测厚仪 Plating/ Electroplated CoatingThickness Test46 离子污染度测试仪Ion Contamination Tester Contamino CT100Tester47 C含量测试仪 Carbon51 去氧化 HSCUDescale52 预浸 Pre-dip53 电镀电流 Current54 镀液温度 Temperature 电镀液platingsolution电镀槽 plating tank56 中和 Neutralization59 烘干 Curingball60 锡球 Solder61 锡厚度和成分Sn thickness & composition62 冲废 De-junk 去胶渣63 去溢料 Degate 冲塑,冲胶64 去飞边 Deflash 去胶(塑封工序)65 锡铅电镀Tin lead plating66 无铅电镀Lead free plating; Pure tinplatingbump67 镀层起泡 Solder68 镀层剥落Solder peel off69 镀层偏厚或偏薄Thick or Thin Platingremove70 退锡 Solder71 电镀报废 Platingscrappeeling72 锡渣 Solderbump73 电镀锡块 Solderbridge74 电镀桥接 PlatingDiscoloration75 电镀变色 SPContamination76 电镀污染 SP77 电镀锡攀爬 SPadhere78 电解除油 Electro-degreasing测试Testing1 测试 Testingmark2 打印 Laser3 编带机Tape & Reel Machine4 编带 Reel5 测试机 TesterHandlerTest6 分选机 Tray11 振动盘Bowl ?vision12 Vision检测 Direction15 划伤 Scratchmark16 打错 Wrongcharacter17 断字 Broken18 漏字 Nomarkingmark19 模糊 Fadelength20 脚长 Leadwidth21 脚宽 Leadup22 站立度 Standpitch23 脚间距 Lead24 共面性 Coplanarityspace25 跨度 Row27 电性能测试 Electricaltesttube28 塑料管 Plastic/Tape29 编带 Reel30 托盘,盘装 TrayScan/Inspection31 扫描测脚 Leadsscanner 32 扫描测脚机 LeadsProjector33 投影仪 Profile切筋Trimming1 切筋 Trimmingdie2 切筋模 Trimdie3 成形入管模 Form4 定位 Location6 封塞(软塞) Plug8 支持棒 Suspensionbarbar/Fishtail/Tiepress10 切筋打弯机 TrimLoader11 上料匣 Framepress12 压模机 Mold14 共面性不良Poor LDS Coplanarity15 缺损/缺角 Crackformingorientation16 反切 Wrong17 擦伤/划伤 Scratchlead18 弯脚 Bentlead19 长短脚 Unevenflash20 废胶 Mold21 切偏dambar22 连筋 Uncut23 分离 Singulationscratches24 管脚刮伤 Leadpackage25 裂缝、胶体破裂 Crackcrack26 微裂缝 Micro27切割 Sawing1 切割 Sawing2 切割分离系统Sawing & Placement System/ Singulation3 磨边 Perimeter4 偏差 Offset5 划伤 Scratch6 划痕 Residuecharactermark7 打错位 Wrongposition8 毛刺 Burr9 崩角、缺角Chip package / Chipping10 共面性不良Poor LDS Coplanaritytype11 冲压式 Punch12 切割式Saw type / Singulation Type13 刀片高度 Heightspeed15 进刀速度 Feedpressure16 清洗水压力 Cleantime17 清洗时间 Clean18 纯水电阻率DI water resistivitytemperature19 烘干温度 Curingtime 20 烘干时间 Curingtemperature21 切割水温度 Sawingwaterflowmeter22 去离子水流量 DI。
晶圆减薄工艺
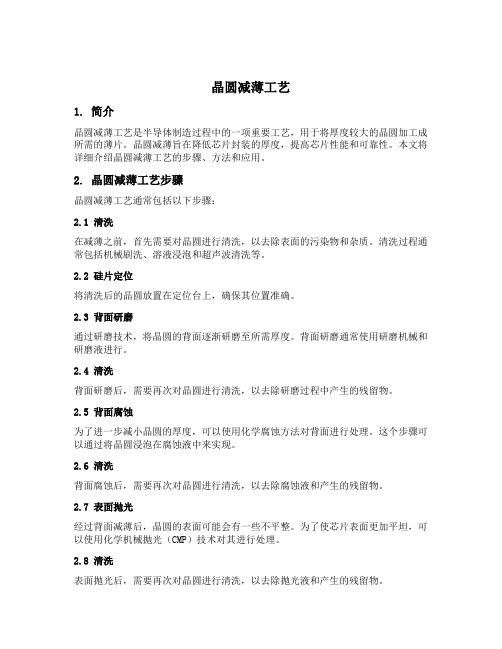
晶圆减薄工艺1. 简介晶圆减薄工艺是半导体制造过程中的一项重要工艺,用于将厚度较大的晶圆加工成所需的薄片。
晶圆减薄旨在降低芯片封装的厚度,提高芯片性能和可靠性。
本文将详细介绍晶圆减薄工艺的步骤、方法和应用。
2. 晶圆减薄工艺步骤晶圆减薄工艺通常包括以下步骤:2.1 清洗在减薄之前,首先需要对晶圆进行清洗,以去除表面的污染物和杂质。
清洗过程通常包括机械刷洗、溶液浸泡和超声波清洗等。
2.2 硅片定位将清洗后的晶圆放置在定位台上,确保其位置准确。
2.3 背面研磨通过研磨技术,将晶圆的背面逐渐研磨至所需厚度。
背面研磨通常使用研磨机械和研磨液进行。
2.4 清洗背面研磨后,需要再次对晶圆进行清洗,以去除研磨过程中产生的残留物。
2.5 背面腐蚀为了进一步减小晶圆的厚度,可以使用化学腐蚀方法对背面进行处理。
这个步骤可以通过将晶圆浸泡在腐蚀液中来实现。
2.6 清洗背面腐蚀后,需要再次对晶圆进行清洗,以去除腐蚀液和产生的残留物。
2.7 表面抛光经过背面减薄后,晶圆的表面可能会有一些不平整。
为了使芯片表面更加平坦,可以使用化学机械抛光(CMP)技术对其进行处理。
2.8 清洗表面抛光后,需要再次对晶圆进行清洗,以去除抛光液和产生的残留物。
3. 晶圆减薄工艺方法晶圆减薄工艺有多种方法可供选择,常见的方法包括:3.1 机械研磨机械研磨是晶圆减薄的一种常用方法。
通过使用磨料和研磨机械,可以逐渐去除晶圆的背面材料,从而实现减薄的目的。
3.2 化学机械抛光化学机械抛光(CMP)结合了化学腐蚀和机械研磨的特点,能够更加精确地控制减薄过程。
通过在抛光液中加入硬颗粒,可以实现对晶圆表面材料的去除和平整。
3.3 激光剥离激光剥离是一种非接触式减薄方法,通过使用激光束对晶圆进行加工。
激光能量可以选择性地去除晶圆背面的材料,并且可以实现高精度和高效率。
4. 晶圆减薄工艺应用晶圆减薄工艺广泛应用于半导体制造和封装领域。
其主要应用包括:4.1 芯片封装晶圆减薄使得芯片变得更薄,从而方便后续的封装工艺。
超薄晶圆减薄工艺研究
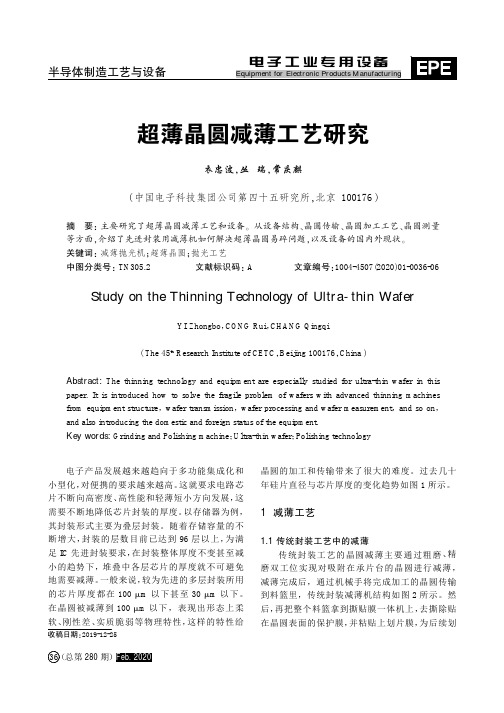
粗磨 精磨
承片台
图 4 带划片膜的晶圆
1.1.1 晶圆表面损伤 为了保证减薄机的加工精度和效率,通常选用
金刚石磨粒较大的磨轮进行粗磨,磨粒直径通常大 小在 40~50 滋m 之间;为了控制磨削表面的划痕 深度和损伤层深度,精磨通常采用精磨磨粒直径大 小在 4~8 滋m 之间的磨轮,精磨完成后,晶圆表面 虽然存在一定的微裂纹,晶圆表面粗糙度可以达到 0.02 滋m 左右,厚度可以达到 150 滋m 以下。由于 残余应力的影响,这种厚度的晶圆传输极为困难。
薄自身的挑战外,后续工艺晶圆的传输、搬运也遇 到了很大的问题。尤其在目前先进封装领域,晶圆 直径已经发展到 300 mm。这种大尺寸超薄晶圆即 使通过应力消除减少了翘曲度,仍然表现出形态 上柔软、刚性差,实质脆弱等物理特性,超薄晶圆 的柔软性和通透性如图 8、图 9 所示。晶圆在自身 重力作用下产生弯曲变形,这种晶圆的搬运会因 空气阻力产生断裂破碎现象。从以下 5 个方面介 绍先进封装的减薄工艺[2]。
YI Zhongbo,CONG Rui,CHANG Qingqi
( The 45th Research Institute of CETC,Beijing 100176,China )
Abstract: The thinning technology and equipment are especially studied for ultra-thin wafer in this paper. It is introduced how to solve the fragile problem of wafers with advanced thinning machines from equipment structure,wafer transmission,wafer processing and wafer measurement,and so on, and also introducing the domestic and foreign status of the equipment. Key words: Grinding and Polishing machine;Ultra-thin wafer;Polishing technology
晶圆减薄工艺

晶圆减薄工艺概述晶圆减薄工艺是集成电路制造流程中的一个重要环节。
通过减薄晶圆,可以降低芯片厚度,提高芯片的性能和可靠性。
本文将详细介绍晶圆减薄工艺的原理、步骤和应用。
原理晶圆减薄工艺的原理是通过机械或化学方法将晶圆的厚度减薄至目标值。
常用的减薄方法包括机械研磨、化学机械研磨和激光磨削。
机械研磨机械研磨是最早应用的晶圆减薄方法之一。
它通过在研磨盘上使用研磨液和研磨颗粒对晶圆进行研磨,从而减小晶圆的厚度。
机械研磨的优点是工艺简单、成本低,但是容易引入研磨损伤和晶圆表面不平整问题。
化学机械研磨化学机械研磨是一种结合了化学腐蚀和机械研磨的方法。
它通过在研磨液中加入化学溶液和研磨颗粒,同时进行机械研磨和化学腐蚀,从而实现高效的晶圆减薄。
化学机械研磨可以减小研磨损伤和晶圆表面不平整问题,但是其研磨液的配方和工艺参数需要进行精确控制。
激光磨削激光磨削是一种非接触的减薄方法,它利用激光束的加热和蒸发作用,将晶圆表面的材料蒸发掉,从而减小晶圆的厚度。
激光磨削具有减小研磨损伤和晶圆表面不平整问题的优点,但是需要精确控制激光参数和扫描路径。
步骤晶圆减薄工艺通常包括以下步骤:去背面设备准备在晶圆减薄前,需要对去背面设备进行准备工作。
这包括校准设备、清理器具、检查设备状态等。
粗磨粗磨是晶圆减薄的第一步,旨在快速减小晶圆的厚度。
通常使用机械研磨方法进行粗磨,选择合适的研磨颗粒和磨剂,控制研磨力和速度,使晶圆表面平整度达到要求。
中磨中磨是对粗磨后的晶圆进行进一步的减薄和平整处理。
常用的方法是化学机械研磨,通过调整化学研磨液的配方和工艺参数,控制研磨颗粒和化学反应,使晶圆表面更为平整。
精磨精磨是对中磨后的晶圆进行最后的减薄和平整处理。
常用的方法包括化学机械研磨和激光磨削。
通过精确调整研磨液的配方和工艺参数,控制研磨颗粒和化学反应的微观作用,使晶圆获得所需的薄度和表面光洁度。
清洗和检测减薄后的晶圆需要进行清洗和检测工作,以去除研磨残留物和检查减薄效果。
晶圆背面减薄的标准-概述说明以及解释

晶圆背面减薄的标准-概述说明以及解释1.引言1.1 概述:晶圆背面减薄是半导体制造过程中的关键步骤之一,它通过精密的切割工艺将晶圆背面的厚度减少到所需的尺寸。
这一步骤在集成电路、光电子器件等领域中广泛应用,其减薄的标准直接影响到产品的质量和性能。
本文将重点介绍晶圆背面减薄的标准,包括减薄的重要性、减薄的方法和标准,以及减薄对晶圆质量和性能的影响。
通过深入探讨这些内容,读者将更好地了解晶圆背面减薄的意义和必要性,进而为相关领域的研究和生产提供参考。
1.2 文章结构文章结构部分介绍了本文的整体结构和组成部分。
本文分为引言、正文和结论三个部分。
引言部分包括概述、文章结构和目的三个小节,主要是对本文的主题进行简要介绍和阐述,说明文章的意义和重要性。
正文部分分为三小节,分别是晶圆背面减薄的重要性、减薄的方法和标准以及减薄对晶圆质量和性能的影响。
在这部分,将对晶圆背面减薄的相关知识和技术进行全面的阐述和分析。
结论部分包括总结、展望和结论三个小节,对本文的主要内容进行总结和归纳,并展望未来可能的发展方向和趋势,最终给出本文的结论和观点。
通过以上文章结构的设计,读者可以清晰地了解本文的内容与组织,便于阅读和理解。
1.3 目的本文的主要目的是探讨晶圆背面减薄的标准,并分析减薄对晶圆质量和性能的影响。
通过对减薄方法和标准的研究,我们希望能够为晶圆制造行业提供一套科学的减薄标准,帮助生产厂家更好地控制晶圆背面减薄的过程,保证产品质量和性能的稳定和可靠性。
同时,通过深入分析减薄对晶圆质量和性能的影响,我们也可以为后续研究和实践提供参考,推动晶圆制造技术的进步和发展。
2.正文2.1 晶圆背面减薄的重要性晶圆背面减薄在半导体制造过程中扮演着至关重要的角色。
晶圆背面减薄的主要目的是为了减小晶圆的厚度,以便在接下来的工艺步骤中更加灵活地处理晶圆。
通过减薄晶圆背面,可以降低晶圆的重量和厚度,从而提高晶圆的热传导性能和处理效率。
另外,晶圆背面减薄还可以减少晶圆之间的热阻,提高散热效果,从而可以更好地保护晶圆内部的电路元件不受过热的影响。
晶圆减薄工艺与基本原理

晶圆减薄工艺与基本原理展开全文1 减薄的目的直径150mm(6寸)和200mm(8寸)的晶圆厚度分别为625um和725um,而直径为300mm硅片平均厚度达到775um。
在晶圆中总厚度90%以上的衬底材料是为了保证晶圆在制造,测试和运送过程中有足够的强度。
晶圆减薄工艺的作用是对已完成功能的晶圆(主要是硅晶片)的背面基体材料进行磨削,去掉一定厚度的材料。
有利于后续封装工艺的要求以及芯片的物理强度,散热性和尺寸要求晶圆减薄后对芯片有以下优点1)散热效率显著提高,随着芯片结构越来越复杂,集成度越来越高,晶体管数量急剧增加,散热已逐渐称为影响芯片性能和寿命的关键因素。
薄的芯片更有利于热量从衬底导出。
2)减小芯片封装体积。
微电子产品日益向轻薄短小的方向发展,厚度的减小也相应地减小了芯片体积。
3)减少芯片内部应力。
芯片厚度越厚芯片工作过程中由于热量的产生,使得芯片背面产生内应力。
芯片热量升高,基体层之间的热差异性加剧,加大了芯片内应力,较大的内应力使芯片产生破裂。
4)提高电气性能。
晶圆厚度越薄背面镀金使地平面越近,器件高频性能越好。
5)提高划片加工成品率。
减薄硅片可以减轻封装划片时的加工量,避免划片中产生崩边、崩角等缺陷,降低芯片破损概率等。
2 减薄的工艺流程3 减薄的原理国际当前主流晶圆减薄机的整体技术采用了In-Feed磨削原理设计。
该技术基本原理是,采用了晶圆自旋,磨轮系统以极低速进给方式磨削。
如图1图 1 Schematic of self-rotating grinding mechanism: (a)Experimental set up of wafer grinding; (b) Illustration of the rotating waferand wheel具体步骤是把所要加工的晶圆粘接到减薄膜上,然后把减薄膜及上面芯片利用真空吸附到多孔陶瓷承片台上,杯形金刚石砂轮工作面的内外圆舟中线调整到硅片的中心位置,硅片和砂轮绕各自的轴线回转,进行切进磨削。
碳化硅晶圆减薄砂轮及制备方法及包含其的加工设备与流程
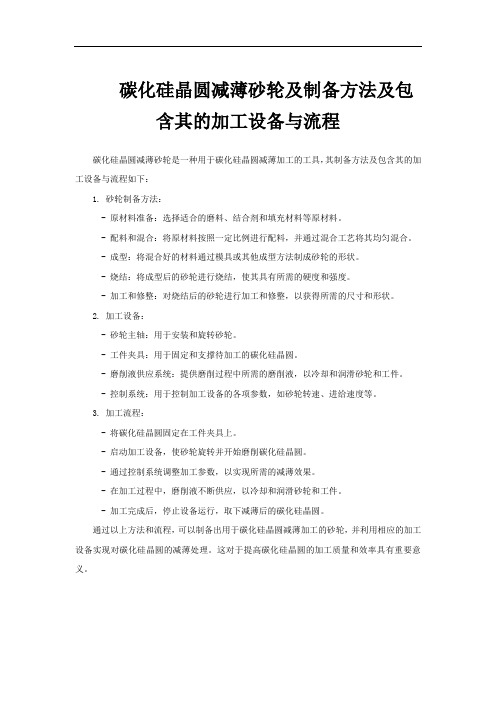
碳化硅晶圆减薄砂轮及制备方法及包
含其的加工设备与流程
碳化硅晶圆减薄砂轮是一种用于碳化硅晶圆减薄加工的工具,其制备方法及包含其的加工设备与流程如下:
1. 砂轮制备方法:
- 原材料准备:选择适合的磨料、结合剂和填充材料等原材料。
- 配料和混合:将原材料按照一定比例进行配料,并通过混合工艺将其均匀混合。
- 成型:将混合好的材料通过模具或其他成型方法制成砂轮的形状。
- 烧结:将成型后的砂轮进行烧结,使其具有所需的硬度和强度。
- 加工和修整:对烧结后的砂轮进行加工和修整,以获得所需的尺寸和形状。
2. 加工设备:
- 砂轮主轴:用于安装和旋转砂轮。
- 工件夹具:用于固定和支撑待加工的碳化硅晶圆。
- 磨削液供应系统:提供磨削过程中所需的磨削液,以冷却和润滑砂轮和工件。
- 控制系统:用于控制加工设备的各项参数,如砂轮转速、进给速度等。
3. 加工流程:
- 将碳化硅晶圆固定在工件夹具上。
- 启动加工设备,使砂轮旋转并开始磨削碳化硅晶圆。
- 通过控制系统调整加工参数,以实现所需的减薄效果。
- 在加工过程中,磨削液不断供应,以冷却和润滑砂轮和工件。
- 加工完成后,停止设备运行,取下减薄后的碳化硅晶圆。
通过以上方法和流程,可以制备出用于碳化硅晶圆减薄加工的砂轮,并利用相应的加工设备实现对碳化硅晶圆的减薄处理。
这对于提高碳化硅晶圆的加工质量和效率具有重要意义。
- 1、下载文档前请自行甄别文档内容的完整性,平台不提供额外的编辑、内容补充、找答案等附加服务。
- 2、"仅部分预览"的文档,不可在线预览部分如存在完整性等问题,可反馈申请退款(可完整预览的文档不适用该条件!)。
- 3、如文档侵犯您的权益,请联系客服反馈,我们会尽快为您处理(人工客服工作时间:9:00-18:30)。
Flip Chip
Wafer Test
Wafer Mount
Dicing
Die Attach
Wirebond
Encapsulation
Profile of Typical Silicon Wafer
Left side of this wafer was ground.
Grinding Wafers with Bevel
Sam Kao PhD – Tru-Si
Outline
• Introduction • Where does B/G fit in • Why do it • What are some typical problems encountered
• Objective of Presentation • Experimental method
Objective
Evaluate effect of grinding wheel specification on 8” thin wafers for optimum tool selection
> Effectቤተ መጻሕፍቲ ባይዱof grit size and grade ( wheel hardness) on thin wafer
- Wafers were de-taped manually
- Surface finish (Ra, Rt), Wafer Bow and Strength measured
- Chipping was classified as per number and size of chips using a microscope
• Machine used to grind, Wheels used to grind, metrology • equipment,recipe used • Experimental Results 5. Conclusions
Wafer Fabs Work Flow
Wafer Manufacturing
CAD Drawings illustrate the effect of the bevel on grinding thin wafers.
Bevel Full Radius
Thin Wafer with Bevel and Device
1 in
1 in = 200 µm
Device
Close Up of Thin Wafer With Bevel
x = Total Wafer Thickness-Circuitry Thickness y = Function (x)
x
Very Thin
y
0.25 in.
1 in = 200 µm
Thin Wafer Grinding
• Thinner wafers do not have the inherent mass to resist bending stresses due to
• Close up shows that the tip of the thin wafer is very thin. • The thin tip leads to chipping around the edge of the wafer. • The damage propagates around wafer and further into wafer.
> Clean edges : NC (No Chippage at all) > Rough edge with no visible chippage : RE ( Rough Edge) > One chip within 1 x 1 mm : MC (Medium chippage) > More than one chip or one chip bigger than 1 x 1 mm : LC (Large chippage)
Recent Developments in Thin wafer grinding – An Application Review
Thomas Puthanangady, Rama Vedantham, J Ikeda PhD. Saint Gobain Abrasives-Norton
Sal Kassir – Strasbaugh
Grinding Process Demonstration – Equipment used for Tests
Epitaxy
Backgrinding
Back-end
RTP
Ion Implant
Deposition
CMP
SEM Inspect
Spin On
Mask
Etching
Photo
Lithography
Thin Wafer Processing
handling
Back Grind
De Tape
Etch
- Test wheels used to grind 25 nos of 8” wafers each to 125 um thickness on the Strasbaugh 7AF grinder
- The force during grinding, cycle time and the wheel wear rates were monitored.
• Surface stresses • Wafer strength • Surface Roughness characteristics
Final wafer thickness : 125 um
Test Methodoloy
- 8” wafers manually taped using a vacuum chuck
• Gravity • Residual grinding/ machining stresses • This results in Bow and Warp • Creates handling issues and may ultimately result in wafer breakage •This effect is more pronounced in 200mm and larger wafers