宣钢生产大方坯品种钢的连铸工艺实
连铸生产工艺流程
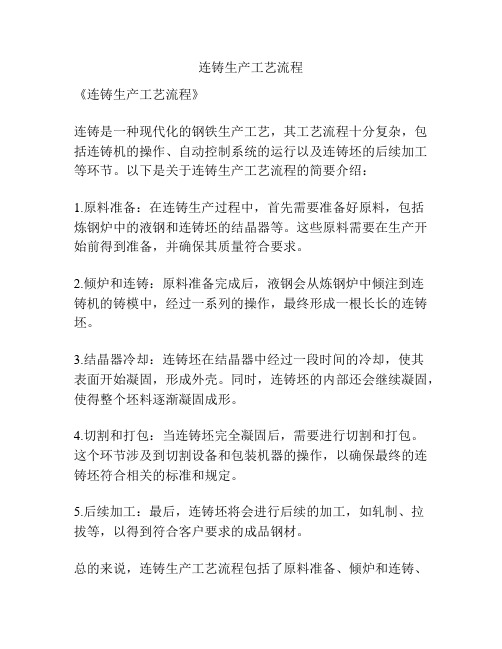
连铸生产工艺流程
《连铸生产工艺流程》
连铸是一种现代化的钢铁生产工艺,其工艺流程十分复杂,包括连铸机的操作、自动控制系统的运行以及连铸坯的后续加工等环节。
以下是关于连铸生产工艺流程的简要介绍:
1.原料准备:在连铸生产过程中,首先需要准备好原料,包括
炼钢炉中的液钢和连铸坯的结晶器等。
这些原料需要在生产开始前得到准备,并确保其质量符合要求。
2.倾炉和连铸:原料准备完成后,液钢会从炼钢炉中倾注到连
铸机的铸模中,经过一系列的操作,最终形成一根长长的连铸坯。
3.结晶器冷却:连铸坯在结晶器中经过一段时间的冷却,使其
表面开始凝固,形成外壳。
同时,连铸坯的内部还会继续凝固,使得整个坯料逐渐凝固成形。
4.切割和打包:当连铸坯完全凝固后,需要进行切割和打包。
这个环节涉及到切割设备和包装机器的操作,以确保最终的连铸坯符合相关的标准和规定。
5.后续加工:最后,连铸坯将会进行后续的加工,如轧制、拉
拔等,以得到符合客户要求的成品钢材。
总的来说,连铸生产工艺流程包括了原料准备、倾炉和连铸、
结晶器冷却、切割和打包以及后续加工等几个主要环节。
通过这些操作,连铸生产工艺可以实现高效、自动化的生产,为钢铁行业的发展做出了重要贡献。
方坯连铸技术操作规程(2010A)
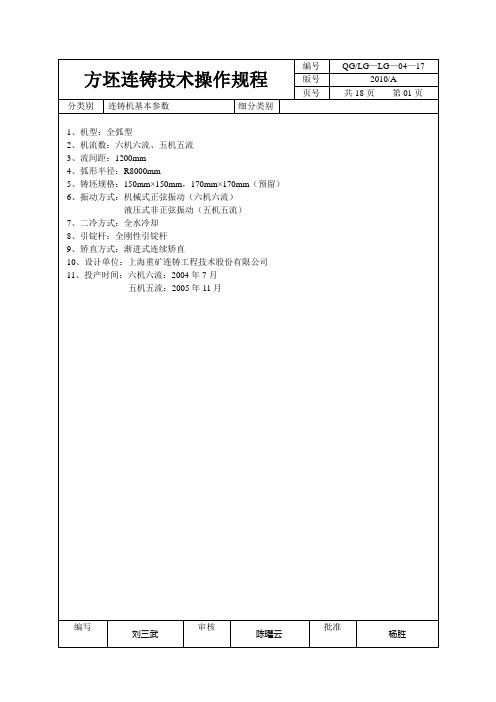
大包工
大包工
大包工
钢包处于正常浇注时,对回动台进行转动调整只能采用点动操作,严禁操作转动选择开关。
回转台的液动操作一般只在电动操作方式失效时才使用,禁止两种操作同时进行。
7、取下油缸和风冷插管,操作回转台将空钢包转至吊运位。
8、操作下一炉大包开浇,或停机操作。
大包工
浇钢班长
机长
大包工
电动和手动不可同时操作。
中间包开浇第一炉,必须得到机长的通知后大包才能开浇。
编写
刘三武
审核
陈曜云
批准
杨胜
方坯连铸技术操作规程
编号
QG/LG—LG—04—17
版号
2010/A
页号
共18页第05页
浇钢工
主控工
浇钢工
主控工
编写
刘三武
审核
陈曜云
批准
杨胜
方坯连铸技术操作规程
编号
QG/LG—LG—04—17
版号
2010/A
页号
共18页第09页
分类别
浇铸准备操作
细分类别
结晶器点检及安装
使用工具:大板手,钢钎,呆板手,手电筒
操作顺序
操作者
特别注意事项
1、结晶器本体点检
1.1结晶器安装前,先检查足辊喷淋架堵头、喷嘴(型号3/4”PZ11167Q2)是否松动,再随机拆取3~5个喷嘴检查是否堵塞。
分类别
中间包测温、排渣操作规程
细分类别
使用工具:测温枪,热电偶,引流管,氧气皮管
(工艺流程)炼钢连铸工艺流程介绍

连铸工艺流程介绍将高温钢水浇注到一个个的钢锭模内,而是将高温钢水连续不断地浇到一个或几个用强制水冷带有“活底”(叫引锭头)的铜模内(叫结晶器),钢水很快与“活底”凝结在一起,待钢水凝固成一定厚度的坯壳后,就从铜模的下端拉出“活底”,这样已凝固成一定厚度的铸坯就会连续地从水冷结晶器内被拉出来,在二次冷却区继续喷水冷却。
带有液芯的铸坯,一边走一边凝固,直到完全凝固。
待铸坯完全凝固后,用氧气切割机或剪切机把铸坯切成一定尺寸的钢坯。
这种把高温钢水直接浇注成钢坯的新工艺,就叫连续铸钢。
【导读】:转炉生产出来的钢水经过精炼炉精炼以后,需要将钢水铸造成不同类型、不同规格的钢坯。
连铸工段就是将精炼后的钢水连续铸造成钢坯的生产工序,主要设备包括回转台、中间包,结晶器、拉矫机等。
本专题将详细介绍转炉(以及电炉)炼钢生产的工艺流程,主要工艺设备的工作原理以及控制要求等信息。
由于时间的仓促和编辑水平有限,专题中难免出现遗漏或错误的地方,欢迎大家补充指正。
连铸的目的: 将钢水铸造成钢坯。
将装有精炼好钢水的钢包运至回转台,回转台转动到浇注位置后,将钢水注入中间包,中间包再由水口将钢水分配到各个结晶器中去。
结晶器是连铸机的核心设备之一,它使铸件成形并迅速凝固结晶。
拉矫机与结晶振动装置共同作用,将结晶器内的铸件拉出,经冷却、电磁搅拌后,切割成一定长度的板坯。
连铸钢水的准备一、连铸钢水的温度要求:钢水温度过高的危害:①出结晶器坯壳薄,容易漏钢;②耐火材料侵蚀加快,易导致铸流失控,降低浇铸安全性;③增加非金属夹杂,影响板坯内在质量;④铸坯柱状晶发达;⑤中心偏析加重,易产生中心线裂纹。
钢水温度过低的危害:①容易发生水口堵塞,浇铸中断;②连铸表面容易产生结疱、夹渣、裂纹等缺陷;③非金属夹杂不易上浮,影响铸坯内在质量。
二、钢水在钢包中的温度控制:根据冶炼钢种严格控制出钢温度,使其在较窄的范围内变化;其次,要最大限度地减少从出钢、钢包中、钢包运送途中及进入中间包的整个过程中的温降。
品种钢优特钢连铸工艺技术

品种钢优特钢连铸工艺技术l 特殊钢连铸有什么特点?与普通钢连铸相比,特殊钢连铸具有以下特点:(1)特殊钢的合金元素较多,含量较高,碳含量范围大(0.02%~2.3%C),受合金元素影响,其凝固特性与普通碳素钢差异大。
(2)特殊钢的纯洁度、均匀性、气体含量、低倍组织、夹杂物形态等要求比普通碳素钢高。
(3)有些特殊钢含Cr、V、Ti、Nb、Al等活泼元素,极易与氧、氮反应生成高熔点化合物,给铸坯质量带来一定危害;还有些合金元素则与钢中碳生成碳化物或碳氮化物,容易产生高温固相析出,对钢的热塑性有重要影响。
(4)由于连铸过程的特殊冷却凝固条件,成分偏析和组织不均匀性更为突出。
2 针对特殊钢凝固的特点,特殊钢连铸需解决的关键技术问题有哪些?(1)提高钢液洁净度提高钢液洁净度的主要措施有:1)低铝洁净钢技术,通过采用非铝脱氧剂,在降低钢中残铝和氧化物夹杂中A1203比例的前提下,使钢中氧含量比传统铝脱氧显著降低;2)钢包软吹氩技术;3)钢包下渣自动检测及控制技术;4)中间包冶金技术;5)中间包和结晶器保护渣的优化;6)结晶器冶金技术。
(2)提高铸坯质量铸坯质量的提高主要依赖于连铸装备和工艺的优化,就我国目前现有装备而言,提高特殊钢铸坯质量的主要措施是采取低过热度浇铸与电磁搅拌相结合的办法来扩大等轴晶区,减轻偏析和疏松的集中度。
同时根据不同钢种的特点选择合适的保护渣、结晶器设计与冷却、二冷和拉坯制度,以防止裂纹等缺陷的产生。
为进一步提高铸坯质量,近年出现了一些新的技术:1)浇铸过程液面自动控制;2)结晶器和凝固末段电磁搅拌工艺优化;3)大方坯轻压下技术;4)利用外场或形核剂细化铸态组织技术;5)复式结晶器控制凝固组织技术;6)结晶器钢液流动控制技术等。
3 目前我国使用的中间包,尤其是方坯连铸机使用的中间包存在的突出问题表现在哪些方面?目前我国使用的中间包存在较多的问题,尤其是方坯连铸机用的中间包存在的问题更为突出。
大方坯品种钢连铸工艺实践

总第188期2011年第8期HEBEI M ETALLU R GYTotal 1882011,N umber 8收稿日期:2011-06-26作者简介:刘永军(1973-),男,工程师,2005年毕业于河北理工大学钢铁冶金专业,现在河北钢铁集团宣钢公司炼钢厂工作,E -mail.:xgliuyongjun@yahoo.cn大方坯品种钢连铸工艺实践刘永军,席玉军,郝忠,张国荣,杨春江(河北钢铁集团宣钢公司炼钢厂,河北宣化075100)摘要:介绍了宣钢6#连铸机为满足大方坯品种钢生产需要进行的设备改造及工艺优化,改进后6#连铸机由原来只生产普钢变为普钢与优质钢均能生产,铸坯质量得到改善,热顶锻合格率99.8%,低位合格率99.6%,达到了同类铸机先进水平。
关键词:连铸机:大方坯;品种钢;质量中图分类号:TF777.2文献标识码:B文章编号:1006-5008(2011)08-0058-03PRACTICE OF CONTINUOUS CASTINGOF LARGE -SCALE SQUARE BILLET OF GRADE STEELLiu Yongjun ,Xi Yujun ,Hao Zhong ,Zhang Guorong ,Yang Chunjiang(Steelworks ,Xuanhua Iron and Steel Company ,Hebei Iron and Steel Group ,Xuanhua ,Hebei ,075100)Abstract :It is introduced the equipment reformation and process optimization in 6#caster of Xuan Steel to meet demand for large square billet of grade steel.After that both normal and qualified steel can be pro-duced ,casting billet's quality improved.Key Words :caster ;large square billet ;grade steel ;quality1前言宣钢炼钢厂于2006年10月份投产了120t 转炉精炼炉—130t LF —12流方坯连铸机生产线,以生产普钢为主。
连铸生产工艺流程
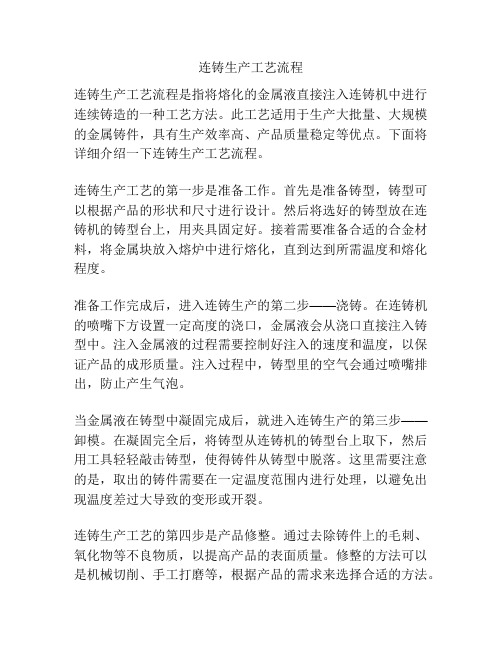
连铸生产工艺流程连铸生产工艺流程是指将熔化的金属液直接注入连铸机中进行连续铸造的一种工艺方法。
此工艺适用于生产大批量、大规模的金属铸件,具有生产效率高、产品质量稳定等优点。
下面将详细介绍一下连铸生产工艺流程。
连铸生产工艺的第一步是准备工作。
首先是准备铸型,铸型可以根据产品的形状和尺寸进行设计。
然后将选好的铸型放在连铸机的铸型台上,用夹具固定好。
接着需要准备合适的合金材料,将金属块放入熔炉中进行熔化,直到达到所需温度和熔化程度。
准备工作完成后,进入连铸生产的第二步——浇铸。
在连铸机的喷嘴下方设置一定高度的浇口,金属液会从浇口直接注入铸型中。
注入金属液的过程需要控制好注入的速度和温度,以保证产品的成形质量。
注入过程中,铸型里的空气会通过喷嘴排出,防止产生气泡。
当金属液在铸型中凝固完成后,就进入连铸生产的第三步——卸模。
在凝固完全后,将铸型从连铸机的铸型台上取下,然后用工具轻轻敲击铸型,使得铸件从铸型中脱落。
这里需要注意的是,取出的铸件需要在一定温度范围内进行处理,以避免出现温度差过大导致的变形或开裂。
连铸生产工艺的第四步是产品修整。
通过去除铸件上的毛刺、氧化物等不良物质,以提高产品的表面质量。
修整的方法可以是机械切削、手工打磨等,根据产品的需求来选择合适的方法。
修整完成后,再次对产品进行目视或非破坏性检测,确认产品的质量问题。
最后一步是产品的后处理。
后处理的内容会根据具体的产品需求而有所不同,主要包括清洗、镀膜、热处理等。
清洗是为了去除表面的污垢和残留物,保持产品的干净和光亮。
镀膜是为了增加产品的耐腐蚀性能和美观度。
热处理是为了改变产品的性能和结构,使其满足特殊需求。
以上就是连铸生产工艺的主要流程。
通过这一工艺流程可以实现大规模、高效率的金属铸造。
当然,实际操作中还需要注意一些细节问题,比如对机器设备的维护保养、工作环境的整洁以及操作人员的技术培训等,以确保连铸生产工艺的稳定和可靠。
连铸坯生产工艺

连铸坯生产工艺连铸坯生产工艺是一种将炼钢后的金属浇铸成特定形状和尺寸的制钢工艺。
以下是连铸坯生产工艺的主要步骤:1.炼钢生产炼钢生产是连铸坯生产的第一步。
在这个过程中,铁水被加入到炼钢炉中,并加入碳和其他合金元素,以调整钢的化学成分。
炼钢过程中需要注意安全,避免高温和化学成分对工人健康的影响。
2.连铸浇铸连铸浇铸是将钢水连续地浇铸成特定形状和尺寸的工艺过程。
浇铸时,钢水通过钢包注入结晶器,在结晶器中冷却并形成一定形状的连铸坯。
这个过程中需要注意控制钢水的温度和流量,以保证连铸坯的质量。
3.冷却与切割连铸坯在浇铸完成后需要进行冷却和切割。
冷却过程中,连铸坯被送入冷却塔或水冷装置中,以去除热量并防止变形。
切割则是将连铸坯按照需要的长度和形状进行切割,以便后续加工。
这个过程中需要注意避免连铸坯变形和开裂。
4.矫直与弯曲矫直和弯曲是使连铸坯恢复到原来形状和尺寸的工艺过程。
矫直是将连铸坯的弯曲部分矫直,使其形状更加平整。
弯曲则是将矫直后的连铸坯按照需要的形状进行弯曲。
这个过程中需要注意控制机械力和温度,以避免对连铸坯造成损伤。
5.表面清理表面清理是去除连铸坯表面杂质和缺陷的工艺过程。
清理时可以采用机械方法或化学方法。
机械方法包括磨削、抛光、打毛等,可以去除表面粗糙、划痕等缺陷。
化学方法则是使用酸、碱等化学试剂,去除表面氧化皮、锈蚀等缺陷。
这个过程中需要注意保护工人健康,避免粉尘和化学试剂对环境的影响。
6.质量检测质量检测是确保连铸坯符合质量要求的工艺过程。
检测时可以采用各种仪器和设备,如超声波探伤、X射线探伤、磁粉探伤等,以检测连铸坯内部和表面的缺陷。
这个过程中需要注意控制检测精度和可靠性,以确保产品质量。
7.成品加工成品加工是将连铸坯加工成最终产品或半成品的工艺过程。
加工时可以采用各种机械加工方法和热处理方法,如车削、铣削、钻孔、热轧、冷拔等,以得到需要的形状和性能。
这个过程中需要注意提高加工效率和精度,降低成本。
炼钢厂连铸工艺流程

炼钢厂连铸工艺流程
《炼钢厂连铸工艺流程》
炼钢厂连铸工艺是现代炼钢工业中的重要环节,它是将炼钢炉中熔化的钢液通过连续铸造成坯料或板材的工艺过程。
下面将介绍炼钢厂连铸工艺的流程。
首先,炼钢厂连铸工艺流程开始于钢液的浇入。
炼钢炉中的钢液被加热至适宜温度后,通过喷嘴或水口将钢液浇入到连铸模具中。
模具是一个由水冷却的铜板制成的管道,其内部形状和尺寸将决定最终坯料或板材的形状和尺寸。
接着,钢液在模具中逐渐冷却凝固成坯料或板材。
冷却过程中,模具的水冷却系统将快速冷却钢液,使其凝固成坯料或板材。
在这个过程中,需要根据钢液的成分和温度来控制模具的冷却速度,以确保坯料或板材的质量。
最后,坯料或板材被切割至所需要的长度。
炼钢厂通常会根据客户的需求将坯料或板材切割至所需要的长度,以便进一步的加工或生产。
总的来说,炼钢厂连铸工艺流程是一个高效、精密的工艺过程,它使得炼钢厂能够生产高质量的钢材坯料和板材,为各种工业领域提供了重要的原材料支持。
炼钢厂连铸工艺操作流程
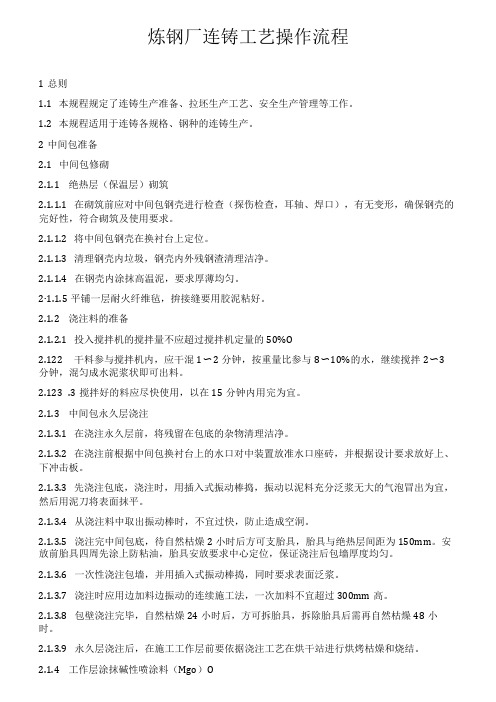
炼钢厂连铸工艺操作流程1总则1.1本规程规定了连铸生产准备、拉坯生产工艺、安全生产管理等工作。
1.2本规程适用于连铸各规格、钢种的连铸生产。
2中间包准备2.1中间包修砌2.1.1绝热层(保温层)砌筑2.1.1.1在砌筑前应对中间包钢壳进行检查(探伤检查,耳轴、焊口),有无变形,确保钢壳的完好性,符合砌筑及使用要求。
2.1.1.2将中间包钢壳在换衬台上定位。
2.1.1.3清理钢壳内垃圾,钢壳内外残钢渣清理洁净。
2.1.1.4在钢壳内涂抹高温泥,要求厚薄均匀。
2∙1.1.5平铺一层耐火纤维毡,拚接缝要用胶泥粘好。
2.1.2浇注料的准备2.1.2.1投入搅拌机的搅拌量不应超过搅拌机定量的50%O2.122干料参与搅拌机内,应干混1〜2分钟,按重量比参与8〜10%的水,继续搅拌2〜3分钟,混匀成水泥浆状即可出料。
2.123.3搅拌好的料应尽快使用,以在15分钟内用完为宜。
2.1.3中间包永久层浇注2.1.3.1在浇注永久层前,将残留在包底的杂物清理洁净。
2.1.3.2在浇注前根据中间包换衬台上的水口对中装置放准水口座砖,并根据设计要求放好上、下冲击板。
2.1.3.3先浇注包底,浇注时,用插入式振动棒捣,振动以泥料充分泛浆无大的气泡冒出为宜,然后用泥刀将表面抹平。
2.1.3.4从浇注料中取出振动棒时,不宜过快,防止造成空洞。
2.1.3.5浇注完中间包底,待自然枯燥2小时后方可支胎具,胎具与绝热层间距为150mm。
安放前胎具四周先涂上防粘油,胎具安放要求中心定位,保证浇注后包墙厚度均匀。
2.1.3.6一次性浇注包墙,并用插入式振动棒捣,同时要求表面泛浆。
2.1.3.7浇注时应用边加料边振动的连续施工法,一次加料不宜超过300mm高。
2.1.3.8包壁浇注完毕,自然枯燥24小时后,方可拆胎具,拆除胎具后需再自然枯燥48小时。
2.1.3.9永久层浇注后,在施工工作层前要依据浇注工艺在烘干站进行烘烤枯燥和烧结。
2.1.4工作层涂抹碱性喷涂料(Mgo)O1.1.1.1中间包内倒入干式料,用木板或其他工具刮平,厚度大于30mm,小于冲击板厚度20mm;在中间包烘烤器外表均匀涂一层石墨,将其放入中间包内,调整其位置,使其与冲击板下口吻合,并且与中间包四周的间距保持一致,大约30mm。
炼钢连铸工艺流程介绍
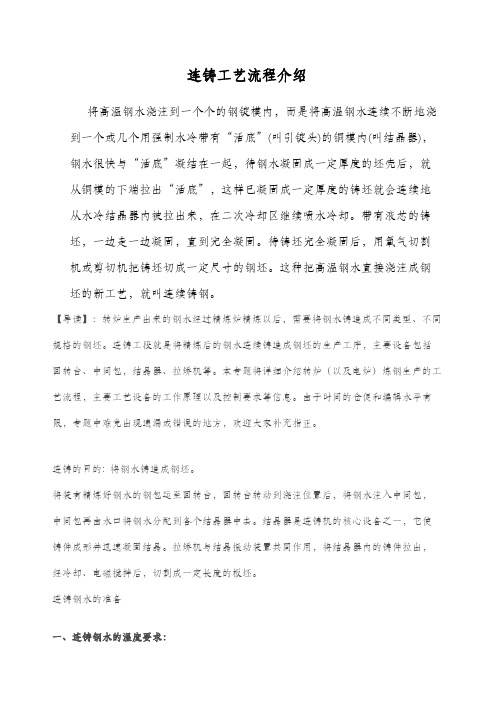
连铸工艺流程介绍将高温钢水浇注到一个个的钢锭模内,而是将高温钢水连续不断地浇到一个或几个用强制水冷带有“活底”(叫引锭头)的铜模内(叫结晶器),钢水很快与“活底”凝结在一起,待钢水凝固成一定厚度的坯壳后,就从铜模的下端拉出“活底”,这样已凝固成一定厚度的铸坯就会连续地从水冷结晶器内被拉出来,在二次冷却区继续喷水冷却。
带有液芯的铸坯,一边走一边凝固,直到完全凝固。
待铸坯完全凝固后,用氧气切割机或剪切机把铸坯切成一定尺寸的钢坯。
这种把高温钢水直接浇注成钢坯的新工艺,就叫连续铸钢。
【导读】:转炉生产出来的钢水经过精炼炉精炼以后,需要将钢水铸造成不同类型、不同规格的钢坯。
连铸工段就是将精炼后的钢水连续铸造成钢坯的生产工序,主要设备包括回转台、中间包,结晶器、拉矫机等。
本专题将详细介绍转炉(以及电炉)炼钢生产的工艺流程,主要工艺设备的工作原理以及控制要求等信息。
由于时间的仓促和编辑水平有限,专题中难免出现遗漏或错误的地方,欢迎大家补充指正。
连铸的目的: 将钢水铸造成钢坯。
将装有精炼好钢水的钢包运至回转台,回转台转动到浇注位置后,将钢水注入中间包,中间包再由水口将钢水分配到各个结晶器中去。
结晶器是连铸机的核心设备之一,它使铸件成形并迅速凝固结晶。
拉矫机与结晶振动装置共同作用,将结晶器内的铸件拉出,经冷却、电磁搅拌后,切割成一定长度的板坯。
连铸钢水的准备一、连铸钢水的温度要求:钢水温度过高的危害:①出结晶器坯壳薄,容易漏钢;②耐火材料侵蚀加快,易导致铸流失控,降低浇铸安全性;③增加非金属夹杂,影响板坯内在质量;④铸坯柱状晶发达;⑤中心偏析加重,易产生中心线裂纹。
钢水温度过低的危害:①容易发生水口堵塞,浇铸中断;②连铸表面容易产生结疱、夹渣、裂纹等缺陷;③非金属夹杂不易上浮,影响铸坯内在质量。
二、钢水在钢包中的温度控制:根据冶炼钢种严格控制出钢温度,使其在较窄的范围内变化;其次,要最大限度地减少从出钢、钢包中、钢包运送途中及进入中间包的整个过程中的温降。
大方坯品种钢连铸工艺实践
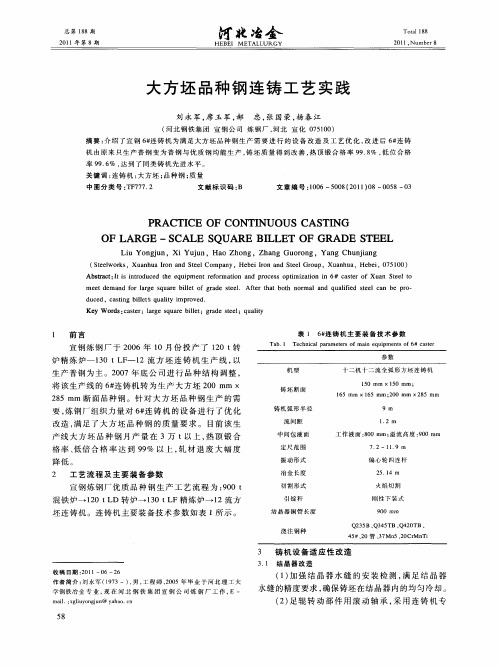
宣钢 炼钢 厂 于 2 0 0 6年 1 0月份 投 产 了 10 t 2 转 炉精 炼 炉一 10 t F 2流 方 坯 连铸 机 生 产 线 , 3 一1 L 以 生产普 钢 为主 。2 0 0 7年底 公 司 进行 品种结 构 调 整 , 将该 生产 线 的 6 连铸 机转 为 生产 大 方坯 2 0 mm × # 0
总 第 1 8期 8
21 0 1年 第 8期
河 北冶金
HE BEI M E TA L U K GY L
To a l 8 tl 8
2 1, u b r8 01 N m e
大 方 坯 品 种 钢 连 铸 工 艺 实 践
刘永 军 , 玉 军 , 席 郝 忠 , 国荣 , 春 江 张 杨
9 m 1 2 m .
要, 炼钢 厂组 织力 量对 6 连铸 机 的设备 进 行 了优化 # 改造 , 足 了大 方 坯 品种 钢 的质 量 要求 。 目前该 生 满 产线 大 方 坯 品种 钢 月 产 量 在 3万 t 以上 , 热顶 锻 合 格率 、 低倍 合 格 率 达 到 9 % 以 上 , 材 退 废 大 幅度 9 轧
( 河北 钢 铁 集 团 宣 钢 公 司 炼 钢 厂 , 北 宣 化 0 50 ) 河 7 10 摘 要 : 绍 了宣 钢 6 连 铸 机 为满 足 大方 坯 品 种 钢 生 产 需 要 进 行 的设 备 改 造 及 工 艺 优 化 , 进 后 6 连 铸 介 # 改 # 机 由原 来 只 生 产 普 钢 变 为普 钢 与 优 质 钢 均 能 生 产 , 坯 质 量 得 到 改 善 , 顶 锻 合 格 率 9 . % , 位 合 格 铸 热 98 低 率 9 . % , 到 了 同类 铸 机 先 进 水 平 。 96 达 关键词 : 连铸 机 : 方 坯 ; 种 钢 ; 量 大 品 质
炼钢连铸工艺流程
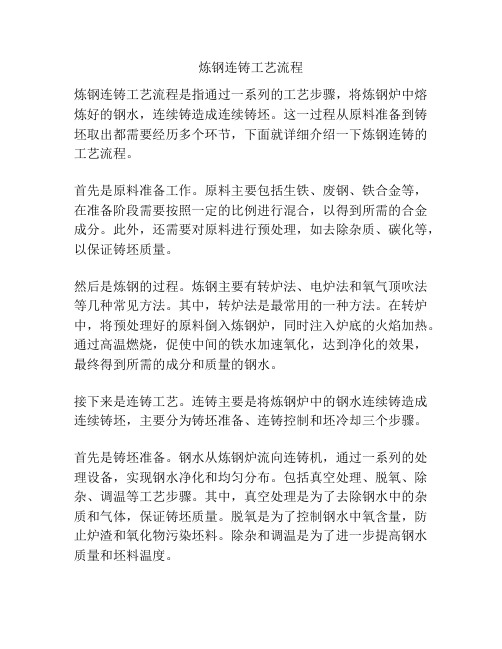
炼钢连铸工艺流程炼钢连铸工艺流程是指通过一系列的工艺步骤,将炼钢炉中熔炼好的钢水,连续铸造成连续铸坯。
这一过程从原料准备到铸坯取出都需要经历多个环节,下面就详细介绍一下炼钢连铸的工艺流程。
首先是原料准备工作。
原料主要包括生铁、废钢、铁合金等,在准备阶段需要按照一定的比例进行混合,以得到所需的合金成分。
此外,还需要对原料进行预处理,如去除杂质、碳化等,以保证铸坯质量。
然后是炼钢的过程。
炼钢主要有转炉法、电炉法和氧气顶吹法等几种常见方法。
其中,转炉法是最常用的一种方法。
在转炉中,将预处理好的原料倒入炼钢炉,同时注入炉底的火焰加热。
通过高温燃烧,促使中间的铁水加速氧化,达到净化的效果,最终得到所需的成分和质量的钢水。
接下来是连铸工艺。
连铸主要是将炼钢炉中的钢水连续铸造成连续铸坯,主要分为铸坯准备、连铸控制和坯冷却三个步骤。
首先是铸坯准备。
钢水从炼钢炉流向连铸机,通过一系列的处理设备,实现钢水净化和均匀分布。
包括真空处理、脱氧、除杂、调温等工艺步骤。
其中,真空处理是为了去除钢水中的杂质和气体,保证铸坯质量。
脱氧是为了控制钢水中氧含量,防止炉渣和氧化物污染坯料。
除杂和调温是为了进一步提高钢水质量和坯料温度。
然后是连铸控制。
在连铸机中,通过多个连铸模具,将钢水连续铸造成坯料。
在这一过程中,需要对连铸机进行严格的控制,包括浇注速度、结晶器冷却、引钢速度等。
通过控制这些参数,可以控制铸坯的形态、尺寸和质量。
最后是坯冷却。
在连铸机铸造出坯料后,需要经过一段时间的冷却才能取出。
坯料通过运输系统进入冷却台,并通过喷淋冷却,使其快速降温。
冷却完成后,使用自动机械将坯料取出并送往后续的加工环节。
总之,炼钢连铸工艺流程是从原料准备到铸坯取出的全过程,通过各个环节的准备和控制,可以实现优质的连铸坯料的生产。
这一工艺流程在现代钢铁生产中得到广泛应用,为提高钢材质量、降低生产成本提供了有效的解决方案。
炼钢连铸工艺流程介绍
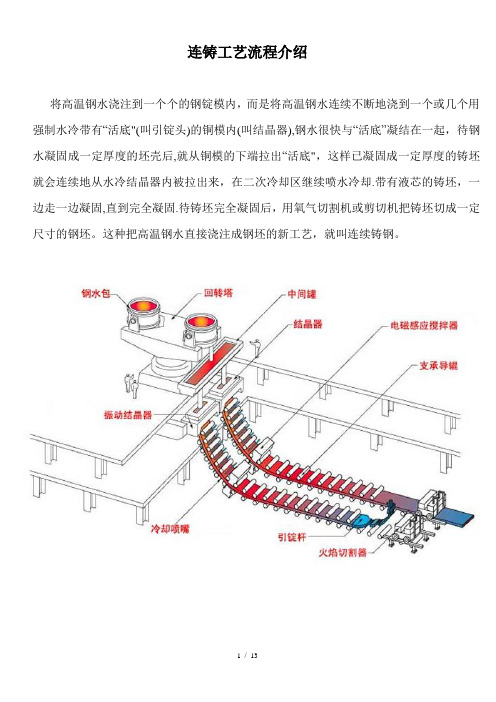
连铸工艺流程介绍将高温钢水浇注到一个个的钢锭模内,而是将高温钢水连续不断地浇到一个或几个用强制水冷带有“活底"(叫引锭头)的铜模内(叫结晶器),钢水很快与“活底”凝结在一起,待钢水凝固成一定厚度的坯壳后,就从铜模的下端拉出“活底",这样已凝固成一定厚度的铸坯就会连续地从水冷结晶器内被拉出来,在二次冷却区继续喷水冷却.带有液芯的铸坯,一边走一边凝固,直到完全凝固.待铸坯完全凝固后,用氧气切割机或剪切机把铸坯切成一定尺寸的钢坯。
这种把高温钢水直接浇注成钢坯的新工艺,就叫连续铸钢。
【导读】:转炉生产出来的钢水经过精炼炉精炼以后,需要将钢水铸造成不同类型、不同规格的钢坯。
连铸工段就是将精炼后的钢水连续铸造成钢坯的生产工序,主要设备包括回转台、中间包,结晶器、拉矫机等。
本专题将详细介绍转炉(以及电炉)炼钢生产的工艺流程,主要工艺设备的工作原理以及控制要求等信息。
由于时间的仓促和编辑水平有限,专题中难免出现遗漏或错误的地方,欢迎大家补充指正.连铸的目的: 将钢水铸造成钢坯。
将装有精炼好钢水的钢包运至回转台,回转台转动到浇注位置后,将钢水注入中间包,中间包再由水口将钢水分配到各个结晶器中去。
结晶器是连铸机的核心设备之一,它使铸件成形并迅速凝固结晶.拉矫机与结晶振动装置共同作用,将结晶器内的铸件拉出,经冷却、电磁搅拌后,切割成一定长度的板坯。
连铸钢水的准备一、连铸钢水的温度要求:钢水温度过高的危害:①出结晶器坯壳薄,容易漏钢;②耐火材料侵蚀加快,易导致铸流失控,降低浇铸安全性;③增加非金属夹杂,影响板坯内在质量;④铸坯柱状晶发达;⑤中心偏析加重,易产生中心线裂纹。
钢水温度过低的危害:①容易发生水口堵塞,浇铸中断;②连铸表面容易产生结疱、夹渣、裂纹等缺陷;③非金属夹杂不易上浮,影响铸坯内在质量。
二、钢水在钢包中的温度控制:根据冶炼钢种严格控制出钢温度,使其在较窄的范围内变化;其次,要最大限度地减少从出钢、钢包中、钢包运送途中及进入中间包的整个过程中的温降。
宣钢大方坯品种钢的连铸工艺优化
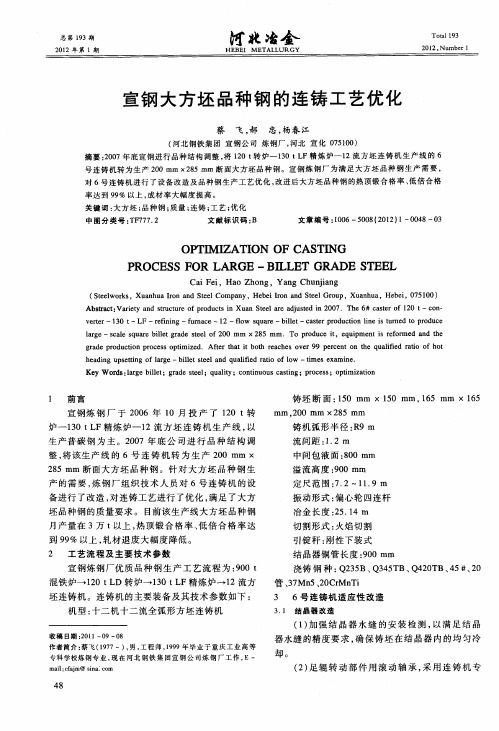
河 北冶全
HE BEI M ETAL U R GY L
To a 9 t11 3 2 1 , u b r1 0 2 N m e
21 0 2年 第 1期
宣钢 大 方 坯 品种钢 的连铸 工 艺优 化
蔡 飞, 郝 忠 , 杨春 江
( 北钢铁集团 宣钢公 司 炼钢厂 , 北 宣 化 050) 河 河 7 10
h a n ps tig o age— ble te n uai e ai fl w —tm e xa i e e dig u etn flr iltse la d q lf d rto o o i i se m n .
Ke o ds lr e b le ; g a e se l q a i y W r :a g ilt r d t e ; u lt y;c tn ou a tn oni u s c si g;p o e s o tm iai n r c s ; pi z to
A s a tV r t n t c r o rd cs n X a t l ea js di 0 7 h #c s r f10 t c n b t c : ai ya ds u t e f o u t i u n Se du t 2 0 .T e r e r u p ea r e n 6 at 2 — o ・ eo
浇铸 钢 种 : 2 5 Q 4 T Q 2 T 4 # 2 Q 3 B、 3 5 B、 4 0 B、 5 、 0
1
前 言
铸坯 断 面 : 5 1 0 mm ×10 mm, 6 5 1 5 mm ×1 5 6
m m , 0 m ×28 2 0m 5 mm
宣钢 炼 钢 厂 于 2 0 0 6年 1 0月 投 产 了 1 0 t 2 转 炉一 10t F精炼 炉一 1 3 L 2流 方 坯 连铸 机 生 产 线 , 以 生产 普碳 钢 为 主。2 0 0 7年 底 公 司进 行 品种 结 构 调 整 , 该生 产 线 的 6号 连 铸 机 转 为 生 产 2 0 mm × 将 0 2 5mm 断面大 方坯 品 种 钢 。针 对 大方 坯 品 种钢 生 8 产 的需 要 , 钢 厂组 织 技术 人 员对 6号 连铸 机 的设 炼 备进 行 了改造 , 对连 铸工艺 进行 了优 化 , 足 了大方 满 坯 品种钢 的质 量要 求 。 目前该 生产线 大方 坯 品种 钢
1#方圆坯连铸工艺技术操作规程

1 连铸工艺流程1.1炼钢厂工艺流程高炉铁水→炉外脱硫→转炉→LF炉(或VD炉)→1#方/圆坯连铸机→连铸方/圆坯1.2方/圆坯连铸工艺流程钢包回转台→中间包→结晶器→二冷区铸坯导向→拉矫机→中间辊道→辅助拉矫→切割机→输送辊道→活动挡板→固定挡板→翻钢机→捞钢机→翻转冷床→收集台架2 主要设备性能及工艺参数连铸机主要的技术性能及工艺参数3 连铸钢水要求3.1对钢水化学成分要求到站钢水化学成分符合钢种要求。
品种钢连铸钢水必须经过炉外精练,保证充分脱氧。
连铸钢水要求成份均匀,温度均匀,连浇炉次炉与炉之间成份波动范围小。
3.2钢水温度控制3.2.1液相线温度计算:1)C<0.51%TL=1534℃-〖90.4×%C+8×%Si+5×%Mn+34×%P+40×%S+10×%Sn+14×%As+1.5×%Cr+4×%Ni+7×%Nb+2×%V+60×%B+2×%Mo+17×%Ti+1%W〗2)C≥0.51%TL=1521℃-〖65×%C+8×%Si+5×%Mn+34×%P+40×%S+10×%Sn+14×%As+1.5×%Cr+4×%Ni+7×%Nb+2×%V+60×%B+2×%Mo+17×%Ti+1%W〗3.2.2中间包中钢水温度:T = TL +T中过TL:钢水液相线温度T中过:中间包中钢水过热度到达连铸平台的钢水温度应符合连铸浇铸的规定。
连铸中间包钢水温度应符合钢种规定要求。
对于新砌钢包及连铸五个流浇注的情况,到达连铸的钢包钢水温度可提高5-10℃。
浇注过程中每减少一个流,到达连铸的钢包钢水温度可提高5℃。
新包、挖补包不能作为第一炉。
宣钢炼钢连铸工艺优化和技术改造

Abstract : Through the technical innovation and optimization of ladle refining furnace , continuous caster tundish , mould and secondary cooling zone , the steelmaking plant of Xuanhua Steel has improved its quality of continuous casting blank. Key words : ladle furnace ; continuous caster ; flow field of tundish ; secondary cooling water distribution ; mould electromag2 netic stirring
1 LF 炉技术改造 LF 精炼炉通过吹氩搅拌钢水 、电弧加热技术 、造
白渣精炼 、双线喂丝 、合金加料等手段 ,强化热力学和 动力学条件 ,使钢水在短时间内达到脱氧 、脱硫 、合金 微调 、升温等综合精炼效果 ,确保达到钢水成分精确 、 温度均匀 、夹杂物充分上浮 、净化钢水的目的 ,同时很 好地协调炼钢和连铸工序 ,保证多炉连浇的顺利进 行。
设备系统改造完成后 ,针对一段时期的铁水硫高 问题 ,我们适时地制定了铁水脱硫站 →复吹转炉 →连 铸机和复吹转炉 →LF 炉 →连铸机两条生产工艺路 线 ,保证了高硫铁水时期的生产顺行 。根据现场具体 情况 ,重新修订了 90tLF 炉的岗位操作规程 ,进一步 对供电制度 、吹氩制度 、造渣制度 、温度制度等细化 , 使工艺得到了优化 ,目前 90tLF 炉作业率达到 92 % , 脱硫效率达到 63 % ,成为冷镦钢 、优碳钢等品种冶炼 的重要工艺环节 。
连铸工艺简介
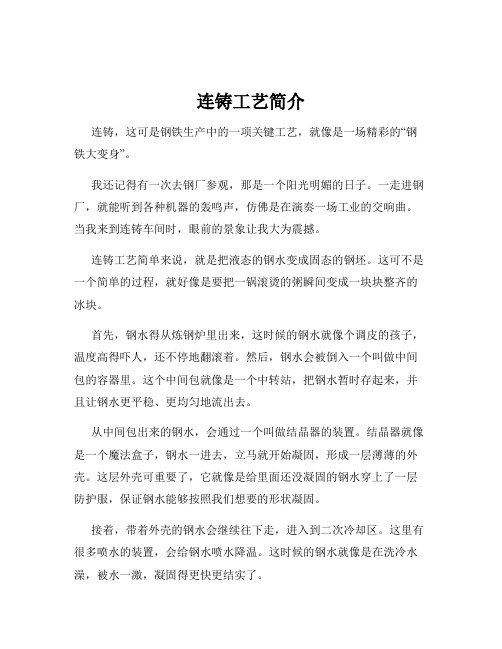
连铸工艺简介连铸,这可是钢铁生产中的一项关键工艺,就像是一场精彩的“钢铁大变身”。
我还记得有一次去钢厂参观,那是一个阳光明媚的日子。
一走进钢厂,就能听到各种机器的轰鸣声,仿佛是在演奏一场工业的交响曲。
当我来到连铸车间时,眼前的景象让我大为震撼。
连铸工艺简单来说,就是把液态的钢水变成固态的钢坯。
这可不是一个简单的过程,就好像是要把一锅滚烫的粥瞬间变成一块块整齐的冰块。
首先,钢水得从炼钢炉里出来,这时候的钢水就像个调皮的孩子,温度高得吓人,还不停地翻滚着。
然后,钢水会被倒入一个叫做中间包的容器里。
这个中间包就像是一个中转站,把钢水暂时存起来,并且让钢水更平稳、更均匀地流出去。
从中间包出来的钢水,会通过一个叫做结晶器的装置。
结晶器就像是一个魔法盒子,钢水一进去,立马就开始凝固,形成一层薄薄的外壳。
这层外壳可重要了,它就像是给里面还没凝固的钢水穿上了一层防护服,保证钢水能够按照我们想要的形状凝固。
接着,带着外壳的钢水会继续往下走,进入到二次冷却区。
这里有很多喷水的装置,会给钢水喷水降温。
这时候的钢水就像是在洗冷水澡,被水一激,凝固得更快更结实了。
在整个连铸过程中,对温度、速度的控制那是相当严格的。
温度太高了,钢水凝固不好;温度太低了,又容易出现裂纹。
速度快了不行,慢了也不行,得恰到好处。
这就像是做饭的时候掌握火候,多一分少一分都不行。
而且,为了保证铸出来的钢坯质量好,还得时刻监测钢水的成分和纯净度。
要是里面有杂质,就像我们吃饭吃到沙子一样,会影响整个钢坯的品质。
连铸出来的钢坯,表面光滑,形状规整,就像是刚刚从生产线上下来的“钢铁士兵”,排列整齐,等待着被送去加工成各种钢材制品。
想象一下,这些钢坯最后会变成高楼大厦里的钢梁、汽车上的零部件、家里的厨具等等。
连铸工艺就像是钢铁世界的源头,为我们的生活提供了各种各样坚固耐用的钢铁产品。
总之,连铸工艺虽然看似复杂,但其实每一个步骤都有它的道理和妙处。
它就像是一场精心编排的舞蹈,每个环节都紧密配合,最终为我们呈现出优质的钢铁成果。
大方圆坯连铸技术工艺规程

大方圆坯连铸技术工艺规程大方圆坯连铸技术工艺规程1 连铸钢水要求连铸钢水必须经炉外精炼,保证脱氧充分,成分、温度均匀,符合连铸要求。
1.1液相线温度的确定钢水液相线温度按照下式计算:TL=1536℃-[78×C%+7.6×Si%+4.9×Mn%+34×(P+S)%+5×Al%+1.5%×Cr%+2. 0×Mo%+2.0×V%+18.0×Ti%+4.0×Ca%+5.0×Cu%]其中:C%——为钢种中碳的百分含量Si%——为钢种中硅的百分含量Mn%——为钢种中锰的百分含量(P+S)%——为钢种中的硫和磷的百分含量Al%——为钢种中铝的百分含量1536℃——为纯铁的液相线温度,TL——为钢种液相线温度1.2 连铸钢水温度要求钢包钢水温度必须控制在连铸要求的范围内,即:a.低碳钢:TL+(70~80)℃(第一炉)b.中碳钢:TL+(65~75)℃(第一炉)c.高碳钢:TL+(55~65)℃(第一炉)d.三流浇注、零次罐+5:℃e.浇注小断面:+5℃第二炉及以后各炉均比第一炉低10~20℃2中间包准备2.1 中间包修砌2.1.1 绝热层砌砖A.砖与座砖模子应留出120mm的间距。
B.不得使用有裂纹、受潮变质及严重残缺的砖。
C.砖缝≯2mm,并保证砌缝灰浆饱满。
D.砌筑用高温火泥搅拌均匀、稠度合适。
2.1.2 中间包永久层浇注A.投入搅拌机的搅拌量不应超过搅拌机定量的50%。
B.干料加入搅拌机内,应干混1-2分钟,按重量比加入8-10%的水,继续搅拌2-3分钟,混匀即可出料。
C.搅拌好的料应尽快使用,以在15分钟内用完为宜。
D.浇注时应用边加料边振动的连续施工法,一次加料不宜超过300mm高。
E.包底浇注高度距包底钢板180mm。
F.振动以泥料充分泛浆无大的气泡冒出为宜,从料中取出振动棒时,不宜过快,防止造成空洞。
- 1、下载文档前请自行甄别文档内容的完整性,平台不提供额外的编辑、内容补充、找答案等附加服务。
- 2、"仅部分预览"的文档,不可在线预览部分如存在完整性等问题,可反馈申请退款(可完整预览的文档不适用该条件!)。
- 3、如文档侵犯您的权益,请联系客服反馈,我们会尽快为您处理(人工客服工作时间:9:00-18:30)。
宣钢生产大方坯品种钢的连铸工艺实践刘永军席玉军张明海(河北钢铁集团宣钢公司炼钢厂,河北宣化075100)摘要本文介绍了宣钢炼钢厂为满足大方坯品种钢生产需要,对6号连铸机进行的设备改造及品种钢生产工艺优化,和改进后大方坯品种钢的质量提升效果。
关键词连铸机大方坯品种钢质量宣钢炼钢厂于2006年10月份投产了120t转炉—130tLF—12流方坯连铸机生产线,以生产普钢为主。
2007年底公司进行品种结构调整,将该生产线的6号连铸机转为生产大方坯200×285mm断面品种钢。
针对大方坯品种钢生产的需要,炼钢厂组织力量对6号连铸机的设备进行了改造优化,满足了大方坯品种钢的质量要求。
目前该生产线大方坯品种钢月产量在3万吨以上,热顶锻合格率、低倍合格率达到99%以上,轧材退废大幅度降低。
本文对6号连铸机的大方坯品种钢适应性改造及大方坯品种钢生产工艺优化做简单介绍。
1 工艺流程及主要装备参数宣钢炼钢厂转炉优钢生产工艺流程为:900t混铁炉→120tLD转炉→130tLF精炼炉→12流方坯连铸机。
连铸机主要装备技术参数如表1所示。
表 1 6号连铸机主要装备技术参数参数机型十二机十二流全弧形方坯连铸机铸坯断面150mm×150mm,165mm×165mm,200×285mm铸机弧形半径R9m流间距 1.2m中间包液面工作液面:800mm;溢流高度:900mm定尺范围7.2~11.9m振动形式偏心轮四连杆冶金长度25.14米切割形式:火焰切割引锭秆刚性下装式结晶器铜管长度900mm浇注钢种:Q235B、Q345TB、Q420TB、45#、 20管、37Mn5、20CrMnTi2 铸机设备适应性改造2.1 结晶器改造(1)加强结晶器水缝的安装检测,满足结晶器水缝的精度要求,确保铸坯在结晶器内的均匀冷却。
(2)足辊转动部件用滚动轴承,采用连铸机专用耐高温润滑脂润滑,转动灵活;足辊弧度的调整通过旋转足辊架上的定位和调整螺栓来实现,调整范围大,并且调整起来更加方便快捷。
(3)足辊配淋集管采用环管式结构,将各喷淋集管联为整体,刚性好、不易变形,一般不用调整,能够有效保证应有的强冷却效果。
2.2 二冷改造(1)二冷一段全部安装密排辊,采用密排辊夹持连铸工艺。
通过安装使用密排辊架以后,在其他工艺参数保持不变的情况下,铸坯宽面鼓肚得以控制到205mm以下,虽然增加了更换断面检修的难度,但是铸坯外观质量有了根本保证,并且可在此基础上根据浇铸钢种调整拉速及二冷强度,进一步提高铸坯的内部质量。
(2)二冷系统、压缩空气管路及阀门全部采用不锈钢的,消除因普通管路锈蚀杂物造成的喷嘴堵塞。
(3)将全水冷却改造为气雾冷却,满足优钢生产要求。
(4)对三段喷淋管喷嘴间距长度进行调整优化,使生产时的工艺水量与喷嘴的设计水量相适应,提高了配水的有效性。
(5)在原二冷水中配加软水,形成半软水,半软水的硬度为小于14德国度,能有效的防止二冷水过热结垢避免喷嘴堵塞。
2.3 浇注系统改造将目前的塞棒自动控制升级为塞棒自动控制和拉矫自动控制双系统运行,可有效的减少单流事故,提高铸坯质量。
3 品种钢生产工艺优化3.1 低过热度浇注合理控制中间包钢液的过热度是减轻铸坯中心偏析和缩孔缺陷的基础,过热度对铸坯中心偏析有明显的影响。
由于连铸钢水的过热度直接影响铸坯柱状晶的生长,而柱状晶发达是产生疏松,缩孔,偏析的主要原因。
通过加强钢包周转管理,强化烘烤措施,大包加盖等措施,减少并稳定了钢包温降。
钢水过热度达到了5±℃控制水平,中间包钢水过热度控制在20—30℃。
3.2 全程保护浇注为了减少钢水温降和钢水二次氧化,铸机采用全程保护浇注措施,大包至中包采用保护套管吹氩密封,并增加氩气流量计。
大包长水口、浸入水口增加纤维密封垫,减少水口接缝吸气。
中间包采用碱性覆盖剂,有利于减少温降和促进夹杂物的上浮吸收。
3.3优化保护渣针对钢种成分及特点开发专用结晶器保护渣,改善结晶器润滑和传热,改善铸坯表面质量。
保护渣液渣层达到10mm以上,有较强的吸附夹杂能力,可有效提高表面质量,减少钢中夹杂。
增加保护渣在线烘烤设施,将水分控制在0.4%以下,避免因保护渣造成的钢种气体含量高的问题。
3.4 恒拉速、低拉速浇注铸机拉速不稳定,造成二冷水水量的忽大忽下,影响铸坯的内部质量的均质化,易造成缩孔、疏松等缺陷;拉速变化大,钢水液面出现波动,易造成卷渣,影响铸坯内部质量。
通过采用塞棒自动控制系统,实现了拉速的恒定,提高了铸坯内部质量。
控制拉速对铸坯内裂有较大影响,实践表明,适当降低拉速可减轻机械应力,增加坯壳厚度,缩短液芯长度和减少铸坯内裂纹。
6号连铸机弧形半径小,且为单点矫直,生产优钢存在先天缺陷,针对优钢生产较多的200×285断面,铸坯易出现矫直裂纹,采用低拉速浇注是必需的。
3.5采用弱冷工艺连铸的冷却包括结晶器一次冷却和二冷段二次冷却,结晶器内的一次冷却目的是形成足够厚度的坯壳,以支持由钢水内部产生的静压力;二冷段的二次冷却目的是使带液芯的铸坯完全凝固,而不使铸坯产生质量缺陷。
采用弱冷工艺能有效减少由于热应力引起的表面裂纹和内部裂纹等缺陷,弱冷工艺首先要从结晶器冷却抓起,然后与二冷弱冷配合才能取得事半功倍的效果。
(1)首先采用结晶器弱冷,品种钢的一冷水水量比普钢降低10%,适当提高进出水温差,增强结晶器内初生坯壳的均匀性。
结晶器水缝水流速为5-8 m/s(水缝尺寸为4mm)将出现间歇沸腾,对于低碳钢水速小于6 m/s、中碳钢水速小于9 m/s,会在结晶器冷面引起间歇沸腾。
水速大于10 m/s可抑制间歇沸腾,但导出热流的增加被坯壳与铜壁之间的气隙热阻所抵消,生产200×285mm断面品种钢的结晶器水缝水流速定为18-20 m/s,对应的结晶器水流量设定为134-149m3/h,比普钢降低10%,结晶器采用弱冷制度可以满足坯壳生长的均匀性。
结晶器冷却水进水温度的高低在一定程度上决定了结晶器壁和铸坯坯壳之间的温度梯度。
它代表了在结晶器冷却水流量和冷却面积不变的情况下结晶器铜板的冷却能力。
结晶器进水温度低,与铜板的温度梯度大,由铜板导出的热量多,结晶器平均热流大,造成弯月面下平均热流大,加剧了钢水在结晶器内的传热不均,导致铸坯坯壳生长不均匀。
对于要求缓冷的大断面品种钢,提高冷却水进水温度,就变相满足了缓冷的要求。
但结晶器冷却水的进水温度也不能无限制的提高,因为冷却水温度升高后,很有可能在局部达到水的形核沸腾,使得结晶器导出热流不均匀。
研究得出合适的结晶器进水温度在35℃左右。
(2)降低二冷比水量,目前比水量在0.3L/Kg左右。
3.6中间包浸入式水口浸入式水口对中不好、水口插入深度太浅或过深都易引起钢水冲刷初生坯壳而增加不均匀性,造成卷渣,必须严格控制。
目前中包水口插入深度稳定控制在80-100mm,对中偏差小于5mm。
由于中包无升降功能、中间包高度无法调整,通过增减中间包两侧横梁垫板来调整中间包高度,杜绝了由于包壳变形等原因造成的浸入深度不足或过深,利于结晶器内钢水流场的稳定和钢中夹杂物的上浮与铸坯质量的提高。
采用高寿命铝锆碳质浸入式水口,水口寿命已由原来的3小时提高到现在的6~8小时,减少水口更换次数,每个流由原来每班更换3~4支水口减少为1支,甚至不换,大大降低了铸坯卷渣几率。
3.7提高设备维护质量针对连铸机二冷系统管路锈蚀严重,喷嘴堵塞较多、、二冷支撑辊磨损变形、零段足辊转动不灵活、中包水口不对中、插入深度较低等问题,专门成立连铸机设备整治攻关组,确定改进方案,利用定修及停机时间有计划地进行逐一整改。
目前,通过持续改造,零段供水管路已全部采用了不锈钢管路,消除了零段喷嘴堵塞现象;定期更换二冷辊,确保使对弧精度控制在0.5mm以内,二冷系统设备精度得到根本提高。
3.8完善质量控制体系(1)制定质量提升计划,实施差错管理制度,对连铸工序中间包温度、喷嘴堵塞、中包水口对中、浸入水口插入深度、保护浇铸等多个参数进行差错考核,实现过程控制参数群的稳定,以此保证铸坯质量稳定。
(2)建立铸坯低倍档案、低倍内部标准。
优钢每炉每流都有坯样,及时掌握铸坯内部质量情况。
(3)建立轧材质量日反馈制度,每天了解轧材质量信息,对出现的质量缺陷及时分析整改,实现了铸坯质量的动态控制。
(4)推行岗位标准化操作,规范员工的操作细节。
4 对于大规格控铝圆钢表面出现微裂纹的连铸工艺探讨经过铸机设备适应性改造及工艺优化以后,优质碳素钢铸坯合格率大幅度提高,但是对于控铝优质品种钢轧材表面出现的大量微裂纹目前工艺无法克服,理论分析研究表明轧材表面质量取决于轧件在热轧过程中晶粒边界析出物的数量和形态。
这些析出物会在材料热变形过程中阻碍晶界移动,从而在这些位置产生机械应力。
当这些位置的应力超过极限应力时,便会产生裂纹。
热轧时轧材的温度在650-1000℃的范围内,在这个温度范围内,诸如氮化铝(AlN)、氮化硼(BN)、碳氮化钒(VCN)、及碳氮化铌(NbCN)等N析出物会严重降低金属的延展性。
其中,影响最大的析出物是氮化铝(AlN)。
不过,在铸坯的凝固过程中,这些析出物的数量是可以控制的。
在均匀的奥氏体结构中,AlN的析出是非常缓慢的。
但是,相向相的相变会显著提高析出的速度。
产生这一现象的原因是在铁素体中,AlN的溶解度非常低。
研究表明,出现最大析出率的温度范围在750-900℃之间,具体则取决于钢种的化学成分。
一般来说,这个温度范围在图1中的Ar1至Ar3之间。
在直接热装过程中,有一种方法可以有效控制AlN的析出,即确保铸坯在连铸到热轧输送的过程中,其表面温度始终高于Ar3值,但在铸坯输送到加热炉的实际生产过程中,铸坯表面温度经常落在Ar3至Ar1之间,就会在晶粒边界伴随相铁素体产生大量的AlN析出。
图1 AlN在相变中的析出过程为了避免上述现象的发生,采用表面淬火是一种十分稳妥且灵活的措施。
经过表面淬火后,铸坯表面的温度可以冷却到300°C以下。
显微镜试验显示,经过淬火处理后,在约20mm的铸坯表面会形成细密的回火马氏体结构层。
与未经冷却处理的内部组织相比,表面的这层结构要精细很多。
在铸坯由淬火箱经过火切机,进入出坯辊道的过程中,其表面因冷却形成的马氏体层会被铸坯中心传导出的热量进行回火。
经过这样一个过程,在铸坯外表层就可以形成一层致密稳定的结构。
经过这样的处理,铸坯在加热后,会形成很好的晶粒尺寸,而且在晶粒边界仅有少量的AlN析出。
从而避免了在热轧过程中,由于AlN析出所造成的奥氏体晶粒边界延展性的显著降低。
5 结语6号铸机经过工艺设备技术改造后,由原来的普钢连铸机转变为优钢铸机,大大改善了铸坯低倍组织,杜绝了中间裂纹、角裂等缺陷,大大降低了铸坯脱方、疏松、缩孔等缺陷的几率;通过不断工艺优化,轧材热顶锻合格率、低倍合格率大幅度降低。