立铣刀参数(精)
整体合金立铣刀的设计
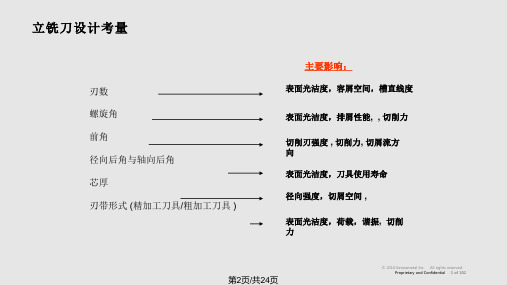
第3页/共24页
刀柄直径
立铣刀设计基本参数
侧视图
端视图
径向前角
主后角
轴向锲角 主后角
次后角
次后角
过中心刃
© 2010 Kennametal Inc. l All rights reserved. l Proprietary and Confidential l 3 of 102
凹角
锲角
第4页/共24页
切削面
次要后角
第10页/共24页
© 2010 Kennametal Inc. l All rights reserved. l Proprietary and Confidential l 9 of 102
前刀面设计
传统前刀面 (一个表面) 接触区大
切屑速度慢 接触区小
快速切屑 前刀面 (两个表面)
刀尖条件
刃数
容屑空间
2刃 过中心切削
3刃 过中心切削
4刃 过中心切削
6刃
8刃
过中心切削 过中心切削
表面光洁度
第5页/共24页
© 2010 Kennametal Inc. l All rights reserved. l Proprietary and Confidential l 4 of 102
齿距
© 2010 Kennametal Inc. l All rights reserved. l Proprietary and Confidential l 12 of 102
粗加工齿形
粗加工刀具
粗齿 铝,非铁材料
深槽铣 主轴荷载少
半精加工刀具
密齿 钢,铸铁 仿形,槽铣 耐磨损性能好
超密齿 不锈钢,钛,高温合金
NC刀具参数

刀柄长400/450mm
以上刀具参数只适用于 平面开槽、孔加工 Φ 30球刀(双刀片) 2-4mm Φ 25球刀(双刀片) ≤4mm Φ 20球刀 Φ 16球刀 Φ 12球刀 Φ 10球刀 Φ 8球刀 Φ 6球刀 ≤2mm ≤2mm ≤1mm ≤1mm ≤0.7mm ≤0.3mm
以上刀具参数只适用于 型面粗清根 Φ 50球头铣刀 Φ 30球头铣刀 Φ 20球头铣刀 0.8-1mm 0.5-0.8mm 0.5-0.7mm 1200 1800 2000 4000 3000 2500 2500 2500 2500 2500 1000 1000 200 600 600 600 300 300 300 300 1800 1800 1800 4000 3000 2000 1800 1800 1500 1500 1800 1800 150 250 200 200 200 300 300 300 ≤2mm ≤1.5mm ≤1mm ≤1mm ≤0.35mm ≤0.2mm ≤0.1mm ≤0.1mm 200 600 600 600 300 300 300 300 200 150 100 100 100 300 300 200 0.8-1mm 0.4-0.7mm 0.4-0.7mm ≤0.4mm ≤0.35mm ≤0.35mm ≤0.25mm ≤0.25mm ≤0.2mm ≤0.2mm 1200 1800 2000 4000 3000 2500 2500 2500 2500 2500 1800 1800 1800 3500 3000 1500 1500 1200 1200 1200
以上刀具参数只适用于 导板、导滑面、轮廓加工等立面加工
注:切削参数中进给速度为刀具最大进给速度,在加工过程中可以下调%10-%20
钢
标准铣刀规格及长度表

标准铣刀规格及长度表铣刀是一种常用的金属加工工具,广泛应用于机械加工、模具加工等领域。
不同的加工需求需要选择不同规格和长度的铣刀,以确保加工效果和加工质量。
下面将介绍一些常见的标准铣刀规格及长度表,希望对大家有所帮助。
1. 铣刀规格。
铣刀的规格通常包括直径、刃长、总长等参数。
常见的直径包括,Ф6、Ф8、Ф10、Ф12、Ф16、Ф20、Ф25等,刃长和总长也有相应的标准尺寸。
在选择铣刀时,需要根据加工材料的硬度、加工精度要求等因素来确定合适的规格。
2. 铣刀长度。
铣刀的长度对于加工效果有着重要的影响。
一般来说,铣刀的长度越长,刚性越好,适用于加工深槽、深槽面等工件;而长度较短的铣刀适用于小型零件的加工。
常见的铣刀长度包括,50mm、75mm、100mm、150mm等,根据具体的加工需求来选择合适的长度。
3. 不同材质的铣刀选择。
铣刀的材质对于其使用寿命和加工效果也有着重要的影响。
常见的铣刀材质包括高速钢、硬质合金、立方氮化硼等。
在选择铣刀时,需要根据加工材料的硬度和耐磨性来确定合适的材质。
4. 铣刀的应用。
铣刀广泛应用于平面加工、轮廓加工、曲面加工等多种加工过程中。
不同的加工方式需要选择不同类型的铣刀,如平底铣刀、球头铣刀、立铣刀等。
在实际应用中,需要根据加工要求来选择合适的铣刀类型。
5. 铣刀的保养。
铣刀作为常用的加工工具,需要定期进行保养和维护,以延长其使用寿命和保证加工质量。
保养工作包括清洁、润滑、修磨等,需要严格按照操作规程来进行。
总结:标准铣刀规格及长度表是选择合适的铣刀的重要参考依据,合理选择铣刀规格和长度,根据加工材料和加工要求来确定铣刀材质和类型,定期进行铣刀的保养和维护,可以有效提高加工效率和加工质量,降低加工成本,是每个机械加工工作者需要了解和掌握的知识。
希望本文介绍的内容对大家有所帮助,谢谢阅读!。
各材料常用刀具转速进给参数对照表

各材料常用刀具转速进给参数对照表在机械加工领域,刀具的转速和进给参数对于加工质量、效率和成本都有着至关重要的影响。
不同的材料具有不同的物理和机械性能,因此需要根据材料的特性来选择合适的刀具转速和进给参数。
下面是一份常见材料的刀具转速进给参数对照表,希望能为您的加工工作提供一些参考。
一、铝合金铝合金是一种广泛应用于航空航天、汽车制造和电子工业等领域的轻质材料。
由于其良好的导热性和较低的强度,加工时需要较高的转速和较快的进给速度。
1、粗加工刀具:硬质合金立铣刀转速:3000 5000 rpm进给速度:800 1500 mm/min切削深度:2 5 mm切削宽度:刀具直径的 70% 80%2、半精加工刀具:硬质合金立铣刀转速:5000 8000 rpm进给速度:500 1000 mm/min切削深度:05 15 mm切削宽度:刀具直径的 50% 60%3、精加工刀具:硬质合金球头铣刀转速:8000 12000 rpm进给速度:200 500 mm/min切削深度:01 03 mm切削宽度:刀具半径的 20% 30%二、钢材钢材是机械加工中最常见的材料之一,其种类繁多,性能各异。
以下是常见钢材的加工参数。
1、低碳钢粗加工刀具:硬质合金涂层立铣刀转速:1500 2500 rpm进给速度:300 600 mm/min切削深度:3 6 mm切削宽度:刀具直径的 60% 70%半精加工刀具:硬质合金涂层立铣刀转速:2500 4000 rpm进给速度:200 400 mm/min切削深度:1 2 mm切削宽度:刀具直径的 40% 50%精加工刀具:硬质合金涂层球头铣刀转速:4000 6000 rpm进给速度:100 200 mm/min切削深度:01 02 mm切削宽度:刀具半径的 15% 20% 2、中碳钢粗加工刀具:硬质合金涂层立铣刀转速:1000 1800 rpm进给速度:200 400 mm/min切削深度:2 4 mm切削宽度:刀具直径的 50% 60%半精加工刀具:硬质合金涂层立铣刀转速:1800 3000 rpm进给速度:150 300 mm/min切削深度:05 10 mm切削宽度:刀具直径的 30% 40%精加工刀具:硬质合金涂层球头铣刀转速:3000 5000 rpm进给速度:80 150 mm/min切削深度:005 015 mm切削宽度:刀具半径的 10% 15% 3、高碳钢粗加工刀具:硬质合金涂层立铣刀转速:800 1200 rpm进给速度:100 200 mm/min切削深度:1 3 mm切削宽度:刀具直径的 40% 50%半精加工刀具:硬质合金涂层立铣刀转速:1200 2000 rpm进给速度:80 150 mm/min切削深度:03 08 mm切削宽度:刀具直径的 20% 30%精加工刀具:硬质合金涂层球头铣刀转速:2000 3500 rpm进给速度:50 100 mm/min切削深度:003 008 mm切削宽度:刀具半径的 8% 12%三、不锈钢不锈钢具有良好的耐腐蚀性和耐磨性,但加工难度较大,需要较低的转速和较慢的进给速度。
加工中心切削参数
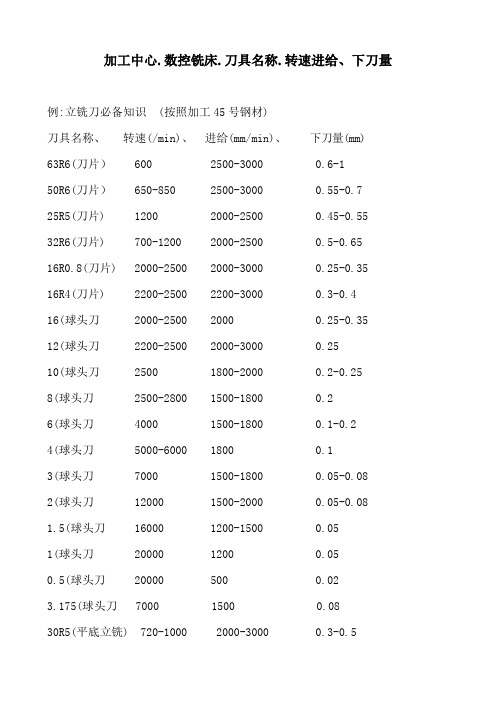
加工中心.数控铣床.刀具名称.转速进给、下刀量例:立铣刀必备知识(按照加工45号钢材)刀具名称、转速(/min)、进给(mm/min)、下刀量(mm)63R6(刀片) 600 2500-3000 0.6-150R6(刀片) 650-850 2500-3000 0.55-0.725R5(刀片) 1200 2000-2500 0.45-0.5532R6(刀片) 700-1200 2000-2500 0.5-0.6516R0.8(刀片) 2000-2500 2000-3000 0.25-0.3516R4(刀片) 2200-2500 2200-3000 0.3-0.416(球头刀 2000-2500 2000 0.25-0.3512(球头刀 2200-2500 2000-3000 0.2510(球头刀 2500 1800-2000 0.2-0.258(球头刀 2500-2800 1500-1800 0.26(球头刀 4000 1500-1800 0.1-0.24(球头刀 5000-6000 1800 0.13(球头刀 7000 1500-1800 0.05-0.082(球头刀 12000 1500-2000 0.05-0.08 1.5(球头刀 16000 1200-1500 0.051(球头刀 20000 1200 0.050.5(球头刀 20000 500 0.023.175(球头刀 7000 1500 0.0830R5(平底立铣) 720-1000 2000-3000 0.3-0.540(平底立铣) 300-600 2000-2500 1.0-2.020(平底立铣) 600-1000 2000-2500 1.0-2.016(平底立铣) 1600 2000-2500 0.3-0.412(平底立铣) 2000-2200 2000-2500 0.25-0.3510(平底立铣) 2200-2500 2000-2500 0.25-0.38(平底立铣) 2500 1500-2000 0.2-0.36(平底立铣) 3000 1500-2000 0.15-0.24(平底立铣) 3500-4000 1500-2000 0.13(平底立铣) 6000 1500-1800 0.08-0.12(平底立铣) 9000 1500 0.05-0.081.5(平底立铣) 12000 1200-1500 0.05-0.081(平底立铣) 18000 1000-1500 0.03-0.05铣刀大体上分为:1.平头铣刀.进行粗铣.去除大量毛坯.小面积水平平面或者轮廓精铣2.球头铣刀.进行曲面半精铣和精铣.小刀可以精铣陡峭面/直壁的小倒角。
切削参数表(铣刀)

铣削用量的选择
1 铣削速度V指铣刀旋转时的圆周线速度,单位为m/min。
计算公式;V=兀DN/1000
式中D——铣刀直径,mm;
N——主轴(铣刀)转速,r/min。
从上式可得到:主轴(铣刀)转速:N=1000V/兀D
铣削速度V推荐值
2进给量
在铣削过程中,工件相对于铣刀的移动速度称为进给量.有三种表示方法:
铣刀每转过一个齿,工件沿进.给方向移动的距离, (1) 每齿进给量a
f
单位为mm/z。
(2) 每转进给量f铣刀每转过一转, 工件沿进.给方向移动的位为距
离, 单位为mm/r.。
(3) 每分钟进给量V f铣刀每旋转1min, 工件沿进.给方向移动的位为距离, 单位为mm/ min。
.
zn
三种进给量的关系为: V f=a
f
——每齿进给量,mm/z。
.
式中a
f
z——铣刀(主轴)转速,r/min。
n——铣刀齿数.。
(mm/z.) 推荐值
铣刀每齿进给量, a
f
3铣削层用量
铣刀在一次进给中所切掉工件表面的宽度,单位为(1)铣削宽度a
e
mm。
.
一般立铣刀和端铣刀的铣削宽度约为铣刀直径的50%~60%左右。
(切削深度) 铣刀在一次进给中所切掉工件表面的厚(2)背吃刀量a
p
度,即工件的已加工表面和待加工表面间的垂直距离,单位为mm。
一般立铣刀粗铣时的背吃刀量以不超过铣刀半径为原则,以防背吃刀量过大而造成刀具的损坏,精铣时约为0.05~0.30mm;端铣刀粗铣
时约为2~5mm,精铣时约为0.10~0.50mm.。
刀具参数
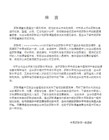
E21R0.8 2200 2000 160 0.4
E17R0.8 2500 2000 160/200 0.3
E40R0.8 1500 2000 200/300 0.7 (柄32、头长50)
E32R0.8 2000 2000 150 0.6
E20R4 2200 2000 150/160/200 0.4
E16R4 2500 2000 150 0.25 (柄15)
E80R8 Βιβλιοθήκη D16 E63R6 D12
E50R5 D10
E40R6 D8
E35R5 D8
E32R6 D6
E30R5 D6
E26R0.8 D5
六.刀具命名:
圆鼻刀 E直径R角
球刀 B直径
筒夹:ER11/ER16/ER20/ER25/ER32/ER40
长度:100/120/150/180/200
八.刀具圆角过度参数
直径 圆角半径 最小半径
Φ50以上 4 3
Φ50~Φ35 3 2
D10 3000 2000 60(75) 75(100) 0.25
D8 3500 2000 45(60) 75(100) 0.2
B16 2500 2000 150 0.2 2 0.35 (单片)
B12 2800 2000 150 0.15 1.5 0.3
D20 2000 2000 70(100) 0.35
D16 2000 2000 70(100) 0.3
D12 2500 2000 60(75) 75(100) 0.25
ER32 50 φ2~φ20mm 100 63
立铣刀 切削参数

立铣刀切削参数一、切削速度切削速度是指立铣刀在单位时间内切削物料的线速度。
切削速度的选择对切削质量和刀具寿命有着重要的影响。
切削速度过高会导致刀具磨损加剧,切削温度升高,甚至可能引起刀具断裂等问题;切削速度过低则会降低生产效率。
因此,在选择切削速度时,需要根据加工材料的硬度、刀具材料和刀具直径等因素进行综合考虑,选择一个合适的切削速度。
二、进给速度进给速度是指立铣刀在单位时间内沿工件表面移动的速度。
进给速度的选择与切削速度密切相关,两者需要相互配合,以保持切削过程的稳定性和刀具的寿命。
进给速度过高会导致切削负荷过大,刀具容易磨损或折断;进给速度过低则会降低加工效率。
因此,在选择进给速度时,需要根据刀具类型、切削条件和工件材料等因素进行合理的选择。
三、切削深度切削深度是指立铣刀每次切削过程中刀具与工件表面的最大距离。
切削深度的选择直接影响到切削力和切削温度的大小,进而影响刀具的寿命和加工质量。
切削深度过大会导致切削力过大,刀具容易磨损或折断,同时还会加剧切削温度的升高;切削深度过小则会降低加工效率。
因此,在选择切削深度时,需要综合考虑刀具的刚度、切削条件和工件材料等因素,选择一个合适的切削深度。
四、切削方式切削方式是指立铣刀在切削过程中的运动方式。
常见的切削方式有径向切削和轴向切削。
径向切削是指刀具在切削过程中与工件表面的相对运动方向与工件表面法线方向垂直;轴向切削是指刀具在切削过程中与工件表面的相对运动方向与工件表面法线方向平行。
选择合适的切削方式可以提高加工效率和加工质量。
在具体应用中,需要根据工件形状、切削条件和刀具类型等因素进行综合考虑,选择一个适合的切削方式。
总结:立铣刀的切削参数包括切削速度、进给速度、切削深度和切削方式等。
在实际应用中,合理选择这些切削参数可以提高切削质量和刀具寿命,提高生产效率。
因此,根据加工材料的硬度、刀具材料和刀具直径等因素,综合考虑切削速度、进给速度、切削深度和切削方式等参数,选择合适的数值,以实现高效、高质量的加工过程。
加工中心切削参数

加工中心.数控铣床.刀具名称.转速进给、下刀量例:立铣刀必备知识(按照加工45号钢材)刀具名称、转速(/min)、进给(mm/min)、下刀量(mm) 63R6(刀片) 600 2500-3000 0.6-150R6(刀片) 650-850 2500-3000 0.55-0.7 25R5(刀片) 1200 2000-2500 0.45-0.55 32R6(刀片) 700-1200 2000-2500 0.5-0.65 16R0.8(刀片) 2000-2500 2000-3000 0.25-0.35 16R4(刀片) 2200-2500 2200-3000 0.3-0.4 16(球头刀 2000-2500 2000 0.25-0.35 12(球头刀 2200-2500 2000-3000 0.2510(球头刀 2500 1800-2000 0.2-0.25 8(球头刀 2500-2800 1500-1800 0.26(球头刀 4000 1500-1800 0.1-0.2 4(球头刀 5000-6000 1800 0.13(球头刀 7000 1500-1800 0.05-0.08 2(球头刀 12000 1500-2000 0.05-0.08 1.5(球头刀 16000 1200-1500 0.051(球头刀 20000 1200 0.050.5(球头刀 20000 500 0.023.175(球头刀 7000 1500 0.0830R5(平底立铣) 720-1000 2000-3000 0.3-0.540(平底立铣) 300-600 2000-2500 1.0-2.020(平底立铣) 600-1000 2000-2500 1.0-2.016(平底立铣) 1600 2000-2500 0.3-0.412(平底立铣) 2000-2200 2000-2500 0.25-0.3510(平底立铣) 2200-2500 2000-2500 0.25-0.38(平底立铣) 2500 1500-2000 0.2-0.36(平底立铣) 3000 1500-2000 0.15-0.24(平底立铣) 3500-4000 1500-2000 0.13(平底立铣) 6000 1500-1800 0.08-0.12(平底立铣) 9000 1500 0.05-0.081.5(平底立铣) 12000 1200-1500 0.05-0.081(平底立铣) 18000 1000-1500 0.03-0.05铣刀大体上分为:1.平头铣刀.进行粗铣.去除大量毛坯.小面积水平平面或者轮廓精铣2.球头铣刀.进行曲面半精铣和精铣.小刀可以精铣陡峭面/直壁的小倒角。
加工中心新刀具常用切削参数参照表1

8 8
120-150 120-150
20-30 20-25
半精铣T型 粗精槽铣T型
槽
焊刃 焊刃
φ68-72/T型刀
8
120-150
20-25 粗铣T型槽
焊刃
铸铁/滑块 φ68-72/T型刀 φ68-72/T型刀
8 8
120-150 120-150
30-45 30-40
半精铣T型 粗精槽铣T型
槽
焊刃 焊刃
400-600 300-400
50-70 40-50
16 20
16 20
高速钢
φ25高速钢立铣 4刃
260-360
60-100
20
10
φ32高速钢立铣 4刃
200-260
60-100
20
10
φ36高速钢立铣 4刃
180-200
60-100
20
10
φ30立铣
4刃
320-420
60-100
20
φ32立铣
专门试验的
φ2钻头
s4600 琢钻每次钻深0.3mm F30 最深60mm 高速钢
常用铰刀切削参数参照表
加工材料 钢
铰刀直径d(mm)
<10 10-20
切削深度 进给量 a(mm) f(mm/r)
0.08-0.12 0.15-0.25 0.12-0.15 0.20-0.35
切削速度v(m/min) 6-12
800
60
800
20
700
50
400
60
400
80
120
40-50
120
40-50
用途
钻孔 扩孔 钻孔 钻孔 扩孔 精铰孔 精铰孔
立铣刀加工参数

立铣刀加工参数
立铣刀是一种常用的金属加工工具,它广泛应用于机械制造、航空航天、汽车制造等领域。
在使用立铣刀进行加工时,合理的加工参数对于加工质量和效率起着至关重要的作用。
刀具的转速是一个重要的参数。
转速过高可能会导致刀具磨损加剧,甚至断刀,转速过低则会影响加工效率。
因此,在选择转速时需要考虑工件材料的硬度、加工深度等因素,并根据经验进行合理的调整。
进给速度也是一个关键参数。
进给速度过快会导致刀具负荷过大,容易造成刀具磨损和加工表面粗糙度增加。
而进给速度过慢则会降低加工效率。
因此,根据刀具的切削能力和工件的要求,选择合适的进给速度非常重要。
切削深度也是一个需要考虑的因素。
切削深度过大容易引起振动和切削力增大,对刀具寿命和加工质量都有不利影响。
而切削深度过小则会降低加工效率。
因此,根据工件的要求和刀具的切削能力,选择适当的切削深度是必要的。
除了上述参数外,还有一些其他的加工参数也需要注意。
例如切削速度、切削角度等。
切削速度是指刀具在单位时间内切削的长度,它与转速和进给速度有关。
切削角度则是刀具与工件表面的夹角,它会影响切削力和加工表面质量。
立铣刀的加工参数对于加工质量和效率都有着重要影响。
合理选择转速、进给速度、切削深度等参数,可以提高加工效率,保证加工质量。
同时,根据具体情况进行调整和优化,也是提高加工效果的关键。
希望以上内容对您有所帮助。
07数控加工刀具参数表
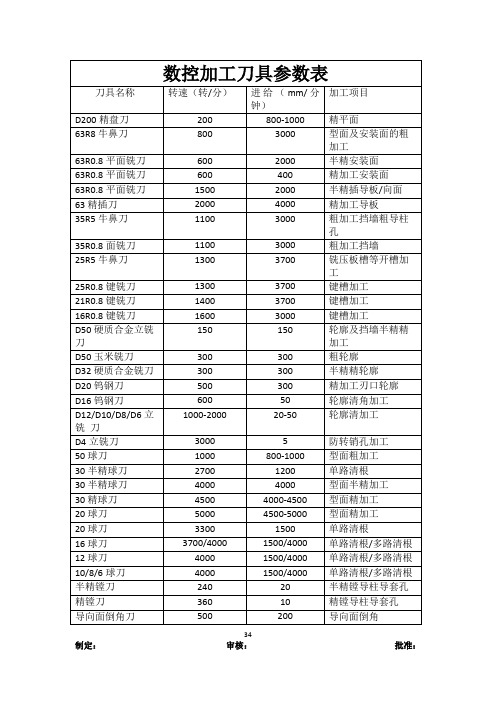
10/8/6球刀
4000
1500/4000
单路清根/多路清根
半精镗刀
240
20
半精镗导柱导套孔
精镗刀
360
10
精镗导柱导套孔
导向面倒角刀
500
200
导向面倒角
2000
4000
精加工导板
35R5牛鼻刀
1100
3000
粗加工挡墙粗导柱孔
35R0.8面铣刀
1100
3000
Байду номын сангаас粗加工挡墙
25R5牛鼻刀
1300
3700
铣压板槽等开槽加工
25R0.8键铣刀
1300
3700
键槽加工
21R0.8键铣刀
1400
3700
键槽加工
16R0.8键铣刀
1600
3000
键槽加工
D50硬质合金立铣刀
150
150
轮廓及挡墙半精精加工
D50玉米铣刀
300
300
粗轮廓
D32硬质合金铣刀
300
300
半精精轮廓
D20钨钢刀
500
300
精加工刃口轮廓
D16钨钢刀
600
50
轮廓清角加工
D12/D10/D8/D6立铣刀
1000-2000
20-50
轮廓清加工
D4立铣刀
3000
5
防转销孔加工
50球刀
1000
800-1000
型面粗加工
30半精球刀
2700
1200
单路清根
30半精球刀
4000
4000
切削参数表(铣刀)
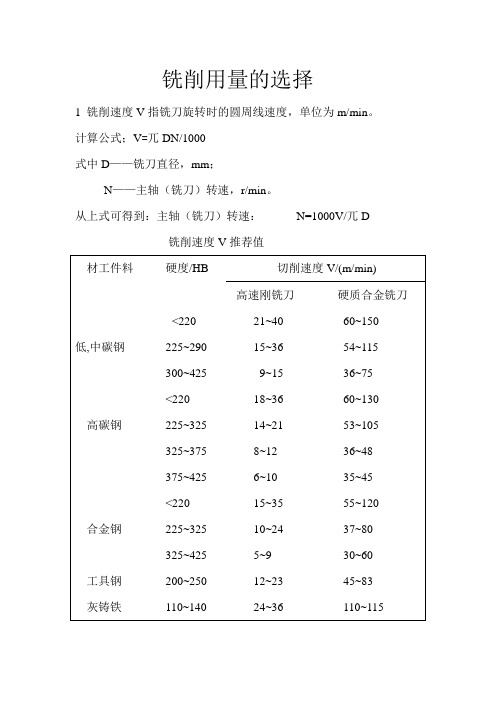
铣削用量的选择
1 铣削速度V指铣刀旋转时的圆周线速度,单位为m/min。
计算公式;V=兀DN/1000
式中D——铣刀直径,mm;
N——主轴(铣刀)转速,r/min。
从上式可得到:主轴(铣刀)转速:N=1000V/兀D
铣削速度V推荐值
2进给量
在铣削过程中,工件相对于铣刀的移动速度称为进给量.有三种表示方法:
铣刀每转过一个齿,工件沿进.给方向移动的距离, (1) 每齿进给量a
f
单位为mm/z。
(2) 每转进给量f铣刀每转过一转, 工件沿进.给方向移动的位为距
离, 单位为mm/r.。
(3) 每分钟进给量V f铣刀每旋转1min, 工件沿进.给方向移动的位为距离, 单位为mm/ min。
.
zn
三种进给量的关系为: V f=a
f
——每齿进给量,mm/z。
.
式中a
f
z——铣刀(主轴)转速,r/min。
n——铣刀齿数.。
(mm/z.) 推荐值
铣刀每齿进给量, a
f
3铣削层用量
铣刀在一次进给中所切掉工件表面的宽度,单位为(1)铣削宽度a
e
mm。
.
一般立铣刀和端铣刀的铣削宽度约为铣刀直径的50%~60%左右。
(切削深度) 铣刀在一次进给中所切掉工件表面的厚(2)背吃刀量a
p
度,即工件的已加工表面和待加工表面间的垂直距离,单位为mm。
一般立铣刀粗铣时的背吃刀量以不超过铣刀半径为原则,以防背吃刀量过大而造成刀具的损坏,精铣时约为0.05~0.30mm;端铣刀粗铣
时约为2~5mm,精铣时约为0.10~0.50mm.。
06整体式硬质合金立铣刀切削参数简表

最小最大<0.25%C 退火125(-)220230≥0.25%C 退火190(11)170190<0.55%C 淬火和回火250(24.5)140150≥0.55%C 退火220(18)140150≥0.55%C 淬火和回火300(32)120130最小最大最小最大退火200(13.8)140150Fz Fz Fz Fz 淬火和回火275(28)10011010.0030.00510.0030.007淬火和回火300(32)1101201.30.0030.01 1.30.0030.012P 非合金钢和铸钢、易切削钢D(mm)铣槽D(mm)方肩铣/仿型铣低合金钢和铸钢(所有合金元素比例低于5%)标准切削条件材 质条件布氏硬度(HB)≈(HRC)Vc (m/min)淬火和回火350(37.9)1201301.50.0030.02 1.50.0030.022退火200(13.8)110130 1.80.0050.025 1.80.0050.028淬火和回火325(34.5)607020.0050.0320.0050.033铁素体/马氏体200(13.8)1001702.30.0050.03 2.30.0050.033马氏体型240(22.8)601502.50.0050.03 2.50.0050.03奥氏体型180(8)701002.80.010.035 2.80.010.038铁素体/珠光体180(8)7022030.010.0430.010.044珠光体260(26.6)1102003.30.0150.04 3.30.010.044铁素体型160(3.2)13023040.0150.04540.0150.049珠光体250(24.5)702304.30.020.045 4.30.0150.049铁素体型130(-)13023050.0250.0550.020.055珠光体230(20.5)11020060.030.0660.0250.066M 不锈钢和铸钢K 球墨铸铁GGG 灰口铸铁GG 可锻铸铁高合金钢、铸钢和工具钢标准切削条件未固化6067070070.030.0770.030.077固化10061069080.030.0880.030.088≤12%Si 未固化7567070090.030.0890.030.088固化90610690100.0350.09100.030.098>12%Si 高温130270280120.040.1120.0350.108>1%Pb 易切削110330350140.050.11140.040.119黄铜90330350160.050.12160.050.13电解铜100230250180.050.13180.050.14---200.050.15200.050.17---250.060.15250.060.18N 变形铝合金铸造铝,铝合金铜合金非金属硬质塑料、纤维塑料硬质橡胶铁基退火200(13.8)2030铁基固化280(29)2020镍基或铜基退火250(24.5)2030镍基或铜基固化350(37.9)2020镍基或铜基铸造320(34.2)3060RM4003060RM10503060淬火55HRC 3040淬火60HRC 3030冷硬铸铁铸铁400(43.1)5060铸铁淬火55HRC 30403、粗铣用ap 最大=1.5D V=1.25×Vc 高速切削高硬度材料(硬度最高HRC60):使用小切深:Vc 为80~160m/min 时,ap 等于0.1~0.3mm 1、铣槽用M 型材料--ap 最大=0.5D S 型材料--ap 最大=0.25D 2、精铣用P 型材料--ap 最大=1.5D S 高温合金钛和钛合金α-β固化合金H 淬火钢。
铣刀加工工艺参数表

在铰孔加工过程中,经常出现孔径超差、内孔表面粗糙度值高等诸多问题。
问题产生的原因孔径增大,误差大铰刀外径尺寸设计值偏大或铰刀刃口有毛刺;切削速度过高;进给量不当或加工余量过大;铰刀主偏角过大;铰刀弯曲;铰刀刃口上粘附着切屑瘤;刃磨时铰刀刃口摆差超差;切削液选择不合适;安装铰刀时锥柄表面油污未擦干净或锥面有磕碰伤;锥柄的扁尾偏位装入机床主轴后锥柄圆锥干涉;主轴弯曲或主轴轴承过松或损坏;铰刀浮动不灵活;与工件不同轴;手铰孔时两手用力不均匀,使铰刀左右晃动。
孔径缩小铰刀外径尺寸设计值偏小;切削速度过低;进给量过大;铰刀主偏角过小;切削液选择不合适;刃磨时铰刀磨损部分未磨掉,弹性恢复使孔径缩小;铰钢件时,余量太大或铰刀不锋利,易产生弹性恢复,使孔径缩小;内孔不圆,孔径不合格。
铰出的内孔不圆铰刀过长,刚性不足,铰削时产生振动;铰刀主偏角过小;铰刀刃带窄;铰孔余量偏;内孔表面有缺口、交叉孔;孔表面有砂眼、气孔;主轴轴承松动,无导向套,或铰刀与导向套配合间隙过大;由于薄壁工件装夹过紧,卸下后工件变形。
孔的内表面有明显的棱面铰孔余量过大;铰刀切削部分后角过大;铰刀刃带过宽;工件表面有气孔、砂眼;主轴摆差过大。
内孔表面粗糙度值高切削速度过高;切削液选择不合适;铰刀主偏角过大,铰刀刃口不在同一圆周上;铰孔余量太大;铰孔余量不均匀或太小,局部表面未铰到;铰刀切削部分摆差超差、刃口不锋利,表面粗糙;铰刀刃带过宽;铰孔时排屑不畅;铰刀过度磨损;铰刀碰伤,刃口留有毛刺或崩刃;刃口有积屑瘤;由于材料关系,不适用于零度前角或负前角铰刀。
铰刀的使用寿命低铰刀材料不合适;铰刀在刃磨时烧伤;切削液选择不合适,切削液未能顺利地流动切削处;铰刀刃磨后表面粗糙度值太高。
铰出的孔位置精度超差导向套磨损;导向套底端距工件太远;导向套长度短、精度差;主轴轴承松动。
铰刀刀齿崩刃铰孔余量过大;工件材料硬度过高;切削刃摆差过大,切削负荷不均匀;铰刀主偏角太小,使切削宽度增大;铰深孔或盲孔时,切屑太多,又未及时清除;刃磨时刀齿已磨裂。
刀具基本切削参数表
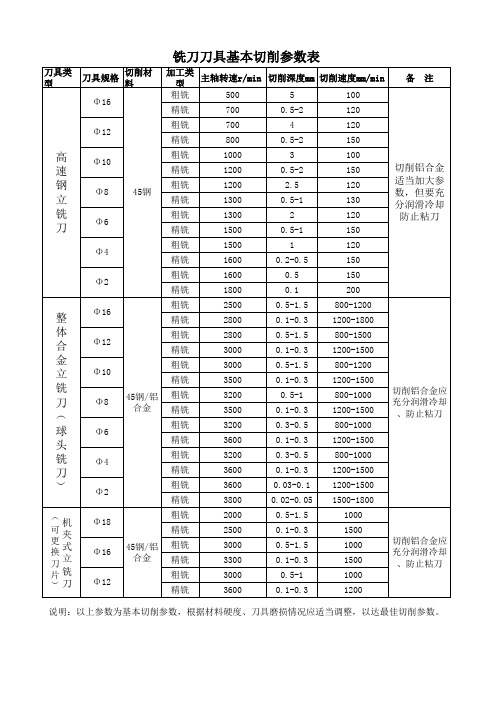
120
防止粘刀
精铣
1500
0.5-1
150
粗铣
1500
1
120
精铣
1600
0.2-0.5
150
粗铣
1600
0.5
150
精铣
1800
0.1
200
粗铣
2500
0.5-1.5
800-1200
精铣
2800
0.1-0.3
1200-1800
粗铣
2800
0.5-1.5
800-1500
精铣
3000
0.1-0.3
1200-1500
说明:以上参数为基本切削参数,根据材料硬度、刀具磨损情况应适当调整,以达最佳切削参数。
刀具类 型
高 速 钢 立 铣 刀
整 体 合 金 立 铣 刀 (
球 头 铣 刀 )
(机
可 更 换 刀
夹 式 立
片铣
)刀
刀具规格
切削材 料
Φ16
Φ12
Φ10
Φ8
45钢
Φ6
Φ4
Φ2
Φ16
Φ12
Φ10
Φ8
45钢/铝 合金
Φ6
Φ4
Φ2
Φ18
Φ16
45钢/铝 合金
Φ12
铣刀刀具基本切削参数表
加工类 型
主轴转速r/min
1500 1000 1500 1000
切削铝合金应 充分润滑冷却 、防止粘刀
精铣
3600
0.1-0.3
1200
说明:以上参数为基本切削参数,根据材料硬度、刀具磨损情况应适当调整,以达最佳切削参数。
铣刀刀具基本切削参数表
- 1、下载文档前请自行甄别文档内容的完整性,平台不提供额外的编辑、内容补充、找答案等附加服务。
- 2、"仅部分预览"的文档,不可在线预览部分如存在完整性等问题,可反馈申请退款(可完整预览的文档不适用该条件!)。
- 3、如文档侵犯您的权益,请联系客服反馈,我们会尽快为您处理(人工客服工作时间:9:00-18:30)。
立铣刀参数
铣刀种类及直径代木铝钢铜
转速 S 进给 F 转速 S 进给 F 转速 S 进给 F 转速 S 进给 F
立铣刀 0.5 3500 1000 3500 1000 3500 1000 3500 1000 立铣刀 1 3500 1000 3500 500 3500 500 3500 500 立铣刀 2 3500 1600 3500 1500 3500 1000 3200 800 立铣刀 4 3300 2000 3500 2000 3500 1500 3200 1600 立铣刀 6 3200 2000 3500 2800 3500 1800 3000 2000 立铣刀 8 3000 2000 3000 2800 2800 1800 2800 2200 立铣刀 10 2800 2000 2700 2800 2500 1800 2500 2000 立铣刀 12 2000 2800 2000 3000 1800 2500 2200 2000 立铣刀 16 1000 2000 1600 2000 1300 2000 1800 1800 立铣刀 20 900 1200 800 1800 750 1000 700 1000 立铣刀 25 850 1000 750 1100 700 900 700 950 球头立铣刀 0.5 3500 6000 3500 6000 3500 1000 3500 1000
球头立铣刀 1 3500 6000 3500 3500 3500 300 3500 3500
球头立铣刀 2 3500 6000 3500 1000 3500 600 3500
1000
球头立铣刀 3 3500 6000 3500 1000 3500 800 3500 1500
球头立铣刀 4 3500 6000 3500 1000 3500 800 3200 1000
球头立铣刀 6 3500 6000 3500 800 3500 800 3000 1000
最佳答案常用計算公式
一、三角函數計算
1.tan θ=b/a θ=tan-1b/a
2.Sin θ=b/c Cos=a/c
二、切削刃上选定点相对于工件的主运动的瞬时速度。
2.1 铣床切削速度的計算
V c =(π*D *S /1000
Vc :線速度(m/min π:圓周率 (3.14159 D:刀具直徑 (mm 例題 . 使用Φ25的銑刀Vc 為 (m/min25 求 S=?rpm
Vc=πds/1000
25=π*25*S/1000
S=1000*25/ π*25
S=320rpm
2.2 车床切削速度的計算
计算公式如下v c=( πd w n /1000 (1-1
式中 v c ——切削速度 (m/s ;
dw ——工件待加工表面直径(mm ;
n ——工件转速(r/s 。
S :轉速 (rpm
三、進給量 (F值的計算
F=S*Z*F z
F :進給量 (mm/min S:轉速 (rpm Z:刃數
F z :(實際每刃進給
例題 . 一標準 2刃立銑刀以 2000rpm 速度切削工件,求進給量 (F 值為多少? (F z=0.25mm
F=S*Z*F z
F=2000*2*0.25
F=1000(mm/min
四、殘料高的計算
Scallop =(ae *ae /8R
Scallop :殘料高 (mm ae:XY pitch(mm R刀具半徑 (mm
例題. Φ20R10精修 2枚刃,預殘料高 0.002mm ,求 Pitch 為多少? mm
Scallop=ae2/8R
0.002=ae2/8*10
ae=0.4mm
五、逃料孔的計算
Φ=√2R 2X、Y=D/4
Φ:逃料孔直徑 (mm R刀具半徑 (mm D:刀具直徑 (mm 例題 . 已知一模穴須逃角加工 (如圖 ,
所用銑刀為ψ10;請問逃角孔最小
為多少?圓心座標多少?
Φ=√2R 2
Φ=√2*52
Φ=7.1(mm
X、Y=D/4
X、Y=10/4
X、Y=2.5 mm
圓心座標為 (2.5,-2.5
六、取料量的計算
Q=(ae *ap *F/1000
Q:取料量 (cm3/minae :XY pitch(mm ap:Z pitch(mm 例題 . 已知一模仁須 cavity 等高加工, Φ35R5的刀 XY pitch是刀具的 60%
,每層切 1.5mm ,進給量為 2000mm/min, 求此刀具的取料量為多少?
Q=(ae *ap *F/1000
Q=35*0.6*1.5*2000/1000
Q=63 cm3/min
七、每刃進給量的計算
F z =h m * √ (D/ap
F z :實施每刃進給量 h m :理論每刃進給量 ap :Z pitch(mm D :刀片直徑 (mm
例題 (前提 depo XY pitch是刀具的 60%
depo Φ35R5的刀, 切削 NAK80材料h m 為 0.15mm , Z 軸切深 1.5mm , 求每刃進給量為多少?
F z =h m * √ (D/ap
F z =0.2*√ 10/1.5
F z =0.5mm
沖模刀口加工方法刀口加工深度=板厚-刀口高+鉆尖(0.3D)D表示刀徑鑽頭鑽孔時間公式T(min)=L(min)/N(rpm)*f(mm/rev)=π DL/1000vfL:鑽孔全長D:鑽頭直徑如圖孔深lN:回轉數v:切削速度鑽頭孔全長L則L=l+D/3f:進刀量系數T=L/Nf=π DL/1000vf系數表f直徑mm進刀mm/rev 1.6~3.2 0.025~0.075 3.2~6.4 0.05~0.15 6.4~12.8 12.8~25 25 以上 0.10~0.25 0.175~0.375
0.376~0.625 1英寸=25.4mm=8分25.4/牙數=牙距例如25.4/18=1.414管牙計算公式牙距為5/16絲攻馬力(槍鑽)W=Md*N/97.410
W:所要動力(KW)Md:扭矩(kg-cm)N:回轉數(r.p.m)扭矩計算公式如下:Md=1/20*f*ps*f為進給量mm/rev系數r為鑽頭半徑賽(mm)α :切削抵抗比值ps.在小進給時,一般鋼為500kg/m㎡;一般鑄鐵為300kg/m㎡;说说常用立铣刀具参数的确定原则。
答:(1 刀具半径 r 应小于零件内轮廓面的最小曲率半径 r ,一般取 r =(0.8~0.9)r; (2 零件的加工高度 H =(1/4~1/6)r,以保证刀具有足够的刚度; (3 对深槽孔,选取 l = H+(5~10)mm。
l 为刀具切削部分长度,H 为零件高度; (4 加工外形及通槽时,选取 l =H+re+(5~10)mm。
re 为刀尖转角半径;
(5 粗加工内轮廓面时,铣刀最大直径 D 粗可按下式计算 D粗 =2x +D 式中 D ------ 轮廓的最小凹圆角半径 d ------- 圆角邻边夹角等分线上的精加工余量 d1 ----- 精
加工余量 j ------ 圆角两邻边的最小夹角 (6 加工肋时,刀具直径为 D =(5~10)b (b 为肋的厚度)。