一篇关于切削加工表面残余应力研究的好文章
高速车轴车削加工表面残余应力的研究
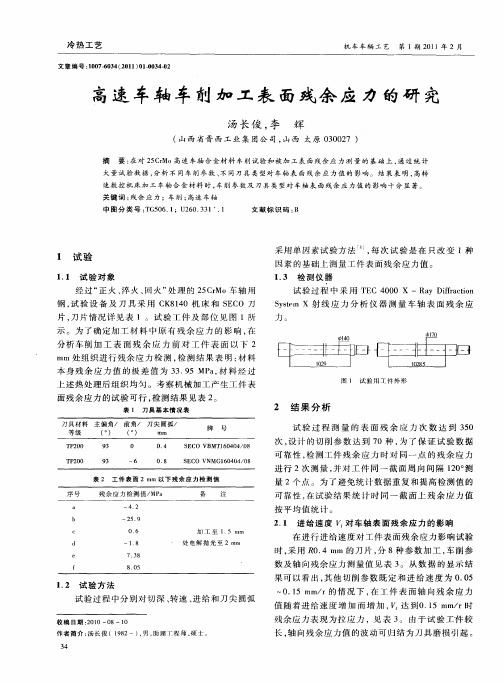
可靠性 , 检测 工件 残余 应 力 时对 同一 点 的残 余 应力
进 行 2次 测 量 , 对 工 件 同 一 截 面 周 向 间 隔 1 0 测 并 2。
表 2 工 件 表面 2 m 以 下 残余 应 力 检 测 值 m
摘 要 : 对 2CM 在 5 r o高 速 车轴 合 金 材 料 车 削试 验 和被 加 _ 表 面 残余 应 力 测 量 的 基 础 上 . T - 通过 统 计
大量 试 验 数 据 , 分析 不 同 车 削参 数 、 同 刀具 类 型 对 车 轴 表 面残 余 应 力值 的 影 响 。 结 果 表 明 , 不 高转
刀 片 ,6个 值 利 用 R . m 刀 片 , 图 3 数 据 表 2 0 4m 见 。 明 较 为 锋 利 的 R . 0 4 mm 刀 片 易 在 工 件 表 面 产 生 残
余压应 力 。R . 0 8mm 的刀 片 使 工 件 表 面 易 于 产 生 拉应 力 , 当然 刀尖 圆 弧 只是 控 制 残 余 应 力 的条 件 之
上 述 热 处 理 后 组 织 均 匀 。 考 察 机 械 加 工 产 生 工 件 表
图 1 试 验 用 工件 外 形
面残 余应力 的试 验可行 , 检测 结果见 表 2 。
表 1 刀 具 基 本 情 况 表
2 结 果 分 析
试 验 过 程 测 量 的表 面残 余 应 力 次 数 达 到 3 0 5
一
,
能否产 生利 于工 件 表 面疲 劳 强 度 的残 余 压 应 力
2 2 切 削 深 度 对 车 轴 轴 向 残 余 应 力 的 影 响 .
超细硬质合金磨削表面残余应力的实验研究

其加工和残余应力测试与调整,yuanyg@ dhu. edu. cn
目前,使用金刚石砂轮的磨削加工仍然是硬质 合金最主要的加工方法。然而,由于超细硬质合金 材料的高硬度和高脆性,加工过程中刀具磨削表面 易产生裂 纹,影 响 产 品 的 强 度 与 使 用 寿 命[2,3]。 许 多研究表 明,残 余 应 力 是 磨 削 裂 纹 产 生 的 主 要 原 因[4 ~ 7]。但至今为止,国内外对超细硬质合金的研 究大多集中于材料物理性能的改进和烧结质量的控 制方面,而对超细硬质合金的磨削加工,尤其是磨削 表面残余应力研究甚少[8,9]。为了保证刀具的磨削 质量,延长其使用寿命,很有必要对超细硬质合金磨 削表面残余应力开展深入的研究。为此,本文作者
此,试样原始 应 力 状 态 对 磨 削 表 面 残 余 应 力 的 影
响并不大 ( 见 表 3 ) ,磨 削 表 面 残 余 应 力 主 要 是 磨
削过程中产生的磨削残余应力。
材料磨 削 过 程 中,有 多 种 工 艺 因 素,如 磨 削
热 、相 变 以 及 磨 削 力 作 用 下 的 不 均 匀 塑 性 变 形 等 ,
图 2 切削深度对磨削表面残余应力 的影响( 砂轮粒度: 150#)
图 3 超细硬质合金磨削表面的 X 射线衍射谱线
第7 期
原一高等: 超细硬质合金磨削表面残余应力的实验研究
1219
对磨削前后超细硬质合金试样表面进行了 X 射线衍射( XRD) 分析,图 3 所示为用 150 #砂轮、αp = 20 μm 磨削后试样磨削表面的 X 射线衍射谱线。 由图可见,试样磨削表面物相主要是由 WC 和少量 Co 相构成,与磨削前比并无明显的变化。
难加工材料硬态干车削中切削参数对残余应力的影响
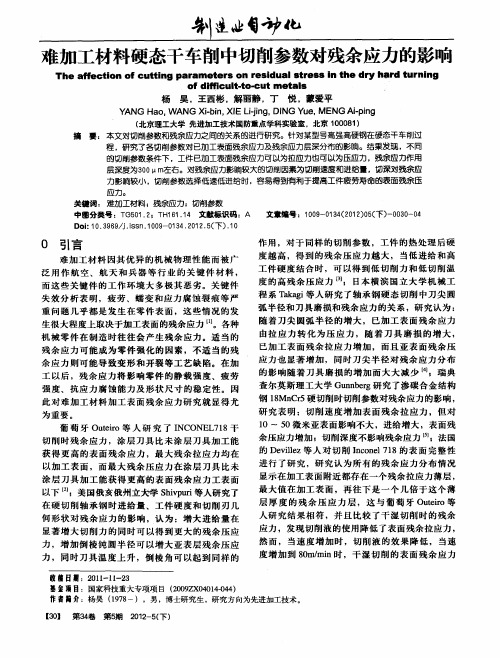
随 着 刀尖 圆弧 半 径 的增 大 ,已 加 工 表 面残 余 应 力 由 拉 应 力 转 化 为 压 应 力 ,随 着 刀具 磨 损 的 增 大 , 已 加 工 表面 残 余 拉 应 力增 加 ,而且 亚 表面 残余 压 应 力也 显著 增 加 ,同 时 刀尖 半 径 对 残 余 应 力分 布 的 影 响 随 着 刀具 磨 损 的 增 加 而 大 大 减 少 ;瑞 典
( 北京 理工大学 先进加工技术国防重点学科实验 室 .北京 1 0 8 ) 0 0 1
摘
要 : 本文对切 削参 数和残余 应力之间的 关系的进行研 究。针对某型号 高强高硬钢在 硬态干车削过 程 ,研究 了各切削参数 对已加工表面残 余应力及残余 应力层深分布 的影响 。结果 发现 ,不 同 的切削参 数条件下 ,工件已加工表面残 余应力可 以为拉应力也 可以为压应 力 ,残余应力作用 层深度为 30 m 0 左右 。对残 余应力影响较大 的切 削因素为切削速度和进给 量 ,切深对残 余应 力影 响较小 ,切 削参数选择低 速低进给 时,容 易得到有利于提 高工件疲劳 寿命 的表面残 余压
余压 应力增 加 ;切 削深 度不影 响残 余 应力 L;法 国 5 】 的 Deie vl z等 人 对 切 削 Ic nl 1 l n o e 7 8的 表 面 完 整 性
此 对 难 加 工 材料 加 工 表面 残 余 应 力 研 究 就 显o等 人 研 究 了 I O L 1 i NC NE 7 8干
I
訇 地
难加工材 料硬态千车削中切削参数对残余应 力的影响
The f ecton ofcut i ar a i tng p am et s on r i aI r er es du ess i he y har ur ng st n t dr d t ni
硬态切削表面残余应力分析研究
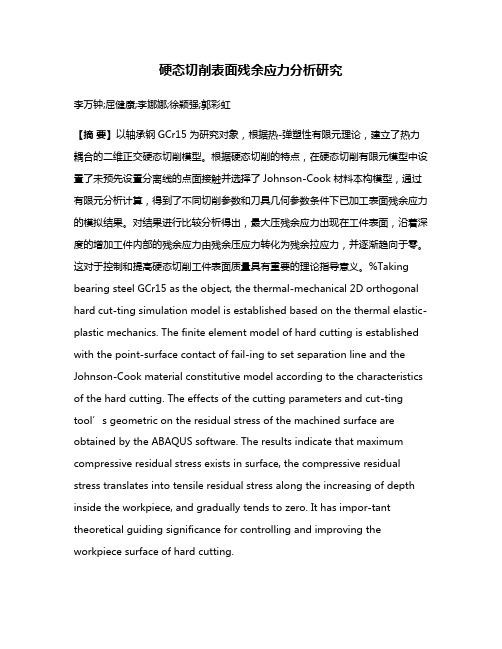
硬态切削表面残余应力分析研究李万钟;屈健康;李娜娜;徐颖强;郭彩虹【摘要】以轴承钢GCr15为研究对象,根据热-弹塑性有限元理论,建立了热力耦合的二维正交硬态切削模型。
根据硬态切削的特点,在硬态切削有限元模型中设置了未预先设置分离线的点面接触并选择了Johnson-Cook材料本构模型,通过有限元分析计算,得到了不同切削参数和刀具几何参数条件下已加工表面残余应力的模拟结果。
对结果进行比较分析得出,最大压残余应力出现在工件表面,沿着深度的增加工件内部的残余应力由残余压应力转化为残余拉应力,并逐渐趋向于零。
这对于控制和提高硬态切削工件表面质量具有重要的理论指导意义。
%Taking bearing steel GCr15 as the object, the thermal-mechanical 2D orthogonal hard cut-ting simulation model is established based on the thermal elastic-plastic mechanics. The finite element model of hard cutting is established with the point-surface contact of fail-ing to set separation line and the Johnson-Cook material constitutive model according to the characteristics of the hard cutting. The effects of the cutting parameters and cut-ting tool’s geometric on the residual stress of the machined surface are obtained by the ABAQUS software. The results indicate that maximum compressive residual stress exists in surface, the compressive residual stress translates into tensile residual stress along the increasing of depth inside the workpiece, and gradually tends to zero. It has impor-tant theoretical guiding significance for controlling and improving the workpiece surface of hard cutting.【期刊名称】《航空制造技术》【年(卷),期】2015(000)006【总页数】5页(P64-68)【关键词】硬态切削;热力耦合;温度场;残余应力;有限元【作者】李万钟;屈健康;李娜娜;徐颖强;郭彩虹【作者单位】西北工业大学机电学院;西北工业大学机电学院;西北工业大学机电学院;西北工业大学机电学院;中航光电科技股份有限公司【正文语种】中文随着切削技术的发展,尤其是超硬刀具材料陶瓷、聚晶立方氮化硼(PCBN)的出现,使得精密切削加工淬硬钢成为可能,产生了“以车带磨”的硬态切削加工技术。
几何缺陷和残余应力

几何缺陷和残余应力全文共四篇示例,供读者参考第一篇示例:随着科技的进步和工业的发展,几何缺陷和残余应力已经成为工程设计和制造过程中需要重点关注的问题之一。
几何缺陷和残余应力对材料的性能和可靠性有着重要影响,因此需要认真分析和有效控制。
让我们先来了解一下什么是几何缺陷和残余应力。
几何缺陷是指材料或产品在制造过程中出现的形状、尺寸、表面质量不合格的问题。
几何缺陷可能是由于材料的选择、工艺参数的控制不当或者生产设备的失效等原因造成的。
几何缺陷会导致产品的性能下降,甚至在使用过程中出现故障,对产品的可靠性和安全性造成威胁。
而残余应力是指在材料制造或加工过程中,由于内部应力不完全释放所产生的残余应力。
残余应力的产生与材料的加工方式、工艺流程、热处理过程密切相关。
残余应力会导致材料的变形、开裂,甚至影响产品的使用寿命。
针对几何缺陷和残余应力,工程技术人员需要采取一系列有效的措施来进行分析和控制。
对于几何缺陷,工程技术人员应该加强对材料选择和工艺参数控制的重要性认识。
合理的材料选择和严格的工艺控制可以有效降低几何缺陷的发生率,提高产品的质量和可靠性。
建立完善的检测和检验制度也是很重要的,及时发现和解决几何缺陷问题。
对于残余应力,工程技术人员需要深入研究材料的物理性能和结构特点,合理调整材料加工工艺,降低残余应力的产生。
采用适当的热处理和应力释放技术也可以有效地降低残余应力的大小,提高材料的可靠性和稳定性。
在实际工程设计和制造中,我们应该密切关注几何缺陷和残余应力的问题,制定相应的分析和控制方案,确保产品的质量和性能符合要求。
只有不断改进和提高我们的技术水平,才能在激烈的市场竞争中立于不败之地。
【2000字】第二篇示例:几何缺陷和残余应力是固体材料中常见的两种问题,它们会对材料的性能和使用寿命产生影响。
几何缺陷指的是材料中存在的形状不规则或者尺寸不符合要求的问题,而残余应力则是由于材料加工或者热处理过程中所产生的内部应力。
车轴加工表面残余应力分析
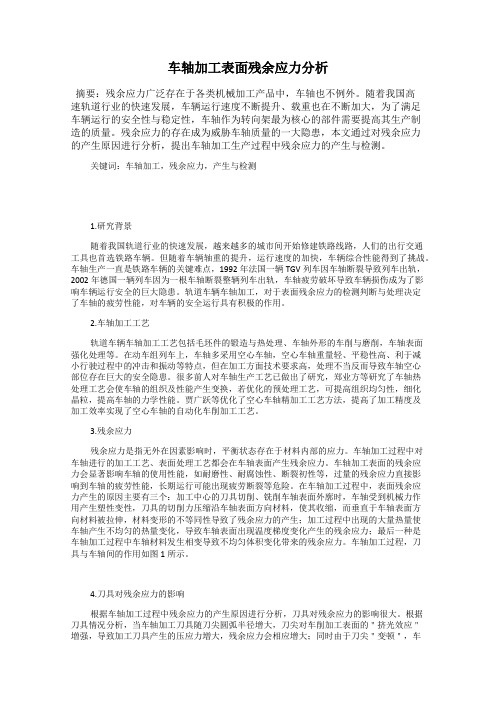
车轴加工表面残余应力分析摘要:残余应力广泛存在于各类机械加工产品中,车轴也不例外。
随着我国高速轨道行业的快速发展,车辆运行速度不断提升、载重也在不断加大,为了满足车辆运行的安全性与稳定性,车轴作为转向架最为核心的部件需要提高其生产制造的质量。
残余应力的存在成为威胁车轴质量的一大隐患,本文通过对残余应力的产生原因进行分析,提出车轴加工生产过程中残余应力的产生与检测。
关键词:车轴加工,残余应力,产生与检测1.研究背景随着我国轨道行业的快速发展,越来越多的城市间开始修建铁路线路,人们的出行交通工具也首选铁路车辆。
但随着车辆轴重的提升,运行速度的加快,车辆综合性能得到了挑战。
车轴生产一直是铁路车辆的关键难点,1992年法国一辆TGV列车因车轴断裂导致列车出轨,2002年德国一辆列车因为一根车轴断裂整辆列车出轨,车轴疲劳破坏导致车辆损伤成为了影响车辆运行安全的巨大隐患。
轨道车辆车轴加工,对于表面残余应力的检测判断与处理决定了车轴的疲劳性能,对车辆的安全运行具有积极的作用。
2.车轴加工工艺轨道车辆车轴加工工艺包括毛坯件的锻造与热处理、车轴外形的车削与磨削,车轴表面强化处理等。
在动车组列车上,车轴多采用空心车轴,空心车轴重量轻、平稳性高、利于减小行驶过程中的冲击和振动等特点,但在加工方面技术要求高,处理不当反而导致车轴空心部位存在巨大的安全隐患。
很多前人对车轴生产工艺已做出了研究,郑业方等研究了车轴热处理工艺会使车轴的组织及性能产生变换,若优化的预处理工艺,可提高组织均匀性,细化晶粒,提高车轴的力学性能。
贾广跃等优化了空心车轴精加工工艺方法,提高了加工精度及加工效率实现了空心车轴的自动化车削加工工艺。
3.残余应力残余应力是指无外在因素影响时,平衡状态存在于材料内部的应力。
车轴加工过程中对车轴进行的加工工艺、表面处理工艺都会在车轴表面产生残余应力。
车轴加工表面的残余应力会显著影响车轴的使用性能,如耐磨性、耐腐蚀性、断裂初性等,过量的残余应力直接影响到车轴的疲劳性能,长期运行可能出现疲劳断裂等危险。
金属切削加工表面层的残余应力及其处理方法
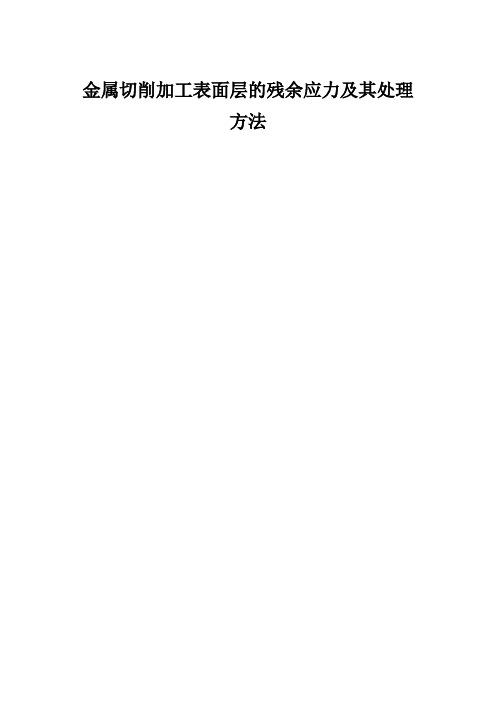
金属切削加工表面层的残余应力及其处理方法金属切削加工表面层的残余应力加工金属表面残余应力的大小、方向及分布情况就是表面完整性的重要评价指标之一,除此之外,表面完整性的评价指标还有表面形貌(包括表面粗糙度、表面波纹度和纹理)、表面缺陷(包括宏观裂纹、伤痕、腐蚀)、微观组织(包括微观裂纹、晶粒大小、晶间腐蚀)和表层其他工程技术特性。
在这里我简单谈谈金属切削加工中表面残余应力产生及其类型。
机械加工过程是一个复杂的过程,受众多因素的影响(以铣削加工为例见下图)因此产生复杂的应力变化,造成工件的质量不可保证,甚至变形。
机械加工中工件表面层组织发生变化时,在表面及其与基体材料的交界处就会产生相互平衡的弹性应力,这种应力即是表面层的残余应力。
它的产生主要有三种原因:◇冷态塑性变形◇热态塑性变形◇局部金相组织变化实际切削加工后表面层的残余应力是上述三方面原因的综合结果。
冷态塑性变形占主导地位时,表面层会产生残余压应力;当热塑性变形占主导地位时,表面层会产生残余拉应力。
2.其处理方法机加工中工件表面残余应力的产生主要受三个因素的制约:机械力引起的塑性变形、热应力引起的塑性变形和相变引起的体积变化。
在机械应力的作用下表面层发生塑性流动和延展现象,而里层金属的弹性恢复变形受到已塑性变形表面金属的牵制,表面产生残余压应力。
磨削中产生的工件表面的高温,使表面层进入完全塑性状态,工件冷却后表面层金属收缩受到里层金属的牵制,使表面产生残余拉应力。
当砂轮与工件接触区温度达到金属相变温度后,表面组织发生金相组织变化,其表面残余应力的性质,随磨削前后金相组织的变化而变化。
已加工表面内残余应力的产生是综合以上几个因素共同作用的结果。
在一般磨削过程中,比压和摩擦较大,产生的磨削区温度较高。
工件表面常常因热塑性变形而产生残余拉应力。
对此,有针对性地降低磨削表面的温度,减少由此产生的塑性变形,就能抑制残余拉应力的产生,甚至会产生残余压应力。
铸造件切削加工残余应力及变形机理研究

Th s a c fCa tn sPa t a h ni sdu lS r s n f r a in M e h n s e Re e r h o si g r sMm to c a im
L U S u— u I h q n
( c a ia n lcrncE gn eigD p r n fHE Me h nc l d E e t i n ie r e at t NAN P Y E HNI a o n me o OL T C C,Z e gh u4 0 4 h n zo 5 0 6,C ia hn )
t e rsd lsrs e n u tn e iu lsr s e i ee i h e me r h e iua te s sa d c ti gr sd a te s sw l d tr net e g o ty.S o t e ita d c n r lt e l m o h w o prd c n o to h
c tig r sd a te s sd srb to n c sig pat ,a d w i h u r sto f so a e rsd lsr s e o u t e iu lsrs e iti u in i a t s n t t e S pepo iin o t rg e iua te s s t n n r h n l e c h mer st e k y p n n ma hnn . n t i i fu n e t e g o ty i h e oiti c iig I hspa rf rbgs r cu a rsb s d o h iiee- e pe o i tu t r l pat a e n t efnt l e n e h o o y w er s ac hec tig r sd a te s s gv h eains i ew en r sd a te s a d d - me ttc n l g e e rh t u t e iu ls rs e , ie t e r lto hp b t e e iu lsrs n n e f r to Themo e a o uief rprv n in t e d f r a in a ptmi ai n t em a h i gpaa t r o ma in. d lh sag od g d e e to h eo o m to nd o i z to h c in r mee . n K e r s:m a h n g e iu lsr s e ;f t lm e t deo a in o a t gpa s y wo d c i i ;r sd a te s s i e ee n ; f r to fc si r n ni m n t
LY12硬铝合金高速切削加工残余应力的研究
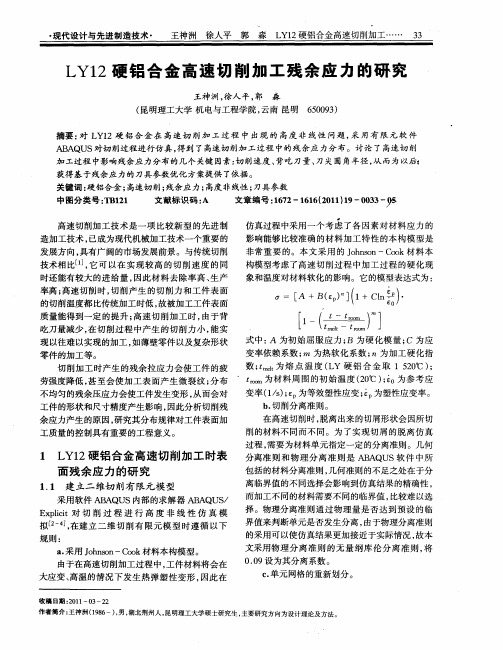
关键词 : 硬铝合金 ; 高速切 削; 残余应力; 高度非线性 ; 刀具参数 中 图分类 号 :B 2 T 11 文献标识 码 : A 文章 编号 :6 2—1 1 (0 1 1 17 6 6 2 1 )9—0 3 —9 03 s
高 速切 削加 工 技 术 是一 项 比较 新 型 的 先进 制 造 加工 技术 , 已成为 现代 机械 加工技 术 一个 重要 的 仿真 过程 中采 用 一个 考 虑 了各 因素 对材 料 应 力 的 影 响能够 比较 准 确 的材 料 加 工 特 性 的本 构 模 型 是 非 常重 要 的。本 文采 用 的 Jh sn—C o o no ok材 料 本 构模 型考 虑 了高 速切 削 过 程 中加 工 过程 的硬 化 现 象 和温度 对材 料软 化 的影 响。它 的模 型表 达式为 :
分 离准 则 和 物 理 分 离 准 则 是 AB QUS软 件 中所 A
包 括 的材料 分离 准则 , 几何 准则 的不 足之 处在 于分
离临界值的不同选择会影响到仿真结果的精确性 , 而加工 不 同 的材 料需 要不 同 的临界值 , 比较难 以选 择 。物 理分 离准 则 通 过 物 理量 是 否 达 到 预设 的 临 界值来判断单元是否发生分离 , 由于物理分离准则 的采用 可 以使仿 真结 果更 加接 近于 实际情 况 , 故本
零 件 的加 工 等 。
[+( ( ) A B ]+ ・ £ 1(_ ̄ ] 一 Lt -~ ] - 一
式中: A为初始屈服应力 ; 为硬化模量 ; B C为应 变率依赖系数 ; 为热软化系数 ; m 咒为加工硬化指
数 ; e为 熔 点 温 度 ( Y 硬 铝 合 金 取 15 0 ) l L 2℃ ; £ 为材 料 周 围 的初 始 温 度 (0 ;0为参 考 应 一 2 ̄ C) 变率 ( /)e 为 等效 塑性应 变 ; 为塑 性应 变率 。 1s ;。
高速铣削加工铝合金表面残余应力研究_唐志涛
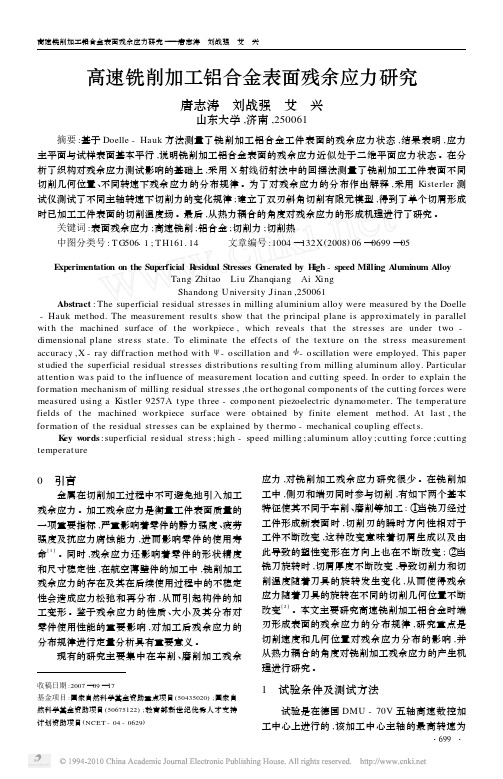
3 - 33. 7 - 36. 1 0
4 - 35. 6 11. 4
0
5
40. 7 57. 2
0
6 110. 3 125. 0
0
σ12 23. 6 - 25. 5 3. 9 12. 6 14. 3 4. 9
Key words : superficial residual st ress ; high - speed milling ; aluminum alloy ; cut ting force ; cut ting temperat ure
0 引言
金属在切削加工过程中不可避免地引入加工 残余应力 。加工残余应力是衡量工件表面质量的 一项重要指标 ,严重影响着零件的静力强度 、疲劳 强度及抗应力腐蚀能力 ,进而影响零件的使用寿 命[1] 。同时 ,残余应力还影响着零件的形状精度 和尺寸稳定性 ,在航空薄壁件的加工中 ,铣削加工 残余应力的存在及其在后续使用过程中的不稳定 性会造成应力松弛和再分布 ,从而引起构件的加 工变形 。鉴于残余应力的性质 、大小及其分布对 零件使用性能的重要影响 ,对加工后残余应力的 分布规律进行定量分析具有重要意义 。
表 1 残余应力测试条件
使பைடு நூலகம்靶材
Cr Kα靶
定峰方法
交相关法
准直器直径
3mm
X 管电压
30kV
ψ摇摆
±6°
X 管电流
6. 7mA
<摇摆
±30°
曝光时间
15s
布拉格角
139. 3°
校准
Ni 粉
倾角
±45°
衍射晶面
311 晶面
2 铣削加工铝合金表面残余应力状态分析
2. 1 X 射线法三维残余应力测试 已有的研究表明[3] , 磨削加工表面层以及加
高速铣削加工铝合金表面残余应力研究
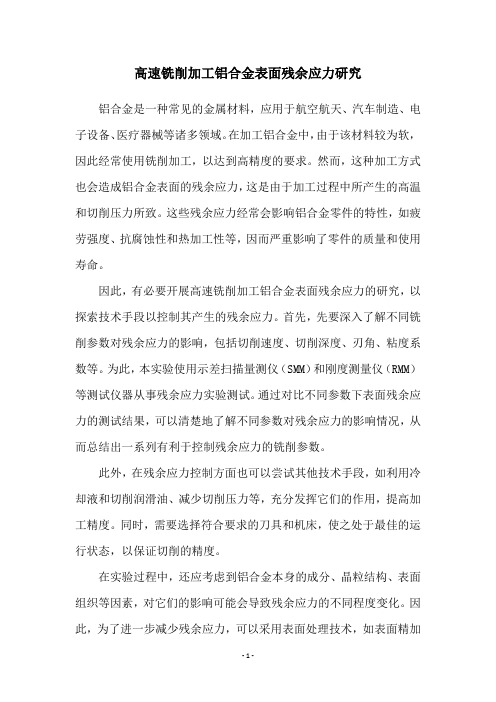
高速铣削加工铝合金表面残余应力研究铝合金是一种常见的金属材料,应用于航空航天、汽车制造、电子设备、医疗器械等诸多领域。
在加工铝合金中,由于该材料较为软,因此经常使用铣削加工,以达到高精度的要求。
然而,这种加工方式也会造成铝合金表面的残余应力,这是由于加工过程中所产生的高温和切削压力所致。
这些残余应力经常会影响铝合金零件的特性,如疲劳强度、抗腐蚀性和热加工性等,因而严重影响了零件的质量和使用寿命。
因此,有必要开展高速铣削加工铝合金表面残余应力的研究,以探索技术手段以控制其产生的残余应力。
首先,先要深入了解不同铣削参数对残余应力的影响,包括切削速度、切削深度、刃角、粘度系数等。
为此,本实验使用示差扫描量测仪(SMM)和刚度测量仪(RMM)等测试仪器从事残余应力实验测试。
通过对比不同参数下表面残余应力的测试结果,可以清楚地了解不同参数对残余应力的影响情况,从而总结出一系列有利于控制残余应力的铣削参数。
此外,在残余应力控制方面也可以尝试其他技术手段,如利用冷却液和切削润滑油、减少切削压力等,充分发挥它们的作用,提高加工精度。
同时,需要选择符合要求的刀具和机床,使之处于最佳的运行状态,以保证切削的精度。
在实验过程中,还应考虑到铝合金本身的成分、晶粒结构、表面组织等因素,对它们的影响可能会导致残余应力的不同程度变化。
因此,为了进一步减少残余应力,可以采用表面处理技术,如表面精加工、电解抛光等,从而达到有效地减少残余应力的目的。
本实验旨在分析高速铣削加工铝合金表面残余应力的影响因素,以探索技术手段以控制其产生的残余应力。
为此,需要综合运用实验测试技术、表面处理技术、刀具技术及机床技术,建立相应的理论及具体方法,以达到比较优良的加工精度及残余应力控制要求。
通过以上研究,期望能够探索出一套更优化更可靠的高速铣削加工铝合金表面技术方案,指导相关行业实践应用,提高加工精度及零件质量,有助于推动行业的发展。
以上就是本文对高速铣削加工铝合金表面残余应力的研究,希望通过本研究能够为相关行业提供参考。
硬质合金表面加工 残余应力
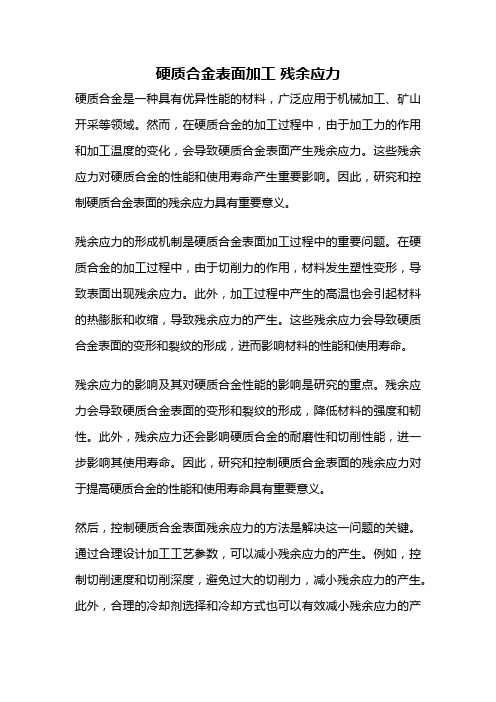
硬质合金表面加工残余应力硬质合金是一种具有优异性能的材料,广泛应用于机械加工、矿山开采等领域。
然而,在硬质合金的加工过程中,由于加工力的作用和加工温度的变化,会导致硬质合金表面产生残余应力。
这些残余应力对硬质合金的性能和使用寿命产生重要影响。
因此,研究和控制硬质合金表面的残余应力具有重要意义。
残余应力的形成机制是硬质合金表面加工过程中的重要问题。
在硬质合金的加工过程中,由于切削力的作用,材料发生塑性变形,导致表面出现残余应力。
此外,加工过程中产生的高温也会引起材料的热膨胀和收缩,导致残余应力的产生。
这些残余应力会导致硬质合金表面的变形和裂纹的形成,进而影响材料的性能和使用寿命。
残余应力的影响及其对硬质合金性能的影响是研究的重点。
残余应力会导致硬质合金表面的变形和裂纹的形成,降低材料的强度和韧性。
此外,残余应力还会影响硬质合金的耐磨性和切削性能,进一步影响其使用寿命。
因此,研究和控制硬质合金表面的残余应力对于提高硬质合金的性能和使用寿命具有重要意义。
然后,控制硬质合金表面残余应力的方法是解决这一问题的关键。
通过合理设计加工工艺参数,可以减小残余应力的产生。
例如,控制切削速度和切削深度,避免过大的切削力,减小残余应力的产生。
此外,合理的冷却剂选择和冷却方式也可以有效减小残余应力的产生。
通过对加工工艺参数的优化和改进,可以降低硬质合金表面的残余应力,提高材料的性能和使用寿命。
研究硬质合金表面残余应力的发展趋势是未来研究的方向。
随着科学技术的不断进步,研究硬质合金表面残余应力的技术也在不断发展。
例如,利用数值模拟方法可以模拟硬质合金表面加工过程中的残余应力分布和变化规律,为优化加工工艺提供理论依据。
此外,利用先进的材料表征技术可以实时监测和评估硬质合金表面的残余应力,为加工工艺的控制和改进提供指导。
硬质合金表面加工残余应力是一个重要的研究课题。
研究和控制硬质合金表面的残余应力对于提高材料的性能和使用寿命具有重要意义。
车铣加工表面层残余应力的研究

金属切 削加工是 一个伴 随着高温 、 高压 、 高 应变率的塑性大变形过程 ,在已加工表面 上往 往存在着较大的残余应力 ,已加 工表面层残余 应力对零件的使用性能有着重要的影响 。残余 拉应力会降低 ̄  ̄ T 的疲劳强度 , 时甚 至在切 - - 4 有 削加工后 , 会使零件表 面产生微裂纹 : 面残余压 应力却能提高零件的疲劳强度。当各部 分的残 余应力 山于分布小均 匀, 还会发生 ]件 变形 , 二 影 响工件 的形状精度 和尺寸精度。因此 , 究加工 研 表面层残余应力 ,对保证零件表面质量有重要 意义 。
作用去 除后 ,整个物体山于 内部残余应力 的作
用将发生形变。
1 . 2残余应力的分类 第一类残余应力 , 标记 为 。它在材料较 的热弹塑性 问题 。 棚 图所示1 。 大范 围内或许多 品粒 范围 内存在 并保持 平衡 , 2单 因素实验方案 3试验分析结论 在多个连续品体范围内保持常数 , 它的大小 、 方 21实验 目的 . 为 了深人研究铣 刀转速 和刀具轴 向进  ̄t AJ t 向和性 质可 用通 常 的物 理或 机 械方法 进行 测 通常 山于切削加工产生的残余应 力是指宏 对表 面层残余 应力 的影响规律 ,我们设计 了单 量。如果 第—类残余应力所 产生 的力 或力矩 的 观残余应力 , 即第一类残余应力。 也 本文从影 响 因素试验方案 , 运用金属切削原理的知识 , 详细 平衡状 态遭 到破坏 , 将导致构件宏观 尺寸的变 车铣加工工件表 面残余应力 的两个主要因素( 铣 地分析 了试验结果 , 中得出以下结论 : 从 化。通常 山于切 削加工产生 的残余应 力足指 宏 刀转速 n和轴 向进给量 D出发 , 单 因素 实 采用 1 ) 金属的热塑性变形作用对 车铣加工工件 观残余应力 。 根据加工残余应力 的性质小同 , 可 验方法 , 分别改变铣刀 转速 n和轴向进给量 £ 表面残余应力 的产生和变化大小 的影响起主导 , 分 为残余拉应力和残余压应力 ,应 力的大小 随 进行单因素正交车铣 6 # 5 钢实验 ,研究车铣加 作用 ,里层 金属的弹性恢 复和表层 金属 在切削 表层的深度面变化 。 工的切削用量 与工件表面残余应力的关 系。 热作用下发生 的相变是次要作用。 第二类残余应力称 为微 观结构应力 (,0 s- 一 t . 2 . 验 条 件 2实 2 削速 度从 15 mr n增 大 到 17 , 1切 2. /i 6 a 5r n tr r s标 记为 Il它存在于品粒 尺度 内且 u se) l a ts,  ̄I Fo r 文验机 床 : 数控车铣加 T中心 M Z K I — rn工件表 面残余应力 为拉应力但增大趋 势小 A A N a , i 0 保持平衡 , 在一个或几个 品粒 的部分 范围内保 TEGEX2 0Y。 明显 , 1 7 / i 从 5 mm n增大 到 1 8 mm n 表 面残 8A / i, 持均匀。如果第 二类残余应力平衡状 态得 到改 工 件 材料 : ,铁 素 体 ,其 硬 度 为 余 拉 应力 急剧增 大 ,但从 18 mmn 大到 6 钢 5 8. /i增 4 变 , 会造成宏观尺寸的变化 。 也 H Cl R 2 ,屈服强度 o= 8 M a L7 4 P ,抗拉强 度 盯】 29 mrn , I 1. /i时 表面残余拉应力急剧下降。 = 8 n 增大 第 三类残 余应力 称品 内亚 结构 应力(u— 9 0 a S b 8 MP ,延 伸率 6 9 = %,断 面收缩 率 _ 5 轴 向进给量 f, 3% a 对车铣 加工工 件的表面残余应 sutr t s, t c a ses标记为 “ r ul r ) 。它是在 品粒若 干 3 %, 5 化学成分见表 1 。 力影响显著。 随着轴向进给量无的增大 , 表面残 个原子范 围内存在并在 品粒 的小部分 内保持平 表 1 试验铜 的化 学成分噘 量分数) 余应力逐渐减 小。 衡, 在品体亚结构范 围内大小小均匀。 第 类残 3 刀转 速 n 为 3 0 r i  ̄ 1 8 mm n ) 铣 c 0 0/ n m ( 8. /i 4 ) 附一近是切削振动的固有一频率 ,为了工 件得 余应力平衡状态的破坏 ,小会引起宏观尺寸 的 变化。 到较好的残余应力状态 ,车铣 切削用 量应 避开 在大多数情况下 ,宏观残余应力与微观残 刀具 : 可转位立铣刀 , 直径 2 m 齿数 0 m, B 为 3 0 r n a 0 mm/的组合 。 e 0 0/ ,f 为 . r mi 8 余应力总是同时存在的 ,产生 第一类 残余应力 Z 2刀片为 Wii 公 司的 XD 0 0 0 =, da HT 9 3 8 4 比车削加 工 , 铣加工 能够 在更高 的 1 对 车 的加工过程 必须伴 随第 二 、 三类残余 应力的 第 T 5 5型 MT C N 5l — VD- i — 2 T N AI03涂 层 刀 铣 刀转速 n 和更大的轴 向进 给量 f的切削条 c a 产生。 片。 件下, 使工件得 到表 面残余压应力 以提高工件 1 - 3残余应力 的产生机理 切削条件 : 正交顺铣 , 乳化液冷却 的表面质量 。 目前 , 于残余应力 的产 生机 理 , 关 从理论 I } = 实验测量仪器 : 兰 Pn ye 公 司 , 荷 aa ta l i l 多晶 参 考 文献 定量分析还存在 困难 。下面仅从 已加工表面彤 X射线衍射仪 P 00 X射线 C K W34 , ua 【 晋烧 , l 】 诩舟. 车铣复合 开创未 来一本 刊主编刘 成过程的角度分析残余应力的产生机理。 照射 , 衍射品面(1) 于 0 5 n 衍射角 柱 与奥地利 WF 2 , 1等 . 4 m, 1 L车铣 技术公 司首席代表 李锋 1. .1机械应力引起的残余 应力 3 为 2 = 5 _ ,残余应 力的测试采用 0 -5法测 博士对话航 空制造技术. 0 .4 4 — 4 0 16 。 4  ̄ o - 4 2 7 ( 2 3 0 1 工件装夹时 , 如果夹紧力过大 , 将会使 件 量 。 贾春德 , 姜增辉. 车铣原 理. 北京: 国防土业 出版 2 035 6 发生塑性变形 , 从面使工件产生残余应力。 切削 金相显微 镜 : L MP S O Y U 公司 , 倒置 型金相 社 .0 .- 过程 中,刀刃前方 的工件材料受 到前 刀面的挤 显微镜 GX 7 。 一 1 【z素 玉扁 速铣 削加 土表 而质量的研 究. 东 3 1 【 山 压 , 面使将成 为已加工表 面层 的金属 , 削 从 在切 23实验方 案 - 大学: 博士学位论文1 0 6 56 , 0 . - 2
车铣加工表面层残余应力的研究

车铣加工表面层残余应力的研究作者:章一亨来源:《中国新技术新产品》2010年第13期摘要:本文通过对多种金属材料进行车铣加工实验,从表面层残余应力的性质及其大小等方面,对车铣加工进行深入的理论分析,从而为选择合理的工艺参数提供依据,以提高车铣的加工效率和工件的表面质量,达到指导实际生产加工的目的。
关键词:车铣技术;残余应力;单因素试验金属切削加工是一个伴随着高温、高压、高应变率的塑性大变形过程,在已加工表面上往往存在着较大的残余应力,已加工表面层残余应力对零件的使用性能有着重要的影响。
残余拉应力会降低零件的疲劳强度,有时甚至在切削加工后,会使零件表面产生微裂纹:面残余压应力却能提高零件的疲劳强度。
当各部分的残余应力山于分布小均匀,还会发生工件变形,影响工件的形状精度和尺寸精度。
因此,研究加工表面层残余应力,对保证零件表面质量有重要意义。
1 残余应力的定义、分类与产生机理1.1 残余应力的定义残余应力以平衡状态存在于物体内部,是固有应力域中局部内应力的一种。
残余应力是一种小稳定的应力状态,当物体受到外力作用时,作用应力与残余应力相互作用,使其某些局部呈现塑性变形,截面内应力重新分配:当外力作用去除后,整个物体山于内部残余应力的作用将发生形变。
1.2 残余应力的分类第一类残余应力,标记为?滓r1。
它在材料较大范围内或许多品粒范围内存在并保持平衡,在多个连续品体范围内保持常数,它的大小、方向和性质可用通常的物理或机械方法进行测量。
如果第一类残余应力所产生的力或力矩的平衡状态遭到破坏,将导致构件宏观尺寸的变化。
通常山于切削加工产生的残余应力是指宏观残余应力。
根据加工残余应力的性质小同,可分为残余拉应力和残余压应力,应力的大小随表层的深度面变化。
第二类残余应力称为微观结构应力(Structural stress),标记为?滓r11。
它存在于品粒尺度内且保持平衡,在一个或几个品粒的部分范围内保持均匀。
如果第二类残余应力平衡状态得到改变,也会造成宏观尺寸的变化。
机械切削加工过程的应力分析与控制
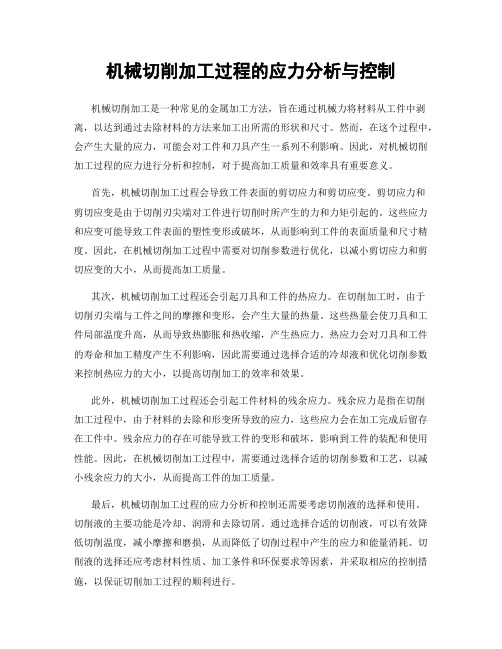
机械切削加工过程的应力分析与控制机械切削加工是一种常见的金属加工方法,旨在通过机械力将材料从工件中剥离,以达到通过去除材料的方法来加工出所需的形状和尺寸。
然而,在这个过程中,会产生大量的应力,可能会对工件和刀具产生一系列不利影响。
因此,对机械切削加工过程的应力进行分析和控制,对于提高加工质量和效率具有重要意义。
首先,机械切削加工过程会导致工件表面的剪切应力和剪切应变。
剪切应力和剪切应变是由于切削刃尖端对工件进行切削时所产生的力和力矩引起的。
这些应力和应变可能导致工件表面的塑性变形或破坏,从而影响到工件的表面质量和尺寸精度。
因此,在机械切削加工过程中需要对切削参数进行优化,以减小剪切应力和剪切应变的大小,从而提高加工质量。
其次,机械切削加工过程还会引起刀具和工件的热应力。
在切削加工时,由于切削刃尖端与工件之间的摩擦和变形,会产生大量的热量。
这些热量会使刀具和工件局部温度升高,从而导致热膨胀和热收缩,产生热应力。
热应力会对刀具和工件的寿命和加工精度产生不利影响,因此需要通过选择合适的冷却液和优化切削参数来控制热应力的大小,以提高切削加工的效率和效果。
此外,机械切削加工过程还会引起工件材料的残余应力。
残余应力是指在切削加工过程中,由于材料的去除和形变所导致的应力,这些应力会在加工完成后留存在工件中。
残余应力的存在可能导致工件的变形和破坏,影响到工件的装配和使用性能。
因此,在机械切削加工过程中,需要通过选择合适的切削参数和工艺,以减小残余应力的大小,从而提高工件的加工质量。
最后,机械切削加工过程的应力分析和控制还需要考虑切削液的选择和使用。
切削液的主要功能是冷却、润滑和去除切屑。
通过选择合适的切削液,可以有效降低切削温度,减小摩擦和磨损,从而降低了切削过程中产生的应力和能量消耗。
切削液的选择还应考虑材料性质、加工条件和环保要求等因素,并采取相应的控制措施,以保证切削加工过程的顺利进行。
综上所述,机械切削加工过程的应力分析和控制对于提高加工质量和效率具有重要意义。
不锈钢切削表面残余应力的模拟
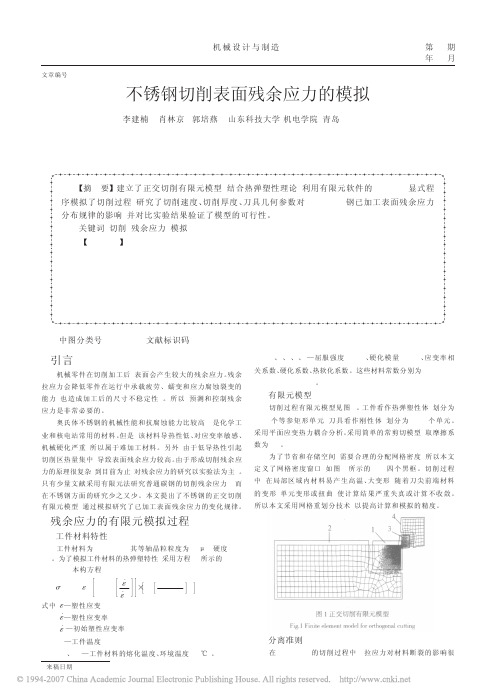
LI Jian- nan, XIAO Lin- jing, GUO Pei- yan ( College of Mechanical and Electronic Engineering, SDUST, Qingdao 266510, China) !!!!!!!!!!!!!!!!!!!!!!!!!!!!!!!!!!!!!!!!!!!" 【摘 要】建立了正交切削有限元模型, 结合热弹塑性理论, 利用有限元软件的 Lagrange 显式程 序模拟了切削过程, 研究了切削速度、切削厚度、刀具几何参数对 AISI 316L 钢已加工表面残余应力 分布规律的影响, 并对比实验结果验证了模型的可行性。 关键词: 切削; 残余应力; 模拟 【Abstr act】 An orthogonal cutting model is presented, and the cutting process is simulated by a fi- nite element software based on the thermal - elastic - plastic FEM theory and updated Lagrange method. The distributions of residual stresses in machined layer of AISI 316L steel are obtained.The effects of cutting speeds, cutting depths and tool geometry on residual stress distributions are investigated in this paper. Comparing to experimental results, the cutting model is feasible. Key wor ds: Cutting; Residual str ess; Simulate
切削加工过程与残余应力仿真研究
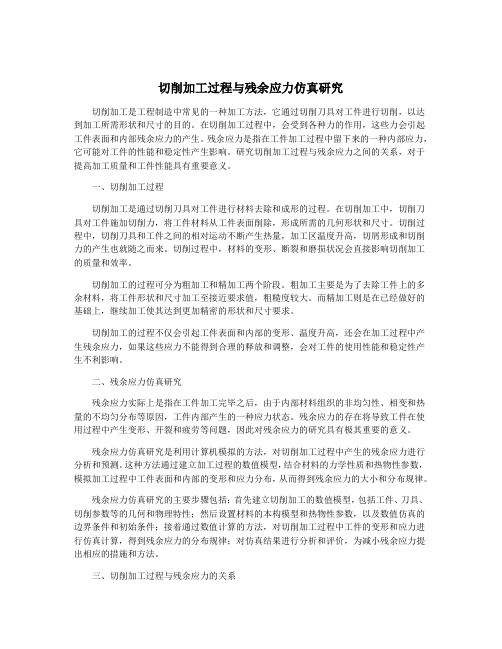
切削加工过程与残余应力仿真研究切削加工是工程制造中常见的一种加工方法,它通过切削刀具对工件进行切削,以达到加工所需形状和尺寸的目的。
在切削加工过程中,会受到各种力的作用,这些力会引起工件表面和内部残余应力的产生。
残余应力是指在工件加工过程中留下来的一种内部应力,它可能对工件的性能和稳定性产生影响。
研究切削加工过程与残余应力之间的关系,对于提高加工质量和工件性能具有重要意义。
一、切削加工过程切削加工是通过切削刀具对工件进行材料去除和成形的过程。
在切削加工中,切削刀具对工件施加切削力,将工件材料从工件表面削除,形成所需的几何形状和尺寸。
切削过程中,切削刀具和工件之间的相对运动不断产生热量,加工区温度升高,切屑形成和切削力的产生也就随之而来。
切削过程中,材料的变形、断裂和磨损状况会直接影响切削加工的质量和效率。
切削加工的过程可分为粗加工和精加工两个阶段。
粗加工主要是为了去除工件上的多余材料,将工件形状和尺寸加工至接近要求值,粗糙度较大。
而精加工则是在已经做好的基础上,继续加工使其达到更加精密的形状和尺寸要求。
切削加工的过程不仅会引起工件表面和内部的变形、温度升高,还会在加工过程中产生残余应力,如果这些应力不能得到合理的释放和调整,会对工件的使用性能和稳定性产生不利影响。
二、残余应力仿真研究残余应力实际上是指在工件加工完毕之后,由于内部材料组织的非均匀性、相变和热量的不均匀分布等原因,工件内部产生的一种应力状态。
残余应力的存在将导致工件在使用过程中产生变形、开裂和疲劳等问题,因此对残余应力的研究具有极其重要的意义。
残余应力仿真研究是利用计算机模拟的方法,对切削加工过程中产生的残余应力进行分析和预测。
这种方法通过建立加工过程的数值模型,结合材料的力学性质和热物性参数,模拟加工过程中工件表面和内部的变形和应力分布,从而得到残余应力的大小和分布规律。
残余应力仿真研究的主要步骤包括:首先建立切削加工的数值模型,包括工件、刀具、切削参数等的几何和物理特性;然后设置材料的本构模型和热物性参数,以及数值仿真的边界条件和初始条件;接着通过数值计算的方法,对切削加工过程中工件的变形和应力进行仿真计算,得到残余应力的分布规律;对仿真结果进行分析和评价,为减小残余应力提出相应的措施和方法。
加工表面产生压缩残余应力和拉伸残余应力原因
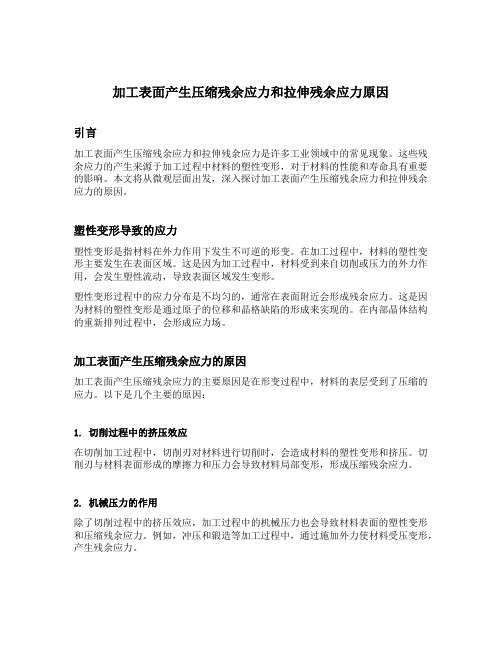
加工表面产生压缩残余应力和拉伸残余应力原因引言加工表面产生压缩残余应力和拉伸残余应力是许多工业领域中的常见现象。
这些残余应力的产生来源于加工过程中材料的塑性变形,对于材料的性能和寿命具有重要的影响。
本文将从微观层面出发,深入探讨加工表面产生压缩残余应力和拉伸残余应力的原因。
塑性变形导致的应力塑性变形是指材料在外力作用下发生不可逆的形变。
在加工过程中,材料的塑性变形主要发生在表面区域。
这是因为加工过程中,材料受到来自切削或压力的外力作用,会发生塑性流动,导致表面区域发生变形。
塑性变形过程中的应力分布是不均匀的,通常在表面附近会形成残余应力。
这是因为材料的塑性变形是通过原子的位移和晶格缺陷的形成来实现的。
在内部晶体结构的重新排列过程中,会形成应力场。
加工表面产生压缩残余应力的原因加工表面产生压缩残余应力的主要原因是在形变过程中,材料的表层受到了压缩的应力。
以下是几个主要的原因:1. 切削过程中的挤压效应在切削加工过程中,切削刃对材料进行切削时,会造成材料的塑性变形和挤压。
切削刃与材料表面形成的摩擦力和压力会导致材料局部变形,形成压缩残余应力。
2. 机械压力的作用除了切削过程中的挤压效应,加工过程中的机械压力也会导致材料表面的塑性变形和压缩残余应力。
例如,冲压和锻造等加工过程中,通过施加外力使材料受压变形,产生残余应力。
3. 热加工引起的残余应力热加工过程中的温度变化会导致材料的热膨胀和收缩。
当材料表面受到不均匀加热或冷却时,会发生残余应力。
热加工过程中的残余应力可以通过控制加热和冷却速度等参数进行调节。
加工表面产生拉伸残余应力的原因除了压缩残余应力,加工表面也可能产生拉伸残余应力。
这些拉伸残余应力的主要原因如下:1. 切削过程的拉伸效应在切削过程中,不仅可以产生压缩残余应力,还可能导致拉伸残余应力的形成。
例如,在部分切削过程中,切削刃对材料表面施加拉伸力,导致材料表面的拉伸变形和产生拉伸残余应力。
2. 冷加工引起的残余应力冷加工过程中,材料受到外力的挤压和变形。
残余应力对切削加工精度的影响及消除
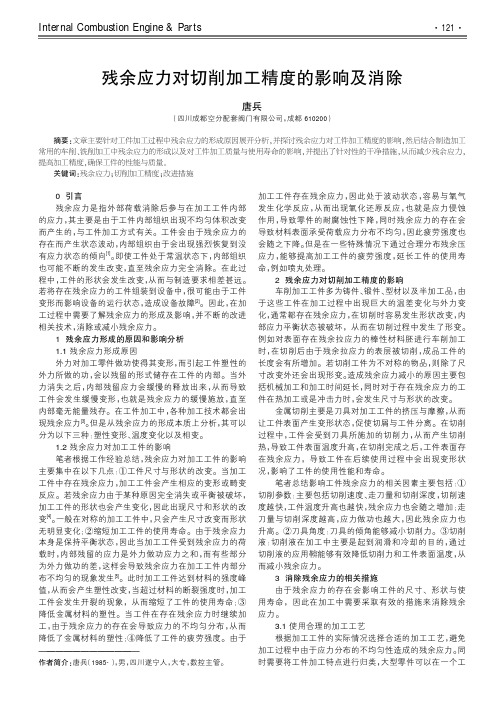
Internal Combustion Engine&Parts0引言残余应力是指外部荷载消除后参与在加工工件内部的应力,其主要是由于工件内部组织出现不均匀体积改变而产生的,与工件加工方式有关。
工件会由于残余应力的存在而产生状态波动,内部组织由于会出现强烈恢复到没有应力状态的倾向[1]。
即使工件处于常温状态下,内部组织也可能不断的发生改变,直至残余应力完全消除。
在此过程中,工件的形状会发生改变,从而与制造要求相差甚远。
若将存在残余应力的工件组装到设备中,很可能由于工件变形而影响设备的运行状态,造成设备故障[2]。
因此,在加工过程中需要了解残余应力的形成及影响,并不断的改进相关技术,消除或减小残余应力。
1残余应力形成的原因和影响分析1.1残余应力形成原因外力对加工零件做功使得其变形,而引起工件塑性的外力所做的功,会以残留的形式储存在工件的内部。
当外力消失之后,内部残留应力会缓慢的释放出来,从而导致工件会发生缓慢变形,也就是残余应力的缓慢施放,直至内部毫无能量残存。
在工件加工中,各种加工技术都会出现残余应力[3]。
但是从残余应力的形成本质上分析,其可以分为以下三种:塑性变形、温度变化以及相变。
1.2残余应力对加工工件的影响笔者根据工作经验总结,残余应力对加工工件的影响主要集中在以下几点:①工件尺寸与形状的改变。
当加工工件中存在残余应力,加工工件会产生相应的变形或畸变反应。
若残余应力由于某种原因完全消失或平衡被破坏,加工工件的形状也会产生变化,因此出现尺寸和形状的改变[4]。
一般在对称的加工工件中,只会产生尺寸改变而形状无明显变化;②缩短加工工件的使用寿命。
由于残余应力本身是保持平衡状态,因此当加工工件受到残余应力的荷载时,内部残留的应力是外力做功应力之和,而有些部分为外力做功的差,这样会导致残余应力在加工工件内部分布不均匀的现象发生[5]。
此时加工工件达到材料的强度峰值,从而会产生塑性改变,当超过材料的断裂强度时,加工工件会发生开裂的现象,从而缩短了工件的使用寿命;③降低金属材料的塑性。
切削加工表面残余应力研究综述

切削加工表面残余应力研究综述王增强;刘超锋【摘要】主要研究了切削加工过程中残余应力产生的机理,并对残余应力的测量方法以及残余应力的调整和消除手段进行了较为系统的阐述和比较,提出了在残余应力检测和消除领域的一些建议,为进一步研究提供参考和借鉴。
【期刊名称】《航空制造技术》【年(卷),期】2015(000)006【总页数】5页(P26-30)【作者】王增强;刘超锋【作者单位】西北工业大学现代设计与集成制造教育部重点实验室;西北工业大学现代设计与集成制造教育部重点实验室【正文语种】中文残余应力主要是由构件内部不均匀的塑性变形引起的。
各种工程材料和构件在毛坯的制备、零件的加工、热处理和装配的过程中都会产生不同程度的残余应力。
残余应力因其直观性差和不易检测等因素往往被人们忽视。
残余应力严重影响构件的加工精度和尺寸稳定性、静强度、疲劳强度和腐蚀开裂。
特别是在承力件和转动件上,残余应力的存在易导致突发性破坏且后果往往十分严重。
因此,自20世纪50年代以来国内外技术人员花费了大量的精力研究残余应力的产生机理、检测手段、消除方法以及残余应力对构件的影响[1]。
Guo等通过试验的方法研究了车削和磨削产生的不同性质的残余应力对工件疲劳强度的影响[2];Seo等通过试验和有限元模拟的方法揭示了在车轮制造和火车刹车过程中引起的残余应力和火车车轮疲劳寿命之间的代数关系[3];Liu等用试验的方法研究了残余应力对滚动接触疲劳强度的影响[4];董辉跃等研究了材料去除过程中残余应力的重新分布及该过程所引起的工件变形[5];孙杰等基于理论计算和有限元模拟,研究了毛坯的初始残余应力对大型整体结构件数控加工变形的影响[6];Hiroyuki等研究了不同加工参数引起的残余应力对零件疲劳强度的影响[7],并且结合正交切削模型和刀尖圆角压痕模型建立了残余应力预测模型[8];王立涛对于铣削加工航空框类整体结构件时的残余应力和变形机理进行了研究,并将研究成果应用于实际生产[9]。
- 1、下载文档前请自行甄别文档内容的完整性,平台不提供额外的编辑、内容补充、找答案等附加服务。
- 2、"仅部分预览"的文档,不可在线预览部分如存在完整性等问题,可反馈申请退款(可完整预览的文档不适用该条件!)。
- 3、如文档侵犯您的权益,请联系客服反馈,我们会尽快为您处理(人工客服工作时间:9:00-18:30)。
一篇关于切削加工表面残余应力研究的好文章残余应力主要是由构件内部不均匀的塑性变形引起的。
各种工程材料和构件在毛坯的制备、零件的加工、热处理和装配的过程中都会产生不同程度的残余应力。
残余应力因其直观性差和不易检测等因素往往被人们忽视。
残余应力严重影响构件的加工精度和尺寸稳定性、静强度、疲劳强度和腐蚀开裂。
特别是在承力件和转动件上,残余应力的存在易导致突发性破坏且后果往往十分严重。
因此,自20世纪50年代以来国内外技术人员花费了大量的精力研究残余应力的产生机理、检测手段、消除方法以及残余应力对构件的影响。
Guo 等通过试验的方法研究了车削和磨削产生的不同性质的残余应力对工件疲劳强度的影响;Seo等通过试验和有限元模拟的方法揭示了在车轮制造和火车刹车过程中引起的残余应力和火车车轮疲劳寿命之间的代数关系;Liu 等用试验的方法研究了残余应力对滚动接触疲劳强度的影响[4];董辉跃等研究了材料去除过程中残余应力的重新分布及该过程所引起的工件变形;孙杰等基于理论计算和有限元模拟,研究了毛坯的初始残余应力对大型整体结构件数控加工变形的影响;Hiroyuki 等研究了不同加工参数引起的残余应力对零件疲劳强度的影响[7],并且结合正交切削模型和刀尖圆角压痕模型建立了残余应力预测模型;王立涛对于铣削加工航空框类整体结构件时的残余应力和变形机理进行了研究,并将研究成果应用于实际生产。
在机械加工过程中残余应力的存在不仅影响零件的加工精度而且影响零件的使用性能和寿命。
因此,充分了解残余应力产生的机理并掌握残余应力测量和消除方法对于充分利用残余应力的有益的一面,避免残余应力带来的危害以及改进加工工艺,延长工件的使用寿命和确保安全生产是十分有意义的。
本文主要研究了切削加工过程中残余应力产生的机理,并对残余应力的测量方法以及残余应力的调整和消除手段进行了较为系统的阐述和比较,提出了在残余应力检测和消除领域的一些建议,为进一步研究提供参考和借鉴。
残余应力的定义和分类1 残余应力的定义残余应力是指在没有外力作用于物体时,物体内部保持平衡的应力。
在没有外力的作用下,物体内部保持平衡的应力称为固有应力,残余应力是固有应力的一种。
现在用一个简单的例子说明残余应力的产生。
假设图1中3根弹簧在自由状态下的长度分别为L1、L2、L3,弹性常数为c。
用两块刚性板将3 根弹簧连接后的长度为L,并且连接之后整个系统不受外力的影响。
设连接后3根弹簧上产生的力分别为F1、F2、F3,这时的F1、F2、F3 就相当于这个系统的残余应力且F1+F2+F3=0。
2 残余应力的分类(1)根据残余应力影响的程度把残余应力分为宏观应力和微观应力。
1973 年德国学者E.Macherauch进一步把宏观应力称为第一类残余应力;把微观应力分为第二类和第三类残余应力。
第一类残余应力存在于材料的较大范围或许多晶粒范围内并且保持相互平衡,它的大小和方向可以用常用的机械和物理方法进行检测。
这种残余应力对于所加工的产品是否合格以及最终产品的性能能否达到设计要求等都会产生很大的影响。
因此,在实际生产过程中所关注的残余应力一般指第一类残余应力。
第二类残余应力是指存在于晶粒范围内的残余应力。
第三类残余应力是指存在于晶粒内部的粒子之间的晶内应力。
(2)根据残余应力产生的原因,把宏观应力相对应地叫做体积应力;微观应力叫做结构应力。
体积应力是由于物体受到外部不均匀的机械的、热的、化学的作用而产生的。
内部组织结构均匀的物体也会产生这种残余应力。
结构应力是由于物体内部组织结构不均匀造成的,即使受到均匀的外部作用也会产生这种残余应力。
(3)残余应力按其表现形式可以分为残余拉应力和残余压应力。
当工件在使用过程中承受外部载荷时,工件所受到的实际载荷是外部载荷和内部残余应力的叠加。
这就会影响到工件的实际承载能力,使工件在使用过程中容易发生突然的过载断裂等,如果这种突然失效发生在关键部件可能会带来重大的事故。
另外,残余拉应力的存在会加速零件表面裂纹的萌生和扩展,降低零件的抗疲劳强度、耐腐蚀性和尺寸稳定性等。
而残余压应力则会在一定程度上提高零件的抗疲劳强度和耐腐蚀性[14-15]。
因此,研究如何使零件表面产生残余压应力的加工工艺是非常有意义的。
金属切削加工过程和残余应力产生的机理1 金属切削过程在金属的切削过程中,切屑是被加工材料受到刀具前刀面的推挤而沿剪切面剪切滑移形成的。
在这个过程中,切削层金属会发生一系列的变形,同时产生大量的热。
通常把金属切削的变形过程分为3 个变形区来研究(图2)。
第一变形区集中在刀尖与工件接触的前端。
在这个变形区内,随着刀具和工件的相对运动,切削层的金属在达到材料的屈服强度之后就开始产生滑移,直到切削层与前刀面基本平行后停止滑移,退出第一变形区。
由于第一变形区内存在大的剪切变形和摩擦,因此会产生大量的热。
在第一变形区内形成的切屑会随着刀具的移动沿着前刀面的方向流动。
流动过程中,切屑底层和前刀面会发生进一步的摩擦和挤压,这个过程伴随着塑性变形的产生和热量的释放,这就形成了第二变形区。
由于刀尖钝角的存在,在第一变形区中切削层金属并没有被完全切除而会留下薄薄一层未被去除的金属。
当刀具和工件相对运动时,这一薄层金属会被挤压通过切削刃钝角和后刀面。
在这个过程中表层金属会发生塑性变形并产生热量而基体则产生弹性变形,这就是金属切削过程的第三变形区。
2 残余应力产生的机理关于残余应力产生的机理,从理论上定量分析还存在困难,因此只能对其进行定性分析。
切削过程中残余应力的产生既与机械应力所造成的塑性变形有关,也与热应力所造成的塑性变形有关。
(1)由机械应力引起的残余应力。
刀具切削工件材料过程中,刀尖前方的三角形区域会随着刀具的运动而产生沿着切削方向的压缩塑性变形和垂直于切削表面方向的拉伸塑性变形(塑性凸出效应), 如图3 所示。
因此,在沿着切削表面的方向会有拉伸残余应力的产生。
与此同时,刀具的后刀面会对已加工表面有进一步的挤压和摩擦,会使其表面发生塑性伸长而产生沿表面方向的压缩残余应力。
实际加工过程中由机械应力所产生的残余应力是刀具接触点前方塑性凸出效应和刀具接触点后方压延效应的叠加。
(2)由热应力所引起的残余应力[10-13]。
金属切削加工过程中的3个变形区由于摩擦和塑性变形的存在都会产生大量的热。
这些热量很难及时散发出去,从而导致工件材料表面的受热膨胀。
但是表面的膨胀行为会受到基体的束缚而最终产生压缩塑性变形。
当工件完成加工逐渐冷却到室温后,产生压缩塑性变形的表层会在工件表面形成拉伸残余应力。
以上所说的情况并不包括工件在受热和冷却过程中可能发生的相变。
如果切削过程中产生的热量达到了工件材料的相变转化温度,则工件表层材料会在冷却过程中发生相变而使其体积发生变化,最终在工件表层产生残余应力。
在实际加工过程中,工件表面最终的残余应力状态是以上几种情况的叠加。
一般情况下,若切削速度较低,冷却情况良好,切削温度不是太高时,机械应力会对残余应力的产生和性质起主导作用。
当切削速度较高、切削温度也相应升高时,工件材料表面的热塑性变形会起主导作用。
当切削速度进一步升高,切削温度达到一定数值时,工件材料的相变就会对工件表面最终的残余应力性质起主导作用。
由此可以看出,在切削加工过程中残余应力的产生是一个非常复杂的过程,与切削加工过程中的热力耦合密切相关。
残余应力的检测及消除方法残余应力的检测方法有很多,根据其测试过程对被测构件是否产生破坏可以分为有损检测法(取条法、切槽法和钻孔法等)和无损检测法(X 射线法、磁性法和超声法等)。
有损检测法又叫做机械检测法或应力释放法,无损检测法又叫做物理检测法。
1 有损检测法有损检测法是指通过切槽、取条或逐层剥除等方法使构件相应部位的残余应力释放出来, 再通过对被测构件尺寸变化的测量来计算得到残余应力的具体数值的检测方法。
(1)取条法:取条法是指在存在残余应力的构件上,沿着残余应力存在的方向切取矩形等截面长条,使存在的残余应力完全释放,再通过测量在残余应力存在方向上构件尺寸的变化值计算出该方向的残余应力的值。
(2)切槽法:切槽法需要在构件表面上切削围成一定区域的沟槽,使所围成的区域内残余应力完全释放出来,再通过对应变的测量来计算获得残余应力。
(3)钻孔法:钻孔法是一种对构件破坏性相对较小的一种有损检测方法。
对存在残余应力构件的表面钻一个小孔,使小孔处的残余应力得以释放,再通过粘贴在孔邻近区域的应变片来测量相应的位移和应变,最后可以通过计算来得到在钻孔处深度方向上的平均残余应力值。
采用有损检测法检测残余应力时,会对被测部件的表面造成损伤和破坏,因而在一定程度上影响了零件的力学性能甚至导致直接报废。
在实际生产中需要进行残余应力检测的部件往往运用在关键部位且造价不菲,不允许对被测部件表面造成损伤。
因而,有损检测法会对被测部件造成损伤的缺点严重制约了它的应用范围和发展前景。
2 无损检测法残余应力的无损检测法主要是通过物理光学和核物理技术来测量材料内部的物理常量(如晶格常数)在应力场中的变化来间接算出物体内部残余应力值的方法。
(1)X 射线衍射法。
X 射线衍射法测量残余应力是基于X 射线衍射理论。
当一束波长为λ的X 射线照射在晶体表面时,会在特定的角度(2θ)上接收到X 射线反射光的波峰,这就是X 射线衍射现象。
1912 年Braag 和Laue 提出了布拉格方程,建立了宏观上可测量的衍射角(2θ)和晶面间距的确定关系,使得用X 射线衍射法测量残余应力成为了可能[12]。
用X 射线衍射法测量残余应力的原理见图4。
布拉格方程:式中,θ为X 射线衍射角的1/2,d 为被测材料的晶面间距,λ为入射X 射线的波长。
假设某晶面间距在无外力作用下为d0,受力后变为d,则应变为:根据胡克定律,应力为:式中,K 为弹性常数,当入射线的波长选定之后(λ一定),通过测定衍射角θ,即可由布拉格方程得到受力之后的晶面间距,继而得到相应的残余应力值。
这里需要指出的是由于晶体是各向异性的,因此式(3)中的弹性常数K 和宏观意义上的弹性模量E 是不同的,需要根据所选择的衍射晶面来计算出弹性常数K。
1961 年德国学者Macherauch 结合弹性理论和布拉格方程提出了测二维残余应力的sin2ψ法,基本方程为:式中,E 为弹性模量,μ为泊松比,θ0为没有外力作用时被测材料的布拉格角,ψ为空间任意方向和被测点Z轴方向的夹角。
用sin2ψ法只能得到距离材料表面10μm深度范围内二维残余应力的平均值,但配合电解抛光可得到任意深度的残余应力。
若想得到三维残余应力沿其深度方向的分布,可通过X 射线积分法、泰勒级数展开法、拉氏变换法及剥层法和法配合使用等方法来实现。
图5为用X 射线衍射法检测叶片表面残余应力的应用实例。