数控车床自动回转刀架结构设计
CK6136数控卧式车床机械结构设计(有cad图)

硬质合金刀具粗加工铸铁工件 硬质合金刀具半精加工碳钢工件 螺纹(丝杠等)加工和铰孔
通过比较最后选取:
Vmax=300 Vmin=6
m min
m min
(2) 主轴的极限转速 计算车床主轴极限转速时的的加工直径, 按经验分别取 (0.1~0.2) D 和(0.45~0.5)D。 则主轴极限转速应为:
1
1 数控车床的加工特点分析
1.1 数控车床的优点
数控车床已越来越多的应用于现代制造业,并发挥出普通车床无法比拟的优势, 数控车床主要有以下几优点: (1) 传动链短,与普通车床相比主轴驱动不再是电机 皮带 齿轮副机构变速, 而是采用横向和纵向进给分别由两台伺服电机驱动运动完成,不再使用挂轮、离合器 等传统部件,传动链大大缩短。 (2) 刚性高,为了与数控系统的高精度相匹配,数控车床的刚性高,以便适应 高精度的加工要求。 (3) 轻拖动,刀架(工作台)移动采用滚珠丝杠副,摩擦小,移动轻便。丝杠 两端的支承式专用轴承,其压力角比普通轴承大,在出厂时便选配好;数控车床的润 滑部分采用油雾自动润滑,这些措施都使得数控车床移动轻便。
1.2 数控车床加工特点 qq2567214873
(1) 自动化程度高,可以减轻操作者的体力劳动强度。数控加工过程是按输入 的程序自动完成的,操作者只需起始对刀、装卸工件、更换刀具,在加工过程中, 主 要是观察和监督车床运行。但是,由于数控车床的技术含量高,操作者的脑力劳动相 应提高。 (2) 加工零件精度高、 质量稳定。 数控车床的定位精度和重复定位精度都很高, 较容易保证一批零件尺寸的一致性,只要工艺设计和程序正确合理,加之精心操作, 就可以保证零件获得较高的加工精度,也便于对加工过程实行质量控制。 (3) 生产效率高。数控车床加工是能再一次装夹中加工多个加工表面,一般只 检测首件,所以可以省区普通车床加工时的不少中间工序,如划线、尺寸检测等,减 少了辅助时间,而且由于数控加工出的零件质量稳定,为后续工序带来方便,其综合 效率明显提高。 (4) 便于新产品研制和改型。数控加工一般不需要很多复杂的工艺装备,通过 编制加工程序就可把形状复杂和精度要求较高的零件加工出来,当产品改型,更改设 计时,只要改变程序,而不需要重新设计工装。所以,数控加工能大大缩短产品研制 周期,为新产品的研制开发、产品的改进、改型提供了捷径。 (5) 可向更高级的制造系统发展。数控车床及其加工技术是计算机辅助制造的 基础。
毕业设计--φ400数控车床设计及六角回转刀架设计

毕业设计说明书设计题目:Φ400mm数控车床总体设计及六角回转刀架设计学生班级学号指导教师摘要装备工业的技术水平和现代化程度决定着整个国民经济的水平和现代化程度,数控技术及装备是发展新兴高新技术产业和尖端工业的使能技术和最基本的装备,又是当今先进制造技术和装备最核心的技术。
数控技术是用数字信息对机械运动和工作过程进行控制的技术,而数控装备是以数控技术为代表的新技术对传统制造产业和新兴制造业的渗透形成的机电一体化产品,其技术范围覆盖很多领域。
经济型数控车床,对于保证和提高被加工零件的精度,主要依靠两方面来实现:一是系统的控制精度;二是机床本身的机械传动精度。
数控车床的进给传动系统,由于必须对进给位移的位置和速度同时实现自动控制。
所以,数控车床与卧式车床相比应具有有更好的精度.以确保机械传动系统的传动精度和工作平稳性。
关键词:车床,数控,传动系统目录第1章数控机床发展概述 (1)1.1数控机床 (1)1.1.1数控机床的特点 (1)1.1.2数控机床的发展简史 (2)1.1.3数控机床的组成 (3)第2章数控机床总体方案的制订及比较 (5)2.1总体方案设计要求 (5)2.2总体设计方案的确定 (10)2.2.1系统的运动方式与伺服系统的选择 (10)2.2.2计算机系统 (10)2.2.3机械传动方式 (10)第3章确定切削用量及选择刀具 (11)3.5刀具材料 (15)第4章传动系统图的设计 (16)4.1 确定极限转速 (16)4.2 确定公比 (16)4.3 求出主轴转速级数Z (16)4.4确定结构网或结构式 (16)4.5绘制转速图 (16)第5章数控车床六角回转刀架的结构设计........................................ 错误!未定义书签。
5.1设计内容和研究方法 ................................................................ 错误!未定义书签。
毕业设计(论文)-fanuc数控车床的刀架控制系统设计[管理资料]
![毕业设计(论文)-fanuc数控车床的刀架控制系统设计[管理资料]](https://img.taocdn.com/s3/m/381bb21b6294dd88d1d26bbd.png)
毕业设计说明书课题名称:FANUC数控车床的刀架控制系统设计学生姓名学号二级学院(系)电气电子工程学院专业机电一体化技术班级指导教师起讫时间:2012年2月13日~2012 年4月 6 日课题名称:FANUC数控车床摘要六工位简易刀架是经济型车床上最常用的一种自动换刀机构。
刀架采用三相异步电动机驱动,刀位检测采用霍尔元件。
这种刀架只能单方向换刀,电动机正转换刀,反转锁紧。
数控车床的刀架是机床的重要组成部分,刀架用于夹持切削用的刀具,其结构直接影响机床的切削性能和切削效率。
因此数控车床的刀架设计的好与坏、效率高与低将直接影响到产品的加工时间和质量,进而影响到制造业的飞速发展。
本设计主要对总体结构设计、主要传动部件的设计和电气控制部分设计。
包括电气电路和控制软件的设计。
本设计的自动回转刀架控制系统电路简单,可靠性高,有效地解决了传统机床换刀主要依靠手工换刀,辅助时间长,精度不高,累积误差大,加工出的产品既费时且质量不如数控加工的问题,也为车床数控改造中的自动换刀问题提供一种有效的解决途径。
关键词:机械设计;刀架控制原理;刀架电气控制系统;自动换刀;自动回转刀架。
目录摘要 (I)第1章机械结构 (2)刀架总述 (2)数控车床刀架的分类 (2)数控车床刀架传动装置的原理与应用 (3)数控车床六工位刀架换刀工作原理 (8)第2章数控车刀架电气控制系统设计 (12)霍尔原理在刀架中运用的简单概述 (12) (13)六工位刀架梯形图 (14)第3章数控车刀架常见故障分析....... (15)数控车刀架机械与电气故障分析排除 (15)数控车床刀架常见故障的实例分析 (16)刀架使用注意事项 (17)第4章结论 (19)参考文献 (20)致谢 (21)附录 (22)第1章机械结构刀架总述数控刀架安装在数控车床的滑板上。
它上面可以装夹多把刀具,在加工中实现自动换刀刀架的作用是装夹车刀,孔加工刀具及螺纹刀具并能准确迅速的选择刀具进行对工件的切削。
数控车床六工位刀架毕业设计

数控车床六工位刀架设计第1章设计内容和要求(1)设计数控车床六工位刀架及床身;(2)电动功率:120w;(3)电机转速:1400r/min;(4)刀位数:6(5)床身最大加工直径:400mm;(6)刀尖到导轨距离:200mm。
第2章刀架结构方案的确定2.1 刀架结构方案刀架换刀过程工作原理:换刀信号→电机正转→刀架抬起→刀架转位→刀位信号→电机反转→初定位→精定位刀架压紧→电机过流停转→换刀结束。
刀架的设计必须满足以下要求:(1)切削刀具数量较多,可安装多种形式的刀具,至少应能安装同类表面加工所需各种的各种车外圆刀具或孔加工刀具,并且刀具易于更换和调正;(2)须切削的空间太小。
为了能加工最大规格零件,刀架上两把相邻刀具之间要有合适的距离,避免刀具对工件、卡盘、尾座等发生干涉和碰撞;刀架大小要合理;(3)换刀快速准确,在PC可编程序器及其软件配合下,可实现最短路线逻辑选刀;(4)结构简单,定位夹紧可靠,强度高,能承受机床强力切削和连续长时间正常工作;(5)定位精度高,且应具有较高的精度稳定性和保持性。
2.1.1 液压式结构六角回转刀架的全部动作由液压系统通过电磁换向阀和顺序阀进行控制,其换刀动作可以分为以下四个步骤。
(1)刀架抬起当数控装置发出换刀指令后,压力油由A孔进入压紧液压缸的下腔,活塞上升,刀架体抬起使定位活动插销与固定插销脱开。
同时,活塞杆下端的端齿离合器与空套齿轮结合。
(2)刀架转位当刀架抬起之后,压力油由C孔转入液压缸左腔,活塞向右移动,通过连接板带动齿条移动,使空套齿轮做逆时针方向转动,通过端齿离合器使刀架转过60°。
活塞的行程应等于齿轮节圆周长的1/6,并由限位开关控制。
(3)刀架压紧刀架转位之后,压力油由B孔进入压紧液压缸的上腔,活塞带动刀架体下降。
中心轴轴套的底盘上精确的安装着六个带斜楔的圆柱固定插销,利用活动插销消除定位销与孔之间的间隙,从而实现可靠定位。
刀架体下降时,定位活动插销与另一个固定插销卡紧,同时中心轴轴套与刀架套的锥面接触,刀架在新的位置定位并压紧。
自动换刀装置的形式---回转刀架换刀

8.4.1 自动换刀装置的形式自动换刀装置是加工中心的重要执行机构,它的形式多种多样,目前常见的有以下几种。
1.回转刀架换刀数控机床使用的回转刀架是最简单的自动换刀装置,有四方刀架、六角刀架,即在其上装有四把、六把或更多的刀具。
回转刀架必须具有良好的强度和刚度,以承受粗加工的切削力:同时要保证回转刀架在每次转位的重复定位精度。
图8-17为数控车床六角回转刀架,它适用于盘类零件的加工。
在加工轴类零件时,可以用四方回转刀架。
由于两者底部安装尺寸相同,更换刀架十分方便。
图8-17 数控车床六角回转刀架1-活塞2-刀架体3、7-齿轮4-齿圈5-空套齿轮6-活塞8-齿条9-固定插销10、11-推杆12-触头回转刀架的全部动作由液压系统通过电磁换向阀和顺序阀进行控制,它的动作分为4个步骤:(1)刀架抬起当数控装置发出换刀指令后,压力油由a孔进入压紧液压缸的下腔,活塞1上升,刀架体2抬起,使定位用的活动插销10与固定插销9脱开。
同时,活塞杆下端的端齿离合器与空套齿轮5结合。
(2)刀架转位当刀架抬起后,压力油从c孔进入转位液压缸左腔,活塞6向右移动,通过联接板带动齿条8移动,使空套齿轮5作逆时针方向转动。
通过端齿离合器使刀架转过60º。
活塞的行程应等于齿轮5分度圆周长的1/6,并由限位开关控制。
(3)刀架压紧刀架转位之后,压力油从b孔进入压紧液压缸上腔,活塞1带动刀架体2下降。
齿轮3的底盘上精确地安装有6个带斜楔的圆柱固定插销9,利用活动插销10消除定位销与孔之间的间隙,实现反靠定位。
刀架体2下降时,定位活动插销10与另一个固定插销9卡紧,同时齿轮3与齿圈4的锥面接触,刀架在新的位置定位并夹紧。
这时,端齿离合器与空套齿轮5脱开。
(4)转位液压缸复位刀架压紧之后,压力油从d孔进入转位液压缸的右腔,活塞6带动齿条复位,由于此时端齿离合器已脱开,齿条带动齿轮3在轴上空转。
如果定位和夹紧动作正常,推杆11与相应的触头12接触,发出信号表示换刀过程已经结束,可以继续进行切削加工。
毕业设计FANUC数控车床刀架操纵系统设计

毕业设计说明书课落款称: FANUC数控车床刀架操纵系统设计学生姓名学号二级院(系)专业班级指导教师起讫时刻:2021 年 2 月13 日~ 2021 年 4 月 6 日FANUC数控车床的刀架操纵系统设计摘要数控车床尔后将向中高级进展,中档采纳普及型数控刀架配套,高级采纳动力型刀架,兼有液压刀架、伺服刀架、立式刀架等品种。
估量最近几年来对数控刀架需求量将大大增加。
数控刀架的进展趋势是:随着数控车床的进展,数控刀架开始向快速换刀、电液组合驱动和伺服驱动方向进展。
本部份要紧对四工位立式电动刀架的操纵系统进行设计。
关键词:数控刀架;四工位;电动回转刀架目录摘要 (1)第1章绪论 (3)课题的研究背景 (3)1.2 课题的研究意义 (3)设计内容 (4)第2章数控刀架电气操纵系统设计 (5)数控机床的组成 (5)霍尔原理及在刀架中运用的简单概述 (6)霍尔效应与工作原理 (6)霍尔效应的普遍运用 (6)霍尔元件在刀架中运用的简单概述 (7)2.3刀架电气操纵 (7).1 刀架的锁紧时刻操纵 (8)2.3.2刀架刀位信号的监控 (8)2.3.3换刀时刻的监控 (9)2.3.4刀架上电进程 (9)2.4刀架机械结构 (10)第3章数控刀架PLC操纵系统设计 (13)四工位刀架PLC梯形图与原理运用 (13)3.3.1 PLC的概述 (13)3.3.2 PLC梯形图运用 (13)3.3.3刀架的操作 (14)数控车床刀架PLC梯形图 (17)3.3.5 程序的调试 (23)小结 (24)参考文献 (25)致谢 (26)第1章绪论数控技术是现代制造技术的核心,是企业现代化水平的标志。
采纳数控系统操纵的数控机床在机械制造、模具加工、航天航空和造船等领域发挥着极为重要的作用。
本章介绍了本课题的研究背景,意义,大体内容1.1 课题研究的背景FANUC数控系统是由日本富士通公司研制开发,目前在我国取得了普遍的应用。
在中国市场上应用于车床的数控系统要紧有FANUC Oi -TA/TB/TC 和FANUC Oi mate- MA等。
数控车床自动回转刀架的控制设计

目录第一章引言 (1)1.1概述 (1)1.2数控车床自动回转刀架的发展趋势 (1)1.3刀架的设计准则 (2)第二章数控车床自动回转刀架的设计 (3)2.1数控车床刀架应满足的要求 (3)2.2刀架的工作原理 (6)2.3步进电机的选用 (7)2.4蜗杆及蜗轮的选用与校核 (8)2.5蜗杆轴的设计 (10)2.6蜗轮轴的设计 (17)2.7中心轴的设计 (18)2.8齿盘的设计 (20)2.9轴承的选择 (23)第三章PLC控制单元设计 (26)3.1PLC与工业控制计算机(IPC)和集散控制系统(DSC)的比较 (26)3.2控制电路硬件接线图 (27)3.3PLC控制流程图 (31)总结 (32)参考文献 (33)第一章引言1.1 概述数控车床的刀架是机床的重要组成部分。
刀架用于夹持切削用的刀具,因此其结构直接影响机床的切削性能和切削效率。
在一定程度上,刀架的结构和性能体现了机床的设计和制造技术水平。
随着数控车床的不断发展,刀架结构形式也在不断翻新。
其中按换刀方式的不同,数控车床的刀架系统主要有回转刀架、排式刀架和带刀库的自动换刀装置等多种形式。
其中,带刀库的数控加工中心自动换刀装置自1958年研制成功以来,其机械结构和控制方式不断得到改进和完善。
自动换刀装置时加工中心的重要执行机构,它的形式多种多样,目前常见的有更换主轴头换刀以及带刀库的自动换刀系统。
1.2 数控车床自动回转刀架的发展趋势数控刀架的发展趋势是:随着数控车床的发展,数控刀架开始向快速换刀、电液组合驱动和伺服驱动方向发展。
目前国内数控刀架以电动为主,分为立式(如图1-1)和卧式(如图1-2)两种。
立式主要用于简易数控车床;卧式刀架有八、十、十二等工位,可正、反方向旋转,就近选刀,用于全功能数控车床。
另外,卧式刀架还有液动刀架和伺服驱动刀架。
电动刀架是数控车床重要的传统结构,合理地选配电动刀架,并正确实施控制,能够有效的提高劳动生产率,缩短生产准备时间,消除人为误差,提高加工精度与加工精度的一致性等等。
数控车床自动回转刀架机电系统设计说明书
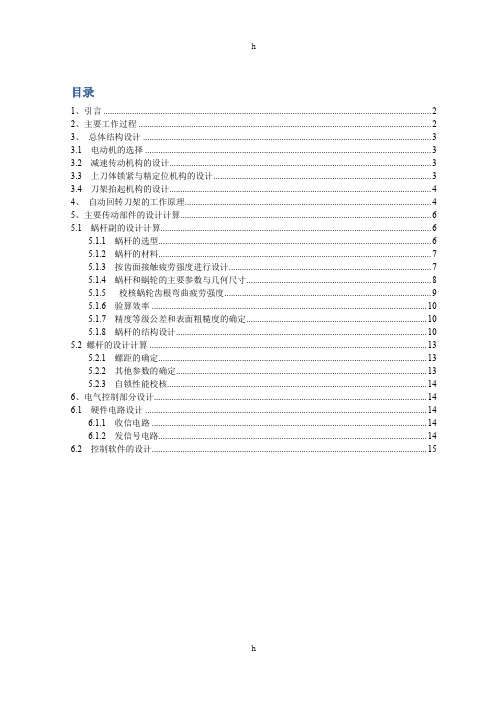
目录1、引言 (2)2、主要工作过程 (2)3、总体结构设计 (3)3.1 电动机的选择 (3)3.2 减速传动机构的设计 (3)3.3 上刀体锁紧与精定位机构的设计 (3)3.4 刀架抬起机构的设计 (4)4、自动回转刀架的工作原理 (4)5、主要传动部件的设计计算 (6)5.1 蜗杆副的设计计算 (6)5.1.1 蜗杆的选型 (6)5.1.2 蜗杆的材料 (7)5.1.3 按齿面接触疲劳强度进行设计 (7)5.1.4 蜗杆和蜗轮的主要参数与几何尺寸 (8)5.1.5 校核蜗轮齿根弯曲疲劳强度 (9)5.1.6 验算效率 (10)5.1.7 精度等级公差和表面粗糙度的确定 (10)5.1.8 蜗杆的结构设计 (10)5.2 螺杆的设计计算 (13)5.2.1 螺距的确定 (13)5.2.2 其他参数的确定 (13)5.2.3 自锁性能校核 (14)6、电气控制部分设计 (14)6.1 硬件电路设计 (14)6.1.1 收信电路 (14)6.1.2 发信号电路 (14)6.2 控制软件的设计 (15)数控车床自动回转刀架机电系统设计摘要:本设计以 C616 或 C6132 经济型数控车床的四位的卧式自动回转刀架为研究对象,从该刀架的总体结构、主要传动机构、主要传动部件、硬件电路和控制程序等方面进行了设计。
并在文中给出了详细的关于传动零件的设计计算。
关键词:数控、四工位、卧式刀架、自动回转、定位1、引言数控车床为了能在工件的一次装夹中完成多工序加工,缩短辅助时间,减少多次安装所引起的加工误差,必须带有自动回转刀架,数控车床上的回转刀架是一种简单的自动换刀装置。
传统的普通车床换刀的速度慢、精度不高,生产效率低,不能适应现代化生产的需要。
而目前我国有大量多年积累使用的通用的机床,要在几年内更新换代,不论是在资金上还是经济效益上都是不可行的,所以对其进行半自动化改造显得重要和迫切。
而普通车床的数控改造既经济又快捷,是符合我国国情的。
Φ320mm的数控车床总体设计及六角回转刀架设计

摘要全面阐述了数控车床的结构原理,设计特点,论述了数控车床的设计计算过程,具体阐述如下:1、数控机床发展概述:数控机床及其特点,数控机床的工艺范围及加工精度,数控机床的经济分析,数控机床的发展趋向。
2、数控机床总体方案的制订及比较3、确定切削用量及选择刀具4、本文主要进行的是Φ320mm的数控车床总体设计及六角回转刀架设计关键词:车床,数控,伺服电机AbstractComprehensively elaborated numerical control lathe structure principle, design features, discusses the CNC lathes horizontal feed system design and calculation process, described specifically as follows:1, the development of CNC Machine Tools Overview: CNC machine tool and its characteristics, the process of NC machine tool and machining accuracy of NC machine tools, CNC machine tools of economic analysis, development trend.2, NC machine overall plan formulation and comparison3, determine the cutting parameters and selection of cutting tool4, this paper mainly carries on is Φ320mm CNC lathe design and transverse feeding design,Key Words: lathe, numerical control, servo motor, ball screw, a transverse feed目录摘要 (I)Abstract (II)目录 (III)第1章绪论 (1)1.1数控机床及其特点 (1)1.2数控机床的工艺范围及加工精度 (2)1.3 数控机床的经济分析 (3)1.4 数控机床的发展趋向 (4)第2章数控机床总体方案的制订及比较 (8)2.1 总体方案比较 (8)2.2 数控车床方案确定 (15)第3章确定切削用量及选择刀具 ........................................................ 错误!未定义书签。
数控车床工位自动回转刀架结构设计
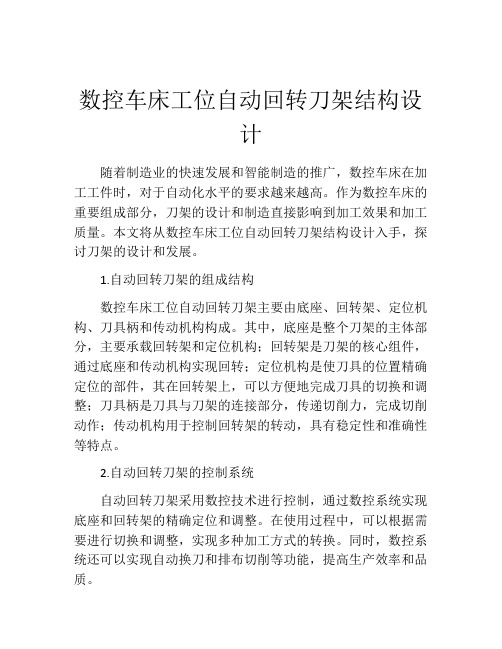
数控车床工位自动回转刀架结构设计随着制造业的快速发展和智能制造的推广,数控车床在加工工件时,对于自动化水平的要求越来越高。
作为数控车床的重要组成部分,刀架的设计和制造直接影响到加工效果和加工质量。
本文将从数控车床工位自动回转刀架结构设计入手,探讨刀架的设计和发展。
1.自动回转刀架的组成结构数控车床工位自动回转刀架主要由底座、回转架、定位机构、刀具柄和传动机构构成。
其中,底座是整个刀架的主体部分,主要承载回转架和定位机构;回转架是刀架的核心组件,通过底座和传动机构实现回转;定位机构是使刀具的位置精确定位的部件,其在回转架上,可以方便地完成刀具的切换和调整;刀具柄是刀具与刀架的连接部分,传递切削力,完成切削动作;传动机构用于控制回转架的转动,具有稳定性和准确性等特点。
2.自动回转刀架的控制系统自动回转刀架采用数控技术进行控制,通过数控系统实现底座和回转架的精确定位和调整。
在使用过程中,可以根据需要进行切换和调整,实现多种加工方式的转换。
同时,数控系统还可以实现自动换刀和排布切削等功能,提高生产效率和品质。
3.自动回转刀架的发展趋势随着自动化技术的不断创新和应用,自动回转刀架的发展也日益向智能化、自动化方向发展。
多刀位刀架、柔性制造单元等新技术的应用,使刀架能够适应更加个性化和定制化的生产需求,为加工行业带来了很大的便利。
同时,自动化控制系统和机器视觉技术等的应用,使刀架在操作和控制方面得到了进一步的提升,为加工行业发展带来了新的机遇和挑战。
综上,数控车床工位自动回转刀架的设计和制造,是制造业向自动化、智能化转型的重要一步,对于提高生产效率和保证产品质量都具有重要意义。
未来,随着技术的不断发展和创新,自动回转刀架的应用前景将更加广阔,也将为制造业发展带来更大的贡献。
普通数控车床八工位回转刀架设计

优秀设计C616卧式车床八工位数控回转刀架设计【摘要】数控加工的加工精度高,生产率高,能减轻操作者劳动强度、改善劳动条件,有利于生产管理的现代化以及经济效益的提高,它的发展和运用,影响着制造业水平高低,实现生产过程的数控化,已经成为当今制造业的发展方向,所以非常值得我们去研究。
本设计通过对八工位卧式电动控制刀架的工作原理的分析,确定了多种方案,综合考虑各种方案的优缺点、性价比后,采用电动回转刀架。
其刀架机构的主要部件包括减速传动机构、刀架的抬起机构、锁紧与转位精定位机构等,控制系统软件包括控制系统的选择,控制系统软硬件的设计,收发信电路的设计等,设计中所采用螺杆抬起机构、端齿盘定位机构和单片机控制系统都计较经济实用,适合我们我国现阶段数控机床的发展需要。
【关键词】八工位,电动刀架,自动化,8051单片机[Abstract]Machining accuracy of NC processing is high, high productivity, can reduce the operator's labor intensity, improve working conditions, conducive to the modernization of production management and improving economic benefit, its development and use, affects the level of manufacturing industry, the NC manufacturing process, has become the development direction of manufacturing industry, it is worth we are going to study.This design through the analysis of the working principle of the eight station horizontal electric control tool, a variety of scheme is determined, considering the advantages and disadvantages of various schemes, the price, the electric rotary turret. The cutter mechanism mainly comprises a deceleration transmission mechanism, cutter lifting mechanism, locking and indexing precision positioning mechanism, control system consists of control system selection, design of software and hardware of the control system, the transceiver circuit design, the screw lift mechanism, the tooth disk positioning mechanism and a single-chip microcomputer control system each of them is economic and practical design, development suited to our needs in our country at the present stage of CNC machine tools.Key word:The eight station, electric tool, automation, 8051 single chip microcomputer目录1 绪论 (5)1.1 引言 (5)1.2 国内外研究现状 (5)1.3 存在的问题 (6)1.4 解决的方法 (7)2 方案设计 (8)2.1 自动刀架的基本要求和类型 (8)2.1.1自动刀架的基本要求 (8)2.1.2自动刀架的类型 (8)2.2 方案的拟定和确定 (9)3 总体结构设计 (11)3.1 减速传动机构方案设计 (11)3.2 刀架抬起机构设计 (12)3.3 上刀体锁紧与精定位机构设计 (13)4 主要部件的设计计算 (15)4.1 减速传动机构的设计计算 (15)4.1.1蜗杆的选型 (15)4.1.2蜗杆副的材料选择 (15)4.1.3按齿面接触疲劳强度进行设计 (15)4.1.4蜗杆和蜗轮的主要参数与几何尺寸 (19)4.1.5校核蜗轮齿根弯曲疲劳强度 (19)4.2 螺杆的设计计算 (21)4.2.1螺距的确定 (21)4.2.2其他参数的确定 (21)4.2.3自锁性能校核 (21)4.3 端齿盘设计 (22)4.3.1 端齿盘的特点 (22)4.3.2 端齿盘主要参数的设计计算 (22)5 电气控制部分设计 (26)5.1 控制系统的选择 (26)5.2 控制方式的选择 (27)5.3 硬件电路设计 (27)5.3.1收信电路设计 (27)5.3.2发信电路设计 (29)5.4 控制软件设计 (31)6 致谢 (37)7 参考文献 (38)1 绪论1.1 引言电动刀架是数控车床重要的传统结构,应用了自动控制、微电子、传感测量等方面的最新成就,是典型的机电一体化产品。
数控车床自动回转刀架机电系统设计

数控车床自动回转刀架机电系统的设计涉及机械结构、电气控制和编程等多个方面。
以下是设计该系统时需要考虑的关键要点:
1. 机械结构设计
-设计回转刀架的结构,包括支撑轴承、回转机构等,确保其稳定可靠地进行自动回转;
-确定回转角度范围和精度要求,根据加工需求设计相应的回转机构。
2. 电气控制系统设计
-选择合适的电机作为驱动源,考虑其扭矩、速度和精度等参数;
-设计控制电路,包括限位开关、传感器等,用于检测刀架位置和控制回转动作;
-配备必要的安全装置,例如急停按钮、防护罩等,确保操作安全。
3. PLC/数控系统编程
-编写程序实现自动回转功能,包括控制电机驱动、位置检测、回转角度设定等;
-考虑编程中的异常情况处理,例如限位保护、电机故障等。
4. 人机界面设计
-如果需要,设计操作界面用于设定回转角度、启动自动回转等操作;-界面设计应直观友好,便于操作员使用。
5. 性能测试与调试
-进行机械部件的装配和调试,确保回转刀架运动平稳、精度满足要求;
-对电气控制系统进行联调和功能测试,验证自动回转功能的准确性和稳定性。
6. 安全考虑
-确保机械结构和电气系统符合相关安全标准和规定;
-检查系统运行过程中可能存在的安全隐患,并采取相应的安全措施。
设计数控车床自动回转刀架机电系统需要综合考虑机械、电气、控制等多个方面,确保系统能够稳定可靠地实现自动回转功能,并且满足加工工艺的要求。
在设计过程中,需要充分考虑系统的易用性、安全性和可靠性。
车床六角回转刀架系统数控改造

目录1 方案设计 (3)1.1 自动刀架的基本形式和应满足的要求 (3)1.1.1自动刀架的形式 (3)1.1.2 自动刀架的基本要求和功能分析 (4)1.2 初步确定自动刀架的方案 (4)2 总体结构设计 (6)2.1 减速传动机构方案设计 (6)2.2 上刀体锁紧与精定位机构设计 (6)2.3 刀架抬起机构设计 (7)3 自动回转刀架的工作原理 (8)3.1 自动回转刀架的换刀流程 (8)3.2 自动回转刀架的换刀过程中有关销的位置 (9)4 主要传动部件的设计计算 (10)4.1 蜗杆副的设计计算及电动机的选择 (10)4.1.1蜗杆的选型 (10)4.1.2蜗杆副的材料 (10)4.1.3按齿面接触疲劳强度进行设计 (11)4.1.4蜗杆和蜗轮的主要参数与几何尺寸 (12)4.1.5校核蜗轮齿根弯曲疲劳强度 (13)4.2 螺杆的设计计算 (13)4.2.1螺距的确定 (13)4.2.2其他参数的确定 (13)4.2.3自锁性能校核 (14)5 锁紧定位机构的设计 (14)5.1 端齿盘设计 (14)5.2 端齿盘的特点 (15)5.3 端齿盘主要参数的设计计算 (15)5.3.1齿数z的确定 (16)5.3.2端齿盘外径d (16)5.3.3端齿盘齿形角...................................................................... 错误!未定义书签。
5.3.4齿根角(啮合斜角) (17)5.3.5最大齿距(周节)t和最大齿厚B (18)5.3.6齿顶高h及啮合高度 (18)5.3.7齿宽(径向)F (19)5.3.8齿底槽宽b和齿顶宽b1 (19)6 电气控制部分设计 (19)6.1 自动控制系统设计 (19)6.2 单片机选型 (20)6.3 硬件电路的设计 (21)6.4 硬件电路主要电子元件的工作原理 (22)6.4.1霍尔元件的工作原理和特性 (22)6.4.2 霍尔开关的工作原理 (24)6.4.3 光电耦合器的工作原理 (25)6.4.4 8255芯片的工作原理 (26)6.5 控制软件的设计 (26)6.5.1 换刀工作原理的程序流程图 (27)6.5.2 程序的实现方法 (27)参考文献 (29)1 方案设计普通的机械零件的加工制造过程中,大量的时间用于更换刀具、装卸零件、测量和搬运零件等非切削时间上,切削加工时间仅占整个工时中较小的比例。
- 1、下载文档前请自行甄别文档内容的完整性,平台不提供额外的编辑、内容补充、找答案等附加服务。
- 2、"仅部分预览"的文档,不可在线预览部分如存在完整性等问题,可反馈申请退款(可完整预览的文档不适用该条件!)。
- 3、如文档侵犯您的权益,请联系客服反馈,我们会尽快为您处理(人工客服工作时间:9:00-18:30)。
哈尔滨理工大学课程设计说明书设计题目:数控车床自动回转刀架结构设计班级:学号:姓名:指导老师:日期:设计任务题目:数控车床自动回转刀架结构设计任务:设计一台四工位立式回转刀架,适用于C616或C6132经济型数空车床。
要求绘制自动回转刀架的机械结构图。
推荐刀架所用电动机的额定功率为90W,额定转速1480r/min,换刀时要求刀架转动的速度为40r/min,减速装置的传动比为i=37。
总体结构设计1、减速传动机构的设计普通的三项异步电动机因转速太快,不能直接驱动刀架进行换刀,必须经过适当的减速。
根据立式转位刀架的结构特点,采用蜗杆副减速时最佳选择。
蜗杆副传动可以改变运动的方向,获得较大的传动比,保证传动精度和平稳性,并且具有自锁功能,还可以实现整个装置的小型化。
2、上刀体锁紧与精定位机构的设计由于刀具直接安装在上刀体上,所以上刀体要承受全部的切削力,其锁紧与定位的精度将直接影响工件的加工精度。
本设计上刀体的锁进玉定位机构选用端面齿盘,将上刀体和下刀体的配合面加工成梯形端面齿。
当刀架处于锁紧状态时,上下端面齿相互啮合,这时上刀体不能绕刀架的中心轴旋转;换刀时电动机正转,抬起机构使上刀体抬起,等上下端面齿脱开后,上刀体才可以绕刀架中心轴转动,完成转位动作。
3、刀架抬起机构的设计要想使上、下刀体的两个端面齿脱离,就必须设计适合的机构使上刀体抬起。
本设计选用螺杆-螺母副,在上刀体内部加工出内螺纹,当电动机通过蜗杆-涡轮带动蜗杆绕中心轴转动时,作为螺母的上刀体要么转动,要么上下移动。
当刀架处于锁紧状态时,上刀体与下刀体的端面齿相互啮合,因为这时上刀体不能与螺杆一起转动,所以螺杆的转动会使上刀体向上移动。
当端面齿脱离啮合时,上刀体就与螺杆一起转动。
设计螺杆时要求选择适当的螺距,以便当螺杆转动一定的角度时,使得上刀梯与下刀体的端面齿能够完全脱离啮合状态。
下图为自动回转刀架的传动机构示意图,详细的装配图在一号图纸上。
三、自动回转刀架的工作原理自动回转刀架的换刀流程如下图。
图上表示自动回转刀架在换刀过程中有关销的位置。
其中上部的圆柱销2和下部的反靠销6起着重要作用。
当刀架处于锁紧状态时,两销的情况如图A所示,此时反靠销6落在圆盘7的十字槽内,上刀体4的端面齿和下刀体的端面齿处于啮合状态(上下端面齿在图中未画出)。
需要换刀时,控制系统发出刀架转位信号,三项异步电动机正向旋转,通过蜗杆副带动蜗杆正向转动,与螺杆配合的上刀体4逐渐抬起,上刀体4与下刀体之间的端面齿慢慢脱开;与此同时,上盖圆盘1也随着螺杆正向转动(上盖圆盘1通过圆柱销与螺杆联接),当转过约1700时,上盖圆盘1直槽的另一端转到圆柱销2的正上方,由于弹簧3的作用,圆柱销2落入直槽内,于是上盖圆盘1就通过圆柱销2使得上刀体4转动起来(此时端面齿已完全脱开)。
上盖圆盘1、圆柱销2以及上刀体4在正转的过程中,反靠销6能够从反靠圆盘7中十字槽的左侧斜坡滑出,而不影响上刀体4寻找刀位时的正向转动。
上刀体4带动磁铁转到需要的刀位时,发信盘上对应的霍尔元件输出低电平信号,控制系统收到后,立即控制刀架电动机反转,上盖圆盘1通过圆柱销2带动上刀体4开始反转,反靠销6马上就会落入反靠圆盘7的十字槽内,至此,完成粗定位。
此时,反靠销6从反靠圆盘7的十字槽内爬不上来,于是上刀体4停止转动,开始下降,而上盖圆盘1继续反转,其直槽的左侧斜坡将圆柱销2的头部压入上刀体4的销空内,之后,上盖圆盘1是下表面开始与圆柱销2的头部滑动。
再次期间,上、下刀体的端面齿逐渐啮合,实现精定位,经过设定的延时时间后,刀架电动机停转,整个换刀过程结束。
由于蜗杆副具有自锁功能,所以刀架可以稳定地工作。
蜗杆-涡轮减速销连接主要传动部件的设计1.蜗杆副的设计计算自动回转刀架的动力源是三相异步电动机。
其中蜗杆与电动机直联,刀架转位时蜗轮与上刀体直联。
已知电动机额定功率p1=90W。
,额定转速n1=1480r/min,上刀体设计转速n2=40r/min,蜗杆副的传动比i=n1/n2=37。
刀架从转位到锁紧时,需要蜗杆反向,工作载荷不均匀,启动时冲击较大,今要求蜗杆副的使用寿命L h=10000h。
(1)蜗杆的选型 GB/T10085-1988推荐采用渐开线蜗杆和锥面包络蜗杆。
本设计采用结构简单,制造方便的渐开线型圆柱蜗杆。
(2)蜗杆副的材料刀架中的蜗杆副传动的功率不大,但蜗杆转速干,一次,蜗杆的材料选用45钢,其螺旋齿面要淬火,硬度为45~55HRC,以提高其表面耐磨行;蜗轮的转速较低,其材料主要考虑耐磨性,选用铸锡磷青铜ZCuSn10P1,采用金属模制造。
(3)按齿面接触疲劳强度进行设计刀架中的蜗杆副采用闭式传动,多因齿面胶合或点蚀而失效。
因此,进行载荷计算时,先按齿面接触疲劳强度进行设计,再按齿根弯曲疲劳强度进行校核。
按蜗轮接触疲劳强度条件设计计算的公式a≥√ KT2( Z E Z P[σH] )23(4-1)式中 a——蜗杆副的传动中心距,单位mm;K——载荷系数;T2——作用在涡轮上的转矩T2,单位;Z E——弹性影响系数ZE;[σH]——许用接触应力,单位为MPa。
从式4-1算出蜗杆副的中心距a之后,根据已知的传动比i=35,查表选择一个合适的中心距a值,以及相应的蜗杆,蜗轮参数。
1)确定作用在蜗轮上的转矩T2,设蜗杆头数Z1=1,蜗杆副的传动效率η=,由电动机的额定功率p1=90W,可以算出蜗轮传动的功率p2=p1η,再由蜗轮的转速n2=40r/min求得作用在蜗轮上的转矩T2=p2n2=p1ηn2=·m=22923N·mm2)确定载荷系数K 载荷系数K= KA KB K。
其中KA为使用系数,有表6-3查得,由于工作载荷不均匀,启动时冲击较大,因此取KA=K A;Kβ为齿向分布系数,因工作载荷在启动和停止时有变化,故取KB Kβ=;K V为动载系数,由于转数不高。
冲击不大,可取K K V=。
则载荷系数K=KA KB K ≈E手册查的弹性影响系数 ZE=160Mpa 1/2;4)确定接触系数Z P先假设蜗杆分度圆直径d1 和传动中心距a的比值d1d1/a=。
查表的Zp Zρ=5H金属模制造蜗杆螺旋齿面硬度大于45HRC可查表的蜗轮的基本许用应力[σH] ‘=268MPa已知蜗杆为单头,蜗轮每转一转时每个轮齿啮合的次数j=1;蜗轮转数n2=40r/min;蜗杆副的使用寿命L h=10000h。
则应力循环次数:N=60j n2 L h = ×10 7寿命系数:KHN =K HN许用接触应力:[σ ]=KHN× [σH] ‘K HN=186MPa6)计算中心距将以上各参数带入4-1,求得中心距:a = mm查表取a=63,已知蜗杆头数z1=1,设模数m=,得蜗杆分度圆直径d1d1=28mm。
这时d1d1/a=,查表得接触系数Z`P=。
因为Z`P<Z P较大,所以上述计算结果可用。
(4)蜗杆和涡轮的主要参数与几何尺寸由蜗杆和涡轮的基本尺寸和主要参数,算的蜗杆和涡轮的主要几何尺寸后,即可绘制蜗杆副的工作图。
1)蜗杆的参数与尺寸头数z1=1,模数m=,轴向齿距p a=πm=轴向齿厚s a=π=,分度圆直径d1=28,⁄=,直径系数q=d1m=3016‘14“。
分度圆导程角γ=tan−1z1q取齿顶高系数h a∗=1,径向间隙系数c∗=,则齿顶圆直径d a1=d1+2h a∗m=,齿根圆直径d f1=d1-2m(h a∗+c∗)=。
2)涡轮参数与尺寸齿数z2=60,模数m=,分度圆直径为d2=m z2=96mm,变位系数x2=[a-(d1+d2)/2]/m=,涡轮喉圆直径为d a2=d2+2m(h a∗+x2)=,涡轮齿根圆直径d f2=d 2-2m (h a ∗-x 2+c ∗)=,涡轮咽喉母圆半径r g2=a-d a2/2=。
(5)校核涡轮齿根弯曲疲劳强度 即检验下式是否成立:σF =1.53KT 2d 1d 2m Y Fa2Y β≤[σF ]由蜗杆头数z 1=1,传动比i=35,可以计算出涡轮齿数z 2=i z 1=35则涡轮的当量齿数:z v2=z 2cos γ3= 根据涡轮变位系数x 2=和当量齿数z v2=,查表的齿形系数Y Fa2=螺旋角影响系数Y β=1-γ140°=根据涡轮的材料和制造方法,查表得涡轮基本许用弯曲应力:[σF ]′=56MPa涡轮的寿命系数:K FN =√106N 9= 涡轮的许用弯曲应力:[σF ]= [σF ]′ K FN =将数据带入得:[σF ]≈25.33MPa可见, [σF ]≤ [σF ]′,涡轮齿根的弯曲强度满足要求。
蜗轮材料 铸造方法单侧工作双侧工作铸锡青铜ZCuSn10P1 砂模铸造40 29 金属模铸造56 40 铸锡锌铅青铜ZCuSn5Pb5Zn5 砂模铸造 26 22 金属模铸造32 26 铸铝铁青铜ZCuAl10Fe3 砂模铸造 80 57 金属模铸造90 64 灰铸铁 HT150 砂模铸造 40 282.(1)螺距的确定刀架转位时,要求螺杆在转动约的情况下,上刀体的端面齿与下刀体的端面齿完全脱离;在锁紧的时候,要求上下端面的啮合深度达2mm。
因此,螺杆的螺距P应满足P>,今取螺杆的螺距P=6mm。
(2)确定其他参数采用单头梯形螺杆,头数n=1,牙侧角β= 150,外螺纹大径d1=50mm,牙顶间隙a c=,基本牙型高度H1==3mm,外螺纹牙高h3=,外螺纹中径d2=47mm,外螺纹小径d3=43mm,螺杆螺纹部分长度H=50mm。
(3)自锁性能校核螺杆-螺母材料均用45钢,查表取摩擦系数f=;再求得梯形螺旋副的当量摩擦角:≈6.50φV=tan−1fcosβ而螺纹升角:Ψ=tan−1nP=πd2小于当量摩擦角。
因此满足自锁条件。