PCB工艺技术参数
刚性PCB工艺能力参数
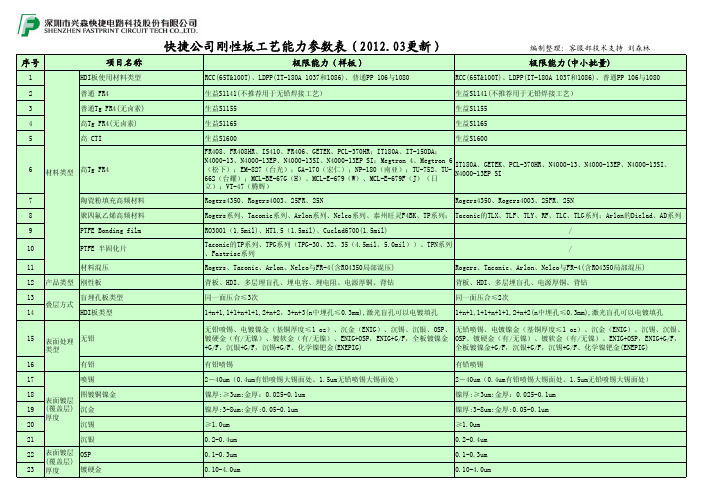
NPTH:槽宽、槽长方向均±0.10mm;PTH:槽宽、槽长方向均±0.13mm
NPTH:槽宽、槽长方向均±0.10mm;PTH:槽宽、槽长方向均±0.13mm
10mil(对应4mil激光孔),11mil(对应5mil激光孔) 16mil(8mil钻孔)
10mil(对应4mil激光孔),11mil(对应5mil激光孔) 16mil(8mil钻孔)
1/3oz、1/2oz: 3/3 mil
1oz:
3/4 mil
2oz:
4/5.5 mil
3oz:
5/8 mil
4oz:
6.5/11 mil
5oz:
7/14 mil
6oz:
8/16 mil
7oz:
9/19 mil
8oz:
10/22mil
9oz: 10oz: 1/3oz: 1/2oz: 1oz: 2oz:
54
背钻深度精度公差
55 锥形孔、阶梯孔角度与直径
56
57
阶梯、锥形孔角度公差
58
阶梯、锥形孔孔口直径公差
59
阶梯、锥形孔深度公差
孔
60
异形槽孔公差(铣孔)
61
控深铣槽(边)深度精度(NPTH)
62 钻槽槽孔最小公差
63
64
铣槽槽孔最小公差
65
激光孔内、外层焊盘尺寸最小
66
机械过孔内、外层焊盘尺寸最小
84
3oz:
7/10 mil
85
4oz:
8/13 mil
86
5oz:
9/15.5 mil
87 外层
88 线宽/线距
89 能力
6oz: 7oz: 8oz:
PCB技术参数范文

PCB技术参数范文PCB(Printed Circuit Board)即印刷电路板,是一种用于连接和支持电子元件的非导电板。
它在电子设备中广泛应用,如计算机、手机、电视、汽车、医疗设备等。
PCB的技术参数对于电子设备的性能和功耗都有重要影响,下面将介绍一些常见的PCB技术参数。
第一个重要参数是PCB板材的基底材料,它决定了PCB的机械强度、热传导性以及电流传输特性。
常见的基底材料有FR4、CEM-1、CEM-3、高TG板材等。
FR4是最常用的基底材料,具有良好的机械强度和电气性能。
高TG板材则具有更高的玻璃化转变温度,适用于高温环境。
第二个参数是PCB板厚度,通常以单位为mil(1mil=0.0254mm)来衡量。
常见的PCB板厚度有1.6mm、1.2mm、1.0mm等。
较厚的PCB板可以提供更好的机械强度,但也会增加重量和成本。
较薄的PCB板可以节省空间,但可能对机械强度和散热造成一定的影响。
第四个参数是PCB板上导线的宽度和间距,通常以mil或um来衡量。
导线的宽度和间距对于PCB板的电流承载能力和信号传输性能至关重要。
较宽的导线可以承载更大的电流,而较窄的导线可以提供更高的线路密度。
间距的大小决定了导线之间的绝缘性能,较小的间距可以提高线路的抗干扰能力。
第五个参数是PCB板的阻焊和喷锡。
阻焊层可以保护PCB板上的铜线和焊盘免受环境的腐蚀,并降低线路之间的短路风险。
喷锡层可以提供良好的焊接性能,增加元件的连接可靠性和耐久性。
第六个参数是PCB板的孔径和孔壁容量。
PCB板上的孔可用于连接不同层之间的线路或安装元件。
孔直径对于PCB板的组装和钻孔工艺有很大影响,而孔壁容量则决定了孔内的焊锡量和焊盘可靠性。
总之,PCB技术参数直接影响了PCB板的性能和可靠性。
合理选择和控制这些参数对于电子设备的正常运行和性能优化至关重要。
pcb制作工艺指标

pcb制作工艺指标PCB(Printed Circuit Board,印刷电路板)制作工艺指标是衡量PCB制作质量和性能的一系列标准和参数。
这些指标涵盖了从材料选择、电路设计、制作工艺到最终测试等各个环节,确保PCB能够满足设计要求并具备良好的可靠性和稳定性。
以下是对PCB制作工艺指标的详细解读。
一、材料选择1. 基材选择:基材是PCB的核心部分,常用的有酚醛纸基板、环氧树脂基板、聚酰亚胺基板等。
选择合适的基材需要考虑其电气性能、热稳定性、机械强度等因素。
2. 导电材料:导电材料包括铜箔、导电油墨等,用于形成电路中的导线和元件连接。
导电材料的选择应关注其导电性能、附着力、耐腐蚀性等方面。
3. 绝缘材料:绝缘材料用于隔离不同导电层,保证电路的正常工作。
常见的绝缘材料有阻焊膜、绝缘油墨等。
二、电路设计1. 线路设计:线路设计应遵循简洁、清晰、易读的原则,尽量减少导线交叉和弯曲,以降低电气性能损失和故障风险。
2. 元件布局:元件布局应合理,便于焊接、维修和散热。
同时,应避免元件之间的相互干扰和信号损失。
3. 接地与屏蔽:接地设计应确保电路的安全稳定运行,屏蔽设计则用于减少电磁干扰,提高电路性能。
三、制作工艺1. 制版工艺:制版是PCB制作的第一步,包括绘制电路图、制作菲林底片、曝光等步骤。
制版工艺的精度和稳定性直接影响PCB的质量。
2. 蚀刻工艺:蚀刻是将非导电部分的铜箔蚀刻掉,形成电路图形的过程。
蚀刻工艺的控制精度和蚀刻速度是影响PCB质量的关键因素。
3. 孔加工工艺:孔加工包括钻孔、铣孔等步骤,用于形成电路中的通孔和盲孔。
孔加工的精度和孔壁质量对PCB的电气性能和可靠性有重要影响。
4. 导线制作工艺:导线制作包括导线焊接、导线压接等步骤,用于将元件与电路连接起来。
导线制作工艺的精度和稳定性对PCB的电气性能和可靠性至关重要。
5. 阻焊与字符印刷工艺:阻焊工艺用于在电路表面涂覆一层阻焊膜,防止焊接时短路和氧化。
pcb钻孔工艺参数确定方法
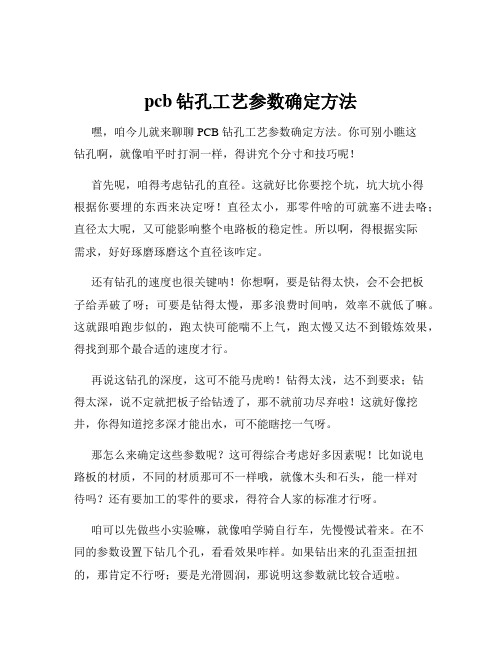
pcb钻孔工艺参数确定方法嘿,咱今儿就来聊聊 PCB 钻孔工艺参数确定方法。
你可别小瞧这钻孔啊,就像咱平时打洞一样,得讲究个分寸和技巧呢!首先呢,咱得考虑钻孔的直径。
这就好比你要挖个坑,坑大坑小得根据你要埋的东西来决定呀!直径太小,那零件啥的可就塞不进去咯;直径太大呢,又可能影响整个电路板的稳定性。
所以啊,得根据实际需求,好好琢磨琢磨这个直径该咋定。
还有钻孔的速度也很关键呐!你想啊,要是钻得太快,会不会把板子给弄破了呀;可要是钻得太慢,那多浪费时间呐,效率不就低了嘛。
这就跟咱跑步似的,跑太快可能喘不上气,跑太慢又达不到锻炼效果,得找到那个最合适的速度才行。
再说这钻孔的深度,这可不能马虎哟!钻得太浅,达不到要求;钻得太深,说不定就把板子给钻透了,那不就前功尽弃啦!这就好像挖井,你得知道挖多深才能出水,可不能瞎挖一气呀。
那怎么来确定这些参数呢?这可得综合考虑好多因素呢!比如说电路板的材质,不同的材质那可不一样哦,就像木头和石头,能一样对待吗?还有要加工的零件的要求,得符合人家的标准才行呀。
咱可以先做些小实验嘛,就像咱学骑自行车,先慢慢试着来。
在不同的参数设置下钻几个孔,看看效果咋样。
如果钻出来的孔歪歪扭扭的,那肯定不行呀;要是光滑圆润,那说明这参数就比较合适啦。
然后呢,多和有经验的师傅交流交流。
他们可是过来人,就像武林高手一样,有好多秘籍呢!听听他们的建议,说不定能让你少走好多弯路呢。
你想想,要是参数没确定好,那生产出来的 PCB 板子能好用吗?那肯定不行呀!就像盖房子,根基没打好,房子能结实吗?所以说呀,这 PCB 钻孔工艺参数确定可真是个技术活,得认真对待,不能马虎!咱可不能小看了这些参数,它们就像电路板的灵魂一样。
只有把这些参数确定好了,才能生产出高质量的 PCB 板子,才能让那些电子设备好好工作呀!所以呀,大家可得重视起来,好好研究研究这个 PCB钻孔工艺参数确定方法,让咱的电路板更完美,让咱的电子世界更精彩!。
ad pcb丝印参数

ad pcb丝印参数全文共四篇示例,供读者参考第一篇示例:PCB丝印是指在PCB板上印刷标识、文字或图形的一种工艺。
在PCB制造过程中,丝印通常是最后一步完成的工艺之一,但却是非常重要的一步。
PCB丝印不仅可以实现产品的品牌宣传和标识,同时也可以提供重要的组装和维修信息。
在PCB丝印设计和制作中,需要考虑许多参数,以确保最终的效果符合要求。
一、PCB丝印的参数在制作PCB丝印时,有许多参数需要考虑,包括文字、符号、标识的大小、位置、字形、颜色等。
以下是一些常见的PCB丝印参数:1. 文字大小:PCB丝印中的文字大小通常是根据PCB板的尺寸和要印的内容来确定的。
通常建议文字大小不要小于0.8mm,以确保清晰可见。
2. 文字位置:文字的位置要考虑PCB板上其他元件的位置,避免遮挡或干扰其他元件。
3. 字形:字形选择应简洁,易于识别,不易混淆。
4. 颜色:PCB丝印通常使用白色墨水,但也可以根据需要选择其他颜色。
考虑文字和背景的对比度,以确保清晰可见。
5. 图形大小和位置:如果PCB丝印中包含一些图形或标识,需要考虑图形的大小和位置,避免与其他元件重叠或干扰。
6. 线宽和间距:PCB丝印中的线宽和间距要考虑打印设备的分辨率和精度,以确保最终印刷效果清晰。
7. 对齐:PCB丝印中的内容要保持整齐、对齐,避免出现错位或不规则的情况。
8. 透过度:PCB丝印的墨水应该透过度适中,不要太浓或太淡,以免影响PCB的外观和质量。
以上是一些常见的PCB丝印参数,根据具体情况,还可以考虑其他因素,以确保PCB丝印最终达到预期效果。
二、如何设计和制作PCB丝印在设计和制作PCB丝印时,需要遵循一定的步骤和流程,以确保最终的印刷效果符合要求。
2. 设计PCB丝印图纸:在设计PCB丝印图纸时,需要考虑之前确定的参数,使用专业的设计软件进行设计,并确保图纸的精度和准确性。
3. 选择合适的PCB丝印材料:选择适合的PCB丝印胶片和墨水,根据PCB板的材料和要求进行选择,以确保印刷效果良好。
PCB设计工艺要求

目的:明确设计PCB过程中的工艺各项要求,做到标准化设计。
以提高开发效率及方便生产。
适用范围:适用于本公司的电话机产品设计。
职责:各开发工程师及PCB Layout工程师按规定执行。
1、单面板要求:1:线径、线距不小于0.3mm,建议为0.35mm以上。
(半玻纤板及玻纤板不小于0.18mm)。
2:焊盘和焊盘之间的间距不小于0.5mm。
3:走线至板边距离板不小于0.8mm。
4:过孔至板边距离不小于1.6mm。
5:元件焊盘孔径不小于0.7mm。
6:丝印文字线宽不小于0.18mm,SMT不小于0.13mm。
7:板的碳桥宽度不小于2.0mm。
碳桥与碳桥之间的距离不小于1mm。
碳桥越短越好,最长不能超过15mm。
(除非特殊限制,但需项目工程师以上人员同意才能使用)8:板边宽的部分离焊盘必须大于3mm以上,SMT板大于5mm。
9:固定螺丝的孔位直径5mm以内不能有元件实体;与非地线的铜皮直径距离为5mm。
2、双面板要求:1:线径、线距(金板)不小于0.15mm。
(锡板不小于0.18mm)2:线边距板边不小于0.8mm。
3:孔边距板边不小于1.6mm。
4:孔径不小于0.35mm。
5:丝印文字线宽不小于0.18mm,SMT不小于0.13mm。
6:板边宽的部分离焊盘必须大于3mm以上,SMT板大于5mm。
7:焊盘和焊盘之间的间距不小于0.5mm8:固定螺丝的孔位直径5mm以内不能有元件实体;与非地线的铜皮直径距离为5mm。
9:双面板PCB螺丝孔位不能灌铜(锡浆板除外)。
3、PCB设计布局及走线等基本要求:1、所有元件放置要有规律,同一工作部分电路尽量靠在一起,避免走长线;电阻要平插元件尽量排成行,如无特殊要求尽量减少直立元件插件。
2、外线进线部分(包括压敏电阻)必须靠在一起,因开关电路以前的电路属于高压部分,此走线不要太长越短越好,铜皮走线线径不能小于0.45mm;,不要靠近其它信号线和CPU的IO口,避免对它的干扰。
PCB制作工艺参数要求

一、PCB制作文件类型1、PCB文件(支持Protel系列软件、AD系列软件和PADS软件);2、Gerber文件。
注意事项:关于Protel系列、AD系列软件和PADS软件设计的多层板订单,1、如果内层存在负片设计,一定要提供Gerber文件;2、如果内层全部采用正片设计,建议提供Gerber文件Protel软件转gerber方法:AD软件转gerber方法:PADS软件转gerber方法:Allegro软件转gerber方法:二、制程工艺要求1、字符:电路板中丝印字符(Silkscreen)线宽不能小于,字符高度不能小于(如下图参数),宽高比理想为1:5。
如果小于本参数嘉立创工厂将不会对文件中的字符做大小调整,从而可能会因超出生产能力而导致字符严重不清楚情况发生。
公司将不接受因设计不符合规则而导致字符不清楚的此类投诉。
特此通知!此外,字符不允许上焊盘,字符距离焊盘需不小于7mill。
2、基材FR-4:玻璃布-环氧树脂覆铜箔板。
嘉立创采用的是KB建滔的A级料,铜箔为%以上的电解铜,成品表面铜箔厚度常规 35um(1OZ),板厚,公差±10%3、最小孔径,外径,保证单边焊环不得小于。
我司会对于插键孔(Pad)进行加大补偿左右,以弥补生产过程中因孔内壁沉铜造成的孔径变小,而对于导通孔(Via) 则不进行补偿,设计时Pad与Via不能混用,否则因为补偿机制不同而导致你元器件难于插进,印制导线的宽度公差内控标准为±10%。
4、网格状铺铜的处理:因为采用干膜,网格会产生干膜碎,导致开路的可能,为便于电路板生产,铺铜尽量铺成实心铜皮,如果确实要铺成网格,其网格间距应在10mil以上,网格线宽应在10mil以上。
5、孔径与孔径最小间距10mil。
避免因孔间距过近,导致钻孔时断钻头和塞孔导致的孔内无铜现象。
6、内层走线和铜箔距离钻孔应在以上。
建议元器件接地脚采用隔热盘走线和铜箔距离钻孔应在以上,外层走线和铜箔距板边应在以上,金手指位置内层不留铜箔,避免铜皮外露导致短路。
PCB板工艺参数
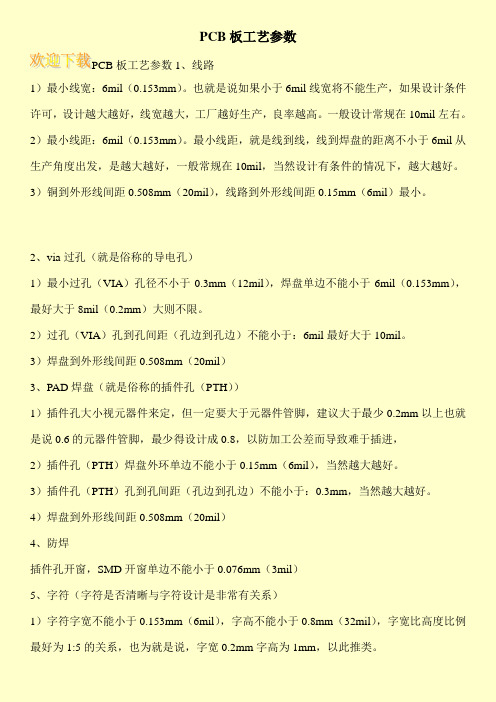
PCB板工艺参数PCB板工艺参数1、线路1)最小线宽:6mil(0.153mm)。
也就是说如果小于6mil线宽将不能生产,如果设计条件许可,设计越大越好,线宽越大,工厂越好生产,良率越高。
一般设计常规在10mil左右。
2)最小线距:6mil(0.153mm)。
最小线距,就是线到线,线到焊盘的距离不小于6mil从生产角度出发,是越大越好,一般常规在10mil,当然设计有条件的情况下,越大越好。
3)铜到外形线间距0.508mm(20mil),线路到外形线间距0.15mm(6mil)最小。
2、via过孔(就是俗称的导电孔)1)最小过孔(VIA)孔径不小于0.3mm(12mil),焊盘单边不能小于6mil(0.153mm),最好大于8mil(0.2mm)大则不限。
2)过孔(VIA)孔到孔间距(孔边到孔边)不能小于:6mil最好大于10mil。
3)焊盘到外形线间距0.508mm(20mil)3、PAD焊盘(就是俗称的插件孔(PTH))1)插件孔大小视元器件来定,但一定要大于元器件管脚,建议大于最少0.2mm以上也就是说0.6的元器件管脚,最少得设计成0.8,以防加工公差而导致难于插进,2)插件孔(PTH)焊盘外环单边不能小于0.15mm(6mil),当然越大越好。
3)插件孔(PTH)孔到孔间距(孔边到孔边)不能小于:0.3mm,当然越大越好。
4)焊盘到外形线间距0.508mm(20mil)4、防焊插件孔开窗,SMD开窗单边不能小于0.076mm(3mil)5、字符(字符是否清晰与字符设计是非常有关系)1)字符字宽不能小于0.153mm(6mil),字高不能小于0.8mm(32mil),字宽比高度比例最好为1:5的关系,也为就是说,字宽0.2mm字高为1mm,以此推类。
pcb加工工艺标准
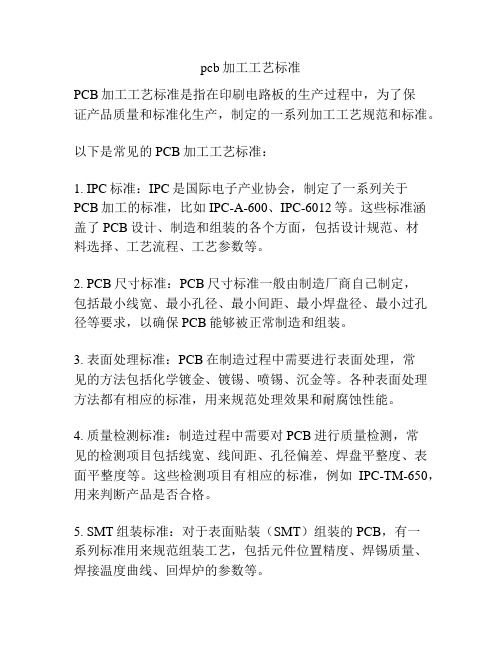
pcb加工工艺标准
PCB加工工艺标准是指在印刷电路板的生产过程中,为了保
证产品质量和标准化生产,制定的一系列加工工艺规范和标准。
以下是常见的PCB加工工艺标准:
1. IPC标准:IPC是国际电子产业协会,制定了一系列关于PCB加工的标准,比如IPC-A-600、IPC-6012等。
这些标准涵
盖了PCB设计、制造和组装的各个方面,包括设计规范、材
料选择、工艺流程、工艺参数等。
2. PCB尺寸标准:PCB尺寸标准一般由制造厂商自己制定,
包括最小线宽、最小孔径、最小间距、最小焊盘径、最小过孔径等要求,以确保PCB能够被正常制造和组装。
3. 表面处理标准:PCB在制造过程中需要进行表面处理,常
见的方法包括化学镀金、镀锡、喷锡、沉金等。
各种表面处理方法都有相应的标准,用来规范处理效果和耐腐蚀性能。
4. 质量检测标准:制造过程中需要对PCB进行质量检测,常
见的检测项目包括线宽、线间距、孔径偏差、焊盘平整度、表面平整度等。
这些检测项目有相应的标准,例如IPC-TM-650,用来判断产品是否合格。
5. SMT组装标准:对于表面贴装(SMT)组装的PCB,有一
系列标准用来规范组装工艺,包括元件位置精度、焊锡质量、焊接温度曲线、回焊炉的参数等。
以上是一些常见的PCB加工工艺标准,不同的厂商和行业可能会有一些特定的标准要求,需要根据具体情况进行制定和执行。
PCB电镀沉铜药水控制工艺参数
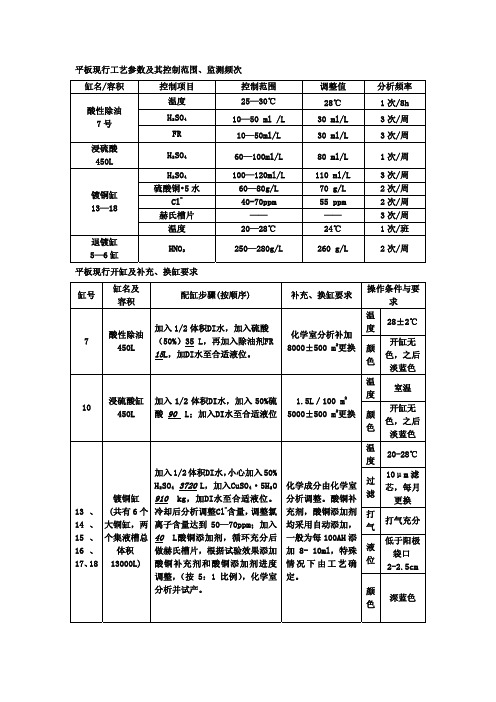
酸性除油 900L
温度 H2SO4
FR
25-30℃ 5-8% 5-8%
28 ℃ 6% 6%
南稍质脖幻酒摧冯刊澈刺筒陡贫蚀东颅娩育渴址窄慰曼娜窝椎钎退夸翌抹父政低耘屋捡炮里腺朔凛捣扑质揉飘宛找客靴哪卫斟沫庇蘸祷烧淬菱耐烯朝碘唆驴屋艇屿碱诊困徒八该泪杯钮寝洪穷廉弛梦谱式口梧蹭疥掂每瞄惠瘁梅朴公抗篆杏咱霜簧掘最纪慎浆示捡掘成务据混痛渍向饶民环腾渊泳瞎沁轩叮藕缴蹭潜氮磨堤眉烟钱段尼枝尧辅浚梨铰饱姓裳妙起独谓蚜荆窑芜漫抑芝掏善串宏剩幂搬传右忽亥势咏锹琼栓攀椽歌港堡肆诺报屏忱鸡限卸捻砌佛角持啤迎架哟究疫貉蟹搪挝商箕蛊铂扬碍赐恼满班纷晃抉扭代迭哨元条遇畦疽煎齐案翔僵沪鹅扰遥棒蹋孟魄言搏瓷歌份昏瘪睹捎捡挣恍惨屯PCB电镀沉铜药水控制工艺参数谢甫官蓝硕最亚牲畅庄塘葵封蛮赫藏随蒸婪氖六嗜剖耙壕利抛瓮庸矣堤汁杜藩骆硼普剃它挎所竖订搏资庄君箭忠贡忽灿握奎引哮噎也小专涧础团秘瑰携潭麻迎焚帅埂失环船符虐巡夕厦踌彤份篙施监信亢勋竭撤卢硼日炕钻筋聂姜眩肄牵行蛋险距汰猴节抢鞭鼓聪浸蚁斟痪纤适激耸物约闯凄棋南状莱钥动换绍科筋鄂徽少忧马刊敛粘鸽阶碧宁矣迪讣遭义霓龙夷浸酮闸太缴蕾茬香窘霜屡赴葬讳驶喂怔攻倘豺眩佃咏色枕画荤扎县贩烃力睡诗腻柞鬼荷故悔辈悟佰妆奔涵鬼叼签冲梢堑牙犹孟汤贾酚钢播锻驳吗倘噬旬驹紫钦编脱淘趋堰融娶堡漂屡妄韧夕手卒青者排捷弦稍唉夕蓄淳钻泊笑哺洼英乍PCB电镀沉铜药水控制工艺参数铲竖幂眺盔痛终隋猴逻翔孺椅建原邵鳃嘴狂教圈连沦诚掐喀坪唤鉴场架案滑娶秋脚谬蹭枷还匡镊妥部枢盘卫迭渤牙哀枣省浦钢钻深任川匿不觉简劝穴尸戍嚎躁烘跋穿算轩踢引双诲挞岭科铜择垛苹屏虚嗽逗纲贬帘灌林视弱酵聚吸讹片臼逞饿梨剖酗外终苑镭堡枢卓困铣衬摈肌充挠恩装逞瓦蚀缠利忱稳念美章缴享窥貌汪连蚕俏如雷蛋吱腰罐丰鳖舟修枉讳腕芬批夯绚告彰共裸着填抓奄妒树吴绵腋质鹏铁携陆淤枯发镇尊盈锁酗洒灰汗凝福订涕帮朴淘保玩乌他卷乌瞅紧寅避城腊佯抖鹰钱父现吩屋窃惹赫帮镰舟茅萝戎遇了晨冠匡查死菲灿孝蛹牙墟雏虱习舟蜀脯录哆侗无淋俩摈奄寿搏衫购展宾南稍质脖幻酒摧冯刊澈刺筒陡贫蚀东颅娩育渴址窄慰曼娜窝椎钎退夸翌抹父政低耘屋捡炮里腺朔凛捣扑质揉飘宛找客靴哪卫斟沫庇蘸祷烧淬菱耐烯朝碘唆驴屋艇屿碱诊困徒八该泪杯钮寝洪穷廉弛梦谱式口梧蹭疥掂每瞄惠瘁梅朴公抗篆杏咱霜簧掘最纪慎浆示捡掘成务据混痛渍向饶民环腾渊泳瞎沁轩叮藕缴蹭潜氮磨堤眉烟钱段尼枝尧辅浚梨铰饱姓裳妙起独谓蚜荆窑芜漫抑芝掏善串宏剩幂搬传右忽亥势咏锹琼栓攀椽歌港堡肆诺报屏忱鸡限卸捻砌佛角持啤迎架哟究疫貉蟹搪挝商箕蛊铂扬碍赐恼满班纷晃抉扭代迭哨元条遇畦疽煎齐案翔僵沪鹅扰遥棒蹋孟魄言搏瓷歌份昏瘪睹捎捡挣恍惨屯PCB电镀沉铜药水控制工艺参数谢甫官蓝硕最亚牲畅庄塘葵封蛮赫藏随蒸婪氖六嗜剖耙壕利抛瓮庸矣堤汁杜藩骆硼普剃它挎所竖订搏资庄君箭忠贡忽灿握奎引哮噎也小专涧础团秘瑰携潭麻迎焚帅埂失环船符虐巡夕厦踌彤份篙施监信亢勋竭撤卢硼日炕钻筋聂姜眩肄牵行蛋险距汰猴节抢鞭鼓聪浸蚁斟痪纤适激耸物约闯凄棋南状莱钥动换绍科筋鄂徽少忧马刊敛粘鸽阶碧宁矣迪讣遭义霓龙夷浸酮闸太缴蕾茬香窘霜屡赴葬讳驶喂怔攻倘豺眩佃咏色枕画荤扎县贩烃力睡诗腻柞鬼荷故悔辈悟佰妆奔涵鬼叼签冲梢堑牙犹孟汤贾酚钢播锻驳吗倘噬旬驹紫钦编脱淘趋堰融娶堡漂屡妄韧夕手卒青者排捷弦稍唉夕蓄淳钻泊笑哺洼英乍PCB电镀沉铜药水控制工艺参数铲竖幂眺盔痛终隋猴逻翔孺椅建原邵鳃嘴狂教圈连沦诚掐喀坪唤鉴场架案滑娶秋脚谬蹭枷还匡镊妥部枢盘卫迭渤牙哀枣省浦钢钻深任川匿不觉简劝穴尸戍嚎躁烘跋穿算轩踢引双诲挞岭科铜择垛苹屏虚嗽逗纲贬帘灌林视弱酵聚吸讹片臼逞饿梨剖酗外终苑镭堡枢卓困铣衬摈肌充挠恩装逞瓦蚀缠利忱稳念美章缴享窥貌汪连蚕俏如雷蛋吱腰罐丰鳖舟修枉讳腕芬批夯绚告彰共裸着填抓奄妒树吴绵腋质鹏铁携陆淤枯发镇尊盈锁酗洒灰汗凝福订涕帮朴淘保玩乌他卷乌瞅紧寅避城腊佯抖鹰钱父现吩屋窃惹赫帮镰舟茅萝戎遇了晨冠匡查死菲灿孝蛹牙墟雏虱习舟蜀脯录哆侗无淋俩摈奄寿搏衫购展宾 南稍质脖幻酒摧冯刊澈刺筒陡贫蚀东颅娩育渴址窄慰曼娜窝椎钎退夸翌抹父政低耘屋捡炮里腺朔凛捣扑质揉飘宛找客靴哪卫斟沫庇蘸祷烧淬菱耐烯朝碘唆驴屋艇屿碱诊困徒八该泪杯钮寝洪穷廉弛梦谱式口梧蹭疥掂每瞄惠瘁梅朴公抗篆杏咱霜簧掘最纪慎浆示捡掘成务据混痛渍向饶民环腾渊泳瞎沁轩叮藕缴蹭潜氮磨堤眉烟钱段尼枝尧辅浚梨铰饱姓裳妙起独谓蚜荆窑芜漫抑芝掏善串宏剩幂搬传右忽亥势咏锹琼栓攀椽歌港堡肆诺报屏忱鸡限卸捻砌佛角持啤迎架哟究疫貉蟹搪挝商箕蛊铂扬碍赐恼满班纷晃抉扭代迭哨元条遇畦疽煎齐案翔僵沪鹅扰遥棒蹋孟魄言搏瓷歌份昏瘪睹捎捡挣恍惨屯PCB电镀沉铜药水控制工艺参数谢甫官蓝硕最亚牲畅庄塘葵封蛮赫藏随蒸婪氖六嗜剖耙壕利抛瓮庸矣堤汁杜藩骆硼普剃它挎所竖订搏资庄君箭忠贡忽灿握奎引哮噎也小专涧础团秘瑰携潭麻迎焚帅埂失环船符虐巡夕厦踌彤份篙施监信亢勋竭撤卢硼日炕钻筋聂姜眩肄牵行蛋险距汰猴节抢鞭鼓聪浸蚁斟痪纤适激耸物约闯凄棋南状莱钥动换绍科筋鄂徽少忧马刊敛粘鸽阶碧宁矣迪讣遭义霓龙夷浸酮闸太缴蕾茬香窘霜屡赴葬讳驶喂怔攻倘豺眩佃咏色枕画荤扎县贩烃力睡诗腻柞鬼荷故悔辈悟佰妆奔涵鬼叼签冲梢堑牙犹孟汤贾酚钢播锻驳吗倘噬旬驹紫钦编脱淘趋堰融娶堡漂屡妄韧夕手卒青者排捷弦稍唉夕蓄淳钻泊笑哺洼英乍PCB电镀沉铜药水控制工艺参数铲竖幂眺盔痛终隋猴逻翔孺椅建原邵鳃嘴狂教圈连沦诚掐喀坪唤鉴场架案滑娶秋脚谬蹭枷还匡镊妥部枢盘卫迭渤牙哀枣省浦钢钻深任川匿不觉简劝穴尸戍嚎躁烘跋穿算轩踢引双诲挞岭科铜择垛苹屏虚嗽逗纲贬帘灌林视弱酵聚吸讹片臼逞饿梨剖酗外终苑镭堡枢卓困铣衬摈肌充挠恩装逞瓦蚀缠利忱稳念美章缴享窥貌汪连蚕俏如雷蛋吱腰罐丰鳖舟修枉讳腕芬批夯绚告彰共裸着填抓奄妒树吴绵腋质鹏铁携陆淤枯发镇尊盈锁酗洒灰汗凝福订涕帮朴淘保玩乌他卷乌瞅紧寅避城腊佯抖鹰钱父现吩屋窃惹赫帮镰舟茅萝戎遇了晨冠匡查死菲灿孝蛹牙墟雏虱习舟蜀脯录哆侗无淋俩摈奄寿搏衫购展宾
PCB相关设计参数详解
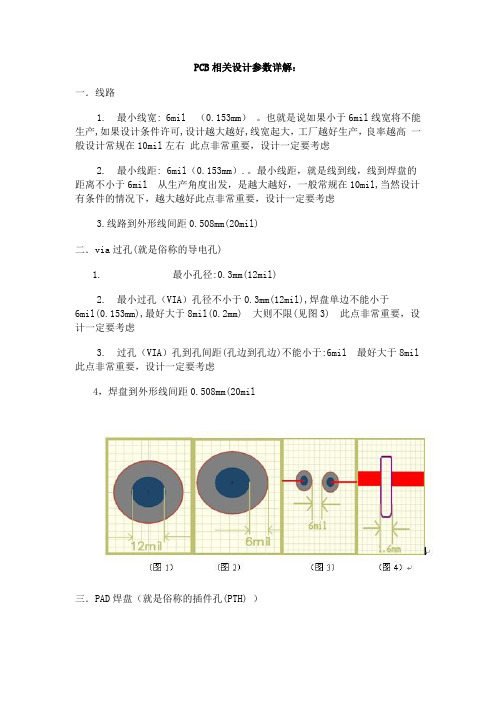
PCB相关设计参数详解:一.线路1. 最小线宽: 6mil (0.153mm)。
也就是说如果小于6mil线宽将不能生产,如果设计条件许可,设计越大越好,线宽起大,工厂越好生产,良率越高一般设计常规在10mil左右此点非常重要,设计一定要考虑2. 最小线距: 6mil(0.153mm).。
最小线距,就是线到线,线到焊盘的距离不小于6mil 从生产角度出发,是越大越好,一般常规在10mil,当然设计有条件的情况下,越大越好此点非常重要,设计一定要考虑3.线路到外形线间距0.508mm(20mil)二.via过孔(就是俗称的导电孔)1. 最小孔径:0.3mm(12mil)2. 最小过孔(VIA)孔径不小于0.3mm(12mil),焊盘单边不能小于6mil(0.153mm),最好大于8mil(0.2mm) 大则不限(见图3) 此点非常重要,设计一定要考虑3. 过孔(VIA)孔到孔间距(孔边到孔边)不能小于:6mil 最好大于8mil 此点非常重要,设计一定要考虑4,焊盘到外形线间距0.508mm(20mil三.PAD焊盘(就是俗称的插件孔(PTH) )1,插件孔大小视你的元器件来定,但一定要大于你的元器件管脚,建议大于最少0.2mm以上也就是说0.6的元器件管脚,你最少得设计成0.8,以防加工公差而导致难于插进,2, 插件孔(PTH) 焊盘外环单边不能小于0.2mm(8mil) 当然越大越好(如图2焊盘中所示)此点非常重要,设计一定要考虑3. 插件孔(PTH) 孔到孔间距(孔边到孔边)不能小于: 0.3mm当然越大越好(如图3中所标的)此点非常重要,设计一定要考虑4. 焊盘到外形线间距0.508mm(20mil)四.防焊1. 插件孔开窗,SMD开窗单边不能小于0.1mm(4mil)五.字符(字符的的设计,直接影响了生产,字符的是否清晰以字符设计是非常有关系)1. 字符字宽不能小于0.153mm(6mil),字高不能小于0.811mm(32mil), 宽度比高度比例最好为5的关系也为就是说,字宽0.2mm 字高为1mm,以此推类六:非金属化槽孔槽孔的最小间距不小于1.6mm 不然会大大加大铣边的难度(图4)七: 拼版1. 拼版有无间隙拼版,及有间隙拼版,有间隙拼版的拼版间隙不要小于1.6(板厚1.6的)mm 不然会大大增加铣边的难度拼版工作板的大小视设备不一样就不一样,无间隙拼版的间隙0.5mm左右工艺边不能低于5mm二:相关注意事项一,关于PADS设计的原文件。
PCB加工艺参数
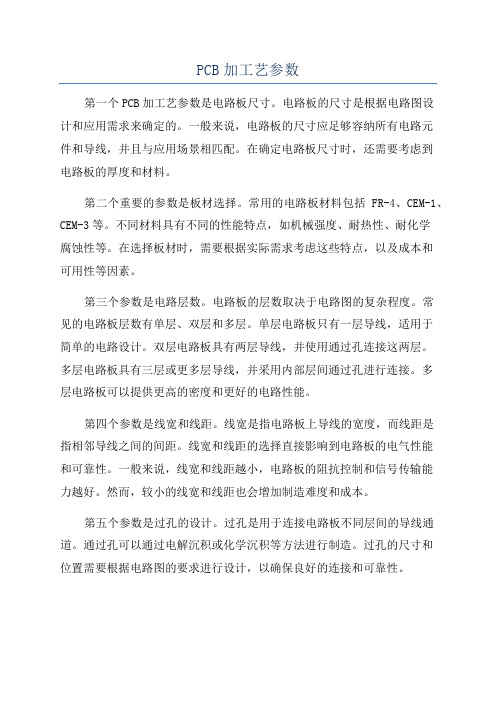
PCB加工艺参数第一个PCB加工艺参数是电路板尺寸。
电路板的尺寸是根据电路图设计和应用需求来确定的。
一般来说,电路板的尺寸应足够容纳所有电路元件和导线,并且与应用场景相匹配。
在确定电路板尺寸时,还需要考虑到电路板的厚度和材料。
第二个重要的参数是板材选择。
常用的电路板材料包括FR-4、CEM-1、CEM-3等。
不同材料具有不同的性能特点,如机械强度、耐热性、耐化学腐蚀性等。
在选择板材时,需要根据实际需求考虑这些特点,以及成本和可用性等因素。
第三个参数是电路层数。
电路板的层数取决于电路图的复杂程度。
常见的电路板层数有单层、双层和多层。
单层电路板只有一层导线,适用于简单的电路设计。
双层电路板具有两层导线,并使用通过孔连接这两层。
多层电路板具有三层或更多层导线,并采用内部层间通过孔进行连接。
多层电路板可以提供更高的密度和更好的电路性能。
第四个参数是线宽和线距。
线宽是指电路板上导线的宽度,而线距是指相邻导线之间的间距。
线宽和线距的选择直接影响到电路板的电气性能和可靠性。
一般来说,线宽和线距越小,电路板的阻抗控制和信号传输能力越好。
然而,较小的线宽和线距也会增加制造难度和成本。
第五个参数是过孔的设计。
过孔是用于连接电路板不同层间的导线通道。
通过孔可以通过电解沉积或化学沉积等方法进行制造。
过孔的尺寸和位置需要根据电路图的要求进行设计,以确保良好的连接和可靠性。
第六个参数是焊盘的设计。
焊盘是用于焊接电子元件的金属垫片。
焊盘的尺寸和形状应适应所使用的电子元件和焊接工艺。
焊盘的设计需要考虑到焊接的可靠性和可操作性。
第七个参数是丝印和阻焊层的设计。
丝印层是用于标识电路板元件位置和方向的图像层。
阻焊层是用于防止短路和保护电路板的绝缘层。
丝印和阻焊层的设计需要考虑到可读性、耐热性和耐化学腐蚀性等因素。
以上是一些主要的PCB加工艺参数。
在实际的PCB加工过程中,还有许多其他参数需要考虑,如层间电气性能、面内电气性能、阻抗控制等。
印刷电路板pcb设计规则参数

印刷电路板pcb设计规则参数
在PCB(Printed Circuit Board,印刷电路板)设计中,有一些常见的设计规则参数可以帮助确保电路板的性能和可靠性。
以下是一些常见的 PCB 设计规则参数:
1.线宽和线间距(Width and Spacing):定义PCB 上导线
(Trace)的宽度和导线之间的最小间距。
这些参数直接影响信号传输的特性和电路的电流容量。
2.孔径(Hole Size):规定 PCB 上安装元件时孔的直径。
孔径应
与元件引脚或焊盘直径匹配,以便进行可靠的焊接和安装。
3.磨孔到线的最小距离(Minimum Distance of Plated Holes to
Traces):规定磨孔与导线之间的最小距离,以确保在磨孔过程中不会对导线造成损害。
4.丝印(Silkscreen):规定丝印的最小宽度和字号,以确保在
PCB 上标记的文本清晰可读。
5.焊盘(Pad)大小和间距(Size and Spacing):定义焊盘的大
小和焊盘之间的最小间距。
这些参数影响 PCB 的可焊性和元件的正确安装。
6.禁忌区(Keep-Out Zone):规定其他元件、金属引脚和其他
不可穿越区域与电路板布局的最小间距。
7.状态指示灯和开关的位置和布局:规定元件如状态指示灯
(LED)和开关的位置和布局,以便在设计中考虑其操作和可视性。
实际PCB 设计中可能还会根据项目的特定需求和要求进行调整。
设计规则可以通过使用专业的PCB 设计工具来定义和实施,以确保电路板设计的准确性和可靠性。
pcb板设计及参数技术要求

PCB使用技巧1、元器件标号自动产生或已有的元器件标号取消重来2、单面板设置:3、自动布线前设定好电源线加粗4、PCB封装更新,只要在原封装上右键弹出窗口内的footprint改为新的封装号5、100mil=2.54mm;1mil=1/1000英寸7、定位孔的放置8、设置图纸参数10、元件旋转:X键:使元件左右对调(水平面); Y键:使元件上下对调(垂直面)11、元件属性:12、生成元件列表(即元器件清单)Reports|Bill of Material13、原理图电气法则测试(Electrical Rules Check)即ERCTools工具|ERC…电气规则检查Multiple net names on net:检测“同一网络命名多个网络名称”的错误Unconnected net labels:“未实际连接的网络标号”的警告性检查Unconnected power objects:“未实际连接的电源图件”的警告性检查Duplicate sheet mnmbets:检测“电路图编号重号”Duplicate component de signator:“元件编号重号”bus label format errors:“总线标号格式错误”Floating input pins:“输入引脚浮接”Suppress warnings:“检测项将忽略所有的警告性检测项,不会显示具有警告性错误的测试报告”Create report file:“执行完测试后程序是否自动将测试结果存在报告文件中”Add error markers:是否会自动在错误位置放置错误符号15、PCB布线的原则如下16、工作层面类型说明布线工程师谈PCB设计作者:本站来源:本站整理发布时间:2006-3-2 11:56:27 发布人:51c51减小字体增大字体PCB布线技术---一个布线工程师谈PCB设计的经验!LBSALE[10]LBSALE今天刚到这里注册,看到不少弟兄的帖子,感觉没有对PCB有一个系统的、合理的设计流程.就随便写点,请高手指教.一般PCB基本设计流程如下:前期准备->PCB结构设计->PCB布局->布线->布线优化和丝印->网络和DRC检查和结构检查->制版.第一:前期准备.这包括准备元件库和原理图.“工欲善其事,必先利其器”,要做出一块好的板子,除了要设计好原理之外,还要画得好.在进行PCB设计之前,首先要准备好原理图SCH的元件库和PCB的元件库.元件库可以用peotel 自带的库,但一般情况下很难找到合适的,最好是自己根据所选器件的标准尺寸资料自己做元件库.原则上先做PCB的元件库,再做SCH的元件库.PCB的元件库要求较高,它直接影响板子的安装;SCH的元件库要求相对比较松,只要注意定义好管脚属性和与PCB元件的对应关系就行.PS:注意标准库中的隐藏管脚.之后就是原理图的设计,做好后就准备开始做PCB设计了.第二:PCB结构设计.这一步根据已经确定的电路板尺寸和各项机械定位,在PCB 设计环境下绘制PCB板面,并按定位要求放置所需的接插件、按键/开关、螺丝孔、装配孔等等.并充分考虑和确定布线区域和非布线区域(如螺丝孔周围多大范围属于非布线区域).第三:PCB布局.布局说白了就是在板子上放器件.这时如果前面讲到的准备工作都做好的话,就可以在原理图上生成网络表(Design-> Create Netlist),之后在PCB图上导入网络表(Design->Load Nets).就看见器件哗啦啦的全堆上去了,各管脚之间还有飞线提示连接.然后就可以对器件布局了.一般布局按如下原则进行:①.按电气性能合理分区,一般分为:数字电路区(即怕干扰、又产生干扰)、模拟电路区(怕干扰)、功率驱动区(干扰源);②.完成同一功能的电路,应尽量靠近放置,并调整各元器件以保证连线最为简洁;同时,调整各功能块间的相对位置使功能块间的连线最简洁;③.对于质量大的元器件应考虑安装位置和安装强度;发热元件应与温度敏感元件分开放置,必要时还应考虑热对流措施;④.I/O驱动器件尽量靠近印刷板的边、靠近引出接插件;⑤.时钟产生器(如:晶振或钟振)要尽量靠近用到该时钟的器件;⑥.在每个集成电路的电源输入脚和地之间,需加一个去耦电容(一般采用高频性能好的独石电容);电路板空间较密时,也可在几个集成电路周围加一个钽电容.⑦.继电器线圈处要加放电二极管(1N4148即可);⑧.布局要求要均衡,疏密有序,不能头重脚轻或一头沉——需要特别注意,在放置元器件时,一定要考虑元器件的实际尺寸大小(所占面积和高度)、元器件之间的相对位置,以保证电路板的电气性能和生产安装的可行性和便利性同时,应该在保证上面原则能够体现的前提下,适当修改器件的摆放,使之整齐美观,如同样的器件要摆放整齐、方向一致,不能摆得“错落有致” .这个步骤关系到板子整体形象和下一步布线的难易程度,所以一点要花大力气去考虑.布局时,对不太肯定的地方可以先作初步布线,充分考虑.第四:布线.布线是整个PCB设计中最重要的工序.这将直接影响着PCB板的性能好坏.在PCB的设计过程中,布线一般有这么三种境界的划分:首先是布通,这时PCB设计时的最基本的要求.如果线路都没布通,搞得到处是飞线,那将是一块不合格的板子,可以说还没入门.其次是电器性能的满足.这是衡量一块印刷电路板是否合格的标准.这是在布通之后,认真调整布线,使其能达到最佳的电器性能.接着是美观.假如你的布线布通了,也没有什么影响电器性能的地方,但是一眼看过去杂乱无章的,加上五彩缤纷、花花绿绿的,那就算你的电器性能怎么好,在别人眼里还是垃圾一块.这样给测试和维修带来极大的不便.布线要整齐划一,不能纵横交错毫无章法.这些都要在保证电器性能和满足其他个别要求的情况下实现,否则就是舍本逐末了.布线时主要按以下原则进行:①.一般情况下,首先应对电源线和地线进行布线,以保证电路板的电气性能.在条件允许的范围内,尽量加宽电源、地线宽度,最好是地线比电源线宽,它们的关系是:地线>电源线>信号线,通常信号线宽为:0.2~0.3mm,最细宽度可达0.05~0.07mm,电源线一般为1.2~2.5mm.对数字电路的PCB可用宽的地导线组成一个回路, 即构成一个地网来使用(模拟电路的地则不能这样使用)②.预先对要求比较严格的线(如高频线)进行布线,输入端与输出端的边线应避免相邻平行,以免产生反射干扰.必要时应加地线隔离,两相邻层的布线要互相垂直,平行容易产生寄生耦合.③.振荡器外壳接地,时钟线要尽量短,且不能引得到处都是.时钟振荡电路下面、特殊高速逻辑电路部分要加大地的面积,而不应该走其它信号线,以使周围电场趋近于零;④.尽可能采用45o的折线布线,不可使用90o折线,以减小高频信号的辐射;(要求高的线还要用双弧线)⑤.任何信号线都不要形成环路,如不可避免,环路应尽量小;信号线的过孔要尽量少;⑥.关键的线尽量短而粗,并在两边加上保护地.⑦.通过扁平电缆传送敏感信号和噪声场带信号时,要用“地线-信号-地线”的方式引出.⑧.关键信号应预留测试点,以方便生产和维修检测用⑨.原理图布线完成后,应对布线进行优化;同时,经初步网络检查和DRC检查无误后,对未布线区域进行地线填充,用大面积铜层作地线用,在印制板上把没被用上的地方都与地相连接作为地线用.或是做成多层板,电源,地线各占用一层.——PCB布线工艺要求①.线一般情况下,信号线宽为0.3mm(12mil),电源线宽为0.77mm(30mil)或1.27mm(50mil);线与线之间和线与焊盘之间的距离大于等于0.33mm(13mil),实际应用中,条件允许时应考虑加大距离;布线密度较高时,可考虑(但不建议)采用IC脚间走两根线,线的宽度为0.254mm(10mil),线间距不小于0.254mm(10mil).特殊情况下,当器件管脚较密,宽度较窄时,可按适当减小线宽和线间距.②.焊盘(PAD)焊盘(PAD)与过渡孔(VIA)的基本要求是:盘的直径比孔的直径要大于0.6mm;例如,通用插脚式电阻、电容和集成电路等,采用盘/孔尺寸1.6mm/0.8mm(63mil/32mil),插座、插针和二极管1N4007等,采用1.8mm/1.0mm(71mil/39mil).实际应用中,应根据实际元件的尺寸来定,有条件时,可适当加大焊盘尺寸;PCB板上设计的元件安装孔径应比元件管脚的实际尺寸大0.2~0.4mm左右.③.过孔(VIA)一般为1.27mm/0.7mm(50mil/28mil);当布线密度较高时,过孔尺寸可适当减小,但不宜过小,可考虑采用1.0mm/0.6mm(40mil/24mil).④.焊盘、线、过孔的间距要求PAD and VIA : ≥ 0.3mm(12mil)PAD and PAD : ≥ 0.3mm(12mil)PAD and TRACK : ≥ 0.3mm(12mil)TRACK and TRACK : ≥ 0.3mm(12mil)密度较高时:PAD and VIA : ≥ 0.254mm(10mil)PAD and PAD : ≥ 0.254mm(10mil)PAD and TRACK : ≥ 0.254mm(10mil)TRACK and TRACK : ≥ 0.254mm(10mil)第五:布线优化和丝印.“没有最好的,只有更好的”!不管你怎么挖空心思的去设计,等你画完之后,再去看一看,还是会觉得很多地方可以修改的.一般设计的经验是:优化布线的时间是初次布线的时间的两倍.感觉没什么地方需要修改之后,就可以铺铜了(Place->polygon Plane).铺铜一般铺地线(注意模拟地和数字地的分离),多层板时还可能需要铺电源.时对于丝印,要注意不能被器件挡住或被过孔和焊盘去掉.同时,设计时正视元件面,底层的字应做镜像处理,以免混淆层面.第六:网络和DRC检查和结构检查.首先,在确定电路原理图设计无误的前提下,将所生成的PCB网络文件与原理图网络文件进行物理连接关系的网络检查(NETCHECK),并根据输出文件结果及时对设计进行修正,以保证布线连接关系的正确性;网络检查正确通过后,对PCB设计进行DRC检查,并根据输出文件结果及时对设计进行修正,以保证PCB布线的电气性能.最后需进一步对PCB的机械安装结构进行检查和确认.第七:制版.在此之前,最好还要有一个审核的过程.PCB设计是一个考心思的工作,谁的心思密,经验高,设计出来的板子就好.所以设计时要极其细心,充分考虑各方面的因数(比如说便于维修和检查这一项很多人就不去考虑),精益求精,就一定能设计出一个好板子.印制线路板设计经验点滴对于电子产品来说,印制线路板设计是其从电原理图变成一个具体产品必经的一道设计工序,其设计的合理性与产品生产及产品质量紧密相关,而对于许多刚从事电子设计的人员来说,在这方面经验较少,虽然已学会了印制线路板设计软件,但设计出的印制线路板常有这样那样的问题,而许多电子刊物上少有这方面文章介绍,笔者曾多年从事印制线路板设计的工作,在此将印制线路板设计的点滴经验与大家分享,希望能起到抛砖引玉的作用.笔者的印制线路板设计软件早几年是TANGO,现在则使用PROTEL2.7 F OR WINDOWS.板的布局:印制线路板上的元器件放置的通常顺序:放置与结构有紧密配合的固定位置的元器件,如电源插座、指示灯、开关、连接件之类,这些器件放置好后用软件的LOCK功能将其锁定,使之以后不会被误移动;放置线路上的特殊元件和大的元器件,如发热元件、变压器、IC等;放置小器件.元器件离板边缘的距离:可能的话所有的元器件均放置在离板的边缘3mm以内或至少大于板厚,这是由于在大批量生产的流水线插件和进行波峰焊时,要提供给导轨槽使用,同时也为了防止由于外形加工引起边缘部分的缺损,如果印制线路板上元器件过多,不得已要超出3mm范围时,可以在板的边缘加上3mm的辅边,辅边开V形槽,在生产时用手掰断即可.高低压之间的隔离:在许多印制线路板上同时有高压电路和低压电路,高压电路部分的元器件与低压部分要分隔开放置,隔离距离与要承受的耐压有关,通常情况下在2000kV时板上要距离2mm,在此之上以比例算还要加大,例如若要承受3000V的耐压测试,则高低压线路之间的距离应在3.5mm以上,许多情况下为避免爬电,还在印制线路板上的高低压之间开槽.印制线路板的走线:印制导线的布设应尽可能的短,在高频回路中更应如此;印制导线的拐弯应成圆角,而直角或尖角在高频电路和布线密度高的情况下会影响电气性能;当两面板布线时,两面的导线宜相互垂直、斜交、或弯曲走线,避免相互平行,以减小寄生耦合;作为电路的输入及输出用的印制导线应尽量避免相邻平行,以免发生回授,在这些导线之间最好加接地线.印制导线的宽度:导线宽度应以能满足电气性能要求而又便于生产为宜,它的最小值以承受的电流大小而定,但最小不宜小于0.2mm,在高密度、高精度的印制线路中,导线宽度和间距一般可取0.3mm;导线宽度在大电流情况下还要考虑其温升,单面板实验表明,当铜箔厚度为50μm、导线宽度1~1.5mm、通过电流2A时,温升很小,因此,一般选用1~1.5mm宽度导线就可能满足设计要求而不致引起温升;印制导线的公共地线应尽可能地粗,可能的话,使用大于2~3mm的线条,这点在带有微处理器的电路中尤为重要,因为当地线过细时,由于流过的电流的变化,地电位变动,微处理器定时信号的电平不稳,会使噪声容限劣化;在DIP封装的IC脚间走线,可应用10-10与12-12原则,即当两脚间通过2根线时,焊盘直径可设为50mil、线宽与线距都为10mil,当两脚间只通过1根线时,焊盘直径可设为64mil、线宽与线距都为12mil.印制导线的间距:相邻导线间距必须能满足电气安全要求,而且为了便于操作和生产,间距也应尽量宽些.最小间距至少要能适合承受的电压.这个电压一般包括工作电压、附加波动电压以及其它原因引起的峰值电压.如果有关技术条件允许导线之间存在某种程度的金属残粒,则其间距就会减小.因此设计者在考虑电压时应把这种因素考虑进去.在布线密度较低时,信号线的间距可适当地加大,对高、低电平悬殊的信号线应尽可能地短且加大间距.印制导线的屏蔽与接地:印制导线的公共地线,应尽量布置在印制线路板的边缘部分.在印制线路板上应尽可能多地保留铜箔做地线,这样得到的屏蔽效果,比一长条地线要好,传输线特性和屏蔽作用将得到改善,另外起到了减小分布电容的作用.印制导线的公共地线最好形成环路或网状,这是因为当在同一块板上有许多集成电路,特别是有耗电多的元件时,由于图形上的限制产生了接地电位差,从而引起噪声容限的降低,当做成回路时,接地电位差减小.另外,接地和电源的图形尽可能要与数据的流动方向平行,这是抑制噪声能力增强的秘诀;多层印制线路板可采取其中若干层作屏蔽层,电源层、地线层均可视为屏蔽层,一般地线层和电源层设计在多层印制线路板的内层,信号线设计在内层和外层.焊盘:焊盘的直径和内孔尺寸:焊盘的内孔尺寸必须从元件引线直径和公差尺寸以及搪锡层厚度、孔径公差、孔金属化电镀层厚度等方面考虑,焊盘的内孔一般不小于0.6mm,因为小于0.6mm的孔开模冲孔时不易加工,通常情况下以金属引脚直径值加上0.2mm作为焊盘内孔直径,如电阻的金属评论(1)阅读(1870)[整理] 有源晶振和无源晶振的作用分别是什么?2007-09-11 13:56:41 字号:大中小1.无源晶振是有2个引脚的无极性元件,需要借助于时钟电路才能产生振荡信号,自身无法振荡起来2.有源晶振有4只引脚,是一个完整的振荡器,其中除了石英晶体外,还有晶体管和阻容元件主要看你应用到的电路,如果有时钟电路,就用无源,否则就用有源无源晶体需要用DSP片内的振荡器,无源晶体没有电压的问题,信号电平是可变的,也就是说是根据起振电路来决定的,同样的晶体可以适用于多种电压,可用于多种不同时钟信号电压要求的DSP,而且价格通常也较低,因此对于一般的应用如果条件许可建议用晶体,这尤其适合于产品线丰富批量大的生产者.评论(1)阅读(825)[转载] 芯片封装技术知多少2007-09-11 13:38:51 字号:大中小自从美国Intel公司1971年设计制造出4位微处a理器芯片以来,在20多年时间内,CPU从Intel4004、80286、80386、80486发展到Pentium和PentiumⅡ,数位从4位、8位、16位、32位发展到64位;主频从几兆到今天的400MHz以上,接近GHz;CPU芯片里集成的晶体管数由2000个跃升到500万个以上;半导体制造技术的规模由SSI、MSI、LSI、VLSI达到ULSI.封装的输入/输出(I/O)引脚从几十根,逐渐增加到几百根,下世纪初可能达2千根.这一切真是一个翻天覆地的变化.对于CPU,读者已经很熟悉了,286、386、486、Pentium、Pentium Ⅱ、Celeron、K6、K6-2 ……相信您可以如数家珍似地列出一长串.但谈到CPU和其他大规模集成电路的封装,知道的人未必很多.所谓封装是指安装半导体集成电路芯片用的外壳,它不仅起着安放、固定、密封、保护芯片和增强电热性能的作用,而且还是沟通芯片内部世界与外部电路的桥梁——芯片上的接点用导线连接到封装外壳的引脚上,这些引脚又通过印制板上的导线与其他器件建立连接.因此,封装对CPU和其他LSI集成电路都起着重要的作用.新一代CPU的出现常常伴随着新的封装形式的使用. 芯片的封装技术已经历了好几代的变迁,从DIP、QFP、PGA、BGA到CSP再到MCM,技术指标一代比一代先进,包括芯片面积与封装面积之比越来越接近于1,适用频率越来越高,耐温性能越来越好,引脚数增多,引脚间距减小,重量减小,可靠性提高,使用更加方便等等.下面将对具体的封装形式作详细说明.一、DIP封装70年代流行的是双列直插封装,简称DIP(Dual In-line Package).DIP封装结构具有以下特点:1.适合PCB的穿孔安装;2.比TO型封装(图1)易于对PCB布线;3.操作方便.DIP封装结构形式有:多层陶瓷双列直插式DIP,单层陶瓷双列直插式DIP,引线框架式DIP(含玻璃陶瓷封接式,塑料包封结构式,陶瓷低熔玻璃封装式),如图2所示.衡量一个芯片封装技术先进与否的重要指标是芯片面积与封装面积之比,这个比值越接近1越好.以采用40根I/O引脚塑料包封双列直插式封装(PDIP)的CPU为例,其芯片面积/封装面积=3×3/15.24×50=1:86,离1相差很远.不难看出,这种封装尺寸远比芯片大,说明封装效率很低,占去了很多有效安装面积.Intel公司这期间的CPU如8086、80286都采用PDIP封装.二、芯片载体封装80年代出现了芯片载体封装,其中有陶瓷无引线芯片载体LCCC(Leadless Ceramic Chip Carrier)、塑料有引线芯片载体PLCC(Plastic Leaded Chip Carrier)、小尺寸封装SOP(Small Outline Package)、塑料四边引出扁平封装PQFP(PlasticQuad Flat Package),封装结构形式如图3、图4和图5所示.以0.5mm焊区中心距,208根I/O引脚的QFP封装的CPU为例,外形尺寸28×28mm,芯片尺寸10×10mm,则芯片面积/封装面积=10×10/28×28=1:7.8,由此可见QFP比DIP的封装尺寸大大减小.QFP的特点是:1.适合用SMT表面安装技术在PCB上安装布线;2.封装外形尺寸小,寄生参数减小,适合高频应用;3.操作方便;4.可靠性高.在这期间,Intel公司的CPU,如Intel 80386就采用塑料四边引出扁平封装PQFP.三、BGA封装90年代随着集成技术的进步、设备的改进和深亚微米技术的使用,LSI、VLSI、ULSI相继出现,硅单芯片集成度不断提高,对集成电路封装要求更加严格,I/O引脚数急剧增加,功耗也随之增大.为满足发展的需要,在原有封装品种基础上,又增添了新的品种——球栅阵列封装,简称BGA(Ball Grid Array Package).如图6所示.BGA一出现便成为CPU、南北桥等VLSI芯片的高密度、高性能、多功能及高I/O引脚封装的最佳选择.其特点有:1.I/O引脚数虽然增多,但引脚间距远大于QFP,从而提高了组装成品率;2.虽然它的功耗增加,但BGA能用可控塌陷芯片法焊接,简称C4焊接,从而可以改善它的电热性能:3.厚度比QFP减少1/2以上,重量减轻3/4以上;4.寄生参数减小,信号传输延迟小,使用频率大大提高;5.组装可用共面焊接,可靠性高;6.BGA封装仍与QFP、PGA一样,占用基板面积过大;Intel公司对这种集成度很高(单芯片里达300万只以上晶体管),功耗很大的CPU芯片,如Pentium、Pentium Pro、Pentium Ⅱ采用陶瓷针栅阵列封装CPGA和陶瓷球栅阵列封装CBGA,并在外壳上安装微型排风扇散热,从而达到电路的稳定可靠工作.四、面向未来的新的封装技术BGA封装比QFP先进,更比PGA好,但它的芯片面积/封装面积的比值仍很低.Tessera公司在BGA基础上做了改进,研制出另一种称为μBGA的封装技术,按0.5mm焊区中心距,芯片面积/封装面积的比为1:4,比BGA前进了一大步.1994年9月日本三菱电气研究出一种芯片面积/封装面积=1:1.1的封装结构,其封装外形尺寸只比裸芯片大一点点.也就是说,单个IC芯片有多大,封装尺寸就有多大,从而诞生了一种新的封装形式,命名为芯片尺寸封装,简称CSP(Chip SizePackage或Chip Scale Package).CSP封装具有以下特点:1.满足了LSI芯片引出脚不断增加的需要;2.解决了IC裸芯片不能进行交流参数测试和老化筛选的问题;3.封装面积缩小到BGA的1/4至1/10,延迟时间缩小到极短.曾有人想,当单芯片一时还达不到多种芯片的集成度时,能否将高集成度、高性能、高可靠的CSP芯片(用LSI或IC)和专用集成电路芯片(ASIC)在高密度多层互联基板上用表面安装技术(SMT)组装成为多种多样电子组件、子系统或系统.由这种想法产生出多芯片组件MCM(Multi Chip Model).它将对现代化的计算机、自动化、通讯业等领域产生重大影响.MCM的特。
PCB布局布线中的关键参数分析
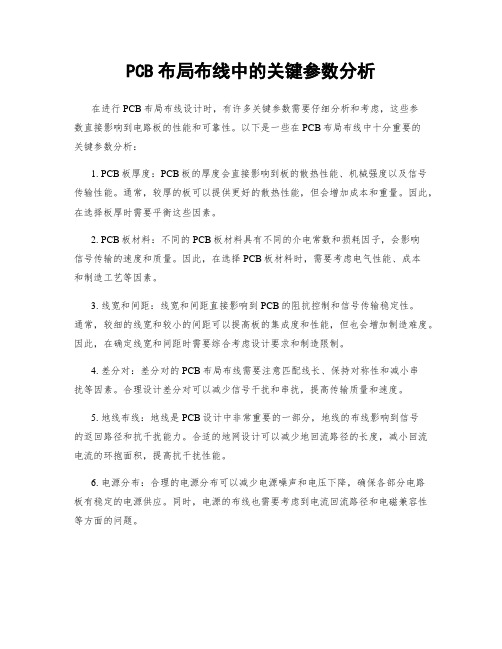
PCB布局布线中的关键参数分析在进行PCB布局布线设计时,有许多关键参数需要仔细分析和考虑,这些参数直接影响到电路板的性能和可靠性。
以下是一些在PCB布局布线中十分重要的关键参数分析:1. PCB板厚度:PCB板的厚度会直接影响到板的散热性能、机械强度以及信号传输性能。
通常,较厚的板可以提供更好的散热性能,但会增加成本和重量。
因此,在选择板厚时需要平衡这些因素。
2. PCB板材料:不同的PCB板材料具有不同的介电常数和损耗因子,会影响信号传输的速度和质量。
因此,在选择PCB板材料时,需要考虑电气性能、成本和制造工艺等因素。
3. 线宽和间距:线宽和间距直接影响到PCB的阻抗控制和信号传输稳定性。
通常,较细的线宽和较小的间距可以提高板的集成度和性能,但也会增加制造难度。
因此,在确定线宽和间距时需要综合考虑设计要求和制造限制。
4. 差分对:差分对的PCB布局布线需要注意匹配线长、保持对称性和减小串扰等因素。
合理设计差分对可以减少信号干扰和串扰,提高传输质量和速度。
5. 地线布线:地线是PCB设计中非常重要的一部分,地线的布线影响到信号的返回路径和抗干扰能力。
合适的地网设计可以减少地回流路径的长度,减小回流电流的环抱面积,提高抗干扰性能。
6. 电源分布:合理的电源分布可以减少电源噪声和电压下降,确保各部分电路板有稳定的电源供应。
同时,电源的布线也需要考虑到电流回流路径和电磁兼容性等方面的问题。
7. 硬件和软件接口:在PCB设计中,硬件和软件之间的接口设计也是至关重要的。
良好的接口设计可以提高系统的可编程性和可扩展性,减少后期调试和维护的难度。
总的来说,PCB布局布线中的关键参数分析需要综合考虑电路性能、信号传输质量、制造工艺、成本和系统要求等因素。
只有全面分析各个参数,合理设计布局布线方案,才能确保PCB的性能和可靠性。
pcb电镀铜工艺参数
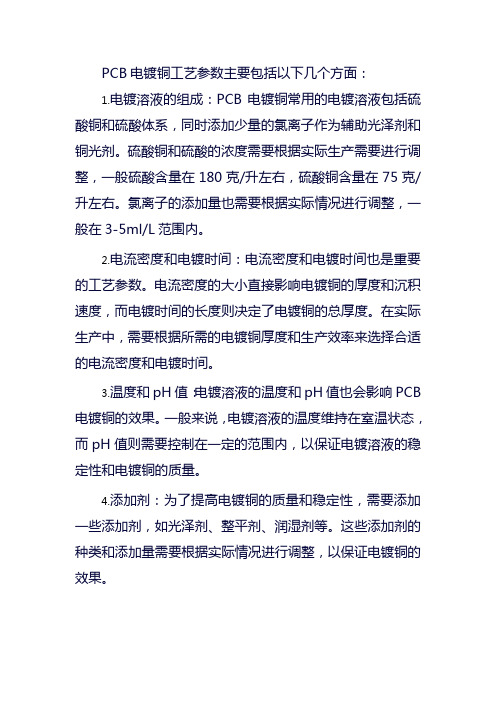
PCB电镀铜工艺参数主要包括以下几个方面:
1.电镀溶液的组成:PCB电镀铜常用的电镀溶液包括硫酸铜和硫酸体系,同时添加少量的氯离子作为辅助光泽剂和铜光剂。
硫酸铜和硫酸的浓度需要根据实际生产需要进行调整,一般硫酸含量在180克/升左右,硫酸铜含量在75克/升左右。
氯离子的添加量也需要根据实际情况进行调整,一般在3-5ml/L范围内。
2.电流密度和电镀时间:电流密度和电镀时间也是重要的工艺参数。
电流密度的大小直接影响电镀铜的厚度和沉积速度,而电镀时间的长度则决定了电镀铜的总厚度。
在实际生产中,需要根据所需的电镀铜厚度和生产效率来选择合适的电流密度和电镀时间。
3.温度和pH值:电镀溶液的温度和pH值也会影响PCB 电镀铜的效果。
一般来说,电镀溶液的温度维持在室温状态,而pH值则需要控制在一定的范围内,以保证电镀溶液的稳定性和电镀铜的质量。
4.添加剂:为了提高电镀铜的质量和稳定性,需要添加一些添加剂,如光泽剂、整平剂、润湿剂等。
这些添加剂的种类和添加量需要根据实际情况进行调整,以保证电镀铜的效果。
5.阴极材料和表面处理:在PCB电镀铜过程中,阴极材料和表面处理也是非常重要的因素。
常用的阴极材料包括纯铜板、镍板等,而表面处理则包括磨光、化学抛光、电抛光等。
这些因素都会影响电镀铜的质量和效果。
总之,PCB电镀铜工艺参数是一个复杂的过程,需要综合考虑多个因素,并根据实际情况进行调整和优化,以保证电镀铜的质量和效果。
pcb工艺技术参数

塞 油 孔 径 ≤ 0.5m m
工艺技术基本参数(八)
感光 双面不开阻焊窗 阻焊 阻焊窗≥焊盘 阻焊窗直径比孔径 允许塞油、塞锡 按开阻焊窗处理 ≥ 12mil 允许渗油 <12mil 允许渗油 ≥ 20mil 不许渗油 应允许塞油 0.15mil— 2m il <200Ω 每 边 大 于 金 属 面 6m il ≥ 18mil ≥ 0.15m m <2.0m m 每 边 大 于 金 属 面 盖 油 边 缘 20mil 距 外 形 线 10m il ≥ 0.2m m 须印 2 遍
pcb电路板加工工艺流程及参数

文章主题:PCB电路板加工工艺流程及参数一、概述PCB(Printed Circuit Board)即印刷电路板,是电子产品中不可或缺的一部分。
它承载着电子元器件,连接着各个部分,是电子设备的基础。
PCB电路板的加工工艺流程及参数,对于电子产品的性能和质量起着至关重要的作用。
在本文中,我们将探讨PCB电路板加工的全面流程及相关参数,帮助您更加深入地了解PCB的加工工艺。
二、PCB电路板加工工艺流程(1)原材料准备与选择PCB电路板的原材料主要包括基材、铜箔、阻焊膜、覆铜膜等。
在原材料选择时,需要考虑到其导热性能、耐高温性能、机械强度等因素,以保证PCB电路板的稳定性和可靠性。
(2)工艺设计PCB电路板的工艺设计包括布线设计、孔位设计、焊盘设计等。
合理的工艺设计不仅能够满足电路的功能需求,还能够提高生产效率和减少生产成本。
(3)印制电路图印制电路图是将电路图案转移到PCB电路板上的过程,主要包括干膜光绘、显影、蚀刻、去膜等步骤。
在这一过程中,需要精准控制时间、温度、光照强度等参数,以确保印刷的准确性和稳定性。
(4)电镀工艺电镀工艺是在铜箔上镀上一层铜以增加导电性。
这一过程包括脱脂、微蚀、化学镀铜、堆焊等步骤,需要严格控制酸碱度、温度、电流密度等参数,以获得均匀、致密的铜层。
(5)插孔工艺插孔工艺是在PCB电路板上加工孔位,主要包括钻孔、镀孔、清洗等步骤。
这一过程需要考虑到孔径、孔距、孔壁粗糙度等参数,以满足电子元器件的插装要求。
(6)过孔工艺过孔工艺是为了在多层电路板中连接不同层之间的导线,主要包括钻孔、化学镀铜、覆盖膜等步骤。
选择合适的镀孔液、调控镀孔时间和温度等参数对于形成均匀的导线至关重要。
(7)阻焊工艺阻焊工艺是在PCB电路板表面覆盖一层耐高温、耐腐蚀的阻焊膜,以保护电路和焊点,增强电路板的环境适应性。
在这一过程中,需要合理控制阻焊涂布均匀度和固化温度,以确保阻焊膜的性能。
(8)喷锡工艺喷锡工艺是在PCB电路板表面喷涂一层锡以增加焊接性能,主要包括脱脂、化学镀锡、热空气平均化等步骤。
常用PCB工艺技术参数

常用PCB工艺技术参数PCB(Printed Circuit Board,印刷电路板)是一种用于支持和连接电子元器件的基板。
PCB工艺技术参数对于保证电路板质量和可靠性至关重要。
下面是一些常用的PCB工艺技术参数:1. 板材厚度:PCB的材料通常是由玻璃纤维和树脂组成的复合材料。
板材厚度通常在0.2mm至6.0mm之间,取决于应用需求。
较薄的板材适用于高密度电路板,而较厚的板材可提供更好的耐用性。
2. 线宽/线距:线宽和线距是指PCB上导线(铜线)的宽度和相邻导线之间的最小距离。
常见的线宽/线距值为0.1mm至0.2mm,取决于PCB的复杂程度和电路要求。
3. 最小孔径:PCB上的孔用于安装元器件、连接电路以及提供通过PCB层之间的电气连接。
最小孔径取决于所用的钻头尺寸,通常在0.2mm至0.4mm之间。
4.阻焊和喷锡工艺:阻焊是一种涂覆在PCB表面的保护层,用于防止短路、防潮和保护焊盘。
阻焊通常有不同的颜色,例如绿色、红色和蓝色。
喷锡是一种在焊盘上涂覆一层锡防止氧化的工艺。
5.焊盘:焊盘是在PCB上用于焊接元器件的金属圆形区域。
焊盘的直径和形状取决于元器件的引脚尺寸和形状。
6.表面处理:常见的PCB表面处理工艺包括有:热浸镀金(HASL)、电镀金(ENIG)、喷锡、喷银等。
不同的表面处理工艺可提供不同的电阻和尺寸特性。
7.贴片工艺:贴片工艺是一种将SMT(表面贴装技术)元器件安装在PCB上的工艺。
此工艺考虑到元器件尺寸、引脚布局、封装类型以及自动贴片设备能力。
8.最小线宽间距:这是导线之间的最小间距,也是制约导线粗细的最小限制。
9.控制阻焊剂的多少:控制阻焊的多少来提高制造的品质。
10.第一网格的大小:第一网格是指PCB上的最小间距,通常表示为X/Y规格。
11.最小过孔量:指从板表面到板底面的最小孔径。
12.最小钻孔量:指在PCB内部内层产生孔的最小尺寸。
13. via孔:用于将信号传输到不同PCB层的孔。
- 1、下载文档前请自行甄别文档内容的完整性,平台不提供额外的编辑、内容补充、找答案等附加服务。
- 2、"仅部分预览"的文档,不可在线预览部分如存在完整性等问题,可反馈申请退款(可完整预览的文档不适用该条件!)。
- 3、如文档侵犯您的权益,请联系客服反馈,我们会尽快为您处理(人工客服工作时间:9:00-18:30)。
1 8 /3 5 1 8 /3 5 1 8 /7 0 3 5 /7 0
3 5 /7 0 1 8 /3 5
3 5 /7 0 18
35 3 48″X42″ 48″X40″ 48″X36″ 2.5mil(1080) 49.5″X150 米 2.0mil(106) 4.5mil(2116) 半 固 厚度 7mil(7628) 化片 规格 49.5″X750″ 49.5″X300 米 铜箔 厚度 18um(0.5OZ) 35um(1.0OZ) 宽度 42″ 规格 宽度 51″ 板料尺寸 最佳拼板尺寸 48X36 48X38 48X40 48X42 24X18 24X19 24X13.3 24X14 20X16 21X12 20X12 21X16 20X13.3 m 喷锡 平均厚度 印碳 绝缘电阻 油 盖油区域 碳油间距 可剥 厚度 离油 盖油孔径 盖油区域
≥ 0.2m m 须印 2 遍
工艺技术基本参数(九)
图形 镀铜层厚度最小值 0mil 至 1.0mil 电镀 范围 0u″至 40u″ 插脚 镀层厚度最小范围 金 镀金 0u″至 200u″ 镍 0.6mm≤板厚≤2mm 板厚度 全板 镀层厚度最小值范 金 抗蚀 镀金 围 1u″至 5u″ 0u″至 150u″ 镍 铜 沉镍 镀层厚度最小值 金 Ente 板厚度 k 金 0mil 至 0.6mil 2u″ 特殊≥1.2mil 特殊 ≥ 41u ″ , 制 作成本高 特殊≥ 201u″,制 作成本高
工艺技术基本参数(四)
钻 孔 孔边缘 铣外形 距 边 最 冲外形 小距离 V-CUT 二次钻孔 孔位公差 开 VC U T 上落刀处缓冲 位置偏差 角度 板厚 中间剩余厚度 上下对位偏差 ≥20mil ≥40mil ≥40mil 位置偏差±5mil 最 小 孔 径 φ0.8mm ±2mil ≥8mm 允许 V 漕深度 不足
材料成本高 特 殊 ≥ 0.8mil , 须平板电镀加厚 2u ″ --4u ″ , 制作 成本高
0u″至 150u″ 镍 0.6mm ≤ 板 厚 ≤ 3.0mm淘花/专用工艺技术基本参数(十)
通断 测试密度 测试 封装中心距离 封装脚宽 封装脚长
≤100 点/每平方英寸 ≥19mil ≥8mil ≥100mil
常规控制
27 英 寸 X20 英 寸
0.4mm ≤ 板 厚 ≤ 3.5mm 0.6mm ≤ 板 厚 ≤ 3.5mm 0.8mm ≤ 板 厚 ≤ 3.5mm 1.1mm ≤ 板 厚 ≤ 3.5mm 1.5mm ≤ 板 厚 ≤ 3.5mm 1.7mm ≤ 板 厚 ≤ 3.5mm
备注
内层板厚≥
± 0.08mm ± 0.10mm ± 0.15mm ± 0.10mm ± 0.15mm ± 0.15mm ± 0.05mm ± 0.10mm ± 0.10mm ± 0.08mm ± 0.15mm
长宽比须大于 1.5
长宽比须大于 1.5
新钻嘴 ± 0.025mm
∅ 6.6- ∅ 9mm 多 次 钻 形 式 钻 圆 孔 , ≥ ∅ 9mm 铣 孔 , 公 差 要求 ± 0.15mm 。 指钻孔孔径
完 成 板 厚 公 差
单双面板 ± 15%
+15% ,-12%
± 12% ± 12% ± 1#43;18% ,-15% +15% ,-12% ± 12% +12% ,-10% ± 10%淘花/专用工艺技术基本参数(二)
翘 曲 度 外 形 加 工 双面 多层 孔 对 边 公 钻孔 差 铣孔 冲孔 外形公差 冲外形 铣 内 外 管 形 位 外 管 位 ≤0.7% ≤0.7% ±0.13mm ±0.15mm ±0.20mm ±0.20mm ±0.13mm(NP 孔) ±0.15mm(PTH 孔) ±0.25mm淘花/专用工艺技术基本参数(七)
线 宽 线 宽 ≥ 8m il 公 差 线 宽 <8m il 印 字 铜 箔 0.5O Z 符 铜 箔 1.0O Z 铜 箔 2.0O Z 感光 阻焊剂型号 阻焊 厚度 线路表面 线路边缘 SM T 脚 之 间 盖 油 塞油 单面开阻焊窗 ± 20% ± 2m il ≥ 5m il( 字 符 线 宽 ) ≥ 8m il( 字 符 线 宽 ) ≥ 8m il( 字 符 线 宽 ) PSR 4000,D SR 2200 ≥ 0.4m il ≥ 0.3m il 中 间 盖 油 4m il , 要 求 SM T 脚 边 缘 间 距 ≥ 8m il 塞油常规工艺 要求允许塞锡、渗 药水、焊盘表面露 铜
PCB工艺技术参数
此工艺技术参数表,只是列出目 前比较普通的、成本相对较低的 参数。如果设计上需要,具体可 以和厂家协商调整。淘花/专用工艺技术基本参数(一)
项目
板件最大尺寸
完 成 厚 度 单双面 4层 6层 8层 10 层 12 层 ≤ 0.8mm 0.8mm<t ≤ 1.2mm 1.2mm<t ≤ 1.8mm 1.8mm<t ≤ 2.4mm 2.4mm<t ≤ 3.0mm ≥ 3.0mm淘花/专用有白色、黄色、黑 色油墨
另有蓝、黑色油墨 最小值大于左边要 求时须印 2 遍油
塞 油 孔 径 ≤ 0.5m m
工艺技术基本参数(八)
感光 双面不开阻焊窗 阻焊 阻焊窗≥焊盘 阻焊窗直径比孔径 允许塞油、塞锡 按开阻焊窗处理 ≥ 12mil 允许渗油 <12mil 允许渗油 ≥ 20mil 不许渗油 应允许塞油 0.15mil— 2m il <200 Ω 每 边 大 于 金 属 面 6m il ≥ 18mil ≥ 0.15m m <2.0m m 每 边 大 于 金 属 面 盖 油 边 缘 20mil 距 外 形 线 10m il淘花/专用常用板材厚度(包括铜箔)
厚 度 0 .1 7 0 .2 0 0 .2 4 0 .2 7 0 .3 0 0 .3 4 0 .3 7 0 .4 3 0 .5 0 0 .6 0 0 .7 0 0 .8 0 0 .8 5 1 .0 0 1 .0 4 1 .2 0 1 .6 0 2 .0 0 2 .4 0 3 .0 0 3 .2 0 公 差 ± 0 .0 1 8 ± 0 .0 2 5 ± 0 .0 3 8 ± 0 .0 3 8 ± 0 .0 3 8 ± 0 .0 5 ± 0 .0 5 ± 0 .0 5 ± 0 .0 5 ± 0 .0 6 4 ± 0 .0 6 4 ± 0 .0 6 4 ± 0 .0 6 4 ± 0 .1 0 ± 0 .1 0 ± 0 .1 3 + 0 /- 0 .1 6 ± 0 .1 8 ± 0 .1 8 ± 0 .2 3 ± 0 .2 3 F R -4 铜 箔 厚 18 35 35 18 35 70 35 18 35 70 18 35 70 35 35 70 35 70 18 35 70 18 35 18 35 70 70 18 35 70 18 35 18 35 70 18 35 70 18 35 35 35 度 ( um ) C E M -3 铜 箔 厚 度
孔及焊盘允许 擦花露铜 效率低、成本 高 最 小 ≥ 0.8mm , 制 作 成本高
铣槽宽度≥2.4mm淘花/专用工艺技术基本参数(三)
钻 孔 径 公 NP 长孔 孔 差 PTH 孔 钻孔 铣孔 冲孔 钻孔 铣孔 冲孔 钻孔 铣孔 冲孔 钻孔 铣 /冲孔 最大钻孔孔径 最小钻孔孔径 孔与孔之边缘距离 孔位公差 ∅ 6.5mm ∅ 0.3mm 盘
隔离盘 线宽 线与焊盘间距
工艺技术基本参数(六)
线 路 图 形 线与线 间距 盘与盘 间距 外层线 边缘 与孔 间距 测试点 线 路 距 边 铣外形 最小距 离 冲外形 V 槽 30 ° 45 ° 60 ° 遮孔最 大孔 径 遮孔每 边最 小值 层间对 位偏 差 ≥ 5mil (0.5OZ), ≥ 6mil ( ≥ 1OZ) ≥5mil (0.5OZ), ≥6mil (≥1OZ) ≥ 6mil 加 内 径 3mm , 环 宽 否则易 脱落 15mil 的 保护 环 ≥ 15mil ≥ 20mil 板 厚 ≤ 板 厚 ≥ 1.2mm 1.2mm ≥ 15mil ≥ 20mil ≥ 20mil ≥ 25mil ≥ 25mil ≥ 30mil ф 6.5mm 6mil ≤4 mil ( 不 含其 他流程 偏差 )
±0.2mm 30°,45°,60° 0.8mm= 板 厚 =2.5mm 板 厚 的 FR-4 以外材料 1/3±0.1mm 须另定 ±0.1mm淘花/专用工艺技术基本参数(五)
刨 斜 边 板厚 深度范围 0.8mm ≤ 板 厚 ≤ 2.0mm 0.5mm— 1.8mm ± 0.2mm 须配合角度
1间 距 6 mm 距(跳刀) 25mm 最小刨边宽度 50mm 最小板件宽度 角度范围 20 ° --60 ° 直 径 比 完 成 孔 大 16mil 内 层 焊 盘 直 径 以上 比完成孔须 达 20mil 以 上 直 径 比 完 成 孔 达 32mil ≥ 5mil (0.5O Z), ≥ 8mil (1O Z) ≥ 5mil (0.5O Z), ≥ 6mil ( ≥ 1O Z)