铝熔体在线除气净化机制研究
铝及铝合金的熔体净化(baidu)

夹杂物的生成途径主要是: • 从炉村中吸收杂质; • 从熔剂和熔炼添加剂中吸收杂质; • 从炉气中反应并吸收杂质; • 从炉料及炉渣中吸收杂质。
•夹杂物的危害
并不是熔体中的所有异物都是有害夹杂。金属中 非金属异质点的形态和大小,对金属性质有重要影 响。细小,弥散均匀分布的夹杂颗粒,在金属凝固 时,可以成为结晶的异质核心,同时也可以阻碍晶 粒的长大,起到细化晶粒的作用。所以高纯铝较一 般的工业纯铝更容易形成粗大晶粒。
• 非金属夹杂的种类很多,按其化学成分可分为氧 化物(FeO,SiO2,Al2O3,TiO2,MgO,ZnO等);氮化 物(AlN,ZrN,TiN等);硫化物(Ni3S2,CeS,Cu2S 等);氯化物(NaCl,KCl,MgCl2等);氟化物 (CaF2,NaF等);硅酸盐(Al2O•SiO2等)。这些 夹杂以不同形态和大小分布在金属熔体中,对金 属性能产生不同影响。
铝及铝合金的熔体净化
• 有色金属及其合金熔体在熔炼过程存在气体、各 种非金属夹杂物等,影响金属的纯洁度,往往会使 产品产生气孔、夹杂、疏松、裂纹等缺陷,影响铸 锭的加工性能及制品强度、塑性、抗蚀性、阳极 氧化性和外观质量。同时,在有色金属中除气体 和非金属夹杂之外,还含有少量的金属杂质,如 铝合金的钠、钙等低熔点金属。钠在含镁量高的 镁-铝系合金中易引起热裂敏感性,合金热轧时易 产生开裂,通常称之谓“钠脆性”,此外还影响 熔体的流动性和铸造性。
Al中Al2O3夹杂物的形态(两维)
Al中Al2O3夹杂物的形态(三维)
AlN
采用先进的测渣方法捕捉到的夹渣
Refractories
采用先进的测渣方法捕捉到的夹渣
• 夹杂物的来源与危害 • 杂质的吸收和积累主要是熔炼过程中,金属熔体
铸造铝合金熔体净化技术及工艺进展杨途才

铸造铝合金熔体净化技术及工艺进展杨途才文章首先简要分析了铝合金铸造中的熔体净化技术,在此基础上对铝合金熔体净化技术的工艺进展进行论述。
期望通过本文的研究能够对铝合金铸造质量的提升有所帮助。
标签:铝合金熔体;铸造;净化技术1铝合金铸造中的熔体净化技术分析在对铝合金进行铸造的过程中,受熔炼工艺的影响,使得熔体当中不可避免地会存在一些气体、夹杂物及金属杂质等,由此可能会导致铸造出来的铝合金出现裂纹、气孔等质量缺陷,对铝合金制品的整体强度、抗蚀性以及外观品质会造成影响。
熔体净化技术的出现,为这一问题的解决提供了途径,在铝合金铸造中,常用的熔體净化技术有两类,一类是吸附净化,另一类是非吸附净化。
下面分别对这两类技术进行分析。
1.1吸附净化技术。
此类技术主要利用熔体与吸附剂进行直接接触,通过吸附剂的理化和机械作用,去除铝合金熔体当中的气体和杂质。
具体包括以下几种方法:过滤法、气泡浮游法和溶剂法。
1.1.1过滤法。
以具有一定活性的材料制成过滤容器,将铝合金熔体置于其中,从而将悬浮在熔体当中的固态夹杂物分离出来,进而达到净化的目的。
这里所指的活性材料有陶瓷泡沫、玻璃丝布、微孔陶瓷管等等。
在上述几种材料中,最为常用的是以玻璃丝布制作成的过滤网,其优点是制作成本低、结构简单、实用性强,但在实践中发现,这种净化方法存在一些不足,其中最为突出的是过滤效果的稳定性欠佳,在过滤时,只能凭借滤网的网眼将一些尺寸较大的夹杂物去除掉,而比较微小的夹杂物则很难有效去除,并且每个滤网仅能使用一次,不可以重复利用。
陶瓷泡沫虽然净化效果比较好,并且使用也比较方便,但它的空隙率比较高,净化效率一般。
陶瓷管具有良好的过滤除渣能力,可将小到微米级的夹杂物过滤掉,但这种方法只适用于高质量铝合金制品的生产。
1.1.2气泡浮游法。
该方法也被称之为吹气法,可有效去除铝合金熔体当中的氢气,除此之外,在处理过程中,气泡上浮还可以吸附少部分氧化夹杂物,具有除杂的效果。
真空状态下铝合金熔体中除气的研究
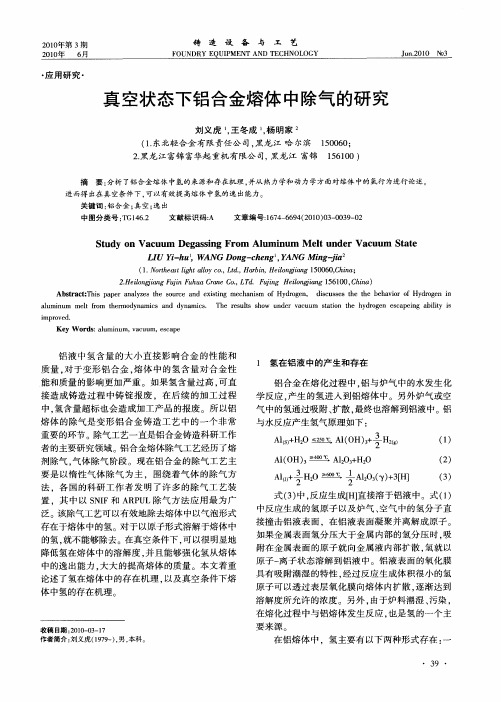
・
铸 造
设
备
与 工
艺
F 0UNDRY E OUI ME P NT AND T HNOL EC 0GY
应 用研 究 ・
真 空状态下铝合金熔体 中除气 的研 究
刘 义虎 , 王冬 成 . 明家 杨
(冻 北轻合 金 有 限责任 公 司 , 1 黑龙 江 哈 尔滨
() 3
A 2 3H2 1 + 0 0
2
Al1 0 —60C 1 A1 (+ 3 H ) > —  ̄0 ̄
0 ( ) 3H 3 y+ [ ] ^
式() , 3 中 反应 生 成 [J 接溶 于 铝液 中 。式 () H直 1 中反 应 生成 的氢 原子 以及 炉 气 、 空气 中 的氢 分子 直 接 撞 击 铝液 表 面 .在 铝 液 表 面凝 聚 并离 解 成 原子 。 如果 金 属表 面氢 分 压 大于 金 属 内部 的氢 分压 时 , 吸
关键词 : 合金 ; 空; 出 铝 真 逸
中图分类号 : G 4 . T 162
文献标识码 : A
文章编号: 5 — 64 2 1 ) 3 0 3 — 2 1 6 9 (0 0 0 — 0 9 0 64
St dy o c m g s i o u i u e tu u n Va uu De a sng Fr m Al m n m M l nde c m t t r Va uu S a e
10 6 ; 50 0
2黑龙 江 富锦 富华起 重机 有 限公 司, . 黑龙 江 富锦 160 5 10)
摘 要: 分析 了铝合金 熔体 中氢的来源和存在机理 , 并从热力 学和动力 学方 面对熔体 中的 氢行 为进行论述。
铝及铝合金的熔体净化及晶粒细化

铝及铝合金的熔体净化和晶粒细化摘要:综述了铝合金熔体净化的技术特点,重点分析了气泡浮游法、过滤法、熔剂法等几种常见的熔体吸附净化方法的工作原理和工艺改进,介绍了新型的旋转脉冲喷吹工艺、超声波净化工艺和电磁净化工艺,并展望了熔体净化工艺研究发展的趋势;综述了晶粒细化剂的发展历史及细化剂的细化机理和各种细化剂的比较,并着重介绍了新一代的Al-Ti-C晶粒细化剂。
关键词:铝合金;熔体净化;细化剂;细化机理1综述近年来铝合金材料大致向两个方向发展:一是发展高强高韧等高性能铝合金新材料,以满足航空航天等军事工业和特殊工业部门的需要;二是发展一系列可以满足各种条件用途的民用铝合金新材料。
与国外相比,我国铝合金研究的整体水平还比较落后,基础理论研究和技术装备水平及其完善程度都与国外的差距很大。
目前,铝合金研究的重点之一是研究和采用各种先进的熔体净化与变质处理方法,去除铝液中的气体和夹杂物,降低杂质含量,提高铝熔体的纯度,细化铝的晶粒从而改善铝合金的性能。
这也是可持续发展战略中废铝回收亟待解决的技术难题。
熔体净化是保证铝合金材料冶金质量的关键技术,引起企业界的广泛关注。
铝合金熔体净化的目的,主要是降低熔体中的含气量和非金属夹杂物含量。
对熔体纯洁度的要求,一般铝合金制品的含气量应小于0.15ml/100gAl,特殊的航空材料要求在0.10ml/100gAl以下;钠含量应在5ppm以下;非金属夹杂物不允许有1~5Lm尺寸的颗粒和聚集物,夹杂物含量越低越好。
可见,对铝合金熔体的纯洁度要求是非常严格的。
要达到上述要求,需采用各种先进的净化处理技术。
铝及其合金组织的微细化,可显著提高铝材的力学性能和加工工艺性能。
晶粒细化处理是使铝及其合金组织微细化,获取优质铝锭,改善铝材质量的重要途径。
铝加工工业的迅速发展促进了各种铝晶粒细化剂的开发与生产。
本文将在初步总结和分析国内外熔体净化和晶粒细化剂生产实践及文献资料的基础上,较全面地讨论各种铝合金熔体净化技术及其发展趋势,讨论各种晶粒细化剂及发展趋势。
铝熔体中杂气关系及排杂净化熔剂润湿行为的分子动力学模拟与试验

铝熔体中杂气干系及排杂净化熔剂润湿行为的分子动力学模拟与试验关键词:铝熔体;杂气排除;排杂净化熔剂;润湿行为;分子动力学模拟;试验探究铝熔体中杂气干系及排杂净化熔剂润湿行为的分子动力学模拟与试验前言随着铝合金在工业、航空、汽车等领域的广泛应用,铝及其合金的质量要求越来越高。
其中,杂气排除是影响铝及其合金材料性能的重要因素之一。
铝是一种氧化性较强的金属,处于液态状态时,易与大气中的氧、氮等气体发生反应,从而形成各种气泡和夹杂物。
这些气泡和夹杂物若果未能完全排除,容易对铝及其合金的性能产生不良影响,如气孔、疏松、裂纹等。
因此,探究铝液态表面与杂气原子之间的互相作用及杂气排除机理对于提高铝及其合金的质量有着重要意义。
除了杂气排除外,铝液态表面的润湿性也是影响铝及其合金加工性能的重要因素。
在铝熔体中,由于表面张力的存在,在铝液态表面浸润熔剂的能力受到限制,导致润湿性较差。
因此,探究排杂净化熔剂的润湿行为,期望找到一种新的方法来改善铝液态表面的润湿性。
为了深度理解铝熔体中杂气运动及其排除机制,以及排杂净化熔剂的润湿行为,本文起首接受分子动力学方法对铝熔体中杂气原子的行为进行了模拟探究,探讨了杂气原子对铝液态表面润湿性的影响。
同时,开展了试验探究,并探究了排杂净化熔剂的润湿行为。
本文旨在提供一种新的思路来改善铝及其合金材料的质量和加工性能。
方法分子动力学模拟:本文接受分子动力学方法对铝熔体中杂气的行为进行了模拟。
模拟系统包括2500个铝原子和50个杂气原子(含氢、氮、氧等),温度设定为700K,模拟时间为50ps。
模拟使用的分子动力学软件为LAMMPS。
试验探究:本文在试验室中接受平面铝杯进行试验,通过向铝液态表面添加杂气来模拟铝液态表面的杂气聚集行为。
同时,引入排杂净化熔剂来探究其对铝液态表面润湿性的影响。
试验中使用的熔剂是由氯化钠和氯化铝组成的混合物。
结果与谈论分子动力学模拟结果显示,杂气原子在铝熔体中会形成气泡,并对铝熔体的物理性质产生显著影响。
铝及铝合金熔体净化处理

铝及铝合金熔体净化处理铝料的表面都有一层厚薄不均的氧化膜,有时还吸附水分,夹杂灰沙,粘有油污,涂有油漆等。
在熔化时,铝料在高温环境中进一步氧化,氧化膜厚度增加,并与气氛中的水分起化学反应,生成氧化铝和氢,使氧化夹杂和气体含量增加。
所以,铝料熔化以后,必须进行净化处理,以清除铝液内部的杂质和气体。
用于净化铝液的物质统称为熔剂。
熔剂在室温多数是固体或气体,也有个别熔剂是液体,如CCl4。
固体熔剂的优点是体积小,容易运输和储存,但都具有较强的吸湿性,必须密封包装。
为了提高固体熔剂的净化效果,可将熔剂压紧成紧密小块用铝箔包裹,放入长柄的钻孔容器内插入熔池底部。
对以NaCl和KCl的混合盐为基体的熔剂,可先按配比将混合盐熔化后,加入难熔组分,例如Na3AlF6,经搅拌冷却后注入密封铁箱内。
熔剂使用前应存放在室温较高的干燥地点,如熔炉旁,以防受潮。
在熔炉内施加覆盖熔剂,可以减少熔化消耗,阻止铝液从炉膛气氛中吸收气体,但覆盖熔剂的耗用量大(约相当于铝料重量的10%),使生产成本提高,中小型铝加工厂一般不采用。
净化熔剂的使用通常是在铝料熔化以后将按配比混合的粉状熔剂撒在熔池表面,然后用长柄工具搅动铝液促使灰渣上浮。
在搅动过程中,部分熔剂加入熔池内部,与铝液发生化学反应,生成不溶于铝的气态物质,在气泡上升过程中起除气和除灰的作用。
使用较多的一种熔剂是2份冰晶石与1份氯化铵混合的粉末,其净化铝液时的化学反应如下:Na3AlF6+Al→2AlF3+3NaNH4Cl+2Al→AlN+AlCl+2H2AlF3+2Al→3AlFAlCl3+2Al→3AlCl6AlF+3O2→2Al2O3+2AlF36AlCl+3O2→2Al2O3+2AlCl3以上化学反应中所生成的Al2O3,AlN和H2,连同铝液中原有的Al2O3和H2一起被AlF3和AlCl3气泡带出液面。
有时也用Na2SiF6作为熔剂,但其净化效果不如Na3AlF6。
铝熔体在线电磁净化技术及设备

铝熔体在线电磁净化技术及设备1何向问2张昌兵3疏达1中色科技股份有限公司,河南洛阳,邮编4710392上海中跃能源科技有限公司,上海,邮编2001253上海交通大学,上海,邮编200240摘要:铝熔体净化的种类根据熔体位置和净化机理可以分为不同类型,本文着重介绍了铝熔体在线电磁净化技术和设备,描述了该设备的组成及其工作原理,最后通过将其与目前市场上常见的陶瓷板过滤装置、管式过滤装置和深床过滤装置进行对比,分析其优势和缺点,指出了其光明的前景。
关键词:铝熔体净化电磁净化技术陶瓷板过滤管式过滤深床过滤铝熔体净化的主要目的是除去其中的气体(主要是游离态的氢)、碱金属(主要为钠离子、钾离子等)和非金属夹杂物(主要为氧化铝等)。
一般情况下,铝熔体中的气体和非金属夹杂物可以同时去除,只是每种技术和设备的侧重各不相同,而碱金属的去除则需要特殊的精炼剂(或气体)进行专门的去除。
1铝熔体净化技术铝及铝合金熔体内氢含量、碱金属含量和氧化铝含量的多少对产品质量有着至关重要的影响。
因此,人们为了从源头上提高铝及铝合金产品的质量,开发出了多种铝熔体净化技术。
根据铝熔体处理的位置不同可以分为炉前预处理、炉内处理和炉外在线处理;根据净化的机理可以分为吸附净化技术和非吸附净化技术。
吸附净化技术主要是依靠精炼剂(精炼气体)或其他介质对铝熔体中的氢和非金属夹杂物进行吸附,达到净化铝熔体的目的;非吸附净化技术是除此之外依靠其他物理化学作用,达到铝熔体净化的目的。
炉前预处理,主要是指在加入熔铝炉之前对铝熔体的净化。
目前国内外很多铝及铝合金产品的生产厂家采用电解铝液作为原料。
电解铝液虽然能大大减少配料和熔化时间,节约能源,但熔体中却存在“二多、一少、一高”的现象,即氢含量多、夹杂物多、活性晶核少、铝熔体温度高,非常容易造成铸坯的冶金缺陷,如气孔、夹渣、晶粒粗大等,对最终产品质量产生不良影响。
为确保原料的纯净度,必须对电解铝液提前采取净化处理。
铝熔体净化处理方法分析
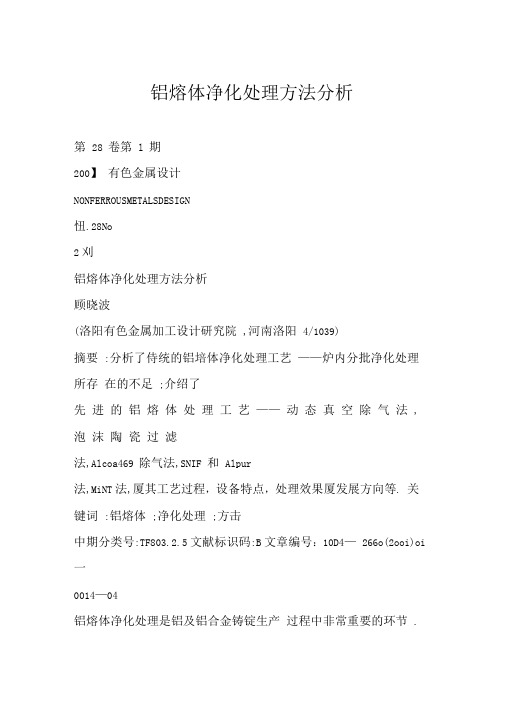
铝熔体净化处理方法分析第28 卷第l 期200】有色金属设计NONFERROUSMETALSDESIGN忸.28No2刈铝熔体净化处理方法分析顾晓波(洛阳有色金属加工设计研究院,河南洛阳4/1039)摘要:分析了侍统的铝培体净化处理工艺——炉内分批净化处理所存在的不足;介绍了先进的铝熔体处理工艺——动态真空除气法, 泡沫陶瓷过滤法,Alcoa469 除气法,SNIF 和Alpur法,MiNT法,厦其工艺过程,设备特点,处理效果厦发展方向等. 关键词:铝熔体;净化处理;方击中期分类号:TF803.2.5文献标识码:B文章编号:10D4—266o(2ooi)oi 一0014—04铝熔体净化处理是铝及铝合金铸锭生产过程中非常重要的环节.传统铝液净化处理工艺一般都是在保温炉内分批进行操作的, 普遍采用氮——氯混合气体,熔剂进行精炼.这种净化处理工艺,大多由人工操作, 除气率低,精炼不彻底,铝液在从保温炉向铸造机输送过程中,铝液会再次被污染,且工人劳动强度大,劳动环境差,污染严重, 对大容量的炉子.人工操作难以实现.随着航空用高质量铝合金,双零铝箔等高精制品的出现,对锭坯的质量要求越来越高,传统的铝液净化处理工艺已不能适应大规模生产,高质量锭坯的要求.为此,国内外有关人士经过长期摸索,做了大量的工作,开发出了先进的铝熔体净化处理新工艺——炉外铝熔体净化处理新工艺,即铝熔体在从保温炉向铸造机输送过程中,进行精炼,过滤处理, 可以高效去除熔体中的可溶和不溶的杂质 1 铝熔体净化目的1.1铝熔体中存在的杂质1.1.1氢铝及铝合金在熔炼过程中,氢极易溶解于液态铝中,在冶炼温度范围内,温度越高气体溶解度越高,特别是在固态一液态相变时,气体溶解度骤然增高,详见表 1.裹 1 氢在铝中的溶解度nd./10~在熔点温度时高于熔点温度时1.1.2 非金属夹杂铝熔体中存在的非金属夹杂物有:(1)氧化物:AI2,MgO,sjo2,A12等;(2)残余的细化剂Al—Ti—B 中间合金的粗大一 B 粒子;(3)耐火砖碎片,脱落的流槽和工具上的保护涂料.1.2铝熔体净化目的和要求熔体中存在的气体,各种夹杂物熔体中氢溶解度要求mlJl00g 以下,对于一些特殊要求0.15 〜0.2的制品, 应在0.1mlJl00g 以下.2 铝熔体净化机理铝熔体净化处理根据净化机理的不同, 可分为吸附净化和非吸附净化两大类.2.1 吸附净化靠精炼剂产生的吸附作用达到去除气体和氧化物夹杂的目的.2.1.1 惰性气体净化惰性气体是指与铝熔体及溶解的氢不起化学反应,叉不溶解于铝中的气体,通常使用氩气,氮气. 惰性气体刚吹人铝熔体中时,惰性气体气泡中氢的分压PH=0,惰性气体气泡和铝液的界面上有氢的压力差,使金属中的氢不断地扩散进惰性气体气泡中,惰性气体气泡浮出液面后,气泡中的氢随之逸出由于铝液和氧化物夹杂互不湿润,使夹杂与惰性气体气泡之间满足金—杂+金—气> —公式,根据热力学第二定律,铝液中的氧化物夹杂能自动吸附在惰性气体气泡上而被带出液面.由此可以得出结论,惰性气体气泡与铝熔体的接触面积越大,净化效果就越好.2.1.2 活性气体净化对于铝来说,活性气体主要是指氯气. 氯气本身不溶于铝中,但氯气和铝及溶于铝中的氢会发生如下反应: ck+H2—2Hcb 十3caz+2AI--~2AICt3+反应生成物HC1和alch(沸点183oC)均为气态,不溶于铝液,和未参加反应的氯气一起都能起精炼作用.氯气精炼效果虽好,但它对人体有害,污染环境,易腐蚀设备及加热元件,因此,在实际生产中大多用氮一氯混合气体进行精炼,以提高精炼效果,减少其危害作用.2.2 非吸附净化非吸附净化包括真空处理和机械过滤. 真空处理,主要是去除铝熔体中的氢,即在真空状态下,铝熔体的吸气倾向趋于零,而且溶解在铝液中的氢有强烈的析出倾向;机械过滤,是靠微孔过滤去除铝熔体中的不溶3 铝熔体净化处理新工艺铝熔体净化处理方法很多,归纳起来大致可分为三大类:(1)以除气为主的方法有ASV 公司的动态真空除气法;(2)以除不溶性夹杂物为主的凯撒公司的陶瓷管过滤法和柯那尔公司的泡沫陶瓷过滤法;(3)既可除气,又可去夹杂物的有英国铝业公司的FILD 法,美国铝业公司的A1.Coa469法,美国联合碳化物公司的SNIF法, 法国彼西涅公司的Alpur 法,美国联合铝业公司的MINT 法.3.1 除气为主的净化处理方法——动态真空障气洼动态真空除气是相对于静态真空除气而言的.在熔炼温度范围内,铝液表面有致密的Y—AJ203 膜存在,阻碍氢的析出.因此, 必须清除这层氧化膜的阻碍作用才能获得好的除气效果.静态真空除气是在真空处理的同时,在熔体表面撒上一层溶剂以便使氢气通过氧化膜除气,但从使用情况来看,除气效果并不好.1969 年,挪威ASV 公司开始采用动态真空除气工艺来净化铝液.动态真6 有色金属设计第28 卷空除气的工艺过程是先将真空炉抽成10m 的真空,然后打开进料口密封盖, 把从保温炉来的铝熔体借真空抽力喷人真空室内,喷人真空室内的熔体,呈细小弥散的液滴,因而,溶解在铝液中的氢能快速扩散出去,钠被蒸发燃烧掉.动态真空处理的除气速度,取决于氢的扩散速度和扩散面积, 为了提高除气速度,必须增大熔体与真空气氛的接触面积.使用结果表明,经动态真空处理后的铝熔体氢溶船度低于0.12 mL/100g.动态真空除气工艺的优点是:除气效果好,无公害,处理过程造渣少;缺点是:除其它有害杂质的效果差,不能实现连续处理,设备结构复杂,设备价格昂贵,而且设备的密封性难以保证.3.2除不溶性夹杂物为主的净化处理方法饱沫陶瓷过滤法泡沫陶瓷是近年发展起来的新型陶瓷过滤材料.柯那尔公司泡沫陶瓷过滤板是用氧化铝,氧化钙等制成的海绵状多孔板.用该工艺处理铝液的工艺过程是:在保温炉和铸造机之间的流槽上,放人该装置,将该装置加热到一定温度后,开始放流铸造,以实现铝熔体的连续过滤.过滤板的孔隙大小,形状以及板的厚度,对过滤的效果有很大的影响.一般板厚为50Hn孔隙率达85%9D%.这种工艺能过滤微量级的氧化物夹杂. 效果好而且成本低,设备结构简单,使用方便,适用于各种合金.事实证明,使用该装置后,3003 合金印刷板成品率提高了9%; 1145 合金电容器铝箔两次断头间的平均重量提高了45%;6063 台金建筑铝型材挤压速度提高20%.其缺点是该工艺本身不具有除氢功能,过滤板需定期更换,易破损, 常给生产带来麻烦.3.3既可除气,又可去夹杂物的净化处理方法3.3.1Alcoa469 除气法此工艺是美国铝业公司研究成功的铝液在线处理工艺,可实现铝液连续净化.见图 1.出口At+At+C]2固1Alcoa469 蝽体处理装置熔体 2 一氧化铝球 3 气体扩散器 4 一隔板该装置有 2 个处理室(称为两单元),采用氩一氯混台气体精练和氧化铝球过滤在此装置中,熔体先经粗过滤床过滤,再经细过滤床过滤流向铸造机.在 2 个过滤床的底部设有气体扩散器,气体的流向与熔体的流向相反并均匀分布到整个过滤床截面上经Alcoa469 法处理的铝液氢溶解度可控制在0.15mL/100g 以内,见表 2.袁2Alcoa469 装置除氢效果表AA铝{庄流量给气量氢溶解度/(?h '' )/(?h '' )/(?1130 '' g) 3.3.2SNIF 法和Alpur 法这两种方法都是利用快速旋转的石墨气体喷头使精练气体呈微细气泡喷出分散于熔体中,从而达到去除熔体中的氢和部分氧化物夹杂的目的.SNIF 法是美国联合碳化物公司发明的种在线式铝熔体处理装置.该装置是用惰性气体喷人快速旋转的石墨喷嘴,喷嘴是由锭子和转子组成,惰性气体从高速旋转的转第l 期麒晓渡:铝髂#净化处理方{ 盎分析子和锭子之间的缝隙(<5mm) 喷出,惰性气体变成极细的弥散气泡,由于转子高速旋转搅拌金属液,使得弥散气泡均匀分布在整个熔体中,增大了气体与熔体的接触面积,使可溶性氢更有效地进入气泡中,使之与气泡一起上浮排除,从而达到快速,高效地从熔体中清6710140 g 640】600756016—020006—0】l45—6250.30.1057O230156.5015—023009—01240—478 0.301260AJ.pm”法由法国彼西涅公司发明,1981 年1O 月取得专利.该方法与SNW 法除气工艺类似,但喷嘴设计与SNIF 不同,其结构更为简单.在喷头上有两种不同形式的通道,一种是径向排列的8条小通道(I〜 3 一),小通道同转动的中空心轴相通,喷人惰性气体;另一种为锥形排列的8 条大通道(帆一15rm n),通道中心交点与喷头转动轴同心,通道中心线与转动轴成45o 角,喷头上有4 个叶片,在高速转动下搅拌金属液,使气泡细小而分布均匀,它同时能搅动熔体进入喷嘴内使金属液与气充分混合,因此使净化效果提高.据资料介绍,除气效率可达75%.3.3.3M 法MINT 法是美国联合铝业公司研制, 1982 年以后开始在工业上使用.该方法是将熔体从装置上方成切线方向流入反应器内,并以螺旋状向下流动.在反应器底部装有高压气体喷嘴,喷入细小的氩一氯气泡, 气泡上浮,熔体向下流动,在漩涡流动作用下,把细小气泡均匀弥散分布到熔体中,把熔体中的氢除去.熔体从反应器底部流出, 通过上升管流入泡沫陶瓷过滤器,氧化物夹杂则被过滤掉.该装置用氩气加上0.5%一3%的氯气, 除氢效率可达48%一73%,见表4;金相低倍检查除氧化物夹杂的效率可达90%,见表 5..表4MINT 除氢效果表(下转菇*页J有色金属设计第28 卷应用,积累了一些实践经验,装置及规模也参考文献不断地向过滤法由于其本身不具有除气功能,生产上往往不单独使用;Alcm469 法由于要定期更换氧化铝球,使用前要加热过滤床.因此使用起来方便性较差;Mpur 与sN 装置除气效果好,使用方便,深受广大用户的青睐.Alpllr与SMF相比较,设备结构简单,价格便宜,处理箱内衬没有石墨材料,使用寿命长,炉内不用气体保护,清渣方便,生产上常将Mpur 和sN 与泡沫陶瓷过滤相结合,净化效果更好.MINT 结构最简单,没有同熔体接触的运动部件,占地面积小,更换合金品种方便,除渣效率高,更加适用于多合金生产的熔铸机组上使用. 当然,上述净化方法也存在着以下缺点:八、、-(1)由于装置处在保温炉和铸造机之间,拉长了保温炉和铸造机的距离,增加了不必要的面积;而且由于距离的拉长,除气箱一定要加热,增加了能耗. (2)在更换合金品种时,除气箱内的铝液要排放掉,给生产造成了很大的不方便. 而且,除气箱中的原有铝液将作为废品处理,增加了生产成本. 在有效地净化铝熔体的前提下如何解决上述问题,是摆在我们每个铝加工工作者面前的重要课题.国外目前正在研制开发的所谓紧凑型净化处理设备虽然较好地解决了上述问题,但密封及快速撇渣问题仍未解决. 我们相信,经过努力,在不远的将来,一定会使铝熔体净化处理工艺在节约资源,节能,环保及生产上取得突破性进展.。
铝及铝合金熔体净化方法研究
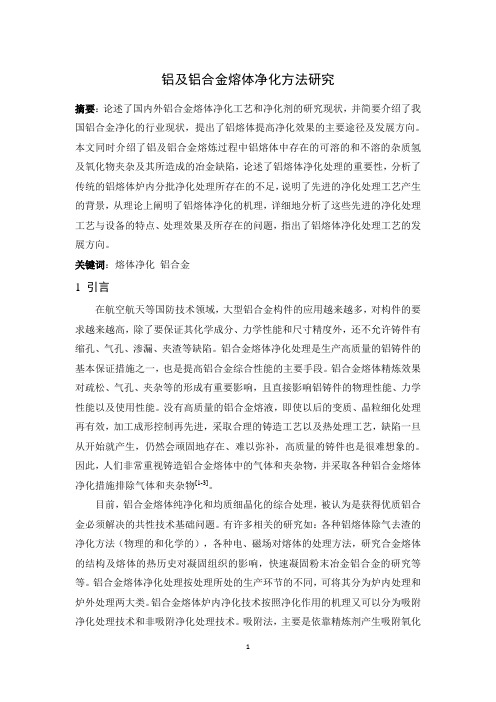
铝及铝合金熔体净化方法研究摘要:论述了国内外铝合金熔体净化工艺和净化剂的研究现状,并简要介绍了我国铝合金净化的行业现状,提出了铝熔体提高净化效果的主要途径及发展方向。
本文同时介绍了铝及铝合金熔炼过程中铝熔体中存在的可溶的和不溶的杂质氢及氧化物夹杂及其所造成的冶金缺陷,论述了铝熔体净化处理的重要性,分析了传统的铝熔体炉内分批净化处理所存在的不足,说明了先进的净化处理工艺产生的背景,从理论上阐明了铝熔体净化的机理,详细地分析了这些先进的净化处理工艺与设备的特点、处理效果及所存在的问题,指出了铝熔体净化处理工艺的发展方向。
关键词:熔体净化铝合金1 引言在航空航天等国防技术领域,大型铝合金构件的应用越来越多,对构件的要求越来越高,除了要保证其化学成分、力学性能和尺寸精度外,还不允许铸件有缩孔、气孔、渗漏、夹渣等缺陷。
铝合金熔体净化处理是生产高质量的铝铸件的基本保证措施之一,也是提高铝合金综合性能的主要手段。
铝合金熔体精炼效果对疏松、气孔、夹杂等的形成有重要影响,且直接影响铝铸件的物理性能、力学性能以及使用性能。
没有高质量的铝合金熔液,即使以后的变质、晶粒细化处理再有效,加工成形控制再先进,采取合理的铸造工艺以及热处理工艺,缺陷一旦从开始就产生,仍然会顽固地存在、难以弥补,高质量的铸件也是很难想象的。
因此,人们非常重视铸造铝合金熔体中的气体和夹杂物,并采取各种铝合金熔体净化措施排除气体和夹杂物[1-3]。
目前,铝合金熔体纯净化和均质细晶化的综合处理,被认为是获得优质铝合金必须解决的共性技术基础问题。
有许多相关的研究如:各种铝熔体除气去渣的净化方法(物理的和化学的),各种电、磁场对熔体的处理方法,研究合金熔体的结构及熔体的热历史对凝固组织的影响,快速凝固粉末冶金铝合金的研究等等。
铝合金熔体净化处理按处理所处的生产环节的不同,可将其分为炉内处理和炉外处理两大类。
铝合金熔体炉内净化技术按照净化作用的机理又可以分为吸附净化处理技术和非吸附净化处理技术。
铝熔体在线除气装置的特性及其改进
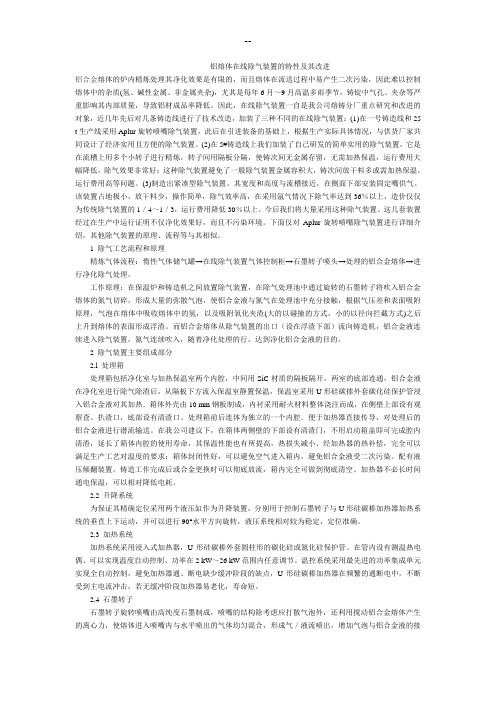
铝熔体在线除气装置的特性及其改进铝合金熔体的炉内精炼处理其净化效果是有限的,而且熔体在流送过程中易产生二次污染,因此难以控制熔体中的杂质(氢、碱性金属、非金属夹杂),尤其是每年6月~9月高温多雨季节,铸锭中气孔、夹杂等严重影响其内部质量,导致铝材成品率降低。
因此,在线除气装置一自是我公司熔铸分厂重点研究和改进的对象,近几年先后对几条铸造线进行了技术改造,加装了三种不同的在线除气装置:(1)在一号铸造线和25 t生产线采用Aplur旋转喷嘴除气装置,此后在引进装备的基础上,根据生产实际具体情况,与供货厂家共同设计了经济实用且方便的除气装置。
(2)在5#铸造线上我们加装了自己研发的简单实用的除气装置,它是在流槽上用多个小转子进行精炼,转子间用隔板分隔,使铸次间无金属存留,无需加热保温,运行费用大幅降低,除气效果非常好;这种除气装置避免了一般除气装置金属容积大,铸次间放干料多或需加热保温,运行费用高等问题。
(3)制造出紧凑型除气装置。
其宽度和高度与流槽接近,在侧面下部安装固定嘴供气。
该装置占地极小,放干料少,操作简单,除气效率高,在采用氩气情况下除气率达到36%以上,造价仅仅为传统除气装置的1/4~1/3,运行费用降低30%以上。
今后我们将大量采用这种除气装置。
这几套装置经过在生产中运行证明不仅净化效果好,而且不污染环境。
下面仅对Aplur旋转喷嘴除气装置进行详细介绍,其他除气装置的原理、流程等与其相似。
1 除气工艺流程和原理精炼气体流程:惰性气体储气罐→在线除气装置气体控制柜→石墨转子喷头→处理的铝合金熔体→进行净化除气处理。
工作原理:在保温炉和铸造机之间放置除气装置,在除气处理池中通过旋转的石墨转子将吹入铝合金熔体的氮气切碎,形成大量的弥散气泡,使铝合金液与氮气在处理池中充分接触,根据气压差和表面吸附原理,气泡在熔体中吸收熔体中的氢,以及吸附氧化夹渣(大的以碰撞的方式,小的以径向拦截方式)之后上升到熔体的表面形成浮渣。
浅谈铝熔体在线处理系统性能特点

126研究与探索Research and Exploration ·工艺与技术中国设备工程 2019.10 (下)有效地运用氢氧化钠元素、碳酸钠元素等辅助类的试剂将设备当中所残留的酸性清洗试剂进行中和,避免酸性试剂对中央空调设备造成极为不利的影响,当中央空调主机设备中的酸碱度达到7左右,方可达到标准,而到试剂的酸碱程度达标之后,相关的中央空调主机化学清洗工作人员才能够进行最后的钝化处理。
另外,中央空调主机化学清洗工作人员在实际进行中和处理的过程中还要打开主机的端盖,并运用高压设备对中央空调主机内部的通关进行清洗处理。
当完成高压清洗工作完成后,要分别打开中央空调主机内部冷凝装置的进水口阀门以及出水口阀门,当阀门打开后需要对中央空调主机进行反洗处理,以此保证中央空调主机内部的试剂残液能够得到有效的清除,避免对整个设备造成极为不利的影响。
2.4 钝化处理钝化处理属于中央空调主机化学清洗工作最后的一个处理环节,该项工作的主要作用就是提升设备的防腐性,避免一些残留的酸性试剂对整个设备造成不利影响,从而保证设备能够持续有效且稳定地运行下去。
具体而言,如锅炉经酸洗、水冲洗、漂洗后,金属表面很清洁,非常活化,很容易遭受腐蚀,所以必须立即进行钝化处理,使清洗后的金属表面生成保护膜,减缓腐蚀。
中央空调主机化学清洗工作人员在实际工作期间必须要准备好钝化预膜试剂,将酸碱值调整到8~9,以此有效地保证钝化处理工作的质量。
而在中央空调主机清洗工作中的有效落实钝化处理措施,可以有效地降低二次腐朽问题出现的概率,进而保证中央空调在经过化学清洗处理后,可以持续有效且稳定地运行下去。
从实际角度出发,现阶段,在社会中常见的中央空调主机类型主要分为两种,其一为地温式中央空调冷凝装置,其二为地温式中央空调蒸发装置,而对于这两种装置的化学清洗方法并无明显的差异,但是相关的清洗管理人员在实际清洗蒸发装置的过程中严禁打开设备进行清洗。
铝合金熔炼过程中除渣及精炼除气的分析
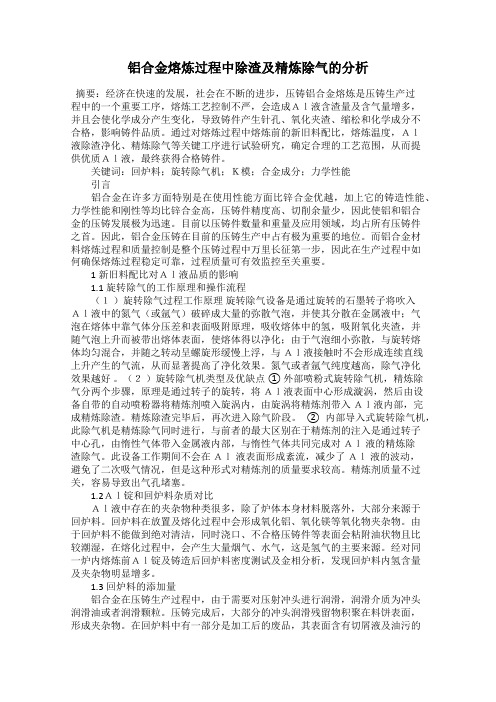
铝合金熔炼过程中除渣及精炼除气的分析摘要:经济在快速的发展,社会在不断的进步,压铸铝合金熔炼是压铸生产过程中的一个重要工序,熔炼工艺控制不严,会造成Al液含渣量及含气量增多,并且会使化学成分产生变化,导致铸件产生针孔、氧化夹渣、缩松和化学成分不合格,影响铸件品质。
通过对熔炼过程中熔炼前的新旧料配比,熔炼温度,Al液除渣净化、精炼除气等关键工序进行试验研究,确定合理的工艺范围,从而提供优质Al液,最终获得合格铸件。
关键词:回炉料;旋转除气机;K模;合金成分;力学性能引言铝合金在许多方面特别是在使用性能方面比锌合金优越,加上它的铸造性能、力学性能和刚性等均比锌合金高,压铸件精度高、切削余量少,因此使铝和铝合金的压铸发展极为迅速。
目前以压铸件数量和重量及应用领域,均占所有压铸件之首。
因此,铝合金压铸在目前的压铸生产中占有极为重要的地位。
而铝合金材料熔炼过程和质量控制是整个压铸过程中万里长征第一步,因此在生产过程中如何确保熔炼过程稳定可靠,过程质量可有效监控至关重要。
1新旧料配比对Al液品质的影响1.1旋转除气的工作原理和操作流程(1)旋转除气过程工作原理旋转除气设备是通过旋转的石墨转子将吹入Al液中的氮气(或氩气)破碎成大量的弥散气泡,并使其分散在金属液中;气泡在熔体中靠气体分压差和表面吸附原理,吸收熔体中的氢,吸附氧化夹渣,并随气泡上升而被带出熔体表面,使熔体得以净化;由于气泡细小弥散,与旋转熔体均匀混合,并随之转动呈螺旋形缓慢上浮,与Al液接触时不会形成连续直线上升产生的气流,从而显著提高了净化效果。
氮气或者氩气纯度越高,除气净化效果越好。
(2)旋转除气机类型及优缺点① 外部喷粉式旋转除气机,精炼除气分两个步骤,原理是通过转子的旋转,将Al液表面中心形成漩涡,然后由设备自带的自动喷粉器将精炼剂喷入旋涡内,由旋涡将精炼剂带入Al液内部,完成精炼除渣。
精炼除渣完毕后,再次进入除气阶段。
② 内部导入式旋转除气机,此除气机是精炼除气同时进行,与前者的最大区别在于精炼剂的注入是通过转子中心孔,由惰性气体带入金属液内部,与惰性气体共同完成对Al液的精炼除渣除气。
铝熔体在线除气净化机制的工艺性研究

化吸收MINT后对其改型研制的D刚,琢神公司在消化吸收ALPUR的基础上开发的CQ500精
炼装置等等。尽管也有不是仿制仿造,但因未能深入从根本上理解挖潜,也因高校和生产应用 厂家间的体制等状况,未能发挥产学研最大优势,也没有单位保持较长期的技术创新性深入实 践研究。麦特新团队正是依托高校而成立的铝熔体处理技术的综合性研究应用团队,从2001 年承担高校课题“大流量液态金属连续除气净化技术研究”开始,对国内外各种形式的铝熔体 在线除气净化技术进行模拟研究耨实践应用参数毙对,寻找出规律性、科学性、可行性的研究 实践工作o
-除气过程可以分为两种情况:一种是能够形成氢气泡的除氢过程;另一种是不能形成氢气 泡的除氢过程。
对于前者,大致可以分为三个阶段:首先是气泡的形核;然后是气泡的生长和上浮;最后是 气泡的逸出。在铝熔体中,气泡的形核必须满足以下两个条件:铝熔体溶解的氢气处于过饱和 状态而具有析出压力;气泡内气体压力大于作用于气泡的外压力,即:
Technical research of molten aluminum on-line purification mechanism
KE Dong-jie,CHEN Qua,LIN Zhong,LI Yu-hang (Fuzhou Metal-new High-Temp.Tech.Co.。Ltd.,Fujian Metal-new Alun血um Tech.Co.,Ltd.,Fuzhou 350000,China)
附层中发生反应,生成气体分子从表面脱附。根据Langmuir公式,传质系数可以表示为:
浅谈铝及铝合金熔体中的熔体净化方法

浅谈铝及铝合金熔体中的熔体净化方法来源:艾特贸易网熔体净化就是利用物理化学的方法和相应的工艺措施,除掉液态金属中各种杂质以获得成分符合要求的金属熔体的工艺方法。
随着铝合金应用领域越来越广泛以及高性能铝合金的研制与问世,对铝合金熔体的净化技术提出了越来越高的要求。
铝熔体净化的方法很多,不同的方法有各自的优缺点,实际生产中应根据原料所含杂质情况及对产品的质量要求进行合理选择。
如果按净化工序所在位置,铝熔体净化方法可分为炉内精炼和炉外净化过程。
炉外净化过程也称在线精炼,就是从熔炼炉流放出的金属熔体在铸造成形之前进行的连续净化处理。
因为铝合金熔体炉内处理,在熔体转注过程中又有二次污染的可能,为了提高净化处理的效果和保证熔体成形前的质量稳定可靠,炉外连续净化处理得到了迅速发展。
根据对铸锭质量的要求,炉外在线精炼可选择采用以脱气为主、以除去非金属夹杂为主或同时兼顾脱气和除渣等不同工艺。
目前方法主要有:玻璃丝布过滤法、泡沫陶瓷过滤法、无烟连续脱气和净化法、旋转喷嘴惰性气体浮选法。
如果按净化处理的主要杂质种类,铝熔体净化方法可分为除渣精炼和脱气精炼。
(1)铝熔体的除渣精炼。
铝合金中的非金属夹杂主要是氧化物、氯化物、氮化物、硫化物以及硅酸盐等,它们大都以颗粒或薄膜状的独立相存在,对铝合金及制品性质产生很大的影响。
目前,普遍采用的除渣精炼方法主要有静置澄清法、浮选法、过滤法和熔剂法。
前三者分别利用密度差、吸附作用以及机械过滤作用的原理进行除渣。
而熔剂净化法则是在熔体中加入适当的熔剂,与熔体中的杂质发生物理化学反应,生成轻质固相组分进入渣中,在除渣操作中予以排除,使熔体得以净化。
(2)铝熔体的脱气精炼。
铝合金熔体中的气体主要是氢、氧、氮三种气体,而氢占80%~85%,因此,脱气精炼主要是指从熔体中去除氢气。
在熔炼过程中,必须尽可能地降低熔体中的氢含量,否则在铝合金制品中会出现气孔、缩孔、疏松等缺陷,影响制品的使用性能。
- 1、下载文档前请自行甄别文档内容的完整性,平台不提供额外的编辑、内容补充、找答案等附加服务。
- 2、"仅部分预览"的文档,不可在线预览部分如存在完整性等问题,可反馈申请退款(可完整预览的文档不适用该条件!)。
- 3、如文档侵犯您的权益,请联系客服反馈,我们会尽快为您处理(人工客服工作时间:9:00-18:30)。
铝熔体在线除气净化机制研究柯东杰;陈群;李宇航【摘要】阐述液态铝液在线除气的物理化学原理,分析国内外铝液在线除气的研究状况和存在的不足.创新性地采用同实际铝液流量相当的动态水模拟试验进行研究,发现了动态两相流运动中存在合泡和短流现象.并提出有效的解决措施.同时发明了多项专利技术,发挥产学研密切配合的优势,研发出节能减排的在线除气工艺技术和装备.【期刊名称】《轻合金加工技术》【年(卷),期】2012(040)008【总页数】10页(P13-22)【关键词】铝合金;在线除气;动态水模拟;工艺研究【作者】柯东杰;陈群;李宇航【作者单位】福州麦特新高温材料有限公司,福建麦特新铝业科技有限公司,福建福州350001;福州麦特新高温材料有限公司,福建麦特新铝业科技有限公司,福建福州350001;福州麦特新高温材料有限公司,福建麦特新铝业科技有限公司,福建福州350001【正文语种】中文【中图分类】TG292铝及其合金在熔炼炉内高温熔炼过程中,来自纯金属锭、中间合金、废料、高温炉气、耐火材料和工具对铝熔体纯洁度的影响,使铸锭产生气孔和夹渣等冶金缺陷。
因此在生产过程中采用熔剂和惰性气体精炼来减少冶金缺陷的产生,然而炉内精炼处理均存在以下问题:(1)纯惰性气体精炼流量大、气泡大、熔体翻滚严重,容易氧化造渣,除气效果较好,但除渣效果差;且大流量氩气成本高,用氮气容易生成MgN和AlN,净化程度不良。
(2)氯气净化毒性和活性大,反应太激烈,害处多,净化效果更差。
(3)混合气体精炼用氮气和氯气混合或者氩气和氯气混合气体精炼,提高净化效果不明显,对人体健康有害,对周围设备腐蚀严重,为此必须有完好的通风防护设备。
(4)纯熔剂净化虽能较好清除氧化夹渣,也可以去除一些气体,但不彻底,还会带来熔剂夹渣。
(5)真空处理去气效果很好,但去除杂质的作用很小,而且设备造价、运行成本昂贵。
综上所述,当今最经济实用有效的具有熔剂净化效果和气体净化效果的炉内喷粉精炼是铝合金熔体最有效的精炼方法[1]。
但是在熔炼炉内的铝熔体的氢含量均在0.24 mL/100 g~3.0 mL/100 g之间,使铸锭达不到通常的质量要求,必须进一步净化;由此发展了炉外在线除气和过滤净化处理技术,本文重点阐述在线除气工艺技术的进步。
炉外处理方法很多,按其主要作用可分为以除气为主的,如Air-Liquid法;以除渣为主的,如玻璃丝布、陶瓷管和泡沫陶瓷过滤法等;除气除渣兼有的,如AlCOA469、FILD、SNIF、AlPur、MINT、RDU、GBF等。
经过几十年的发展,国外已经有许多用于在线旋转喷吹净化工艺的专利产品,例如:美国联合碳化物公司的SNIF法、法国彼西涅公司的ALPUR法、英国Foseco公司的RDU法、Foseco日本公司的GBF法、美国Hitchcock公司的RID法、澳大利亚Pyroteck公司开发的旋转喷射熔剂法的系列设备、意大利铝业公司工艺研究部研发的ALUDEF(铝除气与过滤)等。
国内在引进一些国外先进净化技术和设备的基础上,开展了铝合金熔体净化技术的研究。
例如:大连理工大学与华东铝加工厂设计研制了DUT-89铝液净化设备,西南铝加工厂消化吸收MINT技术后研制的DFU,琢神公司在消化吸收ALPUR的基础上开发的CQ500精炼装置等等。
从2001年起,麦特新公司依托高校而成立的铝熔体处理技术的综合性研究应用团队,承担高校课题“大流量液态金属连续除气净化技术研究”,对国内外各种形式的铝熔体在线除气净化技术进行模拟试验研究和对实践应用参数进行对比,取得了一些成果。
1 在线除气净化的理论依据1.1 惰性气体除气净化的物理化学过程描述氢在铝中的溶解度决定于与铝熔体接触的气相中氢气的分压。
当铝熔体中的氢含量对应的平衡状态的氢分压大于与铝熔体接触的实际气体中氢分压时,铝熔体中的氢会向气相中扩散而实现除氢。
这就是气泡浮游法除氢的原理。
据此向熔体中通入纯净的惰性气体,因为惰性气泡氢的分压p'H2=0,而熔体中氢含量对应的平衡状态的氢分压p H2>0,熔体中的氢会向气泡中扩散,复合成氢气分子随气泡排出熔体。
为了用尽可能少的惰性气体除掉尽可能多的铝熔体中的氢,在线惰性气体除氢应遵循以下原则:(1)隋性气体中氢和氧的含量越低越好;(2)吹入熔体中的惰性气体形成的气泡数量越多、越细小、越弥散越好;(3)气泡在铝熔体中停留的时间越长越好。
为此惰性气体除气设备多采用高速旋转喷头,从喷头叶片喷出的流体,产生强烈的紊流。
从高速旋转的喷头喷射出来的气泡,在靠近喷头处,被由喷头叶片喷出的熔体和周围速度相对较慢的熔体迅速捕获,气泡受到两层流体产生的紊流切应力的作用,当大于气泡的承受能力时被从中切断,分裂为两个气泡。
分裂的气泡再被其他相切的液体层所捕获,就能继续分裂成更小的气泡,直到两层流体间的切应力不足以使气泡破碎或气泡脱离此切应力的作用范围为止。
从而可以产生比单管或多管更加细小、更加均匀的气泡,有效增加比表面积,也有效增加传质扩散能力,同时延长了气-液界面的接触时间,在净化气体进气流量一定时,使得净化气泡逸出铝熔体时其中氢的浓度更大,有效利用了净化气体,从而可以获得极佳的净化效果。
预热吹入铝熔体的惰性气体,可以减少因惰性气体升温导致的气泡体积增大;使除气室腔体的横截面积沿高向逐渐增大可以减少由于气泡上升,熔体中压力下降使气泡体积增大带来的气泡合并的可能;若能实现负压除气也可进一步改善除气效果。
铝熔体的除氢过程是除气-吸气的动态过程,由铝熔体内部的除氢过程和铝熔体表面的氧化吸氢过程组成。
除氢效果由这两个方向相反过程的动态平衡所决定。
铝熔体除氢净化效果很大程度上取决于铝熔体和大气以及铝熔体和净化气泡的传质扩散系数,同时,夹杂的去除效率也很大程度上取决于相互之间的碰撞、净化气泡对夹杂的吸附以及净化气泡的大小和分布等。
总之,铝熔体内部的动力学条件对净化效率有很大的影响。
除气过程可以分为两种情况:一种是能够形成氢气泡的除氢过程;另一种是不能形成氢气泡的除氢过程。
对于前者,大致可以分为三个阶段:首先是气泡的形核,然后是气泡的生长和上浮,最后是气泡的逸出。
除非真空除气,通常第一阶段的气泡形核会很困难,因而对第一种情况下再多加讨论。
实际除气主要是通过形成其他种类的气泡而除氢,例如前述的气泡浮游法除氢。
铝熔体中的氢向外来初始无氢的气泡迁移的除氢动力学过程可以分解为以下五个步骤:(1)通过对流和扩散,熔体中的氢迁移到铝熔体与气泡的气-液界面;(2)氢原子由溶解状态转变为吸附状态;(3)气-液界面吸附的氢原子彼此相互作用结合为氢分子;(4)氢分子从气-液界面脱附;(5)氢分子扩散进入气相,并随气泡上浮而逸出铝熔体。
第一阶段,主要是气体原子从铝熔体内部向熔体表面或气泡表面迁移。
惰性气体上浮过程中,与铝熔体产生相对运动。
假设气泡不动,那么铝熔体就相当于沿气泡表面流动,与Machlin模型完全相似,因此,传质系数可以表示为:式中:βm——气体原子在铝熔体中的传质系数,cm/s;D——气体原子在铝熔体中的扩散系数,cm2/s;v——惰性气泡上浮速度,cm/s;r——惰性气泡的半径,cm。
气泡上浮的速度可以用Stoke's公式计算:式中:υ——气泡上浮的速度,cm/s;r——气泡的半径,cm;ρM——铝合金熔体的密度,g/cm3;ρB——气泡的密度,g/cm3;η——铝熔体的动力黏度系数,N·s·cm-2。
传质速度为:式中:C m——铝合金熔体中气体含量;C ms——惰性气泡表面处熔体中气体含量。
不同时间和不同表面积的气体原子通量为:式中:A——惰性气泡表面积,cm2;t——除气时间,s。
可以看出,气体原子在铝熔体中向表面或惰性气泡扩散的通量与气体原子的扩散系数、惰性气泡上浮速度、熔体内部与表面的浓度差、表面面积和时间成正比,与惰性气泡的半径成反比。
第二阶段,主要包括步骤2、步骤3、步骤4,气体原子从溶解状态转变为吸附状态,并在吸附层中发生反应,生成气体分子从表面脱附。
根据Langmuir公式,传质系数可以表示为:传质速度可以表示为:式中:K L——Langmuir方程系数,当p e以托为单位时,K L=0.05833;ε——凝结系数;p e(i)——铝合金熔体上方或惰性气泡内气体 i的饱和蒸气压,N/mm2;p g(i)——在表面附近气体空间气体的蒸气分压,N/mm2;T ms——表面的铝熔体温度,℃;M i——气体的相对原子量。
不同时间和不同表面积的气体原子通量为:可以看出:气体原子挥发量与气体原子饱和蒸气压和实际蒸气压的差、表面面积和时间成正比,与铝熔体表面温度成反比。
第三阶段,气体分子扩散进入气体空间或气泡内,进行得很快,不会成为控制环节,不予考虑。
因此,应该整体考虑旋转喷吹除气净化铝熔体的过程,根据实际情况,选择合适的进气流量和旋转速度,合适的除气时间、静止时间以及除气温度等工艺参数,改善净化过程,提高净化效果。
2 国内外研究方法和研究深度广度方面存在的不足国际上铝液净化设备供货主要包括美国PYROTEK公司SNIF在线处理设备,法铝PECHINEY公司ALPUR在线处理设备,以及加拿大STAS公司ACD在线处理设备。
在SNIF处理方法中,惰性气体从高速旋转的转子和定子之间的缝隙喷出,形成极细的弥散气泡,使氢更有效地进入气泡中上浮排除。
ALPUR石墨转子喷头上有两种不同形式的气体通道,一种是径向排列的8条小通道(直径1 mm~3mm),小通道和转动的中空心轴相同,喷入惰性气体;另一种为锥形排列的8条大通道(直径8 mm~15 mm),通道中心与喷头转动轴同心,通道中心线与转动轴成45°,喷头上有4个叶片,在高速转动下搅拌金属液,使气泡细小而分布均匀,提高净化效果。
STAS公司生产的ACD在线处理是在一段流槽内进行,该流槽与铸造用流槽类似,叶轮安装在转轴上,除气时叶轮下降到流槽内,叶轮通过挡板隔离,挡板控制熔体流量,在流槽中完成除气处理[2]。
在线除气净化技术在除气机制和动力学条件研究较多,但是在除气净化设备的实用性研究方面较薄弱:(1)在线除气设备的整体能耗较大,惰性净化气体通入参数研究较少,通气方式以及参数未有优化,惰性气体在净化过程中未得到充分利用;(2)除气设备的石墨转子、加热保护装置以及内衬材料寿命不稳定,在高温以及铝液侵蚀的恶劣工况条件下,损耗件的寿命无法估计预测,导致生产过程中无法预知的停工;(3)除气设备中熔体冷却后需清理,即冷却至较低温后清理,但是随着温度降低,残存铝熔体和残渣凝固在一起,造成清理难度增大,这时要通过施以较大的外力进行剥离。
尤其当需要变换合金时,由于清理时间长,且不彻底,一方面会造成工作效率低,同时会造成累计冶金缺陷。