转底炉工艺与熔融还原技术开发
国内外转底炉的发展趋势及我国发展转底炉技术的建议

一、国内外转底炉技术的发展过程简介
1、转底炉直接还原工艺简介
转底炉炼铁工艺是非高炉炼铁工艺的一种,从1978年加拿大国际镍集团 (Inco,Ltd)建成第一座转底炉以来,已有近30年的历史,它从美国发源ห้องสมุดไป่ตู้先在日 本推广、后在中国得到发展。
转底炉法以其原料适应性强和操作工艺的灵活性等优点,引起冶金界的高度重视。 但由于原料加工方法条件和对产品质量要求的不同,转底炉直接还原炼铁分为 Inmetco法、DRYIRON法, FASTMET法和ITKM3等不同工艺路线。
国内外转底炉的发展趋势及 我国发展转底炉技术的建议
周渝生 齐渊洪 严定鎏 洪益成
钢铁研究总院先进钢铁流程及材料国家重点实验室 钢研晟华工程技术有限公司 20141106
目录
一、国内外转底炉技术的发展过程简介 二、国内外转底炉技术的发展趋势 三、我国发展转底炉技术的背景 四、对我国发展转底炉技术的建议
项目
单位
原料 铁精矿粉 还原煤 皂土 有机粘结剂 小计 能源 电 天然气 氮气 水 小计 其他 消耗品 维修与备件
kg kg kg kg
kwh m3(STP) m3(STP) t
美元 美元
消耗量 单位
1335 410 5 5
65 60 10 0.30
转底炉工艺技术存在的问题与发展建议

( 1 . T e c h n o l o g y Ce n t r e o f A n g a n g S t e e l C o . ,L t d .,An s h a n 1 1 4 0 1 1 ,L i a o n i n g ;2 . S c i e n c e a n d T e c h n o l o g y De p a  ̄-
提 出 了发 展 转 底 炉 工 艺 技术 的 几 点建 议 。 关键词 转底炉 ; 冶金尘泥 ; 直接 还 原 文献标识码 : A 文章编号 : 1 6 7 1 — 3 8 1 8 ( 2 0 1 3 ) 0 2— 0 0 4 2—0 3 .
中图 分 类 号 : T F 7 0 2 . 9
d e s c r i be d i n t h e p a p e r ,a n d s o me p r o b l e ms d u r i n g p r o d u c t i o n p r o c e s s a r e s y s t e ma t i c a l l y i n t r o d u c e d a n d
o b j e c t i v e l y a n a l y z e d .At t h e e n d,s o me a d v i c e s f o r d e v e l o p me n t o f Ro t a r y He a r t h F u r n a c e a r e p r o p o s e d .
me n t o f A n g a n g S t e e l G r o u p,An s h a n 1 1 4 0 1 1,L i a o n i n g )
Abs t r a c t Th e c u r r e n t s t a t u s o f Ro t a r y He a r t h F ur n a c e d i r e c t r e d u c t i o n pr o c e s s a t h o me a n d a b o a r d i s
转底炉直接还原炼铁工艺的发展

转底炉直接还原炼铁工艺的发展2010-02-24 17:02:19 作者:phpcms来源:浏览次数:571 网友评论 0 条一、前言为了满足冶炼高纯净钢的要求, 炼钢生产对纯净铁资源的需求越来越大。
与此同时, 优质废钢与铁资源却日益短缺其价格不断升高, 对炼钢生产影响很大, 为此,各国冶金工作者开发了许多直接还原或熔融还原工艺来为炼钢生产提供质优价廉的纯净铁资源。
但由于技术、投资等方面的原因,真正具有市场竞争力、适合于工业应用的并不多见。
同时,钢铁厂每年生产的大量含铁废弃物也给环保带来很大的压力。
如何对其进行回收利用是困扰冶金行业的一个难题。
直接还原工艺中气基法虽然具有生产效率高,生产规模大,能耗低和容易操作等优点,但必须以一次能源---天然气为还原剂,因此该工艺只能在天然气资源丰富的国家得以发展。
而煤基法以煤作为还原剂,较好的解决了气基法的不足。
目前世界上很多国家都在开发煤基直接还原新技术,有些技术已经应用于工业生产。
其中,转底炉法以其原料适应性强和操作工艺的零活性等优点,引起冶金界的高度重视。
但由于原料条件和对产品质量要求的不同,转底炉直接还原炼铁又发展为FASTMET,ITKM3和DRYIRON等不同工艺路线。
二、FASTMET工艺早在50年代Midex的前身Ross公司就发明了转底炉含碳球团直接还原法。
1964~1966年进行了2t/h规模试验。
1974年Inco公司开始研究把转底炉用于处理电炉生产不锈钢产生的氧化物粉尘的方法,并建立了一座年处理2.5万吨废料的工厂。
经转底炉预还原的球团,通过运输罐热装入电炉。
1978年美国Inmetco在宾州埃尔伍德市建成一座年处理5.6万吨电炉钢厂粉尘能力的转底炉,回收锌及可用作电炉原料的含Cr,Ni的还原铁。
1982年Mid ex公司将转底炉法命名为FASTMET,用于煤基直接还原。
神户制钢收购Midex公司后,199 5年开始建设2.5t/h示范装置,经过两年半试验后,认为Fastmet技术成熟可靠,已达到商业水平化水平。
基于转底炉直接还原技术
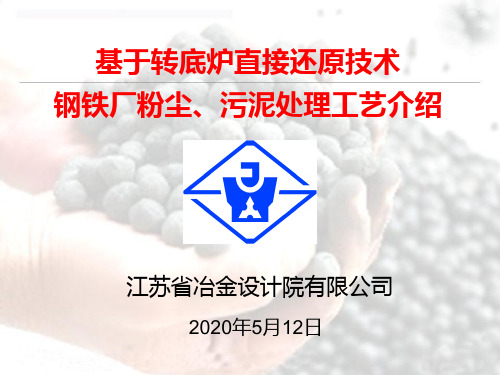
3.神雾集团 江苏省冶金设计院有限公司 转底炉技术的研究成果
3.1 蓄热式技术 3.2 研究试验数据 3.3 获取发明专利 3.4 已有工程业绩
4.钢铁厂含铁粉尘、污泥的处理方法简介
4.1 粉尘特性 4.2 处理方法 4.3 转底炉与回转窑比较 4.4 已有工程情况
5.沙钢利用粉尘、污泥年产30万吨转底炉直接还原工程简介
气基法(块矿或造块) 煤基法(块矿或造块) COREX(原料为块矿)
非高 炉炼 铁法
熔融还原法 (产品多为液态铁水)
FINEX(原料为粉矿) HIsmelt(原料为粉矿)
2019/3/11
4
返回目录
基于转底炉直接还原技术 钢铁厂粉尘、污泥处理工艺介绍 1.直接还原技术的兴起及分类
1.1 直接还原技术简述
2019/3/11
17
返回目录
基于转底炉直接还原技术 钢铁厂粉尘、污泥处理工艺介绍 2.转底炉技术目前发展情况
2.3 转底炉技术应用方向
目前神雾集团开发的转底炉直接还原技术,应用方向为: 熔融炼铁(转底炉-埋弧炉)
原料为精矿粉,产品为铁水
转底炉处理钢铁厂粉尘
转底炉处理海砂等钒钛矿 转底炉处理红土镍矿
机械化、自动化程度较高的转底炉法是目前比较先进、可 靠、经济的工艺。已成为煤基法直接还原铁工艺的首选。
2019/3/11
9
返回目录
基于转底炉直接还原技术 钢铁厂粉尘、污泥处理工艺介绍
2.转底炉技术目前发展情况
2.1 转底炉技术由来及发展
2.2 转底炉技术特点
2.3 转底炉技术应用方向 2.4 转底炉产品用途
◆ 2006年,由神雾集团设计及承建,我国第一条采用蓄热式转底炉工
透视ITmk3炼铁新工艺发展历程与技术特点

透视ITmk3炼铁新工艺发展历程与技术特点非高炉炼铁作为21世纪全世界钢铁行业的前沿技术,是未来技术发展的主要方向。
在此领域,国际冶金工作者不断进行着广泛、深入的研究和开发,形成了众多直接还原、熔融还原技术。
煤基转底炉法因其原料适应性强、操作灵活受到很多国家的重视。
日本神户制钢在过去几十年转底炉技术基础上提出了ITmk3(Ironmaking Technology Mark Three)工艺,使金属化球团在还原时能进一步熔化并实现渣铁分离,在短时间内生产出成分如生铁的高纯度粒铁产品。
该工艺突破了直接还原工艺范畴,彻底改变了直接还原产品对原料品位苛求的状况,而且还可以使用粉矿和非焦煤作原料,因而备受瞩目。
高炉-转炉工艺被称为第一代炼铁法,以气基梅德瑞克斯(MIDREX)法为代表的直接还原工艺被称为第二代炼铁法,而把煤基ITmk3工艺称作具有划时代意义的第三代炼铁技术。
目前首座ITmk3商业工厂已成功在美国投产。
1 ITmk3工艺发展过程ITmk3转底炉炼铁工艺由日本神户制钢开发。
最早的技术思想源于1994年,当时神户制钢对美国子公司梅德瑞克斯(Midrex)开发的快速融化(Fastmet/Fastmelt)法进行了一次评价试验,目的是考察适宜的反应温度和原料条件,却意外发现还未到铁的熔点时球团就熔化,而且形成的粒状小铁块与渣能干净利落地分离,所得粒铁纯度很高(铁含量为96%-97%)。
随后,神户制钢对此发现进行了一些基础实验,逐渐掌握了ITmk3的基本原理。
1996年神户制钢同Midrex子公司开始对ITmk3技术进行深入研究和改进,1999年在加古川厂区内建成了规模为年产能3000吨的中试厂,同年10月连续运转成功,到2000年12月完成了2次生产测试,其工艺设计得到实际验证。
随后ITmk3的发展转移到美国,2001年9月实施了梅萨比纳吉特(Mesabi Nugget)计划,于明尼苏达州合资建设一座年产能2.5万吨的示范工厂,成立梅萨比纳吉特公司,投资方除了神户制钢之外,还包括明尼苏达州政府、北美最大矿山公司克利夫兰·克利夫斯公司和美国第二大电炉制造厂钢动态公司(SDI),此外还得到了美国能源部(DOE)的资助,项目总投资达到2600万美元。
转底炉
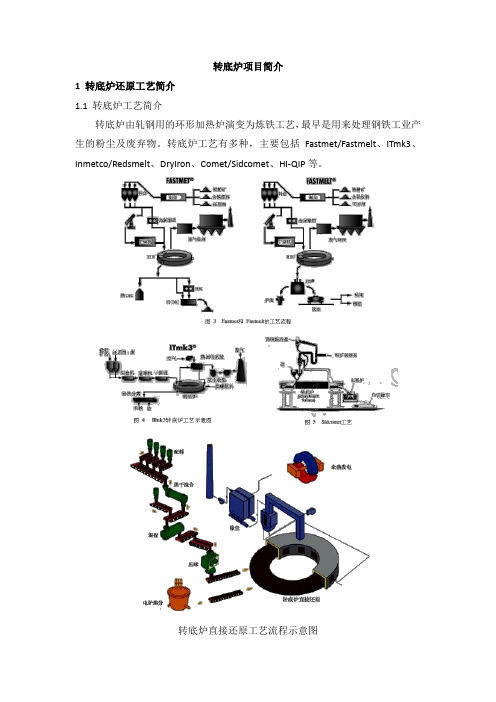
转底炉项目简介1 转底炉还原工艺简介1.1 转底炉工艺简介转底炉由轧钢用的环形加热炉演变为炼铁工艺,最早是用来处理钢铁工业产生的粉尘及废弃物。
转底炉工艺有多种,主要包括Fastmet/Fastmelt、ITmk3、Inmetco/Redsmelt、DryIron、Comet/Sidcomet、HI-QIP等。
转底炉直接还原工艺流程示意图1.2 转底炉工艺与其它相似工艺比较转底炉是煤基直接还原工艺中的核心设备之一,煤基直接还原工艺主要包括回转窑法(如SL-RN法)和转底炉法(如COMET法)。
而煤基直接还原工艺和气基直接还原工艺都是直接还原工艺,以铁产品为例直接还原工艺的产品为海绵铁(又称直接还原铁—DRI即Direct Reduced Iron)。
直接还原和熔融还原是两种主要的非高炉炼铁思路。
当转底炉的原料加入含碳球团时,其产品为金属化球团,可供电炉使用,也作为高炉的原料。
而链篦机—回转窑—环冷机(链回环)生产出来的产品是氧化球团,是为高炉炼铁提供的原料之一,称之为球团矿,而高炉炼铁的含铁原料还包括天然块矿、烧结矿。
转底炉直接还原技术采用含碳球团作原料,反应速度快,同时符合中国以煤为主要能源的特点。
以直接还原技术用于钒钛磁铁矿为例,转底炉技术相比隧道窑、回转窑工艺,以ITmk3为代表的转底炉工艺的优点主要是:○1还原原料在预热和还原过程中始终处于静止状态下随炉底一起进行,所以对生球强度要求不高;○2较高的还原温度(1350℃或更高)、反应快、效率高。
反应时间可在10-50min范围,可与矿热电炉熔炼容易实现同步热装;○3可调整喷入炉内燃料(可以是煤粉、煤气或油)和风量,能准确控制炉膛温度和炉内气氛;○4过程能耗低,回转窑法折算成每吨海绵铁的煤耗通常大于800kg,而转底炉法为600kg;○5从工艺角度来看,ITmk3技术流程简单,投资成本低,产品价格低,铁矿石原料及还原剂选择灵活。
另外,据马鞍山钢铁设计研究总院秦廷许的研究:转底炉-电炉炼铁流程与高炉传统炼铁流程比较,虽在铁精矿消耗量、还原剂和燃料的能源消耗量上相差不大,但吨铁成本低约10%;基建投资省22%左右;全流程电耗低48.6%。
熔融还原炼铁法开发现状

冶炼世界金属导报/2002年/11月/12日/第002版/熔融还原炼铁法开发现状廖建国结合日本钢铁工业未来发展的趋势,介绍了DIOS法研究概况。
熔融还原炉的特点是它能和其它直接还原法相结合构成Duplex-DIOS设备,扩大了熔融还原技术的应用。
本文简要介绍了由DIOS-SRF和转底炉组合的Duplex-DIOS的特征,同时还介绍了H is-melt、AusIron、ROM ELT、AISI法、CCF和CleanSMelt等其它几种已出现的熔融还原技术。
与其它熔融还原技术相比,DIOS更突出开发和技术应用的力度。
本文还介绍了COREX的现状。
COREX法是最早的熔融还原炼铁法,其它的熔融还原法都是在此基础上开发的。
1、前言目前,占世界粗钢产量60%以上的生铁是采用高炉法生产的。
高炉法已有数百年的历史,经过长时间的技术改造,最近出现了一座高炉日产1万t以上铁水的记录,因此高炉法已成为能长时间稳定大量生产的非常成熟的炼铁工艺。
但是,根据炼铁原理,装入高炉的各种原料必须是块状的,在矿山现场开采的粉状铁矿石不能直接入炉使用,需经预处理制成烧结矿或球团矿后才能入炉。
另外,煤必须用焦炉进行干馏制成所谓的冶金焦,因此仅占世界煤储量10%左右的炼焦煤必须和数十种煤进行配合使用。
由此可知,高炉法除了高炉本身外,还要有用于原料预处理的烧结机或球团生产设备和焦炉。
除这些附属设备外,还需要有热风炉来预热供给高炉的空气。
而且,在这些预处理设备中,一旦铁矿石或煤被加热到1200~1400 左右后,为使原料的粒度一致,需将它们冷却至常温。
虽然已采取了各种节能措施,但从总体上来说高炉法并不是一种能效高的炼铁法。
高炉是一座大型设备。
一座年产300万t 以上铁水的高炉,其高度大约100m,内容积达5000m3左右。
因此,高炉设备的更新需要巨大的费用(一座日产1万t级高炉的更新需要数百亿日元,与之配套焦炉的更新费用也基本相同)。
另外,全世界对高炉法所不可缺少的焦炉、烧结机和球团生产设备的环保措施提出了非常严格的要求,而且由于担心炼焦煤资源的短缺,因此围绕高炉法的生产环境日益严峻。
神雾的最新的转底炉直接还原技术国际领先

神雾的最新的转底炉直接还原技术国际领先神雾集团的核心节能与大气雾霾治理技术创新专利成果“蓄热式转底炉直接还原技术及成套工程化装备”,可处理各种低品位难选矿、复合共伴生矿、低品位红土镍矿、钢铁厂粉尘、有色行业冶金渣等劣质含铁资源。
该技术在高效提取复杂原矿中铁资源的同时,还能够实现对Ni、Ti、V、K、Na、Pb、Zn等元素的协同提取和高值化利用。
该项技术摒弃传统高炉烧结、焦化等高能耗、高污染工序的弊端,对原料的适应性广,只采用普通煤炭资源,就能节能、环保、高效、经济的实现劣质含铁矿物的高效清洁冶炼。
从目前我国铁矿资源来看,普遍存在含铁品位低、含铁矿物粒度细、矿物组成复杂的特点,劣质含铁资源占国内铁矿石储量的97%以上。
此外,现有钢铁厂大量的含铁粉尘、有色行业每年产生的上亿吨冶金废渣的综合开发利用也已迫在眉睫。
为满足高炉炼铁对优质铁矿石资源的刚性需求,国内钢铁企业长期从国外进口优质铁矿石,在进口铁矿石价格谈判上十分被动,这使得积极开发国内现存的大量低品位劣质含铁资源意义重大。
神雾蓄热式转底炉直接还原技术处理劣质含铁资源和冶金固废的技术指标先进:低品位难选矿金属化球团磨矿磁选铁粉品位大于90%,铁回收率大于85%;劣质含铁资源熔分铁回收率大于95%;红土镍矿金属化球团熔分可获得高镍铁,镍回收率大于95%。
神雾技术的工艺能耗较低,以沙钢含锌粉尘的转底炉处理工艺为例,单位产品的投资额相比国外转底炉降低约60%以上,单位产品能耗为209.3kgce,比回转窑工艺节能25%,比普通转底炉工艺节能16%,二氧化碳排放下降15%以上,作业率超过90%。
沙钢30万吨转底炉项目年新增产值3.52亿元、利润1.14亿元,投资回收期1.84年(不含建设期),项目具有较好的经济效益。
据不完全统计,我国每年约产生1800万吨含锌粉尘,如全部采用神雾转底炉直接还原冶炼技术进行处理,可生产直接还原铁球团1100万吨,解决6000多人就业,每年新增产值180亿左右,未来随着含锌粉尘量的不断提高,转底炉处理含锌粉尘将具有更加广阔的市场前景。
利用转底炉直接还原与矿热电炉熔融还原处理铜渣的方法与流程

利用转底炉直接还原与矿热电炉熔融还原处理铜渣的方法与流程技术特征:1.一种利用转底炉直接还原与矿热电炉熔融还原处理铜渣的方法,其特征在于,包括以下步骤:1)原料处理:将铜渣、硅石粉、还原剂与粘结剂经过配料、混合后,再经过压球工艺制备成铜渣含碳球团,将铜渣含碳球团烘干待用;2)转底炉还原与球团焦化增强:将步骤1)所得铜渣含碳球团送入转底炉进行还原,得到氧化锌粉、金属化球团;3)硅铁冶炼:将步骤2)转底炉排出的高温金属化球团直接送入矿热电炉冶炼,得到硅铁合金与炉渣。
2.如权利要求1所述的利用转底炉直接还原与矿热电炉熔融还原处理铜渣的方法,其特征在于:所述步骤1)中,铜渣为火法炼铜排出的炉渣经过缓冷、细磨浮选回收铜之后的尾矿,含tfe:30%~50%,zn:1%~3%、sio2:30%~40%,粒度-325目占比大于80%。
3.如权利要求2所述的利用转底炉直接还原与矿热电炉熔融还原处理铜渣的方法,其特征在于:所述步骤1)中,硅石粉含sio2大于97%,粒度组成为:3mm~2mm占13%~15%、2mm~1mm占40%~50%、1mm以下占35%~45%。
4.如权利要求3所述的利用转底炉直接还原与矿热电炉熔融还原处理铜渣的方法,其特征在于:所述步骤1)中,还原剂为炼焦用煤,其粒度为-3mm占比100%,粘结指数大于90。
5.如权利要求4所述的利用转底炉直接还原与矿热电炉熔融还原处理铜渣的方法,其特征在于:所述步骤1)中,铜渣、硅石粉、还原剂的质量配比为100:(270~290):(240~260),铜渣烘干后水分小于2%。
6.如权利要求1所述的利用转底炉直接还原与矿热电炉熔融还原处理铜渣的方法,其特征在于:所述步骤2)中,转底炉内的还原温度为1150℃~1330℃,还原时间为25min~40min,所得氧化锌粉的锌含量大于60%。
7.如权利要求6所述的利用转底炉直接还原与矿热电炉熔融还原处理铜渣的方法,其特征在于:所述步骤2)中,转底炉排出的金属化球团抗压强度达到2500n~2800n/个,金属化率大于85%。
转底炉
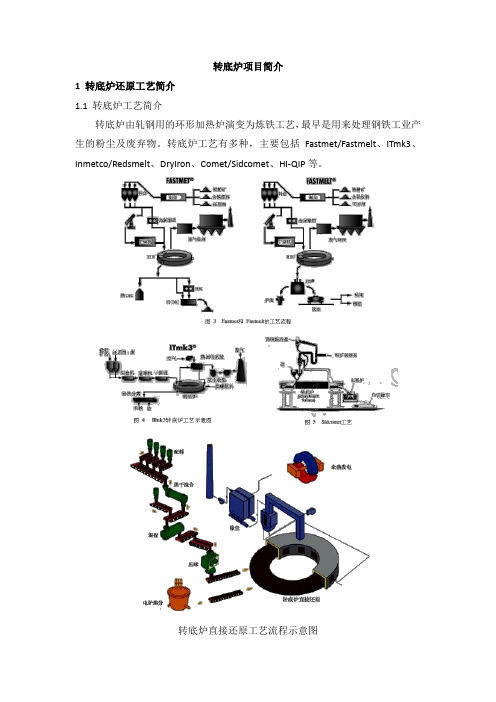
转底炉项目简介1 转底炉还原工艺简介1.1 转底炉工艺简介转底炉由轧钢用的环形加热炉演变为炼铁工艺,最早是用来处理钢铁工业产生的粉尘及废弃物。
转底炉工艺有多种,主要包括Fastmet/Fastmelt、ITmk3、Inmetco/Redsmelt、DryIron、Comet/Sidcomet、HI-QIP等。
转底炉直接还原工艺流程示意图1.2 转底炉工艺与其它相似工艺比较转底炉是煤基直接还原工艺中的核心设备之一,煤基直接还原工艺主要包括回转窑法(如SL-RN法)和转底炉法(如COMET法)。
而煤基直接还原工艺和气基直接还原工艺都是直接还原工艺,以铁产品为例直接还原工艺的产品为海绵铁(又称直接还原铁—DRI即Direct Reduced Iron)。
直接还原和熔融还原是两种主要的非高炉炼铁思路。
当转底炉的原料加入含碳球团时,其产品为金属化球团,可供电炉使用,也作为高炉的原料。
而链篦机—回转窑—环冷机(链回环)生产出来的产品是氧化球团,是为高炉炼铁提供的原料之一,称之为球团矿,而高炉炼铁的含铁原料还包括天然块矿、烧结矿。
转底炉直接还原技术采用含碳球团作原料,反应速度快,同时符合中国以煤为主要能源的特点。
以直接还原技术用于钒钛磁铁矿为例,转底炉技术相比隧道窑、回转窑工艺,以ITmk3为代表的转底炉工艺的优点主要是:○1还原原料在预热和还原过程中始终处于静止状态下随炉底一起进行,所以对生球强度要求不高;○2较高的还原温度(1350℃或更高)、反应快、效率高。
反应时间可在10-50min范围,可与矿热电炉熔炼容易实现同步热装;○3可调整喷入炉内燃料(可以是煤粉、煤气或油)和风量,能准确控制炉膛温度和炉内气氛;○4过程能耗低,回转窑法折算成每吨海绵铁的煤耗通常大于800kg,而转底炉法为600kg;○5从工艺角度来看,ITmk3技术流程简单,投资成本低,产品价格低,铁矿石原料及还原剂选择灵活。
另外,据马鞍山钢铁设计研究总院秦廷许的研究:转底炉-电炉炼铁流程与高炉传统炼铁流程比较,虽在铁精矿消耗量、还原剂和燃料的能源消耗量上相差不大,但吨铁成本低约10%;基建投资省22%左右;全流程电耗低48.6%。
转体炉工艺
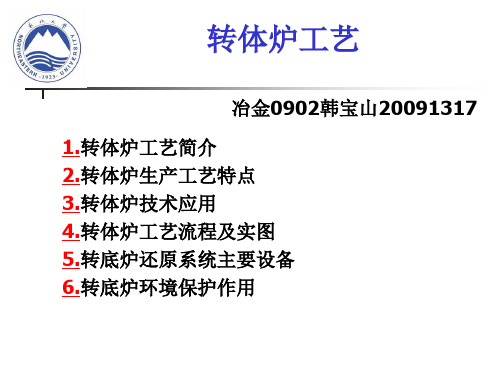
熔融还 MFe % 金属 化率 % SO2 % 6.0 6.54 16.62 C %
产品
77.90
68.21
87.56
10.18
1.85
煤炭灰分4%
煤炭灰分12.5%
转底炉应用之二
钢铁厂粉尘颗粒纤细,容易还原,产品金属化率较高
高效脱除钢铁厂粉尘中的Zn,并且可以将Zn回收
可将TiO2在炉渣中富余 V进入铁相→再提V 铁用于炼钢
实现Fe、V、Ti综合分离和利用
4.转体炉工艺流程及实图
5.转底炉还原系统主要设备
1.转底炉 作用:转底炉生产工艺核心设备,用于金属化球团的还原生成 主要构成:驱动部、炉床、上下轨道梁、燃烧系统 2.振动布料机 作用:混合生球布料,将生球均匀的布置在转底炉炉床上 主要构成:振源(电机、柔性联轴器、激振器)、箱体、弹簧、导料板 3.螺旋排料机 作用:成品金属化球团矿的热态排料 主要构成:电机减速机、传动链系统、前后轴承座、主轴装配(含螺旋 片)、水冷系统 4.筒式冷却机 作用:热态成品球的冷却 构成:驱动部、筒体、托辊、齿轮
名称 钢铁厂粉尘 金属化球团 TFe % 45.80 60.10 52.83 MFe % Zn % 0.89 0.01 SiO2 % 3.53 8.00 CaO % 16.80 23.30
1250下℃加热25分钟,金属化率88%
转底炉应用之三
将V、Ti磁铁矿中的铁精矿、钛精矿制成含炭球团,经转底炉预 还原,再用电炉或矿热炉进行终还原和熔分。
2.转体炉生产工艺特点
1)以煤粉作为还原剂, 仅用少量煤气, 对煤的质量要 求也没有回转窑法那么严格, 故有利于广泛应用。 2)主要设备为环形转底炉,与回转窑相比,该工艺设备 较简单、投资省、能耗较低。 3) 对炉料的强度要求不高。因为料层很薄炉料既不 受压且随炉底一起转动,炉料与炉底之间没有相对运动,可 用含碳生球团.(10~20min) ,操作容易。 4)转底炉工艺可直接使用含铁废粉料(或粉矿)和 粉煤, 在矿石和能源上具有很好的适应性和经济性。金属 化率可达80%以上。
神雾转底炉直接还原炼铁技术介绍

蓄热式转底炉示意图
蓄热式烧嘴
烟道
布料器
炉底
炉底支撑机构
炉底传动机构
第十三页,共67页。
出料螺旋
国外转底炉存在的主要问题
加热用燃料气必须采用
高热值燃料(天然气、 焦炉煤气等)
产能受到限制
成品的金属化率较低
台湾中钢
第十四页,共67页。
神雾蓄热式转底炉的优势 (对比国外正在运行的转底炉)
神雾公司的煤基转底炉直接还原工艺采用了神雾自主创 新的先进的蓄热式燃烧技术,因此:
第四十一页,共67页。
四、神雾直接还原炼铁工厂鸟瞰图
第四十二页,共67页。
沙钢30万吨/年含锌.含铁粉尘处理 生产线签约仪式
第四十三页,共67页。
上料矿槽
流程布置示意图
转底炉室干燥机室
烟囱
高压压球机室
配料室成品料仓
热布压袋余块烟收润热气尘磨锅换处室热炉理降器尘室室
第四十四页,共67页。
沙钢固废处理厂俯瞰
第六十四页,共67页。
荣程钢铁80万吨/年煤基转底炉 直接还原炼铁项目
第六十五页,共67页。
天津荣程钢铁公司直接还原转底炉
用途:铁精矿直接还原 生产能力:800000 TPY
外径:65 m
第六十六页,共67页。
北京神雾实验室直接还原转底炉
用途:各种含铁矿直接还原试验 外径:11 m
第六十七页,共67页。
上料成矿槽品料上仓成上料上料通品料通廊通廊通(廊(干(湿廊干)))
转底炉厂房 配料配室料室
烘干厂房
压球机室 烘干机润室磨室 生球上料通廊
湿料返回通廊
第四十五页,共67页。
转底炉
烘配磨干料煤室润造室室磨球机室 转运站 料链熔场篦分机室
- 1、下载文档前请自行甄别文档内容的完整性,平台不提供额外的编辑、内容补充、找答案等附加服务。
- 2、"仅部分预览"的文档,不可在线预览部分如存在完整性等问题,可反馈申请退款(可完整预览的文档不适用该条件!)。
- 3、如文档侵犯您的权益,请联系客服反馈,我们会尽快为您处理(人工客服工作时间:9:00-18:30)。
1 转底炉工艺概述
1.1 前言
转底炉用于生产直接还原铁不过约30年的历史,其设备和结构原本脱胎于轧钢用的环形加热炉,其最初目的就是用于处理钢铁厂生产过程中产生的含铁和其他金属的粉尘和废弃物,实践证明其环保功能和价值甚至超过了金属回收本身。
随着规模的扩大,也逐渐形成为一种炼铁新工艺,进入煤基直接还原法的先进行列,但仍处在初始阶段,目前最大的转底炉(美国动力钢公司)的规模年产铁不过50万吨,以铁精矿为原料,生产出的DRI经埋弧电炉熔分后为大电炉供应铁水。
其他分布在美国、日本等地的一些转底炉几乎都是处理粉尘,其规模一般年产能力20万吨左右,生产出的DRI金属化率70~85%不等,一般不用作电炉原料,其用途或作为高炉原料,或给转炉作冷却剂,或经埋弧电炉熔分后生产出铁水,给炼钢电炉热装。
转底炉的环保效益是与其工艺特点分不开的,主要特点是高温快速还原。
首先是把含金属氧化物的粉尘和废弃物还原成金属;其次是高温下许多有害元素和物质能够挥发或分解,能燃烧的用作燃料;第三是本身是封闭系统,微负压操作,过程中基本无排放,最终的固体产物和经过净化的烟气均符合环保要求,而且烟气余热得到充分利用。
因此转底炉在一些发达国家(如美国、日本)已列为处理所在地域冶金厂粉尘和废弃物的有效措施,并要求冶金企业无偿提供,并倒贴一定处理费用。
这些厂家因为国家环保要求深埋而要花费更高费用,所以也乐于如此。
1.2 发展状况
最早生产规模的转底炉处理冶金厂粉尘和废弃物的是美国INMETCO,由国际镍集团INCO.Ltd开发,该集团国际金属回收公司1978年在美国宾州Eillwood 城建成第一座转底炉,外径16.7米,炉底宽4.3米,主要是用来处理多种冶金厂含铁粉尘和废弃物,生产出的金属化率85~92%的金属化球团(DRI)进入埋弧电炉熔化,获得铁水和炉渣(作为副产品出售),与此同时还回收Zn、Ni、Cr
等金属。
已运行近30年,效益良好,成为美国中东部钢铁厂废弃物处理中心。
此外,美国MR&E公司开发的Dry-Iron转底炉工艺于1997年4月在田纳西州的Jackson建成一座转底炉,年处理粉尘能力为20万吨,产品金属化率达90%,脱锌率达95%,同时还可脱锑、钾、钠等元素。
日本神户制钢同美国Midrex公司共同开发的Fastmet转底炉当前主要是用于处理含铁粉尘和废弃物,现在正常生产的有神户加古川1座,新日铁4座(广田1座,君津2座,光1座),详见附表。
附表国外处理含铁粉尘和废弃物的转底炉RHF
1.3 处理流程
一般转底炉处理含金属粉尘和废弃物的流程包含以下几个系统:
(1)、以转底炉为中心的主体系统,包括炉体和转动机构,以及辅助设施。
(2)、热工系统,包括供热、加热、热能利用等。
(3)、烟气处理系统以及后续的各种有关金属回收系统。
(4)、原料贮运及上料系统。
(5)、产品及副产品处理系统。
1.4 结语
转底炉的特点是高温还原过程,操作系统处于封闭微负压状态,有利于在回收有用金属的同时,保持环境友好,其经济效益与环保效益相得益彰。
国外已有近30年的成功经验,中国作为世界钢铁大国,有效解决粉尘和废弃物的积压已提到议事日程。
如何借鉴国外经验,结合我国实际进行转底炉工艺研究开发是目前钢铁工业的一个比较迫切需要解决的问题。
北京科技大学有关科技人员对此已进行多年探索,积累了相应的知识和经验,并在山西建成了我国第一条连续生产的工业化转底炉生产线。
该生产线在2006年~2007年连续生产了6个月,加工精矿粉9000多吨。
2 转底炉熔融还原技术开发。