转底炉直接还原炼铁工艺的发展
国内外转底炉的发展趋势及我国发展转底炉技术的建议

一、国内外转底炉技术的发展过程简介
1、转底炉直接还原工艺简介
转底炉炼铁工艺是非高炉炼铁工艺的一种,从1978年加拿大国际镍集团 (Inco,Ltd)建成第一座转底炉以来,已有近30年的历史,它从美国发源ห้องสมุดไป่ตู้先在日 本推广、后在中国得到发展。
转底炉法以其原料适应性强和操作工艺的灵活性等优点,引起冶金界的高度重视。 但由于原料加工方法条件和对产品质量要求的不同,转底炉直接还原炼铁分为 Inmetco法、DRYIRON法, FASTMET法和ITKM3等不同工艺路线。
国内外转底炉的发展趋势及 我国发展转底炉技术的建议
周渝生 齐渊洪 严定鎏 洪益成
钢铁研究总院先进钢铁流程及材料国家重点实验室 钢研晟华工程技术有限公司 20141106
目录
一、国内外转底炉技术的发展过程简介 二、国内外转底炉技术的发展趋势 三、我国发展转底炉技术的背景 四、对我国发展转底炉技术的建议
项目
单位
原料 铁精矿粉 还原煤 皂土 有机粘结剂 小计 能源 电 天然气 氮气 水 小计 其他 消耗品 维修与备件
kg kg kg kg
kwh m3(STP) m3(STP) t
美元 美元
消耗量 单位
1335 410 5 5
65 60 10 0.30
炼钢工艺发展的趋势
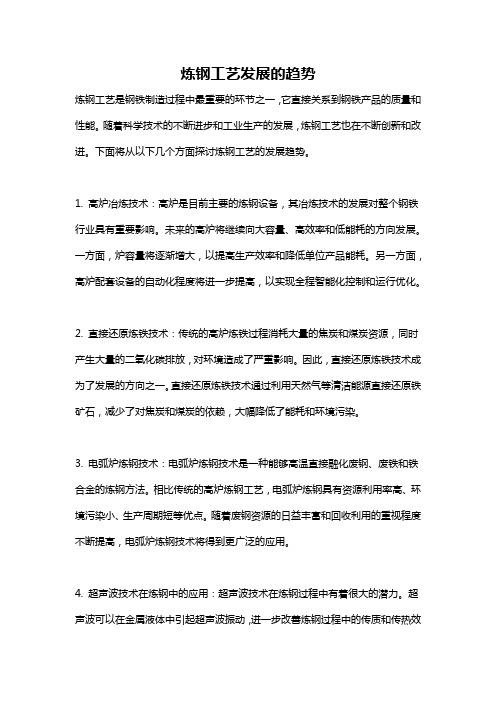
炼钢工艺发展的趋势炼钢工艺是钢铁制造过程中最重要的环节之一,它直接关系到钢铁产品的质量和性能。
随着科学技术的不断进步和工业生产的发展,炼钢工艺也在不断创新和改进。
下面将从以下几个方面探讨炼钢工艺的发展趋势。
1. 高炉冶炼技术:高炉是目前主要的炼钢设备,其冶炼技术的发展对整个钢铁行业具有重要影响。
未来的高炉将继续向大容量、高效率和低能耗的方向发展。
一方面,炉容量将逐渐增大,以提高生产效率和降低单位产品能耗。
另一方面,高炉配套设备的自动化程度将进一步提高,以实现全程智能化控制和运行优化。
2. 直接还原炼铁技术:传统的高炉炼铁过程消耗大量的焦炭和煤炭资源,同时产生大量的二氧化碳排放,对环境造成了严重影响。
因此,直接还原炼铁技术成为了发展的方向之一。
直接还原炼铁技术通过利用天然气等清洁能源直接还原铁矿石,减少了对焦炭和煤炭的依赖,大幅降低了能耗和环境污染。
3. 电弧炉炼钢技术:电弧炉炼钢技术是一种能够高温直接融化废钢、废铁和铁合金的炼钢方法。
相比传统的高炉炼钢工艺,电弧炉炼钢具有资源利用率高、环境污染小、生产周期短等优点。
随着废钢资源的日益丰富和回收利用的重视程度不断提高,电弧炉炼钢技术将得到更广泛的应用。
4. 超声波技术在炼钢中的应用:超声波技术在炼钢过程中有着很大的潜力。
超声波可以在金属液体中引起超声波振动,进一步改善炼钢过程中的传质和传热效果,提高钢的纯净度和均匀性。
此外,超声波还可以用于检测和监测钢铁产品中的缺陷和杂质,提高质量控制的准确性和效率。
5. 粉煤气化技术:粉煤气化技术是一种利用煤炭资源进行炼钢的新技术。
通过对煤炭进行气化,产生合成气,再利用合成气进行炼钢,既能够提高煤炭资源的利用率,又能够减少对传统能源的依赖和环境污染。
粉煤气化技术属于绿色环保型炼钢工艺,对于改善钢铁行业的能源结构和减少碳排放具有重要意义。
总体来说,炼钢工艺的发展趋势是朝着高效、环保、智能化和资源综合利用的方向发展。
转底炉工艺技术存在的问题与发展建议

( 1 . T e c h n o l o g y Ce n t r e o f A n g a n g S t e e l C o . ,L t d .,An s h a n 1 1 4 0 1 1 ,L i a o n i n g ;2 . S c i e n c e a n d T e c h n o l o g y De p a  ̄-
提 出 了发 展 转 底 炉 工 艺 技术 的 几 点建 议 。 关键词 转底炉 ; 冶金尘泥 ; 直接 还 原 文献标识码 : A 文章编号 : 1 6 7 1 — 3 8 1 8 ( 2 0 1 3 ) 0 2— 0 0 4 2—0 3 .
中图 分 类 号 : T F 7 0 2 . 9
d e s c r i be d i n t h e p a p e r ,a n d s o me p r o b l e ms d u r i n g p r o d u c t i o n p r o c e s s a r e s y s t e ma t i c a l l y i n t r o d u c e d a n d
o b j e c t i v e l y a n a l y z e d .At t h e e n d,s o me a d v i c e s f o r d e v e l o p me n t o f Ro t a r y He a r t h F u r n a c e a r e p r o p o s e d .
me n t o f A n g a n g S t e e l G r o u p,An s h a n 1 1 4 0 1 1,L i a o n i n g )
Abs t r a c t Th e c u r r e n t s t a t u s o f Ro t a r y He a r t h F ur n a c e d i r e c t r e d u c t i o n pr o c e s s a t h o me a n d a b o a r d i s
直接还原铁生产工艺及发展方向

直接还原铁(海绵铁)生产工艺及发展方向习惯上,我们把铁矿石在高炉中先还原冶炼成含碳高的生铁,而后在炼钢炉内氧化,降低含碳量并精炼成钢,这项传统工艺,称作间接炼钢方法;在低于矿石熔化温度下,通过固态还原,把铁矿石炼制成铁的工艺,称作直接炼铁(钢)法或者直接还原法,用这种方法生产出的铁也就称作直接还原铁(即DRI)。
由于这种铁保留了失氧时形成的大量微气孔,在显微镜下观察形似海绵,所以直接还原铁也称之为海绵铁。
一、直接还原铁(海绵铁)的用途直接还原铁是精铁粉在炉内经低温还原形式的低碳多孔状物质,其化学成分稳定,杂质含量少(碳、硅含量低),主要用作电炉炼钢的原料,也可作为转炉炼钢的冷却剂,如果经二次还原还可供粉末冶金用。
一次还原铁粉(海绵铁)的主要用途有:①作为粉末冶金制品的原料,耗用量约占铁粉总耗用量的60~80%;②作为电焊条的原料,在药皮中加入10~70%铁粉可改进焊条的焊接工艺并显著提高熔敷效率;③作为火焰切割的喷射剂,在切割钢制品时,向氧-乙炔焰中喷射铁粉,可改善切割性能,扩大切割钢种的范围,提高可切割厚度;④还可作为有机化学合成中的还原剂、复印机油墨载体等。
近年来由于钢铁产品朝小型轻量化、功能高级化、复合化方向发展,故钢材中非金属材料和有色金属使用比例增加,致使废钢质量不断下降。
废钢作为电炉钢原料,由于其来源不同,化学成分波动很大,而且很难掌握、控制,这给电炉炼钢作业带来了极大的困难。
如果用一定比例的直接还原铁(30~50%)作为稀释剂与废钢搭配不仅可增加钢材的均匀性,还可以改善和提高钢的物理性质,从而达到生产优质钢的目的。
因此,直接还原铁(海绵铁)不仅仅是优质废钢的替代物,还是生产优质钢材必不可少的高级原料(天津无缝钢管公司国外设计中就明确要求必须配50%的直接还原铁(海绵铁))。
根据国外报导,高功率电炉冶炼时,炉料搭配30~50%直接还原铁,生产率提高10~25%,作业率提高25~30%。
直接还原铁生产工艺的分析

直接还原铁生产工艺的分析世界上直接还原铁生产技术已经成熟, 技术发展极为迅速, 根据Midrex 公司预测, 2010年全世界直接还原铁产量将超过7300万t。
于高炉流程存在着生产成本过高和环境污染的两大难题, 炼铁工艺由高炉流程逐步向直接还原铁短流程过渡已成为定局。
当今的钢铁企业对这一革命性技术工艺越早开发越能占据主动; 不敢承担风险, 迟疑不前, 必将处于被动和落后的局面。
因此, 直接还原铁的开发不是“有所为”和“有所不为”的问题, 而是生产工艺的选择问题。
1 世界直接还原铁生产技术现状1.1 生产工艺发展态势由于某些国家天然气资源丰富, 直接还原铁生产技术在南美洲、南非和东南亚诸国的发展极为迅速,而印度则后来居上; 特别是委内瑞拉、墨西哥等国, 生产历史已超过20余年, 生产规模不断扩大, 直接还原铁产量已占本国钢铁产量的绝对份额; 而奥钢联、韩国合作开发的直接还原与熔融还原技术与日俱进; 浦项钢铁公司的直接还原铁生产大有代替高炉炼铁之势。
对这样的发展态势, 作为世界钢铁生产大国的中国, 我们绝不可掉以轻心。
1.2 世界直接还原铁主要生产工艺??? 世界直接还原铁生产工艺大致可分为两大类: 一种是气基竖炉生产工艺; 一种是煤基回转窑生产工艺。
前者生产量约占总产量的92%, 而后者约占总产量的8%。
在这两种生产技术的基础上, 又发展了熔融还原生产技术。
近年来, 将直接还原与熔融还原技术加以组合, 形成了COREX-Midrex联合流程, 颇受人们的关注。
直接还原铁主要生产工艺见表1。
??? 应该指出, 世界上Midrex法和HYL法应用的比较普遍, 各项技术经济指标亦趋稳定, 生产工艺成熟可靠。
特别是墨西哥的HYL法, 生产技术不断创新, 由于开发了“自重整”技术, 使建设费用减少了26% , 电炉的耗电降低了5%~6%。
印度由于缺乏天然气, 但精煤的资源丰富, 因此多采用煤基回转窑的生产方法。
透视ITmk3炼铁新工艺发展历程与技术特点

透视ITmk3炼铁新工艺发展历程与技术特点非高炉炼铁作为21世纪全世界钢铁行业的前沿技术,是未来技术发展的主要方向。
在此领域,国际冶金工作者不断进行着广泛、深入的研究和开发,形成了众多直接还原、熔融还原技术。
煤基转底炉法因其原料适应性强、操作灵活受到很多国家的重视。
日本神户制钢在过去几十年转底炉技术基础上提出了ITmk3(Ironmaking Technology Mark Three)工艺,使金属化球团在还原时能进一步熔化并实现渣铁分离,在短时间内生产出成分如生铁的高纯度粒铁产品。
该工艺突破了直接还原工艺范畴,彻底改变了直接还原产品对原料品位苛求的状况,而且还可以使用粉矿和非焦煤作原料,因而备受瞩目。
高炉-转炉工艺被称为第一代炼铁法,以气基梅德瑞克斯(MIDREX)法为代表的直接还原工艺被称为第二代炼铁法,而把煤基ITmk3工艺称作具有划时代意义的第三代炼铁技术。
目前首座ITmk3商业工厂已成功在美国投产。
1 ITmk3工艺发展过程ITmk3转底炉炼铁工艺由日本神户制钢开发。
最早的技术思想源于1994年,当时神户制钢对美国子公司梅德瑞克斯(Midrex)开发的快速融化(Fastmet/Fastmelt)法进行了一次评价试验,目的是考察适宜的反应温度和原料条件,却意外发现还未到铁的熔点时球团就熔化,而且形成的粒状小铁块与渣能干净利落地分离,所得粒铁纯度很高(铁含量为96%-97%)。
随后,神户制钢对此发现进行了一些基础实验,逐渐掌握了ITmk3的基本原理。
1996年神户制钢同Midrex子公司开始对ITmk3技术进行深入研究和改进,1999年在加古川厂区内建成了规模为年产能3000吨的中试厂,同年10月连续运转成功,到2000年12月完成了2次生产测试,其工艺设计得到实际验证。
随后ITmk3的发展转移到美国,2001年9月实施了梅萨比纳吉特(Mesabi Nugget)计划,于明尼苏达州合资建设一座年产能2.5万吨的示范工厂,成立梅萨比纳吉特公司,投资方除了神户制钢之外,还包括明尼苏达州政府、北美最大矿山公司克利夫兰·克利夫斯公司和美国第二大电炉制造厂钢动态公司(SDI),此外还得到了美国能源部(DOE)的资助,项目总投资达到2600万美元。
转底炉
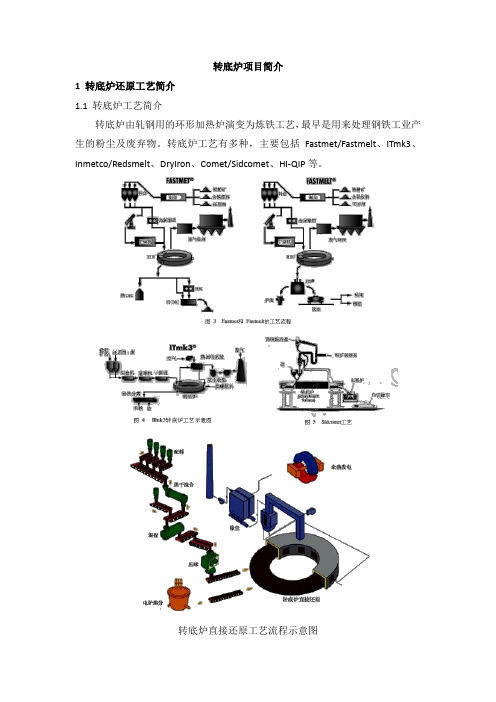
转底炉项目简介1 转底炉还原工艺简介1.1 转底炉工艺简介转底炉由轧钢用的环形加热炉演变为炼铁工艺,最早是用来处理钢铁工业产生的粉尘及废弃物。
转底炉工艺有多种,主要包括Fastmet/Fastmelt、ITmk3、Inmetco/Redsmelt、DryIron、Comet/Sidcomet、HI-QIP等。
转底炉直接还原工艺流程示意图1.2 转底炉工艺与其它相似工艺比较转底炉是煤基直接还原工艺中的核心设备之一,煤基直接还原工艺主要包括回转窑法(如SL-RN法)和转底炉法(如COMET法)。
而煤基直接还原工艺和气基直接还原工艺都是直接还原工艺,以铁产品为例直接还原工艺的产品为海绵铁(又称直接还原铁—DRI即Direct Reduced Iron)。
直接还原和熔融还原是两种主要的非高炉炼铁思路。
当转底炉的原料加入含碳球团时,其产品为金属化球团,可供电炉使用,也作为高炉的原料。
而链篦机—回转窑—环冷机(链回环)生产出来的产品是氧化球团,是为高炉炼铁提供的原料之一,称之为球团矿,而高炉炼铁的含铁原料还包括天然块矿、烧结矿。
转底炉直接还原技术采用含碳球团作原料,反应速度快,同时符合中国以煤为主要能源的特点。
以直接还原技术用于钒钛磁铁矿为例,转底炉技术相比隧道窑、回转窑工艺,以ITmk3为代表的转底炉工艺的优点主要是:○1还原原料在预热和还原过程中始终处于静止状态下随炉底一起进行,所以对生球强度要求不高;○2较高的还原温度(1350℃或更高)、反应快、效率高。
反应时间可在10-50min范围,可与矿热电炉熔炼容易实现同步热装;○3可调整喷入炉内燃料(可以是煤粉、煤气或油)和风量,能准确控制炉膛温度和炉内气氛;○4过程能耗低,回转窑法折算成每吨海绵铁的煤耗通常大于800kg,而转底炉法为600kg;○5从工艺角度来看,ITmk3技术流程简单,投资成本低,产品价格低,铁矿石原料及还原剂选择灵活。
另外,据马鞍山钢铁设计研究总院秦廷许的研究:转底炉-电炉炼铁流程与高炉传统炼铁流程比较,虽在铁精矿消耗量、还原剂和燃料的能源消耗量上相差不大,但吨铁成本低约10%;基建投资省22%左右;全流程电耗低48.6%。
直接还原铁生产工艺
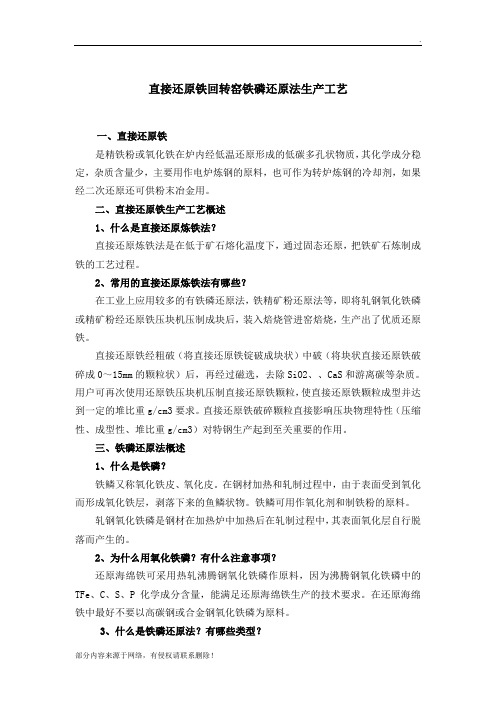
直接还原铁回转窑铁磷还原法生产工艺一、直接还原铁是精铁粉或氧化铁在炉内经低温还原形成的低碳多孔状物质,其化学成分稳定,杂质含量少,主要用作电炉炼钢的原料,也可作为转炉炼钢的冷却剂,如果经二次还原还可供粉末冶金用。
二、直接还原铁生产工艺概述1、什么是直接还原炼铁法?直接还原炼铁法是在低于矿石熔化温度下,通过固态还原,把铁矿石炼制成铁的工艺过程。
2、常用的直接还原炼铁法有哪些?在工业上应用较多的有铁磷还原法,铁精矿粉还原法等,即将轧钢氧化铁磷或精矿粉经还原铁压块机压制成块后,装入焙烧管进窑焙烧,生产出了优质还原铁。
直接还原铁经粗破(将直接还原铁锭破成块状)中破(将块状直接还原铁破碎成0~15mm的颗粒状)后,再经过磁选,去除SiO2、、CaS和游离碳等杂质。
用户可再次使用还原铁压块机压制直接还原铁颗粒,使直接还原铁颗粒成型并达到一定的堆比重g/cm3要求。
直接还原铁破碎颗粒直接影响压块物理特性(压缩性、成型性、堆比重g/cm3)对特钢生产起到至关重要的作用。
三、铁磷还原法概述1、什么是铁磷?铁鳞又称氧化铁皮、氧化皮。
在钢材加热和轧制过程中,由于表面受到氧化而形成氧化铁层,剥落下来的鱼鳞状物。
铁鳞可用作氧化剂和制铁粉的原料。
轧钢氧化铁磷是钢材在加热炉中加热后在轧制过程中,其表面氧化层自行脱落而产生的。
2、为什么用氧化铁磷?有什么注意事项?还原海绵铁可采用热轧沸腾钢氧化铁磷作原料,因为沸腾钢氧化铁磷中的TFe、C、S、P化学成分含量,能满足还原海绵铁生产的技术要求。
在还原海绵铁中最好不要以高碳钢或合金钢氧化铁磷为原料。
3、什么是铁磷还原法?有哪些类型?铁鳞还原法就是以铁鳞为原料的直接还原法生产工艺。
铁鳞还原法生产过程可分为粗还原与精还原。
在粗还原过程中,铁氧化物被还原,铁粉颗粒烧结与渗碳。
增高还原温度或延长保温时间皆有利于铁氧化物还原、铁粉颗粒烧结,但会生产部分渗碳。
鉴于在精还原过程中脱碳困难,在粗还原过程中,控制铁氧化物还原到未渗碳的程度是必要的。
直接还原炼铁的现状及发展趋势

气基还原 , 产 厂主要集 中在南 美、 东 、 生 中 东 南 亚 等地 区 , 委 内瑞 拉 、 如 墨西 哥 、 非 、 南 印度
维普资讯
攀 钢 技 术 似烧 结 的环冷 机 , 近 年才 开 发 的还 原设 备 。 是
2 12 燃 料 . .
・5 ・
Arx是 M irx 的 一 种 改 进 形 式 , 取 e de 它
目前 使 用 最 广 泛 的 是 天 然 气 , 用 天 然 使
消 了天 然 气 的 重 整 炉 , 天 然 气 部 分 氧 化 后 将 入炉 , 炉 内 热 海 绵 铁 催 化 裂 解 【 。HYL一 靠 3 J Ⅲ也 在 尝试 采 取 这 种 工 艺 , 消 重 整 炉 【J 取 4。
之一 。
生产 工 艺 主 要 集 中 在 竖 炉 气 基 还 原 的
Mirx HYLⅢ 、 de 、 HYLI三 种 工 艺 , 原 块 状 还
矿 石 , 图 2所 示 ; 如 回转 窑 S / R 工 艺 占有 L N
一
1 世 界 直 接 还 原 铁 生 产 简 况
定 比例 ; 外 , oe 另 C rx工 艺 近 年发 展 迅 速 。
世 界 直接 还 原 铁 产 量 增 长 迅 速 , 2 0 到 05 年 , 接 还 原 铁 产 量 将 达 到 70 0万 t1 】如 直 0 _l , 2
图 1所 示 。
。
年 份
’
0 o
o 0
图 2 直 接 还 原 炼 铁 工 艺 的种 类
一 。
图 1 世 界 直 接 还 原 铁 年 产 量
典 型 的 竖炉 还 原 工 艺 有 米 德 雷 克 斯 直 接 还 原公 司 ( 户 钢铁 公 司 子公 司 ) Mir ( 神—I ( 4 、 e l 图 ) Arx l
转底炉的发展及其功能

转底炉的发展及其功能佘雪峰;孔令坛【摘要】Experiment or industrial practices on disposal of dust generated by iron and steel plant, production of sponge iron and comprehensive utilization of compound mineral were introduced briefly and the development of Rotary Hearth Furnace(RHF) was comprehensively discussed in domestic and overseas. American, Japan, China and Korea had disposed the dust and sludge generated by iron and steel plant. Hazardous elements were removed from the dust and the zinc was recycled for improving the environment. At the same time metallized pellets and hot briquette iron(HBI) were produced by RHF used as raw materials of BF. In addition, DRI produced by RHF was used as raw materials of steelmaking which can be simplified the steelmaking process. Many compound iron ore containing vanadium, titanium, boron, magnesium, rare earth were investigated in lab and industry.%在对国内外转底炉的发展进行综合论述的同时,简要介绍了转底炉在处理钢铁厂粉尘,生产海绵铁,以及复合矿综合利用方面的实验研究和工业生产实践。
我国煤基直接还原炼铁工艺发展
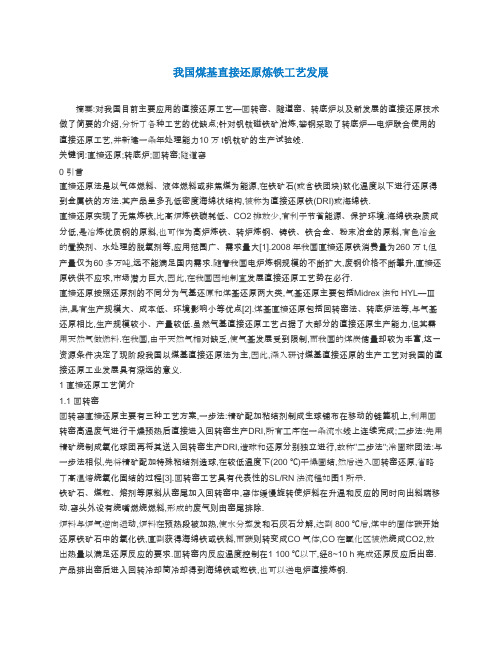
我国煤基直接还原炼铁工艺发展摘要:对我国目前主要应用的直接还原工艺—回转窑、隧道窑、转底炉以及新发展的直接还原技术做了简要的介绍,分析了各种工艺的优缺点;针对钒钛磁铁矿冶炼,攀钢采取了转底炉—电炉联合使用的直接还原工艺,并新建一条年处理能力10万t钒钛矿的生产试验线.关键词:直接还原;转底炉;回转窑;隧道窑0 引言直接还原法是以气体燃料、液体燃料或非焦煤为能源,在铁矿石(或含铁团块)软化温度以下进行还原得到金属铁的方法.其产品呈多孔低密度海绵状结构,被称为直接还原铁(DRI)或海绵铁.直接还原实现了无焦炼铁,比高炉炼铁碳耗低、CO2排放少,有利于节省能源、保护环境.海绵铁杂质成分低,是冶炼优质钢的原料,也可作为高炉炼铁、转炉炼钢、铸铁、铁合金、粉末冶金的原料,有色冶金的置换剂、水处理的脱氧剂等,应用范围广、需求量大[1].2008年我国直接还原铁消费量为260 万t,但产量仅为60多万吨,远不能满足国内需求.随着我国电炉炼钢规模的不断扩大,废钢价格不断攀升,直接还原铁供不应求,市场潜力巨大,因此,在我国因地制宜发展直接还原工艺势在必行.直接还原按照还原剂的不同分为气基还原和煤基还原两大类,气基还原主要包括Midrex法和HYL—Ⅲ法,具有生产规模大、成本低、环境影响小等优点[2].煤基直接还原包括回转窑法、转底炉法等,与气基还原相比,生产规模较小、产量较低.虽然气基直接还原工艺占据了大部分的直接还原生产能力,但其需用天然气做燃料.在我国,由于天然气相对缺乏,使气基发展受到限制,而我国的煤炭储量却较为丰富,这一资源条件决定了现阶段我国以煤基直接还原法为主,因此,深入研讨煤基直接还原的生产工艺对我国的直接还原工业发展具有深远的意义.1 直接还原工艺简介1.1 回转窑回转窑直接还原主要有三种工艺方案,一步法:精矿配加粘结剂制成生球铺布在移动的链篦机上,利用回转窑高温废气进行干燥预热后直接进入回转窑生产DRI,所有工序在一条流水线上连续完成;二步法:先用精矿烧制成氧化球团再将其送入回转窑生产DRI,造球和还原分别独立进行,故称"二步法";冷固球团法:与一步法相似,先将精矿配加特殊粘结剂造球,在较低温度下(200 ℃)干燥固结,然后送入回转窑还原,省略了高温焙烧氧化固结的过程[3].回转窑工艺具有代表性的SL/RN法流程如图1所示.铁矿石、煤粒、熔剂等原料从窑尾加入回转窑中,窑体缓慢旋转使炉料在升温和反应的同时向出料端移动.窑头外设有烧嘴燃烧燃料,形成的废气则由窑尾排除.炉料与炉气逆向运动,炉料在预热段被加热,使水分蒸发和石灰石分解,达到800 ℃后,煤中的固体碳开始还原铁矿石中的氧化铁,直到获得海绵铁或铁料,而碳则转变成CO气体,CO在氧化区被燃烧成CO2,放出热量以满足还原反应的要求.回转窑内反应温度控制在1 100 ℃以下,经8~10 h完成还原反应后出窑.产品排出窑后进入回转冷却筒冷却得到海绵铁或粒铁,也可以送电炉直接炼钢.与高炉工艺相比较,回转窑工艺设备简单,投资少,适用于地方钢铁工业,弥补了高炉—转炉工艺的不足,此外,回转窑还适用于复合矿冶炼,冶金灰尘及各种工业废渣的回收利用,减少环境污染,降低了钢铁生产能耗.同时,回转窑工艺也存在一些缺点,包括窑内结圈、还原温度低(1 100 ℃以下)、流程长、对块矿或球团矿冷强度要求高、要求使用低硫煤等[4].我国山东鲁中矿山公司通过采取提高冷固烧结球团的冷热态强度、加强还原煤的选择和管理、优化回转窑的送风、抛煤、控温温度等措施,预防并降低回转窑结圈,取得了较好的收效.图1 SL/RN法工艺流程1.2 隧道窑隧道窑工艺即将精矿粉、煤粉、石灰石粉,按照一定的比例和装料方法,分别装入还原罐中,然后把罐放在罐车上,推入条形隧道窑中或把罐直接放到环形轮窑中,料罐经预热到1 150 ℃加热焙烧和冷却之后,得到直接还原铁.目前江苏永钢集团拥有两条260 m长煤气隧道窑,为亚洲最长隧道窑.隧道窑生产海绵铁工艺流程如图2所示.图2 隧道窑生产海绵铁工艺流程煤基隧道窑直接还原工艺具有技术成熟、作简单的特点,可因地制宜采用此工艺,利用当地小型分散的铁矿及煤矿资源优势,发展直接还原铁生产,为电炉提供优质原料.但是,总体上讲,我国隧道窑直接还原中存在生产规模较小、能耗高、污染严重、缺乏稳定的原料供应渠道等问题[5],所以,提高机械化程度、改变原料入炉方式、改进燃料及其燃烧、增设余热回收等成为各厂家不断努力改进工艺的方向.我国已建成或正在建设的隧道窑有100多座,约70多个单位规划建设产能5~30 万t/a的隧道窑直接还原铁厂,在不断总结实践经验的基础上,改进现行工艺,开发出诸如大型隧道窑直接还原、AMR—CBI隧道窑直接还原工艺、宽体球状海绵铁隧道窑、L-S快速还原工艺等多种新技术,掀开了隧道窑工艺规模扩大、产能提高、机械及自动化提升的序幕.1.3 转底炉转底炉煤基直接还原是最近几十年间发展起来的炼铁新技术,代表工艺为Fastmet,它由美国Midrex公司与日本神户制钢于20世纪60年发,是采用环形转底炉生产直接还原铁的一种方法.经过多年的半工业性试验和深入的可行性研究,现已完成工艺作参数和装置设计的优化.Fastmelt和ITmk3工艺是在此基础上增加对直接还原铁的处理.图3显示了这三种以转底炉为主体的直接还原工艺流程.图3 转底炉直接还原工艺流程煤粉与铁精粉按比例混匀制成球团,干燥后以1~3层球铺放在转底炉床面,随着炉底的旋转,炉料依次经过预热区、还原区和冷却区.还原区内球团被加热到1 250~1 350 ℃,由于煤粉与铁氧化物紧密接触,铁氧化铁被碳迅速还原成DRI,成品在800~1 000 ℃左右连续从转底炉卸出.球团矿在炉底停留8~30 min,这取决于原料特性、料层厚度及其他因素,成品可作电炉热装炉料或者转炉炉料,也可冷却或生产热压块(HBI).Fastmet工艺技术特点:①在高温敞焰下加热实现快速还原,反应时间只需10~20 min,生产效率高;②原料来源广泛,铁原料方面,除使用高品位粉矿、精矿外,还可用氧化铁皮、代油铁泥、炼钢粉尘、含En、Pb、As等有害杂质的铁矿等;还原剂方面,除煤以外焦末、沥青均可利用,不必担心出现结圈问题;③炉料相对炉底静止,对炉料强度要求不高;④废气中含有大量显热,可用作预热空气、干燥原料等[6]. Fastmelt工艺流程基本与Fastmet一致,只是在后续添加一个熔炉来生产高质量的液态铁水.Itmk3工艺是使金属化球团在转底炉中还原时熔化,生成铁块(Nuggets),同时脉石也熔化,形成渣铁分离.当然转底炉也存在着设备复杂、炉内气氛难控制、传热效率低以及对还原剂硫含量要求严格的缺点.就目前转底炉工艺开发的水平和规模而论,与高炉还有较大差距,但仍存在发展的广阔空间,天津荣程联合钢铁集团已兴建一条100万t级Fastmet生产线,建成目前世界最大的转底炉.另外,用转底炉可处理一些特殊铁矿,如含锌、铅、砷等有害杂质,或含镍、钒、钛等有用元素,均可利用转底炉的工艺优势,或高温挥发,或选择性还原,配合后续工艺,实现资源综合利用.马钢尘泥脱锌转底炉工程项目于2008年5月开工建设,2009年7月6日正式竣工投产,建成了整套转底炉(RHF)脱锌工艺技术装置,不仅解决了含锌尘泥循环利用的后顾之忧,而且将综合利用技术上升到高品质资源化水平.1.4 其他新工艺1.4.1 PF法煤基竖炉直接还原工艺中冶集团北京冶金设备研究设计总院,结合国内情况创新发明了PF法竖炉直接还原工艺.PF法是在吸收K-M法外热式竖炉煤基直接还原工艺的经验基础上,设计的以一种中国特色的罐式还原炉为主反应器的直接还原法.这种工艺技术可靠,技术经济指标在各种煤基直接还原工艺中属先进水平.PF法直接还原工艺流程如图4所示.图4 PF法直接还原工艺流程PF法直接还原工艺主要特点[1]:1)主体设备选用外热式竖炉,预热、还原、冷却三段根据不同的作用和温度选用不同材质和结构,便于传热和化学反应进行,提高热效率和设备寿命.2)原燃料适用性强,对精矿、还原剂和燃料没有特殊要求.3)采用外配碳工艺,还原剂适当过量,扩大了煤的选用范围,造球工艺也因不定量配入煤粉而简化,球团强度较高,DRI质量较好.4)多个反应罐可并列组成任意规模的还原设备,设计和组织生产灵活.1.4.2 低温快速还原新工艺2004年钢铁研究总院提出了低温快速冶金新工艺.新工艺利用纳米晶冶金技术的特点将铁矿的还原温度降低到700 ℃以下.新流程分为气基和煤基两种方法,工艺流程如图5、图6所示.图5 煤基低温快速还原新工艺图6 气基低温快速还原新工艺煤基法使用煤粉为还原剂,在700℃左右快速还原铁精矿粉;气基法使用还原性气体还原铁精矿粉,还原温度可低于600℃.新工艺具有能耗低、环境友好等特点,省去了烧结或造球工艺,缓解了钢铁行业对焦煤的依赖,符合我国国情[7].2 攀钢现状钒钛磁铁矿是攀西地区的特色资源,与普通矿相比,钒钛矿直接还原温度较高、还原时间较长,还原过程产生特有的膨胀粉化现象,因此,存在竖炉结瘤、流化床失流和黏结、回转窑结圈等技术难题.高炉流程冶炼钒钛矿,只回收了铁和钒,钛进入高炉渣没有回收,造成钛资源的大量流失.2005年以来,攀钢科研人员在充分吸收、借鉴新流程及相关研究成果的基础上,通过大量的试验研究,针对钒钛磁铁矿特点,提出并验证了钒钛磁铁矿"转底炉直接还原—电炉深还原—含钒铁水提钒—含钛炉渣提钛"工艺路线,彻底打通了钒钛矿资源综合利用新工艺流程,稳定获得了质量满足要求的低碳生铁、达到GB3283-87要求的片状V2O5和PTA121质量要求的钛白产品.依托该研究成果,攀钢集团攀枝花钢铁研究院于2008年5月4日正式启动了攀钢10 万t/a钒钛矿资源综合利用新工艺中试线工程项目,新建一条转底炉—熔分电炉联合使用,年处理能力10万t钒钛矿的试验生产线,为更深入地研究实践,实现转底炉处理钒钛矿的规模化生产提供了广阔的平台.中试线工艺流程如图7所示.本流程采用硫含量较低的白马铁精矿,还原剂采用无烟煤煤粉,粘结剂为有机粘结剂,原料混合后经高压压球机压球,生球烘干后进入转底炉系统.球团在转底炉内停留10~30 min后出料,金属化球团直接热装进入熔分电炉,在一定温度下还原后,产出含钒铁水及含钛炉渣.继续对铁水进行脱硫、提钒后,得到半钢、脱硫渣及钒渣,半钢进入铸铁机铸铁,生产出铸铁块.钛渣制取钛白,实验室条件下钛回收率达到80%以上;钒渣制取钒氧化物(V2O5),实验室条件下,钒回收率达到65%以上.与高炉流程相比,转底炉流程采用100%钒钛矿冶炼,克服了高炉流程必须配加普通矿的不足,在当前铁资源紧张的形势下,有助于充分发挥攀西地区资源优势,拉动区域经济发展.此外,转底炉流程的铁精矿不需烧结处理,不使用焦炭,从根本上避免了烧结烟气脱硫、焦煤资源采购困难以及环保压力大等问题.3 结语图7 资源综合利用中试线工艺流程煤炭资源总量丰富、焦煤短缺,铁矿资源储量大、富矿少、贫矿和共生矿多是中国钢铁工业面临的现实状况.这种能源、资源结构给煤基直接还原法生产海绵铁的发展提供了机遇.转底炉直接还原技术由于在生产率、规模化、投资费用、单位成本等方面都占有明显的优势,可作为发展直接还原技术的首选工艺.鉴于转底炉处理钒钛磁铁矿技术尚属世界首创,并无较多的经验借鉴,因此要大力开展针对钒钛磁铁矿直接还原的基础研究工作,在实践中借鉴各种直接还原方法已取得的成果,开拓创新,开创钒钛矿直接还原新纪元.参考文献[1] 陈守明,黄超,张金良.煤基竖炉直接还原工艺//2008年非高炉炼铁年会文集.中国金属学会,2008:132-135.[2] 杨婷,孙继青.世界直接还原铁发展现状及分析.世界金属导报,2006.[3] 刘国根,邱冠周,王淀佐.直接还原炼铁中的粘结剂.矿产综合利用,2001(4):27-30.[4] 韩跃新,高鹏,李艳军.白云鄂博氧化矿直接还原综合利用前景.金属矿山,2009 (5):1-6.[5] 魏国,赵庆杰,沈峰满,等.非高炉生产技术进步//2004年全国炼铁生产技术暨炼铁年会文集.2004:878-882.[6] 陶晋. 环形转底炉直接还原工艺现状及发展趋势. 冶金信息工作, 1997.6.[7] 郭培民,赵沛,张殿伟.低温快速还原炼铁新技术特点及理论研究.炼铁,2007,26(1): 57-60.来源:攀枝花钢铁研究院网站。
转底炉
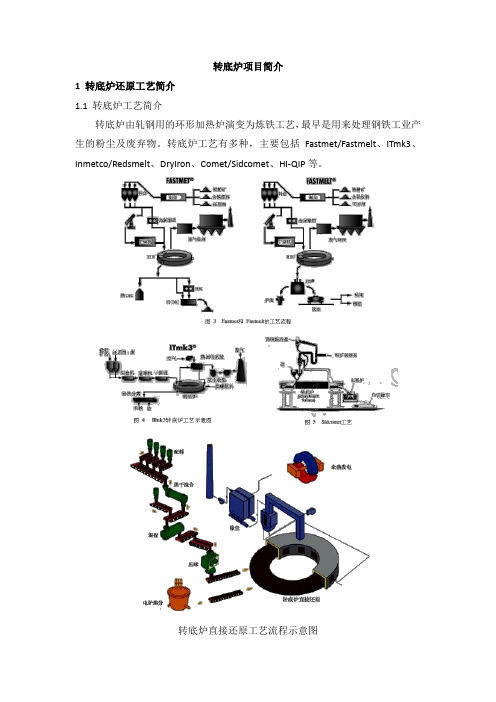
转底炉项目简介1 转底炉还原工艺简介1.1 转底炉工艺简介转底炉由轧钢用的环形加热炉演变为炼铁工艺,最早是用来处理钢铁工业产生的粉尘及废弃物。
转底炉工艺有多种,主要包括Fastmet/Fastmelt、ITmk3、Inmetco/Redsmelt、DryIron、Comet/Sidcomet、HI-QIP等。
转底炉直接还原工艺流程示意图1.2 转底炉工艺与其它相似工艺比较转底炉是煤基直接还原工艺中的核心设备之一,煤基直接还原工艺主要包括回转窑法(如SL-RN法)和转底炉法(如COMET法)。
而煤基直接还原工艺和气基直接还原工艺都是直接还原工艺,以铁产品为例直接还原工艺的产品为海绵铁(又称直接还原铁—DRI即Direct Reduced Iron)。
直接还原和熔融还原是两种主要的非高炉炼铁思路。
当转底炉的原料加入含碳球团时,其产品为金属化球团,可供电炉使用,也作为高炉的原料。
而链篦机—回转窑—环冷机(链回环)生产出来的产品是氧化球团,是为高炉炼铁提供的原料之一,称之为球团矿,而高炉炼铁的含铁原料还包括天然块矿、烧结矿。
转底炉直接还原技术采用含碳球团作原料,反应速度快,同时符合中国以煤为主要能源的特点。
以直接还原技术用于钒钛磁铁矿为例,转底炉技术相比隧道窑、回转窑工艺,以ITmk3为代表的转底炉工艺的优点主要是:○1还原原料在预热和还原过程中始终处于静止状态下随炉底一起进行,所以对生球强度要求不高;○2较高的还原温度(1350℃或更高)、反应快、效率高。
反应时间可在10-50min范围,可与矿热电炉熔炼容易实现同步热装;○3可调整喷入炉内燃料(可以是煤粉、煤气或油)和风量,能准确控制炉膛温度和炉内气氛;○4过程能耗低,回转窑法折算成每吨海绵铁的煤耗通常大于800kg,而转底炉法为600kg;○5从工艺角度来看,ITmk3技术流程简单,投资成本低,产品价格低,铁矿石原料及还原剂选择灵活。
另外,据马鞍山钢铁设计研究总院秦廷许的研究:转底炉-电炉炼铁流程与高炉传统炼铁流程比较,虽在铁精矿消耗量、还原剂和燃料的能源消耗量上相差不大,但吨铁成本低约10%;基建投资省22%左右;全流程电耗低48.6%。
煤基直接还原及转底炉工艺的发展现状

a dm r s f ahcat ae eci d T eget re d m n f ee p gdrc rd cdi n( R )tc — n ei c rf r sr e . h ra k t e a do vl i i t eu e o D I eh toe s d b ma d on e r
摘 要 : 阐述 了煤基直接还原工艺在国内外的发展现状 , 对煤基直接还原 中转底炉的各工艺进行了系
统地 介 绍 和 客观 地 分 析 , 出 了各 工 艺 的特 色 和 优 点 。 表 明 发展 D 技 术 将 有 较 大 的 市 场 需 求 。转 底 指 RI
炉规 模 化 生产 尚未 到 达 成 熟 的 阶段 , 具有 良好 的 发 展前 景 。 但
关键 词 : 煤基 ; 直接还 原; R ; D I转底炉
中 图分 类 号 : F5 T 51
文 献 标识 码 : A
PRES ENT TATU S OF S COAL— BAS ED RECT DI REDU CTI ON AND ROTARY HEARTH FU RN ACE PROCES ES S
随着世界钢 铁工业 的飞速发 展和 国际社会 对环
是 缓解这 些矛盾 的有 效措施 之一 , 目前 , 国际上 电炉
钢 比例 已经 接 近 5 %且 还 在 不 断 发 展 。 电炉钢 生 O 产 需要大 量 的废 钢及 其替代 品 。据 我 国废钢 铁应用 协会 测算 , 0 7年 我 国社 会 废 钢 产 生 量约 为 4 0 20 40 万 t钢铁 企业废 钢产 生量 约 为 2 0 , 7 0万 t两项 相加 , 为 70 10万 t 0 7年我 国粗 钢 产 量预 计 为 4 5亿 。2 0 .
国内外转底炉的发展趋势及我国发展转底炉技术的建议

• 含碳球团内,矿粉与还原剂具有良好的接触条件。在高温下 ,还原反应以高速进行。经过15~20min的还原,球团矿金 属化率即可达到88%~92%。还原好的球团经一个螺旋排料 机卸出转底炉,供电炉作炼钢原料。
属化球团经过冷却区后被排出炉外冷却,部分再氧化金属化率降低一些。煤气燃烧
及反应生成的烟气沿着与炉料转动相反的方向流动,最后流入废气净化处理及余热 回收系统。
装料 区
900~1100 ℃
预热区
烟气流动方向 1200~1400℃
还原区
1100~900℃
烧嘴
冷却区
排料区
转底炉炉底转动方向
一、国内外转底炉技术的发展过程简介
一、国内外转底炉技术的发展过程简介
DRYIRON工艺流程图
料仓
空气
换热器
烟气
混 压球机
布料器
螺旋排料
DRI料罐
布袋除尘器
一、国内外转底炉技术的发展过程简介
⑵. 干铁法
GLOBA公司(原MR&E公司)在1960年是米德兰-罗斯的快速加热工艺的技 术开发部门,1985年成为独立公司。曾经为美国Ameristeel公司的电炉粉 尘处理系统以及美国Rouge Steel公司综合钢铁厂的粉尘和污泥处理系统提 供DRYIRON法的相关设备,具备丰富的应用实绩。GLOBA公司开发的干铁法 有两项专利技术:用废糖浆作为粘结剂,利用氧化铁粉与碳粉混合物成型 的干压块方式对辊压球机压成球团后直接装入转底炉,取消了球团的烘干 程序;采用特殊的震动传送装置的炉料装入方法。可以得到金属化率大于 90%的DRI。 是一种较理想的煤基直接还原工艺。 该工艺过程中在转底炉 内的高温作用与短暂的停留时间(约10min),其操作具有巨大的灵活性, 而且设备的操作控制非常容易。考虑到上述炼铁厂粉尘和污泥处理以及还 原铁生产的需要,新日铁钢铁事业部于1999年从美国MR&E公司引进转底炉 DRYIRON法,并且争取到代理推销资格。 这是日本FASTMET法发展的基础。
直接还原技术的发展及前景
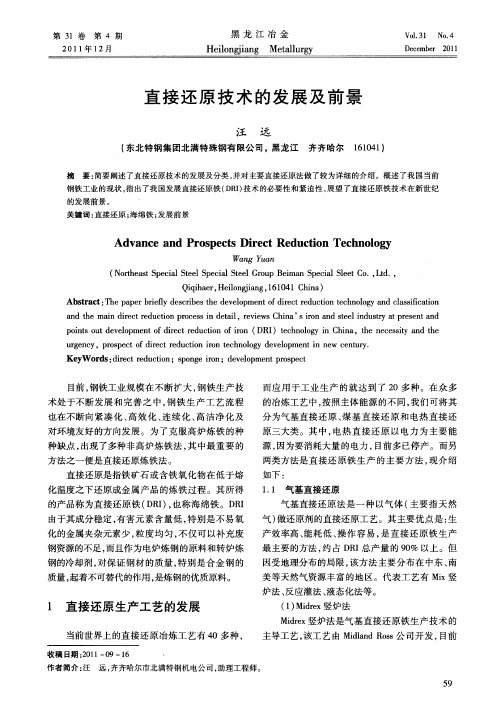
我 国天然气 资源 非常 有 限 , 煤 炭 资源 ( 其 但 尤 是非 焦煤 )的首选 工艺 。 目前 在 国 内实 施 的工艺 主
铁 ) 03年我 国从 国外进 口直接还原铁 ( 绵铁 ) 。20 海 20万 t而 我 国 直 接 还 原 铁 生 产 能 力 仅 为 6 5 , 0 万 t年 ,03年产量为 4 / 20 , 0万 t远远不 能满足需求 。 ,
收 稿 日期 :0 1— 9—1 21 0 6 ・
Mirx 炉法 是气 基 直接 还 原铁 生 产 技 术 的 de 竖
主导工艺 , 该工艺 由 Md n os iadR s 公司开发, l 目前
作者简介 : 汪
远 , 齐哈尔市北满特钢机 电公 司 , 齐 助理工程师 。
5 9
黑
p it o t eeomet f i c rd c o frn( R )tcn l hn ,t eesyadte ons u vlp n r t e ut n o i d od e i o D I eh oo i C ia h n cs t n y g n e i h
第 3 1卷
第 4 期
黑 龙 江 冶 金
Vo . 1 13
N . o4
2 1 1 0 年 1 2月
He o g a g Me l ry i nj n l i t l g au
D c mb r 2 e e e 01 1
直 接 还 原 技 术 的发 展 及 前 景
汪 远
Ad a c nd Pr s e t r c du to Te hn lg v n e a o p cs Die tRe c in c o o y
国内外转底炉的发展趋势及我国发展转底炉技术的建议
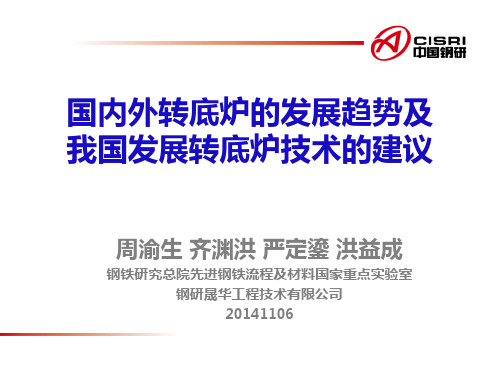
HBI水冷后使用。Fastmet煤气热值必须大于2000kcal/m3。炉内辐射传热
的火焰温度1200-1400℃,设备作业率为92%左右,Fastmet生产每t DRI 需消耗天然气2.24GJ(约63m3)、80度电及320kg煤粉,转底炉的设计
一、国内外转底炉技术的发展过程简介
FASTMET和小高炉间的燃料消耗、总能耗比较
项 目 单位 FASTMET 700m3小高炉
耗煤量
耗外供气体燃料量 耗电量 总能耗
GJ/thm
GJ/thm GJ/thm GJ/thm
11.2
4.6 2.2 18.0
22.8
1.4 24.2
一、国内外转底炉技术的发展过程简介
Kakogawa Commercial Plant Material Flow 加古川示范工厂的物料平衡
Waste to be treated (14,000ton/y ) BF Filter Cake BOF Flue Dust EAF Dust Other Waste : 5,000ton/y : 6,000ton/y : 2,000ton/y : 1,000ton/y
一、国内外转底炉技术的发展过程简介
1、转底炉直接还原工艺简介 钢铁厂每年产生大量含锌、铅高的废弃含铁粉尘,高炉不宜使用,环保限制其排 放输出(美国的委托处理费是~250$/t ,欧洲200欧元/t ,日本是2000日元/t ), 如何对其经济地回收利用是困扰冶金行业的一个难题。因此,转底炉煤基直接还原 技术应运而生。 冷固结含碳球团炉料从装料区装入转底炉炉内仅1-2层,炉料随着炉底一起转动, 不会受到挤压。先在预热区内被加热到1000℃以上,然后进入1200 ℃ -1400℃的还 原区加热10-20min。在还原区,炉料中的Fe和K、Na、Pb、Zn等氧化物陆续被含碳 球团中的碳自还原,K、Na、Pb、Zn等元素以气体的形式随烟气逸除。还原后的金 属化球团经过冷却区后被排出炉外冷却,部分再氧化金属化率降低一些。煤气燃烧 及反应生成的烟气沿着与炉料转动相反的方向流动,最后流入废气净化处理及余热 回收系统。
我国转底炉工艺技术发展现状与前景浅析

供 少许 借鉴 与参 考 。 关键词 转底 炉 直接 还原
炼铁
1 转 底 炉 发 展 概 况 转 底 炉 ( o r er u ae 简 称 R t y H at F r c , a h n R F 工 艺 是 以一 种 煤 基 快 速 直 接 还 原 技 术 。 H ) 该 工 艺 思 想 最早 由 R s 公 司 ( de os Mir x公 司前
目前 , 国内 D I R 生产达 到工业 化规模 的 10万吨/ 0 年座 的转底 炉 , 各种直接 还原装置 直接还原技 术有转底 炉 、 回转 窑 和隧道 窑三 的生产能力 见表 2 。转底炉生产 的单 位能耗 种, 这三种工艺都 属煤基 直接还 原技 术。其 也小于 回转窑和隧道窑工艺 , 具备一定优势 。
另有多家钢铁企业规划设计上 马转底炉 ,转
转底 炉发展过程 中美 国、 国、 德 日本等 国家 都 底 炉工 艺逐 渐成 为直接还原铁领域 的一个建 相继投入力 量 开发研 究 , 先后建 立 起工 业 化 设热点 。 目前 ,国内工业规模转底 炉建设情 生产厂 。 目前该技术 已经逐渐趋 于成熟并 表 况如下 表 1 。
17 年在美 国 Elod市建 成第一 座具 有商 几年在消化吸收 国外转底 炉技术 发展 的基础 98 l o w
业意义的转底 炉 I ME C N T O工 艺起 到 现在 转 上 ,先 后有 多家企 业投 资建 设转 底炉 装置 ,
底 炉的发 展 已经 有 3 0多 年 的历 史 H 3。 在 -
第3 5卷
・
第 4期
攀枝 花科 技 与信息
( 总第 13期 ) 0
非 高炉 炼铁会 议专题 ・
我 国 转 底 炉 工 艺 技 术 发 展 现 状 与 前 景 浅 析
-=-周渝生 中国直接还原铁技术发展及市场供需分析 (终稿)
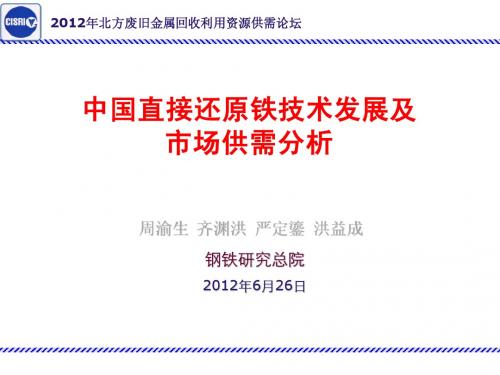
粘结,炉内不必设置机械破碎装置。
5.加压煤制气工艺是我国发展直接还原新工艺的基础和条件 煤气化是煤基DRI、发电、供热多联产工艺过程的共性和关 键技术。在过去20年间,煤气化技术取得极大发展,几乎世界 上所有类型的煤气化技术的生产装置都能在中国找到。很难说 现在有哪一种煤气化技术可以占有绝对优势,每种煤气化技术
2012年北方废旧金属回收利用资源供需论坛
中国直接还原铁技术发展及 市场供需分析
周渝生 齐渊洪 严定鎏 洪益成 钢铁研究总院
2012年6月26日
内 容 提 要
1.中国近几年铁产量及直接还原铁的产量和比例 2.废钢比提高将推动我国直接还原的发展 中国目前DRI发展及 市场需求 3.低品质难选含铁原料用转底炉炼粒铁是煤基DRI的创新方向 4.气基竖炉直接还原工艺技术是我国直接还原的主要发展方向 5.加压煤制气工艺是我国发展直接还原新工艺的基础和条件
平均容积仅600m3左右,导致我国钢铁行业的劳动生
产率较低、总能耗和CO2排放量很高。2011年全球粗
钢产量15.27亿吨,其中中国粗钢产量6.83亿吨,占全
球粗钢产量44.73%。
1.中国近几年铁产量及直接还原铁的产量和比例
2011年世界生铁产量为10.8亿t,中国的生铁产量 6.297亿t,占世界的比重58.31%,铁钢比高达0.922。 2011年世界直接还原铁(DRI/HBI)总产量约为6347 万吨,约为世界生铁产量9.52亿吨的6.67%。 2011年中国直接还原铁(DRI/HBI)年产量约为60万 吨,约占生铁年产量6.297亿吨的0.095%,中国的DRI 产量不到高炉生铁产量的千分之一。
钛铁矿转底炉固相直接还原工艺制备高钛渣
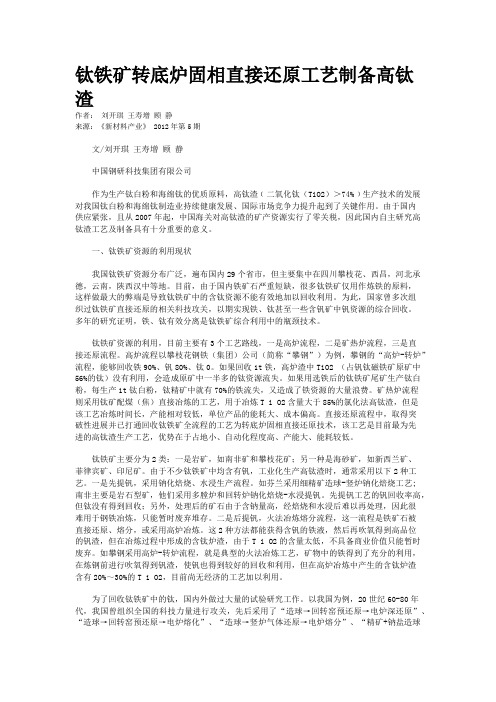
钛铁矿转底炉固相直接还原工艺制备高钛渣作者:刘开琪王寿增顾静来源:《新材料产业》 2012年第5期文/刘开琪王寿增顾静中国钢研科技集团有限公司作为生产钛白粉和海绵钛的优质原料,高钛渣﹝二氧化钛(TiO2)>74%﹞生产技术的发展对我国钛白粉和海绵钛制造业持续健康发展、国际市场竞争力提升起到了关键作用。
由于国内供应紧张,且从2007年起,中国海关对高钛渣的矿产资源实行了零关税,因此国内自主研究高钛渣工艺及制备具有十分重要的意义。
一、钛铁矿资源的利用现状我国钛铁矿资源分布广泛,遍布国内29个省市,但主要集中在四川攀枝花、西昌,河北承德,云南,陕西汉中等地。
目前,由于国内铁矿石严重短缺,很多钛铁矿仅用作炼铁的原料,这样做最大的弊端是导致钛铁矿中的含钛资源不能有效地加以回收利用。
为此,国家曾多次组织过钛铁矿直接还原的相关科技攻关,以期实现铁、钛甚至一些含钒矿中钒资源的综合回收。
多年的研究证明,铁、钛有效分离是钛铁矿综合利用中的瓶颈技术。
钛铁矿资源的利用,目前主要有3个工艺路线,一是高炉流程,二是矿热炉流程,三是直接还原流程。
高炉流程以攀枝花钢铁(集团)公司(简称“攀钢”)为例,攀钢的“高炉-转炉”流程,能够回收铁90%、钒80%、钛0。
如果回收1t铁,高炉渣中TiO2 (占钒钛磁铁矿原矿中56%的钛)没有利用,会造成原矿中一半多的钛资源流失。
如果用选铁后的钛铁矿尾矿生产钛白粉,每生产1t钛白粉,钛精矿中就有70%的铁流失,又造成了铁资源的大量浪费。
矿热炉流程则采用钛矿配煤(焦)直接冶炼的工艺,用于冶炼T i O2含量大于85%的氯化法高钛渣,但是该工艺冶炼时间长,产能相对较低,单位产品的能耗大、成本偏高。
直接还原流程中,取得突破性进展并已打通回收钛铁矿全流程的工艺为转底炉固相直接还原技术,该工艺是目前最为先进的高钛渣生产工艺,优势在于占地小、自动化程度高、产能大、能耗较低。
钛铁矿主要分为2类:一是岩矿,如南非矿和攀枝花矿;另一种是海砂矿,如新西兰矿、菲律宾矿、印尼矿。
炼钢中的直接还原技术及其应用

炼钢中的直接还原技术及其应用随着钢铁行业的发展,炼钢技术也在不断的变革与创新。
直接还原技术作为一种新型炼钢技术,已经开始得到广泛的应用。
本文将从直接还原技术的基础和应用方面进行阐述,以期为读者提供更深入的了解。
一、直接还原技术的基础直接还原技术是使用还原剂将炉料中的氧化铁还原为金属铁的炼钢技术。
与传统的高炉技术相比,在直接还原技术中,直接使用还原剂还原炉料中的氧化铁,不需要通过高温和高压使其发生氧化还原反应。
这种技术具有明显的优点,主要表现在以下几个方面:1.制造成本低:由于直接还原技术不需要高压和高温,所需能源也更少,因此生产成本低于传统的高炉技术。
2.环保节能:使用直接还原技术炼钢可以减少CO2和NOx等大气污染物的排放,一定程度地保护了环境。
另外,由于直接还原技术对能源的需求更小,也有利于节能减排。
3.操作简便:在直接还原技术中,制造过程更加简单直接,操作也更加方便,更容易实现自动化和智能化。
以上3个方面是直接还原技术的主要优点。
相比于传统的高炉技术,直接还原技术在生产成本、环保和操作方便等方面都有更多的优势。
二、直接还原技术的应用1.直接还原工艺的应用直接还原技术的应用范围很广,从小型加工厂到大型钢铁制造企业都在使用该技术。
其中,直接还原工艺是一种常见的应用方式。
直接还原工艺主要包括三部分:还原反应、冶金物理化学过程和钢水净化过程。
还原反应过程是指在以还原剂为主体的还原反应中,将冶金炉中的氧化铁还原为冶金铁的化学反应过程。
冶金物理化学过程是指冶金炉内金属铁的脱硫、脱锰、脱孔及相应物理化学反应。
钢水净化过程是指将冶金炉内钢水经过捞渣、渣加剂、精炼等工艺处理后实现除杂,使钢水纯净。
直接还原工艺是炼钢企业中最常用的炼钢技术之一,它主要的应用优势在于高效、短周期、节能、环保等方面。
2.直接冶炼的应用直接冶炼是指将原料中的氧化铁直接还原至金属铁进行炼制的技术。
在直接冶炼过程中,仅使用还原剂,不需要其它辅助材料。
- 1、下载文档前请自行甄别文档内容的完整性,平台不提供额外的编辑、内容补充、找答案等附加服务。
- 2、"仅部分预览"的文档,不可在线预览部分如存在完整性等问题,可反馈申请退款(可完整预览的文档不适用该条件!)。
- 3、如文档侵犯您的权益,请联系客服反馈,我们会尽快为您处理(人工客服工作时间:9:00-18:30)。
转底炉直接还原炼铁工艺的发展2010-02-24 17:02:19 作者:phpcms来源:浏览次数:571 网友评论 0 条一、前言为了满足冶炼高纯净钢的要求, 炼钢生产对纯净铁资源的需求越来越大。
与此同时, 优质废钢与铁资源却日益短缺其价格不断升高, 对炼钢生产影响很大, 为此,各国冶金工作者开发了许多直接还原或熔融还原工艺来为炼钢生产提供质优价廉的纯净铁资源。
但由于技术、投资等方面的原因,真正具有市场竞争力、适合于工业应用的并不多见。
同时,钢铁厂每年生产的大量含铁废弃物也给环保带来很大的压力。
如何对其进行回收利用是困扰冶金行业的一个难题。
直接还原工艺中气基法虽然具有生产效率高,生产规模大,能耗低和容易操作等优点,但必须以一次能源---天然气为还原剂,因此该工艺只能在天然气资源丰富的国家得以发展。
而煤基法以煤作为还原剂,较好的解决了气基法的不足。
目前世界上很多国家都在开发煤基直接还原新技术,有些技术已经应用于工业生产。
其中,转底炉法以其原料适应性强和操作工艺的零活性等优点,引起冶金界的高度重视。
但由于原料条件和对产品质量要求的不同,转底炉直接还原炼铁又发展为FASTMET,ITKM3和DRYIRON等不同工艺路线。
二、FASTMET工艺早在50年代Midex的前身Ross公司就发明了转底炉含碳球团直接还原法。
1964~1966年进行了2t/h规模试验。
1974年Inco公司开始研究把转底炉用于处理电炉生产不锈钢产生的氧化物粉尘的方法,并建立了一座年处理2.5万吨废料的工厂。
经转底炉预还原的球团,通过运输罐热装入电炉。
1978年美国Inmetco在宾州埃尔伍德市建成一座年处理5.6万吨电炉钢厂粉尘能力的转底炉,回收锌及可用作电炉原料的含Cr,Ni的还原铁。
1982年Mid ex公司将转底炉法命名为FASTMET,用于煤基直接还原。
神户制钢收购Midex公司后,199 5年开始建设2.5t/h示范装置,经过两年半试验后,认为Fastmet技术成熟可靠,已达到商业水平化水平。
神户制钢与三井公司合资对在美国建设年产DRI50~100万吨项目进行报价,1998年9月神户钢铁公司报价年产DRI50万吨的转底炉装置,每套售价1亿美元。
世界上首次利用FASTMET工艺以含铁废料为原料的商业化直接还原铁厂,于2000年二季度在日本新日本制铁株式会社广火田厂投产,年产能力19万吨,其中14万吨将直接装入广火田厂的氧气转炉。
神户制钢株式会社新加古川厂是第二个用该工业建设的直接还原铁厂。
2002年5月,日本神户制钢株式会社和尼日利亚签订基本协议,日方将帮助AJAOKUTA 钢公司建设一座年产50万吨的FASTMET直接还原铁工厂。
2.1 工艺流程FASTMET法的工艺流程见图1。
铁精矿(或含铁废料)、煤粉和粘结剂经混合搅拌器后进入造球机造球,生球可装入干燥器,也可直接装入转底炉。
在转底炉中,球团矿均匀地铺在炉底上,料层为1~3层球的高度。
随着炉底的旋转,球团矿被加热到1250℃~1350℃。
同时,约90%~95%的氧化铁被球团内部的固体碳还原成DRI。
球团矿在炉底停留时间一般为8~30分钟,它取决于原料的特性、球团矿层数及其他因素。
从转底炉出来的煤气经过焚化炉和热交换器将转底炉烧嘴助燃空气预热,并将高温废气用来干燥球团,生产用水循环使用,生产中产生的粉末回收利用。
2.2 工艺特点与其他直接还原工艺相比,FASTMET工艺具有以下特点:(1)以煤粉作为还原剂,摆脱了天然气地域分布不均的限制,对煤的质量也没有回转窑那么严格,故其应用地域广泛。
(2)主要设备是环形转底炉,与回转窑相比,该工艺设备简单、投资省、能耗低。
(3)对炉料的强度要求不高,因为料层很薄且随炉底一起转动,炉料既不受压,又与炉底之间没有相对运动,破碎量很少。
(4)炉料在转底炉内停留时间短(约20min),操作容易。
FASTMET法直接使用粉矿和煤粉,因而在矿石和能源上具有很好的适应性和经济性。
该法生产出的典型DRI成分主要与原料条件有关,若以铁精矿和低灰份煤为原料,生产的DRI 产品TFe可达98%,金属化率可达95%。
2.3 存在问题(1)由于采用敞焰加热,还原的铁可能会被再氧化,只有抑制这一现象才能获得较高的金属化率。
(2)燃烧燃料的选择与供应问题。
目前工业化及试验设备均用天然气或重油作燃料,使控制简化。
在气体、液体燃料较贵的地区,可以采用煤粉,但煤的储存、干燥、制粉及烟气除尘设备的投资、维护费用大。
而且污染环境,在大城市附近的工厂因环保要求严格而难于采用,使用煤气必须解决煤气稳定供应问题。
(3)由于全部还原剂均加入到球团矿内,因而还原剂中所含的灰分和有害元素将直接影响DRI的质量。
这对还原剂质量提出了较高的要求:固定碳的含量要高,灰粉及挥发分含量要低,硫磷含量也要低。
尽管如此,FASTMET法已日益引起人们的重视。
日本神户制钢株式会社新加古川厂建成了2.5t/h的试验设备,如果进展顺利,Midex公司拟在北美建设第一个工业性生产厂,年产规模45万吨,基建建设估计为6500~7500万美元。
三、干铁法MR&E公司新开发的专利技术干铁法(DRuIron)工艺是一种较理想的煤基直接还原工艺。
该工艺是由米德兰-罗斯快速加热工艺发展而来的,由于采用了无粘结剂干压块、能源利用及环保方面的最新技术,以及合理的转底炉设计,它克服了通常煤基还原带来的粉化、脉石含量高、硫高、金属化率低等缺点。
该工艺过程中的反应基于煤基直接还原动力学,加之在转底炉内的高温作用与短暂的停留时间(约10min),其操作具有巨大的灵活性,而且设备的操作控制非常容易。
煤的化学能在反应中100%得到利用,不会被其它工艺步骤(如气化等)所消耗。
尾气中的热能可回收用于发电或其他辅助工艺。
大量工业试验表明,该工艺不仅可用铁精粉矿为原料生产质量稳定的海绵铁或热压块铁,作为优质废钢的理想替代品供应电炉,而且可用于处理钢铁厂各类含铁废弃物。
所采用的转底炉工业化设备很适合规模化生产,当达到10万吨/年以上的生产规模时,效益就比较显著。
3.1 工艺流程干铁法的核心设备为转底炉,其工艺流程为:混料-冷态干法压球-转底炉焙烧-热压快。
其中,采用的冷态干法(无粘接剂)压球工艺使压制的球团无需干燥即可直接送入转底炉处理,简化了工艺步骤。
对于转底炉的加料、排料装置的改进则使得操作控制更为容易。
转底炉焙烧过程产生的尾气中蕴含着大量的化学能和热能,用余热锅炉回收产生的蒸汽或用来发电,还可用于预热助燃空气。
尾气中的粉尘与有害气体如SO2等采用喷有石灰水的布袋除尘装置去除,同时还使用MR&E公司的低NOX控制专利技术处理尾气,从而使其对环境的污染降至最低限度,尤其是通过一项称作金属氧化物粉末处理工艺的综合专利技术的使用,使得干铁法工艺不仅可用铁精矿粉作原料,而且同样适用于钢铁厂含铁粉尘的回收利用。
该专利包括一系列先进技术:无粘接剂压块,转底炉内的单层布料,高辐射加热,转底炉温控技术,各种非铁金属氧化物的有效去除。
这些技术的应用,大大地改进了海绵铁的生产。
3.2 基本原理干铁法工艺的理论基础是碳与铁氧化物之间的直接还原反应与固-固相反应动力学。
实际应用过程是将铁氧化物与煤粉或焦粉均匀混合后冷压成球,使得铁氧化物与碳紧密接触,具备良好的反应动力学条件。
然后用转底炉进行加热处理。
在炉内的高温作用下,铁氧化物与固定碳反应生成金属铁并释放CO2。
干铁法压块中固定碳与铁氧化物的理论摩尔比为1.5:1,但这实际反应过程中均会产生CO2与CO,MR&E公司在试验中摸索到控制球团中碳与铁氧化物重量之比为1.6:1较为适当。
此时,不仅生成CO2与CO,而且在反应后的球团中留有约4%的残碳,这有利于保持球团中的还原气氛,加速还原反应速度,减少再氧化的发生。
因此,该工艺的关键是要控制CO2与CO的比率,以达到尽量降低再氧化,减少碳消耗与缩短炉内停留时间的目的。
3.3 干铁法的工业试验MR&E公司在俄亥俄州匹兹堡的工业试验厂对干铁法工艺进行了试验验证。
该试验厂分别用铁精粉矿粉、电炉除尘灰及传统流程钢铁厂的废弃物为原料进行了一系列工业试验,获得了大量工业试验数据。
(1)用铁精粉矿生产海绵铁(DRI)或热压块铁(HBI)将铁精矿粉与煤粉混合压球后加入转底炉,球团在炉内受控的还原气氛中被加热。
当达到反应温度时,铁氧化物被还原为金属铁。
反应所需的热能全部由煤提供。
从转底炉出来的海绵铁带有较多显热,可采用热压块工艺加工为热压块铁,以便运输与存储。
该法生产的热压块铁TFe含量达92%,金属化率高达95%,C含量约4%,脉石含量约2.4%,S含量仅为0. 04%,可见其品质纯净,脉石与硫等杂质含量很低,可作为优质废钢的理想替代品。
而且与废钢相比,其质量均匀稳定,波动小,对于炼钢生产极为有利。
(2)回收电炉除尘灰与轧钢铁鳞电炉除尘灰与轧钢铁鳞的特点是含有较多非铁金属的氧化物,如锌、铅、镉等,被美国环保部门定为有害物质,称作KO61。
在干铁法工艺处理过程中,这些非铁氧化物将以气态逸出,并在后续的烟气处理装置中予以收集,此时KO61已转化为提炼有价值非铁金属的原料。
球团中ZnO脱除率高于95%,生成的海绵铁金属化率高达91%。
转底炉焙烧含锌粉尘时以气态逸出的非金属氧化物在尾气处理过程中,由布袋除尘器收集,可作为提炼锌的原料使用。
(3)回收钢铁厂传统废弃物传统钢铁厂废弃物包括转炉尘泥,热轧污泥,连铸氧化铁皮及高炉粉尘与瓦斯泥。
这些物质总体来说碳含量很高,与电炉除尘灰相比,锌含量低,而铅、镉含量极少。
灰泥原料中的铁与碳含量较高,经转底炉焙烧后,生成的海绵铁金属化率高于90%,其尾气收尘富含Z nO,可以回收增加收入。
干铁法工艺的投资与效益估算。
建造年产100万吨海绵铁的生产厂的单位投资成本约1 25美元/(t.a),由于干铁法可以用较便宜的铁精粉矿作原料,用非炼焦煤做热源及还原剂,所以原料与能源价格较低,单位生产成本约为72美元/吨DRI。
干铁法工艺不仅在能源及原料结构上特别适合中国的国情,而且在投资与生产运行成本上都比传统的直接还原工艺法更有竞争力。
干铁法工艺用优质铁矿粉生产的海绵铁及热压块铁作为优质废钢的替代品供应电炉,所带来的效益十分显著,这主要源于其稳定均匀的成分与质量,与废钢相比,其质量与成分波动小,对稳定钢水质量有利。
且其生产成本不会象废钢价格那样随市场变化产生较大波动,对稳定电炉生产非常有利。
四、Itmk3工艺Itmk3是由神户钢铁公司开发的一种新型炼钢技术。
它是一种灵活、环保的一步法生产粒铁块的方法,其产品质量与高炉生铁相当。
神户钢铁公司视Itmk3为第三代炼铁方法。
第一代炼铁方法定义为高炉炼铁法,第二代则是包括Midrex技术在内的气基直接还原法。