《车辆现代设计理论与方法》-太原理工硕士作业
现代汽车设计与理论方法
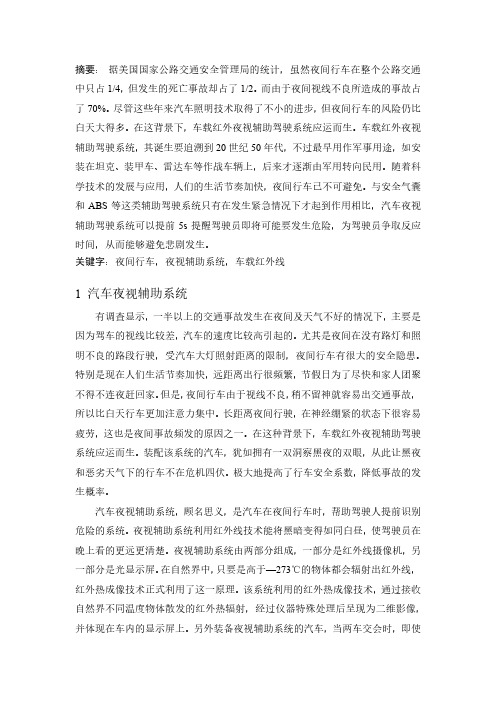
摘要:据美国国家公路交通安全管理局的统计,虽然夜间行车在整个公路交通中只占1/4,但发生的死亡事故却占了1/2。
而由于夜间视线不良所造成的事故占了70%。
尽管这些年来汽车照明技术取得了不小的进步,但夜间行车的风险仍比白天大得多。
在这背景下,车载红外夜视辅助驾驶系统应运而生。
车载红外夜视辅助驾驶系统,其诞生要追溯到20世纪50年代,不过最早用作军事用途,如安装在坦克、装甲车、雷达车等作战车辆上,后来才逐渐由军用转向民用。
随着科学技术的发展与应用,人们的生活节奏加快,夜间行车已不可避免。
与安全气囊和ABS等这类辅助驾驶系统只有在发生紧急情况下才起到作用相比,汽车夜视辅助驾驶系统可以提前5s提醒驾驶员即将可能要发生危险,为驾驶员争取反应时间,从而能够避免悲剧发生。
关键字:夜间行车,夜视辅助系统,车载红外线1汽车夜视辅助系统有调查显示,一半以上的交通事故发生在夜间及天气不好的情况下,主要是因为驾车的视线比较差,汽车的速度比较高引起的。
尤其是夜间在没有路灯和照明不良的路段行驶,受汽车大灯照射距离的限制,夜间行车有很大的安全隐患。
特别是现在人们生活节奏加快,远距离出行很频繁,节假日为了尽快和家人团聚不得不连夜赶回家。
但是,夜间行车由于视线不良,稍不留神就容易出交通事故,所以比白天行车更加注意力集中。
长距离夜间行驶,在神经绷紧的状态下很容易疲劳,这也是夜间事故频发的原因之一。
在这种背景下,车载红外夜视辅助驾驶系统应运而生。
装配该系统的汽车,犹如拥有一双洞察黑夜的双眼,从此让黑夜和恶劣天气下的行车不在危机四伏。
极大地提高了行车安全系数,降低事故的发生概率。
汽车夜视辅助系统,顾名思义,是汽车在夜间行车时,帮助驾驶人提前识别危险的系统。
夜视辅助系统利用红外线技术能将黑暗变得如同白昼,使驾驶员在晚上看的更远更清楚。
夜视辅助系统由两部分组成,一部分是红外线摄像机,另一部分是光显示屏。
在自然界中,只要是高于—273℃的物体都会辐射出红外线,红外热成像技术正式利用了这一原理。
现代设计理论与方法(最终版)
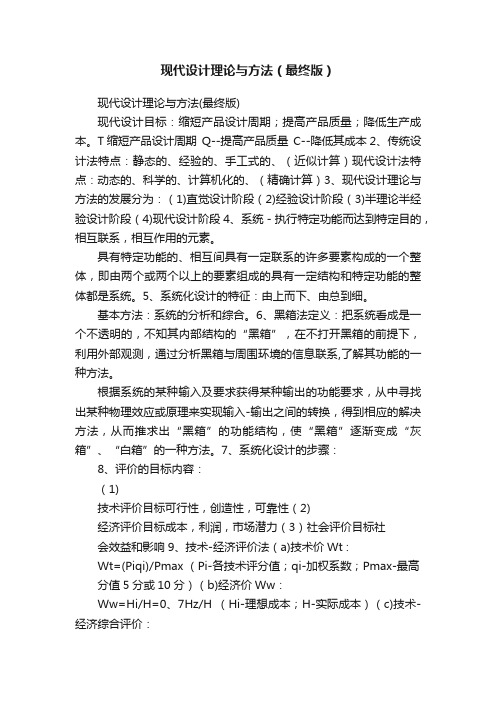
现代设计理论与方法(最终版)现代设计理论与方法(最终版)现代设计目标:缩短产品设计周期;提高产品质量;降低生产成本。
T缩短产品设计周期Q--提高产品质量C--降低其成本2、传统设计法特点:静态的、经验的、手工式的、(近似计算)现代设计法特点:动态的、科学的、计算机化的、(精确计算)3、现代设计理论与方法的发展分为:(1)直觉设计阶段(2)经验设计阶段(3)半理论半经验设计阶段(4)现代设计阶段4、系统-执行特定功能而达到特定目的,相互联系,相互作用的元素。
具有特定功能的、相互间具有一定联系的许多要素构成的一个整体,即由两个或两个以上的要素组成的具有一定结构和特定功能的整体都是系统。
5、系统化设计的特征:由上而下、由总到细。
基本方法:系统的分析和综合。
6、黑箱法定义:把系统看成是一个不透明的,不知其内部结构的“黑箱”,在不打开黑箱的前提下,利用外部观测,通过分析黑箱与周围环境的信息联系,了解其功能的一种方法。
根据系统的某种输入及要求获得某种输出的功能要求,从中寻找出某种物理效应或原理来实现输入-输出之间的转换,得到相应的解决方法,从而推求出“黑箱”的功能结构,使“黑箱”逐渐变成“灰箱”、“白箱”的一种方法。
7、系统化设计的步骤:8、评价的目标内容:(1)技术评价目标可行性,创造性,可靠性(2)经济评价目标成本,利润,市场潜力(3)社会评价目标社会效益和影响9、技术-经济评价法(a)技术价Wt :Wt=(Piqi)/Pmax (Pi-各技术评分值;qi-加权系数;Pmax-最高分值5分或10分)(b)经济价Ww:Ww=Hi/H=0、7Hz/H (Hi-理想成本;H-实际成本)(c)技术-经济综合评价:均值法:W=(Wt+Ww)/2 双曲线法:W= (Wt、Ww )10、产品价值 V=F/C ( F-功能 C-成本)11、寿命周期成本(要会画出它的曲线图,并做分析)C=C1+C2 C1-生产成本 C2-使用成本12、提高V途径(分5种情况讨论)F ↑ /C → =V ↑ 功能F → /C ↓ =V ↑ 成本F ↑ /C ↓ =V ↑ 功能、成本F ↑↑ /C ↑ =V ↑ 功能F ↓ /C ↓↓ =V ↑ 成本第二章机械优化设计1、优化设计的数学模型统一形式描述:min f(x)x=[x1,x2,………xn]T s、t、gi(x)<=0 i=1,2,3…mhj(x)=o j=1,2,……n(p(k)s(k) x(k)第K步迭代点α(k)第K步迭步长 s(k)第K步迭代方向3、终止准则:(1)点距准则:(2)下降准则:(3)梯度准则:4、一维搜索方法: 对一维(也称一元或单变量)目标函数f(x)寻求其最优解x*的过得程称为一维优化,所使用的方法称为一维优化方法。
现代汽车的设计方法
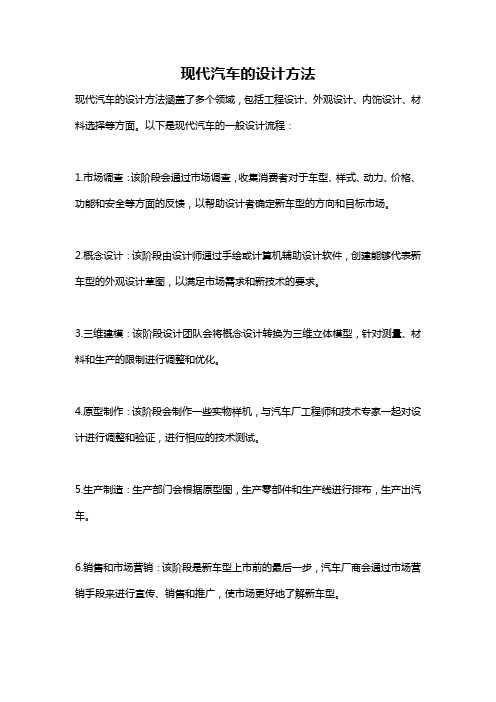
现代汽车的设计方法
现代汽车的设计方法涵盖了多个领域,包括工程设计、外观设计、内饰设计、材料选择等方面。
以下是现代汽车的一般设计流程:
1.市场调查:该阶段会通过市场调查,收集消费者对于车型、样式、动力、价格、功能和安全等方面的反馈,以帮助设计者确定新车型的方向和目标市场。
2.概念设计:该阶段由设计师通过手绘或计算机辅助设计软件,创建能够代表新车型的外观设计草图,以满足市场需求和新技术的要求。
3.三维建模:该阶段设计团队会将概念设计转换为三维立体模型,针对测量、材料和生产的限制进行调整和优化。
4.原型制作:该阶段会制作一些实物样机,与汽车厂工程师和技术专家一起对设计进行调整和验证,进行相应的技术测试。
5.生产制造:生产部门会根据原型图,生产零部件和生产线进行排布,生产出汽车。
6.销售和市场营销:该阶段是新车型上市前的最后一步,汽车厂商会通过市场营销手段来进行宣传、销售和推广,使市场更好地了解新车型。
总之,现代汽车的设计方法是非常综合的,需要整个设计团队的专业技能,以确定车型,并为客户提供最佳的汽车体验。
车辆现代设计方法(2)

填空题1、从设计定义出发可以看出,产品设计应该具有以下需求特征、创造性特征、程序特征和时代特征。
2、设计方法的发展分为直觉设计阶段、经验设计阶段、传统设计阶段和现代设计阶段。
3、最常用的两种实体造型方法包括几何体素法和边界表示法。
4、插值法要求生成的曲线通过每个给定的型值点。
5、逼近法要求生成的曲线靠近每个型值点,但不要求通过每个点。
6、产品造型设计的核心技术是实体建模。
7、特征树中存在两种基本关系:父子关系和邻接关系。
8、根据Bernstein基函数的性质,可以推导出Bezier曲线具有端点性和凸包性和几何不变性。
9、二维工程图的主要内容包括视图、零件图、装配图。
10、相对于满约束状态,参数化草图还可能存在的状态包括欠约束状态和过约束状态。
11、反求工程设计的基本类型包括老产品复制、对己有产品改进、新产品设计。
12、据反求对象的不同实物反求可分为整体反求、部件反求、零件反求。
13、坐标侧量分为接触式和非接触式两大类。
14、特征模型的操纵对象是产品的技术信息、管理信息、功能要素。
15、曲面造型采用表面模型表示三维物体的外形。
16、车身外表面的测量一般包括三种:油泥模型测量、白车身测量、成品汽车测量。
17、作用于物体上的外力通常分为两类:体积力和表面力。
18、边界条件可分为位移边界条件、应力边界条件和混合边界条件。
19、有限元求解应力类问题时,根据未知量和分析方法的不同有三种基本解法:位移法、力法和混合法。
20、虚拟现实的四大特点:沉浸感、交互性、构想性和实时性。
21、原型可分为:物理原型和分析原型。
22、一般来说物体的成型方式可分为三类即:去除成型、静尺寸成型、添加成型。
23、工作可靠性分别用固有可靠性和使用可靠性来反映。
24、可靠性学科主要包括以下三方面的内容:可靠性设计、可靠性分析和可靠性数学。
25、浴盆失效曲线可分为三个特征区:早期失效期、规定失效期和耗损失效期。
26、面向过程的设计包括:___________、___________、___________。
第10章 汽车现代设计方法

CAD技术在汽车行业中的应用
——汽车行业是最早应用CAD技术的领域之一; ——目前,国外的汽车大约每4年进行一次换代,而新的 乘用车产品的开发周期已缩短至两三年,汽车的每次换 代都力求提高汽车的各项性能指标,使外形美观,增加 新功能,适应有关排气、噪声、安全、燃料消耗等各种 规定指标,应用CAD技术可以有效地解决这类问题。
数字汽车造型设计 数字汽车人机工程学分析
1.人体尺寸和人体模型 2.人体的姿势与布置
3.人体的操纵范围
4.人眼的视觉和视野范围
5.人体头部位置包络线
数字汽车车身设计
10.3 现代设计技术
1.优化设计方法
运用数学方法和系统工程方法对产品结构和性能 进行分析、决策,以获取最优解的设计方法。
优化设计与可靠性设计、模糊设计等方法相结合, 可形成许多新的优化设计方法。
展设计工作的时空维度。
6.反求工程
此种设计方法以先进产品的实物或软件(程 序、图样、文件资料等)作为研究对象,综合运 用现代工程设计的相关理论和方法,进行解剖、 分析和研究,进而开发出同类的先进产品。
7.绿色设计
将产品与环境看作一个系统,充分考虑产品
及其制造系统的,会当水击三千里!
1 1
1
第10章 汽车现代设计方法
10.1 概述
10.2 数字汽车车身设计 10.3 主要的现代设计方法
10.1 概述
为保证设计质量、加快设计速度、避免和减 少设计失误,并适应科学技术发展的要求,使设 计工作现代化,引发了“现代设计方法”的研究。 设计方法可理解为:设计中的一般过程及解 决具体设计问题的方法、手段。前者可认为是战 略问题,后者是战术问题。 现代设计技术
现代设计技术是根据产品功能要求及市场竞争要素 如质量、成本、服务、环保等方面的要求,综合运用现 代科学技术,通过设计开发人员科学、规范以及创造性 的工作,产生载有相应的文字、数据、图形等信息的技 术文件,制定用于产品制造的设计方案。
太原理工大学201年硕士研究生招生目录院系所专业研究方
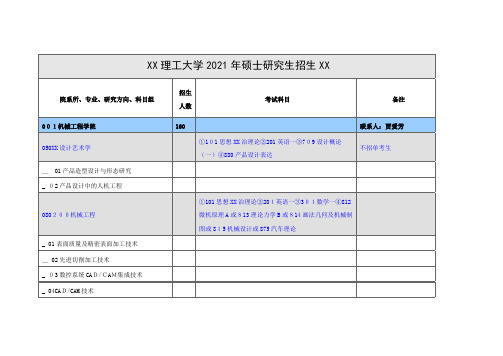
_15岩土工程防灾减灾
_16古建筑结构保护研究
085213建筑与土木工程(专业学位)
①101思想XX治理论②204英语二③302数学二④501建筑设计或502历史建筑复原设计或835建筑构造或836材料力学D或837结构力学A
1.建筑类研究方向参考081301建筑历史与理论和081304建筑技术科学;2。土木类的研究方向参考土木工程;3。按以上XX专业的要求确定考试科目.
_05宽带通信网络
_ 06信号检测与处理
_07XX信号处理
_ 08软件无线电技术
_ 09图像处理与图像通信
_10信息传输理论与技术
081100控制科学与工程
①101思想XX治理论②201英语一③301数学一④830自动控制理论或831数字电子技术
_01计算智能与智能信息处理
_ 02智能控制与自动化
_03现代控制理论与应用
和2#绘图纸)XX不招收单考生
_ 01建筑声学与声环境
_ 02生态与节能建筑
_03城市设计与技术
_04建筑设计及其技术
_ 05环境设计与光艺术
081400土木工程
①101思想XX治理论②201英语一③301数学一④836材料力学D或837结构力学A
含081402结构工程、081401岩土工程、081405防灾减灾工程及防护工程、081406桥梁与隧道工程
_01岩土的工程性质
_ 02基础工程与地基处理
_ 03环境岩土工程
_04结构分析与工程CAD
_ 05钢结构与空间结构
_ 06钢筋混凝土结构
_ 07工程抗震与防灾
_ 08土木工程施工与管理
_09结构耐撞性
_ 10结构抗震减震控制
《现代设计方法》考题及答案

《现代设计方法》考题及答案机械与自动化学院普通硕士研究生《现代设计方法》考试试题姓名:专业:研究方向:成绩:一、填空题(每题1分,共15分)1、现代设计所指的新兴理论与方法包括(现代设计方法学、计算机辅助设计技术、可信性设计技术)等等。
2、优化设计是(以数学规划理论为基础,以计算机为工具,优化设计参数)的一种现代设计方法。
3、功能设计法的基本过程包括(任务抽象、功能分解、功能载体、载体组合、方案评价)。
4、功能分解的常用方法有(按解决问题的因―果关系,或手段―目的关系分解;、按产品工艺过程的空间顺序或时间顺序分解;)。
5、解决供求矛盾的措施有(互换性原理、组合机床、系列化、通用化、标准化)。
6、模块化设计可分类成(横系列模块化、纵系列模块化、跨系列、全系列模块化、跨类模块化)。
7、模块的划分将影响(模块通用性、产品性能、产品外观、产品成本)。
8、遗传算法是一种(模拟生物进化过程)的搜索算法。
9、遗传算法最常用和基本的选择方法(选择算子)是(适应度比例选择)。
10、遗传算法中采用罚函数法的目的是(对违背约束条件的情况给予惩罚,并将此惩罚体现在目标函数设计中。
2.2)。
11、遗传算法常用的编码方法有(二进制编码二进制编码方法、格雷码编码方法、实数编码、多参数级联编码)等等。
12、神经网络的样本数据应包括(训练样本数据和检验样本数据)。
13、当神经网络的样本数据不在[0~1]范围内时,应对数据进行(归一化)处理。
14、前馈型人工神经网络包括(1、线性阈值单元组成的前馈网络2、非线性单元组成的前馈网络输入层、隐层和输出层)3章。
15、神经网络的学习规则有(Hebb学习规则、感知器(perceptron)学习规则、Delta学习规则、Widrow-Hoff 学习规则)2章。
二、选择题(每题1分,共10分)1、在遗传算法中,若两个个体的二进制编码为01111、*****,以这两个个体为双亲,随机地选一个交叉点(如第二点),交叉点后的基因链码相互交换,从而产生两个新个体作为后代。
车辆现代设计方法

车辆现代设计方法车辆现代设计方法:让你的座驾“酷”到没朋友嘿,朋友!今天咱来唠唠车辆现代设计方法,这可是能让你的车从“路人甲”秒变“超级巨星”的秘籍哦!第一步,咱得先有个“梦想蓝图”。
这就好比你要盖个超级豪华大别墅,总得先在脑子里把那金碧辉煌的样子给想出来对吧?对于车呢,你得先想好你想要它长成啥样,是酷炫的跑车风,还是稳重大气的商务范,或者是萌到爆的可爱型。
我跟你说,我有次做梦,梦到自己设计了一辆车,那造型,跟个大汉堡包似的,轮子还是甜甜圈!哈哈,当然这只是个奇葩的梦,咱可不能真这么搞。
确定了整体风格后,接下来就是“骨架搭建”。
这就像是人的骨头,得结实还得合理。
要考虑车辆的结构强度,哪里放发动机,哪里坐人,怎么保证碰撞的时候咱们不变成“肉饼”。
这可不是闹着玩的,要是结构没设计好,开着开着车散架了,那可就悲剧啦!然后呢,到了“外观美容”环节。
这就好比给人化妆,得让车的线条流畅,颜色炫酷。
你想想,一辆车要是长得歪瓜裂枣的,谁愿意多看一眼?我见过一辆车,那前脸设计得,跟被谁揍了一拳似的,丑哭了!咱们可不能犯这样的错误,得让车的外观帅到让人忍不住流口水。
再说说“内饰装修”。
车内得舒服啊,座椅要像大沙发,操控台要简洁明了,别搞那些密密麻麻的按钮,看得人眼花缭乱。
有一回我坐进一辆车,找个车窗升降按钮找了半天,还以为是啥高科技隐藏式的,结果发现就是设计得太奇葩了,这不是给自己找麻烦嘛!还有很重要的一点,就是“科技武装”。
现在都啥时代了,车也得跟上潮流。
什么自动驾驶辅助、智能互联系统,能装上的都给它装上。
想象一下,你坐在车里,动动嘴就能控制一切,那感觉是不是爽歪歪?另外,“节能减排”也不能忘。
咱可不能光图车跑得快,还得让它少“喝油”,少排放。
这不仅省钱,还环保,为咱们的地球妈妈出份力。
不然以后地球变成个大“毒气室”,咱们都没地方跑啦!最后,可别忘了“测试检验”。
就像考试一样,得看看咱这设计到底合不合格。
跑一跑,颠一颠,各种路况都试试,有问题赶紧改。
汽车现代设计理论与方法

汽车现代设计理论与方法汽车现代设计理论与方法试题答案1、用结构框图表示并行工程的一般步骤,列出每一步中涉及到的关键技术。
(1)并行工程的产品开发工程:(2)并行工程的运行模式:(3)并行工程(ce)的关键技术:①多功能内置产品开发团队;②产品开发的过程建模;③产品生命周期数字化建模;④产品数字管理;⑤质量功能配置;⑥面向x的设计;⑦并行工程集成框架。
2、详述动态设计包含的主要内容,动态设计过程使用的建模方式就是什么?主要内容:所谓“动态设计”是指机械结构和机器系统的动态性能在其图纸的设计阶段就应得到充分考虑,整个设计过程实质上是运用动态分析技术、借助计算机分析、计算机辅助设计和仿真来实现的,达到缩短设计周期、提高设计效率和设计水平的目的。
机械系统的动态特性就是指机械系统本身的固有频率、阻尼特性和对应于各阶固有频率的振型以及机械在动载荷促进作用下的积极响应。
机械系统动态设计的主要包含两个方面:1)创建一个切合实际的机械系统动态力学模型,从而为展开机械系统动态力学特性分析提供更多条件;2)挑选有效率的机械系统动态优化设计方法,以赢得一个具备较好的机械系统动态性能的产品结构设计方案。
机械系统的建模方法分为两大类:理论建模法、实验建模法。
(1)理论建模法按机械系统相同而使用相同的技巧,因而存有多种方法(通常主要使用有限元方法和传达矩阵法);(2)实验建模法是指对机械系统(实物或模型)进行激振(输入),通过测量与计算获得表达机械系统动态特性的参数(输出),再利用这些动态特性参数,经过分析与处理建立系统的数。
3、什么就是平稳设计?平稳设计中主要牵涉了哪些模型和方法?稳健性设计①起源:这种新的设计概念认为:使用最昂贵的高等级、一致性最好的元器件并不一定能组装出稳健性最好的整机,成本最高,并不一定质量最好。
产品抗干扰能力的强弱主要取决于各种设计参数(因素)的搭配。
设计参数搭配不同,输出性能的波动大小不同,平均值也不同。
现代汽车设计方法概论

现代汽车设计方法概论计算机学院张洋100610892012年4月23日一、汽车概述1、汽车工业的发展汽车诞生于德国、成长于法国、成熟于美国、发展于欧洲、挑战于日本。
1886年德国人奔茨和戴姆勒发明了汽车后,在欧洲出现了一些生产汽车的公司。
最早成立的汽车公司有德国的奔驰公司、戴母勒公司、法国的标致公司、雷诺公司、英国的奥斯汀公司、意大利的菲亚特公司等,欧洲是汽车工业的摇篮。
德国人发明了汽车,而促进汽车发展的是法国人。
1891年法国人阿尔芒•标致对汽车结构进行了重新设计:发动机前置,后轮驱动,脱离了马车式的设计思路,奠定了传动系的基本构造,汽车制造也从德国移向了法国。
但手工生产,追求豪华,成本高,限制了汽车工业的发展。
●第一次变革(成熟于美国)1903年,亨利•福特汽车公司成立。
1908年推出了大众化的T型车,使家庭轿车的梦想成为现实,在长达20年的T型车生产期间,T型车被称为“运载整个世界”的工具。
1913年福特汽车公司在汽车城底特律市建成了世界上第一条汽车装配流水线,使T 型车成为大批量生产的开端,1915年,福特汽车公司的产量占美国各公司总产量的70%,而德、英、法等欧洲各国的汽车总产量也不过是美国汽车产量的5%。
1908年美国通用汽车公司成立。
由于亨利•福特不注重T型车的改进,使其显得单调、简陋。
1927年带有豪华饰件的通用公司的雪佛兰型汽车赢得了人们的普遍欢迎,击败了独霸世界汽车市场20年的福特T型汽车,使其最终退出了汽车舞台。
●第二次变革(发展于欧洲)欧洲人不甘心美国汽车一统天下,但又无法在规模和价格上与美国竞争,因此,采用了:1、品种多样化利用自己的技术优势,针对美国车型单一、体积庞大、油耗高等弱点开发了多姿多彩的新产品,如发动机前置前驱动,发动机后置后驱动,承载式车身,微型节油车等,尽量适应不同的道路条件、个人爱好等要求,与美国汽车公司抗衡。
2、取消欧盟各国关税20世纪50年代末至60年代初,欧盟取消各国关税,各国汽车可在欧洲自由销售,多样化的设计一下子变成了最大优势,世界工业重心一下子由美国移向西欧。
太原理工大学研究生考试参考书目
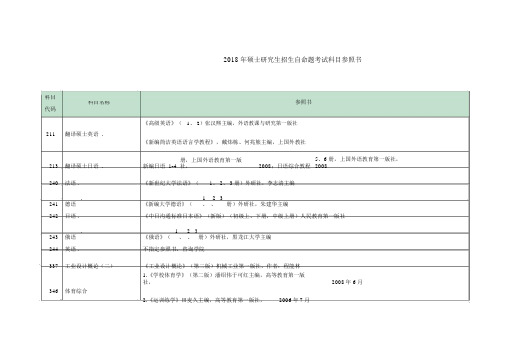
2018 年硕士研究生招生自命题考试科目参照书科目参照书科目名称代码《高级英语》(1、 2)张汉熙主编,外语教课与研究第一版社211翻译硕士英语 .《新编简洁英语语言学教程》,戴炜栋、何兆熊主编,上国外教社213 翻译硕士日语 . 新编日语 1-4 册,上国外语教育第一版社,2008;日语综合教程5、6 册,上国外语教育第一版社,2008240 法语 . 《新世纪大学法语》(1、 2、 3 册)外研社,李志清主编241 德语.《新编大学德语》(1 2 3册)外研社,朱建华主编、、242 日语 . 《中日沟通标准日本语》(新版)(初级上、下册,中级上册)人民教育第一版社243 俄语.《俄语》(1 2 3册)外研社,黑龙江大学主编、、244 英语 . 不指定参照书,咨询学院337 工业设计概论(二)《工业设计概论》(第二版)机械工业第一版社,作者:程能林1.《学校体育学》(第二版)潘绍伟于可红主编,高等教育第一版社,2008年 6月346 体育综合2.《运训练学》田麦久主编,高等教育第一版社,2006年7月《适用翻译教程》增订本,冯庆华主编,上国外教社;357英语翻译基础《英汉翻译简洁教程》庄绎传编著,外语教课与研究第一版社359 日语翻译基础汉日翻译教程(重排版),苏琦,商务印书馆2008;日汉翻译教程,陶振孝,高等教育第一版社2007 448 汉语写作与百科知识中国文化读本,叶朗,外研社2008501 建筑设计建筑设计、城市设计、城市景观设计、室内设计类参照书502 历史建筑还原设计历史建筑设计类参照书;城市设计、建筑设计、室内设计类参照书505 艺术专业基础快题设计,各方向依据各自特色分别命题查核本方向的创作及艺术设计能力,要求考生自备颜料、制图尺等画具,考试时间为 5 小时506 设计基础各方向依据各自特色分别命题查核本方向的专业设计能力,要求考生自备颜料、制图尺等画具,考试时间为 5 小时1.《教育学》(第六版)王道俊,郭文安主编,人民教育第一版社(2009-05 第一版)610 专业综合基础2. 《运动生理学》(第二版)邓树勋,王健,乔德才主编,高等教育第一版社(2009-06 第一版)1. 《马克思主义基来源理概论》高等教育第一版社2013 版701 马克思主义基来源理2.《简洁马克思主义史》人民第一版社,庄福龄主编,2004 年1.《高级英语》(1、 2)张汉熙主编,外语教课与研究第一版社702英语综合2.《新编语言学教程》刘润清、文旭主编,北京外研社1. 田自秉:《中国工艺美术史》,北京,2012 年 08 年 01 日,东方第一版社2. 张夫也:《外国工艺美术史》,2003 年 09 月 01 日,中央编译第一版社703设计史论3.王受之:《世界现代设计史》(第 2 版), 2015 年 12 月 01 日,中国青年第一版社4.李砚祖:《艺术设计概论》,2013 年 04 月,湖北长江第一版社、湖北美术第一版社704 数学剖析《数学剖析》华东师大数学系编,高等教育第一版社(第三版)705 物理化学 A 《物理化学》傅献彩主编,高等教育第一版社706 建筑理论综合含中外建筑史、建筑知识综合708 一般物理《大学物理》第三版(上、下),王纪龙编,科学第一版社709 工业设计概论(一)《工业设计概论》(第二版)机械工业第一版社,作者:程能林美术领域:1.中央美术学院人文美术系外国史教研室:《外国美术简史》,北京,2014 年 10 月 01 日,中国青年第一版社;710 艺术史论2.中央美术学院美术史系,中国美术史教研室:《中国美术简史》,北京,2010 年 06 月 01 日,中国青年第一版社;3.彭吉象:《艺术学概论》(第 4 版),北京, 2015 年 05 月 01 日,北京大学第一版社;4.叶朗:《美学原理》,北京,2016 年 1 月,北京大学第一版社。
现代汽车的设计方法

现代汽车的设计方法现代汽车的设计方法是一个复杂而综合性的过程,它涉及到多个方面,包括外观设计、车身结构设计、动力系统设计、内饰设计、人机工程学设计等等。
现代汽车的设计方法主要可分为以下几个步骤:1. 市场调研:在设计一款新车型之前,汽车设计师需要进行市场调研,了解消费者的需求和喜好。
这样可以使设计师更好地把握市场需求和潮流趋势,确保设计的产品能够满足消费者的需求。
2. 概念设计:在进行市场调研后,设计师会进行概念设计,包括外观造型、车身结构、车辆比例等。
概念设计是一个创意过程,设计师需要将市场需求和自己的创意相结合,形成独特而富有吸引力的设计方案。
3. 造型设计:在概念设计确定后,设计师会进行具体的造型设计。
这一过程涉及到外观线条的塑造、曲线的修饰、细节的雕琢等。
设计师需要运用各种设计软件和工具,如CAD、CAM等,来实现设计图纸的绘制和模型的制作。
4. 工程设计:在完成造型设计后,设计师需要进行工程设计,包括车身结构设计、动力系统设计、底盘设计等。
这一步骤需要考虑到安全性、可靠性、乘坐舒适性等方面的要求。
设计师需要与工程师紧密合作,确保设计方案的可行性。
5. 内饰设计:在设计过程中,内饰设计也是非常重要的一环。
内饰设计需要考虑到人机工程学、乘坐舒适性、功能性等方面的要求。
设计师需要和工程师、人机工程学专家等密切合作,确保内饰设计与整车设计相协调。
6. 原型制作:在设计方案确定后,设计师会制作原型车或3D打印模型。
通过原型的制作,设计师可以更好地了解设计方案的实际效果,并进行调整和改进。
原型制作是设计过程中的一个关键环节。
7. 试制和测试:在原型制作完成后,设计师会进行试制和测试。
这一步骤涉及到车辆性能测试、安全性测试等,以确保设计方案的可靠性和安全性。
8. 生产准备:在设计方案得到验证和完善后,设计师需要进行生产准备。
这一步骤涉及到工艺设计、生产工艺准备、供应链管理等。
设计师需要和工程师、生产经理等密切合作,确保设计方案能够顺利投入生产。
【东大】21春学期《现代机械设计理论与方法》在线作业1满分答案

【东大】21春学期《现代机械设计理论与方法》在线平时作业1
提示:认真复习课程知识,并完成课程作业,本资料仅供学习参考!!
一、单选题 (共 7 道试题,共 35 分)
1.( ) 是比较分析两个对象之间某些相同或相似之点,从而认识事物或解决问题的方法。
【A项.】联想法
【B项.】类比法
【C项.】仿生法
[此题为必答题,请从以上选项中选择您认为正确的答案]
参考选项是:B
2.内燃机的实际输出功率称为()
【A项.】有效功率
【B项.】标定功率
【C项.】升功率
[此题为必答题,请从以上选项中选择您认为正确的答案]
参考选项是:A
3.机械设计学强调()来看机器的组成,因为这更有利于和设计过程中的工作特点相协调。
【A项.】从机构学的观点
【B项.】从结构学的观点
【C项.】从专业的角度
【D项.】从功能的观点
[此题为必答题,请从以上选项中选择您认为正确的答案]
参考选项是:D
4.功能原理设计的结果可以用()表达出来。
【A项.】装配图
【B项.】示意图
【C项.】总体布局图
【D项.】零件图
[此题为必答题,请从以上选项中选择您认为正确的答案]
参考选项是:B
5.布置传动系统时,一般把转变运动形式的机构(如凸轮机构、连杆机构等)布置在传动链的(),与执行机构靠近,这样安排可使传动链简单,且可减小传动系统的惯性冲击。
【A项.】低速端
【B项.】高速端
[此题为必答题,请从以上选项中选择您认为正确的答案]
参考选项是:A。
车辆现代设计方法

面饰工艺规程
各种制造、装配、
设
效果图、检验标准 造型、装饰、检 各种工艺学
计
技术文件
验等方法
造型工艺文件
试制 商
品 化
修改
批量生产
第三节 车辆的现代设计
车辆的现代设计方法
(1) 车辆计算机辅助设计CAD; (2) 车辆计算机辅助工程CAE; (3) 车辆优化设计; (4) 车辆可靠性设计; (5) 车辆性能的计算机仿真; (6) 车辆噪声分析及设计; (7) 车辆动态设计。 现代的汽车设计方法并不是各自孤立的,它们既有自己的优势, 又互相渗透,在汽车设计的技术领域中发挥着各自的重要作用。
1.产品规划阶段:决策开发新产 品,为新技术系统设定技术 过程和边界,明确设计任务。
2.原理方案设计阶段:新产品的 功能原理设计。
3.技术设计阶段:新产品最优原 理具体化。
4.施工设计阶段:技术设计的结 果变成施工的技术文件。
第二节 机械产品设计
产品设计一般进程
阶段
步骤
方法
信息集约(技术造型) 产品设计任务
第三节 车辆现代设计
计算机辅助工程CAE
主要内容 目前在汽车设计中,有限元方法普遍地应用于车架和车身的强
度计算、车架和车身的振动特性分析、车身的结构动态特性对车 内噪声的影响分析等。
在发动机的曲轴和连杆、变速器的壳体和齿轮、车桥的壳体 和齿轮、转向系的转向节臂、悬架系的钢板弹簧和导向装置、车 轮的轮辋、制动系的制动毂和制动盘等一些形状复杂的重要零部 件的应力和变形计算中,有限元方法也提供了有力的设计手段。
评价决策方法
系统工程学 形态学 创造学
思维心理学 决策论 模糊数学
第二节 机械产品设计
现代设计理论与方法作业-(大作业)

现代机械设计理论与方法(大作业)1、采用系统化设计流程及所学现代设计方法详细阐述某公司需要投资研发一款新型产品的整个设计流程和采用方法。
(1)请具体阐述采用哪些设计方法,如何去完成新产品的规划设计过程?(2)请具体阐述采用哪些设计方法,如何去完成新产品的方案设计过程?(3)请具体阐述采用哪些设计方法,如何去完成新产品的技术设计过程?(4)请具体阐述采用哪些设计方法,如何去完成新产品的施工设计过程?答:(1)产品规划设计包括三个主要阶段:第一个阶段是市场细分及选择阶段。
在这个阶段,主要通过市场调研与分析,研究如何细分市场,以及企业如何选择细分市场,最后确定企业对细分市场的战略选择。
第二个阶段是定义新产品概念。
在这个阶段中要对某个细分市场,收集其需求的主要内容,包括客户需求、竞争需求及企业内部需求,并确定企业在该细分市场的产品定位,然后寻找和定义新产品概念。
第三个阶段是确定产品规划阶段。
在这一阶段中需要从技术层面分析新产品属于哪个产品族及其开发路径,并根据公司的战略确定新产品开发的优先顺序和组合策略,然后依据企业资源状况,制定新产品开发的时间计划。
产品规划设计的步骤为:信息集约→产品设计任务→预测调研→可行性分析→明确任务要求→可行性报告、设计要求项目表。
进行产品规划设计的主要方法有:设计方法和预测技术。
支持产品规划设计的主要理论有:设计方法学、技术预测理论、市场学、信息学等。
(2)新产品的方案设计过程大致可以分为方案设计和方案评审两个阶段。
方案设计阶段的步骤为:总共能分析→功能分解→功能元求解→功能载体组合→获得功能原理方案(多个原理方案)→原理试验→评价决策→最优原理方案→原理参数表、方案原理图。
进行产品的方案设计的方法主要有:系统化设计方法、创造技法、评价决策法、形态学矩阵法。
主要的理论指导包括:系统工程学、形态学、创造学、思维心理学、决策论、模糊数学等。
(3)对产品进行技术设计时,首先要对结构进行总体设计,包括了对产品的结构设计和造型设计。
基于现代设计方法的r研究生科研能力培养实践运用r——以《车辆现代设计方法》课程为例

基于现代设计方法的r研究生科研能力培养实践运用r——以《车辆现代设计方法》课程为例于国飞;盛精;王海兵【摘要】以厦门理工学院研究生学位课程《车辆现代设计方法》为例,探讨专业型硕士研究生的科研能力培养模式,针对不同专业的硕士生,选择适合各自研究方向的车辆现代先进设计方法,达到快速有效精确地设计车辆零部件、各总成和整车,预测分析车辆性能的能力目标.汇总多种车辆现代设计方法,以归纳总结案例教学模式为主体,采用有效的教学方法和教学手段,提高研究生独立分析问题和解决问题的科研能力,使其尽快进入所学专业研究方向的科研状态,达到案例分析—课题研究一体化目的,为其后续顺利进入课题研究奠定良好的基础.【期刊名称】《教学研究》【年(卷),期】2018(041)003【总页数】5页(P65-69)【关键词】现代设计方法;专业硕士研究生;案例教学;案例课题一体化【作者】于国飞;盛精;王海兵【作者单位】厦门理工学院机械与汽车工程学院;福建省客车和特种车辆协同创新研究与开发中心,福建厦门 361024;厦门理工学院机械与汽车工程学院;福建省客车和特种车辆协同创新研究与开发中心,福建厦门 361024;厦门理工学院机械与汽车工程学院【正文语种】中文【中图分类】G643.20 引言厦门理工学院(以下简称学院)研究生院招收专业型硕士研究生已有6届,招生人数逐年增加,所招收专业以车辆工程和电气工程为主,而研究的课题则因学生选择导师不同而有明显的差异。
来自不同大学的学生,其本科阶段的专业背景也有所不同,主要是以车辆工程专业、机械制造专业、汽车服务工程、汽车运用工程、电气工程、自动化专业、材料科学与工程等专业为主。
《车辆现代设计方法》课程(以下简称课程)是学院车辆工程专业硕士研究生培养方案的专业学位课。
首届研究生授课时,并没有合适的教材,而是选用机械类现代设计方法课程教材为试用教材,利用网上资料和笔者课题组多年的研究成果,归纳总结不同的车辆现代设计理论和方法,以案例教学方式为研究生讲解。
- 1、下载文档前请自行甄别文档内容的完整性,平台不提供额外的编辑、内容补充、找答案等附加服务。
- 2、"仅部分预览"的文档,不可在线预览部分如存在完整性等问题,可反馈申请退款(可完整预览的文档不适用该条件!)。
- 3、如文档侵犯您的权益,请联系客服反馈,我们会尽快为您处理(人工客服工作时间:9:00-18:30)。
1.自从汽车问世以来,车辆的设计方法经历了变革,请论述你对车辆现代化设计及其本质的理解,给出传统设计和现代化设计间的区别。
(30分)答:现代设计方法是在传统方法的基础上,不断吸收现代理论、方法和技术以及相邻学科最新成就发展起来的。
所以现代设计和传统设计并不是相互对立甚至割裂的,而是对传统是、设计方法的继承和发展。
总的来说,设计方法的区别主要体现在以下几点:设计手段计算机化、设计范畴扩展、设计制造一体化、设计过程智能化、多种手段综合应用、设计寻求最优化、重视产品宜人性、强调产品环保性。
回顾机械设计发展简史,不难发现传统的设计学只是机械学,主要研究运动学,动力学,强度,断裂,摩擦等问题。
而现代设计方法可以描述为以满足应市产品的质量、性能、时间、成本/价格综合效益最优为目的,以计算机辅助设计技术为主体,以知识为依托,以多种科学方法及技术为手段,研究、改进、创造产品活动过程所用到的技术群体的总称。
从以上对于现代设计方法的定义可以看出:现代设计技术有以下两个明显特点:(1)现代设计技术是多学科交叉融合的产物。
就目前现代设计技术所涉及的理论、方法的范畴来看,可以认为它是由现代设计方法学、计算机辅助设计技术、试验设计技术等多种学科的交叉与融合。
而其中每一个具体的设计技术,同样也是若干学科的交叉与融合。
例如计算机辅助设计可以看作是数学建模、计算机软件和硬件技术、工程图学等的有机结合;模糊优化设计是模糊方法与优化技术的结合等等。
在这个现代设计技术群体各学科之间既相对独立又相互联系、相互渗透。
根据设计对象与任务的不同,以及设计各个阶段的特点,宜采用其中某些适宜的、有效的方法和技术,以解决设计中的总体和各个具体问题。
(2)现代设计是传统设计技术的继承、延伸和发展。
从传统设计发展至现代设计,都有着时序性、继承性,并在一定时间和一定的对象中它们共存于一体。
例如,传统的运动学、动力学、机构学、结构力学、强度理论等基本原理与方法是现代设计技术的数学建模及许多分支学科(如可靠性设计、疲劳设计、防断裂设计、健壮设计等)的基础;另外,许多现代设计技术与方法是在吸收了传统设计技术中的思想、观点、方法之精华而发展起来的,如系统设计、功能设计、模块化设计、优化设计、并行设计等。
2.结合你的研究方向或工作基础,举例说明在车辆现代化设计中如何实现优化设计和计算机辅助设计。
(30分)答:(1)优化设计在汽车上的应用①车架结构优化设计车架的作用是承受载荷,包括汽车自身零部件的重量和行驶时所受的冲击、扭曲、惯性力等。
根据纵梁的结构特点,车架可以分为周边式、X型式、梯形、脊梁式和综合式几种。
其中梯型车架又称为边梁式车架,是比较常用的一种车架。
下面以边梁式车架的客车结构为模型。
车架的纵梁结构一方面要保证车架的功能,另一方面还要满足整车总体布局的要求,同时要求形状简单。
纵梁的形状有上翼面是平直的和弯曲的两种:上翼面平直式的车厢地板平整纵梁制造方便;翼面弯曲式纵梁部分区段降低,地板相应高度降低,车辆的稳定性增强。
车架在使用中会受到负载弯曲(Vertical bending),发生非水平扭动 (longitudinal torsion)、横向弯曲(lateral bending)、水平菱形扭动(horizontal lozenging),为在确保车架结构稳固的情况下提高车辆的平稳性和路面适应性,设计的时候应尽量达到最优平衡,必须的应用优化设计,其对车架设计与制造的重要性不言而喻。
在对大客车车架进行优化设计时,首先应确定设计变量。
由于车架一般是槽型的,矩形的或者工字形的,优化目的是要减轻车架的质量,所以选择钢的截面形状参数(截面长度、宽度和钢的厚度) 来作为设计变量。
其次是确定目标函数,优化的目的是尽量减少客车底架的质量, 所以对于槽型钢目标函数F =LρT ( H + 2 B) ,对于矩形钢F = L ρT (2 H + 2 B) 。
其他的还包括状态变量的确定,即优化过程中的车架结构响应,如应力、变形和车架的最大应力要小于许用应力。
②发动机优化设计发动机设计以结构、热力、燃烧、强度、振动、流体、传热等多个学科为基础,可变因素多,随机性大,是一个可变互耦系统的优化问题。
为了降低汽车的耗油量和废气排放,我们一般采用优化匹配动力传动系统。
因为汽车的动性燃油经济性和排放特性的好坏在很大程度上取决于发动机的性能和传动系形式参数的选择。
利用计算机对汽车动力传动系统进行模拟仿真计算,通过对汽车动力传动系参数的优选,从而达到改善汽车的燃油经济性、动力性和尾气排放。
发动机结构优化主要是优化关键零部件的形状以改善发动机性能。
有人提出了一种将动态分析与结构形状优化设计相结合的新方法:阐述了 CAD/CFD 技术在汽车发动机设计开发中的重要性,给出了 CAD/CFD 技术在电喷汽油机气歧管设计和柴油机螺旋气道设计的应用效果;将边界元法与罚函数优化方法相结合,研究了承受拉、压交变载荷的发动机连杆的形状优化;基于一种高效的有限元方法对三维复杂形状连杆进行优化设计;基于有限元分析和优化技术,对发动机曲轴的结构进行了优化等。
发动机的燃烧过程同样是优化的重要方面。
目前主要是从喷射系统、进气管系、燃烧室形状等几方面对其进行优化设计。
在发动机燃烧喷射系统方面,借助于先进电子控制技术,能准确地调节燃油供给,优化喷油定时和喷油次数,控制气缸内的混合状态、燃烧室内的燃油分布,降低排放污染。
③CAE在汽车冲压件生产工艺中的优化应用冲压件在最初设计阶段采用CAD和CAE相结合技术, 根据CAE的成本计算结果,调整几何形状,使冲压件展开后的外轮廓面积最小, 结合 FormingSuite 、Costoptimizer 优化软件包,对汽车冲压件的仿真工艺设计过程进行分析,通过降低材料等级、厚度和增大冲压件设计的圆角半径及修剪冲压件的边缘各项措施, 达到降低材料成本的目的。
在钣金冲压件和工艺设计阶段, 对于已有的冲压件,不能预知坯料的几何形状,可结合拉延件产生起皱状况, 通过快速冲压CAE 分析, 找到合理的拉延成形条件,加速冲压件开发进度。
结合有限元软件,通过计算机模拟、分析冲压件的冲压可行性,设计阶段利用各种降低成本的措施,达到了大大降低生产成本的目的, 分析结果指导制定合理的冲压工艺。
对于汽车零件, 若表面质量要求不高, 起皱部位无需严格控制; 若冲压件对表面质量要求较高时,则可通过适当增大压边力、添加拉延筋等工艺措施消除起皱,满足控制冲压件外观质量的要求。
以有限元法为基础的冲压成形过程中计算机仿真技术或数值模拟技术,为模具设计、冲压过程设计与工艺参数优化提供了科学的新途径, 将是解决复杂冲压过程设计和模具设计的最有效手段。
④优化设计在汽车零部件轻量化中的应用汽车轻量化已成为整车企业适应市场发展趋势的必然要求。
目前,对于现有车型的轻量化,主要方法是从零部件轻量化做起.逐步积累。
最终满足整车轻量化的目标。
对零件实现轻量化时主要借助CAE方法重新对其结构进行优化设计,以分析校核——优化分析设计——再次分析校核的“循环式”方法减轻零件的重量并提高强度。
(2)计算机辅助设计在汽车上的应用随着计算机辅助软件设计技术的日益成熟,在汽车方面应用越来越广。
CAD、CAM、CAE技术的发展及其在汽车车身设计中的广泛应用,现代汽车车身设计在深层次发生着巨大的变化,计算机辅助软件已成为推动汽车技术变革的主要力量。
计算机辅助设计技术,将计算机迅速、准确地处理信息的特点与人类的创造思维能力及推理判断能力巧妙地结合起来,用计算机硬件、软件的新成就,特别是计算机绘图、数据库、智能模拟技术等,为现代设计提供理想手段;结合计算机辅助制造(CAM)技术,能与数控加工技术配合,用于机械制造以及设计中。
下面以车身设计为例,来说明计算机辅助设计用UG画出车身草图,如图1所示图1再对车身进行拉伸,如图2所示图2最后画车窗和轮拱,如图3此车在焊接处均采用圆角处理,美观大方。
并且车窗面积大,视野开阔,可减少因视线不好而引起的交通事故。
3.以你的研究方向为基础,通过在CNKI上查取相关资料,写一篇3000字内的文献综述,对国内外现代化的设计方法进行综合论述。
(40分)现代设计方法在汽车设计中的应用摘要:现代科学技术的发展对汽车的性能、可靠性、经济性等提出更高的要求,同时也为汽车的设计、制造提供了改进和创新的设计方法。
本文将现代设计技术与传统设计方法进行了简单的对比,简要介绍了现代设计技术的新方法,其中重点论述了现代设计技术在汽车设计中的应用。
关键词:现代设计技术;汽车设计;人机工程;造型设计;虚拟设计;绿色设计Abstract: The development of modern science and technology to the car's performance, reliability, economy and put forward higher requirements, but also for car design, manufacture provides improved and innovative design. In this paper, modern design techniques and traditional design methods were simple comparison, a brief introduction of new methods of modern design technology,which focuses on the application of modern design technology in the automotive design.Key Words: modern design techniques ;automotive design ;virtual design ;ergonomic design ;green design1.引言先进制造技术(AMT)是保障制造业高水平持续快速发展的基础。
21世纪是知识经济时代,用户针对产品的T、Q、C、S、E5项市场竞争指标,将传统制造技术与飞速发展的计算机技术、信息技术、自动化技术、现代管理技术及系统技术有机融合,逐渐研究形成了新一代先进制造技术。
现代设计技术是先进制造技术的一个组成部分,是制造技术的第一个环节。
据统计,一汽车的质量和性能有60%~70%取决于汽车设计。
因此,在设计新产品时应研究和采用新的设计方法和技术,以适应现代汽车发展的要求。
2.现代设计和传统设计的比较传统的设计方法是以经验总结为基础,运用力学和数学而形成的经验、公式、图表、设计手册等作为设计的依据,通过经验公式、近似系数或类比等方法进行设计。