BGA虚焊问题分析报告
BGA虚焊问题分析报告
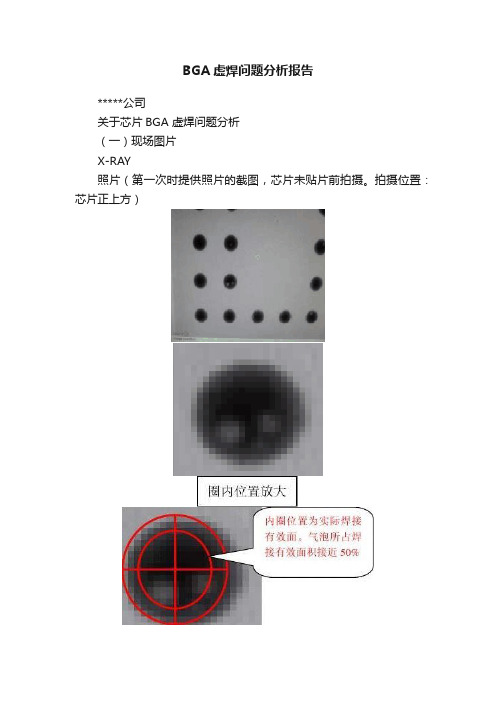
BGA虚焊问题分析报告*****公司关于芯片BGA 虚焊问题分析(一)现场图片X-RAY照片(第一次时提供照片的截图,芯片未贴片前拍摄。
拍摄位置:芯片正上方)回流焊后异常芯片剥离照片问题芯片剥离图片放大图片1位置放大图片2位置问题芯片剥离图片细节放大放大图片1 放大图片2放大图片3回流焊后检测合格芯片剥离照片(芯片焊接面100%剥离)放大图片4(二)图片分析1.图片1焊接面使用高倍显微镜观察:锡面灰暗,空洞很多。
请特别注意红框位置;2.锡面灰暗应是焊锡高温氧化的迹象。
我们认为这里的锡面氧化应是在回流焊的高温影响后发生。
发生的原因与植球与芯片焊面的虚焊有关,并且这种虚焊在回流焊时无法得到改善。
我们认为芯片植球时已存在异常,导致植球与芯片接触面未初步形成有效地IMC(红色框)。
综合后我们认为植球与芯片间的有虚焊现象。
正常时植球后应该形成初步的焊点。
3.空洞较多也说明植球与芯片焊接面存在异常情况的发生;4.根据材质及焊接结合力、拉力分析:我们认为良好的植球与芯片形成良好的IMC后,当我们剥离芯片时大部分的芯片焊接面应被拉起脱落(各图片的蓝色框)。
而且我们剥离的合格芯片产品的焊接面观察,在芯片剥离后确实也是100%脱落(见放大图4)。
而有问题的芯片仅有四点拉脱(见回流焊后异常芯片剥离照片蓝色框);5.我司在外协厂贴片后植球与PCB间形成了良好的IMC,(参见图片3中的紫色框体内)。
整体移除锡球后没有看见异常现象。
(三)图片分析结论1.供方提供的芯片在植球时已出现植球与芯片有效焊接面的虚焊及不确定异常导致的较多空洞现象;2.供方植球时已出现植球与芯片有效焊接面的虚焊及不确定异常导致的较多空洞现象直接导致了SMT回流焊后无法调校的缺陷:芯片焊接面与植球间的虚焊或简单称为融合异常问题在回流焊后没有改善,导致芯片功能异常;(四)供方的回复(以下原文)发件人: **********发送时间: 2010年**月**日 ****收件人: *********主题: RE: Fw: 植球不良照片Hi ******空洞和虚焊是两个概念。
BGA失效分析报告
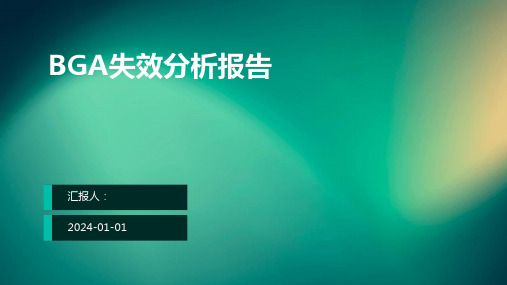
随着电子设备向高集成度、高可靠性 方向发展,BGA封装广泛应用于各类 电子产品中。然而,BGA失效问题逐 渐凸显,对产品性能和可靠性产生严 重影响。
BGA封装介绍
01
BGA封装特点
高密度、低电感、低热阻、易于 实现高速信号传输等。
02
BGA封装工艺流程
03
BGA失效类型
芯片粘接、引脚焊接、塑封固化 等。
01
03
一款笔记本电脑在使用过程中频繁出现蓝屏和死机现 象,拆解后发现芯片与BGA基板间的粘接材料老化,
芯片脱落导致电路故障。
04
一款平板电脑在使用过程中突然发生屏幕破裂,经检 查发现BGA封装体存在制造缺陷,无法承受机械冲击 。
失效影响分析
性能下降
BGA失效会导致电路性能下降,引发 各种故障现象,如死机、重启、数据 丢失等。
可靠性。
04 BGA失效预防和改进措施
优化封装设计
优化封装设计是预防BGA失效的重要 措施之一。
通过改进BGA的封装设计,可以减少 潜在的缺陷和问题,提高其可靠性和 稳定性。这包括优化焊球间距、改进 焊球材料和减小焊球直径等措施。
提升制造工艺水平
提升制造工艺水平是降低BGA失效风险的关键。
通过采用先进的制造技术和设备,提高BGA的制造精度和一致性,可以显著降低制造过程中可能出现的缺陷和问题。这包括 采用高精度的焊接设备、优化焊接工艺参数和加强过程控制等措施。
BGA失效进行分析和预测,为预防性维护提供支持。
THANKS FOR WATCHING
感谢您的观看
安全风险
对于关键性电子设备,BGA失效可能 引发严重安全问题,如设备损坏、数 据泄露或人身伤害等。
生产成本
PCBA之BGA虚焊原因及改善

PCBA之BGA焊点“虚焊”一、概念:电路板调试过程中,会出现“BGA器件外力按压有信号,否则没有信号的现象",我们称之为“虚焊”。
二、原因分析:从焊点的形貌方面分析,BGA焊点的接收标准在IPC-A-610D中的定义为:优选的BGA经X光检测,焊点光滑、边界清晰、无空洞,所有焊点的直径、体积、灰度和对比度均一样,位置准确,无偏移或扭转,无焊锡球,如图1所示。
实际经验得出明显的虚焊焊点形状不规则或圆形四周不光滑或焊点尺寸小,如图2所示。
图1 图22.1焊球及焊盘表面氧化若器件焊球氧化或PCB板焊盘氧化,焊料很难与焊盘之间形成牢固的冶金结合,从而不能提供持续可靠的电气性能,即表现为“虚焊”现象。
2.2焊点裂纹若BGA焊点在界面处出现裂纹,从而导致机械及电气性能失效,我们也称之为“虚焊”。
BGA焊点裂纹主要是因为PCB基板和元器件的基膨胀系数不匹配(FR4的CTE为18ppm/℃,而硅芯片的CTE为2.8ppm/℃),焊点中存在残余应力而导致的。
BGA焊点(无论是SnPb还是SnAgCu焊点)裂纹绝大多数都是出现在焊球与器件的基板之间,即封装一侧,并且裂纹非常靠近封装一侧的金属间化合物。
软件模拟与试验结果是吻合的。
个人认为这种结论在一定程度上暴露了器件本身存在的质量问题。
如图3、4为BGA焊点的金相分析图及光学检测图,裂纹出现在器件上端。
IPC-A-610D中指出:只要裂纹底部不深入到焊点内部影响电气及力学性能就能判定为合格。
但如果焊点中有裂纹,可能暂时不会影响整机的电气性能,但是在高低温循环或冲击的载荷下裂纹进一步扩展使焊点断开,则会导致整机失效。
因此在实际生产中,尤其是军品,BGA焊点是不允许出现裂纹的。
2.3冷焊焊点在回流阶段,如果焊料在液相线以上温度时间过短,焊料与焊球还没有充分融合到一起随即进入冷却区,这样就会出现冷焊焊点,这种焊点表面粗糙,长期可靠性差,很容易引起焊点失效,形成“虚焊”。
BGA虚焊分析报告
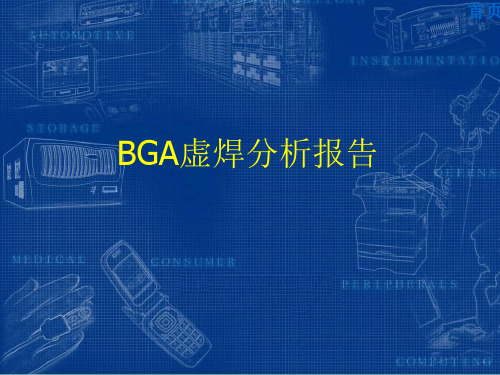
9号板卡 U1球与元 器件焊盘 之间厚度
11号板卡 U1球与元 器件焊盘 之间厚度
实验
9号板卡U1球 与PCB焊盘之
间厚度, 1~4um之间,
焊接良好
11号板卡U1球 与PCB焊盘之
间厚度, 1~4um之间,
焊接良好
• 实验
6、切片实验结论如下所示
2、 5482S器件批次质量问题,导致虚焊。 BGA来料异常,BGA锡球破损、氧化等等,导致BGA虚焊。
3、 无铅器件和有铅焊锡工艺,导致虚焊。 生产过程中,工艺参数设定不当,如回流焊设定、印刷机参数设定等等,导致虚焊。
针对上述原因,在即将进行的20套BBBC生产过程中,相关的工艺、质量人员将对BGA来料以及工艺参数 进行严格管控,以消除物料及生产方面的原因而造成的虚焊,具体措施请见下文所示
3、生产前确认物料状况,如无真空包装,上线前一律进行烘烤,并 检验BGA外观
4、优化工艺参数,确保BGA焊接质量(为优化工艺参数,需要申请一 块成品实物板uCCT量测回流焊曲线)
尾页
谢谢!
首页
BGA虚焊分析报告
概述
• 工位
中试测试线
• 现象
PCBA板卡导致基站无法启动问题
• 问题描述
7月29日中试测试线发现的PCBA板卡导致基站无法启动问题,经 初步定位为U2等位置虚焊,物料编码为: XXXXXXX,物料MPN: MPNXXXX,BGA锡球:11*11=121;该物料在 PCBA上有四个用量,位 号分别为U1,U2,U3,U4;测试过程中,发现U1,U2易发生虚焊
形状
• 实验
实验
为进一步确认BGA焊接效果,随机抽取两块板卡,委托中国赛宝华东实验做切片实验,实验过程如下所示: 1、两块板卡,编号为0009,0011;切片观察U1,U2,U4所有BGA锡球
BGA不良分析、改善报告

小结
对BGA、PCB、锡膏的来料质量的严格把控,对提升 BGA上线合格率有很大帮助。须确保以下三点:
1.选择高端的有质量保证的供应商; 2.对来料要进行必要的检验,保证上线质量; 3.BGA、PCB板、锡膏来料储存、使用要符合工艺要
求。
返回
2.SMT制程控制
在SMT制程中导致BGA失效的工艺环节和原因 很多,比如ESD、钢网开孔、锡膏印刷、贴片、 回流焊接、炉温板制作等等,要想降低SMT制 程中BGA的失效,需要在多方面进行全面控制。
●浸润阶段 这一阶段助焊剂开始挥发。温度在150℃~ 180℃之间
应保持70~90 秒,以便助焊剂能够充分发挥其作用。
●回流阶段 这一阶段的温度已经超过焊膏的熔点温度,焊膏熔化
成液体,元器件引脚上锡。该阶段中温度在220℃以上 的时间应控制在50 ~ 90 秒之间。如果时间太少或过 长都会造成焊接的质量问题。BGA焊点峰值温度应该 控制在240~250 ℃。 ●冷却阶段 这一阶段焊膏开始凝固,元器件被固定在线路板上。 同样的是降温的速度也不能够过快,一般控制在4℃/ 秒 以下,较理想的降温速度为3℃/秒。由于过快的降 温速度会造成线路板产生冷变形,它会引起BGA焊接 的质量问题,特别是BGA外圈引脚的虚焊。
二、计划&生产管控 1. OSP PCB生产必须于拆封后24小时内完成SMT,生管计划根据SMT的
工时排线,不得超过规定时限。 2. 计划把握进料状况. 料齐后才可以安排上线。 3. BGA一般布置在PCB的B面,先生产完A面后,B面有机防护膜被高温破
坏,所以,计划需要保证生产连续性,要求A面生产后,B面生产时间 间隔不超过24小时。 4. OSP工艺PCB一般不要烘烤;如果回潮必须要烘烤,条件:100℃,4h。 5. 生产时不能一次拆很多包,使用完一包再拆一包; 6. 禁止裸手接触PCB板内元件焊盘。 7. 拆包前检查包装是否破裂,确认PCB焊盘是否变色,如果变形,需要 退回仓库,待供应商重工处理。
光机检测BGA 焊球虚焊情况分析

06 未来研究方向
提高光机检测技术的精度和稳定性
优化光机检测系统
通过改进光学元件、提高成像质量、降低噪声 等手段,提高检测精度。
引入人工智能技术
利用深度学习、机器学习等技术,对图像进行 自动识别和分析,提高检测速度和准确性。
数据分析结果
01
虚焊焊球直径较小,高度较低,与正常焊球相比存在明显差异。
02
虚焊焊球与焊盘的相对位置关系发生变化,偏离正常位置。
虚焊焊球的颜色和亮度与正常焊球存在差异,可以通过图像处
03
理算法进行识别。
结论与建议
根据数据分析结果,可以得出BGA焊球虚焊的特征和规律,为后续的虚焊检测提供 依据。
建议在生产过程中加强质量控制,定期进行BGA焊球虚焊检测,及时发现并解决虚 焊问题,提高产品质量。
高精度和高效率
光机检测技术具有高精度和高效率的特点,能够 快速准确地识别出焊球的虚焊问题,提高生产效 率。
自动化程度高
光机检测技术可实现自动化检测,降低人工干预 和误差,提高检测的一致性和可靠性。
04 光机检测BGA焊球虚焊实 验
实验设备与材料
实验设备
高分辨率光学显微镜、高精度图 像采集系统、计算机分析软件
根据软件分析结果,判断BGA焊球是否存 在虚焊现象,并记录实验数据。
实验结果与分析
结果
通过实验获取了大量BGA焊球图像,并分析了不同条件下 BGA焊球的虚焊情况。
分析
通过对实验数据的分析,得出了BGA焊球虚焊的主要原因包 括焊接工艺参数不当、焊球与基板不匹配、焊料质量不佳等 。同时,还探讨了如何优化焊接工艺参数、选择合适的焊球 和焊料等措施来减少虚焊现象的发生。
BGA不良分析改善报告

二、计划&生产管控 1. OSP PCB生产必须于拆封后24小时内完成SMT,生管计划根据SMT的
工时排线,不得超过规定时限。 2. 计划把握进料状况. 料齐后才可以安排上线。 3. BGA一般布置在PCB的B面,先生产完A面后,B面有机防护膜被高温破
坏,所以,计划需要保证生产连续性,要求A面生产后,B面生产时间 间隔不超过24小时。 4. OSP工艺PCB一般不要烘烤;如果回潮必须要烘烤,条件:100℃,4h。 5. 生产时不能一次拆很多包,使用完一包再拆一包; 6. 禁止裸手接触PCB板内元件焊盘。 7. 拆包前检查包装是否破裂,确认PCB焊盘是否变色,如果变形,需要 退回仓库,待供应商重工处理。
本文主要针对BGA失效原因及质量提升方法进行分析,并提供相 应失效原因的解决办法,为提高含BGA元件PCBA合格率提供技 术参考。希望能为公司当前在生产制造含BGA产品中遇到的问题, 提供帮助。
BGA有不同类型,不同类型的BGA有不同的特点,只有 深入了解不同类型BGA的优缺点,才能更好地制定满 足BGA制程要求的工艺,才能更好地实现BGA的良好装 配,降低BGA的制程成本。
目前含BGA的PCB板采用的工艺形式较多是 OSP(有机保焊剂)和 ENIG(化镍金)。我 公司产品对两种工艺的PCB都有使用。
两种不同工艺的PCB,因为其本身的工艺特 点,使用不当,会导致不同方式的失效。有 必要分别予以详细介绍。
业界对含BGA PCB工艺选用情况:
8
7
6
5 Percentage of Voids
左图是ENIG工艺PCB焊盘NI层 存在裂纹,当有裂纹存在时, 镍层的表面致密性差,后续浸 金工艺中的酸液容易残留其中, 致使NI层腐蚀氧化,导致焊盘 的可焊性不好。由于焊盘的可 焊性较差才导致焊盘与焊料之 间润湿不良,不能形成良好的 金属间化合物层。出现:“黑 焊盘”、不浸润等不良现象。
BGA元件引起的不良分析
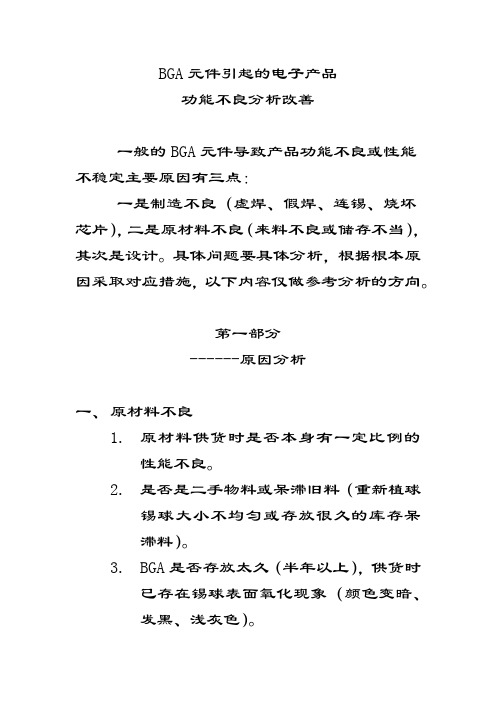
BGA元件引起的电子产品功能不良分析改善一般的BGA元件导致产品功能不良或性能不稳定主要原因有三点:一是制造不良(虚焊、假焊、连锡、烧坏芯片),二是原材料不良(来料不良或储存不当),其次是设计。
具体问题要具体分析,根据根本原因采取对应措施,以下内容仅做参考分析的方向。
第一部分------原因分析一、原材料不良1.原材料供货时是否本身有一定比例的性能不良。
2.是否是二手物料或呆滞旧料(重新植球锡球大小不均匀或存放很久的库存呆滞料)。
3.BGA是否存放太久(半年以上),供货时已存在锡球表面氧化现象(颜色变暗、发黑、浅灰色)。
二、包装方式1.BGA散料、尾数包装方式是否合理,是否由于包装方式不恰当导致BGA锡球压扁或掉球,是否长期将BGA元件放置在非真空环境中,导致锡球氧化。
2.原包装物料在运输和储存过程能否保证真空包装无破损漏气现象,存放的环境是否符合这类元件要求。
三、贴装前的准备工作1.BGA包装漏气或非真空包装时间超过72小时,是否经过烘烤后贴装。
2.BGA上线前是否经过基本抽检(目视锡球大小是否均匀,锡球表面是否变色,银白色为正常,锡球发黑,颜色变暗或变成浅灰色,证明锡球已经发生不同程度的氧化,有可能导致焊接不良)四、锡膏印刷质量控制1.SMT印刷时是否针对BGA元件焊盘的印刷质量做了100%检查,然后再投入贴片。
2.SMT钢网是否有堵孔现象,导致漏印或少锡;印刷机刮刀压力是否适中,保证锡膏厚度均匀(目测印刷后PCB焊盘上的锡膏无明显拉尖或锡膏厚度不均匀现象)3.印刷前目检BGA焊盘的焊接点大小是否一致,油墨覆盖是否均匀,油墨过后会导致印刷拉尖,锡膏厚度不均匀(目视焊盘大小无明显区别,油墨无明显凸起或目视焊盘明显呈凹下去状态, PCB的油墨厚度在实际操作中可测性不大,目前最实用的非标准检查方式就是目测,可操作性比较强)。
4.PCB表面是否有异物或灰尘,PCB油墨共面性是否有保证。
(目视PCB焊盘与油墨几乎处于同一平面,或用手刮油墨无明显阻力,油墨覆盖不可过厚且厚度要均匀)五、贴装设备(贴片机)贴装BGA元件的设备,是否有激光识别矫正装置,能否识别锡球不大小规则或变形的BGA,能否进行激光图像识别,区别锡球表面是否氧化或少球。
BGA芯片虚焊问题的探讨
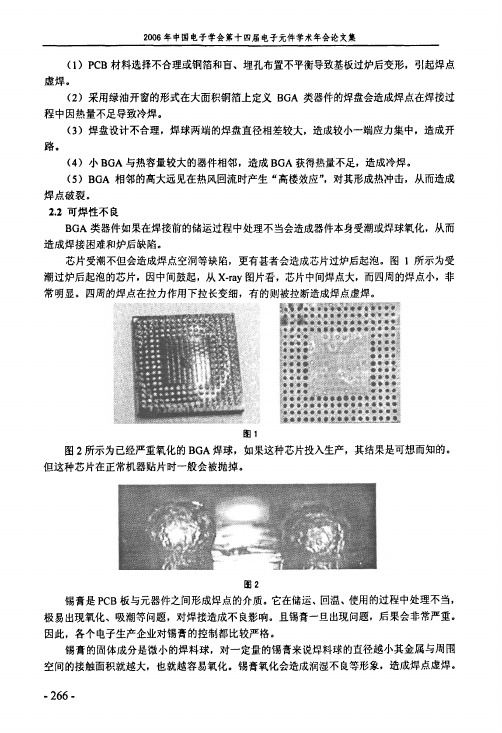
2006年中国电子学会第十四届电子元件学术年会论文集(1)PCB材料选择不合理或铜箔和盲、埋孔布置不平衡导致基板过炉后变形,引起焊点虚焊。
(2)采用绿油开窗的形式在大面积铜箔上定义BGA类器件的焊盘会造成焊点在焊接过程中因热量不足导致冷焊。
(3)焊盘设计不合理,焊球两端的焊盘直径相差较大,造成较小一端应力集中,造成开路。
(4)小BGA与热容量较大的器件相邻,造成BGA获得热量不足,造成冷焊。
(5)BGA相邻的高大远见在热风回流时产生“高楼效应”,对其形成热冲击,从而造成焊点破裂。
2.2可焊性不良BGA类器件如果在焊接前的储运过程中处理不当会造成器件本身受潮或焊球氧化,从而造成焊接困难和炉后缺陷。
芯片受潮不但会造成焊点空洞等缺陷,更有甚者会造成芯片过炉后起泡。
图l所示为受潮过炉后起泡的芯片,因中间鼓起,从X.ray图片看,芯片中间焊点大,而四周的焊点小,非常明显。
四周的焊点在拉力作用下拉长变细,有的则被拉断造成焊点虚焊。
图1图2所示为已经严重氧化的BGA焊球,如果这种芯片投入生产,其结果是可想而知的。
但这种芯片在正常机器贴片时一般会被抛掉。
图2锡膏是PCB板与元器件之间形成焊点的介质。
它在储运、回温、使用的过程中处理不当,极易出现氧化、吸潮等问题,对焊接造成不良影响。
且锡膏一旦出现问题,后果会非常严重。
因此,各个电子生产企业对锡膏的控制都比较严格。
锡膏的固体成分是微小的焊料球,对一定量的锡膏来说焊料球的直径越小其金属与周围空间的接触面积就越大,也就越容易氧化。
锡膏氧化会造成润湿不良等形象,造成焊点虚焊。
.266.随着细间距器件的大量采用,小粉粒度锡膏的使用会越来越多。
因此就需要对锡膏的使用采取更加严格的管理措施。
众所周知,焊接过程分为润湿、扩散和形成合金三个步骤。
当焊料与被焊金属之间有氧化层和其它污染物时,会在焊接界面上形成阻挡层,妨碍金属原子自由接近,阻止金属的相互扩散。
其次,这些阻挡层的表面自由能通常小于洁净的铜表面的自由能,从而使焊料不易产生润湿作用,这是形成虚焊的原因之一。
BGA元件焊点“虚焊”原因分析及控制方法
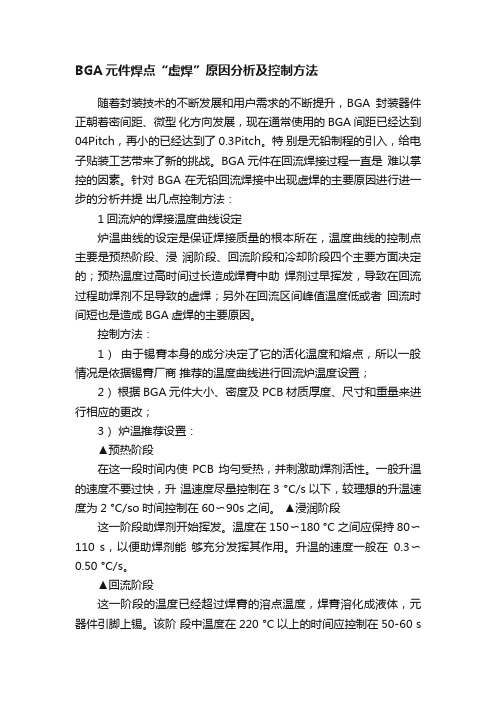
BGA元件焊点“虚焊”原因分析及控制方法随着封装技术的不断发展和用户需求的不断提升,BGA封装器件正朝着密间距、微型化方向发展,现在通常使用的BGA间距已经达到04Pitch,再小的已经达到了 0.3Pitch。
特别是无铅制程的引入,给电子贴装工艺带来了新的挑战。
BGA元件在回流焊接过程一直是难以掌控的因素。
针对BGA在无铅回流焊接中出现虚焊的主要原因进行进一步的分析并提出几点控制方法:1回流炉的焊接温度曲线设定炉温曲线的设定是保证焊接质量的根本所在,温度曲线的控制点主要是预热阶段、浸润阶段、回流阶段和冷却阶段四个主要方面决定的;预热温度过高时间过长造成焊膏中助焊剂过早挥发,导致在回流过程助焊剂不足导致的虚焊;另外在回流区间峰值温度低或者回流时间短也是造成BGA虚焊的主要原因。
控制方法:1)由于锡膏本身的成分决定了它的活化温度和熔点,所以一般情况是依据锡膏厂商推荐的温度曲线进行回流炉温度设置;2)根据BGA元件大小、密度及PCB材质厚度、尺寸和重量来进行相应的更改;3)炉温推荐设置:▲预热阶段在这一段时间内使PCB均勻受热,并刺激助焊剂活性。
一般升温的速度不要过快,升温速度尽量控制在3 °C/s以下,较理想的升温速度为2 °C/so时间控制在60〜90s之间。
▲浸润阶段这一阶段助焊剂开始挥发。
温度在150〜180 °C之间应保持80〜110 s,以便助焊剂能够充分发挥其作用。
升温的速度一般在0.3〜0.50 °C/s。
▲回流阶段这一阶段的温度已经超过焊膏的溶点温度,焊膏溶化成液体,元器件引脚上锡。
该阶段中温度在220 °C以上的时间应控制在50-60 s之间。
如果时间太短或过长都会造成焊接的质量问题。
峰值温度控制在235〜245 °C,时间不低于10 s,这样可以增加锡膏熔融态时间,有利于锡膏焊接。
▲冷却阶段这一阶段焊膏开始凝固,元器件被固定在线路板上。
BGA元件引起的不良分析
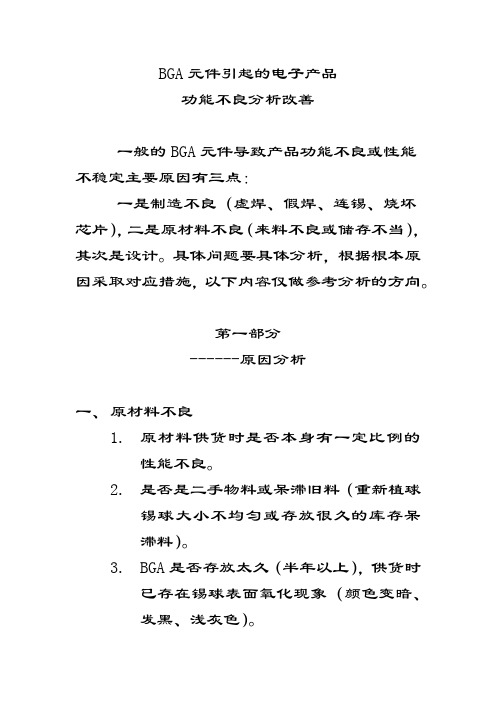
BGA元件引起的电子产品功能不良分析改善一般的BGA元件导致产品功能不良或性能不稳定主要原因有三点:一是制造不良(虚焊、假焊、连锡、烧坏芯片),二是原材料不良(来料不良或储存不当),其次是设计。
具体问题要具体分析,根据根本原因采取对应措施,以下内容仅做参考分析的方向。
第一部分------原因分析一、原材料不良1.原材料供货时是否本身有一定比例的性能不良。
2.是否是二手物料或呆滞旧料(重新植球锡球大小不均匀或存放很久的库存呆滞料)。
3.BGA是否存放太久(半年以上),供货时已存在锡球表面氧化现象(颜色变暗、发黑、浅灰色)。
二、包装方式1.BGA散料、尾数包装方式是否合理,是否由于包装方式不恰当导致BGA锡球压扁或掉球,是否长期将BGA元件放置在非真空环境中,导致锡球氧化。
2.原包装物料在运输和储存过程能否保证真空包装无破损漏气现象,存放的环境是否符合这类元件要求。
三、贴装前的准备工作1.BGA包装漏气或非真空包装时间超过72小时,是否经过烘烤后贴装。
2.BGA上线前是否经过基本抽检(目视锡球大小是否均匀,锡球表面是否变色,银白色为正常,锡球发黑,颜色变暗或变成浅灰色,证明锡球已经发生不同程度的氧化,有可能导致焊接不良)四、锡膏印刷质量控制1.SMT印刷时是否针对BGA元件焊盘的印刷质量做了100%检查,然后再投入贴片。
2.SMT钢网是否有堵孔现象,导致漏印或少锡;印刷机刮刀压力是否适中,保证锡膏厚度均匀(目测印刷后PCB焊盘上的锡膏无明显拉尖或锡膏厚度不均匀现象)3.印刷前目检BGA焊盘的焊接点大小是否一致,油墨覆盖是否均匀,油墨过后会导致印刷拉尖,锡膏厚度不均匀(目视焊盘大小无明显区别,油墨无明显凸起或目视焊盘明显呈凹下去状态, PCB的油墨厚度在实际操作中可测性不大,目前最实用的非标准检查方式就是目测,可操作性比较强)。
4.PCB表面是否有异物或灰尘,PCB油墨共面性是否有保证。
(目视PCB焊盘与油墨几乎处于同一平面,或用手刮油墨无明显阻力,油墨覆盖不可过厚且厚度要均匀)五、贴装设备(贴片机)贴装BGA元件的设备,是否有激光识别矫正装置,能否识别锡球不大小规则或变形的BGA,能否进行激光图像识别,区别锡球表面是否氧化或少球。
BGA焊接失效分析报告完整版
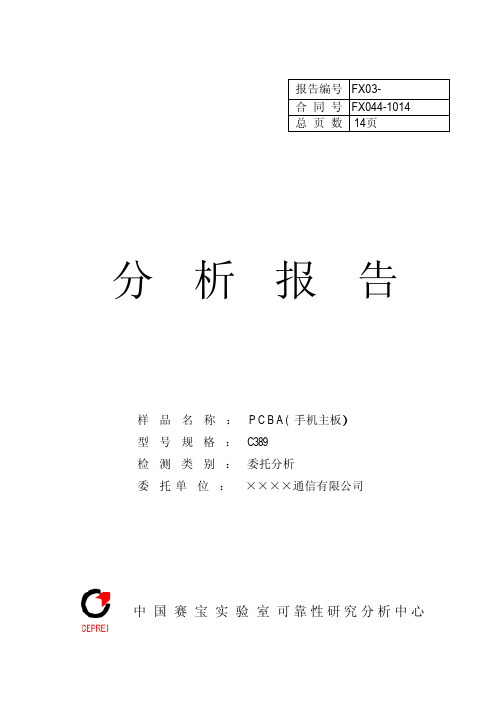
分析报告样品名称:P C B A(手机主板)型号规格:C389检测类别:委托分析委托单位:××××通信有限公司中国赛宝实验室可靠性研究分析中心PCBA 分析报告合同号:FX044- 1014 第2页共 14 页分析报告所送样品包括三片 PCBA (手机主板)、四片相应的空白 PCB 以及工艺过程中使 用的CPU 器件和焊锡膏,PCBA (手机主板)的型号为C389,样品的外观照片见图1焊锡膏空白 PCBCPUFlashCPU 器件二 分析过程2.1 外观检查图 1 样品的外观照片用立体显 微 镜对空白 PC B 和 BGA 器 件 进 行 外观 检 测,发现 BGA 器件的焊 球大小均匀一 致,共面 性良好(见图 2 和 图 3);空白 PC B 焊 盘表面存在一些坑 洼点(见图 4 和图 5), 除 此 之外未 观 察 到 明 显的 异 常。
图 2 CPU 器件中 BGA 焊球的外观照片 图 3 CPU 器件中 BGA 焊球的局部外观照片坑洼点图 4 PCB板中CPU焊盘的外观照片图 5 PCB板中Flash的外观照片2.2 X-RAY检测为了对焊点的内部状况进行检测,采用 X 射线系统对焊点质量进行无损检测,(X-Ray 的照片见图 6 至图9),由照片可观察得出 BGA 焊点大小均匀一致,除发现焊点内部存在少量空洞外,未发现焊球错位,焊料熔融不完全以及桥连等明显焊接缺陷。
图 6 CPU焊点的X-ray典型照片图7 Flash焊点的X-ray典型照片图8倾斜后观察到的CP U焊点的X-ray照片图9倾斜后观察到的Flas h焊点的X-r ay照片空洞空洞图10部分CPU焊点的放大照片图11部分Flash焊点的放大照片2.3金相切片分析在样品上截取失效的BGA器件,用环氧树脂镶嵌后打磨抛光,用金相显微镜观察BGA器件焊点的金相切片,焊点的金相照片见图12~图25。
X光机检测BGA-焊球虚焊情况分析

.
材料 塑料 金 铅 铝 锡 铜 环氧树脂 硅
表1不同材料对X射线的不透明度系数
用途 包装 芯片引线键合 焊料 芯片引线键合,散热片 焊料 PCB印制线 PC. B基板 半导体芯片
X射线不透明度系数 极小 非常高 高 极小 高 中等 极小 极小
2,剖面图说明“Dark Ring”的形成 原理
区域
A区
而由于现代BGA封装技术,对高I/O数的不断要求和发展,也要求BGA焊球之间的 间距向更小间距发展。采用3D技术的检测设备,当其探测器在倾斜到一定角度时,焊球 与焊球之间因互相遮挡,对BGA内部的焊球底部,因“视线遮挡”已经无法直接观测。 而对BGA外部的焊球来说,也可能存在检测限制,即BGA旁边的其他元器件可能对BGA 焊球底部造成的“视线遮挡”,从而可能对3D检测效果产生不利影响。即便BGA旁边无 其他元器件对焊球造成遮挡时,3D检测手段亦只能对BGA焊球的外侧进行局部观察,这 仍然是因为BGA焊球之间因微小间距而造成的“视线遮挡”。所以3D检测虚焊,理论上 是以通过直接的目视观察,以提高“虚焊”检测的直观性,而实际操作中也存在着一定 的局限性。同时,3D检测手段除了上述的检测覆盖范围的局限性外,检测方法与手段太 耗时,无法满足制造厂商日益高密度、高速度的生产需求,也是突出的问题,同时制造 厂商还必须应对设备高投资,高维护成本的风险。
焊球明显偏大,且看不到“Dark Ring”(图四)
图四
OPEN
造成原因: PCB焊盘铜箔喷锡的表面氧化层太厚,对焊锡膏产生拒焊,尽管焊锡膏已 完全熔融,但焊锡膏无法润湿PCB的焊盘,导致PCB焊盘上的焊膏与BGA 焊球熔融为一体,造成BGA焊球球体变大的现象。
.
三、总结
BGA焊球的虚焊现象,在焊球底部与焊盘之间是非常细微的,所以对比度变 化很细微。目前市场上亦有运用3D 技术的X-RAY,意图是对焊球的虚焊进行直接 目视观察。其工作原理为:将探测器倾斜后围绕BGA焊球进行360度旋转,以创造 直接目视观察焊球底部与焊盘之间的焊接状况的机会。
光机检测BGA焊球虚焊情况分析课件
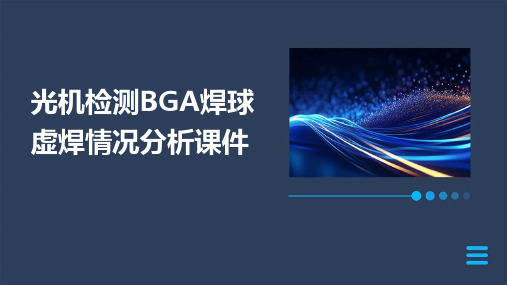
环境因素影响
湿度的影响
如果工作环境湿度过高,可能会导致焊 球受潮,影响焊接质量,从而出现虚焊 现象。
VS
温度的影响
如果工作环境温度过高或过低,可能会导 致焊球与基板之间的熔合受到影响,从而 出现虚焊现象。
05
防止BGA焊球虚焊的 措施
选择合适的焊接材料
总结词
选择合适的焊接材料是防止BGA焊球虚焊的重要措施之 一。
感谢观看
总结词
详细描述
优化焊接工艺参数可以有效防止BGA焊球 虚焊。
通过调整焊接温度、时间和压力等参数, 可以控制焊接过程中材料的流动和润湿行 为,从而减少虚焊现象的发生。
总结词
详细描述
优化后的焊接工艺参数可以提高焊缝的强 度和可靠性,降低虚焊风险。
例如,适当提高焊接温度可以促进焊接材 料的流动和润湿,但同时也要避免温度过 高导致焊球氧化或基板变形等问题。
针床检测法(PWI/SPI)
总结词
通过探针接触焊球,检测其导电性能判断虚焊。
详细描述
针床检测法利用精密探针直接接触BGA焊球,通过测量导电性能判断是否存在虚焊。该方法对于焊球的导电性能 要求较高,且可能会对焊球造成损伤。
X-ray检测法
总结词
利用X射线穿透焊点,通过影像分析判断虚焊。
详细描述
X-ray检测法利用X射线对BGA焊球进行穿透,通过影像分析判断焊点的内部结构,从而判断是否存在 虚焊。X-ray检测法能够检测到深层的虚焊,但设备成本较高,且对人体有一定的辐射影响。
光机检测的优势
01
02
03
非接触式检测
光机检测采用非接触式的 方式进行检测,不会对被 检测物体造成任何损伤或 影响。
高精度和高效率
BGA焊接分析报告
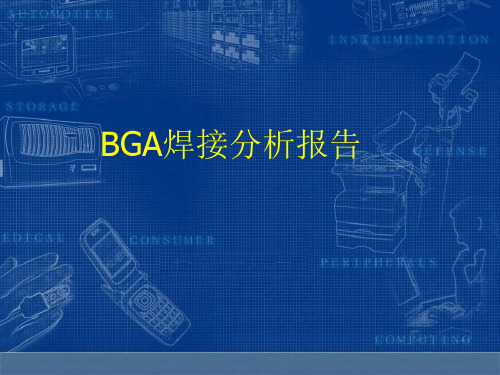
(3) CCGA:CCGA是CBGA尺寸大于32*32mm时的另一种形式,不同之处在于采用焊料柱代替焊料球。焊料柱采用共晶焊料连 接或直接浇注式固定在陶瓷底部。 优缺点与CCGA大体相同,不同在于焊料柱能够承受CTE不同所产生的应力,能够应用在大尺寸封装。
泡和损坏不良。 --铜箔的粘合强度。 --弯曲强度要达到25kg/mm以上。 --电性能要求。 --对清洁剂的反应,在液体中浸渍5分钟,表面不产生任何不良,并有良好的冲载性。
(2)表面贴装元件具备的条件:
--元件的形状适合于自动化表面贴装 --尺寸,形状在标准化后具有互换性 --有良好的尺寸精度 --适应于流水或非流水作业 --有一定的机械强度 --可承受有机溶液的洗涤 --可执行零散包装又适应编带包装 --耐焊耐热应符合相应的规定
(2)保温区:指从120度升温至160度的区域,使PCB上各元件的温度趋于均匀。
要点---保证在达到再流温度之前焊料能够完全干燥。到保温区结束时,焊盘、锡膏球及元件引脚 上的氧化物被除去。过程约60-120秒,视焊料性质有所差异。
(3)回流区:本区加热温度设置得最高,峰值温度根据所用锡膏的不同而有差异。
要点---降温速率一般为-4度/sec,冷却至75度左右即可。
回流焊接视图
回流焊接视图
焊接流程视图
6、清洗
作用:将组装好的pcb上对人体有害的焊接残留物除去。 设备:清洗机。
7、检测
电子产品生产中虚焊不良分析及预防总结
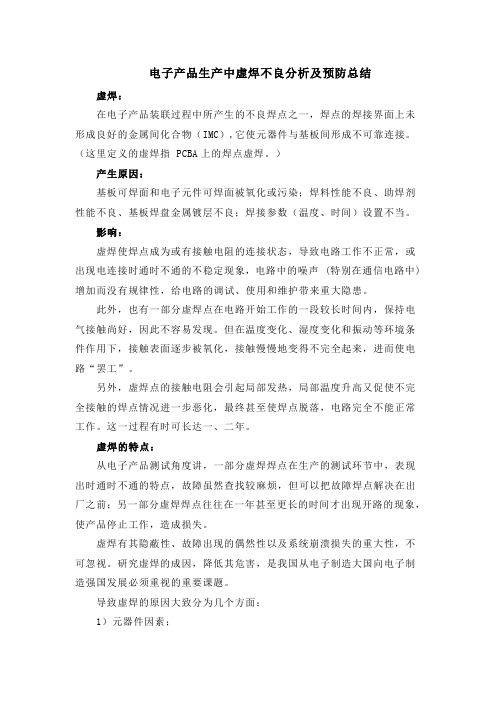
电子产品生产中虚焊不良分析及预防总结虚焊:在电子产品装联过程中所产生的不良焊点之一,焊点的焊接界面上未形成良好的金属间化合物(IMC),它使元器件与基板间形成不可靠连接。
(这里定义的虚焊指 PCBA上的焊点虚焊。
)产生原因:基板可焊面和电子元件可焊面被氧化或污染;焊料性能不良、助焊剂性能不良、基板焊盘金属镀层不良;焊接参数(温度、时间)设置不当。
影响:虚焊使焊点成为或有接触电阻的连接状态,导致电路工作不正常,或出现电连接时通时不通的不稳定现象,电路中的噪声 (特别在通信电路中) 增加而没有规律性,给电路的调试、使用和维护带来重大隐患。
此外,也有一部分虚焊点在电路开始工作的一段较长时间内,保持电气接触尚好,因此不容易发现。
但在温度变化、湿度变化和振动等环境条件作用下,接触表面逐步被氧化,接触慢慢地变得不完全起来,进而使电路“罢工”。
另外,虚焊点的接触电阻会引起局部发热,局部温度升高又促使不完全接触的焊点情况进一步恶化,最终甚至使焊点脱落,电路完全不能正常工作。
这一过程有时可长达一、二年。
虚焊的特点:从电子产品测试角度讲,一部分虚焊焊点在生产的测试环节中,表现出时通时不通的特点,故障虽然查找较麻烦,但可以把故障焊点解决在出厂之前;另一部分虚焊焊点往往在一年甚至更长的时间才出现开路的现象,使产品停止工作,造成损失。
虚焊有其隐蔽性、故障出现的偶然性以及系统崩溃损失的重大性,不可忽视。
研究虚焊的成因,降低其危害,是我国从电子制造大国向电子制造强国发展必须重视的重要课题。
导致虚焊的原因大致分为几个方面:1)元器件因素;2)基板(通常为 PCB)因素;3)助焊剂、焊料因素;4)、工艺参数及其他因素。
下面进行详细分析。
1、元器件因素引起的虚焊及其预防元器件可焊部分的金属镀层厚度不够、氧化、污染、变形都可造成虚焊的结果。
1.1 可焊部分的金属镀层厚度不够通常元器件可焊面镀有一定厚度的、银白色的、均匀的易焊锡层,如果镀层太薄或者镀层不均匀,以及铜基镀锡或钢基镀铜再镀锡,其铜和锡之间相互接触形成的铜锡界面,两种金属长时间接触就会相互渗透形成合金层扩散,使锡层变薄,导致焊面的可焊性下降。
BGA不良分析、改善报告

B.器件的放置
BGA的准确贴放很大程度上取决于贴片机的精确度, 以及镜像识别系统的识别能力。SIEMENS设备均能满 足要求,唯一要确保设备状态稳定,使用feeder、吸 嘴正常,无抛料现象。
有可能某个焊球在Z方向上略小于其他焊球。为了保证 焊接的良好性,使BGA器件在安放时其焊球能够与焊 膏充分接触。减少BGA某个引脚空焊的现象。通常可 以将BGA的器件高度减去0.1~0.2mm。
二、计划&生产管控
1.
OSP PCB生产必须于拆封后24小时内完成SMT,生管计划根据SMT的 工时排线,不得超过规定时限。
计划把握进料状况. 料齐后才可以安排上线。 BGA一般布置在PCB的B面,先生产完A面后,B面有机防护膜被高温破 坏,所以,计划需要保证生产连续性,要求A面生产后,B面生产时间 间隔不超过24小时。 OSP工艺PCB一般不要烘烤;如果回潮必须要烘烤,条件:100℃,4h。 生产时不能一次拆很多包,使用完一包再拆一包; 禁止裸手接触PCB板内元件焊盘。
2、CBGA(CERAMIC BGA)陶瓷封装BGA 其优点是: ①封装组件的可靠性高。 ②共面性好,焊点形成容易,但焊点不平行度交差。 ③对湿气不敏感。 ④封装密度高。 其缺点是: ①由于热膨胀系数不同,和环氧板的热匹配差,焊点 疲劳是主要的失效形式。 ②焊球在封装体边缘对准困难。 ③封装成本高。
a.BGA来料质量控制
BGA机器本身的失效或不良是导致焊接 不良的一个潜在危害。 右图是未焊接使用的BGA图片,焊球内 部存在裂缝缺陷。这种裂缝将可能引起 焊球与BGA本体PCB之间形成假焊。 这种问题,在不良分析中往往容易忽视, 或找不出不良原因。 来料检验部门有必要对来料进行抽样, 在显微镜下检验确认。
BGA不良分析、改善报告
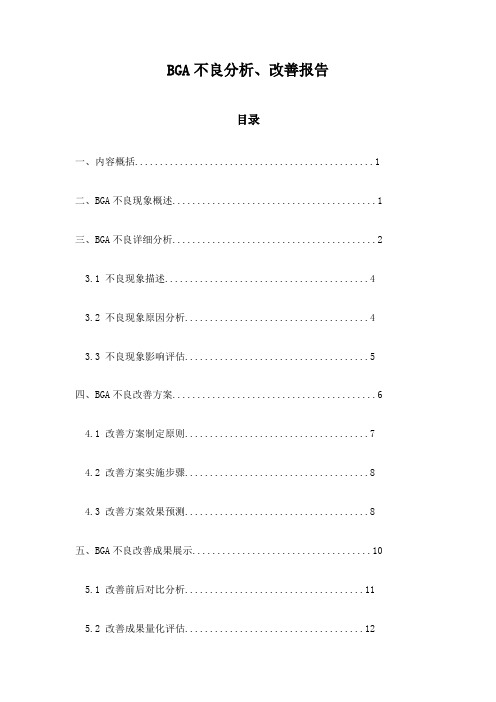
BGA不良分析、改善报告目录一、内容概括 (1)二、BGA不良现象概述 (1)三、BGA不良详细分析 (2)3.1 不良现象描述 (4)3.2 不良现象原因分析 (4)3.3 不良现象影响评估 (5)四、BGA不良改善方案 (6)4.1 改善方案制定原则 (7)4.2 改善方案实施步骤 (8)4.3 改善方案效果预测 (8)五、BGA不良改善成果展示 (10)5.1 改善前后对比分析 (11)5.2 改善成果量化评估 (12)5.3 改善成果应用前景展望 (13)六、结论与建议 (14)6.1 结论总结 (16)6.2 建议提出 (16)一、内容概括本报告旨在深入分析BGA(球栅阵列)不良品产生的原因,并提出针对性的改善措施。
通过对不良品的详细统计与分析,结合生产工艺、材料特性等多方面因素,我们识别出主要的不良模式及成因,为后续的改进工作提供了明确的方向。
在改善方案方面,我们提出了切实可行的改进措施,并对实施效果进行了预测。
通过这些改善措施的实施,我们期望能够有效降低BGA不良率,提升产品的整体质量和可靠性,从而满足客户的需求和期望。
本报告还强调了持续改进的重要性,建议公司应建立长期的不良分析与改善机制,不断优化生产工艺和管理流程,以实现产品质量的持续提升。
二、BGA不良现象概述在电子制造行业中,BGA(Ball Grid Array,球栅阵列)封装技术因其高密度、高可靠性和良好的电性能而广泛应用。
随着电子产品向高性能、小型化发展,BGA封装的不良品率也逐渐上升,给企业带来了巨大的经济损失和市场竞争压力。
焊球缺陷:焊球是BGA封装的重要组成部分,其质量直接影响到BGA的整体性能。
焊球缺陷主要包括焊球偏移、焊球缺失、焊球断裂等,这些问题会导致BGA无法正常工作,甚至引发更严重的产品故障。
封装体破裂:BGA封装体的强度和密封性对其性能至关重要。
在制造过程中或使用过程中,由于各种因素的影响,如高温、湿度、压力等,可能导致封装体破裂,从而影响产品的可靠性。
- 1、下载文档前请自行甄别文档内容的完整性,平台不提供额外的编辑、内容补充、找答案等附加服务。
- 2、"仅部分预览"的文档,不可在线预览部分如存在完整性等问题,可反馈申请退款(可完整预览的文档不适用该条件!)。
- 3、如文档侵犯您的权益,请联系客服反馈,我们会尽快为您处理(人工客服工作时间:9:00-18:30)。
*****公司
关于芯片BGA 虚焊问题分析
(一)现场图片
X-RAY
照片(第一次时提供照片的截图,芯片未贴片前拍摄。
拍摄位置:芯片正上方)
回流焊后异常芯片剥离照片
问题芯片剥离图片
放大图片1位置
放大图片2
位置
问题芯片剥离图片细节放大
放大图片1 放大图片2
放大图片3
回流焊后检测合格芯片剥离照片(芯片焊接面100%剥离)
放大图片4
(二)图片分析
1.图片1焊接面使用高倍显微镜观察:锡面灰暗,空洞很多。
请特别注意红框位置;
2.锡面灰暗应是焊锡高温氧化的迹象。
我们认为这里的锡面氧化应是在回流焊的高温影响后发生。
发生
的原因与植球与芯片焊面的虚焊有关,并且这种虚焊在回流焊时无法得到改善。
我们认为芯片植球时已存在异常,导致植球与芯片接触面未初步形成有效地IMC(红色框)。
综合后我们认为植球与芯片间的有虚焊现象。
正常时植球后应该形成初步的焊点。
3.空洞较多也说明植球与芯片焊接面存在异常情况的发生;
4.根据材质及焊接结合力、拉力分析:我们认为良好的植球与芯片形成良好的IMC后,当我们剥离芯片
时大部分的芯片焊接面应被拉起脱落(各图片的蓝色框)。
而且我们剥离的合格芯片产品的焊接面观察,
在芯片剥离后确实也是100%脱落(见放大图4)。
而有问题的芯片仅有四点拉脱(见回流焊后异常芯片剥离照片蓝色框);
5.我司在外协厂贴片后植球与PCB间形成了良好的IMC,(参见图片3中的紫色框体内)。
整体移除锡球
后没有看见异常现象。
(三)图片分析结论
1.供方提供的芯片在植球时已出现植球与芯片有效焊接面的虚焊及不确定异常导致的较多空洞现象;
2.供方植球时已出现植球与芯片有效焊接面的虚焊及不确定异常导致的较多空洞现象直接导致了SMT
回流焊后无法调校的缺陷:芯片焊接面与植球间的虚焊或简单称为融合异常问题在回流焊后没有改善,导致芯片功能异常;
(四)供方的回复(以下原文)
发件人: **********
发送时间: 2010年**月**日 ****
收件人: *********
主题: RE: Fw: 植球不良照片
Hi ******
空洞和虚焊是两个概念。
锡球里有空洞,如有合适IR参数,经SMT IR 炉后,空洞会至少缩小或消失,空洞不会影响功能,可靠性问题,业界至今还没定论。
而虚焊,是锡膏或IR参数不好导致未融合,虚焊可能导致功能不良肯定影响可靠性。
(五)最后总结
回流焊机理我们不用再讨论。
对于回复的意见我们表示赞同,但我司出现的实际情况并非普通的空洞和虚焊混淆问题。
本次发现的空洞较多应该较充分的说明了植球时异常的出现。
而且X-RAY拍摄的照片中部分空洞面积接近焊接面积的50%,一旦在回流时其中的气体受热后释放带来的后果可想而知!这样程度的空洞通过调节回流参数得到的改善也十分有限。
我司前期指出的只是图片表面看到的表象。
没有详细的诠释所有证据及图片。
但根据供方回复看来有必要提供更加详细的讯息。
所以这次以本篇报告形式完全提报我司本次发现的所有问题照片及情况,如有不明确的希望及时联系,交换必要的意见。