浅谈检测传感技术的应用及进展
传感器技术应用及发展趋势探析
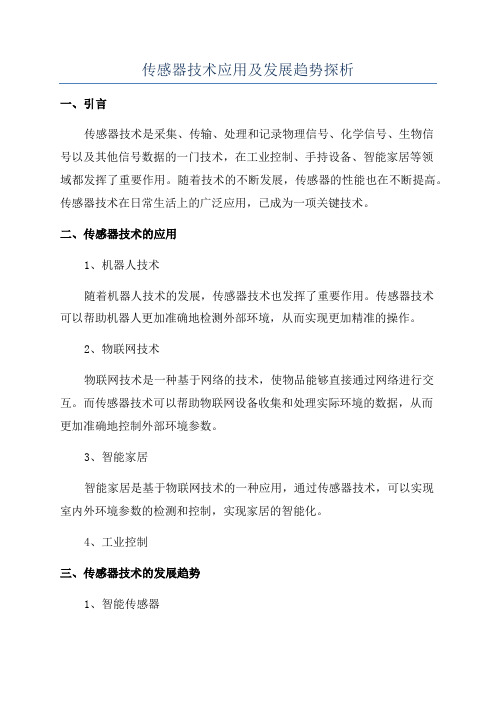
传感器技术应用及发展趋势探析
一、引言
传感器技术是采集、传输、处理和记录物理信号、化学信号、生物信
号以及其他信号数据的一门技术,在工业控制、手持设备、智能家居等领
域都发挥了重要作用。
随着技术的不断发展,传感器的性能也在不断提高。
传感器技术在日常生活上的广泛应用,已成为一项关键技术。
二、传感器技术的应用
1、机器人技术
随着机器人技术的发展,传感器技术也发挥了重要作用。
传感器技术
可以帮助机器人更加准确地检测外部环境,从而实现更加精准的操作。
2、物联网技术
物联网技术是一种基于网络的技术,使物品能够直接通过网络进行交互。
而传感器技术可以帮助物联网设备收集和处理实际环境的数据,从而
更加准确地控制外部环境参数。
3、智能家居
智能家居是基于物联网技术的一种应用,通过传感器技术,可以实现
室内外环境参数的检测和控制,实现家居的智能化。
4、工业控制
三、传感器技术的发展趋势
1、智能传感器
随着智能技术的发展,智能传感器也成为传感器技术的主流发展趋势。
传感检测技术及应用论文

传感检测技术及应用论文传感检测技术是一种通过感知环境中的物理量或化学量,并将其转化为可用于监测、控制或诊断的电信号的技术。
它在各个领域中都有广泛的应用,如环境监测、医疗诊断、工业生产等。
本文将介绍传感检测技术的原理、分类以及在不同领域中的应用。
传感检测技术的原理主要基于物理、化学或生物的感知原理。
根据感知原理的不同,传感检测技术可以分为物理传感、化学传感和生物传感。
物理传感主要是通过感知环境中的物理量,如温度、压力、湿度等。
化学传感主要是通过感知环境中的化学物质的浓度或反应。
生物传感主要是通过感知生物体内的生理参数或生物分子的浓度。
在物理传感中,温度传感是最常见的一种。
温度传感器可以通过测量物体的热辐射、电阻、电容等方式来感知温度。
压力传感器可以通过测量物体受力后的形变或电阻的变化来感知压力。
湿度传感器可以通过测量物体中水分的含量或电容的变化来感知湿度。
在化学传感中,气体传感是一种常见的应用。
气体传感器可以通过感知环境中气体的浓度或反应来检测气体的种类和浓度。
例如,二氧化碳传感器可以通过感知环境中二氧化碳的浓度来判断空气的质量。
氧气传感器可以通过感知环境中氧气的浓度来监测氧气的供应。
在生物传感中,血糖传感是一种常见的应用。
血糖传感器可以通过感知人体血液中葡萄糖的浓度来监测血糖水平。
这对于糖尿病患者来说非常重要,可以帮助他们控制血糖水平并及时采取措施。
除了以上几种传感检测技术,还有许多其他的传感检测技术,如光学传感、声学传感、生物传感等。
这些技术在不同领域中有着广泛的应用。
在环境监测领域,传感检测技术可以用于监测空气质量、水质、土壤质量等。
例如,空气质量传感器可以通过感知环境中的气体浓度来监测空气中的污染物。
水质传感器可以通过感知水中的溶解氧、PH值等参数来监测水质的好坏。
土壤质量传感器可以通过感知土壤中的湿度、温度、养分等参数来监测土壤的适宜性。
在医疗诊断领域,传感检测技术可以用于监测人体的生理参数、疾病标志物等。
传感器与检测技术的应用

传感器与检测技术的应用在现代社会中,传感器和检测技术已经被广泛应用于各个领域,包括医疗、交通、安全、环保等等。
它们能够快速、准确地采集各种信息,并将这些信息转化为数字信号,为我们提供了更多的数据和信息。
本文将探讨传感器和检测技术的应用,以及它们未来的发展方向和挑战。
一、医疗领域在医疗领域,传感器和检测技术的应用非常广泛,涵盖了医疗诊断、治疗监控、健康管理等方面。
例如,血糖仪、血压计、体温计等常见的医疗设备都是基于传感器和检测技术实现的。
此外,传感器还广泛应用于生物医学领域,例如神经监测、心脏监测、血氧饱和度监测等等。
这些设备不仅可以实时监测患者的生理状态,还可以通过将数据传输到云端进行分析,帮助医生做出更加准确的诊断和治疗计划。
二、交通领域在交通领域,传感器和检测技术被应用于车辆监测、智能交通系统中等多个方面。
例如,在城市交通管理中,传感器可以被安装在路面、交通信号灯等地方,实时感知道路拥堵情况以及车辆密度,在交通拥堵时自动调度路灯和交通信号灯,帮助缓解交通堵塞。
此外,自动驾驶技术的发展也离不开传感器和检测技术的支持。
自动驾驶汽车需要通过激光雷达、摄像头等传感器实时感知周围环境,在不同的交通情况下做出正确的决策和操作,保证安全、高效的行驶。
三、安全领域在安全领域,传感器和检测技术的应用范围也比较广泛,如智能家居、安防监控、消防救援等。
例如,智能家居安保系统可以通过红外线传感器、门磁传感器等设备对屋内环境进行监测,一旦发现异常情况就会及时触发报警装置,保护家人的安全。
安防监控方面,传感器可以帮助监控人员随时感知目标物的动静,提高监控效率和准确性。
消防救援方面,传感器可以检测火情、烟雾等情况,及时预警,以便进行紧急救援和处理。
四、环保领域在环保领域,传感器和检测技术也被广泛应用于污染检测、气象监测等方面。
例如,传感器可以通过测量空气中的污染物浓度、水质指标等参数,实时监测环境的变化,并通过数据传输和处理,提供有效的环境保护决策。
传感器在检测技术中的应用及发展的研究

传感器在检测技术中的应用及发展的研究一:传感器在检测技术中的作用及地位检测(Detection)是利用各种物理、化学效应,选择合适的方法与装置,将生产、科研、生活等各方面的有关信息通过检查与测量的方法赋予定性或定量结果的过程。
能够自动的完成整个检测处理过程的技术称为自动检测与转换技术。
检测技术是现代化领域中很有发展前途的技术,他在国民经济中起着极其重要的作用。
近几十年来,自动控制理论和计算机技术迅速发展,并已应用到生产和生活的各个领域。
但是,由于作为“感觉器官”的传感器技术没有与计算机技术协调发展,出现了信息处理功能发达、检测功能不足的局面。
目前许多国家已投入大量人力、物力,发展各类新型传感器,检测技术在国民经济中的地位也日益提高。
传感器是能感受规定的被测量并按一定规律转换成可用输出信号的器件或装置,主要用于检测机电一体化系统自身与操作对象、作业环境状态,为有效控制机电一体化系统的运作提供必须的相关信息。
随着人类探知领域和空间的拓展,电子信息种类日益繁多,信息传递速度日益加快,信息处理能力日益增强,相应的信息采集——传感技术也将日益发展,传感器也将无所不在。
传感器技术是实现自动控制、自动调节的关键环节,也是机电一体化系统不可缺少的关键技术之一,其水平高低在很大程度上影响和决定着系统的功能;其水平越高,系统的自动化程度就越高。
在一套完整的机电一体化系统中,如果不能利用传感检测技术对被控对象的各项参数进行及时准确地检测出并转换成易于传送和处理的信号,我们所需要的用于系统控制的信息就无法获得,进而使整个系统就无法正常有效的工作。
传感器(Sensor)是一种常见的却又很重要的器件,它是感受规定的被测量的各种量并按一定规律将其转换为有用信号的器件或装置。
对于传感器来说,按照输入的状态,输入可以分成静态量和动态量。
我们可以根据在各个值的稳定状态下,输出量和输入量的关系得到传感器的静态特性。
传感器的静态特性的主要指标有线性度、迟滞、重复性、灵敏度和准确度等。
光纤传感检测技术的应用与进展

光纤传感检测技术的应用与进展1 光纤传感器的基本原理光纤传感器是将待测量在光纤内传输的光波参量进行调制,并对被调制过的光波信号进行解调检测,从而获得待测量值的一种装置.它可广泛用于位移、振动、转动、压力、弯曲、应变、加速度、电流、磁场、电压、温度、声场、流量、浓度、pH值等各种参量的测量,并具有灵敏度高、响应速度快、无源性、防爆、防电磁干扰、超高电绝缘、耐腐蚀、体积小、重量轻、成本低等优点。
2 光纤检测技术光纤检测技术在工程中应用有以下要求:高精度、长距离、分布式和长期性。
2.1 光纤传感器的多路复用技术复用技术的基本思想是充分利用光纤具有大容量传输信息的特点.在同一信息传输母线上传输来自各个传感点的信息,并通过解复用处理最终获得各个传感器列阵点上的被测信息.复用技术主要有分幅多路复用、分时多路复用和分频多路复用等3种方法。
复用技术原理和复用传感器原理见图1和图2。
图1 复用技术原理图2 三路服用传感器原理图这些光纤传感器的复用方案,原理上具有普遍的适用性.由于受到光纤元器件技术的限制,使复用数量受到限制,因而这是一种准分布式的光纤检测技术,没有从根本上改变点式传感技术的局限。
2.2 布喇格光纤光栅技术布喇格((Bragg)光纤光栅是指单模掺锗光纤经紫外光照射成栅技术形成的全新光纤型Bragg光栅.成栅后的光纤纤芯折射率呈现周期性分布条纹并产生Bragg光栅效应。
这种光栅的基本光学特性就是以共振波长为中心的窄带光学滤波器.当一束光送进Bragg光纤光栅时,根据光栅理论,在满足Bragg条件的情况下,就会发生全反射,其反射光谱在Bragg 波长又处出现峰值。
光栅受到外部物理场(如应力、应变、温度等)的作用时,其栅距n随之发生变化,从而改变了后向反射光的波长又。
根据又变化的大小就可以确定待测部位相应物理量的变化.当把多个不同周期的光纤光栅按一定规定排成阵列,就构成了多点分布传感系统。
其传感原理及检测技术原理见图3和图4。
生物传感技术的应用和新进展

生物传感技术的应用和新进展生物传感技术是将生物学与工程学、化学等交叉学科相结合而建立起来的新兴学科。
它主要研究如何将微生物、细胞、酶、抗体、核酸等生物分子或元素作为生物传感器,实现对环境、食品、医药等领域中的相关分子、物质、病理等生物信息进行快速、准确地检测、识别和定量分析。
在各个领域的应用中都有相当可观的成效,为整个人类社会的进步,健康的发展提供了强有力的支持。
一、生物传感技术在健康医疗领域中的应用生物传感技术广泛应用于医药领域,可以用于快速检测人体内各种生化指标,提高临床诊断的准确率和治疗效果。
比如,肿瘤标志物测定、病毒感染检测等。
目前,有国外研制的生物传感芯片,可根据不同的药物制品的代谢方式,定制不同的实验芯片,用于定量测定特定药物和其代谢产物的含量。
这对于临床药物疗效和中药的药性评价有重要意义。
二、生物传感技术在食品安全领域中的应用生物传感技术在食品安全领域的应用主要是针对食品中残留有害物质的检测及肉类、乳制品等食品的鉴别和检测。
现在,一些国家和地区已经开始实行可追溯的食品安全管理体制,生物传感技术在其中具有重要的作用。
比如,鱼类生物传感器可以检测出鱼类中的环境激素水平并作出及时反应,有助于提高水产养殖的环境状况和产品质量。
三、生物传感技术在环境检测中的应用生物传感技术在环境检测中可以应用于多方面信息的传感,如检测二氧化碳浓度、空气中的有害气体、土壤中的重金属污染等等。
环境传感技术已经开始广泛应用,如氨气传感器、有害气体传感器等。
通过这些传感器,可以及早发现空气中的一些有害气体,如二氧化硫、氮氧化物等,确保居民们呼吸到新鲜的空气。
最近,国内外一些新进展也给生物传感技术的应用带来了新的思路和探索的方向。
例如:德国研究人员成功地结合全息照相术和生物传感技术,制造出一种高精度的胶体带传感器,可用于快速识别病原体,为医学中药品研发和生产提供更多的实践经验;我国科研人员也取得了不少有意义的进展:北京大学张震教授团队研制出一种基于吸附富集技术和发光技术的荧光免疫检测技术,提高了药物残留物检测效能。
传感器技术的新进展与应用
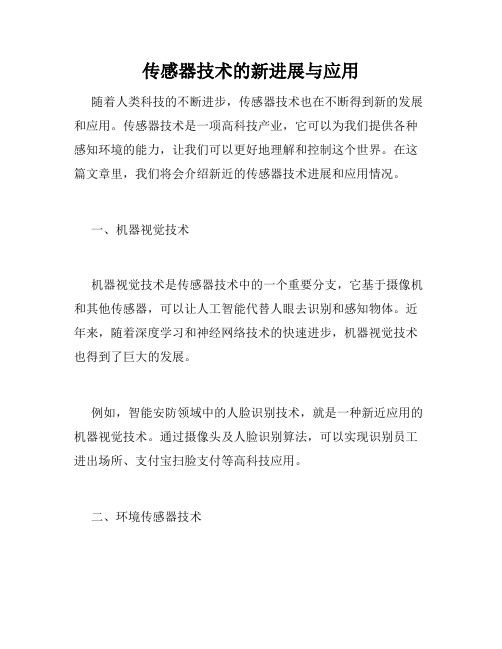
传感器技术的新进展与应用随着人类科技的不断进步,传感器技术也在不断得到新的发展和应用。
传感器技术是一项高科技产业,它可以为我们提供各种感知环境的能力,让我们可以更好地理解和控制这个世界。
在这篇文章里,我们将会介绍新近的传感器技术进展和应用情况。
一、机器视觉技术机器视觉技术是传感器技术中的一个重要分支,它基于摄像机和其他传感器,可以让人工智能代替人眼去识别和感知物体。
近年来,随着深度学习和神经网络技术的快速进步,机器视觉技术也得到了巨大的发展。
例如,智能安防领域中的人脸识别技术,就是一种新近应用的机器视觉技术。
通过摄像头及人脸识别算法,可以实现识别员工进出场所、支付宝扫脸支付等高科技应用。
二、环境传感器技术环境传感器技术可以用来感知周围环境中的不同物理量,通过对这些物理量的监测和分析,可以帮助我们更好地理解和控制环境。
例如,气象传感器技术可以使用多种传感器来监测气温、湿度、压强、风速等气象参数,从而可以实现天气预报等便利功能。
三、运动传感器技术运动传感技术是指能够检测和监视身体运动的传感器技术,该技术广泛应用于运动医学、运动健身、生物力学等领域。
像智能手环、智能手表、智能鞋垫等都是运动传感器技术的应用。
四、医学传感器技术医学传感器技术是指将传感器技术应用于病人身体检测、康复等方面,用来实现更加方便、快速、精确的医疗服务。
例如,随身手持型体温计、血压计、血氧计等均是传感器技术在医疗领域的应用。
五、自然环境传感器技术自然环境传感器技术是指通过传感器技术,对自然环境进行监测和分析,帮助人们更好地理解自然环境的变化。
比如通过对森林、水源等环境的污染和破坏进行实时监测,我们可以更好地了解环境状况,更好地保护我们的地球。
六、农业传感器技术传感器技术也可以应用于农业领域,通过对土壤质量、气候、作物生长等进行检测和分析,可以帮助农民做出更合理的决策,提高农作物产量和品质。
七、智慧城市传感器技术智慧城市是一个处于建设中的新领域,传感器技术在此处可以发挥至关重要的作用。
浅谈传感器技术的发展现状与趋势
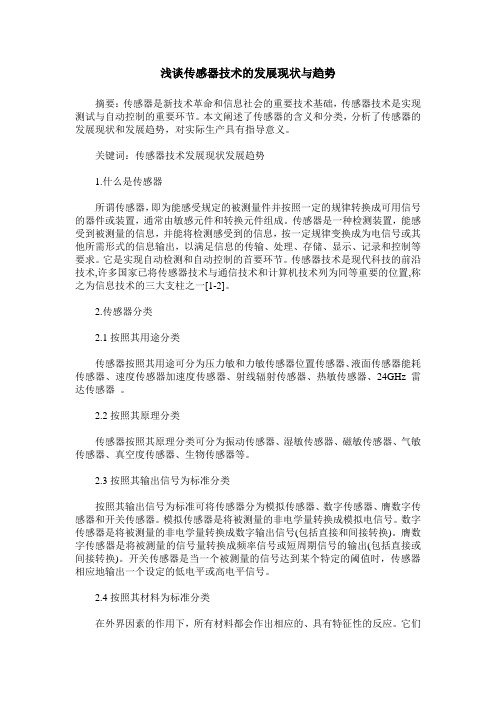
浅谈传感器技术的发展现状与趋势摘要:传感器是新技术革命和信息社会的重要技术基础,传感器技术是实现测试与自动控制的重要环节。
本文阐述了传感器的含义和分类,分析了传感器的发展现状和发展趋势,对实际生产具有指导意义。
关键词:传感器技术发展现状发展趋势1.什么是传感器所谓传感器,即为能感受规定的被测量件并按照一定的规律转换成可用信号的器件或装置,通常由敏感元件和转换元件组成。
传感器是一种检测装置,能感受到被测量的信息,并能将检测感受到的信息,按一定规律变换成为电信号或其他所需形式的信息输出,以满足信息的传输、处理、存储、显示、记录和控制等要求。
它是实现自动检测和自动控制的首要环节。
传感器技术是现代科技的前沿技术,许多国家已将传感器技术与通信技术和计算机技术列为同等重要的位置,称之为信息技术的三大支柱之一[1-2]。
2.传感器分类2.1按照其用途分类传感器按照其用途可分为压力敏和力敏传感器位置传感器、液面传感器能耗传感器、速度传感器加速度传感器、射线辐射传感器、热敏传感器、24GHz雷达传感器。
2.2按照其原理分类传感器按照其原理分类可分为振动传感器、湿敏传感器、磁敏传感器、气敏传感器、真空度传感器、生物传感器等。
2.3按照其输出信号为标准分类按照其输出信号为标准可将传感器分为模拟传感器、数字传感器、膺数字传感器和开关传感器。
模拟传感器是将被测量的非电学量转换成模拟电信号。
数字传感器是将被测量的非电学量转换成数字输出信号(包括直接和间接转换)。
膺数字传感器是将被测量的信号量转换成频率信号或短周期信号的输出(包括直接或间接转换)。
开关传感器是当一个被测量的信号达到某个特定的阈值时,传感器相应地输出一个设定的低电平或高电平信号。
2.4按照其材料为标准分类在外界因素的作用下,所有材料都会作出相应的、具有特征性的反应。
它们中的那些对外界作用最敏感的材料,即那些具有功能特性的材料,被用来制作传感器的敏感元件。
从所应用的材料观点出发可将传感器分成下列几类:(1)按照其所用材料的类别分:金属聚合物和陶瓷混合物;(2)按材料的物理性质分:导体绝缘体和半导体磁性材料;(3)按材料的晶体结构分:单晶、多晶和非晶材料。
传感器技术的进展与应用

传感器技术的进展与应用随着科技的不断发展,人类能够探究和利用的事物越来越多。
而传感器技术在现代社会中的应用越来越广泛,可谓是科技发展的重要一环。
本文将从传感器技术的进展和应用两个方面,来探究目前这一领域的情况。
一、传感器技术的进展传感器是一种检测并传递物理量和/或化学量的装置,通常由敏感元件、信号转换器和数据处理器等组成。
传感器技术是一门多学科交叉的技术,涵盖了物理、化学、材料学、电子工程、计算机科学等多个学科,而它的进展也与这些学科的发展密切相关。
目前,传感器技术进展主要表现在以下几个方面:1. 精度提高:随着微电子技术和纳米技术的发展,传感器制造工艺得到了极大的改进和提高。
如今,已经有越来越多的传感器能够达到亚纳米级别的分辨率,具备更高的精度。
2. 小型化:随着芯片技术的不断进步,一些传感器不仅尺寸越来越小,而且功耗更低。
这使得传感器能够运用于更多的领域中,并能够实现更广泛的应用。
3. 多功能化:随着传感器技术的不断提升,除了能检测传统的物理量和化学量外,现今的传感器还能检测声音、光线、压力、温度、湿度等一系列信息。
这使得传感器具备了更加多样化的功能和应用场景。
4. 网络化:随着物联网的普及,传感器技术得到了大力推广。
传感器与其他设备的结合,通过互联网技术实现了设备之间的互通,使得信息的获取和传输更加便利和高效。
二、传感器技术的应用随着传感器技术的不断发展,传感器已经被广泛地应用于各个领域,如智能家居、医疗保健、环境监测、车载电子、工业自动化、安防监控等。
1. 智能家居:目前,越来越多的智能家居设备如温控器、灯光系统、智能门锁等都与传感器技术相结合,实现了更加智能化和高效的家居管理。
2. 医疗保健:传感器技术在医疗保健领域中的应用主要体现在生命体征监测、健康管理和医疗辅助方面。
如今,有越来越多的医疗设备如心电图、口氧仪、血糖仪等都与传感器相结合,实现了更加精细化和高效的医疗管理和服务。
3. 环境监测:随着环境污染的日益严重,传感器技术在环境监测方面的应用越来越重要。
传感器与检测技术的发展趋势

传感器与检测技术的发展趋势随着科技的不断进步和人类社会的发展,传感器与检测技术的应用领域日益广泛。
传感器是一种能够感知和检测各种物理量和环境参数的设备,而检测技术则是利用传感器获得的数据进行分析和处理的方法和技术。
本文将重点探讨传感器与检测技术的发展趋势,并分析其在不同领域的应用。
一、物联网与传感器网络的发展随着物联网的兴起,传感器网络成为物联网中的核心技术之一。
传感器网络是由大量布置在空间中的传感器节点组成,利用无线通信技术实现节点之间的数据传输和协同工作。
传感器网络的发展趋势主要体现在两个方面:一是传感器节点的小型化与低功耗化;二是网络通信技术的进步与创新。
随着小型化和低功耗化技术的不断发展,传感器节点可以更加轻便和节能,可以被广泛应用于环境监测、智能家居、智慧城市等领域。
二、人工智能与传感器技术的结合人工智能的快速发展为传感器技术的应用提供了新的机遇和挑战。
传感器与人工智能的结合可以使传感器具备更高级的功能和智能化的处理能力。
例如,通过使用深度学习算法,传感器可以学习和识别不同类型的数据模式,并做出智能的决策。
此外,还可以利用传感器获取的数据进行机器学习和数据挖掘,进一步优化传感器的性能和功能。
三、新材料与传感器技术的融合新材料的发展对传感器技术的进步具有重要影响。
传感器需要具备高灵敏度、高稳定性和高选择性,而新材料的应用可以满足这些要求。
例如,纳米材料的应用可以增加传感器的灵敏度和响应速度;纳米结构材料的制备可以提高传感器的选择性和稳定性。
因此,新材料与传感器技术的融合将为传感器的应用领域带来新的突破。
四、生物传感器的发展趋势生物传感器是一种能够利用生物材料和生物分子进行检测和分析的传感器。
生物传感器的发展趋势主要包括两个方向:一是生物传感器的多功能化与智能化;二是生物传感器与医疗健康领域的深度融合。
通过引入新的生物材料和生物分子,生物传感器可以实现对多种物质和参数的检测。
同时,生物传感器在医疗健康领域的应用也是一个热点研究方向,如血糖仪、心率监测器等,为人们的生活提供了更多便利和保障。
传感检测技术发展现状及未来发展趋势

传感检测技术发展现状及未来发展趋势下载提示:该文档是本店铺精心编制而成的,希望大家下载后,能够帮助大家解决实际问题。
文档下载后可定制修改,请根据实际需要进行调整和使用,谢谢!本店铺为大家提供各种类型的实用资料,如教育随笔、日记赏析、句子摘抄、古诗大全、经典美文、话题作文、工作总结、词语解析、文案摘录、其他资料等等,想了解不同资料格式和写法,敬请关注!Download tips: This document is carefully compiled by this editor. I hope that after you download it, it can help you solve practical problems. The document can be customized and modified after downloading, please adjust and use it according to actual needs, thank you! In addition, this shop provides you with various types of practical materials, such as educational essays, diary appreciation, sentence excerpts, ancient poems, classic articles, topic composition, work summary, word parsing, copy excerpts, other materials and so on, want to know different data formats and writing methods, please pay attention!一、现状分析1. 传感检测技术在工业生产中的应用。
检测传感技术的应用
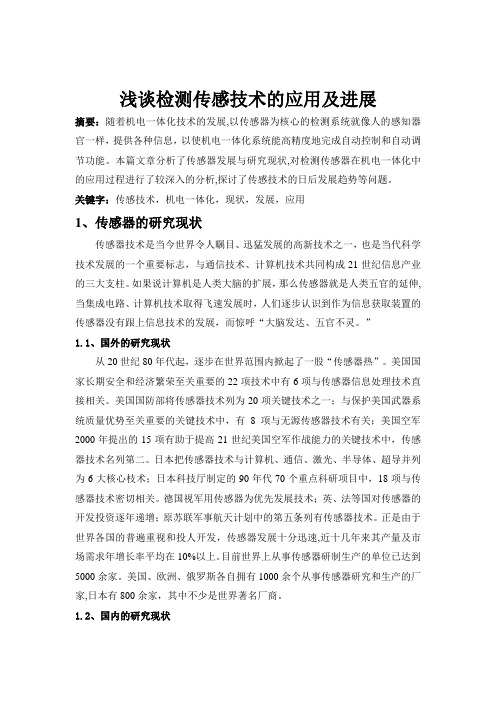
浅谈检测传感技术的应用及进展摘要:随着机电一体化技术的发展,以传感器为核心的检测系统就像人的感知器官一样,提供各种信息,以使机电一体化系统能高精度地完成自动控制和自动调节功能。
本篇文章分析了传感器发展与研究现状,对检测传感器在机电一体化中的应用过程进行了较深入的分析,探讨了传感技术的日后发展趋势等问题。
关键字:传感技术,机电一体化,现状,发展,应用1、传感器的研究现状传感器技术是当今世界令人瞩目、迅猛发展的高新技术之一,也是当代科学技术发展的一个重要标志,与通信技术、计算机技术共同构成21世纪信息产业的三大支柱。
如果说计算机是人类大脑的扩展,那么传感器就是人类五官的延伸,当集成电路、计算机技术取得飞速发展时,人们逐步认识到作为信息获取装置的传感器没有跟上信息技术的发展,而惊呼“大脑发达、五官不灵。
”1.1、国外的研究现状从20世纪80年代起,逐步在世界范围内掀起了一股“传感器热”。
美国国家长期安全和经济繁荣至关重要的22项技术中有6项与传感器信息处理技术直接相关。
美国国防部将传感器技术列为20项关键技术之一;与保护美国武器系统质量优势至关重要的关键技术中,有8项与无源传感器技术有关;美国空军2000年提出的15项有助于提高21世纪美国空军作战能力的关键技术中,传感器技术名列第二。
日本把传感器技术与计算机、通信、激光、半导体、超导并列为6大核心枝术;日本科技厅制定的90年代70个重点科研项目中,18项与传感器技术密切相关。
德国视军用传感器为优先发展技术;英、法等国对传感器的开发投资逐年递增;原苏联军事航天计划中的第五条列有传感器技术。
正是由于世界各国的普遍重视和投人开发,传感器发展十分迅速,近十几年来其产量及市场需求年增长率平均在10%以上。
目前世界上从事传感器研制生产的单位已达到5000余家。
美国、欧洲、俄罗斯各自拥有1000余个从事传感器研究和生产的厂家,日本有800余家,其中不少是世界著名厂商。
传感与检测技术的研究与应用
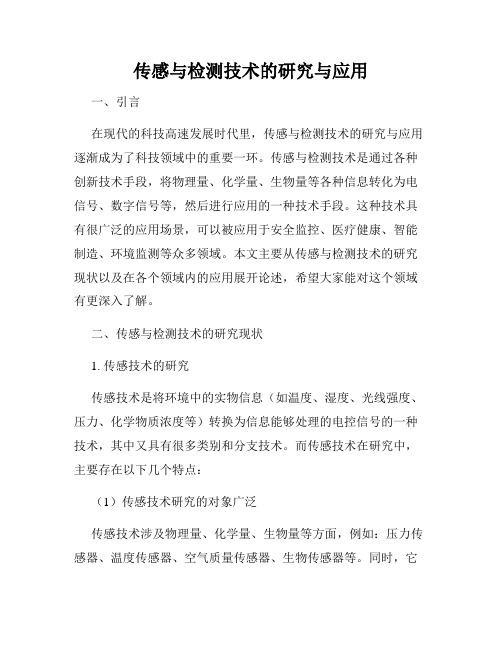
传感与检测技术的研究与应用一、引言在现代的科技高速发展时代里,传感与检测技术的研究与应用逐渐成为了科技领域中的重要一环。
传感与检测技术是通过各种创新技术手段,将物理量、化学量、生物量等各种信息转化为电信号、数字信号等,然后进行应用的一种技术手段。
这种技术具有很广泛的应用场景,可以被应用于安全监控、医疗健康、智能制造、环境监测等众多领域。
本文主要从传感与检测技术的研究现状以及在各个领域内的应用展开论述,希望大家能对这个领域有更深入了解。
二、传感与检测技术的研究现状1. 传感技术的研究传感技术是将环境中的实物信息(如温度、湿度、光线强度、压力、化学物质浓度等)转换为信息能够处理的电控信号的一种技术,其中又具有很多类别和分支技术。
而传感技术在研究中,主要存在以下几个特点:(1)传感技术研究的对象广泛传感技术涉及物理量、化学量、生物量等方面,例如:压力传感器、温度传感器、空气质量传感器、生物传感器等。
同时,它们所涉及的场所也异常分散,可以被设计为室外设备、室内设备、个人膜式装置等各种不同形态。
(2)传感技术特点复杂传感技术不同于机器学习或数据挖掘类技术,它的研究需要特别操作及稳定性保障,还需要针对具体应用环境进行深入的研究,是具有很高难度的研究课题。
(3)传感技术涉及应用广泛由于传感技术应用场景较为广泛,可以被应用于供应链管理、农业监控、医疗救护、对环境的管理等多个领域。
因此,传感技术也具有很大的研究价值与应用价值。
2. 检测技术的研究检测技术是一种侦测生产过程或输出产物质量指标的技术手段,它可以通过物、化、生物技术等多种途径实现。
随着生产制造和医疗技术的发展,近年来检测技术研究成果在各行各业中越来越受到关注,检测技术研究存在以下几个特点:(1)检测技术分支众多检测技术的研究方向十分分散,例如生产工艺检测、医学诊断检测、食品质量检测等等。
(2)检测技术数据处理需求强烈检测技术所产生的数据处理需求较强,需要通过数据处理手段将原始数据进行处理分析,再做出最终判定。
传感器技术的新进展和应用

传感器技术的新进展和应用随着科技的不断发展,传感器技术也在不断地进步和创新,越来越多的新型传感器被开发出来,应用也在不断扩大和深化。
在本文中,我们将探讨当前传感器技术的新进展和应用,并分析其未来的发展趋势。
一、新型传感器的研发和应用1.光纤传感器光纤传感器是一种通过光纤传输光信号来测量物理量的传感器。
相对于传统的电子传感器,光纤传感器具有更高的精度、更高的信号传输速度和更低的噪声干扰。
目前,光纤传感器已被广泛应用于油气勘探、地震监测、石油化工、航天航空等领域。
2.生物传感器生物传感器是一种通过生物化学反应来检测生物分子的传感器。
生物传感器广泛应用于医疗、环保、食品安全等领域。
例如,血糖仪、血氧仪、血压计等医疗设备都是基于生物传感器技术开发的。
3.压力传感器压力传感器是一种用于测量介质压力的传感器。
随着航空航天、汽车工业的发展,对压力传感器的需求也越来越高。
目前,国内外压力传感器的市场竞争依旧激烈,但随着智能制造的进一步推广,压力传感器的应用前景将变得更加广阔。
4.气体传感器气体传感器是一种通过检测气体中的物质来测量气体浓度的传感器。
气体传感器广泛应用于煤气检测、空气净化、环境监测等领域。
未来,随着环保意识的提升,气体传感器市场的需求将会持续增长。
二、传感器技术的未来发展趋势1.智能化随着物联网技术和人工智能技术的不断发展,传感器的智能化程度将越来越高。
未来,传感器将会更加智能化、协同化、自适应化,能够实现更高效、更安全、更低成本的应用。
2.微型化微传感器是一种体积较小、功耗低的传感器。
微传感器已被广泛应用于生物、医疗、环保等领域,并在一定程度上改变了传统传感器的布局和设计。
未来,随着微纳制造技术和互连技术的发展,微传感器的市场需求也将继续增长。
3.多功能化传统的传感器只能测量一种物理量,但现在的传感器已经具备了多种测量功能。
未来,随着传感器技术的不断发展,传感器的功能将越来越丰富、多样化,能够同时测量多种物理量,更好地适应市场的实际需求。
浅谈检测传感技术在机电一体化中的应用
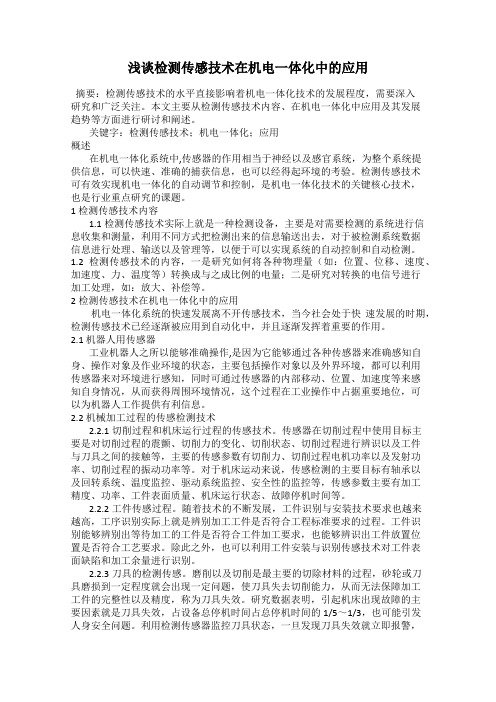
浅谈检测传感技术在机电一体化中的应用摘要:检测传感技术的水平直接影响着机电一体化技术的发展程度,需要深入研究和广泛关注。
本文主要从检测传感技术内容、在机电一体化中应用及其发展趋势等方面进行研讨和阐述。
关键字:检测传感技术;机电一体化;应用概述在机电一体化系统中,传感器的作用相当于神经以及感官系统,为整个系统提供信息,可以快速、准确的捕获信息,也可以经得起环境的考验。
检测传感技术可有效实现机电一体化的自动调节和控制,是机电一体化技术的关键核心技术,也是行业重点研究的课题。
1 检测传感技术内容1.1检测传感技术实际上就是一种检测设备,主要是对需要检测的系统进行信息收集和测量,利用不同方式把检测出来的信息输送出去,对于被检测系统数据信息进行处理、输送以及管理等,以便于可以实现系统的自动控制和自动检测。
1.2检测传感技术的内容,一是研究如何将各种物理量(如:位置、位移、速度、加速度、力、温度等)转换成与之成比例的电量;二是研究对转换的电信号进行加工处理,如:放大、补偿等。
2检测传感技术在机电一体化中的应用机电一体化系统的快速发展离不开传感技术,当今社会处于快速发展的时期,检测传感技术已经逐渐被应用到自动化中,并且逐渐发挥着重要的作用。
2.1 机器人用传感器工业机器人之所以能够准确操作,是因为它能够通过各种传感器来准确感知自身、操作对象及作业环境的状态,主要包括操作对象以及外界环境,都可以利用传感器来对环境进行感知,同时可通过传感器的内部移动、位置、加速度等来感知自身情况,从而获得周围环境情况,这个过程在工业操作中占据重要地位,可以为机器人工作提供有利信息。
2.2 机械加工过程的传感检测技术2.2.1切削过程和机床运行过程的传感技术。
传感器在切削过程中使用目标主要是对切削过程的震颤、切削力的变化、切削状态、切削过程进行辨识以及工件与刀具之间的接触等,主要的传感参数有切削力、切削过程电机功率以及发射功率、切削过程的振动功率等。
传感器技术的最新进展和应用前景

传感器技术的最新进展和应用前景传感器技术是物联网时代的关键技术之一,它被广泛应用于各个领域。
传感器是一种能够感知环境信息并将其转化为可用信号的设备,它的应用范围涵盖了工业制造、自动化控制、医疗健康、环境监测等众多领域。
随着科技的不断进步,传感器技术也在不断发展,取得了许多突破性的进展。
本文将介绍传感器技术的最新进展和应用前景。
一、传感器技术的最新进展1. 多功能集成化设计随着技术的发展,传感器的尺寸越来越小,功能越来越强大。
最新的传感器产品不仅能够感知环境的温度、湿度,还可以测量光强、气压、声音等多种参数。
此外,传感器的设计也趋向于集成化,通过将多种传感器集成到同一芯片上,减少了设备的体积和成本,提高了传感器系统的可靠性和稳定性。
2. 无线传输和云端连接传感器的数据传输方式也在不断创新。
传统的有线传输方式限制了传感器的使用范围和布局。
而最新的传感器产品采用了无线传输技术,如蓝牙、Wi-Fi、LoRa 等,可以使传感器与其他设备实现无缝连接。
此外,传感器还可以通过云端连接实现数据的存储和分析,提高传感器系统的智能化和自动化水平。
3. 精度和灵敏度的提升随着制造工艺和材料的进步,传感器的精度和灵敏度不断提高。
最新的传感器产品能够实现微小物体的探测和测量,能够感知微小变化并进行精确的数据采集。
这些传感器广泛应用于微米级制造、精密测量和科学研究等领域,推动了相关行业的发展和创新。
4. 智能化和自适应控制最新的传感器产品不仅仅是数据采集的工具,还具备智能化和自适应控制的功能。
传感器可以通过学习和算法优化来实现数据的自动分析和处理,提供更加智能化的服务。
例如,在智能家居中,温度传感器可以根据用户的习惯和喜好自动调节室内温度,提升居住舒适度。
二、传感器技术的应用前景1. 工业制造传感器技术在工业制造中的应用前景广阔。
传感器可以实时监测生产设备的状态和运行情况,通过数据分析和预测,提高生产效率和质量。
另外,传感器还可以用于检测工作环境的安全性,实现自动化控制和智能化管理。
传感器技术在环境监测中的应用与发展

传感器技术在环境监测中的应用与发展近年来,随着环境污染和气候变化等问题的加剧,越来越多的人开始关注环境质量的监测和改善。
而传感器技术,作为一种能够实时感知环境信息的技术手段,发挥着越来越重要的作用。
本文将介绍传感器技术在环境监测中的应用与发展。
一、传感器技术的概述传感器技术是一种能够将物理量、化学量等转换为电信号的技术手段。
传感器可以实时感知环境信息,并将结果反馈给数据处理器或其他控制器。
传感器技术广泛应用于测量和监测领域,涉及到气体、温度、湿度、光、声、压力等多个领域。
传感器的工作原理分为两个部分:信号采集和信号处理。
信号采集是指将环境信息转换为电信号的过程,主要涉及到传感器元件的选择和电路的设计。
信号处理是指对信号进行分析、处理的过程,旨在提高传感器的灵敏性、准确性和稳定性。
二、传感器技术在环境监测中的应用1. 大气环境监测大气污染成为影响人们生活品质的一大问题,而传感器技术在大气环境监测中发挥着重要的作用。
气体传感器可以检测空气中的各种污染物,如二氧化硫、氮氧化物、臭氧、PM2.5等,实现对大气环境的监测和掌控。
2. 土壤监测土壤也是环境中重要的组成部分,其中有机物和化学物质的浓度会对农作物的生长产生重要影响,甚至会导致作物死亡。
传感器技术可以检测土壤中的湿度、温度、pH值等指标,实时了解土壤的状况并提供有效的农业数据。
3. 水环境监测水环境的监测涉及到地下水、河流、湖泊、海洋等多个方面,而传感器技术可以用于监测水位、水质、水温、流速等指标。
传感器技术可以在短时间内对水环境的状况进行监测,有助于制定相应的水资源管理措施。
三、传感器技术在环境监测中的发展传感器技术在环境监测中的应用,使得人们能够更加全面地了解环境状况,确保环境质量的稳定和改善。
未来,传感器技术在环境监测中的发展将会越来越多样化和智能化。
智能传感器是一种通过自学习和优化算法实现自我修正和自我适应的传感器。
智能传感器具有更高的灵敏度和更低的信噪比,可以更准确地感知环境信息。
浅谈检测传感技术的应用及进展

浅谈检测传感技术的应用及进展摘要:检测传感技术是机电一体化系统的关键技术之一,对于机电一体化技术的发展具有十分重要的意义。
本文主要介绍和探讨检测传感技术在机电一体化中的应用,并讨论了其发展的趋势。
关键词:检测传感机电一体化应用发展趋势检测传感技术是机电一体化系统的关键技术之一,它是一门多学科,知识密集的应用技术。
传感检测装置是系统的感受器,是实现自动控制,自动调节的关键环节,其功能越强,系统的自动化程序越高[1]。
现代工程要求传感器能快速、准确地获取信息并能经受严酷环境的考验,它是机电一体化系统达到高水平的保证。
因此,发展检测传感技术,对于机电一体化技术的发展具有十分重要的意义。
1、检测传感技术在机电一体化中的应用今天,检测传感技术已经渗透到生产和生活的各个领域。
高度自动化的工厂,设备,装置或系统,可以说是“传感检测技术的大集合”。
各种仪器设备、家电,办公自动化设备,加工中心,扎钢生产线等,传感检测技术的应用已然非常广泛。
考虑到所学的机电系统设计课程和自身专业背景,下面重点介绍一下传感检测技术在机电一体化中的应用。
1.1检测传感技术在数控机床的应用数控机床是现代高科技发展的产物,每当一批零件开始加工时,有大量的检测需要完成,包括夹具和零件的装卡,找正,零件编程点的测定、工序间检测及加工完毕检测等。
数控机床的在线检测系统结构如图1所示,由软件和硬件两部分组成。
图1数控机床的在线检测系统结构将检测技术融于数控加工的内容之中,采用在线测量的方式,能使操作者及时发现工件存在的问题,并反馈给数控系统。
在线检测技术应用于数控系统,提高了测量精度,更好地保证了机床的加工质量,促进加工测量一体化的发展。
1.2 检测传感技术在汽车中的应用检测传感技术在汽车中的应用很广泛,例如:为使汽车安全行驶,研制的电子防滑控制装置与电子变速控制装置。
为防止排气污染,大力研制的电子燃料喷射装置、排气再循环装置等。
下面以电子防滑控制装置与电子燃料喷射装置为例,说明检测传感技术的应用状况。
传感检测技术的作用和发展方向探索

传感检测技术的作用和开展方向探索传感检测技术不仅是机电一体化中不可缺少的技术,也是实现自动控制、自动调节的关键环节。
在很大程度上传感器的检测技术影响着自动化系统的质量。
在一个自动化系统中,只有利用传感器的检测技术对各方面参数进行检查,才能使整个自动化系统正常的工作。
在科技高速开展的'今天,不管是生活中还是生产中都能利用到检测传感技术。
例如,局部仪器设备、办公设备、家电中的计算机继承制造系统、C机床、大型发电机等等。
在国防事业和装备武器上,传感检测技术同样有着重要的作用。
可以看出,传感检测技术在提高生产设备和系统平安经济运行监控检测手段、控制产品质量等方面都推动了社会生产力和科学技术的开展。
总的来说,无论从宇宙到陆地,从陆地到海洋,从顶尖技术到根底知识,从复杂的大自动化设备到社会中每个细节,传感检测技术都扮演着重要的角色。
1.精度的开展。
在原有的根底上研究出更加具有灵敏度、准确度、灵活性的传感器。
2.可靠性的开展。
传感器的抗温度性能、抗压力性能、抗干扰性能都是影响传感器可靠性的关键因素,所以我们应该注重这些因素,增强传感器的可靠性。
3.微型化开展。
努力开发出更好的材料与技术使传感器微型化的理想成为现实。
4.节能性开展。
传感器的工作是建立在电源的根底上的,既消耗能源又费时费力。
所以我们应该努力研制m不靠电源的传感器。
虽说目前我国在传感器上的研制与传感检测技术的应用已经有所成就,但是与外国的很多先进技术还具有很大的差距。
所以,我们应该从研究手法和设备上做出提高,从而使传感器与检测技术在整体的运用上有所增强。
[1]李小玲传感器与检测技术在机电一体化系统中的应用[J] 现代电子技术应用.xx(01).[2]林青.浅析传感器技术在机电一体化系统中的应用.附件播送电视大学学报,xx(03).[3]季俊星.浅析传感器在机电一体化系统中的应用.使用科技.xx(09).。
传感器智能检测技术的应用与发展(一)

传感器智能检测技术的应用与发展(一)引言:传感器智能检测技术是一种基于传感器的智能化检测技术,通过传感器收集环境信息并经过处理分析,为人们提供更准确、更高效的检测结果。
随着科技的不断进步,传感器智能检测技术在各个行业中得到了广泛应用和快速发展。
本文将从以下五个方面阐述传感器智能检测技术的应用与发展。
正文:一、农业领域1. 实时监测土壤水分和温度2. 植物叶片光合作用的实时监测3. 动态监测氮、磷、钾等土壤养分含量4. 发现并预测病虫害的发生5. 自动化灌溉系统的智能检测与控制二、工业领域1. 在生产线中实时监测生产过程的关键参数2. 确定设备状态,提前预测可能出现的故障3. 控制温湿度等环境因素,维护最佳生产条件4. 监测危险品和有害物质的浓度以及泄漏情况5. 实现智能化的仓储和物流管理三、医疗健康领域1. 身体生理参数的实时监测,如心率、血压、体温等2. 预防和治疗过程中的病情监测与评估3. 自动化药物配送和用药提醒4. 智能化的康复训练和辅助器具5. 远程医疗监护与诊断四、交通运输领域1. 实时监测和优化交通流量2. 智能车辆监测与控制,包括自动驾驶技术3. 实时监测道路状况和交通安全4. 预测交通拥堵,优化道路规划和交通信号灯控制5. 高精度导航系统的实时监测和改进五、环境保护领域1. 气体浓度监测,包括空气质量和有害气体排放2. 水质监测与污染源追踪3. 声音、震动等环境噪声监测4. 火灾监测与预警系统5. 自然灾害的实时监测与预警总结:传感器智能检测技术在农业、工业、医疗健康、交通运输和环境保护等领域中得到了广泛应用。
它为各个行业提供了更高效、更准确的检测方法,有着重要的意义和广阔的发展空间。
随着科技的不断进步与创新,传感器智能检测技术将在更多领域发挥更大的作用,促进社会进步和经济发展。
- 1、下载文档前请自行甄别文档内容的完整性,平台不提供额外的编辑、内容补充、找答案等附加服务。
- 2、"仅部分预览"的文档,不可在线预览部分如存在完整性等问题,可反馈申请退款(可完整预览的文档不适用该条件!)。
- 3、如文档侵犯您的权益,请联系客服反馈,我们会尽快为您处理(人工客服工作时间:9:00-18:30)。
浅谈检测传感技术的应用及进展
摘要:检测传感技术是机电一体化系统的关键技术之一,对于机电一体化技术的发展具有十分重要的意义。
本文主要介绍和探讨检测传感技术在机电一体化中的应用,并讨论了其发展的趋势。
关键词:检测传感机电一体化应用发展趋势
检测传感技术是机电一体化系统的关键技术之一,它是一门多学科,知识密集的应用技术。
传感检测装置是系统的感受器,是实现自动控制,自动调节的关键环节,其功能越强,系统的自动化程序越高[1]。
现代工程要求传感器能快速、准确地获取信息并能经受严酷环境的考验,它是机电一体化系统达到高水平的保证。
因此,发展检测传感技术,对于机电一体化技术的发展具有十分重要的意义。
1、检测传感技术在机电一体化中的应用
今天,检测传感技术已经渗透到生产和生活的各个领域。
高度自动化的工厂,设备,装置或系统,可以说是“传感检测技术的大集合”。
各种仪器设备、家电,办公自动化设备,加工中心,扎钢生产线等,传感检测技术的应用已然非常广泛。
考虑到所学的机电系统设计课程和自身专业背景,下面重点介绍一下传感检测技术在机电一体化中的应用。
1.1检测传感技术在数控机床的应用
数控机床是现代高科技发展的产物,每当一批零件开始加工时,有大量的检测需要完成,包括夹具和零件的装卡,找正,零件编程点的测定、工序间检测及加工完毕检测等。
数控机床的在线检测系统结构如图1所示,由软件和硬件两部分组成。
图1数控机床的在线检测系统结构
将检测技术融于数控加工的内容之中,采用在线测量的方式,能使操作者及时发现工件存在的问题,并反馈给数控系统。
在线检测技术应用于数控系统,提高了测量精度,更好地保证了机床的加工质量,促进加工测量一体化的发展。
1.2 检测传感技术在汽车中的应用
检测传感技术在汽车中的应用很广泛,例如:为使汽车安全行驶,研制的电子防滑控制装置与电子变速控制装置。
为防止排气污染,大力研制的电子燃料喷射装置、排气再循环装置等。
下面以电子防滑控制装置与电子燃料喷射装置为例,说明检测传感技术的应用状况。
要使汽车停车,应该根据汽车轮胎与地面的状态求出最有效的滑移率,使制动压力接近这种最佳状态[2]。
然而,对于实际的电子防滑控制装置来说,采用电气方式检测路面状态和汽车对地的速度是非常困难的。
所以,一般都是只检测车轮的旋转速度。
如图2所示,而且,从车轮的旋转速度与时间的关系计算出车轮的减速度。
在超出预先设定的基准减速度情况下,与驾驶员踩制动器的力无关,而由制动器压力控制装置自动减弱制动器的压力,防止打滑。
图2 电子防滑控制装置工作原理
可是,因为这一方法原则上讲并不太好,所以现在正在研究在车内安装加速计与雷达,以检测出对地速度,然后根据滑移率来控制制动器压力。
电子燃料喷射装置的功能如图3所示。
这里,其电气传感器用来检测影响发动机工作的大量参数,而其数据则由集成电路或大规模集成电路构成的控制器进
行运算处理。
然后,根据其处理信息,控制在燃料喷射用的注油器上所安装的脉冲电流计的时刻与加电流的时间长短,使发动机内的燃烧始终保持最佳状态。
图3 电子燃料喷射装置
由此可见,随着传感器技术和其他新技术的应用,现代化汽车工业进入了全新时期。
汽车的机电一体化要求,用自动控制系统取代纯机械式控制部件,这不仅体现在发动机上,为更全面地改善汽车性能,增加人性化服务功能,降低油耗,减少排气污染,提高行驶安全性、可靠性、操作方便和舒适性,先进的检测和控制技术已扩大应用到汽车全身。
在其所有重点控制系统中,必不可少地使用曲轴位置传感器、吸气及冷却水温度传感器、压力传感器、气敏传感器等各种传感器。
1.3 检测传感技术在机器人中的应用
在手工操作的复杂工作中,就使用了机器人。
在这种情况下,机器人必须具备高度信息处理能力的大脑以及相当于人的手足的操作机构。
工业机器人之所以能够准确操作,是因为它能够通过各种传感器来准确感知自身、操作对象及作业环境的状态,包括:其自身状态信息的获取通过内部传感器(位置、位移、速度、加速度等)来完成,操作对象与外部环境的感知通过外部传感器来实现,这个过程非常重要,足以为机器人控制提供反馈信息[3]。
通常微动开关、光电开关、电涡流等传感器安装在机器人的每个关节上进行零位和极限位置的检测,前者保证机器人的重复定位精度和轨迹精度,后者则起保护机器人和安全动作的作用。
1.4 检测传感技术在机械加工过程中的应用
切削过程传感检测的目的,在于优化切削过程的生产率、制造成本或(金属)材料的切除率等。
切削过程传感检测的目标,有切削过程的切削力及其变化、切削过程颤震、刀具与工件的接触和切削时切屑的状态及切削过程辨识等,而最重要的传感参数有切削力、切削过程振动、切削过程声发射、切削过程电机的功率等。
对于机床的运行而言,主要的传感检测目标有驱动系统、轴承与回转系统、温度的监测与控制及安全性等,其传感参数有机床的故障停机时间、被加工件的表面粗糙度和加工精度、功率、机床状态与冷却润滑液的流量等[4]。
与刀具和机床的过程检测技术相比,工件的过程监视是研究和应用最早、最多的。
它们多数以工件加工质量控制为目标。
20世纪80年代以来,工件识别和工件安装位姿监视要求,也提到日程上来。
粗略地说,工序识别,是为辨识所执行的加工工序是否是工件加工要求的工序;工件识别,是辨识送入机床待加工的工件或毛坯是否是要求加工的工件或毛坯,同时还要求辨识工件安装的位姿,是否是工艺规程要求的位姿。
此外,还可以利用工件识别和工件安装监视传感待加工毛坯或工件的加工裕量和表面缺陷。
完成这些识别与监视,将采用或开发许多传感器,如基于TV或CCD的机器视觉传感器、激光表面粗糙度传感系统等。
2、检测传感技术的发展趋势
随着半导体、计算机技术的发展,新型、具有特殊功能的传感器不断涌现出来,检测装置也向小型化、固体化及智能化方向变革,应用领域也越加宽广,从工业控制、科学实验,以至家用电器、个人用品,都可发现检测传感技术的广泛应用。
目前,检测传感技术的发展主要表现在以下几个方面。
(1) 不断提高检测系统的测量精度、量程范围、延长使用寿命、提高可靠性等。
(2) 应用新技术和新的物理效应,扩大检测领域。
(3) 采用微型计算机技术,使检测传感技术智能化。
(4) 不断开发新型、微型、智能化传感器,如智能型传感器,生物传感器,高性能集成传感器等。
(5)不断开发传感器的新型敏感元件材料和采用新的加工工艺,提高仪器的性能、可靠性,扩大应用范围,使测试仪器向高精度和多功能方向发展。
(6) 不断研究和发展微电子技术、微型计算机技术、现场总线技术与仪器仪表和传感器相结合的多功能融合技术,形成智能化测试系统,使测量精度、自动化水平进一步提高。
(7) 不断研究开发仿生传感器,主要是指模仿人或动物的感觉器官的传感器,即视觉传感器、听觉传感器、嗅觉传感器、味觉传感器、触觉传感器等。
(8) 参数测量和数据处理的高度自动化。
综上所述,检测传感技术在工业现代化发展的过程中扮演着越来越重要的角色。
检测传感技术的不断发展必将对传统的机械制造业带来新的变革,注入新的力量。
唯有不断得发展先进的机电一体化技术,我们才能更好地面对工业4.0时代带来的机遇与挑战!
参考文献
[1] 陈荷娟编著.机电一体化系统设计[M].北京:北京理工大学出版社,2008
[2] 高桥清(日) 编著,颜杰先译.传感器技术入门[M].北京:国防工业出版社,1985
[3] 卞海玲.浅析机电一体化中的检测传感技术[J].装备制造技术,2010(4):125−126
[4] 赵一心.论检测传感技术在机电一体化中现状、应用及其发展[J].制造业自动化,2010(11):186−187
[5] 祝诗平主编.传感器与检测技术[M].北京:北京大学出版社,2006
[6] 苏艳阳等.传感技术综述[J].数字通信,2008(4):25−30
[7] 胡向东,刘京诚.传感技术[M].重庆:重庆大学出版社, 2002
[8] 欧廷印,胡筱婧.传感技术发展综述[J].电工技术,2006(11): 48-51.
[9] 高玉民.传感器概述[J].世界汽车, 2002, (4): 55-58
[10] 武昌俊.自动检测技术及应用[M].北京:机械工业出版社,2005.
[11] 梁景凯. 机电一体化技术与系统[M]. 北京:机械工业出版社,1999.。