成本控制的案例分析共8页文档
成本控制案例分析

成本控制案例分析在当今竞争激烈的市场环境下,企业要想在激烈的竞争中立于不败之地,必须要不断地寻求成本控制的方法和途径。
成本控制不仅可以提高企业的盈利能力,还可以增强企业的市场竞争力。
下面,我们将通过一个实际的案例来分析成本控制的重要性和方法。
某公司是一家生产家具的企业,最近由于原材料价格上涨和人工成本增加,导致企业的生产成本大幅上升,利润急剧下降。
为了解决这一问题,公司决定对成本进行全面的分析和控制。
首先,公司对原材料成本进行了详细的分析。
他们发现,由于没有与供应商签订长期合同,导致原材料价格波动较大。
为了解决这一问题,公司与供应商进行了深入的谈判,最终签订了长期合作协议,确保原材料价格的稳定。
同时,公司还加强了对原材料库存的管理,避免了因为库存积压而导致资金的浪费。
其次,公司对人工成本进行了分析。
他们发现,由于员工的加班费用较高,导致了人工成本的增加。
为了解决这一问题,公司进行了生产流程的优化,提高了生产效率,减少了员工的加班时间。
同时,公司还加强了对员工的培训,提高了员工的技能水平,从而减少了因为操作不当而导致的生产损耗。
最后,公司对其他成本进行了全面的审查。
他们发现,由于企业的管理成本较高,导致了整体成本的增加。
为了解决这一问题,公司进行了管理体制的改革,优化了企业的组织结构,减少了管理层次,降低了管理成本。
同时,公司还加强了对各项费用的审查,避免了因为费用的浪费而导致成本的增加。
通过以上的分析,公司成功地控制了成本,提高了企业的盈利能力。
这个案例告诉我们,成本控制是企业生存和发展的关键,只有不断地寻求成本控制的方法和途径,才能在激烈的市场竞争中立于不败之地。
因此,企业要想在市场中立于不败之地,必须要重视成本控制,不断地寻求成本控制的方法和途径,从而提高企业的盈利能力,增强企业的市场竞争力。
成本控制案例分析

成本控制案例分析随着市场竞争的日益激烈,企业在追求利润最大化的同时,也必须不断寻求成本控制的策略。
本文将通过分析一家企业的案例,探讨成本控制的重要性以及实施成本控制的有效方法。
案例背景某电子产品制造企业作为行业的领导者,一直在市场上保持着良好的竞争地位。
然而,近年来,随着原材料价格的波动以及劳动力成本的上升,该企业的利润率逐渐下降。
因此,为了保持竞争优势,他们迫切需要找到有效的成本控制方法。
一、成本控制的重要性成本控制对企业的可持续发展至关重要。
首先,成本控制可以提升企业的利润率。
通过降低生产成本,企业可以在保持产品价格竞争力的同时提高利润水平。
其次,成本控制可以提高企业的竞争优势。
在市场竞争激烈的行业中,那些能够灵活控制成本的企业更有可能扩大市场份额并持续增长。
最后,成本控制有助于企业的稳定发展。
通过合理分配资源和降低浪费,企业能够更好地应对市场的变化和挑战。
二、成本控制的有效方法1. 成本分析首先,企业需要进行全面的成本分析。
通过分析企业的各项成本,识别出哪些是非必要的开支,进一步寻找降低成本的空间。
在这个案例中,该企业通过对各个生产环节的成本进行详细分析,发现了一些可以改善的地方,如减少能源消耗和降低运输费用等。
2. 采购策略优化其次,企业可以优化采购策略,降低原材料和设备的采购成本。
合理的供应商选择和谈判技巧可以帮助企业获得更有竞争力的价格,并确保原材料和设备的质量不受影响。
在这个案例中,该企业与多个供应商协商,最终获得了更有利的采购价格和条件。
3. 生产流程优化另外,企业可以通过优化生产流程来提高效率和降低成本。
识别出生产过程中的瓶颈,采取适当的措施来提高生产效率,并减少废品和不合格品的产生。
该企业在这方面进行了深入研究,并通过引入自动化设备和改进工艺流程,进一步提高了生产效率,降低了生产成本。
4. 管理控制最后,企业需要建立科学的成本管理和控制体系。
通过设定合理的成本预算和绩效评估指标,监控成本的使用情况,并及时发现和纠正偏差。
中小企业成本控制的案例分析

中小企业成本控制的案例分析在当今竞争激烈的商业环境中,中小企业如何有效地控制成本是一个关键问题。
本文将通过分析一家中小企业的实际案例,探讨该企业是如何通过创新的成本控制方法来提高效益并保持竞争力的。
案例背景该中小企业是一家专注于生产和销售高品质手工艺家具的家具制造商。
由于市场需求的波动以及原材料和劳动力成本的增加,该企业面临着严峻的成本压力。
为了保持盈利能力并维持发展,他们意识到必须采取措施来控制成本。
一、流程优化该企业首先进行了流程优化,以提高生产效率和降低成本。
他们对整个生产过程进行了全面审查,并通过精确测量和管理每个环节的时间和成本,找出了潜在的优化和改进点。
通过优化流程,该企业成功地减少了生产过程中的时间和废料,降低了生产成本,提高了产品质量。
二、供应链优化供应链优化是该企业进行成本控制的另一个重要手段。
他们与各供应商建立了长期的合作伙伴关系,并通过与供应商进行定期的沟通和协商,确保了原材料的及时交付和优惠价格。
此外,该企业还优化了物流和库存管理,减少了库存积压和资金占用,降低了物流成本。
三、员工培训与激励该企业充分认识到员工是成本控制的关键因素,因此他们注重员工培训和激励。
通过提供培训和学习机会,提高员工的技能水平和生产效率。
此外,该企业实行了灵活的激励机制,如绩效奖金和晋升机会,以激发员工的积极性和主动性。
这样不仅提高了员工的工作满意度和忠诚度,同时也减少了员工的流失和招聘成本。
四、技术升级与创新为了应对市场的快速变化,该企业不断进行技术升级和创新。
他们引进了先进的生产设备和工艺,并将数字化和自动化技术应用于生产过程中。
这不仅提高了生产效率和质量,还减少了人力资源的需求和成本。
五、市场定位与差异化在竞争激烈的市场中,该企业通过明确的市场定位和差异化战略来有效地控制成本。
他们针对高端客户提供独特的定制化家具,而不是大规模生产低价产品,从而降低了市场竞争的压力。
通过专注于高附加值产品并与客户建立长期合作关系,该企业成功地提高了产品的溢价能力和市场份额。
案例分析---仓储成本控制案例

案例月山啤酒集团的仓储管理月山啤酒集团在几年前就借鉴国内外物流公司的先进经验,结合自身的优势,制定了自己的仓储物流改革方案。
首先,成立了仓储调度中心,对全国市场区域的仓储活动进行重新规划,对产品的仓储、转库实行统一管理和控制。
由提供单一的仓储服务,到对产成品的市场区域分布、流通时间等全面的调整、平衡和控制,仓储调度成为销售过程中降低成本、增加效益的重要一环。
其次,以原运输公司为基础,月山啤酒集团注册成立具有独立法人资格的物流有限公司,引进现代物流理念和技术,并完全按照市场机制运作。
作为提供运输服务的“卖方”,物流公司能够确保按规定要求,以最短的时间、最少的投入和最经济的运送方式,将产品送至目的地。
第三,筹建了月山啤酒集团技术中心。
月山啤酒集团应用建立在Internet信息传输基础上的ERP系统,筹建了月山啤酒集团技术中心,将物流、信息流、资金流全面统一在计算机网络的智能化管理之下,建立起各分公司与总公司之间的快速信息通道,及时掌握各地最新的市场库存、货物和资金流动情况,为制定市场策略提供准确的依据,并且简化了业务运行程序,提高了销售系统工作效率,增强了企业的应变能力。
通过这一系列的改革,月山啤酒集团获得了很大的直接和间接经济效益。
首先是集团的仓库面积由7万多m2下降到不足3万m2,产成品平均库存量由12 000吨降到6 000吨。
其次,这个产品物流体实现了环环相扣,销售部门根据各地销售网络的要货计划和市场预测,制定销售计划,仓储部门根据销售计划和库存及时向生产企业传递要货信息;生产厂有针对性地组织生产,物流公司则及时地调度运力,确保交货质量和交货期。
第三,销售代理商在有了稳定的货源供应后,可以从人、财、物等方面进一步降低销售成本,增加效益,经过一年多的运转,月山啤酒物流网取得了阶段性成果。
实践证明,现代物流管理体系的建立,使月山集团的整体营销水平和市场竞争能力大大提高。
思考题:1.结合案例分析仓储成本分析的意义所在?2.分析月山啤酒集团是如何控制仓储成本的?3.分析月山集团是怎样通过控制仓储成本,获得经济效益的?1 / 11.通过仓储成本分析开发出的信息资料,是正确核算仓储成本、制造仓储服务收费价格等策略的依据。
成本控制案例分析
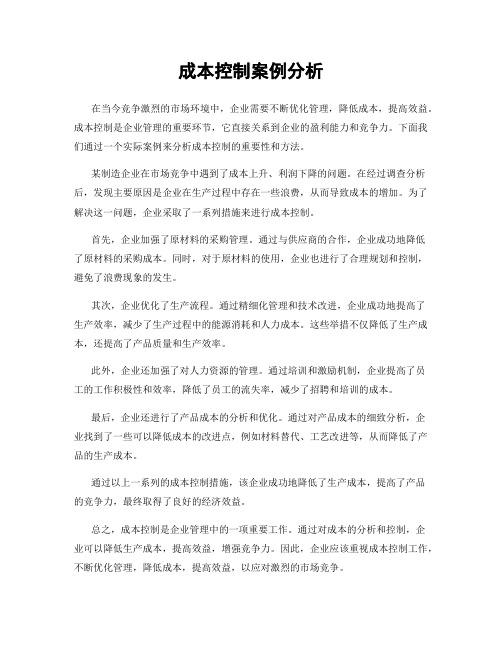
成本控制案例分析在当今竞争激烈的市场环境中,企业需要不断优化管理,降低成本,提高效益。
成本控制是企业管理的重要环节,它直接关系到企业的盈利能力和竞争力。
下面我们通过一个实际案例来分析成本控制的重要性和方法。
某制造企业在市场竞争中遇到了成本上升、利润下降的问题。
在经过调查分析后,发现主要原因是企业在生产过程中存在一些浪费,从而导致成本的增加。
为了解决这一问题,企业采取了一系列措施来进行成本控制。
首先,企业加强了原材料的采购管理。
通过与供应商的合作,企业成功地降低了原材料的采购成本。
同时,对于原材料的使用,企业也进行了合理规划和控制,避免了浪费现象的发生。
其次,企业优化了生产流程。
通过精细化管理和技术改进,企业成功地提高了生产效率,减少了生产过程中的能源消耗和人力成本。
这些举措不仅降低了生产成本,还提高了产品质量和生产效率。
此外,企业还加强了对人力资源的管理。
通过培训和激励机制,企业提高了员工的工作积极性和效率,降低了员工的流失率,减少了招聘和培训的成本。
最后,企业还进行了产品成本的分析和优化。
通过对产品成本的细致分析,企业找到了一些可以降低成本的改进点,例如材料替代、工艺改进等,从而降低了产品的生产成本。
通过以上一系列的成本控制措施,该企业成功地降低了生产成本,提高了产品的竞争力,最终取得了良好的经济效益。
总之,成本控制是企业管理中的一项重要工作。
通过对成本的分析和控制,企业可以降低生产成本,提高效益,增强竞争力。
因此,企业应该重视成本控制工作,不断优化管理,降低成本,提高效益,以应对激烈的市场竞争。
最新成本控制的案例分析
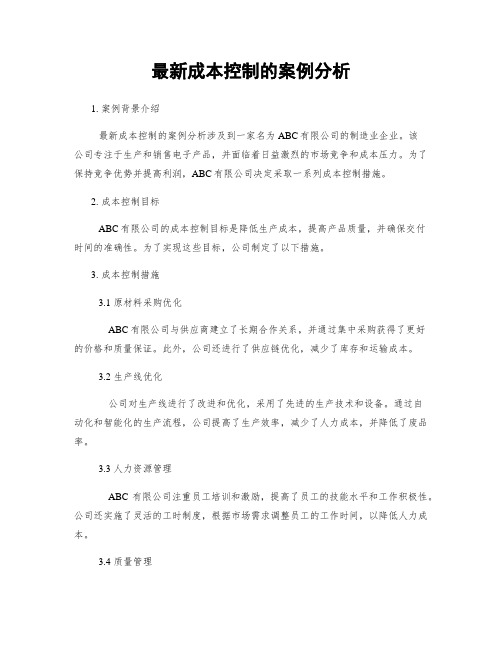
最新成本控制的案例分析1. 案例背景介绍最新成本控制的案例分析涉及到一家名为ABC有限公司的制造业企业。
该公司专注于生产和销售电子产品,并面临着日益激烈的市场竞争和成本压力。
为了保持竞争优势并提高利润,ABC有限公司决定采取一系列成本控制措施。
2. 成本控制目标ABC有限公司的成本控制目标是降低生产成本,提高产品质量,并确保交付时间的准确性。
为了实现这些目标,公司制定了以下措施。
3. 成本控制措施3.1 原材料采购优化ABC有限公司与供应商建立了长期合作关系,并通过集中采购获得了更好的价格和质量保证。
此外,公司还进行了供应链优化,减少了库存和运输成本。
3.2 生产线优化公司对生产线进行了改进和优化,采用了先进的生产技术和设备。
通过自动化和智能化的生产流程,公司提高了生产效率,减少了人力成本,并降低了废品率。
3.3 人力资源管理ABC有限公司注重员工培训和激励,提高了员工的技能水平和工作积极性。
公司还实施了灵活的工时制度,根据市场需求调整员工的工作时间,以降低人力成本。
3.4 质量管理公司引入了严格的质量管理体系,包括质量控制和质量保证。
通过提高产品质量,减少了售后服务成本和退货率,提高了客户满意度。
3.5 节约能源ABC有限公司采取了节能措施,例如使用高效的照明设备和设备休眠模式。
这些措施不仅降低了能源成本,还有助于减少对环境的影响。
4. 成本控制效果通过以上成本控制措施的实施,ABC有限公司取得了显著的成本控制效果。
4.1 原材料采购优化使公司节省了10%的采购成本。
4.2 生产线优化提高了生产效率,降低了生产成本,每年节约了20%的人力成本。
4.3 人力资源管理措施使公司员工的工作积极性和满意度提高,减少了员工离职率,降低了招聘和培训成本。
4.4 质量管理措施减少了售后服务成本和退货率,提高了产品质量和客户满意度。
4.5 节约能源措施减少了能源成本,每年节约了5%的能源费用。
5. 案例总结ABC有限公司通过实施一系列成本控制措施,取得了显著的成本降低和效益提升。
成本控制的案例分析
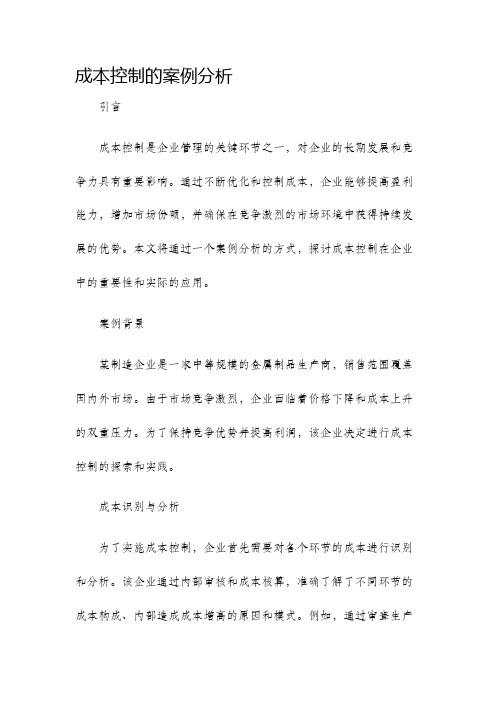
成本控制的案例分析引言成本控制是企业管理的关键环节之一,对企业的长期发展和竞争力具有重要影响。
通过不断优化和控制成本,企业能够提高盈利能力,增加市场份额,并确保在竞争激烈的市场环境中获得持续发展的优势。
本文将通过一个案例分析的方式,探讨成本控制在企业中的重要性和实际的应用。
案例背景某制造企业是一家中等规模的金属制品生产商,销售范围覆盖国内外市场。
由于市场竞争激烈,企业面临着价格下降和成本上升的双重压力。
为了保持竞争优势并提高利润,该企业决定进行成本控制的探索和实践。
成本识别与分析为了实施成本控制,企业首先需要对各个环节的成本进行识别和分析。
该企业通过内部审核和成本核算,准确了解了不同环节的成本构成、内部造成成本增高的原因和模式。
例如,通过审查生产线,企业发现原材料的浪费和生产过程中的不合理操作导致了成本的上升。
此外,能源和劳动力成本也是企业成本增高的主要因素。
成本控制策略在了解成本构成的基础上,该企业采用了一系列的成本控制策略,以降低成本并提高效益。
首先,企业通过引入先进的生产设备和生产工艺,提高生产效率和质量,减少了人力资源的浪费和能源的消耗。
其次,企业优化了原材料采购和供应链管理,与供应商建立了长期合作关系,降低了采购成本和库存成本。
另外,企业还注重员工的培训和技能提升,提高了员工的生产能力和工作积极性。
此外,企业还通过节约能源、优化运输和物流成本等措施,进一步降低了成本。
成本控制效果评估经过一定时期的成本控制实践,该企业取得了显著的成本控制效果。
例如,原材料和能源消耗下降,产品质量和交货速度得到了明显提升,员工的劳动积极性和团队合作意识增强。
这些措施共同导致了生产成本和运营成本的降低,企业的利润增加。
同时,企业还通过与客户保持密切的沟通和合作,提高了产品的附加值,进一步扩大了市场份额。
结论通过以上案例分析,我们可以得出以下结论:1. 成本控制是企业管理中不可或缺的一环,能够提高企业的竞争力和盈利能力。
制造业成本控制案例分析

制造业成本控制案例分析一、引言制造业成本控制对企业运营和盈利至关重要。
本文将通过案例分析,探讨一家制造业企业在成本控制方面的经验和策略,以帮助其他企业对成本控制进行有效管理和优化。
二、公司概况该制造业公司是一家专注于生产电子产品的企业,主要产品包括智能手机和平板电脑。
公司成立于2005年,总部位于中国,并在全球范围内设有几家生产基地和销售办事处。
三、成本控制策略为了有效控制成本并保持竞争力,该公司采取了以下策略:1.优化供应链管理该公司与供应链合作伙伴建立了紧密的合作关系,并通过合理的物流和运输规划,降低了运输成本和库存成本。
此外,他们通过合理的供应商选择和谈判,以获得更有竞争力的价格和服务。
2.生产线自动化公司积极投入研发和引进先进的生产设备和自动化技术,减少了人力资源成本,并提高了生产效率和质量。
自动化生产线降低了人为错误的风险,提高了产品的一致性和可靠性。
3.精益生产该公司采用精益生产方法,通过精确的生产计划和物料需求计划,避免了过剩库存和浪费。
通过优化生产过程,最大限度地减少了废品和次品的产生,降低了生产成本。
4.质量管理为了减少质量问题和不良产品率,公司实施了严格的质量管理体系。
通过监控关键指标和分析数据,他们能够快速发现并纠正生产中的问题,降低了返工和报废的成本。
5.员工培训和激励公司重视员工培训和激励,为员工提供相关技能和知识的培训,使其能够更好地适应生产工作的要求。
员工激励机制也被引入,通过奖金和福利等方式激励员工提高生产效率和质量。
四、成本控制效果上述成本控制策略帮助该制造业公司有效地降低了成本并提高了盈利能力。
具体效果如下:1.降低了运输成本和库存成本,减少了供应链中的浪费。
2.通过自动化生产线,减少了人工成本,提高了生产效率和质量。
3.精益生产方法减少了废品和次品的产生,有效降低了制造成本。
4.严格的质量管理体系降低了返工和报废的成本,并提高了客户满意度。
5.员工培训和激励使员工能力提升,推动公司生产效率不断改进。
成本控制的案例分析

第二部分成本控制的案例分析案例一美的的成本控制中国制造企业有 90%的时间花费在物流上,物流仓储成本占据了总销售成本的30%〜40%,供应链上物流的速度以及成本更是令中国企业苦恼的老大难问题。
美的针对供应链的库存问题,利用信息化技术手段,一方面从原材料的库存管理做起,追求零库存标准;另一方面针对销售商,以建立合理库存为目标,从供应链的两段实施挤压,加速了资金、物资的周转,实现了供应链的整合成本优势。
零库存梦想美的虽多年名列空调产业的“三甲”之位,但是不无一朝城门失守之忧。
自2000 年来,在降低市场费用、裁员、压低采购价格等方面,美的频繁变招,其路数始终围绕着成本与效率。
在广东地区已经悄悄为终端经销商安装进销存软件,即实现“供应商管理库存”(以下简称 VMI )和“管理经销商库存”中的一个步骤。
对于美的来说,其较为稳定的供应商共有 300 多家,其零配件(出口、内销产品)加起来一共有 3 万多种。
从 2002 年中期,利用信息系统,美的集团在全国范围内实现了产销信息的共享。
有了信息平台做保障,美的原有的 100多个仓库精简为 8 个区域仓,在 8小时可以运到的地方,全靠配送。
这样一来美的集团流通环节的成本降低了15%-20%。
运输距离长(运货时间 3-5 天的)的外地供应商,一般都会在美的的仓库里租赁一个片区(仓库所有权归美的),并把其零配件放到片区里面储备。
在美的需要用到这些零配件的时候,它就会通知供应商,然后再进行资金划拨、取货等工作。
这时,零配件的产权,才由供应商转移到美的手上——而在此之前,所有的库存成本都由供应商承担。
此外,美的在ERP (企业资源管理)基础上与供应商建立了直接的交货平台。
供应商在自己的办公地点,通过互联页( WEB )的方式就可登录到美的公司的页面上,看到美的的订单内容;品种、型号、数量和交货时间等等,然后由供应商确认信息,这样一张采购订单就已经合法化了。
实施 VMI 后,供应商不需要像以前一样疲于应付美的的订单,而只需做一些适当的库存即可。
成本控制案例分析
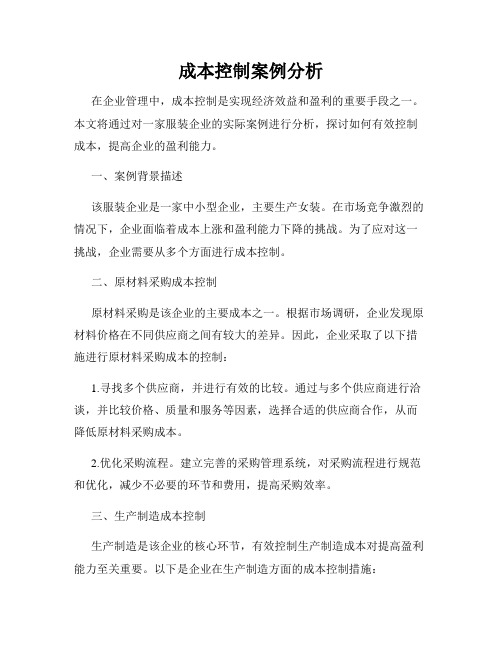
成本控制案例分析在企业管理中,成本控制是实现经济效益和盈利的重要手段之一。
本文将通过对一家服装企业的实际案例进行分析,探讨如何有效控制成本,提高企业的盈利能力。
一、案例背景描述该服装企业是一家中小型企业,主要生产女装。
在市场竞争激烈的情况下,企业面临着成本上涨和盈利能力下降的挑战。
为了应对这一挑战,企业需要从多个方面进行成本控制。
二、原材料采购成本控制原材料采购是该企业的主要成本之一。
根据市场调研,企业发现原材料价格在不同供应商之间有较大的差异。
因此,企业采取了以下措施进行原材料采购成本的控制:1.寻找多个供应商,并进行有效的比较。
通过与多个供应商进行洽谈,并比较价格、质量和服务等因素,选择合适的供应商合作,从而降低原材料采购成本。
2.优化采购流程。
建立完善的采购管理系统,对采购流程进行规范和优化,减少不必要的环节和费用,提高采购效率。
三、生产制造成本控制生产制造是该企业的核心环节,有效控制生产制造成本对提高盈利能力至关重要。
以下是企业在生产制造方面的成本控制措施:1.优化生产线布局。
通过重新规划生产线布局,减少物料运输距离和时间,提高生产效率,降低物料损耗。
2.加强员工培训。
培训生产线员工,提高其操作技能和生产效率,减少生产过程中的错误和浪费。
四、销售与市场成本控制在成本控制的过程中,企业还需关注销售和市场成本,以下是企业在销售与市场方面的成本控制措施:1.精准定位目标市场。
通过市场细分和目标客户定位,精准把握目标市场需求,减少不必要的市场推广费用。
2.建立完善的销售渠道。
与合适的渠道伙伴合作,优化销售渠道,减少销售环节中的中间环节成本。
五、财务成本控制财务成本控制是企业成本控制的核心,以下是企业在财务方面的成本控制措施:1.制定严格的财务预算。
根据企业的实际情况和发展目标,制定严格的财务预算,合理分配资源,降低不必要的支出。
2.加强财务数据分析。
通过加强财务数据分析,了解成本结构和成本构成,找出成本高的环节,采取措施进行优化。
成本控制的案例分析与启示
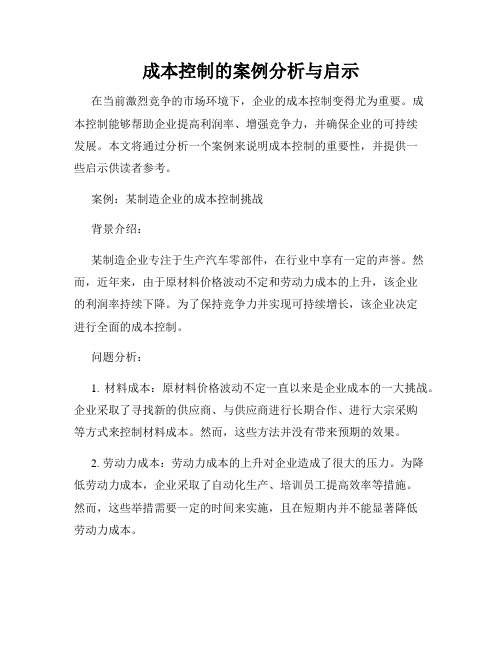
成本控制的案例分析与启示在当前激烈竞争的市场环境下,企业的成本控制变得尤为重要。
成本控制能够帮助企业提高利润率、增强竞争力,并确保企业的可持续发展。
本文将通过分析一个案例来说明成本控制的重要性,并提供一些启示供读者参考。
案例:某制造企业的成本控制挑战背景介绍:某制造企业专注于生产汽车零部件,在行业中享有一定的声誉。
然而,近年来,由于原材料价格波动不定和劳动力成本的上升,该企业的利润率持续下降。
为了保持竞争力并实现可持续增长,该企业决定进行全面的成本控制。
问题分析:1. 材料成本:原材料价格波动不定一直以来是企业成本的一大挑战。
企业采取了寻找新的供应商、与供应商进行长期合作、进行大宗采购等方式来控制材料成本。
然而,这些方法并没有带来预期的效果。
2. 劳动力成本:劳动力成本的上升对企业造成了很大的压力。
为降低劳动力成本,企业采取了自动化生产、培训员工提高效率等措施。
然而,这些举措需要一定的时间来实施,且在短期内并不能显著降低劳动力成本。
3. 管理费用:企业的管理费用一直居高不下。
在成本控制过程中,企业加强了对各个部门的预算管理,并实施了费用审核制度,但由于各个部门管理水平不一,费用控制效果并不尽如人意。
案例启示:基于上述案例,我们可以得出以下成本控制的启示:1. 多元化供应链:在面临原材料价格波动不定的情况下,企业应积极开拓多个供应商,并与之建立长期合作关系。
同时,加强供应链风险管理,确保原材料供应的稳定性。
2. 面向未来的投资:为了降低劳动力成本,企业应考虑投资于自动化设备和技术创新。
虽然这涉及到一定的成本,但从长远来看,将会产生显著的效益。
3. 精细化的预算管理:企业应建立全面的预算管理制度,将预算分解到各个部门,并设定合理的目标和指标。
此外,还需要加强对各个部门的培训和辅导,提高管理水平,确保费用控制的有效性。
结论:本文通过分析一个制造企业的成本控制挑战以及相应的解决方案,强调了成本控制在提高企业利润率和竞争力方面的重要性。
成本控制案例
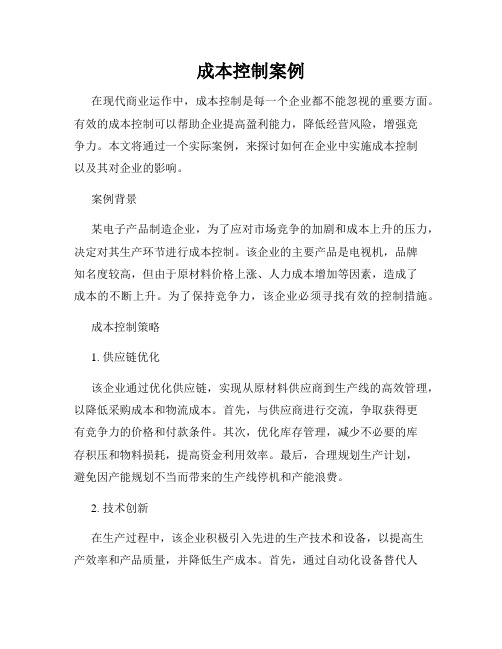
成本控制案例在现代商业运作中,成本控制是每一个企业都不能忽视的重要方面。
有效的成本控制可以帮助企业提高盈利能力,降低经营风险,增强竞争力。
本文将通过一个实际案例,来探讨如何在企业中实施成本控制以及其对企业的影响。
案例背景某电子产品制造企业,为了应对市场竞争的加剧和成本上升的压力,决定对其生产环节进行成本控制。
该企业的主要产品是电视机,品牌知名度较高,但由于原材料价格上涨、人力成本增加等因素,造成了成本的不断上升。
为了保持竞争力,该企业必须寻找有效的控制措施。
成本控制策略1. 供应链优化该企业通过优化供应链,实现从原材料供应商到生产线的高效管理,以降低采购成本和物流成本。
首先,与供应商进行交流,争取获得更有竞争力的价格和付款条件。
其次,优化库存管理,减少不必要的库存积压和物料损耗,提高资金利用效率。
最后,合理规划生产计划,避免因产能规划不当而带来的生产线停机和产能浪费。
2. 技术创新在生产过程中,该企业积极引入先进的生产技术和设备,以提高生产效率和产品质量,并降低生产成本。
首先,通过自动化设备替代人工操作,降低人力成本和人为失误的风险。
其次,优化生产流程,减少生产环节中不必要的时间浪费和资源消耗。
最后,加强质量管理,减少次品率,避免因次品产生的副产品和重新加工所导致的额外成本。
成本控制成效通过以上的成本控制策略,该企业取得了显著的成本控制成效。
首先,在供应链优化方面,通过与供应商的合作和库存管理的改进,该企业成功降低了采购成本和物流成本,有效提高了资金利用效率。
其次,在技术创新方面,引入先进的生产技术和设备,使得生产效率和产品质量得到了大幅提升,生产成本也得到了有效的控制。
这些措施的综合效果,使得该企业在激烈的市场竞争中保持了竞争力,并且取得了更为优异的财务业绩。
结论成本控制是企业经营管理中的关键要素,对企业的长期发展具有重要意义。
通过供应链优化和技术创新等措施,企业可以有效降低成本,提高盈利能力和竞争力。
成本管理经典案例(doc 9页)(完美版)
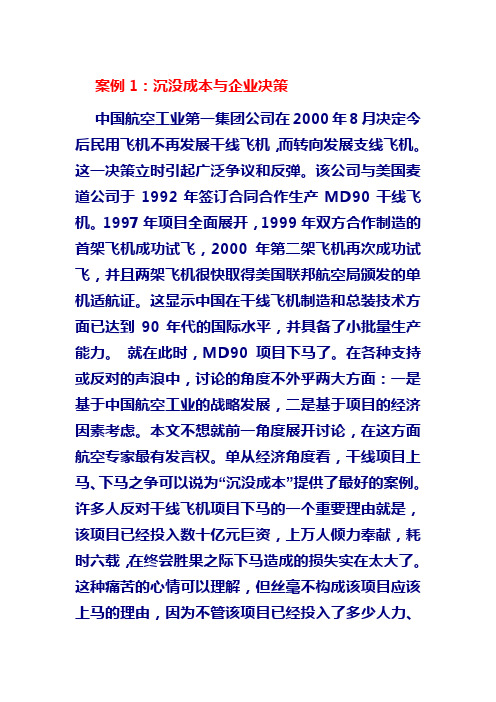
案例1:沉没成本与企业决策中国航空工业第一集团公司在2000年8月决定今后民用飞机不再发展干线飞机,而转向发展支线飞机。
这一决策立时引起广泛争议和反弹。
该公司与美国麦道公司于1992年签订合同合作生产MD90干线飞机。
1997年项目全面展开,1999年双方合作制造的首架飞机成功试飞,2000年第二架飞机再次成功试飞,并且两架飞机很快取得美国联邦航空局颁发的单机适航证。
这显示中国在干线飞机制造和总装技术方面已达到90年代的国际水平,并具备了小批量生产能力。
就在此时,MD90项目下马了。
在各种支持或反对的声浪中,讨论的角度不外乎两大方面:一是基于中国航空工业的战略发展,二是基于项目的经济因素考虑。
本文不想就前一角度展开讨论,在这方面航空专家最有发言权。
单从经济角度看,干线项目上马、下马之争可以说为“沉没成本”提供了最好的案例。
许多人反对干线飞机项目下马的一个重要理由就是,该项目已经投入数十亿元巨资,上万人倾力奉献,耗时六载,在终尝胜果之际下马造成的损失实在太大了。
这种痛苦的心情可以理解,但丝毫不构成该项目应该上马的理由,因为不管该项目已经投入了多少人力、物力、财力,对于上下马的决策而言,其实都是无法挽回的沉没成本。
究竟什么是沉没成本呢?沉没成本是指业已发生或承诺、无法回收的成本支出,如因失误造成的不可收回的投资。
沉没成本是一种历史成本,对现有决策而言是不可控成本,不会影响当前行为或未来决策。
从这个意义上说,在投资决策时应排除沉没成本的干扰。
衡量投资项目成本,只能包含因进行或选择该行动方案而发生的相关成本。
相关成本指与特定决策、行动有关的,在分析评价时必须加以考虑的成本,包括差额成本、未来成本、重置成本、机会成本等。
非相关成本则指在决策之前就已发生或不管采取什么方案都要发生的成本,它与特定决策无关,因而在分析评价和最优决策过程中不应纳入决策成本的范畴,如过去成本、账面成本等。
从决策的相关性看,沉没成本是决策非相关成本,若决策时计入沉没成本,将使项目成本高估,从而得到错误的结论。
成本控制案例分析

案例一美的的成本控制中国制造企业有90%的时间花费在物流上, 物流仓储成本占据了总销售成本的30%~40%, 供应链上物流的速度以及成本更是令中国企业苦恼的老大难问题。
美的针对供应链的库存问题, 利用信息化技术手段, 一方面从原材料的库存管理做起, 追求零库存标准; 另一方面针对销售商, 以建立合理库存为目标, 从供应链的两段实施挤压, 加速了资金、物资的周转, 实现了供应链的整合成本优势。
零库存梦想美的虽多年名列空调产业的”三甲”之位, 可是不无一朝城门失守之忧。
自来, 在降低市场费用、裁员、压低采购价格等方面, 美的频繁变招, 其路数始终围绕着成本与效率。
在广东地区已经悄悄为终端经销商安装进销存软件, 即实现”供应商管理库存”( 以下简称VMI) 和”管理经销商库存”中的一个步骤。
对于美的来说, 其较为稳定的供应商共有300多家, 其零配件( 出口、内销产品) 加起来一共有3万多种。
从中期, 利用信息系统, 美的集团在全国范围内实现了产销信息的共享。
有了信息平台做保障, 美的原有的100多个仓库精简为8个区域仓, 在8小时能够运到的地方, 全靠配送。
这样一来美的集团流通环节的成本降低了15%-20%。
运输距离长( 运货时间3-5天的) 的外地供应商, 一般都会在美的的仓库里租赁一个片区( 仓库所有权归美的) , 并把其零配件放到片区里面储备。
在美的需要用到这些零配件的时候, 它就会通知供应商, 然后再进行资金划拨、取货等工作。
这时, 零配件的产权, 才由供应商转移到美的手上——而在此之前, 所有的库存成本都由供应商承担。
另外, 美的在ERP( 企业资源管理) 基础上与供应商建立了直接的交货平台。
供应商在自己的办公地点, 经过互联页( WEB) 的方式就可登录到美的公司的页面上, 看到美的的订单内容; 品种、型号、数量和交货时间等等, 然后由供应商确认信息, 这样一张采购订单就已经合法化了。
实施VMI后, 供应商不需要像以前一样疲于应付美的的订单, 而只需做一些适当的库存即可。
有效的成本控制案例分析
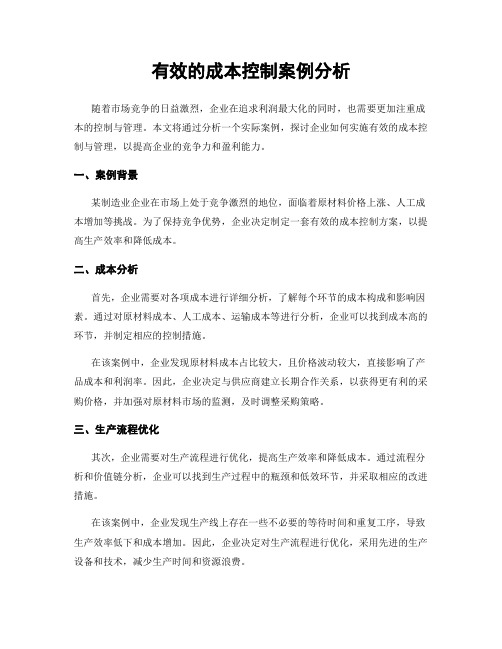
有效的成本控制案例分析随着市场竞争的日益激烈,企业在追求利润最大化的同时,也需要更加注重成本的控制与管理。
本文将通过分析一个实际案例,探讨企业如何实施有效的成本控制与管理,以提高企业的竞争力和盈利能力。
一、案例背景某制造业企业在市场上处于竞争激烈的地位,面临着原材料价格上涨、人工成本增加等挑战。
为了保持竞争优势,企业决定制定一套有效的成本控制方案,以提高生产效率和降低成本。
二、成本分析首先,企业需要对各项成本进行详细分析,了解每个环节的成本构成和影响因素。
通过对原材料成本、人工成本、运输成本等进行分析,企业可以找到成本高的环节,并制定相应的控制措施。
在该案例中,企业发现原材料成本占比较大,且价格波动较大,直接影响了产品成本和利润率。
因此,企业决定与供应商建立长期合作关系,以获得更有利的采购价格,并加强对原材料市场的监测,及时调整采购策略。
三、生产流程优化其次,企业需要对生产流程进行优化,提高生产效率和降低成本。
通过流程分析和价值链分析,企业可以找到生产过程中的瓶颈和低效环节,并采取相应的改进措施。
在该案例中,企业发现生产线上存在一些不必要的等待时间和重复工序,导致生产效率低下和成本增加。
因此,企业决定对生产流程进行优化,采用先进的生产设备和技术,减少生产时间和资源浪费。
四、人力资源管理此外,企业还需要注重人力资源的管理,以提高员工的工作效率和减少人力成本。
通过员工培训、绩效考核和激励机制等措施,企业可以激发员工的积极性和创造力,提高工作效率和质量。
在该案例中,企业发现员工的技能水平和工作积极性存在差异,导致生产效率和产品质量不稳定。
因此,企业决定加强员工培训和技能提升,建立绩效考核制度,激励员工积极参与成本控制和质量改进。
五、成本监控与评估最后,企业需要建立成本监控与评估体系,及时了解成本的变化和影响因素,以便及时采取相应的调整措施。
通过建立成本核算系统和成本控制指标,企业可以实时监控成本的变化和偏差,并进行成本效益评估。
成本控制的案例分析与启示
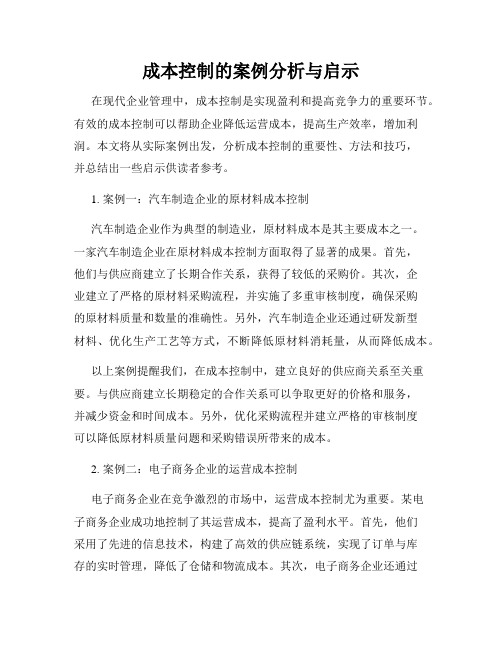
成本控制的案例分析与启示在现代企业管理中,成本控制是实现盈利和提高竞争力的重要环节。
有效的成本控制可以帮助企业降低运营成本,提高生产效率,增加利润。
本文将从实际案例出发,分析成本控制的重要性、方法和技巧,并总结出一些启示供读者参考。
1. 案例一:汽车制造企业的原材料成本控制汽车制造企业作为典型的制造业,原材料成本是其主要成本之一。
一家汽车制造企业在原材料成本控制方面取得了显著的成果。
首先,他们与供应商建立了长期合作关系,获得了较低的采购价。
其次,企业建立了严格的原材料采购流程,并实施了多重审核制度,确保采购的原材料质量和数量的准确性。
另外,汽车制造企业还通过研发新型材料、优化生产工艺等方式,不断降低原材料消耗量,从而降低成本。
以上案例提醒我们,在成本控制中,建立良好的供应商关系至关重要。
与供应商建立长期稳定的合作关系可以争取更好的价格和服务,并减少资金和时间成本。
另外,优化采购流程并建立严格的审核制度可以降低原材料质量问题和采购错误所带来的成本。
2. 案例二:电子商务企业的运营成本控制电子商务企业在竞争激烈的市场中,运营成本控制尤为重要。
某电子商务企业成功地控制了其运营成本,提高了盈利水平。
首先,他们采用了先进的信息技术,构建了高效的供应链系统,实现了订单与库存的实时管理,降低了仓储和物流成本。
其次,电子商务企业还通过精细的数据分析,了解了客户的消费行为和需求,定制了有针对性的促销活动,提高了销售效率,降低了市场营销成本。
从以上案例可以得出一些启示:充分发挥信息技术在成本控制中的作用是非常重要的。
采用先进的信息系统帮助企业实现订单、库存和物流的有效管理,可以降低运营成本。
另外,精细的市场调研和数据分析,有助于企业了解客户需求,提高销售效率,减少市场营销成本。
3. 案例三:餐饮业的人力资源成本控制餐饮业是劳动密集型行业,人力资源成本是其主要成本之一。
一家连锁餐饮企业成功地控制了人力资源成本,并提高了服务质量。
- 1、下载文档前请自行甄别文档内容的完整性,平台不提供额外的编辑、内容补充、找答案等附加服务。
- 2、"仅部分预览"的文档,不可在线预览部分如存在完整性等问题,可反馈申请退款(可完整预览的文档不适用该条件!)。
- 3、如文档侵犯您的权益,请联系客服反馈,我们会尽快为您处理(人工客服工作时间:9:00-18:30)。
第二部分成本控制的案例分析案例一美的的成本控制中国制造企业有90%的时间花费在物流上,物流仓储成本占据了总销售成本的30%~40%,供应链上物流的速度以及成本更是令中国企业苦恼的老大难问题。
美的针对供应链的库存问题,利用信息化技术手段,一方面从原材料的库存管理做起,追求零库存标准;另一方面针对销售商,以建立合理库存为目标,从供应链的两段实施挤压,加速了资金、物资的周转,实现了供应链的整合成本优势。
零库存梦想美的虽多年名列空调产业的“三甲”之位,但是不无一朝城门失守之忧。
自2000年来,在降低市场费用、裁员、压低采购价格等方面,美的频繁变招,其路数始终围绕着成本与效率。
在广东地区已经悄悄为终端经销商安装进销存软件,即实现“供应商管理库存”(以下简称VMI)和“管理经销商库存”中的一个步骤。
对于美的来说,其较为稳定的供应商共有300多家,其零配件(出口、内销产品)加起来一共有3万多种。
从2019年中期,利用信息系统,美的集团在全国范围内实现了产销信息的共享。
有了信息平台做保障,美的原有的100多个仓库精简为8个区域仓,在8小时可以运到的地方,全靠配送。
这样一来美的集团流通环节的成本降低了15%-20%。
运输距离长(运货时间3-5天的)的外地供应商,一般都会在美的的仓库里租赁一个片区(仓库所有权归美的),并把其零配件放到片区里面储备。
在美的需要用到这些零配件的时候,它就会通知供应商,然后再进行资金划拨、取货等工作。
这时,零配件的产权,才由供应商转移到美的手上——而在此之前,所有的库存成本都由供应商承担。
此外,美的在ERP(企业资源管理)基础上与供应商建立了直接的交货平台。
供应商在自己的办公地点,通过互联页(WEB)的方式就可登录到美的公司的页面上,看到美的的订单内容;品种、型号、数量和交货时间等等,然后由供应商确认信息,这样一张采购订单就已经合法化了。
实施VMI后,供应商不需要像以前一样疲于应付美的的订单,而只需做一些适当的库存即可。
供应商则不用备很多货,一般有能满足3天的需求即可。
美的零部年库存周转率,在2019年上升到70-80次/年。
其零部件库存也由原来平均的5-7天存货水平,大幅降低为3天左右,而且这3天的库存也是由供应商管理并承担相应成本。
库存周转率提高后,一系列相关的财务“风向标”也随之“由阴转晴”,让美的“欣喜不已”;资金占用降低、资金利用率提高、资金风险下降、库存成本直线下降。
消解分销链存货在业务链后端的供应体系进行优化的同时,美的也正在加紧对前端销售体系的管理进行渗透。
在经销商管理环节上,美的利用销售管理系统可以统计到经销商的销售信息(分公司、代理商、型号、数量、日期等),而近年来则公开了与经销商的部分电子化往来,以前半年一次的手工性的繁杂对帐,现在则进行业务往来的实时对帐和审核。
在前端销售环节,美的作为经销商的供应商,为经销商管理库存。
这样的结果是,经销商不用备货了,“即使备也是五台十台这种概念”——不存在以后听淡季打款。
经销商缺货,美的立刻就会自动送过去,而不需经销商提醒。
经销商的库存“实际是美的自己的库存”。
这种存货管理上的前移,美的可以有效地削减和精准的鬼斧神工制销售渠道上昂贵的存货,而不是任其堵塞在渠道中,让其占用经销商的大量资金。
2019年,美的以空调为核心对整条供应链资源进行整合,更多的优秀供应商被纳入美的空调的供应体系,美的空调供应体系的整体素质有所提升。
依照企业经营战略和重心的转变,为满足制造模式“柔性”和“速度”的要求,美的对供应资源布局进行了结构性调整,供应链布局得到优化。
通过厂商的共同努力,整体供应链在“成本”、“品质”、“响应期”等方面的专业化能力得到了不同程度的发育,供应链能力得到提升。
目前,美的空调成品的年库存周转率大约是接近10次,而美的的短期目标是将成品空调的库存周转率提高1.5~2次。
目前,美的空调成品的年库存周转率不仅远低于戴尔等电脑厂商,也低于年周转率大于10次的韩国厂商。
库存周率提高一次,可以直接为美的空调节省超过2000万元人民币的费用。
由于采取了一系列措施,美的已经在库存上尝到了甜头,2019年度,美的销售量同比2019年度增长50%-60%,但成品库存却降低了9万台,因而保证了在激烈的市场竞争下维持了相当的利润。
案例二: 正泰的成本控制2019年初,1.2万~1.3万元/吨的矽钢片;10月份,涨到了2万元/吨;11月份,涨到了2.7万~2.8万元/吨;2019年初,涨到了4.2万~4.3万元/吨。
仅一年时间涨幅超过200%。
与此同时,浙江大范围电荒,很多地方已开始执行生产企业的“开三停四”的供电计划。
霎时间将很多低压电器生产厂至于水与火的煎熬当中,很多企业产品尚未销售亏损便已成定局,更多的则是采取提高售价,向市场转移成本,以求暂避劫难。
正泰却逆市飚扬,质量不仅没有因为压力而缩水,而且价格保持着足够的竞争力,“这是一次利用价格杠杆实现产业集中的机遇,我们必须做到利润和份额的同步增长。
挺过去,正泰就可以迈进行业第一!”“混合型”生产正泰所在的温州柳市虽然是个群山环绕的小市镇,但是由于浙江省整体闹电荒,加之上万家的电器厂如同发豆芽一样地挤在这个小镇中,电力供应的矛盾非常严峻,而这时人机交互式生产在保障订单的交付方面的优势就显而易见。
同时,低压电器行业属于劳动密集型产业,对设备的使用可以大大减轻劳动力市场波动的影响。
“毕竟设备又不会像员工那样可以招之即来挥之即去。
”虽然自动化生产效率高,但是设备购置费是一笔最大的投入,终端车间的4条自动生产线,一条要500多万元人民币,设备的逐年折旧肯定会加大企业的生产成本。
“而且,越是复杂的设备,维修成本也越高。
目前终端车间的自动线每年的维修费也要几十万元。
一条自动线一般能够替代五六十个工人,按目前正泰的工资水平计算,这些工人一年的工资才只有10多万元。
”用人工还是机器,正泰的角度就是看成本。
“人要比机械更灵活。
比如在组装时,一个零件如果稍微有一点变形,人会自动调整一下方向把它安装上,但自动线就不行,会马上就淘汰掉,这样无形增加了采购质量和成本,同时生产的材料消耗也随之上升。
”正泰生产采购中心总经理邓华祥说,这也是正泰上下的共识。
在整个正泰工业园,只有12条全自动生产线,手工仍占70%以上,目前终端公司的装配仍是由手工完成。
在正泰终端电器公司的第一间生产车间,通道右边是真正的手工生产线,一排排望不到头的工作台,没有我们惯常所见的传送带。
年轻的女工将工件拼装好后,就会用一根普通的橡皮筋轻轻捆起,放到一边,隔一段时间由搬运工送到下一个工序。
几千个工作台上同时传来的“卡卡”的工件碰撞声,显得热烈而忙碌。
另一边是四条纯粹的自动化生产线,工件由机器手传到下一个工序,长长的生产线上只有两个工人走来走去,来回巡视。
除了拼装和包装工序外,中间的几个工序已经都由机器来完成。
正是采用了这种混合式生产单元,不仅仅成本得到了有效控制,提高了效率,而且生产线更具有了弹性,在处理多品种多规格订单时有时更加明显。
这里也因此成为目前全球最大的小型断路器生产中心,目前日产量可以达到24万台。
拆分流水线“不要迷信自动化。
”在对人力的应用上,正泰仔细研究生产线分解与劳动力要素配置的关系,根据每一道工序对生产速度的要求,对上游的工序进行重新整合。
“定型的、量大的产品就用自动线。
”邓华祥说,“订单小的用自动线做效率反而低,特别是一些有客户附加要求比较特殊的产品,我们需要在生产线中间加工序,如果是自动线就无法加工序。
”正泰对处理不同型号订单的生产方式别出心裁,由于订单的多样性,必然使固定的自动流水线生产变得困难,并且不经济,而采用人机混合的方式就可以合理调度这种变动。
另外,对于一些经常自动流水线生产效率并不高的工序,也从整条生产线上抽离出来,采用密集劳力的方式单独进行加工,这样改进后发现效率提高很多。
正泰对生产成本的敏感是外人无法想象的,他们精确计算生产线上的某些环节是否适用引进自动线,这似乎不能被简单指责为拒绝技术升级的保守。
在降低生产成本方面的举措不仅体现在对生产线的生产要素分解、组合与替代的理解上,也体现在它们对生产损耗的控制上。
“机器对标准的要求较高,而人就具有足够的适应能力。
”正泰将原材料进行分级处理,充分利用人力和机器的不同特点实现原料的最大利用。
在对纯粹人工操作的生产线上,一道工序和另一道工序之间的搬运时间都被精确测量,直至整体效率达到最佳。
对于工序的设计,也是秉持最佳效率原则,经过试验,一个人负责的工序越少,速度才能更快,就将工序进一步细分,更密集地使用人力,从而使正泰的流水线保证了对大量订单的处理能力。
人机合成模式虽然可以降低成本,但是如果没有工人良好的素质,一切都白搭。
特别是在中国大多数还是受教育水平很低、流动频繁的普通民工。
为了保证新招聘员工快速上手,降低培训成本,对于包括技术文件等很小的细节,正泰也正在进行适当的修改。
“让图形发挥更大的价值”,采用形象教育手段,工人在干中学,整体素质提高很快。
在文件处理上,也尽可能采用让较低文化程度的员工看得懂的表达方式。
此外,人的效率不同于流水线,需要不断摸索、改进和提高。
而正泰通过劳动竞赛和奖罚制度、目标定人定岗承包等方式,不断调动非流水线部分的工人效率。
同时建立了内部计算机网,随时了解一线生产情况,包括每个员工的出勤,员工的到位情况,员工的生产情况,缺勤的原因等。
案例三: 百安居的成本控制节俭从来就不是个大问题,但却需要大本领才能做得彻底、做得不留遗憾。
特别是对于当今零售行业来说,利润微薄的同时还要快速扩张,不实行低成本运营就难以生存,可谓成本决定存亡。
百安居(B&Q),隶属于世界500强企业之一、拥有30多年历史的大型国际装饰建材零售集团——英国翠丰集团,从2019年进入中国内地,至今已开设了23家分店。
中国公司2019年的营业额约为32亿人民币,利润达7000万人民币,如此财大气粗的公司却将节俭发展为一种生存哲学,在日常的运营中阐释着什么叫“细者为王”。
客户不会为你的奢侈买单北京四季青桥百安居一楼卖场,偏僻的西南角摆了张小桌子,来访者在有些破旧的登记簿上签字后,通过狭窄的楼道,华北区的百安居总部就借居在此,与明亮宽敞的卖场相比,办公区显得寒碜。
办公用品适用而不奢华华北区总经理办公室照样简陋,一张能容6人的会议桌,毫无档次可言的普通灰白色文件柜。
没有老板桌,总经理文东坐的椅子(用“凳子”这个词也可以)和普通员工一样,连扶手都没有,就这几件物品,办公室已不宽裕。
总经理手中的签字笔只要1.5元,由行政部门按不高于公司的指导价去统一采购——这听上去有些令人惊叹。
而他们选用廉价笔的理由是,既然都能写字,为什么要用贵的呢?这就是百安居的节俭哲学:企业的所有支出,都是建立在可以给客户提供更多价值的基础之上。