铝合金鼓形车体结构设计与计算分析
铝合金车体大型部件变形分析及加工方案研究

铝合金车体大型部件变形分析及加工方案研究摘要:在轨道交通行业中铝合金车体大部件加工过程中,变形缺陷对其会产生较大影响。
本文主要对铝合金车体部件结构、变形类别、形成原因进行了分析,并分析产生的型材变形、焊接变形、工艺变形等缺陷类别,同时提出变形产生的原因以及对应的解决措施,并针对解决措施进行了详细的分析和验证。
关键词:铝合金车体;大型部件;变形缺陷;加工方案一、铝合金车体的基本结构及特性铝合金由于自身刚度较小的材料特性,且部分车体大型部件在加工前还需经过组焊、预置挠度等工艺过程,会导致待加工部件在加工前就已经产生了较大的变形量,这一特点需要在加工工艺策划过程中重点考虑。
铝合金车体主要由底架组成、侧墙组成、端墙组成、车顶边梁、车顶板等结构及小部件组成。
上述各大型部件基本是使用大型数控铣床对组焊后的铝型材进行加工而成。
二、部件变形的类别及其成因2.1 型材变形铝合金型材在挤压成型的过程中会产生缺陷,对车体加工的影响较大,尤其尺寸超差、型材的扭曲变形,端面不均匀等问题都是影响加工的主要因素。
在工艺流程的策划过程中需要考虑各部件的平面度、直线度及轮廓度等参数标准。
2.2 焊接变形对于轨道交通车辆来说,车体上相关部件如:地板、侧墙、底架、端墙、车顶板等大型部件在进行加工之前需通过焊接将若干块小型材组焊成一个大的构件,而在焊接过程中会产生焊接变形,特别是在长度较长、平面较大、或是采用搅拌摩擦焊的部件上表现尤为明显[1-2]。
工件在焊缝附近会产生沿焊缝垂直方向上的收缩变形,进而使焊缝两侧的型材出现翘曲,最终导致部件直线度和平面度出现偏差。
2.3 工艺变形在轨道车辆铝合金车体的制造与使用过程中,多种因素可能会导致车体产生向下的挠度,例如车体自重和载重,运行过程中的垂向振动等。
为补偿这个向下的挠度,一般都会在制造过程中增加向上的预置挠度,其中侧墙和底架是需要预置挠度的核心部件[3-4]。
但预置挠度会对加工造成一定的影响,因此,在进行加工工艺策划时需要采取相应的措施来降低其对加工精度的影响。
基于轻量化与模块化的铝合金车体结构设计_1
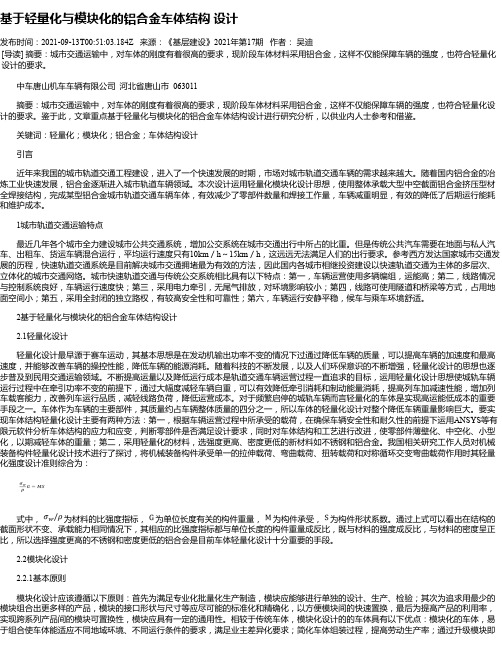
基于轻量化与模块化的铝合金车体结构设计发布时间:2021-09-13T00:51:03.184Z 来源:《基层建设》2021年第17期作者:吴迪[导读] 摘要:城市交通运输中,对车体的刚度有着很高的要求,现阶段车体材料采用铝合金,这样不仅能保障车辆的强度,也符合轻量化设计的要求。
中车唐山机车车辆有限公司河北省唐山市 063011摘要:城市交通运输中,对车体的刚度有着很高的要求,现阶段车体材料采用铝合金,这样不仅能保障车辆的强度,也符合轻量化设计的要求。
鉴于此,文章重点基于轻量化与模块化的铝合金车体结构设计进行研究分析,以供业内人士参考和借鉴。
关键词:轻量化;模块化;铝合金;车体结构设计引言近年来我国的城市轨道交通工程建设,进入了一个快速发展的时期,市场对城市轨道交通车辆的需求越来越大。
随着国内铝合金的冶炼工业快速发展,铝合金逐渐进入城市轨道车辆领域。
本次设计运用轻量化模块化设计思想,使用整体承载大型中空截面铝合金挤压型材全焊接结构,完成某型铝合金城市轨道交通车辆车体,有效减少了零部件数量和焊接工作量,车辆减重明显,有效的降低了后期运行能耗和维护成本。
1城市轨道交通运输特点最近几年各个城市全力建设城市公共交通系统,增加公交系统在城市交通出行中所占的比重。
但是传统公共汽车需要在地面与私人汽车、出租车、货运车辆混合运行,平均运行速度只有10km/h~15km/h,这远远无法满足人们的出行要求。
参考西方发达国家城市交通发展的历程,快速轨道交通系统是目前解决城市交通拥堵最为有效的方法,因此国内各城市相继投资建设以快速轨道交通为主体的多层次、立体化的城市交通网络。
城市快速轨道交通与传统公交系统相比具有以下特点:第一,车辆运营使用多辆编组,运能高;第二,线路情况与控制系统良好,车辆运行速度快;第三,采用电力牵引,无尾气排放,对环境影响较小;第四,线路可使用隧道和桥梁等方式,占用地面空间小;第五,采用全封闭的独立路权,有较高安全性和可靠性;第六,车辆运行安静平稳,候车与乘车环境舒适。
地铁铝合金车体轻量化设计与结构设计

地铁铝合金车体轻量化设计与结构设计摘要:铝及铝合金因其低密度、强度高、塑性好、易成形和良好的导电、导热性及耐蚀性等特点,逐渐成为近年来工业生产中使用最多的结构材料之一,其中,以牌号为6082-T6,6005A-T6为代表的6XXX系列(Al-Mg-Si)铝合金,其热挤压性能、焊接性能及强度介于7XXX系列铝合金和5XXX系列铝合金之间,焊接性能和机加工工艺良好,且具有较高的强度和耐腐蚀性能,成为轨道车体首选的铝合金原材料。
轨道车辆用铝合金多采用大型中空铝合金薄壁挤压型材及不同厚度的铝合金板材的形式,同时,对比其他焊接材料,铝合金热膨胀系数较大,所以,在焊接过程中,随着快速加热和快速冷却而带来的膨胀和收缩发生时,必然出现不同形式的变形。
铝合金地铁车体主要由底架、侧墙、车顶、端墙、司机室骨架等几大部分组成,其中,底架又由地板、牵枕缓、边梁、端梁、连接板等几部分焊接而成,地板由数根长大铝合金地板型材拼焊而成,前端地板组成则位于地铁车辆车体底架的一端,司机室骨架的下部.基于此,本篇文章对地铁铝合金车体轻量化设计与结构设计进行研究,以供参考。
关键词:地铁;铝合金车体;轻量化设计;结构设计引言轨道交通车辆是轨道交通要件之一。
随着我国城市的增质提速发展,轨道交通需求和速度的增加,带动轨道交通车辆需求增加。
轨道交通速度的提高和对车辆的需求增加也带来一些问题,比如节能减排和绿色发展。
铝合金属于Al-Zn-Mg系可热处理强化的中高强铝合金,具有很好的塑性成形性能和热处理性能,可以挤压成各种复杂的大型薄壁空心型材,用在轨道交通车辆和汽车车架上,可以大幅度减轻车辆本身的重量,减少二氧化碳的排放,提高交通速度,符合绿色低碳的发展需求,可以获得较好的经济效益和社会效益。
由于传统加工方法生产的铝合金不能很好地满足轨道交通车辆用铝合金的强度、刚度和耐蚀性的要求,所以对提升铝合金力学性能展开研究。
由于晶粒细化可以改善铝合金的塑性变形能力,因而研究铝合金的晶粒细化方法具有重要的理论和应用意义,作为晶粒细化方法之一的等径角挤压技术(简称ECAP)得到了越来越多的关注。
铝合金车体的有限元分析和结构评估方法研究

2019年(第 41卷)第 6期 doi:10.19562/j.chinasae.qcgc.2019.06.001
汽 车 工 程 Automห้องสมุดไป่ตู้tiveEngineering
2019(Vol.41)No.6
铝合金车体的有限元分析和结构评估方法研究
王万林,徐从昌,王震虎,王哲阳,李落星
(1湖南大学,汽车车身先进设计制造国家重点实验室,长沙 410082; 2湖南大学机械与运载工程学院,长沙 410082)
关键词:铝合金车体;有限元分析;广义结构刚度;结构评估方法;轻量化
AStudyonFiniteElementAnalysisandStructuralAssessment MethodforAluminumalloyVehicleBody
WangWanlin,XuCongchang,WangZhenhu,WangZheyang& LiLuoxing
地铁铝合金车体的结构设计和强度分析

地铁铝合金车体的结构设计和强度分析发布时间:2021-09-11T04:58:18.004Z 来源:《基层建设》2021年第17期作者:李思[导读] 摘要:随着我国经济的快速发展,我国目前正处在城市化的高速推进阶段,给现有的城市交通基础设施造成了巨大挑战,此外城市建设规模也日趋增大,在大环境的影响下,城市轨道交通建设成为我国的首选。
中车唐山机车车辆有限公司河北省唐山市 063011摘要:随着我国经济的快速发展,我国目前正处在城市化的高速推进阶段,给现有的城市交通基础设施造成了巨大挑战,此外城市建设规模也日趋增大,在大环境的影响下,城市轨道交通建设成为我国的首选。
地铁是城市轨道交通中非常重要的组成部分,地铁具有安全、准点、快捷、舒适、环保的特点,它庞大的运量具有地面任何交通工具都不可比拟的优越性。
随着地铁的广泛应用,对其结构及轻量化的要求也越来越高,因此对车体进行仿真分析以及优化设计十分必要。
鉴于此,文章重点就地铁铝合金车体的结构设计和强度分析进行研究分析,以供参考。
关键词:地铁车辆;铝合金车体;结构设计;强度分析引言铝合金材料以其重量轻、耐腐蚀性好和易于采用挤压方法成型等优点成为铁路机车车辆制造业中的理想材料。
为确保机车车辆在工作状态下安全可靠,铝合金车体结构同样要求具有足够的强度和刚度,并满足相关技术标准。
目前机车车辆车体结构的强度计算分析主要采用有限元法,在施工设计后进行有限元计算可以检验设计的合理性和结构是否达到设计要求,并对车体结构改进提供科学依据。
1铝合金地铁的优势以及发展概况以车体的材料为标准来进行分类,其主要分为碳钢车体、铝合金车体以及不锈钢车体三种。
铝合金车体和不锈钢车体属于轻量化车体,相对于这两种车体来说,碳钢车体在生产成本以及加工制造方面花销要明显地更小,然而随着社会发展,人们更加关注车体轻量化、节能减排和可持续发展思想等,地铁车辆采用应用碳钢车体的比例大幅度降低,已经不适合现在发展的步伐,逐渐的被社会所淘汰,现在越来越多的地铁车体都是铝合金车体和不锈钢车体。
全焊接A型地铁车辆铝合金鼓形车体制造工艺
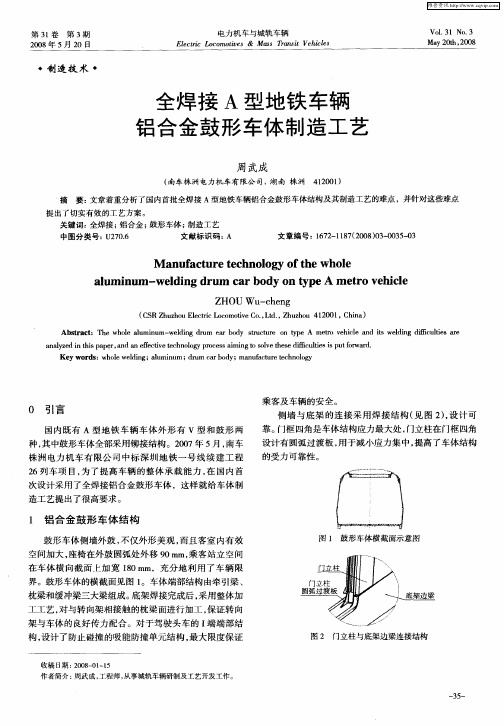
O 引言
国 内既有 A型地 铁 车辆 车体 外形 有 V型和 鼓形 两 种 , 中鼓形车体全部采用铆接结构。20 其 07年 5月 , 南车 株洲 电力 机车 有 限公 司 中标 深圳 地 铁一 号线 续 建工 程 2 6列车项 目, 为了提 高车辆 的整体 承 载能 力 , 国内首 在 次设计采用 了全焊接铝合 金鼓形车体 ,这样就 给车体制 造工艺提出 了很高要求。
反装是 以侧墙单元外 侧作为定位基准 ,采用机械压紧方
式, 确保 门立柱与侧墙板外侧 与工装贴紧 , 以获得理想的 鼓形外侧成形 。通过采用整体鼓形侧墙单 元检测 工装检 测 , 形侧墙单元 的整体变形量控制在设计范围之 内。 鼓
31 底架对车体轮廓度的影 响 .3 .
2 铝合金鼓形车体制造工艺难点
维普资讯
第 3 卷 第 3期 1 20 年 5月 2 日 08 0
电力 机 车 与 城 轨 车 辆
Elcrc e ti Lo o c mot e & M a s r n i Ve ces i s v s T a st hil
Vo . No 1 31 .3 M a t 20 y20 h, 08
鼓形车体制造主要存在如下难点 : 1控 制铝合金 车体 的焊接 变形 , ) 保证 车体 的轮廓 度 符合设计要求 。 车体 的轮廓度控 制是 限界 的需要 , 也直接 关 系到车 门的安装及调试。 另外 , 侧墙在窗 口区的平面度
直接关 系到窗户 的安装以及 车窗粘 接的美观性 。
底架 的宽度 和底架边梁 的直线度对车体 的轮廓度有 着较 大的影 响。 由于侧墙与底架边梁是插接结构 , 底架边 梁 的直线度 直接影响着侧墙 的装配 。底架 的宽度虽然有
枕梁和缓 冲梁三 大梁组成 。 底架焊接完成后 , 采用 整体 加
A型地铁铝合金车体结构设计

A型地铁铝合金车体结构设计【摘要】车体是车辆结构的主体,车体强度、刚度关系到车辆运行的可靠性和安全性。
合理选择车体的材料和车体结构是保证地铁“安全、可靠、快速、轻量、经济、适用”运营的重要因素之一。
【关键词】材料;参数;车体结构1.A型地铁铝合金车体材料选择车体承载结构主要采用铝合金大型中空挤压型材6005A-T6、7005-T6、6063-T5及板材5083-H111、6082-T6系列,铝合金大型中空挤压型材耐腐蚀性高、易于焊接、密度小,同时还有抗拉强度高、屈服强度高的优点,因此在国外A型地铁车辆中被广泛应用。
A型地铁所使用的铝合金的强度数据,满足欧洲标准EN755-2及德国标准DIN 1748要求,热处理满足DIN EN515或相应的欧洲或国际标准的规定。
2.主要技术参数所设计的车体为采用大型中空铝合金挤压型材A型地铁鼓形车体;头车车体的主要技术参数如下:1)车辆长度:23619mm;2)车辆定距:15700mm;3)车辆宽度:3000mm;4)车辆高度:3760mm;5)车钩中心线至轨面的高度:720mm。
中间车车体的主要技术参数如下:1)车辆长度:21885mm;2)车辆定距:15700mm;3)车辆宽度:3000mm;4)车辆高度:3760mm;5)车钩中心线至轨面的高度:720mm。
3.A型地铁铝合金车体承载形式3.1 车体总成如图1、2所示,车体外形为鼓型,这样能很好的降低空气阻力,减少能源的消耗。
车体采用通长大断面铝合金中空挤压型材全焊接或部分铆接结构,由底架、车顶、侧墙、端墙、司机室等部分组成,底架、侧墙、端墙及车顶均承受载荷,能够承受垂直、纵向、横向、扭转等载荷。
车体由纵向长尺寸的挤压铝合金型材制造,不需要对接。
车体结构基本要求是进行轻量化设计,整体承载结构,底架无中梁。
司机室为框架结构,外部由玻璃钢罩板包裹,前端的玻璃钢罩板符合空气动力学要求。
司机室端部结构设计能满足意外撞车时的能量吸收。
地铁铝合金车体轻量化设计与结构设计王鸿越

地铁铝合金车体轻量化设计与结构设计王鸿越发布时间:2021-09-26T08:02:19.696Z 来源:《中国科技人才》2021年第19期作者:王鸿越马维国段鹏飞蒋吉利吕起越[导读] 随着我们国家的轨道交通行业不断发展与壮大,特别是在城市的建设过程中,地铁已经成为主要的建设项目之一。
中车长春轨道客车股份有限公司 130062摘要:随着我们国家的轨道交通行业不断发展与壮大,特别是在城市的建设过程中,地铁已经成为主要的建设项目之一。
地铁在出行中占比较高,作为常用的交通工具,地铁的安全性能也受到大众的重点关注。
目前地铁已经大量采用铝合金式的合金材料,确实能够减轻车体的重量,从优化设计和结构设计的角度进行地铁生产的考虑。
本文主要针对铝合金车体轻量化设计和结构设计这样的角度进行讨论与分析。
关键词:地铁;铝合金车体;轻量化设计;结构设计引言:在地铁的日常运营过程中,地铁的安全性能是运营的首要关注问题,保障乘客的生命财产安全,也是地铁工作人员的首要责任。
对于地铁出现安全事故,特别是出现碰撞事故的时候,会第一时间产生较大的应力冲击,因此地铁的车体刚度与强度要有较高的要求。
现阶段车体采用的铝合金材质,能够保障车辆的强度,也符合轻量化的设计要求与标准。
本文就此进行分析与讨论。
一、地铁铝合金车辆轻量化设计铝合金这样的材质不仅具有强度较高,还具有质量较轻的综合优点,在地铁行业中应用范围比较广泛。
铝合金材质在运用工业制造方面,主要体现在强度等级上,能在地铁制造生产的过程中,减轻地铁的重量。
通常情况下,为了保障地铁材质的弯曲强度,铝合金车体的选取断面系数是钢体的三倍之高。
铝合金和钢结构存在本质的区别,在使用车体设计中也需要经过严密的计算,在车体的焊接和连接施工作业的时候,复杂程度相对较高,因此铝合金的车体生产过程中,尽可能减少焊接或者是螺栓连接方面的使用。
一般情况来说,传统的地铁车辆设计采用的是钢结构的板梁式结构设计,这样的设计方式相对落后,而且大量的零件都由焊接而成,导致在设备需求量不断增加的时候,生产难度较高。
铝合金汽车车身结构设计与分析

铝合金汽车车身结构设计与分析随着汽车工业的不断发展,铝合金正成为汽车制造业的关键材料之一。
因为铝合金具有高强度、轻质、耐腐蚀、良好的成型性和可回收利用等诸多优点,广泛应用于汽车车身的设计和制造。
在本文中,我们将探讨铝合金汽车车身结构设计和分析的相关问题。
一、铝合金汽车车身的重要性汽车车身是车辆结构的核心部分,其主要功能是保护车内乘客,维持车辆稳定,降低噪音和提高燃油经济性。
与传统的钢铁材料相比,铝合金更轻、更强、更节能,因此受到了汽车制造商们的广泛青睐。
铝合金车身能够有效降低汽车的整体重量,提高汽车的燃油经济性和行驶稳定性,减少废气排放。
此外,铝合金车身还能减少材料损耗,因为它可在较高的温度下重复使用和熔炼。
二、铝合金汽车车身设计的基本原则1、重量优化:铝合金的最大优点是轻量化,因此在设计车身结构时,应该尽可能地将总重量降低,提高整个车辆的燃油经济性。
2、强度优化:虽然铝合金比钢弱一些,但是有很大的改进空间。
设计时应尽可能提高铝合金车身的强度和韧性,以确保安全性。
3、成本优化:虽然铝合金材料的成本比钢高,但是在设计时,可以采用合理的制造工艺和设计方法,降低成本。
4、材料优化:选择适合的铝合金材料,是铝合金汽车车身设计中的重要一环。
车身结构设计者需要评估每种可用的铝合金材料的特性和优劣,选择最合适的一种作为车身的基本材料。
三、铝合金汽车车身结构分析铝合金汽车车身结构分析可以帮助设计者选择合适的方案,优化设计,并提高车身强度和刚度。
下面,我们来看一些常用的分析方法。
1、有限元分析有限元分析是在计算机上用数值方法对结构进行分析和优化的一种方法。
通过有限元分析,设计者能够预测车身结构在模拟载荷下的应力分布和变形情况,从而有效地评估结构的强度和刚度。
同时,有限元分析还可以分析材料疲劳寿命、极限载荷等车身承载性能指标,为车身设计提供指导。
2、模态分析模态分析是一种预测结构动力学特性的方法。
通过模态分析,设计者可以确定结构在弹性范围内的振动频率和振型,并预测当结构受到激励时的响应情况。
铝合金车身结构设计与优化研究
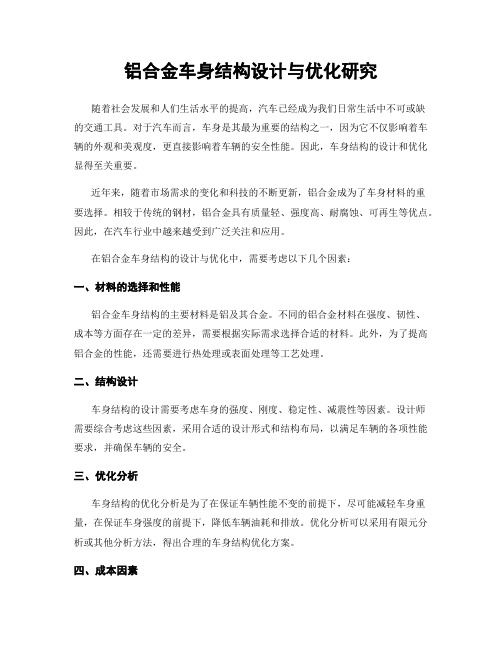
铝合金车身结构设计与优化研究随着社会发展和人们生活水平的提高,汽车已经成为我们日常生活中不可或缺的交通工具。
对于汽车而言,车身是其最为重要的结构之一,因为它不仅影响着车辆的外观和美观度,更直接影响着车辆的安全性能。
因此,车身结构的设计和优化显得至关重要。
近年来,随着市场需求的变化和科技的不断更新,铝合金成为了车身材料的重要选择。
相较于传统的钢材,铝合金具有质量轻、强度高、耐腐蚀、可再生等优点。
因此,在汽车行业中越来越受到广泛关注和应用。
在铝合金车身结构的设计与优化中,需要考虑以下几个因素:一、材料的选择和性能铝合金车身结构的主要材料是铝及其合金。
不同的铝合金材料在强度、韧性、成本等方面存在一定的差异,需要根据实际需求选择合适的材料。
此外,为了提高铝合金的性能,还需要进行热处理或表面处理等工艺处理。
二、结构设计车身结构的设计需要考虑车身的强度、刚度、稳定性、减震性等因素。
设计师需要综合考虑这些因素,采用合适的设计形式和结构布局,以满足车辆的各项性能要求,并确保车辆的安全。
三、优化分析车身结构的优化分析是为了在保证车辆性能不变的前提下,尽可能减轻车身重量,在保证车身强度的前提下,降低车辆油耗和排放。
优化分析可以采用有限元分析或其他分析方法,得出合理的车身结构优化方案。
四、成本因素铝合金车身比传统的钢质车身成本高,而汽车制造商需要控制成本,提高竞争力。
因此,在设计铝合金车身时,需要注意成本的控制,降低制造成本,并兼顾车身的性能。
总的来说,铝合金车身结构设计与优化需要考虑多个因素,包括材料的选择和性能、结构设计、优化分析以及成本控制。
对于汽车制造商而言,他们需要综合考虑这些因素,以达到理想的车身结构,在满足车辆性能和安全性的前提下,降低车身重量,提高汽车的燃油经济性和环保性。
铝合金汽车车身结构的优化设计

铝合金汽车车身结构的优化设计随着汽车工业技术的不断发展,车身材料也在不断更新换代。
铝合金车身作为轻量化车身的一种代表,由于其具有高强度、高韧性、耐腐蚀等优点,被越来越多的汽车厂商所采用。
本文将从优化设计的角度出发,分析铝合金汽车车身结构的特点和设计原则,并探讨如何实现更好的轻量化效果和安全性。
一、铝合金汽车车身结构的特点1. 高强度铝材料的强度比钢材低,但是铝合金材料的强度和韧性都比纯铝高出很多。
铝合金车身可以在相同重量下承受更大的力,保证车身结构的稳定和安全性。
2. 轻量化铝合金车身相对于传统钢质车身更轻,可以使汽车整体质量减轻30%以上。
这样可以减少燃油消耗、降低车辆排放,同时也降低了车辆对道路的磨损。
3. 耐腐蚀铝合金车身具有良好的耐腐蚀性能,特别是在海滨地区和雪区使用的车辆中,更具有显著的优势。
4. 安全性铝合金车身可以吸收撞击能量,减少车内乘员对事故的伤害,同时也能降低车身损坏的程度。
二、铝合金汽车车身结构的设计原则1. 结构优化铝合金汽车车身结构优化设计的关键在于结构的合理性。
通过对车身零部件的精细设计和统筹考虑,减少零部件的数量和重量,实现车身结构的优化。
2. 材料选择铝合金材料的选择非常重要,应根据车型、性能及设计要求等因素进行选择。
优先考虑成本、强度、韧性和加工性等因素,并充分考虑复杂工艺的实施。
3. 制造工艺铝合金车身制造具有一定的复杂程度,需要采用适当的工艺和设备。
汽车生产企业应根据车身设计要求,选择适合的加工设备和工艺,并考虑到铝合金的特性,保证精度和质量。
三、如何实现更好的轻量化效果和安全性1. 加强材料强度采用高强度的铝合金材料可以达到轻量化的目的,但是这样可能会降低安全性。
因此,可以采用增加材料厚度、加强螺栓连接和使用高强度碳纤维等方式来强化材料,提高材料强度和车身的稳定性。
2. 加强车身结构加强车身结构可以提高车身的稳固性和抵抗撞击能力。
可以采用四柱式车身结构,增加侧面支撑,增加车身刚度,提高车身的稳固性。
动车组铝合金车体结构强度分析的开题报告
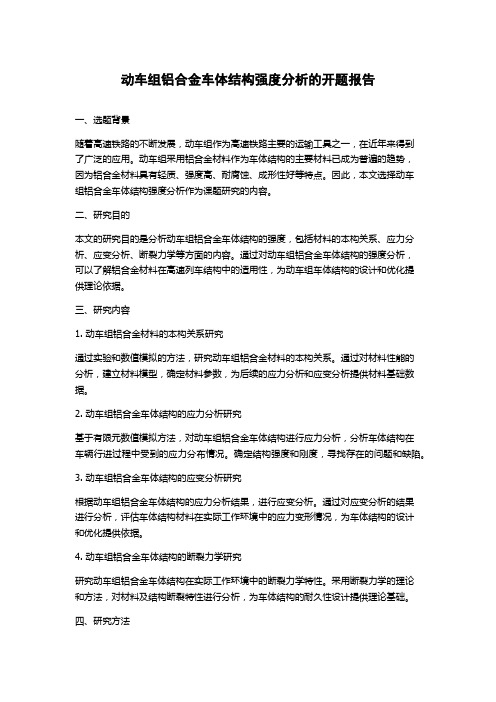
动车组铝合金车体结构强度分析的开题报告一、选题背景随着高速铁路的不断发展,动车组作为高速铁路主要的运输工具之一,在近年来得到了广泛的应用。
动车组采用铝合金材料作为车体结构的主要材料已成为普遍的趋势,因为铝合金材料具有轻质、强度高、耐腐蚀、成形性好等特点。
因此,本文选择动车组铝合金车体结构强度分析作为课题研究的内容。
二、研究目的本文的研究目的是分析动车组铝合金车体结构的强度,包括材料的本构关系、应力分析、应变分析、断裂力学等方面的内容。
通过对动车组铝合金车体结构的强度分析,可以了解铝合金材料在高速列车结构中的适用性,为动车组车体结构的设计和优化提供理论依据。
三、研究内容1. 动车组铝合金材料的本构关系研究通过实验和数值模拟的方法,研究动车组铝合金材料的本构关系。
通过对材料性能的分析,建立材料模型,确定材料参数,为后续的应力分析和应变分析提供材料基础数据。
2. 动车组铝合金车体结构的应力分析研究基于有限元数值模拟方法,对动车组铝合金车体结构进行应力分析,分析车体结构在车辆行进过程中受到的应力分布情况。
确定结构强度和刚度,寻找存在的问题和缺陷。
3. 动车组铝合金车体结构的应变分析研究根据动车组铝合金车体结构的应力分析结果,进行应变分析。
通过对应变分析的结果进行分析,评估车体结构材料在实际工作环境中的应力变形情况,为车体结构的设计和优化提供依据。
4. 动车组铝合金车体结构的断裂力学研究研究动车组铝合金车体结构在实际工作环境中的断裂力学特性。
采用断裂力学的理论和方法,对材料及结构断裂特性进行分析,为车体结构的耐久性设计提供理论基础。
四、研究方法在研究过程中,主要采用实验、数值模拟和分析等方法进行研究。
主要研究工具包括有限元分析软件、高速列车模拟测试设备、车体应变测试仪、破裂试验设备等。
五、预期成果通过对动车组铝合金车体结构强度分析的研究,预计能够获得以下预期成果:1. 动车组铝合金车体材料本构关系和性能特点的研究成果。
铝合金车体结构设计构思_常树民

焊 接 性、耐 蚀 性 车 辆 结 构
差, 强 度 最 高。 Al 材、飞 机 杆 Zn Mg 合 金 的 焊 接 件、体育用品 接头效率高, 代表合 金 有 7005A、7075、 7178、7N01、7003 等
接处, 从而避免了大梁中部的破坏。
5 结论
通过应用有限单元法对翻车机钢结构进行仿真分 析和优化计算, 得出不同工况下的应力和变形值, 并依
的负载主要是拉伸应力, 压缩应力不大, 而且仅在列车
制动时, 在有限的制动距离内周期产生。
在上述承载条件下, 流线型裙板应是组合结构, 底 部制成承载的平板或曲率小的平板, 而侧面部分制成
可拆卸的非承载的盖或可放下的门, 以便车下设备的
安装和检修。裙板仅在两端与底架有刚性连接, 其余 部分则通过骨架连接。这些骨架在横向平面、局部在
图 2 带盲窗的侧墙 局部结构
挤压型材形状, 同时应将焊接部位放在低应力区。
3. 3. 5 底架 底架由 2 根空腹多室断面的侧梁、若干宽幅空心
薄壁桁架 式断面的长大 闭口型材( 厚 60 mm) 及牵引
梁、枕梁、缓冲梁、端梁等组成。边梁、地板型材上部 C
形夹沟用来固定地板, 并通过焊接管通风, 以免形成冷 凝水。边梁、地板型材下面的沟槽沿底架纵向布置, 与
因铝合金具有良好的耐蚀性、挤压加工性和较高 的强度, 挤压型材外表面和腹板最小壁厚可达2 8 mm 和 2 5 mm, 所以 纵向挤压 型材采用 6005A 材 料( 200 MPa s 225 MPa) 。底架牵引梁、枕梁、缓冲梁、端梁 因需要较高的强度而断面又不复杂, 故采用 7005A( s = 290 MPa) 。 3. 3. 2 车顶结构
( 5) 易于再生。铝的熔点低( 660 ) , 再生简单。 在废弃处理时也无公害, 有利于环保, 符合可持续发展 战略。
地铁铝合金车体轻量化设计与结构设计

Technology Application技术应用DCW169数字通信世界2019.02铁道运输中,对车体的刚度有着很高的要求,现阶段车体材料采用铝合金。
这样不仅能保障车辆的强度,也符合轻量化设计的要求。
文章介绍一款轻量化设计的B 型铝合金鼓形车体,用有限元模型对设计的结构强度作出了分析。
1 铝合金车体的轻量化设计铝在地壳中的含量非常高,但强度较低,经过合金化后,强度会得到显著的提升。
同时相比于钢结构,铝的密度较低,因此铝合金在生产中得到了广泛的应用。
铝合金车体设计过程中要注意到车体的刚度问题,为了保障弯曲刚度,选取断面系数要是钢的3倍,设计中要充分考虑到铝合金的断面高和板厚度。
铝合金车体中各个零部件的连接中有焊接和铆接等结构。
其中,焊接的难度较大,操作起来较为复杂,容易产生较大的热应力[1]。
2 车体结构设计该轻量化车体设计中,是由底架、车顶、侧墙和司机室骨架等构成的,采用铝合金全焊接的结构。
设计中的长度是19300mm ,高度是3687mm ,最大宽度是2800mm ,门间距是4450mm ,车俩定距为12600mm ,车身自重为6.6吨[2]。
2.1 主体结构型材设计车体主体结构占总质量的80%,设计中采用了大断面中空型材,包括了车顶边梁、门立柱和底架地板等。
车体焊接使用MIG 焊,铝合金厚度的减小,会增加其焊接的难度。
在该设计中,为了保障焊接的安全程度,主体结构中保障了型材的厚度。
通常状况下,车顶边梁中用到大断面、厚度较大的筋板时,会造成车顶重量增大。
该设计中为了防止重量过大,对筋板的数量进行了科学的调控。
结构设计中对空调梁进行了单独设计,焊在长梁上,在一定程度上节省了材料。
侧墙板型材断面用三角形截面,内筋板2到3mm ,外壁为3到4mm ,保障了侧墙平面程度。
底架边梁内筋板厚度是3到4mm ,外闭厚度在5mm 左右,对底架的结构强度作出保障。
长地板中分布较多的U 形槽,增加长地板的设备悬挂能力[3]。
微鼓形铝合金车体轻量化结构研制
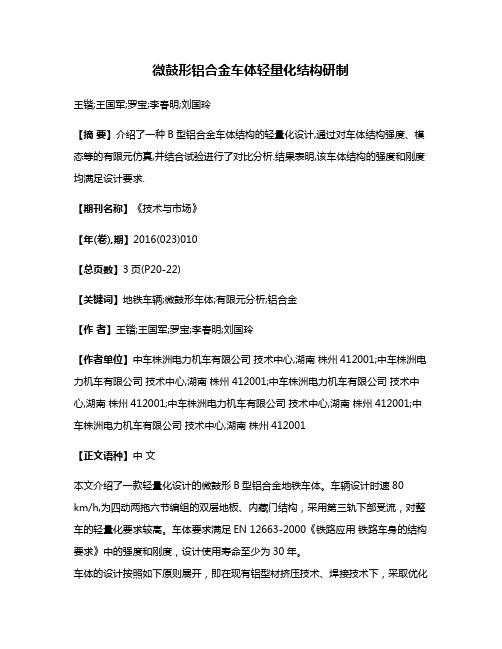
微鼓形铝合金车体轻量化结构研制王锴;王国军;罗宝;李春明;刘国玲【摘要】介绍了一种B型铝合金车体结构的轻量化设计,通过对车体结构强度、模态等的有限元仿真,并结合试验进行了对比分析.结果表明,该车体结构的强度和刚度均满足设计要求.【期刊名称】《技术与市场》【年(卷),期】2016(023)010【总页数】3页(P20-22)【关键词】地铁车辆;微鼓形车体;有限元分析;铝合金【作者】王锴;王国军;罗宝;李春明;刘国玲【作者单位】中车株洲电力机车有限公司技术中心,湖南株州412001;中车株洲电力机车有限公司技术中心,湖南株州412001;中车株洲电力机车有限公司技术中心,湖南株州412001;中车株洲电力机车有限公司技术中心,湖南株州412001;中车株洲电力机车有限公司技术中心,湖南株州412001【正文语种】中文本文介绍了一款轻量化设计的微鼓形B型铝合金地铁车体。
车辆设计时速80km/h,为四动两拖六节编组的双层地板、内藏门结构,采用第三轨下部受流,对整车的轻量化要求较高。
车体要求满足EN 12663-2000《铁路应用铁路车身的结构要求》中的强度和刚度,设计使用寿命至少为30年。
车体的设计按照如下原则展开,即在现有铝型材挤压技术、焊接技术下,采取优化布置型材筋板、简化组装结构、采用搅拌摩擦焊结构等轻量化措施,优化设计车体结构,并通过充分的计算分析、试验验证和再优化设计,研制一款模块化、轻量化、低成本、焊接高安全性、高可靠性的铝合金车体。
本轻量化车体为整体承载的铝合金全焊接结构,由底架、侧墙、端墙、车顶和司机室骨架结构等部分组成,如图1所示。
其主要技术参数如下:车体长度/mm 19 300车体宽度/mm 2 800车辆定距/mm 12 600车门间距/mm 4 450整备重量/空载(AW0)/t 31超载(AW3)/人326按照CJJ96中对BⅡ型车的限界要求,车体设计时充分利用了限界空间,扩展了车辆内部的乘用空间,并依照人体工学原理,确定了车体的外部拐点及轮廓线。
上海A型地铁铝合金车体结构设计
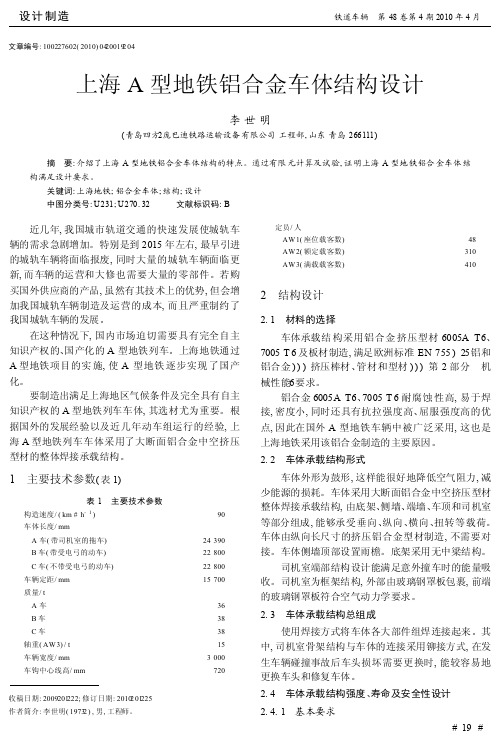
在使用期内能承受正常载荷的作用, 而不产生永 久变形, 能满足修理和纠正脱轨的要求。
车体刚度满足要求, 在 AW0( 空载) 工况时上挠度 [ 3 mm, AW3( 满载) 工况时下挠度 [ 7 mm, 并保证在 所有载荷下, 车门能正常动作。 # 20 #
在底架边梁上枕梁中心的位置设 4 个支撑点。 在两端的缓冲梁中央分别设 1 个架车支撑点, 作 复轨用。在缓冲梁下方架车能够抬起空载的整车的一 端。 在车辆的端部设 4 个起吊点, 在车辆定距 内设 4 个起吊点, 用于吊车或紧急情况下的架车。 架车、吊车、复轨用的 架车支撑点可满足车辆拆 卸、组装、检修、吊运和救援作业的需要。 车体强度能保证在使用任何一对架车机架车时不 会使车体结构的任何部位发生屈服变形。每个架车支 撑点处设有定位点。架车、吊车点( 共 14 个) 处有标记 以指导作业。 2. 4. 10 防爬装置 在每个 A 车的前端设置一套带有能量吸收装置 的防爬器, 且能与指定线路上的车辆的防爬器匹配。 在车辆的其余端设有 不带能量吸收 装置的防爬 器, 当车辆发生严重碰撞时保证相邻的两辆车之间不 会发生爬顶事故而造成更大的损失。
215
顶车工况边梁支撑处 215
窗角
225
门角
215
各种工况下车体结构板单元的最大应力及其相应 部位见表 2。由表 2 可见, 在各个工况下车体的应力 均小于车体的许用应力, 满足设计要求。 3. 5 强度计算结果 ) ) ) 变形
在 AW 0、AW 3 工况下车体结构边梁中央和地板中 心位置的挠度如表 3 所示。由表 3 可见, 在 AW 3 工况 下车体边梁的垂向位移为 91 05 mm, 满足设计要求。
地铁鼓形铝合金车体承载结构设计要点及限界校核
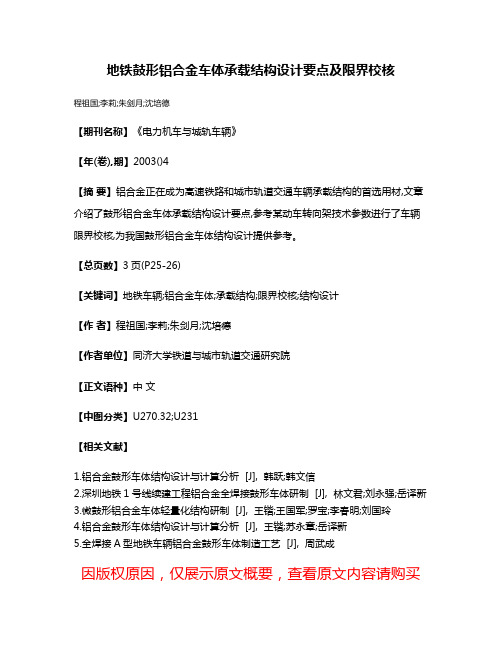
地铁鼓形铝合金车体承载结构设计要点及限界校核
程祖国;李莉;朱剑月;沈培德
【期刊名称】《电力机车与城轨车辆》
【年(卷),期】2003()4
【摘要】铝合金正在成为高速铁路和城市轨道交通车辆承载结构的首选用材,文章介绍了鼓形铝合金车体承载结构设计要点,参考某动车转向架技术参数进行了车辆限界校核,为我国鼓形铝合金车体结构设计提供参考。
【总页数】3页(P25-26)
【关键词】地铁车辆;铝合金车体;承载结构;限界校核;结构设计
【作者】程祖国;李莉;朱剑月;沈培德
【作者单位】同济大学铁道与城市轨道交通研究院
【正文语种】中文
【中图分类】U270.32;U231
【相关文献】
1.铝合金鼓形车体结构设计与计算分析 [J], 韩跃;韩文信
2.深圳地铁1号线续建工程铝合金全焊接鼓形车体研制 [J], 林文君;刘永强;岳译新
3.微鼓形铝合金车体轻量化结构研制 [J], 王锴;王国军;罗宝;李春明;刘国玲
4.铝合金鼓形车体结构设计与计算分析 [J], 王锴;苏永章;岳译新
5.全焊接A型地铁车辆铝合金鼓形车体制造工艺 [J], 周武成
因版权原因,仅展示原文概要,查看原文内容请购买。
浅论铝合金车体的制造
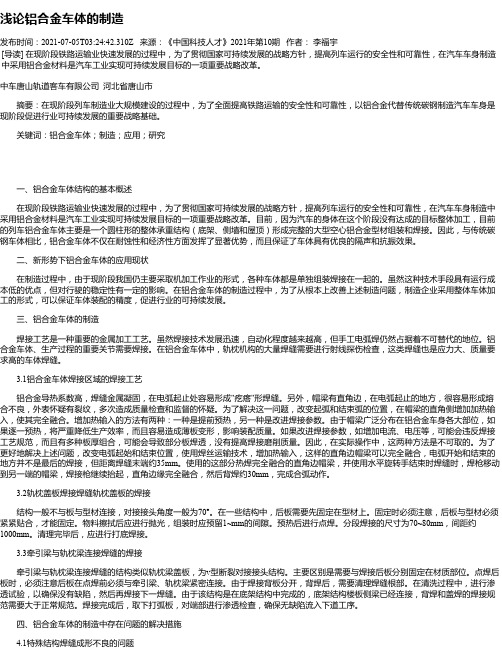
浅论铝合金车体的制造发布时间:2021-07-05T03:24:42.310Z 来源:《中国科技人才》2021年第10期作者:李福宇[导读] 在现阶段铁路运输业快速发展的过程中,为了贯彻国家可持续发展的战略方针,提高列车运行的安全性和可靠性,在汽车车身制造中采用铝合金材料是汽车工业实现可持续发展目标的一项重要战略改革。
中车唐山轨道客车有限公司河北省唐山市摘要:在现阶段列车制造业大规模建设的过程中,为了全面提高铁路运输的安全性和可靠性,以铝合金代替传统碳钢制造汽车车身是现阶段促进行业可持续发展的重要战略基础。
关键词:铝合金车体;制造;应用;研究一、铝合金车体结构的基本概述在现阶段铁路运输业快速发展的过程中,为了贯彻国家可持续发展的战略方针,提高列车运行的安全性和可靠性,在汽车车身制造中采用铝合金材料是汽车工业实现可持续发展目标的一项重要战略改革。
目前,因为汽车的身体在这个阶段没有达成的目标整体加工,目前的列车铝合金车体主要是一个圆柱形的整体承重结构(底架、侧墙和屋顶)形成完整的大型空心铝合金型材组装和焊接。
因此,与传统碳钢车体相比,铝合金车体不仅在耐蚀性和经济性方面发挥了显著优势,而且保证了车体具有优良的隔声和抗振效果。
二、新形势下铝合金车体的应用现状在制造过程中,由于现阶段我国仍主要采取机加工作业的形式,各种车体都是单独组装焊接在一起的。
虽然这种技术手段具有运行成本低的优点,但对行驶的稳定性有一定的影响。
在铝合金车体的制造过程中,为了从根本上改善上述制造问题,制造企业采用整体车体加工的形式,可以保证车体装配的精度,促进行业的可持续发展。
三、铝合金车体的制造焊接工艺是一种重要的金属加工工艺。
虽然焊接技术发展迅速,自动化程度越来越高,但手工电弧焊仍然占据着不可替代的地位。
铝合金车体、生产过程的重要关节需要焊接。
在铝合金车体中,轨枕机构的大量焊缝需要进行射线探伤检查,这类焊缝也是应力大、质量要求高的车体焊缝。
- 1、下载文档前请自行甄别文档内容的完整性,平台不提供额外的编辑、内容补充、找答案等附加服务。
- 2、"仅部分预览"的文档,不可在线预览部分如存在完整性等问题,可反馈申请退款(可完整预览的文档不适用该条件!)。
- 3、如文档侵犯您的权益,请联系客服反馈,我们会尽快为您处理(人工客服工作时间:9:00-18:30)。
本设计存在两 大技术难点 :其一是据 现有挤压和焊接 工 艺, 设计满足全寿命使用要求 的轻 量化车体结构 ; 其二是设计 满足流线形头罩安装 的功能性司机室骨架结构 。 本文将 就上述 两点分析车体结构 , 并利用有 限元方法对其结构强度和模态振
析 了其在 各 个 工况 下 的 应 力 、 变形 及 模 态 频 率 。 结果 表 明 , 车体 结构 的强 度 和 刚 度 均 满足 相 关技 术 要 求 。 该 关 键 词 : 铁 车辆 地 鼓形车体 有 限元 铝合 金
di 03 6  ̄i n10 - 542 1.5 0 o: . 9 .s. 6 8 5 .0 0 . 1 1 9 s 0 00
Ke r s mer e il d u C o y F M ; l miu y wo d : t v h ce; r m a b o r d ;E A u n m
0 引 言 .
本文介绍 的是一款具有流线外形 , 采用轻量 化设 计 , 合 适
在城市高架线路上运 营的全新B 型铝合金鼓形车体。得益于铝
技术与市场
第 1卷第5 0 0 7 期2 1 年
攮 硪 凌
铝合金鼓形车体 结构 设计 与计算分析
王 苏永章 岳译新 锴
湖南株 0 10 1
摘要 : 文章 介 绍 了一 种B型铝 合 金 鼓 形 车 体 结 构 的轻 量 化 设 计 , 立 了该 车 体 结 构 的 有 限 元模 型 , 依 据 相 关标 准 分 建 并
本轻量化车体为整体承载的铝合金全焊接结构 ,由底架 、 侧墙 、 端墙 、 车顶和司机室骨架结构等部分组成 , 图1 如 所示 。 其 主要技术参数如下 :
长度 / m m 1 30 9O
量 达8%。 目前 , 0 国内企业能挤压 出满足铁路应用要求的铝合
金 型材最小壁厚为2 m,随着 截面增大 和内部筋板厚度 的降 a r
厚度较 大的筋板 , 直接导致了车顶重量 的增加 。这里通过合理
配比筋板数量 、 截面材料利用率等 , 使重量大 幅下降。 与以往在
长梁型材上加工空调梁不 同, 本结构单独设计空调梁并 阻焊在 长梁上 , 节省 了大量 的材料 和加 工成 本 , 图3 如 车顶边梁 、 长梁 和空调梁组装图。 侧墙板型材 断面大量采用三角形或梯形截面 ,- mm的外 34
型进行分析。
1 车 体 结 构 设 计 .
11 车 体 主 体 结 构 型 材 设 计 .
图 1 车 体 整 车 结 构
图2 车体 断 面 图
车体 的主体结构均为大断面中空型材 ,主要有底架边梁 、
车顶边梁 、 端墙、 门立柱 、 侧墙板 、 底架地板等 , 总重 占车体重 其
45 40
时, 考虑焊接质量 和安全性 , 主体结构须保证连接处 型材 外壁
具有足够的厚度 。
车体 自重/ t
6 . 6
整备重量, 空载( w0 / A ) t
超 载 ( W3 / A ) A
3 1
36 2
设计时速/m h l / (
9 0
车体鼓形断面 以车辆 限界为基础确定 车体外部 轮廓线及 车体鼓形拐点 , 分利用 了限界 空间 , 充 扩展 了车辆 内部的乘客
De i n a d S m u a i n An l s so u i u d u r Bo y S r cu e sg n i l to ay e fAl m n m r m Ca d t u t r
WA NG Ka , U Yo g z a g YUE Yi xn iS n - hn , - i
Ab t a t T i a e rs nsa c n q e o g t eg t n a l mi u d u c r o y s u tr f p . c r i g t s r c : h sp p rp e e t n t h iu fl h ih n au n m r m a d t cu e o t e Ac o d n e i w o b r B y o s mer lt n l r e o s is t p F M d e f h a o yo a iu a st n y ei t s , tana d mo ef q e c . h o a o a i r n , t esu E mo l eC r d n v ro sl d a a z ss e s sri n d e u n y T e e i c ti ot b o o l t r r
站立空间。图2 为车体结构断面图。
图 3车顶 边梁 、 梁 、 调 梁 组装 图 长 空 图4侧 墙 板 组 装 图
3
鼹 嚣
T C N L G N R E E H o o Y A D MA K T
Vo . 7 No5 2 0 11 , ., 01
一
般情况下 , 车顶 边梁 和长梁型材均采用 大断 面、 稀疏 而
低, 挤压难度 增加 ; 在车体焊 接方面 , 国内主要 采用MI 焊 , G 且
随着铝合金板厚的降低 , 其焊接难度 和变形是不断增 大的。同
最大宽度/ mm 高( 轨面至车顶 ) m / m 车辆定距/ m m
车 门 间 距 ,m m
20 80 3 8 67 16 0 20
r s l h w ta ec rb yd sg a s e er q i me t o lv n a d r s d tc n l g p cf a o . e ut s o t a o e in s t f s h ur s h t h d ii t e e n f ee a t t n ad h oo ys e i c t n s r s n a e i i