磷化膜影响因素
磷化质量影响因素及其提高途径

磷化质量影响因素及其提高途径引言磷化是一种化学与电化学反应形成磷酸盐化学转化膜的过程。
早在1869年W. A. Ross 就申请了磷化专利技术 [ 2 ] ,随着科技的不断进步,金属磷化处理作为传统的表面处理技术在金属防护、减磨耐磨及涂层打底等方面得到广泛的发展和应用。
磷化处理有多种分类方法:按成膜体系可分为锌系、锌锰系、锰系、铁系、锌钙系及非晶相铁系等六大类;按磷化处理温度可分为常温(不加温)、低温(30~45℃)、中温(60~70℃)、高温(大于80℃)四类;按材质可分为钢铁件、铝件、锌件以及混合件磷化;其它的还有按磷化膜厚度或促进剂类型等分类。
用于防锈磷化的主要有铁系磷化、锌系磷化、锰系磷化三种;用于耐磨减磨磷化的种类有锌系磷化和锰系磷化;而锌锰系和锌钙系主要用于漆前磷化。
一磷化基本原理磷化成膜是一个化学动态平衡,目前,大多数学者认同的磷化原理由以下四个步骤组成:首先是金属的溶解过程。
当金属浸入磷化液中时,先与磷化液中的磷酸作用,生成一代磷酸铁,并有大量的氢气析出。
其化学反应为;Fe –2e→Fe2+2H+ + 2e→H2上式表明,磷化开始时,仅有金属的溶解,而无膜生成。
第二是促进剂加速形成磷化膜。
其化学反应式为:[O]+[H] → [R]+H2OFe2++[O] → Fe3++[R]式中[O]为促进剂(氧化剂),[R]为还原产物,由于促进剂氧化掉第一步反应所产生的氢原子,加快了反应(1)的速度,进一步导致金属表面H+浓度急剧下降。
同时也将溶液中的Fe2+氧化成为Fe3+。
第三是磷酸根的多级离解。
H3PO4→H2PO4-+H+→HPO42-+2H+→PO43-+3H+由于金属表面的H+浓度急剧下降,导致磷酸根各级离解平衡向右移动,最终离解为PO43-。
最后磷酸盐沉淀结晶成为磷化膜当金属表面离解出的PO43-与溶液中(金属界面)的金属离子(如Zn2+、Mn2+、Ca2+、Fe2+)达到溶度积常数Ksp时,就会形成磷酸盐沉淀Zn2++ Fe2++ PO43-+H2O→Zn2Fe(PO4)2·4H2O↓ (4)3Zn2++2PO43-+4H2O=Zn3(PO4)2·4H2O↓ (5)磷酸盐沉淀与水分子一起形成磷化晶核,晶核继续长大成为磷化晶粒,无数个晶粒紧密堆集形而上学成磷化膜。
磷化膜影响因素
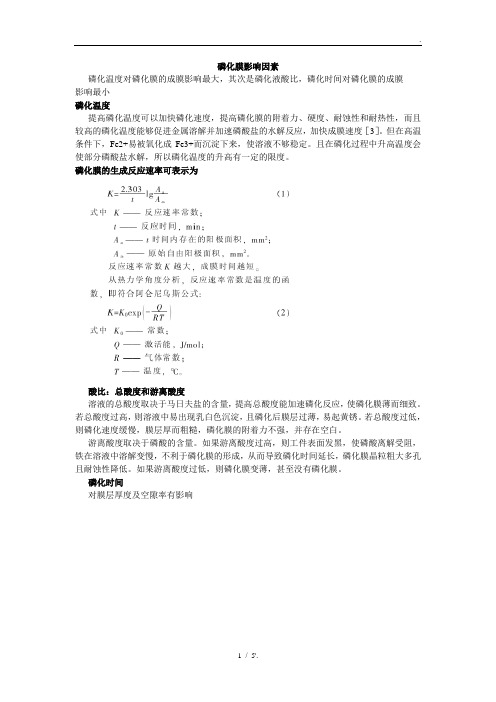
磷化膜影响因素磷化温度对磷化膜的成膜影响最大,其次是磷化液酸比,磷化时间对磷化膜的成膜影响最小磷化温度提高磷化温度可以加快磷化速度,提高磷化膜的附着力、硬度、耐蚀性和耐热性,而且较高的磷化温度能够促进金属溶解并加速磷酸盐的水解反应,加快成膜速度[3]。
但在高温条件下,Fe2+易被氧化成Fe3+而沉淀下来,使溶液不够稳定。
且在磷化过程中升高温度会使部分磷酸盐水解,所以磷化温度的升高有一定的限度。
磷化膜的生成反应速率可表示为酸比:总酸度和游离酸度溶液的总酸度取决于马日夫盐的含量,提高总酸度能加速磷化反应,使磷化膜薄而细致。
若总酸度过高,则溶液中易出现乳白色沉淀,且磷化后膜层过薄,易起黄锈。
若总酸度过低,则磷化速度缓慢,膜层厚而粗糙,磷化膜的附着力不强,并存在空白。
游离酸度取决于磷酸的含量。
如果游离酸度过高,则工件表面发黑,使磷酸离解受阻,铁在溶液中溶解变慢,不利于磷化膜的形成,从而导致磷化时间延长,磷化膜晶粒粗大多孔且耐蚀性降低。
如果游离酸度过低,则磷化膜变薄,甚至没有磷化膜。
磷化时间对膜层厚度及空隙率有影响图:磷化时间与孔隙率的关系曲线--------------------------------------------------------------1 Fe2+含量控制起决定性作用,过高则磷化膜晶粒粗大多孔、Fe2+含量上升快、磷化时间延长,而偏低会使磷化膜变薄或不能成膜。
严格控制Fe2+的过快增多是磷化溶液维护的关键之一。
控制酸度比及NO-3与H2PO-4的最佳比例、适量添加铬合稳定剂如酒石酸等都能有效控制Fe2+过快升高,且有利于减少磷化沉渣生成、提高磷化膜层质量。
若Fe2+含量超过允许范围,则磷化沉渣会增多,磷化膜质量劣化。
-----------------------------------------------------174 试验证明磷化液中Fe2+的最佳含量为1. 5~3. 0 g/L。
影响金属磷化膜效果的因素
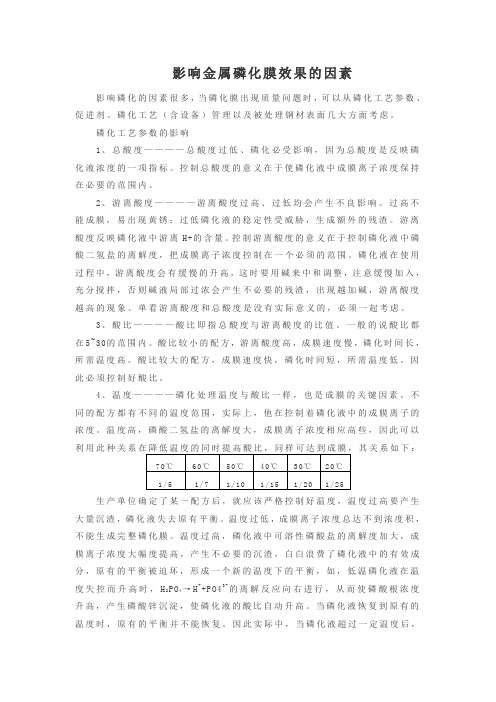
影响金属磷化膜效果的因素影响磷化的因素很多,当磷化膜出现质量问题时,可以从磷化工艺参数、促进剂、磷化工艺(含设备)管理以及被处理钢材表面几大方面考虑。
磷化工艺参数的影响1、总酸度————总酸度过低、磷化必受影响,因为总酸度是反映磷化液浓度的一项指标。
控制总酸度的意义在于使磷化液中成膜离子浓度保持在必要的范围内。
2、游离酸度————游离酸度过高、过低均会产生不良影响。
过高不能成膜,易出现黄锈;过低磷化液的稳定性受威胁,生成额外的残渣。
游离酸度反映磷化液中游离H+的含量。
控制游离酸度的意义在于控制磷化液中磷酸二氢盐的离解度,把成膜离子浓度控制在一个必须的范围。
磷化液在使用过程中,游离酸度会有缓慢的升高,这时要用碱来中和调整,注意缓慢加入,充分搅拌,否则碱液局部过浓会产生不必要的残渣,出现越加碱,游离酸度越高的现象。
单看游离酸度和总酸度是没有实际意义的,必须一起考虑。
3、酸比————酸比即指总酸度与游离酸度的比值。
一般的说酸比都在5~30的范围内。
酸比较小的配方,游离酸度高,成膜速度慢,磷化时间长,所需温度高。
酸比较大的配方,成膜速度快,磷化时间短,所需温度低。
因此必须控制好酸比。
4、温度————磷化处理温度与酸比一样,也是成膜的关键因素。
不同的配方都有不同的温度范围,实际上,他在控制着磷化液中的成膜离子的浓度。
温度高,磷酸二氢盐的离解度大,成膜离子浓度相应高些,因此可以利用此种关系在降低温度的同时提高酸比,同样可达到成膜,其关系如下:70℃60℃50℃40℃30℃20℃1/5 1/7 1/10 1/15 1/20 1/25生产单位确定了某一配方后,就应该严格控制好温度,温度过高要产生大量沉渣,磷化液失去原有平衡。
温度过低,成膜离子浓度总达不到浓度积,不能生成完整磷化膜。
温度过高,磷化液中可溶性磷酸盐的离解度加大,成膜离子浓度大幅度提高,产生不必要的沉渣,白白浪费了磷化液中的有效成分,原有的平衡被迫坏,形成一个新的温度下的平衡,如,低温磷化液在温度失控而升高时,H2PO4→H++PO43-的离解反应向右进行,从而使磷酸根浓度升高,产生磷酸锌沉淀,使磷化液的酸比自动升高。
磷化处理影响因素及常见问题审批稿

磷化处理影响因素及常见问题YKK standardization office【 YKK5AB- YKK08- YKK2C- YKK18】一、磷化工艺参数的影响1、总酸度————总酸度过低、磷化必受影响,因为总酸度是反映磷化液浓度的一项指标。
控制总酸度的意义在于使磷化液中成膜离子浓度保持在必要的范围内。
2、游离酸度————游离酸度过高、过低均会产生不良影响。
过高不能成膜,易出现黄锈;过低磷化液的稳定性受威胁,生成额外的残渣。
游离酸度反映磷化液中游离H+的含量。
控制游离酸度的意义在于控制磷化液中磷酸二氢盐的离解度,把成膜离子浓度控制在一个必须的范围。
磷化液在使用过程中,游离酸度会有缓慢的升高,这时要用碱来中和调整,注意缓慢加入,充分搅拌,否则碱液局部过浓会产生不必要的残渣,出现越加碱,游离酸度越高的现象。
单看游离酸度和总酸度是没有实际意义的,必须一起考虑。
3、酸比————酸比即指总酸度与游离酸度的比值。
一般的说酸比都在5~30的范围内。
酸比较小的配方,游离酸度高,成膜速度慢,磷化时间长,所需温度高。
酸比较大的配方,成膜速度快,磷化时间短,所需温度低。
因此必须控制好酸比。
4、温度————磷化处理温度与酸比一样,也是成膜的关键因素。
不同的配方都有不同的温度范围,实际上,他在控制着磷化液中的成膜离子的浓度。
温度高,磷酸二氢盐的离解度大,成膜离子浓度相应高些,因此可以利用此种关系在降低温度的同时提高酸比,同样可达到成膜,其关系如下:70℃ 60℃ 50℃ 40℃ 30℃ 20℃1/5 1/7 1/10 1/15 1/20 1/25生产单位确定了某一配方后,就应该严格控制好温度,温度过高要产生大量沉渣,磷化液失去原有平衡。
温度过低,成膜离子浓度总达不到浓度积,不能生成完整磷化膜。
温度过高,磷化液中可溶性磷酸盐的离解度加大,成膜离子浓度大幅度提高,产生不必要的沉渣,白白浪费了磷化液中的有效成分,原有的平衡被迫坏,形成一个新的温度下的平衡,如,低温磷化液在温度失控而升高时,H2PO4→H++PO43- 的离解反应向右进行,从而使磷酸根浓度升高,产生磷酸锌沉淀,使磷化液的酸比自动升高。
影响磷化的工艺因素
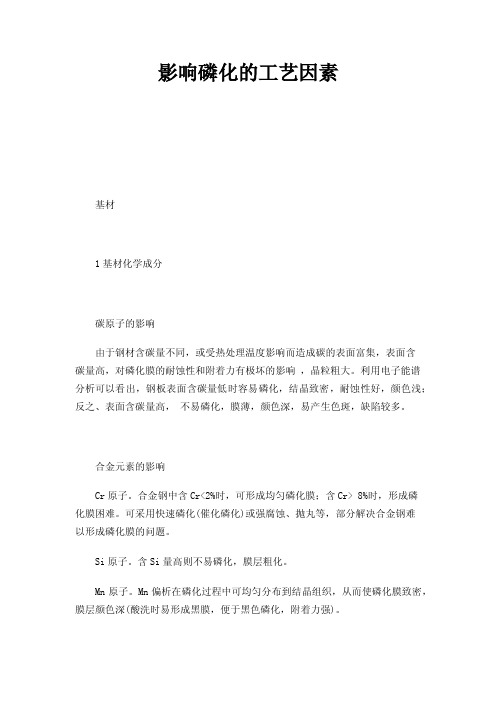
影响磷化的工艺因素基材1基材化学成分碳原子的影响由于钢材含碳量不同,或受热处理温度影响而造成碳的表面富集,表面含碳量高,对磷化膜的耐蚀性和附着力有极坏的影响,晶粒粗大。
利用电子能谱分析可以看出,钢板表面含碳量低时容易磷化,结晶致密,耐蚀性好,颜色浅;反之、表面含碳量高,不易磷化,膜薄,颜色深,易产生色斑,缺陷较多。
合金元素的影响Cr原子。
合金钢中含Cr<2%时,可形成均匀磷化膜;含Cr> 8%时,形成磷化膜困难。
可采用快速磷化(催化磷化)或强腐蚀、抛丸等,部分解决合金钢难以形成磷化膜的问题。
Si原子。
含Si量高则不易磷化,膜层粗化。
Mn原子。
Mn偏析在磷化过程中可均匀分布到结晶组织,从而使磷化膜致密,膜层颜色深(酸洗时易形成黑膜,便于黑色磷化,附着力强)。
Ni原子。
含Ni材质经热处理后,合金组织发生变化,磷化困难,且易出现缺陷。
活性冷轧钢板的活性大小对磷化效果产生不同的影响。
即活性小的冷轧钢板磷化效果好;而活性大的磷化效果差。
生产表明,几种冷轧钢板的活性大小顺序:宝钢板2030>日本板>宝钢1550。
需要钢板生产厂家,降低钢板活性。
表面状态粗糙度在相同磷化条件下,磷化工件表面光洁度越高,磷化过程进行越缓慢,获得的膜层薄而致密,且颜色浅。
反之,表面粗糙,磷化反应快,膜层厚而疏松,均匀性差,颜色深。
可以解释为:光洁度高的表面比粗糙的表面电位正,基体表面在磷化液中不易被酸蚀所致。
所以,光洁度高的工件,磷化前必须进行充分预处理(抛丸或酸蚀)。
锈蚀度。
锈蚀钢板会影响磷化质量(无论采用何种涂锈方法,其磷化膜耐蚀性差)。
况且由于酸洗造成工件表面黑白不均匀,同样影响磷化效果(白色部位较难磷化)。
因此,尽量不要选用锈蚀的钢板加工工件。
特别要防止采用不同厂家、不同批次的钢板来加工同一工件(如汽车车身等)。
否则。
因钢板的差异而造成磷化质量不一样。
同时要注意加工过程中尽量不要破坏钢板防锈膜和加工后长时间存放(采取防锈措施)。
磷化膜影响因素

磷化膜影响因素磷化温度对磷化膜的成膜影响最大,其次是磷化液酸比,磷化时间对磷化膜的成膜影响最小磷化温度提高磷化温度可以加快磷化速度,提高磷化膜的附着力、硬度、耐蚀性和耐热性,而且较高的磷化温度能够促进金属溶解并加速磷酸盐的水解反应,加快成膜速度[3]。
但在高温条件下,Fe2+易被氧化成Fe3+而沉淀下来,使溶液不够稳定。
且在磷化过程中升高温度会使部分磷酸盐水解,所以磷化温度的升高有一定的限度。
磷化膜的生成反应速率可表示为酸比:总酸度和游离酸度溶液的总酸度取决于马日夫盐的含量,提高总酸度能加速磷化反应,使磷化膜薄而细致。
若总酸度过高,则溶液中易出现乳白色沉淀,且磷化后膜层过薄,易起黄锈。
若总酸度过低,则磷化速度缓慢,膜层厚而粗糙,磷化膜的附着力不强,并存在空白。
游离酸度取决于磷酸的含量。
如果游离酸度过高,则工件表面发黑,使磷酸离解受阻,铁在溶液中溶解变慢,不利于磷化膜的形成,从而导致磷化时间延长,磷化膜晶粒粗大多孔且耐蚀性降低。
如果游离酸度过低,则磷化膜变薄,甚至没有磷化膜。
磷化时间对膜层厚度及空隙率有影响图:磷化时间与孔隙率的关系曲线--------------------------------------------------------------1 Fe2+含量控制起决定性作用,过高则磷化膜晶粒粗大多孔、Fe2+含量上升快、磷化时间延长,而偏低会使磷化膜变薄或不能成膜。
严格控制Fe2+的过快增多是磷化溶液维护的关键之一。
控制酸度比及NO-3与H2PO-4的最佳比例、适量添加铬合稳定剂如酒石酸等都能有效控制Fe2+过快升高,且有利于减少磷化沉渣生成、提高磷化膜层质量。
若Fe2+含量超过允许范围,则磷化沉渣会增多,磷化膜质量劣化。
-----------------------------------------------------174 试验证明磷化液中Fe2+的最佳含量为1. 5~3. 0 g/L。
磷化工艺参数的影响
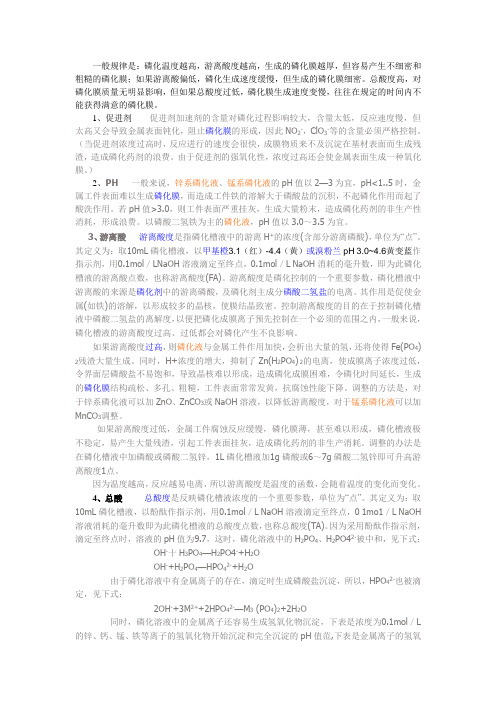
一般规律是:磷化温度越高,游离酸度越高,生成的磷化膜越厚,但容易产生不细密和粗糙的磷化膜;如果游离酸偏低,磷化生成速度缓慢,但生成的磷化膜细密。
总酸度高,对磷化膜质量无明显影响,但如果总酸度过低,磷化膜生成速度变慢,往往在规定的时间内不能获得满意的磷化膜。
1、促进剂促进剂加速剂的含量对磷化过程影响较大,含量太低,反应速度慢,但太高又会导致金属表面钝化,阻止磷化膜的形成,因此NO2-,ClO3-等的含量必须严格控制。
(当促进剂浓度过高时,反应进行的速度会很快,成膜物质来不及沉淀在基材表面而生成残渣,造成磷化药剂的浪费。
由于促进剂的强氧化性,浓度过高还会使金属表面生成一种氧化膜。
)2、PH一般来说,锌系磷化液、锰系磷化液的pH值以2—3为宜,pH<1..5时,金属工件表面难以生成磷化膜,而造成工件铁的溶解大于磷酸盐的沉积,不起磷化作用而起了酸洗作用。
若pH值>3.0,则工件表面严重挂灰,生成大量粉末,造成磷化药剂的非生产性消耗,形成浪费。
以磷酸二氢铁为主的磷化液,pH值以3.0~3.5为宜。
3、游离酸游离酸度是指磷化槽液中的游离H+的浓度(含部分游离磷酸),单位为“点”。
其定义为:取10mL磷化槽液,以甲基橙3.1(红)-4.4(黄)或溴粉兰pH 3.0~4.6黄变蓝作指示剂,用0.1mol/LNaOH溶液滴定至终点,0.1mol/L NaOH消耗的毫升数,即为此磷化槽液的游离酸点数,也称游离酸度(FA)。
游离酸度是磷化控制的一个重要参数,磷化槽液中游离酸的来源是磷化剂中的游离磷酸,及磷化剂主成分磷酸二氢盐的电离。
其作用是促使金属(如铁)的溶解,以形成较多的晶核,使膜结晶致密。
控制游离酸度的目的在于控制磷化槽液中磷酸二氢盐的离解度,以便把磷化成膜离子预先控制在一个必须的范围之内,一般来说,磷化槽液的游离酸度过高、过低都会对磷化产生不良影响。
如果游离酸度过高,则磷化液与金属工件作用加快,会析出大量的氢,还将使得Fe(PO4) 2残渣大量生成。
磷化处理影响因素及常见问题

磷化处理影响因素及常见问题一、磷化工艺参数的影响1、总酸度————总酸度过低、磷化必受影响,因为总酸度是反映磷化液浓度的一项指标。
控制总酸度的意义在于使磷化液中成膜离子浓度保持在必要的范围内。
2、游离酸度————游离酸度过高、过低均会产生不良影响。
过高不能成膜,易出现黄锈;过低磷化液的稳定性受威胁,生成额外的残渣。
游离酸度反映磷化液中游离H+的含量。
控制游离酸度的意义在于控制磷化液中磷酸二氢盐的离解度,把成膜离子浓度控制在一个必须的范围。
磷化液在使用过程中,游离酸度会有缓慢的升高,这时要用碱来中和调整,注意缓慢加入,充分搅拌,否则碱液局部过浓会产生不必要的残渣,出现越加碱,游离酸度越高的现象。
单看游离酸度和总酸度是没有实际意义的,必须一起考虑。
3、酸比————酸比即指总酸度与游离酸度的比值。
一般的说酸比都在5~30的范围内。
酸比较小的配方,游离酸度高,成膜速度慢,磷化时间长,所需温度高。
酸比较大的配方,成膜速度快,磷化时间短,所需温度低。
因此必须控制好酸比。
4、温度————磷化处理温度与酸比一样,也是成膜的关键因素。
不同的配方都有不同的温度范围,实际上,他在控制着磷化液中的成膜离子的浓度。
温度高,磷酸二氢盐的离解度大,成膜离子浓度相应高些,因此可以利用此种关系在降低温度的同时提高酸比,同样可达到成膜,其关系如下:70℃ 60℃ 50℃ 40℃ 30℃ 20℃1/5 1/7 1/10 1/15 1/20 1/25生产单位确定了某一配方后,就应该严格控制好温度,温度过高要产生大量沉渣,磷化液失去原有平衡。
温度过低,成膜离子浓度总达不到浓度积,不能生成完整磷化膜。
温度过高,磷化液中可溶性磷酸盐的离解度加大,成膜离子浓度大幅度提高,产生不必要的沉渣,白白浪费了磷化液中的有效成分,原有的平衡被迫坏,形成一个新的温度下的平衡,如,低温磷化液在温度失控而升高时,H2PO4→H++PO43- 的离解反应向右进行,从而使磷酸根浓度升高,产生磷酸锌沉淀,使磷化液的酸比自动升高。
影响磷化液磷化膜性质的因素
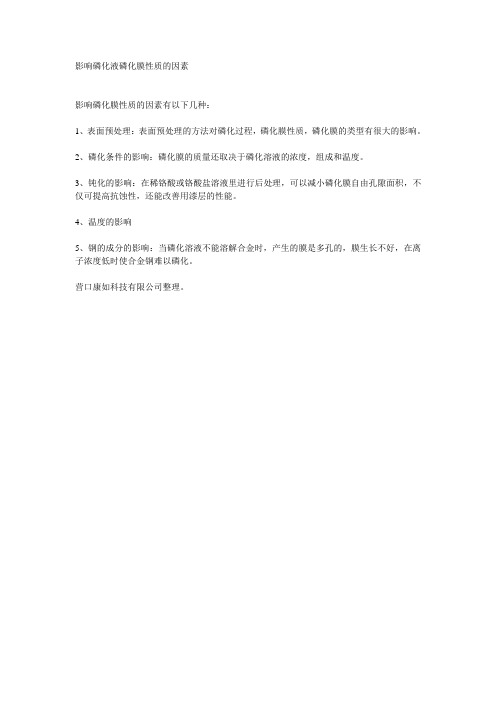
影响磷化液磷化膜性质的因素
影响磷化膜性质的因素有以下几种:
1、表面预处理:表面预处理的方法对磷化过程,磷化膜性质,磷化膜的类型有很大的影响。
2、磷化条件的影响:磷化膜的质量还取决于磷化溶液的浓度,组成和温度。
3、钝化的影响:在稀铬酸或铬酸盐溶液里进行后处理,可以减小磷化膜自由孔隙面积,不仅可提高抗蚀性,还能改善用漆层的性能。
4、温度的影响
5、钢的成分的影响:当磷化溶液不能溶解合金时,产生的膜是多孔的,膜生长不好,在离子浓度低时使合金钢难以磷化。
营口康如科技有限公司整理。
电泳溶解磷化膜

电泳溶解磷化膜
电泳溶解磷化膜,主要涉及磷化膜在电泳过程中的溶解程度。
以下是影响磷化膜在电泳中溶解程度的主要因素:
1.磷化膜的组成:不同的磷化膜对电泳的抗蚀性有显著影响。
磷化膜的磷酸锌、铁、镍、锰、钙等组成成分的含量和比例,会影响其耐碱性,从而影响其电泳过程中的溶解程度。
2.磷化膜的耐碱性:磷化膜的耐碱性与其组成密切相关。
一般来说,当pH值超过一定值时,磷化膜的溶解度会直线上升。
因此,可以通过测定磷化膜在不同pH值下的溶解度,来评估其耐碱性。
3.阳极电泳前的磷化膜:阳极电泳涂装前的磷化膜不仅要外观好,均匀致密,无发蓝或锈痕,而且还需要具备良好的耐碱性。
作为阴极电泳涂装前的磷化膜,不仅外观要求高,而且要求具有良好的耐碱性,作为配套性的评价标准之一。
综上所述,为了在电泳过程中减少磷化膜的溶解,需要选择合适的磷化膜组成和耐碱性好的磷化膜。
此外,还要考虑在电泳过程中的其他因素,如电导率、槽液温度、涂装条件等,这些因素也会对磷化膜的溶解程度产生影响。
磷化参数对磷化成膜影响
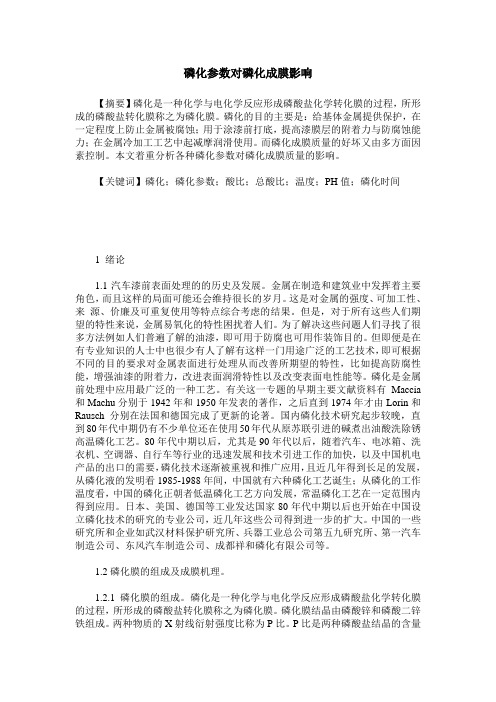
磷化参数对磷化成膜影响【摘要】磷化是一种化学与电化学反应形成磷酸盐化学转化膜的过程,所形成的磷酸盐转化膜称之为磷化膜。
磷化的目的主要是:给基体金属提供保护,在一定程度上防止金属被腐蚀;用于涂漆前打底,提高漆膜层的附着力与防腐蚀能力;在金属冷加工工艺中起减摩润滑使用。
而磷化成膜质量的好坏又由多方面因素控制。
本文着重分析各种磷化参数对磷化成膜质量的影响。
【关键词】磷化;磷化参数;酸比;总酸比;温度;PH值;磷化时间1 绪论1.1汽车漆前表面处理的的历史及发展。
金属在制造和建筑业中发挥着主要角色,而且这样的局面可能还会维持很长的岁月。
这是对金属的强度、可加工性、来源、价廉及可重复使用等特点综合考虑的结果。
但是,对于所有这些人们期望的特性来说,金属易氧化的特性困扰着人们。
为了解决这些问题人们寻找了很多方法例如人们普遍了解的油漆,即可用于防腐也可用作装饰目的。
但即便是在有专业知识的人士中也很少有人了解有这样一门用途广泛的工艺技术,即可根据不同的目的要求对金属表面进行处理从而改善所期望的特性,比如提高防腐性能,增强油漆的附着力,改进表面润滑特性以及改变表面电性能等。
磷化是金属前处理中应用最广泛的一种工艺。
有关这一专题的早期主要文献资料有Maccia 和Machu分别于1942年和1950年发表的著作,之后直到1974年才由Lorin和Rausch分别在法国和德国完成了更新的论著。
国内磷化技术研究起步较晚,直到80年代中期仍有不少单位还在使用50年代从原苏联引进的碱煮出油酸洗除锈高温磷化工艺。
80年代中期以后,尤其是90年代以后,随着汽车、电冰箱、洗衣机、空调器、自行车等行业的迅速发展和技术引进工作的加快,以及中国机电产品的出口的需要,磷化技术逐渐被重视和推广应用,且近几年得到长足的发展,从磷化液的发明看1985-1988年间,中国就有六种磷化工艺诞生;从磷化的工作温度看,中国的磷化正朝者低温磷化工艺方向发展,常温磷化工艺在一定范围内得到应用。
磷化处理工艺
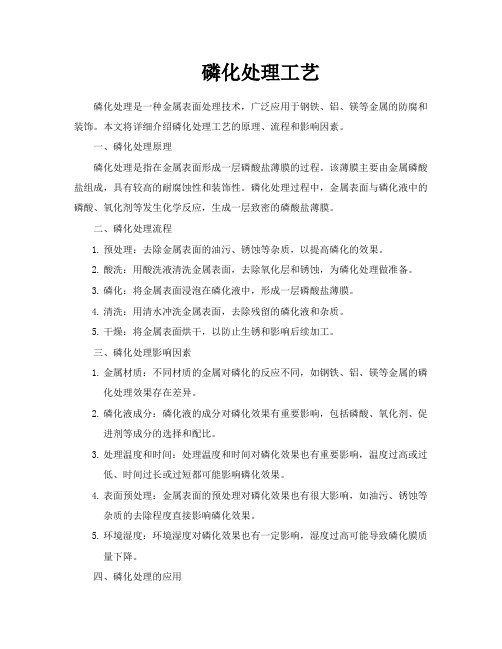
磷化处理工艺磷化处理是一种金属表面处理技术,广泛应用于钢铁、铝、镁等金属的防腐和装饰。
本文将详细介绍磷化处理工艺的原理、流程和影响因素。
一、磷化处理原理磷化处理是指在金属表面形成一层磷酸盐薄膜的过程。
该薄膜主要由金属磷酸盐组成,具有较高的耐腐蚀性和装饰性。
磷化处理过程中,金属表面与磷化液中的磷酸、氧化剂等发生化学反应,生成一层致密的磷酸盐薄膜。
二、磷化处理流程1.预处理:去除金属表面的油污、锈蚀等杂质,以提高磷化的效果。
2.酸洗:用酸洗液清洗金属表面,去除氧化层和锈蚀,为磷化处理做准备。
3.磷化:将金属表面浸泡在磷化液中,形成一层磷酸盐薄膜。
4.清洗:用清水冲洗金属表面,去除残留的磷化液和杂质。
5.干燥:将金属表面烘干,以防止生锈和影响后续加工。
三、磷化处理影响因素1.金属材质:不同材质的金属对磷化的反应不同,如钢铁、铝、镁等金属的磷化处理效果存在差异。
2.磷化液成分:磷化液的成分对磷化效果有重要影响,包括磷酸、氧化剂、促进剂等成分的选择和配比。
3.处理温度和时间:处理温度和时间对磷化效果也有重要影响,温度过高或过低、时间过长或过短都可能影响磷化效果。
4.表面预处理:金属表面的预处理对磷化效果也有很大影响,如油污、锈蚀等杂质的去除程度直接影响磷化效果。
5.环境湿度:环境湿度对磷化效果也有一定影响,湿度过高可能导致磷化膜质量下降。
四、磷化处理的应用1.防腐:磷化膜具有较高的耐腐蚀性,可用于钢铁、铝、镁等金属的防腐处理。
例如,在建筑、船舶、汽车等领域,磷化处理被广泛应用于金属结构的防腐保护。
2.装饰:磷化膜具有较好的装饰性,可用于金属表面的美化处理。
例如,在电子产品、家具等领域,磷化处理被广泛应用于产品的外观装饰。
3.耐磨:磷化膜还具有较好的耐磨性,可用于提高金属表面的耐磨性能。
例如,在机械零件、工具等领域,磷化处理被广泛应用于提高产品的耐磨性能。
4.粘合:磷化膜还可以作为粘合剂使用,将不同金属材料粘合在一起。
磷化膜的缺陷原因及改进措施

磷化膜失光,发暗、疤痕、缩孔
某些金属盐类污染磷化膜
磷化后避免用NaNo2进行防锈,保持磷化膜的清洁。
磷化膜的缺陷原因及改进措施
磷化后及时彻底清洗,降低槽液温度,严格热水清洗工艺、烘干工艺。
表面浮灰多
游离酸度低,酸度比例失调,Fe2+偏了,细化剂偏低,难溶性盐类沉积物太多。
调整游离酸度及游离酸和总酸之比,控制Fe2+或更换槽液,补充Ca2+等细化剂,过滤槽液。
磷化膜发粘
Mn、Fe等硝酸盐在预烘炉内受溶剂蒸汔烘熏,生成锰铁为主的膜。
缺陷
原因
措施
膜层发花
除油不净,酸洗不良,金属表面不均匀
彻底除油,严格酸洗时间,改善磷化前的表面状态。
膜层发黑
游离酸度过高,Fe2+过多。磷化前表面状态不好。
降低游离酸度,调整磷化液,降低Fe2+量。改善表面状态。
膜层不均匀,有花脸现象
槽液温度太低,Zn2+、H2Po4—含量偏低游离酸度高,金属表面状态不好。
补加细化剂如Ca2+,严格酸洗工艺,补充N03—调整游离酸度和总酸比例。
白色沉淀
酸度高,磷化槽液温度高,磷化后清洗不好。
降低游离酸度,降低槽液温度,磷化后彻底清洗。
局部有光亮疤迹或锈蚀
氢气排除不好
调整工件在磷化液中的位置,使氢气便于排除。
水流痕状腐蚀
磷化后不及时清洗,磷化槽液温度高热水清洗工艺不当,烘干工艺不当。
提高槽液温度,补充Zn2+、H2Po4—降低游离酸度,改善表面状态。
膜层粗糙,膜薄或无磷化膜
游离酸度高,总酸度低,磷化温度低。
磷化工艺中的各种影响因素

磷化工艺的影响因素磷化膜的质量直接影响与有机膜、涂层的附着力和防护性,影响磷化工件的耐磨、耐微动力磨损和抗擦伤性,以及磷化膜能否成为润滑剂的载体。
磷化膜质量的高低,取决于磷化所采用的工艺是否恰当,磷化过程是否符合工艺要求,因此要十分注意影响磷化工艺的因素。
影响磷化工艺的主要因素有:材质及表面状态、磷化前处理、磷化后处理、磷化液的化学成分等。
下面试就影响磷化工艺的主要因素作一分析。
(一)材质及表面状态。
同是钢铁工件,受含有的其它元素不同,表面晶格是否遭受腐蚀等因素的影响,形成的磷化膜颜色、均匀性、抗腐蚀能力不一样。
低碳钢容易磷化,膜的结晶致密,颜色较浅;中、高碳钢和低合金钢比较容易磷化,结晶有变粗的倾向,磷化膜颜色深;含有较多铬、钼、钨、钒、硅等元素的钢材不容易磷化。
磷化膜随钢材中碳化物含量和分布的不同存在差异,因此,不同钢材应选用不同的磷化工艺和相应的磷化产品。
(二)前处理。
磷化前的表面处理程度是影响磷化质量的重要因素。
因此,要求除净所有的锈迹、油污。
具体要求是,脱脂后的工件,不应有油脂、乳浊液等污物,其表面应能被水完全湿润;酸洗后的工件,不应有目视可见的氧化物、锈及过腐蚀现象.为防止过腐蚀,减轻氢脆,应在酸洗液中加入缓蚀剂.为防止酸雾,酸洗液中可加入酸雾抑制剂;喷抛丸清理后的工件,不应有漏喷、磨料粘附、锈蚀及油污,其表面应露出金属本色.从除油后到磷化前这一过程,工件不允许直接接触手或有油的污物。
经强酸、强碱处理后的钢铁件,一般会增大结晶粒度,增加膜的重量。
水洗是将工件表面从前道处理工序中带出来的残留化学成分除去,防止对下道处理工序的影响。
除油后的不良水洗会使油污再沉积,更多地消耗酸,造成不均匀的酸洗,形成不均匀的磷化膜;酸洗后的不良水洗,导致磷化槽液游离酸度升高,形成稀疏、不均匀的磷化膜,甚至磷化后的工件生锈。
要保证水洗质量,应保持清水的特定pH值或更有效的导电率,延长清洗时间和次数。
(三)后处理。
磷化膜影响因素
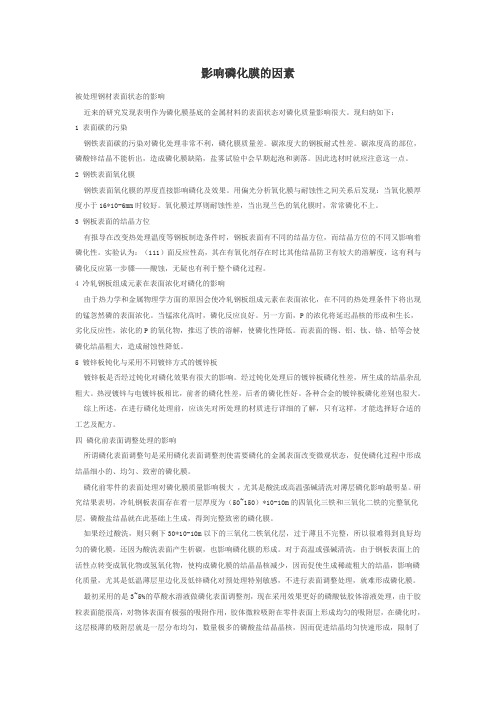
影响磷化膜的因素被处理钢材表面状态的影响近来的研究发现表明作为磷化膜基底的金属材料的表面状态对磷化质量影响很大。
现归纳如下:1 表面碳的污染钢铁表面碳的污染对磷化处理非常不利,磷化膜质量差。
碳浓度大的钢板耐式性差。
碳浓度高的部位,磷酸锌结晶不能析出,造成磷化膜缺陷,盐雾试验中会早期起泡和剥落。
因此选材时就应注意这一点。
2 钢铁表面氧化膜钢铁表面氧化膜的厚度直接影响磷化及效果。
用偏光分析氧化膜与耐蚀性之间关系后发现:当氧化膜厚度小于16*10-6mm时较好。
氧化膜过厚则耐蚀性差,当出现兰色的氧化膜时,常常磷化不上。
3 钢板表面的结晶方位有报导在改变热处理温度等钢板制造条件时,钢板表面有不同的结晶方位,而结晶方位的不同又影响着磷化性。
实验认为:(111)面反应性高,其在有氧化剂存在时比其他结晶防卫有较大的溶解度,这有利与磷化反应第一步骤——酸蚀,无疑也有利于整个磷化过程。
4 冷轧钢板组成元素在表面浓化对磷化的影响由于热力学和金属物理学方面的原因会使冷轧钢板组成元素在表面浓化,在不同的热处理条件下将出现的锰忽然磷的表面浓化。
当锰浓化高时,磷化反应良好。
另一方面,P的浓化将延迟晶核的形成和生长,劣化反应性,浓化的P的氧化物,推迟了铁的溶解,使磷化性降低。
而表面的锡、铝、钛、铬、铅等会使磷化结晶粗大,造成耐蚀性降低。
5 镀锌板钝化与采用不同镀锌方式的镀锌板镀锌板是否经过钝化对磷化效果有很大的影响。
经过钝化处理后的镀锌板磷化性差,所生成的结晶杂乱粗大。
热浸镀锌与电镀锌板相比,前者的磷化性差,后者的磷化性好。
各种合金的镀锌板磷化差别也很大。
综上所述,在进行磷化处理前,应该先对所处理的材质进行详细的了解,只有这样,才能选择好合适的工艺及配方。
四磷化前表面调整处理的影响所谓磷化表面调整句是采用磷化表面调整剂使需要磷化的金属表面改变微观状态,促使磷化过程中形成结晶细小的、均匀、致密的磷化膜。
磷化前零件的表面处理对磷化膜质量影响极大,尤其是酸洗或高温强碱清洗对薄层磷化影响最明显。
磷化膜影响因素(内容清晰)
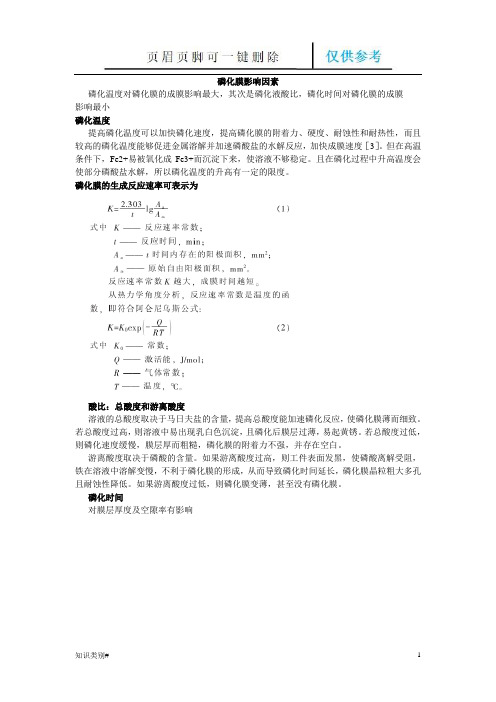
磷化膜影响因素磷化温度对磷化膜的成膜影响最大,其次是磷化液酸比,磷化时间对磷化膜的成膜影响最小磷化温度提高磷化温度可以加快磷化速度,提高磷化膜的附着力、硬度、耐蚀性和耐热性,而且较高的磷化温度能够促进金属溶解并加速磷酸盐的水解反应,加快成膜速度[3]。
但在高温条件下,Fe2+易被氧化成Fe3+而沉淀下来,使溶液不够稳定。
且在磷化过程中升高温度会使部分磷酸盐水解,所以磷化温度的升高有一定的限度。
磷化膜的生成反应速率可表示为酸比:总酸度和游离酸度溶液的总酸度取决于马日夫盐的含量,提高总酸度能加速磷化反应,使磷化膜薄而细致。
若总酸度过高,则溶液中易出现乳白色沉淀,且磷化后膜层过薄,易起黄锈。
若总酸度过低,则磷化速度缓慢,膜层厚而粗糙,磷化膜的附着力不强,并存在空白。
游离酸度取决于磷酸的含量。
如果游离酸度过高,则工件表面发黑,使磷酸离解受阻,铁在溶液中溶解变慢,不利于磷化膜的形成,从而导致磷化时间延长,磷化膜晶粒粗大多孔且耐蚀性降低。
如果游离酸度过低,则磷化膜变薄,甚至没有磷化膜。
磷化时间对膜层厚度及空隙率有影响图:磷化时间与孔隙率的关系曲线--------------------------------------------------------------1 Fe2+含量控制起决定性作用,过高则磷化膜晶粒粗大多孔、Fe2+含量上升快、磷化时间延长,而偏低会使磷化膜变薄或不能成膜。
严格控制Fe2+的过快增多是磷化溶液维护的关键之一。
控制酸度比及NO-3与H2PO-4的最佳比例、适量添加铬合稳定剂如酒石酸等都能有效控制Fe2+过快升高,且有利于减少磷化沉渣生成、提高磷化膜层质量。
若Fe2+含量超过允许范围,则磷化沉渣会增多,磷化膜质量劣化。
-----------------------------------------------------174 试验证明磷化液中Fe2+的最佳含量为1. 5~3. 0 g/L。
影响磷化膜质量的因素

影响磷化膜质量的因素1、前言现代工业的迅速发展,市场对涂装要求急剧增加,涂装行业将会得到更快的发展,而涂装质量的好坏在一定程度取决于涂装前处理技术的高低,而磷化又是涂装前处理的关键,磷化膜的性能好坏直接关系到涂装质量的优劣,因此我们需要详细地了解影响磷化膜质量的因素。
2、影响磷化膜质量的因素2.1. 总酸度(TA)TA是反映磷化槽浓度的一项指标,是指槽液中配合酸(HSO42-)和FA浓度的总和。
控制TA的目的在于保持磷化槽液中成膜离子的浓度在规定的工艺范围内。
TA过高,磷化膜生成困难,磷化膜结晶粗燥,耐腐蚀性差。
2.2 游离酸度(FA)FA是指槽液中游离酸度H+浓度。
FA促使工件溶解产生晶核,使生成磷化膜容易。
控制FA的目的在于控制槽液中磷酸二氢盐的离解度,把成膜离子浓度控制在一个必须范围内。
FA过高,反映加快。
工件与槽液界面的离子浓度被破坏,届面PH值过低,造成成膜困难,成膜时间延长,结晶粗大多孔。
耐腐蚀性低。
FA过低,工件腐蚀缓慢,界面PH值升高,磷化膜薄甚至难以形成,膜成表面易产生浮粉(Zn(PO4) 2沉淀),磷化液易产生异常沉淀,导致Zn2+含量急剧降低。
2.3. 磷化温度磷化温度是形成磷化膜的一个关键因素,适当的提高温度不仅可以激活能量低的点形成“活化中心”使晶核数目增多,结晶速度提高,成膜速度加快,同时可以在枝晶上产生新的结晶,结晶密度提高,形成完整结晶的磷化膜,但温度过高,反映速度太快,膜层晶核粗大,孔隙较大,槽液稳定性差,易浑浊,形成含渣的超重灰磷化膜,耐腐蚀性低。
当温度过低,由于磷化是吸热反应,当所需的热量得不到足够补偿时,成膜速度缓慢,甚至磷化反映难以进行,在家和摩配行业磷化中,多以低温和常温磷化磷化为主。
由于温度低,反映相应减慢,因此必须通过其他途径来调节槽液的酸比,促进剂含量,浓度来补偿温度低而对磷化速度的影响,为满足批量生产,加你最好采用低温磷化为宜。
2.4. 磷化时间不同的磷化液,具有不同的磷化时间要求,随着磷化时间的不同,所获得磷化膜的外观,厚度,耐腐蚀性也不同,磷化时间与膜重不成线形关系,根据不同的板材来确定磷化时间,以获得理想的确凿磷化膜。
钢铁零件磷化缺陷原因分析及解决方案

钢铁零件磷化缺陷原因分析及解决方案
一、磷化缺陷的原因分析
钢铁零件的磷化缺陷主要有以下几个方面的原因:
1. 磷化液配方不合理:磷化液中的成分、浓度、比例等因素会直接影响磷化膜的质量。
如果磷化液配方不合理,可能会导致磷化膜质量不稳定,出现缺陷。
2. 表面清洁度不够:钢铁零件在磷化前必须保证表面的清洁度,否则会影响磷化膜的质量。
如果表面含有油脂、灰尘等杂质,会导致磷化液不能充分与钢铁表面反应,从而形成不完整的磷化膜。
3. 钢铁材质不合适:不同的钢铁材质适合的磷化工艺也不同。
如果选择了不适合的磷化工艺,可能会导致磷化膜质量不稳定,出现缺陷。
4. 磷化时间、温度不合理:磷化时间和温度是影响磷化膜质量的重要因素。
如果磷化时间过长或温度过高,可能会导致磷化膜过厚、颗粒过粗,从而形成缺陷。
5. 磷化设备或工艺的缺陷:磷化设备或工艺的缺陷,如液槽漏液、温度控制不准确等,可能会导致磷化膜质量不稳定,出现缺陷。
钢铁零件磷化缺陷的原因有很多,主要包括磷化液配方不合理、表面清洁度不够、钢铁材质不合适、磷化时间、温度不合理以及磷化设备或工艺的缺陷等。
针对这些原因,可以采取优化磷化液配方、提高表面清洁度、选择合适的钢铁材质、合理控制磷化时间、温度以及改进磷化设备和工艺等解决方案,以改善和优化钢铁零件的磷化质量。
影响磷化的因素

影响因素1、温度温度愈高,磷化层愈厚,结晶愈粗大。
温度愈低,磷化层愈薄,结晶愈细。
但温度不宜过高,否则Fe2+ 易被氧化成Fe3+,加大沉淀物量,溶液不稳定。
2、游离酸度游离酸度指游离的磷酸。
其作用是促使铁的溶解,已形成较多的晶核,使膜结晶致密。
游离酸度过高,则与铁作用加快,会大量析出氢,令界面层磷酸盐不易饱和,导致晶核形成困难,膜层结构疏松,多孔,耐蚀性下降,令磷化时间延长。
游离酸度过低,磷化膜变薄,甚至无膜。
3、总酸度总酸度指磷酸盐、硝酸盐和酸的总和。
总酸度一般以控制在规定范围上限为好,有利于加速磷化反应,使膜层晶粒细,磷化过程中,总酸度不断下降,反映缓慢。
总酸度过高,膜层变薄,可加水稀释。
总酸度过低,膜层疏松粗糙。
4、PH值锰系磷化液一般控制在2-3之间,当PH﹥3时,共件表面易生成粉末。
当PH‹1.5时难以成膜。
铁系一般控制在3-5.5之间。
5、溶液中离子浓度①溶液中Fe2+极易氧化成Fe3+,导致不易成膜。
但溶液中Fe2+浓度不能过高,否则,形成的膜晶粒粗大,膜表面有白色浮灰,耐蚀性及耐热性下降。
②Zn2+的影响,当Zn2+浓度过高,磷化膜晶粒粗大,脆性增大,表面呈白色浮灰;当Zn2+浓度过低,膜层疏松变暗。
表4 锌系、锰系、锌钙系磷化的常见故障常见故障产生的主要原因解决方法工件表面均匀泛黄,但均匀疏松的磷化膜1.总酸度低、酸比低2.促进剂浓度低3.磷化温度低、时间短1.补加磷化液和碱2.补加促进剂3.提高温度4.延长时间磷化成膜速度慢,但延长磷化时间仍可形成均匀完整膜1.表面调整能力不强2.促进剂浓度不够3.酸比低4.磷化温度低1.改进表调或换槽2.补加促进剂3.补加碱4.提高温度磷化膜局部块状条状挂灰,挂灰处磷化膜不均匀,有时彩色膜1.工件在进入磷化槽前已经形成二次黄绿锈2.表面调整能力差3.磷化液中杂质多1.加快工序间周转或实施水膜保护2.改进表调3.更换槽液磷化膜均匀出现彩色膜或均匀挂白1.促进剂含量过高2.表调失去作用或是表调后水洗过度3.磷化液杂质过多、老化1.让促进剂自然降低2.加强表调3.换槽工件表面覆盖一层结晶体1.游离酸度过低2.温度过高1.加一些磷酸2.降低温度槽液沉渣过多1.促进剂浓度过高2.游离酸度过高3.工件磷化时间过长4.中和过度形成结晶沉淀1.让其自然降低2.补加碱3.缩短时间4.补加磷酸建立涂装前处理生产线,先要完成工艺设计,然后才能进行非标设备的设计、制造和安装。
- 1、下载文档前请自行甄别文档内容的完整性,平台不提供额外的编辑、内容补充、找答案等附加服务。
- 2、"仅部分预览"的文档,不可在线预览部分如存在完整性等问题,可反馈申请退款(可完整预览的文档不适用该条件!)。
- 3、如文档侵犯您的权益,请联系客服反馈,我们会尽快为您处理(人工客服工作时间:9:00-18:30)。
磷化膜影响因素磷化温度对磷化膜的成膜影响最大,其次是磷化液酸比,磷化时间对磷化膜的成膜影响最小磷化温度提高磷化温度可以加快磷化速度,提高磷化膜的附着力、硬度、耐蚀性和耐热性,而且较高的磷化温度能够促进金属溶解并加速磷酸盐的水解反应,加快成膜速度[3 ]。
但在高温条件下,Fe2+易被氧化成Fe3+而沉淀下来,使溶液不够稳定。
且在磷化过程中升高温度会使部分磷酸盐水解,所以磷化温度的升高有一定的限度。
磷化膜的生成反应速率可表示为心?罗址彳亠(1)成中K——反网連申第散:1 --- 丈也时f IJ J . min :X.——E时同内存在的阳械血根.mm'A* ------ 厭始自由阳极厨枳.mm\反应速率常数K越丸.虜膜时间越短口賦热力学兌度分祈”反应建率常数足昭度的函数*此符合阿仑尼%斯处成:K=A.?r b Ap IF贞:中心——常救;0------- 激濡能,J/ini)l tR—气休常数孑酸比:总酸度和游离酸度溶液的总酸度取决于马日夫盐的含量,提高总酸度能加速磷化反应,使磷化膜薄而细致。
若总酸度过高,则溶液中易出现乳白色沉淀,且磷化后膜层过薄,易起黄锈。
若总酸度过低, 则磷化速度缓慢,膜层厚而粗糙,磷化膜的附着力不强,并存在空白。
游离酸度取决于磷酸的含量。
如果游离酸度过高,则工件表面发黑,使磷酸离解受阻,铁在溶液中溶解变慢,不利于磷化膜的形成,从而导致磷化时间延长,磷化膜晶粒粗大多孔且耐蚀性降低。
如果游离酸度过低,则磷化膜变薄,甚至没有磷化膜。
磷化时间对膜层厚度及空隙率有影响图:磷化时间与孔隙率的关系曲线------------------------------------------- 1Fe2+含量控制起决定性作用,过高则磷化膜晶粒粗大多孔、Fe2+含量上升快、磷化时间延长,而偏低会使磷化膜变薄或不能成膜。
严格控制Fe2+的过快增多是磷化溶液维护的关键之一。
控制酸度比及NO-3 与H2PO-4 的最佳比例、适量添加铬合稳定剂如酒石酸等都能有效控制Fe2+过快升高,且有利于减少磷化沉渣生成、提高磷化膜层质量。
若Fe2+含量超过允许范围,则磷化沉渣会增多,磷化膜质量劣化。
----------------------------------- 174试验证明磷化液中Fe2+的最佳含量为 1.5~3. 0 g/L。
--------------------------- 176磷化工艺发展现状磷化膜用作钢铁的防腐蚀保护膜,最早的可靠记载是英国CharlesRoss于1869年获得的专利现在磷化处理技术已广泛应用于汽车、船舶、军工、电器、机械等领域,其主要用途是防锈、耐摩减磨、润滑、涂漆底层等,从而较好解决了钢铁在环境中的腐蚀问题。
随着磷化技术的进步,现代磷化正朝着低温节能、工艺简便、投资耗料少、无毒无污染的方向发展,如磷化温度由原来的高温(>85e)逐步降低到中温乃至室温(<30e),磷化处理时间由最初的几个小时缩短到目前的几分钟。
磷化处理方式也从开始的纯浸渍法发展到喷淋法、馄除法以及浸喷馄混和法的自动化生产,磷化体系则由当初的单元体系(只有铁一种金属离子)发展到今天的多元体系(同时含有铁、锌、锰、镍、钙等多种金属离子)磷化添加剂从无到有,大大改善了磷化膜的质量,提高成膜速度,已成为磷化液中不可缺少的成分"时至今日,新技术新工艺逐渐取代了旧技术旧工艺,还出现了常温“四合一” 磷化处理液,多功能磷化处理液能减少处理工序,降低劳动强度,但在膜的致密性和防腐性方面需进一步的改善和提高。
黑色金属的黑化和磷化相结合,在金属表面生成起到修饰、防护的作用共生膜,有着广阔的应用和推广价值。
磷化膜能够提高漆膜或其他有机涂料与金属的结合力及防护性,其主要原因,大体上可归纳如下:(1)磷化膜能够把金属基材表面的活性转化到最小的程度,把以后的腐蚀反应降到最低限度;(2)磷化膜能给金属提供一个“粗糙面” ,给油漆或其它有机膜提供一个很好的咬合力,增强其附着力;(3)由于磷化过程除去了工件表明的各种无机污染物,如金属屑,轻微氧化物以及其它污物等,减少了影响附着力的内在不利因素;(4) 磷化膜作为一种屏障,终止了有机层与基体金属之间的化学反应,如皂化等;⑸磷化膜为金属表面各点提供一个同等的电化学电位,抑制了任何局部的阴极和阳极的“点腐蚀”,从而消除了电化学腐蚀区,减少了电化学腐蚀;(6)由于磷化膜能够提供一个同等的电化学电位,因此也抑制了漆膜或其它有机膜下面的腐蚀扩张,这应归于磷化膜的绝缘性•当未经磷化处理工件表面的金属或非金属涂层破损以后,基体金属裸露出来,在这些部位形成了微电池"由于在膜下形成的电解质及金属的导电性!膜与金属之间的毛细现象,金属开始腐蚀并向各方向扩张,结果在膜下边形成腐蚀气泡”如果金属是经过磷化处理的,由于其它部位的金属被牢固地吸附在基体上的磷化膜所绝缘,因此其腐蚀过程仅限于损坏面,并且防止了电解质水平方向扩展,膜下的腐蚀受到了限制。
总之,和其它各种转化膜相比,磷化膜作为保护膜是最有利的,在某种情况下,其防护性大于金属镀层。
2随着社会对健康及环保要求的不断提高,从环境、能源等各个方面考虑,对磷化技术提出了更高的要求,其发展趋势如下:(1) 绿色磷化液:即无毒低能耗清洁的磷化液,如无亚硝酸盐磷化、无镍磷化、无铬磷化、稀土磷化。
(2) ---------------------------------------------------------------------------------------------------------------------- 多功能磷化液:“三合一”、“四合一”磷化液,从而减少了磷化工序。
----------------------- 22(3) 由中温磷化液转向常温(低温)磷化液。
磷化成膜的步骤:第亠步,廊的浸蚀与促进剂氧化过稈[门酸的漫惊使革体系令届表面/T锻度降低;Fe-2e f Fe:*2才 + 20->2[11]»对(L1> (ii)促遊剂加速’Fe J* + [O]-^Fe u+ (R] (1,2)式中[O]为促进剂(氧化剂),[R]为还原产物,由于促进剂氧化掉第一步反应所产生的氢原子,加快了反应(1.1)的速度,进一步导致金属表面H+浓度急剧下降•同时也将溶液中的Fe+2 氧化成为Fe3+.。
第一步.除酸根逐步离解过程磷检根的多级+H+ <^HPO4^+2H* ^PO;'^3H+ (13) 由丁金属表面的ir浓度质剧下降*导致磷酸抿各錢离解平向右移动,廉终为pgx 第三步.瞋酸款樹优成狠过桎请槪盐沉提结晶感力确化臥:当金属衷面离解出的PO)占君液中(金關界面)的备JK离子〔如Mn Jt, 氏r达到瘠ift轉度税常敷心就發形成辑醸盐沉息Zn2* + F0 +PO广 + H£ f ZnjFE(P6h i G-4)3卅+ 2PO 广+4H3O -血㈣h 的01噩醱盐沉讹与水分子一起形成磷优晶核,晶核雉续怏大成为磷化晶粒*无數个聶粒黑住堆集应碑第匹步.磷酸盐沉淀终止反应过挣磷襯盐沉淀的副反应将形成磷化区旣F0 + PO广=FePO,用于钢铁工件防腐蚀磷化层,可采用zn系、Mn系、Zn-Mn系磷化膜,膜重必须大于10g/m2,磷化膜须涂防锈油!防锈之类防锈剂。
磷化动力学中人们常常希望把磷酸盐的温度尽量提高,但是由于溶液中的某些介质在高温时可能引起分解和变质,因而升高操作温度液有一定的限度”当然,操作温度不能随便降低,因温度降低时磷酸盐溶液将接近于钝化状态"同时在低温下,为了得到所要求的膜重,就需要较长的浸渍时间(反应时间)。
金属的组成,对速度常数k亦有很大影响•但是,各种不同浓度的元素对磷酸盐化学成膜的速度影响究竟有多大,因在大多数情况下伴随有多种催化作用,故不能一概而论。
另外,金属材料表面状态也与速度常数k有密切的关系”例如采用冷轧钢板时,其表面较平滑,粗糙度约为1~3.5林"金属表面愈粗糙,则其表面形成膜层的膜重亦愈大"因此,采用磷酸盐成膜时,达到最大膜重所需的时间也愈短”显微镜粗糙度的提高,可导致晶核的增加,晶核数量越多,速度常数就越大"一般认为,晶核数量与粗糙度呈正比。
处理液的性质是影响速度常数的重要因素•处理液性质包括:()1处理液浓度:(2)相界面处的扩散;(3)溶液成分进入晶格时结晶的排列情况:(4)催化作用和抑制作用.将上述性质与如下观察相结合进行分析时发现,两者是相互关联的”由此可知,磷酸盐化学成膜的过程如下。
(1)在磷酸盐成膜反应区域内,反应物自各相(液相一金属)出发相互接近此接近速度取决于扩散的快慢。
(2)通过反应对金属进行溶解"其速度决定于浓度。
在反应区域内生成过饱和溶液。
(3)由于扩散作用使反应生成物分离和排出,以及使反应生成物或溶液成分进入晶格。
成膜化学反应十分迅速,这是因为当用磷酸盐进行化学处理时,无论处理何种状态,磷化成膜的反应速度仅仅受扩散速度的支配。
磷酸盐成膜时在期相界面,即溶液一金属表面上扩散可根据Fick定律加以说明。
由上式(3.9)得知,离子浓度差(CA-CB)及结合层厚度是扩散速度大小的决定因素。
但在磷酸盐成膜反应是,浓2度差(CA-CB)大体上是一定的,表面积(0)也没有变化,而扩散常数(D),只受特定的溶液添加物的影响。
因此,唯一的变数是结合层厚度(S)。
结合层愈薄,扩散愈快而反应速度越大。
2。