钢件热处理变形的原因总结
cr12mov热处理后加工变形

cr12mov热处理后加工变形
摘要:
1.cr12mov 材料特性
2.cr12mov 热处理过程
3.cr12mov 加工变形原因
4.减少cr12mov 加工变形的措施
正文:
CR12MOV 是一种高强度、高硬度、高韧性的冷作模具钢材料,由于其优异的性能,被广泛应用于各种冷作模具的制造。
然而,在经过热处理后,
CR12MOV 材料在加工过程中容易产生变形,这给模具的制造和使用带来了不少困扰。
下面我们来分析一下CR12MOV 热处理后加工变形的原因及应对措施。
首先,CR12MOV 材料的特性决定了它在热处理过程中容易产生变形。
CR12MOV 钢属于高碳合金钢,碳含量较高,使得钢的硬度和强度得到提高,但塑性和韧性降低。
在热处理过程中,碳原子和合金元素会发生扩散,从而导致晶粒长大和碳化物析出,使钢的硬度和强度进一步提高。
但同时,塑性和韧性会继续降低,这使得CR12MOV 在热处理后加工过程中更容易产生变形。
其次,CR12MOV 热处理过程中,由于温度、保温时间、冷却速度等因素的控制不当,可能导致热处理组织不均匀,从而使钢的性能发生不均匀变化,进一步加大加工变形的可能性。
针对CR12MOV 热处理后加工变形的问题,可以采取以下措施来减少变
形:
1.合理控制热处理工艺参数,如加热速度、保温时间、冷却速度等,以保证热处理组织均匀;
2.在加工过程中,采用适当的切削参数和刀具材料,以降低切削力和热量,减少加工过程中的变形;
3.对模具结构进行优化,尽量避免应力集中,以降低加工变形的风险;
4.在加工过程中,对模具进行适当的时效处理,以消除内应力,降低变形。
热处理变形的原因

热处理变形的原因在实际生产中,热处理变形给后续工序,特别是机械加工增加了很多困难,影响了生产效率,因变形过大而导致报废,增加了成本。
变形是热处理比较难以解决的问题,要完全不变形是不可能的,一般是把变形量控制在一定范围内。
一、热处理变形产生的原因钢在热处理的加热、冷却过程中可能会产生变形,甚至开裂,其原因是由于淬火应力的存在。
淬火应力分为热应力和组织应力两种。
由于热应力和组织应力作用,使热处理后零件产生不同残留应力,可能引起变形。
当应力大于材料的屈服强度时变形就会产生,因此,淬火变形还与钢的屈服强度有关,材料塑性变形抗力越大,其变形程度越小。
1.热应力在加热和冷却时由于零件表里有温差存在造成热胀冷缩的不一致而产生热应力。
零件由高温冷却时表面散热快,温度低于心部,因此表面比心部有更大的体积收缩倾向,但受心部阻碍而使表面受拉应力,而心部则受压应力。
表里温差增大应力也增大。
2.组织应力组织应力是因为奥氏体与其转变产物的比容不同,零件的表面和心部或零件各部分之间的组织转变时间不同而产生的。
由于奥氏体比容最小,淬火冷却时必然发生体积增加。
淬火时表面先开始马氏体转变,体积增大,心部仍为奥氏体体积不变。
由于心部阻碍表面体积增大,表面产生压应力,心部产生拉应力。
二、减少和控制热处理变形的方法1.合理选材和提高硬度要求对于形状复杂,截面尺寸相差较大而又要求变形较小的零件,应选择淬透性较好的材料,以便使用较缓和的淬火冷却介质淬火。
对于薄板状精密零件,应选用双向轧制板材,使零件纤维方向对称。
对零件的硬度要求,在满足使用要求前提下,尽量选择下限硬度。
2.正确设计零件零件外形应尽量简单、均匀、结构对称,以免因冷却不均匀,使变形开裂倾向增大。
尽量避免截面尺寸突然变化,减少沟槽和薄边,不要有尖锐棱角。
避免较深的不通孔。
长形零件避免截面呈横梯形。
3.合理安排生产路线,协调冷热加工与热处理的关系对于形状复杂、精度要求高的零件,应在粗、精加工之间进行预先处理,如消除应力、退火等。
钢件热处理容易变形的温度

钢件热处理容易变形的温度全文共四篇示例,供读者参考第一篇示例:钢件热处理是钢材加工中的一种重要工艺,通过加热和冷却来改变钢件的组织结构和性能。
热处理可以使钢件获得理想的硬度、强度和耐磨性,提高其使用性能和寿命。
在进行热处理过程中,钢件很容易发生变形,这给工艺控制和产品质量带来一定的困扰。
钢件热处理容易变形的主要原因有以下几点:1. 温度变化大:钢件在进行热处理时,需要进行高温加热和快速冷却。
由于钢材的热膨胀系数比较大,加热后钢件表面和内部温度会出现较大的差异,导致钢件形变。
2. 冷却速度不均匀:钢件在热处理过程中,冷却速度是影响钢件性能的重要因素之一。
如果冷却速度不均匀,会导致钢件产生内部应力,从而引起变形。
3. 热处理工艺不当:热处理工艺的参数设置不合理,比如加热温度、保温时间、冷却速度等方面没有进行有效控制,会导致钢件变形。
4. 初始应力存在:钢件在进行热处理之前,可能存在一定的残余应力,这些应力在热处理过程中会被释放出来,导致钢件变形。
钢件热处理容易变形的问题严重影响了产品的质量和生产效率,为了有效解决这一问题,可以采取以下措施:2. 合理设计工装:在热处理过程中,采用合理的工装设计,使钢件受力均匀,避免局部受力过大导致变形。
3. 预热处理:对于特殊形状或要求严格的钢件,可以在热处理前进行预热处理,降低残余应力,减少变形的可能性。
4. 热处理后回火处理:在热处理后进行回火处理,可以减少钢件内部应力,提高稳定性,减少变形。
通过以上措施的采取,可以有效降低钢件热处理过程中的变形问题,提高产品的质量和工艺稳定性,为钢件加工行业的发展提供有力支撑。
第二篇示例:钢件热处理是一种常见的工艺,可以通过加热和冷却钢件来改变其物理和化学性质。
在进行热处理过程中,钢件往往会出现变形的现象,这给生产制造过程带来了一定的困扰。
其中一个重要的原因就是温度控制不当。
钢件在热处理过程中容易发生变形的主要原因之一就是温度过高或者温度变化过快。
金属材料热处理变形的影响因素和控制策略

金属材料热处理变形的影响因素和控制策略
金属材料热处理变形是指在金属材料进行热处理过程中,由于温度、压力和力学应力的作用,导致材料发生形变。
热处理变形是金属加工中不可忽视的问题,对材料的性能和工艺性能有着重要影响。
本文将从影响因素和控制策略两个方面进行讨论。
影响金属材料热处理变形的因素有以下几个方面:
1. 温度:温度是影响金属材料热处理变形的重要因素。
在高温下,金属材料的塑性增强,易于发生变形。
但是温度过高会导致材料的晶粒长大,使材料的性能下降。
在热处理过程中需要控制好温度的选择,避免过高或过低的温度对材料的不良影响。
2. 压力:压力是热处理过程中的控制参数之一,对材料的变形起到重要作用。
适宜的压力可以加快变形过程,改善材料的性能。
但是过大的压力可能会导致材料的破裂和损坏,因此需要根据材料的性质和工艺要求确定合适的压力。
3. 力学应力:在热处理过程中,材料在受到外力作用下容易发生塑性变形。
力学应力的大小和方向对材料的变形有决定性影响。
不同形状和尺寸的材料在受力时会产生不同的应力分布,因此需要合理设计热处理装置和选择适当的应力状态,以控制材料的变形。
4. 热处理时间:热处理时间是影响金属材料热处理变形的另一个重要因素。
时间过长可能会导致材料的晶粒长大和析出相的生成,使材料的性能下降。
在热处理过程中需要精确控制热处理时间,避免时间过长对材料的不良影响。
金属材料热处理变形的影响因素和控制策略是一个复杂的问题。
需要综合考虑材料的性质、工艺要求和设备情况等因素,通过合理的策略和控制手段,实现对金属材料热处理变形的控制和优化。
钢件热处理变形的原因总结

钢件热处理变形的原因总结一、材料特性:1.材料的塑性变形能力不同:不同类型的钢,具有不同的塑性特性。
一般来说,低碳钢和不锈钢等具有良好的塑性,因此容易出现变形。
而高碳钢、合金钢等则具有较差的塑性,不容易变形。
2.材料的尺寸和形状:钢件的形状和尺寸也会影响热处理的变形程度。
尺寸较大、形状复杂的钢件变形较严重,尤其是在加热和冷却不均匀的情况下。
3.各向异性:钢材具有各向异性,即材料在不同的方向上具有不同的物理性能。
不同方向上的热膨胀系数不同,会导致热处理时钢件的不均匀膨胀和收缩,从而引起变形。
二、加热冷却方式:1.加热方式:钢件的加热方式会影响变形的严重程度。
例如,采用局部加热时,钢件的局部温度差异会导致表面和内部的温度差异,进而引起不均匀的膨胀和收缩。
2.加热速率和温度:加热速率和温度的选择也会对变形产生影响。
加热速率过快会导致钢材的内外温度差异增大,形成应力集中,易引发变形。
加热温度过高或过低也会导致钢件的不均匀热膨胀和变形。
三、操作参数:1.冷却速率:冷却速率的选择会直接影响钢件的变形。
冷却速率过快,会导致表面和内部温度差异增大,进而加剧变形。
冷却速率过慢,会使钢件的内部组织结构不均匀,产生不良的热处理效果。
2.冷却介质:冷却介质的选择也与变形有关。
不同的冷却介质冷却速率不同,从而影响变形的严重程度。
例如,水冷速度较快,容易引发变形;而油冷速度较慢,变形相对较小。
3.外部约束:外部约束也是导致钢件变形的重要因素。
外力的作用会导致钢件产生应力,从而引发变形。
因此,操作过程中要合理设置约束以避免变形的发生。
综上所述,钢件热处理变形是由于材料特性、加热冷却方式和操作参数的影响导致的。
合理选择加热冷却方式和操作参数,并根据钢材的特性进行调整,可以最大限度地减少钢件热处理变形的程度,确保热处理效果的稳定性和一致性。
热处理变形问题的解决办法
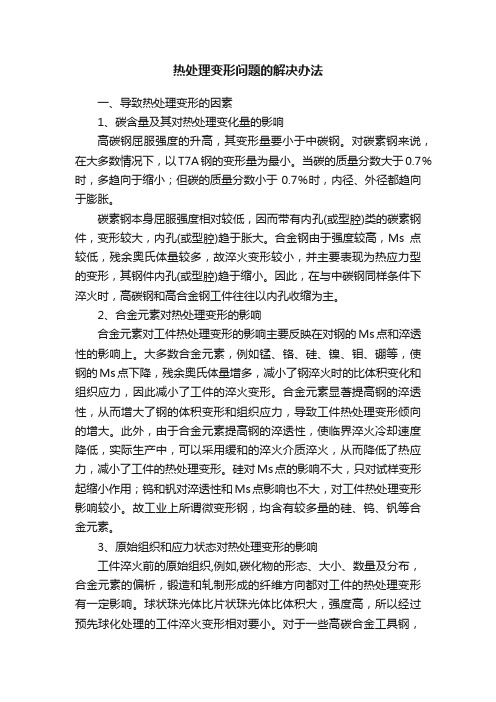
热处理变形问题的解决办法一、导致热处理变形的因素1、碳含量及其对热处理变化量的影响高碳钢屈服强度的升高,其变形量要小于中碳钢。
对碳素钢来说,在大多数情况下,以T7A钢的变形量为最小。
当碳的质量分数大于0.7%时,多趋向于缩小;但碳的质量分数小于0.7%时,内径、外径都趋向于膨胀。
碳素钢本身屈服强度相对较低,因而带有内孔(或型腔)类的碳素钢件,变形较大,内孔(或型腔)趋于胀大。
合金钢由于强度较高,Ms点较低,残余奥氏体量较多,故淬火变形较小,并主要表现为热应力型的变形,其钢件内孔(或型腔)趋于缩小。
因此,在与中碳钢同样条件下淬火时,高碳钢和高合金钢工件往往以内孔收缩为主。
2、合金元素对热处理变形的影响合金元素对工件热处理变形的影响主要反映在对钢的Ms点和淬透性的影响上。
大多数合金元素,例如锰、铬、硅、镍、钼、硼等,使钢的Ms点下降,残余奥氏体量增多,减小了钢淬火时的比体积变化和组织应力,因此减小了工件的淬火变形。
合金元素显著提高钢的淬透性,从而增大了钢的体积变形和组织应力,导致工件热处理变形倾向的增大。
此外,由于合金元素提高钢的淬透性,使临界淬火冷却速度降低,实际生产中,可以采用缓和的淬火介质淬火,从而降低了热应力,减小了工件的热处理变形。
硅对Ms点的影响不大,只对试样变形起缩小作用;钨和钒对淬透性和Ms点影响也不大,对工件热处理变形影响较小。
故工业上所谓微变形钢,均含有较多量的硅、钨、钒等合金元素。
3、原始组织和应力状态对热处理变形的影响工件淬火前的原始组织,例如,碳化物的形态、大小、数量及分布,合金元素的偏析,锻造和轧制形成的纤维方向都对工件的热处理变形有一定影响。
球状珠光体比片状珠光体比体积大,强度高,所以经过预先球化处理的工件淬火变形相对要小。
对于一些高碳合金工具钢,例如,9Mn2V、CrWMn和GCr15钢的球化等级对其热处理变形开裂和淬火后变形的校正有很大影响,通常以2.5-5级球化组织为宜。
钢件热处理容易变形的温度
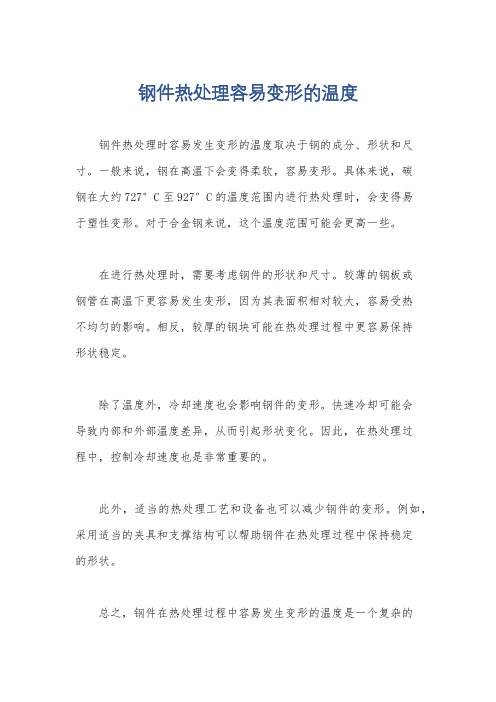
钢件热处理容易变形的温度
钢件热处理时容易发生变形的温度取决于钢的成分、形状和尺寸。
一般来说,钢在高温下会变得柔软,容易变形。
具体来说,碳
钢在大约727°C至927°C的温度范围内进行热处理时,会变得易
于塑性变形。
对于合金钢来说,这个温度范围可能会更高一些。
在进行热处理时,需要考虑钢件的形状和尺寸。
较薄的钢板或
钢管在高温下更容易发生变形,因为其表面积相对较大,容易受热
不均匀的影响。
相反,较厚的钢块可能在热处理过程中更容易保持
形状稳定。
除了温度外,冷却速度也会影响钢件的变形。
快速冷却可能会
导致内部和外部温度差异,从而引起形状变化。
因此,在热处理过
程中,控制冷却速度也是非常重要的。
此外,适当的热处理工艺和设备也可以减少钢件的变形。
例如,采用适当的夹具和支撑结构可以帮助钢件在热处理过程中保持稳定
的形状。
总之,钢件在热处理过程中容易发生变形的温度是一个复杂的
问题,需要综合考虑钢的成分、形状、尺寸以及热处理工艺等因素。
在实际操作中,需要根据具体情况采取合适的措施来减少变形的发生。
浅析金属材料热处理过程变形及开裂问题
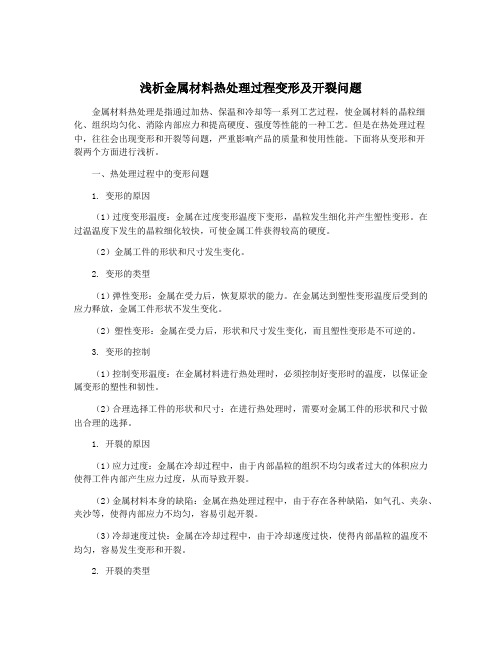
浅析金属材料热处理过程变形及开裂问题金属材料热处理是指通过加热、保温和冷却等一系列工艺过程,使金属材料的晶粒细化、组织均匀化、消除内部应力和提高硬度、强度等性能的一种工艺。
但是在热处理过程中,往往会出现变形和开裂等问题,严重影响产品的质量和使用性能。
下面将从变形和开裂两个方面进行浅析。
一、热处理过程中的变形问题1. 变形的原因(1)过度变形温度:金属在过度变形温度下变形,晶粒发生细化并产生塑性变形。
在过温温度下发生的晶粒细化较快,可使金属工件获得较高的硬度。
(2)金属工件的形状和尺寸发生变化。
2. 变形的类型(1)弹性变形:金属在受力后,恢复原状的能力。
在金属达到塑性变形温度后受到的应力释放,金属工件形状不发生变化。
(2)塑性变形:金属在受力后,形状和尺寸发生变化,而且塑性变形是不可逆的。
3. 变形的控制(1)控制变形温度:在金属材料进行热处理时,必须控制好变形时的温度,以保证金属变形的塑性和韧性。
(2)合理选择工件的形状和尺寸:在进行热处理时,需要对金属工件的形状和尺寸做出合理的选择。
1. 开裂的原因(1)应力过度:金属在冷却过程中,由于内部晶粒的组织不均匀或者过大的体积应力使得工件内部产生应力过度,从而导致开裂。
(2)金属材料本身的缺陷:金属在热处理过程中,由于存在各种缺陷,如气孔、夹杂、夹沙等,使得内部应力不均匀,容易引起开裂。
(3)冷却速度过快:金属在冷却过程中,由于冷却速度过快,使得内部晶粒的温度不均匀,容易发生变形和开裂。
2. 开裂的类型(1)晶间开裂:金属在冷却过程中,由于晶界处的强度较弱,容易出现晶界开裂。
(2)应力开裂:金属在冷却过程中,由于内部应力过大,使得工件产生应力开裂现象。
3. 开裂的控制(1)控制好冷却速度:合理控制金属材料的冷却速度,避免冷却速度过快导致开裂。
(2)减少金属材料的缺陷:在生产过程中,要严格控制金属材料的质量,减少金属材料的缺陷。
(3)采用适当的窑炉:使用适当的窑炉进行热处理,使得金属材料的温度和冷却速度控制得更加精准。
热处理变形产生的原因及控制方法
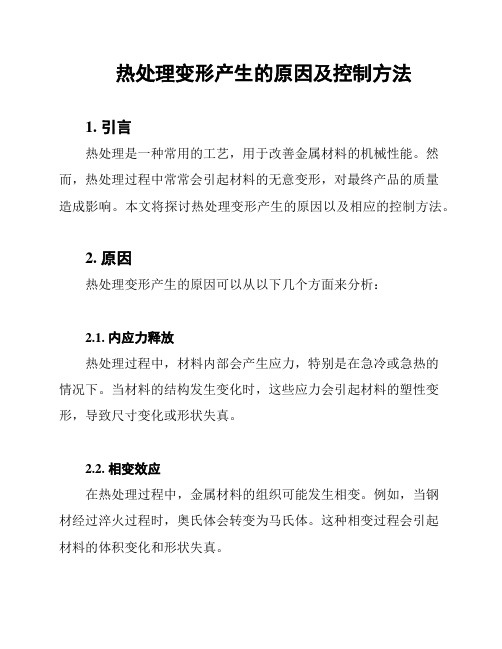
热处理变形产生的原因及控制方法1. 引言热处理是一种常用的工艺,用于改善金属材料的机械性能。
然而,热处理过程中常常会引起材料的无意变形,对最终产品的质量造成影响。
本文将探讨热处理变形产生的原因以及相应的控制方法。
2. 原因热处理变形产生的原因可以从以下几个方面来分析:2.1. 内应力释放热处理过程中,材料内部会产生应力,特别是在急冷或急热的情况下。
当材料的结构发生变化时,这些应力会引起材料的塑性变形,导致尺寸变化或形状失真。
2.2. 相变效应在热处理过程中,金属材料的组织可能发生相变。
例如,当钢材经过淬火过程时,奥氏体会转变为马氏体。
这种相变过程会引起材料的体积变化和形状失真。
2.3. 不均匀加热或冷却如果热处理过程中加热或冷却不均匀,材料的局部温度会存在差异。
这种温度差异会导致材料的非均匀膨胀或收缩,从而引起变形。
3. 控制方法为了减少热处理产生的变形,可以采取以下控制方法:3.1. 控制加热和冷却速率合理控制加热和冷却速率,避免过快或过慢,可以减少材料的变形。
在进行急冷或急热处理时,可以采取预先控制的温度梯度,以缓解内应力的释放。
3.2. 优化工艺参数通过调整热处理过程中的工艺参数,如温度、时间和冷却介质等,可以最大限度地减少材料的变形。
合理选择工艺参数,可以提高材料的均匀性和稳定性。
3.3. 采用合适的支撑结构对于形状复杂的工件,可以采用合适的支撑结构来减少变形。
支撑结构可以提供一定的约束,防止材料发生不受控制的变形。
4. 结论热处理变形是热处理过程中常见的问题,但通过合理的控制方法可以有效减少其影响。
合理控制加热和冷却速率、优化工艺参数以及采用合适的支撑结构都是减少热处理变形的有效途径。
这些控制方法可以提高最终产品的质量和性能。
---以上是关于热处理变形产生的原因及控制方法的内容。
请基于以上内容,进一步完善和添加具体细节,使文档达到800字以上的要求。
热处理变形校正方法

热处理变形校正方法在金属加工行业中,热处理是一个至关重要的环节,它能够改善材料的性能,为产品提供必要的强度和硬度。
然而,热处理过程中往往伴随着变形的问题,这给产品质量带来了挑战。
本文将详细介绍热处理变形校正的方法,帮助读者更好地理解和应对这一工艺难题。
一、热处理变形的原因热处理变形主要是由于材料在加热和冷却过程中,内部应力重新分布所导致的。
当材料暴露在高温环境下,其晶体结构会发生改变,冷却后,这些改变会导致尺寸变化和形状变形。
二、热处理变形校正方法1.预防措施:- 选择合适的材料:不同材料的热处理变形程度不同,选择变形较小的材料是预防变形的有效手段。
- 优化热处理工艺:通过调整加热速度、保温时间、冷却速度等参数,降低热处理变形的风险。
2.变形校正方法:- 机械校正:通过机械力对变形部位进行校正,如锤击、拉伸等,但这种方法仅适用于轻微变形。
- 热校正:利用材料在高温下的塑性变形,对变形部位进行加热至适当温度后进行校正。
这种方法对操作技术要求较高,需防止过度加热导致新的变形。
- 液体校正:将变形部位浸入高温液体中,利用液体的压力和温度对变形进行校正。
此方法适用于复杂形状的零件。
3.数控加工校正:- 采用数控加工技术,根据变形量对零件进行精确加工,以消除变形影响。
这种方法适用于高精度要求的零件。
4.表面处理:- 对变形部位进行表面处理,如喷漆、氧化等,以掩盖或补偿变形。
三、总结热处理变形是金属加工中不可避免的问题,但通过合理的预防措施和校正方法,可以最大限度地降低变形对产品质量的影响。
在实际操作中,应根据具体情况选择合适的校正方法,确保产品达到预期的性能和质量要求。
各种热处理工艺造成变形的原因总结

各种热处理工艺造成变形的原因总结一、变形的原因钢的变形主要原因是钢中存在内应力或者外部施加的应力。
内应力是因温度分布不均匀或者相变所致,残余应力也是原因之一。
外应力引起的变形主要是由于工件自重而造成的“塌陷”,在特殊情况下也应考虑碰撞被加热的工件,或者夹持工具夹持所引起的凹陷等。
变形包括弹性变形和塑性变形两种。
尺寸变化主要是基于组织转变,故表现出同样的膨胀和收缩,但当工件上有孔穴或者复杂形状工件,则将导致附加的变形。
如果淬火形成大量马氏体则发生膨胀,如果产生大量残余奥氏体则相应的要收缩。
此外,回火时一般发生收缩,而出现二次硬化现象的合金钢则发生膨胀,如果进行深冷处理,则由于残余奥氏体的马氏体化而进一步膨胀,这些组织的比容都随着含碳量的增加而增大,故含碳量增加也使尺寸变化量增大。
二、淬火变形的主要发生时段1加热过程:工件在加热过程中,由于内应力逐渐释放而产生变形。
2保温过程:以自重塌陷变形为主,即塌陷弯曲。
3冷却过程:由于不均匀冷却和组织转变而至变形。
三、加热与变形当加热大型工件时,存在残余应力或者加热不均匀,均可产生变形。
残余应力主要来源于加工过程。
当存在这些应力时,由于随着温度的升高,钢的屈服强度逐渐下降,即使加热很均匀,很轻微的应力也会导致变形。
一般,工件的外缘部位残余应力较高,当温度的上升从外部开始进行时,外缘部位变形较大,残余应力引起的变形包括弹性变形和塑性变形两种。
加热时产生的热应力和相变应力都是导致变形的原因。
加热速度越快、工件尺寸越大、截面变化越大,则加热变形越大。
热应力取决于温度的不均匀分布程度和温度梯度,它们都是导致热膨胀发生差异的原因。
如果热应力高于材料的高温屈服点,则引起塑性变形,这种塑性变形就表现为“变形”。
相变应力主要源于相变的不等时性,即材料一部分发生相变,而其它部分还未发生相变时产生的。
加热时材料的组织转变成奥氏体发生体积收缩时可出现塑性变形。
如果材料的各部分同时发生相同的组织转变,则不产生应力。
热处理变形原因及其控制方法

在实际的加工生产中,热处理变形往往困扰着许多加工制造者,热处理变形给后续的加工造成了很多困难,影响生产效率。
由于热处理工艺对工件产生的温度变化,变形是在所难免的,要做到完全不变形也是不可能的,一般解决方法是吧变形量控制在一定的范围内。
一、热处理变形产生的原因钢在热处理的加热、冷却过程中可能会产生变形,甚至开裂,其原因是由于淬火应力的存在。
淬火应力分为组织应力和热应力两种。
由于组织应力和热应力作用,使热处理后零件产生不同残留应力,可能引起变形。
当应力大于材料的屈服强度时变形就会产生,因此,淬火变形还与钢的屈服强度有关,材料塑性变形抗力越大,其变形程度也就越小。
二、减少和控制热处理变形的方法1.合理选择材料和提高硬度要求对于形状复杂,截面尺寸相差较大而又要求变形较小的零件,应选择淬透性较好的材料,以便使用较缓和的淬火冷却介质淬火。
对于薄板状精密零件,应选用双向轧制板材,使零件纤维方向对称。
对零件的硬度要求,在满足使用要求前提下,尽量选择下限硬度。
2.正确设计零件零件外形应尽量简单、均匀、结构对称,以免因冷却不均匀,使变形开裂倾向增大。
尽量避免截面尺寸突然变化,减少沟槽和薄边,不要有尖锐棱角。
避免较深的不通孔。
长形零件避免截面呈横梯形。
3.合理安排生产路线,协调冷热加工与热处理的关系对于形状复杂、精度要求高的零件,应在粗、精加工之间进行预先处理,如消除应力、退火等。
做好毛坯预备热处理,使组织更加均匀化。
4.改进热处理工艺和操作(1)热处理温度的控制在满足热处理工艺要求的情况下,尽量降低淬火加热温度且缩短保温时间,这样零件的高温强度损失较少。
塑性抗力增强,零件的抗应力形变、抗淬火变形的综合能力增强,从而减少了变形。
(2)选择较缓和的淬火冷却介质采用分级淬火能显著减少金属淬火时产牛的热应力和组织应力,是减少一些形状复杂零件的有效办法。
这种淬火方法由于在马氏体转变前零件各部分温度已经趋于均匀,并在缓慢冷却条件下完成马氏体转变,这样不仅减小了淬火热应力,而且显著降低组织应力,因而有效地减小或预防止零件淬火变形。
金属材料热处理变形的影响因素和控制策略
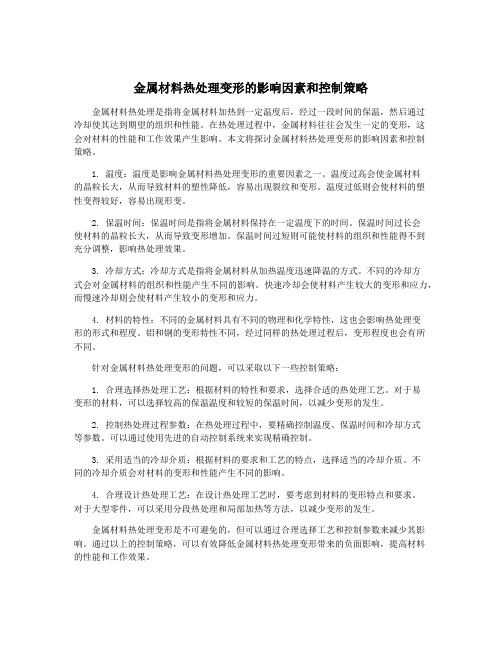
金属材料热处理变形的影响因素和控制策略金属材料热处理是指将金属材料加热到一定温度后,经过一段时间的保温,然后通过冷却使其达到期望的组织和性能。
在热处理过程中,金属材料往往会发生一定的变形,这会对材料的性能和工作效果产生影响。
本文将探讨金属材料热处理变形的影响因素和控制策略。
1. 温度:温度是影响金属材料热处理变形的重要因素之一。
温度过高会使金属材料的晶粒长大,从而导致材料的塑性降低,容易出现裂纹和变形。
温度过低则会使材料的塑性变得较好,容易出现形变。
2. 保温时间:保温时间是指将金属材料保持在一定温度下的时间。
保温时间过长会使材料的晶粒长大,从而导致变形增加。
保温时间过短则可能使材料的组织和性能得不到充分调整,影响热处理效果。
3. 冷却方式:冷却方式是指将金属材料从加热温度迅速降温的方式。
不同的冷却方式会对金属材料的组织和性能产生不同的影响。
快速冷却会使材料产生较大的变形和应力,而慢速冷却则会使材料产生较小的变形和应力。
4. 材料的特性:不同的金属材料具有不同的物理和化学特性,这也会影响热处理变形的形式和程度。
铝和钢的变形特性不同,经过同样的热处理过程后,变形程度也会有所不同。
针对金属材料热处理变形的问题,可以采取以下一些控制策略:1. 合理选择热处理工艺:根据材料的特性和要求,选择合适的热处理工艺。
对于易变形的材料,可以选择较高的保温温度和较短的保温时间,以减少变形的发生。
2. 控制热处理过程参数:在热处理过程中,要精确控制温度、保温时间和冷却方式等参数。
可以通过使用先进的自动控制系统来实现精确控制。
3. 采用适当的冷却介质:根据材料的要求和工艺的特点,选择适当的冷却介质。
不同的冷却介质会对材料的变形和性能产生不同的影响。
4. 合理设计热处理工艺:在设计热处理工艺时,要考虑到材料的变形特点和要求。
对于大型零件,可以采用分段热处理和局部加热等方法,以减少变形的发生。
金属材料热处理变形是不可避免的,但可以通过合理选择工艺和控制参数来减少其影响。
热处理钢材变形及其解决

热处理钢材变形及其解决二、模具结构设计的影响有些模具选材和钢的材质都很好往往因为模具结构设计不合理如薄边、尖角、沟槽、突变的台阶、厚薄悬殊等造成模具热处理后变形较大。
1、变形的原因由于模具各处厚薄不均或存在尖锐圆角因此在淬火时引起模具各部位之间的热应力和组织应力的不同导致各部位体积膨胀的不同使模具淬火后产生变形。
2、预防措施设计模具时在满足实际生产需要的情况下应尽量减少模具厚悬殊结构不对称在模具的厚薄交界处尽可能采用平滑过渡等结构设计。
根据模具的变形规律预留加工余量在淬火后不致于因为模具变形而使模具报废。
对形状特别复杂的模具为使淬火时冷却均匀可采用给合结构。
三、模具制造工序及残余应力的影响在工厂经常发现一些形状复杂、精度要求高的模具在热处理后变形较大经认真调查后发现模具在机械加工和最后热处理未进行任何预先热处理。
1、变形原因在机械加工过程中的残余应力和淬火后的应力叠加增大了模具热处理后的变形。
2、预防措施1粗加工后、半精加工前应进行一次去应力退火即630-680℃×3-4h炉冷至500℃以下出炉空冷也可采用400℃×2-3h去应力处理。
2降低淬火温度减少淬火后的残余应力。
3采用淬油170ordmC出油空冷分级淬火。
4采用等温淬火工艺可减少淬火残余应力。
采用以上措施可使模具淬火后残余应力减少模具变形较小。
四、热处理加热工艺的影响1、加热速度的影响模具热处理后的变形一般都认为是冷却造成的这是不正确的。
模具特别是复杂模具加工工艺的正确与否对模具的变形往往产生较大的影响对一些模具加热工艺的对比可明显看出加热速度较快往往产生较大的变形。
1变形的原因任何金属加热时都要膨胀由于钢在加热时同一个模具内各部分的温度不均即加热的不均匀就必然会造成模具内各部分的膨胀的不一致性从而形成因加热不均的内应力。
在钢的相变点以下温度不均匀的加热主要产生热应力超过相变温度加热不均匀还会产生组织转变的不等时性既产生组织应力。
钢的热处理淬火时工件的变形规律

淬火时,工件发生的变形有两类,一是翘曲变形,一是体积变形。
翘曲变形包括形状变形和扭曲变形。
扭曲变形主要是加热时工件在炉内放置不当,或者淬火前经变形校正后没有定型处理,或者是由于工件冷却时工件各部位冷却不均匀所造成,这种变形可以针对具体情况分析解决。
1、引起各种变形的原因及其变化规律(1)由于淬火前后组织变化而引起的体积变形工件在淬火前的组织状态一般为珠光体型,即铁素体和渗碳体的混合组织,而淬火后为马氏体型组织。
由于这些组织体积不同,淬火前后将引起体积变化,从而产生变形。
这种变形只按比例使工件胀缩,但不改变形状。
淬火前后由此而引起的体积变化,可以计算求得。
(2)热应力引起的形状变形热应力引起的变形发生在钢件屈服强度较低,塑性较高,而表面冷却快,工件内外温差最大的高温区。
此时瞬时热应力是表面张应力,心部压应力,心部温度高,屈服强度比表面低很多,易于变形。
因此表现为在多向压应力作用下的变形,即立方体向呈球形方向变化。
由此导致尺寸较大的一方缩小,而尺寸较小的一方则胀大。
(3)组织应力引起的形状变形组织应力引起的变形也产生在早期组织应力最大时刻。
此时截面温度较大,心部温度较高,仍处于奥氏体状态,塑性较好,屈服强度较低。
瞬时组织应力是表面压应力,心部拉应力;其变形表现为心部在多向拉应力作用下的拉长。
由此导致的结果为在组织应力作用下,工件中尺寸较大的一方伸长,而尺寸较小的一方缩短。
2、影响淬火变形的因素(1)影响体积变形和形状变形的因素。
凡是影响淬火前后组织比体积变化的因素均影响体积变形。
(2)其他影响淬火变形的因素。
影响淬火变形的因素有两种,一种是夹杂物和带状组织对淬火变形的影响。
(3)淬火前残存应力及加热冷却不均匀对变形的影响。
淬火前工件内残余应力没有消除,淬火加热装炉不当,淬火冷却不当均引起工件的扭曲变形。
金属材料热处理变形的影响因素和控制策略分析
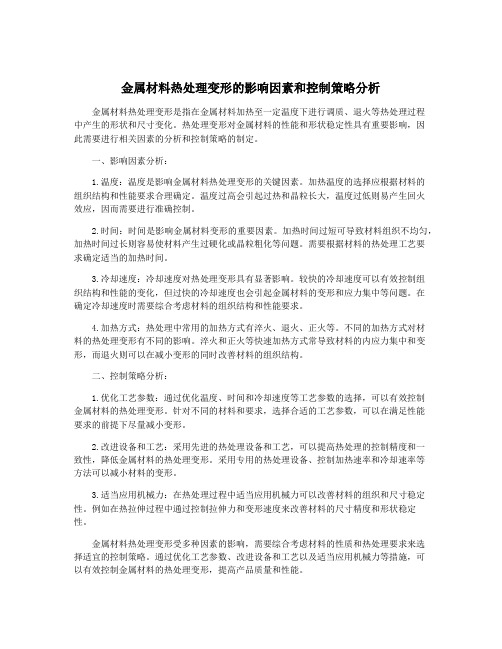
金属材料热处理变形的影响因素和控制策略分析金属材料热处理变形是指在金属材料加热至一定温度下进行调质、退火等热处理过程中产生的形状和尺寸变化。
热处理变形对金属材料的性能和形状稳定性具有重要影响,因此需要进行相关因素的分析和控制策略的制定。
一、影响因素分析:1.温度:温度是影响金属材料热处理变形的关键因素。
加热温度的选择应根据材料的组织结构和性能要求合理确定。
温度过高会引起过热和晶粒长大,温度过低则易产生回火效应,因而需要进行准确控制。
2.时间:时间是影响金属材料变形的重要因素。
加热时间过短可导致材料组织不均匀,加热时间过长则容易使材料产生过硬化或晶粒粗化等问题。
需要根据材料的热处理工艺要求确定适当的加热时间。
3.冷却速度:冷却速度对热处理变形具有显著影响。
较快的冷却速度可以有效控制组织结构和性能的变化,但过快的冷却速度也会引起金属材料的变形和应力集中等问题。
在确定冷却速度时需要综合考虑材料的组织结构和性能要求。
4.加热方式:热处理中常用的加热方式有淬火、退火、正火等。
不同的加热方式对材料的热处理变形有不同的影响。
淬火和正火等快速加热方式常导致材料的内应力集中和变形,而退火则可以在减小变形的同时改善材料的组织结构。
二、控制策略分析:1.优化工艺参数:通过优化温度、时间和冷却速度等工艺参数的选择,可以有效控制金属材料的热处理变形。
针对不同的材料和要求,选择合适的工艺参数,可以在满足性能要求的前提下尽量减小变形。
2.改进设备和工艺:采用先进的热处理设备和工艺,可以提高热处理的控制精度和一致性,降低金属材料的热处理变形。
采用专用的热处理设备、控制加热速率和冷却速率等方法可以减小材料的变形。
3.适当应用机械力:在热处理过程中适当应用机械力可以改善材料的组织和尺寸稳定性。
例如在热拉伸过程中通过控制拉伸力和变形速度来改善材料的尺寸精度和形状稳定性。
金属材料热处理变形受多种因素的影响,需要综合考虑材料的性质和热处理要求来选择适宜的控制策略。
热处理变形的因素
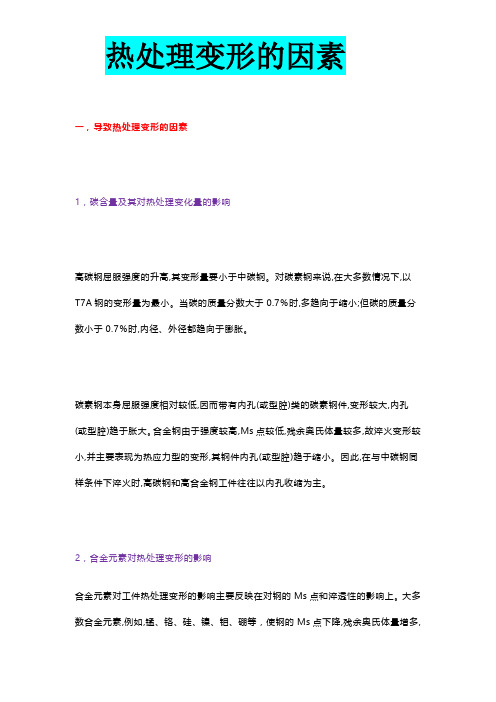
一,导致热处理变形的因素1,碳含量及其对热处理变化量的影响高碳钢屈服强度的升高,其变形量要小于中碳钢。
对碳素钢来说,在大多数情况下,以T7A钢的变形量为最小。
当碳的质量分数大于0.7%时,多趋向于缩小;但碳的质量分数小于0.7%时,内径、外径都趋向于膨胀。
碳素钢本身屈服强度相对较低,因而带有内孔(或型腔)类的碳素钢件,变形较大,内孔(或型腔)趋于胀大。
合金钢由于强度较高,Ms点较低,残余奥氏体量较多,故淬火变形较小,并主要表现为热应力型的变形,其钢件内孔(或型腔)趋于缩小。
因此,在与中碳钢同样条件下淬火时,高碳钢和高合金钢工件往往以内孔收缩为主。
2,合金元素对热处理变形的影响合金元素对工件热处理变形的影响主要反映在对钢的Ms点和淬透性的影响上。
大多数合金元素,例如,锰、铬、硅、镍、钼、硼等,使钢的Ms点下降,残余奥氏体量增多,减小了钢淬火时的比体积变化和组织应力,因此,减小了工件的淬火变形。
合金元素显著提高钢的淬透性,从而增大了钢的体积变形和组织应力,导致工件热处理变形倾向的增大。
此外,由于合金元素提高钢的淬透性,使临界淬火冷却速度降低,实际生产中,可以采用缓和的淬火介质淬火,从而降低了热应力,减小了工件的热处理变形。
硅对Ms点的影响不大,只对试样变形起缩小作用;钨和钒对淬透性和Ms点影响也不大,对工件热处理变形影响较小。
故工业上所谓微变形钢,均含有较多量的硅、钨、钒等合金元素。
3,原始组织和应力状态对热处理变形的影响工件淬火前的原始组织,例如,碳化物的形态、大小、数量及分布,合金元素的偏析,锻造和轧制形成的纤维方向都对工件的热处理变形有一定影响。
球状珠光体比片状珠光体比体积大,强度高,所以经过预先球化处理的工件淬火变形相对要小。
对于一些高碳合金工具钢,例如,9Mn2V、CrWMn和GCr15钢的球化等级对其热处理变形开裂和淬火后变形的校正有很大影响,通常以2.5-5级球化组织为宜。
调质处理不仅使工件变形量的绝对值减小,并使工件的淬火变形更有规律,从而有利于对变形的控制。
各种热处理工艺造成变形的原因总结

各种热处理工艺造成变形的原因总结引言:热处理工艺是一种常见的金属加工方法,它通过对金属材料进行加热和冷却来改变其结构和性能。
然而,热处理过程中往往会导致材料发生变形,这对于一些精密零件的加工和制造带来一定的困扰。
本文将从各种热处理工艺的角度,总结造成变形的原因,并探讨相应的解决方法。
一、淬火过程中的变形原因淬火是一种通过快速冷却来使金属材料达到高强度和硬度的热处理工艺。
然而,淬火过程中常常会出现变形现象。
造成淬火变形的主要原因有以下几点:1. 冷却速度不均匀:淬火过程中,材料表面和内部的冷却速度不一致,导致应力不均匀分布,从而引起变形。
2. 材料内部组织不均匀:金属材料内部的组织不均匀,如晶粒尺寸、相含量等差异,会导致淬火时的收缩和变形不一致。
3. 冷却介质选择不当:不同的冷却介质对材料的冷却速度有不同的影响,选择不当可能导致应力集中和变形。
解决方法:针对淬火过程中的变形问题,可以采取以下措施:1. 控制冷却速度:通过优化冷却介质的选择和控制冷却速度,使材料表面和内部的冷却速度尽可能一致,减少应力的不均匀分布。
2. 优化材料组织:通过调整材料的化学成分和热处理工艺,使材料内部的组织更加均匀,减少淬火时的收缩和变形差异。
3. 采用适当的淬火工艺:根据材料的特性和要求,选择适当的淬火工艺,控制冷却速度和温度,减少变形的发生。
二、退火过程中的变形原因退火是一种通过加热和缓慢冷却来改善材料的性能和结构的热处理工艺。
然而,退火过程中同样存在变形的问题。
造成退火变形的主要原因有以下几点:1. 温度不均匀:退火过程中,材料的温度分布不均匀,导致应力分布不均匀,从而引起变形。
2. 冷却速度过快:退火结束后,如果冷却速度过快,会导致材料内部的残余应力无法得到充分释放,从而引起变形。
3. 材料内部缺陷:金属材料内部存在各种缺陷,如气孔、夹杂物等,这些缺陷在退火过程中会扩散和移动,导致变形的发生。
解决方法:针对退火过程中的变形问题,可以采取以下措施:1. 控制温度均匀性:通过合理设计加热设备和工艺参数,确保材料的温度分布均匀,减少应力的不均匀分布。
- 1、下载文档前请自行甄别文档内容的完整性,平台不提供额外的编辑、内容补充、找答案等附加服务。
- 2、"仅部分预览"的文档,不可在线预览部分如存在完整性等问题,可反馈申请退款(可完整预览的文档不适用该条件!)。
- 3、如文档侵犯您的权益,请联系客服反馈,我们会尽快为您处理(人工客服工作时间:9:00-18:30)。
钢件热处理变形的原因总结
引起热处理变形的因素颇多,总括起来,基本上有三点:
1、固态相变时,各相质量体积的变化必然引起体积的变化,造成零件的胀与缩的尺寸变化;
2、热应力,包括急热热应力和急冷热应力,当它们超过零件在该温度下所具有的屈服极限时,将使零件产生塑性变形,造成零件的形状变化,即歪扭,或称为畸变;
3、组织应力也会引起形状的改变,即畸变。
一般说,淬火工件的变形总是由于以上的两种或三种因素综合作用的结果,但究竟哪一个因素对变形的影响较大,则需要具体情况作具体的分析。
总的来说,体积变化是由相变时比容的改变而引起的。
马氏体的质量体积比钢的其他组成相的质量体积要大,热处理时钢由其他组成相转化为马氏体时,必然引起体积的增加。
而奥氏体的质量体积要比钢的其他组织质量体积要小,在热处理时由其他组成相转变为奥氏体时,则引起体积的减小。
关于形状的变化,歪扭或称为畸变,主要是由于内应力或者外加应力作用的结果。
在加热、冷却过程中,因工件各个部位的温度有差别,相变在时间上有先后,有时发生的组织转变也不一致,而造成内应力。
这种内应力一旦超过了该温度下材料的屈服极限,就产生塑性变形,引起形状的改变。
此外工件内的冷加工残余应力在加热过程中的松弛,以及由于加热时受到较大的外加应力也会引起形状的变化。
在热处理时可能引起体积变化和形状变化的原因见下表。
表中“体积变化原因” 一栏未列入钢因热胀冷缩现象而产生的体积变化,钢由淬火加热温度到零下温度进行冷处理,均随温度的变化而有相应的体积变化,因热胀冷缩而引起的体积变化不均匀乃是热应力产生的原因,而且对变形有相当的影响。
热处理可能引起体积变化和形状变化的原因。