新版近十年来国内RH真空精炼技术的发展
RH高效生产技术的发展
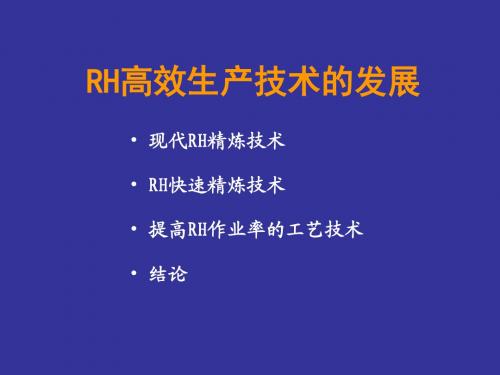
RH脱碳速度Kc与[C]的关系
Kc
W Q / ak
钢水的循环流量可按下式计算[7]:
0.3 1.1 Q 3.8 103 Du Dd G 0.31 H 0.5
体积传质系数可按经验公式计算[8]:
ak = 2.2710-7· G0.67· [C]1.76· [O]0.75· {ln(101.3/P2)}0.67· S
钢包容量与浸渍管直径的关系
提升气体流量与浸渍管直径的关系
RH快速脱碳技术的发展
快速脱氢技术
RH具有很强的脱氢能力,RH脱氢反应的动力 学表达式如下: -d[H]/dt=KH([%H]-[%H]e)
KH
Q ak V (Q ak )
试验和生产证明,随着浸渍管直径的增大,RH
脱氢表观速度常数KH增大,脱氢速度提高,当 [H]≥110-6时K
20
≤2.0 ≤30 80-90 无 0.3-0.4 0.8
RH适合各种高品质钢的精炼要求
新一代钢铁材料的发展趋势是:超洁净、高均匀和微细组织结构控制。RH可以满足各 类高品质钢材洁净度的要求。对于同时要求超低碳、超低硫的钢种(如电工硅钢)和同时 要求超低碳、超低氮的钢种(如IF钢)以及同时要求低碳、低硅的钢种(如涂镀钢板) RH 是唯一最佳的精炼设备。而对于要求氧、硫含量的钢种(如低合金高强度钢和特殊钢)可 以选择RH也可以选择LF-VD(或LF-RH)。而对于不锈钢冶炼VOD是最佳的冶炼设备,但 日本许多钢厂也采用RH取代VOD生产不锈钢。 表2 各种高品质钢的性能和洁净度要求及其相适应的精炼方法
务川进等人通过实验研究钢水增氮(或脱氮)速度与钢 中表面活性元素硫和氧的含量的关系。随钢中 [%O]和[%S] 含量的增加,钢水吸氮(或脱氮)速度降低(或增高)。日 本川崎公司千叶厂通过生产实践发现:RH浸渍管内的钢板在 高温下发生变形,造成浸渍管漏气是钢水增氮的主要原因。 采用吹氩密封技术,可以降低钢水吸氮量,进而提高 RH的脱 氮效率。水上等人通过160tRH试验证明,向熔池吹入少量 CO和Ar的混合气体可以提高RH的脱氮能力,稳定生产出 [N]≤2010-6的超低氮钢。
RH精炼技术的发展

1 前言 在炉外精炼方法中主要有 RH、DH、VAD 、
VD 、VOD 、ASEA2SKF、LF 等 , 其中 RH 法是最 为重要的一种 。 ( RH) 处理工艺具有精炼效率 高 、适应批量处理 、装备投资少 、易操作等一系 列优点 , 在炼钢生产中获得了广泛应用和显著进 展 。它不仅提高钢产量 , 改善钢材质量 , 增加品 种 , 降低成本 , 提高经济效益 , 而且极大地优化 了现代炼钢工艺 。目前 , RH 的主要功能已经由 原来单一的脱气设备发展成为包含真空脱气脱 碳 、吹氧脱碳 、喷粉脱硫 、温度补偿 、均匀温度 和成分等的一种多功能炉外精炼设备 。 2 RH 方法的吹氧脱碳功能的发展
RH 吹氧技术的发展经历了 RH2O , RH2OB , RH2KTB , MFB 等四个主要阶段 。
第6期
黄会发等 : RH 精炼技术的发展
7
图 1 RH2KTB 脱碳规律
211 RH —O 真空吹氧技术[4] 1969 年德国蒂森钢铁公司亨利希钢厂开发
了 RH —O 技术 (图 2) , 首次用铜质水冷氧枪从 真空室顶部向真空室内循环着的钢水表面吹氧以 强化脱碳冶炼低碳不锈钢 , 既缩短了冶炼周期又 降低了脱碳过程中铬的氧化损失 。但在工业生产 中 RH —O 技术暴露出以下问题 : 氧枪结瘤严重 , 因氧枪动密封不良而使氧枪枪位无法调整 。这些 问题一时无法解决 , 而当时 VOD 精炼技术能较 好地满足不锈钢生产的要求 , 所以 RH —O 技术 未能得到广泛应用 。
在传统的 RH 基础上 , 日本川崎公司于 1986 年成 功 地 开 发 了 RH 顶 吹 氧 ( RH —KTB) 技 术 (图 4) , 将 RH 技术的发展推向一个新阶段。该法 是从 RH 真空室顶部插入一可垂直升降的水冷氧 枪 (160t 装置的喷枪内径为 25mm) , 通过该氧枪 向真空室内钢液吹定量氧气和惰性气体 , 强化脱 碳 , 同时利用炉气中 CO 的二次燃烧提供附加热 量 , 以此来补偿精炼过程中的温降。其综合效果 可使转炉出钢温度降低约 26 ℃。图 5 给出了 RH 和 RH —KTB 过程排气成分和二次燃烧率的比较。
RH精炼炉工艺

RH精炼炉工艺摘要:介绍了RH的发展历史,对RH中最关键的真空系统原理进行了说明,介绍了莱钢RH的功能、设备及工艺,针对莱钢情况,对莱钢品种开发进行了探讨。
关键词: RH 原理工艺品种1 RH的历史与发展RH精炼全称为RH真空循环脱气精炼法。
于1959年由德国人发明,其中RH为当时德国采用RH精炼技术的两个厂家的第一个字母。
真空技术在炼钢上开始应用起始于1952年,当时人们在生产含硅量在2%左右的硅钢时在浇注过程中经常出现冒渣现象,经过各种试验,终于发现钢水中的氢和氮是产生冒渣无法浇注或轧制后产生废品的主要原因,随之各种真空精炼技术开始出现,如真空铸锭法、钢包滴流脱气法、钢包脱气法等,从而开创了工业规模的钢水真空处理方法,特别是蒸汽喷射泵的出现,更是加速了真空炼钢技术的发展。
随着真空炼钢技术的开发与发展,最终RH和VD因为处理时间短、成本低、可以大量处理钢水等优点而成为真空炼钢技术的主流,70年代开始随着全连铸车间的出现,RH因为采用钢水在真空槽环流的技术从而达到处理时间短、效率高、能够与转炉连铸匹配的优点而被转炉工序大量采用。
RH从开始出现到现在40多年来,有多项关键性技术的出现,从而加速了RH精炼技术的发展。
表1为40多年来RH技术的发展情况。
表1 RH技术发展情况2 RH系统概述RH系统设备是一种用于生产优质钢的钢水二次精炼工艺装备。
整个钢水冶金反应是在砌有耐火衬的真空槽内进行的。
真空槽的下部是两个带耐火衬的浸渍管,上部装有热弯管。
被抽气体由热弯管经气体冷却器至真空泵系统排到厂房外。
钢水处理前,先将浸渍管浸入待处理的钢包钢水中。
当真空槽抽真空时,钢水表面的大气压力迫使钢水从浸渍管流入真空槽内(真空槽内大约0.67mbar时可使钢水上升1.48m高度)。
与真空槽连通的两个浸渍管,一个为上升管,一个为下降管。
由于上升管不断向钢液吹入氩气,相对没有吹氩的下降管产生了一个较高的静压差,使钢水从上升管进入并通过真空槽下部流向下降管,如此不断循环反复。
RH资料

RH真空罐有两个咀,其中一个内部布有吹气管,处理钢液时RH真空罐的两个咀插入钢包钢液,开始抽真空,上升管钢液进入,这是由于上升管内往钢液中吹气,钢液密度较小,下降管则是钢液密度比上升管内小,从而形成循环,钢液可持续循环进行。
冶金功能:脱气(氮气,氢气),脱碳和脱氧(真空下降低一氧化碳分压,使脱碳反应持续进行到新的平衡,碳可降到20PPM以下),合金化(真空室上部有加料管道,料仓内的合金通过减压阀进入真空室),调整温度(化学升温和降温,一般是加铝后吹氧升温,加低碳钢小料降温),微调成分,终脱氧(脱氧剂可以是铝,也可以是硅锰等)。
RH真空处理一般脱气处理称为轻处理,而深脱碳合金化等处理称为本处理。
钢铁厂RH精炼真空炉,可处理什么规格的钢水?或要求什么条件RH精炼是处理高精尖板带材的炉外精炼工序,由于精炼过程中的温降、电耗、耐材消耗、节奏等,会增加成本,所以,一般材质的钢材不用,只用LF、CAS-OB 等就可以啦。
经过RH精炼处理后的钢水H含量、夹杂物等明显降低,性能明显提高。
但是,要求转炉工序提高出钢温度20度左右。
网上有的资料我都有但没有生产实践的资料------那就要生产一线去,积累经验,实际操作,总结经验,提高水平,做一个真正的原理很简单钢水经由上升管进入真空室被脱气再由下降管流回钢包如此循环,直至达到要求止把这个图看明白就可以了RH多功能真空精炼技术开发RH真空精炼技术产生于50年代末期。
在近30年的时间里,RH的功能和精炼的钢种范围不断扩大,发展成为多功能真空精炼技术,在炉外精炼中占主导地位。
至今,全世界已有100余台。
在西欧、日本、美国得到普遍推广,仅日本就有40余台,1989年日本转炉钢真空精炼率达56.5%,新日铁大分厂、川崎制铁水岛厂已全量进行RH真空精炼。
实践证明,RH真空精炼技术是提高产品质量,降低成本,扩大品种,提高炼钢生产能力,保证连铸顺行,实现全连铸,优化炼钢生产工艺的重要手段。
RH培训
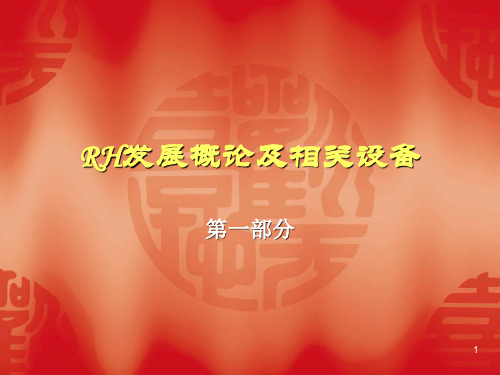
第一部分
1
RH的发展简史
RH真空精炼技术起源于50年代,1957年阿尔贝德公司申请了钢水真空
精炼脱气法的技术专利,这是真空脱气法发展的开端。 1958年德国 Rheinstahl(莱茵钢公司)和 Heratus(赫拉乌斯)真空 泵厂合作成功地进行了工业性生产实验,取得了可喜的处理效果,在 1959年德国冶金工作者协会上引起了同行的极大关注,定名RH。以后 各国都在真空循环脱气法上开展了研究。其中以日本发展最为迅速。新 日铁在1972年发明了RH-OB法,能起到铝升温的作用。80年代中期, 大分厂、名古屋厂为了得到低硫钢水,采用喷吹脱硫剂的方法生产出 S≤10ppm的RH钢。80年代后期~90年代初期,日本川崎发明了RH- KTB,实现了二次燃烧和吹O2脱C,和KPB(MFB)用顶枪喷吹脱S剂。 中国的RH发展是在90年代以后开始的,但近几年来随着低碳钢在市场 上所占比例越来越高,RH的用途越来越广。目前,一般中、大型钢厂 都配置有RH炉。 RH新技术的发展 新日铁发明的KPB(MFB)利用外加能源介质,实现了处理位上的真空 槽烘烤,其吹氧脱碳的功能,使生产出C≤20ppm的超低碳钢。
22
二、RH脱气原理
2、RH脱氮原理及影响因素
A:氮主要以化合物形态存在于钢中; B:氮可作为提高钢的硬度、耐磨性、抗蚀性的合金元素; C:对低碳钢Fe4N的析出将造成时效和蓝脆,达到一定程度时形成气泡
和疏松,使钢的塑性下降,对超低碳钢影响更大; D:氮在α-Fe、δ-Fe中的溶解度随温度升高而增加,在γ-Fe中相反; E:就氮在钢中的溶解度而言,遵循以下规律:[%N]=K [N] *(PN2)1/2, 在1600℃、1mbar下K [N] =0.045%,所以[%N]= 0.045%(PN2)1/2; F:V、Cr、Nb、Mn将提高N在钢中的溶解度,Si、C、Ni将降低其溶 解度; G:影响因素:原始氮含量、RH处理时间、真空度、钢中[O]、[S]的含 量、真空系统的泄漏率、环流量等。
RH精炼炉

RH精炼炉1 RH的历史与发展RH精炼全称为RH真空循环脱气精炼法。
于1959年由德国人发明,其中RH为当时德国采用RH精炼技术的两个厂家的第一个字母。
真空技术在炼钢上开始应用起始于1952年,当时人们在生产含硅量在2%左右的硅钢时在浇注过程中经常出现冒渣现象,经过各种试验,终于发现钢水中的氢和氮是产生冒渣无法浇注或轧制后产生废品的主要原因,随之各种真空精炼技术开始出现,如真空铸锭法、钢包滴流脱气法、钢包脱气法等,从而开创了工业规模的钢水真空处理方法,特别是蒸汽喷射泵的出现,更是加速了真空炼钢技术的发展。
随着真空炼钢技术的开发与发展,最终RH和VD因为处理时间短、成本低、可以大量处理钢水等优点而成为真空炼钢技术的主流,70年代开始随着全连铸车间的出现,RH因为采用钢水在真空槽环流的技术从而达到处理时间短、效率高、能够与转炉连铸匹配的优点而被转炉工序大量采用。
RH从开始出现到现在40多年来,有多项关键性技术的出现,从而加速了RH精炼技术的发展。
表1为40多年来RH技术的发展情况。
2RH系统概述RH系统设备是一种用于生产优质钢的钢水二次精炼工艺装备。
整个钢水冶金反应是在砌有耐火衬的真空槽内进行的。
真空槽的下部是两个带耐火衬的浸渍管,上部装有热弯管。
被抽气体由热弯管经气体冷却器至真空泵系统排到厂房外。
钢水处理前,先将浸渍管浸入待处理的钢包钢水中。
当真空槽抽真空时,钢水表面的大气压力迫使钢水从浸渍管流入真空槽内(真空槽内大约0.67mbar时可使钢水上升1.48m高度)。
与真空槽连通的两个浸渍管,一个为上升管,一个为下降管。
由于上升管不断向钢液吹入氩气,相对没有吹氩的下降管产生了一个较高的静压差,使钢水从上升管进入并通过真空槽下部流向下降管,如此不断循环反复。
在真空状态下,流经真空槽钢水中的氩气、氢气、一氧化碳等气体在钢液循环过程中被抽走。
同时,进入真空槽内的钢水还进行一系列的冶金反应,比如碳氧反应等;如此循环脱气精炼使钢液得到净化。
RH
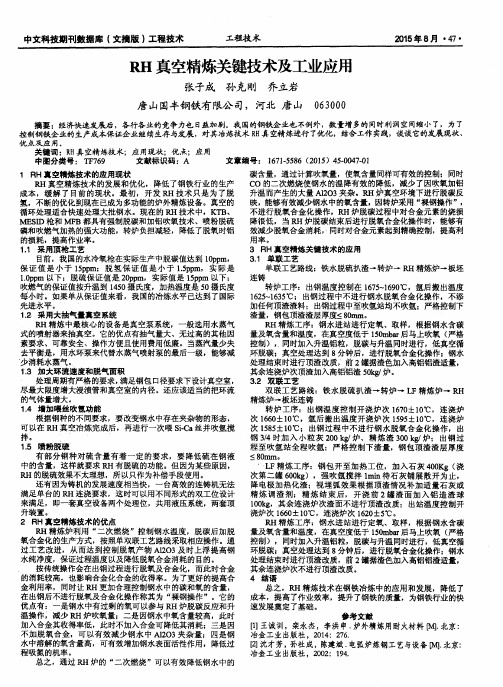
碳含量 ,通过计算吹氧量,使氧含量 同样可有效的控制 :同时 C O 的二次燃烧使钢 水的温降有效的 降低 ,减少 了因吹氧加铝 升温而产 生的大量 A 1 2 0 3 夹杂 。 R I - I 炉真 空环境下进行脱碳反 映,能够有效减少钢水中的氧含量 ,因转炉采用 “ 裸钢操作 ”, 不进 行脱氧合金化操作 ,R H炉脱碳过程 中对合金元素 的烧 损 降很低 ,当 R H炉脱碳结束后进行脱氧合金化操作时,能够有 效减 少脱氧合金消耗 , , 同时对合金元素起到精确控制,提高利 用率。 3 _ R H真空精炼关键技术的应用 3 . 1 单联工艺 单联工艺路线 :铁水脱硫扒渣一转炉一 R H 精炼炉一板坯 连铸 转炉工序 :出钢温度控 制在 1 6 7 5  ̄ 1 6 9 0 ℃,氩后搬 出温 度 1 6 2 5  ̄ 1 6 3 5 ℃;出钢 过程 中不进行钢 水脱氧合金化操作 ,不添 加任 何顶渣渣料 ;出钢过程 中至吹氩 站均不吹氩 ;严格控制下 渣量,钢包顶渣渣层厚度 8 0 a r m。 R H精 炼工序:钢水进站 进行定氧、取样 ,根据钢 水含碳 量及氧含量和温度 ,在真空度低 于 1 5 0 mb a r 后 马上吹氧 ( 严格 控制),同时加入升温铝粒 ,脱碳与升温 同时进行 ,低真空循 环 脱碳;真空处理达到 8分钟后 ,进行脱氧合金化操作 ;钢水 处理结束 时进行顶渣改质 ,前 2罐据渣色 加入 高铝铝渣适量 , 其余连浇 炉次顶渣加入高铝铝渣 5 0 k e , / 炉。 3 . 2 双联工艺 双联 工艺路线 :铁水脱硫 扒渣 一转炉 一 L F精炼 炉一 R H 精炼炉一板坯连铸 转炉 工序 :出钢温 度控制 开浇 炉次 1 6 7 0 5 - 1 0 ℃,连 浇炉 次1 6 6 0 ±1 0 ℃,氩后 搬 出温度 开浇炉 次 1 5 9 5 ±1 0 ℃,连 浇炉 次1 5 8 5 ±1 0 ℃;出钢 过程 中不进行钢 水脱氧 合金化操 作, 出 钢3 , 4 时 加入 小 粒 灰 2 0 0k g / 炉 、精 炼 渣 3 0 0 k g / 炉 ;出钢 过 程至 吹氩站全 程吹氩 ;严格控 制下渣 量,钢包顶渣 渣层系统 R H精炼 中最核 心的设备是真 空泵 系统,一般选用水蒸 气 式的喷射器来抽真 空。它 的优 点有抽气量大、无过高的其他 因 素要求、可靠安全、操 作方便且使用 费用低廉 。当蒸汽 量少失 去平衡是 ,用水环泵来代替水蒸气喷射泵 的最后一级,能够 减 少消耗水蒸气 。 3 加 大环流速度和脱气面积 处理周期有严格的要求, 满足钢包 口径要求下设计 真空室, 尽最大 限度增大浸渍管和真 空室 的内径 。还应该适当的把环 流 的气体量增大 。 1 . 4 增加喂丝吹氨功能 根据钢种 的不 同要求 ,要改变钢水中存在夹杂物的形态, 可以在 R I - I 真 空冶 炼完 成后 ,再进行 一次喂 S i . C a 丝并 吹氩 搅 拌。 1 . 5 喷粉脱硫 有 部分钢 种对硫 含量 有着 一定 的要求 ,要 降低硫 在钢 液 中的含量 ,这样就要求 R H有脱硫 的功能 。但 因为某些原因 , R H的脱硫 效果不太 理想 ,所 以只作为补偿 手段使用 。 还有 因为铸机 的发展速度相 当快 ,一 台高效的连铸机无法 满足 单台的 R H连浇要求 ,这时可 以用不 同形式的双工位设计 来满足 ,即一套真空设备两个处理位 ,共用液压系统 ,两套顶 升装 置。 2 R H真空精炼技术 的优点 R H精炼炉利用 “ 二次燃烧 ”控制钢 水温度 ,脱碳后加 脱 氧合金化 的生产方式 ,按照单双 联工艺路线采取相应操作 。通 过工艺 改进 ,从而达 到控制 脱氧产物 A1 2 0 3及 时上浮提 高钢 水纯净度 ,保证过程温 度以及 降低脱氧合金消耗的 目的。 按传 统操作会在 出钢过程进行脱氧及合金化,而此时合金 的消耗较 高,也影响合金化合金的收得率 。为 了更好的提高合 金利用率 ,同时让 R I - I 更加合理控制钢水 中的碳和氧的含量 , 在 出钢后不进行脱氧及合金化操 作称其为 “ 裸钢操作 ”。它的 优 点有 :一是钢水 中有过剩 的氧可 以参与 R H炉脱碳反应和升 温操作 减少 R H炉吹氧量 ;二是因钢水中氧 含量较高,此时 加入合金其收得率低,此时不加入合金可 降低其消耗;三是因 不加脱氧 合金 ,可 以有效减 少钢水 中 A 1 2 0 3夹 杂量; 四是 钢 水 中溶解 的氧含量高,可有效增加钢水表面活性作用,降低 过 程吸氮 的机率 。 总之 ,通过 R H炉 的 “ 二次燃烧 ”可 以有效 降低钢水 中的
RH精炼技术的应用与发展
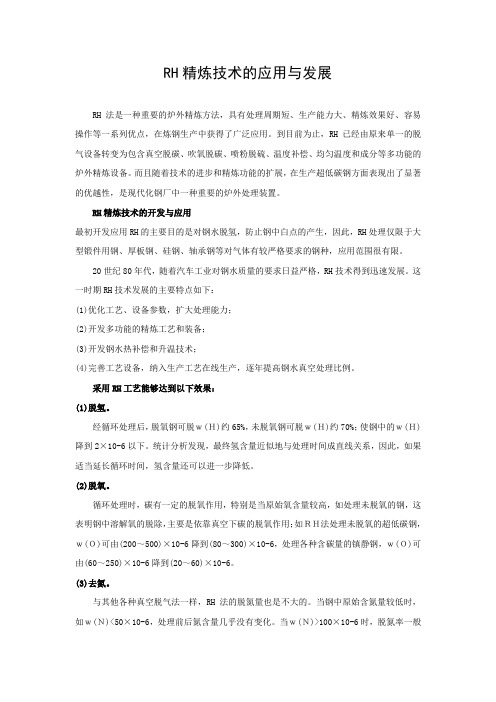
RH精炼技术的应用与发展RH法是一种重要的炉外精炼方法,具有处理周期短、生产能力大、精炼效果好、容易操作等一系列优点,在炼钢生产中获得了广泛应用。
到目前为止,RH已经由原来单一的脱气设备转变为包含真空脱碳、吹氧脱碳、喷粉脱硫、温度补偿、均匀温度和成分等多功能的炉外精炼设备。
而且随着技术的进步和精炼功能的扩展,在生产超低碳钢方面表现出了显著的优越性,是现代化钢厂中一种重要的炉外处理装置。
RH精炼技术的开发与应用最初开发应用RH的主要目的是对钢水脱氢,防止钢中白点的产生,因此,RH处理仅限于大型锻件用钢、厚板钢、硅钢、轴承钢等对气体有较严格要求的钢种,应用范围很有限。
20世纪80年代,随着汽车工业对钢水质量的要求日益严格,RH技术得到迅速发展。
这一时期RH技术发展的主要特点如下:(1)优化工艺、设备参数,扩大处理能力;(2)开发多功能的精炼工艺和装备;(3)开发钢水热补偿和升温技术;(4)完善工艺设备,纳入生产工艺在线生产,逐年提高钢水真空处理比例。
采用RH工艺能够达到以下效果:(1)脱氢。
经循环处理后,脱氧钢可脱w(H)约65%,未脱氧钢可脱w(H)约70%;使钢中的w(H)降到2×10-6以下。
统计分析发现,最终氢含量近似地与处理时间成直线关系,因此,如果适当延长循环时间,氢含量还可以进一步降低。
(2)脱氧。
循环处理时,碳有一定的脱氧作用,特别是当原始氧含量较高,如处理未脱氧的钢,这表明钢中溶解氧的脱除,主要是依靠真空下碳的脱氧作用;如RH法处理未脱氧的超低碳钢,w(O)可由(200~500)×10-6降到(80~300)×10-6,处理各种含碳量的镇静钢,w(O)可由(60~250)×10-6降到(20~60)×10-6。
(3)去氮。
与其他各种真空脱气法一样,RH法的脱氮量也是不大的。
当钢中原始含氮量较低时,如w(N)<50×10-6,处理前后氮含量几乎没有变化。
武钢RH多功能真空精炼技术开发
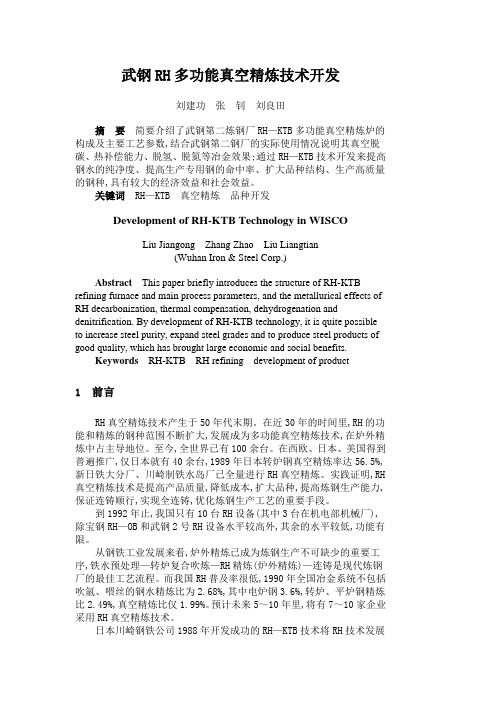
武钢RH多功能真空精炼技术开发刘建功张钊刘良田摘要简要介绍了武钢第二炼钢厂RH—KTB多功能真空精炼炉的构成及主要工艺参数,结合武钢第二钢厂的实际使用情况说明其真空脱碳、热补偿能力、脱氢、脱氮等冶金效果;通过RH—KTB技术开发来提高钢水的纯净度、提高生产专用钢的命中率、扩大品种结构、生产高质量的钢种,具有较大的经济效益和社会效益。
关键词RH—KTB 真空精炼品种开发Development of RH-KTB Technology in WISCOLiu Jiangong Zhang Zhao Liu Liangtian(Wuhan Iron & Steel Corp.)Abstract This paper briefly introduces the structure of RH-KTB refining furnace and main process parameters, and the metallurical effects of RH decarbonization, thermal compensation, dehydrogenation and denitrification. By development of RH-KTB technology, it is quite possible to increase steel purity, expand steel grades and to produce steel products of good quality, which has brought large economic and social benefits.Keywords RH-KTB RH refining development of product1 前言RH真空精炼技术产生于50年代末期。
在近30年的时间里,RH的功能和精炼的钢种范围不断扩大,发展成为多功能真空精炼技术,在炉外精炼中占主导地位。
最新RH真空精炼技术
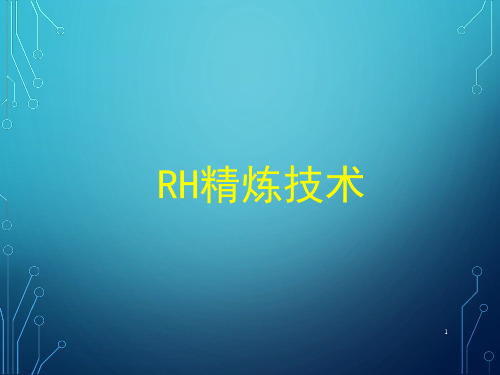
产品 热轧钢板 冷轧深冲钢板 镀层板,涂层板 锅炉板、桥梁板 造船板
产品 IF 钢 电工用钢 石油管线钢 低温用钢 超 深 冲4钢
5
特殊钢厂冶炼工艺路线
废钢
UHP
生铁
电炉
D R I/H B I
VD
轴轴承承钢钢
精炼
齿齿轮轮钢钢
优优质质弹弹簧簧钢钢
LF
大方
硬硬线线钢钢
精炼
坯连
帘帘线线钢钢
RH
铸
精炼
石石油油套套管管
RH精炼技术
__________________________________________________
1
现代纯净钢生产工艺流程
在纯净钢生产中,RH是最重要的真空精炼装置之一,
应用越来越广泛,新建钢厂多数选择RH精炼。 __________________________________________________
• 对钢水进行该钢种所必须进行的处理,(如脱氢处理,深
脱碳处理,轻处理,深脱氧处理等)。处理过程中真空度 和环流气体流量按各处理模式自动进行变换。
• 处理结束前再次测温取样,确认处理目的是否已达到。 • 合金微调及最终脱氧。 • 测温取样后关闭主真空阀,破真空。 • 钢包下降,座落到钢包台车,同时将环流气体切换成氮气。 • 钢包台车运行到喂丝工(加保温剂)位,按钢种要求喂丝,
2
钢
铁
冶
炼工艺Fra bibliotek路线 __________________________________________________
3
大型联合企业冶炼工艺流程
CAS-OB
板坯连铸
铁水脱硫 转炉复吹
RH钢水真空循环脱气装置的发展及现状

备如 上海重 型 机器 厂 和 大 冶 钢 厂 , 这两 台设 备处 理 的钢种 以电炉 冶炼 的合 金 结 构 钢 为 主 , 有 部分 轴 也 承 钢等 其它 钢种 。此 后 的很长 时 问 内 ,R H技 术在
RH q i m e ta o . e u p n th me
Ke r s: y wo d RH o a c c r u ain d g s i h d a l y t m ;er c o tra tp l n e; ic lto e a sng; y r u i s se r fa tr ma e l c y i
处理 , 以防止 钢 中 白点 的产 生 , 因而 R H仅 用 于处 理
2 11 R . . H—O B真 空 吹氧 技 术 ( 1 1 7 图 ) 9 2年 新 日铁 M rrn厂 依 据 V D法 生 产 不 锈 钢 的原 理 uoa O 开 发 了 R —O H B真 空 吹 氧技 术 ,顺 利 地 生产 出含 铬 不锈 钢 。之 后 新 日铁 Qt 在 此 基 础 上 发 展 了 i a厂
维普资讯
莱 钢科 技
第 4期 ( 总第 10期 ) 3
R H钢 水 真 空循 环 脱 气 装 置 的发 展 及 现 状
刘 凯, 陈宝堂 刘 凯 件 宗贤 朱振村 ( 改指挥部 ) 技
摘
性。
要: 阐述 了 R 钢 水 真 空精 炼技 术及设 备 的历 史 、 H 发展 及 现 状 , 绍 了几 种 主要 工 艺技 术 的特 点 和 介
对 气体 有较严 格要 求 的钢 种 , 大 型锻件用 钢 、 如 厚板 钢、 硅钢 及轴 承 钢 等 , 由此 造 成 R 应 用 范 围很 有 H
限 。上世纪 六 十 年 代 , 内也 曾引进 过 小 型 R 设 国 H
RH真空精炼技术的发展

RH 的发展历史
7
RH精炼技术是1959年德国Rheinstahl和Hutlenwerke公司联合开发成 功的。RH将真空精炼与钢水循环流动结合起来,具有处理周期短,生产 能力大,精炼效果好等优点,适合冶炼周期短,生产能力大的转炉工厂采
Hale Waihona Puke 用。RH发展到今天,大体分为三个发展阶段: (1)发展阶段(1968年~1980年):RH装备技术在全世界广泛采用。 (2)多功能RH精炼技术的确立(1980年~2000年):RH技术几乎达到
OD AOD
大板
脱磷 脱硫
坯连 铸
不锈钢
RH-
OB/
KTB
编辑课件ppt
6
短流程钢厂冶炼工艺路线
铁水 脱硫
废钢
转炉 电炉
CASOB
LF 炉
小方坯 连铸
各类建材 普碳钢 普通低合金钢 机械工程用钢 易切削钢
废钢 生铁 DRI/HBI
UHP 电炉
LF 精炼
薄板坯 连铸
编辑课件ppt
普通热轧板 冷轧板 镀层板
编辑课件ppt
RH装置示意图
9
RH处理钢水过程
• 钢水处理前,先将浸渍管浸入待处理的钢包钢水中。当 真空槽抽真空时,钢水表面的大气压力迫使钢水从浸渍 管流入真空槽内。(真空槽内大约0.67 mbar时可使钢水 上升1.48m高度)。与真空槽连通的两个浸渍管,一个为 上升管,一个为下降管。由于上升管不断向钢液吹入氩 气,形成气泡泵,使钢水从上升管进入并通过真空槽下 部流向下降管,如此不断循环反复。在真空状态下,流 经真空槽钢水中的氩气、氢气、一氧化碳等气体在钢液 循环过程中被抽走。同时,进入真空槽内的钢水还进行 一系列的冶金反应,比如碳氧反应等如此循环脱气精炼 使钢液得到净化。
降低RH真空精炼成本的工艺技术集成
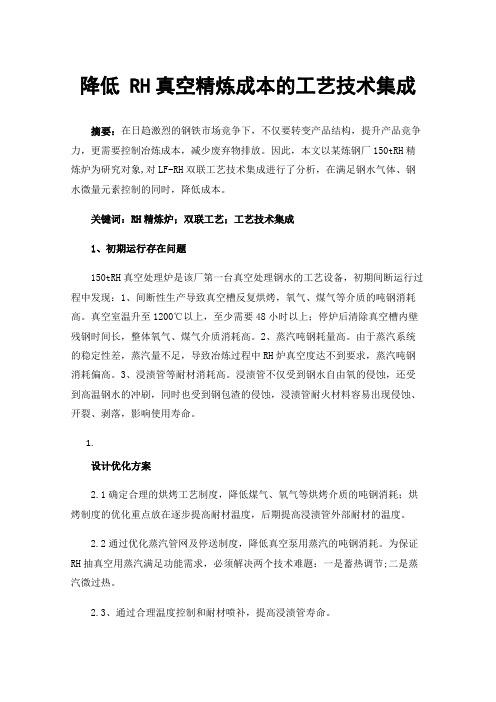
降低 RH真空精炼成本的工艺技术集成摘要:在日趋激烈的钢铁市场竞争下,不仅要转变产品结构,提升产品竞争力,更需要控制冶炼成本,减少废弃物排放。
因此,本文以某炼钢厂150tRH精炼炉为研究对象,对LF-RH双联工艺技术集成进行了分析,在满足钢水气体、钢水微量元素控制的同时,降低成本。
关键词:RH精炼炉;双联工艺;工艺技术集成1、初期运行存在问题150tRH真空处理炉是该厂第一台真空处理钢水的工艺设备,初期间断运行过程中发现:1、间断性生产导致真空槽反复烘烤,氧气、煤气等介质的吨钢消耗高。
真空室温升至1200℃以上,至少需要48小时以上;停炉后清除真空槽内壁残钢时间长,整体氧气、煤气介质消耗高。
2、蒸汽吨钢耗量高。
由于蒸汽系统的稳定性差,蒸汽量不足,导致冶炼过程中RH炉真空度达不到要求,蒸汽吨钢消耗偏高。
3、浸渍管等耐材消耗高。
浸渍管不仅受到钢水自由氧的侵蚀,还受到高温钢水的冲刷,同时也受到钢包渣的侵蚀,浸渍管耐火材料容易出现侵蚀、开裂、剥落,影响使用寿命。
1.设计优化方案2.1确定合理的烘烤工艺制度,降低煤气、氧气等烘烤介质的吨钢消耗;烘烤制度的优化重点放在逐步提高耐材温度,后期提高浸渍管外部耐材的温度。
2.2通过优化蒸汽管网及停送制度,降低真空泵用蒸汽的吨钢消耗。
为保证RH抽真空用蒸汽满足功能需求,必须解决两个技术难题:一是蓄热调节;二是蒸汽微过热。
2.3、通过合理温度控制和耐材喷补,提高浸渍管寿命。
1.制定措施及运行状况3.1、改进烘烤模型设置为新槽烘烤、真空槽化冷钢、旧真空槽预热三类烘烤模型,烘烤制度的优化重点放在逐步提高耐材温度,后期提高浸渍管外部耐材的温度。
一是浸渍管耐材的传热,内部烘烤温度升高后,通过传热来升高外部耐材的烘烤温度;另一个是外溢火焰的烘烤,通过在线烘烤顶枪氧煤比、流量、枪位的变化,让火焰从浸渍管下口溢出,对浸渍管外部耐材进行烘烤,获得良好的火焰外溢情况,是的浸渍管外部耐材的温度有了一定的提高。
RH炉外精炼用耐火材料发展现状和趋势(定稿)

RH炉外精炼用耐火材料发展现状和趋势王堂玺,李享成,姜广坤武汉科技大学耐火材料与高温陶瓷国家重点实验室培育基地,武汉430081摘要随着冶炼洁净钢的发展,炉外精炼主要用耐火材料发展迅速。
RH炉用耐火材料以前以镁铬砖为主,但由于环境污染,目前无铬耐材越来越受到耐火材料专业人员的重视。
本文结合我国钢铁行业尤其是不锈钢及特殊钢的发展,对炉外精炼用耐材发展和趋势进行分析。
关键词炉外精炼镁尖晶石刚玉尖晶石材料1、前言近年来,随着我国国民经济快速发展,不锈钢及其他特殊钢的需求增长很快,这对钢产品质量也提出了更高的要求。
据统计,2009年我国钢铁行业的粗钢产量为56784万吨,其中32家主要特殊钢企业的粗钢产量为7610.84吨(占13%),而世界上OECD国家的特殊钢占其钢总产量约15-22%,其中瑞典达到45%左右[1],预计我国未来的特殊钢生产仍有很大的发展空间。
不锈钢及其它特殊钢产品的生产工艺主要采用炉外精炼工艺。
经过几十年的发展,炉外精炼领域逐渐开发了DH、RH、AOD、VOD、LF、V AD、ASEA-SKF等技术,各种炉外精炼设备也不断涌现。
炉外精炼工况比较苛刻,耐火材料要具有高温强度高、在真空下体积稳定性好,耐冲刷、耐剥落性好、抗侵蚀性强等,目前国内外已经开发和使用了各种优质的炉外精炼用耐火材料。
2、RH炉外精炼用主要耐火材料2.1镁铬系耐火材料镁铬系耐火材料分直接结合镁铬砖、再结合和半再结合镁铬砖。
镁铬砖在炉外精炼炉如VOD、AOD以及RH浸渍管、真空室使用效果较好。
镁铬砖的损毁原因主要考虑熔渣渗入而使砖体变质引起的结构剥落。
目前,大部分国家限制使用镁铬砖,一方面是由于其中的铬会造成环境污染,另一方面价格相对镁尖晶石砖或刚玉尖晶石浇注料更高,再有我国《产业结构调整指导目录》(2007年本)也将“含铬质耐火材料生产线”列限制类生产项目。
2.2 镁锆系耐火材料镁锆系耐火材料主要为烧成镁锆砖。
镁锆砖在炉外精炼炉如RH浸渍管、真空室使用效果较好。
科技成果——RH精炼功能提升关键技术

科技成果——RH精炼功能提升关键技术技术开发单位北京科技大学所属领域钢铁冶金成果简介钢铁工业是我国国民经济的重要基础产业和实现工业化的支柱产业。
钢的高效化、洁净化、稳定化和智能化生产是钢铁企业生存和发展的方向。
钢铁生产过程中,根据钢种的不同,所采用的精炼工艺和设备也不同。
其中,RH真空精炼工艺具有高效、高洁净的生产特点,广泛应用于IF钢和硅钢为代表的冷轧钢种、管线钢为代表的热轧钢种、以及轴承钢为代表的特殊钢种的生产。
因此,提升RH真空精炼的效率和能力能够一方面缩短各高品质钢种的精炼时间,更好地与高拉速连铸相匹配,提升生产效率,另一方面能够更好地脱碳和去除夹杂物,提升产品质量,这两方面都能够给钢铁企业带来很好的效益。
根据几何相似和动力学相似建立了对应实际RH模型比例为1:5的RH物理模型。
利用PIV技术测量流场,示踪粒子选用空心SiO2微球,获得了RH水模型钢包和真空室内中心纵截面上的速度矢量分布,并根据速度场分布计算出对应的湍动能及其耗散率的分布;在RH水模型钢包内布置监测点,在加入示踪粒子(饱和NaCl溶液)的同时开始测量监测点处电导率的变化,获得电导率变化曲线后,将电导率变化在±5%之内的时间为混匀时间,密集布置监测点并多次重复测量,得到整个钢包中心纵截面上的混匀时间分布。
根据上述方法分别研究吹气流量、真空室压力、吹气孔数对RH内部流场特性及混匀状态的影响。
图1 项目技术方案在原物理模型基础上改变浸渍管的形状,分别设计两浸渍管均为椭圆管RH、两浸渍管中上升管为圆管下降管为椭圆管RH以及标准圆管对比RH水模型,研究浸渍管形状对流场特性及混匀状态的影响。
两浸渍管均为椭圆管时,能够增大液体的循环流量,降低钢包整体的混匀时间;当只改变下降管形状,选用椭圆管作为下降管时,能够起到增大钢水涌入真空室的速度同时降低钢水对钢包底部的冲击的效果。
通过工业实验,对某超低碳钢RH全精炼过程进行密集取样,分别取圆管和椭圆管RH冶炼的钢样分析,检测钢中碳含量。
冶金工业RH炼技术的发展

RH精炼技术的发展
2
现代纯净钢生产工艺流程
在纯净钢生产中,RH是最重要的真空精炼装置之一, 应用越来越广泛,新建钢厂多数选择RH精炼。
3
钢 铁 冶 炼 工 艺 路 线
4
大型联合企业冶炼工艺流程
5
特殊钢厂冶炼工艺路线
脱硫
6
短流程钢厂冶炼工艺路线
7
RH的发展历史
RH精炼技术是1959年德国Rheinstahl和Hutlenwerke公司联合开发成
RH装置示意图
9
RH处理钢水过程
• 钢水处理前,先将浸渍管浸入待处理的钢包钢水中。当 真空槽抽真空时,钢水表面的大气压力迫使钢水从浸渍 管流入真空槽内。(真空槽内大约0.67 mbar时可使钢水 上升1.48m高度)。与真空槽连通的两个浸渍管,一个为 上升管,一个为下降管。由于上升管不断向钢液吹入氩 气,形成气泡泵,使钢水从上升管进入并通过真空槽下 部流向下降管,如此不断循环反复。在真空状态下,流 经真空槽钢水中的氩气、氢气、一氧化碳等气体在钢液 循环过程中被抽走。同时,进入真空槽内的钢水还进行 一系列的冶金反应,比如碳氧反应等如此循环脱气精炼 使钢液得到净化。
1
提高循环流量和体积传质系数。如图,千叶厂RH最初的工况,脱碳速度
常数K = 0.1min-1。扩大上升管直径增加环流后,达到K= 0.15min-1。进一步改进
吹Ar方式使传质系数 k值增大,K= 0.2min-1。
2 提高抽气速率。定义RH真空系统的抽气速度常数R:R=-ln( / 0)/t (min-1)。 3 吹氧。采用KTB顶吹氧工艺,提高了RH前期脱碳速度,使表观脱碳速度常
数Kc从0.21min-1提高到0.35min-1。
RH精炼
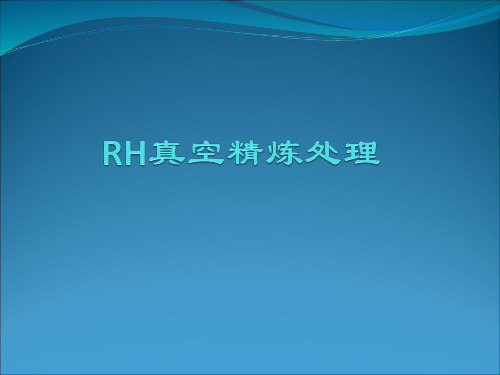
4.RH真空精炼的冶金功能
在短时间就可达到较低的碳、氢、氧含量;不用采 取专门的渣对策;可准确调整化学成分,Al,Si等合金收 得率在90~97%。汽车钢板以及电工钢等是RH钢生产的典 型产品。最初RH装置主要是对钢水脱氢,随着RH真空精炼 实践和精炼技术的发展,其冶金功能得到了充分的发展。
1)脱氢 可生产[H]≤0.00015%,延长钢水精炼时间,可使 [H]≤0.00010%。 2)脱碳 在20min处理周期内可生产出[C]≤0.002%的超低碳钢水。在脱碳过程 中,钢水中的碳和氧反应形成一氧化碳并通过真空泵排出。如钢中氧含量不够, 可通过顶枪吹氧提供氧气。脱碳结束时,钢水通过加铝进行脱氧。 3)脱氧 RH真空精炼后T[O]量可≤0.0020%,如和 LF法配合,钢水T[O]可降到 0.0010%以下。
近年来,我国钢铁企业普遍对钢水炉外精炼技术的应 用较为重视,投入大量资金上马先进的炉外精炼技术装备, 炉外精炼已经不再是特大型钢铁企业或特钢企业的专利品。 炉外精炼在提高钢材产品质量、扩大品种、提高炼钢生产 能力、保障连铸顺行、降低成本、优化炼钢生产工艺等方 面发挥着极其重要的作用,甚至成为限制环节。而RH真空 处理又是炉外精炼领域的一个突出典型。铁水预处理-转炉 复合吹炼(或电弧炉冶炼)-炉外精炼(LF、VD、VOD、RH)-连 铸,已成为越来越多的钢铁企业炼钢厂的典型流程模式。
3.在真空条件进行精炼,脱碳、脱氧、脱硫、合金化、净化钢质,减少 钢中非金属夹杂物,提高合金收得率,减小成分波动范围。冶炼出一 般平炉电炉转炉中作不能冶炼的钢种,为冶炼很多新钢种提供了一个 新的工艺。 4.RH真空精炼可以实现计算机自动控制,从而使其精炼工艺过程实现高 度的自动化。 5.由于双真空室设备和计算机自动控制的应用,使得RH真空精炼设备的 作业率大幅度提高,从而达到了LD—RH—CC三者配合连续作业。
RH精炼技术
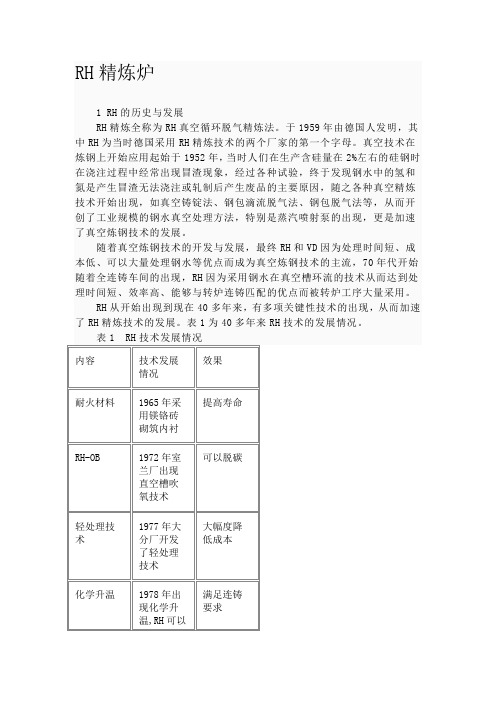
空槽内的钢水还进行一系列的冶金反应,比如碳氧反应等;如此循环脱气精炼使钢液得到净化。
经RH处理的钢水优点明显:合金基本不与炉渣反应,合金直接加入钢水之中,收得率高;钢水能快速均匀混合;合金成分可控制在狭窄的范围之内;气体含量低,夹杂物少,钢水纯净度高;还可以用顶枪进行化学升温的温度调整,为连铸机提供流动性好、纯净度高、符合浇铸温度的钢水,以利于连铸生产的多炉连浇。
3真空泵工作原理在工业炼钢生产中,现经常采用的抽真空设备主要有罗茨泵、水环泵和蒸汽喷射泵,其中以水环泵和蒸汽喷射泵最为常见。
1)水环泵工作原理水环泵中带有叶片的转了被偏心的与泵的壳体相配合,在泵体中装有适量的水作为工作液。
当叶轮顺时针方向旋转时,水被叶轮抛向四周,由于离心力的作用,水形成了一个决定于泵腔形状的近似于等厚度的封闭圆环。
水环的下部分内表面恰好与叶轮轮毂相切,水环的上部内表面刚好与叶片顶端接触(实际上叶片在水环内有一定的插入深度)。
此时叶轮轮毂与水环之间形成一个月牙形空间,而这一空间又被叶轮分成和叶片数目相等的若干个小腔。
如果以叶轮的下部0°为起点,那么叶轮在旋转前180°时小腔的容积由小变大,且与端面上的吸气口相通,此时气体被吸入,当吸气终了时小腔则与吸气口隔绝;当叶轮继续旋转时,小腔由大变小,使气体被压缩;当小腔与排气口相通时,气体便被排出泵外。
2)蒸汽喷射泵工作原理喷射泵是由工作喷嘴和扩压器及混合室相联而组成。
工作喷嘴和扩压器这两个部件组成了一条断面变化的特殊气流管道。
气流通过喷嘴可将压力能转变为动能。
工作蒸汽压强和泵的出口压强之间的压力差,使工作蒸汽在管道中流动。
在这个特殊的管道中,蒸汽经过喷嘴的出口到扩压器入口之间的这个区域(混合室),由于蒸汽流处于高速而出现一个负压区。
此处的负压要比工作蒸汽压强和反压强低得多。
此时,被抽气体吸进混合室,工作蒸汽和被抽气体相互混合并进行能量交换,把工作蒸汽由压力能转变来的动能传给被抽气体。
炼钢rh炉技术资料(第二期)
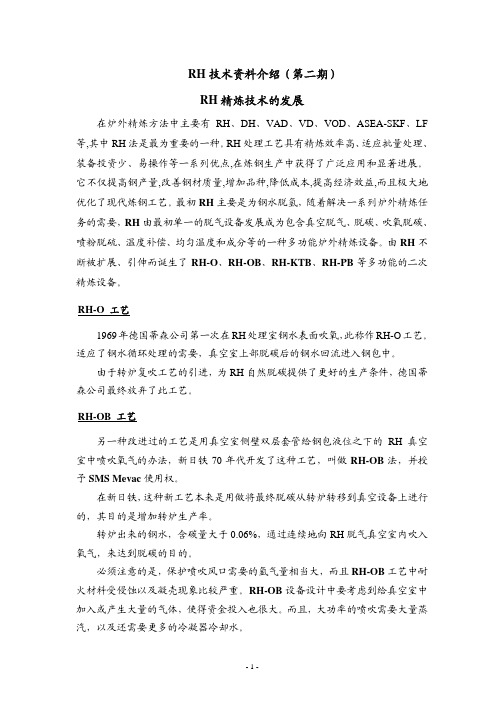
[H]<2ppm [N]<40ppm [O]<20~40ppm
原为钢水 脱氢开 发,短时 间内可使 [H] 降 到 远低于白 点敏感极 限以下
1972 年 新 日铁公司 名古屋厂
同 1,还可 同 1,并能 生 产 不 锈 吹氧脱碳、 钢,多用于 加热钢水 超 低 碳 钢
的生产
同 RH,并可使 终 点 [C] ≤ 35ppm
RH-O 工艺
1969 年德国蒂森公司第一次在 RH 处理室钢水表面吹氧,此称作 RH-O 工艺。 适应了钢水循环处理的需要,真空室上部脱碳后的钢水回流进入钢包中。
由于转炉复吹工艺的引进,为 RH 自然脱碳提供了更好的生产条件,德国蒂 森公司最终放弃了此工艺。
RH-OB 工艺
另一种改进过的工艺是用真空室侧壁双层套管给钢包液位之下的 RH 真空 室中喷吹氧气的办法,新日铁 70 年代开发了这种工艺,叫做 RH-OB 法,并授 予 SMS Mevac 使用权。
并申请专利。此顶枪系统使用脉冲气流,能对气体和固体的混合物进行喷吹;再
者,顶枪烧嘴可实现真空室耐材的加热与保温。
表 1 为几种 RH 真空精炼方法的持点比较。
表 1 RH 及多功能 RH 技术的特点
序 类型
号
1
RH
2 RH-OB 3 RH-PB(IJ)
代号意义
开发厂家 主要功能 适用钢种 处理效果
备注
开发了高级多功能顶枪系统。这些创新包括在高位置喷吹(称之为短枪),从而
减小了 RH 处理设施的高度。最近的创新表现在用同一套顶喷枪系统,结合现有
的技术开发其它工艺应用。
1995 年 1 月份比利时根特的 SIDMAR 公司,在其 RH 设施上使用了顶枪
- 1、下载文档前请自行甄别文档内容的完整性,平台不提供额外的编辑、内容补充、找答案等附加服务。
- 2、"仅部分预览"的文档,不可在线预览部分如存在完整性等问题,可反馈申请退款(可完整预览的文档不适用该条件!)。
- 3、如文档侵犯您的权益,请联系客服反馈,我们会尽快为您处理(人工客服工作时间:9:00-18:30)。
邱勤
宝钢工程技术集团有限公司
1.
近十年来国内RH真空精炼技术发展现状
2.
RH真空精炼技术的完善和发展
1 近十年来国内RH真空精炼技术发展现状
2009年在太钢召开 全国精炼年会。
2011年………
2007年在宝钢召开了 第一届RH年会。
中国RH真空装置增长趋势图
宝钢股份炼钢厂转炉分厂钢水RH真空精炼比
阀站照片
监控画面
监控画面
(2) 布置的多样化
布置工位 多样化
、双台车单工位、大包回转台 式 双工位:两车三位、两车四位、 三车五位、四车六位。
(3) 设备的适应性更强
整体槽、分体槽
单路、多路 小合金料仓的设计 不同真空料斗的设计 环流的控制
真空泵形式多样化
(4)研发的核心技术装备 大型真空泵 真空主阀 大吨位钢包 顶升技术 钢包提升装置 顶枪预热枪技术
“多功能 化”的充 分应用
进一步实 现高效化
如何在生产中不断优化RH工艺和设备将是今后重点工作
2 RH真空精炼技术的完善和发展
RH喷粉工艺、设备、控制技术完善 RH氮控制技术完善 耐火材料合理选择和开发
开发适应电炉厂的RH真空精炼设备
开发新的RH钢水热补偿升温技术
如何在生产中不断优化RH工艺和设备将是今后重点工作
1.1
RH真空精炼生产工艺技术的发展和应用推广
产品品种的变化, 质量的不断提高
RH真空精炼生产 工艺技术的发展 RH真空精炼生产 工艺技术的推广
1.2
RH真空精炼工艺和设备技术的开发和应用
1.2.1 RH真空精炼工艺设备设计的创新和发展 (1)功能的多样化 去除有害气体 脱碳 成分微调 脱硫 降低非金属夹杂物含量 钢水升温 协调转炉、连铸生产
可调的高温 视频监控装置
1.2.2 RH真空精炼控制技术的开发和应用
RH一体化阀站 RH过程控制 和模型
自动化系统
1.3 RH真空精炼设备制造技术和 耐火材料技术的开发和应用
RH真空精炼设备制造技术 RH真空耐火材料技术
2 RH真空精炼技术的完善和发展
动态模型 的完善和 应用
合理配置 设备
优化工艺、 设备参数, 节能降耗