螺纹车削方法[车削螺纹时常见故障及解决方法]
车削螺纹时常见故障及解决方法探讨
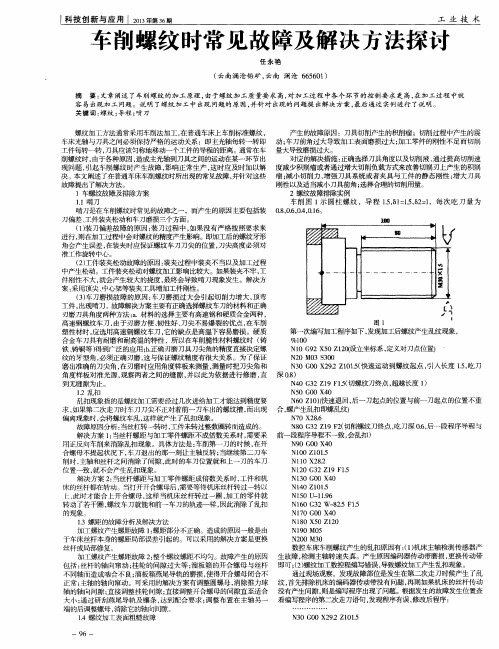
螺 纹加工 方法通 常采用 车削法 加工 , 在普 通车 床上车 削标准 螺纹 , 车床光轴与刀具之间必须保持严格的运动关系 :即主光轴每转一转即 工件每转 一转 , 刀具应 该匀称地 移动一个 工件 的导 程的距离 。通常在车 削螺纹 时 , 由于各 种原 因 , 造成 主光轴 到刀具 之间 的运动在某 一 环节 出 现 问题 , 引起 车削 螺纹 时产 生故 障 , 影 响正 常生 产 , 这时 应及 时加 以解 决。 本文阐述了在普通车床车削螺纹时所出现的常见故障, 并针对这些 故障提 出了解决方 法 。 1车螺纹 故障及排 除方案
1 . 1啃刀 8 0 . 6 , 0 . 4 , 0 . 1 6 。 啃刀是在 车削螺纹时 常见 的故障之一 ,而 产生 的原因 主要包括 装 0. 刀偏差 、 工件装夹 松动和 车刀磨损三个 方面 。
产生的故障原因:刀具切削产生的积削瘤;切削过程中产生的震 动; 车刀前 角过大 导致加 工表 面磨损过 大 ; 加工零 件 的刚性不 足 而切 削 量 大导致磨 损过大 。 对应 的解 决措施 : 正确选 择刀具 角度 以及切 削液 、 通过 提高 切削速 度减少积削瘤或者通过增大切削负载方式来改善切削刃上产生的积削 瘤; 减小 切削 力 、 增 强刀具 系 统或 者夹 具与 工件 的静 态 刚性 ; 增大 刀具 刚性 以及适 当减小 刀具前角 ; 选 择合理 的切 削用量 。 2螺 纹故障 排除实例 车削 图 1 示 圆柱 螺 纹 ,导 程 1 . 5 , 8 1 = 1 . 5 , 8 2 = 1 ,每 次 吃 刀 量 为
( 1 ) 装刀偏差故障的原 因: 装刀过程中, 如果没有严格按照要求来 进行 , 则 在加工过 程中会 对螺 纹的精度产 生影 响。即加工后 的螺纹牙 形 角会产 生误 差 , 在装 夹时应 保证螺 纹车 刀刀尖 的位置 , 刀 尖高度 必须 对 准工作 旋转 中心。 ( 2 ) 工件 装夹松 动故 障的原 因 : 装夹过 程 中装 夹不 当 以及加 工过 程 中产生松动 。工件装 夹松动对 螺纹加工 影响 比较 大。如果装夹不 牢 , 工 件 刚性不 大 , 就会 产生较 大的挠度 , 最终会 导致 啃刀现象 发生 。解决 方 案: 采用顶尖 、 中心架等装夹工具增加工件刚性。 ( 3 ) 车刀磨 损故 障 的原 因 : 车刀 磨损 过 大会 引起 切削 力增 大 , 顶 弯 工件, 出现啃刀。故障解决方案主要有正确选择螺纹车刀的材料和正确 刃磨刀具角度两种方法 : a . 材料的选择主要有高速钢和硬质合金两种 , 图 1 高速钢螺纹车刀, 由于刃磨方便、 韧性好 、 刀尖不易爆裂的优点 , 在车削 塑性材 时 , 应选用 高速 钢螺纹 车刀 , 它 的缺点是 高温下 容易磨 损 。硬质 第一次编 写加工程 序如下 , 发现 加工后螺 纹产生乱 纹现象 , %1 0 O 合金车 刀具有 耐磨 和耐高 温的特 ,所 以在车削 脆性材 料螺纹 时 ( 铸 铁、 铸铜等 ) 得 到广泛 的应用 l b . 正确 刃磨刀具 刀尖 角的精 度直接决 定螺 N 1 0 G 9 2 X 5 0 z l 2 0 c 没立坐标 系 , 定义对 刀点位置 ) ’ N2O M 03 S3 0 0 纹的牙型角 , 必须正确刃磨 , 这与保证螺纹精度有很大关系。为了保证 磨出准确的刀尖角 , 在刃磨时应用角度样板来测量 , 测量时把刀尖角和 N 3 0 C O O X 2 9 . 2 Z 1 0 1 . 5 ( 快 速运 动到 螺纹 起 点 , 引 入长 度 1 . 5 , 吃 刀 . 8 ) 角度样板对准光源, 观察两者之间的缝隙, 并以此为依据进行修磨 , 直 深 O N 4 0 G 3 2 Z 1 9 F 1 . 5 ( 切螺纹 刀终点 , 超越长 度 1 ) 到无缝 隙为止 。 N5 0 GO0 X4 0 1 . 2乱扣 乱 扣现象指 的是螺纹 加工需要 经过几 次进 给加工 才能达 到精度 要 N 6 0 z 1 0 l 决速退 回 , 后 一刀起 点的位 置与前 一刀起 点的位 置不 重 求, 如果第 二次 走 刀时车 刀刀尖不 正对着 前一 刀车 出的螺纹槽 , 而 出现 合 , 螺产生乱 扣即螺乱 纹) N7 0 X2 8 . 6 偏离 现象时 , 会将 螺纹车乱 , 这 样就产生 了乱扣现 象 。 N S 0 G 3 2 Z 1 9 F 2 ( 切削螺纹 刀终点 , 吃 刀深 0 . 6 , 后一 段程 序导程 与 故障原因分析: 当丝杠转一转时 , 工件未转过整数圈转而造成的。 解决方 案 1 : 当丝杆 螺距 与加 工零件 螺距 不成 倍数关 系 时 , 需要 采 前一段 程序导程 不一致 , 会乱 扣 ) N90 ( 0 X40 用正反向车削来消除乱扣现象 。具体方法是 : 车削第一刀的时候 , 在开 N1 00 Z1 01 _ 5 合螺母不提起状况下 , 车刀退出的那一刻让主轴反转 ; 当继续第二刀车 Nl 1 O X28 - 2 削时 , 主轴 和丝杆 之 间消除 了间隙 , 此 时的车刀 位置就 和上一 刀 的车刀 Nl 2 O G3 2 Z1 9 F1 - 5 位 置一致 。 就不 会产生乱 扣现象 。 N1 3 0 GO0 X4 0 解决 方案 2 : 当丝杆螺 距与加 工零 件螺 距成倍 数 关系 时 , 工件 和机 N1 4 0 Z1 01 . 5 床的丝杆都在转动。当打开开合螺母后 , 需要等待机床丝杆转过一转以 N1 5 0 U一1 1 . 9 6 匕 , 此 时才能 合上 开合螺 母 , 这样 当机 床丝 杆转 过一 圈 , 加工 的零 件就 N1 6 O G3 2 W— 8 2 . 5 F1 . 5 转动 了若干 圈 , 螺纹 车刀就 能和前 一车刀 的轨迹一 样 , 因此 消除 了乱扣 N1 7 0 G0 0 X4 0 的现象 。 Nl 8 O X5 0 Z1 2 0 1 - 3螺距 的故 障分析及解决 方法 N1 9 0 M05 加_ 丁螺纹产生螺距故障 1 : 螺距部分不正确。造成的原因一般是由 N2 0 0 M3 0 于车 床丝杆 本身 的螺距局 部误差 引起 的。可 以采 用 的解 决方 案是更换 数控 车床 车削螺纹 产生 的乱扣原 因有 : ( 1 ) 机床 主轴检测 传感 器 产 丝杆 或局部修复 。 检测主轴转速失真。产生原因编码器传动带磨损 , 更换传动带 加工螺纹产生螺距故障 2 : 整个螺纹螺距不均匀 。故障产生的原因 生故障, 包括 : 丝杆的轴向窜动; 挂轮的间隙过大等 ; 溜板箱的开合螺母与丝杆 即可 ; ( 2 ) 螺纹加工数控程编写错误, 导致螺纹加工产生乱扣现象。 通过现场观察 ,发现故障部位是发生在第二次走刀时候产生了乱 不同轴而造成啮合不良; 溜板箱燕尾导轨的磨损, 使得开合螺母闭合不 正常; 主轴 的轴 向窜动 。可采用 的解决 方案有 调整 圆螺 母 , 消 除推力 球 纹 , 首先排除机床的编码器传动带没有问题, 再则如果机床的丝杆传动 则是 编写程序 出现 了问题 。 根据 发生的故 障发生位 置查 轴的轴向问隙; 直接调整挂轮间隙; 直接调整开合螺母的间隙直至适合 没有产 生间 隙 , 发现程序有误 , 修改后程序 : 大小 ; 通 过研 刮燕尾 导轨 及镶 条 , 达到 配合要 求 ; 调整 布置 在 主轴 另一 看编写程序的第二次走刀语句, 端的后调整 螺母 , 消除 它的轴 向间隙 。 N3 0 G0 O X2 9 . 2 ZI O1 . 5 1 4 螺纹 加 _ 『 = 表 面粗 糙故障
车削螺纹时常见故障及解决方法

车削螺纹时常见故障及解决方法螺纹车削是机械加工中的一项重要工艺,常用于制作螺栓、螺母等产品。
在车削螺纹过程中,有时会遇到一些常见的故障,如螺纹断裂、螺纹毛刺等问题。
本文将针对这些常见故障,给出相应的解决方法。
一、螺纹断裂螺纹断裂是车削螺纹中最常见的故障之一,主要原因有以下几点:1. 切削量过大。
车削螺纹时,如果一次性切削量过大,容易导致螺纹切削力过大,从而造成螺纹断裂。
2. 车削速度过高。
车削速度过高,会使螺纹材料在车削过程中产生过热现象,从而影响螺纹强度,导致断裂。
3. 切削刃磨损严重。
切削刃磨损严重会导致螺纹车削时切削力不均匀,从而容易引起断裂。
解决方法:1. 合理控制切削量。
在车削螺纹时,应根据工件的材料和尺寸,选择合适的切削量,避免一次性过大的切削力。
2. 控制切削速度。
根据螺纹材料的硬度和热处理情况,选择合适的切削速度,避免过高的车削速度造成螺纹断裂。
3. 及时更换刀具。
定期检查和更换切削刃,保证切削刃的锐利度,避免因刀具磨损产生过大的切削力。
二、螺纹毛刺螺纹毛刺是车削螺纹常见的表面缺陷之一,主要原因有以下几点:1. 加工精度不高。
车削螺纹时,如果刀具偏斜、工件夹紧不稳定等,容易导致精度不高,从而产生毛刺。
2. 切削液不合适。
切削液在车削螺纹时起到冷却、润滑的作用,选用不合适的切削液容易造成毛刺。
3. 刀具磨损严重。
刀具磨损严重会导致切削力不均匀,从而产生毛刺。
解决方法:1. 提高加工精度。
在车削螺纹前,检查刀具和夹持装置,确保工艺参数设置正确,以提高加工精度。
2. 合理选择切削液。
根据螺纹材料的特性和切削条件,选择合适的切削液,保证切削液的冷却和润滑效果,减少毛刺。
3. 及时更换刀具。
定期检查和更换刀具,保证刀具的切削锋利度,减少切削力不均匀引起的毛刺问题。
三、螺纹尺寸不准确螺纹尺寸不准确是车削螺纹常见的质量问题之一,主要原因有以下几点:1. 刀具磨损不均匀。
刀具磨损不均匀会导致切削力不均匀,从而影响螺纹尺寸的精度。
关于数控车床螺纹车削的加工工艺常见问题分析及解决办法探讨

关于数控车床螺纹车削的加工工艺常见问题分析及解决办法探讨数控车床螺纹车削是机械加工中常见的一种工艺,常常用于制造螺纹连接件、螺纹轴等零部件。
在实际的加工过程中,经常会遇到一些常见的问题,这些问题不仅影响了生产效率,还可能导致产品质量不达标。
探讨数控车床螺纹车削的加工工艺常见问题及解决办法对于提高加工质量和效率具有重要意义。
一、加工过程中的常见问题分析及解决办法1、螺纹质量不达标螺纹质量不达标是数控车床螺纹车削中常见的问题之一。
造成这一问题的原因是多方面的,比如刀具磨损严重、切削参数设置不当、机床振动过大等。
针对这些问题,可以采取以下一些解决办法。
(1)定期更换刀具,确保刀具的切削性能;(2)合理设置切削参数,包括进给速度、主轴转速等,保证切削质量;(3)对机床进行定期维护,减小机床振动,改善加工质量。
2、芯部和头部连接不紧密螺纹加工中,芯部和头部连接不紧密会导致产品的质量问题。
这一问题可能是由于机床的刚性不够、夹具安装不稳等原因导致的。
对于这一问题,可以采取以下措施加以解决。
(1)提高机床的刚性,加强机床的支撑和固定;(2)优化夹具的设计和安装方式,确保夹具的稳定性;(3)增加刚性支撑,减小加工振动,保证连接的紧密性。
3、螺纹表面粗糙二、如何提高数控车床螺纹车削的加工效率除了解决加工过程中的常见问题外,提高数控车床螺纹车削的加工效率也是非常重要的。
以下是一些提高加工效率的方法。
1、优化切削参数合理设置切削参数,比如切削速度、进给速度、切削深度等,是提高加工效率的关键。
通过优化切削参数,可以达到快速而稳定的加工效果。
2、提高刀具和设备的使用寿命通过定期更换刀具、科学维护设备等方法,可以保证刀具和设备的良好状态,提高使用寿命,减少因刀具和设备磨损导致的停机次数,从而提高加工效率。
3、精心设计夹具和工装合理设计夹具和工装,确保工件的固定和稳定,可以有效地提高加工效率。
夹具和工装的设计应该考虑到工件的特性和加工过程的需要,从而提高加工效率。
浅谈螺纹车削原理及常见问题的解决办法

浅谈螺纹车削原理及常见问题的解决办法作者:李建军来源:《职业·下旬》2014年第08期摘要:用车削的方法加工螺纹,是常用的加工方法和车工的基本技能之一。
但是,在螺纹加工中,初学者往往因为操作不当,无法正确加工出所需要的螺纹。
本文对螺纹车削中出现的问题,提出了相应的解决办法。
关键词:螺纹车削原理故障解决办法一、螺纹的加工原理螺纹的加工方法很多,其中用车削的方法加工螺纹是目前常用的加工方法。
无论车削哪一种螺纹,车床主轴与刀具之间必须保持严格的运动关系:主轴每转一圈(即工件转一圈),刀具应均匀地移动一个导程的距离。
工件的转动和车刀的移动都是通过主轴的带动来实现的,从而保证了工件和刀具之间严格的运动关系。
二、常见故障原因及解决办法螺纹车削是机械加工中非常普遍而且又比较复杂的问题。
螺纹车削的要求要高于其他普通车削操作,车削时所产生的切削力一般较大。
车削螺纹时,由于螺纹升角的影响,引起切削平面和基面位置的变化,从而使车刀工作时的前角和后角与刃磨的前角和后角的数值不同,影响正常车削。
在车削螺纹时,若有一个环节出现问题,就会产生意想不到的后果,影响正常加工,这时应及时加以解决。
下面,笔者就对车削螺纹时最常见的故障谈谈自己的见解和解决办法。
1.啃刀和打刀(1)故障原因之一:车刀安装得过高。
车刀装夹过高,在切削时,由于工件与车刀之间产生的主切削力的作用,螺纹车刀刀尖受到工件压力而向下移动,从而使车刀被压到工件的最大外圆处,使本来车削不深的车刀越来越进入工件深处,从而车削深度变深,使工件与车刀之间的车削力进一步增大,造成啃刀或打刀现象。
解决方法:应及时调整车刀高度,使其刀尖与工件的轴线等高(可利用尾座顶尖对刀)。
(2)故障原因之二:工件装夹强度不够。
在车削螺纹时,工件与车刀主要产生的车削力是背向力(即切深抗力),与工件的直径方向一致,此时工件随时受到一个向外的力,这个力使工件随时有向外弯曲的趋势。
这样造成工件在车削时一边车削浅,一边车削深。
车削螺纹时常见故障及解决方法

车削螺纹时常见故障及解决方法在机械加工中,车削螺纹是一项基本技能。
然而,在操作过程中经常会发生一些故障,例如螺纹深度不够、刀具磨损过快等,这些问题会影响到加工效率和产品质量。
本文将介绍几种常见的车削螺纹故障及其解决方法。
1. 螺纹深度不够螺纹深度不够是一个常见而难以发现的问题,经常在现场加工中出现。
它通常是由于刀具高度不够或车削深度过浅引起的。
以下是解决该问题的方法:•提高刀具高度:可以通过增加支撑刀杆高度或调整刀具上的螺纹垫片来解决。
•增加车削深度:可以通过增加刀具与工件的接触时间或增加刀具超前量来解决。
2. 刀具磨损过快刀具磨损过快通常是由于切削速度太高或切削深度过大引起的。
如果您遇到这种问题,请参考以下建议:•降低切削速度:将切削线速降低到合适的范围内,通常介于5~20 m/min。
•降低切削深度:通过减少车削深度来降低切削负荷。
•更换高质量的刀具:选择具有高刚性和切削耐受性的刀具,可以显著提高刀具的使用寿命。
3. 螺纹折断或错位螺纹折断或错位通常是由于不当的刀具选择、不均匀的切削、机床闲置时间过长和工件内部缺陷引起的。
为了防止发生这种情况,请使用以下技巧:•选择合适的工具:使用专业用于螺纹车削的刀具,确保刀具的角度和尺寸正确。
•均匀切削:确保刀具与工件之间的接触均匀,并避免在工件周边产生太多的压力。
•机床保养:确保机床在加工前和加工后进行适当的保养,防止闲置过长,影响机床的性能。
4. 边角毛刺边角毛刺通常是由于刀尖磨损、粗糙的工件表面和不规则的车刀线轮廓等原因引起的。
如果您的工件出现边角毛刺,可以尝试以下措施:•更换刀具:将刀具钝化或磨损过度的刀具更换为新的刀具。
•改进车床设置:通过改变车床的速度、进给和角度等参数来改善车削表面的粗糙度。
•维护工件表面:对工件表面进行抛光、喷砂或磨削等操作,以改善表面质量。
5. 超出公差范围对于车削螺纹来说,公差范围非常重要。
如果您的工件超出了规定的公差范围,则可能会导致部件的不适合和效率低下。
普通车床螺纹车削常见故障及解决方法(三篇)

普通车床螺纹车削常见故障及解决方法1. 放松刀夹:在车削过程中,如果刀夹没有固定好,会导致刀具松动或者偏位,从而造成螺纹不良。
解决方法是检查刀夹固定螺母是否紧固,如果松动则重新固定。
2. 刀具磨损:长时间使用刀具会磨损,导致刀尖变钝,从而无法进行正常的车削。
解决方法是更换刀具,保持刀具的锐利度。
3. 机床不稳定:如果机床本身存在不稳定的问题,例如床身变形、主轴不平衡等,会导致螺纹加工时产生偏差。
解决方法是定期检测和调整机床,确保其稳定性。
4. 刀具与工件匹配不良:在螺纹车削过程中,刀具与工件的匹配也非常重要。
如果选用的刀具尺寸不合适,就会导致螺纹加工结果不理想。
解决方法是选择合适尺寸的刀具,确保刀具与工件的配合良好。
5. 刀具进给速度不恰当:刀具进给速度过快或者过慢都会影响螺纹加工的质量。
解决方法是根据不同的工件材料和螺纹规格,调整刀具的进给速度,确保加工的质量。
6. 冷却液不适用:在螺纹车削过程中,适当使用冷却液可以降低温度,减少摩擦,提高切削润滑效果,从而改善加工质量。
如果使用的冷却液性质不合适,也会影响螺纹加工结果。
解决方法是选择合适的冷却液,根据加工工件的要求进行选择。
7. 机床刚度不足:机床刚度不足会导致在螺纹车削过程中产生振动和共振,造成螺纹不良。
解决方法是增加机床的刚度,例如加强机床床身的结构,增加加工时的稳定性。
8. 机床零件磨损:长时间使用机床,有些零部件会磨损,例如导轨、导向轨等,会导致加工误差。
解决方法是定期检查和更换机床零部件,保证机床的准确性和稳定性。
总之,普通车床螺纹车削常见故障的解决方法就是:确保刀具的固定和锐利度,稳定机床的结构和性能,选择合适尺寸和质量的刀具,调整进给速度和冷却液的使用,定期检查和维护机床零部件,确保加工质量和效果。
普通车床螺纹车削常见故障及解决方法(二)车床螺纹车削是机械加工中常见的一种加工方式,常用于制作螺纹零件。
然而,在车削过程中,可能会遇到一些常见的故障。
普通车床螺纹车削常见故障及解决方法

普通车床螺纹车削常见故障及解决方法普通车床螺纹车削的常见故障及解决方法非常多,下面将就其中一些常见的故障进行详细介绍:1. 刀具折断:刀具折断是螺纹车削中最常见的故障之一。
主要原因可能是材料刀具的材质不合适、刃口磨损过度、刀具固定不牢等。
解决方法如下:a. 检查刀具的材质是否符合加工材料的要求,选择合适的刀具材质。
b. 定期磨刃,控制刃口磨损程度,确保刀具刃口的锋利度。
c. 确保刀具夹紧牢固,避免刀具松动。
2. 尺寸偏差:尺寸偏差是指车削零件的尺寸与设计要求的尺寸之间的差异。
尺寸偏差可能是由于夹具不稳定、车刀与工件之间的间隙过大、车刀刃口圆周度不好等原因造成。
解决方法如下:a. 检查夹具的夹持是否稳定,并采取稳定的夹持方式。
b. 调整车刀与工件之间的间隙,确保刀具能充分切削工件。
c. 定期磨刃,提高车刀刃口的圆周度。
3. 表面粗糙度不合格:表面粗糙度不合格是指车削零件表面的光洁度不符合设计要求。
造成表面粗糙度不合格的原因主要有切削速度不合理、进给速度不合理、刀具磨损等。
解决方法如下:a. 调整切削速度和进给速度,选择合适的加工参数,提高车削效率和表面质量。
b. 定期更换刀具或磨刃,保持刀具的锋利度。
4. 异常声音:车削过程中出现异常声音通常是由于机床轴承损坏、切削过程中刀具碰撞工件等原因造成的。
解决方法如下:a. 检查机床轴承的使用情况,确保轴承正常工作。
b. 调整切削过程中刀具与工件之间的间隙,避免刀具碰撞工件。
c. 定期对机床进行维护保养。
5. 螺纹无法加工出来:可能的原因包括进给速度过慢、螺纹刀具选择不合适、车削槽设计不合理等。
解决方法如下:a. 调整进给速度,确保切削过程中刀具与工件的相对运动速度达到要求。
b. 选择合适的螺纹刀具,确保刀具能够正确切削螺纹。
c. 对车削槽进行重新设计,确保槽形符合螺纹加工要求。
以上仅是螺纹车削中一些常见的故障及解决方法,实际情况可能因不同的车削工艺和加工材料而有所不同。
车削螺纹时常见故障及解决方法

车削螺纹时常见故障及解决方法摘要:本人主要介绍分析了车削螺纹时螺纹表面粗糙故障、中径不正确故障、螺距故障、乱扣故障、啃刀故障等几种常见故障并提出了针对性的解决方法。
关键词:车削螺纹常见故障中图分类号:th16 文献标识码:a 文章编号:1672-3791(2012)11(a)-0075-01机械制造业中,经常使用带螺纹的零件。
对带螺纹零件的加工,目前最常用的方法就是车削。
一般情况下,使用卧式车床进行带螺纹零件的加工处理时,卧式车床可以加工出不同类型以及标准的螺纹零件。
但是不管使用车削螺纹技术进行哪种类型或者标准的螺纹零件的加工制作,在进行加工制作的过程中,都需要对于车床的主轴以及车床刀具之间的运动距离关系,保持车削螺纹时,车床的主轴每转动一圈时,车床刀具的运动情况是均匀移动一个导程距离。
在进行车削螺纹加工制作时,车床主轴与车床刀具之间的运动关系主要是车削螺纹加工时,车床主轴运动带动整个车床工件同时进行运转工作,并且车床运转的过程中,通过车床运转工作的带动影响,由车床的进给箱的变速运转控制,通过车床丝杠与车床溜板箱之间的配合,最终通过车床的开合螺母与车床刀具之间的带动运转作用,实现车床主轴与车床刀具之间的车削螺纹零件的加工制作运转关系。
在车削螺纹时,需要进行注意的是,由于车削螺纹过程中会受到一些影响因素对于车床螺纹零件制作加工的影响,导致车削螺纹零件加工制作过程中出现一些故障问题,不仅对于车削螺纹的正常加工制作过程会产生一定的影响,还会对于车削螺纹零件的质量造成一定的影响。
因此,在进行车削螺纹加工制作时,应注意结合车削螺纹加工制作实际,对于车削螺纹过程中的故障问题进行处理避免,以保证车削螺纹加工制作质量。
1 车削螺纹啃刀故障问题及解决方法在进行车削螺纹加工制作过程中,出现啃刀故障主要是因为车削螺纹时的车床车刀在安装过程中,由于过高或者过低的不正确安装,导致车床进行螺纹零件加工制作过程中,出现车床车刀的工件装夹不牢固或者是车床车刀出现严重的磨损问题,对于车削螺纹的正常运转以及加工会产生很大的影响。
车削螺纹时的故障判断及解决方法

8 O・
科 技 论 坛
车 削螺纹时 的故 障判 断及解 决方法
谭跃峰 赵宝云Leabharlann 程晓 龙 ( 北方华- A  ̄ - . r . - &集 团有限公司机械加工厂, 黑龙江 齐齐哈 尔 1 6 1 0 4 6 ) 摘 要: 经过本人 多年在理论与 实践中积 累的经验 , 发现 了一 系列的车削螺纹时故障的判 断方 法以及对应的解决方式 , 希望此文章可 以辅导青工及新 工的理论和 实践操作技能 , 提 高螺纹加工质量及 经济效益。 关键词 : 车 削螺纹; 故障分析; 解决方法 不正确 :原因是 由于车床丝杆本身 的螺距局部误差 ( 一般 由磨损引 在北方华安集 团飞速发展 的的今天 ,我车间承担某产品螺纹部 起 ) 。可更换丝杆或局部修复 。 分的机加任务。由于现有设备大部分老化 , 青工和新工 的大量加入 , 螺纹全长螺距不均匀原 因: 丝杆的轴 向窜动 ; 主轴的轴 向窜动; 溜 理论知识不足实践工作经验较低 , 在螺纹工件加工时常出现扎刀、 乱 板箱 的开合螺母与丝杆不 同轴而造成啮合不 良;溜板箱燕尾导轨磨 扣、 螺距不正确 、 螺纹表面粗糙度 等一些 问题 ( 其 中以扎刀现象较为 损而造成开合螺母闭合时不稳定 ; 挂轮间隙过大等。通过检测 ; 如果 严重 ) , 刀具消耗过大 , 工件次品、 废 品率高 , 次品率约为 1 0 %, 废品率 是丝杆轴向窜动造成的 ,可对车床丝杆与进 给箱连接处的调整圆螺 约5 %, 造成很大的经济损失 , 大大降低了生产效率和经济效益。 母进行调整 , 以消除连接处推力球轴承轴向间隙 ; 如果是主轴轴 向窜 2提高质量的必要性 动引起的 ,可调整主轴后调整螺母 ,以消除后推力球轴承的轴 向间 2 . 1 公司生产规模扩大后 , 机加设 备投 入相对较少 , 大部分设备 隙 ; 如果是溜板箱的开合螺母 与丝杆不同轴 而造成啮合不 良引起的 , 老化 , 加工精度下降 , 生产压力很大。 可修整开合螺母并调整开合螺母间隙 ; 如果是燕尾导轨磨损 , 可配刮 2 . 2急需 在生产实践 中快速培训提高青新工车削加工的理论和 燕尾导轨及镶条 , 以达到正确的配合要求 ; 如果是挂轮 间隙过 大 , 可 操作技能 , 提高生产效率 , 确保公司各单位备品备件及急件维修任务 采用重新调整挂轮间隙。 完成。 出现“ 竹节纹” 原 因: 从主轴到丝杆之间的齿轮传动有周期性误差 2 - 3保证员工的操作安全 ,确保 岗位安全生产责任制 目标的实 引起 的。如挂轮箱 内的齿轮 , 进给箱 内齿轮 由于本身制造误差 、 局部 现。 磨损或齿轮在轴上安装偏心等造成旋转精度低 ,从而引起丝杆旋转 3车削螺纹常见故障及解决方法 周期性不均匀 , 带动刀具移动的周期 性的不均匀 , 导致“ 竹节纹” 的出 以普通车床为例 , 介绍了车削螺纹中的常见故障及解决方法 。 分 现。可以修换有误差或磨损的齿轮 。 别介绍了啃刀 、 乱扣 、 螺距不正确 、 中径不正确 和螺纹表面粗糙等常 3 . 4中径不正确的故 障分析及解决方法 见故障现象 , 并分析 了其产生的原 因及解决方法 。 故 障阐发 : 精车时要详细检查刻度盘是否松动 , 精车余量要适当 , 3 . 1 啃刀 的故障分析及解决方法 车刀刃 口要锋利 , 要及 时测量。螺纹中径常用螺纹量规测量。同时要 啃刀是在车削螺纹时常见的故障之一 ,而产生这些故障的原 因 正确 的使用螺纹量规 , 才能得 到正确的中径测量值。 通常有三种 : 装刀偏差 、 工件装夹不牢或车刀磨损过大 。在本节中分 3 . 5 螺纹表面粗糙的故障分析及解决方法 析了啃刀故障产生的原 因及相应的解决方法。 螺纹表面粗糙度值大的原因 : 刀尖产生积屑瘤 ; 刀柄 刚性不够切 第一种故障情况是装刀偏差对螺纹精度 的影响及解决方法。在 削过程产生振动 , 车刀纵 向前角太大 , 中滑板丝杆螺母 间隙大产生扎 车削加工的过程中 , 车刀的安装应严格按照要求操作 , 因为螺纹车刀 刀 ; 高速钢切削螺纹时, 切削厚度太小或切 屑向倾斜 方向推出 , 拉毛 的安装是否正确对螺纹精度会产生一定影响。 如果装刀有偏差 , 即使 已加工牙侧 的表面 ; 工件刚性差 , 且切削用量过大; 车刀面粗糙 。 螺纹车刀刀具 十分准确 , 加 工后 的螺纹牙形角仍会产生偏差 , 因此 , 解决方法是 : 如果是积屑瘤引起的 , 应适 当调整切削速度 , 避开积 在安装车刀时应用样板校正螺纹车刀刀尖 的位置 ,刀尖高度必须对 屑瘤产生 的范 围; 用高速钢刀切削时 , 适 当降低切 削速度 , 并正确选 准工作旋转 中心。车刀安装得过高 , 使刀具实际后角减小 , 则吃刀到 择切削液 ; 用硬质合金 车螺纹时 , 应适 当提高切削速度 。增加刀柄 的 定深度 时, 车刀 的后刀面顶住工件 , 增大摩擦力 , 甚至把工件顶弯 , 截面积并减小刀柄伸出的长度 , 以增加车刀的刚性 , 避免振动。减小 造成扎刀现象 ; 车刀安装得 过低 , 使刀具实际前角增大 , 则切屑不易 车刀径 向前角 , 调整中滑板丝杠螺母 , 使其间隙尽可能最小。高速钢 排出 , 造成扎刀。 切削螺纹时 , 最后一刀 的切屑度一般要大于 0 . 1 mm, 并使切屑沿垂直 第二种故障工件装夹不牢。工件 自己的刚性不能承受车削时的 方向排出 , 以免切屑接触 已加工表面。 另外 , 选择合理的切削用量 。 刀 车削力 ,因而产生过大 的翘度 ,从而改变了车刀与工件的 中心高度 具切削刃 口的表面粗糙 度要 比螺纹加工表面 的粗糙度小 2 - 3 档次 , ( 工件被抬高 了) , 形成 切削深度 的突增 , 出现啃刀现象 , 此时应把工 砂轮刃磨车刀完后要用油石研磨。总的来说就是 , 正确修正砂轮或用 件装夹牢 固, 可使用尾座顶尖等 , 以增加工件 的刚性 。 油石精研 刀具 ; 选择适 当切削用量和冷却液 ; 调 整车床大拖板压板 、 第三种故障状况是车刀磨损过大 。引起切削力增大 , 顶弯工件 , 中、 小拖板燕 尾导轨的镶条等 , 保证各 导轨 间隙的准确性 , 防止切削 出现啃刀 , 这时就应对车刀进行刃磨 。同时也可以选择优质 的合金 , 时产生振动 ; 减小 车刀纵 向前角 , 调整 中拖板丝杆螺母 间隙 , 防止 出 以增加刀具的耐磨度 , 减少 啃刀现象的发生 。 现扎刀现象。 3 . 2乱扣 的故障分析及解决方法 3 . 6 螺纹角度误差过大的故障分析及解决方法 避免 “ 乱扣” 。当第一条螺旋线车好以后, 第二次进刀后车削, 刀尖 故障阐发 : 原因是车刀刃磨角度与工件要求不一致所造成的。 不在原来 的螺旋线( 螺旋桩) 中, 而是偏左或偏右, 甚至在牙顶 中间 , 将 解决方法是 : 正确刃磨刀具角度 , 同时用对刀板仔细检察 。 同时我 螺纹车乱这个现象 就叫做“ 乱扣现象 ” 。预防的方法是采用倒顺车法 们也可以直接选用数控成型刀片来加工工件 ,这样就不需要 刃磨刀 车削。在车削时应该注意若车削途 中刀具损坏或者无意提起开合螺 具 , 消除了刃磨带来的刃磨误差 , 同时也可以提高生产效率 。 母时 , 应该注意及 时对刀。 根据我多年 的实践经验已及查阅参考《 车工实用技术手册》 《 车工 采用打开开合螺母进行螺纹加工时必须注意以下两点 :要求车 工艺学》 等资料 , 通过对螺纹加工缺陷分析 , 并总结提出解决方法 , 消 削车床丝杠螺距与工件螺距 比值成整倍数的螺纹 ,同时也要对开合 除了螺纹加工中的诸多缺陷,同时又言传身教地辅导 了青工的实际 螺母镶条 的间隙做适当的调整 。 这对螺纹加工的质量才能保证 , 丝杠 操作 , 提高了青工的操作技能 , 使螺纹加工质量大 幅度提高( 9 8 . 7 %以 也较安全 。 上) , 降低生产成本 , 保证了车 间生产任务的正常完成 。 3 . 3螺距不正确的故障分析及解决方法 参考文献 总体原 因有两个 : ①螺纹全长不正确 : 原 因是挂轮搭配不当或进 【 1 】 车工实用技术手册[ M ] . 南京 : 江苏科学技 术出版社. 给箱手柄位置不对 , 可重新检查进给箱手柄位置或验算挂轮。②局部 [ 2 ] 车工工艺学[ M】 . 北京 : 机械工业 出版社.
车削螺纹时常见故障及解决方法

车削螺纹时常见故障及解决方法车削螺纹是机械加工中常用的一种加工方法,用于制作螺纹管、螺纹孔等零件。
然而,在车削螺纹的过程中,常会遇到各种故障,如螺纹形状不符合要求、螺纹表面粗糙等问题。
本文将介绍车削螺纹常见的故障及解决方法。
1. 螺纹形状不符合要求螺纹形状不符合要求是车削螺纹中最常见的问题之一。
原因可能是刀具刃磨不良、刀具进给过快、车床导程不准确等。
解决方法:- 检查刀具刃磨情况,确保刀具的切削刃锋利。
- 调整刀具的进给速度,过快的进给速度会导致螺纹形状不准确。
- 检查车床导程是否准确,必要时进行校准。
2. 螺纹表面粗糙在车削螺纹的过程中,螺纹表面可能会出现粗糙现象,影响螺纹的质量。
解决方法:- 检查车床的切削液供给情况,确保切削液充足,能够起到降温和润滑的作用。
- 调整刀具的进给速度和切削速度,过高的进给速度和切削速度会导致表面粗糙。
- 检查刀具的刃磨情况,确保刀具的刃口尖锐。
3. 刀具刃口出现龟裂刀具刃口出现龟裂是一种常见的故障,会导致螺纹表面的质量下降。
解决方法:- 检查刀具刃口是否过热,过热会导致刃口的变质,进而出现裂纹。
- 调整刀具的进给速度和切削速度,过高的进给速度和切削速度会增加刀具的磨损和热量积聚。
- 使用高质量的刀具,避免刃磨不良或材质不合格的刀具。
4. 螺纹深度不均匀螺纹深度不均匀可能是由于车削过程中切削刃与工件之间的接触不均匀或车床导程不准确导致的。
解决方法:- 检查车床导程是否准确,必要时进行校准。
- 检查刀具刃口的磨损情况,确保切削刃的锋利度和接触面积。
- 调整进给速度和切削速度,使切削刃与工件的接触更加均匀。
5. 刀具与工件之间出现卡紧现象卡紧现象在车削螺纹中比较常见,可能是由于切削刃与工件之间的接触不良或刀具位置不正确导致的。
解决方法:- 检查切削刃与工件的接触情况,确保切削刃能够顺利进入工件。
- 调整刀具的位置,确保切削刃与工件之间的接触面积足够。
总之,在车削螺纹的过程中,经常会遇到各种故障。
螺纹车削常见问题及解决方法

动 。b 主轴 的轴 向窜 动 。c溜 板 箱 的开 合 螺母 与 丝 杠不 同 . . 轴 而 造 成 啮合 不 良。 . d 溜板 箱 燕 尾 导轨 磨 损而 造 成 开合 螺
母 闭合 时不 稳 定 。e挂 轮 间 隙过 大等 。 .
刀 。此 时 , 及 时调 整 车 刀 高 度 , 其 刀 尖 与 工 件 的轴 线 应 使
过 一 转 时 , 件转 了整 数 倍 , 刀就 能 进 入 前 一 刀 车 出 的 工 车 螺 旋槽 内 , 就不 会 出现 乱 扣 , 样 就 可 以采 用 打 开 开合 螺 这
障 , 响正 常 生 产 , 时 应 及 时 加 以 解 决 。 车 削 螺纹 时 常 影 这
见 故 障及 解 决 方法 如 下 : 1 啃 刀 故 障分 析 及 解 决方 法 原 因是 车 刀
等高 ( 可利 用 尾座 顶 尖 对 刀 ) 。在 粗 车 和半 精 车时 , 尖 位 刀 置 比工 件 的 中 心 高 出 1 D左 右 ( 表示 被 加 工 工 件 直 % D
的。
的零 件 应 用 得 十分 广 泛 。用 车削 的方法 加 工 螺纹 , 目前 是 常用 的加 工 方 法 。在 卧式 车 床 ( C 6 4 如 A 10)上 能 车 削 米
制 、 寸 制 、 数 和径 节 制 四 种 标 准 螺 纹 , 论 车 削 哪 一 英 模 无 种螺 纹 , 车床 主轴 与 刀 具 之 间必 须 保 持严 格 的关 系 : 主 即
工 艺 与 装 备
4 1
螺纹 车 削 常见 问题 及 解决 方法
高 进 李 子 震
( 南 重工 股 份 有 限公 司 , 南 2 0 0 济 济 5 19)
摘 要 : 文 对 螺 纹车 削常见 问题 及 解决 方 法方 面进 行 了简单介 绍 , 本 文章 中 的许 多 内容 都 是 些 概要 性 的解
车削螺纹时的故障及解决措施
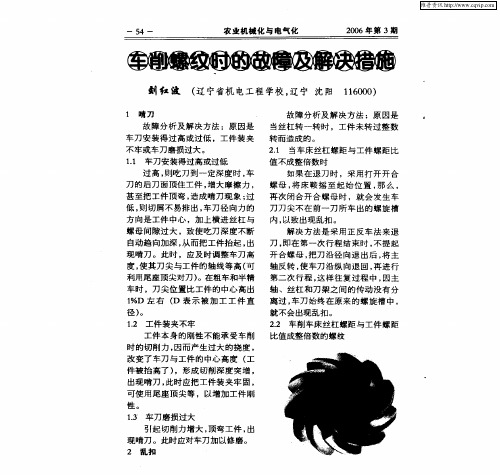
一
5 4一
农 业机 械 化 与 电 气 化
20 0 6年 第 3期
刘 红 波 ( 辽宁省机 电工程学校, 辽宁 沈阳 160) 100
1 啃 刀
故 障 分 析 及 解 决方 法 :原 因 是
故 障 分 析 及 解 决 方 法 :原 因 是 当 丝 杠 转 一 转 时 ,工 件 未 转 过 整 数
性。
1 车 刀 磨Байду номын сангаас 过 大 . 3
引起 切削力增大 , 弯工件 , 顶 出 现 啃 刀 。此 时 应 对 车刀 加 以修 磨 。
2 乱 扣
维普资讯
2 0 第 3期 0 6年
农业 机 械 化 与 电气 化
一5 5一
工 件 和 丝 杠 都 在 旋 转 ,提 起 开
( ) 果 是 挂 轮 间 隙 过 大 , 重 5如 可 用打开开合螺母 , 手动退 刀。这样退 刀快 ,有利于提 高生产率 和保持丝 新调整挂轮间隙 。 杠精度 , 同时 丝 杠 也 较安 全 。
3 螺 距 不正 确
34 出现 竹 节 纹 . 原 因 是 从 主 轴 到 丝杠 之 间 的 齿
径 ) 。
就 不会 出现 乱 扣 。 22 车 削 车 床 丝 杠 螺 距 与 工 件 螺 距 . 比值 成 整 倍 数 的 螺 纹
1 工件 装 夹不 牢 . 2
工件本 身的刚性不能 承受车 削 时的切削 力 , 因而产 生过 大的挠 度 ,
改 变 了 车 刀 与 工 件 的 中心 高 度 ( 工 件被 抬高了 ) ,形成 切削深度 突增 , 出 现 啃 刀 , 时 应把 工 件 装 夹 牢 固 , 此 可 使 用 尾 座 顶 尖 等 , 以增 加 工 件 刚
车削加工中常见的问题及解决方法
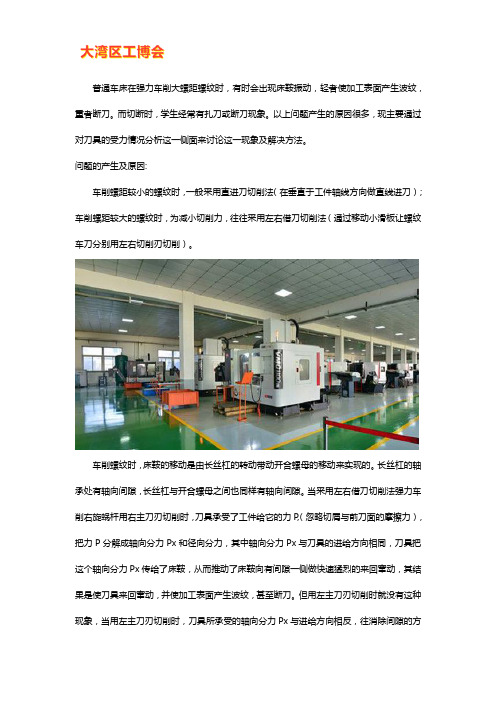
普通车床在强力车削大螺距螺纹时,有时会出现床鞍振动,轻者使加工表面产生波纹,重者断刀。
而切断时,学生经常有扎刀或断刀现象。
以上问题产生的原因很多,现主要通过对刀具的受力情况分析这一侧面来讨论这一现象及解决方法。
问题的产生及原因:车削螺距较小的螺纹时,一般采用直进刀切削法(在垂直于工件轴线方向做直线进刀);车削螺距较大的螺纹时,为减小切削力,往往采用左右借刀切削法(通过移动小滑板让螺纹车刀分别用左右切削刃切削)。
车削螺纹时,床鞍的移动是由长丝杠的转动带动开合螺母的移动来实现的。
长丝杠的轴承处有轴向间隙,长丝杠与开合螺母之间也同样有轴向间隙。
当采用左右借刀切削法强力车削右旋蜗杆用右主刀刃切削时,刀具承受了工件给它的力P,(忽略切屑与前刀面的摩擦力),把力P分解成轴向分力Px和径向分力,其中轴向分力Px与刀具的进给方向相同,刀具把这个轴向分力Px传给了床鞍,从而推动了床鞍向有间隙一侧做快速猛烈的来回窜动,其结果是使刀具来回窜动,并使加工表面产生波纹,甚至断刀。
但用左主刀刃切削时就没有这种现象,当用左主刀刃切削时,刀具所承受的轴向分力Px与进给方向相反,往消除间隙的方向运动,这时床鞍做匀速运动。
切断时,中滑板的移动是由中滑板丝杠的旋转带动螺母的移动来实现的,丝杠轴承处有轴向间隙,丝杠与螺母之间也有轴向间隙。
在车床上切断时,刀具前刀面(带有前角的)承受了工件给它的力P,(忽略切屑与前刀面的摩擦力),把力P分解成力Pz和径向分力巧,其中径向分力巧与切断车刀的进给方向相同,指向工件,将刀具朝工件里推,从而会拉动中滑板向有间隙方向窜动,使切断刀突然扎人工件,造成扎(断)刀或工件弯曲。
解决方法:当车削螺距较大采用左右借刀切削法的螺纹时,除了调整好车床有关参数外,还应调整床鞍同床身导轨之间的配合间隙,使其稍紧一些,以增大移动时的摩擦力,减少床鞍窜动的可能性,但这个间隙也不能调的太紧,以能平稳摇动床鞍为宜。
调整好中滑板的间隙,尽量使间隙最小;调整好小滑板的松紧,使其稍紧一些,以防车削时车刀移位。
浅析教学中车削螺纹常见问题及解决方法

·教学实践探索·在各种机械产品中,带有螺纹的零件应用广泛,形状也多种多样,常用于固定连接、调节或测量,又可用于传递动力,如车床上很多箱体都用螺纹固定连接,车床上的丝杠与开合螺母之间用螺纹传递动力。
车削螺纹是常用的方法,也是车工的基本技能。
在车工实习教学中,车削螺纹是车削加工中较为复杂的加工内容。
在实际教学中,车削螺纹时产生问题的原因比较复杂,往往会影响正常的加工训练和教学进度。
本文分析造成车削螺纹时产生废品的常见问题及其解决方法,具有一定的实践指导意义。
一、螺距(导程)不正确1.螺纹全长不正确。
原因:交换齿轮计算或组装错误,进给箱、溜板箱有关手柄位置扳错。
解决方法:可重新检查进给箱手柄位置或验算、更换挂轮。
2.螺纹局部不正确。
原因:车床丝杠和主轴的窜动过大;溜板箱手轮转动不平衡;开合螺母间隙过大。
解决方法:调整好主轴和丝杠的轴向窜动量;将溜板箱手轮拉出使之与传动轴脱开,使床鞍均匀运动;调整好开合螺母间隙。
3.车削中开合螺母自动抬起。
解决方法:可以调整开合螺母镶条,适当减小间隙,或是重物挂在开合螺母手柄上以防止开合螺母传动时自动抬起。
二、牙型不正确1.刀尖角不正确。
原因:车刀刃磨时刀尖角不对,导致加工出的螺纹角度不正确。
解决方法:正确刃磨车刀,磨刀时用角度样板来检测。
2.径向前角的影响。
原因:在加工螺纹时为了使车刀顺利排屑,提高表面质量,经常磨有径向前角,这样就使车出的螺纹牙型角大于车刀的刀尖角,同时使车削出的螺纹牙型在轴向剖面内不是直线,而是曲线,会影响螺纹副的配合质量。
解决方法:磨车刀的径向前角较大时,必须对两刃夹角进行修正,其修正值可以查表得到。
3.车刀安装不正确。
原因:车刀安装不正确即车刀装得不正,导致车出的牙型角歪斜(俗称倒牙)。
解决方法:装刀时用角度样板对刀,将车刀装正,同时保证刀尖与工件中心等高。
4.车刀磨损。
原因:车刀使用中有磨损不锋利了,但没有及时刃磨,导致车出的牙型角不直。
车削螺纹时常见故障及解决方法

车削螺纹时常见故障及解决方法车削螺纹是机械加工中常见的工艺,常见的故障有:1. 切削刀具损坏:车削过程中,切削刀具可能会出现磨损或断裂等问题,导致工件螺纹加工不良。
解决方法是定期检查切削刀具的磨损情况,及时更换磨损严重的刀具。
2. 切削速度不合适:切削速度过高或过低都会导致工件螺纹加工不良。
切削速度过高会导致切削刀具产生过多的热量,容易引起刀具变韧性、变硬度,导致加工螺纹时出现切削刀具折断等现象。
切削速度过低则会使切削进给量过大,造成敲击刀具、加工表面粗糙、切削刃磨损等问题。
解决方法是根据工件材料的硬度、切削刀具材料、螺纹尺寸等因素调整切削速度,保证加工过程中切削刀具和工件之间的匹配。
3. 切削进给量不合适:切削进给量过大会导致工件表面粗糙,切削刃损坏等问题;切削进给量过小则会导致加工效率低下。
解决方法是根据工件材料的硬度、切削刀具材料、切削速度等因素合理选择切削进给量,保证加工过程中切削刃的磨损与切削效率之间的平衡。
4. 工件装夹不牢固:工件装夹不牢固会导致工件在车削过程中产生偏移、震动等问题,使螺纹加工不精确。
解决方法是选择适当的装夹工装和夹具,确保工件在车削过程中保持良好的稳定性和牢固性。
5. 机床刚性不足:机床刚性不足会导致工件在车削过程中产生振动,影响加工精度。
解决方法是选择合适的机床,提高机床的刚性,减少振动对螺纹加工的影响。
6. 不合适的切削液:切削液的选择不合适会导致螺纹加工过程中切削刃和工件之间的磨擦增大,容易产生高温区,使切削刀具过早磨损,加工精度下降。
解决方法是选择合适的切削液,并根据实际情况进行润滑和冷却。
7. 加工参数设置不合理:车削螺纹时,加工参数的设置不合理会导致工件螺纹加工不良。
解决方法是根据工件材料、螺纹尺寸、切削刀具等因素选择合适的加工参数,保证加工过程中切削质量和加工效率的平衡。
8. 操作不当:操作人员的经验和技术水平也会影响螺纹加工的质量。
解决方法是提高操作人员的技术水平,加强培训和学习,熟悉设备的使用和加工工艺,注重操作规范,减少人为因素对螺纹加工的影响。
螺纹车削的常见问题及解决方法

螺纹车削的常见问题及解决方法针对公司叶轮及轴在车削螺纹时常出现的问题,提出解决方法,从而最大限度地保证螺纹加工的质量。
标签:螺纹;常见问题;加工工艺;解决方法我公司目前大多数叶轮、轴均使用螺纹进行连接,起传递动力的作用,目前公司叶轮与轴的连接大多为梯形螺纹,有单线螺纹,即由一条螺旋线形成的螺纹叫单线(单头)螺纹;也有多线螺纹,即由两条或者两条以上的轴向等距分布的螺旋线所形成的螺纹叫多线(多头)螺纹。
螺纹的螺旋线沿轴向等距分布,单线螺纹每旋转一周,移动一倍的螺距;多线螺纹每旋转一周时,能移动几倍的螺距,它广泛的应用于快速机构中,但其牙型深,切削层面积大,加工过程中更容易出现“乱扣”、“扎刀”现象,除此之外,操作者的技术水平不同,常出现中径不正确等问题,针对上述的问题,结合实际工作中的经验,谈谈解决上述问题的办法。
1.螺纹加工过程中常见的问题1.1加工过程中出现乱扣、扎刀的现象在加工螺纹时,刀具到退刀槽的中间需退刀时,采用打开开合螺母,将床鞍摇至起始位置,主轴带动丝杠旋转一圈时,被加工的工件未旋转整数圈或者丝杠的轴向间隙过大,在车削过程中产生轴向的窜动,那么,再次闭合开合螺母时,就会发生车刀刀尖不在前一刀所车出的螺旋槽内,容易出现乱扣。
车床中滑板、小滑板的间隙没有调整适当;安装刀具时刀杆伸出过长或刀杆刚性不足;刀尖低于工件中心;工件的刚性不足;车刀的前角过大,造成径向切削力把车刀拉向工件造成扎刀,操作方法不当致使车刀同时受力。
1.2螺纹中径不正确在车削过程中,车刀切削量过大,刻度盘不准或间隙过大,未能及时发现;加工螺纹前的圆柱面车削时同轴度误差较大,导致车削螺纹时吃刀不均匀,螺纹量规旋到中间旋不进去。
1.3螺纹的表面质量不高車刀刃磨的角度不合理,不光洁;采用的切削参数与工件不匹配;刀具的刚性不足产生较大的震动。
车削螺纹时产生的故障有很多,造成缺陷的原因也很多,从上述的分析可看出,有设备的原因,也有刀具和人员的原因。
车削螺纹常见的工艺问题及解决办法
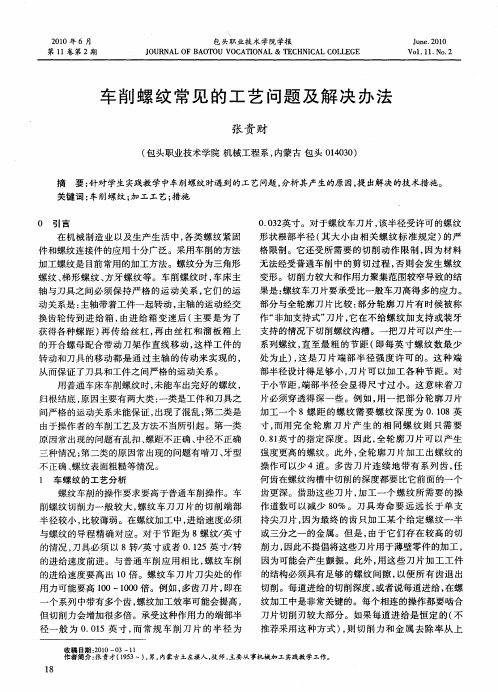
获 得各 种 螺 距 ) 传 给 丝 杠 , 由丝 杠 和 溜板 箱 上 再 再 的开 合螺 母配 合 带 动刀 架 作 直 线 移 动 , 样 工 件 的 这
系列螺 纹 , 至 最 粗 的节 距 ( 每英 寸 螺 纹 数 最 少 直 即 处 为止 ) 这 是 刀 片 端 部 半 径 强 度 许 可 的 。这 种 端 , 部 半径 设计 得 足 够 小 , 片可 以加 工 各 种 节 距 。对 刀
件 和 螺纹连 接件 的应 用 十分 广泛 。采 用车 削 的方法 加 工螺 纹是 目前 常 用 的加工 方法 。螺 纹分 为三 角形 螺 纹 、 形 螺纹 、 牙 螺纹 等 。 车削 螺 纹 时 , 床 主 梯 方 车 轴 与刀 具之 间 必须 保 持 严 格 的 运 动关 系 , 它们 的运 动 关 系是 : 主轴 带 着工 件一 起转 动 , 主轴 的运 动经交
换齿 轮 传 到 进 给 箱 , 由进 给 箱 变 速 后 ( 主要 是 为 了
无法 经 受普通 车 削 中 的剪 切 过 程 , 则 会 发生 螺 纹 否 变形 。切 削 力较 大和作 用 力聚集 范 围较 窄导 致 的结 果 是 : 纹 车刀 片要 承受 比一般 车 刀高 得多 的应 力 。 螺 部 分与 全轮 廓刀 片 比较 : 分 轮 廓 刀 片有 时候 被称 部 作“ 非加 支 持式 ” 片 , 在 不 给螺 纹 加 支 持 或装 牙 刀 它
何齿 在 螺纹 沟槽 中切 削 的深度都 要 比它前 面的一 个
不 正确 、 螺纹表 面粗 糙等 情况 。
1 车 螺 纹的 工艺分 析
螺 纹 车削 的操 作要 求要 高 于普通 车削 操 作 。车 削 螺 纹切 削力 一 般较 大 , 纹 车刀 刀 片 的 切 削 端部 螺 半 径 较小 , 比较薄 弱 。在螺 纹加工 中 , 给速 度必须 进 与螺 纹 的导 程 精 确 对应 。对 于节 距 为 8螺 纹/ 寸 英 的情 况 , 刀具 必 须 以 8转/ 寸 或者 0 15英 寸/ 英 .2 转 的进 给 速度 前进 。 与普 通 车 削 应 用 相 比 , 纹 车 削 螺 的进 给 速度要 高 出 l O倍 。螺 纹 车 刀 片 刀 尖 处 的作 用 力 可 能要 高 10一10 0 00倍 。例 如 , 多齿 刀 片 , 即在
普通车床螺纹车削常见故障及解决方法

普通车床螺纹车削常见故障及解决方法螺纹车削是机械加工中非常重要的一项工艺,通常在各种零部件的制造过程中都需要进行螺纹车削。
然而,在螺纹车削过程中,常常会出现一些故障,如刀具磨损、精度偏差、刀具掉刃等。
本文将针对普通车床螺纹车削中的常见故障进行分析,并提供相应的解决方法。
一、刀具磨损刀具磨损是螺纹车削最常见的故障之一,主要表现为刀尖磨损、后角磨损以及侧刃磨损。
刀具磨损会导致工件表面粗糙度增大、尺寸偏差增加等问题。
解决方法:1.定期检查刀具的磨损情况,及时更换磨损严重的刀具。
2.选择合适的刀具材料,提高刀具的耐磨性能。
3.加强刀具的润滑,减少磨损。
4.使用合适的切削参数,减少刀具的磨损。
二、精度偏差精度偏差是指螺纹车削过程中工件的实际尺寸与设计尺寸之间的差异。
精度偏差可能来自于车床本身的误差,也可能是由于操作不当或刀具磨损造成的。
解决方法:1.定期检查车床的准直度,及时调整车床的各个零部件,确保车床的准确度。
2.合理选择刀具,根据工件的要求选择适当的切削速度和进给速度,减小精度偏差。
3.加强操作人员的技术培训,提高操作人员的技能水平。
三、刀具掉刃刀具掉刃是螺纹车削中的一个严重故障,会导致螺纹质量不合格,同时也对安全造成威胁。
解决方法:1.选择优质的刀具,确保刀具的质量。
2.加强刀具的紧固力,定期检查刀具是否松动。
3.根据切削工况合理选择刀具的进给速度和切削深度。
4.在进给过程中避免突然变速,防止刀具发生震动。
5.定期检查刀具的磨损情况,及时更换磨损严重的刀具。
四、切削液问题切削液在螺纹车削过程中起到冷却、润滑、清洁的作用,然而切削液的质量差或使用不当会引起一系列问题,如工件表面粗糙度增大、刀具磨损加快等。
解决方法:1.选择合适的切削液,根据加工材料的不同,选择适当的切削液种类。
2.合理调节切削液的浓度和温度。
3.加强对切削液的管理,定期更换切削液。
4.根据切削工况,调整切削液的喷射方式和位置。
总结起来,普通车床螺纹车削中常见的故障包括刀具磨损、精度偏差、刀具掉刃以及切削液问题。
- 1、下载文档前请自行甄别文档内容的完整性,平台不提供额外的编辑、内容补充、找答案等附加服务。
- 2、"仅部分预览"的文档,不可在线预览部分如存在完整性等问题,可反馈申请退款(可完整预览的文档不适用该条件!)。
- 3、如文档侵犯您的权益,请联系客服反馈,我们会尽快为您处理(人工客服工作时间:9:00-18:30)。
螺纹车削方法[车削螺纹时常见故障及解决方法]
螺纹是在圆柱工件表面上,沿着螺旋线所形成的,具有相同剖面的连续凸起和沟槽。
在机械制造业中,带螺纹的零件应用十分广泛。
用车削方法加工螺纹,是目前常用的加工方法。
在卧式车床(如CA6140)上能车削米制、英寸制、模数和径节制四种标准螺纹,无论车削哪一种螺纹,车床主轴与刀具之间必须保持严格的运动关系:即主轴每转
一转(工件转一转),刀具应均匀地移动一个工件导程的距离。
保证这种运动关系的理论依据是:主轴带着工件一起转动,主轴的运动及动
力经挂轮传到进给箱;由进给箱变速以后(主要是为了获得各种螺距)再传递给丝杠;然后再由丝杠和溜板箱上的开合螺母配合,带动刀架
作直线移动,这样工件的转动和刀具的移动都是通过主轴的带动来实现的,从而保证了工件和刀具之间严格的运动关系。
实际车削螺纹时,由于各种原因,造成从主轴到刀具之间的运动,在某一环节出现问题,引起螺纹车削时产生故障,影响正常生产。
因此,必须及时解决问题。
车削螺纹时常见故障及解决方法如下:
一、啃刀
故障原因:⑴车刀安装得过高或过低;⑵工件装夹不牢或车刀磨损过大。
解决方法:
1、车刀安装得过高或过低:过高,则吃刀到一定深度时,车刀的后刀面顶住工件,增大摩擦力,甚至把工件顶弯,造成啃刀现象;过低,则切屑不易排出,车刀径向力的方向是工件中心,加上横进丝杠与螺母间隙过大,致使吃刀深度不断自动趋向加深,从而把工件抬起,出现啃刀。
此时,应及时调整车刀高度,使其刀尖与工件的轴线等高(可利用尾座顶尖对刀)。
在粗车和半精车时,刀尖位置比工件的中心高出1%D左右(D表示被加工工件直径)。
2、工件装夹不牢:工件本身的刚性不能承受车削时的切削力,因而产生过大的挠度(弯曲度),改变了工件的中心高度(工件被抬高了),形成切削深度突增,出现啃刀。
此时应把工件装夹牢固,并使用尾座顶尖等,以增加工件刚性。
3、车刀磨损过大:引起切削力增大,顶弯工件,出现啃刀。
此时应对车刀加以修磨。
二、乱扣
故障原因:当丝杠转一转时,工件未转过整数转而造成的。
解决方法:
1、当车床丝杠螺距与工件螺距比值不成整倍数时:如果退刀时,采用打开开合螺母,将床鞍摇至起始位置,那么,再次闭合开合螺母时,就会发生车刀刀尖不在前一刀所车出的螺旋槽内,以致出现乱扣。
解决方法是:采用正反车法退刀,即在第一次行程结束时,不提起开合螺母,把刀沿径向退出后,将主轴反转,使车刀沿纵向退回,再进行第二
次行程,这样往复过程中,因主轴、丝杠和刀架之间的传动没有分离过,车刀始终在原来的螺旋槽中,就不会出现乱扣。
2、对于车削车床丝杠螺距与工件螺距比值成整倍数的螺纹:工件和丝杠都在旋转,提起开合螺母后,至少要等丝杠转过一转,才能重新合上开合螺母,这样当丝杠转过一转时,工件转了整数倍,车刀就能进入前一刀车出的螺旋槽内,不会出现乱扣,可以采用打开开合螺母,
手动退刀。
这样退刀快,有利于提高生产率和保持丝杠精度,同时丝杠也较安全。
三、螺距不正确
故障原因:螺纹全长或局部上不正确,螺纹全长上螺距不均匀或螺纹上出现竹节纹。
解决方法:
1、螺纹全长上不正确:原因是挂轮搭配不当或进给箱手柄位置不对,可重新检查进给箱手柄位置或验算挂轮。
2、螺纹局部不正确:原因是由于车床丝杠本身的螺距局部误差(一般由磨损引起),可更换丝杠或局部修复。
3、螺纹全长上螺距不均匀,原因是:
⑴丝杠的轴向窜动。
⑵主轴的轴向窜动。
⑶溜板箱的开合螺母与丝杠不同轴而造成啮合不良。
⑷溜板箱燕尾导轨磨损而造成开合螺母闭合时不稳定。
⑸挂轮间隙过大等。
通过检测:
如果是丝杠轴向窜动造成的,可对车床丝杠与进给箱连接处的
调整圆螺母进行调整,以消除连接处推力球轴承轴向间隙。
如果是主轴轴向窜动引起的,可调整主轴后调整螺母,以消除后推力球轴承的轴向间隙。
如果是溜板箱的开合螺母与丝杠不同轴而造成啮合不良引起的,可修整开合螺母并调整开合螺母间隙。
如果是燕尾导轨磨损,可配制燕尾导轨及镶条,以达到正确的配合要求。
如果是挂轮间隙过大,可采用重新调整挂轮间隙。
4、出现竹节纹的原因是:从主轴到丝杠之间的齿轮传动有周期性误差(如挂轮箱内的齿轮传动,进给箱内的齿轮传动),这些误差的形成是由于齿轮传动本身存在制造误差,或局部磨损,或齿轮在轴上安装偏心等造成旋转中心低,从而引起丝杠旋转周期性不均匀,带动刀具移动的周期性不均匀,导致竹节纹的出现。
解决方法:修换有误差或磨损的齿轮。
四、中径不正确
故障原因:吃刀太大,刻度盘不准,而又未及时测量所造成。
解决方法:
精车时要详细检查刻度盘是否松动,精车余量要适当,车刀刃口要锋利,要及时测量。
五、螺纹表面粗糙超差
故障原因:车刀刃口磨得不光洁,切削液不适合,切削速度和工件材料选择不当以及切削过程产生振动等造成。
解决方法:
正确修整砂轮或用油石精研刀具;选择适当切削速度和切削液;调整车床床鞍压板及中、小滑板燕尾导轨的镶条等,保证各导轨间隙的准确性,防止切削时产生振动。
总之,车削螺纹时产生的故障形式多种多样,既有设备的原因,也有刀具、操作者等的原因,在排除故障时要具体情况具体分析,通过各种检测和诊断手段,找出具体的影响因素,采取有效的解决方法。
内容仅供参考。