橡胶的工艺流程
橡胶的工艺流程

橡胶的工艺流程(精品)2014—10—22橡胶技术网橡胶工艺流程开始1 综述橡胶制品的主要原料是生胶、各种配合剂、以及作为骨架材料的纤维和金属材料,橡胶制品的基本生产工艺过程包括塑炼、混炼、压延、压出、成型、硫化6个基本工序.橡胶的加工工艺过程主要是解决塑性和弹性矛盾的过程,通过各种加工手段,使得弹性的橡胶变成具有塑性的塑炼胶,在加入各种配合剂制成半成品,然后通过硫化是具有塑性的半成品又变成弹性高、物理机械性能好的橡胶制品。
2 橡胶加工工艺2.1塑炼工艺生胶塑炼是通过机械应力、热、氧或加入某些化学试剂等方法,使生胶由强韧的弹性状态转变为柔软、便于加工的塑性状态的过程.生胶塑炼的目的是降低它的弹性,增加可塑性,并获得适当的流动性,以满足混炼、亚衍、压出、成型、硫化以及胶浆制造、海绵胶制造等各种加工工艺过程的要求.掌握好适当的塑炼可塑度,对橡胶制品的加工和成品质量是至关重要的。
在满足加工工艺要求的前提下应尽可能降低可塑度。
随着恒粘度橡胶、低粘度橡胶的出现,有的橡胶已经不需要塑炼而直接进行混炼。
在橡胶工业中,最常用的塑炼方法有机械塑炼法和化学塑炼法。
机械塑炼法所用的主要设备是开放式炼胶机、密闭式炼胶机和螺杆塑炼机。
化学塑炼法是在机械塑炼过程中加入化学药品来提高塑炼效果的方法.开炼机塑炼时温度一般在80℃以下,属于低温机械混炼方法.密炼机和螺杆混炼机的排胶温度在120℃以上,甚至高达160-180℃,属于高温机械混炼。
生胶在混炼之前需要预先经过烘胶、切胶、选胶和破胶等处理才能塑炼.几种胶的塑炼特性:天然橡胶用开炼机塑炼时,辊筒温度为30—40℃,时间约为15—20min;采用密炼机塑炼当温度达到120℃以上时,时间约为3-5min。
丁苯橡胶的门尼粘度多在35—60之间,因此,丁苯橡胶也可不用塑炼,但是经过塑炼后可以提高配合机的分散性顺丁橡胶具有冷流性,缺乏塑炼效果。
顺丁胶的门尼粘度较低,可不用塑炼.氯丁橡胶得塑性大,塑炼前可薄通3-5次,薄通温度在30-40℃。
橡胶生产工艺流程
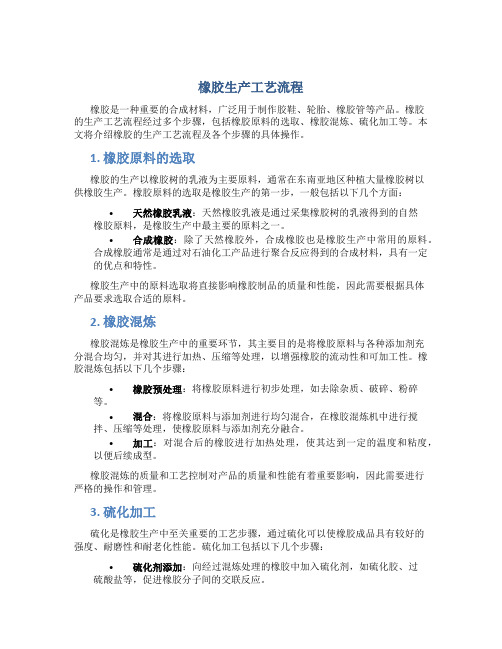
橡胶生产工艺流程橡胶是一种重要的合成材料,广泛用于制作胶鞋、轮胎、橡胶管等产品。
橡胶的生产工艺流程经过多个步骤,包括橡胶原料的选取、橡胶混炼、硫化加工等。
本文将介绍橡胶的生产工艺流程及各个步骤的具体操作。
1. 橡胶原料的选取橡胶的生产以橡胶树的乳液为主要原料,通常在东南亚地区种植大量橡胶树以供橡胶生产。
橡胶原料的选取是橡胶生产的第一步,一般包括以下几个方面:•天然橡胶乳液:天然橡胶乳液是通过采集橡胶树的乳液得到的自然橡胶原料,是橡胶生产中最主要的原料之一。
•合成橡胶:除了天然橡胶外,合成橡胶也是橡胶生产中常用的原料。
合成橡胶通常是通过对石油化工产品进行聚合反应得到的合成材料,具有一定的优点和特性。
橡胶生产中的原料选取将直接影响橡胶制品的质量和性能,因此需要根据具体产品要求选取合适的原料。
2. 橡胶混炼橡胶混炼是橡胶生产中的重要环节,其主要目的是将橡胶原料与各种添加剂充分混合均匀,并对其进行加热、压缩等处理,以增强橡胶的流动性和可加工性。
橡胶混炼包括以下几个步骤:•橡胶预处理:将橡胶原料进行初步处理,如去除杂质、破碎、粉碎等。
•混合:将橡胶原料与添加剂进行均匀混合,在橡胶混炼机中进行搅拌、压缩等处理,使橡胶原料与添加剂充分融合。
•加工:对混合后的橡胶进行加热处理,使其达到一定的温度和粘度,以便后续成型。
橡胶混炼的质量和工艺控制对产品的质量和性能有着重要影响,因此需要进行严格的操作和管理。
3. 硫化加工硫化是橡胶生产中至关重要的工艺步骤,通过硫化可以使橡胶成品具有较好的强度、耐磨性和耐老化性能。
硫化加工包括以下几个步骤:•硫化剂添加:向经过混炼处理的橡胶中加入硫化剂,如硫化胶、过硫酸盐等,促进橡胶分子间的交联反应。
•硫化处理:将橡胶制品放入硫化罐中进行硫化处理,通常在高温高压下进行,使橡胶形成交联结构,提高其强度和耐磨性。
硫化加工是橡胶生产的关键环节,对产品的质量和性能具有重要的影响,需要进行严格控制和管理。
橡胶的工艺流程
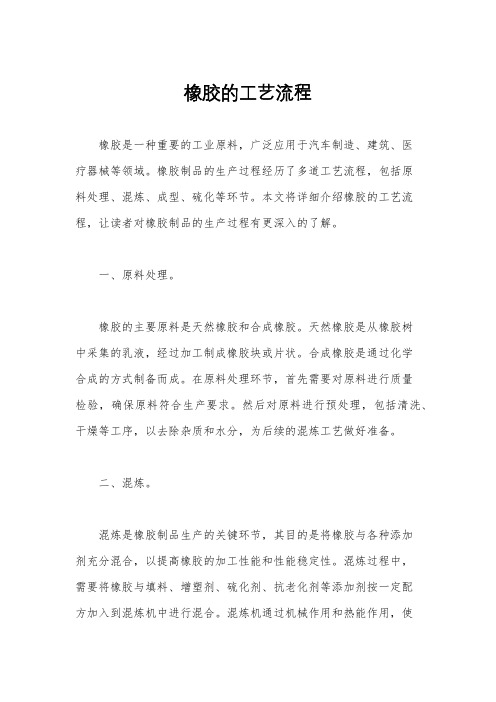
橡胶的工艺流程橡胶是一种重要的工业原料,广泛应用于汽车制造、建筑、医疗器械等领域。
橡胶制品的生产过程经历了多道工艺流程,包括原料处理、混炼、成型、硫化等环节。
本文将详细介绍橡胶的工艺流程,让读者对橡胶制品的生产过程有更深入的了解。
一、原料处理。
橡胶的主要原料是天然橡胶和合成橡胶。
天然橡胶是从橡胶树中采集的乳液,经过加工制成橡胶块或片状。
合成橡胶是通过化学合成的方式制备而成。
在原料处理环节,首先需要对原料进行质量检验,确保原料符合生产要求。
然后对原料进行预处理,包括清洗、干燥等工序,以去除杂质和水分,为后续的混炼工艺做好准备。
二、混炼。
混炼是橡胶制品生产的关键环节,其目的是将橡胶与各种添加剂充分混合,以提高橡胶的加工性能和性能稳定性。
混炼过程中,需要将橡胶与填料、增塑剂、硫化剂、抗老化剂等添加剂按一定配方加入到混炼机中进行混合。
混炼机通过机械作用和热能作用,使各种添加剂均匀分散在橡胶中,形成均匀的橡胶混合料。
三、成型。
混炼后的橡胶混合料需要进行成型,以得到所需的橡胶制品。
成型过程根据不同的制品要求,可以采用压延、挤出、注塑等不同的成型方法。
在成型过程中,需要根据产品的形状和尺寸,选择合适的模具和成型设备,将橡胶混合料加工成所需的形状,如轮胎、密封圈、橡胶管等。
四、硫化。
硫化是橡胶制品生产中的重要工艺环节,通过硫化可以使橡胶获得良好的物理性能和耐热耐老化性能。
硫化过程是将成型后的橡胶制品放入硫化炉中,加热并加入硫化剂,使橡胶分子间发生交联反应,从而增强橡胶的强度和弹性。
硫化时间和温度根据不同的橡胶制品和硫化体系有所不同,需要根据实际情况进行调整。
五、检验与包装。
最后,经过硫化的橡胶制品需要进行质量检验,包括外观质量、尺寸精度、物理性能等方面的检测。
合格的橡胶制品经过检验后,将进行包装和存储,待出厂销售或使用。
总结,橡胶制品的生产过程经历了原料处理、混炼、成型、硫化等多道工艺流程,每道工艺环节都对最终产品的质量和性能有着重要的影响。
橡胶加工工艺流程
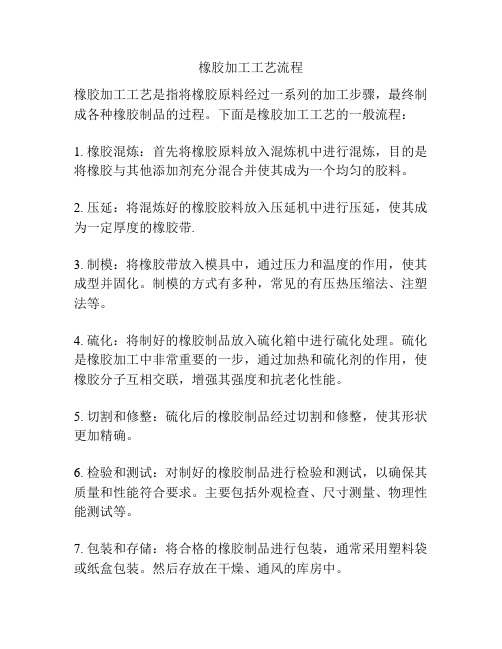
橡胶加工工艺流程
橡胶加工工艺是指将橡胶原料经过一系列的加工步骤,最终制成各种橡胶制品的过程。
下面是橡胶加工工艺的一般流程:
1. 橡胶混炼:首先将橡胶原料放入混炼机中进行混炼,目的是将橡胶与其他添加剂充分混合并使其成为一个均匀的胶料。
2. 压延:将混炼好的橡胶胶料放入压延机中进行压延,使其成为一定厚度的橡胶带.
3. 制模:将橡胶带放入模具中,通过压力和温度的作用,使其成型并固化。
制模的方式有多种,常见的有压热压缩法、注塑法等。
4. 硫化:将制好的橡胶制品放入硫化箱中进行硫化处理。
硫化是橡胶加工中非常重要的一步,通过加热和硫化剂的作用,使橡胶分子互相交联,增强其强度和抗老化性能。
5. 切割和修整:硫化后的橡胶制品经过切割和修整,使其形状更加精确。
6. 检验和测试:对制好的橡胶制品进行检验和测试,以确保其质量和性能符合要求。
主要包括外观检查、尺寸测量、物理性能测试等。
7. 包装和存储:将合格的橡胶制品进行包装,通常采用塑料袋或纸盒包装。
然后存放在干燥、通风的库房中。
以上是橡胶加工工艺的一般流程,不同的橡胶制品可能会有一些特殊的工艺步骤。
橡胶加工的过程中,需注意橡胶原料的质量、混炼工艺参数、硫化条件等。
只有严格控制每一个环节,才能制备出质量稳定、性能优越的橡胶制品。
橡胶生产工艺流程
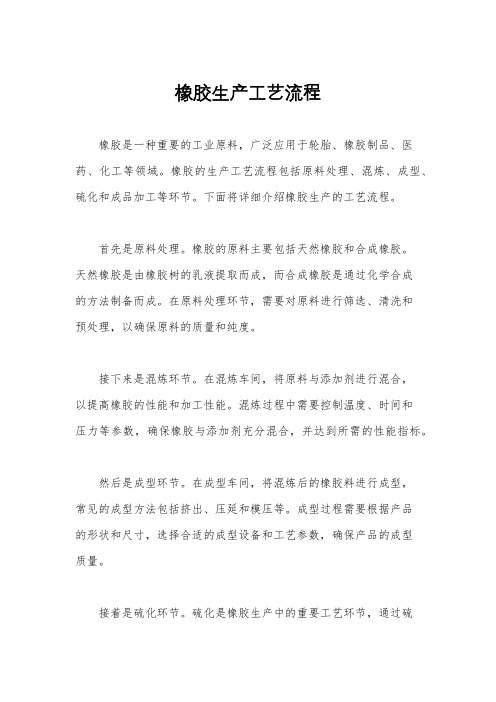
橡胶生产工艺流程橡胶是一种重要的工业原料,广泛应用于轮胎、橡胶制品、医药、化工等领域。
橡胶的生产工艺流程包括原料处理、混炼、成型、硫化和成品加工等环节。
下面将详细介绍橡胶生产的工艺流程。
首先是原料处理。
橡胶的原料主要包括天然橡胶和合成橡胶。
天然橡胶是由橡胶树的乳液提取而成,而合成橡胶是通过化学合成的方法制备而成。
在原料处理环节,需要对原料进行筛选、清洗和预处理,以确保原料的质量和纯度。
接下来是混炼环节。
在混炼车间,将原料与添加剂进行混合,以提高橡胶的性能和加工性能。
混炼过程中需要控制温度、时间和压力等参数,确保橡胶与添加剂充分混合,并达到所需的性能指标。
然后是成型环节。
在成型车间,将混炼后的橡胶料进行成型,常见的成型方法包括挤出、压延和模压等。
成型过程需要根据产品的形状和尺寸,选择合适的成型设备和工艺参数,确保产品的成型质量。
接着是硫化环节。
硫化是橡胶生产中的重要工艺环节,通过硫化可以使橡胶材料具有良好的弹性和耐磨性。
硫化过程中需要控制硫化温度、时间和压力等参数,确保橡胶材料的硫化度和性能达到要求。
最后是成品加工环节。
在成品加工车间,对硫化后的橡胶制品进行修整、检验和包装等工序,最终将成品交付给客户。
成品加工环节需要严格控制产品的质量,确保产品符合客户的要求。
总的来说,橡胶生产工艺流程包括原料处理、混炼、成型、硫化和成品加工等环节,每个环节都需要严格控制工艺参数,确保产品的质量和性能。
随着科技的发展,橡胶生产工艺也在不断创新,以适应市场对橡胶制品的不断需求。
希望本文的介绍能够对橡胶生产工艺有所帮助,谢谢阅读!。
橡胶制作的基本工艺流程及硫化罐在橡胶制品生产中的作用
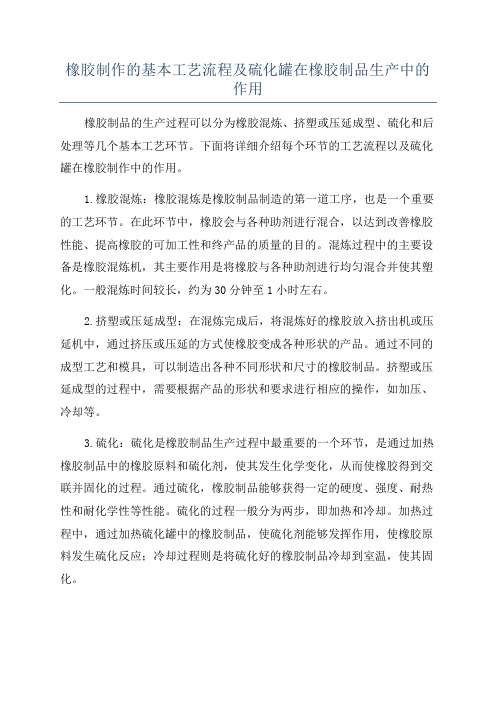
橡胶制作的基本工艺流程及硫化罐在橡胶制品生产中的作用橡胶制品的生产过程可以分为橡胶混炼、挤塑或压延成型、硫化和后处理等几个基本工艺环节。
下面将详细介绍每个环节的工艺流程以及硫化罐在橡胶制作中的作用。
1.橡胶混炼:橡胶混炼是橡胶制品制造的第一道工序,也是一个重要的工艺环节。
在此环节中,橡胶会与各种助剂进行混合,以达到改善橡胶性能、提高橡胶的可加工性和终产品的质量的目的。
混炼过程中的主要设备是橡胶混炼机,其主要作用是将橡胶与各种助剂进行均匀混合并使其塑化。
一般混炼时间较长,约为30分钟至1小时左右。
2.挤塑或压延成型:在混炼完成后,将混炼好的橡胶放入挤出机或压延机中,通过挤压或压延的方式使橡胶变成各种形状的产品。
通过不同的成型工艺和模具,可以制造出各种不同形状和尺寸的橡胶制品。
挤塑或压延成型的过程中,需要根据产品的形状和要求进行相应的操作,如加压、冷却等。
3.硫化:硫化是橡胶制品生产过程中最重要的一个环节,是通过加热橡胶制品中的橡胶原料和硫化剂,使其发生化学变化,从而使橡胶得到交联并固化的过程。
通过硫化,橡胶制品能够获得一定的硬度、强度、耐热性和耐化学性等性能。
硫化的过程一般分为两步,即加热和冷却。
加热过程中,通过加热硫化罐中的橡胶制品,使硫化剂能够发挥作用,使橡胶原料发生硫化反应;冷却过程则是将硫化好的橡胶制品冷却到室温,使其固化。
4.后处理:硫化完成后的橡胶制品通常需要进行后处理,以达到最终要求的质量和性能。
后处理包括修整、修边、磨光、清洗、质量检测等环节,根据不同的产品要求,可以采取不同的后处理方法。
硫化罐在橡胶制品生产中的作用:硫化罐是用于进行橡胶制品硫化反应的特殊设备。
它主要起到以下作用:1.提供加热环境:硫化罐可以提供均匀的加热环境,使橡胶制品中的橡胶原料和硫化剂能够充分热化,并发生化学反应。
通过控制加热罐的温度和时间,可以控制硫化反应的速度和程度,从而控制橡胶制品的硬度和性能。
2.提供压力环境:在硫化过程中,通过增加硫化罐内的压力,可以提高硫化反应的速度,并使橡胶制品具有更好的质量。
橡胶生产工艺流程设计与温度控制

橡胶生产工艺流程设计与温度控制橡胶是一种重要的工业原料,广泛应用于各个领域,如轮胎、橡胶制品等。
为了保证橡胶的质量和性能,橡胶生产需要经过一系列的工艺流程,并对温度进行精确的控制。
本文将详细介绍橡胶生产工艺流程的设计以及温度的控制。
一、橡胶生产工艺流程设计1. 原料准备橡胶的生产首先需要准备好原料。
常见的橡胶原料有乳胶、胶乳、合成橡胶等。
在原料准备阶段,需要按照配方要求进行称量和混合,确保原料的配比准确。
2. 橡胶混炼橡胶混炼是橡胶生产的核心环节。
在混炼过程中,将各种原料进行机械剪切和热塑变形,使橡胶的分散度提高,增加其可塑性和加工性能。
通常采用的混炼设备有开炼机、密炼机等。
3. 橡胶成型橡胶混炼完成后,需要进行成型。
成型可以分为挤出成型、压延成型、注射成型等不同方式。
通过不同的成型方式,可以将橡胶加工成所需的形状和尺寸。
4. 硫化加工硫化是橡胶生产中重要的一步。
通过硫化,可以使橡胶具备优异的力学性能和耐热性。
硫化过程中,橡胶与硫进行化学反应,形成交联结构。
硫化的时间、温度和压力等参数需要根据橡胶的种类和产品要求进行调控。
5. 后处理橡胶生产的最后一步是后处理。
在后处理中,需要对橡胶制品进行修整、清理、检验等操作,确保产品的质量达到标准要求。
同时,还需要进行包装和储存,以便后续销售和使用。
二、橡胶生产中的温度控制温度的控制是橡胶生产中非常重要的一部分。
适当的温度可以促进橡胶的加工性能和品质提升。
以下将从混炼、成型和硫化三个环节介绍橡胶生产中的温度控制。
1. 混炼温度控制橡胶混炼的温度控制对橡胶的分散度和加工性能具有重要影响。
一般来说,较高的混炼温度有利于橡胶添加剂的分散以及橡胶分子链的塑化,但过高的温度可能导致橡胶老化。
具体的温度控制需根据橡胶种类和配方来确定,通常在150℃-180℃之间进行混炼。
2. 成型温度控制成型温度对橡胶制品的成型效果和表面质量具有直接影响。
成型温度过低可能导致橡胶制品的缩短和凝固不完全,而成型温度过高则容易引起气泡、变形等问题。
橡胶加工工艺

橡胶加工工艺橡胶加工工艺是将天然橡胶或合成橡胶进行加工,制造成各种橡胶制品的过程。
由于橡胶具有良好的弹性、耐磨、耐压、耐酸碱等特性,所以广泛应用于机械、汽车、电子、医疗等领域。
下面就来介绍橡胶加工的工艺流程,以及影响橡胶加工质量的因素。
橡胶加工的工艺流程主要包括橡胶混炼、成型、硫化三个过程。
1. 橡胶混炼橡胶混炼是将原料橡胶与各种填料、助剂、硫化剂按一定比例混合并加热、搅拌,使其均匀分散,达到预先设定的物理、机械、化学性能要求的过程。
混炼也是影响橡胶加工质量的关键环节。
橡胶混炼一般分为二次混炼和三次混炼,其中二次混炼是为了将原料橡胶与填料、助剂充分混合,三次混炼是为了均匀分散硫化剂,使橡胶具有较好的硫化性能。
2. 成型成型是将混炼好的橡胶料按设计要求加工成各种形状的过程,包括挤出成型、压延成型、模压成型等。
在成型过程中,需要注意橡胶与模具的接触面要光滑,压力均匀,否则会影响产品的质量。
3. 硫化硫化是将加工好的橡胶制品放入硫化炉中,在一定时间内加热硫化处理,使其具有良好的强度、硬度、弹性和耐用性。
硫化的温度、时间、压力等参数需要根据橡胶种类和要求进行设置。
因此,硫化是影响橡胶制品质量的关键环节之一。
除了上述工艺流程外,影响橡胶加工质量的因素还包括原材料质量、工艺控制、操作人员技术水平等方面。
橡胶加工使用的原材料包括原料橡胶、填充料、助剂、硫化剂等。
因此,需要选择优质的原材料,控制各种物料和剂量的比例,确保各项物理、机械、化学性能达到预期。
此外,工艺控制也十分关键,需要根据不同的橡胶种类和要求,对加热、搅拌、压力等参数进行精确控制。
对操作人员技术水平的要求也很高,需要经过专业培训和实际操作,熟练掌握各种加工工艺和设备使用技巧。
总之,橡胶加工工艺是一项综合性很强的技术活,在加工中需要注意各种细节问题,进行有效的质量控制,才能制造出性能良好、品质优异的橡胶制品。
橡胶制品工艺流程

橡胶制品工艺流程橡胶制品是一种常见的工业原料,广泛应用于汽车、电子、医疗等领域。
橡胶制品的生产过程经过多道工艺流程,包括原料准备、混炼、成型、硫化等环节。
本文将详细介绍橡胶制品的工艺流程,以帮助读者更好地了解橡胶制品的生产过程。
1. 原料准备。
橡胶制品的生产过程首先需要准备原料,主要包括橡胶、填料、添加剂和油料。
橡胶是橡胶制品的主要原料,常见的橡胶包括天然橡胶和合成橡胶。
填料用于增强橡胶的硬度和耐磨性,常见的填料有碳黑和硅石粉。
添加剂包括硫化剂、促进剂、防老剂等,用于改善橡胶的加工性能和使用性能。
油料用于提高橡胶的柔软性和延展性。
2. 混炼。
混炼是橡胶制品生产的重要工艺环节,其目的是将各种原料混合均匀,形成均匀的橡胶混合料。
混炼过程中需要将橡胶、填料、添加剂和油料按一定配方投入到混炼机中进行混炼。
混炼机通常采用开炼机或密炼机,通过机械作用和热能作用使各种原料充分混合,形成均匀的橡胶混合料。
3. 成型。
混炼后的橡胶混合料需要进行成型,将其加工成所需的形状。
常见的成型方法包括挤出、压延、压缩成型等。
挤出是将橡胶混合料通过挤出机挤出成型,常用于生产橡胶管、橡胶带等产品。
压延是将橡胶混合料通过压延机压延成型,常用于生产橡胶板、橡胶片等产品。
压缩成型是将橡胶混合料放入模具中,在加热和压力作用下成型,常用于生产橡胶零件、橡胶密封件等产品。
4. 硫化。
硫化是橡胶制品生产的关键工艺环节,其目的是通过硫化剂使橡胶分子间发生交联,提高橡胶的硬度、强度和耐磨性。
硫化过程中需要将成型后的橡胶制品放入硫化机中进行硫化。
硫化机通常采用热风硫化机或硫化炉,通过加热和加压使橡胶制品在一定温度和压力下进行硫化,形成最终的橡胶制品。
5. 检验和包装。
硫化后的橡胶制品需要进行检验和包装。
检验主要包括外观质量、尺寸精度、物理性能等方面的检测,确保橡胶制品达到设计要求。
包装通常采用塑料袋、纸箱等包装材料,将橡胶制品包装成成品,便于运输和销售。
橡胶工艺流程
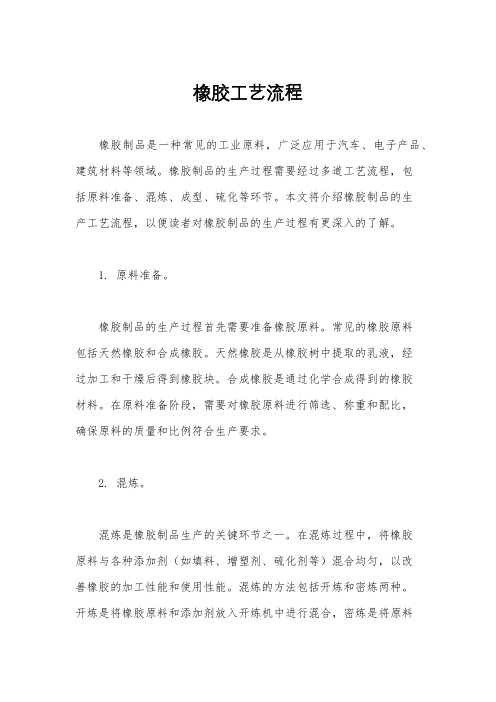
橡胶工艺流程橡胶制品是一种常见的工业原料,广泛应用于汽车、电子产品、建筑材料等领域。
橡胶制品的生产过程需要经过多道工艺流程,包括原料准备、混炼、成型、硫化等环节。
本文将介绍橡胶制品的生产工艺流程,以便读者对橡胶制品的生产过程有更深入的了解。
1. 原料准备。
橡胶制品的生产过程首先需要准备橡胶原料。
常见的橡胶原料包括天然橡胶和合成橡胶。
天然橡胶是从橡胶树中提取的乳液,经过加工和干燥后得到橡胶块。
合成橡胶是通过化学合成得到的橡胶材料。
在原料准备阶段,需要对橡胶原料进行筛选、称重和配比,确保原料的质量和比例符合生产要求。
2. 混炼。
混炼是橡胶制品生产的关键环节之一。
在混炼过程中,将橡胶原料与各种添加剂(如填料、增塑剂、硫化剂等)混合均匀,以改善橡胶的加工性能和使用性能。
混炼的方法包括开炼和密炼两种。
开炼是将橡胶原料和添加剂放入开炼机中进行混合,密炼是将原料放入密炼机中进行混合。
混炼过程需要控制时间、温度和压力,确保橡胶混合均匀。
3. 成型。
成型是将混炼后的橡胶料加工成所需形状的过程。
常见的成型方法包括挤出、压延和模压。
挤出是将橡胶料挤出成型,压延是将橡胶料通过压延机加工成片状,模压是将橡胶料放入模具中进行成型。
成型过程需要根据产品要求选择合适的成型方法,并控制温度、压力和速度,确保成型品质量符合要求。
4. 硫化。
硫化是橡胶制品生产的最后一个环节。
在硫化过程中,将成型后的橡胶制品放入硫化炉中进行硫化处理,使橡胶分子间发生交联,提高橡胶的强度和弹性。
硫化过程需要控制温度、压力和硫化时间,确保橡胶制品硫化均匀,达到设计要求的性能指标。
总结。
橡胶制品的生产工艺流程包括原料准备、混炼、成型和硫化四个主要环节。
每个环节都需要严格控制生产参数,确保橡胶制品的质量和性能符合要求。
同时,随着科技的进步,橡胶制品的生产工艺也在不断创新和改进,以满足不同领域对橡胶制品的需求。
希望本文能为读者对橡胶制品的生产工艺有所了解,并对橡胶制品的应用和发展有所启发。
橡胶基本工艺流程
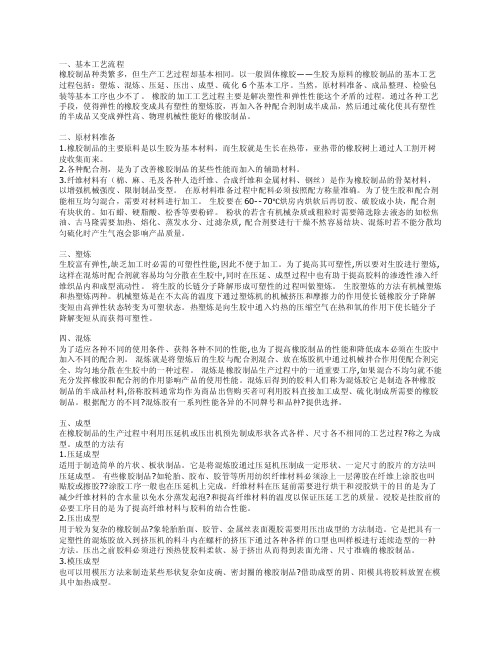
一、基本工艺流程橡胶制品种类繁多,但生产工艺过程却基本相同。
以一般固体橡胶——生胶为原料的橡胶制品的基本工艺过程包括:塑炼、混炼、压延、压出、成型、硫化6个基本工序。
当然,原材料准备、成品整理、检验包装等基本工序也少不了。
橡胶的加工工艺过程主要是解决塑性和弹性性能这个矛盾的过程。
通过各种工艺手段,使得弹性的橡胶变成具有塑性的塑炼胶,再加入各种配合剂制成半成品,然后通过硫化使具有塑性的半成品又变成弹性高、物理机械性能好的橡胶制品。
二、原材料准备1.橡胶制品的主要原料是以生胶为基本材料,而生胶就是生长在热带,亚热带的橡胶树上通过人工割开树皮收集而来。
2.各种配合剂,是为了改善橡胶制品的某些性能而加入的辅助材料。
3.纤维材料有(棉、麻、毛及各种人造纤维、合成纤维和金属材料、钢丝)是作为橡胶制品的骨架材料,以增强机械强度、限制制品变型。
在原材料准备过程中配料必须按照配方称量准确。
为了使生胶和配合剂能相互均匀混合,需要对材料进行加工。
生胶要在60--70℃烘房内烘软后再切胶、破胶成小块,配合剂有块状的。
如石蜡、硬脂酸、松香等要粉碎。
粉状的若含有机械杂质或粗粒时需要筛选除去液态的如松焦油、古马隆需要加热、熔化、蒸发水分、过滤杂质, 配合剂要进行干燥不然容易结块、混炼时若不能分散均匀硫化时产生气泡会影响产品质量。
三、塑炼生胶富有弹性,缺乏加工时必需的可塑性性能,因此不便于加工。
为了提高其可塑性,所以要对生胶进行塑炼,这样在混炼时配合剂就容易均匀分散在生胶中,同时在压延、成型过程中也有助于提高胶料的渗透性渗入纤维织品内和成型流动性。
将生胶的长链分子降解形成可塑性的过程叫做塑炼。
生胶塑炼的方法有机械塑炼和热塑炼两种。
机械塑炼是在不太高的温度下通过塑炼机的机械挤压和摩擦力的作用使长链橡胶分子降解变短由高弹性状态转变为可塑状态。
热塑炼是向生胶中通入灼热的压缩空气在热和氧的作用下使长链分子降解变短从而获得可塑性。
四、混炼为了适应各种不同的使用条件、获得各种不同的性能,也为了提高橡胶制品的性能和降低成本必须在生胶中加入不同的配合剂。
橡胶生产工艺流程介绍
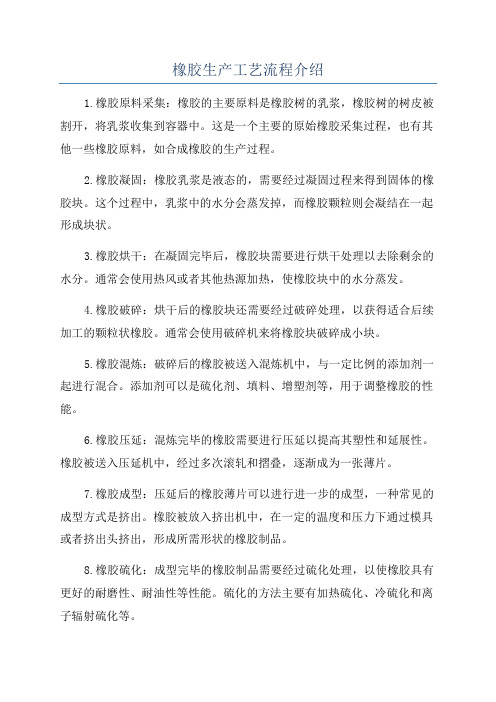
橡胶生产工艺流程介绍1.橡胶原料采集:橡胶的主要原料是橡胶树的乳浆,橡胶树的树皮被割开,将乳浆收集到容器中。
这是一个主要的原始橡胶采集过程,也有其他一些橡胶原料,如合成橡胶的生产过程。
2.橡胶凝固:橡胶乳浆是液态的,需要经过凝固过程来得到固体的橡胶块。
这个过程中,乳浆中的水分会蒸发掉,而橡胶颗粒则会凝结在一起形成块状。
3.橡胶烘干:在凝固完毕后,橡胶块需要进行烘干处理以去除剩余的水分。
通常会使用热风或者其他热源加热,使橡胶块中的水分蒸发。
4.橡胶破碎:烘干后的橡胶块还需要经过破碎处理,以获得适合后续加工的颗粒状橡胶。
通常会使用破碎机来将橡胶块破碎成小块。
5.橡胶混炼:破碎后的橡胶被送入混炼机中,与一定比例的添加剂一起进行混合。
添加剂可以是硫化剂、填料、增塑剂等,用于调整橡胶的性能。
6.橡胶压延:混炼完毕的橡胶需要进行压延以提高其塑性和延展性。
橡胶被送入压延机中,经过多次滚轧和摺叠,逐渐成为一张薄片。
7.橡胶成型:压延后的橡胶薄片可以进行进一步的成型,一种常见的成型方式是挤出。
橡胶被放入挤出机中,在一定的温度和压力下通过模具或者挤出头挤出,形成所需形状的橡胶制品。
8.橡胶硫化:成型完毕的橡胶制品需要经过硫化处理,以使橡胶具有更好的耐磨性、耐油性等性能。
硫化的方法主要有加热硫化、冷硫化和离子辐射硫化等。
9.橡胶终检:硫化后的橡胶制品需要进行终检,检查其外观质量、尺寸是否符合要求。
一般是通过目检、拉伸测试、硬度测试、水密度测试等方法进行。
10.橡胶包装和储存:通过终检合格的橡胶制品进行包装,常见的包装方式有纸箱、托盘和编织袋等。
包装完毕后,橡胶制品需要进行储存,储存条件对于橡胶制品的质量和使用寿命至关重要。
以上就是一种常见的橡胶生产工艺流程介绍。
橡胶的生产过程涵盖了原料采集、凝固、烘干、破碎、混炼、压延、成型、硫化、终检和包装储存等环节,每个环节都有其特定的工艺要求。
随着技术的进步,橡胶生产工艺也在不断演变和改进,以提高橡胶制品的质量和性能。
橡胶制品生产工艺流程

橡胶制品生产工艺流程橡胶制品是指以橡胶为主要原料,经过一系列的加工工艺制成的各种橡胶制品,包括橡胶密封件、橡胶管件、橡胶垫片、橡胶异形制品等。
橡胶制品广泛应用于汽车、电力、航空航天、建筑和家电等领域。
橡胶制品的生产工艺流程主要包括原料准备、混炼、挤出成型和硫化等几个主要步骤。
以下是橡胶制品的典型工艺流程:第一步:原料准备橡胶制品的主要原料是橡胶。
橡胶分为天然橡胶和合成橡胶两种。
在生产过程中,需要根据产品的要求选择合适的橡胶,并将其切割成片状或颗粒状。
此外,还需要准备一些辅助原料,如碳黑、助剂、填料等。
第二步:混炼混炼是橡胶制品生产过程中最关键的一步。
首先,将橡胶和辅助原料放入开放式橡胶混炼机中,然后通过摩擦加热和机械剪切使其混合均匀。
混炼的时间和温度需要根据不同的橡胶种类和产品要求进行调整。
混炼完成后,会得到一个具有特定性能的黏性橡胶混合物。
第三步:挤出成型挤出成型是将混炼好的橡胶通过挤出机的挤压作用,使其通过模具挤出成型的过程。
首先,将橡胶混合物通过进料系统送入挤出机的螺杆筒中。
螺杆转动时,会将橡胶混合物从筒子前端挤出,并通过模具形成所需的形状。
挤出速度和压力需要根据产品要求进行调整。
在挤出成型之前,可以通过预成型操作,将橡胶混合物初步成型,以便更好地进行后续挤出成型。
第四步:硫化硫化是橡胶制品生产中的重要工艺环节。
硫化是指将挤出成型的橡胶制品放入硫化炉中,经过一段时间的加热处理使其具有弹性和耐磨性能。
硫化炉的温度和时间需要根据产品要求以及不同橡胶种类进行调整。
在硫化过程中,橡胶中的硫和橡胶分子会发生化学反应,形成交叉结构,从而使橡胶变得硬化。
第五步:后处理硫化后的橡胶制品需要进行一些后处理工艺,以保证其最终产品的质量。
后处理工艺包括修整、清洗、检验和包装等。
修整是指对橡胶制品进行切割和修整,使其尺寸和形状符合产品要求。
清洗是指将橡胶制品清洁干净,去除表面的油污和杂质。
检验是通过对橡胶制品进行外观和性能检验,以保证其质量合格。
橡胶生产工艺流程

橡胶生产工艺流程橡胶生产工艺流程主要包括原料准备、混炼、模压、硫化等环节。
以下是一个大致的橡胶生产工艺流程。
首先是原料准备环节。
橡胶的主要原料有天然橡胶和合成橡胶,此外还需要添加剂如促进剂、防老化剂、增塑剂等。
原料需要按照一定的配方比例加入到生产设备中。
接下来是混炼环节。
混炼是指将原料进行机械拌和工艺,使其在一定温度条件下充分混合,同时提高橡胶的弹性和可塑性。
混炼一般分为开炼和密炼两个阶段。
开炼时将橡胶原料与一些添加剂加入到混炼机中,通过转动的刀叶将原料进行充分切割、破碎,使之达到均匀分散的目的。
密炼则是在开炼的基础上,进一步加入剂料进行混炼,使橡胶获得更好的塑胶性态。
然后是模压环节。
模压是将混炼好的橡胶放入到模具中,经过加热和压力作用,使橡胶在模具中变形成所需的形状。
模压通常采用加热板式压力机,通过加热板的加热和模具的压力,使橡胶在短时间内完成硫化反应,达到所需的硬度和强度。
最后是硫化环节。
硫化是指将已经成型的橡胶制品加热到一定温度,在一定时间内与硫化剂发生化学反应,使橡胶分子中的交联结构增加,从而提高橡胶的强度和耐磨性。
硫化过程一般分为热硫化和冷硫化两种形式。
热硫化是将橡胶制品放入加热箱中进行硫化,冷硫化则是在室温下进行硫化。
硫化时间和温度需要根据橡胶的种类和产品的要求进行调整。
整个橡胶生产工艺流程需要严格控制各个环节的参数和工艺要求,以确保橡胶制品的质量和性能。
同时,还需要注意生产中的环境保护和能源消耗,采取相应的措施减少污染和资源浪费。
总结起来,橡胶生产工艺流程主要包括原料准备、混炼、模压和硫化。
在这个流程中,需要控制好每个环节的参数和工艺要求,以确保橡胶制品的质量和性能。
橡胶工艺流程

橡胶工艺流程
《橡胶工艺流程》
橡胶制品是一种常见的工业原料,广泛应用于汽车、建筑、医疗等领域。
橡胶工艺流程是指将橡胶原料通过一系列的加工工序,最终制成成品的过程。
下面将介绍一下橡胶工艺流程的主要步骤。
首先是原料的准备。
橡胶工艺流程的第一步是将橡胶原料进行分类和配比,以保证生产出的制品符合设计要求。
一般来说,橡胶原料是由天然橡胶和合成橡胶组成的。
根据不同的制品要求,原料配比可以有所不同。
接下来是粉碎和混合。
将橡胶原料通过粉碎设备将其制成粉末状,然后将不同种类的橡胶原料混合在一起,以确保成品的性能均衡。
然后是胶料的制备。
将混合后的橡胶原料加入胶料设备中,在一定的温度和压力下进行反应,使其形成聚合链,从而得到胶料。
接下来是成型。
将胶料在模具内进行成型,有压缩成型、挤出成型、注塑成型等不同的方式,形成所需的制品形状。
最后是热处理和成品检验。
经过成型后的橡胶制品需要进行热处理,以使其具有所需的性能。
同时进行成品检验,对制品的外观和性能进行检测,确保符合标准。
通过以上的工艺流程,我们可以将原始的橡胶原料加工成各种成品,如轮胎、密封件、橡胶管等。
橡胶工艺流程不仅需要严格的工艺控制,还需要确保原料和成品的质量,以满足市场需求和行业标准。
橡胶生产工艺流程介绍

橡胶生产工艺流程介绍首先,原料处理阶段,生产商需要将橡胶原料进行清洗和干燥处理,以确保原料的质量和干净程度。
接下来是混炼阶段,将橡胶和各种添加剂(例如硫化剂、填料、增塑剂等)混合在一起,通过橡胶研磨机或橡胶硫化机进行混合、研磨和加热,使各种添加剂充分分散,从而得到均匀的胶料。
然后是挤出和成型阶段,通过挤出机或压延机将混炼好的橡胶料挤出成所需的形状,或者放入模具中进行成型,以得到符合产品要求的各种橡胶制品。
接着是硫化阶段,橡胶制品需要在硫化炉中进行硫化处理,以使橡胶分子交联,提高产品的力学性能和耐热性能。
最后是包装阶段,经过严格的质量检验后,橡胶制品进入包装环节,以便于存储和运输。
总的来说,橡胶生产工艺流程是一个复杂的过程,需要严格控制各个环节的工艺参数和质量要求,才能生产出高质量的橡胶制品。
橡胶生产工艺流程是一个系统工程,需要严格控制原料的质量、混炼的工艺参数、硫化温度和时间等关键因素,才能确保最终产品的质量和性能。
下面我们来详细介绍一下橡胶生产的工艺流程。
首先是原料处理阶段。
橡胶的生产原料主要包括天然橡胶和合成橡胶。
天然橡胶是从橡胶树的橡胶乳中提取而来,合成橡胶是通过化学合成的方法获得。
在原料处理阶段,首先对原料进行清洗和干燥处理,以确保原料的质量和干净程度。
天然橡胶需要经过挤薄机、洗涤机等设备进行初步加工,去除杂质,保证原料的纯净度和质量。
合成橡胶在原料处理阶段主要进行物理或化学法的分散处理,以增加其可加工性和混炼性。
原料处理的环节需要控制原料的含水率、杂质含量和颗粒度,以确保后续生产的正常进行。
接下来是混炼阶段。
在混炼阶段,橡胶和各种添加剂(例如硫化剂、填料、增塑剂等)混合在一起,通过橡胶研磨机或橡胶硫化机进行混合、研磨和加热,使各种添加剂充分分散,从而得到均匀的胶料。
混炼的目的是使各种添加剂与橡胶充分融合,确保橡胶混合料具有一定的塑性和流动性,便于后续挤出和成型。
然后是挤出和成型阶段。
在这个阶段,混炼好的橡胶料通过挤出机或压延机进行挤出成所需的形状,或者放入模具中进行成型,以得到符合产品要求的各种橡胶制品。
橡胶加工流程(原料-塑炼-混炼-硫化)

橡胶加工流程(原料-塑炼-混炼-硫化)1.基本工艺流程伴随现代工业尤其是化学工业的迅猛发展,橡胶制品种类繁多,但其生产工艺过程,却基本相同。
以一般固体橡胶(生胶)为原料的制品,它的生产工艺过程主要包括:原材料准备→塑炼→混炼→成型→硫化→修整→检验2.原材料准备橡胶制品的主要材料有生胶、配合剂、纤维材料和金属材料。
其中生胶为基本材料;配合剂是为了改善橡胶制品的某些性能而加入的辅助材料;纤维材料(棉、麻、毛及各种人造纤维、合成纤维)和金属材料(钢丝、铜丝)是作为橡胶制品的骨架材料,以增强机械强度、限制制品变型。
在原材料准备过程中,配料必须按照配方称量准确。
为了使生胶和配合剂能相互均匀混合,需要对某些材料进行加工:1.基本工艺流程伴随现代工业尤其是化学工业的迅猛发展,橡胶制品种类繁多,但其生产工艺过程,却基本相同。
以一般固体橡胶(生胶)为原料的制品,它的生产工艺过程主要包括:原材料准备→塑炼→混炼→成型→硫化→休整→检验2.原材料准备橡胶制品的主要材料有生胶、配合剂、纤维材料和金属材料。
其中生胶为基本材料;配合剂是为了改善橡胶制品的某些性能而加入的辅助材料;纤维材料(棉、麻、毛及各种人造纤维、合成纤维)和金属材料(钢丝、铜丝)是作为橡胶制品的骨架材料,以增强机械强度、限制制品变型。
在原材料准备过程中,配料必须按照配方称量准确。
为了使生胶和配合剂能相互均匀混合,需要对某些材料进行加工:生胶要在60--70℃烘房内烘软后,再切胶、破胶成小块;块状配合剂如石蜡、硬脂酸、松香等要粉碎;粉状配合剂若含有机械杂质或粗粒时需要筛选除去;液态配合剂(松焦油、古马隆)需要加热、熔化、蒸发水分、过滤杂质;配合剂要进行干燥,不然容易结块、混炼时旧不能分散均匀,硫化时产生气泡,从而影响产品质量;3.塑炼生胶富有弹性,缺乏加工时的必需性能(可塑性),因此不便于加工。
为了提高其可塑性,所以要对生胶进行塑炼;这样,在混炼时配合剂就容易均匀分散在生胶中;同时,在压延、成型过程中也有助于提高胶料的渗透性(渗入纤维织品内)和成型流动性。
橡胶生产工艺流程

橡胶生产工艺流程橡胶是一种重要的工业原料,广泛应用于汽车制造、建筑材料、医药等领域。
橡胶的生产工艺流程主要包括原材料采集、橡胶制备、混炼和成型四个步骤。
下面将详细介绍橡胶的生产工艺流程。
首先,原材料采集。
橡胶主要由橡胶树提供,并通过采集树液进行生产。
采集树液的过程被称为橡胶脱液,通常在早晨的时候进行。
工人会将树液从树干上切口处采集到集液器中,然后将橡胶脱水、净化并过滤。
然后是橡胶制备。
采集到的橡胶树液需要进行初步净化、干燥和固化,以去除杂质并变为固体状。
首先,将橡胶树液加热,使其变为胶态,并加入草木灰和石灰等材料进行固化。
然后,将固化后的橡胶进行蒸煮和搅拌,以增加其硫化性能和可塑性。
最后,经过冷却和干燥处理,得到成品橡胶。
接下来是混炼。
混炼是将橡胶与其他添加剂进行混合,以改善橡胶的性能和加工性。
首先,将橡胶放入混炼机中进行预热和破碎,使其变得柔软易塑。
然后,加入加工助剂、加硫剂、硫化剂等,进行搅拌和混合。
混炼的目的是使橡胶与添加剂充分融合,并达到所需的硬度、弹性和抗老化等性能。
最后是成型。
将混炼好的橡胶通过挤出机或压延机进行成型。
挤出机是将橡胶通过模具挤压成型,可以得到各种形状和尺寸的橡胶制品。
压延机是将橡胶通过辊筒压延成型,可以制造橡胶片、橡胶带等。
需要注意的是,橡胶的生产工艺还需考虑到橡胶的硫化。
硫化是橡胶加工的关键步骤,通过加热和加压使橡胶与硫化剂反应,形成交联结构,提高橡胶的强度、耐磨性和耐老化性能。
综上所述,橡胶的生产工艺流程包括原材料采集、橡胶制备、混炼和成型四个步骤。
每个步骤都起着重要的作用,决定了成品橡胶的质量和性能。
随着科技的进步,橡胶的生产工艺也在不断创新和改进,以提高生产效率和产品质量。
橡胶生产基本工艺流程介绍

橡胶生产基本工艺流程介绍橡胶生产是指将胶乳经过一系列工艺加工,制成橡胶制品的过程。
橡胶生产的基本工艺流程包括橡胶采集、橡胶预处理、橡胶混炼、橡胶压制成型、橡胶硫化等环节。
首先是橡胶采集。
橡胶是从橡胶树中采集得到的一种胶乳,一般采用刻刀划割橡胶树的皮肤,使胶乳流出,然后用容器接收胶乳。
橡胶采集主要在橡胶树早晨黎明时或下午降雨时进行,因为温度合适时胶乳产量较高。
接下来是橡胶预处理。
橡胶在采集后会产生一些杂质和水分,需要对橡胶进行预处理。
橡胶预处理包括清洗、割碎、过沟等环节。
首先是清洗,将橡胶浸泡在水中,去除表面的杂质。
然后是割碎,将橡胶切成小片状。
最后是过沟,将割碎的橡胶通过沟槽进行洗净和滤干。
然后是橡胶混炼。
橡胶混炼是将橡胶与各种添加剂进行充分混合和加工,使橡胶具有一定的黏度和强度。
橡胶混炼主要包括研磨、培育、裁切、内炼等环节。
首先是研磨,将预处理好的橡胶放入研磨机中进行研磨,使其更加柔软和易于混炼。
然后是培育,将研磨好的橡胶加入混炼机中,与各种添加剂进行混合,并通过机械切割和压榨使其混合均匀。
接下来是裁切,将混炼好的橡胶割成适当大小的块状。
最后是内炼,将裁切好的橡胶放入内炼机中进行高温和高压加工,使其成为柔软且有弹性的胶料。
接着是橡胶压制成型。
橡胶压制成型是将混炼好的橡胶胶料通过模具压制成各种形状的橡胶制品。
橡胶压制成型主要包括模具设计、模具制造、模具装卸、热压成型等环节。
首先是模具设计,根据橡胶制品的形状和尺寸要求设计模具。
然后是模具制造,根据设计好的模具图纸制造模具。
接着是模具装卸,将混炼好的橡胶胶料放入模具中,并将模具装入压机中进行压制。
最后是热压成型,将模具中的橡胶胶料在高温和高压下进行成型。
最后是橡胶硫化。
橡胶硫化是将压制好的橡胶制品经过一定时间的高温加热处理,使其具有较高的强度和耐磨性。
橡胶硫化主要包括硫化罐体设计、硫化曲线设计、硫化工艺参数控制等环节。
首先是硫化罐体设计,根据橡胶制品的尺寸和硫化工艺要求设计硫化罐体。
橡胶加工工艺流程

橡胶加工工艺流程橡胶加工是将天然橡胶或合成橡胶进行加工处理,制成各种橡胶制品的过程。
橡胶制品广泛应用于汽车、电子、医疗、建筑等领域,因此橡胶加工工艺的质量和效率对产品质量和生产成本有着重要影响。
下面将介绍橡胶加工的工艺流程。
1. 橡胶混炼。
橡胶混炼是橡胶加工的第一步,其目的是将橡胶与各种添加剂充分混合均匀。
混炼过程中需要将橡胶与填料、增塑剂、硫化剂等添加剂放入橡胶混炼机中,通过机械剪切和翻转,使各种添加剂均匀分散在橡胶中,形成均匀的混炼胶料。
2. 压延。
混炼后的橡胶胶料需要通过压延机进行压延,将其压成一定厚度的橡胶片。
压延机通过辊子的旋转将橡胶胶料不断压延,使其变得更加均匀、平整。
压延后的橡胶片可根据需要进行裁切或进一步加工。
3. 模压。
模压是将橡胶片通过模具加工成各种形状的橡胶制品的过程。
在模压过程中,橡胶片被放入模具中,经过一定的温度和压力作用下,形成所需的产品形状。
模压是橡胶加工中非常重要的一步,决定了最终产品的形状和尺寸精度。
4. 硫化。
硫化是橡胶加工中最关键的一步,通过硫化可以使橡胶获得良好的物理性能。
硫化过程中,橡胶制品放入硫化炉中,加热至一定温度,并在一定时间内进行硫化处理。
硫化可以使橡胶分子链发生交联,增强橡胶的强度、弹性和耐磨性。
5. 表面处理。
部分橡胶制品需要进行表面处理,以提高其外观质量和耐用性。
表面处理可以包括喷涂、印刷、抛光等工艺,使橡胶制品表面光滑、均匀,并且具有一定的装饰效果。
6. 检验与包装。
最后一步是对橡胶制品进行检验和包装。
检验包括外观质量、尺寸精度、物理性能等多个方面的检测,确保产品符合质量标准。
通过包装将橡胶制品进行包装,以便运输和销售。
综上所述,橡胶加工工艺流程包括混炼、压延、模压、硫化、表面处理、检验与包装等多个环节。
每个环节都需要严格控制,以确保最终产品的质量和性能。
随着橡胶工艺技术的不断发展,橡胶制品的品种和质量将会得到进一步提升,满足不同行业的需求。
- 1、下载文档前请自行甄别文档内容的完整性,平台不提供额外的编辑、内容补充、找答案等附加服务。
- 2、"仅部分预览"的文档,不可在线预览部分如存在完整性等问题,可反馈申请退款(可完整预览的文档不适用该条件!)。
- 3、如文档侵犯您的权益,请联系客服反馈,我们会尽快为您处理(人工客服工作时间:9:00-18:30)。
橡胶的工艺流程(精品)2014-10-22橡胶技术网橡胶工艺流程开始1 综述橡胶制品的主要原料是生胶、各种配合剂、以及作为骨架材料的纤维和金属材料,橡胶制品的基本生产工艺过程包括塑炼、混炼、压延、压出、成型、硫化6个基本工序。
橡胶的加工工艺过程主要是解决塑性和弹性矛盾的过程,通过各种加工手段,使得弹性的橡胶变成具有塑性的塑炼胶,在加入各种配合剂制成半成品,然后通过硫化是具有塑性的半成品又变成弹性高、物理机械性能好的橡胶制品。
2 橡胶加工工艺2.1塑炼工艺生胶塑炼是通过机械应力、热、氧或加入某些化学试剂等方法,使生胶由强韧的弹性状态转变为柔软、便于加工的塑性状态的过程。
生胶塑炼的目的是降低它的弹性,增加可塑性,并获得适当的流动性,以满足混炼、亚衍、压出、成型、硫化以及胶浆制造、海绵胶制造等各种加工工艺过程的要求。
掌握好适当的塑炼可塑度,对橡胶制品的加工和成品质量是至关重要的。
在满足加工工艺要求的前提下应尽可能降低可塑度。
随着恒粘度橡胶、低粘度橡胶的出现,有的橡胶已经不需要塑炼而直接进行混炼。
在橡胶工业中,最常用的塑炼方法有机械塑炼法和化学塑炼法。
机械塑炼法所用的主要设备是开放式炼胶机、密闭式炼胶机和螺杆塑炼机。
化学塑炼法是在机械塑炼过程中加入化学药品来提高塑炼效果的方法。
开炼机塑炼时温度一般在80℃以下,属于低温机械混炼方法。
密炼机和螺杆混炼机的排胶温度在120℃以上,甚至高达160-180℃,属于高温机械混炼。
生胶在混炼之前需要预先经过烘胶、切胶、选胶和破胶等处理才能塑炼。
几种胶的塑炼特性:天然橡胶用开炼机塑炼时,辊筒温度为30-40℃,时间约为15-20min;采用密炼机塑炼当温度达到120℃以上时,时间约为3-5min。
丁苯橡胶的门尼粘度多在35-60之间,因此,丁苯橡胶也可不用塑炼,但是经过塑炼后可以提高配合机的分散性顺丁橡胶具有冷流性,缺乏塑炼效果。
顺丁胶的门尼粘度较低,可不用塑炼。
氯丁橡胶得塑性大,塑炼前可薄通3-5次,薄通温度在30-40℃。
乙丙橡胶的分子主链是饱和结构,塑炼难以引起分子的裂解,因此要选择门尼粘度低的品种而不用塑炼。
丁腈橡胶可塑度小,韧性大,塑炼时生热大。
开炼时要采用低温40℃以下、小辊距、低容量以及分段塑炼,这样可以收到较好的效果。
2.2混炼工艺混炼是指在炼胶机上将各种配合剂均匀的混到生胶种的过程。
混炼的质量是对胶料的进一步加工和成品的质量有着决定性的影响,即使配方很好的胶料,如果混炼不好,也就会出现配合剂分散不均,胶料可塑度过高或过低,易焦烧、喷霜等,使压延、压出、涂胶和硫化等工艺不能正常进行,而且还会导致制品性能下降。
混炼方法通常分为开炼机混炼和密炼机混炼两种。
这两种方法都是间歇式混炼,这是目前最广泛的方法。
开炼机的混合过程分为三个阶段,即包辊(加入生胶的软化阶段)、吃粉(加入粉剂的混合阶段)和翻炼(吃粉后使生胶和配合剂均达到均匀分散的阶段)。
开炼机混胶依胶料种类、用途、性能要求不同,工艺条件也不同。
混炼中要注意加胶量、加料顺序、辊距、辊温、混炼时间、辊筒的转速和速比等各种因素。
既不能混炼不足,又不能过炼。
密炼机混炼分为三个阶段,即湿润、分散和涅炼、密炼机混炼石在高温加压下进行的。
操作方法一般分为一段混炼法和两段混炼法。
一段混炼法是指经密炼机一次完成混炼,然后压片得混炼胶的方法。
他适用于全天然橡胶或掺有合成橡胶不超过50%的胶料,在一段混炼操作中,常采用分批逐步加料法,为使胶料不至于剧烈升高,一般采用慢速密炼机,也可以采用双速密炼机,加入硫磺时的温度必须低于100℃。
其加料顺序为生胶—小料—补强剂—填充剂—油类软化剂—排料—冷却—加硫磺及超促进剂。
两段混炼法是指两次通过密炼机混炼压片制成混炼胶的方法。
这种方法适用于合成橡胶含量超过50%得胶料,可以避免一段混炼法过程中混炼时间长、胶料温度高的缺点。
第一阶段混炼与一段混炼法一样,只是不加硫化和活性大的促进剂,一段混炼完后下片冷却,停放一定的时间,然后再进行第二段混炼。
混炼均匀后排料到压片机上再加硫化剂,翻炼后下片。
分段混炼法每次炼胶时间较短,混炼温度较低,配合剂分散更均匀,胶料质量高。
2.3压延工艺压延是将混炼胶在压延机上制成胶片或与骨架材料制成胶布半成品的工艺过程,它包括压片、贴合、压型和纺织物挂胶等作业。
压延工艺的主要设备是压延机,压延机一般由工作辊筒、机架、机座、传动装置、调速和调距装置、辊筒加热和冷却装置、润滑系统和紧急停车装置。
压延机的种类很多,工作辊筒有两个、三个、四个不等,排列形式两辊有立式和卧式;三辊有直立式、Γ型和三角形;四辊有Γ型、L型、Z型和S型等多种。
按工艺用途来分主要有压片压延机(用于压延胶片或纺织物贴胶,大多数三辊或四辊,各辊塑度不同)、擦胶压延机(用于纺织物的擦胶,三辊,各辊有一定得速比,中辊速度大。
借助速比擦入纺织物中)、通用压延机(又称万能压延机,兼有压片和擦胶功能、三辊或四辊,可调速比)、压型压延机、贴合压延机和钢丝压延机。
压延过程一般包括以下工序:混炼胶的预热和供胶;纺织物的导开和干燥(有时还有浸胶)胶料在四辊或三辊压延机上的压片或在纺织物上挂胶依机压延半成品的冷却、卷取、截断、放置等。
在进行压延前,需要对胶料和纺织物进行预加工,胶料进入压延机之前,需要先将其在热炼机上翻炼,这一工艺为热炼或称预热,其目的是提高胶料的混炼均匀性,进一步增加可塑性,提高温度,增大可塑性。
为了提高胶料和纺织物的粘合性能,保证压延质量,需要对织物进行烘干,含水率控制在1-2%,含水量低,织物变硬,压延中易损坏,含水量高,粘附力差。
几种常见的橡胶的压延性能天然橡胶热塑形大,收缩率小,压延容易,易粘附热辊,应控制各辊温差,以便胶片顺利转移;丁苯橡胶热塑性小,收缩率大,因此用于压延的胶料要充分塑炼。
由于丁苯橡胶对压延的热敏性很显著,压延温度应低于天然橡胶,各辊温差有高到低;氯丁橡胶在75-95℃易粘辊,难于压延,应使用低温法或高温法,压延要迅速冷却,掺有石蜡、硬酯酸可以减少粘辊现象;乙丙橡胶压延性能良好,可以在广泛的温度范围内连续操作,温度过低时胶料收缩性大,易产生气泡;丁腈橡胶热塑性小,收缩性大,在胶料种加入填充剂或软化剂可减少收缩率,当填充剂重量占生胶重量的50%以上时,才能得到表面光滑的胶片,丁腈橡胶粘性小易粘冷辊。
2.4压出工艺压出工艺是通过压出机机筒筒壁和螺杆件的作用,使胶料达到挤压和初步造型的目的,压出工艺也成为挤出工艺。
压出工艺的主要设备是压出机。
几种橡胶的压出特性:天然橡胶压出速度快,半成品收缩率小。
机身温度50-60℃,机头70-80℃,口型80-90℃;丁苯橡胶压出速度慢,压缩变形大,表面粗糙,机身温度50-70℃,机头温度70-80℃,口型温度100-105℃;氯丁橡胶压出前不用充分热炼,机身温度50℃,机头℃,口型70℃;乙丙橡胶压出速度快、收缩率小,机身温度60-70℃,机头温度80-130℃,口型90-140℃。
丁腈橡胶压出性能差,压出时应充分热炼。
机身温度50- 60℃,机头温度70-80℃。
2.5注射工艺橡胶注射成型工艺是一种把胶料直接从机筒注入模性硫化的生产方法。
包括喂料、塑化、注射、保压、硫化、出模等几个过程。
注射硫化的最大特点是内层和外层得胶料温度比较均匀一致,硫化速度快,可加工大多数模压制品。
橡胶注射成型的设备是橡胶注射成型硫化机。
2.6压铸工艺压铸法又称为传递模法或移模法。
这种方法是将胶料装在压铸机的塞筒内,在加压下降胶料铸入模腔硫化。
与注射成型法相似。
如骨架油封等用此法生产溢边少,产品质量好。
2.7硫化工艺早先,天然橡胶的主要用途只是做擦字橡皮;后来才用于制造小橡胶管。
直到1823年,英国化学家麦金托什才发明将橡胶溶解在煤焦油中然后涂在布上做成防水布,可以用来制造雨衣和雨靴。
但是,这种雨衣和雨靴一到夏天就熔化,一到冬天便变得又硬又脆。
为了克服这一缺点,当时许多人都在想办法。
美国发明家查理?古德伊尔也在进行橡胶改性的试验,他把天然橡胶和硫黄放在一起加热,希望能获得一种一年四季在所有温度下都保持干燥且富有弹性的物质。
直到1839年2月他才获得成功。
一天他把橡胶、硫黄和松节油混溶在一起倒入锅中(硫黄仅是用来染色的),不小心锅中的混合物溅到了灼热的火炉上。
令他吃惊的是,混合物落入火中后并未熔化,而是保持原样被烧焦了,炉中残留的未完全烧焦的混合物则富有弹性。
他把溅上去的东西从炉子上剥了下来,这才发现他已经制备了他想要的有弹性的橡胶。
经过不断改进,他终于在1844年发明了橡胶硫化技术。
在橡胶制品生产过程中,硫化是最后一道加工工序。
硫化是胶料在一定条件下,橡胶大分子由线型结构转变为网状结构的交联过程。
硫化方法有冷硫化、室温硫化和热硫化三种。
大多数橡胶制品采用热硫化。
热硫化的设备有硫化罐、平板硫化机等。
2.8其他生产工艺橡胶制品的生产工艺还有浸渍法、涂刮法、喷涂法、蕉塑法等。
3橡胶配方设计3.1橡胶的硫化(交联)交联是橡胶高弹性的基础,其特点是在一个橡胶分子链上仅形成少数几处交联点,因此不会影响橡胶分子链段的运动。
橡胶的硫化体系较多,常见的有:硫黄硫化体系、过氧化物硫化体系、树脂硫化体系、氧化物硫化体系等3.1.1硫黄硫化体系主要适应于二烯类橡胶,其硫化活性点是在双键旁边的α氢原子。
组成:硫黄活性剂:氧化锌,硬脂酸促进剂:噻唑类(DM,M),次磺酰胺类(CZ,NOBS),秋兰姆类(TETD,TMTM,TMTD),胍(D)硫化体系硫黄/促进剂(S/A)比交联键组成性能特点普通硫黄硫化体系>1 以多硫键为主动态疲劳性能好;老化性能差半有效硫黄硫化体系(Semi-EV)≈1 以单硫键和双硫键为主老化性能好;压缩永久变形小;无硫化返原有效硫黄硫化体系(EV)《13.1.2过氧化物硫化体系-自由基机理1 常见的过氧化物有:DCP(二枯基过氧化物)、BPO、DCBP、双2,52 助交联剂:抑制聚合难自由基无用的副反应。
如TAIC,TAC,HVA-23 过氧化物硫化橡胶性能特点:老化性能好,压缩永久变形小,制品透明性好。
3.1.3氧化物硫化体系这是含卤素橡胶的主要硫化剂。
通常有氧化锌/氧化镁(5/4)、氧化铅或四氧化三铅(10-20,耐水制品)3.2橡胶的填料未加填料的橡胶,力学性能和工艺性能均较差,无法使用。
3.2.1作用补强性:拉伸强度,撕裂强度,耐磨性加工性能降低成本3.2.2填料的结构3.2.2.1粒径一般来说,粒径越小,强度越高。
表3 常用补强剂及填充剂的粒径范围(mμ)填料名称缩写料径范围槽黑23-30高耐磨炭黑HAF 26-35半补强炭黑SRF 60-130气相法白炭黑水合二氧化硅10-25沉淀法白炭黑10-40氧化锌ZnO 100-500轻质碳酸钙CaCO3 1000-3000超细碳酸钙白艳华25-100硬质陶土90% < 1000普通滑石粉TALC 5000-200003.2.2.2结构粒子形状及内部结构(吸油值法,DBP)。