塑料异型材挤出成型模具AutoUTOCAD设计
开式异型材挤出模通用机头CAD系统的研究与开发

机 械 设 计 与 制 造
~
第 9期
20 0 8年 9月
1 6一 5 文章编号:0 1 3 9 (0 80 — 16 0 10 — 9 7 20 )9 05 — 2
M a hi e y De i n c n r sg
Hale Waihona Puke &M a u a t r n fc u e
.
d el. em tosadep r n e edv l m n s ol e x n e . epy T ehd x ei so t eeo e t hudb t d d h n e c fh p ee
:
Ke r s Un v ra xr so o l g; u t e e eo me tS l W o k ; ywo d : i e s l tu in to i F rh rd v lp n ; oi e n d r s
i f xbed s n rtee t so oi a u rad a dteu i r l x ui oi A yt e il ei x ui t l gW p t ow r ,n nv s t so t l g C D ss m l gf h o r no n s f h e ae r n o n e r h p nn r lsw ihW p a ee& do e W eeoe T eds teet s nt l g eO e igPo e , hc a a a m t e n ,a dv l  ̄ h ei o h xr i oi t i f s r r s p n gf uo o n W p ae ydoe ep a t s I d c ae et eo s n adpe aig r a uatr g s a u dtd b r dt a mee . t ers d t i d i n r r f nfcui v h r r e h m f eg p no m n
冲压件1塑料件1的成型模具CADUG课程设计说明书

课程设计指导主题1:冲压件1和塑料件1的成型模具CAD题目:冲压件1和塑料件1成形模CAD专业类别号教师一、设计任务1.冲压件和塑料件1见附产品图,取第一套尺寸。
具体任务:1.制定冲压件和塑料件的规定成型工艺,正确选择成型设备;2.合理选择模具结构和必要的工艺计算;3.正确确定模具零件和其他零件的形状和尺寸;4.采用UG软件设计模具,并对模具进行虚拟装配,生成爆炸图,从而验证模具设计的正确性;5.利用UG绘图模块,完成模具装配图和工作零件图;6.撰写模具设计说明书;7.课程设计完成工作量:(1)冲压模具和塑料模具装配图1张(待打印);冲压模具工作部件的零件图;(2)设计说明书(包括冲压件的冲压工艺卡和塑件的成型工艺参数;模具设计计算过程;UG模具设计流程)。
二、设计要求1.在课程设计中,学生要独立思考和学习,学会根据具体情况灵活运用所学知识,不能盲目抄袭其他样本或他人设计;2.课程设计的每一个环节都必须认真细致的完成;3.设计应按计划进行,并保证设计的模具结构合理、操作方便、制造方便、成本低廉,设计图纸符合国家标准和行业标准,以及设计规范;4.设计时间表:(1)冲压工艺、冲压模具设计及绘制模具装配图和工作零件图2天;(2)塑料成型工艺、模具设计及绘制模具装配图和工作零件图2天;(3)写设计说明书,答辩1天(是否答辩由指导老师决定)。
5.提交材料(单独包装):(1)设计资料光盘(文件放在以下三个文件夹中:1设计说明书、2重庆亚木居、3住宿木居)(2)纸质印刷材料(冲压模具装配图、注塑模具装配图)序在现代社会,人们的日常生活与工业密切联系,工业及其工业产品触及人类生活的方方面面。
很多日常用品都是用模具制作的:比如机动车(大部分)、航空航天仪器、仪器仪表、家用电器、五金制品、塑料管等。
,几乎涵盖了整个模具行业,包括钣金制品、塑料件、压铸件等。
因此,模具是现代工业生产中生产各种产品(绝大多数)的重要工艺装备,模具制造的工艺水平和更新速度往往制约着上述行业产品的发展和更新速度。
(强烈推荐)冲压件1塑料件1的成型模具CAD UG设计毕业论文说
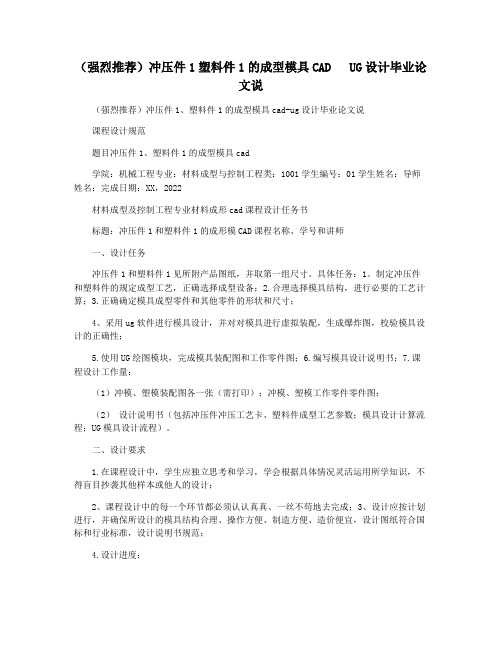
(强烈推荐)冲压件1塑料件1的成型模具CAD UG设计毕业论文说(强烈推荐)冲压件1、塑料件1的成型模具cad-ug设计毕业论文说课程设计规范题目冲压件1、塑料件1的成型模具cad学院:机械工程专业:材料成型与控制工程类:1001学生编号:01学生姓名:导师姓名:完成日期:XX,2022材料成型及控制工程专业材料成形cad课程设计任务书标题:冲压件1和塑料件1的成形模CAD课程名称、学号和讲师一、设计任务冲压件1和塑料件1见所附产品图纸,并取第一组尺寸。
具体任务:1。
制定冲压件和塑料件的规定成型工艺,正确选择成型设备;2.合理选择模具结构,进行必要的工艺计算;3.正确确定模具成型零件和其他零件的形状和尺寸;4、采用ug软件进行模具设计,并对对模具进行虚拟装配,生成爆炸图,校验模具设计的正确性;5.使用UG绘图模块,完成模具装配图和工作零件图;6.编写模具设计说明书;7.课程设计工作量:(1)冲模、塑模装配图各一张(需打印);冲模、塑模工作零件零件图;(2)设计说明书(包括冲压件冲压工艺卡、塑料件成型工艺参数;模具设计计算流程;UG模具设计流程)。
二、设计要求1.在课程设计中,学生应独立思考和学习,学会根据具体情况灵活运用所学知识,不得盲目抄袭其他样本或他人的设计;2、课程设计中的每一个环节都必须认认真真、一丝不苟地去完成;3、设计应按计划进行,并确保所设计的模具结构合理、操作方便、制造方便、造价便宜,设计图纸符合国标和行业标准,设计说明书规范;4.设计进度:(1)冲压件工艺、冲模设计并绘制模具装配图、工作零件图2天;(2)塑件成型工艺、模具设计并绘制模具装配图、工作零件图2天;(3)撰写设计说明书、答辩1天(是否需要答辩由指导老师决定)。
5、提交资料(单独装袋提交):(1)设计数据光盘(将文件放在以下三个文件夹中:1设计规范、2冲亚木居、3朱素木居)(2)纸质打印资料(冲压模具装配图,注塑模具装配图)前言现代社会,人类日常生活与工业的接触异常紧密,工业及其工业产产品涉及人类生活的方方面面,许多生活产品都是用模具制造的:例如,汽车(大部分)、航空航天仪器、仪器仪表、家用电器、五金制品、塑料管等,几乎覆盖了整个模具行业,包括钣金件、塑料件、压铸件等。
使用CAD进行模具设计和注塑工艺仿真

使用CAD进行模具设计和注塑工艺仿真使用CAD软件进行模具设计和注塑工艺仿真模具设计是制造业中非常重要的一环,它直接关系到产品的质量和生产效率。
而注塑工艺仿真则可以帮助工程师在设计阶段就进行模拟和预测,提前发现问题和优化解决方案。
在此,将着重介绍如何使用CAD软件进行模具设计和注塑工艺仿真。
首先,我们需要选择一款专业的CAD软件,如SolidWorks、CATIA、AutoCAD等。
这些软件都提供了强大的建模和仿真功能,可以满足不同类型的模具设计需求。
接下来,我们将以SolidWorks为例进行详细介绍。
在开始之前,我们需要准备好产品的三维模型。
可以从现有的CAD文件中导入模型,也可以利用软件的建模工具进行创建。
一旦模型准备完毕,我们就可以开始进行模具设计了。
首先,我们需要使用软件的建模工具创建模具的主体结构。
可以根据产品的尺寸和形状,使用不同的工具进行建模,如拉伸、旋转、倒角等。
需要注意的是,模具的设计应符合产品的要求,并且考虑到后续的注塑工艺。
接下来,我们需要添加模具的一些关键组件,如模仁、模座、顶针等。
这些组件将直接影响到产品的成型效果和质量。
在进行组件添加时,我们可以使用软件提供的库存件,也可以根据需要自行设计。
在组件的设计过程中,我们需要确保它们的尺寸和位置准确无误,并且能够实现所需的功能。
完成模具的主体结构和关键组件后,我们可以利用软件的装配功能将它们组合在一起。
这将帮助我们检查模具的各个组件之间是否存在干涉,并进行必要的调整。
一旦确认没有问题,我们就可以进入注塑工艺仿真的环节了。
在注塑工艺仿真中,我们可以通过对模具进行填充、冷却和收缩等分析,来预测和优化注塑成型的过程。
这将帮助我们避免一些常见的问题,如短流、翘曲、缺陷等。
同时,我们还可以通过仿真结果来指导模具的设计和优化,以提高产品的质量和效率。
在仿真过程中,我们可以根据实际需求和预测结果进行一些参数的调整,如注塑速度、温度、压力等。
基于AutoCAD小型注塑产品的模具设计

倒 圆角 R .。 05 其他锐 边倒圆角 R . , 02 底边缘不倒 角。
0 丑分淞
,
, 茁分 谨 / / E
命 令 :衄 e 一 t
当前 模 式 : 式 = 剪 , 径 = 0 0 0 模 修 半 1. 0 0
样 能 更 好 地 消 除 应 力 。 在 设 计 流 道 时 , 果 一 味追 求 对 称 性 , 如
圆 形 按钮 是 一 个 简单 的 小 型 注 塑 产 品 。一 般 来 说 . 圆形 按 钮 的 功 能 是 用 手 指 按 下 去 。 它 底 面 的机 构 受 力 向后 退 。松开 使 手 , 形 按 钮 可 以 复 位 , 可 以重 复 按 下使 之 复 位 。 圆形 按钮 圆 也
如图 1所示 的程序 。 中操作流程是一条直线结构 的步骤。 图 主
要 是利 用 Au C t AD 的“ 列 ” 能 设 计 型 腔 。小 型无 腔 注 塑 产 o 阵 功
品的模具通常 以上下两块模块组 合。其特点是 由于其 尺寸比
较 小 。 塑 成 型后 , 注 收缩 的几 何 尺 寸 也 很 小 , 得 产 生 的凝 固 使
就会显得繁琐 , 而且不利于加工 。通常加 工流道使用 的铣床执
行 的是 直 线 路 径 , 度 精 度 不 高 , 分 如果 要 加 工 较 多 的 呈 辐 射 状
的流道 . 不利于铣床加工 , 同时还 会降低模具的刚度 。因此在
型 腔排 布 数 量 多 的 情 况 下 , 用 A tC D设 计 流 道 时 可 采 用 利 uo A 矩 形阵 列 命 令 实 现 流 道 的 排布 。
指定 圆柱体底面的 中心 点或[ 圆() O 0 O :回车确定 椭 E] , 。> <
塑料异型材挤出模工程图自动标注系统研究
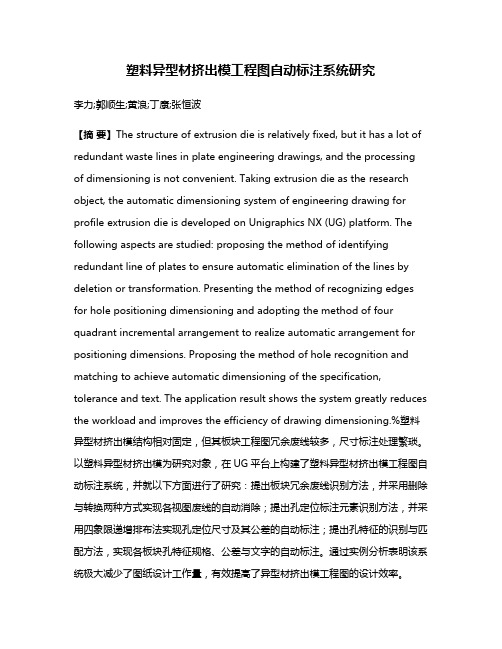
塑料异型材挤出模工程图自动标注系统研究李力;郭顺生;黄浪;丁康;张恒波【摘要】The structure of extrusion die is relatively fixed, but it has a lot of redundant waste lines in plate engineering drawings, and the processing of dimensioning is not convenient. Taking extrusion die as the research object, the automatic dimensioning system of engineering drawing for profile extrusion die is developed on Unigraphics NX (UG) platform. The following aspects are studied: proposing the method of identifying redundant line of plates to ensure automatic elimination of the lines by deletion or transformation. Presenting the method of recognizing edges for hole positioning dimensioning and adopting the method of four quadrant incremental arrangement to realize automatic arrangement for positioning dimensions. Proposing the method of hole recognition and matching to achieve automatic dimensioning of the specification, tolerance and text. The application result shows the system greatly reduces the workload and improves the efficiency of drawing dimensioning.%塑料异型材挤出模结构相对固定,但其板块工程图冗余废线较多,尺寸标注处理繁琐。
塑料挤出模头流道结构CAD系统研究与应用

塑料挤出模头流道结构CAD系统研究与应用【摘要】:塑料异型材流线型挤出模头形状复杂,模腔表面要求平滑过渡,无滞料,流速要求稳定增加,其结构设计和曲面设计难度大,目前主要依赖于设计者的经验和操作者的熟练程度,设计效率低,无法满足越来越高的整体质量要求。
针对以上问题,提出了模具内腔结构曲面的三维建模方法,基于UG和VS平台,应用UG/Open二次开发和MFC技术,实现了多封闭环快速识别,草图曲线一键排序,通过人机交互界面进行曲线匹配和曲面构造,从而搭建了从二维草图到三维建模的CAD集成模块,有效地提高了挤出模流道曲面设计效率和质量,并为后续CAE分析和CAM加工提供有力支撑。
Abstract:Plastic profile streamlined extrusion die head has a complex shape. For the die cavity surface,smooth transition, no lag material,and stability of the flowing velocity are required. It make s the design of structu re and surface is difficult and because of depending on the designer’expe rience and proficiency of the operator,the design efficiency is low and it can’t meet higher and h igher requirement of overall quality. To solve the above problems,the curved die design methodof the cavity structure is proposed. Based on the UG and VC platform,UG/Open secondary deve lopment and MFC technology were used,fast recognition algorithm of a multi-closed loop and on e-click sorting of the sketch curve were realized,and through the human-computer interaction to match curves and construct surface,and CAD integration module from 2 D sketch to 3 D modeli ng was set up,the efficiency of extrusion die flow surface design is effectively improved,and it provides strong support for CAE analysis and CAM processing.由于塑料异型材挤出模头内腔具有复杂的曲面,作为模头的关键部件,它的型面质量直接影响挤出产品的质量。
基于AutoCAD的典型注塑模具设计
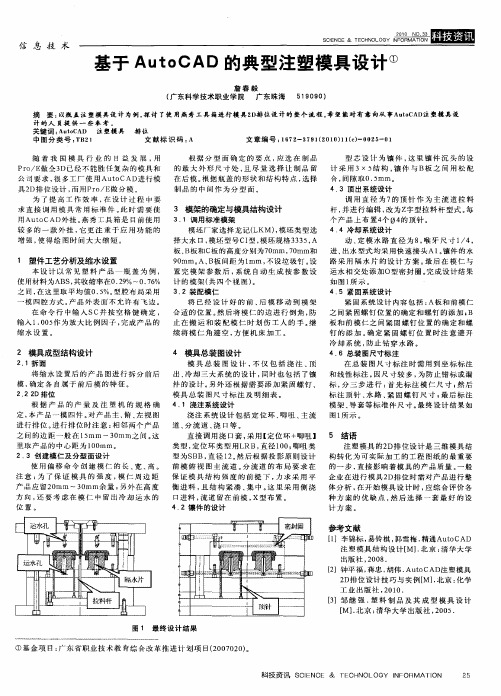
根 据 产 品 的 产 量 及 注 塑 机 的 规 格 确 4. 浇注 系统设 计 1 定 , 产 品 一 模 四件 。 产 品主 、 、 本 对 俯 左视 图 浇 注 系 统 设 计 包 括 定 位 环 、 咀 、 流 唧 主
模架 、 套 等 标 准 件 尺 寸 。 终 设 计 结 果 如 导 最
计 的 人 员提 供 一 些 参 考 。 关 键 词 : tC 注 塑模 具 排 位 Auo AD
中图分 类号 : B2 T 1
文 献标 识码 : A
文 章编 号 : 7 -3 9 ( 0 0 1 () 0 5 0 1 7 l2 1 ) 1c一0 2 - 1 62
随 着 我 国 模具 行 业 的 日益 发 展 , 用
计 采 用 3×5结 构 , 件 与 B板 之 间 用 松 配 镶 间隙 取0. mm。 5 在 后 模 。 据 瓶 盖 的形 状 和 结构 特 点 , 择 合 , 根 选 制 品 的 中 间 作 为 分 型面 。 4 3 顶 出系统 设计 .
为 了提 高 工 作 效 率 , 设 计 过 程 中 要 在 调 用 直 径 为 7 顶 针 作 为 主 流 道 拉 料 的 求 直 接 调 用 模 具 常 用 标 准 件 。 时 需 要 使 3 模架 的确定与模具结构 设计 此 杆 , 进 行 编辑 , 为 Z 型拉 料 杆 型 式 。 并 改 字 每 用 Aut oCAD外 挂 。 秀 工具 箱 是 目前 使 用 3. 燕 1调 用标 准模 架 个产 品上 布 置4 0 的 顶 针 。 个 4 较 多的 一 款 外 挂 , 更 注 重 于 应 用 功 能 的 它 模坯 厂 家 选择 龙 记 ( LKM) 模坯 类 型 选 4 , 4冷 却 系统设 计 增 强 , 得 绘 图时 间 大 大 缩 短 。 使 择 大 水 口, 模坯 型 号 C 型 , I 模坯 规 格 3 3 , 3 5A 动 、 模 水 路 直 径 为 8 喉 牙 尺 寸 l 4, 定 , /
塑料微管挤出模具CAD系统开发

塑料微管挤出模具CAD系统开发1 研发背景随着微/纳米科学技术的蓬勃发展,产品逐渐向微型化、小型化、轻量化方向发展,塑料成型技术也正悄然发生变化,传统的塑料挤出成型技术也正朝着微型化方向发展,出现了塑料微挤出成型技术。
成型出的微小截面塑料制品如介入导管、新型塑料光纤、汽车油气路塑料微管等在医学、通讯、汽车等领域应用越来越多,尤其是高技术含量、高附加值的介入疗法用微细导管。
介入治疗是一种新兴疗法,在不开刀的情况下,通过皮肤、血管上的微小通道,利用影像设备和医疗器械直接对病处进行局部微创治疗,由于这是一种简便安全、创伤小、副作用小的治疗方法,患者恢复速度快,药物使用量少,故发展迅速。
介入医疗器械除导管外还包括导管接头和导丝等,随着介入医疗技术的发展,其需求量越来越大。
介入导管是连接人体内外管腔制品的总称,在排液、投药、采血、灌流、辅助导入其他医疗器具和通过感应原件检测生物体状况等方面应用广泛。
其具有尺寸微小(外径<2?[、壁厚<0.2?[)、截面形状复杂、几何精度高、卫生指标高、生化稳定性高等特点。
受挤出设备、挤出模具和配套生产工艺技术的制约,目前我国医用介入导管主要依赖进口,其价格昂贵,每支从几十至几百或上千美元,严重制约了我国介入医学技术的研究和临床应用。
医用导管目前已成为一个高附加值、高技术含量的新兴产业,作为医疗器械的重要组成部分,具有很大的发展潜力。
在某种程度上,一个国家医用制品的生产技术、消费水平和产量,反映了该国的科技和经济水平.导管接头的主要作用是辅助导管完成介入治疗过程,其类型丰富,有接头开关、单腔管接头、双腔管接头、螺纹管接头、Y型接头等多种结构形式,每种接头均发挥着其不同的作用,可以满足不同的使用需求,如辅助控制导管的走向、将导管与其他装置相连、保护导管和控制药剂流量等。
通过不同导管接头间的配合使用,各类介入医疗器械被整合成一个整体,为治疗过程提供了方便。
研发意义聚合物挤出成型中,挤出模具是基础,也是挤出成型的重点和难点,它直接决定了挤出制品的质量和形状。
塑料异型材挤出模具

型坯挤出模头后受牵引经过气隙进入定型模 中,至少还将受到3种不能忽略的作用:
离模膨胀 拉伸变形 冷却收缩,
改变型坯截面的形状和尺寸→ 挤出模头出口截面形状的设计 必须考虑到这些作用的结果
离膜膨胀
聚合物熔体挤出物的尺寸和截面形状与挤出口 模不同,有明显的胀大,这一现象被称为巴拉 斯(Barus)效应,又称为离模膨胀(Die Swell)或 出口膨胀
选择异型材的挤出中心对分流流道的形状、大 小和方向,对均衡分流的影响会更加强烈。因 此,选择异型材的挤出中心,应该综合考虑分 流流道的结构设计
异型材挤出的方位
异型材挤出方位的选择主要取决于型材牵引夹持 的需要和定型模型腔的型板分块加工的有关要求
要求既能便于稳定地夹紧型材,又不至于让夹紧 力造成形状还没有完全稳定的异型材有大的变形, 要求异型材在挤出生产线上的上下两个面最好能 为平行面(异型材牵引几乎都是采用履带式牵引 装置,牵引力是通过两根履带的橡胶块夹持型材 来传递的)。
由于平缝口模的离模膨胀只发生在型坯壁厚 方向,所以可以认为该型材型坯的离模膨胀,以 口模缝隙中心线为中心对称发生,即型材壁厚中 心线之间的距离不受离模膨胀作用的影响,但仍 受到牵引收缩和冷却收缩两方面的作用,
-------5-9
型材壁厚中心线之间的距离不受离模膨胀的 影响,仅受到牵伸收缩和冷却收的作用
挤出模头设计
在塑料异型材挤出成型过程中,对于由挤 出机挤出的熔融的模塑料,挤出模头起着 稳流、分流和成型3种作用
通过挤出模头流道被挤出的模塑料型坯, 还须经过气隙之后,被牵引进入定型模进 行定型和冷却,才能最终成为塑料异型材 产品。
挤出模头流道的基本要求
①要有正确的出口截面形状
从模头挤出的异型材型坯的截面形状,不是 产品的最终截面形状,最多只是近似形状。
塑料异型材挤出定型模 CAD 系统

塑料异型材挤出定型模CAD系统*摘要: 针对塑料异型材挤出定型模分型繁琐、孔多易干涉、定型板块重复性设计等问题,提出了整体式设计和参数化设计方案。
设计了 1 套智能分型算法,自动创建分型片体,构建分型板块,当调用标准件时自动修改相应参数,智能加载。
基于 UG 平台,以 VC 为开发工具,应用 UG / Open 二次开发技术和 MFC 技术,通过人机交互界面进行参数化设计,开发了塑料异型材挤出定型模 CAD 系统,规范了定型模设计流程,提高了定型模设计效率。
塑料异型材是非圆管、板、片、膜等截面形状不规则的塑料制品,通过挤出成型加工制造,在建材等行业得到广泛应用。
1个成型的异型材挤出模生产线主要由送料装置、模头、定型、水箱、切料输送装置等部分构成。
其中模头和定型模是挤出模设计的重点与难点。
塑料门窗是常见的塑料异型材,其定型由相似的几节定型模构成,一般是 4 到 5 节,每节长度相等,不低于200 mm。
当有 5 节时,从靠近模头端起依次称为定一、定二、定三、定四、定五。
当对定型冷却要求不高时,定型可能只有 1 ~ 3节。
在某些特定情况下定型会有 6 ~ 7 节,更大的甚至有 10 节。
平开窗挤出模定一结构如图 1 所示,同一定型中,每一节定型模都是由上板、前板一、前板二、后板一、后板二、后板三、下板构成,定型模的板块数量主要根据分型需要确定,对双轨门窗而言,一般不会多于7 块板。
在实际生产中,当预成型的异型材型胚从模头出来进入定型时,温度还比较高。
在气槽处真空吸附力的作用下,型胚紧紧依附在定型模型腔壁上,在定型模冷却水路作用下进一步冷却固化最后进入水箱快速均匀冷却[1 - 3]。
由于异型材在不同温度下的应变变化,每一节定型模型腔会有细微变化,而随之分型面发生改变,导致 1 个完整的定型板块多且分型繁琐,从定二开始的每一节定模的设计都是重复性的设计,同时,定型模还存在孔多,易发生干涉等问题。
传统的挤出模具设计更依赖于设计人员的经验,对设计人员的要求高,其 CAD 设计也主要停留在二维设计上。
AutoCAD在塑料成型模具设计中的应用 工程
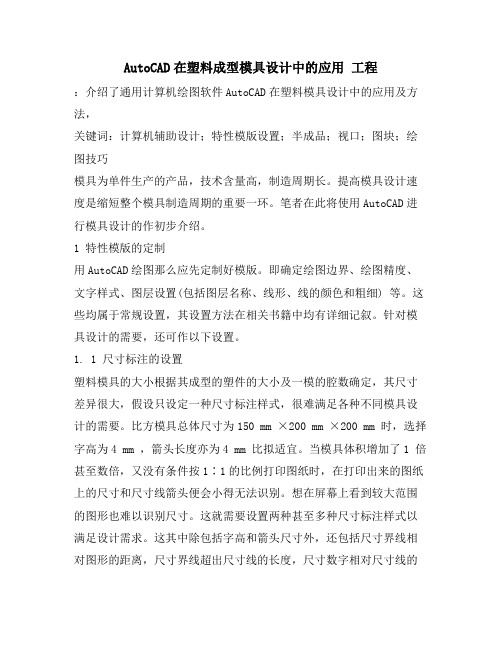
AutoCAD在塑料成型模具设计中的应用工程:介绍了通用计算机绘图软件AutoCAD在塑料模具设计中的应用及方法,关键词:计算机辅助设计;特性模版设置;半成品;视口;图块;绘图技巧模具为单件生产的产品,技术含量高,制造周期长。
提高模具设计速度是缩短整个模具制造周期的重要一环。
笔者在此将使用AutoCAD进行模具设计的作初步介绍。
1 特性模版的定制用AutoCAD绘图那么应先定制好模版。
即确定绘图边界、绘图精度、文字样式、图层设置(包括图层名称、线形、线的颜色和粗细) 等。
这些均属于常规设置,其设置方法在相关书籍中均有详细记叙。
针对模具设计的需要,还可作以下设置。
1. 1 尺寸标注的设置塑料模具的大小根据其成型的塑件的大小及一模的腔数确定,其尺寸差异很大,假设只设定一种尺寸标注样式,很难满足各种不同模具设计的需要。
比方模具总体尺寸为150 mm ×200 mm ×200 mm 时,选择字高为4 mm ,箭头长度亦为4 mm 比拟适宜。
当模具体积增加了1 倍甚至数倍,又没有条件按1∶1的比例打印图纸时,在打印出来的图纸上的尺寸和尺寸线箭头便会小得无法识别。
想在屏幕上看到较大范围的图形也难以识别尺寸。
这就需要设置两种甚至多种尺寸标注样式以满足设计需求。
这其中除包括字高和箭头尺寸外,还包括尺寸界线相对图形的距离,尺寸界线超出尺寸线的长度,尺寸数字相对尺寸线的距离等等,均需调整适宜。
假设逐一调整,比拟繁琐。
这里介绍一种简便方法,仅调整尺寸标注样式中的“整体比例”即可。
具体方法如下。
点击工具按钮“Dimension Style. (尺寸标注样式) ”,翻开“Dimension Style. Manager (尺寸标注样式器) ”对话框,单击对话框中“New ...(新建) ”按钮,翻开“C reate New Dimension Style. (增添新的尺寸标注样式) ”对话框,在“New Style. Name”框中输入新的名称,如“2 倍机械图”,然后单击“Continue”键,出现对话框“New Dimension Style.:2 倍机械图”,翻开对话框中“Fit (匹配) ”标签页,在“Scale For Dimension Features(比例缩放尺寸特征) ”栏中将“Use overall Dimension scale of (使用整体尺寸比例) ”单项选择框中的“1”改为“2”,然后单击“OK”,回到“Dimension Style. Manager”对话框,会看到“Styles”栏中多了刚设置的类型。
基于UG的塑料异型材挤出模CAD建模系统

分流支架 设计 型芯 设计 分 流惟设计
自动绘图
—
l
一
l
J
口‘ z)
一
p( z
~
一
一
( ) 模 子 系 统 C D 搋 程 Il b建 A 墼
蕊雕嘲鼬蛐嘲
圈 1挤 出 模 C AD系 统 图
F g CAD y tm fExr so e i .1 s se o tu i n Di
个 系统的先进性 、 成熟性 、 经济合理性 。 完成后的系统具有并行 工程思想 、 多轨制的分析程序 、 闭环 C D、 A 可扩充性几个方面功
2 2口模 图形的确 定 .
口模板是挤出模 上型材坯料的出 口,对型材的外形尺寸起
着至关重要的作用。而 口模 图形是 口模板设计的关键所在,也 是整个模具设计的关键 。口模板设计是塑料异型材制 品断画图
1 异型材挤出模 C D建模技术方案 A
挤 出模 C D C M系统在软件工程的思想指导下 。 A /A 保证整
1O 0 0 10 1 0 . 4— . 510 1 1 0— . 10 0 — . 815— . 8 2 010 0 0 5 5x1'0 3 0 4 . 5 . 5 n 0 0 0 . 1 0 0 , 3 0
设计程序 口横图形设计 成型板设计
品密实…。 对流道的初步设计 , 主要是解决 流道 内压力降的平衡 问题 ,则需要对塑料 熔体进行流体微元受力分 析和流动分析 。
如 图 2所 示 :
图形数据库
横塑料 参数 挤 出机 参数 横具 材料性 能
预成型扳设计
压缩板设 计
模具设计参数
图 2流 体 微 J 受力 分计 L
塑料异型材挤出成型模具CAD系统
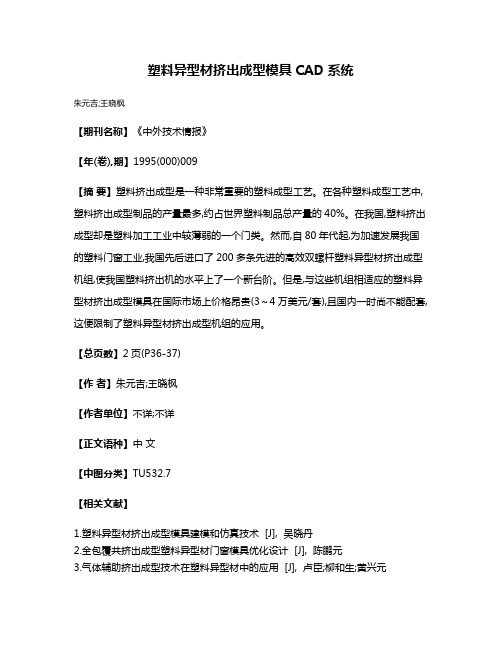
塑料异型材挤出成型模具CAD系统
朱元吉;王晓枫
【期刊名称】《中外技术情报》
【年(卷),期】1995(000)009
【摘要】塑料挤出成型是一种非常重要的塑料成型工艺。
在各种塑料成型工艺中,塑料挤出成型制品的产量最多,约占世界塑料制品总产量的40%。
在我国,塑料挤出成型却是塑料加工工业中较薄弱的一个门类。
然而,自80年代起,为加速发展我国的塑料门窗工业,我国先后进口了200多条先进的高效双螺杆塑料异型材挤出成型机组,使我国塑料挤出机的水平上了一个新台阶。
但是,与这些机组相适应的塑料异型材挤出成型模具在国际市场上价格昂贵(3~4万美元/套),且国内一时尚不能配套,这便限制了塑料异型材挤出成型机组的应用。
【总页数】2页(P36-37)
【作者】朱元吉;王晓枫
【作者单位】不详;不详
【正文语种】中文
【中图分类】TU532.7
【相关文献】
1.塑料异型材挤出成型模具建模和仿真技术 [J], 吴晓丹
2.全包覆共挤出成型塑料异型材门窗模具优化设计 [J], 陈鹏元
3.气体辅助挤出成型技术在塑料异型材中的应用 [J], 卢臣;柳和生;黄兴元
4.计算机辅助系统在塑料异型材挤出成型中的应用研究 [J], 陈丽
5.塑料异型材气辅挤出成型实验 [J], 柳和生;卢臣;黄兴元
因版权原因,仅展示原文概要,查看原文内容请购买。
矩形截面型材挤出模具AutoCAD自动设计
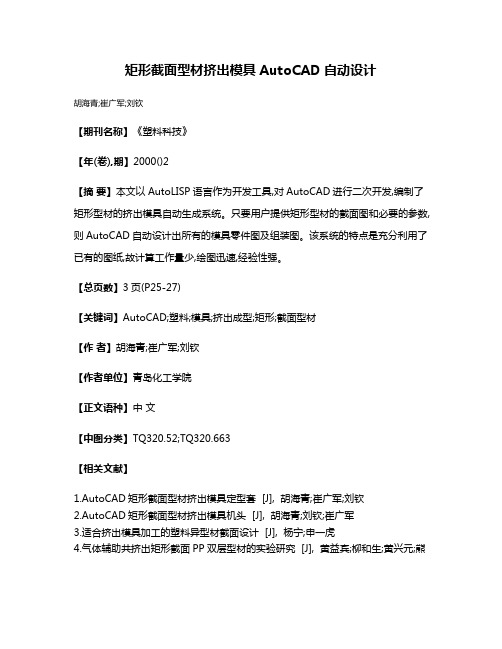
矩形截面型材挤出模具AutoCAD自动设计
胡海青;崔广军;刘钦
【期刊名称】《塑料科技》
【年(卷),期】2000()2
【摘要】本文以AutoLISP语言作为开发工具,对AutoCAD进行二次开发,编制了矩形型材的挤出模具自动生成系统。
只要用户提供矩形型材的截面图和必要的参数,则AutoCAD自动设计出所有的模具零件图及组装图。
该系统的特点是充分利用了已有的图纸,故计算工作量少,绘图迅速,经验性强。
【总页数】3页(P25-27)
【关键词】AutoCAD;塑料;模具;挤出成型;矩形;截面型材
【作者】胡海青;崔广军;刘钦
【作者单位】青岛化工学院
【正文语种】中文
【中图分类】TQ320.52;TQ320.663
【相关文献】
1.AutoCAD矩形截面型材挤出模具定型套 [J], 胡海青;崔广军;刘钦
2.AutoCAD矩形截面型材挤出模具机头 [J], 胡海青;刘钦;崔广军
3.适合挤出模具加工的塑料异型材截面设计 [J], 杨宁;申一虎
4.气体辅助共挤出矩形截面PP双层型材的实验研究 [J], 黄益宾;柳和生;黄兴元;熊
爱华
5.美式截面PVC塑料异型材挤出模具的设计 [J], 肖学仕
因版权原因,仅展示原文概要,查看原文内容请购买。
- 1、下载文档前请自行甄别文档内容的完整性,平台不提供额外的编辑、内容补充、找答案等附加服务。
- 2、"仅部分预览"的文档,不可在线预览部分如存在完整性等问题,可反馈申请退款(可完整预览的文档不适用该条件!)。
- 3、如文档侵犯您的权益,请联系客服反馈,我们会尽快为您处理(人工客服工作时间:9:00-18:30)。
工业设计之模具工艺原创塑料异型材挤出成型模具AutoUTOCAD设计李辉塑料异型材大多采用PVC—U塑料,其配方成分复杂,制品的结构和形状复杂,且配合尺寸和精度要求高,故而影响挤出成型的因素较多,模具设计难度也较大。
机头设计机头设计理念:①支承板流道截面积为口模截面积的4倍以上,便于调节料流速度和异型材挤出形状。
②要有足够的压缩比和定型长度,以保证制品密实和消除熔接痕。
③异型材横截面厚的部位定型段长度要比薄的部位长,以均一流速,防止制品变形。
④模腔的流量与定型长度成反比,与口模间隙的三次方成正比。
⑤制品形状复杂部位,料流多,压缩角要大一些。
⑥平直段过长,则机头压力大,挤出速度慢,机头负荷大;⑦平直段过短,则物料不稳,型材内应力大,易变形,型材强度低。
1、机头结构选择其主要组成部分如图一所示。
模具设计时一般采用此结构,尤其适用于塑料门窗的主型材等复杂断面形式。
其优点在于:①有利于对PVC—U料流进行加热塑化,使其内外温度趋于均匀。
②减少易引起紊流的压缩段的长度,使PVC—U料流尽可能地形成稳定流动,有利于减少离模膨胀(也称Barus效应)。
③分流锥是平直走向,有利于减少料流阻力,预防高聚物受热降解。
④型芯内开设了单独给内筋供料的流道腔,有利于减少PVC—U料流在模内的界面应力,有利于减少形变应力。
2、机头流道设计近几年,机头流道设计中开始运用塑料流变学原理,但PVC—U异型材,尤其是塑料门窗异型材机头内料流的特殊流动形式,国内外仍在研究之中,大多还是靠经验设计和试模修正的方法。
①塑料门窗异型材截面重心的位置坐标塑料门窗异型材截面重心必须位于挤出机的输出物料的中心轴线上,以确保熔融物料对复杂中空异型材截面有较均匀的分布。
用AutoCAD软件可以容易地求出截面重心的位置坐标。
先用region,Subtract等命令把截面图形组成一个面域,再用list命令可以方便地查出重心的X、Y值。
②口模横截面型腔尺寸对于异型材流道理论计算可参阅相关的书籍,一般可作为设计验证,本文拉伸比、成型收缩比。
A、口模间隙计算求成型壁厚的间隙h,对于异型材壁厚H,筋厚T有经验数据统计表明:——壁厚H大于2.5mm,口模间隙h=0.85~0.89H。
——壁厚H小于2.5mm大于2mm,口模间隙h=0.9~0.95H。
——筋厚T大于1.5mm,口模间隙h=0.9~1T。
——筋厚T小于1.5mm,口模间隙h=0.8T。
——毛条开口处取系数0.9,胶条开口处取系数0.95,压条开口处取系数1。
——实际挤出生产中,牵引拉伸比、冷却收缩对异型材截面的型腔尺寸影响大,而离模膨胀比对内筋影响甚大,因而对于口模中类似突筋、卡脚突起结构的部分间隙,考虑到其由于物料流动性能与膨胀不同而产生较大的收缩,其系数一般取1.04~1.1,通常取1.06左右。
对于型材突起部分一般为塑料门窗的配合部分,尺寸大多数是相同的。
在不断地总结试模经验的基础上,可利用Autolisp编写程序实现模块化设计,以利于提高设计开发速度。
B、口模型腔外形尺寸计算对于塑料门窗外形尺寸放大系数γ,一般取1.02~1.06,其中半开式取1.05~1.06,开式取1.1~1.5,高速挤出取1.03,低速挤出取1.05。
相对大尺寸的横截面的粘贴命令中的X、Y方向输入不同的数值来计算图形的形状。
设计口模型腔的外形及型芯的步骤:——求出定型模型腔外的图形。
(具体参见定型模设计2)——对定型模型腔外形的图形放大γ倍(AutoCAD中用Scale命令),求出口模型腔外形。
——根据口模的间隙,依次求出各个型芯的图形。
C、口模形状修正有些塑料门窗型材的空腔过小,给型芯的强度与机械加工带来一定的困难,可对其口模形状进行放大处理,再靠定型模的定型作用来回复原来结构的尺寸要求(如图2所示)。
图2图3a 图3b易出现制品弯筋的现象。
对于模具温度△T从200℃降到60℃,查表得PVC—U的线性收缩率α为(5~18.5)×10-5/℃,则△L=Lα△T。
考虑到料流在缝隙机头中的流动性,一般△L取0.5~0.8。
③机头成型段长度的计算A、理论法(塑料门窗型材机头可作为缝隙机头的数学模型)L=PWh3/12Qη其中:P—异型材机头的挤出压力。
单螺杆挤出机机头挤出压力一般为8~12MPa,双螺杆则为12.5~20MPa。
有条件的应测出挤出压力的实际数据。
W—口模缝隙当量宽度cm,即为异型材中型层的宽度。
h—口模缝隙当量高度cm,即口模壁厚间隙。
η—熔融物料表观粘度Pas。
Q—口模流量cm3/s。
Q=GV/pmG—异型材每米长的理论重量g/m。
V—异型材挤出时牵引速度m/s。
pm—熔融物料密度g/cm3。
B、经验法成型段长度的经验公式L=(30~40)h(h为模壁厚间隙),求出的数值应代非牛顿流体在宽扁孔模壁处剪切速率v=6Q/Wh2。
验证剪切速率是否超过临界剪切速率。
综上所述,PVC—U的临界剪切速率以-40s-1为佳,口模挤出压力不超过80mm。
异型材断面尺寸小,取偏小值,反之则取偏大值。
成型段长短直接影响到机头挤出压力和产量高低,因而在不超过临界剪切速率的前提下,尽可能地实现高产和高质量的型材。
④压缩角的计算压缩段的作用:使物料产生一定的压缩比,以保证有足够的挤压力,消除由于支承筋而产生的熔接痕,从而形成塑化均匀、密实度良好、内应力小的型胚。
设计时应在压缩角的大小(15°~20°),压缩比ε、压缩段长度L(15~35mm)三者之间合理调整地其数据(如图4)。
图4PVC—U物料不宜采用过高的压缩比,一般取4~8t(t为壁厚),常用3.6t。
异型材断面尺寸小,取偏小值。
压缩比过大,导致模压上升,螺杆背压和扭矩明显增大。
压缩比过小,会使物料在模腔流动不稳,塑化程度不够。
实际的压缩比应是支承板与口模型芯的压缩角(内筋)应2倍于,L长度要大些(如图5)。
⑤机头进料部位的计算A、机颈设计由支架板型腔的各点与多孔板相对应的各点相连组成机颈型腔的三维面(在Pro/E 软件中应用),求出最大角度值。
若最大值小于60°,则应调整压缩角的大小。
一般来说,模体的型腔比较复杂、沟槽多、狭缝多,传统的加工手段用摇臂铣床加工,易产生死角和停滞区,PVC—U物料就会发生过热分解。
现一般采用慢走丝线切割来加工机颈型腔异型部分。
图5B、分流锥设计挤出成型有别于其它成型工艺的显著特点,是物料及制品的成型、定型始终是在连续的、动态的过程中进行。
因而要求料流及其工艺因素应尽量突出一个”稳”字。
要有稳定的温度、稳定的压力、稳定的料流与型坯、稳定的冷却水流、稳定的真空、稳定的牵引等(如图6)。
图6多孔板距离分流锥头部空间较大,并有锥度,料流通过该区段达到初步有序流动,并有较小的背压,最大限度减少了刚从挤出机不稳定料流对机头内稳定料流的影物料阻力大,α太小,不利于料层很快变薄,对加热不利。
经验数据如下:K:10~20mm或稍小于0.1Ds;30°≤α≤50°;L≈1~1.5D0;R=0.5~2mm加热系统设计加热线圈最好设计成四个单独工作的电热板,若口模处的物料流速不均匀时可通过温度来调节。
理论公式:加热线圈加热功率W=CpV(t-t0)3600η其中:p——模具钢材的比重9.8g/cm3V——模具总体积cm3C——模具钢材比热容KJ/Kg℃t——模具工作温度℃t0——模具起始温度℃η——加热线圈效率,常取0.3~0.5经验公式:0.04×模具的重量(Kg)考虑到挤出机料筒自身加热及料流在模具内由剪切产生的热量,因而一般取比计算值偏小的值。
定型模设计定型模通过真空将型坯吸附在模具壁上进行冷却定型,获得所需异型材的尺寸和形状精度,并在此过程中将型胚的形变内应力和热内应力基本消除。
1、合理的结构设计结构设计原则:①选择上、下分型面要考虑便于操作,出故障时能取出型胚,易于清理。
②冷却水孔分布均匀。
③真空吸附足够且均匀。
④真空槽(孔)和冷却水道加工工艺性好。
⑤水冷回路和真空吸附回路分别相联组成独立的、可循环的系统,要交替设置,但不能串通。
现在行业内普遍采用干式真空定型模(如图7)及包抄式真空定型模(如图8)。
图7干式真空定型模比较常见,现把设计时要注意的要点整理如下:①真空吸附面积和真空槽(孔)设计:A、真空吸附面积真空吸附面积S=0.67fG/M其中:G——型材每米的重量Kg/mf——系数,取16~30,f与型材、壁厚、质量、真空度有关M——定型模真空度,一般在-0.05~0.08MPa算出的数值需验证,可按下式验证:牵引力/真空吸附面积<型材的拉伸强度,其结果必须小于型材的拉伸强度(≥36.8MPa),否则要调整真空吸附面积和牵引力。
B、真空槽(孔)设计由于进入第一节定型模时,挤出的型胚仍是粘流态,易被吸入真空沟槽中,故第一段定型模的前面1~6道的真空吸附沟槽宽度采用0.8mm,间距为25~30mm,其余沟槽宽度为1.2mm,间距为30~40mm。
吸附力要布置均匀,定型模上下两半真空沟槽要对齐,并要各自相通,但在分型面处尽量与大气相通。
在型胚的筋和棱边的部位要有较大的吸附力(冷却慢),故应使抽气孔对准筋和棱边。
②冷却水路设计定型模冷却水路设计应注意:A、根据型胚所含热量的分布来布置水路。
B、水路应尽量靠近定型模型腔,水孔孔壁与型腔距离大于5mm,上下定型板的水孔的中心距应大于14mm。
水孔孔壁与真空槽孔的距离应大于3mm,以防止距离过薄,加工时引起水气相穿的现象。
C、定型模上型板冷却速率应大于下型板。
因为模脚与定型台相连利于传热,型胚由于自重的作用与下型板的型腔面贴合得更好,也利于传热。
③本文侧重推荐包抄式真空定型模(如图8所示)。
其优点在于:它兼顾了冷却水道的均匀性和大的冷却水道面积这两大因素。
其特征是冷却水道与型腔的外形呈平行闭合状,包容了全部型腔,显然大大提高了冷却水道的面积;加之冷却水是沿型腔的外形呈双向包抄乎可以达到一致。
且该定型模的冷却水道在定型模的纵截面方向呈螺旋状布置,并设置在真空区域内,因而在整个定型模型腔各处的冷却都很均匀。
这种高冷却效率、高冷却均匀性的定型模对于提高型材的挤出速度很有意义。
另外,由于该结构形式的定型模的型腔、水槽、气槽可采用一次整体加工而成,对于降低模具制造成本,提高模具制造精度也是很有意义的。
该形式的定型模已获国家专利(ZL00218173.8)。
为了提高挤出产量及异型材制品的质量,便于定型模装卸,定型模可采用浮动定位形式置于挤出机辅机上。
此结构形式目前正在申请国家专利。
2、定型模型腔尺寸计算一般来说,挤出速度越快,型腔横截面平面应越凸翘,相应外形尺寸要越大;制品壁越厚,型腔的横截面应越凸翘,相应外形尺寸要越大,反之亦然;定型模越长,其型腔的横截面平面越平坦,尺寸越小,反之亦然;冷却定型水箱无真空负压时,则定型模型腔尺寸应大,横截面平面越凸翘,反之亦然。