高速磨削工艺特点及其发展现状
高速超高速磨削技术发展与关键技术

* 国家自然科学基金资助项目(编号:50475052) 教育部科学技术研究重点项目(编号:104190)高校博士学科点专项科研基金资助项目(编号:20040145001)高速超高速磨削技术发展与关键技术*青岛理工大学 机械工程学院 ( 266033) 李长河东北大学 机械工程与自动化学院 (110004) 修世超 蔡光起摘 要 论述了高速超高速磨削加工技术的发展、特点以及关键技术。
关键词 高速超高速 磨粒加工 关键技术1 高速/超高速磨削技术发展超高速磨削技术是现代新材料技术、制造技术、控制技术、测试技术和实验技术的高度集成,是优质与高效的完美结合,是磨削加工工艺的革命性变革。
德国著名磨削专家T.Tawakoli 博士将超高速磨削誉为“现代磨削技术的最高峰”。
日本先端技术研究学会把超高速加工列为五大现代制造技术之一。
在1996年国际生产工程学会(CIRP )年会上超高速磨削技术被正式确定为面向21世纪的中心研究方向之一,是当今在磨削领域最为引人注目的技术。
高速加工(High-speed Machining)和超高速加工(Ultra-High Speed Machining )的概念是由德国切削物理学家Carl.J.Salomon 博士于1931年首先提出,他发表了著名的Salomon 曲线,创造性地预言了超越Talor 切削方程式的非切削工作区域的存在,提出如能够大幅度提高切削速度,就可以越过切削过程产生的高温死谷而使刀具在超高速区进行高速切削,从而大幅度减少切削工时,成倍地提高机床生产率。
他的预言对后来的高速甚至超高速磨削的发展指明了方向,为高速超高速磨削技术研究开辟了广阔的空间,对于高速超高速磨削技术的实用化也起到了直接的推动作用。
通常将砂轮线速度大于45 m/s 的磨削称为高速磨削,而将砂轮线速度大于150 m/s 的磨削称为超高速磨削。
超高速磨削在欧洲、日本和美国等发达国家发展较快。
欧洲高速超高速磨削技术的发展起步比较早, 最初在20世纪60年代末期就开始进行高速超高速 磨削的基础研究,当时实验室的磨削速度就已经达到210~230 m/s 。
磨削技术论文:超高速磨削及其优势探析
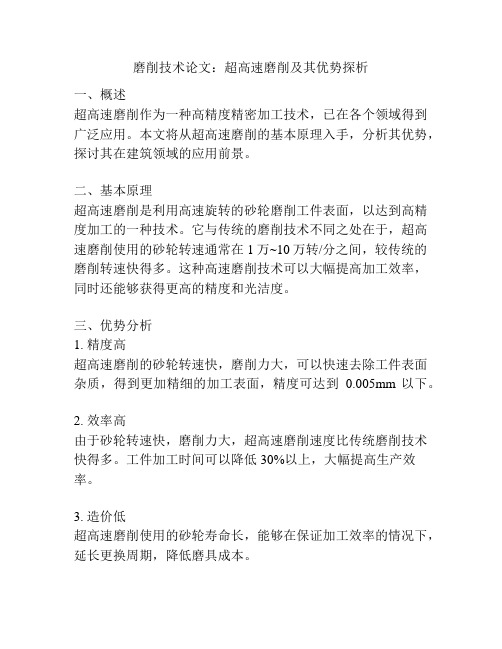
磨削技术论文:超高速磨削及其优势探析一、概述超高速磨削作为一种高精度精密加工技术,已在各个领域得到广泛应用。
本文将从超高速磨削的基本原理入手,分析其优势,探讨其在建筑领域的应用前景。
二、基本原理超高速磨削是利用高速旋转的砂轮磨削工件表面,以达到高精度加工的一种技术。
它与传统的磨削技术不同之处在于,超高速磨削使用的砂轮转速通常在1万~10万转/分之间,较传统的磨削转速快得多。
这种高速磨削技术可以大幅提高加工效率,同时还能够获得更高的精度和光洁度。
三、优势分析1. 精度高超高速磨削的砂轮转速快,磨削力大,可以快速去除工件表面杂质,得到更加精细的加工表面,精度可达到0.005mm以下。
2. 效率高由于砂轮转速快,磨削力大,超高速磨削速度比传统磨削技术快得多。
工件加工时间可以降低30%以上,大幅提高生产效率。
3. 造价低超高速磨削使用的砂轮寿命长,能够在保证加工效率的情况下,延长更换周期,降低磨具成本。
4. 应用范围广超高速磨削是一种高效、环保、精细化的磨削技术,可适用于各种材料的加工,包括金属、非金属材料、陶瓷材料等。
5. 环保超高速磨削使用的是无毒、无害、无污染的磨料,减少了对环境的污染。
四、应用前景在建筑领域,超高速磨削技术可以用于加工各类构件。
它能够大幅节约加工时间,提高生产效率。
同时,它还能精细加工各类构件表面,达到工艺标准,节约原材料,降低生产成本。
在未来,超高速磨削技术有望得到更加广泛的应用。
五、案例分析1. XXX公司的构件加工中,采用超高速磨削技术,成功优化了加工效率,降低了产品成本,得到了客户的一致好评。
2. XX公司将超高速磨削技术应用于钢筋加工中,减少了加工时间,提高了钢筋的精度和尺寸的一致性,受到了建筑公司的赞扬。
3. XX公司采用超高速磨削技术加工门窗构件,成功提高了构件的表面精度和光洁度,降低了产品的废品率,提高了客户的满意度。
4. XX公司采用超高速磨削技术加工凸轮、传动齿轮等构件,减少了加工时间,提高了精度和表面光洁度,获得了广泛应用。
超过速磨削的技术及发展

超高速磨削砂轮的发展及关键技术超高速磨削通常指砂轮速度大于150m/s的磨削。
超高速磨削在欧洲、日本和美国等发达国家发展很快,被誉为“现代磨削技术的最高峰”。
国际生产工程学会(CIRP)将其确定为面向21世纪的中心研究方向,并进行了一些著名的合作研究。
超高速磨削可以对硬脆材料实现延性域磨削加工,对高塑性等难磨材料也有良好的磨削表现。
与普通磨削相比,超高速磨削显示出极大的优越性: 大幅度提高磨削效率,减少设备使用台数。
如采用电镀CBN砂轮以123m/s的高速磨削割草机曲轴,原来需要6个车削和3个磨削工序,现在只需要3个磨削工序,生产时间减少65%,每小时可以加工180件。
再如人们以125m/s的速度应用普通砂轮高效磨削淬硬低碳钢42CrMo4,切除率达167mm3/mms,比缓进给磨削大11倍。
磨削力小,零件加工精度高。
速度360m/s以下的试验表明,在一个较窄的速度范围(180-200 m/s)内,摩擦状态由固态向液态急剧变化,并伴随着磨削力的急剧下降。
笔者在单颗磨粒高速磨削45钢和20Cr钢试验中发现,摩擦系数在临界速度以下,随速度的增大而大幅度减少;超过临界速度后,摩擦系数却随速度的增大而略有增加。
降低加工工件表面粗糙度。
在其它条件相同时33m/s,100m/s和200m/s的速度磨削时,表面粗糙度值分别为Ra2.0,Ra1.4和Ra1.1μm。
砂轮寿命延长。
在金属切除率相同的条件下,砂轮速度由80m/s提高到200m/s,砂轮寿命提高8.5倍。
在200m/s的速度磨削时,以2.5倍于80m/s时的磨除率,寿命仍然提高1倍。
1 超高速磨削的发展欧洲,高速磨削技术的发展起步早。
最初高速磨削基础研究是在60年代末期,实验室磨削速度已达210-230m/s。
70年代末期,高速磨削采用CBN砂轮。
意大利的法米尔(Famir)公司在1973年9月西德汉诺威国际机床展览会上,展出了砂轮圆周速度120m/s的RFT-C120/50R型磨轴承内套圈外沟的高速适用化磨床。
高速强力磨削在机械加工中的发展与应用

高速强力磨削在机械加工中的发展与应用
高速强力磨削(High-speed strong grinding)是指通过使用更高转速及更高切削速
率的研磨工具,以达到更高的加工效率和更好的加工质量。
其发展历程起源于20世纪60
年代,随着磨削技术、设备和工具的不断进步,也不断地推动着高速强力磨削的应用领域
不断扩大,如航空、汽车、模具、压力容器、光电子等行业。
高速强力磨削的优点主要表现在以下几个方面:
1.高效率:由于使用高转速、高切削速率的工具,磨削过程可以更加迅速、高效地完成。
2.高精度:磨削工具具备更好的刚度和振动抑制能力,可以在更高的速度下保证磨削
质量。
3.高表面质量:由于磨削工具的高速磨削作用,能够对工件表面进行更充分的去毛刺、去匀层、去表面膜等处理,从而使工件表面质量得到提高。
4.高加工质量稳定性:由于磨削工具具备较高的韧性和手感,可以更好的控制加工过程,从而提高加工质量的稳定性和一致性。
应用方面,高速强力磨削在航空、汽车、模具、压力容器等行业中得到了广泛应用。
在航空领域,高速强力磨削被用于高精度航空零部件的制造,如液压阀等。
在汽车行业中,高速强力磨削在发动机气门、气缸套等高精度部件的磨削加工中得到
了广泛应用。
模具领域中,高速强力磨削被广泛应用于大型压铸模和挤铸模等模具的制造。
总之,高速强力磨削在机械加工中的应用领域不断扩大,将会为我们的生产带来更高
效率、更好质量的加工服务。
高速磨削

高速磨削高速磨削是国内外正在大力研究并逐步推广的一种先进的机械加工方法 , 它是近代磨削加工技术发展的一种新工艺 , 与普通磨削相比 , 其优点是能够大大提高被加工工件的精度 , 降低零件表面粗糙度。
随着科学技术的不断进步和发展 , 对零件的加工精度和生产率提出了更高的要求 , 高速磨削技术更加显示出它的重要性。
1 国外高速磨削技术的现状与发展趋势早在上世纪 50年代 , 国外就已经开始研究高速磨削 , 到 60年代 , 许多国家在高速磨削方面的研究更加得到普遍重视 , 并取得了许多成功经验 , 如日本京都大学工学部冈村健二郎教授首先提出了高效磨削理论 , 当时在日本也是盛行一时。
德国阿亨大学Optiz教授系统地发表了 60m /s高速磨削的实验结果。
在 70年代 , 高速磨削在许多工业国家迅速发展 , 60m /s以上高速磨床品种超过 50种 , 少数磨床磨削速度达到 125m /s, 到了 80年代 , 许多国家继续在提高磨削速度上进行努力 , 但是高速磨削并未按原先预料的情况发展 , 它受到许多条件的制约 , 如受到机床结构、动态特性、砂轮速度及磨料耐磨性等的限制 , 实际上在这个时期磨削速度的提高也受到了一定的限制。
近年来 , 高速磨削加工技术又有了很大发展 , 主要表现在以下几个方面 :(1)高速磨削机理方面。
在越过能产生磨削热损伤的国限带之后 , 磨削用量进一步加大不仅不会使热损伤加剧 , 反而会使其不再发生。
这一发现 , 开拓出一个广阔的高速磨削参数领域 , 为实现超高速的磨削提供了理论基础 , 加上人造金刚石和立方氮化硼在砂轮制造中的大量应用 , 高速磨削得以再度兴起 , 并实现了线速度高于普通磨削 5 - 6倍甚至更高的超高速磨削。
(2)高速磨削的有利环节。
继喷雾润滑轴承和空气润滑轴承之后 , 利用磁力承受负荷的磁悬浮轴承已进入实用阶段 , 它的转速可以在主轴强度所能承受的限度内任意提高。
高速强力磨削在机械加工中的发展与应用
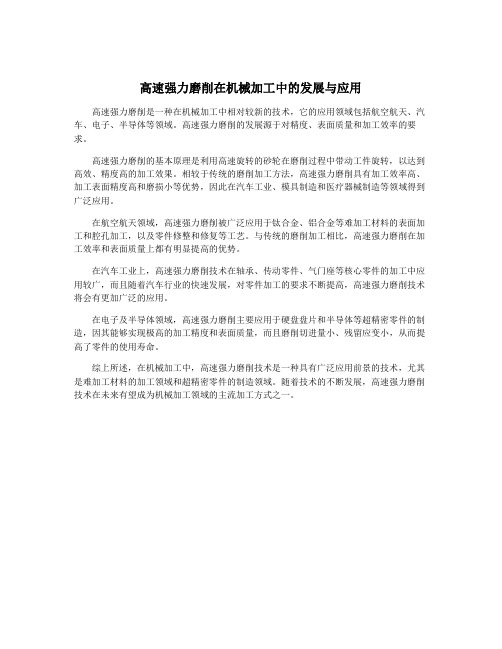
高速强力磨削在机械加工中的发展与应用
高速强力磨削是一种在机械加工中相对较新的技术,它的应用领域包括航空航天、汽车、电子、半导体等领域。
高速强力磨削的发展源于对精度、表面质量和加工效率的要求。
高速强力磨削的基本原理是利用高速旋转的砂轮在磨削过程中带动工件旋转,以达到高效、精度高的加工效果。
相较于传统的磨削加工方法,高速强力磨削具有加工效率高、加工表面精度高和磨损小等优势,因此在汽车工业、模具制造和医疗器械制造等领域得到广泛应用。
在航空航天领域,高速强力磨削被广泛应用于钛合金、铝合金等难加工材料的表面加工和腔孔加工,以及零件修整和修复等工艺。
与传统的磨削加工相比,高速强力磨削在加工效率和表面质量上都有明显提高的优势。
在汽车工业上,高速强力磨削技术在轴承、传动零件、气门座等核心零件的加工中应用较广,而且随着汽车行业的快速发展,对零件加工的要求不断提高,高速强力磨削技术将会有更加广泛的应用。
在电子及半导体领域,高速强力磨削主要应用于硬盘盘片和半导体等超精密零件的制造,因其能够实现极高的加工精度和表面质量,而且磨削切进量小、残留应变小,从而提高了零件的使用寿命。
综上所述,在机械加工中,高速强力磨削技术是一种具有广泛应用前景的技术,尤其是难加工材料的加工领域和超精密零件的制造领域。
随着技术的不断发展,高速强力磨削技术在未来有望成为机械加工领域的主流加工方式之一。
高速强力磨削在机械加工中的发展与应用

高速强力磨削在机械加工中的发展与应用高效率是国内外机械加工的主要发展方向之一。
提高效率的重要方法,是提高切削,磨削速度及增大进给量。
目前高速磨削已广泛应用于生产,普遍认为50-80m/s的高速磨削是经济可行的。
最高磨削速度已达到120m/s,试验室的速度已达到210-250m/s。
现在有的工件的实际磨削速度可以提高到300m/s。
目前正朝着高速度磨削、强力磨削,高速强力磨削力一向发展。
1高速磨削高速磨削是指砂轮线速度在45米/秒以上的磨削力一法。
高速磨削是提高磨削效率的重要途经之一。
1.1高速磨削的特点(1)它与普通磨削相比,可以提高生效率1-3倍;(2)由于磨削速度的提高,工件表面在磨粒犁耕后所形成的隆起高度减小,因而使磨削的表面粗糙度减小;(3)砂轮的寿命提高1倍左右;(4)磨髁ο陆?0%左右,加工的精度相应也提高。
1.2高速磨削必须采取的措施(1)使用高速砂轮;(2)使用高速磨床;(3)采用自动上料、自动检测装置以减小辅助时间。
1.3高速磨削的发展与应用近年来,国内外高速磨床品种已有外圆磨床、曲轴磨床、凸轮磨床,轴承磨床、平面磨床,内圆磨床等。
工业发达的国家在推广采用45-60m/s的高速磨削,80-150m/s的高速磨削已在一些国家开始应用。
我国已生产磨削速度为50-80m/s的外圆磨床、凹轮磨床和轴承磨床等。
目前国外高速磨削采用较多的是轴承行业磨削轴承环内外沟,在发动机行业高速磨削也得到广泛应用,如,美国AIM公司磨削V8发动机曲轴连杆颈用高速磨削,英国的Newall公司高速磨削锻钢4拐汽车曲轴。
不少国家磨削曲轴还采用多砂轮高速磨削(用三、四个,甚至七、八个砂轮同时磨),大大提高了磨削效率。
高速磨削对于多数牌号的钢材是适用的,但对磨削时易产生裂纹的材料,如钦合金,耐热合金则不适用。
对于某些材料,如,不锈钢,当砂轮线速度高于45m/s时,磨削效率反而下降。
由于高速磨削对机床、砂轮、冷却和安全技术力一面都有特殊要求,这将增加机床成本。
磨削技术的发展现状
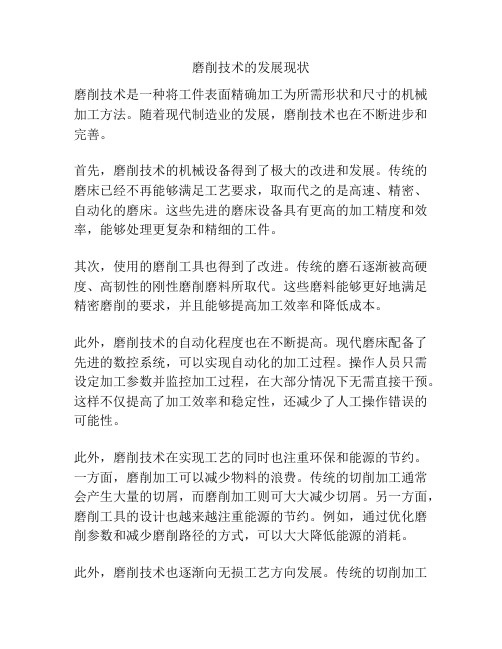
磨削技术的发展现状磨削技术是一种将工件表面精确加工为所需形状和尺寸的机械加工方法。
随着现代制造业的发展,磨削技术也在不断进步和完善。
首先,磨削技术的机械设备得到了极大的改进和发展。
传统的磨床已经不再能够满足工艺要求,取而代之的是高速、精密、自动化的磨床。
这些先进的磨床设备具有更高的加工精度和效率,能够处理更复杂和精细的工件。
其次,使用的磨削工具也得到了改进。
传统的磨石逐渐被高硬度、高韧性的刚性磨削磨料所取代。
这些磨料能够更好地满足精密磨削的要求,并且能够提高加工效率和降低成本。
此外,磨削技术的自动化程度也在不断提高。
现代磨床配备了先进的数控系统,可以实现自动化的加工过程。
操作人员只需设定加工参数并监控加工过程,在大部分情况下无需直接干预。
这样不仅提高了加工效率和稳定性,还减少了人工操作错误的可能性。
此外,磨削技术在实现工艺的同时也注重环保和能源的节约。
一方面,磨削加工可以减少物料的浪费。
传统的切削加工通常会产生大量的切屑,而磨削加工则可大大减少切屑。
另一方面,磨削工具的设计也越来越注重能源的节约。
例如,通过优化磨削参数和减少磨削路径的方式,可以大大降低能源的消耗。
此外,磨削技术也逐渐向无损工艺方向发展。
传统的切削加工往往会对工件表面产生变形和残余应力,而磨削加工则可以减少或避免这些问题。
因此,磨削技术在航空航天、汽车、船舶等高精度产品行业得到广泛应用。
总的来说,磨削技术在机械设备、磨削工具、自动化程度、环保性能和应用范围等方面都取得了显著的发展。
随着科技的不断进步和制造业的高速发展,磨削技术将继续迎来新的突破,以满足不断增长的工艺需求。
我国高速加工技术现状及发展趋势
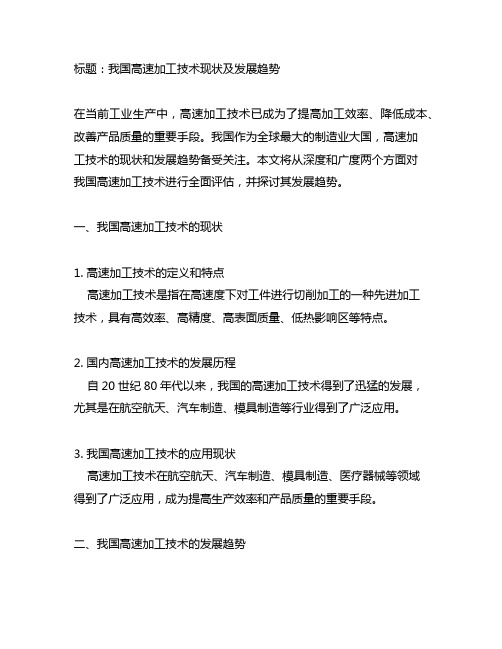
标题:我国高速加工技术现状及发展趋势在当前工业生产中,高速加工技术已成为了提高加工效率、降低成本、改善产品质量的重要手段。
我国作为全球最大的制造业大国,高速加工技术的现状和发展趋势备受关注。
本文将从深度和广度两个方面对我国高速加工技术进行全面评估,并探讨其发展趋势。
一、我国高速加工技术的现状1. 高速加工技术的定义和特点高速加工技术是指在高速度下对工件进行切削加工的一种先进加工技术,具有高效率、高精度、高表面质量、低热影响区等特点。
2. 国内高速加工技术的发展历程自20世纪80年代以来,我国的高速加工技术得到了迅猛的发展,尤其是在航空航天、汽车制造、模具制造等行业得到了广泛应用。
3. 我国高速加工技术的应用现状高速加工技术在航空航天、汽车制造、模具制造、医疗器械等领域得到了广泛应用,成为提高生产效率和产品质量的重要手段。
二、我国高速加工技术的发展趋势1. 技术创新推动高速加工技术的发展随着科技的进步和不断创新,高速加工技术将会更加高效、精密、稳定,能够满足更加复杂的加工需求。
2. 智能制造与高速加工技术的融合智能制造将成为未来高速加工技术发展的重要方向,通过智能化、自动化技术,提高生产效率和产品质量。
3. 绿色制造与高速加工技术的结合高速加工技术在减少碳排放、节能减排方面将会有更大的发展空间,应用于绿色制造领域。
4. 人工智能在高速加工技术中的应用随着人工智能技术的快速发展,其在高速加工技术中的应用将会成为新的发展趋势,将提高生产效率和产品质量。
三、总结与展望我国高速加工技术在不断发展创新的过程中,已经取得了令人瞩目的成绩,但与发达国家相比仍有一定差距。
在未来发展中,需要加大科技投入力度,加强技术研发和创新,培养更多高端技术人才,不断提升我国的高速加工技术水平,推动制造业向高质量发展。
个人观点:高速加工技术作为先进制造技术的代表,将会对我国工业生产产生深远影响。
在未来,我相信随着科技的进步和不断创新,我国的高速加工技术将不断迈向更加高效、精密、稳定的发展方向,并为我国制造业的转型升级和智能制造提供重要支撑。
超高速磨削技术最新进展综述
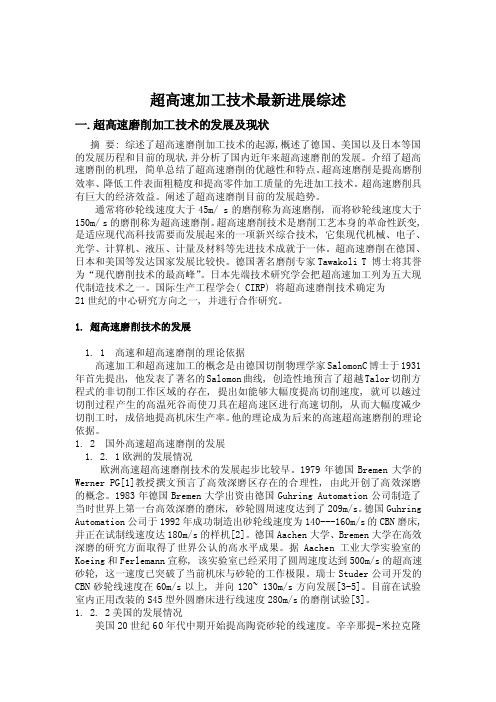
超高速加工技术最新进展综述一.超高速磨削加工技术的发展及现状摘要: 综述了超高速磨削加工技术的起源,概述了德国、美国以及日本等国的发展历程和目前的现状,并分析了国内近年来超高速磨削的发展。
介绍了超高速磨削的机理, 简单总结了超高速磨削的优越性和特点。
超高速磨削是提高磨削效率、降低工件表面粗糙度和提高零件加工质量的先进加工技术。
超高速磨削具有巨大的经济效益。
阐述了超高速磨削目前的发展趋势。
通常将砂轮线速度大于45m/ s的磨削称为高速磨削, 而将砂轮线速度大于150m/ s的磨削称为超高速磨削。
超高速磨削技术是磨削工艺本身的革命性跃变, 是适应现代高科技需要而发展起来的一项新兴综合技术, 它集现代机械、电子、光学、计算机、液压、计量及材料等先进技术成就于一体。
超高速磨削在德国、日本和美国等发达国家发展比较快。
德国著名磨削专家Tawakoli T 博士将其誉为“现代磨削技术的最高峰”。
日本先端技术研究学会把超高速加工列为五大现代制造技术之一。
国际生产工程学会( CIRP) 将超高速磨削技术确定为21世纪的中心研究方向之一, 并进行合作研究。
1. 超高速磨削技术的发展1. 1 高速和超高速磨削的理论依据高速加工和超高速加工的概念是由德国切削物理学家SalomonC博士于1931年首先提出, 他发表了著名的Salomon曲线, 创造性地预言了超越Talor切削方程式的非切削工作区域的存在, 提出如能够大幅度提高切削速度, 就可以越过切削过程产生的高温死谷而使刀具在超高速区进行高速切削, 从而大幅度减少切削工时, 成倍地提高机床生产率。
他的理论成为后来的高速超高速磨削的理论依据。
1. 2 国外高速超高速磨削的发展1. 2. 1欧洲的发展情况欧洲高速超高速磨削技术的发展起步比较早。
1979年德国Bremen大学的Werner PG[1]教授撰文预言了高效深磨区存在的合理性, 由此开创了高效深磨的概念。
1983年德国Bremen大学出资由德国Guhring Automation公司制造了当时世界上第一台高效深磨的磨床, 砂轮圆周速度达到了209m/s。
高速磨削工艺特点及其发展现状(root)

机电动平衡系统
(2)高速磨削砂轮 )
砂轮基体(满足通用化,降低连接处应力, ①砂轮基体(满足通用化,降低连接处应力,满足磨削时的强度和刚度 要求) 要求) 锋利(也就是说,磨粒突出高度要大 以便能容纳大量的长切屑, 突出高度要大, ②锋利(也就是说,磨粒突出高度要大,以便能容纳大量的长切屑,一 般采用电镀结合砂轮) 般采用电镀结合砂轮) 结合剂必须具有很高的耐磨性 以减少砂轮的磨损。(电镀结合砂轮, 必须具有很高的耐磨性, 。(电镀结合砂轮 ③结合剂必须具有很高的耐磨性,以减少砂轮的磨损。(电镀结合砂轮, 多孔陶瓷结合剂砂轮) 多孔陶瓷结合剂砂轮)
பைடு நூலகம்
(2)高速精密磨削 )
高速精密磨削在日本应用最为广泛。 高速精密磨削在日本应用最为广泛。因为日本的高速磨削主要 不是以获得高生产率为目的,而是对磨削过程的综合性能( 不是以获得高生产率为目的,而是对磨削过程的综合性能(如加工精 度和表面质量)更感兴趣,它的磨削效率普遍地维持60mm3/mm.s 度和表面质量)更感兴趣,它的磨削效率普遍地维持 以下,这是与欧洲高速磨削高效深磨工艺的显著差别。 以下,这是与欧洲高速磨削高效深磨工艺的显著差别。
二、高速磨削的加工特点
(1)生产效率高。由于单位时间内作用的磨粒数增加,使材料磨除率 成倍增加,比普通磨削可提高30%-100% ; (2)砂轮使用寿命长。由于每颗磨粒的负荷减小,磨粒磨削时间相应 延长,提高了砂轮使用寿命。磨削力一定时,200m/s磨削砂轮的寿 命是80m/s 磨削的两倍;磨削效率一定时,200m/s 磨削砂轮的寿命 则是80m/s磨削的7. 8倍。这非常有利于实现磨削自动化; (3)磨削表面粗糙度值低。超高速磨削单个磨粒的切削厚度变小,磨 削划痕浅,表面塑性隆起高度减小,表面粗糙度数值降低;同时由于 超高速磨削材料的极高应变率,磨屑在绝热剪切状态下形成,材料去 除机制发生转变,因此可实现对脆性和难加工材料的高性能加工; (4)磨削力和工件受力变形小,工件加工精度高。由于切削厚度小, 法向磨削力Fn相应减小,从而有利于刚度较差工件加工精度的提高。 在切深相同时,磨削速度250 m/ s 磨削时的磨削力比磨削速度 180m/s 时磨削力降低近一倍;
高速切削加工技术的现状和发展
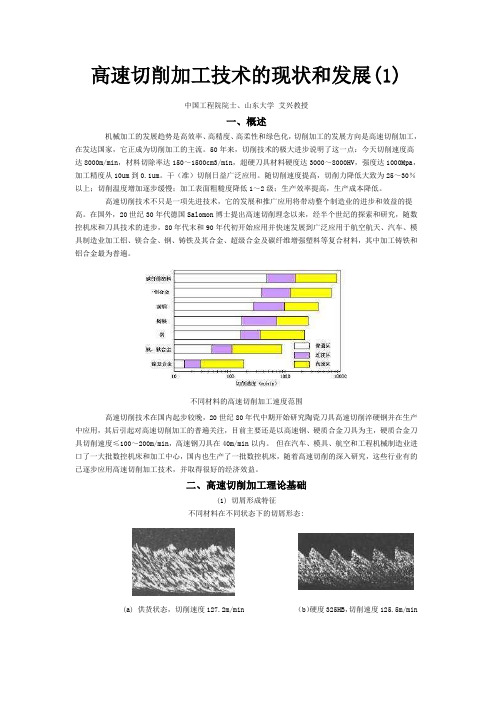
高速切削加工技术的现状和发展(1)中国工程院院士、山东大学艾兴教授一、概述机械加工的发展趋势是高效率、高精度、高柔性和绿色化,切削加工的发展方向是高速切削加工,在发达国家,它正成为切削加工的主流。
50年来,切削技术的极大进步说明了这一点:今天切削速度高达8000m/min,材料切除率达150~1500cm3/min,超硬刀具材料硬度达3000~8000HV,强度达1000Mpa,加工精度从10um到0.1um。
干(准)切削日益广泛应用。
随切削速度提高,切削力降低大致为25~30%以上;切削温度增加逐步缓慢;加工表面粗糙度降低1~2级;生产效率提高,生产成本降低。
高速切削技术不只是一项先进技术,它的发展和推广应用将带动整个制造业的进步和效益的提高。
在国外,20世纪30年代德国Salomon博士提出高速切削理念以来,经半个世纪的探索和研究,随数控机床和刀具技术的进步,80年代末和90年代初开始应用并快速发展到广泛应用于航空航天、汽车、模具制造业加工铝、镁合金、钢、铸铁及其合金、超级合金及碳纤维增强塑料等复合材料,其中加工铸铁和铝合金最为普遍。
不同材料的高速切削加工速度范围高速切削技术在国内起步较晚,20世纪80年代中期开始研究陶瓷刀具高速切削淬硬钢并在生产中应用,其后引起对高速切削加工的普遍关注,目前主要还是以高速钢、硬质合金刀具为主,硬质合金刀具切削速度≤100~200m/min,高速钢刀具在40m/min以内。
但在汽车、模具、航空和工程机械制造业进口了一大批数控机床和加工中心,国内也生产了一批数控机床,随着高速切削的深入研究,这些行业有的已逐步应用高速切削加工技术,并取得很好的经济效益。
二、高速切削加工理论基础(1) 切屑形成特征不同材料在不同状态下的切屑形态:(a) 供货状态,切削速度127.2m/min (b)硬度325HB,切削速度125.5m/min连续带状切屑(D.LEE)锯齿状切屑(c)硬度325HB,切削速度250m/min锯齿状切屑(d)硬度325HB,切削速度2600m/min即将分离的锯齿状切屑高速切削不同状态AISI4340钢(40CrNiMoA)时的切屑形态(纵截面微观照片)((b)、(c)、(d)从komarduri)切削渗碳淬硬20CrMnTi钢(HRC60~62)在100~110m/min时的切屑形貌工件材料及其性能和切削条件对切屑形态起主要作用,其中工件材料及其性能有决定性的影响。
超高速磨削技术在机械制造领域中的运用
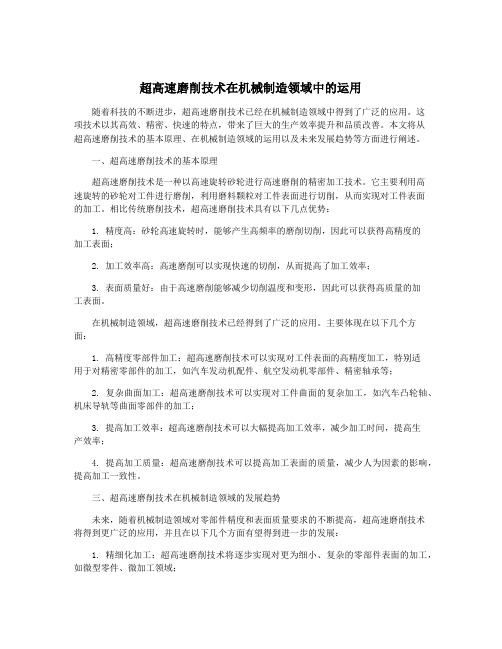
超高速磨削技术在机械制造领域中的运用随着科技的不断进步,超高速磨削技术已经在机械制造领域中得到了广泛的应用。
这项技术以其高效、精密、快速的特点,带来了巨大的生产效率提升和品质改善。
本文将从超高速磨削技术的基本原理、在机械制造领域的运用以及未来发展趋势等方面进行阐述。
一、超高速磨削技术的基本原理超高速磨削技术是一种以高速旋转砂轮进行高速磨削的精密加工技术。
它主要利用高速旋转的砂轮对工件进行磨削,利用磨料颗粒对工件表面进行切削,从而实现对工件表面的加工。
相比传统磨削技术,超高速磨削技术具有以下几点优势:1. 精度高:砂轮高速旋转时,能够产生高频率的磨削切削,因此可以获得高精度的加工表面;2. 加工效率高:高速磨削可以实现快速的切削,从而提高了加工效率;3. 表面质量好:由于高速磨削能够减少切削温度和变形,因此可以获得高质量的加工表面。
在机械制造领域,超高速磨削技术已经得到了广泛的应用。
主要体现在以下几个方面:1. 高精度零部件加工:超高速磨削技术可以实现对工件表面的高精度加工,特别适用于对精密零部件的加工,如汽车发动机配件、航空发动机零部件、精密轴承等;2. 复杂曲面加工:超高速磨削技术可以实现对工件曲面的复杂加工,如汽车凸轮轴、机床导轨等曲面零部件的加工;3. 提高加工效率:超高速磨削技术可以大幅提高加工效率,减少加工时间,提高生产效率;4. 提高加工质量:超高速磨削技术可以提高加工表面的质量,减少人为因素的影响,提高加工一致性。
三、超高速磨削技术在机械制造领域的发展趋势未来,随着机械制造领域对零部件精度和表面质量要求的不断提高,超高速磨削技术将得到更广泛的应用,并且在以下几个方面有望得到进一步的发展:1. 精细化加工:超高速磨削技术将逐步实现对更为细小、复杂的零部件表面的加工,如微型零件、微加工领域;2. 自动化生产:超高速磨削技术将逐步实现自动化生产,通过自动控制系统实现加工过程的自动监控和调整,提高生产效率;3. 高速高效加工:超高速磨削技术将进一步提高旋转速度和切削频率,实现更高速、更高效的加工;4. 精密模具加工:超高速磨削技术将在模具加工领域得到更广泛的应用,如塑料模具、压铸模具等精密模具的加工。
2014 - 13 - 高速超高速磨削

D 超高速磨削相关技术--超高速磨削液选择
油基磨削液(矿物油)的润滑作用比水基磨削液优越。 (1)可以防止CBN磨粒切刃的磨耗,抑制CBN磨粒的水解反应,提 高砂轮耐用度。 (2)降低磨削功率,提高工件的表面完整性。 油基磨削液中加入硫系及氯系挤压添加剂可以获得更为优越的效果。
高速回转的砂轮表面存在各种回转气流,速度越高,空气层越厚。 空气层的存在使磨削液难以进入磨削区。 一般采用高压(几个甚至几 十个MPa)冷却液体。 超高速磨削中,以实现无磨削液为目标。日本开发出采用低温压缩 空气冷却法,环保、清洁、安全舒适。
D 超高速磨削机理
(3)表面粗糙度
普通磨削中,砂轮磨损的主要原因是磨粒磨耗磨损和磨粒的破损
与脱落。
高速磨削中,未变形磨削层厚度较小,磨粒不易破损和脱落,砂
轮耐用度增加,磨削力下降。 一定金属切除率条件下,砂轮速度增加,砂轮径向磨损量降低, 表面粗糙度得到改善。 线速度增加,切屑变薄,工件表面的磨痕深度变浅,表面残留凸 峰变小,表面粗糙度得到改善。
C
超高速磨削加工的应用
P 17
C 超高速磨削技术的应用
超高速磨削技术最先在德国发展,其中德国 Guehring Automation 公司较为著名。
80年代最先推出超高速磨床,与阿亨大学开展500m/s磨削研究制造
了设备。 FD613超高速平面磨床上磨削宽1-3mm,深30mm的转子槽 时,进给速度可达到3000mm/min(CBN砂轮,150m/s)。 轴齿轮齿槽、扳手开口槽、蜗杆螺旋齿槽等的一次性高效磨削加工 是Guehring公司超高速磨床的主要工艺。 欧洲还有许多公司推出了自己超高速磨床,反映出欧洲超高速磨削 技术实用化的地位。
高速磨削技术的现状及发展前景

高速磨削技术的现状及发展前景The Situ ation and Developing Vistas ofHigh-Speed G rinding T echnology荣烈润 摘 要:本文综述了高速磨削的概念、优势、关键技术、应用近况和发展前景。
关键词:高速磨削 动平衡 砂轮修整 精密高速磨削 高效深磨Abstract:This paper introduced concept,advantages,key technical points,application and developing vistas of high2speed grinding technology.K ey w ords:high2speed grinding dynamic balancing grinding wheel trim precision high2speed grind2 ing high2efficiency deep grinding0 引言人们一直对于提高磨削的砂轮速度所带来的技术优势和经济效益给予了充分的注意和重视。
但是在高速磨削过程中,工件受热变形和表面烧伤等均限制了砂轮速度的进一步提高,砂轮强度和机床制造等关键技术也使得高速磨削技术在一段时间内进展缓慢。
当20世纪90年代以德国高速磨床FS-126为主导的高速磨削(High-speed Grinding)技术取得了突破性进展后,人们意识到一个全新的磨削时代已经到来。
高速磨削技术是磨削工艺本身的革命性跃变,是适应现代高科技需要而发展起来的一项新兴综合技术,它集现代机械、电子、光学、计算机、液压、计量及材料等先进技术成就于一体。
随着砂轮速度的提高,目前磨削去除率已猛增到了3000mm3/ mm・s甚至更多,可与车、铣、刨等切削加工相媲美,尤其近年来各种新兴硬脆材料(如陶瓷、光学玻璃、光学晶体、单晶硅等)的广泛应用更推动了高速磨削技术的迅猛发展。
高速切削加工的发展及需求

高速切削加工的发展及需求高速切削加工是当代先进制造技术的重要组成部分,拥有高效率、高精度及高表面质量等特征。
本文介绍此技术的定义、发展现状、适用领域以及中国的需求情况。
高速切削加工的定义高速切削加工是面向21世纪的一项高新技术,它以高效率、高精度和高表面质量为基本特征,在汽车工业、航空航天、模具制造和仪器仪表等行业中获得了愈来愈广泛的应用,并已取得了重大的技术经济效益,是当代先进制造技术的重要组成部分。
高速切削是实现高效率制造的核心技术,工序的集约化和设备的通用化使之具有很高的生产效率。
可以说,高速切削加工是一种不增加设备数量而大幅度提高加工效率所必不可少的技术。
高速切削加工的优点主要在于:提高生产效率、提高加工精度及降低切削阻力。
有关高速切削加工的含义,目前尚无统一的认识,通常有如下几种观点:切削速度很高,通常认为其速度超过普通切削的5-10倍;机床主轴转速很高,一般将主轴转速在10000-20000r/min 以上定为高速切削;进给速度很高,通常达15-50m/min,最高可达90m/min;对于不同的切削材料和所釆用的刀具材料,高速切削的含义也不尽相同;切削过程中,刀刃的通过频率(Tooth Passing Frequency)接近于“机床-刀具-工件”系统的主导自然频率(Dominant Natural Frequency)时,可认为是高速切削。
可见高速切削加工是一个综合的概念。
1992年,德国Darmstadt工业大学的H. Schulz教授在CIRP上提出了高速切削加工的概念及其涵盖的范围。
认为对于不同的切削对象,过渡区(Transition)即为通常所谓的高速切削範围,这也是当时金属切削工艺相关的技术人员所期待或者可望实现的切削速度。
高速切削加工技术现状高速切削加工对机床、刀具和切削工艺等方面都有一些具体的要求。
下面分别从这几个方面阐述高速切削加工技术的发展现状和趋势。
机床设备现阶段,为了实现高速切削加工,一般釆用高柔性的高速数控机床、加工中心,也有釆用专用的高速铣、钻床。
磨削技术的发展现状及未来趋势分析

磨削技术的发展现状及未来趋势分析磨削技术是一种高精度、高效率的加工方法,广泛应用于机械制造、航空航天、汽车制造、电子设备等领域。
磨削技术的发展对制造业的提升和产品质量的改善起着重要作用。
本文将对磨削技术的发展现状及未来趋势进行分析。
近年来,磨削技术在国内外得到了快速发展。
一方面,随着高品质工件的需求不断增长,磨削技术逐渐成为高精度加工的主要方法之一。
在传统磨削技术的基础上,出现了多种新型磨削技术,如超声磨削、电化学磨削、电解腐蚀磨削等。
这些新技术不仅提高了工件的表面质量,还降低了加工成本和能耗。
另一方面,随着材料科学和机械制造技术的不断进步,磨削技术也在不断提高。
磨削刀具材料的研发使得切削效率得到了显著提升,磨粒性能的改善使得磨削加工得到了更好的控制,磨削液的优化使得磨削过程更加稳定和可靠。
这些技术进展让磨削技术在加工精度、表面质量和加工效率方面取得了巨大的进步。
未来,随着工业4.0和智能制造的快速发展,磨削技术将继续向着高精度、高效率和智能化方向发展。
首先,利用传感器和数据分析技术,实现磨削过程的监控和优化。
通过收集磨削过程中的各种数据,如刀具磨损情况、温度、振动等,可以实现对加工过程的实时监测和调整,提高加工效率和产品质量。
其次,磨削过程中的自动化和机器人技术将进一步推动磨削技术的发展。
自动化的磨削生产线可以实现对复杂形状工件的连续磨削加工,提高生产效率和稳定性。
机器人磨削系统可以实现对工件的全自动加工,减少人工干预,提高加工精度和一致性。
另外,磨削技术与其他加工技术的融合也将是未来的发展方向。
例如,磨削加工和3D打印技术结合,可以实现对复杂形状工件的加工;磨削加工和激光技术结合,可以实现对高硬度材料的加工。
这些新的磨削技术将进一步推动制造业的升级和创新。
此外,环保和节能也是磨削技术未来发展的重要方向。
随着能源和环境问题的日益突出,磨削工艺中的磨削液和废气处理将成为关注的焦点。
研发环保型磨削液和减少磨削过程中废气排放的技术不仅可以保护环境,还可以提高生产效率和降低成本。
高速切削技术在金属加工中的应用与未来发展趋势
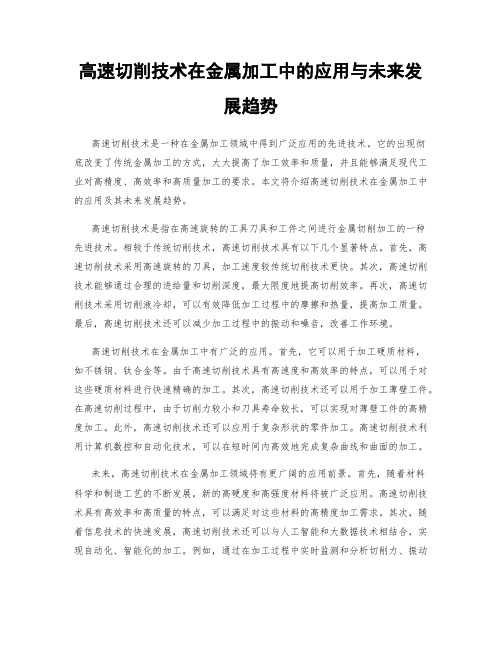
高速切削技术在金属加工中的应用与未来发展趋势高速切削技术是一种在金属加工领域中得到广泛应用的先进技术。
它的出现彻底改变了传统金属加工的方式,大大提高了加工效率和质量,并且能够满足现代工业对高精度、高效率和高质量加工的要求。
本文将介绍高速切削技术在金属加工中的应用及其未来发展趋势。
高速切削技术是指在高速旋转的工具刀具和工件之间进行金属切削加工的一种先进技术。
相较于传统切削技术,高速切削技术具有以下几个显著特点。
首先,高速切削技术采用高速旋转的刀具,加工速度较传统切削技术更快。
其次,高速切削技术能够通过合理的进给量和切削深度,最大限度地提高切削效率。
再次,高速切削技术采用切削液冷却,可以有效降低加工过程中的摩擦和热量,提高加工质量。
最后,高速切削技术还可以减少加工过程中的振动和噪音,改善工作环境。
高速切削技术在金属加工中有广泛的应用。
首先,它可以用于加工硬质材料,如不锈钢、钛合金等。
由于高速切削技术具有高速度和高效率的特点,可以用于对这些硬质材料进行快速精确的加工。
其次,高速切削技术还可以用于加工薄壁工件。
在高速切削过程中,由于切削力较小和刀具寿命较长,可以实现对薄壁工件的高精度加工。
此外,高速切削技术还可以应用于复杂形状的零件加工。
高速切削技术利用计算机数控和自动化技术,可以在短时间内高效地完成复杂曲线和曲面的加工。
未来,高速切削技术在金属加工领域将有更广阔的应用前景。
首先,随着材料科学和制造工艺的不断发展,新的高硬度和高强度材料将被广泛应用。
高速切削技术具有高效率和高质量的特点,可以满足对这些材料的高精度加工需求。
其次,随着信息技术的快速发展,高速切削技术还可以与人工智能和大数据技术相结合,实现自动化、智能化的加工。
例如,通过在加工过程中实时监测和分析切削力、振动等参数,可以实现工艺优化和故障预测,提高加工效率和质量。
此外,高速切削技术还可以与增材制造技术相结合,实现复合加工,进一步拓展应用领域。
高速强力磨削在机械加工中的发展与应用
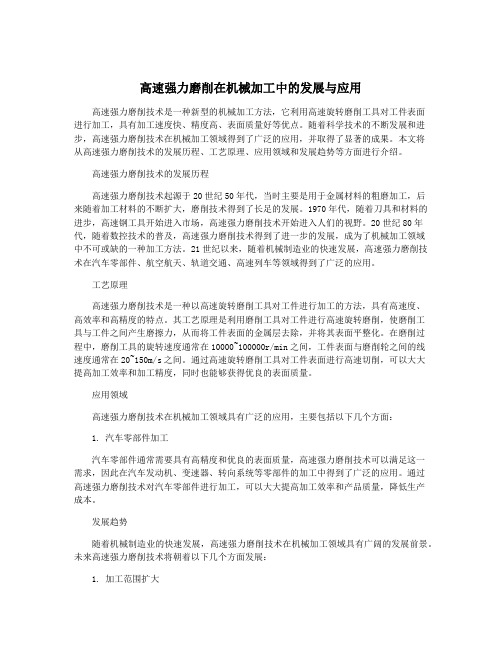
高速强力磨削在机械加工中的发展与应用高速强力磨削技术是一种新型的机械加工方法,它利用高速旋转磨削工具对工件表面进行加工,具有加工速度快、精度高、表面质量好等优点。
随着科学技术的不断发展和进步,高速强力磨削技术在机械加工领域得到了广泛的应用,并取得了显著的成果。
本文将从高速强力磨削技术的发展历程、工艺原理、应用领域和发展趋势等方面进行介绍。
高速强力磨削技术的发展历程高速强力磨削技术起源于20世纪50年代,当时主要是用于金属材料的粗磨加工,后来随着加工材料的不断扩大,磨削技术得到了长足的发展。
1970年代,随着刀具和材料的进步,高速钢工具开始进入市场,高速强力磨削技术开始进入人们的视野。
20世纪80年代,随着数控技术的普及,高速强力磨削技术得到了进一步的发展,成为了机械加工领域中不可或缺的一种加工方法。
21世纪以来,随着机械制造业的快速发展,高速强力磨削技术在汽车零部件、航空航天、轨道交通、高速列车等领域得到了广泛的应用。
工艺原理高速强力磨削技术是一种以高速旋转磨削工具对工件进行加工的方法,具有高速度、高效率和高精度的特点。
其工艺原理是利用磨削工具对工件进行高速旋转磨削,使磨削工具与工件之间产生磨擦力,从而将工件表面的金属层去除,并将其表面平整化。
在磨削过程中,磨削工具的旋转速度通常在10000~100000r/min之间,工件表面与磨削轮之间的线速度通常在20~150m/s之间。
通过高速旋转磨削工具对工件表面进行高速切削,可以大大提高加工效率和加工精度,同时也能够获得优良的表面质量。
应用领域高速强力磨削技术在机械加工领域具有广泛的应用,主要包括以下几个方面:1. 汽车零部件加工汽车零部件通常需要具有高精度和优良的表面质量,高速强力磨削技术可以满足这一需求,因此在汽车发动机、变速器、转向系统等零部件的加工中得到了广泛的应用。
通过高速强力磨削技术对汽车零部件进行加工,可以大大提高加工效率和产品质量,降低生产成本。
- 1、下载文档前请自行甄别文档内容的完整性,平台不提供额外的编辑、内容补充、找答案等附加服务。
- 2、"仅部分预览"的文档,不可在线预览部分如存在完整性等问题,可反馈申请退款(可完整预览的文档不适用该条件!)。
- 3、如文档侵犯您的权益,请联系客服反馈,我们会尽快为您处理(人工客服工作时间:9:00-18:30)。
(5)磨削温度低。超高速磨削中磨削热传入工件的比率减小,使工件表面 磨削温度降低,能越过容易发生热损伤的区域,受力受热变质层减薄, 具有更好的表面完整性。使用CBN 砂轮200 m/ s 超高速磨削钢件的 表面残余应力层深度不足10微米。从而极大地扩展了磨削工艺参数地 应用范围.
(6)充分利用和发挥了超硬磨料的高硬度和高耐磨性的优异性能。电镀和 钎焊单层超硬磨料砂轮是超高速磨削首选的磨具,特别是高温钎焊金 属结合剂砂轮,磨削力及温度更低,是目前超高速磨削新型砂轮.
(4)磨削状态检测及数控技术
高速超高速磨削加工中,由于砂轮线速度极高,砂轮由于 超高速引起的破碎现象时常发生,砂轮破碎及磨损状态的 监测是关系到磨削工作能否顺利进行和保证加工质量和零 件表面完整性的关键;在超高速加工中,砂轮与工件的对 刀精度,砂轮与修整轮的对刀精度将直接影响到工件的尺 寸精度和砂轮的修整质量。
(7)具有巨大的经济效益和社会效益,并具有广阔的绿色特性。 高速超高 速磨削加工能有效地缩短加工时间,提高劳动生产率,减少能源的消 耗和噪声的污染。因超高速磨削热的70%被磨屑所带走,所以加工表 面的温度相对低,所需磨削液的流量和压力可相对减少,使冷却液的 需求量减少,能量需求减少,污染减少。
三、技术支持
一、磨削机理
①在高速超高速磨削加工过程中,在保持其它参数不变的条件下,随着 砂轮速度的大幅度提高,单位时间内磨削区的磨粒数增加,每个磨粒 切下的磨屑厚度变小,导致每个磨粒承受的磨削力大大变小,总磨削 力也大大降低。
②超高速磨削时,由于磨削速度很高,单个磨屑的形成时间极短。在极 短的时间内完成的磨屑的高应变率(可近似认为等于磨削速度) 形成 过程与普通磨削有很大的差别,表现为工件表面的弹性变形层变浅, 磨削沟痕两侧因塑性流动而形成的隆起高度变小,磨屑形成过程中的 耕犁和滑擦距离变小,工件表面层硬化及残余应力倾向减小。
Ⅰ相关概念
磨削定义:
通常所说的“磨削”主要是指用砂轮或砂带进行去除材料加 工的工艺方法,它是应用广泛的高效精密的终加工工艺方 法。
所属范畴:
先进制造技术 →先进加工技术→去除加工→力学加工
分类:
普通磨削 高速磨削 超高速磨削
V<45m/s 45m/s<V<150m/s V>150m/s
Ⅱ工艺特点
机电动平衡系统
(2)高速磨削砂轮
①砂轮基体(满足通用化,降低连接处应力,满足磨削时的强度和刚度 要求)
②锋利(也就是说,磨粒突出高度要大,以便能容纳大量的长切屑,一 般采用电镀结合砂轮)
③结合剂必须具有很高的耐磨性,以减少砂轮的磨损。(电镀结合砂轮, 多孔陶瓷结合剂砂轮)
高速磨削砂轮
(3)冷却润滑系统
③此外,超高速磨削时磨粒在磨削区上的移动速度和工件的进给速度均 大大加快,加上应变率响应的温度滞后的影响,会使工件表面磨削温 度有所降低,因而能越过容易发生磨削烧伤的区域,而极大扩展了磨 削工艺参数的应用范围。
二、高速磨削的加工特点
(1)生产效率高。由于单位时间内作用的磨粒数增加,使材料磨除率 成倍增加,比普通磨削可提高30%-100% ; (2)砂轮使用寿命长。由于每颗磨粒的负荷减小,磨粒磨削时间相应 延长,提高了砂轮使用寿命。磨削力一定时,200m/s磨削砂轮的寿 命是80m/s 磨削的两倍;磨削效率一定时,200m/s 磨削砂轮的寿命 则是80m/s磨削的7. 8倍。这非常有利于实现磨削自动化; (3)磨削表面粗糙度值低。超高速磨削单个磨粒的切削厚度变小,磨 削划痕浅,表面塑性隆起高度减小,表面粗糙度数值降低;同时由于 超高速磨削材料的极高应变率,磨屑在绝热剪切状态下形成,材料去 除机制发生转变,因此可实现对脆性和难加工材料的高性能加工; (4)磨削力和工件受力变形小,工件加工精度高。由于切削厚度小, 法向磨削力Fn相应减小,从而有利于刚度较差工件加工精度的提高。 在切深相同时,磨削速度250 m/ s 磨削时的磨削力比磨削速度 180m/s 时磨削力降低近一倍;
由于高速磨削砂轮转速极高,对机床功率及性能、砂轮强 度、振动、平衡、气流扰动、安全防护和冷却液注入等工 艺措施提出了特殊要求。因此,与其相关的关键技术有:
(1)高速主轴 ①高速主轴须有连续自动动平衡系统 属于自动控制技术,利用反馈调节模式,采用测量元件和控制元件进 行动平衡 ②保证主轴在高速状态下有足够的转矩用于切削 无功功率与转速和砂轮直径有关,在高速磨削状态下可通过选用直径 小的砂轮
冷却润滑系统由冷却润滑液、泵、过滤器等组成,对高精度磨 削还需有温度控制系统以确保冷却润滑液的温度恒定。
冷却润滑液必须完成润滑、冷却、清洗砂轮和传送切屑四大任 务。故它必须满足以下的技术要求:
①较高的热容量和导热率,以提高冷却率 ②能承受较高的压力 ③良好的过滤性能,防腐蚀性和附着力 ④较高的稳定性,不起泡,不变色 ⑤对健康无害,易于清洗 ⑥有利于环境保护,易于处理。
Ⅲ高速磨削的发展现状
一、目前高速磨削的应用主要有三个方面:
(1)高速高效深磨(起源于德国)
以砂轮高速(>150m/s)、高进给速度(0.5~10m/min)和大 切深(0.1~30mm)为主要特征的高效深磨技术是高速磨削在高效 加工方面的最新应用。
(2)高速精密磨削
高速精密磨削在日本应用最为广泛。因为日本的高速磨削主要 不是以获得高生产率为目的,而是对磨削过程的综合性能(如加工精 度和表面质量)更感兴趣,它的磨削效率普遍地维持60mm3/mm.s 以下,这是与欧洲高速磨削高效深磨工艺的显著差别。
(3)难磨材料的高速磨削
利用高速磨削实现对硬脆材料(工程陶瓷及光学透镜等)的高 性能加工是高速磨领域的一个重要组成部分。
二、高速磨削继续发展所要做的技术突破
欲将磨削速度进一步提高,目前仍受许多因素的限制,要 想充分发挥高速磨削的优势,必须从制约切削速度的各个 方面进行研究。 (1)发展高功率高速主轴 关键在于开发大功率高速主轴。 (2) 研制适应高速磨削的新颖砂轮 (3) 磨床结构的改进 尽可能降低机床在高速时由于砂轮不平衡引起的振动,应 配置在线自动动平衡系统,以使机床在不同转速时,始终 处于最佳的运行状态。为了提高生产效率和工件的加工精 度,则应采用高速、高效和高精度进给驱动系统。比如在 平面磨床上采用直线电机替代丝杠螺母传动;在进行偏心 磨削时,外圆磨床除了须具备高速滑台系统外,还要配备 高速数控系统,以保证工件的精度及较高的生产率。