现代制造技术实习报告
数控技术普车实习报告

一、前言随着我国制造业的快速发展,数控技术作为现代制造业的核心技术,其应用越来越广泛。
为了使我对数控技术有更深入的了解,提高我的实践操作能力,我在20xx年3月至20xx年5月期间,在xxx机床厂进行了数控技术普车实习。
以下是我在实习期间的学习体会和收获。
二、实习目的1. 了解数控技术的基本原理和操作方法;2. 掌握数控车床的编程和加工工艺;3. 提高自己的实际操作能力和综合素质。
三、实习内容1. 学习数控车床的基本操作在实习初期,我主要学习了数控车床的基本操作,包括机床的启动、停止、换刀、夹紧等。
通过实践操作,我熟悉了机床的结构和功能,掌握了机床的基本操作步骤。
2. 学习数控编程数控编程是数控车床操作的核心,我学习了G代码、M代码、F代码等编程指令,掌握了数控编程的基本方法。
在师傅的指导下,我尝试编写了简单的数控程序,并成功运行。
3. 学习加工工艺在实习过程中,我学习了各种零件的加工工艺,包括外圆、内孔、螺纹、端面等。
我了解了加工参数的选取、刀具路径的规划等,提高了自己的加工工艺水平。
4. 参与实际生产在实习后期,我参与了实际生产,负责加工一些简单的零件。
通过实际操作,我巩固了所学知识,提高了自己的实际操作能力。
四、实习收获1. 理论知识与实践相结合:通过实习,我将所学的理论知识与实际操作相结合,提高了自己的动手能力。
2. 提高编程能力:实习过程中,我学会了编写数控程序,提高了自己的编程能力。
3. 培养团队协作精神:在实习过程中,我与同事共同完成任务,培养了团队协作精神。
4. 增强职业素养:实习期间,我严格遵守纪律,认真完成工作任务,提高了自己的职业素养。
五、总结数控技术普车实习让我受益匪浅,不仅提高了我的实践操作能力,还培养了我的团队协作精神和职业素养。
在今后的学习和工作中,我将继续努力,不断提高自己的技能水平,为我国制造业的发展贡献自己的力量。
现代制造技术实习报告

现代制造技术实习报告在当今快速发展的工业领域,现代制造技术的不断革新为生产带来了更高的效率和更优的质量。
为了更深入地了解和掌握这些先进技术,我参加了一次意义非凡的现代制造技术实习。
实习单位是一家在行业内具有领先地位的制造企业,拥有先进的生产设备和完善的工艺流程。
刚进入实习单位,我就被其现代化的厂房和高效的生产线所震撼。
在实习过程中,我接触到了多种现代制造技术,其中包括数控加工技术。
数控加工是一种利用数字化控制系统来控制机床运动和加工过程的技术。
通过编程输入指令,机床能够精确地按照预定的轨迹和参数进行加工,大大提高了加工精度和效率。
我观察到操作人员熟练地使用计算机辅助设计(CAD)和计算机辅助制造(CAM)软件,将零件的设计图纸转化为数控加工程序,并在机床上进行实际加工。
这一过程不仅需要对软件的熟练掌握,还需要对加工工艺和刀具选择有深入的理解。
另外,快速成型技术也给我留下了深刻的印象。
这是一种基于离散堆积原理的新型制造技术,能够直接根据三维模型快速制造出实体零件。
实习单位使用的是 3D 打印技术,通过逐层堆积材料,将数字模型转化为实际的物体。
我看到了从医疗领域的人体器官模型到工业领域的复杂零部件,3D 打印技术展现出了其在个性化定制和复杂结构制造方面的巨大优势。
激光加工技术也是现代制造领域的重要组成部分。
激光具有高能量密度和高精度的特点,可以用于切割、焊接、打孔等多种加工工艺。
在实习中,我看到了激光切割设备在薄板金属加工中的高效应用,切割边缘光滑、精度高,而且能够实现复杂形状的切割。
在实际操作环节,我在师傅的指导下亲自参与了一些简单的数控加工编程和操作。
从零件图纸的分析,到工艺路线的制定,再到数控程序的编写和调试,每一个步骤都需要严谨和细致。
在这个过程中,我深刻体会到了理论知识与实际操作之间的差距,也明白了只有通过不断的实践和总结,才能真正掌握一门技术。
通过这次实习,我不仅学到了先进的制造技术,还对现代制造业的发展有了更清晰的认识。
工程训练实习报告激光加工

实习报告
一、实习背景与目的
随着现代制造业的快速发展,激光加工技术在各个领域得到了广泛的应用。
为了更好地了解激光加工技术,提高自己的实践能力,我选择了激光加工实习项目。
本次实习旨在学习激光加工的基本原理、设备操作和应用技巧,将理论知识与实践相结合,提升自己的综合素质。
二、实习内容与过程
在实习期间,我主要进行了激光切割、激光焊接和激光打标等操作。
在导师的指导下,我首先了解了激光加工设备的基本组成、工作原理和操作注意事项。
然后,我学习了如何调整激光发生器、切割头、工作台等部件,以适应不同的加工需求。
在实际操作过程中,我掌握了激光切割参数的设置、焊接工艺的优化和打标图案的设计等技能。
三、实习成果与收获
通过实习,我深入了解了激光加工技术的基本原理和应用领域。
我学会了操作激光加工设备,掌握了不同加工工艺的特点和适用范围。
在实践中,我不仅提高了自己的动手能力,还培养了自己的创新思维和团队协作精神。
此外,我还学会了如何处理激光加工过程中出现的问题,提高了自己的故障排除能力。
四、实习反思与展望
通过本次实习,我认识到理论知识与实践操作之间的联系十分紧密。
在今后的学习中,我将更加注重理论知识的积累,并将所学运用到实践中去。
同时,我也意识到激光加工技术在不断发展和创新,我将继续关注行业动态,学习新技术,提升自己的专业素养。
总之,本次激光加工实习给我留下了深刻的印象。
通过实习,我不仅掌握了激光加工技术的基本操作,还提高了自己的实践能力和综合素质。
我相信这次实习对我今后的学习和职业发展将产生积极的影响。
现代制造实习报告

现代制造实习报告一、实习目的与意义随着科技的飞速发展,现代制造业正逐渐成为国家经济的支柱产业。
为了适应这一发展趋势,提高自身实践能力和专业素养,我参加了为期一个月的现代制造实习。
通过此次实习,旨在了解现代制造业的基本生产流程,掌握相关制造工艺,培养实际操作能力和团队协作精神,为今后的工作奠定基础。
二、实习内容与过程实习期间,我所在的实习小组参观了多家现代制造企业,包括精密仪器制造、汽车配件生产、电子器件加工等。
通过实地参观和动手操作,我们了解了各种制造工艺的基本流程,掌握了部分设备的操作方法,并学会了如何进行生产管理和质量控制。
1. 精密仪器制造我们首先参观了精密仪器制造企业,了解了仪器制造的基本工艺流程,包括零件加工、装配、调试等。
在零件加工环节,我们参观了数控机床、激光切割等先进设备,并学会了如何操作这些设备进行零件加工。
在装配环节,我们学会了如何根据图纸和工艺要求进行零件组装,并进行调试,确保仪器正常运行。
2. 汽车配件生产在汽车配件生产企业,我们参观了冲压、焊接、涂装等生产线,了解了汽车配件生产的全过程。
在冲压环节,我们学会了如何操作冲压设备进行零件冲压。
在焊接环节,我们了解了焊接工艺,并学会了如何操作焊接设备进行焊接。
在涂装环节,我们了解了涂装工艺,并学会了如何操作涂装设备进行涂装。
3. 电子器件加工在电子器件加工企业,我们参观了电子器件的封装、测试等生产线,了解了电子器件加工的基本工艺流程。
在封装环节,我们学会了如何操作封装设备进行器件封装。
在测试环节,我们学会了如何操作测试设备进行器件测试,确保器件性能符合要求。
三、实习收获与反思通过这次实习,我收获颇丰。
首先,我了解了现代制造业的基本生产流程和制造工艺,掌握了部分设备的操作方法。
其次,我学会了如何进行生产管理和质量控制,提高了自己的团队协作能力。
最后,我认识到了理论知识与实际操作的密切结合的重要性,激发了自己继续学习的热情。
然而,在实习过程中,我也发现了自己在理论知识掌握方面仍有不足,需要在今后的学习中加强巩固。
数控实习报告的实习过程
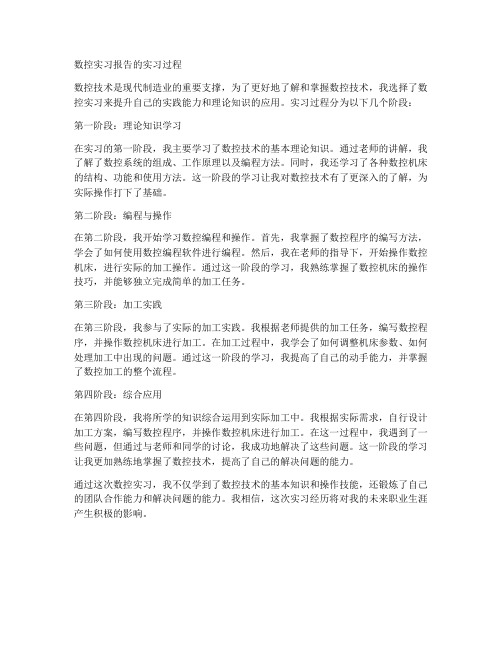
数控实习报告的实习过程数控技术是现代制造业的重要支撑,为了更好地了解和掌握数控技术,我选择了数控实习来提升自己的实践能力和理论知识的应用。
实习过程分为以下几个阶段:第一阶段:理论知识学习在实习的第一阶段,我主要学习了数控技术的基本理论知识。
通过老师的讲解,我了解了数控系统的组成、工作原理以及编程方法。
同时,我还学习了各种数控机床的结构、功能和使用方法。
这一阶段的学习让我对数控技术有了更深入的了解,为实际操作打下了基础。
第二阶段:编程与操作在第二阶段,我开始学习数控编程和操作。
首先,我掌握了数控程序的编写方法,学会了如何使用数控编程软件进行编程。
然后,我在老师的指导下,开始操作数控机床,进行实际的加工操作。
通过这一阶段的学习,我熟练掌握了数控机床的操作技巧,并能够独立完成简单的加工任务。
第三阶段:加工实践在第三阶段,我参与了实际的加工实践。
我根据老师提供的加工任务,编写数控程序,并操作数控机床进行加工。
在加工过程中,我学会了如何调整机床参数、如何处理加工中出现的问题。
通过这一阶段的学习,我提高了自己的动手能力,并掌握了数控加工的整个流程。
第四阶段:综合应用在第四阶段,我将所学的知识综合运用到实际加工中。
我根据实际需求,自行设计加工方案,编写数控程序,并操作数控机床进行加工。
在这一过程中,我遇到了一些问题,但通过与老师和同学的讨论,我成功地解决了这些问题。
这一阶段的学习让我更加熟练地掌握了数控技术,提高了自己的解决问题的能力。
通过这次数控实习,我不仅学到了数控技术的基本知识和操作技能,还锻炼了自己的团队合作能力和解决问题的能力。
我相信,这次实习经历将对我的未来职业生涯产生积极的影响。
数控加工实习报告(最新8篇)

数控加工实习报告(最新8篇)数控加工实习报告篇一一、实习目的和意义数控加工是一种高精度、高效率的加工工艺,具有广泛的应用前景。
通过实习,我旨在了解数控加工的基本原理和技术,掌握数控机床的操作方法,提高自己的实际操作能力和技术水平。
二、实习内容和方法1. 学习数控加工的基本原理和技术:通过阅读相关资料和参观数控加工车间,了解数控加工的基本原理和技术要点,包括数控机床的结构、工作原理、编程方法和加工工艺等。
2. 学习数控机床的操作方法:通过实际操作数控机床,学习数控机床的操作方法,包括开机、关机、切换模式、选择刀具、设置参数等。
3. 编写数控程序并进行加工实验:根据实际加工要求,编写数控程序,并通过数控机床进行加工实验,观察加工过程和结果,分析加工误差和改进措施。
三、实习过程和成果1. 学习数控加工的基本原理和技术:通过阅读相关资料和参观数控加工车间,我对数控加工的基本原理和技术有了初步的了解,包括数控机床的结构、工作原理、编程方法和加工工艺等。
2. 学习数控机床的操作方法:在实习期间,我通过实际操作数控机床,学习了数控机床的操作方法,包括开机、关机、切换模式、选择刀具、设置参数等。
通过反复练习,我逐渐掌握了数控机床的操作技巧。
3. 编写数控程序并进行加工实验:根据实际加工要求,我编写了一段简单的。
数控程序,并通过数控机床进行了加工实验。
在加工过程中,我仔细观察了加工过程和结果,并记录了加工误差。
通过对加工误差的分析,我找出了改进措施,并进行了第二次加工实验。
经过多次试验和改进,我最终取得了满意的加工结果。
四、实习心得和体会通过这次数控加工实习,我深刻认识到数控加工的重要性和广泛应用的前景。
数控加工不仅能够提高加工精度和效率,还能够减少人工操作的错误和劳动强度。
在实习过程中,我不仅学到了专业知识和技能,还培养了团队合作和解决问题的能力。
通过与同学和老师的交流和合作,我解决了许多实际操作中遇到的问题,并取得了良好的实习成果。
装配车间实习报告
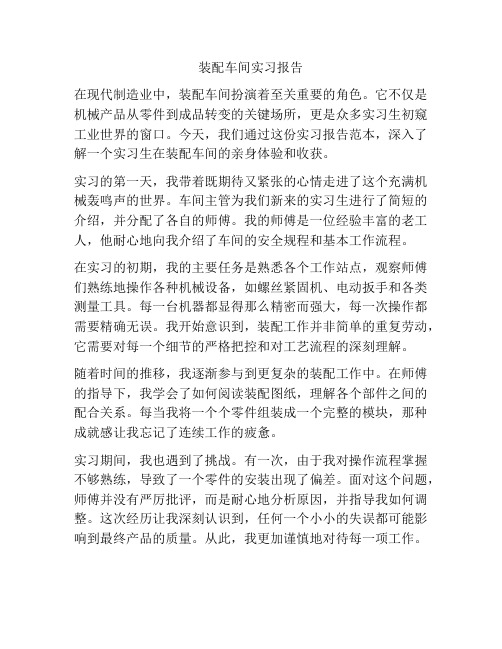
装配车间实习报告在现代制造业中,装配车间扮演着至关重要的角色。
它不仅是机械产品从零件到成品转变的关键场所,更是众多实习生初窥工业世界的窗口。
今天,我们通过这份实习报告范本,深入了解一个实习生在装配车间的亲身体验和收获。
实习的第一天,我带着既期待又紧张的心情走进了这个充满机械轰鸣声的世界。
车间主管为我们新来的实习生进行了简短的介绍,并分配了各自的师傅。
我的师傅是一位经验丰富的老工人,他耐心地向我介绍了车间的安全规程和基本工作流程。
在实习的初期,我的主要任务是熟悉各个工作站点,观察师傅们熟练地操作各种机械设备,如螺丝紧固机、电动扳手和各类测量工具。
每一台机器都显得那么精密而强大,每一次操作都需要精确无误。
我开始意识到,装配工作并非简单的重复劳动,它需要对每一个细节的严格把控和对工艺流程的深刻理解。
随着时间的推移,我逐渐参与到更复杂的装配工作中。
在师傅的指导下,我学会了如何阅读装配图纸,理解各个部件之间的配合关系。
每当我将一个个零件组装成一个完整的模块,那种成就感让我忘记了连续工作的疲惫。
实习期间,我也遇到了挑战。
有一次,由于我对操作流程掌握不够熟练,导致了一个零件的安装出现了偏差。
面对这个问题,师傅并没有严厉批评,而是耐心地分析原因,并指导我如何调整。
这次经历让我深刻认识到,任何一个小小的失误都可能影响到最终产品的质量。
从此,我更加谨慎地对待每一项工作。
除了技术技能的学习,实习还让我对车间的管理和团队协作有了更深的理解。
我发现,一个高效的装配车间不仅需要先进的设备和技术,更需要良好的管理来协调每个人的工作,确保生产线的顺畅运行。
在与同事们的交流中,我学会了如何在团队中发挥自己的作用,如何与他人沟通和协作,共同完成生产任务。
在实习即将结束时,我已经能够独立完成一些基本的装配工作,并对整个装配流程有了全面的认识。
我知道,这段实习经历不仅仅是对专业技能的提升,更是对工作态度和职业素养的锻炼。
回顾这段实习旅程,我深感收获满满。
线切割技术训练实习报告
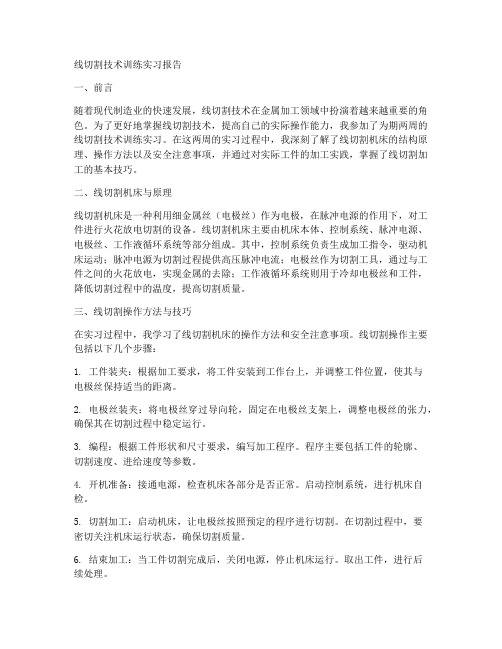
线切割技术训练实习报告一、前言随着现代制造业的快速发展,线切割技术在金属加工领域中扮演着越来越重要的角色。
为了更好地掌握线切割技术,提高自己的实际操作能力,我参加了为期两周的线切割技术训练实习。
在这两周的实习过程中,我深刻了解了线切割机床的结构原理、操作方法以及安全注意事项,并通过对实际工件的加工实践,掌握了线切割加工的基本技巧。
二、线切割机床与原理线切割机床是一种利用细金属丝(电极丝)作为电极,在脉冲电源的作用下,对工件进行火花放电切割的设备。
线切割机床主要由机床本体、控制系统、脉冲电源、电极丝、工作液循环系统等部分组成。
其中,控制系统负责生成加工指令,驱动机床运动;脉冲电源为切割过程提供高压脉冲电流;电极丝作为切割工具,通过与工件之间的火花放电,实现金属的去除;工作液循环系统则用于冷却电极丝和工件,降低切割过程中的温度,提高切割质量。
三、线切割操作方法与技巧在实习过程中,我学习了线切割机床的操作方法和安全注意事项。
线切割操作主要包括以下几个步骤:1. 工件装夹:根据加工要求,将工件安装到工作台上,并调整工件位置,使其与电极丝保持适当的距离。
2. 电极丝装夹:将电极丝穿过导向轮,固定在电极丝支架上,调整电极丝的张力,确保其在切割过程中稳定运行。
3. 编程:根据工件形状和尺寸要求,编写加工程序。
程序主要包括工件的轮廓、切割速度、进给速度等参数。
4. 开机准备:接通电源,检查机床各部分是否正常。
启动控制系统,进行机床自检。
5. 切割加工:启动机床,让电极丝按照预定的程序进行切割。
在切割过程中,要密切关注机床运行状态,确保切割质量。
6. 结束加工:当工件切割完成后,关闭电源,停止机床运行。
取出工件,进行后续处理。
在操作过程中,以下几点技巧对于提高切割质量和效率具有重要意义:1. 合理选择脉冲参数:脉冲参数(如脉冲宽度、脉冲间隔、电流大小等)对切割速度和质量有直接影响。
在实际操作中,要根据工件材料和形状,合理调整脉冲参数。
现代制造实习报告
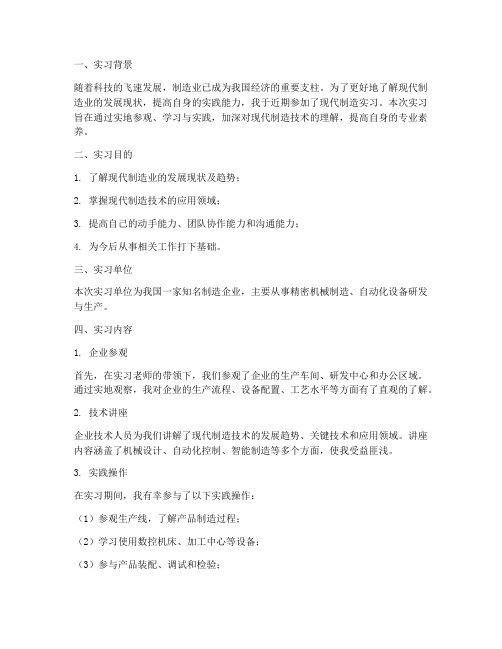
一、实习背景随着科技的飞速发展,制造业已成为我国经济的重要支柱。
为了更好地了解现代制造业的发展现状,提高自身的实践能力,我于近期参加了现代制造实习。
本次实习旨在通过实地参观、学习与实践,加深对现代制造技术的理解,提高自身的专业素养。
二、实习目的1. 了解现代制造业的发展现状及趋势;2. 掌握现代制造技术的应用领域;3. 提高自己的动手能力、团队协作能力和沟通能力;4. 为今后从事相关工作打下基础。
三、实习单位本次实习单位为我国一家知名制造企业,主要从事精密机械制造、自动化设备研发与生产。
四、实习内容1. 企业参观首先,在实习老师的带领下,我们参观了企业的生产车间、研发中心和办公区域。
通过实地观察,我对企业的生产流程、设备配置、工艺水平等方面有了直观的了解。
2. 技术讲座企业技术人员为我们讲解了现代制造技术的发展趋势、关键技术和应用领域。
讲座内容涵盖了机械设计、自动化控制、智能制造等多个方面,使我受益匪浅。
3. 实践操作在实习期间,我有幸参与了以下实践操作:(1)参观生产线,了解产品制造过程;(2)学习使用数控机床、加工中心等设备;(3)参与产品装配、调试和检验;(4)学习编写程序,实现设备自动化控制。
4. 团队协作在实习过程中,我结识了许多志同道合的同学。
我们共同完成各项任务,互相学习、互相帮助,培养了团队协作精神。
五、实习收获1. 理论知识与实践相结合通过实习,我深刻体会到理论知识与实践操作的重要性。
在实际工作中,理论知识能够指导实践,而实践经验又能反过来丰富理论知识。
2. 提高动手能力在实习过程中,我学会了使用多种机械设备,提高了自己的动手能力。
这对于今后从事相关工作具有重要意义。
3. 增强团队协作能力实习期间,我与同学们共同完成任务,学会了如何与他人沟通、协作,提高了自己的团队协作能力。
4. 了解行业现状通过实习,我对现代制造业的发展现状和趋势有了更深入的了解,为今后从事相关工作奠定了基础。
现代加工技术实践实习报告

现代加工技术实践实习报告一、前言随着科技的飞速发展,现代加工技术在制造业中的应用日益广泛,为了更好地了解和掌握这些先进技术,提高自己的实践能力,我参加了为期两周的现代加工技术实践实习。
本次实习主要在学校的现代加工技术实验室进行,通过实习,我对现代加工技术有了更深入的了解和认识。
二、实习内容1. 了解现代加工技术的基本概念、分类和特点。
现代加工技术主要包括数控加工、激光加工、电火花加工、超声波加工等。
这些加工技术具有高精度、高效率、高自动化程度和良好的加工质量等特点。
2. 学习数控加工技术的基本原理和操作方法。
数控加工技术是通过计算机编程控制机床运动和加工过程的一种自动化加工方法。
实习期间,我学习了数控车床、数控铣床和数控加工中心的操作方法,并编写了一些简单的数控程序。
3. 掌握激光加工技术的基本原理和应用。
激光加工技术是利用高能量密度的激光束对材料进行加工的一种非接触式加工方法。
实习期间,我了解了激光切割、激光焊接和激光打标等激光加工技术的原理和应用。
4. 学习电火花加工和超声波加工技术的基本原理和操作方法。
电火花加工是利用电火花放电原理对金属进行加工的一种方法,适用于加工硬质合金、淬硬钢等难加工材料。
超声波加工是利用超声波振动对材料进行加工的一种方法,适用于加工硬质材料和微小零件。
三、实习收获1. 提高了自己的动手能力和实际操作技能。
通过实习,我学会了数控机床、激光切割机、电火花加工机和超声波加工机等现代加工设备的操作方法,并能够独立完成一些简单的加工任务。
2. 加深了对现代加工技术理论和实际应用的理解。
通过实习,我对数控加工、激光加工、电火花加工和超声波加工等现代加工技术的原理和应用有了更深入的了解,为以后的学习和工作打下了坚实的基础。
3. 增强了自己的团队协作能力和沟通能力。
在实习过程中,我与同学们一起完成了一些团队协作的任务,通过相互交流和讨论,提高了自己的沟通能力和团队合作精神。
四、实习总结通过本次现代加工技术实践实习,我对现代加工技术有了更深入的了解和认识,提高了自己的实践能力和动手技能。
现代制造工程系实习报告
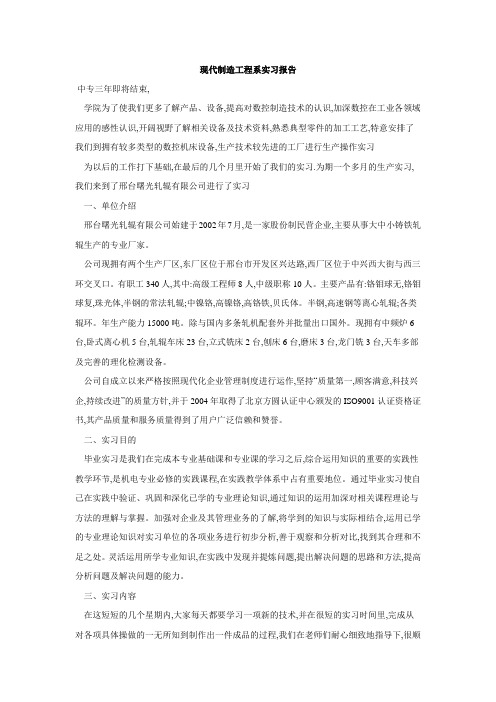
现代制造工程系实习报告中专三年即将结束,学院为了使我们更多了解产品、设备,提高对数控制造技术的认识,加深数控在工业各领域应用的感性认识,开阔视野了解相关设备及技术资料,熟悉典型零件的加工工艺,特意安排了我们到拥有较多类型的数控机床设备,生产技术较先进的工厂进行生产操作实习为以后的工作打下基础,在最后的几个月里开始了我们的实习.为期一个多月的生产实习,我们来到了邢台曙光轧辊有限公司进行了实习一、单位介绍邢台曙光轧辊有限公司始建于2002年7月,是一家股份制民营企业,主要从事大中小铸铁轧辊生产的专业厂家。
公司现拥有两个生产厂区,东厂区位于邢台市开发区兴达路,西厂区位于中兴西大街与西三环交叉口。
有职工340人,其中:高级工程师8人,中级职称10人。
主要产品有:铬钼球无,铬钼球复,珠光体,半钢的常法轧辊;中镍铬,高镍铬,高铬铁,贝氏体。
半钢,高速钢等离心轧辊;各类辊环。
年生产能力15000吨。
除与国内多条轧机配套外并批量出口国外。
现拥有中频炉6台,卧式离心机5台,轧辊车床23台,立式铣床2台,刨床6台,磨床3台,龙门铣3台,天车多部及完善的理化检测设备。
公司自成立以来严格按照现代化企业管理制度进行运作,坚持“质量第一,顾客满意,科技兴企,持续改进”的质量方针,并于2004年取得了北京方圆认证中心颁发的ISO9001认证资格证书,其产品质量和服务质量得到了用户广泛信赖和赞誉。
二、实习目的毕业实习是我们在完成本专业基础课和专业课的学习之后,综合运用知识的重要的实践性教学环节,是机电专业必修的实践课程,在实践教学体系中占有重要地位。
通过毕业实习使自己在实践中验证、巩固和深化已学的专业理论知识,通过知识的运用加深对相关课程理论与方法的理解与掌握。
加强对企业及其管理业务的了解,将学到的知识与实际相结合,运用已学的专业理论知识对实习单位的各项业务进行初步分析,善于观察和分析对比,找到其合理和不足之处。
灵活运用所学专业知识,在实践中发现并提炼问题,提出解决问题的思路和方法,提高分析问题及解决问题的能力。
现代制造技术实习报告总结

实习报告总结:现代制造技术实习一、实习背景与目的随着科技的飞速发展,现代制造技术在各个领域中的应用日益广泛,为了更好地了解和掌握现代制造技术的基本原理和实际操作,提高自身的实践能力,我参加了为期两周的现代制造技术实习。
本次实习旨在让我们深入了解数控加工、加工中心、电火花线切割加工等现代制造技术的基本工艺及操作技术要领,培养我们的实践动手能力和创新思维。
二、实习内容与过程在实习过程中,我们学习了数控加工的基础知识、数控车床、数控铣床、加工中心、电火花线切割加工、数控雕刻机、三坐标测量仪、快速成形等现代制造技术。
通过实地操作和练习,我们初步掌握了各种加工方法的操作要领,并对现代制造技术有了更深入的了解。
1. 数控加工基础知识我们首先学习了数控加工的基本概念、原理和分类,了解了数控系统的组成及工作原理。
同时,学习了数控编程的基本方法,掌握了G代码和M代码的使用方法,为后续的实际操作打下了基础。
2. 数控车床与数控铣床在数控车床和数控铣床的操作实践中,我们学习了刀具的选择、装夹、对刀及加工参数的设置等基本操作步骤。
通过实际操作,掌握了数控车床和数控铣床的操作要领,并学会了如何根据零件图纸进行编程和加工。
3. 加工中心加工中心是现代制造技术中重要的设备之一。
在加工中心的操作实践中,我们了解了加工中心的特点、分类和应用领域。
通过实际操作,掌握了加工中心的刀具更换、工件装夹、加工参数设置等基本操作步骤,提高了加工效率。
4. 电火花线切割加工电火花线切割加工是现代制造技术中的一种特种加工方法。
在实习过程中,我们学习了线切割加工的基本原理、设备组成及操作方法。
通过实际操作,掌握了线切割加工的工艺参数设置、工件装夹等操作要领,并了解了线切割加工在实际生产中的应用。
5. 数控雕刻机、三坐标测量仪及快速成形在数控雕刻机、三坐标测量仪和快速成形的实习过程中,我们分别学习了这些设备的基本原理、操作方法和应用场景。
通过实际操作,掌握了数控雕刻机的刀具路径规划、三坐标测量仪的测量原理及快速成形技术的工艺流程,为今后的实际工作积累了经验。
数控及线切割实习报告

数控及线切割实习报告一、实习目的与意义随着现代制造业的快速发展,数控技术及线切割加工在生产中的应用越来越广泛。
为了更好地将理论知识与实际操作相结合,提高自己的实践能力和综合素质,我参加了数控及线切割实习。
本次实习旨在深入了解数控及线切割加工的基本原理、工艺流程和操作技能,培养自己的创新意识和创新能力。
二、实习内容与过程1. 数控实习数控实习主要包括数控车削、数控铣削和加工中心等加工技术。
在实习过程中,我学习了数控加工的基本原理、数控编程、机床操作和加工工艺等方面知识。
通过实习,我掌握了数控加工的操作步骤,学会了使用数控仿真软件进行编程和仿真操作,并能够独立完成一些简单的数控加工任务。
2. 线切割实习线切割实习主要涉及线切割机床的操作、加工原理和工艺参数设置等方面。
我学习了线切割的基本原理,了解了线切割机床的构成及功能,掌握了线切割加工的操作步骤和工艺参数的选择。
通过实习,我能够独立操作线切割机床,完成一些简单的线切割加工任务。
三、实习收获与体会1. 技能提升通过数控及线切割实习,我掌握了一定的数控和线切割加工操作技能,能够独立完成一些简单的加工任务。
同时,我学会了使用数控仿真软件进行编程和仿真操作,提高了自己的实际操作能力。
2. 工艺理解实习过程中,我深入了解了数控及线切割加工的工艺流程和参数设置,掌握了不同材料和加工要求下的工艺优化方法。
这对我今后在实际生产中解决加工问题具有很大的指导意义。
3. 团队合作与创新意识在实习过程中,我与同学们共同完成了一些加工任务,培养了团队合作精神。
同时,我意识到创新意识在实际生产中的重要性,并在实习过程中不断尝试创新,提高自己的创新能力。
四、总结数控及线切割实习让我受益匪浅,不仅提高了自己的实践能力和综合素质,还对数控及线切割加工技术有了更深入的了解。
通过实习,我认识到理论知识与实际操作相结合的重要性,并为今后在制造业领域的发展奠定了基础。
在今后的学习和工作中,我将继续努力,不断提高自己的专业素养,为我国制造业的繁荣做出贡献。
智能制造工厂实习报告感受
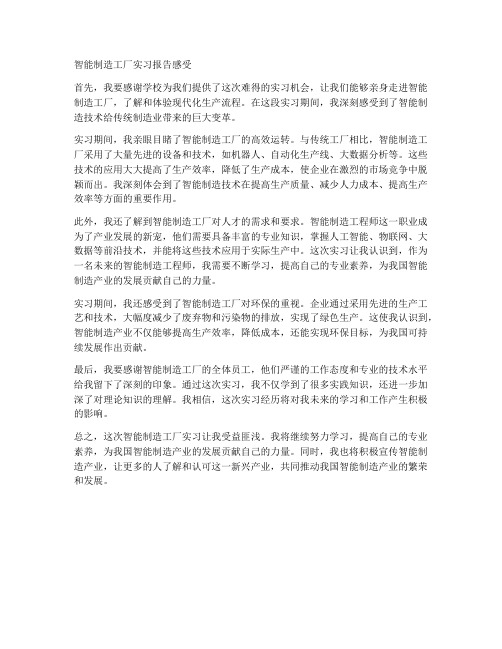
智能制造工厂实习报告感受首先,我要感谢学校为我们提供了这次难得的实习机会,让我们能够亲身走进智能制造工厂,了解和体验现代化生产流程。
在这段实习期间,我深刻感受到了智能制造技术给传统制造业带来的巨大变革。
实习期间,我亲眼目睹了智能制造工厂的高效运转。
与传统工厂相比,智能制造工厂采用了大量先进的设备和技术,如机器人、自动化生产线、大数据分析等。
这些技术的应用大大提高了生产效率,降低了生产成本,使企业在激烈的市场竞争中脱颖而出。
我深刻体会到了智能制造技术在提高生产质量、减少人力成本、提高生产效率等方面的重要作用。
此外,我还了解到智能制造工厂对人才的需求和要求。
智能制造工程师这一职业成为了产业发展的新宠,他们需要具备丰富的专业知识,掌握人工智能、物联网、大数据等前沿技术,并能将这些技术应用于实际生产中。
这次实习让我认识到,作为一名未来的智能制造工程师,我需要不断学习,提高自己的专业素养,为我国智能制造产业的发展贡献自己的力量。
实习期间,我还感受到了智能制造工厂对环保的重视。
企业通过采用先进的生产工艺和技术,大幅度减少了废弃物和污染物的排放,实现了绿色生产。
这使我认识到,智能制造产业不仅能够提高生产效率,降低成本,还能实现环保目标,为我国可持续发展作出贡献。
最后,我要感谢智能制造工厂的全体员工,他们严谨的工作态度和专业的技术水平给我留下了深刻的印象。
通过这次实习,我不仅学到了很多实践知识,还进一步加深了对理论知识的理解。
我相信,这次实习经历将对我未来的学习和工作产生积极的影响。
总之,这次智能制造工厂实习让我受益匪浅。
我将继续努力学习,提高自己的专业素养,为我国智能制造产业的发展贡献自己的力量。
同时,我也将积极宣传智能制造产业,让更多的人了解和认可这一新兴产业,共同推动我国智能制造产业的繁荣和发展。
数车详细实习报告

数控车床实习报告一、前言随着现代制造业的快速发展,数控技术已经成为了机械制造领域的重要技术之一。
数控车床作为数控技术的一种重要应用,具有高精度、高效率、自动化程度高等优点,广泛应用于各种轴类、盘类、套类等零件的加工中。
为了更好地掌握数控车床的操作技能和编程技术,我参加了为期两周的数控车床实习。
本报告将对实习过程中的学习内容、收获和体会进行总结和分享。
二、实习内容1. 数控车床的基本结构和工作原理数控车床主要由床身、主轴、进给系统、刀架、数控系统等部分组成。
在实习过程中,我们首先了解了数控车床的基本结构和工作原理,掌握了各部分的功能和作用。
2. 数控车床的操作方法和步骤实习过程中,我们学习了数控车床的操作方法和步骤,包括开机、关机、对刀、编程、加工等。
通过对操作方法的熟练掌握,我们可以更好地控制数控车床进行零件加工。
3. 数控编程技术数控编程技术是数控车床加工的关键技术之一。
在实习过程中,我们学习了数控编程的基本方法,掌握了常用的G代码、M代码、T代码等功能指令,并能根据零件图纸编写合适的数控程序。
4. 常见零件的加工工艺实习过程中,我们学习了轴类、盘类、套类等常见零件的加工工艺,掌握了各种零件的加工方法和注意事项。
5. 数控车床的维护和故障排除为了保证数控车床的正常运行,我们需要对数控车床进行定期维护和故障排除。
在实习过程中,我们学习了数控车床的维护方法和故障排除技巧。
三、实习收获1. 技能方面:通过实习,我掌握了数控车床的操作方法和编程技术,能够独立完成轴类、盘类、套类等常见零件的加工。
2. 团队合作:在实习过程中,我们学会了与他人合作,共同完成加工任务。
团队合作意识和能力得到了提高。
3. 安全意识:实习过程中,我们深刻认识到安全生产的重要性,掌握了数控车床的安全操作规程,提高了自己的安全意识。
4. 分析问题和解决问题的能力:在实习过程中,我们遇到了各种加工问题和设备故障,通过请教老师、查阅资料等方式,我们学会了分析问题和解决问题,提高了自己的动手能力和创新能力。
数字化制造技术实习报告
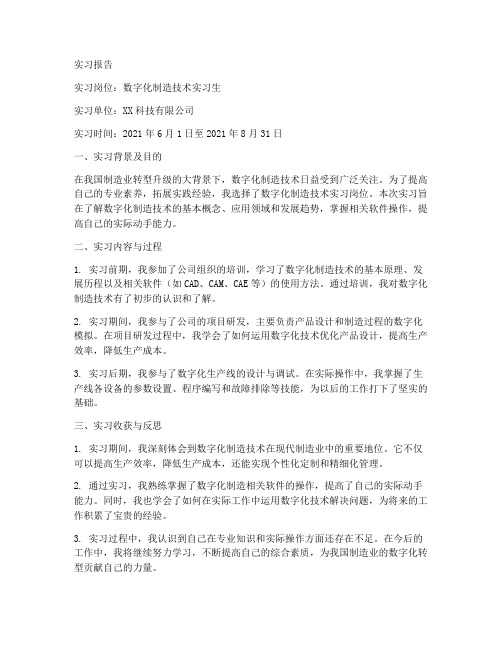
实习报告实习岗位:数字化制造技术实习生实习单位:XX科技有限公司实习时间:2021年6月1日至2021年8月31日一、实习背景及目的在我国制造业转型升级的大背景下,数字化制造技术日益受到广泛关注。
为了提高自己的专业素养,拓展实践经验,我选择了数字化制造技术实习岗位。
本次实习旨在了解数字化制造技术的基本概念、应用领域和发展趋势,掌握相关软件操作,提高自己的实际动手能力。
二、实习内容与过程1. 实习前期,我参加了公司组织的培训,学习了数字化制造技术的基本原理、发展历程以及相关软件(如CAD、CAM、CAE等)的使用方法。
通过培训,我对数字化制造技术有了初步的认识和了解。
2. 实习期间,我参与了公司的项目研发,主要负责产品设计和制造过程的数字化模拟。
在项目研发过程中,我学会了如何运用数字化技术优化产品设计,提高生产效率,降低生产成本。
3. 实习后期,我参与了数字化生产线的设计与调试。
在实际操作中,我掌握了生产线各设备的参数设置、程序编写和故障排除等技能,为以后的工作打下了坚实的基础。
三、实习收获与反思1. 实习期间,我深刻体会到数字化制造技术在现代制造业中的重要地位。
它不仅可以提高生产效率,降低生产成本,还能实现个性化定制和精细化管理。
2. 通过实习,我熟练掌握了数字化制造相关软件的操作,提高了自己的实际动手能力。
同时,我也学会了如何在实际工作中运用数字化技术解决问题,为将来的工作积累了宝贵的经验。
3. 实习过程中,我认识到自己在专业知识和实际操作方面还存在不足。
在今后的工作中,我将继续努力学习,不断提高自己的综合素质,为我国制造业的数字化转型贡献自己的力量。
四、实习总结通过本次实习,我对数字化制造技术有了更加深入的了解,掌握了相关软件的操作,提高了自己的实际动手能力。
同时,我也认识到了自己在专业知识和实际操作方面的不足,明确了今后的学习方向。
在今后的学习和工作中,我将继续努力,为我国制造业的数字化转型贡献自己的力量。
smt工艺实习报告
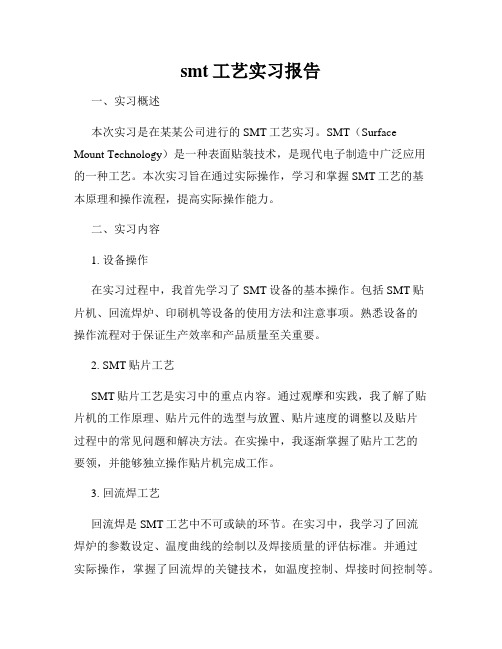
smt工艺实习报告一、实习概述本次实习是在某某公司进行的SMT工艺实习。
SMT(SurfaceMount Technology)是一种表面贴装技术,是现代电子制造中广泛应用的一种工艺。
本次实习旨在通过实际操作,学习和掌握SMT工艺的基本原理和操作流程,提高实际操作能力。
二、实习内容1. 设备操作在实习过程中,我首先学习了SMT设备的基本操作。
包括SMT贴片机、回流焊炉、印刷机等设备的使用方法和注意事项。
熟悉设备的操作流程对于保证生产效率和产品质量至关重要。
2. SMT贴片工艺SMT贴片工艺是实习中的重点内容。
通过观摩和实践,我了解了贴片机的工作原理、贴片元件的选型与放置、贴片速度的调整以及贴片过程中的常见问题和解决方法。
在实操中,我逐渐掌握了贴片工艺的要领,并能够独立操作贴片机完成工作。
3. 回流焊工艺回流焊是SMT工艺中不可或缺的环节。
在实习中,我学习了回流焊炉的参数设定、温度曲线的绘制以及焊接质量的评估标准。
并通过实际操作,掌握了回流焊的关键技术,如温度控制、焊接时间控制等。
4. 质量控制质量控制是保证SMT生产质量的重要环节。
在实习中,我了解了电子元件质量检测的方法和流程。
学习了如何判断元件焊接是否合格,以及如何使用测试工具对元件进行可靠性测试等。
通过这些学习,我能够在实践中进行简单的质量控制工作。
三、实习收获通过这次实习,我对SMT工艺有了更深入的了解和掌握。
具体来说,我获得了以下收获:1. 熟悉SMT设备的操作流程和注意事项,能够独立操作设备,提高了实际操作能力。
2. 掌握了SMT贴片工艺的基本原理和操作要领,能够独立进行贴片操作。
3. 熟悉了回流焊工艺的关键技术和质量控制要点,能够进行回流焊操作和简单的质量控制工作。
4. 培养了团队协作能力和沟通能力,通过与同学和导师的合作,共同解决了实习过程中的问题。
四、实习总结通过这次SMT工艺实习,我对电子制造领域有了更深入的认识,并初步掌握了SMT工艺的核心技术。
现代制造技术实习报告

现代制造技术实习报告————长沙理工大学2014年实习学号:201021030526一、实习目的①、掌握机械制造设计方案和使用制图软件完成图纸绘制;②、了解现代制造工艺中零件的加工过程和工作原理;③、通过实习了解本专业在实际生产中专业课程知识的应用;④、了解现代制造技术在实际生产中的应用。
二、实习内容Ⅰ:数控车加工(Φ35×80)1、实习要求本实习以典型轴零件为例,在CY3600数控车机床上,用Φ35×100的铝棒加工出尺寸如图一所示的零件。
图一2、数控加工工艺路线及工艺参数的设置①根据图纸要求按照先主后次的加工顺序,确定如下工艺路线:a粗加工,b精加工c切螺纹d切槽,切断零件②建立工件坐标系:以O点为编程原点,以零件轴径向为X轴,轴向为Z轴建立工件坐标系。
③选择刀具及换刀点:根据加工要求,选择3把刀:#1为外圆车刀、#2螺纹车刀、#3切槽(切断刀)刀宽3毫米为了避免换刀时刀具与机床、工件及夹具发生干涉现象,加工本零件时,换刀点选为(X40 ,Z150)④分析该零件材料及型面结构,参考《实用机械加工工艺手册》,确定加工工艺参数如表1所示。
序号切削用量备注S/(r/min) F/(mm/r) 1 加料棒外圆伸出长度约为66mm500 1002 粗车右端面等留加工余量单边0.3mm3 精车右端面,圆弧等达到图纸要800 50求4 换二号刀切螺纹200 1.55 换三号刀切槽、切断200 506789表一3、数控加工程序00001N010 G00 X40 Z150 S500 M03N020 G00 X30 Z2N030 T0101N040 G01 Z-65 F100N050 X40N060 G00 Z2N070 X26N080 G01 Z-34N090 G02 X26 Z-34 R1N100 G01 X28 Z-35N110 G00 X20N120 Z2N130 X24N140 G01 Z-34N150 G02 X24 Z-34 R2N160 G01 X28 Z-36N170 Z2N180 G01 Z0 F50 S800N190 X22N200 X24 Z-1N210 Z-34N220 G02 X24 Z-34 R3N230 G01 X30 Z-37N240 G01 X30 Z-65N250 G00 X40 Z150N260 T0100N270 T0202N280 G00 X24 Z5 S200 M03N290 G92 X23.2 Z-16.5 F1.5N300 X22.8N310 X22.6N320 X22.5N330 G00 X40 Z-16.5N330 G00 X40 Z150N340 T0200N350 T0303N360 G00 X30 Z-18.5 S250 M03N370 G01 X20 F80N380 X30N390 G00 X40 Z-60N400G01 X0N410 G00 X40 Z150M05M024、实习操作步骤①装夹工件:…………②数控车床启动:………..③输入零件数据加工程序:……….④对刀及刀具偏置的设定:…………⑤程序校验:…………..⑥切削加工:………….⑦零件测量检验:………(写清楚用什么量具,主要检验了哪些尺寸;一定要有零件加工完了的图片、加工误差分析!!!)⑧关机:………….⑨机床维护与卫生:……….Ⅱ:数控铣加工/加工中心(60×60×8,加工最多到4mm 深度)1、实习要求本实习以零件为例,在数控铣床上,用60X60X8的铝板加工出尺寸如图二所示的零件。
现代制造技术实训实习报告

现代制造技术实训实习报告一、前言随着科技的飞速发展,现代制造技术在工业生产中发挥着越来越重要的作用。
为了适应这一趋势,提高自己的实际操作能力和理论知识,我参加了为期两周的现代制造技术实训实习。
在这段时间里,我学到了很多关于现代制造技术的基本知识和操作技能,对制造业的发展有了更深入的了解。
二、实训内容实训期间,我们主要学习了数控编程、数控机床操作、模具设计、铸造、焊接、切割等现代制造技术。
以下是我在实训过程中所学到的几个方面:1. 数控编程:通过学习数控编程,我了解了数控机床的工作原理和编程方法。
学会了使用数控编程软件进行程序编写,掌握了G代码和M代码的使用,并能根据零件图进行编程。
2. 数控机床操作:在实训中,我学会了操作数控机床,熟悉了数控机床的各种功能和操作方法。
掌握了刀具补偿、对刀、编程零点设置等操作技巧。
3. 模具设计:通过学习模具设计,我了解了模具的结构和设计原理。
学会了使用模具设计软件进行模具设计,掌握了模具各部分的尺寸计算和形状设计。
4. 铸造:学习了铸造工艺的基本原理,了解了铸造过程中的熔炼、浇注、冷却等过程。
掌握了铸件的缺陷识别和修补方法。
5. 焊接:学习了焊接工艺的基本知识,了解了焊接过程中的焊接方法、焊接材料和焊接设备。
掌握了焊接技巧和焊接质量的判断方法。
6. 切割:学习了切割工艺的基本原理,了解了切割过程中的切割方法、切割设备和切割参数。
掌握了切割技巧和切割质量的判断方法。
三、实训收获通过这次实训,我对现代制造技术有了更深入的了解,提高了自己的实际操作能力和理论知识。
同时,我也学会了如何将理论知识与实际操作相结合,提高自己的实践能力。
以下是我在实训过程中的一些收获:1. 提高了自己的动手能力:在实训中,我参与了各种制造过程,掌握了各种制造工艺的操作方法,提高了自己的动手能力。
2. 培养了团队合作精神:在实训过程中,我们分组进行操作,学会了与他人合作,提高了团队协作能力。
3. 增强了自我管理和约束能力:在实训过程中,我需要遵守实训基地的规章制度,按时完成任务,养成了良好的自律习惯。
现代工程训练实习报告车间

实习报告一、实习背景及目的随着现代科技的飞速发展,工程领域对实践能力和创新精神的需求日益增强。
为了提高我们的综合素质,培养实际操作能力,学校安排了为期一个月的现代工程训练实习。
本次实习旨在让我们深入了解机械制造的一般过程,掌握电工技术与计算机组装维护的基本技能,提高工程意识和创新能力。
二、实习内容及过程实习期间,我们参观了现代化的车间,并分组进行了不同工种的训练。
以下是实习的主要内容:1. 机械加工:通过车削、铣削、钳工等实践操作,掌握了机械加工的基本技能,了解了各种机械设备的工作原理和操作方法。
2. 电工技术:学习了电工基础知识,掌握了照明电路的安装、维修,以及变压器、电动机等电气设备的基本原理和操作。
3. 计算机组装与维护:学习了计算机硬件的组装,熟悉了各部件的名称、功能和安装方法;掌握了操作系统和常用软件的安装与调试。
4. 现代制造技术:了解了数控车削、数控铣削等现代制造技术的基本原理和操作方法,学会了使用相关软件进行编程。
5. 安全生产:学习了安全生产的基本知识,了解了车间安全操作规程,提高了安全意识。
三、实习收获及体会1. 实践能力得到提高:通过实习,我们将理论知识与实际操作相结合,掌握了各种机械设备和工具的使用方法,实践能力得到了很大提高。
2. 团队协作意识增强:在实习过程中,我们分组进行实践,需要密切配合、协同完成任务。
这使得我们的团队协作意识得到了加强。
3. 安全意识提高:实习期间,我们学习了安全生产知识,了解了车间安全操作规程,安全意识得到了提高。
4. 对工程领域的认识加深:通过实习,我们了解了工程领域的工作内容和技术要求,为我们未来从事相关工作奠定了基础。
5. 创新能力和综合素质提高:在实习过程中,我们不仅要掌握基本技能,还要解决实际问题。
这使得我们的创新能力和综合素质得到了锻炼和提高。
四、实习总结通过本次现代工程训练实习,我们不仅掌握了机械加工、电工技术、计算机组装与维护等基本技能,还提高了实践能力、团队协作意识和安全意识。
- 1、下载文档前请自行甄别文档内容的完整性,平台不提供额外的编辑、内容补充、找答案等附加服务。
- 2、"仅部分预览"的文档,不可在线预览部分如存在完整性等问题,可反馈申请退款(可完整预览的文档不适用该条件!)。
- 3、如文档侵犯您的权益,请联系客服反馈,我们会尽快为您处理(人工客服工作时间:9:00-18:30)。
现代制造技术实习报告
————长沙理工大学2014年实习
学号:201021030526
一、实习目的
①、掌握机械制造设计方案和使用制图软件完成图纸绘制;
②、了解现代制造工艺中零件的加工过程和工作原理;
③、通过实习了解本专业在实际生产中专业课程知识的应用;
④、了解现代制造技术在实际生产中的应用。
二、实习内容
Ⅰ:数控车加工(Φ35×80)
1、实习要求
本实习以典型轴零件为例,在CY3600数控车机床上,用Φ35×100的铝棒加工出尺寸如图一所示的零件。
图一
2、数控加工工艺路线及工艺参数的设置
①根据图纸要求按照先主后次的加工顺序,确定如下工艺路线:
a粗加工,
b精加工
c切螺纹
d切槽,切断零件
②建立工件坐标系:以O点为编程原点,以零件轴径向为X轴,轴向为Z轴建立工件坐标系。
③选择刀具及换刀点:根据加工要求,选择3把刀:#1为外圆车刀、#2螺纹车刀、
#3切槽(切断刀)刀宽3毫米
为了避免换刀时刀具与机床、工件及夹具发生干涉现象,加工本零件时,换刀点选为(X40 ,Z150)
④分析该零件材料及型面结构,参考《实用机械加工工艺手册》,确定加工工艺参数如表1所示。
序号切削用量备注
S/(r/min) F/(mm/r) 1 加料棒外圆伸出长度约为66mm
500 100
2 粗车右端面等留加工余量单边
0.3mm
3 精车右端面,圆弧等达到图纸要
800 50
求
4 换二号刀切螺纹200 1.5
5 换三号刀切槽、切断200 50
6
7
8
9
表一
3、数控加工程序
00001
N010 G00 X40 Z150 S500 M03
N020 G00 X30 Z2
N030 T0101
N040 G01 Z-65 F100
N050 X40
N060 G00 Z2
N070 X26
N080 G01 Z-34
N090 G02 X26 Z-34 R1
N100 G01 X28 Z-35
N110 G00 X20
N120 Z2
N130 X24
N140 G01 Z-34
N150 G02 X24 Z-34 R2
N160 G01 X28 Z-36
N170 Z2
N180 G01 Z0 F50 S800
N190 X22
N200 X24 Z-1
N210 Z-34
N220 G02 X24 Z-34 R3
N230 G01 X30 Z-37
N240 G01 X30 Z-65
N250 G00 X40 Z150
N260 T0100
N270 T0202
N280 G00 X24 Z5 S200 M03
N290 G92 X23.2 Z-16.5 F1.5
N300 X22.8
N310 X22.6
N320 X22.5
N330 G00 X40 Z-16.5
N330 G00 X40 Z150
N340 T0200
N350 T0303
N360 G00 X30 Z-18.5 S250 M03
N370 G01 X20 F80
N380 X30
N390 G00 X40 Z-60
N400G01 X0
N410 G00 X40 Z150
M05
M02
4、实习操作步骤
①装夹工件:…………
②数控车床启动:………..
③输入零件数据加工程序:……….
④对刀及刀具偏置的设定:…………
⑤程序校验:…………..
⑥切削加工:………….
⑦零件测量检验:………(写清楚用什么量具,主要检验了哪些尺寸;一定要有零件加工完了的图片、加工误差分析!!!)
⑧关机:………….
⑨机床维护与卫生:……….
Ⅱ:数控铣加工/加工中心(60×60×8,加工最多到4mm 深度)
1、实习要求
本实习以零件为例,在数控铣床上,用60X60X8的铝板加工出尺寸如图二所示的零件。
图二
2、机床性能
数控铣床是在普通铣床上集成了数字控制系统,可以在程序代码的控制下较精确地进行铣削加工的机床。
3、加工工艺
切削外圆表面,外圆表面和凹圆。
内部两个半圆内槽
每次切削2mm分,两次切削
4、确定工件坐标系和对刀点
在XOY平面内确定以工件中心为工件原点,Z方向以工件表面为工件原点,建立工件坐标系,
采用手动对刀方法把点O作为对刀点。
5、数控加工程序
Ⅲ:数控电火花线切割加工(50×50×2)
1、实习要求
本实习以零件为例,在7725电火花数控线切割机床上,用50X50的薄铁片加工出尺寸如图三所示的零件。
图三
2、机床性能
数控电火花线切割机床包括机床﹑脉冲电源和数控装置三大部分。
脉冲电源是电火花线
切割加工的工作能源;数控装置是数控机床的核心,它接受输入装置送来的脉冲信号,经过数控装置的系统软件或逻辑电路进行编译、运算和逻辑处理后,输出各种信号和指令,控制机床的各个部分进行有序的动作。
3、加工原理
用细金属丝(钼丝)作工具电极,按预定的轨迹进行加工。
4、加工操作的过程
①在电脑上绘制出图形
②对图进行修改整合
③在加工选项中,读盘、调出此图、转换成G代码转加工
④装夹好工件
⑤打开切割机进行加工
5、加工程序。