汽车零部件电镀和涂装实验室 通用技术要求
3-电镀铬层技术条件

ICSQ/EQY电镀铬层技术条件东风汽车有限公司发布前言本标准根据GB/T1.1-2000《标准化工作导则第1部分:标准的结构和编写规则》首次制定了《电镀锌层技术条件》。
本标准自实施之日起,EQY-3-95《电镀层及化学处理层》第8.4节“镀铬层”停止执行。
本标准由东风汽车有限公司标准化委员会工艺材料标准化分委会提出。
本标准由东风汽车有限公司工艺研究所技术归口。
本标准起草单位:东风汽车有限公司工艺研究所。
本标准主要起草人:郝其勋。
电镀铬层技术条件1范围本标准规定了在铁基体材料上,在水溶性电解液中,用电解的方法获得的铬层。
本标准涉及的电镀铬层限定为耐磨用途的镀层,俗称“硬铬”。
本标准不涉及装饰性电镀中的铬层。
本标准适用于东风汽车有限公司产品开发部门设计的、东风汽车有限公司生产的各类汽车所使用的零部件及总成电镀铬层的质量控制和验收。
2规范性引用文件下列文件中的条款通过本标准的引用而成为本标准的条款。
凡是注日期的引用文件,其随后所有的修改单(不包括勘误的内容)或修订版均不适用于本标准,然而,鼓励根据本标准达成协议的各方研究是否可使用这些文件的最新版本。
凡是不注日期的引用文件,其最新版本适用于本标准。
GB4956—85磁性金属基体上非磁性覆盖层厚度测量磁性方法GB5270—85金属基体上金属覆盖层附着强度试验方法GB5934—86轻工产品金属镀层的硬度测试方法显微硬度法GB6462—86金属和氧化物覆盖层横断面厚度显微镜测量方法GB11379—89金属覆盖层工程用铬电镀层3术语3.1工作面在工件的某些表面上,其镀层对制件的外观和(或)使用性能起着重要作用。
图纸上指定镀铬的区域可以理解为工作面。
3.2厚度镀层厚度是指在工件的工作面上,凡是能与直径为20mm的球体相接触的部位上的镀层厚度的最小值。
4镀覆层的表示方法4.1通用镀覆表示方法基体材料/镀覆方法·镀覆名称·镀覆层厚度·镀覆层特征·后处理对于电镀铬可以是:基体材料/镀覆方法·镀覆名称·镀覆层厚度·后处理4.2后处理表示法AO表示松孔处理;Q表示除氢处理(允许在图纸上用文字说明替代符号Q)。
{技术规范标准}汽车件镀锌标准电镀锌层技术条件
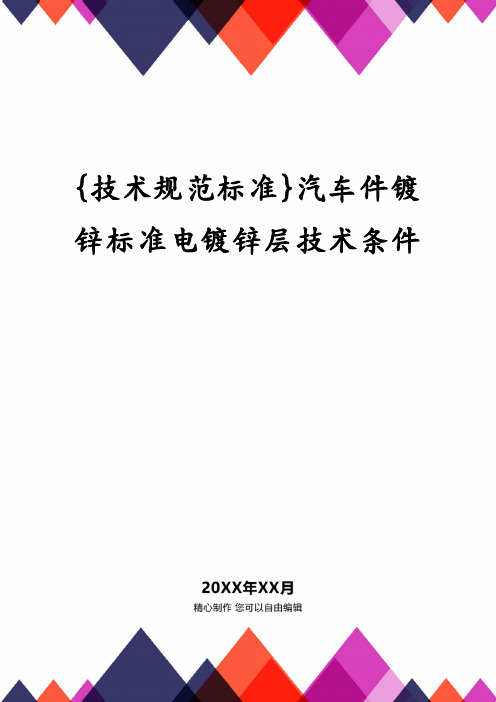
{技术规范标准}汽车件镀锌标准电镀锌层技术条件3.2厚度镀层厚度是指在工件的主要表面上,凡是能与直径为20mm的球体相接触的部位上的镀层厚度的最小值。
4镀覆层的表示方法4.1通用镀覆表示方法基体材料/镀覆方法·镀覆名称·镀覆层厚度·镀覆层特征·后处理对于电镀锌可以是:基体材料/镀覆方法·镀覆名称·镀覆层厚度·钝化膜类型·其它后处理4.2铁基体上电镀锌表示方法4.2.1完整的表示方法例如EP·Zn6CEQ其中EP表示电镀;Zn表示锌;6表示镀层厚度为6μm;C表示彩色钝化;E表示强化钝化;Q表示除氢处理(各种后处理标记见6.2节和6.3节)。
4.2.2省略的表示方法可以省略的内容是:表示螺纹件电镀的符号EP,表示彩色钝化的C,如果将镀层厚度省略则表示无耐蚀性要求,只需保证仓储期间不锈;不可以省略的内容是:表示强化钝化的E,表示去氢的Q(等价于在图纸上注明"去氢处理"),以及表示除彩色钝化外其它钝化的颜色符号。
5镀前零件的质量要求5.1待镀零件应无难于去除的油污、油漆、金属屑、严重锈蚀和氧化皮等。
5.2待镀零件应无毛刺、裂纹、磕碰伤、机械变形或其它机械损伤。
5.3热处理的零件,不允许严重脱碳,不允许带有高温烧结的污垢和锈蚀。
但允许有轻微的氧化色。
5.4焊接件应无多余的焊料和焊渣,焊缝应经喷砂或其它方法清理。
5.5带有复杂内腔的焊接件、铸件或液压成形件,应在不影响使用的部位留有便于液、气排出的工艺孔。
5.6不经机加工的铸件、锻件,其主要表面应进行喷丸或喷砂处理。
喷后不应有残留的砂粒或未除尽的氧化皮和涂料烧结物。
5.7经磨削加工的或探伤检查的零件应无剩磁、磁粉及荧光粉等。
5.8凡设计规定有配合要求的零部件,应留有镀覆层厚度的工艺尺寸。
5.9凡是金属和橡胶、金属和塑料、冷轧钢和未经清理的热轧钢、精加工件和毛坯件、铆焊件及其他特殊组件需要镀覆时,以本标准为依据,制定双方同意的技术验收规范。
《汽车外饰件用PVD涂层技术条件》编制说明

《汽车外饰件用PVD涂层技术条件》编制说明一、工作简况1.1任务来源《汽车外饰件用PVD涂层技术条件》团体标准是由中国汽车工程学会批准立项。
文件号中汽学函【2020】93号,任务号为2020-35。
本标准由中国汽车工程学会防腐蚀老化分会提出,宁波信泰机械有限公司、常州市武进晨光金属涂料有限公司、吉利集团、重庆长安汽车股份有限公司、奇瑞汽车股份有限公司、上海汽车集团股份有限公司、海南热带汽车试验有限公司、九熙(上海)检测技术有限公司、重庆大学、中国科学院兰州化学物理研究所、安伯来科学仪器有限公司、长城汽车股份有限公司、长沙松润新材料有限公司等单位起草。
1.2编制背景与目标现有外饰件的表面处理工艺主要是水电镀,涂装,阳极氧化。
其中水电镀工艺在使用过程中会产生强酸、强碱、重金属离子等无机物和有机溶剂,会严重污染土壤和水源,且该工艺无法满足透光、透波等功能性的外饰件要求。
因此急需一种可替代水电镀表面处理的工艺,既可以达到外饰件的性能要求,又能满足功能性需求。
PVD涂层工艺采用物理气相沉积方法,在工件表面形成一层均匀的金属膜,其抗腐蚀能力,耐磨损性,装饰效果,远远超过传统的表面处理工艺,已成为当今最先进的表面处理方式之一。
为了更好的推广PVD涂层在汽车外饰件上的应用,满足外饰件的服役寿命,我们认为有必要制定行业统一的“汽车外饰件用PVD涂层技术条件”。
这样有利于国内汽车企业相互竞争与对标,合作与提升,共同促进PVD涂层在汽车外饰件的推广应用。
1.3主要工作过程本标准于2018年7月开始标准学习;2019年3月到2020年5月份进行了标准相关的试验操作工作;2019年3月至8月进行了标准编写工作;2019年5月份至2020年7月份对标准进行了专家组讨论、修改及评议。
2020年10月底之前完成了标准的送审稿。
首先调研、收集并分析各主机厂的汽车外饰件用PVD涂层技术标准,结合实际汽车的使用工况,分析其参考价值。
涂装通用技术条件
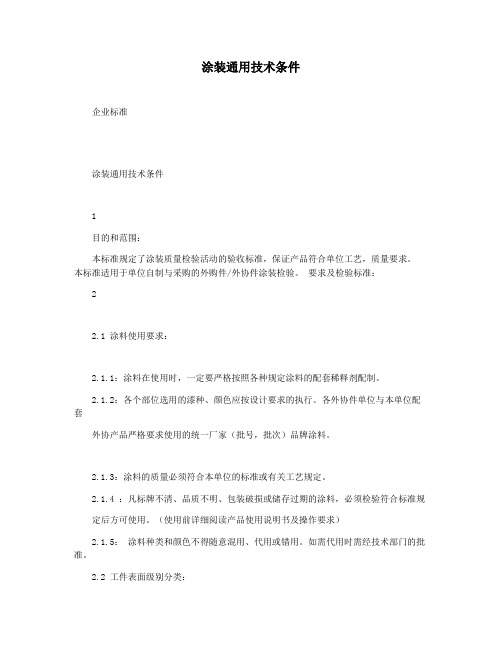
涂装通用技术条件企业标准涂装通用技术条件1目的和范围:本标准规定了涂装质量检验活动的验收标准,保证产品符合单位工艺,质量要求。
本标准适用于单位自制与采购的外购件/外协件涂装检验。
要求及检验标准:22.1 涂料使用要求:2.1.1:涂料在使用时,一定要严格按照各种规定涂料的配套稀释剂配制。
2.1.2:各个部位选用的漆种、颜色应按设计要求的执行。
各外协件单位与本单位配套外协产品严格要求使用的统一厂家(批号,批次)品牌涂料。
2.1.3:涂料的质量必须符合本单位的标准或有关工艺规定。
2.1.4 :凡标牌不清、品质不明、包装破损或储存过期的涂料,必须检验符合标准规定后方可使用。
(使用前详细阅读产品使用说明书及操作要求)2.1.5:涂料种类和颜色不得随意混用、代用或错用。
如需代用时需经技术部门的批准。
2.2 工件表面级别分类:2.2.1: A级表面:为零部件的主要表面。
主要以在距离1m的水平范围内环视,部件最显眼的正面来进行确定。
2.2.2: B级表面:为零部件的次表面。
2.1.2:B级表面主要以站在四周或驾驶室内环视,能一眼看到的部件表面(除A级表面外)来进行确定。
2.2.3 :C级表面:为零部件一般表面。
主要以封闭在整机内但在使用和检修时可以看到的地方,以及装成整机后看不到的地方来进行确定。
2.3 前处理2.3.1:所有部件表面在涂漆前应根据相应工艺或具体情况采用手工打磨、喷丸、除油、酸洗、磷化电泳等处理方法把影响涂漆质量的油污、铁锈、氧化皮、型砂、焊渣飞溅、锐边和灰尘等清除干净。
第 1 页共 6 页企业标准2.3.2:经喷丸处理的零部件,工件表面应达到Sa2.5级,即表面上所有的油脂、污垢、氧化皮锈、腐蚀物、旧漆和其它杂质被清除,允许存在由于清理不彻底而出现的阴影或色差,但至少要有95%的表面一致呈灰白色。
A和B级表面不得有残存氧化皮、型砂、锈迹、焊渣飞溅、锐边等,表面应呈金属本色;C级表面允许残留有不超过表面面积的10%的氧化皮和锈的痕迹,允许残留有少量的不松动的焊渣飞溅,但不得影响装配。
零件喷漆性能要求

零件喷漆性能要求1.范围1.1材料描述:这个标准包括实验室对喷漆的各种等级的检测要求,通常用于汽车零部件表面喷漆。
这个标准不包括表面要求和加工参数(不包括:3.1.1部分),而在材料规格(998XXXX)里面有规定,并且不包括电泳后用于连接真空堆积金属涂料和热处理涂料。
对电泳塑料件的化学成分,表面处理和喷漆都应该按照通用批准的零件表面处理要求(APOPS),当对电泳做测试的时候,至少要对3个样品进行检测,从每一个零件中获得不同的数据。
来自装配车间的初始和最终电泳零件必须能够接受规定的高层表面电泳要求和符合所有的检测要求和标准1.2特殊运用以下几个例子表明了一些过去使用的等级标准和现在使用的标准。
咨询你们的材料工程师,请求帮助指出适用的等级。
特殊运用等级如下:A336-xxx*. 通常用于汽车底盘&外观零件腐蚀,例如:没有电镀的冷扎钢,预涂层钢,压铸锌、铝、镁。
有时用在金属引擎零件上。
A96. 以前用于汽车外观的零件都在明亮的表面上喷漆就像不锈钢,阳极电镀的铝,镀铬金属或塑胶件。
但值得注意的是在明亮的表面上镀上去的漆通常不能保持太久,所以通过了A96的要求并不能保证满足这方面的性能要求。
因此,指定在明亮的底层镀漆是不可取的。
A0. 通常用在汽车外观的零件上,包括塑料件和其它非金属物质.C96-xxx*. 通常用在汽车尾部行李箱的一些可看得见的金属零件和一些暴露在潮湿空气中的零件.C24.通常用在汽车内部的不易暴露在潮湿空气中的金属件.C0.通常用在汽车内部的塑料件和其它非金属件.注:xxx*关于检验等级,在表格4里面有标明.1.3备注1.3.1这里的检验规范用于定期质量管理(第3部分)和电泳过程(第3部分和附录A).附加的检测要求必须在等级编码后面加Z后缀,并且附加的检测要求必须在技术图纸上或材料规格上说明.在表1里面进行举例说明.表格1:加“Z”字尾的例子1.3.2表格2描述了删减一些等级和他们当前应用的等级。
汽车用装饰性镍-铬和铜-镍-铬电镀层的技术条件(共4页)
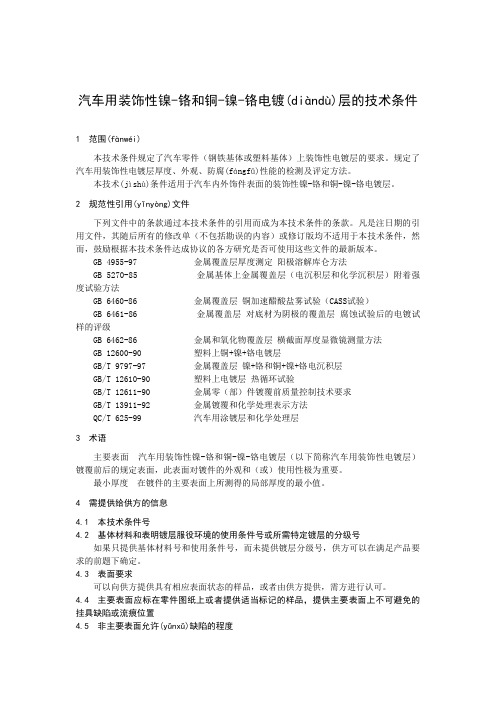
使用条件号
使用环境恶劣程度
事例
4
特别恶劣环境
汽车外部零件,如散热器格栅等
3
恶劣环境
汽车外部零件,如装饰条、天线等
2
一般环境
汽车内部零件,如座椅头枕支杆等
注:
装饰性电镀层分级号按GB 12600-90和QC/T 625-1999。钢铁基体与塑料基体的分级号见表2。
表2 装饰性电镀层的分级号
微裂纹可以不经预处理直接用100倍的金属显微镜以反射光或斜射光观察,如果有争议则要先用铜沉积法显示裂纹,微孔一定要用铜沉积预处理。铜沉积预处理的方法参见GB 9797的规定。
镀层的结合强度
按GB 5270-85的热震试验或磨、锯试验进行镀层结合强度的测定(或双方协商确定),经试验后,镀层与基体、镀层与镀层之间不应出现分离。
GB 4955-97 金属覆盖层厚度测定 阳极溶解库仑方法
GB 5270-85 金属基体上金属覆盖层(电沉积层和化学沉积层)附着强度试验方法
GB 6460-86 金属覆盖层 铜加速醋酸盐雾试验(CASS试验)
GB 6461-86 金属覆盖层 对底材为阴极的覆盖层 腐蚀试验后的电镀试样的评级
GB 6462-86 金属和氧化物覆盖层 横截面厚度显微镜测量方法
13
主要表面 汽车用装饰性镍-铬和铜-镍-铬电镀层(以下简称汽车用装饰性电镀层)镀覆前后的规定表面,此表面对镀件的外观和(或)使用性极为重要。
最小厚度 在镀件的主要表面上所测得的局部厚度的最小值。
14
本技术条件号
基体材料和表明镀层服役环境的使用条件号或所需特定镀层的分级号
如果只提供基体材料号和使用条件号,而未提供镀层分级号,供方可以在满足产品要求的前题下确定。
QBYDQ-A1906.4119-2013 电器件漆膜技术条件

2 规范性引用文件
下列文件对于本文件的应用是必不可少的。凡是注日期的引用文件,仅注日期的版本适用于本文件。 凡是不注日期的引用文件,其最新版本(包括所有的修改单)适用于本文件。
II
Q/BYDQ-A1906.4119—2013
电器件漆膜技术条件
1 范围
本标准规定了比亚迪汽车有限公司所有系列车用电器件,以塑料、金属件为基材的涂装件、移印件、 丝印件、电镀件以及水转印产品漆膜和涂层的技术要求、试验方法、检验规则、标志、包装、运输、贮 存,作为产品进厂检验依据或产品质量内控依据。
3 术语和定义
下列术语和定义适用于本标Байду номын сангаас。 3.1
以塑料、金属件为基材的涂装件、移印件、丝印件、电镀件以及水转印产品漆膜和涂层 以塑料、金属件为基材的涂装件、移印件、丝印件、水转印产品漆膜指产品涂装的漆层,包括底漆 层和面漆层、UV 漆、油墨。 3.2 电镀层 以塑料、金属件为基材的电镀件涂层指电镀层。
砂纸上面不停划圈以摩擦笔芯端面,直至获
得端面平整边缘锐利的铅芯时为止(边缘不
GB/T 得有破损及缺口);装在专用的铅笔硬度测
3 3.2 硬度
6739— 试仪上(施加在笔尖上的载荷为 750g,铅笔 -
2006
与水平面的夹角为 45°),推动铅笔向前滑
动约 5mm 长,共划 5 条(不同位置),再用橡
的材料及喷涂工艺需经产品供应商和原材料供应商双方认可,并经工程院批准;3.样板制备后, 在干燥通风、室温(23±2)℃条件下放置 7 天,方可用于试验
注:对于下列各表中的化学试验项目,如试验中无明确规定,漆膜样板的检查均在试验结束 4h 后立即进行。
《汽车零部件电镀和涂装实验室 通用技术要求》标准全文及编制说明
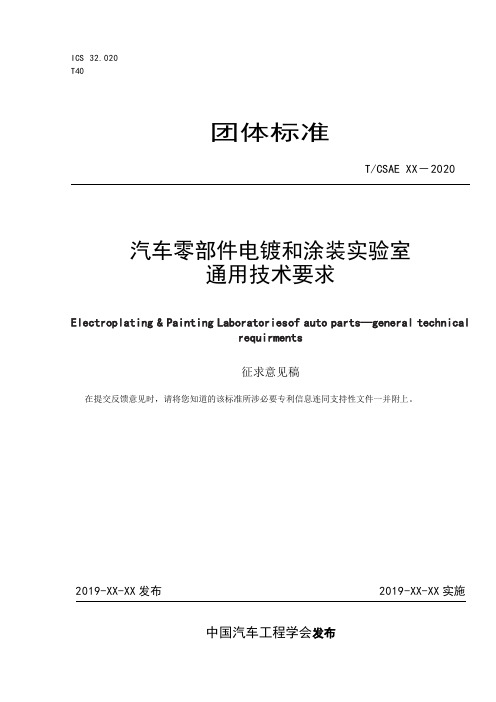
ICS 32.020T40团体标准T/CSAE XX-2020汽车零部件电镀和涂装实验室通用技术要求Electroplating & Painting Laboratoriesof auto parts—general technicalrequirments征求意见稿在提交反馈意见时,请将您知道的该标准所涉必要专利信息连同支持性文件一并附上。
目次前言 (I)1 范围 (2)2 规范性引用文件 (2)3 术语和定义 (2)4 电镀和涂装实验室设计 (2)4.1 电镀和涂装实验室设计基本要求 (2)4.2 电镀和涂装实验室设计特殊要求 (2)4.3 电镀和涂装实验室的分级.......................................................... .. (2)5 电镀和涂装实验室设施和设备要求 (3)5.1 设施和环境一般要求 (3)5.2 各级别电镀和涂装实验室设备要求 (3)6 电镀和涂装实验室分区 (3)6.1 EL-1级和PL-1级实验室分区 (3)6.2 EL-2级和PL-2级实验室分区 (4)6.3EL-3级和PL-3级实验室分区 (4)7 电镀和涂装实验室管理要求 (5)7.1 人员基本要求 (5)7.2 安全防护基本要求 (5)7.3 实验流程及样品基本要求 (6)7.4 实验数据溯源要求 (6)7.5 质量控制及体系要求 (7)7.6 设备管理及检校要求 (7)7.7 耐湿热性 (7)7.8 耐水性 (7)7.9 耐热性 (7)8电镀和涂装实验室废弃物质的处理 (7)8.1 废水处理 (5)8.2 废气处理 (5)8.3 废渣处理 (6)T/CSAE XX-2020前言本标准按照GB/T1.1-2009《标准化工作导则第1部分:标准的结构和编写》给出的规则起草。
请注意本文件的某些内容可能涉及专利,本文件的发布机构不承担识别这些专利的责任。
电镀件试验方法 通用技术要求及试验方法
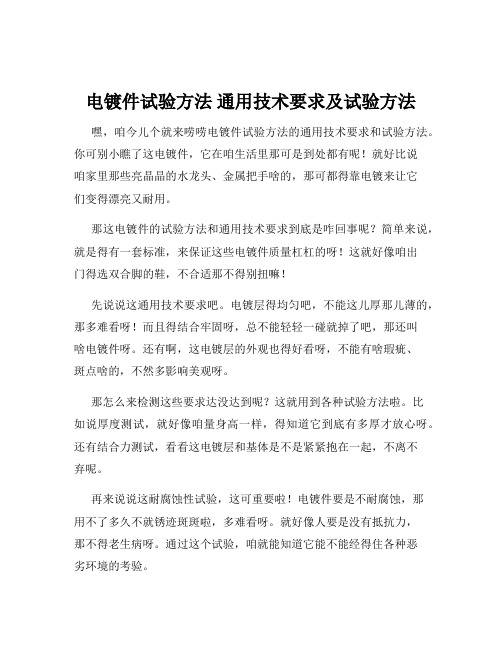
电镀件试验方法通用技术要求及试验方法嘿,咱今儿个就来唠唠电镀件试验方法的通用技术要求和试验方法。
你可别小瞧了这电镀件,它在咱生活里那可是到处都有呢!就好比说咱家里那些亮晶晶的水龙头、金属把手啥的,那可都得靠电镀来让它们变得漂亮又耐用。
那这电镀件的试验方法和通用技术要求到底是咋回事呢?简单来说,就是得有一套标准,来保证这些电镀件质量杠杠的呀!这就好像咱出门得选双合脚的鞋,不合适那不得别扭嘛!先说说这通用技术要求吧。
电镀层得均匀吧,不能这儿厚那儿薄的,那多难看呀!而且得结合牢固呀,总不能轻轻一碰就掉了吧,那还叫啥电镀件呀。
还有啊,这电镀层的外观也得好看呀,不能有啥瑕疵、斑点啥的,不然多影响美观呀。
那怎么来检测这些要求达没达到呢?这就用到各种试验方法啦。
比如说厚度测试,就好像咱量身高一样,得知道它到底有多厚才放心呀。
还有结合力测试,看看这电镀层和基体是不是紧紧抱在一起,不离不弃呢。
再来说说这耐腐蚀性试验,这可重要啦!电镀件要是不耐腐蚀,那用不了多久不就锈迹斑斑啦,多难看呀。
就好像人要是没有抵抗力,那不得老生病呀。
通过这个试验,咱就能知道它能不能经得住各种恶劣环境的考验。
还有硬度测试呢,这电镀件也不能太软了呀,不然稍微碰一下就变形了,那多尴尬呀。
这就跟人的骨头似的,得有一定硬度才能撑得住呀。
你想想,要是没有这些严格的试验方法和通用技术要求,那咱买到的电镀件说不定用不了几天就出问题啦,那多闹心呀!所以呀,这些可都是为了保证咱能用上质量好的电镀件呢。
咱再打个比方,这电镀件就像一个要上战场的士兵,这通用技术要求就是士兵的身体素质和技能要求,得样样过硬。
而这试验方法呢,就是各种考核,得通过这些考核才能证明自己是个合格的士兵呀。
总之呢,电镀件试验方法和通用技术要求那可真是太重要啦!咱在选。
汽车产品 零部件电镀铬层技术条件

三层
底层(s)
>8
中间层(高硫)(b)
—
<0.005 >0.15
≥60 —
≥50 10
面层(b)
—
>0.04 和<0.15
≤40
≤40
1) 伸长率的试验方法按GB/T 9798—1997 的附录B。 2) 规定镍层的含硫量(质量百分比)是为了说明所用镀镍溶液的种类。还没有简单的测量镍层含硫量的方法, 但 是按GB/T 9798—1997 的附录D规定的任何一种方法,采用专门制备的试样,可予精确测量。 3) 按GB/T 6462 的规定,制备镀层的横断面、抛光和浸蚀后,用显微镜测定和鉴别多层镍之间的厚度比和种类。
镀覆层厚度用阿拉伯数字表示,单位为μm。厚度数字标在镀覆层名称之后,该数值为镀覆层厚度 范围的下限,必要时,可以标注镀层厚度范围。 5.1.5 镀覆层特征
镀覆层特征表示符号见表 1。
2
Q/FT B019—2006
表 1 镀覆层特征表示符号
特征名称 光亮 半光亮
符号 b s
特征名称 暗 缎面
符号 m st
3 术语和定义
本标准所采用的定义见 Q/FT B018—2006 的 3.1~3.3。
4 电镀前零部件质量的规定
1
Q/FT B019—2006
零部件电镀前的质量应符合 Q/FT B018—2006 中第 4 章的有关规定。
5 镀铬层
5.1 零部件镀铬层的表示方法 零部件镀铬层按图 1 顺序组成一组符号表示。 □/□·□□□·□ 后处理 镀覆层特征 镀覆层厚度 镀覆层名称 镀覆层方法 基体材料 图 1 零部件镀铬层的表示方法
注:除非另有规定,本标准所规定的镀层的最小厚度要求只适用于能被直径为 20 mm 的球接触的主要表面部分。
电镀件试验要求

电镀件试验要求————————————————————————————————作者:————————————————————————————————日期:塑胶产品装饰性镀铬最低性能要求(14668有删减)电镀试验范围—参照标准---镀层要求1范围本规范涵盖了塑胶零件镀铜-镍-铬的基本要求,包含组装件。
作为公司开发新产品、检验产品质量以及试验产品性能的依据。
规定了汽车上使用的铜-镍-铬装饰电镀层的厚度、外观、结合强度、防腐性能等的检测及评定方法。
汽车零件塑料材料上起到装饰性和防腐蚀性作用1.1材料描述这个电镀标准旨在以下应用内饰件(代码A)。
内部应用不要求使用不连续铬层或多层镍体系。
不连续铬合金(r)可允许内部应用。
内部零件:是指在车身内部的,不会直接或间接地暴露在风雨中的零件。
类型1标准内部使用类型2需要较高涂层厚度的应用和/或类型1达不到性能要求,(例如可能需要类型2的门拉手,人工换档环或玻璃框)。
这些与包括的要求厚度都必须在图纸上说明。
注释:如果内部类型没有在详细的图纸上列出。
采取类型1。
外饰件(代码B)外部零件:是指除了内部零件外的零件。
那些只有部分暴露于气候中的零件称为外部零件。
对于外部应用,应该使用间断的铬板(多微孔(mp)或显微裂纹(mc)),另外还有多层镍体系。
类型1在汽车上很少或不会受到碎石撞击的;类型2会有明显的碎石撞击的。
包括固定在前面车辆区或固定在受自制石削影响的车辆区的电镀塑料零件的突出面(由车胎直线投影作用大于等于15度而定)。
类型3非常严重的服务条件(车轮覆盖和保护盖),包括石削塑胶电镀件的主要面装配于汽车面向前面的部分或那些会遭受汽车自身产生的碎石冲击的区域(定义为从轮胎发出成≥15度角直线撞击区域)。
如果详细图纸上没有标明类型,则默认是类型2。
1.2 典型应用。
这类涂层主要用于装饰目的。
光亮或其它(如:缎面、仿绒、木纹)外观的塑料内饰件或外饰件,由式样和特别外观标准来定义。
汽车涂装通用技术检测标准
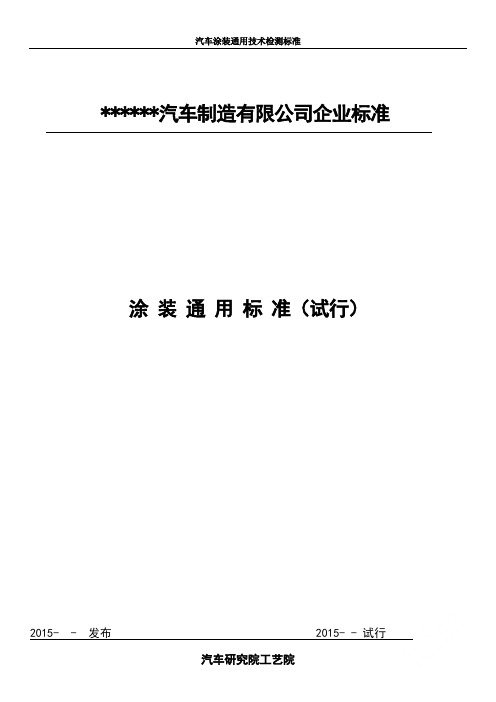
3.前翼子板各外表面。
包括引擎盖、车顶(距离车顶边缘200mm的区域)、侧围、前翼子板、前后门和尾门。车牌安装面和其它被遮盖的面除外。
可见度非常高
B
影响外观较明显的部位
B-S
车顶(距离车顶边缘≥200mm的区域)、保险杠顶部水平延伸一条虚线以下的所有可见外表面(车身外表面除A区、牌照安装面及其他遮盖面外)
1 范围………………………………………………………………………………………………………………………5
2引用标准…………………………………………………………………………………………………………………5
3 术语和定义………………………………………………………………………………………………………………6
4检验条件…………………………………………………………………………………………………………………6
高温处理后,再低温存放(-40±1)°C/24h后室温存放1小时,涂层无起泡、颜色变化,再测附着力0-1级;
见7.2.2.7
硬度(中华铅笔)
≥H
见7.2.2.8
附着力(2mm)
0-1级
见7.2.2.9
冲击强度
≥30㎏·cm
见7.2.2.10
杯突试验
≥4mm
见7.2.2.11
密封胶
硬度
56Hs~80Hs
本标准是设计产品、制定工艺文件、选定涂装材料及检验涂料涂层质量的技术依据。
2、引用标准
下列标准所包含的条文,通过在本标准中引用而构成本标准的条文。由于所有标准均存在被修订的可能性,所以使用本标准的各方应探讨使用最新版本标准的可能性。
GB/T1730-2007 漆膜硬度测定法 摆杆阻尼试验
EQY-3-86电镀层及化学处理层标准(doc 16页)

EQY-3-86电镀层及化学处理层标准(doc 16页)电镀层及化学处理层标准(EQY-3-95 代替EQY-3-86)1 主题内容与适用范围本标准规定了汽车零(部)件的电镀层和化学处理层的技术规范及膜层的质量要求。
本标准适用于汽车零(部)件的电镀层及化学处理层的质量控制和验收。
2 引用标准GB4956-85 磁性金属基体上非磁性覆盖层厚度测量-磁性方法GB5270-85 金属基体上金属覆盖层-附着强度试验方法GB6458-86 金属覆盖层-中性盐雾试验(NSS 试验)GB6460-86 金属覆盖层-铜加速醋酸盐雾试验(CASS试验)4.1 电镀表示方法基体材料/镀覆方法·镀覆名称·镀覆层厚度·镀复层特征·后处理4.2 化学处理表示方法基体材料/处理方法·处理特征·后处理(颜色)4.3 基体材料为钢铁材料时,其符号允许省略。
4.4 如果镀层或化学处理层的特征、厚度、颜色及后处理无具体要求时,其符号允许省略。
4.5 表示符号4.5.1 基体材料表示符号:金属材料用化学元素符号表示,合金材料用其主要成分的化学元素符号表示,非金属材料用国际通用缩写字母表示,如铜用Cu表示,塑料用PL表示。
4.5.2 镀覆方法和处理方法的表示符号见表1。
阳极氧化锰盐磷化锌盐磷化铬酸盐处理(白色)铬酸盐处理(彩色)铬酸盐处理(绿色)铬酸盐处理(黑色)铜及合金钝化AOMnPhZnPhBCGHP包括镀铬阳极松孔磷化无特定要求时只标注Ph磷化无特定要求时只标注Ph简称白钝化简称彩色钝化简称绿钝化简称黑钝化也用于银层钝化表示4.5.3 镀层厚度用阿拉伯数字表示,单位为μm。
4.6 如有特殊要求,应在镀层或化学处理层后面注明,如: EP·Zn15除氢处理5 电镀和化学处理层在产品图纸上的标注5.1 零(部)件所需的电镀层和化学处理层应作为"技术要求"在产品图纸上或有关技术文件中注明。
小件外委涂装技术条件

外委小件涂装技术条件本技术条件规定了海狮系列轻型客车外委小件电泳涂层、中漆涂层、面漆涂层涂膜技术条件、实验方法、涂层检测标准。
一、用语解释起泡:涂层表面呈现鼓包的现象。
针孔:涂膜表面呈现针状小孔或毛孔的现象。
起皱:漆膜表面呈现凹凸不平且无规则线状褶皱的现象。
桔皮:漆膜表面呈现桔皮状纹路的现象。
缺漆(露底):漏涂或未能完全覆盖前道涂层或材料色泽的现象。
遮盖不良:涂敷过薄或涂料遮盖力差致使底色隐约可见的现象。
脱落:涂膜从涂面呈现片状脱离的现象。
流痕(流漆):喷涂在垂直面上的涂料向下流动,使漆面产生条痕的现象,严重时称为流挂。
杂漆(发花):漆膜表面呈现不相溶的色点或块的现象。
颗粒:漆膜表面附着颗粒状物质的现象碰划伤:漆膜表面受外力碰伤而呈划痕的现象漆点:涂料由于分布不均匀,漆膜表面呈现圆滑凸起的现象。
线麻点:漆膜表面附着纤维丝毛状物质的现象。
锈痕:漆膜中产生锈点或接缝处呈现锈斑的现象。
二、电泳涂层技术条件电泳漆膜光滑、平整、连续,膜厚均匀,平均膜厚≥12μm(测厚仪—QuaNix7500 型),漆膜即要干透,又不要烘烤过度,造成漆膜泛黄。
漆膜干燥程度,用MIBK溶液擦拭法不掉色。
电泳漆膜耐盐雾时间≥720小时,按GB/T1171—91色漆和清漆耐中性盐雾性能的测定,(样板边缘封蜡,中间划叉,单侧扩蚀小于2mm)。
三、中漆涂层技术条件中漆漆膜喷涂要光滑、平整、连续,不允许漏涂、漏底、流挂。
漆膜干燥要均匀,不能过烘烤。
表面平均膜厚(20-30)μm(测厚仪—QuaNix7500型)。
四、面漆涂层技术条件1、外观要求:漆膜光滑、平整、连续,不允许漏涂、漏底、流挂、发花。
漆膜干燥均匀,不能过烘烤。
2、膜厚要求:本色面漆膜厚:(25-30)μm。
金属光泽漆膜厚:(12-18)μm。
罩光漆:(25-30)μm。
五、涂层外观质量检查标准1、不允许漆膜表面有缺漆、遮盖不良、起泡、针孔、起皱、脱落、流痕、杂漆、锈痕、麻点(凹陷)和碰划伤。
汽车零部件电镀和涂装实验室技术要求
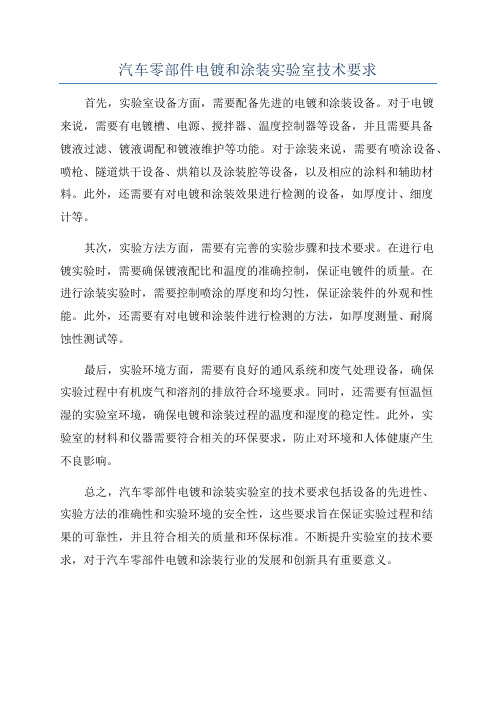
汽车零部件电镀和涂装实验室技术要求首先,实验室设备方面,需要配备先进的电镀和涂装设备。
对于电镀
来说,需要有电镀槽、电源、搅拌器、温度控制器等设备,并且需要具备
镀液过滤、镀液调配和镀液维护等功能。
对于涂装来说,需要有喷涂设备、喷枪、隧道烘干设备、烘箱以及涂装腔等设备,以及相应的涂料和辅助材料。
此外,还需要有对电镀和涂装效果进行检测的设备,如厚度计、细度
计等。
其次,实验方法方面,需要有完善的实验步骤和技术要求。
在进行电
镀实验时,需要确保镀液配比和温度的准确控制,保证电镀件的质量。
在
进行涂装实验时,需要控制喷涂的厚度和均匀性,保证涂装件的外观和性能。
此外,还需要有对电镀和涂装件进行检测的方法,如厚度测量、耐腐
蚀性测试等。
最后,实验环境方面,需要有良好的通风系统和废气处理设备,确保
实验过程中有机废气和溶剂的排放符合环境要求。
同时,还需要有恒温恒
湿的实验室环境,确保电镀和涂装过程的温度和湿度的稳定性。
此外,实
验室的材料和仪器需要符合相关的环保要求,防止对环境和人体健康产生
不良影响。
总之,汽车零部件电镀和涂装实验室的技术要求包括设备的先进性、
实验方法的准确性和实验环境的安全性,这些要求旨在保证实验过程和结
果的可靠性,并且符合相关的质量和环保标准。
不断提升实验室的技术要求,对于汽车零部件电镀和涂装行业的发展和创新具有重要意义。
汽车零部件油漆涂层技术规范
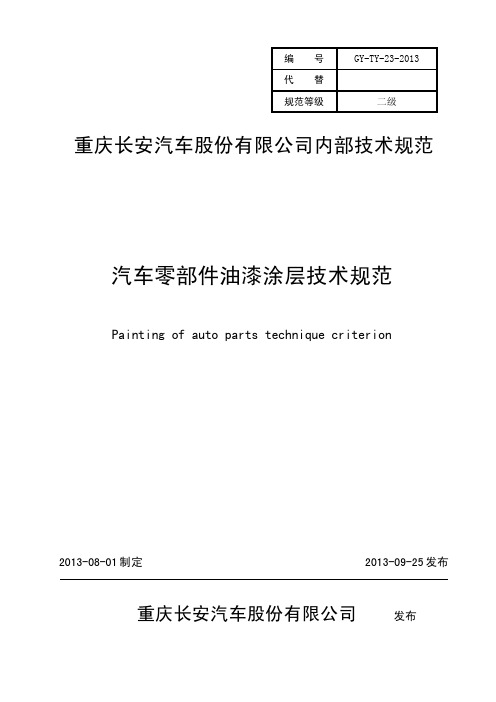
240h
备胎升降器 钢板弹簧
较 电泳漆≥20μm 恶 或喷塑≥40μm 劣 喷漆≥40μm
240h 144h
480h 240h
注: (1) (2) (3)
(4)
高防腐要求适用于市场定位和质量水平高的汽车,如:高级轿车、中高级 SUV、豪华商用车等。 转向节等铸铁件防腐技术难度大,防腐指标有所降低;铝车轮等安全件应提升其防腐指标。 电泳漆烘干温度≥160℃,喷塑烘干温度≥180℃,不耐温零件不适用,只能采用浸漆或喷漆。 喷塑一般采用静电粉末喷涂,受“静电屏蔽”影响,内腔件、复杂件不适用。 工作时,不被砂石撞击的零件,不进行抗石击试验;工作时,不接触水、机油、汽油的零件, 不进行耐水、耐机油、耐汽油试验。
7
6.2 涂覆工艺 6.2.1 油漆涂料应在保质期内,喷涂前调整涂液粘度是关键,应采用粘度计监测并记录。 6.2.2 采用电泳涂覆时,应监测电导率、电压、固体份、灰份、细度、库仑效率、泳透力等 工艺参数,并记录。 6.2.3 采用电泳涂覆时,必须配置超滤、过滤设备,槽液应搅拌均匀,不允许有结块、沉 淀等现象。 6.2.4 采用电泳涂覆时,必须配置纯水设备,配电泳漆槽以及电泳后的水洗(喷淋或浸洗), 必须采用干净的纯水。 6.2.5 采用喷塑时,应采用静电粉末喷涂,需控制装挂方式、喷涂时间、喷涂电压、喷粉 量、粉末导电率、粉末粒度、粉末和空气混合物的速度梯度等。 6.3 烘烤工艺 6.3.1 烘烤设备应具备预加热段、烘烤保温段、吹风冷却装置等。 6.3.2 烘烤温度和时间应严格控制,其直接影响着涂层的外观和附着力。 6.4 标准化作业 6.4.1 供应商应具备规范的半自动或自动涂覆生产线,2015 年 7 月 1 日起必须采用自动生 产线,作业安全规程符合 GB 6514 的规定。 6.4.2 油漆涂料应贮存在专用的库房,配备有防火等设备,库房的温度和湿度应满足要求。 6.4.3 除油、酸洗、抛丸、涂覆、烘烤等关键工序,应编制作业指导书,并做好操作记录。 6.4.4 除油、酸洗、抛丸、涂覆、烘烤等关重设备,应定期检修,并做好检修记录。 6.4.5 应具备规范的试验室,配备涂液分析仪器、涂层测厚仪、附着力测量仪、盐雾试验 箱等试验设备,试验之后做好相关记录。 6.4.6 鼓励供应商开展 ISO9001 质量体系认证。 6.5 环保控制 6.5.1 油漆涂层涂覆供应商应具备规范的废水、废气处理设施,不允许乱排放。 6.5.2 供应商应按 HJ/T 293 规定清洁涂覆生产,鼓励开展清洁生产审核,2015 年 7 月 1 日起必须具备该项要求。 6.6 涂覆供应商评价体系
最新qftb018零部件电镀层技术条件
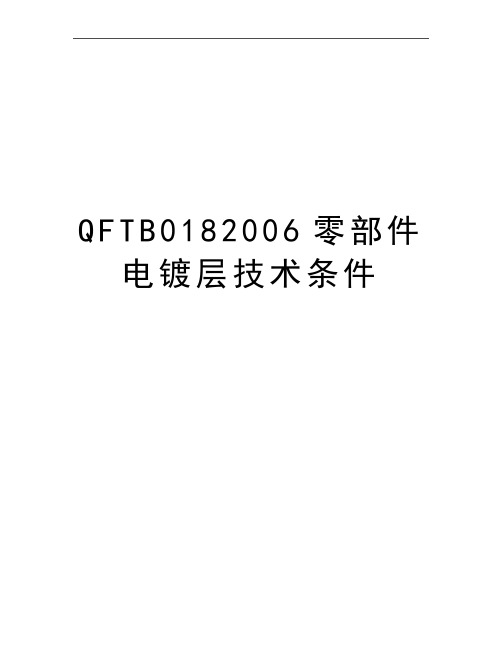
Q F T B0182006零部件电镀层技术条件精品好文档,推荐学习交流汽车产品零部件电镀锌层技术条件技术标准发布发放专用章分发有效分发日期:2006年08月13日仅供学习与交流,如有侵权请联系网站删除谢谢12目次前言 (Ⅱ)1范围 (1)2规范性引用文件 (1)3术语和定义 (1)4电镀前零部件质量的规定 (2)5镀锌层 (2)6对镀层的要求 (6)7自制螺纹紧固件镀层厚度的规定 (7)8提高抗腐蚀性的工艺措施 (8)9镀层性能试验方法 (9)10检验规则 (11)附录A(规范性附录)常用基体材料和镀覆方法符号 (12)前言本标准是根据有关国家标准、行业标准及福田公司的实际情况制定的。
为保证电镀锌零部件的质量,明确了镀层的性能要求、进货检验规则等内容。
同时兼顾产品定位的不同,对用于不同类别的产品提出了不同的要求。
本标准是对Q/FT B018-2000《车辆和农业装备零部件电镀锌层技术条件》的修订。
本标准与Q/FT B018-2000相比,有如下技术差异:——对本标准的适用范围进行了调整:不再包括农业装备,摩托车产品;——对规范性引用文件中的名称作了修订;对文件的格式作了调整;——在4.1中增加了“手指纹”一项,在4.6中增加了“酸洗处理”一项;——取消了热镀锌的相关要求。
本标准的附录A是规范性附录。
本标准由北汽福田汽车股份有限公司工程研究院提出并归口。
本标准起草单位:北汽福田汽车股份有限公司工程研究院产品管理部。
本标准主要起草人:靳宝生、李恒富。
本标准由北汽福田汽车股份有限公司工程研究院产品管理部负责解释。
本标准所代替标准的历次版本发布情况为:——Q/FT B018-2000。
汽车产品零部件电镀锌层技术条件1 范围本标准规定了汽车(含低速货车及运输型拖拉机),发动机产品零部件电镀锌层的镀层要求及表示方法、自制螺纹紧固件镀层的规定、提高抗腐性能的工艺措施、必须满足的质量指标、镀锌层性能检验方法及检验规则。
电镀国家标准.

中华人民共和国国家标准金属覆盖层钢铁制品热镀锌层技术要求Metallic coatings——Hot dip galvanized coatingson fabricated ferrous products—SpecificationGB/T 13912-92本标准参照采用国际标准 ISO 1459——1973(E)《金属覆盖层——热铰锌防腐蚀层——指导原则》和 ISO 1461——1973(E)《金属覆盖层——钢铁制品热镀锌层——技术条件》。
1 主题内容与适用范围本标准规定了钢铁制品上热镀锌层的技术要求。
本标准适用于钢铁制品防腐蚀的热镀锌层。
本标准不适用于未加工成形的钢铁线材、管材和板材上的热镀锌层。
本标准对热镀锌前基体材料的性质、表面状态不作规定。
影响热镀锌效果的基体材料状况参见附录A(参考件)。
本标准对热镀锌产品的后处理未作规定。
2 引用标准GB 2828 逐批检查计数抽样程序及抽样表(适用于连续批的检查)GB 4956 磁性金属基体上非磁性覆盖层厚度测量磁性方法GB 12334 金属和其他无机覆盖层关于厚度测量的定义和一般规则GB/T 13825 金属覆盖层黑色金属材料热镀锌层的质量测定称量法3 术语3.1热镀锌将钢件或铸件浸入熔融的锌液中在其表面形成锌—铁合金或锌和锌—铁合金覆盖层的工艺过程和方法。
3.2热镀锌层(简称:镀层)采用热镀锌方法所获得的锌—铁合金或锌和锌—铁合金覆盖层。
3.3主要表面指制件上热镀锌前和热镀锌后的某些表面。
该表面上的镀层对于制件的外观和(或)使用性能是起主要作用的。
3.4 检查批(简称:批)为实施抽样检查汇集起来的热镀锌件。
在热镀锌厂检验时,指一个生产班内同一镀槽中生产的相同类型和大小的热镀锌件。
交货后由需方检验时,指一次订货或一次交货量。
3.5 样本从批中随机抽取的镀件或镀件组。
3.6基本测量面在主要表面上进行规定次数测量的区域。
3.7局部厚度在基本测量面内进行规定次数厚度测量的算术平均值。
零部件镀铬技术条件

编制: 校对: 标准检查: 审定: 批准: 受控标识:镀铬技术条件1. 范围1.1 本标准规定了深铃车业有限公司无锡分公司电动车主要零部件镀铬前后的质量要求,电镀后的试验方法、检验规则。
1.2 本标准适用于深铃车业有限公司无锡分公司电动车金属和塑料零部件防护装饰性镀铬。
2. 规范性引用文件2.1 下列文件中的条款通过本标准的引用而成为本标准的条款。
凡是注日期的引用文件,其随后所有的修改单(不包括勘误的内容)或修订版均不适用于本标准,然而,鼓励根据本标准达成协议的各方研究是否可使用这些文件的最新版本。
凡是不注日期的引用文件,其最新版本适用于本标准。
2.2 GB/T 4955-1997 金属覆盖层覆盖层厚度测量阳极溶解库仑法2.3 GB/T 4956-2003 磁性基体上非磁性覆盖层覆盖层厚度测量磁性法2.4 GB/T 5270-1985 金属基体上的金属覆盖层(电沉积层和化学层沉积层)附着强度试验方法2.5 GB/T 6461-2002 金属基体上的金属和其它无机覆盖层经腐蚀试验后的试样和试样的评级2.6 GB/T 10125-1997 人造气氛腐蚀试验盐雾试验2.7 GB/T 13911-1992 金属镀覆和化学处理表示方法3. 电镀件外观类别及镀层体系表示方法3.1 电镀件外观类别A类对成车自然观察十分容易看见,装饰价值很高的部位。
包括:方向把管、后货架、保险杠、前照灯、转向灯、后视镜、仪表、装饰件、减震器、刹把等零部件主视面。
B类对成车自然观察容易看见,装饰价值较a级稍低的部位。
包括:标牌、平叉护板装饰件等零部件。
C类对成车自然观察不容易看见,装饰价值低或无装饰价值的零部件。
3.2 镀层体系分类及表示方法3.2.1常用镀层的种类及简化表示的含义见表1。
表13. 零部件电镀前的质量要求3.1 金属零件电镀前的质量要求3.1.1 有配合公差要求的零件,应留有适当的加工余量。
3.1.2 零件表面不允许有经电镀前处理和进行抛磨都无法除去的缺陷,如明显的凹坑,难以抛磨掉的腐蚀点,砂轮打磨伤痕及模具拉伤痕迹等。
- 1、下载文档前请自行甄别文档内容的完整性,平台不提供额外的编辑、内容补充、找答案等附加服务。
- 2、"仅部分预览"的文档,不可在线预览部分如存在完整性等问题,可反馈申请退款(可完整预览的文档不适用该条件!)。
- 3、如文档侵犯您的权益,请联系客服反馈,我们会尽快为您处理(人工客服工作时间:9:00-18:30)。
汽车零部件电镀和涂装实验室通用技术要求1 范围本标准规定了电镀和涂装实验室的设计、设施、设备、人员、操作、管理的基本要求。
本标准适用于汽车零部件电镀和涂装实验室。
2 规范性引用文件下列文件对于本文件的应用是必不可少的。
凡是注日期的引用文件,仅注日期的版本适用于本文件。
凡是不注日期的引用文件,其最新版本(包括所有的修改单)适用于本文件。
GB / T 32146.1 检验检测实验室设计与建设技术要求第1部分:通用要求ISO / IEC 17025 实验室管理体系检测和校准实验室能力的一般要求3 术语和定义无4 电镀和涂装实验室设计电镀和涂装实验室设计除需考虑GB / T 32146.1-2015的第7章外,还应考虑本部分4.1、4.2的要求。
4.1 电镀和涂装实验室设计基本要求4.1.1 电镀和涂装实验室的设计宜以安全、环保、智能为前提,以满足实验室主要功能及特殊要求为原则,合理规划实验室布局,宜对电镀和涂装实验室的不同检测区域进行功能划分。
4.1.2 不同功能的检测区域应是分隔独立的工作室,并有明显的标志,各区域间不能互通,有效避免交叉污染。
4.1.3 对环境有要求的精密检测设备应设置专用实验室单独摆放,同时保证实验室内的温、湿度及空气洁净度满足设备要求。
4.1.4 精密检测设备实验室应与涉及腐蚀性及挥发性物质的实验室(如腐蚀实验室、滴定检测实验室等)相互隔离。
4.1.5有毒、有害、易挥发、有刺激性气味物质的实验操作应配备通风橱或在操作点设置局部排风设备。
4.1.6 涉及化学品操作的实验室,应布置紧急洗眼器、紧急淋浴器等安全装置。
4.2 电镀和涂装实验室设计特殊要求对于有中试线的电镀和涂装实验室,中试线的设计、建造、生产及排放要求应与正规生产线保持一致。
4.3 电镀和涂装实验室的分级4.3.1 电镀实验室分级根据电镀厂规模和镀种的不同,电镀实验室宜分为大型(EL-1级)、中型(EL-2级)、小型(EL-3级)三个级别,详见表1。
4.3.2 涂装实验室分级根据涂装厂规模和涂层种类的不同,涂装实验室宜分为大型(PL-1)、中型(PL-2)、小型(PL-3)三个级别,详见表2。
5 电镀和涂装实验室设施和设备要求5.1 设施和环境一般要求电镀和涂装实验室用于检测的实验设施,应有利于检测的正确实施。
实验室应确保环境条件不会使结果无效,或对所要求的测量质量产生不良影响。
在实验室以外的场所取样、检测时应予以特别注意。
5.2 各级别电镀和涂装实验室设备要求5.2.1 各级别电镀实验室设备要求见表3。
5.2.2 各级别涂装实验室设备要求见表4。
表4各级涂装实验室设备要求电导率仪√○○原子吸收光谱仪(AAS)√○○pH计√√√电泳装置√√○喷枪√○○泳透力测定装置√○○烘箱√○○电阻仪√○○注:√代表必须配备;○代表视涂镀层种类或检测需求选择性配备。
6 电镀和涂装实验室分区6.1 EL-1级和PL-1级实验室分区EL-1级和PL-1级实验室须具备完整的功能分区,各功能分区应完全独立分隔,各分区的分布应合理规划,避免检验过程中出现交叉作业造成样品污损或人员受伤。
实验室典型布局图见图1。
说明:1——业务接待区;11——实验样品留存区;2——办公区;12——设备室;3——资料存档区;13——物理检测实验1区;4——更衣室;14——物理检测实验2区;5——样品接收登记区;15——物理检测实验3区;6——样品制备区;16——光谱分析区;7——化学检测实验1区;17——试制区;8——化学检测实验2区;18——废弃物处理区;9——腐蚀实验区;19——紧急喷淋区;10——实验耗材存放区;20——洗涤区。
注:样品沿箭头方向流动进入检测区。
图1. EL-1级和PL-1级实验室典型布局图6.2 EL-2级和PL-2级实验室分区EL-2级和PL-2级实验室须具备基本的功能分区,各功能分区应完全独立分隔,各分区的分布应合理规划,避免检验过程中出现交叉作业造成样品污损或人员受伤。
实验室典型布局图见图2。
说明:1——物理检测收样制备区;8——NSS雾实验箱;2——物理检测操作区;9——CASS雾实验箱(视实际需求配置);3——实验耗材存放区;10——实验耗材存放区;4——资料存档区;11——物理检测实验区;5——化学检测收样制备区;12——化学检测实验区;6——化学检测操作区;13——腐蚀实验区7——实验耗材存放区注:样品沿箭头方向流动进入检测区。
图2. EL-2级和PL-2级实验室典型布局图6.3 EL-3级和PL-3级实验室分区EL-3级和PL-3级实验室无独立分区要求,但各功能区域应明确划分,并合理规划,避免检验过程中出现交叉作业造成样品污损或人员受伤。
实验室典型布局图见图3。
说明:1——化学检测收样制备区;5——物理检测操作区;2——化学检测操作区;6——资料存档区;3——实验耗材存放区;7——NSS/CASS盐雾箱(视实际需求配置)。
4——物理检测收样制备区;注:样品沿箭头方向流动进入检测区。
图3. EL-3级和PL-3级实验室典型布局图7 电镀和涂装实验室管理要求7.1 人员基本要求7.1.1 实验室管理者和操作人员应具备或熟悉相关专业知识和标准,能够熟练操作实验仪器。
7.1.2 实验室管理者应制定实验室人员的培训计划,按期组织人员培训,并对培训效果进行有效评价。
7.1.3 实验室使用临时工作人员时,应确保其能够胜任工作。
7.1.4 实验人员应保持高度的责任心和安全意识,严守实验室规章制度。
7.2 安全防护基本要求7.2.1 实验室须按国家的规定和要求配备消防灭火设备和安全通道,定期检查消防灭火装置的有效性,定期组织人员学习消防知识并组织演练。
7.2.2实验室电力配置须满足实验室用电需求,电路布局合理,有接地保护需求的实验设备须接地保护。
精密仪器需配置稳压稳流装置。
7.2.3 实验室应保证良好的通风环境,按需配置通风设备。
7.2.4 有毒、有害、腐蚀性危险实验物料需按规定存放、使用及报废,以防对人员和环境产生危害。
7.2.5 实验室应为实验人员提供必要的劳保防护用品。
7.2.6 实验室安全负责人应制定年度安全计划,安全计划应经过管理层的审核与批准。
7.2.7 实验室管理层应负责实施安全检查,每年应至少根据管理体系的要求系统性地检查一次,对关键控制点可根据风险评估报告适当增加检查频率,以确保实验室各系统状态正常运转。
7.3 实验流程及样品要求7.3.1实验流程实验的工作流程为:实验室样品到样验收(确定是否具备检验的基本条件)→样品制备(待检状态)→样品提取→实验检测→结果判定→出具报告。
7.3.2 样品要求液态样品应储存在耐腐蚀且密封良好的容器中,确保样品不会与容器发生反应;样品的提取应有专人负责,确保样品不会在送检前被污染;不能接收从其他检验、检测等分出来的样品,以避免样品间交叉污染。
固态样品应独立包装,避免样品间直接接触;对于需要切削才能获得的样品,需保证端面无毛刺、锐边。
7.4 实验数据溯源要求为确保所有检测和/或校准结果或标准的量值能够最终溯源到国家基准或国际计量基准,对实验室来说一般需要对实验仪器、参考标准及标准物质进行数据溯源,以确保检测和/或校准结果准确可靠。
实验室应配置专门的数据管理设施,还需要专人管理、整理及归档实验数据。
通常实验数据应保存至少五年。
7.5质量控制及体系要求实验室应建立内部质量控制程序, 以确保并证明检测过程受控以及检测结果的准确性和可靠性, 取得数据的记录方式应便于可发现其趋势。
7.5.1 质量控制要求实验室质量控制通常按照人、机、料、法、环五个质量控制因素分别制定计划并严格实施,见表5。
7.5.2 质量体系要求明确质量形成过程和过程的各个阶段可能影响检测报告质量的各项因素。
从而对这些因素采取相应的措施,加以管理和控制,使其过程处于受控状态,以保证最终检测报告的质量。
为使质量管理体系能有效的运行,应配备适应工作需要的各类人员和物质资源。
质量管理体系的运行是通过贯彻实施程序文件实现的,程序文件是规定检测活动和检测过程的途径,制定程序文件应做到全面、适用、可操作。
7.6设备管理及检校要求7.6.1 设备管理要求实验室应有对设施设备(包含个体防护劳保装备)管理的政策和程序,包括设施设备的完好性监控指标、巡检计划、实验前检查、安全操作、使用限制、定期校准等。
设施设备应由经过授权的人员进行操作和维护。
建立实验设备档案,对于主要仪器设备,应以一台一档的方式,实施动态管理,及时补充相关信息和资料内容。
同类的小型实验器具(如测厚仪)可建立一个档案,分类存放管理。
注:设备档案应至少包括以下内容:a) 设备名称、型号、制造厂商、购置日期、验收记录、责任人、放置地点、目前状态(在用、停用、报废);b) 说明书,若是外文说明书应有使用方法及校准部分的中文译文;c) 仪器检定、校准或校验情况记录;仪器检定、校准或校验情况记录;d) 仪器设备使用记录、核查记录、仪器设备损坏、故障、维修记录、仪器设备维护保养记录、报废纪录。
7.6.2 设备检校要求实验室根据检测工作的实际需要制定仪器设备校验计划,设备在使用前应进行校准或核查,以确保能够满足实验室的规范要求。
实验室应采用满足客户需求并适用于所进行的校准方法,应优先使用国际、区域或者国家标准发布的方法,还应确保使用的标准是最新的有效的版本。
8电镀和涂装实验室废弃物质的处理8.18.28.3对于有毒、有害的固废,宜在实验室专设的处理装置中集中处理或者外包由第三方公司处理,严禁埋入地下,污染地面水体。
其他固废可按照国家相关规定进行处理。