武钢1580mm热连轧带钢厂
轧钢主设备

由于连铸机改变连铸板坯宽度的能力较小,不能满足热轧带钢轧机的各种宽度规格,由粗轧机的立辊根据热轧带钢轧机需要的各种宽度规格的板坯宽度进行控制。热轧带钢轧机发展了立辊轧机,定宽压力机等形式的板坯宽度侧压设备。
5、精轧机组
精轧机组是成品轧机,布置在粗轧机组中间辊道或热卷箱的后面,是带钢热连轧线的核心设备。精轧是决定产品质量的主要工序,带钢的力学性能主要取决于精轧机终轧温度和卷取温度。
2国内的情况
1978年12月投产的武汉钢铁公司1700mm热连轧机计算机系统,是我国引进的第一套带钢热连轧计算机控制系统热带轧机。1989年宝钢2050mm热连轧机的建成投产,使我国热轧宽带钢轧机的生产技术和技术装备又上了一个新的高度。
3带钢热连轧生产工艺流程
原料准备→称重→加热→除鳞→定宽→粗轧→(调头尾)→保温(补热)→剪头尾→除鳞→精轧→层流冷却→卷取→热轧卷(检查、打捆、喷印、包装) →平整→热轧卷→精整→纵切→窄带钢→横切→钢板→酸洗→酸洗卷
四我国热连轧带钢生产采用的先进技术与特色技术
目前国内的热轧宽带钢轧机约有4类,其特色分别如下:
1传统热轧宽带钢轧机
(1)连铸坯热装和直接热装。该技术要求炼钢和连铸机稳定生产无缺陷板坯;热轧车间最好和连铸机直接连接,以缩短传送时间;在输送辊道上加设保温罩及在板坯库中设保温坑;板坯库中要具有相应的热防护措施,以保证板坯温度。应设有定宽压力机,减少板坯宽度种类。加热炉采用长行程装料机,以便于冷坯与热坯交换时可将高温坯装入炉内深处,缩短加热时间。精轧机后2机架采用轧辊轴向串动技术,以增加同宽度带钢轧制量。采用连铸、炼钢、轧钢生产计划的计算机一体化管理系统,以保证物流匹配。
第3阶段,这个阶段实际上是近1~2年开始的,是以提高效益、调整品种结构、满足市场需要和提高企业竞争能力为目的的发展阶段。由于近年国家经济快速发展,对钢材需求不断增加,因此除国营大中型企业外,中小型企业,甚至民营企业都把生产宽带钢作为今后发展的重点,或引进或采用国产技术,或建设传统热连轧宽带钢轧机或建设薄板坯连铸连轧生产线。这个阶段以鞍钢1700mm、2150mm(国产),唐钢1780mm薄板坯和1700mm(国产)、马钢1700mm薄板坯和2250mm、涟钢1700mm薄板坯、莱钢1500mm(国产)、本钢薄板坯、济钢1700mm(国产)、新丰1700mm(国产)、宝钢1800mm、首钢2250mm、武钢2250mm、太钢2250mm轧机为代表。同时,这个阶段对引进的二手轧机和原技术较落后的国产轧机进行了全面技术改造,使其达到了现代化水平。
年产200万吨1580热轧带钢生产线设计_毕业设计说明书
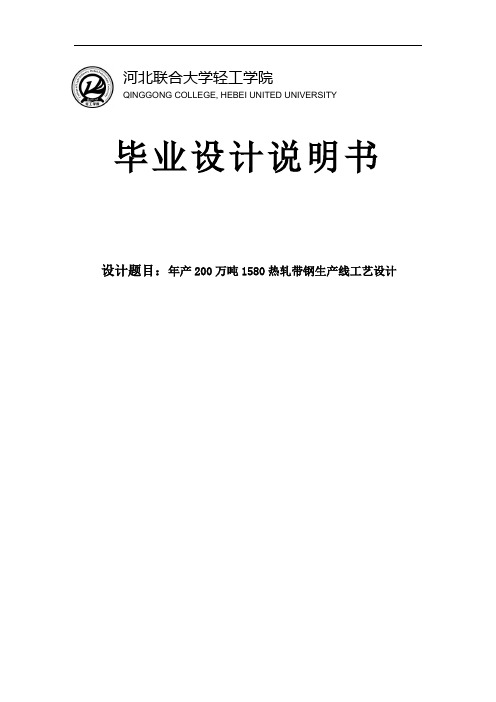
QINGGONG COLLEGE, HEBEI UNITED UNIVERSITY毕业设计说明书设计题目:年产200万吨1580热轧带钢生产线工艺设计摘要本设计任务为年产200万吨热带连轧车间,选择250mm厚坯,双粗轧可逆布置。
产品范围1.5~18mm,典型产品5mm。
产品要求品种广泛,质量优良。
设计内容包括建厂依据,原料选择,轧机数量、形式、能力选择,轧制规程计算,轧制图表,年产量计算,凸度规程计算,电机发热校核,轧辊强度校核,辅助设备校核,金属平衡、燃料消耗计算。
为了能生产高质量的汽车板用热卷,轧制时对中间坯的厚度、凸度、表面光洁度都有较高要求,对温度有更严格的制度。
粗轧机配置CVC,控制凸度,严格控制中间坯凸度,也提高粗轧压下量。
采取辊道边部加热、层流边部遮挡,保证热卷产品残余应力较小。
采用新型板凸度仪,高效处理凸度信息,实现凸度、平直度自动控制,做到表面光洁,尺寸精度高,为后续冷轧提供合格带卷。
所设计热轧厂装备有高效的带钢轧制自学习模型和调节系统,从而使带钢厚度、板形、宽度、终轧和卷取温度的控制精度极高。
能够使产品达到设计产量和品种质量的要求,满足市场需求。
关键字1580热轧带钢;厚板坯;粗轧CVC轧机;汽车板用热卷IAbstractDesigned to complete the design of the task book requirements (more than 2.0 million tons annual output of varieties of tropical plant and rolling). Choice of 250mm thick billet, dual rough layout reversible binding. Product range 1.5 ~ 18mm. Typical Product 5mm.Wide varieties of product requirements, good quality.The basis of content, including plant design, rolling a point of order, the crown of order, the rolling charts, annual production, the crown of order, the electrical heating calibration, intensity calibration roll, check auxiliary equipment, metal balance, fuel consumption calculation.In order to produce high quality hot rolled plate with the car, rolling on the piece thickness, convexity, surface finish requirements are high, the temperature more stringent system. Take roll edge heating, laminar flow edge block, to ensure thermal residual stress in a small volume products. Instrument using the new crown, high crown of information processing to achieve crown, flatness control, so that smooth surface, size and high precision cold-rolled to provide qualified for the follow-up coil.New plant is equipped with hot-rolled strip steel rolling technology and highly efficient model and conditioning systems, so that the strip thickness, flatness, width, end-rolling coiling temperature control and high accuracy. Enable the production of products to meet the design requirements of the quality and variety to meet market demand.Keywords1580 hot rolling mill, double reversible roughing, CVC rolling, strip for carII目录摘要 (I)Abstract (I)引言 (1)第1章文献概述 (2)1.1热轧宽带钢轧机工艺装备的新发展 (2)1.2发展中的问题 (5)第2章建厂依据及产品大纲 (6)2.1建厂依据 (6)2.2产品大纲 (6)2.2.1 坯料规格和技术参数 (7)2.2.2 产品钢种和分类 (7)第3章轧机的比较与选择 (9)3.1 车间布置及设备选用的原则 (9)3.2 轧机的确定与选择 (9)3.2.1 轧机数量的选择 (9)3.2.2 粗轧机形式的选择 (10)3.2.3 精轧机机组的选择 (11)3.2.4精轧板型控制方式选择 (16)第4章典型产品的压下规程设计 (17)4.1 坯料尺寸 (17)4.2粗精轧机组压下量分配 (17)4.3确定速度制度 (20)4.3.1粗轧速度制度的确定 (20)4.3.2精轧速度制度的确定 (21)4.3.3精轧机组轧制延续时间 (22)4.4确定轧制温度制度 (22)4.4.1 粗轧各道次温度确定 (23)4.4.2 精轧各道次温度确定 (24)4.5转速的计算 (24)III河北联合大学轻工学院IV4.5.1前滑值的计算 (24)4.5.2轧辊转速的计算 (26)4.6各机架的空载辊缝值得设定 (27)4.7轧制力矩的计算 (28)4.7.1附加摩擦力矩m M (29)4.7.2空转力矩Mk (31)4.7.3动力矩的计算 (33)第5章 轧制图表与年产量计算 (34)5.1轧制图表的基本形式及其特征 (34)5.1.1单机座可逆式轧机的工作图表 (34)5.1.2连续式轧机的工作图表 (35)5.1.3本次设计轧制图表 (36)5.2 轧钢机的产量计算 (36)5.2.1轧钢机年产量的计算 (37)5.2.2轧钢机平均小时产量的计算 (37)5.2.3轧钢车间年产量的计算 (38)第6章 轧辊强度的校核与电机能力验算 (40)6.1轧辊的强度校核 (40)6.2支撑辊弯曲强度 (40)6.3工作辊扭转强度校核 (42)6.4工作辊与支撑辊的接触应力校核 (45)6.5电机的校核 .............................................................................................. - 48 -6.6主电机的功率计算 (51)第7章 辊型的凸度计算 (53)7.1出口板带凸度计算 (53)7.2热凸度计算 (54)7.3轧制力挠度的计算 (55)7.4 CVC 凸度的计算 (57)第8章 辅助设备的选择 (59)8.1加热炉的选择 (59)8.2除鳞设备的选择 (60)8.3辊道的选择 (62)8.4剪切设备的选择 (64)8.5冷却设备的选择 (65)8.6卷取机的选择 (65)8.7活套支撑器 (67)8.8热卷箱的选择 (67)8.9板坯宽度侧压设备 (69)第9章金属平衡与其他消耗 (72)9.1金属平衡 (72)9.2其他消耗 (73)第10章轧钢车间平面布置及经济技术指标 (74)10.1轧钢车间平面布置 (74)10.1.1 轧钢车间平面布置的原则 (74)10.1.2 金属流程线的确定 (75)10.2 车间技术经济指标 (76)10.2.1 各类材料消耗指标 (76)10.2.2 综合技术经济指标 (79)总结 (82)参考文献 (83)致谢 (1)V引言近几年来我国集中建设了一大批宽带钢热轧机,数量之多,建设速度之快,不仅在我国,在全世界也是空前的。
北京首钢 热轧产品手册说明书

热轧产品手册HOT ROLLED PRODUCTS MANUAL北京首钢股份有限公司B e i j i n g S h o u g a n gC o.,L t d.Chapter 1 Hot rolled products第一章 热轧产品Chapter 2 Product introduction第二章 产品介绍首钢热轧产品以迁安、京唐两个基地为依托,在首钢技术研究院及技术中心支撑下,积累了丰富的热轧生产、技术及品质管理经验,热轧产品具有稳定可靠、产品尺寸精度高、板形控制良好等诸多特点,产品质量广受用户认可,具有良好的市场美誉度。
首钢股份公司有二条2250热连轧生产线,二条1580热连轧生产线以及一条1600MCCR 产线,实现热轧板卷厚度规格0.80-25.4mm,宽度800-2050mm 尺寸的全覆盖。
以首钢热轧产品品种结构为拓展轴,结合两基地热连轧机组和 MCCR 产线热轧品种生产能力,热轧产品主要供应汽车结构、工程机械用钢、管线钢、耐候钢、特殊钢、冷轧基料、专用钢及普通结构钢等众多行业领域。
Shougang hot-rolled products rely on two main iron and steel bases of Qian'an company and Jingtang company. Plenty of experience in production, technology and quality management was accumulated under the support of Technology Institute of Shougang Group and Technology Center of Shougang Group. The hot-rolledproducts of Shougang are feathered with reliable properties and quality, high dimension accuracy, excellent flatness and therefore gained good market reputation.Shougang mainly has two 2250 hot rolling production lines, two 1580 hot rolling production lines and one 1600MCCR production line, realizing the full coverage of hot rolling sheet coil thickness specification 0.80-25.4mmand width 800-2050mm.Based on the hot-rolled products structure and production ability of hot-rolling mills in two bases and MCCRline, Shougang supply various hot-rolled products, such as automobile structure steel,Steel for construction machinery,pipeline steel, weathering steel, special steel, steel for cold rolling and specialized-purpose steel.2.1 汽车结构钢(Automobile structural steel)首钢紧抓商用车节能环保和轻量化的发展趋势,开发适用于商用车全系零件的材料,依托强大的用户服务能力,为客户提供了商用车轻量化整体解决方案,实现了大梁钢、车轮钢、桥壳用钢及厢板用钢等四大系列的整车钢材供应能力,得到市场的充分认可,逐步由产品跟随发展走向市场引领位置。
热卷箱
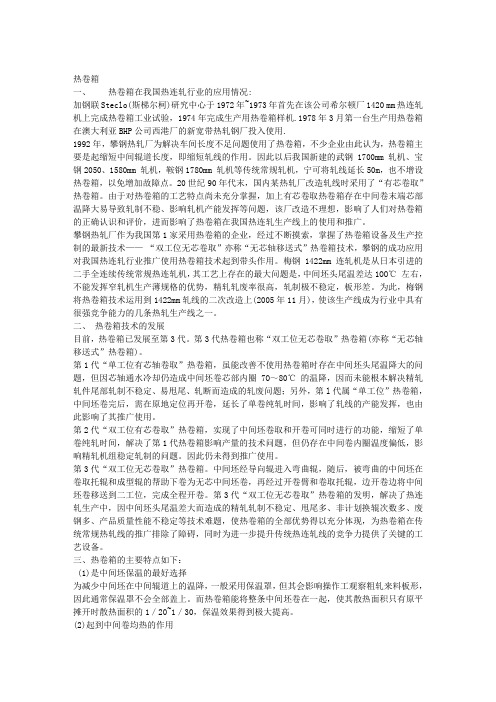
热卷箱一、热卷箱在我国热连轧行业的应用情况:加钢联Steclo(斯梯尔柯)研究中心于1972年~1973年首先在该公司希尔顿厂1420 mm热连轧机上完成热卷箱工业试验,1974年完成生产用热卷箱样机.1978年3月第一台生产用热卷箱在澳大利亚BHP公司西港厂的新宽带热轧钢厂投入使用.1992年,攀钢热轧厂为解决车间长度不足问题使用了热卷箱,不少企业由此认为,热卷箱主要是起缩短中间辊道长度,即缩短轧线的作用。
因此以后我国新建的武钢1700mm 轧机、宝钢2050、1580mm 轧机,鞍钢1780mm 轧机等传统常规轧机,宁可将轧线延长50m,也不增设热卷箱,以免增加故障点。
20世纪90年代末,国内某热轧厂改造轧线时采用了“有芯卷取”热卷箱。
由于对热卷箱的工艺特点尚未充分掌握,加上有芯卷取热卷箱存在中间卷末端芯部温降大易导致轧制不稳、影响轧机产能发挥等问题,该厂改造不理想,影响了人们对热卷箱的正确认识和评价,进而影响了热卷箱在我国热连轧生产线上的使用和推广。
攀钢热轧厂作为我国第1家采用热卷箱的企业,经过不断摸索,掌握了热卷箱设备及生产控制的最新技术——“双工位无芯卷取”亦称“无芯轴移送式”热卷箱技术,攀钢的成功应用对我国热连轧行业推广使用热卷箱技术起到带头作用。
梅钢1422mm 连轧机是从日本引进的二手全连续传统常规热连轧机,其工艺上存在的最大问题是,中间坯头尾温差达1OO℃左右,不能发挥窄轧机生产薄规格的优势,精轧轧废率很高,轧制极不稳定,板形差。
为此,梅钢将热卷箱技术运用到1422mm轧线的二次改造上(2005年11月),使该生产线成为行业中具有很强竞争能力的几条热轧生产线之一。
二、热卷箱技术的发展目前,热卷箱已发展至第3代。
第3代热卷箱也称“双工位无芯卷取”热卷箱(亦称“无芯轴移送式”热卷箱)。
第1代“单工位有芯轴卷取”热卷箱,虽能改善不使用热卷箱时存在中间坯头尾温降大的问题,但因芯轴通水冷却仍造成中间坯卷芯部内圈7O~80℃的温降,因而未能根本解决精轧轧件尾部轧制不稳定、易甩尾、轧断而造成的轧废问题;另外,第l代属“单工位”热卷箱,中间坯卷完后,需在原地定位再开卷,延长了单卷纯轧时间,影响了轧线的产能发挥,也由此影响了其推广使用。
1580mm热轧生产线工程
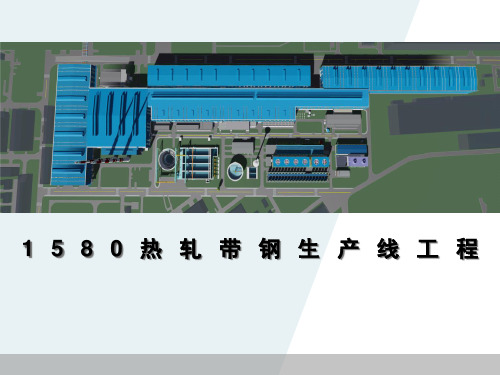
生产线图片资料----主轧线子项 ❖ 主轧线地上部分
生产线图片资料----主轧线子项
❖ 主轧线地上部分
生产线图片资料----主轧线子项 ❖ 主轧线地上部分
生产线图片资料----主轧线子项
❖ 主轧线地下部分
生产线图片资料----主轧线子项 ❖ 隐藏了地面的主轧线
生产线图片资料----主轧线子项
生产线图片资料----板坯库子项
❖ Inventor设计的板坯运输线长达530米。
生产线图片资料----板坯库子项
❖ Inventor设计的板坯运输线长达530米。
生产线图片资料----板坯库子项
生产线图片资料--加热炉子项 ❖ 隐藏了建筑的加热炉子项模型
生产线图片资料--加热炉子项 ❖ 外购设备模型被简化
Inventor机械设计节选
Inventor与Revit协同
❖ 机械设备与管线、建筑、结构的协同。
特点3: 超大型轧钢工艺全流程生产线
❖ 1580热轧项目是一个超大型、全专业、完整的BIM协同设计项目 ,从设计到投产历时2年,投入多达81人的BIM设计团队,共完成 188套BIM施工图、2807张A1、513份材料表。本项目按生产工艺 流程分为8个子项:板坯库、加热炉、主轧线、磨辊间、成品库、 水处理系统、外部综合管线、辅助设施。下面按1580热轧项目的 工艺流程展示一些图片资料。
BIM策划 协同平台 标准建立 应用支持
15个专业 81位设计师 188套BIM施 工图
2807张A1 513份材料表
专业负责人
项目策划 专业协同 三维设计评审 优化设计 现场施工指导
将传统设计策划与BIM策划融合
❖ BIM经理在设计经理策划的基础上进行BIM策划,采用策划 表的形式将模型等级、信息等级、协同方式等信息与套图一 一对应,方便执行、验收。
武钢第二热轧带钢厂工艺设备特点

? 工艺方案
? @ > 生产规模 一期工程生产热轧钢卷 ( / ,其中供 / " 万? E 热平整 分 卷 轧 卷 % ,供 横 切 机 组 热 轧 卷 % ( 万? ,热轧商品卷$ ,送一热轧厂热轧 ’ ’万? " "万? 卷! ,最终规模为年产热轧卷’ 。 ! % , (万? / "万? ? @ ? 产品品种及规格 板坯、产品品种及规格见表$ 。
, , F @ C C ? @ F 6 7 4 A 4 @ G : ) @ 7 ? F 4 7 J : G < E ? : 4 7E 7 L) E : 7@ G : ) @ 7 ? @ < J 4 < ) E 7 F @ @ ? F , * 6 @I < 4 L G F ? C 4 J ? 6 @) : A AH : A A C G A ? 6 @I < 4 L G F M 8 N 9 I 8 9 I I I I N ? : 4 78 E J ? 6 @ ! " " " ) )E 7 L4 O @ <H : L @ C ? < : J 4 G < F 4 G 7 ? < , I4 I4 N
! " # $ % & & ’ ( ( +% ’ / % ( 0 $ 1 * " * $ 0 % " ’ & 0 ’ $ & # 2 0 1 %( % 34 # 0 5 0 " ’ 6 * ( 0 # 27 1 * (8 " # ( )* , . .! * ( +5 0 % % 69 # / * ( . :
0 1 . 2 +3 4 (5 ,5 ,5 ) 6 4 7 : 7 ; < 4 7=> ? @ @ AB @ C : 7= D @ C @ E < F 6 ; 7 C ? : ? G ? @ 6 4 7 : 7 " " " $ ( 6 : 7 E 8 9 8 8 8 9 8’
“热连轧超薄超高强带钢智能轧制技术开发及应用”项目获得2018年冶金科学技术三等奖

பைடு நூலகம்
本 项 目属 于 板 带 轧 制 技 术 与 自 动 化 交 叉 的 科 学 技 术 领 域 。 批 量 、稳 定 、低 成 本 地 生 产 高 性 能 钢 铁 材 料 是 钢 铁 制 造 技 术 发 展 的重 要 方 向 ,是 实现 绿 色 钢 铁 的必然 选 择 。 本项 目攻 克 了热 连 轧 超 薄 规 格 高 强 钢 的智 能 化 轧 制关 键技 术 ,实 现 了极 限规格 、极 限 性 能 (厚 度 1.2 mm、屈 服 强 度 700 MPa级 )产 品 的 大 批 量 稳 定 生 产 ,使 梅 钢 1780热 轧 高 强薄 规格 产 品轧制 比例在 传统 热连 轧线 巾稳居 国内外 同行前 列 ,厚 度 ≤2.0 mm的带 钢 比 例从 单 月8%增 加 至 21%,/J,H ̄产 量在 同类 产线 中稳 居前 列 ,年 均 经 济效益 8 01 1万元 ; 申请 发 明专  ̄1J26件 ,获 得 软件 著作 权5项 ;发 表 核心 期 刊论 文60余 篇 ,其 中SCI/EI收 录 39篇 。项 目在 智 能化 轧 制 模 型 与稳 定 性 控 制 、轧 机 没备 精 度诊 断 、轧 机 振荡 防治 等 技 术 领 域 进 行 了重 点 突破 ,增 强 了梅 钢热 轧 产 品 的竞 争 能 力 盈 利 能力 ,推 动 了钢 铁行 业 的 绿 色 转 型 ,支撑 了 国 家节 能减 排 战 略 ,对 内外 热 连 轧 机 组 的 升级 改 造 和 新 建项 目具 有 重要 示 范 和推 广 价值 。
“热连 轧超薄 超 高强带 钢 智能 轧制 技术 开发 及应 用’’项 目 获 得2018年 冶 金科学 技术三 等奖
上 海 梅 山 钢 铁股 份 有 限公 司 与武 汉 科 技 大学 合 作 申报 的 “热 连 轧 超 薄 超 高 强带 钢 智 能轧 制 技 术 开 发 及 应 用 ” 项 目获 得 20 1 8年 中 国钢铁 一I 业 协 会 、 中 国金 属 学 会 冶 金科 学 技 术 三 等 奖 。
宝钢热轧厂介绍

DIN 17155-83 HⅡ
19Mn6
EN10028-2: 1992
P265GH
P355GH
GB713-1997 GB6654-1996
20g/20R
19Mng/16MnR
Q/BQB320-2003 SB410
JIS G3103-1987 SB410
焊接气瓶用
产品牌号对照表
Q/BQB 321-2003 B440HP B490HP
S235JR
GB 912-89/GB 3274-88
Q195,Q215A, Q215B
Q235B
S235J0 S275JR E295 S355J0
Q235C
Q255B
Q275,Q345A
Q345C,Q390B, Q390C
结构用
产品牌号对照表
Q/BQB303-2003 DIN17102-80
GB 912-89 EU113-72 EN10113-2:1993 GB 3274-88
2050热轧简介
• 成品钢板卷: 宽度:600-1900mm 厚度:1.5-25.4mm 钢板长度:2000-12000mm 钢卷内径:760 钢卷外径:2150 mm
2050热轧简介
材质类别
低碳钢
结构钢板 汽车结构 钢板
特点
普通钢
冲压钢
深冲压钢
保证力学性能 (强度、伸长 率、冲击韧性 汽车专用结构 钢,在保证结 构钢材料的基
1580热轧简介
• 成品钢卷: 宽度:700-1430mm 厚度:1.5-12.7mm 钢卷内径:762mm 钢卷外径:1000-2150mm
1580热轧简介
• 1580的产品及用途: 热轧低碳钢:SPHC、SPHD、SPHE 一般结构钢:SS330、SS400、SS490、SS540 焊接机构用钢:SM400A、SM400B、SM400C、 SM490A、SM490B、SM490C等 钢管用带钢:SPHT1、SPHT2、SPHT3 机械结构用钢:S20C、S35C 汽车结构用钢:SAPH310-SAPH440 集装箱用钢:B480GNQR
武钢生产线

武钢四条热轧生产线设备及产品情况调查2009年02月13日星期五下午 6:361700mm生产线1700mm热轧机于1974年9月破土动工,1978年12月12日一次试轧成功。
它的整套轧机设备从日本引进,配套电气设备从德国和比利时引进,当时具有国际先进水平;整个生产流程由4台电子计算机分为两级进行控制,计算机的控制功能分为跟踪、轧制节奏、设定计算机程序控制、质量控制、数据处理、操作指导等6个方面。
生产的带钢产品厚度为1.2~12.7mm,主要品种有普、优碳素钢,低合金钢和硅钢的板、卷、带材,年设计生产能力为301万t。
1978年12月20日至1979年9月20日,热轧厂在9个月时间内完成了轧制线、1号横切线、2号横切线、3号横切线、纵切线、平整线、板坯修磨机、磨辊间和水处理等9个区进行设备功能和生产能力考核,均一次达到或超过设计指标。
从1700mm生产线投产至今,热连轧生产技术不断地进行着引进、消化、吸收和创新的工作:l 研制开发了自产钢数学模型等生产技术,较好解决了投产初期自产钢坯生产中的问题;l 开发了适合冷轧用钢卷的生产技术,有效减少了热轧工序的带钢表面裂纹;l 1979年2月22日取向硅钢试轧成功,其磁性达到GO的最高牌号G9,比国产的D310高11个级别;l 1994年出色完成主轧线计算机控制系统的改造,为新产品的开发、新工艺的应用及有关技术改造提供了广阔的计算机功能平台,热轧材的宽度、厚度、FT7、CT4项精度命中率由85%提升至95%以上;l 1997年引进法国克莱西姆公司技术,对精轧F4~F7轧机进行改造,带钢凸度超标比由原来的33.9%下降到13.84%,平坦度超过7I单位的比例由原来的19.3%下降到6.9%,年生产2.0mm以下集装箱用钢达2万t以上,超过原设计能力;l 1993-1995年,对卷取机进行系统改造,使故障率下降50%、废钢量减少70%以上,产品规格由原设计厚度不超过12.7mm扩展至16mm,品种增加至管线钢X80级别;l 1998-2000年,分别对精轧电气、卷取电气主干实施改造,及G辊道变频改造,取得显著效果,故障率直降90%;l 研制出带钢钢板矫直机全自位辊系,使矫直机在任何工况条件下工作辊各个环节都具有自动位置调整功能,是国内首次实现的具有全自位功能的矫直机,具有国际先进水平;等等。
热轧知识交流

(二)粗轧机的布置形式
2、 3∕4连续式粗轧机由可逆式轧机和不 可逆式轧机组成,其布置形式有2架轧机, 3架轧机或4架轧机。
(二)粗轧机的布置形式
典型的3∕4连续式粗轧机由4架轧机组成,第1架为 二辊可逆式轧机,第2架为四辊可逆式轧机。第3、 4架均为四辊不可逆式轧机。3∕4连续式粗轧机的 轧制工艺是:板坯在可逆式轧机上往复轧制3~5 道次,在不可逆式轧机上轧制l道次。3∕4连续式粗 轧机兼有全连续式粗轧机的优点,又克服了它的 缺点,与其相比具有生产线短、占地面积小、设 备少、投资省、对板坯厚度范围的适应性好等优 点。且生产能力也不低,适应于多品种的热轧带 钢生产。我国热轧宽带钢粗轧机采用3∕4连续式布 置的有宝钢2050mm、武钢1700mm、太钢 1549mm
(一)热连轧带钢轧机布置形式
6、正在开发的生产热带钢的技术是薄带直接连铸 并轧制的技术,钢水在2 个辊中铸成5~6mm的带钢, 经过1架或2架轧机进行小变形的轧制和平整,生产 出热带钢卷。欧洲、日本和澳大利亚都进行过类 似的试验,2004年美国NUCOR建立了工业试验厂, 德国的THYSSEN-KRUPP也建立了相同的试验工厂, 据介绍年产50万t的带钢厂已经试验成功,但是关于 生产的稳定性、成本、产品质量、产品范围和应 用领域的进一步报道尚未见到
近年材质不断更新,有些厂家试用半高速钢取 得了较好效果。
(四)粗轧四辊轧机工作辊
ห้องสมุดไป่ตู้
半钢辊合金含量不高、硬度较低,耐磨性、抗热 裂性一般,随轧机轧制硬材比率增大,耐磨性限 制轧辊换辊周期问题显现,有时出现热裂深、浅 层掉肉等问题,因此已逐步被高合金复合轧辊取 代。
半钢轧辊整体铸造,无结合层、强度高,一般不 会出现剥落、断辊等恶劣轧制事故,因此新上轧 机、轧制稳定性差轧机仍应首选。
日照钢铁1580mm热轧带钢工程要点

日照钢铁1580mm热轧带钢工程要点简介热轧带钢是一种优质的钢铁材料,具有均匀性好、硬度高、韧性强等特点,广泛应用于建筑、船舶、机械制造等领域。
日照钢铁是我国知名的钢铁生产企业之一,该企业的1580mm热轧带钢工程具有重要的意义。
本文主要介绍日照钢铁1580mm热轧带钢工程的要点,以及该工程在钢铁生产中的应用。
工艺流程该工程的热轧带钢工艺流程如下:原材料→ 炉前处理→ 热轧→ 等温退火→ 冷却→ 水冷却→ 矫直→ 切割→ 产成品其中,热轧过程是该工程中最为关键的环节之一。
在热轧过程中,必须严格控制温度、轧制力度、轧制速度等参数,确保热轧带钢的质量稳定。
在等温退火和冷却过程中,也需要对温度、时间等参数进行控制,以达到想要的材料性能。
关键设备该工程中,涉及到的一些关键设备包括:热轧机组热轧机组是热轧带钢工程中最为核心的设备之一。
该机组包括轧机、三辊送料机、辊道、辊床等部分。
轧机是热轧机组的主要设备,用于实现热轧带钢的轧制。
三辊送料机用于将原材料送入轧机中,完成初轧。
辊道和辊床则用于支撑轧机和原材料,保证其稳定性。
等温退火炉等温退火炉是该工程中必不可少的设备之一。
该设备的主要作用是对热轧带钢进行退火处理,使其具有更好的韧性和延展性。
等温退火炉采用局部加热和整体均热的退火方式,通过对温度、时间等参数的精准控制,实现对热轧带钢的优化处理。
冷却设备冷却设备主要包括自然冷却和快速冷却两种方式。
自然冷却是指将热轧带钢置于室温下自然冷却,该方式适用于对材料硬度、强度等方面要求不高的情况。
快速冷却则是通过水冷却等方式将热轧带钢迅速降温,使其具有更好的硬度和强度。
冷却设备的选择需要根据热轧带钢的具体要求而定。
质量控制热轧带钢的质量控制是钢铁生产中的一个重要环节。
在日照钢铁1580mm热轧带钢工程中,质量控制包括原材料的筛选、热轧过程的控制、等温退火、冷却处理等方面。
工厂通过建立完善的质量管理体系,持续改进生产工艺和技术,确保产品质量稳定。
宝钢1580热轧PC精轧机复合铸造辊的研制

宝钢1580热轧PC精轧机复合铸造辊的研制沈一鸣摘要:宝钢1580热轧厂PC精轧热连轧机组原使用日本3家公司的轧辊,经宝钢与邢台轧辊股份公司联合研制,成功地试制出1套14支3个品种的PC工作辊,其技术参数和使用性能达到国外同类产品先进水平。
关键词:PC轧机;工作辊;研制The development of casting composite roll for PC finishing mill of1580mm hot rolling mills in Baoshan Iron and Steel CompanySHEN Yi-ming( Production Dept., Baoshan Iron & Steel (Group) Co., Shanghai 202100, China )Abstract: The rolls of PC finishing mill of 1580mm hot rolling mills in Baosteel were manufactured by Japan. But by developed, three kinds of and total 14 rolls were successfully made by Baosteel and Xingtai Roll Co. The technique parameters and application index of the rolls are the same to the former.Keywords: PC mill; work roll; development1 前言宝钢1580热轧厂年产热卷280万t,产品厚1.5~12.7mm,宽700~1430mm,其中板厚小在于3mm的占77%。
要紧设备中,PC精轧机组是我国从日本引进的第1套当代先进的板形操纵轧机。
该轧机配备的一组超细长复合铸造精轧工作辊系列,由于国内不能制造,因此开工初期全部配套辊和部分周转辊均由日本引进。
关于热轧1580mm国内生产能力的调研
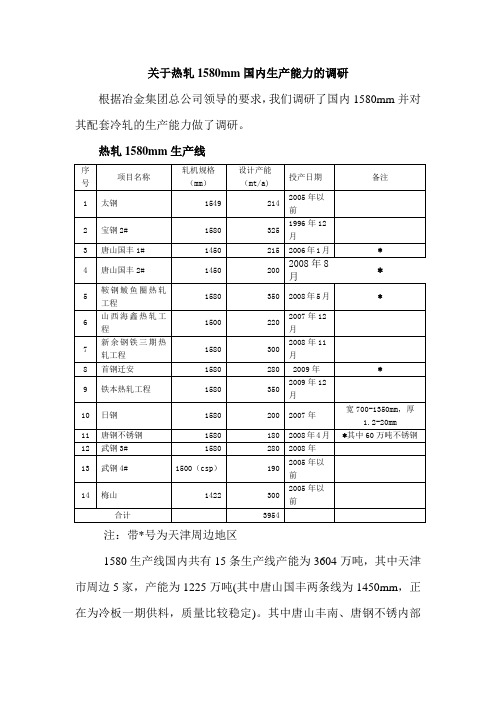
关于热轧1580mm国内生产能力的调研
根据冶金集团总公司领导的要求,我们调研了国内1580mm并对其配套冷轧的生产能力做了调研。
热轧1580mm生产线
注:带*号为天津周边地区
1580生产线国内共有15条生产线产能为3604万吨,其中天津市周边5家,产能为1225万吨(其中唐山国丰两条线为1450mm,正在为冷板一期供料,质量比较稳定)。
其中唐山丰南、唐钢不锈内部
为冷轧配套。
根据上述情况,我轧一集团冷板二期工程原料供应可选范围为以下几家钢厂唐山国丰(余量)、鞍钢鲅鱼圈热轧工程、首钢迁安,通过以上公司实力对比和产品质量情况,我们认为以上几家公司可以初步确定为战略合作伙伴发展对象。
天津轧一钢铁集团有限公司
科技发展部
2012-1-20。
武钢1700热连轧全线过钢
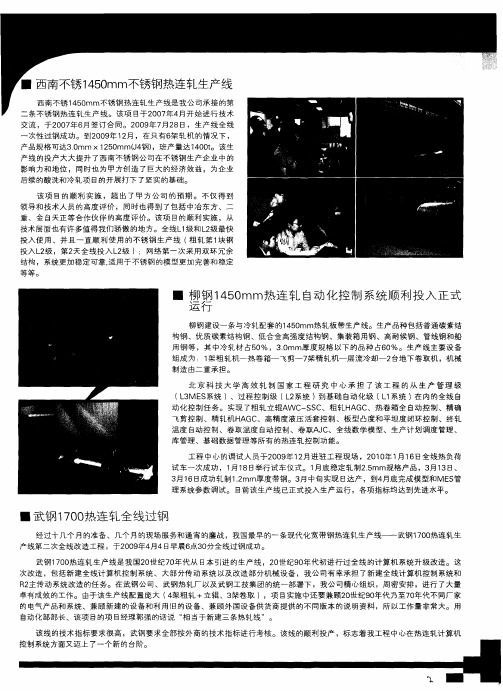
西 南 不 锈 1 5 mm 不锈 钢 热 连 轧 生 产 线 是 我 公 司 承 接 的 第 0 4 二 条 不 锈 钢 热 连 轧 生 产 线 。 该 项 目于 2 0 年 4 开 始 进 行 技 术 07 月 交 流 ,于 2 0 年 6 签 订 合 同 。 2 0 年 7 2 07 月 0 9 月 8日 ,生 产 线 全 线
武钢1 0 热连轧生产 线是我 国2 世纪7 年代从 日本引进 的生产线 ,2 世纪9 年代初进行 过全线 的计 算机系统升 级改造。 这 0 7 O O 0 0
次改造 ,包括 新建全线计算机 控制 系统 、大部分传动 系统 以及 改造部 分机械设 备 ,我公 司有幸承担 了新建全线计 算机 控制 系统和 R 主传 动系统改造 的任 务。在武钢 公司、武钢热轧 厂以及武钢工技集 团的统一部署 下 ,我公司精 心组织 ,周密安排 ,进行 了大量 2 卓有成效的工作。 由于该生 产线 配置庞大 ( 架粗轧 +立辊 、3 4 架卷取 ),项 目实施 中还要兼 顾2 世纪9 年代 乃至7 年代不同厂家 0 O 0 的 电气产品和 系统 、兼顾新建 的设备和利 用 旧的设备 、兼顾外 国设 备供 货商提供 的不 同版 本的说明 资料 ,所 以工作量 非常大。用 自动化部 部长、该项 目的项 目经理郭强 的话说 “ 相当于新建三条热轧线 ”。
次性过钢 成功 。 ̄ 2 0 年1 月 ,在只有6 q0 9 2 架轧机 的情 况下 , 产 品 规 格 可 达 30 .mm 2 0 X1 5 mm(4 ) 产 量达 1 0 t 该 生 J 钢 ,班 4 0。
一
产线 的投产 大大提升 了西南不锈 钢公司在 不锈 钢生产企 业中 的
年产200万吨1780热轧带钢车间设计

关键词:热轧;板带钢;CVC轧机 is one of the main varieties of steel products, widely used in industry, agriculture, transportation and construction. Wide strip in the development of our national economy in great demand. In recent years, countries in the world are paying attention to the development and use of continuous casting and rolling, and other new technologies and new equipment to produce steel strip.
The 1780 is designed to produce 2 million tons of hot rolled strip plant design, a typical product thickness3.0mm. To meet the requirements of high quality and high performance boards, this design combines the Tangshan Iron and Steel1700mm, Ning steel1780mm, Anshan Iron and Steel1780mmhot rolling workshop designed annual output of 2 million tons of1780mmconventional hot rolling workshop. Design uses two four-high reversing roughing mill, rolling six times, finishing mill selected six non-reversible rolling mill six times, through the use of CVC mill, PC mill and thickness control (AGC) to control panels and other technology-based combination and thickness, in the no-mandrel before finishing the heat shield coil box.
热连轧带钢板形控制

热连轧带钢板形控制
张子彦;杜希恩;刘安剑;马小军;王苏州
【期刊名称】《科技信息》
【年(卷),期】2011(000)011
【摘要】简要叙述了七机架热连轧精轧机组板形控制系统的功能配置、组成结构以及应用效果.重点介绍WRS轧机板形设定与控制模型在该系统中的设计与应用,针对实际应用效果,进行总结分析,对于不足之处,提出一些看法.
【总页数】2页(P81-82)
【作者】张子彦;杜希恩;刘安剑;马小军;王苏州
【作者单位】日照钢铁有限公司1580mm热轧带钢厂,山东,日照,276806;日照钢铁有限公司1580mm热轧带钢厂,山东,日照,276806;日照钢铁有限公司1580mm 热轧带钢厂,山东,日照,276806;日照钢铁有限公司1580mm热轧带钢厂,山东,日照,276806;日照钢铁有限公司1580mm热轧带钢厂,山东,日照,276806
【正文语种】中文
【相关文献】
1.热连轧带钢板形控制
2.安钢1780 mm热连轧带钢板形控制的应用实践
3.热连轧带钢的板形控制
4.唐钢不锈钢1580mm热连轧带钢卷取卷形的控制
5.武钢1700热连轧带钢板形控制
因版权原因,仅展示原文概要,查看原文内容请购买。
北京科技大学科技成果——带钢热连轧计算机控制系统

北京科技大学科技成果——带钢热连轧计算机控制系统成果简介高效轧制国家工程研究中心在带钢热连轧计算机控制系统设计和软件开发方面具有较强实力,参加和承担完成了国内多条热连轧计算机控制工程项目。
例如:武钢1700mm热连轧计算机控制系统(获冶金部科技进步特等奖,国家科技进步一等奖);太钢1549mm热连轧计算机控制系统(获国家科技进步二等奖);上海梅山1422mm热连轧计算机控制系统(通过国家验收);攀钢1450mm热连轧粗轧区基础自动化改造;鞍钢1780mm热连轧计算机控制系统(通过国家验收);莱钢1500mm热连轧计算机控制系统(获山东省科技进步三等奖);日照1580mm热连轧三电(传动、自动化和管理、仪表)控制系统。
目前国内外带钢热连轧计算机系统一般分为:传动控制级(L0),基础自动化级(L1),过程控制级(L2),生产控制级(L3)。
高效轧制国家工程研究中心能够提供从L0到L3的全套带钢热连轧计算机系统。
能够完成从系统设计﹑软件设计、编程调试﹑现场服务﹑到开工投产的全过程。
主要内容包括:硬件系统:选用进口硬件,并提供性能价格比最高的硬件产品,也可根据用户的需要,灵活选择硬件品牌。
支持软件:支持软件(Support Software)是一种软件开发环境,是一组软件工具的集合。
支持软件又叫做中间件(Middle Ware),我们将提供自主知识产权的全套中间件。
控制系统:高效轧制国家工程研究中心能够提供用于热轧自动化控制的全套独立开发的应用软件,包括:L0级(传动控制系统):交、直流数字传动,交交变频。
L1级(基础控制系统):炉区控制、定宽机控制、粗轧控制、立辊AWC-SSC控制、保温罩控制、热卷箱控制、飞剪控制、精轧速度控制、液压/电动活套控制、液压HAGC控制、HAPC控制、弯辊控制、串辊控制、换辊控制、层冷控制、卷取机控制、助卷辊AJC控制、运输控制和检查控制等。
L2级(过程控制系统):燃烧计算设定模型、轧制节奏、粗轧计算设定模型、宽度模型、精轧计算设定模型、板形设定和控制模型、终轧温度控制模型、卷取温度控制模型、卷取设定模型等。
- 1、下载文档前请自行甄别文档内容的完整性,平台不提供额外的编辑、内容补充、找答案等附加服务。
- 2、"仅部分预览"的文档,不可在线预览部分如存在完整性等问题,可反馈申请退款(可完整预览的文档不适用该条件!)。
- 3、如文档侵犯您的权益,请联系客服反馈,我们会尽快为您处理(人工客服工作时间:9:00-18:30)。
(HCR)、直接热装(DHCR)三种装炉方式,其中热装板坯约占30%。对于 高牌号无取向硅钢和取向硅钢的板坯送入板坯库后,根据工艺要求可进 入硅钢保温炉进行缓冷和保温,然后根据轧制计划分批装入加热炉。
板坯经测温和板坯核对后,送入加热炉装炉辊道,按布料图进行定 位后,装钢机将板坯推正后等待装炉;当满足装炉条件时炉门打开,装钢 机托起板坯送入炉内,使该块板坯放在与前一块坯料间隔~50mm位置处 (高温工艺加热取向硅钢时采用无间隔方式),板坯停稳后,装钢机低 位快速退出炉外回原位,准备重复装钢动作;同时装料炉门关闭。
一。
表一 钢种分配的年产量计划表
序 号
钢种
1 碳素结构钢
代表钢号 Q195~Q275
优质碳素结构
2
08、MR、DT
钢
3 低合金结构钢 Q345~Q460
4 超低碳钢
IF
5 集装箱用板 SPA-H
6 耐候钢
Q295GNH、295GHL
7 其它
比例 (%)
7.3
年产量 (104t/a)
20.40
47.1
装入炉内的板坯通过步进梁的运动从入炉端运送到出炉端。步进梁 的步进运动是一个矩形运动轨迹。步进梁运动由水平运动和垂直运动组
成。水平运动和垂直运动过程中的速度是变化的,其目的在于保证运作 平移运动。此时,提升缸处于静止状态。步进机构的升降运动是:提升 缸驱动提升框架,使其滚轮沿斜台面滚动,完成升降运动。此时,平移 缸处于静止状态。
板坯年需要量为289万t,板坯规格及要求如下:
1) 碳钢板坯
238.4万t/a
厚度
230mm
宽度
800~1450mm
长度
9800~11000mm
4500~5300mm(少量短尺坯)
板坯重量
Max.28.6t
2) 取向硅钢板坯40.源自万t/a厚度230mm
宽度
1100mm
长度
Max.9600mm
板坯重量
对回炉板坯直接由炉前出料辊道送往返回坯辊道上,由板坯库吊车 吊到板坯库等待处理。
硅钢回炉坯需返回保温炉保温。 b) 轧制 出炉板坯由除鳞机入口辊道输送到高压水除鳞箱,板坯经高压水清 除板坯表面氧化铁皮后送往带附属立辊的二辊可逆式粗轧机E1R1和带附 属立辊的四辊可逆式粗轧机E2R2进行轧制,轧制可采用3+3的道次分配, 将板坯轧制成32-60mm的中间坯。在轧制过程中,根据轧制规程要求, 可在轧机入口侧或出口侧采用高压水清除二次氧化铁皮。经粗轧机组轧 制后的中间坯经中间辊道送往精轧机区。 不能进入精轧机轧制的中间坯,直接送至中间辊道上,再由废品推 出装置将其推到中间辊道操作侧的废品收集台架进行冷却。 中间坯经过中间辊道时依据轧制品种和产品规格的不同而确定是否 采用中间坯保温罩保温。中间坯在进入切头飞剪前将速度降低至切头飞
Max.18.8t
3) 无取向硅钢板坯
9.8万t/a
厚度
230mm
宽度
1300mm
长度
Max.11000mm
板坯重量
Max.25.5t
4) 板坯技术条件
厚度公差
±5mm
宽度公差
±15mm
长度公差
±30mm
侧弯及翘曲
长尺≤40mm ;短尺≤20mm
板坯表面质量:全部为无缺陷合格板坯。
6. 品种规格及产量
b) 本工程采取国内技术总负责的方式,立足国内,采购工艺软件及 国内技术不成熟设备及配套件、控制系统及软件。
c) 严格执行与工程建设有关的法律、法规和标准,如环保、职业安 全卫生、消防和地震设防等。
d) 项目装备水平应达到国际先进水平。 2) 机组选型
根据市场定位及产品方案,武钢新建热带钢轧机确定选用半连续式 轧机,轧机规格选择为1580mm。 3)工艺设备选择:
精轧机组的F1~F7机架配置了长行程的工作辊窜辊,可最大限度地 实现自由轧制以及硅钢和碳钢的混合轧制。 g) 精轧机F1~F7采用带压力传感器的液压活套,活套转动惯量低,利
于控制精轧机组速度和带钢张力。 h) 精轧机F1~F7全部采用全液压压下系统和厚度自动控制(AGC)系
统,提高了带钢全长厚度控制精度。
11.采用的主要新工艺、新设备及新技术 a) 为节省能源和降低生产运行成本,实现最大限度地节能,加热炉采用
直接热装(DHCR)的装炉方式。 b) 碳钢加热炉采用汽化冷却、高效换热器,炉子水梁立柱采用双层绝热
包扎,采用最佳化燃烧控制模型,以配合热装更有效地节省能源。硅 钢高温加热炉,max.1400℃,采用液态出渣以增加一个硅钢轧制周期 的硅钢生产量。 c) 粗轧机组立辊轧机E1、E2采用全液压压下,设备简单便于维护,同 时配置短行程(SSC)和自动宽度控制(AWC)功能,可提高带钢 宽度精度。
当板坯较长时间停在炉内时,要求步进梁停在中位或进行踏步以避 免板坯变形弯曲和黑印加重。正常生产时步进梁停在低位,为减少板坯 加热过程中变形步进梁可停在中位。硅钢生产时步进梁停中位后上升启 动时直接上升不下降。
板坯到达出料端时,被出料端激光检测装置检测到,步进梁继续向 前完成该步步距后停止,已加热到轧制要求温度的板坯等待出钢,当接 到轧机要钢信号后,出料炉门上升到半开位置,出钢机托杆低位进入炉内, 在取料位置前500mm时出料炉门上升到全开位置,出钢机托起板坯快速 退出炉外,将板坯放在出炉辊道,送轧机进行轧制。出钢机退出炉外一定 距离后出料炉门由全开下降到全关闭。出钢机回到原位,等待下一次出 钢。
进入钢卷库的钢卷有以下去向:直接发货的钢卷在热轧钢卷库进行 堆放冷却,之后由火车或汽车外运;需要送到冷轧厂及硅钢厂的钢卷通 过火车或汽车送到冷轧厂或硅钢厂原料库。钢卷在运输和堆放的过程中 均采用卧卷的方式。 从板坯进入板坯库开始直至成品发货为止,全部工艺过程通过轧线物料 跟踪系统及两库管理系统对板坯、轧件和钢卷进行全线跟踪,从而实现 了计算机自动化生产控制和管理。
1580mm热轧生产线其工艺及设备装备采用国内技术总负责,采用 国内制造的方式,点菜式引进关键配套件,主要有板形控制装置、压下 缸、轴承、密封、液压元件、特殊的减速器、传动轴、打捆机、喷印机 等。打捆机、喷印机由武钢负责购置,其余均由一重负责引进。 4)电气设备及技术选择:
在满足生产要求和电控系统整体性能的前提下,电控设备拟采用国 内制造、合作制造、关键设备引进的供货方案。 2. 概述
卷取完毕,卸卷小车按设定程序上升压住带尾,并把钢卷托起,卷 筒收缩,外支撑打开,由卸卷小车把钢卷托出,然后由运卷小车将钢卷 送至钢卷运输系统,运输系统将钢卷继续向后运送,经打捆、称重、喷 印后,运送到热轧钢卷库。需要检查的钢卷则送到检查线,打开钢卷进 行检查后,再卷上,送回运输系统,运至热轧钢卷库。
2.2~2.3mm
宽度
1275mm
卷重
Max.25.5t
钢卷内径 钢卷外径 单位宽度卷重 7. 生产钢种
φ762mm Max.φ2030mm
Max.20.0kg/mm
热轧厂生产的主要钢种有:普通碳素结构钢、优质碳素结构
钢、低合金结构钢、高耐候性结构钢、IF钢、高磁感取向硅钢、普
通取向硅钢、高牌号无取向硅钢等。钢种分配的年产量计划见表
武钢1580mm热连轧生产线生产规模为年产280万吨热轧钢卷。由 1580mm热连轧生产线和1套预留的平整分卷机组组成。钢卷厚度:1.2
~12.7mm;钢卷宽度:730~1430mm ;钢卷内径 :φ762mm;钢卷 最大外径 :Max.φ2080mm;单位宽度最大卷重:Max.22.0kg/mm。生产 钢卷强度等级:≤650MPa。
132
6.5
18.30
10.1 28.40
5.5
15.34
5.5
15.34
1.7
4.72
高磁感取向硅
8
HIB
钢
4.0
11.1
9 普通取向硅钢 CGO
高牌号无取向
10
W7~W14
硅钢
8.9
25
3.4
9.4
合计
100.00
8. 主要工艺设备
主要设备组成为:
板坯输送辊道
1套
硅钢保温炉
20座
步进梁加热炉
4座(其中预留1座)
1) 供三冷轧原料钢卷
110万t/a
厚度
1.5~6.0mm
宽度
730~1430mm
卷重
Max.28.6t
钢卷内径
φ762mm
钢卷外径
Max.φ2080mm
单位宽度卷重
Max.22.0kg/mm
2) 热轧商品钢卷
124.5万t/a
厚度
1.2~12.7mm
宽度
730~1430mm
卷重
Max.28.6t
钢卷内径
粗轧高压水除鳞装置
1座
E1立辊轧机
1套
R1二辊可逆式粗轧机
1套
E2粗轧机立辊轧机
1套
R2四辊可逆式粗轧机
1套
保温罩
1套
切头飞剪
1套
精轧高压水除鳞装置
1套
精轧机组
7架
层流冷却装置
1套
卷取机
3套(其中预留1套)
钢卷运输系统
1套
平整分卷机组
1套(预留位置)
280.0
9. 1580mm热连轧组设备布置图
图三、1580mm热连轧组设备布置图
φ762mm
钢卷外径
Max.φ2080mm
单位宽度卷重
Max.22.0kg/mm
3) 取向硅钢钢卷
36.1万t/a
厚度
2.2~2.3mm
宽度
1080mm