---------电子束加工的特点及其应用
电子束微细加工技术的发展及其应用

电子束微细加工技术的发展及其应用电子束微细加工技术随着科学技术的发展而逐渐成熟,其在加工工业领域有着广泛的应用。
本文将重点探讨电子束微细加工技术的发展历程,技术特点以及在各个领域的应用。
一、电子束微细加工技术的发展历程电子束微细加工技术可以追溯到二十世纪中期,当时美国贝尔实验室的研究人员首次将电子束用于微细加工。
当时,电子束微细加工技术还处于探索阶段,局限于单层薄膜的微细加工。
随着科学技术的发展,电子束微细加工技术经历了从单层薄膜加工到多层薄膜、集成电路、光学器件以及生物医学等领域的拓展过程。
二、电子束微细加工技术的技术特点1.高精度电子束微细加工技术的加工精度可以达到亚微米级别。
由于电子束的微小直径,因此加工精度高。
同时,电子束微细加工技术无需接触到工件表面,因此可以避免因为接触而导致的破坏。
2.高速度电子束微细加工技术的加工速度比传统机械加工技术快得多。
电子束可以在微小的空间内加工,从而提高加工效率。
3.可控性强电子束微细加工技术可以通过调整电子束的加速电压和电子束的聚焦来实现不同的加工效果。
同时,电子束微细加工技术还具有可调的深度控制功能。
三、电子束微细加工技术在各个领域的应用1.集成电路在集成电路制造领域,电子束微细加工技术可以实现极小尺寸的电路设计。
利用电子束微细加工技术可以制造出亚微米级别的电路,这对于集成电路的制造具有重要的作用。
2.生物医学电子束微细加工技术在生物医学领域的应用主要集中在生物芯片制造方面。
利用电子束微细加工技术可以制造出超薄的微处理芯片,这些芯片可以被用于感应、检测和诊断。
3.光学器件利用电子束微细加工技术可以制造出高精度的光学器件,如光纤、光阻、光学芯片等等,这些光学器件可以被应用于通讯、光电子学、测量、材料加工等领域。
4.微纳机械电子束微细加工技术在微纳机械领域具有广泛的应用。
可以利用电子束微细加工技术制造出微米级别的光学器件、电子器件和机械器件等。
在微纳机械领域,电子束微细加工技术在制造微机械设备时具有独特的优势。
电子束加工的原理特点应用

电子束加工的原理特点应用1. 原理介绍电子束加工是一种以电子束为工具,利用其高速度和高能量,对材料进行加工和改变形状的技术。
其原理基于电子束与材料相互作用时的各种效应,包括电子-材料相互碰撞、电子散射和电子热效应等。
通过控制电子束的能量、聚束和扫描方式,可以实现对材料的溶解、沉积和表面改性等加工操作。
2. 特点分析2.1 高精度加工电子束加工具有非常高的定位精度和加工精度。
由于电子束可以聚焦到非常小的区域,因此可以实现微米级别的加工精度。
同时,电子束加工过程不会产生机械接触,避免了传统机械加工过程中的磨损和变形等问题,保证了加工精度的稳定性。
2.2 无热影响区域电子束加工实现了非接触式加工,材料不受热影响区域的限制。
传统热加工方法往往会对材料造成热变形、热裂纹和残余应力等问题,而电子束加工则可以在不产生热影响的情况下进行加工操作,有效防止了材料的热损伤。
2.3 高能量密度加工电子束加工具有极高的能量密度。
电子束在与材料相互作用时,会传递给材料的能量密度非常大,可以迅速将材料加热到高温甚至熔化状态。
这种高能量密度的加工方式适用于一些特殊材料,例如高熔点金属或者难加工的高强度合金等。
2.4 灵活性和可控性高电子束加工具有非常高的灵活性和可控性。
可以通过调节电子束的能量、聚束方式和扫描路径等参数,实现对材料加工过程的精确控制。
这种灵活性和可控性使得电子束加工可以用于不同材料的加工和多种形状的制造。
3. 应用领域3.1 微电子学电子束加工在微电子学领域的应用非常广泛。
由于其高精度和高能量密度的优势,电子束可以用于微芯片的制造、电路板的加工以及微电子器件的制备等。
同时,由于电子束加工不受材料性质的影响,可以适用于各种不同材料的加工。
3.2 航空航天电子束加工在航空航天领域的应用也非常重要。
航空航天领域对材料的高温抗性和高强度要求非常高,而电子束加工恰好可以实现对这些材料的精确加工和形状调整。
同时,由于其非接触式加工的特点,电子束可以用于对高温材料的修复和维护。
电子束加工技术及其应用
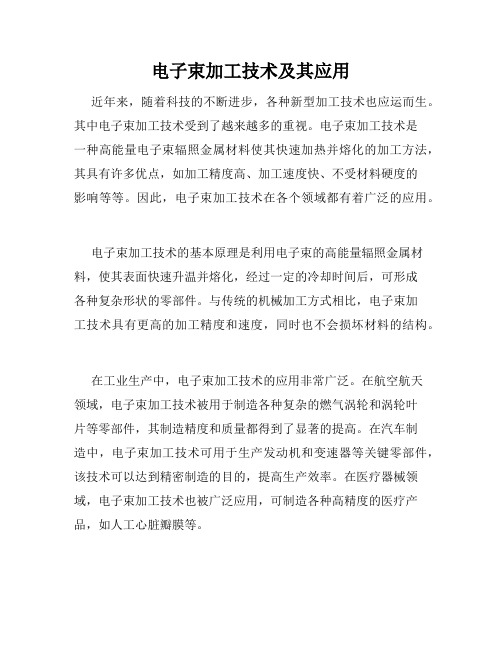
电子束加工技术及其应用近年来,随着科技的不断进步,各种新型加工技术也应运而生。
其中电子束加工技术受到了越来越多的重视。
电子束加工技术是一种高能量电子束辐照金属材料使其快速加热并熔化的加工方法,其具有许多优点,如加工精度高、加工速度快、不受材料硬度的影响等等。
因此,电子束加工技术在各个领域都有着广泛的应用。
电子束加工技术的基本原理是利用电子束的高能量辐照金属材料,使其表面快速升温并熔化,经过一定的冷却时间后,可形成各种复杂形状的零部件。
与传统的机械加工方式相比,电子束加工技术具有更高的加工精度和速度,同时也不会损坏材料的结构。
在工业生产中,电子束加工技术的应用非常广泛。
在航空航天领域,电子束加工技术被用于制造各种复杂的燃气涡轮和涡轮叶片等零部件,其制造精度和质量都得到了显著的提高。
在汽车制造中,电子束加工技术可用于生产发动机和变速器等关键零部件,该技术可以达到精密制造的目的,提高生产效率。
在医疗器械领域,电子束加工技术也被广泛应用,可制造各种高精度的医疗产品,如人工心脏瓣膜等。
电子束加工技术还被用于精密电子加工领域。
例如,在微电子器件制造中,电子束加工技术可以制造出非常小尺寸的芯片,从而提高电子产品的性能。
同时,电子束加工技术还可用于制造LED发光二极管等光电器件,这些器件在舞台照明、汽车照明、电视背景板等领域都有着广泛的应用。
在科学研究领域,电子束加工技术也被广泛应用。
比如,在材料科学中,电子束加工技术可用于制备一些高性能材料,如金属泡沫等。
此外,该技术还可用于制备超导材料,来用于实现磁悬浮列车、核聚变等高技术项目。
在现代生产领域,高精度、高效率和高质量等特点成为了制造业趋势的主要特征。
电子束加工技术正是一种能够提供高精度加工方法的新兴技术,同时也是现代制造业不可或缺的一种重要技术手段。
总之,电子束加工技术是现代制造业中一种不可或缺的技术手段。
随着这一技术的不断发展,它将在更广泛的领域内发挥重要作用。
电子束处理技术在材料加工中的应用研究
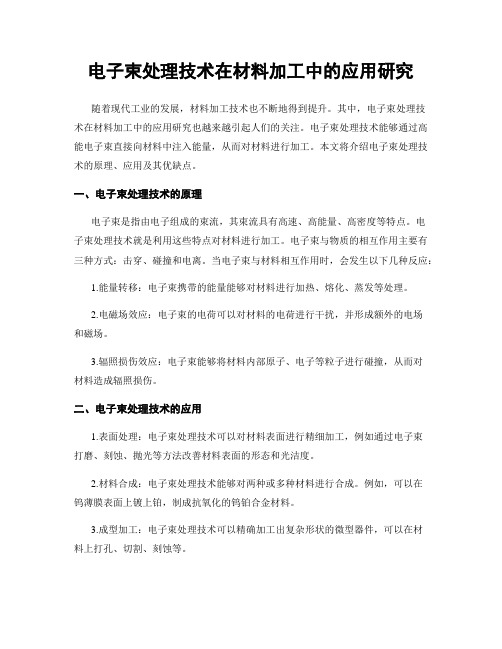
电子束处理技术在材料加工中的应用研究随着现代工业的发展,材料加工技术也不断地得到提升。
其中,电子束处理技术在材料加工中的应用研究也越来越引起人们的关注。
电子束处理技术能够通过高能电子束直接向材料中注入能量,从而对材料进行加工。
本文将介绍电子束处理技术的原理、应用及其优缺点。
一、电子束处理技术的原理电子束是指由电子组成的束流,其束流具有高速、高能量、高密度等特点。
电子束处理技术就是利用这些特点对材料进行加工。
电子束与物质的相互作用主要有三种方式:击穿、碰撞和电离。
当电子束与材料相互作用时,会发生以下几种反应:1.能量转移:电子束携带的能量能够对材料进行加热、熔化、蒸发等处理。
2.电磁场效应:电子束的电荷可以对材料的电荷进行干扰,并形成额外的电场和磁场。
3.辐照损伤效应:电子束能够将材料内部原子、电子等粒子进行碰撞,从而对材料造成辐照损伤。
二、电子束处理技术的应用1.表面处理:电子束处理技术可以对材料表面进行精细加工,例如通过电子束打磨、刻蚀、抛光等方法改善材料表面的形态和光洁度。
2.材料合成:电子束处理技术能够对两种或多种材料进行合成。
例如,可以在钨薄膜表面上镀上铂,制成抗氧化的钨铂合金材料。
3.成型加工:电子束处理技术可以精确加工出复杂形状的微型器件,可以在材料上打孔、切割、刻蚀等。
4.原位生长:电子束处理技术可以利用能量和物质的相互作用,在材料表面上原位生长出纳米或亚纳米结构。
5.材料改性:电子束处理技术可以改变材料内部晶体结构和组成,例如通过电子束辐照对材料进行改质和改性。
三、优缺点分析1.优点:(1)高度的加工精度:电子束利用高速、高能、高密度的电子束流进行加工,可以实现高度的加工精度。
(2)成本低:相较于其他加工技术,电子束处理技术的成本较低。
(3)适用范围广:电子束处理技术适用于多种材料的加工,例如金属、陶瓷等。
2.缺点:(1)安全问题:由于电子束处理技术使用高能电子束流进行加工,对操作人员的安全要求较高。
---------电子束加工的特点及其应用
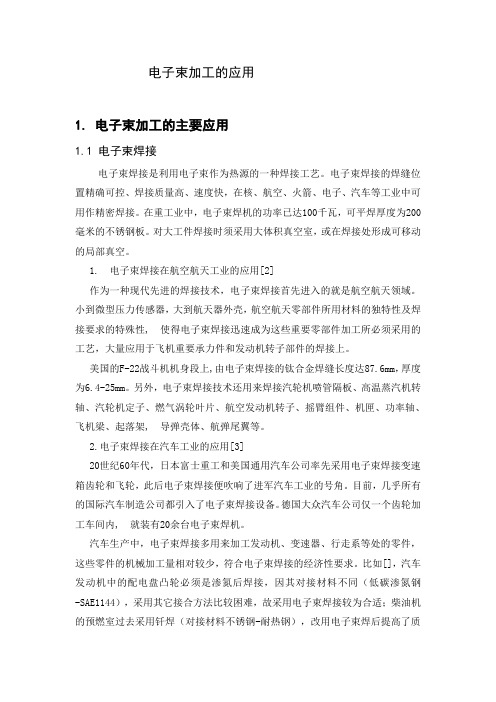
电子束加工的应用1. 电子束加工的主要应用1.1 电子束焊接电子束焊接是利用电子束作为热源的一种焊接工艺。
电子束焊接的焊缝位置精确可控、焊接质量高、速度快,在核、航空、火箭、电子、汽车等工业中可用作精密焊接。
在重工业中,电子束焊机的功率已达100千瓦,可平焊厚度为200毫米的不锈钢板。
对大工件焊接时须采用大体积真空室,或在焊接处形成可移动的局部真空。
1. 电子束焊接在航空航天工业的应用[2]作为一种现代先进的焊接技术,电子束焊接首先进入的就是航空航天领域。
小到微型压力传感器,大到航天器外壳,航空航天零部件所用材料的独特性及焊接要求的特殊性, 使得电子束焊接迅速成为这些重要零部件加工所必须采用的工艺,大量应用于飞机重要承力件和发动机转子部件的焊接上。
美国的F-22战斗机机身段上,由电子束焊接的钛合金焊缝长度达87.6mm,厚度为6.4-25mm。
另外,电子束焊接技术还用来焊接汽轮机喷管隔板、高温蒸汽机转轴、汽轮机定子、燃气涡轮叶片、航空发动机转子、摇臂组件、机匣、功率轴、飞机梁、起落架, 导弹壳体、航弹尾翼等。
2.电子束焊接在汽车工业的应用[3]20世纪60年代,日本富士重工和美国通用汽车公司率先采用电子束焊接变速箱齿轮和飞轮,此后电子束焊接便吹响了进军汽车工业的号角。
目前,几乎所有的国际汽车制造公司都引入了电子束焊接设备。
德国大众汽车公司仅一个齿轮加工车间内, 就装有20余台电子束焊机。
汽车生产中,电子束焊接多用来加工发动机、变速器、行走系等处的零件,这些零件的机械加工量相对较少,符合电子束焊接的经济性要求。
比如[],汽车发动机中的配电盘凸轮必须是渗氮后焊接,因其对接材料不同(低碳渗氮钢-SAE1144),采用其它接合方法比较困难,故采用电子束焊接较为合适;柴油机的预燃室过去采用钎焊(对接材料不锈钢-耐热钢),改用电子束焊后提高了质量, 也降低了成本;起动马达整流子铜环采用电子束焊后,可同时高速焊接数十个,生产率大大提高,成本大幅度下降;转向车轮部分的球窝接头采用电子束焊接,施焊速度非常快, 热影响很小,能很好地防止球接头中封装的黄油受热变质;转向柱管的焊接要求变形小、焊接表面光滑,故也适宜采用电子束焊接。
现代加工技术第7章 电子束离子束加工

2024/10/7
7.1.电子束加工
3 电子束加工的应用
II 加工型孔或特殊外表
切割复杂型面,切口宽度6~3 μm ,边 缘粗糙度可控制在±0.5μm ;
不仅可以加工直孔也可以加工弯孔和 立体曲面;
Page 9
2024/10/7
7.1.电子束加工
3 电子束加工的应用
III 刻蚀
在微电子器件生产中,为了制造多层固体组件,利用电 子束对陶瓷或半导体材料可出许多微细沟槽和孔 ; 制版;
ii 蚀刻加工时,对离子入射能量、束流大小、离子 入射到工件上的角度以及工作室气压等分别控制;
iii 氩气离子蚀刻效率取决于离子能量和入射角度;
入射能量增大蚀刻效率增加;
入射角度增加蚀刻效率增加,但角度过大使有效束流减 小,40º~60º效率最高;
Page 21
2024/10/7
7.2.离子束加工
Page 10
2024/10/7
7.1.电子束加工
3 电子束加工的应用
IV 焊接
当高能量密度的电子束轰击焊件外表时,使焊件接头处 的金属熔融,在电子束不断轰击下,形成一个被熔融金 属环绕的毛细管状的蒸气管,如果焊件按一定速度沿接 缝与电子束作相对运动,那么接缝上的蒸气管由于电子 束的离开而重新凝固,形成焊缝 ; 焊接速度快,焊缝窄、强度好,热影响区小,变形小; 可以焊接难熔金属和化学活性高的金属; 可以焊接不同材料;
Pag.离子束加工
2 离子束加工装置
I 离子源
i 考夫曼型离子源;
Page 19
2024/10/7
7.2.离子束加工
2 离子束加工装置
I 离子源
ii 双等离子体型离子源;
电子束加工的特点及其应用
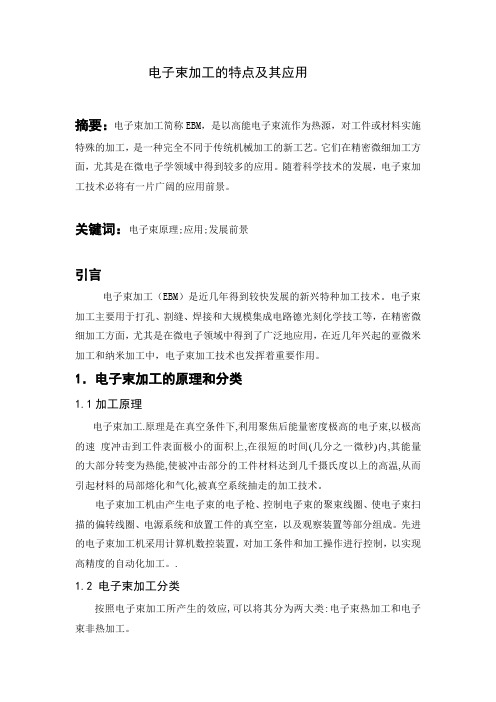
电子束加工的特点及其应用摘要:电子束加工简称EBM,是以高能电子束流作为热源,对工件或材料实施特殊的加工,是一种完全不同于传统机械加工的新工艺。
它们在精密微细加工方面,尤其是在微电子学领域中得到较多的应用。
随着科学技术的发展,电子束加工技术必将有一片广阔的应用前景。
关键词:电子束原理;应用;发展前景引言电子束加工(EBM)是近几年得到较快发展的新兴特种加工技术。
电子束加工主要用于打孔、割缝、焊接和大规模集成电路德光刻化学技工等,在精密微细加工方面,尤其是在微电子领域中得到了广泛地应用,在近几年兴起的亚微米加工和纳米加工中,电子束加工技术也发挥着重要作用。
1.电子束加工的原理和分类1.1加工原理电子束加工.原理是在真空条件下,利用聚焦后能量密度极高的电子束,以极高的速度冲击到工件表面极小的面积上,在很短的时间(几分之一微秒)内,其能量的大部分转变为热能,使被冲击部分的工件材料达到几千摄氏度以上的高温,从而引起材料的局部熔化和气化,被真空系统抽走的加工技术。
电子束加工机由产生电子束的电子枪、控制电子束的聚束线圈、使电子束扫描的偏转线圈、电源系统和放置工件的真空室,以及观察装置等部分组成。
先进的电子束加工机采用计算机数控装置,对加工条件和加工操作进行控制,以实现高精度的自动化加工。
.1.2 电子束加工分类按照电子束加工所产生的效应,可以将其分为两大类:电子束热加工和电子束非热加工。
电子束热加工电子束热加工是将电子束的动能在材料表面转化成热能,以实现对材料的加工,其中包括:1)电子束精微加工。
可完成打孔、切缝和刻槽等工艺, 这种设备一般都采用微机控制,并且常为一机多用;2)电子束焊接。
与其他电子束加工设备不同之处在于,除高真空电子束焊机之外,还有低真空、非真空和局部真空等类型;3)电子束镀膜。
可蒸镀金属膜和介质膜;4)电子束熔炼。
包括难熔金属的精炼,合金材料的制造以及超纯单晶体的拉制等;5)电子束热处理。
电子束加工原理及应用
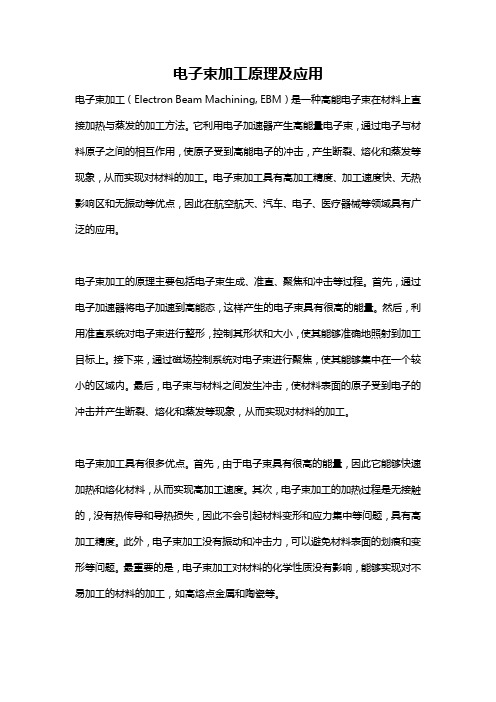
电子束加工原理及应用电子束加工(Electron Beam Machining, EBM)是一种高能电子束在材料上直接加热与蒸发的加工方法。
它利用电子加速器产生高能量电子束,通过电子与材料原子之间的相互作用,使原子受到高能电子的冲击,产生断裂、熔化和蒸发等现象,从而实现对材料的加工。
电子束加工具有高加工精度、加工速度快、无热影响区和无振动等优点,因此在航空航天、汽车、电子、医疗器械等领域具有广泛的应用。
电子束加工的原理主要包括电子束生成、准直、聚焦和冲击等过程。
首先,通过电子加速器将电子加速到高能态,这样产生的电子束具有很高的能量。
然后,利用准直系统对电子束进行整形,控制其形状和大小,使其能够准确地照射到加工目标上。
接下来,通过磁场控制系统对电子束进行聚焦,使其能够集中在一个较小的区域内。
最后,电子束与材料之间发生冲击,使材料表面的原子受到电子的冲击并产生断裂、熔化和蒸发等现象,从而实现对材料的加工。
电子束加工具有很多优点。
首先,由于电子束具有很高的能量,因此它能够快速加热和熔化材料,从而实现高加工速度。
其次,电子束加工的加热过程是无接触的,没有热传导和导热损失,因此不会引起材料变形和应力集中等问题,具有高加工精度。
此外,电子束加工没有振动和冲击力,可以避免材料表面的划痕和变形等问题。
最重要的是,电子束加工对材料的化学性质没有影响,能够实现对不易加工的材料的加工,如高熔点金属和陶瓷等。
电子束加工在航空航天领域有着广泛的应用。
由于电子束加工具有高加工精度和高能量特点,因而能够应用于航空航天领域中对材料性能要求较高的部件的制造。
比如,电子束加工常用于制作航空发动机喷嘴、涡轮叶片以及复杂的结构件等。
此外,电子束加工还可以用于航天器的表面处理,如表面改性、疏水处理等。
在汽车制造方面,电子束加工也具有很大的应用潜力。
汽车零部件通常由高强度和复杂形状的金属材料制成,而电子束加工能够实现对这些材料的高精度加工,从而提高零部件的质量和性能。
电子束加工技术

五应用
打 孔
例三: 电子束加工在人造革上的应用。现在人造革已很普 及,但人造革透气性很差,穿着很不舒服。用电子 束在人造革上打孔可以达到相当好的效果。如以天 然革穿着的舒适度为100,微孔聚氨酯革只有55,而 用电子束打孔的PVC革可达85。电子束打孔成本比 天然革成本低,可替代天然革。加工时,用一组钨 杆将电子枪产生的单个电子束分割为200个孔,效率 非常高。因为对孔型无严格要求,人造革在滚筒上 旋转时,电子束无须随之转动。如1.5mm厚革加工 时,脉冲频率为25Hz,打孔速率为5 000/s,滚筒 转速为6r/min。
四 加工特点
(3) 电子束的强度、位置、聚焦进行直接控制 位置 控制的准确度可达0.1微米左右,强度和束斑的大 小控制误差也易达到1%以下。通过磁场或电场几乎 可以无惯性,无功率的控制电子束,便于采用计算 机控制,实现加工过程自动化。 (4) 真空环境下加工点不受杂质污染 加工点处能保 持原来材料的纯度。适合于加工易氧化的金属及合 金材料,特别是要求纯度极高的半导体材料。 (5)电子束加工需要一套价格昂贵的.专用设备, 加工成本高。
电子束控制系统
束流聚焦控制是为了提高电子束的能量密度,使电 子束聚焦成很小的束斑,它基本上决定着加工点的 孔径或缝宽。聚焦方法有两种,一种是利用高压静 电场使电子流聚焦成细束;另一种是利用“电磁透镜” 靠磁场聚焦。后者更为安全可靠。 所谓电磁透镜,实际上是电磁线圈,通电后它产生 的轴向磁场与电子束中心线平行,径向磁场则与中 心线垂直。根据左手定则,电子束在前进运动中切 割径向磁场时产生圆周运动,而在圆周运动时在轴 向磁场中又将产生径向运动,所以实际上每个电子
电子束加工
简 介
吴爱民等以H13和D2模具钢为基材,通过脉冲电子 束直接淬火和电子束表面合金化等方法进行表面改 性处理试验。
电子束加工的原理及应用

电子束加工的原理及应用电子束加工是一种高速电子束束流通过真空管道对工件表面进行加工的技术。
该技术使用加速器产生高能电子束,通过聚焦系统将电子束聚焦到非常小的直径上,然后将聚焦后的电子束对待加工的工件表面进行瞬时加热和熔化,从而实现对工件表面的精细加工。
电子束加工技术的原理主要包括三个方面:加速原理、聚焦原理和工件加工原理。
首先,电子束加工技术的加速原理是利用高频电场或直流电场对电子进行加速。
通过加速器对电子进行加速,使其获得足够的能量,从而能够对工件表面进行加工。
其次,电子束加工技术的聚焦原理是通过电磁场对电子束进行聚焦。
聚焦系统一般由电磁透镜和偏转系统组成,其中电磁透镜通过调节磁场强度和焦距来实现对电子束的聚焦,而偏转系统则用于控制电子束的运动轨迹,使其能够对工件表面进行精确的加工。
最后,电子束加工技术的工件加工原理是利用高能电子束对工件表面进行瞬时加热和熔化。
当高能电子束聚焦在工件表面时,电子与工件原子之间发生碰撞,使得工件表面的原子发生能量的传递和转换,从而使工件表面被加工的局部瞬时加热和熔化。
电子束加工技术具有以下几个特点和应用领域:1. 高精度加工:电子束加工技术可以控制电子束的位置和能量,从而能够实现对工件表面的高精度加工。
该技术可以用于制造微细结构、光学元件、模具等高精度的工件。
2. 薄壁结构加工:由于电子束加工技术的加热局部,因此可以实现对薄壁结构的加工。
该技术可以用于制造航空航天领域中的燃烧室、气体涡轮叶片等薄壁结构件。
3. 高效率加工:电子束加工技术加工速度快、效率高,可以有效提高生产效率。
该技术可以用于批量加工、大规模生产等领域。
4. 材料熔化温度低:由于工件加工只发生在电子束聚焦的局部区域,因此工件的整体温度相对较低,可以避免材料的过热和变形等问题。
5. 增材制造:电子束加工技术可以直接将粉末熔化成零件,实现对材料的增材制造。
该技术可以用于制造复杂结构的零件和特殊材料的加工。
电子束微细加工技术的发展和应用

电子束微细加工技术的发展和应用电子束微细加工技术是一种高精度、高效率的加工技术,其发展和应用已经超出了传统的加工界限。
本文将从技术原理、应用领域以及未来发展等方面,探讨电子束微细加工技术的现状和前景。
一、技术原理电子束微细加工技术利用电子枪发射的高速电子束,通过密集的电子轰击,把材料表面剥离,并形成所需要的形状。
其主要原理是利用电子束在材料表面的能量转化作用,将部分电子能量转化为材料内部原子的动能,从而产生电离、碰撞、沉积等作用,从而实现微细加工。
该技术的优点在于,可以实现高精度、高速度、高效率、无污染和低成本的微细加工。
同时,电子束微细加工技术还可以通过控制电子束的聚焦、扫描、转移等操作,实现材料的微调和微分形状的加工,从而满足不同材料的加工需求。
二、应用领域电子束微细加工技术已经得到广泛的应用,主要包括微电子、光电子、机械制造、纳米技术等领域。
在微电子领域中,电子束微细加工技术已经成为一种非常重要的工艺。
它可以实现微元件、微结构和微电路的制造,尤其是在微芯片的制造中,电子束微细加工技术可以实现更高的制造精度和分辨率,从而为微芯片的制造提供了有力的支持。
在光电子领域中,电子束微细加工技术一直是光学器件加工的主流技术之一。
它可以实现各种不同的光学元件加工,如光阑、分束器、棱镜、反射镜等,从而为光电子行业提供了更加精密的元器件和设备。
在机械制造领域中,电子束微细加工技术可以实现极小尺寸的微型工件的制造,在航空、汽车、军工等领域中也有广泛应用。
同时,电子束微细加工技术还可以实现不锈钢、钛合金等高强度材料的微细加工,从而提高了材料的利用价值和应用范围。
在纳米技术领域中,电子束微细加工技术可以实现纳米尺寸级别的制造和加工。
它可以制造纳米级别的器件、电路、传感器等。
同时,该技术还可以实现纳米粒子和纳米结构的制造,从而为纳米材料的研究提供了非常关键的加工手段。
三、未来发展未来,随着科学技术的不断进步和应用领域的不断拓展,电子束微细加工技术的应用范围还将不断扩大。
浅析电子束加工工艺特点及其应用

0引言随着科学技术的高速发展,大多数的元器件都要进行超高精度的加工,其数量级可达到纳米级,而电子束加工则在其中起了举足轻重的作用。
电子束加工属于特种加工方法的一种,在工业上的应用已有差不多半个世纪的历史,现已被许多部门完全接受。
最近几年,电子束加工技术日益成熟,应用也是更加广泛。
打孔、焊接、切割、刻蚀、热处理等各个领域都有电子束加工发挥的空间。
其中电子束加工在焊接方面应用最为广泛,也最具竞争力。
1电子束加工的的定义及原理1.1电子束加工的定义电子束加工是利用能量密度非常高的高速电子流,在一定真空度的加工舱中使不同的金属、非金属材料熔化,蒸发和汽化而去除的高能束加工。
1.2电子束加工的原理电子束加工是在真空的环境下,利用加热的阴极发射电子流,使带负电荷的电子流高速飞向阳极,中途通过加速极加速,并经电磁透镜聚焦,使得能量密度高度集中,能够把能量聚集到直径为0.1至10μm的斑点里面,从而获得106至109W/cm2能量密度,在非常短的时间里,将其中的能量转变为热能,使被冲击的材料温度达到数千摄氏度,从而引起被冲击材料的熔化和气化,冲击过程中产生的废弃物质将被真空系统抽出。
简而言之,电子束加工是一种以高能量密度的电子流作为热源,对各种工件材料进行区别于传统机械加工的特殊加工工艺。
2电子束加工的工艺特点因为电子束加工特殊的工作原理,所以使其具有独特的工艺特点。
电子束加工具有许多其他加工方式所不具备的优点,同时它也有一定的缺陷。
2.1电子束加工的优点2.1.1电子束直径很小电子束可以非常微细地聚焦,电子束直径甚至能聚焦到0.01μm。
电子束长度可以达到直径的数十倍以上,因此完全可以进行深孔加工和微细加工。
2.1.2电子束能量密度高电子束集束在直径为几个微米的斑点上时,能量可达到109W/ cm2,足以熔化和气化任何材料。
2.1.3生产效率高因为电子束能量密度很高,并且能量利用率可达90%,所以虽然加工材料、孔的大小有所不同,但总的来说,加工5mm左右厚的工件也就数十秒,非常之短。
电子束加工

电子束加工学院:专业:班级:学号:姓名:接洽方法:电子束加工技巧应用高能量密度的电子束对材料进行工艺处理的一切方法统称为电子束加工。
包含电子束焊接、打孔、别处处理、熔炼、镀膜、物理气相沉积、雕刻、铣切、切割以及电子束曝光等。
个中电子束焊接、打孔、物理气相沉积以及电子束别处处理等在工业上的应用最为广泛,也最具竞争力。
电子束加工作为特种加工方法的一种,在工业上的应用已有30多年的汗青,现已完全被工业部分所接收。
近年来,该技巧赓续成长,在大年夜批量临盆、大年夜型零件制造以及复杂零件的加工方面都显示出其专门的优胜性。
一、电子束加工道理及特点:电子束加工是应用高速电子的冲击动能来加工工件的。
在真空前提下,将具有专门高速度和能量的电子束聚焦到被加工材料上,电子的动能绝大年夜部分改变为热能,是材料局部瞬时熔融、汽化蒸发而去除。
操纵电子束能量密度的大年夜小和能量注入时刻,就能够达到不合的加工目标。
如只使材料局部加热就可进行电子束热处理;使材料局部熔化就可进行电子束焊接;进步电子束能量密度,是材料熔化和汽化,就能够进行打孔、切割等加工;应用较低能量密度的电子束轰击高分子材料时产生化学变更的道理,即可进行电子束光刻加工。
特点:1)电子束能够或许极其微细的聚焦(可达1~0.1um),故可进行微细加工。
2)加工材料的范畴广。
因为电子束能量密度高,可使任何材料瞬时熔化、汽化且机械力的感化极小,不易产生变形和应力,故能加工各类力学机能的导体、半导体和非导体材料。
3)加工在真空中进行,污染少,加工别处不易被氧化。
4)电子束加工须要整套的专用设备和真空体系,价格较贵,故在临盆中受到必定程度的限制。
电子束、离子束、激光束是别处工程范畴内的三大年夜载体,号称三束改性,都具有高能量密度特点。
电子束加工是以激发电子作为载体,离子束则以离子。
离子束加工是一种元素注入过程,具有辐照毁伤、喷丸感化、别处紧缩、形成别处非晶态,形成弥散化合物质点等效应,而电子束与激光束的重要感化在高能量,没有辐照、别处紧缩等特点。
电子束技术与应用

电子束技术与应用电子束技术作为一种新兴的先进加工技术,其独特的性能和技术优势,使得它在材料科学、环境保护、生物科技等领域有着广阔的应用前景。
本文将详细阐述电子束技术的基本原理、特性以及在不同领域的应用。
一、电子束技术的基本原理电子束技术是一种利用电子束的高能量进行材料的表面改性、焊接、切割、钻孔、溅射以及其他加工操作的技术。
其主要包括电子源、聚焦系统、偏转系统、扫描系统和操作系统五大部分。
其中,电子源的主要功能是产生和加速电子,使之具有极高的运动能量;聚焦系统是用来控制电子束的形状和尺寸,使其能够精确地照射在工件上;偏转系统和扫描系统则用于调节电子束的方向和位置,从而实现对工件的精密加工。
二、电子束技术的特性电子束技术具有以下几个显著的特性:1. 高能量:因为电子具有极高的运动能量,所以利用电子束进行加工时可以实现材料的深层加工;2. 高精度:由于电子束的尺寸可以精确控制,所以该技术具有很高的加工精度;3. 宽适应性:电子束技术能够对各种材料进行加工,不论是金属、陶瓷、还是塑料;4. 采用真空环境:为了防止电子与气体的相互碰撞造成散射,电子束技术的应用通常需要在真空环境中进行。
三、电子束技术的应用电子束技术因其优异的技术特性,在多个领域有广泛应用。
1. 材料科学:电子束技术在材料科学中的应用主要表现在材料的合成和处理上,比如用于改善材料的表面硬度、耐磨性、耐腐蚀性等性能,还可以利用电子束技术生产无缺陷的超导材料、纳米复合材料等;2. 环境保护:电子束技术在环保领域的应用主要是利用其高能量将有害物质分解为无害物质,既可以处理有机污染物,也可以处理无机污染物;3. 生物科技:电子束技术在生物科技领域的应用主要体现在对生物样本的形态观察和结构分析上,比如利用电子束技术进行生物组织的切片、染色、固定等操作。
总的来说,电子束技术作为一种精密的高能量加工技术,不仅提高了工件的加工质量,而且为材料科学、环保、生物科技等领域的发展打开了新的可能。
电子束加工技术的研究与应用

电子束加工技术的研究与应用电子束加工技术(Electron Beam Machining)是一种高能量密度的金属加工方法,利用电子束的高速运动和高能量集中,在工件表面瞬间加热并融化材料。
与传统金属加工方法(如机械加工、电火花加工、激光加工)相比,电子束加工具有加工速度快、精度高、能耗低等优点,在航空航天、汽车、电子、医疗等领域均有广泛应用。
本文将着重探讨电子束加工技术的研究进展和应用现状。
一、电子束加工技术的原理和特点电子束加工技术是利用加速器将电子加速到光速附近,并通过特殊的几何形状的电子透镜束缩成一束高速电子束。
当电子束照射到金属表面时,其能量被转化为热能,使金属表面瞬间升温至熔化温度并融化。
同时,电子束在金属中的运动引起金属内部原子的弹性碰撞和不弹性碰撞,从而产生热扩散和塑性变形,最终实现对工件的加工。
电子束加工技术具有以下几个特点:1. 高能量密度:电子束加工的能量密度高达10^9 W/cm2以上,远高于传统加工方法,可以实现对薄膜、微细结构等工艺难度较大的部件的加工。
2. 高精度加工:电子束加工具有高精度、高分辨率和高表面质量的优势,对于形状规则复杂的零件及超精细加工有很强的适应性。
3. 无切削力加工:电子束加工是一种非机械切削类加工方法,不存在机械摩擦或挤压等现象,因此对被加工物的变形、振动、屈曲、拉伸等无任何影响。
4. 处理难加工材料:电子束加工可以处理钨、钼、铌、铬、镍等难加工材料,对黑色金属、色金属、难切削材料以及各种合金均能轻松完成加工。
二、电子束加工技术的研究进展电子束加工技术诞生于20世纪50年代,经过数十年的发展研究,目前已经取得了一系列重要的研究成果。
1.关键技术研究电子束加工技术需要高能量密度、高稳定性的电子束,这需要对电子加速器、透镜束等关键技术进行深入研究。
目前,电子束加工技术主要应用的加速器有线性加速器、驻波加速器和微波加速器等,而电子透镜束的研究则鉴于于电子束聚焦能力的提高和加工精度的进一步提高。
浅析电子束加工工艺特点及其应用

浅析电子束加工工艺特点及其应用作者:何宇来源:《科技视界》2014年第06期【摘要】本文通过对电子束加工的原理及其工艺特点的介绍,阐述了电子束加工这种高速能束加工方式的发展潜力。
并且通过对电子束加工在打孔,焊接,热处理等方面的应用的分析介绍,展现电子束加工在应用方面所具有的特性。
本文主要从这两方面介绍电子束加工,体现其在加工方面的突出优势。
【关键词】电子束;工艺特点;应用0 引言随着科学技术的高速发展,大多数的元器件都要进行超高精度的加工,其数量级可达到纳米级,而电子束加工则在其中起了举足轻重的作用。
电子束加工属于特种加工方法的一种,在工业上的应用已有差不多半个世纪的历史,现已被许多部门完全接受。
最近几年,电子束加工技术日益成熟,应用也是更加广泛。
打孔、焊接、切割、刻蚀、热处理等各个领域都有电子束加工发挥的空间。
其中电子束加工在焊接方面应用最为广泛,也最具竞争力。
1 电子束加工的的定义及原理1.1 电子束加工的定义电子束加工是利用能量密度非常高的高速电子流,在一定真空度的加工舱中使不同的金属、非金属材料熔化,蒸发和汽化而去除的高能束加工。
1.2 电子束加工的原理电子束加工是在真空的环境下,利用加热的阴极发射电子流,使带负电荷的电子流高速飞向阳极,中途通过加速极加速,并经电磁透镜聚焦,使得能量密度高度集中,能够把能量聚集到直径为0.1至10μm的斑点里面,从而获得106至109W/cm2能量密度,在非常短的时间里,将其中的能量转变为热能,使被冲击的材料温度达到数千摄氏度,从而引起被冲击材料的熔化和气化,冲击过程中产生的废弃物质将被真空系统抽出。
简而言之,电子束加工是一种以高能量密度的电子流作为热源,对各种工件材料进行区别于传统机械加工的特殊加工工艺。
2 电子束加工的工艺特点因为电子束加工特殊的工作原理,所以使其具有独特的工艺特点。
电子束加工具有许多其他加工方式所不具备的优点,同时它也有一定的缺陷。
电子束加工技术
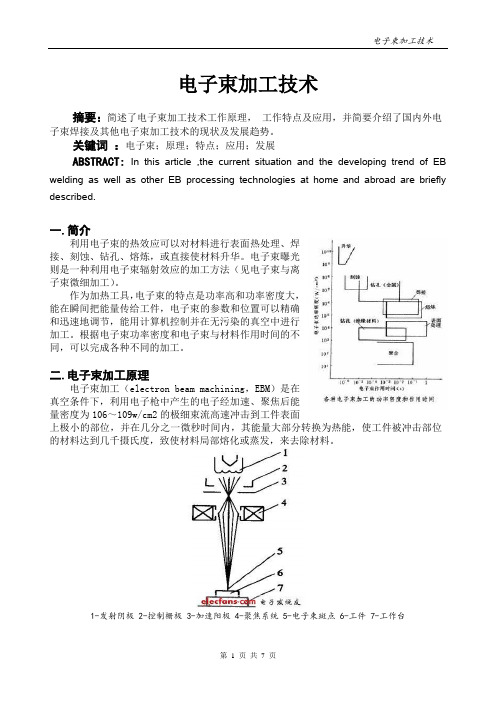
电子束加工技术摘要:简述了电子束加工技术工作原理,工作特点及应用,并简要介绍了国内外电子束焊接及其他电子束加工技术的现状及发展趋势。
关键词:电子束;原理;特点;应用;发展ABSTRACT:In this article ,the current situation and the developing trend of EB welding as well as other EB processing technologies at home and abroad are briefly described.一.简介利用电子束的热效应可以对材料进行表面热处理、焊接、刻蚀、钻孔、熔炼,或直接使材料升华。
电子束曝光则是一种利用电子束辐射效应的加工方法(见电子束与离子束微细加工)。
作为加热工具,电子束的特点是功率高和功率密度大,能在瞬间把能量传给工件,电子束的参数和位置可以精确和迅速地调节,能用计算机控制并在无污染的真空中进行加工。
根据电子束功率密度和电子束与材料作用时间的不同,可以完成各种不同的加工。
二.电子束加工原理电子束加工(electron beam machining,EBM)是在真空条件下,利用电子枪中产生的电子经加速、聚焦后能量密度为106~109w/cm2的极细束流高速冲击到工件表面上极小的部位,并在几分之一微秒时间内,其能量大部分转换为热能,使工件被冲击部位的材料达到几千摄氏度,致使材料局部熔化或蒸发,来去除材料。
1-发射阴极2-控制栅极3-加速阳极4-聚焦系统5-电子束斑点6-工件7-工作台三.电子束加工的优缺点1.优点1)高功率密度属非接触式加工,工件不受机械力作用,很少产生宏观应力变形,同时也不存在工具损耗问题。
2)电子束强度、位置、聚焦可精确控制,电子束通过磁场和电场可在工件上以任何速度行进,便于自动化控制。
3)环境污染少适合加工纯度要求很高的半导体材料及易氧化的金属材料。
4) 加工速度快,如在0.1毫米厚的不锈钢板上穿微小孔每秒可达3000个,切割1毫米厚的钢板速度可达240毫米/分。
- 1、下载文档前请自行甄别文档内容的完整性,平台不提供额外的编辑、内容补充、找答案等附加服务。
- 2、"仅部分预览"的文档,不可在线预览部分如存在完整性等问题,可反馈申请退款(可完整预览的文档不适用该条件!)。
- 3、如文档侵犯您的权益,请联系客服反馈,我们会尽快为您处理(人工客服工作时间:9:00-18:30)。
电子束加工的应用
1. 电子束加工的主要应用
1.1 电子束焊接
电子束焊接是利用电子束作为热源的一种焊接工艺。
电子束焊接的焊缝位置精确可控、焊接质量高、速度快,在核、航空、火箭、电子、汽车等工业中可用作精密焊接。
在重工业中,电子束焊机的功率已达100千瓦,可平焊厚度为200毫米的不锈钢板。
对大工件焊接时须采用大体积真空室,或在焊接处形成可移动的局部真空。
1. 电子束焊接在航空航天工业的应用[2]
作为一种现代先进的焊接技术,电子束焊接首先进入的就是航空航天领域。
小到微型压力传感器,大到航天器外壳,航空航天零部件所用材料的独特性及焊接要求的特殊性, 使得电子束焊接迅速成为这些重要零部件加工所必须采用的工艺,大量应用于飞机重要承力件和发动机转子部件的焊接上。
美国的F-22战斗机机身段上,由电子束焊接的钛合金焊缝长度达87.6mm,厚度为6.4-25mm。
另外,电子束焊接技术还用来焊接汽轮机喷管隔板、高温蒸汽机转轴、汽轮机定子、燃气涡轮叶片、航空发动机转子、摇臂组件、机匣、功率轴、飞机梁、起落架, 导弹壳体、航弹尾翼等。
2.电子束焊接在汽车工业的应用[3]
20世纪60年代,日本富士重工和美国通用汽车公司率先采用电子束焊接变速箱齿轮和飞轮,此后电子束焊接便吹响了进军汽车工业的号角。
目前,几乎所有的国际汽车制造公司都引入了电子束焊接设备。
德国大众汽车公司仅一个齿轮加工车间内, 就装有20余台电子束焊机。
汽车生产中,电子束焊接多用来加工发动机、变速器、行走系等处的零件,这些零件的机械加工量相对较少,符合电子束焊接的经济性要求。
比如[],汽车发动机中的配电盘凸轮必须是渗氮后焊接,因其对接材料不同(低碳渗氮钢-SAE1144),采用其它接合方法比较困难,故采用电子束焊接较为合适;柴油机的预燃室过去采用钎焊(对接材料不锈钢-耐热钢),改用电子束焊后提高了质
量, 也降低了成本;起动马达整流子铜环采用电子束焊后,可同时高速焊接数十个,生产率大大提高,成本大幅度下降;转向车轮部分的球窝接头采用电子束焊接,施焊速度非常快, 热影响很小,能很好地防止球接头中封装的黄油受热变质;转向柱管的焊接要求变形小、焊接表面光滑,故也适宜采用电子束焊接。
另外,从生产成本考虑,汽车工业比航天工业更多地开发和利用非真空电子束焊接。
美国最早把非真空电子束焊接引入到批量汽车零件的生产中,欧洲和日本汽车制造商也相继开始采用该技术。
非真空电子束焊接突破了“真空”的局限,可以在汽车生产线上连续进行,对于现在汽车上广泛使用的铝合金零件,非真空电子束焊接依然可以获得质量良好的焊接接头。
由此可见,电子束焊接热影响小、变形小,可以在工件精加工后进行焊接,又能够实现异种金属焊接。
因此,复杂的工件就可以分成几个简单的零件, 每个零件可以单独使用合适的材料和方法加工制造,最后利用电子束焊接成一个完整的工件, 从而可以获得理想的技术性能和显著的经济效益,这就有利于达到汽车生产降低成本和轻量化的要求
3. 电子束焊接在电子仪表工业的应用[4]
在这一领域里,利用电子束焊接精密可控的独特性能,更容易实现微细精密焊接,同时又能保证焊缝纯净、无污染、不氧化。
电子管阴极是发射电子的心脏部件,性能要求高,一般由钨、钼、钽等高熔点金属或其合金材料组成。
采用真空电子束焊接可获得光滑牢固的焊接,接头不氧化、无夹渣、不脆不裂。
光电管壳由纤维玻璃屏、高铬钢盘、可伐合金筒等组成,内部光电阴极是一种非常敏感的材料,封口焊接作为制管工艺的最后一道工序,不得使粘接的玻璃焊料与纤维屏受伤, 而且不能出现氧化层。
采用真空电子束焊接可获得高质量的焊缝, 光滑平整、无氧化、而且气密性好。
传感器封装焊接。
某种遥测压力传感器似一个金属电子管, 内部装有一组敏感元件和电子元件,为了使该传感器工作稳定可靠, 采用腔体内部具有一定真空度的结构。
该传感器不锈钢外壳上留有一个出气孔。
焊接时将传感器置于焊机真空室内, 当达到一定真空度时, 先焊接电极盘与外壳, 再封焊出气孔。
电子束焊接成品率很高, 性能测试表明各项指标均达到设计标准, 并且未发现
漂移现象,说明缝焊与孔焊的气密性均良好, 内腔具有了一定真空度, 内部元件完好无损。
电子束焊接的稳定性很高, 可用于薄件或超薄件的穿透焊或半穿透焊, 焊接规范可以恰到好处。
应变传感器的半穿透焊接。
某种应变传感器采取薄片与薄壁圆管在外侧相焊的结构, 圆管内充有MgO粉和应变丝。
片与管壁的厚度仅0.1-0.15mm,在外侧焊接时只能半透, 不能全透, 不然薄壁圆管出洞造成管内的MgO溅散而报废。
电子束焊接工艺规范临界, 稳定性好, 获得了满意的焊缝。
4. 电子束焊接在汽轮机制造业的应用[5]
采用电子束焊接汽轮机通用定子,能较好地解决隔板处异种材料焊接、磁性材料焊接的问题,简化工艺流程,提高接头质量和工作效率。
因为隔板由叶栅分别和围带、隔板体组焊成,以前的工艺是采用埋弧焊、气体保护焊,往往热变形和热应力较难控制,需要进一步的后续处理,工艺参数繁琐。
对于汽轮机调速级叶片,为了解决加工困难并提高生产效率,将两个或三个单只叶片组合在一起进行电子束焊接,组成两联、三联调速级叶片,这种方法已取得理想的结果,同时还成功地应用在叶片的修复焊接上。
大型汽轮机所用的重型齿轮,相对通用定子和叶片来说,存在着劳动生产率低、焊接变形大、接头质量不易保证、消耗大、劳动条件恶劣等问题。
常规焊接工艺始终无法突破这一瓶颈,采用大型、大功率电子束焊机焊接重型齿轮才能较好地解决上述问题。
1.2 电子束蚀刻和电子束钻孔
用聚焦方法得到很细的、功率密度为 106~108W/cm²的电子束周期地轰击材料表面的固定点,适当控制电子束轰击时间和休止时间的比例,可使被轰击处的材料迅速蒸发而避免周围材料的熔化,这样就可以实现电子束刻蚀、钻孔或切割。
.电子束可在厚度为0.1~6毫米的任何材料的薄片上钻直径为1至几百微米的孔,能获得很大的深度-孔径比。
1.3 电子束曝光
电子束曝光是先利用低功率密度的电子束照射作为电致抗蚀剂的高分子材料,入射电子与高分子相撞,使分子的链被切断或重新聚合而引起的分子量的变化,这个步骤称为电子束曝光。
1.4 电子束热处理
电子束热处理也是把电子束作为热源,适当控制电子束的功率密度,使金属表面受热但不熔化,从而达到热处理目的。