信钢12X4规格切分轧制技术
材料成型工艺学-轧制原理与工艺基础

z型钢:棒线材无头轧制 z特点:连续生产,提高成材率,简化控制系
统,提高产品质量
2007年10月24日 5
材料成形工艺学(中)——轧制原理
绪 论
5. 采用柔性化的轧制技术
z多品种,小批量,短交货期 → 柔性化轧
制技术:
z热轧自由程序轧制技术 z型钢自由程序轧制:无孔型平辊轧制(H 型钢延伸机组) 成品孔,成品前孔共用
2007年10月24日
ห้องสมุดไป่ตู้
23
材料成形工艺学(中)——轧制原理
1 轧制过程的基本概念
1.1 变形区基本参数
1.1.2 轧制变形的表示方法
1.1.2.1 相对变形量
H −h 100 % H b−B 100 % B l−L 100% L
H −h 100 % h b−B 100 % b l−L 100% l
ADB、CEG 流动产生宽展 变形区 横向流动
2007年10月24日
30
材料成形工艺学(中)——轧制原理
1 轧制过程的基本概念
1.2 金属在变形区内的流动规律
1.2.2 沿轧制宽度方向上的流动规律
l h
较大时(薄轧件),受表面外摩擦影响,出现单鼓变形
lh
<0.5时(厚轧件),变形不能深透到整个断面高度,出现双鼓变形
2
B1 B3
2
的平方
B1C = 2 R B1 B3
如图
18
2007年10月24日
材料成形工艺学(中)——轧制原理
1 轧制过程的基本概念
Δh DB3 = + Δ1 + Δ 2 2
B1 B3 = Δ1 + Δ 2
两线切分轧制技术在阳春新钢铁轧钢厂的应用
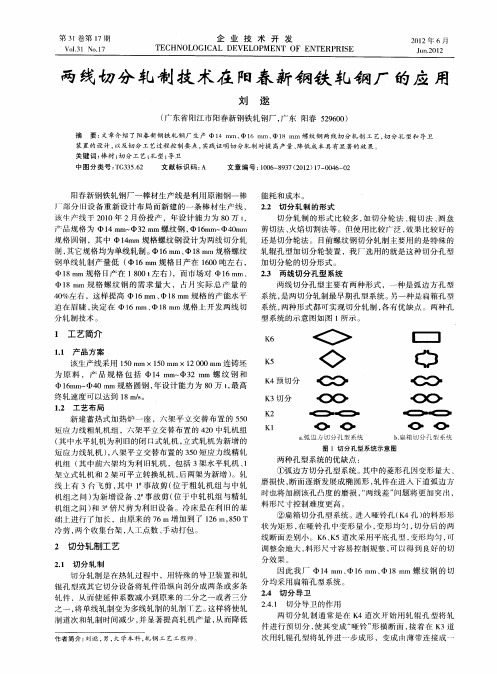
刀处易粘钢 , 从而导致堆钢事故的发生 , 其原因大部分是 前端靠近轧辊处有“ 鼻尖 ” 起引导作用 , 一对切分轮处于 因 为 导 卫 横 梁 标 高 问题 导 致 轧 件 与 导 卫 内 孔 壁 摩 擦 所 中间段 来 撕 开 轧件 , 分 轮后 有 一 把 切 分 刀 , 切 当切 分 轮 未 致 , 因此对导卫对中的安装提出了更高度 的要求 。
12 工 艺布 局 .
K5
◇
.: _ = .: 一 | _ =’ |
C= : l
. I c <
.==I.: . _ = 1 =: | 一| _
K 预切分 4 K 切分 3
K 2
新建蓄热式加热 炉一座 ,六架平立交替 布置 的 50 5 短 应 力线 粗 轧 机 组 ,六 架 平 立交 替 布 置 的 40中轧机 组 2
更 换 成 双通 道 过 渡导 槽 。
从切分道次( 3 出来 的两根并联 圆轧件之 间的连接 K) 3 实际生产控制措施 带 厚度 一 般 为 1m 楔 形 的切 分 轮 边缘 宽度 为 1 m, m, .m 5 而轧件最后是靠切分轮撕开 ,因此切分轮的角度与轧辊
孔 型切 分 楔 的 角度 必 须 严 格 配合 才 能 保 证撕 开 的正 常 完 成 。 型 切分 楔 角 须满 足 轧 件变 形 的要 求 , 切 分轮 的 角 孔 而 度 则直 接 对 能否 将 轧 件 “ 开 ” 切 分 导 卫 的寿 命 产 生 影 撕 及
将 轧件 彻 底撕 开时 , 可通 过 切 分 刀切 开 。 8 1H进 口为滑 动
⑥对于 1H出口扭转导卫扭转辊的角度易跑偏难 紧 8 导 卫 , 口为 R O O * 出 T — B 2型扭 转 导卫 。1H进 口为滚 动 导 固 的问 题 ,采 用 调 整好 角 度 后 再 直 接焊 接 死 的办 法来 得 9 卫 , 口为 方 形滑 动 导卫 。详 细情 况 如 表 1 示 。 出 所 到 了解 决 , 少 了堆 钢 事 故 的发 生 。 减 25 切 分 孔型 的 布 置 . ⑦针对机架及活套 间双通道导槽设计不合理导致频 切分孔型一般布置在精轧道次 ,结合我厂精轧机组 繁堆钢事故 的问题 ,通过优化导槽设计最终得到了很好 的布置形式 ,将 1#和 2#立式轧机 空过 ,7 6 0 1#和 1#平 的解 决 。 8 立可转换轧机全部水平使用 ,9 轧机为终轧道次。孔型 1# 4 效 果 在各 个 机 架 问 的布 置情 况 如 表 2 示 。 所 2 活套 的使 用 及 导槽 的改 进 . 6 自 2 1 年 6月份 开 始 , 步 在 中1 m 、 l m、 00 逐 6m 4m
Φ12螺纹钢五切分技术浅析

2)双预切孔型系统。精轧 13#轧机孔型,16#轧机为切分孔型,17# 轧机为椭圆孔型,18#轧机为成品孔型。
1)切分位置选择。采用 13#一预切、15#二预切、16#切分的 切分方式,切分后的五线轧件经 17#扭转、18#轧制后,经圆管引 导进入加速 辊 道、飞 剪 剪 切;随 后,经 变 频 辊 道 上 冷 床,完 成 卸钢。
2)切分方式。基本原理:利用 16#出口切分导卫前切分轮 切开成“1+3+1”线并联轧件,然后通过后切分轮把“1+3+1” 线并联轧件,切成“1+1+1+1+1”五根单个轧件模式。 2.2 双预切轧制工艺及孔型系统
基础研究[D].北京:北京科技大学,2017.
172
技术应用
TECHNOLOGY AND MARKET Vol.26,No.3,2019
Φ12螺纹钢五切分技术浅析
南书刚
(安钢集团信阳钢铁有限责任公司 炼轧厂,河南 信阳 464194)
摘 要:通过对 Φ12×5双预切工艺的开发、实施,大大提升了机时产量、质量等各项经济技术指标。 关键词:五切分;双预切;技术改造 doi:10.3969/j.issn.1006-8554.2019.03.096
3)切分孔:变形需稳定,延伸系数在 1.0~1.2。孔型充满 度要好,充满度不好,会导致 16#出口切分导卫的切分刀片因负 荷过大破裂。孔型号 1660。
4)立箱孔:立箱孔型延伸系数应较小,基本无宽展,起到轧 件微调平整规范料形的作用,①12#立箱要保证槽底充满度,料 形规范,确保稳定进入一预切道次。②12#立箱压下量不得过 大,不得产生扭转、料转等现象。③12#、13#、15#、16#孔型样板 及五切孔型图表,对上线轧辊进行逐一核对,确保轧辊孔型正 确。 五切分线差调整
轧钢厂棒材轧制工艺与装备

250kN.m 300kN.m
600kW 600-1200r/min
610mm 520mm 700mm 660mm 520mm 280mm
5H 2800kN 300kN.m
6V
2800kN
300KN. m
㈡ 轧制
轧钢厂棒材轧制工艺
3、中轧机组(7#~12#)
中轧机组:420mm×6,平立交替布置。 7#、9#、11#水平轧机为利旧的二辊闭口式轧机,8#、10#、12#立式轧 机为二辊短应力线轧机,立式轧机采用上传动,每架轧机由1台直流电机 单独传动,轧机横移距离±300mm,轧辊轴向调整量±3mm,最大轧制 力1800kN,辊颈直径220mm。
二辊短应力线550轧机
轧钢厂棒材轧制工艺
粗轧轧机性能及技术参数见下表:
项目 最大轧制力 最大轧制力矩
电机功率 电机转速 轧辊最大辊径 轧辊最小辊径 轧辊辊身长度 最大轧辊中心距 最小轧辊中心距 机架移动行程
1H 2800kN 250kN.m
2V
2800kN
300kN. m
3H
4V
2800kN 2800kN
轧钢厂棒材轧制工艺
一、产品大纲
设计年产量:80万吨/年。
品种和规格:
序
Ф16-Ф32(40)mm 热轧 号
光面圆钢;Ф14-Ф32mm
热轧螺纹钢筋。
1
产品以螺纹钢筋为主, 2 其比例约占60%。
3
规格 mm Ф14 Ф16 Ф18-25
品种
螺纹 钢筋
光面 圆钢
40000
0
80000 60000
200000 140000
轧钢厂棒材轧制工艺
㈡ 轧制
结合阳春棒材厂系搬迁湘钢一棒材厂现有轧机的实际情况,本着能用的 轧机尽量利用的原则,并进行适当的改造,最终确定如下轧机布置方案:
轧钢厂棒材轧制工艺与装备

t/a
%
480000
60
320000
40
800000
—
—
100
轧钢厂棒材轧制工艺
按产品钢种分,钢种的比例见下表 :
序号
钢
种
比例(%)
数量(t/a)
1
2 合计
碳素结构钢(Q195、Q235)
低合金钢(20MnSi、20MnSiV)
40
60 100
320000
480000 800000
注:预留优质碳素结构钢、合金结构钢、易切削钢。 目前螺纹钢占比达到了87%左右。
轧钢厂棒材轧制工艺
生产工艺及主要设备
㈠ 坯料加热
加热炉型式: 炉内悬臂辊道侧进侧出纯高炉煤气双 蓄热三段步进梁式连续加热炉 炉子尺寸: 炉子有效长度22.960m; 炉子有效宽度12.760m; 原料尺寸:150*150*12000mm; 装炉温度:常温冷装和500~800℃直接 热送; 钢坯加热温度:950~1150℃; 燃料种类:高炉煤气
加热炉上料系统可以实现钢坯的冷装和热装。采取热装时,热坯由热送辊道从 炼钢厂出坯跨运至棒材车间,由取钢装置将钢坯单根从辊道上取至提升机,然 后再由提升机将钢坯逐根提升到高架平台上,由移出装置将钢坯平托到钢坯台 架上,并经称重、测长,合格的钢坯送往加热炉,不合格钢坯由移出装置剔除 到废坯收集台架上。采取冷装时,既可由辊道、提升机将冷坯提升到上料台架 上,又可由车间吊车直接将钢坯吊至上料台架上,在上料台架上的钢坯经人工 检查外形和表面质量,并经称重、测长,合格的钢坯单根送往加热炉,不合格
2、变形制度 在一定条件下,完成坯料到成品的变形过程。主 要内容是确定总的变形量和道次变形量。小型棒线 材变形制度与其他型钢一样是通过孔型设计来实现。 轧钢是坯料在旋转的轧辊之间产生塑性变形。在 变形过程中,坯料厚度变薄,宽度少许增加,长度 显著加长。 3、速度制度 速度制度就是确定各道次的轧制速度。轧制速度高,轧机产量就大。但速 度并不是越高越好。太高了增加电力消耗,且故障增多。处理故障影响了 生产,产量反而下降。所以,要结合电动机能力,自动化水平,轧机设备 的机械化程度来制定速度制度,连轧机各架轧机的速度确定就属于速度制 度,轧制速度是指各机架的轧辊线速度,计算公式为v=πDn/60
螺纹钢双切分工艺孔型优化实践

螺纹钢双切分工艺孔型优化实践发布时间:2022-06-15T02:24:46.097Z 来源:《科学与技术》2022年2月4期作者:蒲肖强、杨林、赵天喜[导读] 双切分轧制技术目前在国内各钢厂应用广泛,较单线轧制产量提升明显蒲肖强、杨林、赵天喜新疆天山钢铁巴州有限公司轧钢厂摘要:双切分轧制技术目前在国内各钢厂应用广泛,较单线轧制产量提升明显,特别是中大规格双切分轧制技术的运用,促使棒材线产能及生产效率大幅度提升,但双切分生产工艺技术在日常生产中存在着部分工艺技术难点,导致钢材成品存在表面缺陷,本文探究了从工艺孔型优化解决切分螺纹钢表面质量问题。
关键词:孔型优化;降本增效;产品质量引言巴州钢铁轧钢厂棒材生产线于2012年3月份投产,采用了控冷控轧技术、多线切分技术等新工艺、新技术。
全线有18架轧机均采用短应力高强度轧机,并采用平立交替布置。
其中中轧机组有一组活套轧制,中轧机组与精轧机机组间配有穿水装置,精轧机有三组活套轧制,精轧机组后配有穿水装置,实现控冷控轧工艺。
该生产线采用节能、环保、新型步进梁蓄热式加热炉,以160mm*160mm*12000mm连铸坯为原料,采用冷热钢坯交替送轧,生产Φ12.0-Φ36mm热轧带肋钢筋和煤矿支护用高强度锚杆钢,具备生产Φ12~Φ50mm热轧直条圆钢的能力。
其中Φ12-Φ16四切分、Φ18-Φ22双切分,有效平衡大小规格产品产量。
精整区域钢材收集实现设备无人化操作,提高生产效率及产品包装质量。
1 棒材切分轧制技术在实践应用中发展情况切分轧制在热轧钢坯经过特殊的轧辊孔型和导卫装置中切分轮将一根轧件沿纵向切成两根以上轧件,进而轧出两根以上成品轧件的轧制切分工艺,早在100多年前,国外已研究出废旧钢轨的切分轧制。
但是在实践应用中发展不容乐观,应用技术非常落后。
70年代中期,加拿大钢铁公司首先在连续式小型轧机上成功地用切分轧制工艺生产了带肋钢筋和光圆钢筋,并开拓了切分轧制的新领域。
棒材车间工艺简介
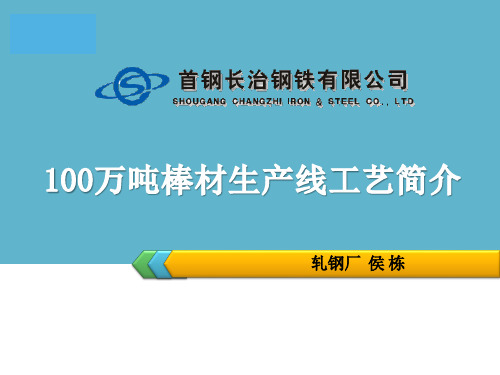
剪切温度:常温~500℃
2016年2月29日星期一
传动电机:160kW
1500rpm
4、850t冷剪
2016年2月29日星期一
3#冷却段
相变点停止冷却 后续控制冷却
2016年2月29日星期一
2、控轧控冷技术
适当控轧 适当控轧
超快速冷却
相变点停止冷却
后续控制冷却
2016年2月29日星期一
3、多线切分轧制技术
多线切分轧制技术
Ф 16~Ф 20mm螺纹钢采用二切分轧制 Ф 12、 Ф 14mm螺纹钢采用四线切分轧制 四线切分轧制技术是在两线和三线切分轧制技术的基础上开发出来的。 四线切分轧制工艺是把加热后的坯料先轧制成扁坯,然后再利用孔型系统
织和力学性能。
即,通过采用适当控轧 + 超快速冷却 + 接近相变点温度停止冷却 + 后续冷却路径控制,通过降低合金元素使用量、适当提高终轧温度,来实
现资源节约型、节能减排型的绿色钢铁产品制造过程。
新一代 MCP 新一代 TMCP
适当控轧 适当控轧
+
超快速冷却 超快速冷却 + 相变点停止冷却
+
后续控制冷却
蓄热式燃烧技术又称高温燃
烧技术,其原理是利用蓄热体吸收 高温烟气的热量,将空气加热到
1000 ℃ ,从而最大程度吸收烟气
余热,提高燃烧效率,节省燃料。 该技术是通过蓄热式烧嘴来实现高 温燃烧技术。
2012年10月31日星期三
1、加热炉——蓄热式燃烧技术
工作原理:对称布置的两个烧嘴交替工作,A 侧烧嘴燃烧时,B 侧烧 嘴关闭,B 侧烧嘴通过引风机将炉内高温烟气吸进烧嘴,从而将蓄热体加 热;A 侧烧嘴燃烧 60 秒之后,A 侧烧嘴关闭,助燃空气进入 B 侧烧嘴, 当空气通过蓄热体时,被快速加热到 1000 ℃ ,随后喷入炉内,与高炉煤 气混合燃烧。
Φ16规格螺纹钢四切分轧制技术的开发与实现
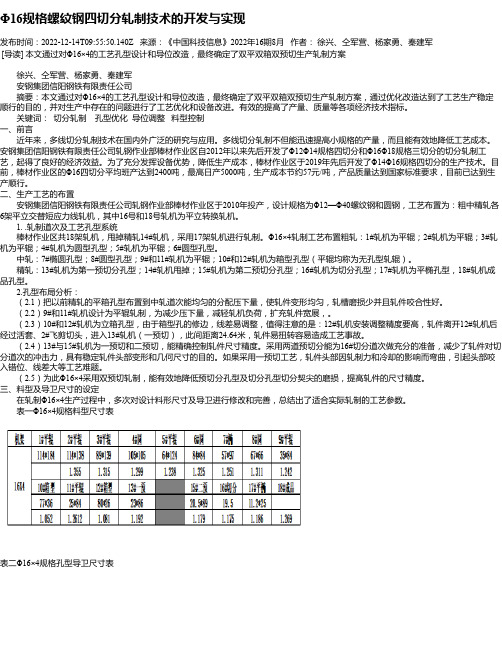
Φ16规格螺纹钢四切分轧制技术的开发与实现发布时间:2022-12-14T09:55:50.140Z 来源:《中国科技信息》2022年16期8月作者:徐兴、仝军营、杨家勇、秦建军[导读] 本文通过对Φ16×4的工艺孔型设计和导位改造,最终确定了双平双箱双预切生产轧制方案徐兴、仝军营、杨家勇、秦建军安钢集团信阳钢铁有限责任公司摘要:本文通过对Φ16×4的工艺孔型设计和导位改造,最终确定了双平双箱双预切生产轧制方案,通过优化改造达到了工艺生产稳定顺行的目的,并对生产中存在的问题进行了工艺优化和设备改进。
有效的提高了产量、质量等各项经济技术指标。
关键词:切分轧制孔型优化导位调整料型控制一、前言近年来,多线切分轧制技术在国内外广泛的研究与应用。
多线切分轧制不但能迅速提高小规格的产量,而且能有效地降低工艺成本。
安钢集团信阳钢铁有限责任公司轧钢作业部棒材作业区自2012年以来先后开发了Φ12Φ14规格四切分和Φ16Φ18规格三切分的切分轧制工艺,起得了良好的经济效益。
为了充分发挥设备优势,降低生产成本,棒材作业区于2019年先后开发了Φ14Φ16规格四切分的生产技术。
目前,棒材作业区的Φ16四切分平均班产达到2400吨,最高日产5000吨,生产成本节约57元/吨,产品质量达到国家标准要求,目前已达到生产顺行。
二、生产工艺的布置安钢集团信阳钢铁有限责任公司轧钢作业部棒材作业区于2010年投产,设计规格为Φ12—Φ40螺纹钢和圆钢,工艺布置为:粗中精轧各6架平立交替短应力线轧机,其中16号和18号轧机为平立转换轧机。
1. .轧制道次及工艺孔型系统棒材作业区共18架轧机,甩掉精轧14#轧机,采用17架轧机进行轧制。
Φ16×4轧制工艺布置粗轧:1#轧机为平辊;2#轧机为平辊;3#轧机为平辊;4#轧机为圆型孔型;5#轧机为平辊;6#圆型孔型。
中轧:7#椭圆孔型;8#圆型孔型;9#和11#轧机为平辊;10#和12#轧机为箱型孔型(平辊均称为无孔型轧辊)。
连轧线多线切分轧制技术的工艺研究及设计
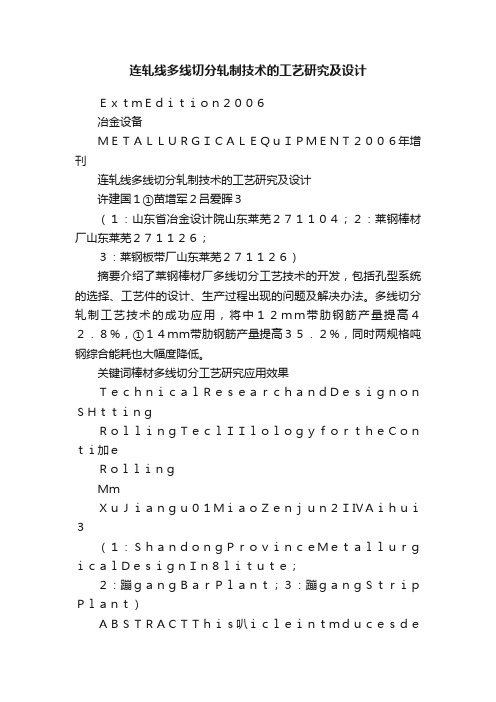
连轧线多线切分轧制技术的工艺研究及设计ExtmEdition2006冶金设备METALLURGICALEQuIPMENT2006年增刊连轧线多线切分轧制技术的工艺研究及设计许建国1①苗增军2吕爱晖3(1:山东省冶金设计院山东莱芜271104;2:莱钢棒材厂山东莱芜271126;3:莱钢板带厂山东莱芜271126)摘要介绍了莱钢棒材厂多线切分工艺技术的开发,包括孔型系统的选择、工艺件的设计、生产过程出现的问题及解决办法。
多线切分轧制工艺技术的成功应用,将中12mm带肋钢筋产量提高42.8%,①14mm带肋钢筋产量提高35.2%,同时两规格吨钢综合能耗也大幅度降低。
关键词棒材多线切分工艺研究应用效果TechnicalResearchandDesignonSHttingRollingTeclIIlologyfortheConti加eRollingMmXuJiangu01MiaoZenjun2IⅣAihui3(1:ShandongProvinceMetallurgicalDesignIn8litute;2:蹦gangBarPlant;3:蹦gangStripPlant)ABSTRACTThis叭icleintmducesdevel叩mentofsliltingmllingtechnology,includingthedesi阴ofthepasssystemandtechnicalparts,theproblemsandsetdemethodsduringproduceprocess.Thesliningrollingtechnol—og)rwasappliedsosuccessfullythattheoutputof垂12mmribbedbarrises42.8%and咖14mmribbedbarrises35.2%.Atthesametime,genemlenergyconsumptionpertonsteelw鹊reducedgready.KEYWoRDSBarsittingmllingtechnology7rechnicalresearchApplicatione艉ct1前言莱钢棒材厂是以生产①12mm~叫Omm带肋钢筋,中14mm~叫Omm圆钢为主的棒材生产厂家。
轧钢技术的分类及在生产中的应用

轧钢技术的分类及在生产中的应用随着经济全球化的发展以及市场经济的发展对于钢产量以及市场要求都特别严格。
我们国家粗钢虽然产量大但利用率不高,目前我国钢材的产量日趋减少,生产效率也偏低,所以每年需从国外进口部分钢材,这样下来我们国家的钢铁生产量就要低于世界平均水平,但是钢铁是我国生产生活都能用到的基础原料,对工业消耗和生活水平有着很大的影响,如果我国的轧钢技术不能提高和创新,就很难拉动国家的经济水平。
所以轧钢技术的优化和创新技术就显得越来越重要了,所以我们需要创新节能环保的轧钢技术并培养专业的技术人员,以便推动我们国家又好又快发展。
以下就轧钢技术的分类及在生产中的应用做一些分析介绍。
with the development of economic globalization and the development of market economy for steel production and market requirements are particularly strict. Our country crude steel although yield but utilization rate is not high, at present, China's steel production is decreasing day by day, the production efficiency is low, so each year from imported parts, steel, so down our country's steel production capacity will be lower than the average level in the world, but steel is basic raw materials of the production and life of our country all can use, has a great impact on industrial consumption and living standards, if China's steel rolling technology can not improve and innovation, it is difficult to pull the economy level of our country. So the optimization and innovation of steel rolling technology is becoming more and more important, so we need to innovate energy saving and environmental protection of steel rolling technology and train professional and technical personnel, in order to promote the sound and fast development of our country. The following is the classification of rolling technology and the application in production to do some analysis.一、轧钢技术的分类情况我们国家生产钢铁的企业众多,钢铁的品种也不尽相同也各有各的特点。
φ12mm螺纹钢三切分工艺中成品中间线折叠的产生原因及消除方法的分析

φ12mm螺纹钢三切分工艺中成品中间线折叠的产生原因及消除方法的分析φ12mm螺纹钢三切分工艺中成品中间线折叠的产生原因及消除方法的分析摘要:介绍了柳钢棒线厂第二棒材生产线φ12mm螺纹钢三切分轧制的生产现状、工艺流程、技术方案,并对轧制过程中成品中间线产生的折叠进行原因以及消除方法的分析。
关键词:三切分孔型料型折叠1 前言柳钢棒线厂于2004年建成投产第二棒材生产线,最初设计年产量60万吨,设计最高速度为18m/s,生产工艺流程为:原料准备—〉加热—〉粗轧—〉1#飞剪—〉中轧—〉2#飞剪—〉精轧—〉穿水冷却—〉3#飞剪—〉裙板—〉冷床—〉冷剪—〉成品收集—〉打捆—〉称重—〉检验—〉入库发货。
经过技术集成与优化,目前已具备年产100万吨的生产能力。
主要产品为φ12—φ25螺纹钢,2012年前主要以两线切分工艺为主,两切分技术在此生产线已经非常成熟。
由于市场形势的需要,φ12螺纹钢在市场上比较畅销,但两切分的机时产量较低,生产线的能力得不到充分发挥,为满足市场需求,落实“优质增效”,实现效益最大化,今年开发三切分轧制工艺生产φ12螺纹钢。
2 成品中间线产生折叠原因的分析在初试φ12mm螺纹钢三切分时,成品出现了横肋及内径折叠等表面缺陷,中间线尤为明显,有的是断续的,有的是通条的,造成了大量的成品判废,对产量以及其它技术经济指标产生了较大的影响。
通过分析认为二棒轧机机架间距较短,扭转导卫不易安装,轧件出K3后中间线较难实现扭转,经过取样观察分析,发现经K3出来的轧件在切分轨迹上有二次甚至三次切痕(如图1所示),此切痕为成品表面缺陷产生的根本原因。
由于K6和K4以及K3的切分轨迹不重合,K3切分带没有沿着K4及K6的轨迹来切分,加上K3出口刀片的作用,造成了中间线两侧表面切痕,而中间线很难实现扭转,于是在横肋上出现了折叠的现象,严重的时候则会在内径上出现折叠。
图1 经K3切分过的实物图分析认为产生二次切痕的原因有:①切分带、孔槽磨损②K3、K4、K5出来的轧件切分轨迹不重合,产生重复切痕。
- 1、下载文档前请自行甄别文档内容的完整性,平台不提供额外的编辑、内容补充、找答案等附加服务。
- 2、"仅部分预览"的文档,不可在线预览部分如存在完整性等问题,可反馈申请退款(可完整预览的文档不适用该条件!)。
- 3、如文档侵犯您的权益,请联系客服反馈,我们会尽快为您处理(人工客服工作时间:9:00-18:30)。
信钢12X4规格切分轧制二棒车间2012.12.12信钢12X4规格切分轧制信钢精棒线生产能力为100万吨/年、最高轧制速度15米/秒,采用150毫米X12米钢坯。
主要产品Φ12mm---Φ25mm的热轧带肋钢筋。
全线轧机共有18架,呈平立交替布置(其中16#机架、18#机架为平立可转换轧机)。
由粗轧机组Φ610X6架、中轧机组Φ480X6架、精轧机组Φ370X6架组成,全部为高刚度短应力线轧机。
粗轧机组1#孔型为箱型、2#孔型为方形、其余为椭—圆交替孔型,中轧机组孔型为椭—圆交替孔型,精轧机组采用活套无张力轧制,有效的降低了辊耗、提高了孔型共用性。
中轧后设有预穿水装置,精轧后设有高强度、耐磨冷却穿水管装置,实现控冷控轧轧制工艺,提高钢材的组织和性能。
产品规格包括:其中Φ12 毫米、Φ14 毫米螺纹钢采用三线切分轧制技术生产,Φ16~20 毫米螺纹钢采用两线切分轧制技术生产,Φ22 毫米、Φ25 毫米螺纹钢进行单线轧制。
2011年7月引进四线切分轧制技术生产Φ12 毫米螺纹钢。
目前,该生产线两线、三线和四线切分的生产能力全部达到了日产3000吨以上,其中Φ18 毫米、Φ20 毫米螺纹钢最高日产达到日产4000吨以上。
四线切分轧制技术在信钢的试生产情况信钢连轧精棒生产线于2011年7 月采用四线切分轧制技术试生产12 毫米螺纹钢,设计终轧速度14米/秒, 机时产量为150 吨/小时,采用17架轧机、双预切轧制。
在调试生产的五个班次中,共生产出了合格产品3018吨。
在随后的六个月中,共生产了12 毫米螺纹钢46960 吨,由于存在轧机堆钢多、加速辊道摆动堆钢、裙板乱钢频繁和质量不稳定等问题而达不到设计水平,作业率低于60%,日产量徘徊在2000 吨以下,没有把四线切分轧制工艺的优越性充分发挥出来。
上述情况说明我们在这六个月的试生产期间,各类事故量较高、各种技术经济指标较低,没有真正掌握四线切分轧制技术的诀窍。
为此,我们必须对四线切分轧制技术进行充分的分析,消化吸收并优化创新。
根据生产中各阶段事故发生集中区域分为:一.12#为扁形孔进入13#时因两架轧机距离26米,容易出现扭转造成13#不进堆钢。
原因分析:12#为立轧容易出现辊错。
解决方法:1.在机架上加焊两个双孔立板、并装四根顶丝可快速进行辊错校正。
2.在两架轧机间辊道上安装2-3个压板强制对扭转轧件进行校正。
3.12#轧槽槽底磨损不均匀易出现扭转,一般轧制5000吨-7000吨进行轧槽更换。
4.11#平辊磨损较快、容易出现扭转,一般3000吨-4000吨进行轧槽更换。
5.12#入口导辊间距过大或导卫与轧槽不在同一中心线。
6.11#轧件宽展与12#轧件上下面尺寸相差4毫米以上同样容易出现扭转。
二.切分刀粘铁皮出现单线窜钢或顶切分导卫造成堆钢。
原因分析:1.切分导卫鼻尖、切分轮中心线、切分刀中心线不在同一中心。
解决方法:安装、调整切分导卫时一定要紧固好各类螺栓,不允许出现上下或左右窜动。
2.切分轮间隙调整过大或过小。
解决方法:1.双切分轮间隙一般调整在0.3毫米-0.5毫米(部分厂家调整在0.1毫米)。
出现两长刀外侧粘铁皮一般为双轮间隙过大造成。
出现两外侧轧件头部在轧出切分导卫时撞击接料口两侧较为严重,一般为双轮间隙过小造成。
2.单切分轮间隙一般调整在1.0毫米-1.2毫米(部分厂家调整在0.5)。
出现双刀内侧粘铁皮一般为单轮间隙过小造成。
出现短刀粘铁皮一般为单轮间隙过大造成。
3.切分轮磨损严重、造成切分带撕开角度不符生产要求,造成切分刀粘铁皮。
4.切分轮或切分刀窜动、偏移,造成切分刀粘铁皮。
5.预切或切分架次因入口偏、导辊间距过大、轧机大斜面、黑头钢、头部肥等出现弯头或线差,造成切分刀粘铁皮。
6.预切或切分架次轧槽磨损严重,切分带过厚造成切分刀粘铁皮。
7.切分导卫冷却水量不足造成切分刀粘铁皮。
三.17#、18#不进或17#、18#顶出口造成堆钢事故。
原因分析:根据事故现象分析原因如下:1.头部肥是出现事故的主要原因。
在原设计料形的基础上尝试对所有架次进行料形尺寸下调,粗轧下调2-5毫米、中轧下调1-2毫米,精轧确保充满度并没用耳子。
2.堆拉关系造成的头尾肥。
主控台根据电流趋势图和现场观察轧件运行情况,合理调整堆拉关系。
标准调整活套设定高度,减少活套起套高度不稳造成的拉钢现象。
3.导卫与轧槽间距过远使轧件头部咬入时出现偏移,造成咬偏或侧弯带来顶出口事故。
4.导卫内孔过大或过小。
内孔过大容易出现轧件运行不稳,来回摆动时咬入轧槽出现头部咬偏堆钢事故。
内孔过小容易卡钢或轧件碰撞内壁造成头部偏移产生咬偏堆钢事故。
5.导卫左右、高低与轧槽不在同一中心线。
轧件头部咬入轧槽后出现侧弯(镰刀弯)、翘头、栽头等顶出口事故。
6.万向节震动。
因联轴器摆动严重,造成轧件头部咬入轧槽的瞬间出现弯头、翘头、栽头等顶出口事故。
7.轧件因辊错较大尺寸不符生产要求。
来料轧件头部因辊错出现单侧或双侧耳子,轧制时出现轧件头部不稳或产生扭转造成弯头、翘头、栽头等顶出口事故。
8.线差原因造成事故。
因料形、堆拉关系、导卫等原因造成四线尺寸出现偏差,单面偏肥或偏瘦,造成轧件不进或顶出口事故。
9.轧辊两侧辊缝误差。
如精轧出现轧辊两侧辊缝误差较大,同样会产生轧件运行不稳定产生事故。
10.入口滚动导卫间隙过大或过小时产生轧件头部咬入时摆动,轧制后头部出现侧弯(镰刀弯)造成顶出口事故。
11.成品入口前分料口因单个磨损或整体高低与入口导卫夹板不在同一水平线,轧件咬入后出现头部摆动造成弯头。
四.成品出口至倍尺剪之间辊道堆钢。
原因分析:1.倍尺剪超前率设置不合适。
因12规格钢筋较细,在剪切过程中如剪切过慢易出现剪刃碰撞下一段轧件头部出现辊道堆钢事故。
如剪切过快易出现连带下一段轧件头部翘起造成辊道事故。
2.辊道电机转速达不到成品速度要求。
因电机型号、辊面磨损等原因出现剪切后轧件运行低于成品速度,造成辊道堆钢事故。
3.因线差过大造成轧件在加速辊道运行速度不一致,轧件产生摆动、出现缠钢,无法达到正常速度,造成辊道堆钢事故。
4.因成品出口至倍尺剪之间辊道堆钢事故居高不下、难以完全控制。
经过现场测量设计、制作成多个单管50厘米长空过管进行连接,底部进行框架固定,加焊少量冷却管口进行弱穿水轧制。
经过半年运行完全符合生产要求,没有再出现成品出口至倍尺剪之间辊道堆钢事故。
五.速度调整在连续轧钢工艺里,轧制速度的调整相当重要(指各机架之间的速度)。
如各机架之问的速度不平衡,则料形尺寸不能保证,成品质量也就不能保证,特别是生产四切分时。
由于四切分工艺的独特性,在生产时由于加热温度存在不均匀、孔型存在有磨损、电气控制系统不稳定,很难给出一个绝对准确的轧制参数表,因此在生产过程中;特别是在刚换完品种调试时,调整工与主控台操作工的配合非常重要。
在过钢时调整工应根据钢坯温度、红钢经过各机架料形是否充满、辊缝印是否平稳、红钢进入下一机架是否稳定来判断机架之问的堆拉情况,并通知主控台,操做工应根据调整工反映的情况和电机的负荷显示来调整各机架的速度,最后调整的结果是粗轧机出来的红钢头、中、尾将近一样大、有微小的辊缝印、进入中轧机机架时红钢平稳地进入、而不是明显地扭转着进入中轧机机架。
同样第l2道次机架出来的方料红钢要求充满、辊缝印平稳,头、中、尾料形尺寸将近一样大。
另外正常更换精轧机轧槽后.过钢时禁止将活套调得过低,这样会造成拉钢,损坏切分箱。
六.上卸钢裙板乱钢事故。
原因分析:从成品轧机出来的四线成品钢,在倍尺剪剪前通过收料装置收拢剪切成一排后、同时沿着裙板辊道到达冷床区域。
在这一过程中,我们必须分析清楚成品钢的主要受力状态。
裙板辊道中每 1.2 米安装了一个旋转的辊子,辊面高出辊道架底面3 毫米,为成品钢的输送提供驱动力。
由于成品钢直径尺寸小、温度高,所以在裙板中并不是呈直线形状,而是波浪形。
因此,成品钢在得到辊子对它的拉动力的同时,还得到了裙板辊道架地面和侧面对它的摩擦阻力。
当成品钢满足拉力大于阻力时,就能够以一定的加速度运动,从而使剪切后的倍尺钢以更快的速度前进,并且与尚未剪切的成品钢产生一定的空隙,配合裙板的动作就可以实现倍尺钢安全到达冷床的目的。
倍尺钢在裙板辊道中的受力状态经过长期的观察和总结分析,发现造成裙板乱钢的现象可以分为两种:第一种是四线里有一线或两线抖动、弯曲,然后堆钢;第二种是前后两根倍尺没有拉开分钢距离,倍尺上冷床过程中乱钢。
1. 解决倍尺钢抖动、弯曲造成堆钢的问题引起倍尺钢抖动、弯曲的主要原因在于切分后的四线成品钢尺寸差异大,造成四线运动速度的差异大而抖动乱钢。
这个尺寸差异一般是两侧的成品纵筋尺寸比中间的两线大或小,中间两线是基本相同的。
为了消除这个差异,我们从以下几点入手。
1) 精细调整速度,消除精轧机以前各架轧机间的拉钢,保证成品钢通长尺寸均匀。
2) 严格控制钢坯加热温度的均匀性,头尾温度差不超过30℃。
另外在待轧时,加热炉均热段炉压保持微正压,避免由于温度不均产生的堆拉关系变化。
3) 控制好13#、15#、16# 架次入口导卫的位置。
当轧件头部通过成品轧机后,迅速用木条检验这三架轧机的充满程度,随时调整入口导卫的位置。
4) 活套的调整按照小冲击速降补偿时活套高度一步到位的原则来进行。
5) 提高成品辊的加工精度,减小磨损速度和差异。
采用数控车床精细加工成品槽,使成品槽尺寸误差保持在0.05 毫米以内。
15#、16#使用高硼钢轧辊,17#、18#使用高速钢成品辊,提高轧槽寿命,减缓轧槽磨损速度。
增设冷却水压力,提高轧辊冷却能力,减缓轧槽磨损速度。
通过上述几个措施的应用,完全解决了由于尺寸差异引起的裙板乱钢问题。
2. 解决倍尺钢在裙板辊道上没有分钢间隙的问题倍尺钢没有与尚未切开的成品钢拉开间隙,说明它没有获得足够的加速度。
经过检查,并没有发现裙板辊的实际速度与设定速度不符的问题出现,因此可以排除自动控制系统的影响。
观察发现,生产较大规格的螺纹钢产品时,并没有出现倍尺钢分不开的现象。
因此,再分析影响倍尺钢运动的因素,怀疑在生产12 毫米螺纹钢时裙板辊道的摩擦力变大了,抵消了裙板辊的拉动力。
为了使倍尺钢获得足够的加速度,可以考虑提高裙板辊拉动力或降低裙板辊道架的阻力的方法。
1) 用砂轮把裙板辊道底面全部打磨光滑,完全清除了粘结的氧化铁皮,彻底改善了裙板辊道底面的状况,摩擦系数大大降低,从而也降低了摩擦阻力。
2) 对于磨损程度达到1.5 毫米以上的裙板辊全部更换。
由于工作辊径增大,使其对成品钢的拉动力提高。
同时,随着裙板辊工作辊径的增大,相应地提升了成品钢的高度,使其与辊道架底面的接触长度减小,相应地就减小了辊道架底面对倍尺钢的摩擦阻力。
3) 对于磨损严重、开裂的裙板辊道架及副冷床挡板进行更换,降低摩擦系数,相应减小对成品钢的阻力。