变换催化剂硫化升温步骤及注意事项
变换催化剂的硫化

R115101硫化总结
1、硫化过程
10月19日,R115101填装1m3新K8-11和4m3旧K8-11,催化剂直接铺在顶层瓷球上面。
10月22日,R115101开始硫化。
12:15,催化剂床层温度为205℃,开始配入H2,低甲界区处阀门控制H2含量。
12:49,开始向系统配入CS2,60Kg/h。
13:49,开工加热炉增加柴油流量,使床层温度升至330℃。
19:45,停止向系统补入CS2,床层温度分别为321℃、311℃、206℃。
开工风机和开工加热炉继续运行,吹扫系统中的H2S和CS2。
20:26,停开工加热炉。
22:12,停风机,系统泄压。
2、分析数据
3、总结
1)由于催化剂较少以及CS2加入量大,不到30min H2S即穿透床层,160min 后变换炉出口H2S开始稳定。
CS2共使用351.74Kg,硫化时间为7.5小时。
2)本次硫化过程中的H2含量很高,主要是由于来自甲醇分厂H2管线的压
力达到3.0MPa,第二道阀门压力达到0.2MPa,开度较大,只需保证第二道阀后压力稍稍大于开工系统压力(0.13MPa)即可。
为了降低系统中H2含量,应该在补入H2后及时补入CS2,同时要增加PV115010的开度。
等温变换催化剂硫化方案

在常温常压下二硫化碳为无色透明微带芳香味的脂溶性液体,有杂质时呈黄色,普通试剂有腐败臭鸡蛋味,具有极强的挥发性、易燃性和爆炸性。
燃烧时伴有蓝色火焰并分解成二氧化碳与二氧化硫。
人吸入最低致死量为4000ppm (30 分钟)。
急性中毒时,初期兴奋、头痛,继而意识丧失、昏睡和死亡。
低浓度长期暴露时,下肢浮现多发性神经炎,伴有头痛、失眠、性欲减退和记忆力下降,脱离接触时能康复。
长期暴露会发生视网膜症和肾疾患为特征的血管损伤。
外观与性状:无色或者淡黄色透明液体,纯品有乙醚味,易挥发。
熔点:-111.9℃密度:1.26g/cm相对蒸气密度(空气=1):2.64沸点:46.2℃稳定性:稳定份子式:CS2相对份子质量:76.14饱和蒸气压(28℃时):53.32kPa燃烧热:1030.8kJ/mol临界温度:279℃临界压力:7.90MPa闪点:-30℃爆炸上限(体积分数):60.0引燃温度:90℃爆炸下限(体积分数):1.0健康危害:二硫化碳是伤害神经和血管的毒物。
急性中毒:轻度中毒有头晕、头痛、眼及鼻粘膜刺激症状;中度中毒尚有酒醉表现;重度中毒可呈短期的兴奋状态,继之浮现谵妄、昏迷、意识丧失,伴有强直性及阵挛性抽搐。
可因呼吸中枢麻痹而死亡。
严重中毒后可遗留神衰综合征,中枢和周围神经永久性伤害。
慢性中毒:表现有神经衰弱综合征,植物神经功能紊乱,多发性周围神经病,中毒性脑病。
眼底检查:视网膜微动脉瘤,动脉硬化,视神经萎缩。
危(wei)险特性:极易燃,其蒸气能与空气形成范围广阔的爆炸性混合物。
接触热、火星、火焰或者氧化剂易燃烧爆炸。
受热分解产生有毒的硫化物烟气。
与铝、锌、钾、氟、氯、叠氮化物等反应剧烈,有燃烧爆炸危(wei)险。
高速冲击、流动、激荡后可因产生静电火花放电引起燃烧爆炸。
其蒸气比空气重,能在较低处扩散到相当远的地方,遇火源会着火回燃。
燃爆危(wei)险:该品极度易燃,具刺激性。
皮肤接触:即将脱去污染的衣着,用大量流动清水冲洗至少 15 分钟,就医。
耐硫变换催化剂循环硫化方案
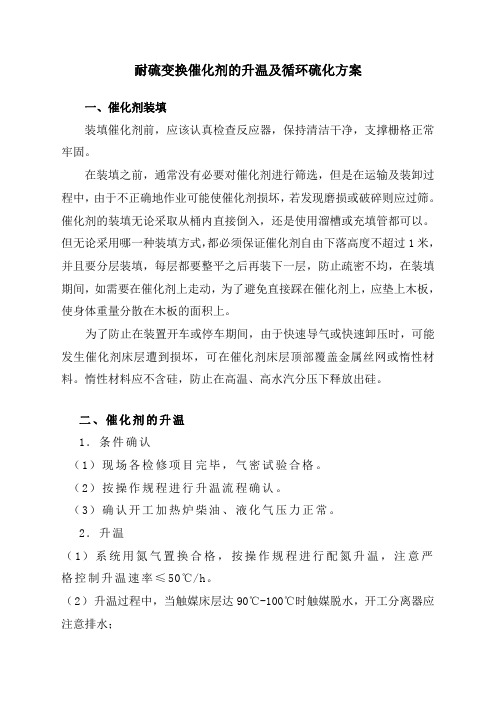
升 0.5 常温~120
30
3
0.5
120
6
温
0.5
120~220
30
3
0.5
220
6
备注 氮气量 20000Nm3/h 恒温释放吸附水
恒温拉平床层温差
三、催化剂的硫化 1、当催化剂床层温度达到 200℃~220℃时,把氢气加到氮气中,控
制反应器入口温度在 200℃~220℃,分析变换炉入口氢气含量 10%(干基) 左右。
耐硫变换催化剂的升温及循环硫化方案
一、催化剂装填 装填催化剂前,应该认真检查反应器,保持清洁干净,支撑栅格正常 牢固。 在装填之前,通常没有必要对催化剂进行筛选,但是在运输及装卸过 程中,由于不正确地作业可能使催化剂损坏,若发现磨损或破碎则应过筛。 催化剂的装填无论采取从桶内直接倒入,还是使用溜槽或充填管都可以。 但无论采用哪一种装填方式,都必须保证催化剂自由下落高度不超过 1 米, 并且要分层装填,每层都要整平之后再装下一层,防止疏密不均,在装填 期间,如需要在催化剂上走动,为了避免直接踩在催化剂上,应垫上木板, 使身体重量分散在木板的面积上。 为了防止在装置开车或停车期间,由于快速导气或快速卸压时,可能 发生催化剂床层遭到损坏,可在催化剂床层顶部覆盖金属丝网或惰性材 料。惰性材料应不含硅,防止在高温、高水汽分压下释放出硅。
H2S 分析 1 次/ 半小时
四、硫化过程中不正常情况的处理 1、床层温升缓慢 配氢量或氮气量过高,入口温度控制较低,可通过增加开工加热器的
蒸汽量,提高变换炉入口温度来控制。 2、床层温度急剧上升 二硫化碳加入过快或入口温度调节过高都可能导致温度急剧上升。可
采取的措施为:降低变换炉入口温度;减少直到停止加入二硫化碳。
中温变换催化剂的升温还原原操作说明
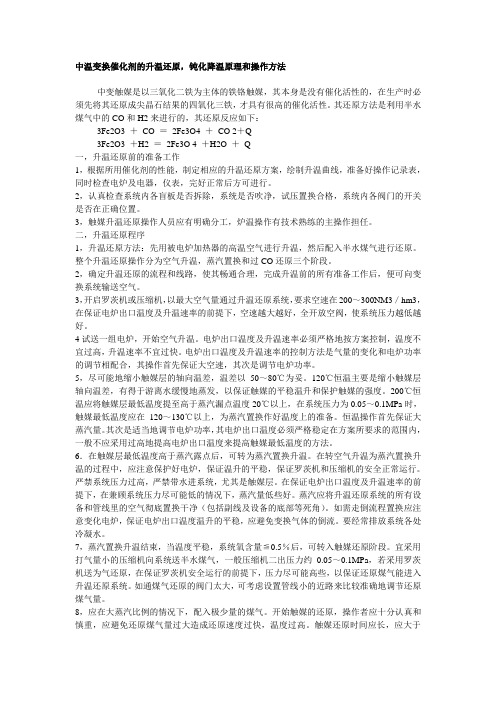
中温变换催化剂的升温还原,钝化降温原理和操作方法中变触媒是以三氧化二铁为主体的铁铬触媒,其本身是没有催化活性的,在生产时必须先将其还原成尖晶石结果的四氧化三铁,才具有很高的催化活性。
其还原方法是利用半水煤气中的CO和H2来进行的,其还原反应如下:3Fe2O3 +CO =2Fe3O4 +CO 2+Q3Fe2O3 +H2 =2Fe3O 4 +H2O +Q一,升温还原前的准备工作1,根据所用催化剂的性能,制定相应的升温还原方案,绘制升温曲线,准备好操作记录表,同时检查电炉及电器,仪表,完好正常后方可进行。
2,认真检查系统内各盲板是否拆除,系统是否吹净,试压置换合格,系统内各阀门的开关是否在正确位置。
3,触媒升温还原操作人员应有明确分工,炉温操作有技术熟练的主操作担任。
二,升温还原程序1,升温还原方法:先用被电炉加热器的高温空气进行升温,然后配入半水煤气进行还原。
整个升温还原操作分为空气升温,蒸汽置换和过CO还原三个阶段。
2,确定升温还原的流程和线路,使其畅通合理,完成升温前的所有准备工作后,便可向变换系统输送空气。
3,开启罗茨机或压缩机,以最大空气量通过升温还原系统,要求空速在200~300NM3/hm3,在保证电炉出口温度及升温速率的前提下,空速越大越好,全开放空阀,使系统压力越低越好。
4试送一组电炉,开始空气升温。
电炉出口温度及升温速率必须严格地按方案控制,温度不宜过高,升温速率不宜过快。
电炉出口温度及升温速率的控制方法是气量的变化和电炉功率的调节相配合,其操作首先保证大空速,其次是调节电炉功率。
5,尽可能地缩小触媒层的轴向温差,温差以50~80℃为妥。
120℃恒温主要是缩小触媒层轴向温差,有得于游离水缓慢地蒸发,以保证触媒的平稳温升和保护触媒的强度。
200℃恒温应将触媒层最低温度提至高于蒸汽漏点温度20℃以上,在系统压力为0.05~0.1MPa时,触媒最低温度应在120~130℃以上,为蒸汽置换作好温度上的准备。
变换催化剂升温硫化注意事项
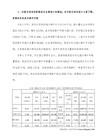
置 换 4~6 200-300 180-200 直 至出 口 硫 化 氢 含 量
≤1g/m3 ,并入系统。
以防电加热器超压。
(3) 在煤气升温结束前,硫化罐应按要求装填好CS2,检查制氮机所送管线是否通畅,升压至
0.1~0.2MPa备用。
3.3. 硫化期
(1) 待低变炉进口温度达210℃,即可用N2将CS2压入系统,用硫化罐出口流量计控制CS2加入量,保证入炉CS2浓度为5~10g/m3,开始硫化。
3.4. 强化期
催化剂层各点为400~450℃,保持~4小时出口H2S含量≥10g/NM3,强化硫化结束。
3.5. 降温置换阶段
(1) 硫化至各段均进入降温置换阶段,控制电炉出口温度200℃,待床层温度降至≤300℃,然后
停止加 CS2置换。
(2) 联系检修拆、加盲板后,即可导气制合格变换气开车。
(3) 变换常压放空运行两小时后至变换气成分合格后方可向后工序送气。
(4) 注意事项:
(1) 升温硫化严格按要求进行,升温期间,单点温度不得超过500℃,升温速率严格按30∽50℃/h
进行。
(2) 硫化过程中,严格控制进口煤气中O2%,严防O2含量跑高造成炉温急骤上升,烧毁触媒, CS
(2) 控制电炉出口温度200~250℃。催化剂床层温度200~300℃,时间约为8~10小时,待于出
口硫化氢≥ 3g/NM3,可认为硫化初期结束。
(3) 硫化时密切注意床层温度,用电加热器组数、CS2加入量及煤气量等调节床层温度。
(4) 硫化时炉进口H2含量应保证≥25%,便于CS2氢解。
反应生成H2S,与CoO、MoO3反应生成CoS、MoS2。
饱和塔流程三段式全低变工艺催化剂升温硫化方案

湖北双雄催化剂有限公司变换催化剂升温硫化方案1 变换催化剂硫化方案1.1 升温硫化应具备的条件:1) 系统改造完,施工方交底。
2) 变换催化剂装填完,装料口按要求封闭。
3) 罗茨机、高压机、电加热器完好备用,仪表及控制系统试用合格。
4) 管道设备保温。
5) 水、电、蒸汽等保证供应。
6) 操作人员熟悉工艺与升温硫化方案。
7) 开风机保压头,用压缩机循环送气,用压缩机调节气量。
在设备内有冷却水流动的状态下利用二水加、冷却器对高温煤气降温。
硫化升温煤气不通过脱盐水加、一水加、热水塔,关闭有关阀门,打开硫化专用线阀门,打开回压缩机一段入口循环线阀门。
硫化工艺见全低变工艺流程图:1.2 升温硫化的准备8) 按要求抽盲板,硫化系统畅通无阻。
9) 变换系统(包括硫化管线)惰气置换合格。
10) 电加热器、箩茨风机、压缩机完好备用,仪表、微机、联锁、信号齐全,试用合格。
11) 二硫化碳装入容器亩好。
每立方米新催化剂需二硫化碳:煤气全放空硫化或电炉功率偏小需150Kg,煤气循环并略放空硫化需120Kg,硫化煤气冷却方式为直接用水淋降温硫化需130Kg,每立方米旧催化剂硫化需30Kg。
氮气接入二硫化碳槽(用前要0.4MPa试露),压力升至~0.2MPa备用。
二硫化碳购买电话:139********12) 硫化时输送二硫化碳的胶管要用有纤维内网的煤气塑料管、新氧气带、新乙炔气带。
严防伪劣商品。
13) 增压机开车送气,总管置换合格,按硫化气量准备好开车风机/压缩机。
14) 分析仪器完好。
15) 水、电、汽保证供应。
1.3 升温期:(常温~210℃,电加热器出口温度≤260℃)16) 启动箩茨风机将合格不脱硫半水煤气引入变换硫化系统,压力保持0.03—0.05MPa。
17) 启动压缩机开始循环,循环气量控制8000~10000NM3/h。
压力保持0.04—0.08MPa。
18) 硫化系统循环5分钟,开启电加热器对每组分别预热后,推电升温。
变换催化剂硫化升温步骤及注意事项

变换催化剂硫化升温步骤及注意事项升温步骤及注意事项用氮气(也可用半水煤气,但控制速率,注意安全)对整个CO变换系统进行置换,置换至O2含量≤0.5%(体积分数)。
然后按制定的升温流程对催化剂进行升温,升温速率控制在15-25℃/h,当催化济床层温度升至80℃时,向升温载气中配入H2;在催化剂床层温度达120℃时,恒温约4h,以利催化剂吸附水的排放及吸附氧的释放、燃烧。
升温过程注意以下几点:一、根据实际情况制定升温流程,管线盲板倒换正确;二、用载气的温度将升温速率控制在安全范围内;三、配氢时,注意分析升温载气中的O2含量,严格控制载气中的O2含量≤0.5%(体积分数),超标时用放空进行调整;四、保持升温系统压力≤0.2Mpa。
变换催化剂硫化注意事项一、在升温、降温期间,采用大空速,要求电炉功率要大(用CS2硫化时,1m3催化剂的电炉功率为30kW,用固体硫化剂时,1m3催化剂的电炉功率要≥50kW,宜分为多组控制),以满足大负荷需要。
二、硫化期间,保持硫化载气中的H2含量≥25%,可采用部分放空和添加新鲜煤气的措施保证循环气中的H2浓度达标。
三、用CS2的加入量及硫化载气温度和流量控制催化剂床层的升温速率及热点温度,必要时可切气通蒸汽降温后再导气硫化,严禁床层温度暴涨、急降,进行强制硫化时,床层温度应控制在450-480℃,最高不得超过500℃。
四、在H2S穿透前,CS2量不可加入过多,否则会把催化剂中COO 直接还原为金属CO,CO有甲烷催化作用,不仅加剧超温,而且使硫化无法继续进行,同时损害催化剂的活性。
五、硫化系统压力应保持在0.2-0.3 Mpa。
六、因湿气硫化会使CO-MO系催化剂丧失部分活性,尤其是丧失低温活性,因此,系统保压、补氢时须用干气,并及时排放冷凝水,严禁冷凝水进入催化剂床层。
七、煤气中O2含量每升高0.1%,系统绝热温升约15℃。
O2会将催化剂中的活性组分氧化成硫酸盐,降低催化剂的活性,因此,在硫化全过程中,须严格控制煤气中O2含量<0.5%,当煤气中O2含量高时,必须迅速切气源,待O2浓度降至合格后再通气硫化。
钴钼系变换催化剂的硫化步骤和方法

硫化步骤:触媒升温硫化曲线表:阶段执行时间(hr) 空速(h-1 ) 床层各点温度(℃) 入炉H2S含量(g/Nm3 ) 备注1.升温12~14 200~300 常温~210 用煤气将系统置换合格后推电炉升温2.硫化期20~24 100~200 210~300 10~15 待出口气的H2S含量≥3g/Nm3 ,床层穿透3.强化期109 100~200 300~350350~450 15~20 变换炉出口H2S含量≥10g/Nm34.降温置换~8 200~300 180~200 0.05 出口H2S含量≤0.5g/Nm3 ,并入系统生产1、煤气升温阶段(1) 常温~120℃(6~8h),120℃恒温2 h,120~200℃(4h)。
(2) 按升温硫化流程调节好有关阀门,压缩机1台三出送气压力<0.2MPa,最大循环气量15000Nm3/h。
(3) 待电加热器、变换炉各处煤气置换O2<0.5%,电加热器通气正常后,启3组电炉丝开始煤气升温。
(4) 打开循环气体出口阀,关低变炉出口DN150放空阀,将循环气体导入压机一入煤气总管,开始循环升温。
(5) 电加热器升温时,采取必要措施严格按升温曲线进行。
升温期间视各段温升情况及时增减电炉丝组数,调节各段进气阀开度、气量或煤气换热器进出口煤气副线阀等。
当两变换炉床层温差较大时,可用进两炉的升温煤气阀调节不同入炉点的气量。
(6) 升温期间,严格控制煤气中O2<0.5%,防止电加热器起火**,严格控制煤气系统压力不得超过0.3MPa。
(7) 恒温前应先降低热煤气温度。
(8) 在煤气升温结束前3h,两硫化罐应按要求灌装好CS2,并连接好N2瓶,升压至0.45~0.5MPa、并排水后备用。
(9) 升温期间,要注意及时排放油分离器和活性炭滤油器导淋,严防油水带入系统。
(10) 循环升温时,不必开放空,待硫化开始后,可在系统出口处打开放空置换一部分气体,以补充氢气含量。
变换触媒升温硫化方案120810全解
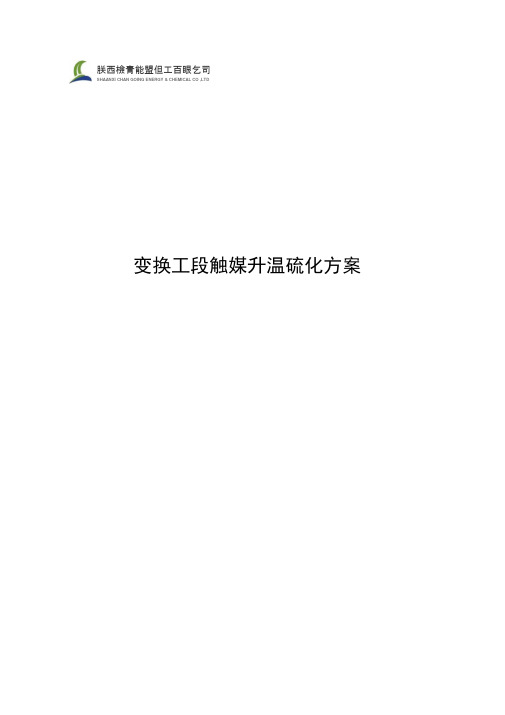
朕西檢青能盟但工百眼乞司SHAANXI CHAN GOING ENERGY & CHEMICAL CO ,LTD变换工段触媒升温硫化方案2012-08-10 生产运行部编制:马小东、蒋保林审核:肖瑞兵审定:袁社路批准:张栓存目录1 目的 (1)2 编写依据 (1)3 催化剂硫化要求 (1)4 催化剂升温硫化概述 (1)4.1 硫化的目的和原理 (1)4.2 升温硫化方法 (2)4.3 升温硫化流程 (2)5 硫化前提条件和准备工作 (2)5.1 前提条件 (2)5.2 阀门、盲板状态确认 (3)5.3 汽提单元投用 (5)5.4 废锅建立液位 (6)5.4 脱盐水加热器、水冷器投用 (6)6 催化剂升温硫化 (6)6.1 催化剂升温 (6)6.2 催化剂硫化 (8)6.3 硫化操作注意事项 (9)7硫化过程突发事件的处理措施 (10)7.1 工艺水煤气突然中断 (10)7.2 系统过氧 (10)7.3 锅炉水故障 (11)7.4 循环水、脱盐水故障 (11)7.5 硫化变换炉超温 (11)8 HSE分析及措施 (11)8.1 人的不安全因素 (11)12 8.2 设备不安全因素............................8.3 介质不安全因素............................1目的为规范变换催化剂升温硫化操作,保证催化剂硫化过程中设备及人身安全,为变换工序全面导气开车做前提准备。
2 编写依据2.1 东华设计院变换工艺PID2.2 催化剂厂家硫化说明书2.3 《长青能化净化装置操作规程》3 催化剂硫化要求3.1 试车前由开车领导小组牵头下达工作指令,负责方案审批。
3.2 装置管理人员负责试车条件确认,负责试车人员培训与方案交底,组织本装置运行人员实施方案,负责开车资料收集、记录回收、问题汇总。
3.3装置技术主管对试车期间安全、消防、健康、环保负责,协调相关安全、消防等部门审批手续;保证试车期间安全物资、消防器材的供给,对安全、消防、健康、环保监督。
变换升温硫化方案

变换硫化方案操作规程⑸硫化线:来自低压机的半水煤气→丝网过滤器→除油剂炉→前热交壳程→后热交管程→变换炉一段进口管1#电加热器→ 2#电加热器→变换炉二段进口管变换炉三段进口管后热交壳程→前热交管程→水加热器→冷却器→气液分离器→⑷变换炉无内保温变换炉分三段:一段上层装20m3抗毒剂、下层30 m3催化剂;二段装30 m3催化剂;三段装55m3催化B、每层底部有篦子板支撑,上面铺两层不锈钢网(3×3),两层耐火球;在触媒上面铺一层不锈钢网,其中一段压200㎜Φ30耐火球,二、三段压300㎜Φ30耐火球;底部铺耐火球目的:a、压好不锈钢网边;b、较好地防止反吹动,避免偏流。
上面铺耐火球地目的:a、气体分布均匀;b、蒸发可能带至变换炉内地水份。
2、和外部直接关联单位的主要控制指标:相关指标:变换入口H2S≥0.10g/Nm3 ;变换入口O2≤0.4%0.4%≤O2<0.8%减量:0.8%≤O2<1.0%减机:O2 ≥1.0%系统停车脱盐水指标:电导率≤5μs/cm,CL-≤5mg/L,碱度≤0.3mmol4、触媒的硫化硫化反应是将氧化态催化剂转化为硫化态产生活性CS2 +4H2 = 2H2S+CH4生成的H2S与CoO和MoO3反应生成CoS和MoS2:CoO+H2S=CoS+H2O MoO3+2H2S+H2 = MoS2+3H2OA、检查电加热器出口测温点是否灵敏,接CS2是否畅通;B、系统加蒸汽阀前加盲板;C、水加热器,冷却器水路畅通;D、CS2槽内贮满CS2,液位计清晰,槽内加压设施、CS2流量计及输送设备安装齐全;E、备好分析器具和分析药品。
⑴硫化方法:采用循环升温硫化法A、循环硫化路线:压缩二出来合格半水煤气→变换系统→回低压机一入B、关闭变换炉进口阀,打开电加热器进口阀,打开一段硫化阀,三段串联硫化,一段硫化结束后打开二段硫化阀关闭一段。
二段硫化结束后打开三段硫化阀关闭二段。
⑵升温硫化过程:A、系统内导入气体后,要保证有一定的循环时间,当分析电加热器入口O2≤0.5%时,启电炉升温;B、以电加热器出口温度为调节点,控制一段进口温度,根据一段温升情况,逐渐加大电炉功率(控制电炉出口温度最高不超过480℃)进入一段升温阶段;C、当催化剂温度升至60-90℃时,因催化剂在此阶段有一个脱水期,需要对各个气相导淋每半小时排放一次;D、当一段上层温度升至210℃时,向一段加CS2,进入一段硫化初期,二段升温阶段;E、当一段触媒上层温度达到300℃,入口H2S达到15——20 g∕Nm3, 二段触媒上层温度达210℃,进口H2S≥3 g∕Nm3时,进入一段硫化主期,二段硫化初期,三段升温阶段;F、当一段各点温度升至350——370℃时,恒温8h以上,并在出口三次取样分析H2S含量达10 g∕Nm3以上时为硫化结束。
低温变换催化剂升温硫化总结

低温变换催化剂升温硫化总结1、概述随着我国合成氨工艺的不断改进,低温变换催化剂的应用越来越广泛。
本公司变换装置采用的就是钴钼系低变耐硫变换催化剂。
由于耐硫变换催化剂的活性组分钴和钼是以氧化态的形式分散在多孔载体上,而催化剂活性相为硫化态,因此在使用前须进行硫化处理。
催化剂的硫化是耐硫变换催化剂应用的关键步骤,直接影响着催化剂的变换活性和稳定性,也将直接影响变换工段的生产负荷、合成气质量和蒸汽消耗等。
本文以变换四段催化剂升温硫化为例,对低变催化剂升温硫化过程进行总结。
2、工艺流程叙述在低变工艺中,因催化剂装填量较大,为减少放空量,本装置采用气体循环硫化法。
工艺气从变换炉四段出来后,经气气换热器与硫化风机出口的工艺气换热,将气体热量回收,进人变冷器降温至常温,进入3#分离器分离液态水,之后工艺气进入硫化风机,维持硫化风机入口处正压,由硫化风机将工艺气送至气气换热器,然后进入电炉加热,最后进入变换炉四段。
由于在硫化过程中要消耗氢,在硫化风机入口处连续加入少量新鲜煤气。
为防止惰性气体在循环气中积累,在3#分离器处设一放空管,连续放空少量循环气,使循环气中H2体积分数维持在25%以上。
CS2从电炉出口加入。
3、升温硫化原理及过程一、硫化原理催化剂中的活性成分是以氧化态形式存在,生产时,须将其转化为硫化态才能显示出催化剂的高活性。
为加速硫化过程,通常采用外加硫化剂(CS2)方法进行,其反应方程式为:CS2 + 4H2 ←→2H2S + CH4 —246KJ/mo (氢解反应)MoO3 +2H2S +H2←→MoS2 +3H2O —48.1 KJ/molCoO + H2S ←→ COS +H2O —13.4 KJ/mol这些反应都是放热反应,特别是CS2的的氢解是很剧烈的放热反应。
二、升温硫化的过程1、升温阶段:四段硫化阀进出口保持全开,加大循环气量和严格控制电炉出口温度,在较低的温度下脱除催化剂的物理水,当触媒下层温度还在120℃以下,必须控制电炉出口温度不得超过150℃;触媒下层温度到120℃后,恒温4小时,以防脱水过猛和未脱除干净而升温使催化剂结块,物理水全部脱除干净后再升温,将温度升到220℃,再恒温2小时。
耐硫变换催化剂升温、硫化方案
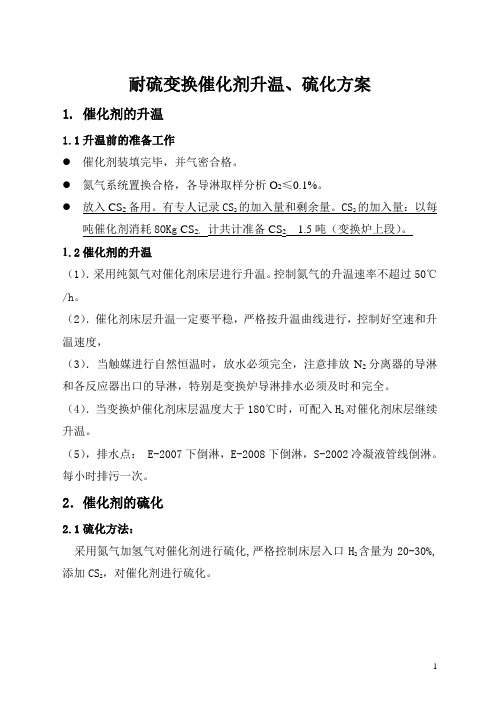
耐硫变换催化剂升温、硫化方案1. 催化剂的升温1.1升温前的准备工作●催化剂装填完毕,并气密合格。
●氮气系统置换合格,各导淋取样分析O2≤0.1%。
●放入CS2备用。
有专人记录CS2的加入量和剩余量。
CS2的加入量:以每吨催化剂消耗8OKg CS2,计共计准备CS2 1.5吨(变换炉上段)。
1.2催化剂的升温(1).采用纯氮气对催化剂床层进行升温。
控制氮气的升温速率不超过50℃/h。
(2).催化剂床层升温一定要平稳,严格按升温曲线进行,控制好空速和升温速度,(3).当触媒进行自然恒温时,放水必须完全,注意排放N2分离器的导淋和各反应器出口的导淋,特别是变换炉导淋排水必须及时和完全。
(4).当变换炉催化剂床层温度大于180℃时,可配入H对催化剂床层继续2升温。
(5),排水点: E-2007下倒淋,E-2008下倒淋,S-2002冷凝液管线倒淋。
每小时排污一次。
2.催化剂的硫化2.1硫化方法:含量为20-30%,采用氮气加氢气对催化剂进行硫化,严格控制床层入口H2,对催化剂进行硫化。
添加CS22.2催化剂硫化反应方程式CS2+4H2=2H2S+CH4+240.6KJ/molCoO+H2S=CoS+H2O+13.4KJ/molMoO3+2H2S+H2=MoS2+3H2O+48.1KJ/mol2.3催化剂的硫化●当变换炉层温度大于180℃,可配入氢气继续对催化剂床层进行升温度,氢气的配入量以H2浓度为准,使H2浓度达到20%左右。
●当触媒升温至230℃时,开始添加CS2对催化剂进行硫化,观察床层温升变化情况,控制CS2补入量稳定在20-40l/h。
同时适当提高触媒床层温度.●当床层温度达260-300℃时,保持CS2补入量,对催化剂进行硫化,同时要定时分析床层出口H2S和H2(每小时分析一次,维持床层出口H2在10--20%)。
●要保证在较低的床层温度(小于300℃)的条件下,使H2S穿透催化剂床层。
当床层出口有H2S穿透时,可加大CS2补入量继续对触媒进行硫化,CS2补入量可增加到80-150l/h,同时增加氢气的补入量,并加强H 2含量的分析,保证床层出口H2在10--20%。
QCS_04催化剂的硫化过程及注意事项1
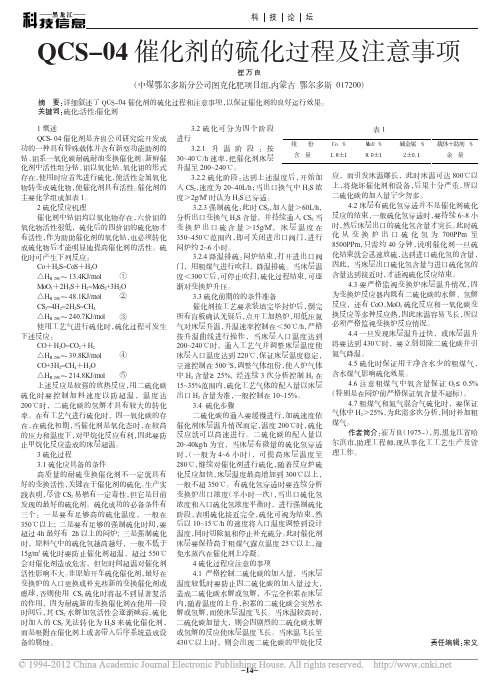
按升温曲线进行操作,当床层入口温度达到
4.4 一旦发现床层温升过快,或床层温升
200~240℃时,通入工艺气并调整床层温度使 将要达到 430℃时,要立刻切除二硫化碳并引
床层入口温度达到 220℃,保证床层温度稳定, 氮气降温。
空速控制在 500-1S,调整气体组份,使入炉气体
4.5 硫化时保证用干净含水少的粗煤气,
4.2 床层有硫化氢穿透并不是催化剂硫化
分析出口变换气 H2S 含量,并持续通入 CS2 当 反应的结束,一般硫化氢穿透时,要持续 6~8 小
变 换 炉 出 口 硫 含 量 >15g/M3, 床 层 温 度 在 时,然后床层出口的硫化氢含量才突长。此时硫
350~450℃范围内,即可关闭进出口阀门,进行 化 从 变 换 炉 出 口 硫 化 氢 为 700PPm 至
进行 3.2.1 升 温 阶 段 : 按
30~40℃/h 速率,把催化剂床层
;; ; ;; ;; ;;
;;; ;; ;;;;;;
;;; ;; ;;;;;;
;;;; ;; ;;;;;; ;;
;;;;;;
;; ;;
化剂中活性组分钴、钼以氧化钴、氧化钼的形式
存在,使用时应首先进行硫化,使活性金属氧化
物转变成硫化物,使催化剂具有活性。催化剂的
ÁÁÂ科技论坛
QCS-04 催化剂的硫化过程及注意事项
崔万良 (中煤鄂尔多斯分公司图克化肥项目组,内蒙古 鄂尔多斯 017200)
摘 要:详细叙述了 QCS-04 催化剂的硫化过程和注意事项,以保证催化剂的良好运行效果。 关键词:硫化;活性;催化剂
1 概述
3.2 硫化可分为四个阶 段
表1
QCS- 04 催化剂是齐鲁公司研究院开发成 功的一种具有特殊载体并含有新型功能助剂的 钴、钼系一氧化碳耐硫耐油变换催化剂。新鲜催
变换触媒升温硫化方案

变换触媒升温硫化方案(一)、变换触媒硫化原理1、变换触媒型号为QCS-04,主要活性组分是氧化钴、三氧化钼,在使用前需将其转化为硫化物才具有活性,这一过程称为硫化。
QCS-04催化剂物化性能催化剂的硫化是在一定温度下,利用煤气中的氢气和向煤气中补充的硫化氢与催化剂作用生成硫化物。
其主要反应式为:MoO3+2H2S+H2=MoS2+3H2O+Q(48.11Kj/mol)CoO+H2S=CoS+H2O+Q(13.4Kj/mol)硫化过程中为使半水煤气中有足够的硫化氢含量,通常采用连续向系统内添加二硫化碳的方法,同时还可以获取大量的反应热,这一过程称为二硫化碳的氢解:CS2+4H2=2H2S+CH4+Q(240.6Kj/mol)全低变的升温硫化一般采用循环硫化法,本岗位采用一次放空的方法,煤气的升温由升温电加热器来控制,也可通过调整粗脱硫气气量加以调节,控制好升温硫化温度,做到既要控制升温速度,又要保证床层能达到硫化最终温度。
升温硫化时,当床层上部温度升至200℃时,方可向系统添加二硫化碳,由于二硫化碳在200℃时发生氢解反应生成硫化氢放出大量的反应热,为防止温度爆涨烧毁催化剂,要控制好二硫化碳的加入量,初期加入量要小,以后逐步增加。
同时要做到二硫化碳加量时不提温,提温时二硫化碳不加量。
触媒硫化时要定期分析床层出口气体中的硫化氢含量,当硫化氢含量达1g/Nm3时,可以提高温度进行强化。
当床层进出口气体中H2S含量基本相同或出口气体硫化氢含量达10 g/Nm3时,可视为硫化结束。
2、低变触媒的反硫化及失活低变触媒的活性组分金属硫化物在一定条件下转化为金属氧化物并放出硫化氢,从而使低变催化剂失去活性,这一现象称为耐硫低变触媒的反硫化反应。
其中主要是MoS2的氧化和放硫现象。
其反应式为:MoS2+H2O=MoO2+2H2S发生反硫化反应的主要原因是不正常的工艺操作条件引起的,如低变进口温度高、气体中硫化氢含量低、汽气比高等。
催化剂升温硫化方案
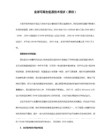
催化剂升温硫化方案一、催化剂的升温1、条件确认(1)现场各检修项目完毕,气密性试验合格,(2)按操作规程进行升温流程确认。
(3)确认开工加热炉柴油,液化压力正常。
2、升温(1)按操作规程进行配氮升温,注意严格控制升温速率≤50℃/h。
(2)当床层(一段)各点温度均达到200℃-220℃时恒温,进行下一步硫化程序。
首次开车升温时,为防止水蒸汽在催化剂上冷凝,应使用惰性气体N2把催化剂加热到工艺气露点以上温度。
采用≤50℃/h升温速度加热催化剂,根据最大可获得流量来设定压力,从而确保气体在催化剂上能很好的分布。
(3)当催化剂床层温度达到200℃-220℃时,进行下一步的硫化程度。
硫化气的切换基本上在常压或较高压力下进行,这取决于气流的方便,(注意:切换工艺气硫化前,一定要开导淋,彻底排放冷凝水)。
二、催化剂的硫化(一)采用工艺气硫化(1)确认工艺气中的硫化氢含量,最好工艺气中的硫化氢含量≥0.2%(VOL)。
(2)当催化剂床层温度达到200℃-220℃时,把湿工艺气加到氮气中(比例:湿工艺气:氮气=1:3)同氮气一起进入开工炉进行加热,控制反应器入口温度在200℃-220℃。
根据催化剂床层温度逐渐增加工艺气量,并且相应减少氮气量,直到氮气完全撤出。
(3)当硫化催化剂床层温度稳定时,再将工艺气流量增加,并控制入口温度200℃-220℃继续硫化。
(4)当有硫穿透催化剂床层时,逐步提高硫化压力和入口温度继续进行硫化,当压力为1.5MPa、入口温度230℃-250℃-时,此时变换炉出口有硫穿透,并且硫含量不再变化,可以认为硫化结束。
(5)硫化结束后,调整入口温度至正常使用要求的温度,同时增大工艺气量,提高系统压力至正常使用要求的压力。
采用补硫硫化1.加硫的位置:一般为第一变换炉前换热器的前面加硫。
2.CS2罐及加硫氮气管线,阀门配好待用。
3.取样点:变换炉入口和出口取样。
4.硫化期间4114-PVC-3保持全开。
耐硫变换催化剂升温及硫化程序

一,条件确认1.煤气化装置稳定运行,含氢工艺气来源稳定;2.高压蒸汽、循环水等公用工程条件具备;3.CS2加注系统备用;二,升温程序1.通低压氮气置换,为获得较大的低压氮气流量,设定较低的含量低于0.5%置换合格;放空压力,分析化验O22.打开开工加热器14-E1408,升温速率一般控制在15~25℃,严格控制升温速率≤50℃/h;3.当催化剂床层温度升至80℃时,往氮气中配入少量工艺气(有效成为为氢气),目的是燃烧催化剂吸附的氧气;4.在100-120℃恒温4小时,脱除催化剂吸附的物理水,燃烧掉催化剂吸附的氧气;5.继续升温,严格控制升温速率≤50℃/h;6.在200-220℃恒温2小时,准备下一步进入硫化程序;7.如果温度不能达到要求,适当提高设定压力降低空速;三,硫化程序1.少量导入工艺气,氢气含量在10%(一般10~30%)左右;2.将床层温度稳定在200-220℃范围内,开CS2计量泵,控制初期加入量20~40L/h,控制变换炉出口氢气含量5~10%;3.为增加硫化载气中的氢气浓度,逐步增大工艺气量,减少氮气量,直至氮气全部退出,氢气浓度不可大于30%;4.采用CS2加注量和硫化载气温度逐步提升床层温度,必须严格控制升温速率≤50℃/h,且控制床层温度不超过460℃,CS2加注量最大不得超过170L/h,如果升温过快,减少或停止CS2加入量,同时适当减少工艺气量或增加氮气量;5.当出口气体中硫含量达到入口气体硫含量的50%以上时,硫化已接近结束,进入高温高压强化硫化阶段,缓慢提升设定压力至0.5MPaG,降低空速控制温度400~500℃,加大CS2的注入量,当最大不得超过170L/h,当H2S浓度在10g/m3以上时,保持加入量不变,恒温3~4h;6.结束条件:H2S在10g/m3以上稳定3小时,停止加注CS2,切出开工加热器14-E1408,同时增加工艺气量,床层温度基本稳定时,调整入口温度至正常使用要求的温度,同时增大工艺气气量,提高系统压力至正常使用要求的压力。
耐硫变换催化剂装填及硫化方案
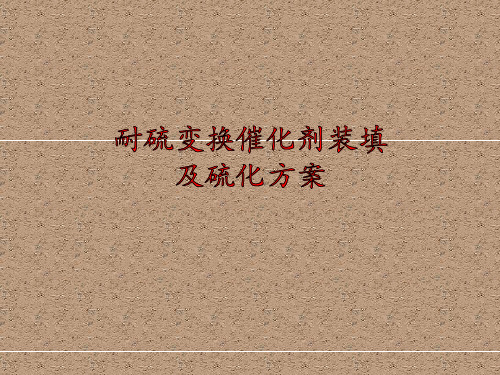
3.1.2把帆布袋接在装催化剂漏斗下面,炉内 作业人员拉住布袋出口,避免瓷球直接落到 下面摔坏。
3.1.3将瓷球铺平,确认达到所规定的高度。 注意先装50瓷球,后装25瓷球。
3.1.4催化剂卸出管也要装填上瓷球。
3.1.5将预制好的金属丝网正确地铺在瓷球上, 留出催化剂卸出管口。
3.2催化剂装填
3.2.1将催化剂装入吊斗
铺上木板,防止破损,在作业完成后,必须 把使用过的木板拿出炉外。
2.5 装填作业中,如果下雨、下雪要立即停 止作业,保护催化剂/过滤剂不被淋
湿。
2.6 在热偶套管周围充填时,注意不要造成 架空。
2.7 作业时,不要将异物带入炉内(铁片、 纸、烟头、泥土等)
2.8 应做好装填记录,包括物料的规格,型
3.2.6达到了规定的高度后,把催化剂表面推 平,把预制好的金属丝网铺在催化剂上面。 再装上300mm的瓷球。
4、四孔柱状过滤剂的装填
4.1按设计要求在所规定的位置上设置三层丝 网。
4.2 画出过滤剂装填的高度,用粉笔作上标 记。
4.3装填过滤剂至规定位置并推平。
4.4在过滤剂上设置一层丝网。再装上300mm
(3)CS2罐冲压,当罐内压力大于系统压力后, 稍开CS2罐入变换系统阀门,将CS2压入系 统,注意严禁CS2罐压力超过罐的设计压力。
(4)CS2和工艺气量的控制:在入口取样,控 制H2S+CS2含量3—5g/NM3,控制H2含量 在10%左右。
(5)控制床层温升T<20C/h,若床层温度上 升较快,应立即减少或停止加CS2量,同时 适当减少工艺气(或H2)量或增加N2量。
(6)注意随时分析出口H2S的含量,当出口
(6)注意随时分析出口H2S的含量,当出口 出现H2S时,可以适当提高入口温度。当 入口温度达到250--260C时,至少保持2h, 出口有H2S时,再慢慢提高入口温度,达 到300C,同时将入口总硫量提高到8--10 g/NM3。当出口气体中H2S含量维持在 4000-5000ppm时,可以认为硫化已结束。
变换触媒升温硫化方案

变换触媒升温硫化方案1 触媒升温硫化前的准备工作(1)变换炉R2001触媒装填完毕。
(2)变换系统吹除、气密性试验完成。
(3)V2009已经装入CS2待用。
(4)DW、S3、S4、LN及仪表空气等公用工程均送至界区。
(5)各仪表调试合格,一次表根部阀打开。
(6)各自调阀、控制阀、手动阀均灵活好用,安全阀及安全装置调试合格。
(7)开工加热炉F2001已经符合使用条件。
(8)除氧给水系统已经具备条件。
(9)硫化所用分析仪器完好,药品备齐。
(10)升温曲线、图表、记录本、画图铅笔、直尺备好待用。
(11)硫化所用H2已经就为待用。
2 置换2.1置换前的确认⑴按《变换原始开车盲板确认表》对变换系统盲板确认变换原始开车盲板确认表⑶按《变换原始开车阀门确认表》对变换手动阀确认。
变换手动阀确认表(4)调节阀确认变换及冷凝液系统调节阀关闭。
2.2变换气系统置换⑴ 统置换路线⑶ 置换步骤① 联系调度变换系统置换。
② 确认MV2001关闭,现场打开开工氮气双手动阀,通氮气置换。
③打开PV2006置换气放空去火炬,用PV2006控制升压,压力PICA2006稳定在0.3MPa 时投自动。
④ 微开AV2003和TV2006。
① 按单体操作规程启动氮气循环风机C2001,启动后打开C2001前阀。
② 在洗氨T2001出口取样分析 O 2≦0.1%为置换合格,系统保压。
2.3变换冷凝液及气提系统置换 ⑴ 置换路线 ① 通知硫回收变换气提不凝汽需要放空。
② 打开PV2007和PV2009。
③ 确认冷凝液泵ⅠP2001和冷凝液泵ⅡP2002进口阀关闭。
① 打开LV2003和LV2009及前后手阀,给冷凝液气提系统送LN置换。
② 在气提塔T2002出口取样分析,O 2≦0.5%时,置换合格。
③关闭LV2003和LV2009及前后手阀,停止置换。
关闭PV2007和PV2009。
3 水煤气废锅E2001和低压蒸汽废锅E2004投运①确认E2001/E2004放空阀打开,并网阀关闭。
- 1、下载文档前请自行甄别文档内容的完整性,平台不提供额外的编辑、内容补充、找答案等附加服务。
- 2、"仅部分预览"的文档,不可在线预览部分如存在完整性等问题,可反馈申请退款(可完整预览的文档不适用该条件!)。
- 3、如文档侵犯您的权益,请联系客服反馈,我们会尽快为您处理(人工客服工作时间:9:00-18:30)。
变换催化剂硫化升温步骤及注意事项
升温步骤及注意事项
用氮气(也可用半水煤气,但控制速率,注意安全)对整个CO变换系统进行置换,置换至O2含量≤0.5%(体积分数)。
然后按制定的升温流程对催化剂进行升温,升温速率控制在15-25℃/h,当催化济床层温度升至80℃时,向升温载气中配入H2;在催化剂床层温度达120℃时,恒温约4h,以利催化剂吸附水的排放及吸附氧的释放、燃烧。
升温过程注意以下几点:
一、根据实际情况制定升温流程,管线盲板倒换正确;
二、用载气的温度将升温速率控制在安全范围内;
三、配氢时,注意分析升温载气中的O2含量,严格控制载气中的O2含量≤0.5%(体积分数),超标时用放空进行调整;
四、保持升温系统压力≤0.2Mpa。
变换催化剂硫化注意事项
一、在升温、降温期间,采用大空速,要求电炉功率要大(用CS2硫化时,1m3催化剂的电炉功率为30kW,用固体硫化剂时,1m3催化剂的电炉功率要≥50kW,宜分为多组控制),以满足大负荷需要。
二、硫化期间,保持硫化载气中的H2含量≥25%,可采用部分放空和添加新鲜煤气的措施保证循环气中的H2浓度达标。
三、用CS2的加入量及硫化载气温度和流量控制催化剂床层的升温速率及热点温度,必要时可切气通蒸汽降温后再导气硫化,严禁床层
温度暴涨、急降,进行强制硫化时,床层温度应控制在450-480℃,最高不得超过500℃。
四、在H2S穿透前,CS2量不可加入过多,否则会把催化剂中COO 直接还原为金属CO,CO有甲烷催化作用,不仅加剧超温,而且使硫化无法继续进行,同时损害催化剂的活性。
五、硫化系统压力应保持在0.2-0.3 Mpa。
六、因湿气硫化会使CO-MO系催化剂丧失部分活性,尤其是丧失低温活性,因此,系统保压、补氢时须用干气,并及时排放冷凝水,严禁冷凝水进入催化剂床层。
七、煤气中O2含量每升高0.1%,系统绝热温升约15℃。
O2会将催化剂中的活性组分氧化成硫酸盐,降低催化剂的活性,因此,在硫化全过程中,须严格控制煤气中O2含量<0.5%,当煤气中O2含量高时,必须迅速切气源,待O2浓度降至合格后再通气硫化。
八、硫化过程中应采用较高的H2S浓度(在循环硫化过程中,采用部分放空可保证循环气中较高的H2S浓度),出口气中H2S含量高于20g/m3才算穿透。
九、要有较长的硫化时间,使硫化彻底,在温度≥350℃、出口H2S 含量≥20g/m3条件下保持8-10h,亦即温度、浓度、时间这三项同步达到指标要求,才能保证硫化彻底,而不是某一单项指标瞬时或短时达到峰值。
硫化不彻底会有部分氧化态钴、钼、钾残留,使用中容易反硫化,少则1-3个月,多则不足1a就会出现催化剂失活现象。
十、降温排硫时,最好用未脱硫的干煤气吹扫,如果只有脱硫煤气,
则在床层温度300℃以上时少量添加CS2(<10L/h)进行降温排硫,以避免因浓度差过大造成反硫化。
十一、无论因何原因停车,都应先关CS2阀门及电炉,2min后再停气,以防烧坏电炉。
这一点很重要,最好安排电工在升温硫化期间,专门值班负责电炉的监护运行。
十二、非原始开车硫化催化剂,最好在反应器入口补充新变换催化剂或γ- Al3O2球,否则使用CS2硫化时起不到显著复活的作用。
这是因为除氧剂或耐硫变换催化剂在使用一段时间后,其CS2水解加氢活性会显著丧失,使硫化时加入的CS2无法转化为H2S用以硫化催化剂,而是吸附在催化剂表面或者带入系统造成设备腐蚀。
十三、若放空气不回收到吹风气而直接放空,要注意周边安全,防止硫化氢中毒。
十四、二硫化碳的压送要有专人看管,在夏天温度高时,二硫化碳的桶上要采取防暴晒的措施,并准备好相应的消防措施。