供应商质量能力评估细则
供应商QCDS评分细则

供应商QCDS评分细则为了确保供应商的产品和服务能够满足公司的需求,我们需要对供应商进行QCDS(即质量、成本、交货和服务)评分。
QCDS评分细则是一套标准,它们可以帮助我们对供应商的绩效进行客观的评估,并确定他们是否符合我们的要求和期望。
以下是供应商QCDS评分细则的主要要点:1.质量评分质量是我们最关注的因素之一,因为一个高质量的供应商可以帮助我们降低退货和重工的成本。
在质量评分中,我们可以考虑以下因素:-产品符合规定的质量标准-产品的可靠性和耐用性-供应商在质量管理方面采取的措施和实施的质量保证体系-供应商的质量问题解决方式和响应时间-供应商的缺陷率和退货率2.成本评分成本是我们决策的重要因素之一、在成本评分中,我们可以考虑以下因素:-产品价格的竞争力-供应商提供的成本节约措施-过去与该供应商合作期间的总成本表现-供应商提供的优惠和折扣3.交货评分及时交付是确保供应链流畅运作的关键。
在交货评分中,我们可以考虑以下因素:-供应商的交货准确度和按时交货的能力-供应商的库存水平和物料供应的稳定性-存货周转率和处理时间-供应商与货运公司的合作情况4.服务评分供应商提供的优质服务可以提高合作关系的稳定性和顺畅性。
-供应商的响应速度和解决问题的能力-供应商的沟通和协调能力-提供技术支持和培训的能力-供应商与我们的合作关系和合作意愿对于以上每个评分因素,我们可以建立一个评分系统,为每个因素设置权重,并根据每个供应商在各个领域的表现进行评分。
这样,我们可以获得一个综合的供应商QCDS评分,以帮助我们确定最适合我们需求的供应商。
最后,供应商QCDS评分细则的制定需要以公司的战略目标和需求为基础,并与供应商进行充分的沟通和协商。
定期评估供应商的QCDS绩效可以帮助我们保持供应链的稳定性和可靠性,同时也可以帮助供应商了解他们需要改进和提升的方面,从而实现双赢的合作关系。
品质部供应商质量控制与评估规定
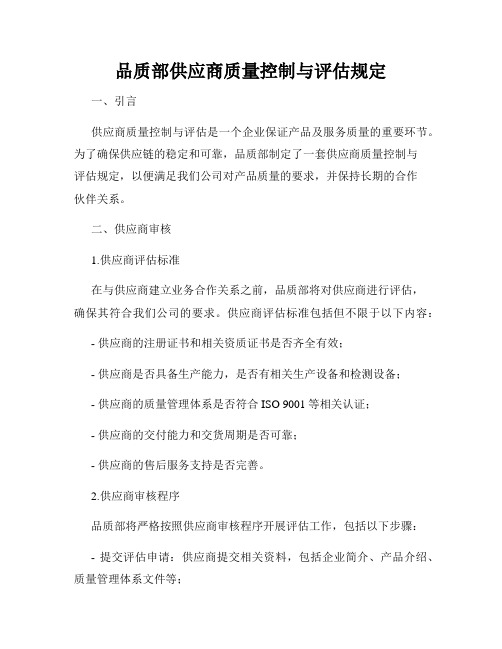
品质部供应商质量控制与评估规定一、引言供应商质量控制与评估是一个企业保证产品及服务质量的重要环节。
为了确保供应链的稳定和可靠,品质部制定了一套供应商质量控制与评估规定,以便满足我们公司对产品质量的要求,并保持长期的合作伙伴关系。
二、供应商审核1.供应商评估标准在与供应商建立业务合作关系之前,品质部将对供应商进行评估,确保其符合我们公司的要求。
供应商评估标准包括但不限于以下内容:- 供应商的注册证书和相关资质证书是否齐全有效;- 供应商是否具备生产能力,是否有相关生产设备和检测设备;- 供应商的质量管理体系是否符合ISO 9001等相关认证;- 供应商的交付能力和交货周期是否可靠;- 供应商的售后服务支持是否完善。
2.供应商审核程序品质部将严格按照供应商审核程序开展评估工作,包括以下步骤:- 提交评估申请:供应商提交相关资料,包括企业简介、产品介绍、质量管理体系文件等;- 资料审核:品质部审核供应商提交的资料,判断其是否符合我们公司的要求;- 现场审核:品质部将安排专业人员对供应商进行现场审核,包括生产设备、质量管理体系、售后服务等;- 评估结果:品质部根据现场审核情况及相关资料评估结果,对供应商进行评分和分类;- 审核报告:品质部将出具供应商审核报告,其中包括供应商的质量状况评估结果和建议;三、供应商质量控制1.合同签订经过供应商审核并评估合格后,品质部将与供应商签订供应协议和质量控制协议,明确双方的责任和义务,确保产品质量的稳定和可靠。
2.质量要求品质部将向供应商明确产品的质量要求,包括但不限于以下方面:- 产品的技术规范和标准;- 包装和运输要求;- 交货期和交货数量;- 特殊要求或限制条件。
3.采购检验品质部将对供应商提供的产品进行采购检验,确保其符合我们公司的质量要求。
采购检验包括样品检验、外观检验、性能指标检验等。
品质部将根据检验结果判断产品是否合格,对不合格的产品采取相应的措施,以保证产品质量。
供应商质量能力评估细则

组织机构------------------------------------------------------------------2 工艺------------------------------------------------------------------------3 检验的一般手段---------------------------------------------------------5 外协件质量---------------------------------------------------------------7 生产过程中的质量------------------------------------------------------9 成品质量-----------------------------------------------------------------12
7- 售后质量-----------------------------------------------------------------14 8- 场地—搬运—库存-----------------------------------------------------15 9- 人员-----------------------------------------------------------------------17 10- 产品开发与可靠性保证-----------------------------------------------18 S1-安全件、法规件的控制------------------------------------------------20 S2-质量改进------------------------------------------------------------------21 注: 1) 最初样件是指用正规工装生产的首批产品; 2) 一、二类产品是指由博耐尔设计,由供应商制造的产品,其它产 品为三类产品; 3) 标有“*”的项目为重要项,标有“@”的项目为安全、法规项。
供应商评分细则范文

供应商评分细则范文评估供应商的绩效对于组织来说至关重要,因为它直接影响到组织的效益和声誉。
为了有效地评估供应商,以下是一些细则,可以帮助组织进行全面而准确的评分。
1.产品质量和可靠性(20分)评估供应商的产品质量和可靠性是评分的重要因素之一、这包括产品的合格率、可靠性、耐用性以及是否符合规定的质量标准和要求。
2.交货准时率(15分)供应商按时交付产品对于组织的运营至关重要。
评估供应商的交货准时率是衡量其可靠性和交付能力的重要指标。
3.价格和成本(15分)供应商所提供的产品或服务的价格和成本对于组织来说也是一个重要的考虑因素。
评估供应商的价格和成本是否在市场竞争范围内,并确定其与其他供应商相比的竞争力。
4.技术能力和创新(15分)评估供应商的技术能力和创新能力对于组织来说也是一个关键因素。
这包括供应商能否提供最新的技术解决方案,并在产品或服务的创新方面有何贡献。
5.供应链管理(10分)供应商的供应链管理能力对于组织的正常运营至关重要。
评估供应商的供应链管理能力,包括物流和库存管理等方面的绩效表现。
6.服务和支持(10分)供应商的服务和支持能力也是一个评估细则。
这包括供应商对组织的响应速度、问题解决能力和售后服务质量等方面的评估。
7.可持续发展(10分)评估供应商的可持续发展能力是现代组织越来越重视的一个方面。
这包括供应商的环保政策、社会责任和可持续发展计划等方面的考虑。
8.业务稳定性(5分)评估供应商的业务稳定性也是一个细节。
这包括评估供应商的财务状况、过去业绩和组织的长期合作关系等方面的考虑。
9.经验和声誉(5分)为了评估供应商的信誉度和经验,评估供应商的历史和声誉也是一项重要指标。
以上是一些供应商评分的细则,组织可以根据其自身的需求和要求进行调整和修订。
评估细则应根据组织的业务特点和行业要求进行定制,以确保评估的准确性和实用性。
同时,评估过程应该包括与供应商的互动,以获得他们的反馈和意见,并建立更强大和互惠的合作关系。
供应商质量评分细则

供应商质量评分细则1.产品或服务质量(权重:30%)-产品或服务的合格率(权重:60%):根据所采购商品或服务的合格率,评估供应商提供的产品或服务是否符合标准要求。
-产品或服务的缺陷率(权重:40%):评估供应商提供的产品或服务是否存在缺陷情况,并根据缺陷率进行打分。
2.供应商交货准时率(权重:20%)-交货准时率(权重:80%):评估供应商的交货准时率,即供应商按照协议或合同规定的时间进行交货的比例。
-交货延迟次数(权重:20%):对供应商交货延迟的次数进行统计,根据次数进行打分。
3.供应商的售后服务(权重:15%)-售后服务质量(权重:60%):评估供应商提供的售后服务质量,包括售后响应速度、解决问题的能力等。
-售后服务满意度(权重:40%):根据采购方对供应商售后服务满意度进行评估,并进行打分。
4.供应商的信誉度(权重:15%)-信誉度评价(权重:70%):评估供应商在行业内的信誉度,包括供应商的企业规模、市场占有率等方面的综合评估。
-信誉度改进(权重:30%):评估供应商在过去一段时间内的信誉度改进情况,包括供应商是否积极参与行业活动、是否与客户合作进行改进等。
5.供应商的价格竞争力(权重:20%)-价格水平(权重:70%):评估供应商提供的商品或服务的价格水平,并与市场平均价格进行对比。
-价格稳定性(权重:30%):评估供应商在一段时间内价格的稳定性,包括是否频繁调整价格等方面的综合评估。
以上是一个供应商质量评分细则的例子,可以根据实际需要进行调整和补充。
在制定供应商质量评分细则时,可以根据不同的行业和企业的需求,对各项指标的权重进行调整,以保证评分结果更加准确和合理。
同时,评分细则应与供应商合作协议或合同进行关联,以便在供应商选择和后续合作中进行综合考虑。
供应商等级评定评分标准

供应商等级评定评分标准
一、目的:
为了提高产品质量,稳定供应商团队,建立
长期互惠供求关系,特制定本法。
二、范围:
本办法适用于向公司供应原辅材料、零部件
及提供配套服务的厂商
三、评定内容:
1、交期
2、品质
3、协调
四、评分权重/定义:
1.交期准时率(40分):=月准时的次数/总交货的次数*100%
交货准时配合良好40分,每延期一天扣3分,当月延期交货累计超过5分以上,单月评定等级不能评为C级以上
2.品质批次合格率(30分):=月合格良批次数/当月进货总批次数*100%
批次合格率为100%,每下降2%扣1分,扣完为止;每特采一批次扣2分.
3.协调度,主要考核供应商的工作配合能力. 重工、批退配合度不好、处理不彻底每次扣2分同一不良现象改善不及时或效果不佳每次扣2分
文件未按指定时间回复每次扣2分,回复不具体,不确定每次扣1分.
五、等级划分:
A级93-100分请保持
B级80-92分正常抽样、需要努力
C级70-79分加严抽样、需要改善
D级70分以下,列入考察,有关损失将扣
款;连续三个月被评为D级,取消供应商资
格.
注:评分B级以下的供应商,须对不良项目回复改善对策。
客户指定的供应商,如不符合要求,将向客户提出取消供应商的资格;每月评定和等级将于供应商品质会议公布及分发给各供应商.。
供应商能力评价标准

供应商能力评价标准一、供应商资质1.合法注册:确保供应商具备合法注册资格,具有独立法人地位,并已获得所有必要的执照和许可证。
2.业务范围:了解供应商的经营范围,确保其能够提供我们所需要的产品或服务。
3.经营状况:评估供应商的经营状况,包括其市场份额、销售渠道、客户群体等。
4.注册资本:评估供应商的注册资本,以了解其经济实力和承担风险的能力。
二、供货能力1.生产能力:了解供应商的生产能力,包括其生产线数量、生产规模、生产周期等。
2.库存管理:评估供应商的库存管理能力,包括其库存水平、库存周转率、库存补给周期等。
3.配送能力:了解供应商的配送网络和能力,以确保其能够按时将产品送达指定地点。
4.订单处理:评估供应商的订单处理能力,包括其订单处理周期、订单处理效率等。
三、质量保证1.质量管理体系:确认供应商是否具有质量管理体系认证,如ISO9001等。
2.质量控制:评估供应商的质量控制流程和标准,了解其如何保证产品质量。
3.质量检测:了解供应商的质量检测设备和流程,以确保其能够及时发现并处理质量问题。
4.持续改进:评估供应商是否具有持续改进的能力和意愿,以提高产品质量和性能。
四、价格因素1.报价合理性:评估供应商的报价是否合理,以确定其是否具有成本效益。
2.价格稳定性:了解供应商的价格稳定性,以避免价格波动对我们的采购计划造成影响。
3.折扣策略:了解供应商的折扣策略和优惠措施,以确定是否可以在采购中获得更多的优惠。
五、售后服务1.服务响应时间:了解供应商的服务响应时间,以确保在出现故障或问题时能够得到及时解决。
2.服务质量:评估供应商的服务质量,包括其解决问题的速度和准确性。
3.服务延续性:了解供应商的服务延续性,以确保在产品使用过程中能够得到持续的支持和服务。
公司材料供应商评价细则

公司材料供应商评价细则1.质量评价-材料质量:评估供应商所提供材料的质量标准和质量稳定性。
检查材料的外观、结构及性能,及时发现并处理质量问题,降低质量风险。
-供应商质量管理:评估供应商是否有良好的质量管理体系,包括采用优质材料、设立严格的质量控制流程、完善的检测手段和设备等。
供应商应能提供相关的质量保证文件和报告,确保所提供材料的质量符合公司的要求。
2.价格评价-价格竞争力:评估供应商的价格是否合理且具有竞争力。
与其他供应商进行比较,了解市场行情,从长远视角考虑采购成本的控制和降低。
-价格稳定性:评估供应商的价格是否稳定。
供应商应能提供稳定的价格政策和合同条款,避免价格波动对公司运营造成的不利影响。
-价格透明度:评估供应商是否能够提供透明的价格信息。
供应商应提供详细的价格清单,包括核心材料和配件的价格,并明确说明任何可能产生的附加费用。
3.交货评价-准时交货:评估供应商是否按照协商的交货日期进行准时交货。
供应商应提供具体的交货时间,充分考虑生产周期和运输时间等因素,以确保按时交货。
-交货可靠性:评估供应商的交货可靠性,包括供应商是否能够按需保证货物数量和质量。
供应商应提供具体的交货计划和备货能力,以满足公司的需求。
-物流管理:评估供应商的物流管理能力,包括货物包装、运输方式以及货物追踪和配送等。
供应商应采取适当的物流管理措施,以确保货物的完整性和安全性。
4.服务评价-售后服务:评估供应商的售后服务水平,包括处理产品质量问题、提供产品维修和更换等。
供应商应能够及时响应并解决问题,确保公司的利益不受损失。
-合作意愿:评估供应商的合作意愿和沟通能力,包括是否能够与公司建立长期稳定的合作关系,并能够积极参与公司的项目和业务发展。
5.管理评价-供应商管理体系:评估供应商是否有健全的管理体系,包括组织架构、管理层次、内部控制等。
供应商应能够通过自身的管理体系保证提供稳定和可靠的产品和服务。
-供应商风险管理:评估供应商的风险管理能力,包括对关键风险的识别和应对措施。
供应商质量保证能力评估
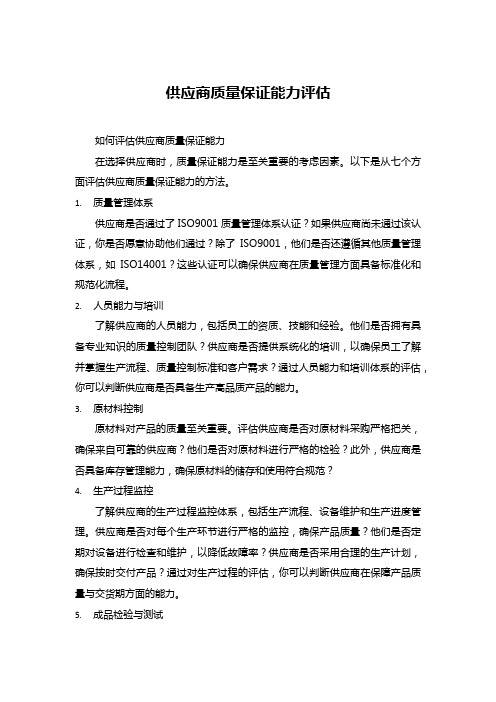
供应商质量保证能力评估如何评估供应商质量保证能力在选择供应商时,质量保证能力是至关重要的考虑因素。
以下是从七个方面评估供应商质量保证能力的方法。
1.质量管理体系供应商是否通过了ISO9001质量管理体系认证?如果供应商尚未通过该认证,你是否愿意协助他们通过?除了ISO9001,他们是否还遵循其他质量管理体系,如ISO14001?这些认证可以确保供应商在质量管理方面具备标准化和规范化流程。
2.人员能力与培训了解供应商的人员能力,包括员工的资质、技能和经验。
他们是否拥有具备专业知识的质量控制团队?供应商是否提供系统化的培训,以确保员工了解并掌握生产流程、质量控制标准和客户需求?通过人员能力和培训体系的评估,你可以判断供应商是否具备生产高品质产品的能力。
3.原材料控制原材料对产品的质量至关重要。
评估供应商是否对原材料采购严格把关,确保来自可靠的供应商?他们是否对原材料进行严格的检验?此外,供应商是否具备库存管理能力,确保原材料的储存和使用符合规范?4.生产过程监控了解供应商的生产过程监控体系,包括生产流程、设备维护和生产进度管理。
供应商是否对每个生产环节进行严格的监控,确保产品质量?他们是否定期对设备进行检查和维护,以降低故障率?供应商是否采用合理的生产计划,确保按时交付产品?通过对生产过程的评估,你可以判断供应商在保障产品质量与交货期方面的能力。
5.成品检验与测试成品检验与测试是确保产品质量的关键环节。
评估供应商是否拥有完善的成品检验与测试体系,能够准确查明产品不合格原因并及时纠正?供应商是否采用先进的检测设备和测试方法?他们的检验与测试流程是否符合行业标准和客户要求?6.质量改进与持续优化供应商是否制定质量改进方案和持续优化计划,以提高产品质量和生产效率?他们是否积极收集和分析质量数据,以便针对性地改进?供应商是否采用六西格玛、PDCA等先进的质量管理工具和方法?通过了解供应商的质量改进与持续优化举措,你可以判断他们是否有能力确保产品质量符合标准和客户要求。
供应商质量评价及合格供方管理规章制度细则
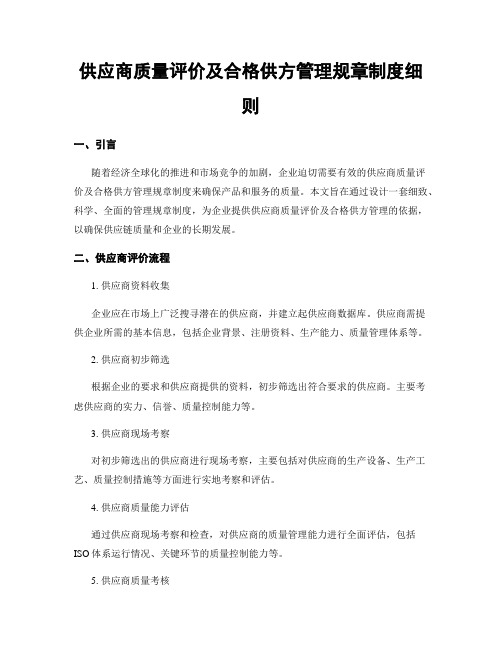
供应商质量评价及合格供方管理规章制度细则一、引言随着经济全球化的推进和市场竞争的加剧,企业迫切需要有效的供应商质量评价及合格供方管理规章制度来确保产品和服务的质量。
本文旨在通过设计一套细致、科学、全面的管理规章制度,为企业提供供应商质量评价及合格供方管理的依据,以确保供应链质量和企业的长期发展。
二、供应商评价流程1. 供应商资料收集企业应在市场上广泛搜寻潜在的供应商,并建立起供应商数据库。
供应商需提供企业所需的基本信息,包括企业背景、注册资料、生产能力、质量管理体系等。
2. 供应商初步筛选根据企业的要求和供应商提供的资料,初步筛选出符合要求的供应商。
主要考虑供应商的实力、信誉、质量控制能力等。
3. 供应商现场考察对初步筛选出的供应商进行现场考察,主要包括对供应商的生产设备、生产工艺、质量控制措施等方面进行实地考察和评估。
4. 供应商质量能力评估通过供应商现场考察和检查,对供应商的质量管理能力进行全面评估,包括ISO体系运行情况、关键环节的质量控制能力等。
5. 供应商质量考核建立科学的供应商质量考核体系,对供应商的交货及时性、产品质量、售后服务等方面进行定期考核,评估供应商的综合质量表现。
三、合格供方管理规范1. 合同签订与合格供方签订合同,并确保合同的合法性和有效性。
合同中明确约定产品规格、质量要求、售后服务等内容,以确保供方的责任和义务。
2. 定期审核和监督定期对合格供方进行审核和监督,检查供方是否按照合同的要求进行生产和质量控制,及时发现并解决问题。
3. 不合格供方的处理对于经过多次审核仍不能达到合格标准的供方,企业应考虑终止合作关系,并寻找替代供应商,以确保产品和服务的质量。
4. 合格供方奖励机制建立合格供方奖励机制,对表现优秀的供应商给予奖励和激励,以激发供应商的积极性和持续改进的动力。
四、问题与建议在供应商质量评价及合格供方管理过程中,可能会遇到一些问题。
为此,建议企业应积极解决以下问题:1. 信息不对称问题供应商所提供的信息可能存在虚假、夸大等情况,企业应通过严格的审核和考核程序,加强对供应商的调查和验证,降低信息不对称的风险。
供应商评价标准

供应商评分标准一、工程类供应商评分标准一施工进度20分1、进度计划10分:能够按照合同约定或甲方指令满足施工进度的,得10分;未按合同约定及甲方指令进行施工的,延误一次扣1分,扣完10分为止;2、甲方指令5分:能够根据甲方要求及时调整工期,不延误施工进度的,得5分;出现因施工单位未及时调整工期造成工期延误的,一次扣1分,扣完5分为止;3、交叉施工5分:交叉施工过程中,因推诿扯皮造成自身他方工期延误的,一次扣1分,扣完5分为止;二施工质量15分1、质量合格15分:按照合同约定未出现质量问题,达到施工质量要求并验收合格的,得15分;出现重大质量问题造成返工或者影响使用功能的,一次扣5分,扣完15分为止;2、质量较合格10分:按照合同约定未出现质量问题并验收合格,有部分瑕疵、不影响使用功能的,得10分;3、质量不合格0分:未按照合同约定的施工质量要求进行施工,验收不合格的,得0分;三安全文明10分1、安全事故4分:施工过程中未出现安全事故的,得4分;出现安全事故,未造成人员伤亡、财产损失的,一次扣1分;出现一次重大财产损失或人员伤亡的,此项不得分;2、成品保护2分:注重施工过程中的成品保护,得2分;对他人成品造成破坏的,一处扣1分,扣完2分为止;3、乙供材料2分:乙供材料符合甲方要求品牌,得2分;发现不符合甲方要求,一次扣1分,扣完2分为止;4、甲供材管理2分:甲供材的现场堆放与管理合理,得2分;未进行材料分类保护,一处扣1分,扣完2分为止;四管理与配合25分1、百日会战配合到位15分:a是否按时参加甲方例会5分,缺勤一次扣分;b服从甲方指令10分;2、合理经济签证10分:a提报时间、内容合理,无夸大成分得10分;b提报有夸大成分但无恶意成分,得5分;c签证恶意多报,得0分;3、加分项:设计变更+10分:施工过程中提出合理化施工建议,节约甲方成本或者提前工期的,此项合理加分,最高得10分;五其他维修及整改10分1、细部检查出现的问题能够及时、按要求整改到位的,得5分;其他酌情打分;2、延期执行甲方维修要求的,一次扣1分,扣完5分为止;六评价人自由打分20分:打分需配有理由可列条描述;最后打分人汇总出此次总得分即可;供应合作单位履约评审表材料设备类合作单位评分供应合作单位履约评审表。
供应商质量能力评估标准
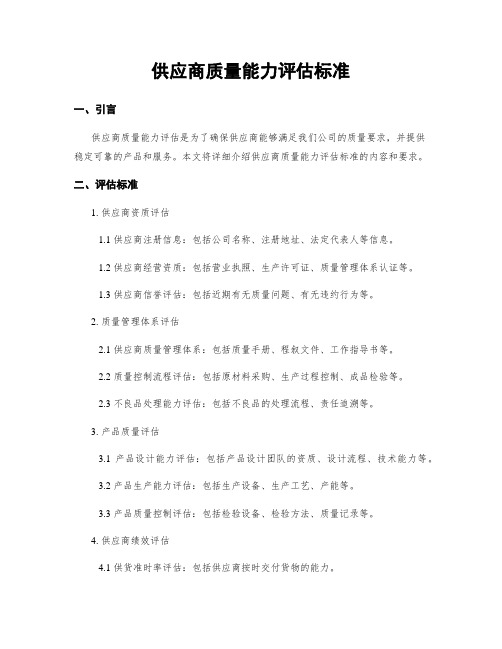
供应商质量能力评估标准一、引言供应商质量能力评估是为了确保供应商能够满足我们公司的质量要求,并提供稳定可靠的产品和服务。
本文将详细介绍供应商质量能力评估标准的内容和要求。
二、评估标准1. 供应商资质评估1.1 供应商注册信息:包括公司名称、注册地址、法定代表人等信息。
1.2 供应商经营资质:包括营业执照、生产许可证、质量管理体系认证等。
1.3 供应商信誉评估:包括近期有无质量问题、有无违约行为等。
2. 质量管理体系评估2.1 供应商质量管理体系:包括质量手册、程叙文件、工作指导书等。
2.2 质量控制流程评估:包括原材料采购、生产过程控制、成品检验等。
2.3 不良品处理能力评估:包括不良品的处理流程、责任追溯等。
3. 产品质量评估3.1 产品设计能力评估:包括产品设计团队的资质、设计流程、技术能力等。
3.2 产品生产能力评估:包括生产设备、生产工艺、产能等。
3.3 产品质量控制评估:包括检验设备、检验方法、质量记录等。
4. 供应商绩效评估4.1 供货准时率评估:包括供应商按时交付货物的能力。
4.2 供货稳定性评估:包括供应商供货的稳定性和可靠性。
4.3 售后服务评估:包括供应商的售后服务能力和响应速度。
5. 风险评估5.1 供应商地理位置评估:包括供应商所在地的地理环境、交通便利性等。
5.2 供应商经济稳定性评估:包括供应商的财务状况、资金流动性等。
5.3 供应商产能扩展能力评估:包括供应商的产能规划、设备投资等。
三、评估方法1. 文件审核:对供应商提交的相关文件进行审核,评估其资质和质量管理体系。
2. 现场考察:对供应商的生产设施、生产过程进行实地考察,评估其生产能力和质量控制流程。
3. 样品检验:对供应商提供的样品进行检验,评估其产品质量。
4. 绩效评估:根据供应商的供货记录和售后服务情况,评估其供货能力和售后服务水平。
5. 风险评估:通过对供应商地理位置、经济稳定性和产能扩展能力的评估,确定其风险等级。
供应商质量能力评估细则
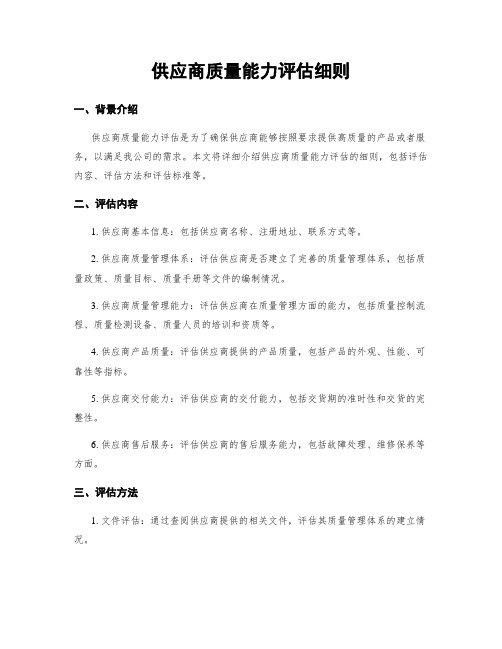
供应商质量能力评估细则一、背景介绍供应商质量能力评估是为了确保供应商能够按照要求提供高质量的产品或者服务,以满足我公司的需求。
本文将详细介绍供应商质量能力评估的细则,包括评估内容、评估方法和评估标准等。
二、评估内容1. 供应商基本信息:包括供应商名称、注册地址、联系方式等。
2. 供应商质量管理体系:评估供应商是否建立了完善的质量管理体系,包括质量政策、质量目标、质量手册等文件的编制情况。
3. 供应商质量管理能力:评估供应商在质量管理方面的能力,包括质量控制流程、质量检测设备、质量人员的培训和资质等。
4. 供应商产品质量:评估供应商提供的产品质量,包括产品的外观、性能、可靠性等指标。
5. 供应商交付能力:评估供应商的交付能力,包括交货期的准时性和交货的完整性。
6. 供应商售后服务:评估供应商的售后服务能力,包括故障处理、维修保养等方面。
三、评估方法1. 文件评估:通过查阅供应商提供的相关文件,评估其质量管理体系的建立情况。
2. 现场考察:实地考察供应商的生产车间、质检设备等,了解其质量管理能力和产品质量情况。
3. 样品测试:选取供应商提供的样品进行测试,评估其产品的质量指标是否符合要求。
4. 供应商访谈:与供应商的质量负责人进行面对面的访谈,了解其质量管理体系的运行情况和售后服务能力。
四、评估标准1. 供应商质量管理体系:符合国际质量管理体系标准,如ISO9001等。
2. 供应商质量管理能力:具备一定的质量管理经验,质量控制流程完善,质量检测设备齐全,质量人员具备相应的培训和资质。
3. 供应商产品质量:产品外观无明显瑕疵,性能稳定可靠,符合相关标准和要求。
4. 供应商交付能力:能够按时交付产品,确保交货的完整性和准时性。
5. 供应商售后服务:能够及时响应客户的售后需求,提供有效的故障处理和维修保养服务。
五、评估结果和改进措施1. 评估结果:根据评估内容和评估标准,对供应商进行综合评估,给出评估结果,如优秀、合格、待改进等。
供应商考核细则
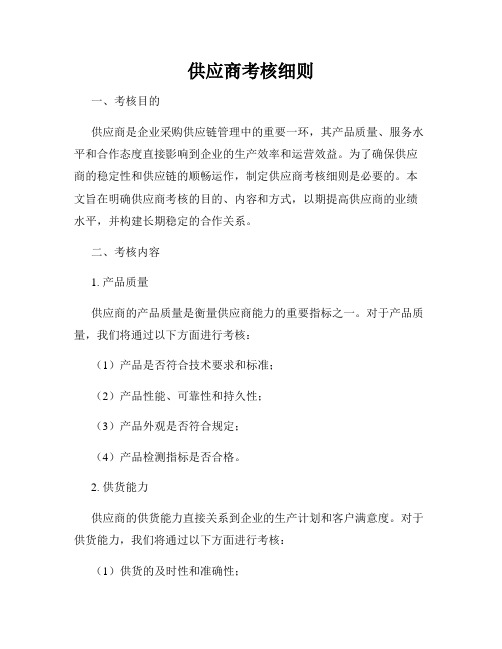
供应商考核细则一、考核目的供应商是企业采购供应链管理中的重要一环,其产品质量、服务水平和合作态度直接影响到企业的生产效率和运营效益。
为了确保供应商的稳定性和供应链的顺畅运作,制定供应商考核细则是必要的。
本文旨在明确供应商考核的目的、内容和方式,以期提高供应商的业绩水平,并构建长期稳定的合作关系。
二、考核内容1. 产品质量供应商的产品质量是衡量供应商能力的重要指标之一。
对于产品质量,我们将通过以下方面进行考核:(1)产品是否符合技术要求和标准;(2)产品性能、可靠性和持久性;(3)产品外观是否符合规定;(4)产品检测指标是否合格。
2. 供货能力供应商的供货能力直接关系到企业的生产计划和客户满意度。
对于供货能力,我们将通过以下方面进行考核:(1)供货的及时性和准确性;(2)供货的稳定性和连续性;(3)供货数量是否符合合同约定。
3. 服务水平供应商的服务水平对于顺利完成交付和解决售后问题至关重要。
对于服务水平,我们将通过以下方面进行考核:(1)售前咨询和技术支持;(2)交货前和交货后的沟通和协调;(3)售后服务和维修保养能力。
4.价格和成本价格和成本是企业采购过程中的重要考虑因素。
对于价格和成本,我们将通过以下方面进行考核:(1)产品价格是否合理;(2)价格的竞争力和变动趋势;(3)供应商的成本管理和降本增效能力。
三、考核方式1. 定期绩效评估供应商的业绩将定期进行绩效评估,评估周期为半年或一年。
评估内容将包括产品质量、供货能力、服务水平、价格和成本等方面。
评估结果将形成评估报告,供供应商参考和改进。
2. 不定期抽查检查除了定期绩效评估外,我们还将不定期对供应商进行抽查检查。
抽查内容将以关键节点的供货和服务为主,重点检查供应商的响应速度、配合度和解决问题的能力。
3. 不合格供应商管理对于绩效评估中出现不合格的供应商,我们将采取以下管理措施:(1)采取纠正措施并设定整改时限;(2)对供应商进行限制采购或暂停合作,直至问题解决;(3)建立不合格供应商黑名单,不再与其合作。
供应商评估标准
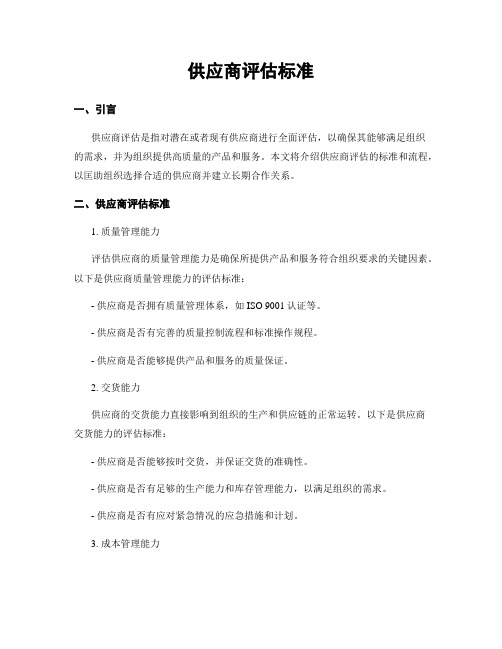
供应商评估标准一、引言供应商评估是指对潜在或者现有供应商进行全面评估,以确保其能够满足组织的需求,并为组织提供高质量的产品和服务。
本文将介绍供应商评估的标准和流程,以匡助组织选择合适的供应商并建立长期合作关系。
二、供应商评估标准1. 质量管理能力评估供应商的质量管理能力是确保所提供产品和服务符合组织要求的关键因素。
以下是供应商质量管理能力的评估标准:- 供应商是否拥有质量管理体系,如ISO 9001认证等。
- 供应商是否有完善的质量控制流程和标准操作规程。
- 供应商是否能够提供产品和服务的质量保证。
2. 交货能力供应商的交货能力直接影响到组织的生产和供应链的正常运转。
以下是供应商交货能力的评估标准:- 供应商是否能够按时交货,并保证交货的准确性。
- 供应商是否有足够的生产能力和库存管理能力,以满足组织的需求。
- 供应商是否有应对紧急情况的应急措施和计划。
3. 成本管理能力供应商的成本管理能力对组织的成本控制和利润率有重要影响。
以下是供应商成本管理能力的评估标准:- 供应商是否能够提供具有竞争力的价格。
- 供应商是否有成本管理体系和成本控制措施。
- 供应商是否能够提供合理的支付条件和灵便的价格策略。
4. 创新能力供应商的创新能力对组织的产品和服务的持续改进和创新具有重要作用。
以下是供应商创新能力的评估标准:- 供应商是否有研发团队和创新能力。
- 供应商是否能够提供新颖的产品和解决方案。
- 供应商是否有持续改进的文化和流程。
5. 可持续发展能力供应商的可持续发展能力对组织的长期合作和稳定供应具有关键作用。
以下是供应商可持续发展能力的评估标准:- 供应商是否遵守环境、社会和法律法规的要求。
- 供应商是否有可持续采购和供应链管理的措施。
- 供应商是否有良好的企业社会责任和道德行为。
三、供应商评估流程1. 评估需求确认:明确组织对供应商的要求和期望。
2. 供应商筛选:根据评估标准,筛选出符合要求的供应商。
供应商质量能力评定准则

供应商质量能力评定准则引言:一、质量管理体系1.ISO认证:供应商是否获得ISO9001质量管理体系认证,是否具备高质量标准的管理体系。
2.文件控制:供应商是否建立完善的文件控制制度,确保所有文件的准确性和及时性。
3.流程管理:供应商是否建立了完善的流程管理体系,包括流程规范、流程流转和流程改进等方面。
二、质量控制能力1.检验设备:供应商是否拥有适应产品特点的检验设备,确保产品的合格率和一致性。
2.检验方法:供应商是否有标准的检验方法和程序,以保证产品的质量可控。
3.抽样检验:供应商是否合理使用抽样检验,以缩短检验周期,提高效率。
4.不良品处理:供应商是否有完善的不良品处理流程,包括不良品的分类、报废和追溯等。
三、供应商管理能力1.供应商评估:供应商是否定期进行评估,评估内容包括供货的及时性、准确性和稳定性等。
2.供应商沟通:供应商是否有建立良好的沟通渠道和机制,及时响应和解决问题。
3.供应商培训:供应商是否有为员工提供培训的机制,确保供应商的工作人员拥有必要的技能和知识。
四、持续改进能力1.常规改进:供应商是否有制定和实施常规改进计划的能力,通过不断改进提高质量管理水平。
2.问题分析:供应商是否能够对问题进行深入的分析,找出问题的根本原因,以避免问题再次发生。
3.数据分析:供应商是否对采集的数据进行分析和利用,以找出问题的症结并采取相应的改进措施。
五、创新能力1.新产品开发能力:供应商是否有自主研发新产品的能力,以满足市场和客户的需求。
2.技术创新能力:供应商是否持续关注行业技术动态,掌握前沿技术,以提升产品质量和竞争力。
3.问题解决能力:供应商是否能迅速响应和解决问题,并提供切实有效的解决方案。
六、供应商质量能力评估方法1.供应商问卷:向供应商发放一份包含质量管理体系、质量控制能力、供应商管理能力等方面的问卷,并要求供应商提供相应的证明材料。
2.供应商现场观察:组织专业人员对供应商的质量管理体系和生产现场进行访问和观察,以获取直观的评估结果。
供应商评估细则
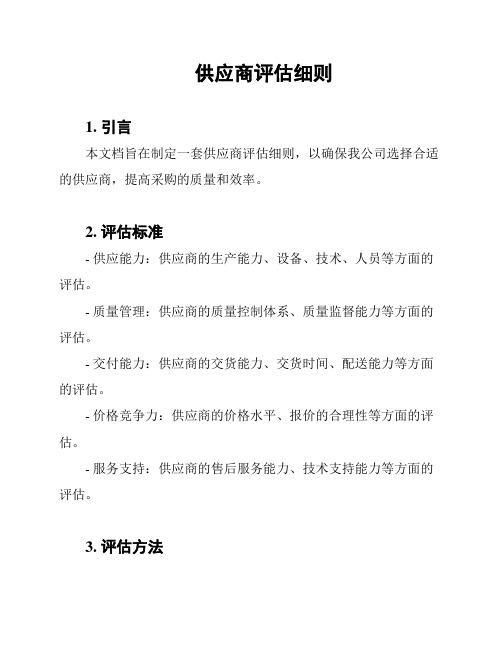
供应商评估细则1. 引言本文档旨在制定一套供应商评估细则,以确保我公司选择合适的供应商,提高采购的质量和效率。
2. 评估标准- 供应能力:供应商的生产能力、设备、技术、人员等方面的评估。
- 质量管理:供应商的质量控制体系、质量监督能力等方面的评估。
- 交付能力:供应商的交货能力、交货时间、配送能力等方面的评估。
- 价格竞争力:供应商的价格水平、报价的合理性等方面的评估。
- 服务支持:供应商的售后服务能力、技术支持能力等方面的评估。
3. 评估方法- 文件评估:评估供应商提交的相关文件,包括企业资质证书、质量管理体系文件、人员组织架构等。
- 现场考察:对供应商的生产场所、设备、技术、人员等进行实地考察,直观了解供应能力。
- 质量抽检:对供应商提供的样品或成品进行抽样检验,评估其质量控制能力。
- 交付能力评估:对供应商的交货记录、运输能力等进行评估。
- 市场调研:调研供应商在市场上的声誉、竞争力等。
- 客户反馈:了解其他客户对供应商的满意度和投诉情况。
4. 评估流程1. 收集供应商资料并初步筛选。
2. 进行文件评估和现场考察。
3. 进行质量抽检和交付能力评估。
4. 进行市场调研和客户反馈收集。
5. 综合评估结果,制定评估报告。
6. 评估报告评审和决策。
5. 评估报告评估报告应包含供应商名称、评估标准、评估结果等内容,并提出建议和意见。
6. 持续改进定期评估供应商,并根据评估结果采取相应的措施,以持续改进采购管理和供应链效率。
7. 结论通过制定供应商评估细则,我们能够选择具备良好供应能力、质量管理能力、交付能力和竞争力的供应商,最终提升公司的采购效益和竞争力。
如需要详细了解评估细则的具体内容,请参阅附录。
- 1、下载文档前请自行甄别文档内容的完整性,平台不提供额外的编辑、内容补充、找答案等附加服务。
- 2、"仅部分预览"的文档,不可在线预览部分如存在完整性等问题,可反馈申请退款(可完整预览的文档不适用该条件!)。
- 3、如文档侵犯您的权益,请联系客服反馈,我们会尽快为您处理(人工客服工作时间:9:00-18:30)。
•产品及工艺更改是否也作为最初样件来实施
•有无证实资料
3-检验的般手段
3.1-计量室。
-设备的状况及其跟踪。
•检测设备能否满足生产需要
•检定周期是否合理
•是否按周期检定
•对检定不合格的是否及时校准或维修
•现场使用的检测设备是否完好
评估内容
扣分
结论
评估记录
-人员。
•人数能否满足工作需要
6-成品质量12
7-售后质量14
8-场地 搬运 库存15
9-人员17
10-产品开发与可靠性保证18
51-安全件、法规件的控制20
52-质量改进21 注:
1)最初样件是指用正规工装生产的首批产品;
2)一、二类产品是指由博耐尔设计,由供应商制造的产品,其它产 品为三类产品;
3)标有“*”的项目为重要项,标有“ @的项目为安全、法规项。
•不合格品是否按要求隔离,有无明确的标记
2.2-参与对产品的定义。
•产品开发、设计程序中是否要求质量部门参与
2.3-参与确定工艺卡及生产手段。
•工艺设计与生产准备程序中是否要求质量部门参与
2.4-质量部门参与的情况。
•质量部门是否参与,有无证实资料
•是否把质量作为主导因素
2.5-确定检验手段及检验工艺卡。
•有无检验工艺设计的程序
评估内容
扣分
结论
评估记录
•有无检验工艺卡
•有无检验设备清单
2.6-检验手段及检验工艺卡的认可。
•检验手段及检验工艺卡应该经质量部门的认可
2.7-技术资料的审定、批准、发放。
•有无技术资料的审疋、批准、发放、归档、更新管理办法
•是否执行
2.8-技术资料的归档及更新。
•是否执行
2.9-最初样件的检验报告。*
•是否进行了验审,有无完整的报告
•试验设备有无操作规程
-结果的存档。
•各种试验有无综合试验报告
•对未达到要求的是否在产品及工艺上采取了改进措施
•试验报告是否按要求存档
•安全件、法规件的试验报告是否与生产日期相对应,以便查询@
4-外协件质量
4.1-对供应商的选择。*
•是否对供应商质量保证能力进行系统的评估
4.2-最初样件的估记分表
审核员审核日期
说明:
本评定标准包括十个章节和十二个附加条款,共115条,每条都有
具体的细则。
。评定时需要考虑企业的大小,具体产品、安全及法规项
。工厂的实施(特殊情况下,还要评估外协工厂)
。实施有效性用以下准则评定:
合适扣o分可接受扣1分
不可接受扣2分完全不合格扣3分
1.10向厂领导反馈严重问题信息。
•是否通过定 期的质量例会,向厂领导反映质量问题,对严重的问
题,是否及时向领导反馈
1.11验证质检部门的效能。
•领导应每天进行质量审核
1对入库的产品进行审核
2对线上的产品进行审核
3对生产工序进行审核
2-工艺
2.1-有作为标准的用户技术特性。(三类产品不作评估) •是否掌握用户对产品的要求
•各班次是否都有检查人员在岗
1.8质量部门与研究部门、工艺部门、生产部门和商业部门之间 的关系。
•质量部门代表用户的,如何站在用户的立场,与其它相关部门 联系,组织质量改进活动
评估内容
扣分
结论
评估记录
1.9向上级反馈产品质里信息。
•是否有一套正式和快速的循环体系,及时向领导反馈产品检验结
果和产品等级
能力水平的评定
能力水平的评定用如下公式计算:
(刀X—E Y)/ 刀X*100%
其中刀X为评价项目数*2
E丫表示所有项目的分总和
四个等级的划分:
能力水平:A级:90〜100分B级:75〜89分
C级:55〜74分D级:0〜54分
1-组织机构2
2-工艺3
3-检验的 般手段5
4-夕卜协件质量7
5-生产过程中的质量9
•试验报告是否按要求存档
•安全件、法规件的试验报告是否与生产日期相对应,以便查询
3.4-理化实验室。
-设备的状况及其跟踪。
•实验设备能否满足生产需要
•检定周期是否合理
•是否按周期进行检定*
•对检定不合格的是否及时校准或维修
•现场使用的实验设备是否完好
-实验规范及标准。
•对各种产品是否在试验之前都有明确的试验规范和执行的标准
•是否按机构职能配备人员
1.4书面的职能程序。*
•有无质量手册,企业的主要质量职能是否描述清楚
1.5质量部门相对于生产部门的独立性。
•是否与生产部门有同等地位
•不能由生产厂长领导
1.6扣压有缺陷产品的权力。
•是否有权停止不合格品的生产和发运,并要求有关部门采取纠 正措施
1.7检查与生产时间的相适应性。
•试验设备能否满足生产需要
•检定周期是否合理
•是否按周期进行检定*
•对检定不合格的是否及时校准或维修
•现场使用的试验设备是否完好
-试验规范。
•对各种产品是否在试验之前都有明确的试验规范
•试验设备有无操作规程
评估内容
扣分
结论
评估记录
-结果的存档。
•各种试验有无综合试验报告
•对未达到要求的是否在产品及工艺上采取了改进措施
检验的符合性检查。
4.6-手段的校检、存档。
•检验手段是否按周期检定、校准
•有无检定档案
4.7-检验工位的总体设置。
•检验工位的设置是否合理
•检验工位的场地是否足够
4.8-批的识别标记。
•所有不同的批次,有无从外购件进厂、制造到成品出厂全过程的
批鉴别的标识
4.9-不合格品的隔离。
•有无外购件不合格品的隔离、处理程序
•检定人员有无资格证明
3.2-生产现场的测量间。
-设备的状况及其跟踪。
•检测设备能否满足生产需要
•检定周期是否合理
•是否按周期进行检定*
•对检定不合格的是否及时校准或维修
•现场使用的检测设备是否完好
-人员。
•人数能否满足工作需要
•检定人员有无资格证明
3.3-性能试验及疲劳试验。
-设备的状况及其跟踪。
扣分
结论
评估记录
•对最初样件是否进行过验审
•有无验审报告
4.3检验工艺及图纸。*
•有无外购件进厂的检验工艺卡及图纸
4.4-定期检验(性能、疲劳、实验室)。
•是否按照检验工艺卡要求的频次进行性能、疲劳、实验室检验
4.5-检验手段(设备及合格证)。
•是否配备足够的检验设备(包括性能、疲劳、实验室)用以接收
1-组织机构
1.1总的组织机构定义(机构表、职能说明)。
•有无总体机构图,是否元善、合理,能否正确地反映企业的组 织体系
•有无各部门职能分配表,是否完善、可行
•是否由最高管理者负责、批准发布质量方针和质量手册
1.2质量部门组织机构定义。*
•是否指定质量各部门负责人,各部门之间的联系是否存在
1.3质量部门人员编制。*