作业准备验证及停工后验证规定
作业准备验证记录表

日期
ቤተ መጻሕፍቲ ባይዱ产品名称/图号
工序名称
验证结果
首检结果
操作人员签字
备注栏
1
2
3
4
5
6
7
8
9
10
11
12
13
14
15
16
17
18
19
20
21
22
23
24
25
26
27
28
29
二、具体验证内容:1、产品名称图号、批号、数量是否正确?2、工艺(作业指导书)文件是否准备好并正确?3、机器设备是否运转正常?4、测量设备是否正确并适用?5、工装夹具是否正常?6、有无异常现象?7、首检是否合格?
三、填写要求:1、验证结果:验证符合的打“√”,不符合的请填写不符合内容及处理结果;2、首检结果:合格的打“√”,不合格的经处理后的结果在“备注栏”内说明。
一、要求:1、在作业的初步运行(包括:计划或非计划停工后)、材料的改变、作业更改、运行间过长的停顿、变换产品生产/加工等情况下,均须进行作业准备验证,并记录于“作业准备验证记录表”中。如验证结果不符合生产所要求,则由相关生产车间进行处理。2、每个工作班,工装、设备调整后加工的首、末件产品,执行首、末件检验。作业准备验证产生的不合格品,按《不合格品控制程序》执行。
IATF16949作业准备验证程序(停工后验证)

按照4.2的内容,各项作业准备的验证项目均无异常后,开始正常生产。
5.相关文件
现场有产品的作业文件:包括工艺流程卡,图纸或者控制计划
挤压首、巡检记录表
检验员
15
做到5S
符合工5S管理程序的要求
不记录
检验员
16
选定检测所需的检具,计量器具,样件
符合检验指导书,图纸,控制计划上的要求
不记录
检验员
17
准备好生产产品的检验文件,例如图纸,控制计划
现场有检验文件:包括图纸或者控制计划
挤压首、巡检记录表
③自然灾害(比如火灾等)后造成生产停工
④公共设施中断(比如停电停水等)后造成生产停工
⑤劳动力短缺后造成生产停工
⑥基础设施的破坏后造成生产停工
4.工作流程及内容
4.1作业准备的内容
审核
批准
日期
-181-
编制部门:质量部
文件名称
作业准备验证程序(停工后验证)
编号:
版次:
版本号:
编制人:
第2页共5页
日期:
-180-
编制部门:质量部
文件名称
作业准备验证程序(停工后验证)
编号:
版次:
版本号:
编制人:
第1页共5页
日期:
1.目的
作业开始前,包括在计划或非计划生产停工期后的作业开始,通过对该作业工位上的人、机、料、法、环、测的检验或测验,来验证作业准备的精确性和准确性。确保作业开始后,能持续生产出合格的产品,避免产生批量的不合格品,预防产生不良的质量成本,确保生产作业的有效性。
检验员
3
转岗人员具备上岗资质
核查人员的培训记录,资质证书
iatf16949-2016中文版标准

控制计划
2
标准化作业
3
作业准备验证
4
停工后的验证
5
全面生产维护
6
工装检具管理
7
生产排程
8
标识及可追溯性
9
顾客或供方财产
10
防护
11
变更控制
12
临时更改
13 产品和服务的放行
14
尺寸功能检验
15
外观项目
16 外部提供的验证
17
不合格品控制
18
可疑产品控制
19
返工品控制
应制定、评审和更新控制计划(发现了不合格品、变更、投诉,基于风险分析的设定频率) 确保操作指导书被传达、清晰易懂、易于得到,并且包含操作员安全规则 准备人员的形成文件信息;适用时,统计验证;首件/末件确认和比较;保留记录 计划或非计划生产停工后,应确定、采取措施确保产品符合性 识别设备;备件;包装防护;目标(OEE、MTBF、MTTR);预防性和预测性防护;周期性检修 维护维修设施与人员;存储、修复;更换;设计修改文件;标识;顾客工具应验证,永久标记 为满足顾客订单需求来安排生产;生产由信息系统支持 识别隔离不合格品或可疑品;如顾客或监管标准有规定,确保序列化标识 应爱护、识别、验证、保护和维护;当不正确使用、丢失、损坏或发现不适用,应报告 评估库存品状况;存储容器放置和存储环境;优化库存管理系统;控制过期产品 应控制,验证和确认变更活动;对风险分析形成文件;保留验证和确认记录;进行试生产 替代控制方法应形成文件过程;实施前应获得批准;定期评审、指导书 符合接受准则的证据;授权放行人员;围绕控制计划进行 按照控制计划中的规定;根据工程材料和性能标准;每一种产品;结果可供顾客评审 资源(包括照明);原版样件;样件及设备维护和控制;人员能力和资格 接收
停产后验证管理制度

停产后验证管理制度一、前言停产后验证管理制度是指企业在停产生产之后,对设备、工艺、设施等进行验证,以确保设备的正常运行、产品的质量稳定以及生产能力的恢复。
停产后验证管理制度建立完善,能够帮助企业降低风险、提高效率,保证生产的正常进行。
本文将从停产后验证的定义、流程、责任分工等方面进行探讨,以期为企业建立健全的停产后验证管理制度提供参考。
二、停产后验证的定义停产后验证是指企业在停产生产之后,对设备、工艺、设施等进行系统性的验证,以评估设备和工艺是否符合设计要求,是否能够满足生产需求,以及是否存在潜在的问题。
停产后验证旨在保证生产设备的正常运行、产品的质量稳定以及生产能力的恢复。
三、停产后验证的流程停产后验证的流程主要包括以下几个步骤:1. 制定停产后验证计划:在停产生产之后,企业应制定停产后验证计划,明确验证的范围、目标及流程。
验证计划应包括验证的内容、方法、时间表、责任人等内容。
2. 进行设备检查:对设备、工艺、设施等进行全面检查,确保设备处于正常状态,满足生产需求。
同时,检查是否存在老化、腐蚀、损坏等问题,及时予以修复或更换。
3. 进行性能验证:对设备的性能进行全面验证,确保设备运行稳定、性能良好。
可通过实验室测试、模拟生产等方式进行验证。
4. 进行质量验证:对生产产品的质量进行验证,确保产品符合设计要求、达到标准。
可以通过抽样检验、质量控制图、质量评估等方式进行验证。
5. 进行环境验证:对生产环境进行验证,确保环境符合生产要求、符合相关法规。
可以通过环境监测、环境评估等方式进行验证。
6. 制定改进措施:根据验证结果,制定改进措施,对设备、工艺、环境等进行优化改进,以提高生产效率、降低风险。
7. 完成验证报告:对停产后验证的全部过程进行总结,形成停产后验证报告,明确验证的结果、存在的问题、改进措施等内容。
8. 保持持续改进:停产后验证并不是一次性的工作,企业应建立持续改进机制,定期对设备、工艺、环境等进行验证,不断完善验证管理制度。
作业准备验证及停工后验证

作业准备验证及停工后验证随着科技的不断发展,各行各业都逐渐数字化,因此在软件开发、系统运维等领域中,验证和测试变得尤为重要。
其中,作业准备验证和停工后验证是两个关键的环节。
本文将以这两个环节为主题,探讨它们在软件开发和系统运维中的重要性和具体实施方法。
一、作业准备验证的重要性作业准备验证是指在软件开发或系统运维开始之前,对准备进行的工作进行验证和确认。
它可以帮助发现问题和风险,并及时采取措施进行修复,从而确保后续工作的顺利进行。
作业准备验证的重要性体现在以下几个方面:1. 发现问题和风险:作业准备验证可以帮助发现在软件开发或系统运维过程中可能存在的问题和风险,如配置错误、安全漏洞等。
通过在验证阶段发现并解决这些问题,可以避免在后续工作中造成更大的损失。
2. 确保工作的准确性:作业准备验证可以帮助确认所做工作的准确性,包括配置文件的正确性、系统的兼容性等。
只有在确认了准备工作的准确性之后,才能进行下一步的工作。
3. 提高工作效率:通过作业准备验证,可以提前发现潜在的问题并解决,避免了后续工作中的不必要的返工和延误。
这样可以有效提高工作的效率,节省时间和资源成本。
二、作业准备验证的实施方法作业准备验证的实施方法可以根据具体情况而定,但一般包括以下几个步骤:1. 确定验证目标:在进行作业准备验证之前,首先需要明确验证的目标和范围。
这可以帮助确定验证的重点和方向,使验证工作更加有针对性。
2. 设计验证方案:根据验证目标,设计验证方案。
验证方案应包括验证的方法、步骤和所需资源等。
可以根据需要,使用自动化测试工具或编写脚本来进行验证。
3. 执行验证工作:根据验证方案,执行验证工作。
这包括准备测试环境、执行测试用例、收集和分析测试结果等。
在执行过程中,应严格按照验证方案的要求进行操作,并记录相关的测试数据和结果。
4. 分析和修复问题:在验证过程中,可能会发现一些问题和风险。
这些问题需要及时记录并进行分析,然后采取相应的措施进行修复。
作业准备验证管理办法

作业准备验证管理办法1. 引言作业准备验证是在进行作业前对所需资源、设备、工具和程序的验证和确认的过程。
它是作业前一项重要的准备工作,通过对作业准备的验证,能够确保作业的安全性、高效性和稳定性。
本文档旨在制定作业准备验证的管理办法,以确保每项作业的顺利进行。
本管理办法适用于所有作业准备验证的过程。
2. 作业准备验证流程作业准备验证流程是指根据作业的要求和程序,对作业所需资源、设备、工具进行验证的步骤。
作业准备验证流程如下:1.确定作业要求:明确作业的目标、范围和要求。
2.制定作业准备验证计划:根据作业要求制定作业准备验证的计划,并确定验证的内容和任务分工。
3.执行作业准备验证:按照制定的计划,对作业所需资源、设备、工具进行验证,包括检查设备的完好性和可用性、确认资源的准备情况、检查工具的可靠性等。
4.记录验证结果:记录每项验证的结果,包括验证时间、验证人员、验证内容、验证方法、验证结果等。
5.评估验证结果:根据验证结果进行评估,确认是否符合作业的要求。
6.提出改进措施:对不符合要求的验证结果,提出相应的改进措施或修复措施,并进行记录。
7.完成作业准备验证:当所有作业准备都验证完成且满足要求时,完成作业准备验证的流程。
3. 作业准备验证的注意事项在进行作业准备验证时,需要注意以下事项:3.1. 验证人员的要求作业准备验证需要经过专业的人员进行验证。
验证人员应具备以下要求:•具备相关的作业知识和技能。
•熟悉作业要求和验证流程。
•具备良好的沟通和协调能力。
3.2. 验证的频率和时机对于重要的作业和设备,需要进行定期验证,以确保其可靠性和安全性。
验证的频率和时机应根据作业的特点和要求来确定。
3.3. 验证结果的记录和保留对每次作业准备验证的结果都应进行记录,并保留在可查阅的地方。
验证结果的记录应包括验证时间、验证人员、验证内容、验证方法、验证结果等。
3.4. 改进措施的落实和跟踪对于不符合要求的验证结果,应及时提出相应的改进措施,并进行落实和跟踪。
IATF16949作业准备验证及停工后验证规定
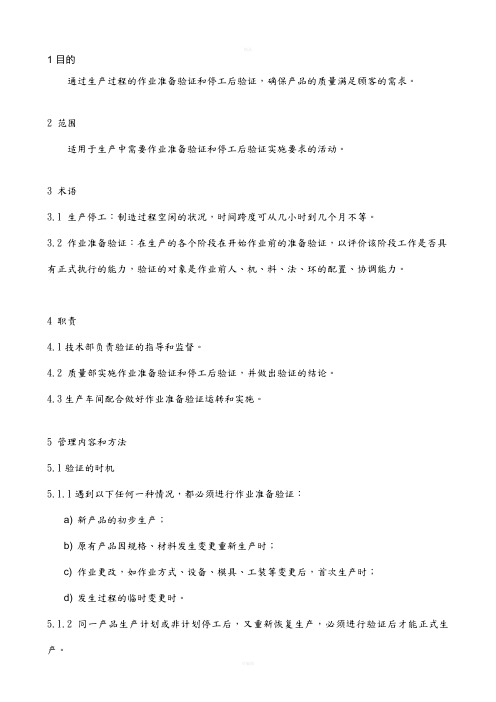
1 目的通过生产过程的作业准备验证和停工后验证,确保产品的质量满足顾客的需求。
2 范围适用于生产中需要作业准备验证和停工后验证实施要求的活动。
3 术语3.1 生产停工:制造过程空闲的状况,时间跨度可从几小时到几个月不等。
3.2 作业准备验证:在生产的各个阶段在开始作业前的准备验证,以评价该阶段工作是否具有正式执行的能力,验证的对象是作业前人、机、料、法、环的配置、协调能力。
4 职责4.1技术部负责验证的指导和监督。
4.2 质量部实施作业准备验证和停工后验证,并做出验证的结论。
4.3生产车间配合做好作业准备验证运转和实施。
5 管理内容和方法5.1验证的时机5.1.1遇到以下任何一种情况,都必须进行作业准备验证:a) 新产品的初步生产;b) 原有产品因规格、材料发生变更重新生产时;c) 作业更改,如作业方式、设备、模具、工装等变更后,首次生产时;d) 发生过程的临时变更时。
5.1.2 同一产品生产计划或非计划停工后,又重新恢复生产,必须进行验证后才能正式生产。
5.2 验证的方法5.2.1评审法按照规定的《作业准备/停工后验证记录》的检查项目,对作业准备进行评审,即是否使用了正确的作业指导书、控制计划、检验标准,以及机器设备参数设置是否按照作业指导书的要求设置。
当评审结果符合规定要求时,得到技术部批准后,才能正式开始生产。
5.2.2首、末件比较法用本批生产的首件和前一批生产的末件进行比较,当本批首件的质量达到或超出前一批末件的质量水平时,才能正式开始生产。
本批生产的首件和末件进行比较,当本批末件的质量达到或超出首件,才能进行下一班的生产。
5.2.3适当时,也使用统计方法进行验证。
生产足够的产品以构成SPC所用容量的子组,对产品进行测量,并将结果绘制成控制图表。
如果这些测量结果落在控制限区域的中间1/3范围内,则作业准备可获批准。
5.3 验证的实施步骤:5.3.1技术部在确认上述时机中的任何一项时,必须以书面的形式通知制造部门进行作业准备验证或停工后验证。
工程开工及停、复工检查验收制度

工程开工及停、复工检查验收制度
1、工程开工前,必须有按照设计程序批准的施工设计,由总工程师组织有关业务科室人员进行会审后,由项目负责人审定、签字后执行。
2、施工单位根据施工计划提前制定作业规程及相关安全技术措施和开工卡片,报主管科室组织会审后,报总工程师批准,方可开工。
3、工程开工前,工程安监部必须按照设计要求标明安全、环境、质量措施,下达安全生产复工通知书。
4、施工过程中,如需变更设计,必须报项目公司总工程部批准后,方可实施。
5、施工地点必须按照规定悬挂相关扬尘治理图板,图板必须字迹工整、清晰,符合技术规范要求。
6、施工过程中地质条件发生变化或其它特殊原因需停工时,由施工单位申请,经有关科室组织验收,符合停工条件后,方可停工。
短时间停工,施工单位必须向有关单位下达停工通知书,长时间停工时,施工单位必须制定停、复专项安全技术措施。
7、复工前,主管科室必须组织相关科室对停工地点进行复工验收,施工单位对复工验收提出的问题,必须及时落实整改,符合复工条件后,方可正式复工。
8、工程竣工后,施工单位通知安全质量科、调度室、生产计划科等相关科室严格按照质量标准化要求进行验收,验收合格后,各相关科室必须在工程验收报告上签字,并存档备查。
生产计划科
2009.3.25。
作业准备的验证指导书

作业准备的验证指导书
文件编号:
1 .目的
对公司生产前工序作业准备规定必要的验证手段,保证生产可以正常、有效进行。
2 .范围
适用于本公司产品生产前的作业准备。
3 .职责
3.1 品质部负责制定验证记录表的相关内容。
3.2 车间班组长负责填写《作业准备验证记录》。
4 .程序及要求
4.1 在作业的初步运行、材料的改变、作业更改、运行间过长的停顿、变换产品生产/加工等情况下,均须进行作业准备验证,并记录于“作业准备验证记录表”中。
如验证结果不符合生产所要求,则由相关生产车间进行处理。
4.2 每个工作班,工装、设备调整后生产的首件产品,按《产品监视和测量控制程序》执行首件检验。
作业准备产生的不合格品,按《不合格品控制程序》执行。
4.3 新产品、过程更改,进行试生产后进行PPAP及生产确认试验,按APQP、PPAP要求执行。
4.4 每次进行作业准备验证,都必须由验证人员认真填写《作业准备验证记录》,由生产部保存。
5 .相关文件
QD7.1.7-2020监测资源控制规范
QD8.6.1-2020产品和服务放行控制规范
QD8.7.1-2020不合格控制规范APQP、PPAP
6 .相关记录
6.1 QR
7.5-16《作业准备验证记录》
7、
编制:审核:批准:
日期:日期:日期:。
IATF16949作业准备验证及停工后验证规定
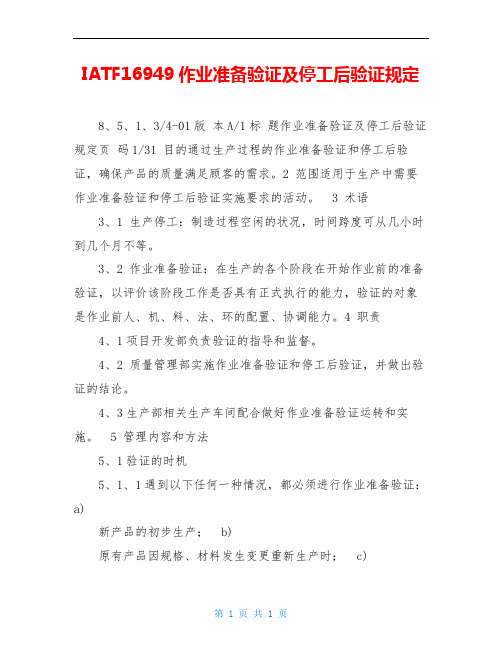
IATF16949作业准备验证及停工后验证规定8、5、1、3/4-01版本A/1标题作业准备验证及停工后验证规定页码1/31 目的通过生产过程的作业准备验证和停工后验证,确保产品的质量满足顾客的需求。
2 范围适用于生产中需要作业准备验证和停工后验证实施要求的活动。
3 术语3、1 生产停工:制造过程空闲的状况,时间跨度可从几小时到几个月不等。
3、2 作业准备验证:在生产的各个阶段在开始作业前的准备验证,以评价该阶段工作是否具有正式执行的能力,验证的对象是作业前人、机、料、法、环的配置、协调能力。
4 职责4、1项目开发部负责验证的指导和监督。
4、2 质量管理部实施作业准备验证和停工后验证,并做出验证的结论。
4、3生产部相关生产车间配合做好作业准备验证运转和实施。
5 管理内容和方法5、1验证的时机5、1、1遇到以下任何一种情况,都必须进行作业准备验证:a)新产品的初步生产;b)原有产品因规格、材料发生变更重新生产时;c)作业更改,如作业方式、设备、模具、工装等变更后,首次生产时;d)发生过程的临时变更时。
5、1、2 同一产品生产计划或非计划停工后,又重新恢复生产,必须进行验证后才能正式生产。
5、2 验证的方法5、2、1评审法按照规定的《作业准备/停工后验证记录》的检查项目,对作业准备进行评审,即是否使用了正确的作业指导书、控制计划、检验标准,以及机器设备参数设置是否按照作业指导书的要求设置。
当评审结果符合规定要求时,得到项目开发部批准后,才能正式开始生产。
5、2、2首、末件比较法用本批生产的首件和前一批生产的末件进行比较,当本批首件的质量达到或超出前一批末件的质量水平时,才能正式开始生产。
本批生产的首件和末件进行比较,当本批末件的质淅川县林吉特精密科技有限公司文件编号LJT-GL/8、5、1、3/4-01版本A/1标题作业准备验证及停工后验证规定页码2/3量达到或超出首件,才能进行下一班的生产。
5、2、3 适当时,也使用统计方法进行验证。
作业准备验证规定

厦门市XXX 有限公司
质 量 环 境 管 理 体 系
Quality&Environmental Management System
作业准备验证规定
(依据GB/T19001-2016 idt ISO9001:2015 《质量管理体系-要求》 标准而制定) (依据GB/T24001-2016 idt ISO14001:2015 《环境管理体系 要求及使用指南》而制定)
YY-QG-06 (第A/0版) 拟编: 审核: 批准:
发布日期:二0一八年六月八日 实施日期:二0一八年六月八日
地址:中国. 福建. 厦门XXX 电话:++86-592-XXX 传真:++86-592-XXXX
受 控 状 态 发 放 编 号
邮政编码:361000
1.0 目的:
进行必要的作业准备验证以确保生产过程的稳定。
2.0 适用范围:
适用于生产过程对作业的初步运行、运行时间过长的停顿的作业准备验证的有效控制。
3.0 职责:
3.1 生产综合部是作业准备验证的归口部门。
3.2 其他部门是配合部门。
4.0 工作程序:
4.1 生产综合部对作业的初步运行、运行间过长的停顿(12个月以上)进行作业准备验证。
4.2 生产前,生产综合部按生产计划合理安排人员组织生产,车间班组长、操作人员应对设备进行检
查。
4.3 产品生产操作规程是否为现行有效版本,并与生产产品相符。
4.4 确认领取原料是产品内容相一致的原料,然后组织产品生产。
5.0 质量记录:
无
1。
煤矿零星工程停工验收制度

煤矿零星工程停工验收制度第一章总则1.1 为了加强煤矿零星工程的管理,提高工程质量,确保安全生产,制定本规定。
1.2 本规定适用于煤矿零星工程项目的停工验收,主要包括工程项目的前期准备、施工过程、验收程序等内容。
1.3 煤矿零星工程项目是指对煤矿生产、运输、保障等方面进行改造、更新或新建工程的项目。
第二章停工验收管理2.1 项目经理是煤矿零星工程项目的主要负责人,负责项目的组织、协调和监督工作。
2.2 项目组设立专门的验收小组,包括项目经理、施工人员、设计人员等相关人员,负责对工程项目的停工验收工作进行监督和检查。
2.3 施工单位应按照设计要求和相关规定进行施工,确保工程质量。
第三章停工验收程序3.1 工程项目竣工后,项目组负责组织验收小组对工程进行停工验收。
3.2 验收小组应对工程质量、施工工艺、安全措施等进行全面检查。
3.3 验收小组应当就工程质量、施工工艺等问题进行讨论,并做出验收意见。
3.4 验收小组应填写验收报告,对工程项目的合格性做出评定,并报主管部门备案。
第四章验收标准4.1 工程项目应符合相关国家标准和规定,确保工程质量。
4.2 工程项目应符合设计要求,施工工艺应正确、合理。
4.3 工程项目应符合安全生产标准,确保员工安全。
第五章责任追究5.1 对未通过停工验收的工程项目,项目经理承担主要责任,必须对问题进行整改。
5.2 对于工程质量、安全问题造成重大事故的,将追究相关责任人的法律责任。
5.3 对于违反本规定的行为,将给予相应的处罚。
第六章附则6.1 本规定的解释权归煤矿公司所有。
6.2 本规定自发布之日起生效。
煤矿零星工程停工验收制度的制定,对于规范煤矿工程项目的建设过程,提高工程质量,保障安全生产具有重要意义。
希望各相关单位严格执行本规定,确保工程的验收工作能够顺利实施。
作业准备验证管理办法
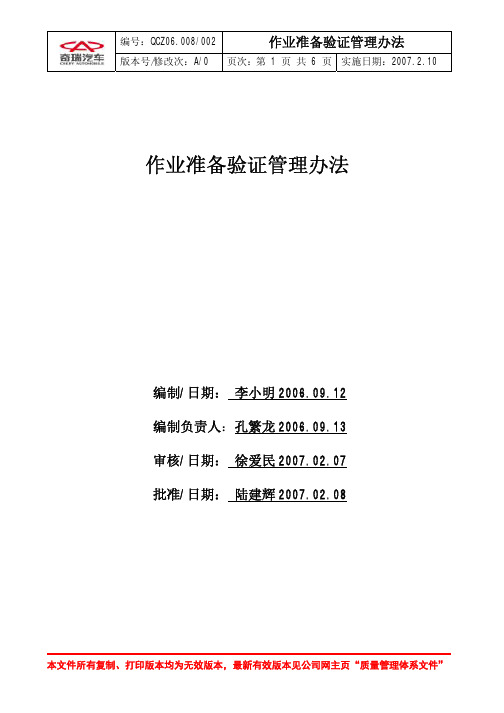
常点重新计算
试装结果 OK
对条件 A,需再次采购样件,并按《生产件 NO 批准程序》进行验证;对条件 B 和 C,应分
析原因,采取措施,并对措施再次验证,具
体验证分别参照《过程变更控制程序》、《生
产系统变更控制办法》执行。
材料更改/供应商工艺更改/停产
生产件批准
OK
8
正式批量生产
9
结束
本文件所有复制、打印版本均为无效版本,最新有效版本见公司网主页“质量管理体系文件”
是指在作业的初步运行材料的改变作业的更改工艺更改或场地更改较长时间停顿停产达12个月或以上等任一情况下在开始批量生产前必须对作业的设备工装材料作业指导书监视和检测装置等是否能满足稳定生产出合格产品进行验证
编号:QCZ06.008/002
作业准备验证管理办法
版本号/修改次:A/0 页次:第 1 页 共 6 页 实施日期:2007.2.10
本文件所有复制、打印版本均为无效版本,最新有效版本见公司网主页“质量管理体系文件”
编号:QCZ06.008/002
作业准备验证管理办法
版本号/修改次:A/0 页次:第 6 页 共 6 页 实施日期:2007.2.10
再次验证,具体参照《过程变更控制程序》执行; 5.5.3、当生产系统 SOP 后产品的工艺更改试装不合格时, 应分析原因,采取措施,并对措施再次验证, 具体参照《生产系统过程变更控制办法》执行; 5.5.4 再次验证通过后,按照 5.1—5.5 要求进行作业准备的再验证。
4、职责
序号 部 门
职
责
4.1
工艺部门
负责提供正确的控制计划和作业指导书,适用时对关键、重要技术要求进行 SPC 控制。
4.2 专业制造公司 负责对批产后的设备、工装、材料、作业指导书、监视和检测装置进行确认,组 织生产。
作业准备验证规定
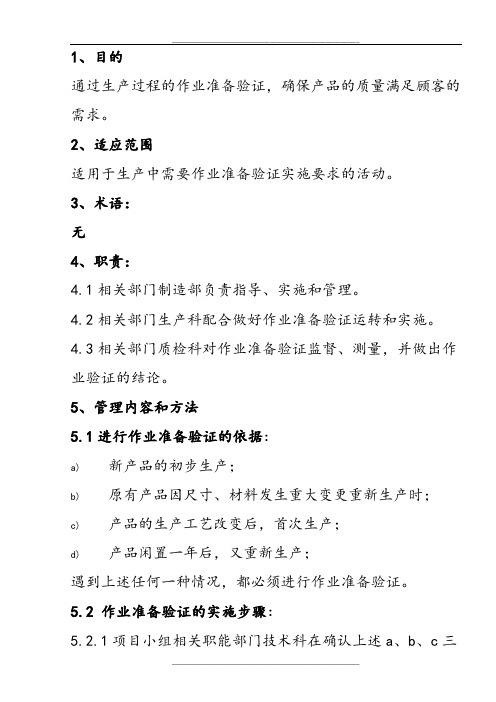
1、目的通过生产过程的作业准备验证,确保产品的质量满足顾客的需求。
2、适应范围适用于生产中需要作业准备验证实施要求的活动。
3、术语:无4、职责:4.1相关部门制造部负责指导、实施和管理。
4.2相关部门生产科配合做好作业准备验证运转和实施。
4.3相关部门质检科对作业准备验证监督、测量,并做出作业验证的结论。
5、管理内容和方法5.1进行作业准备验证的依据:a)新产品的初步生产;b)原有产品因尺寸、材料发生重大变更重新生产时;c)产品的生产工艺改变后,首次生产;d)产品闲置一年后,又重新生产;遇到上述任何一种情况,都必须进行作业准备验证。
5.2 作业准备验证的实施步骤:5.2.1项目小组相关职能部门技术科在确认上述a、b、c三项中的任何一项时,必须以书面的形式通知相关部门生产科。
5.2.1.1当产品的加工尺寸发生重大变化、加工工艺发生更改时,由相关职能部门技术科发出《工艺文件更改通知单》,通知相关部门制造部,操作人员在接到通知后才能生产。
5.2.1.2 当材料规格发生变化或需用其他材料代用时,须重新通过工艺确认,并重新通过PPAP,得到顾客认可后方可正式生产。
5.2.1.3 当产品停止一年以内重新生产,由相关部门制造部通知车间做好作业准备验证,须重新通过工艺确认。
当产品停止一年以上重新生产,当顾客有要求时,必须重新通过PPAP,得到顾客认可后方可正式生产。
5.2.2 相关部门生产科在安排生产计划中注明需要进行作业准备验证的需求。
5.2.3 相关制造部生产科应根据安排的生产时间,提前检查,落实材料准备,工装和文件的准备工作,并及时与车间和操作人员联系。
5.2.4 进行生产作业准备验证时,各部门机修工按照《控制计划》工艺参数要求,调试产品,并记录在《工艺参数记录表》上,并由操作人员按照《控制计划》和《作业指导书》要求自检,认为合格的产品作为首件产品递交巡回检验员检验,相关部门巡回检验员将本次生产的产品与上次生产的产品在主要尺寸、外观质量和其它需要测量的项目上进行比较,巡回检验员按照{控制计划}要求对产品进行逐项检验,并填写《首件检验记录》。
作业准备验证规范(含表格)

作业准备验证规范(含表格)
作业准备验证规范
(ISO9001-2015)
1.目的:
进行必要的作业准备验证,以确保生产过程的稳定。
2.适用范围:
适用于生产过程对作业的初步运行、运行间过长的停顿的作业准备验证的有效控制。
3.定义:
3.1作业的初步运行——每天/每班批量生产、材料或生产品种更换后、工艺更改后、或设备故障排除后的第一次作业运行。
4.职责:
4.1生产部是作业准备验证的归口部门。
4.2其他部门是配合部门。
5.工作程序:
5.1生产部对作业的初步运行,以及运行时间过长的停顿(12个月以上),均应进行作业准备验证。
5.2相关作业人员均需要通过培训合格后才能上岗操作。
5.3作业准备验证的内容:
5.3.1凡是用作试模、校模的生产件一律做好标识,或用规定的容器,或放于
指定的区域,防止不合格品流入生产件中;只有通过检验员验证认可以后,才能作为合格的生产件流入下一道工序。
5.4由生产部、质保部相关人员进行作业准备验证,并做好相关验证记录,只有全部项目达到要求后才能进行正常生产。
6.相关文件
生产管理程序
人力资源管理程序
检验和试验控制程序7.所属记录
设备点检记录卡
设备点检表.d oc
产品首件确认单
产品首检记录表.d
oc 首件确认表.d oc首件检查确认单.d oc
作业准备验证表
作业准备验证记录
表.d oc 作业准备验证记录
表.xl s。
IATF16949作业准备验证程序(停工后验证)

④公共设施中断(比如停电停水等)后造成生产停工
⑤劳动力短缺后造成生产停工
⑥基础设施的破坏后造成生产停工
4.工作流程及内容
4.1作业准备的内容
审核
批准
日期
-181-
编制部门:质量部
文件名称
作业准备验证程序(停工后验证)
编号:
版次:
版本号:
编制人:
第2页共5页
日期:
3.2 末件:当班生产线或生产设备在结束生产或停工停机时,加工的最后一件产品。
3.3造成计划生产停工的情况如下,但不限于下述情况:
①5S工作
②更换产品型号
③更换工装模具
④员工计划性培训或会议
3.4 造成非计划生产停工的情况如下,但不限于下述情况:
①关键设备故障后造成生产停工
②供应链中断后造成生产停工
不记录
检验员
8
有效进行设备点检
核查设备点检记录上的内容是否正确
不记录
检验员
9
选定生产所需的物料
符合工艺操作规程或控制计划上规定的物料
挤压首、巡检记录表
检验员
10
经进料检验合格的物料
核查物料上有无合格标示
不记录
检验员
11
物料标识清晰,批次信息完整
符合工艺操作规程或控制计划上规定的物料信息
挤压首、巡检记录表
-180-
编制部门:质量部
文件名称
作业准备验证程序(停工后验证)
编号:
版次:
版本号:
编制人:
第1页共5页
日期:
1.目的
作业开始前,包括在计划或非计划生产停工期后的作业开始,通过对该作业工位上的人、机、料、法、环、测的检验或测验,来验证作业准备的精确性和准确性。确保作业开始后,能持续生产出合格的产品,避免产生批量的不合格品,预防产生不良的质量成本,确保生产作业的有效性。
作业前准备验证
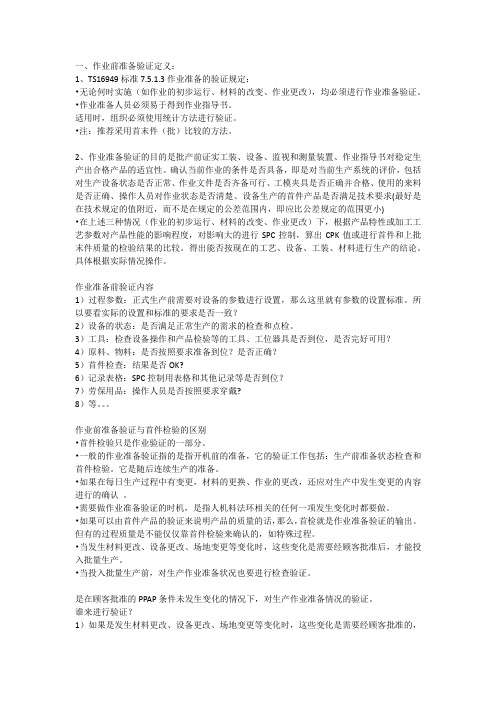
一、作业前准备验证定义:1、TS16949标准7.5.1.3作业准备的验证规定:•无论何时实施(如作业的初步运行、材料的改变、作业更改),均必须进行作业准备验证。
•作业准备人员必须易于得到作业指导书。
适用时,组织必须使用统计方法进行验证。
•注:推荐采用首末件(批)比较的方法。
2、作业准备验证的目的是批产前证实工装、设备、监视和测量装置、作业指导书对稳定生产出合格产品的适宜性。
确认当前作业的条件是否具备,即是对当前生产系统的评价,包括对生产设备状态是否正常、作业文件是否齐备可行、工模夹具是否正确并合格、使用的来料是否正确、操作人员对作业状态是否清楚、设备生产的首件产品是否满足技术要求(最好是在技术规定的值附近,而不是在规定的公差范围内,即应比公差规定的范围更小)•在上述三种情况(作业的初步运行、材料的改变、作业更改)下,根据产品特性或加工工艺参数对产品性能的影响程度,对影响大的进行SPC控制,算出CPK值或进行首件和上批末件质量的检验结果的比较。
得出能否按现在的工艺、设备、工装、材料进行生产的结论。
具体根据实际情况操作。
作业准备前验证内容1)过程参数:正式生产前需要对设备的参数进行设置,那么这里就有参数的设置标准。
所以要看实际的设置和标准的要求是否一致?2)设备的状态:是否满足正常生产的需求的检查和点检。
3)工具:检查设备操作和产品检验等的工具、工位器具是否到位,是否完好可用?4)原料、物料:是否按照要求准备到位?是否正确?5)首件检查:结果是否OK?6)记录表格:SPC控制用表格和其他记录等是否到位?7)劳保用品:操作人员是否按照要求穿戴?8)等。
作业前准备验证与首件检验的区别•首件检验只是作业验证的一部分。
•一般的作业准备验证指的是指开机前的准备,它的验证工作包括:生产前准备状态检查和首件检验。
它是随后连续生产的准备。
•如果在每日生产过程中有变更,材料的更换、作业的更改,还应对生产中发生变更的内容进行的确认。
作业准备验证管理办法

1 适用范围适用于XXX公司所需的作业准备验证。
2 职责2.1技术质量部下达作业验证计划,生产部负责组织作业准备验证。
2.2质量部负责组织有关产品的检验和试验及质量状况的统计。
2.3产品技术部、质量部、采购部、车间参与作业准备验证。
3 管理办法和要求4.1作业准备验证时机4.1.1产品调试生产作业时需进行作业准备验证并进行作业后的认可。
4.1.2形成产品的材料发生改变时。
4.1.3产品生产过程中发生作业内容和方式等更改时。
4.1.4运行间过长时间的停顿时,即本公司停止生产半年以上时间的产品,重新启动生产时。
4.1.5 作业设备发生变更时。
4.1.6外部客户要求对产品进行审核时。
4.2作业准备要求4.2.1作业准备要对人、机、料、法、环、测等方面进行检查,如上岗人员资格、设备、工装、辅具完好情况、检具合格与否、作业指导文件是否有效、材料是否合格、环境是否整洁有序、标准样件是否合乎要求等。
4.3 作业准备验证方法4.3.1产品初次生产作业时, 如新产品试生产结束后,批量生产前,由技术部组织各部门在生产现场验证,由质量员测量连续的5件并进行测量结果记录,如果5件全部在公差范围内则过程是受控的,如有一件未达到产品特性要求,则由车间工艺员重新调整过程至连续5件全部合格则作业准备验证通过,由技术部组织填写“作业准备验证指导书”,并附检验记录。
4.3.2运行间过长时间的停顿、作业更改和作业过程中发生对形成产品的材料有改变时,由技术部组织质量部、采购部、生产部采用首件与末件或上一批次数据和记录(质量记录、纠正措施等)比较的方法进行作业准备验证,由检查员填写首件比较记录,首件与末件或与上一批次数据和记录比较检验合格后,作业准备验证通过;如不合格,由技术部调整过程至合格。
作业准备通过后,由技术部填写“作业准备验证指导书”,相关部门会签,并附检验记录。
4.3.3 量产后每班正式生产时,质量部采用首件与末件或上一批次数据和记录(质量记录、纠正措施等)比较的方法进行作业过程控制,由质量员填写首件比较记录,首件与末件或与上一批次数据和记录比较检验合格后,作业正常进行,检验记录由质量部保存。
- 1、下载文档前请自行甄别文档内容的完整性,平台不提供额外的编辑、内容补充、找答案等附加服务。
- 2、"仅部分预览"的文档,不可在线预览部分如存在完整性等问题,可反馈申请退款(可完整预览的文档不适用该条件!)。
- 3、如文档侵犯您的权益,请联系客服反馈,我们会尽快为您处理(人工客服工作时间:9:00-18:30)。
1目的通过生产过程的作业准备验证和停工后验证,确保产品的质量满足顾客的需求。
2 范围
适用于生产中需要作业准备验证和停工后验证实施要求的活动。
?
3 术语?
3.1 生产停工:制造过程空闲的状况,时间跨度可从几小时到几个月不等。
3.2 作业准备验证:在生产的各个阶段在开始作业前的准备验证,以评价该阶段工作是否具有正式执行的能力,验证的对象是作业前人、机、料、法、环的配置、协调能力。
?
4 职责
4.1技术部负责验证的指导和监督。
?
4.2 质量部实施作业准备验证和停工后验证,并做出验证的结论。
4.3生产车间配合做好作业准备验证运转和实施。
?
5 管理内容和方法
5.1验证的时机
5.1.1遇到以下任何一种情况,都必须进行作业准备验证:
a) 新产品的初步生产;?
b) 原有产品因规格、材料发生变更重新生产时;?
c) 作业更改,如作业方式、设备、模具、工装等变更后,首次生产时;?
d) 发生过程的临时变更时。
5.1.2 同一产品生产计划或非计划停工后,又重新恢复生产,必须进行验证后才能正式生产。
5.2 验证的方法
5.2.1评审法
按照规定的《作业准备/停工后验证记录》的检查项目,对作业准备进行评审,即是否使用了正确的作业指导书、控制计划、检验标准,以及机器设备参数设置是否按照作业指导书的要求设置。
当评审结果符合规定要求时,得到技术部批准后,才能正式开始生产。
5.2.2首、末件比较法
用本批生产的首件和前一批生产的末件进行比较,当本批首件的质量达到或超出前一批末件的质量水平时,才能正式开始生产。
本批生产的首件和末件进行比较,当本批末件的质量达到或超出首件,才能进行下一班的生产。
5.2.3适当时,也使用统计方法进行验证。
生产足够的产品以构成SPC所用容量的子组,对产品进行测量,并将结果绘制成控制图
表。
如果这些测量结果落在控制限区域的中间1/3范围内,则作业准备可获批准。
5.3?验证的实施步骤:?
5.3.1技术部在确认上述时机中的任何一项时,必须以书面的形式通知制造部门进行作业准备验证或停工后验证。
?
5.3.1.1当产品的加工尺寸发生重大变化、加工工艺发生更改时,由技术部发出《工艺文件更改通知单》,通知制造部,操作人员在接到通知后才能生产。
?
5.3.1.3?当产品生产停工后重新恢复生产,由技术部通知车间做好作业准备验证,须重新通过工艺确认。
?
5.3.2??制造部在安排生产计划中注明需要进行作业准备验证的需求。
?
5.3.3??制造部应根据安排的生产时间,提前采用评审法进行自我检查,生产过程的生产条件是否已完全具备,填写《作业准备验证记录表》。
5.3.4??进行生产作业准备验证时,生产车间操作人员按照《生产控制计划》工艺参数要求,调试设备和工装,并开始试产首件产品。
5.3.5 操作人员按照《生产控制计划》和《作业指导书》要求自检,将认为合格的产品作为首件产品报质量部检验员检验。
5.3.6 检验员将本次生产的首件产品与上班生产的末件产品在主要尺寸、外观质量和其它需要测量的项目上进行比较,对产品进行逐项检验,并填写《首件检验记录》。
当确认不合格后操作员应检查设备、工装模具的情况,并重新生产首件,再重复上述过程,不合格品按《不合格品控制程序》执行。
?
5.3.7??经检验合格的首件应放在指定位置,待本班生产任务完成后,操作人员应将认为合格的末件产品报质量部检验员检验。
5.3.7 检验员将本次生产的末件产品与当班生产的首件产品在主要尺寸、外观质量和其它需要测量的项目上进行比较,对产品进行逐项检验,并填写《末件检验记录》。
5.3.8 末件检验合格,则可以放行该批产品。
如不合格,应对该批产品按不合格品控制程序进行标识。
隔离,并按追溯要求进行挑选。
5.3.8 首件随产品流入下道工序。
末件产品应放在指定位置,作为下一班验证的依据。
5.3.9 对于量产产品停工后的验证,除按上述5.3.1~5.3.7进行评审检查和首件检验外,还需试生产小批量,进行过程能力分析,确定过程处于受控状态且能力充分时(Cpk≥1.33),方可进行正常量产。
5.4??作业准备验证和停工后验证的记录应由质量部保存,并按《记录控制程序》的保存要求执行。
5.5? 当产品停止生产一年以上重新生产,当顾客有要求时,必须重新提交PPAP,得到顾客认可后方可重新正式生产。
5.6 当材料发生变化或需用其他材料代用时,应执行《APQP产品先期质量策划控制程序》中的设计更改流程,并重新通过试生产确认,重新提交PPAP,得到顾客批准后方可正式生产。
?
6 引用文件
●不合格品控制程序
●纠正措施控制程序
●APQP产品先期质量策划控制程序
●工程变更控制程序
7 记录表单
发行对象:
生产技术副总经理、技术部、质量部、制造部、销售部、采购部、行政人事部、财务部编制审核批准
日期日期日期
作业准备验证记录表
编号:
过程所有者:制造部/车间主任/班组长:作业员:检验员:验证日期:年月日。