转炉炉型设计计算
《t转炉炉型设计》doc版

《t转炉炉型设计》doc版《t转炉炉型设计》doc版课题名称140T 转炉炉型设计专业班级冶金0504 班姓名秦胜利系部冶金学院指导教师王鸿雁时间2007 年12 月9 日~ 12 月15 日序言现在钢铁联合企业包括炼铁,炼钢,轧钢三大主要生产厂。
炼钢厂则起着承上启下的作用,它既是高炉所生产铁水的用户,又是供给轧钢厂坯料的基地,炼钢车间的成产正常与否,对整个钢铁联合企业有着重大影响。
目前,氧气转炉炼钢设备的大型化,生产的连续化和高速化,达到了很高的生产率,这就需要足够的设备来共同完成,而这些设备的布置和车间内各种物料的运输流程必须合理,才能够使生产顺利进行。
转炉是炼钢车间的核心设备,设计一座炉型合理满足工艺需求的转炉是保证车间正常生产的前提,而炉型设计又是整个转炉设计的关键。
140T 转炉炉型设计 1 炉型设计步骤(1) 列出原始条件:公称容量,铁水条件。
废钢比,氧枪类型以及吹氧时间等。
(2) 根据条件选炉型(3) 确定炉容比(4) 计算熔池直径,熔池深度等尺寸(5) 计算炉帽尺寸(6) 计算炉身尺寸(7) 计算出钢口尺寸(8) 确定炉衬厚度(9) 确定炉壳厚度(10) 校核H/D (11) 绘制炉型图2 炉型设计与计算2.1 本次设计任务:设计140T 转炉炉型(1) 原始条件炉子平均出钢量为140t , 钢水收得率为92% ,最大废钢比取20% ,采用废钢矿石法冷却。
铁水采用低磷生铁[W(si)≤0.85%,W(F)≤0.2% W(5)≤0.05%] ; 氧枪采用三孔拉瓦尔型喷头,设计氧压为1.0mpa (2) 炉型选择根据原始条件采用筒球形炉型作为此次设计的转炉炉型(3) 炉容比,取V/T=0.989 2.2 炉型尺寸的计算(1) 熔池尺寸的计算①熔池直径计算:计算公式: D=k (G/t) 1/2 熔池直径式中: K—常数,取1.57 ;G—金属装入量,t ;T—吹氧时间,min 。
a: 确定初期金属装入量为G G=2T/2+B*1/2 式中:T——平均出钢量为,140t ;B——常数,取15% ;η金——金属收得率为92% ;G=2×140/2+15%*1/92%=141.557(t) V金=G/ρ金=141.557/6.8=20.817(m3) B: 确定吹氧时间:根据生产实践,吨钢耗氧量一般低磷铁水约为50~57 则供氧强度=吨钢耗氧量/吹氧时间=57/14=14[m3/(t*min)] D=1.57(141.557/14)1/2=4.99m 熔炉深度计算筒球型熔池深度的计算公式为:h熔=V金+0.046D3/0.79D2=20.817+0.046*4.993/0.79*4.992=1.35m 熔池其他尺寸的确定球冠的弓形高度: h1=0.15D=0.15×4.99=4.54m 球冠的曲率半径:R=0.91×D=0.15×4.99=4.54m 2.3 炉帽尺寸的确定(1) 炉口直径d0:d0=0.48D=0.48×4.99=2.4m (2) 炉帽倾角θ 取64°;(3) 炉帽高度(H 帽) 式中:Ho——炉口高度,取0.4m 在炉口设置水箱式水冷炉口2.4 炉身尺寸确定(1) 炉膛直径( 无加厚段) (2) 根据选定的炉容比为0.989 ,可求出炉子总容积为炉身高度: 则炉型内高: 2.5 出钢口尺寸计算(1) 出钢口直径: (2) 出钢口衬砖外径dr=63+1.7571/2=(6+1.75*140)1/2=17.5CM=0.175m (3) 出钢口长度dT =6dT=6*17.5=105cm=1.05m (4) 出钢口倾角β取18°LT=TdT=7×17.5=122.5cm=1.225m 符合高宽比的推荐值,因此认为所涉及的炉子尺寸是基本合适的。
140T_转炉炉型设计

1 40T 转炉炉型设计序言现在钢铁联合企业包括炼铁,炼钢,轧钢三大主要生产厂。
炼钢厂那么起着承上启下的作用,它既是高炉所生产铁水的用户,又是供应轧钢厂坯料的基地,炼钢车间的成产正常与否,对整个钢铁联合企业有着重大影响。
目前,氧气转炉炼钢设备的大型化,生产的连续化和高速化,到达了很高的生产率,这就需要足够的设备来共同完成,而这些设备的布置和车间各种物料的运输流程必须合理,才能够使生产顺利进展。
转炉是炼钢车间的核心设备,设计一座炉型合理满足工艺需求的转炉是保证车间正常生产的前提,而炉型设计又是整个转炉设计的关键。
140T 转炉炉型设计1 炉型设计步骤(1) 列出原始条件:公称容量,铁水条件。
废钢比,氧枪类型以及吹氧时间等。
(2) 根据条件选炉型(3) 确定炉容比(4) 计算熔池直径,熔池深度等尺寸(5) 计算炉帽尺寸(6) 计算炉身尺寸(7) 计算出钢口尺寸(8) 确定炉衬厚度(9) 确定炉壳厚度(10) 校核H/D(11) 绘制炉型图2 炉型设计与计算2.1 本次设计任务:设计140T 转炉炉型(1) 原始条件炉子平均出钢量为140t , 钢水收得率为92% ,最大废钢比取20% ,采用废钢矿石法冷却。
铁水采用低磷生铁[W(si)≤0.85%,W(F)≤0.2% W(5)≤0.05%] ; 氧枪采用三孔拉瓦尔型喷头,设计氧压为1.0mpa(2) 炉型选择根据原始条件采用筒球形炉型作为此次设计的转炉炉型(3) 炉容比,取V/T=0.9892.2 炉型尺寸的计算(1) 熔池尺寸的计算①熔池直径计算:计算公式: D=k (G/t) 1/2熔池直径式中:K—常数,取1.57 ;G—金属装入量,t ;T—吹氧时间,min 。
a: 确定初期金属装入量为GG=2T/2+B*1/2式中:T——平均出钢量为,140t ;B——常数,取15% ;η金——金属收得率为92% ;G=2×140/2+15%*1/92%=141.557(t)V金=G/ρ金=141.557/6.8=20.817(m3)B: 确定吹氧时间:根据生产实践,吨钢耗氧量一般低磷铁水约为50~57 那么供氧强度=吨钢耗氧量/吹氧时间=57/14=14[m3/(t*min)] D=1.57(141.557/14)1/2=4.99m熔炉深度计算筒球型熔池深度的计算公式为:h熔=V金+0.046D3/0.79D2=20.817+0.046*4.993/0.79*4.992=1.35m 熔池其他尺寸确实定球冠的弓形高度:h1=0.15D=0.15×4.99=4.54m球冠的曲率半径:R=0.91×D=0.15×4.99=4.54m2.3 炉帽尺寸确实定(1) 炉口直径d0:d0=0.48D=0.48×4.99=2.4m(2) 炉帽倾角θ 取64° ;(3) 炉帽高度(H 帽)式中:H o——炉口高度,取0.4m在炉口设置水箱式水冷炉口2.4 炉身尺寸确定(1) 炉膛直径( 无加厚段)(2) 根据选定的炉容比为0.989 ,可求出炉子总容积为炉身高度:那么炉型高:2.5 出钢口尺寸计算(1) 出钢口直径:(2) 出钢口衬砖外径d r=63+1.7571/2=(6+1.75*140)1/2=17.5CM=0.175m(3) 出钢口长度d T' =6d T=6*17.5=105cm=1.05m(4) 出钢口倾角β取18°L T=T dT=7×17.5=122.5cm=1.225m符合高宽比的推荐值,因此认为所涉及的炉子尺寸是根本适宜的。
钢铁冶金学-毕业设计

东北大学《钢冶金学》毕业设计炉型:80t顶吹氧气转炉学院名称:材料与冶金学院专业:冶金工程年级:学生姓名:学号:指导老师:完成时间:前言氧气转炉是炼钢法是当前国内外主要的炼钢方法。
氧气转炉炼钢自20世纪40年代初问世以来,在世界各国得到了广泛的应用,技术不断地进步,设备不断地改进,工艺不断地完善。
在短短的五十几年里,从顶吹发展到底吹、侧吹发展到复合吹炼。
氧气转炉炼钢的飞速发展,使炼钢生产进入了一个崭新的阶段,钢的产量不断增加,成本不断的下降。
从日前来看,转炉炼钢可以说是最佳的炼钢方法。
本设计是根据学校教学环节安排的一个实践学习环节过程,以社会和经济发展需要为出发点,以职业需求为直接依据。
是冶金技术专业学生在学习专业课程之后进行的一个重要的独立性实践过程,培养学生综合应用所学的炼钢理论知识去分析和解决实际问题的能力。
这也是我们步入社会和工作岗位之前的一次实训,通过这次课程设计的学习,可以帮助我们巩固、深化和拓展炼钢学的知识面,更好的将理论知识与生产实际相合起来,掌握一般设备工艺的基本思路和方法。
为以后踏入工作岗位奠定了一个良好的基础,为实际工程设计奠定基础,使我们能够很快、很好的融入工作岗位和社会。
在本次的炉型设计中,参阅了大量有关转炉炼钢工艺、炼钢生产设备等文献,得到首钢集团提供的资料与经验数据。
还得到了老师们的指导和大力支持,广大同学的帮助。
在此一并表示衷心的感谢。
由于个人所学的知识和水平有限,加上没有实际的生产实践经验,存在缺点和错误之处,敬请老师批评和指正。
目录1设计目的---------------------------------------------------------------- - 1 -2设计内容---------------------------------------------------------------- - 1 -3 设计步骤及说明---------------------------------------------------------- - 1 -3.1物料平衡和热平衡计算 ------------------------------------------------- -1-3.1.1 原始数据的选取-------------------------------------------------- - 1 -3.1.2物料平衡计算--------------------------------------------------- - 3 -3.1.3热平衡计算----------------------------------------------------- - 9 -3.2顶吹转炉炉型的设计及计算------------------------------------------- -13-3.2.1转炉的公称容量及其表示方法 ------------------------------------ - 13 -3.2.2转炉炉型的选择 ------------------------------------------------ - 13 -3.2.3转炉炉型主要参数的确定 ---------------------------------------- - 13 -3.2.4转炉炉型主要尺寸的确定 ---------------------------------------- - 14 -3.2.5 炉衬的组成、材质选择及厚度的确定------------------------------- - 17 -3.2.6炉壳厚度和转角半径的确定 -------------------------------------- - 17 -480T顶吹氧气转炉炉型的绘制--------------------------------------------- - 18 -参考文献------------------------------------------------------------------- - 18 -1设计目的本课程是冶金技术专业学生学习专业课程之后进行的一个重要的独立性实践教学环节。
出钢量为60t转炉设计

转炉设计冶金工程课程设计任务书1 设计题目:转炉设计2已知条件:炉子平均出钢量为60t,钢水收得率取94%,最大废钢比取18%,采用废钢矿石法冷却:铁水采用P08低磷生铁[ω(Si)≦0.85%]ω(P)≦0.2%ω(S)≦0.05%],氧枪采用四孔拉瓦尔喷头,设计氧压为1.0MPa。
3设计内容及要求:(1)确定炉型和炉容比(2)计算熔池尺寸、炉帽尺寸、炉身尺寸、出钢口尺寸、炉衬厚度及炉壳厚度(3)绘制转炉炉型图(4)其它要求:①在课程设计期间要努力工作,勤于思考,仔细检索文献和分析设计过程的问题。
②设计说明书必须认真编写,字迹清楚、图表规范、符合制图要求。
3 设计工作量:设计说明书1份;转炉炉型图1份;参考文献列表1份1.1转炉炉型设计1.1.1转炉炉型设计概述(1)公称容量及其表示方法公称容量(T),对转炉容量大小的称谓。
即平时所说的转炉的吨位。
(2)炉型的定义转炉炉型是指转炉炉膛的几何形状,亦即指由耐火材料切成的炉衬内形。
炉型设计内容包括:炉型种类的选择;炉型主要参数的确定;炉型尺寸设计计算;炉衬和炉壳厚度的确定;顶底复吹转炉设计。
1.1.2炉型种类及其选择(1)炉型种类根据熔池(容纳金属液的那部分容积)的形状不同来区分,炉帽、炉身部位都相同,大体上归纳为以下三种炉型:筒球形、锥球形和截锥形。
①筒球形炉型:该炉型的熔池由一个圆筒体和一个球冠体两部分组成,炉帽为截锥体,炉身为圆筒形。
其特点是形状简单,砌砖简便,炉壳容易制造。
在相同的熔池直径D和熔池深度h的情况下,与其他两种炉型相比,这种炉型熔池的容积大,金属装入量大,其形状接近于金属液的循环运动轨迹,适用于大型转炉。
②锥球形炉型(国外又叫橄榄形):该炉型的熔池由一个倒置截锥体和一个球冠体两部分组成,炉帽和炉身与圆筒形形炉相同。
其特点是,与同容量的其他炉膛相比,在相同熔池深度h下,其反应面积大,有利于钢、渣之间的反应,适用于吹炼高磷铁水。
③截锥体炉型:该炉型的熔池有一个倒置的截锥体组成。
140t氧气顶吹转炉炉型设计
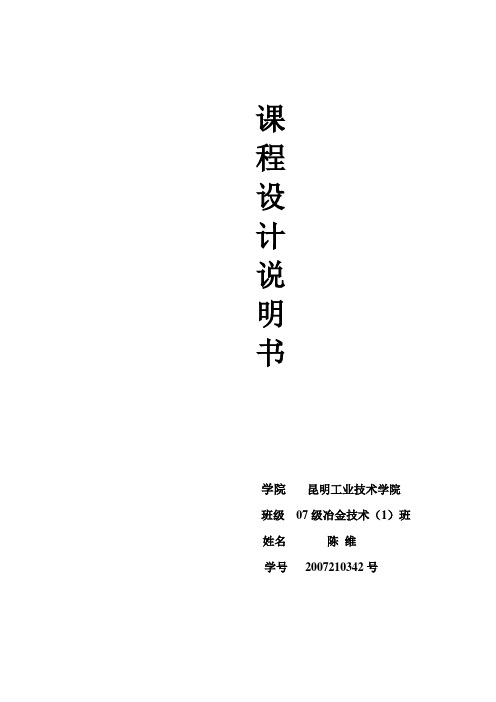
d 零/D=2.424/5.050=0.48
设计部门推存 d 零/D=0.43-0.53,大型转炉取下限,小型转 炉取上限,此设计满足此要求,因此可以根据数据作图。
转 炉设 计 的 主要 数 据尺寸
参数 0.91 炉容比(m3/t) 容池直径/㎜ 容池深度/㎜ 容池体积/m 炉帽倾角/ 炉帽高度/㎜ 炉帽容积/m
本设计选炉身工作层 700 ㎜,永久层 115 ㎜,填充层 100 ㎜,总后:700+115+100=915(㎜)
(2) 炉壳 的内径 D
D 壳内=5.050+0.915=6880(㎜)
D 壳 内 =6880 (㎜)
5
壳内
(3) 炉底 砖 衬总 厚 度
炉帽和炉底的工作层都选 600 ㎜, 炉帽永久层为 150 ㎜炉底 永 久 层 用 标 准 镁 砖 立 砌 一 层 250 ㎜ , 黏 土 砖 平 砌 三 层 67*3=210(㎜),则炉底砖衬总厚度为:600+250+210=1060(㎜) 黏土砖是应用广泛的耐火砖, 它有良好的物理机械性能, 教强的 机械强度,成本较低。
⑵ 炉帽 倾 角
根据炉帽倾角推荐值为 60°~68°,大型转炉取下限,小型 转炉取上限,本设计取 θ=63°
⑶ 炉帽 高 度
炉帽高度:H 帽=H 锥+H 口 式中 H 锥可用公式计算得到:H 锥=
1 (D-d0)tanθ 2 1 = (5.050-2.424)tan63° 2
=2.577(m) 为了保证炉口正常形状, 不会因为炉口耐火材料的熔损而使 炉口扩大,在炉口设置高度为 300~400 ㎜的直线段,本设计取 350 ㎜,因此:H 帽=H 锥+H 口=2.577+0.35=2.927(㎜) 在炉口处设置水箱式水冷炉口
第二章 转炉炉型设计
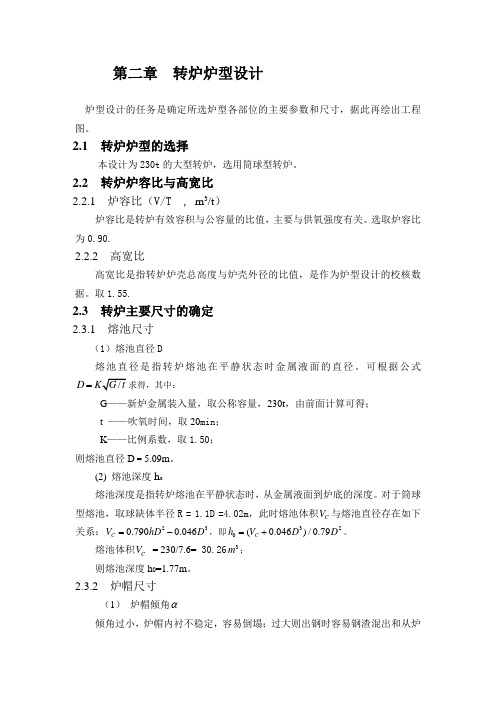
第二章 转炉炉型设计炉型设计的任务是确定所选炉型各部位的主要参数和尺寸,据此再绘出工程图。
2.1 转炉炉型的选择本设计为230t 的大型转炉,选用筒球型转炉。
2.2 转炉炉容比与高宽比2.2.1 炉容比(V/T , m 3/t )炉容比是转炉有效容积与公容量的比值,主要与供氧强度有关。
选取炉容比为0.90.2.2.2 高宽比高宽比是指转炉炉壳总高度与炉壳外径的比值,是作为炉型设计的校核数据。
取1.55.2.3 转炉主要尺寸的确定 2.3.1 熔池尺寸(1)熔池直径D熔池直径是指转炉熔池在平静状态时金属液面的直径。
可根据公式/D K G t =求得,其中:G ——新炉金属装入量,取公称容量,230t ,由前面计算可得; t ——吹氧时间,取20min ; K ——比例系数,取1.50; 则熔池直径D = 5.09m 。
(2) 熔池深度h 0熔池深度是指转炉熔池在平静状态时,从金属液面到炉底的深度。
对于筒球型熔池,取球缺体半径R = 1.1D =4.02m ,此时熔池体积C V 与熔池直径存在如下关系:230.7900.046C V hD D =-,即320(0.046)/0.79C h V D D =+。
熔池体积C V = 230/7.6= 30.263m ; 则熔池深度h 0=1.77m 。
2.3.2 炉帽尺寸(1) 炉帽倾角α倾角过小,炉帽内衬不稳定,容易倒塌;过大则出钢时容易钢渣混出和从炉口大量流渣。
在本设计中取α = 62°。
(2) 炉口直径d 0本设计中取取炉口直径为熔池直径的45%,即d 0 = 5.09×45% =2.29m(3) 炉帽高度H帽取炉口上部直线段高度H口 =350mm ,则炉帽高度为:H 帽 =1/200()tan D d H α-+= 1/2(5.09—2.29)tan62°+ 0.35 = 2.98m 2.3.3 炉身尺寸(1) 炉身直径转炉炉帽以下,熔池面以上的圆柱体部分称为炉身。
120吨转炉倾动结构设计计算,毕业论文

摘要摘要在转炉设备中的倾动机械是实现转炉炼钢生产的关键设备之一,炉体的工作对象是高温的液体金属,在兑铁水、出钢等项操作时,要求炉体能平稳地倾动和准确的停位。
为获得如此低的转速,需要很大的减速比。
转炉炉体自重很大,再加装料重量等,整个被倾转部分的重员要达上百吨或上千吨。
目前己投产的最大炉容量为350吨转炉,其总重达到1450多吨。
要使这样大重员的转炉倾转就必须在转炉耳轴上施加几百,以至几千吨力·米的倾动力矩。
转炉炼一炉钢的时间,通常只有四十分钟左右。
转炉领动机械的工作属于“启动工作制”。
机构巾除承受基本静载荷作用外,还要承受由于启动、制动等引起的动载荷。
这种动载荷在炉口刮渣操作时,其数值甚至达到静载荷的两倍以上。
启、制动额繁,承受较大的动裁荷。
转炉倾动机械随着氧气转炉炼钢生产的普及和发展也在不断的发展和完善,出现了各种型式的倾功机械。
转炉倾动装置是转炉炼钢最主要的机械设备。
一种新型多点啮合全悬挂柔性传动装置,其一次减速机采用行星差动均载机构,使设备运转更加平稳;一、二次减速机之间采取花键套装悬挂式简支结构,并将其应用于转炉倾动装置,可解决传统型全悬挂转炉倾动装置因一、二次减速机之间的静不定联接结构所带来的机构不稳定性问题,从而提高了转炉设备的运行可靠性和检修维护性。
关键字转炉,炼钢机构,倾动机械,倾动装置、ABSTRACTABSTRACTIn the converter device tilting converter steelmaking machinery is the key to achieving one of the devices, the work of the furnace temperature of the liquid metal object is in against the hot metal, a steel other items of operation, the required tilting furnace can be smooth and accurate stop bit. To obtain such a low speed,; requires a lot of reduction ratio. Weight converter furnace, with the massive weight loading, by tilting the entire staff to be part of the weight or thousands of tons of hundreds of tons.Currently has the largest production capacity of 350 tons of converter furnace, the total weight reached more than 1450 tons. Members of such a large weight to make the converter tilting axis to be applied in Converter hundreds of ears, as well as thousands of tons of force Moment m dump. Converter steel smelting pot of the time, usually only four minutes later.Converter dynamic mechanical work leading a "start-up system."In addition to the basic static towel body under load, but also take the start, braking and other dynamic load caused.This dynamic load in the mouth blowing slag operation, its value even up to more than twice the static load.Kai, the amount of fan brake, move the CD under large load.With the converter tilting of oxygen converter steel production machinery popularity and development are constantly develop and improve, there has been dumping of various types of power machinery.Converter tilting device is the main steelmaking machinery and equipment.A new multi-point full suspension of flexible engagement gear, the first planetary gear differential with uniform load, making the equipment run more smoothly; the first and second spline gear set to fly between the simply supported structure, and Tilting converter is applied, can solve traditional full suspension converter tilting device for the first and second gear connection between the structure statically indeterminate problem of instability caused by institutions to improve the operation of converter equipment reliability and repair maintenance.Keywords converter, steel body, tilting machine, tilting devices目录摘要 (I)ABSTRACT ...................................................................................................................... I I1 绪论 (1)2转炉计算 (2)2.1炉型计算 (2)2.1.1炉型的类别 (2)2.1.2炉型尺寸的计算 (2)2.1.3空炉重心计算 (5)2.2转炉的耳轴最佳位置确定 (7)2.2.1计算摩擦力矩 (7)2.2.2预设耳轴的位置 (8)2.2.3计算耳轴的最佳位置 (8)2.3利用黄金分割法对倾动力矩最优化设计 (10)2.3.1黄金分割法的含义 (10)2.3.2黄金分割法的应用 (11)2.3.3计算转炉最优化液体重心 (11)2.3.4计算空炉力矩 (16)2.3.4计算倾动力矩 (18)3设计转炉倾动机构 (20)3.1转炉倾动机构工作方案 (20)3.1.2 倾动机构设计计算 (21)3.1.2配齿计算 (22)3.1.3 初步计算齿轮的主要参数 (24)3.2 啮合参数计算 (26)3.2.1中心距计算 (26)3.2.2计算齿轮的宽度 (27)3.2.3计算变位系数 (27)3.3几何尺寸的计算 (27)3.3.1齿轮参数 (27)3.3.2对行星架的尺寸设计计算 (30)3.4装配条件的验算 (32)3.4.1邻接条件 (32)3.4.2 同心条件 (32)3.4.3 安装条件 (32)3.4.4箱体及前后机盖的设计 (33)4强度计算 (34)4.1强度校核 (34)4.1.1齿轮的参数选用 (34)4.1.2高速级外啮合齿轮副中弯曲强度的校核 (36)4.1.2中速级外啮合齿轮副中接触强度的校核 (38)4.1.3底速级外啮合齿轮副中弯曲强度的校核 (42)4.2基本构件转矩的计算 (44)4.3 密封和润滑 (45)6总结 (46)参考文献 (47)致谢 (48)1 绪论转炉炼钢工艺要求往一个冶炼周期内耍完成小钢、倒边、兑铁水、加废钢和取样、测温以及吹炼等操作,需要要倾动转炉多次,因此电动机启、制动频繁。
150吨转炉设计

转炉炉型设计转炉是转炉炼钢车间的核心设备。
转炉炉型及其主要参数对转炉炼钢的生产率、金属收得率、炉龄等经济指标都有直接的影响,其设计是否合理也关系到冶炼工艺能否顺利进行,车间主厂房高度和转炉配套的其他相关设备的选型。
2.1 炉型的选择本设计为150t的中型转炉,选用筒球型转炉。
2.2 炉容比与高宽比2.2.1 炉容比(V/T , m3/t)炉容比是转炉有效容积与公容量的比值,主要与供氧强度有关,本设计选取炉容比为0.932.2.2 高宽比高宽比是指转炉炉壳总高度与炉壳外径的比值,是作为炉型设计的校核数据。
在1.25-1.45之间。
2.3 转炉主要尺寸的确定2.3.1 熔池尺寸(1)熔池直径D熔池直径是指转炉熔池在平静状态时金属液面的直径。
可根据公式D?KG ——新炉金属装入量,t;(取公称容量) t ——吹氧时间,min,取16min K——比例系数,取1.70则熔池直径D?K1.7×√(150÷16)=5.21m熔池深度是指转炉熔池在平静状态时,从金属液面到炉底的深度。
对于筒球型熔池,取球缺体半径R = 1.1D = 5726mm,此时熔池体积VC与熔池直径存在如下关系:VC?0.790hD?0.046D,即h0?23VC?0.046D0.79D23。
熔池体积VC = 装入量/比重 =150/5.0 = 30m3 则熔池深度h0?VC?0.046D0.79D23=(30+0.046×5.21)/(0.790×5.21)=1.70m322.3.2 炉帽尺寸(1)炉帽倾角?倾角过小,炉帽内衬不稳定,容易倒塌;过大则出钢时容易钢渣混出和从炉口大量流渣。
在本设计中取? = 60°.(2)炉口直径d0本设计中取炉口直径为熔池直径的48%,即d0 = 5.21×48% = 2.5m =2500mm (3) 炉帽高度H帽口 = 350 mm,则炉帽高度为:取炉口上部直线段高度HH帽 = ?(D?d)tan??H= 1/2(5.21 — 2.5)tan60°+ 0.35 = 2.70m 0022.3.3 炉身尺寸(1)炉身直径转炉炉帽以下,熔池面以上的圆柱体部分称为炉身。
转炉炉型设计物料平衡热平衡计算

(Fe2O3)重=13.139×5%=0.657[㎏];
其中Fe氧化量:0.657× =0.460[㎏](转入表7)
*CaO= CaO石灰中— CaOS消耗=5.565-0.109=5.456[kg](表12及附注)
二、矿石及烟尘中的铁量和氧量的计算
1、加入1.0[㎏矿石/100㎏]带入的铁量和氧量为:
0.01
转入表7
说明:
[Si]——碱性渣操作时终点[Si]量为痕迹;
[P]——单渣法去磷约90%(±5%);
[Mn]——终点余锰量约30~40%,这里实测为30%;
[S]——转炉去硫约30~50%;
[C]——终点碳与钢种及磷量有关,要求出钢后加铁合金增碳的量能满足钢的规格中限,即:
[C]终点=[C]中限—[C]增碳;
表4各材料的比热容
项目
固态平均比热/KJ·kg-1·k-1
溶化潜/KJ·kg-1
液(气)态平均比热容/ KJ·kg-1·k-1
生铁
0.744
217.468
0.8368
钢
0.699
217.69
0.8368
炉渣
209.20
1.247
炉气
1.136
烟尘
1.000
209.20
矿石
1.046
209.20
5. 各反应热效应(认为25℃与炼铁温度下两者数值近似)
还原[O]:0.0625× =0.031[㎏]
消耗(CaO)量:0.0625× =0.109[㎏]
6.终渣Σ(FeO)的确定
取R=3.5及Σ(FeO)=15%时可满足终点钢水中[P]=0.013%的要求
这里取Σ(FeO)= (%FeO) +0.9(%FeO) =15%
200吨转炉炉型设计计算

200吨转炉炉型设计计算第⼆部分200吨转炉炉型设计计算(⼀)转炉炉型及主要参数⼀、转炉三种炉型介绍转炉炉型应能适应炉内钢液、溶渣和⾼温⽓的循环运动规律,达到反应快、喷溅少和炉龄⾼等⽬的。
内型应与残余炉衬的轮廓接近,以利减少炉衬的局部侵蚀和降低耐⽕材料的消耗,此外还要容易砌筑。
⽬前,氧⽓顶吹转炉⾦属熔池形状可分为三种炉型:1.筒球形炉型这种炉⼦形状简单、砌砖⽅便、炉壳容易制造。
球形底可使散热⾯积⼩,倒渣时炉底形成拱顶⽽强度相对要⼤。
球底熔池的形状接近⾦属液的循环轨迹。
.常⽤于≧50吨的炉⼦。
2.锥球形炉型这种炉⼦的熔池形状更符合钢流循环的要求,且与筒球形相⽐,当熔池深度相同时,熔池直径与反应⽽积均可稍⼤⽽有利于去磷反应的进⾏(见式2-6和式2-6)。
常⽤于20~80吨的炉⼦。
3.截锥形炉型熔池循环有死⾓,故适⽤于≦30吨的炉⼦。
这种倒圆台的炉底⽐球形炉底易于砌筑.⼆.炉⼦各部分主要尺⼨参数的确定和计算转沪的主要尺⼨如[4]254图23⼀1所⽰.下⾯分五个部分进⾏讨论(I)熔池部分1.熔池直径的计算式中:G——新炉⾦属料装⼊量,T(由原始条件给出)t——吹氧时间,minK——系数>30吨炉⼦K=1.85~2.1系数<30吨炉⼦K=2.0~2.3t=33min′′前期出钢量[T]加废钢后耗氧量[Nm/T]供养强度[Nm/T]G[T]由表1-21可求“加废钢后每吨钢⽔耗氧量”=氧[kg]钢⽔[kg]×1000[Tkg]×332[kg]22.4[Nm]供氧强度可参表2—1,计算后,供养时间应符合表2—2的范围。
32.⾦属熔池体积和熔池深度的计算①当取铁⽔密度ρ=6.8[T/m 3]时则⾦属熔池体积V ⾦属=G[T]×0.147[T/m 3]②锥球形熔池深度h=320.0363D 0.7D +⾦属V (m)③筒球形熔池深度h=320.046D 0.79D +⾦属V (m)由:⽐较式2—6与式2—7可知,当深度两者相同时,锥球形熔池直径稍⼤⽽可扩⼤熔池的渣钢反应界⾯有利于去磷的反应。
150t顶底复吹转炉炉型设计

课程设计说明书题目名称: 150t顶底复吹转炉炉型设计学院机械工程系(部)课程设计任务书2013-2014 学年第2学期2014 年6月27日教研室主任(签名)系(部)主任(签名)目录1.摘要 (1)2 转炉物料平衡与热平衡计算 (1)2.1 原始数据的选取 (2)2.1.1 原材料成分 (2)铁水、废钢成分见表1.1 (2)2.1.2 假设条件 (3)2.1.3 冶炼钢种及规格成分 (3)2.2.1 渣量及其成分计算 (3)2.2.3 氧气消耗量计算 (7)2.2.4 炉气量及成分计算 (8)2.2.5 未加废钢和合金时的物料平衡表 (8)2.3.1 热收入 (9)2.3.2 热支出 (9)2.3.3 热平衡表 (11)2.4 吨钢物料平衡 (11)3 转炉炉型设计 (12)3.1 转炉炉型的选择 (12)3.2 转炉炉容比与高宽比 (12)3.2.1 炉容比(V/T , m3/t) (12)3.2.2高宽比 (13)3.3 转炉主要尺寸的确定 (13)3.3.1熔池尺寸 (13)3.3.2 炉帽尺寸 (13)3.3.4 出钢口尺寸 (14)3.3.5 炉衬 (15)3.3.6 炉壳 (15)结束语 (17)参考文献 (18)1.摘要转炉炼钢(converter steelmaking)是以铁水、废钢、铁合金为主要原料,不借助外加能源,靠铁液本身的物理热和铁液组分间化学反应产生热量而在转炉中完成炼钢过程。
转炉按耐火材料分为酸性和碱性,按气体吹入炉内的部位有顶吹、底吹和侧吹;按气体种类为分空气转炉和氧气转炉。
碱性氧气顶吹和顶底复吹转炉由于其生产速度快、产量大,单炉产量高、成本低、投资少,为目前使用最普遍的炼钢设备。
转炉主要用于生产碳钢、合金钢及铜和镍的冶炼。
2003年我国转炉钢产量已接近1.9亿t,占我国钢产量的85.2%,约占世界转炉钢的25%。
50~300t转炉由2001年的75座增至2003年的134座,工艺技术进一步优化。
转炉炉型设计计算
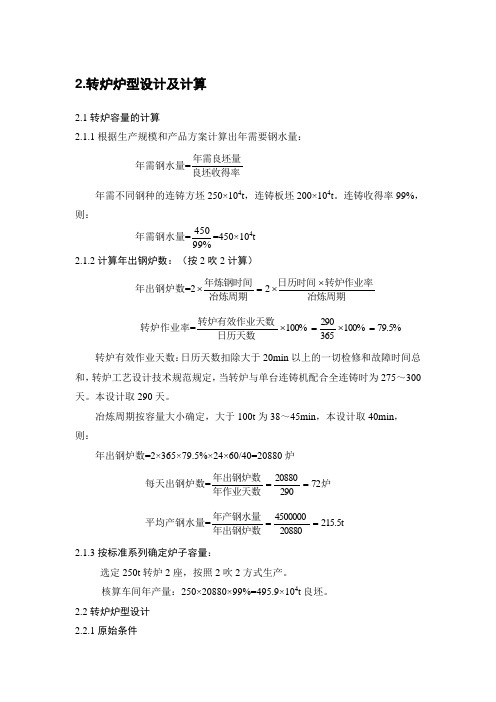
2.转炉炉型设计及计算2.1转炉容量的计算2.1.1根据生产规模和产品方案计算出年需要钢水量:年需钢水量=良坯收得率年需良坯量年需不同钢种的连铸方坯250×104t ,连铸板坯200×104t 。
连铸收得率99%,则:年需钢水量=99%450=450×104t 2.1.2计算年出钢炉数:(按2吹2计算) 年出钢炉数=2冶炼周期转炉作业率日历时间冶炼周期年炼钢时间⨯⨯=⨯2转炉作业率=79.5%100%365290100%=⨯=⨯日历天数转炉有效作业天数转炉有效作业天数:日历天数扣除大于20min 以上的一切检修和故障时间总和,转炉工艺设计技术规范规定,当转炉与单台连铸机配合全连铸时为275~300天。
本设计取290天。
冶炼周期按容量大小确定,大于100t 为38~45min ,本设计取40min , 则:年出钢炉数=2×365×79.5%×24×60/40=20880炉每天出钢炉数=炉年作业天数年出钢炉数7229020880==平均产钢水量=215.5t 208804500000==年出钢炉数年产钢水量2.1.3按标准系列确定炉子容量:选定250t 转炉2座,按照2吹2方式生产。
核算车间年产量:250×20880×99%=495.9×104t 良坯。
2.2转炉炉型设计 2.2.1原始条件炉子平均出钢量为250t ,铁水密度6.8g/cm 3,铁水收得率为92%。
2.2.2炉型选择顶底复吹转炉的炉型基本上与顶吹和底吹转炉相似;它介于顶吹转炉和底吹转炉之间。
为了满足顶底复吹的要求炉型趋于矮胖型,由于在炉底上设置底吹喷嘴,炉底为平底,所以根据原始数据,为了便于设置底部供气构件,选择截锥形炉型。
2.2.3炉容比炉容比指转炉有效容积V t 与公称容量T 之比值V t /T(m 3/t)。
V t 系炉帽、炉身和熔池三个内腔容积之和。
转炉设计

1转炉设计1.1炉型设计1. 原始条件炉子平均出钢量为100吨,钢水收得率取90.36%,最大废钢比取10%,采用废钢矿石法冷却。
铁水采用P08属于低磷生铁;氧枪采用三孔拉瓦尔型喷头.2. 炉型选择:根据原始条件采用锥球形炉型。
3. 炉容比:取V/T=1.004. 熔池尺寸的计算 熔池直径:G=t B T 95.102936.01%1521002122=⨯+⨯=⋅+η (取B=15%)314.158.695.102m G V ===ρ 确定吹氧时间和吨钢耗氧量:本设计采用低磷铁水,取吨钢耗氧量为56.8)(/3钢t m 。
并取吹氧时间为12min ,则 供氧强度min)]/([733.4128.563⋅==t m 取K =1.8则 )(27.51295.1028.1m D == 锥球型熔池深度的计算公式为)(05.127.57.027.50363.014.157.00363.02323m D D V h =⨯⨯+=+=确定D =5.27m, h =1.05m熔池其他尺寸确定 球冠的弓形:)(527.027.510.010.01m D h =⨯== )(717.427.5895.0895.01m D D =⨯==炉底球冠曲率半径:)(797.527.51.11.1m D R =⨯==5. 炉帽尺寸的确定炉口直径:()m D d 530.227.548.048.00=⨯==炉帽倾角:取065=θ 3) 炉帽高度帽H )(94.265tan )53.227.5(21tan 2100m d D H =-=-=θ 取mm H 400=口,则整个炉帽高度为: )(口锥帽m H H H 34.34.094.2=+=+= 由于我们采用水冷炉口炉帽部分容积为:口锥帽)(H d d Dd D H V 202002412ππ+++=)(56.384.053.24)53.253.227.527.5(94.2123222m =⨯⨯++⨯+⨯⨯=ππ6. 炉身尺寸确定1) 炉膛直径D D =膛=5.27m (无加厚段)2) 根据选定的炉容比为1.00,可求出炉子总容积为 )(容31000100.1m V =⨯= )(帽池总身346.438.5615.14100m V V V V =--=--= 3) 炉身高度 )(3.135.27446.4422m D V H =⨯=⨯=ππ身身4) 炉型内高m H H h H 52.813.234.305.1=++=++=身帽内7. 出钢口尺寸的确定1) 出钢口直径)(15.0)(15.5301075.16375.163m cm T d T =≈⨯+=+= 2) 出钢口衬砖外径)(0.915.066m d d T ST =⨯== 3) 出钢口长度)(05.115.077m d L T T =⨯== 4) 出钢口倾角β:取018=β8. 炉衬厚度确定炉身工作层选600mm,永久层115mm,填充层90mm,总厚度为600+115+90=805(mm )炉壳内径为 6.882805.05.27=⨯+=壳内D炉帽和炉底工作层均选600mm,炉帽永久层为150mm,炉底永久层用标准镁砖立砌,一层230mm,粘土砖平砌三层65×3=195(mm ),则炉底衬砖总厚度为600+230+195=1025(mm ),故炉壳内形高度为)(9.545025.18.52m H =+=壳内,工作层材质全部采用镁碳砖。
转炉设计 (2)

1 转炉炉型选型设计及相关参数计算1转炉炉型设计1.1.1 炉型选择氧气顶底复吹转炉是20世纪70年代中、后期,开始研究的一项新炼钢工艺。
其优越性在于炉子的高宽比略小于顶吹转炉却又大于底吹转炉,略呈矮胖型;炉底一般为平底,以便设置底部喷口。
综合以上特点选用转炉炉型为锥球型(适用于中小型转炉见图1-1)。
图1-1 常见转炉炉型(a)筒球型;(b)锥球型;(c)截锥型1.1.2 主要参数的确定本设计选用氧气顶吹转炉(公称容量50t)。
(1) 炉容比炉容比系指转炉有效容积与公称容量之比值。
转炉炉容比主要与供氧强度有关,与炉容量关系不大。
从目前实际情况来看,转炉炉容比一般取0.9~1.05m3/t。
本设计取炉容比为1.05m3/t。
(2) 高径比转炉高径比,通常取1.35~1.65。
小炉子取上限,大炉子取下限。
本设计取高径比:1.40。
(3) 熔池直径D 可按以下经验公式确定:tG KD = (1-1)式中 D ——熔池直径,m ;G ——新炉金属装入量,t ,可取公称容量; K ——系数,参见表1-1;t ——平均每炉钢纯吹氧时间,min ,参见表1-2。
表1-1 系数K 的推荐值注:括号内数系吹氧时间参考值。
设计中转炉的公称容量为50t ,取K 为1.85,t 取15min 。
可得:38.3155085.1==D m(4) 熔池深度h锥球型熔池倒锥度一般为12°~30°,当球缺体半径R=1.1D 时,球缺体高h1=0.09D 的设计较多。
熔池体积和熔池直径D 及熔池深度h 有如下的关系:23665.0033.0DD V h +=池 (1-2)由池V G 1ρ=可得:09.705.7501===ρGV 池(m 3)将池V 代入式(7-2)得:98.038.3665.038.3033.009.7665.0033.02323=⨯⨯+=+=DD V h 池(m)(5) 炉身高度身H转炉炉帽以下,熔池面以上的圆柱体部分称为炉身。
180t氧气炼钢转炉的设计

摘要自1952年第一座氧气顶吹转炉投产以来,氧气顶吹转炉的实践表现出很多的优点,使氧气顶吹转炉炼钢法逐渐的成了世界炼钢的主要方法。
随着社会的发展,各方面对钢材的需求也越来越多。
为了满足社会各方面对钢材的需求,改进炼钢的生产工艺和设备是必不可少的。
作为转炉炼钢的主要设备之一,转炉炉体的设计直接关系到炼钢的产量、质量、炉龄、成本和安全等。
本文以设计180t氧气顶吹转炉炉体为目标,合理的设计出能够安全顺行的转炉炉体。
对转炉炉体的设计主要包括炉型设计、炉衬设计和炉壳设计三方面,为了衔接炉体其它附属部件,也对转炉的托圈和耳轴作出相应的设计。
在炉型设计方面,主要包括炉型的选择、炉容比的确定和炉型主要尺寸的确定。
在炉衬设计方面,主要是对炉衬材质和炉衬厚度的设计,为了提高钢水的质量,增加炉衬的使用寿命,减少炉衬的砌筑成本,选择了新型的镁钙碳大砖作为炉衬材料。
在炉壳设计方面,主要是炉壳材质选择和炉壳钢板厚度的确定,为了增加生产的安全系数和炉龄,选择了综合性能更好的新型炉壳材料SM400ZL。
最后对所设计转炉炉体的高径比进行校核,高径比满足条件,可认为所设计的炉体尺寸是合适的,能够保证转炉的正常冶炼进行。
关键词转炉炉体,炉型,炉衬,炉壳ABSTRACTSince 1952 first BOF put into operation, the BOF practice showed a lot of advantages, the top-blown oxygen converter steelmaking method gradually became the world's steelmaking method. With the development of society, all steel demand is also increasing. In order to meet all sectors of society to face the demand for steel, improved steelmaking production processes and equipment is essential. As one of the main equipment,the BOF converter furnace design is directly related to the production of steel-making, quality, furnace, cost and safety. Design 180t oxygen top-blown converter furnace as the goal, that can ensure safety production facility was reasonable designed out. The design of the converter furnace includes the furnace profile design, lining design and the furnace shell, the convergence of the other subsidiary parts of the furnace, make the appropriate design of the converter trunnion ring and trunnion. The design of furnace includes the choice of furnace profile, determine the furnace volume ratio and furnace size. Lining design is aimed to choose the lining material and determine the lining thickness, in order to improve the quality of molten steel, increase the lining life and reduce the lining cost, the new magnesium calcium carbon brick was chosen as a lining material. For the design of the furnace shell, in order to increase the safety factor of production and furnace life, a new furnace shell material SM400ZL with better comprehensive performance was used. Last check the height to diameter ratio of designed converter furnace. The height to diameter ratio could meet the conditions, it could be concluded that the design of the furnace size is appropriate to ensure the normal smelting converter.Key words converter furnace, furnace profile, furnace linings, furnace shell目录摘要 (1)ABSTRACT................................................................... I I1 绪论 ....................................................错误!未定义书签。
转炉设计

转炉设计1.1转炉炉型设计1.1.1转炉炉型设计概述(1)公称容量及其表示方法公称容量(T),对转炉容量大小的称谓。
即平时所说的转炉的吨位。
(2)炉型的定义转炉炉型是指转炉炉膛的几何形状,亦即指由耐火材料切成的炉衬内形。
炉型设计内容包括:炉型种类的选择;炉型主要参数的确定;炉型尺寸设计计算;炉衬和炉壳厚度的确定;顶底复吹转炉设计。
1.1.2炉型种类及其选择(1)炉型种类根据熔池(容纳金属液的那部分容积)的形状不同来区分,炉帽、炉身部位都相同,大体上归纳为以下三种炉型:筒球形、锥球形和截锥形。
①筒球形炉型:该炉型的熔池由一个圆筒体和一个球冠体两部分组成,炉帽为截锥体,炉身为圆筒形。
其特点是形状简单,砌砖简便,炉壳容易制造。
在相同的熔池直径D和熔池深度h的情况下,与其他两种炉型相比,这种炉型熔池的容积大,金属装入量大,其形状接近于金属液的循环运动轨迹,适用于大型转炉。
②锥球形炉型(国外又叫橄榄形):该炉型的熔池由一个倒置截锥体和一个球冠体两部分组成,炉帽和炉身与圆筒形形炉相同。
其特点是,与同容量的其他炉膛相比,在相同熔池深度h下,其反应面积大,有利于钢、渣之间的反应,适用于吹炼高磷铁水。
③截锥体炉型:该炉型的熔池有一个倒置的截锥体组成。
其特点是,形状简单,炉底砌筑简便,其形状基本上能满足于炼钢反应的要求。
与相同容量的其他炉型相比,在熔池直径相同的情况下,熔池最深,适用于小型转炉。
结合中国已建成的转炉的设计经验,在选择炉型时,可以考虑:100~200t以上的大型转炉,采用筒球形炉型;50~80t的中型转炉,采用锥球形转炉;30t以下的小型转炉,采用截锥体转炉。
1.1.3转炉炉型主要参数的确定迄今为止,国内外还没有一套完整的转炉炉型的理论计算公式,不能完全从理论上确定一个理想的转炉炉型和炉型各部分尺寸参数。
现有的公式都属于经验公式。
目前国内各厂进行转炉炉型设计时,一般都是采用“依炉建炉”的设计方法。
即通过考察和总结同类转炉的长期生产情况和较先进的技术经济指标,结合采用经验公式和进行可行的模拟试验,再结合当地的条件做适当的修改,来确定转炉的炉型尺寸。
- 1、下载文档前请自行甄别文档内容的完整性,平台不提供额外的编辑、内容补充、找答案等附加服务。
- 2、"仅部分预览"的文档,不可在线预览部分如存在完整性等问题,可反馈申请退款(可完整预览的文档不适用该条件!)。
- 3、如文档侵犯您的权益,请联系客服反馈,我们会尽快为您处理(人工客服工作时间:9:00-18:30)。
2.转炉炉型设计及计算2.1转炉容量的计算2.1.1根据生产规模和产品方案计算出年需要钢水量:年需钢水量=良坯收得率年需良坯量年需不同钢种的连铸方坯250×104t ,连铸板坯200×104t 。
连铸收得率99%,则:年需钢水量=99%450=450×104t 2.1.2计算年出钢炉数:(按2吹2计算) 年出钢炉数=2冶炼周期转炉作业率日历时间冶炼周期年炼钢时间⨯⨯=⨯2转炉作业率=79.5%100%365290100%=⨯=⨯日历天数转炉有效作业天数转炉有效作业天数:日历天数扣除大于20min 以上的一切检修和故障时间总和,转炉工艺设计技术规范规定,当转炉与单台连铸机配合全连铸时为275~300天。
本设计取290天。
冶炼周期按容量大小确定,大于100t 为38~45min ,本设计取40min , 则:年出钢炉数=2×365×79.5%×24×60/40=20880炉每天出钢炉数=炉年作业天数年出钢炉数7229020880==平均产钢水量=215.5t 208804500000==年出钢炉数年产钢水量2.1.3按标准系列确定炉子容量:选定250t 转炉2座,按照2吹2方式生产。
核算车间年产量:250×20880×99%=495.9×104t 良坯。
2.2转炉炉型设计 2.2.1原始条件炉子平均出钢量为250t ,铁水密度6.8g/cm 3,铁水收得率为92%。
2.2.2炉型选择顶底复吹转炉的炉型基本上与顶吹和底吹转炉相似;它介于顶吹转炉和底吹转炉之间。
为了满足顶底复吹的要求炉型趋于矮胖型,由于在炉底上设置底吹喷嘴,炉底为平底,所以根据原始数据,为了便于设置底部供气构件,选择截锥形炉型。
2.2.3炉容比炉容比指转炉有效容积V t 与公称容量T 之比值V t /T(m 3/t)。
V t 系炉帽、炉身和熔池三个内腔容积之和。
公称容量以转炉炉役期的平均出钢量表示,这种表示方法不受操作方法和浇注方法的影响。
转炉新砌炉衬的炉容比推荐值为0.85-0.95m 3/t,大转炉取下限,本设计取V/T=0.95。
2.2.4熔池尺寸的计算 2.2.4.1熔池直径的计算tGKD = 式中 D —熔池直径,m ; G —新炉金属装入量,t ; t —垂杨时间,min ; K —比例系数; (1)确定初期装入量G :取B=15% )(金t 252%921%1522502122=⨯+⨯=∙+=ηB T G )(金金3m 2.378.6252G ===ρV 式中 B —老炉比新炉多产钢系数; 金η—钢水收得率;V 金—新炉装入量占的体积; (2)确定吹氧时间:吨耗氧量:57m 3/t ,吹氧时间14minm i n )]/([07.414573∙===t m 吹氧时间吨耗氧量供养强度 取K=1.50 则: D=1.5×14252=6.36m 2.2.4.2熔池深度的计算。
熔池深度h=1.602m 6.360.57437.20.574DV 22=⨯=金2.2.4.3炉帽尺寸的计算确定(1)炉口直径d 0:取d 0=0.43 D=0.43×6.36=2.73(m )。
(2)炉帽倾角θ:选θ=640。
(3)炉帽高度H 帽:H 膛=21(D-d 0)64tan 0=21×(6.36-2.73)×60tan 0=3.72(cm )取H 口=400 mm ,则整个炉帽高度为: H 帽=H 膛+ H 口=3.72+0.4=4.12(m ) 炉帽体积为: V 帽=V 口+V 锥=4π ×d 02H 口+12π ×H 膛×(D 2+Dd 0+d 02) = 4π×2.732×0.4+12π×3.72×(6.362+6.36×2.73+2.732)=63.9(m³) 2.2.4.4炉身尺寸的确定(1)炉膛直径D 膛=D (无加厚段)。
(2)根据选取的炉容比为0.95,可算出炉子的总容积为: V 总=0.95×250=237.5(m³)V 池=V 金=T/ρ=252.8/6.8=37.2(m³)则:V 身 =V 总-V 池-V 帽=237.5-37.1-65.87 =134.13(m³) (3)炉身高度: H 身=24D V ⨯π身=236.6413.134⨯π=4.22(m ) 则炉型内高:H 内=h+H 帽+H 身 =1.602+4.22+4.12 =9.946(m ) 2.2.4.5出钢口尺寸的确定出钢口尺寸的确定。
出钢口一般都设在炉帽与炉身交界处,以便当转炉处于水平位置出钢时其位置最低,可使钢水全部出净。
出钢口的主要尺寸是其中心线的水平倾角和直径。
(1) 出钢口直径:d T =T 75.163+=25075.163⨯+=0.2m (2) 出钢口衬砖外径:d sT =6d T =6×0.2=1.2(m ) (3) 出钢口长度:L T =7d T =7×0.2=1.2(m )(4)出钢口倾角:出钢口角度是指出钢口中心线与水平显得夹角,其大小应考虑缩短出钢口长度,有利维修、减少钢水二次氧气及热损失,大型转炉的出钢口角度趋向减小。
国外不少采用18°,但0°倾角使钢流对钢包内金属的冲力变小。
本设计取θ=18° 2.2.4.5炉衬厚度确定查表知,炉身工作层选700mm ,永久层选115mm ,填充层选100mm 。
总厚度为:800+115+100=915(mm ) 炉壳内径为:D 壳内=6.36+1.015×2=8.19(m )炉帽工作层选600mm ,永久层选150mm ,炉底工作层选600mm ,永久层230mm ,黏土砖平砌三层65×3=195mm 。
则炉底砖衬总厚度为:600+230+195=1025(m ) 故炉壳内型高度为:H 壳内=9.946+1.025=10.971(m )表2.1 转炉炉衬厚度的设计值2.2.4.6炉壳厚度确定查表选择:炉帽:65mm 厚钢板 炉身:75mm 厚钢板 炉底:65mm 厚钢板2.2.4.7验算高宽比:由以上数据可计算得:H 总=11036+65=11036(m ) D 壳=8190+2×75=8340(m )则:壳总D H =32.1834011036由此可知,壳总D H 的比值符合高宽比的推荐值,因此所设计的炉子尺寸基本上是合适的,能够保证转炉的正常冶炼。
2.3材质的选择选用镁碳转,含碳量为14%。
镁碳砖具有耐高温、耐渣侵和耐剥落等优良的使用性能。
与其他镁砖相比,在使用过程中变质层变薄,不至于引起砖体结构的剥落,加入相当的数量的石墨改善了砖的导热性能,具有良好的抗震性。
用镁碳砖砌筑炉衬,大幅度的提高了炉衬的使用寿命,再配合溅渣护炉等护炉技术,炉衬寿命可达1万次以上。
但由于镁碳砖成本较高,因此根据在冶炼过程中,工作层不同部位受损情况的不同,采用不同档次的镁碳砖,这样整个炉衬的受损情况较为均匀,就是综合砌炉。
2.3.1炉口部位该部位温度变化剧烈,熔渣和高温废气的冲刷较严重,在加料和清理残钢、残渣时。
炉口受到撞击,因此用于炉口的耐火砖必须具有抗热震性和抗渣性,耐熔渣和高温废气的冲刷,且不易粘钢的易于清理的镁碳砖。
2.3.2炉帽部位该部位是受熔渣侵蚀最严重的部位,同时还受温度急变的影响和含尘废气的冲刷,故使用抗渣性强和抗热震性好的镁碳砖。
2.3.3炉衬装料部位该部位除受吹炼过程熔渣和钢水时的直接撞击与冲刷、化学侵蚀外,还要受到装入料废钢和兑铁水时的冲蚀,给炉衬带来严重的机械性损伤,因此应砌筑具有较高抗渣性、高强度、高抗热震性的镁碳砖。
2.3.4炉衬出钢侧面此部位主要是受出钢时钢水的热冲击和冲刷作用,损坏速度低于装料侧,所以可砌筑档次低一些的镁碳砖,并且砌筑厚度可薄一些。
出钢口除受高温钢水的冲刷外,还经受温度急变的影响,蚀损严重,需要经常更换,影响冶炼时间,而出钢口则采用等静压成型的整体镁碳砖出钢口,整体结构方便更换。
2.3.5渣线部位此部位在吹炼过程中,炉衬与熔渣长期接触受到严重侵蚀而形成。
在出钢侧渣线位置的变化并不明显,但在排渣侧受到熔渣的强烈侵蚀,再加上吹炼过程中其他作用的共同影响,衬砖损毁较为严重,应砌筑抗渣性良好的镁碳砖。
2.3.6两侧耳轴部位该部位出受吹炼过程的蚀损外,其表面又无保护渣层覆盖,砖体中的碳素极易被氧化,并难于修补,因而损坏严重。
故此部位应砌筑抗渣性好、抗氧化性能强的高级镁碳砖。
2.3.7熔池和炉底部位此部位炉衬在吹炼过程中受钢水强烈冲蚀,并且采用顶底复吹工艺,炉底中心部位容易损毁,可与装料侧砌筑相同材质的镁砖。
2.4炉衬由永久层、填充层和工作层组成无绝热层时,永久层紧贴炉壳,修炉时一般不予拆除,作用是保护炉壳,常用镁砖砌筑。
填充层介于永久层与工作层之间,一般用焦油镁砂捣打而成,厚度约80~100 mm。
工作层与金属、熔渣和炉气接触的内层炉衬,工作条件相当恶劣,用高、中、低不同档次的镁碳砖砌筑。
炉帽可用二步煅烧镁砖。
2.5砖型选择尽可能使用大砖,以提高筑炉速度,减少砖逢,减轻劳动强度。
力争砌筑过程中不打砖和少打砖,以提高砖的利用率和保证砖的质量。
对用小砖组合起来有困难或难以保证砌筑质量的部位,如出钢口和炉底,则选用异型砖。
尽量减少砖型种。
炉壳由炉帽、炉身和炉底三部分组成。
炉帽制成截圆锥型。
由于炉帽,特别是炉口部位受高温作用易变形,所以采用水冷炉口,这样既提高了炉帽的寿命,又减少炉口粘渣。
采用埋管式水冷炉口结构,将通冷却水用的蛇形钢管埋铸在铸铁的炉口圈内。
虽然制作难度大,但使用安全,也比水箱式寿命长。
水冷口采用适合于中、小型转炉的卡板连接方式,将炉口固定在炉帽上,即可拆式的,便于修理。
炉身制成圆柱型,它是整个炉子的承载部分,受力最大。
转炉的整个重量通过炉身钢板支撑在托圈上,并承受倾动力矩,因此用于炉身的钢板要比炉帽和炉底的钢板适当厚些。
为防止炉壳受热变形,延长其使用寿命,可将炉帽外壳上盘旋焊上角钢,内通冷却水;将炉身焊上盘旋槽钢,内通冷却水。
2.6支撑装置支撑装置承载着转炉炉体的全部重量。
其中主要部件有托圈,炉体与托圈的连接装置,耳轴及其轴承。
2.6.1托圈托圈是转炉的重要承载和传动部件,材质选用Q235钢板制作。
托圈断面为箱形。
为增加托圈刚度,在其中间焊有垂直筋板。
托圈内通水冷却,以降低热应力。
托圈的高宽比为3,托圈与炉壳之间有一定的空隙,以改善炉身的散热条件,并留有炉壳受热膨胀变形之空间。