钢液的脱氮
氮在钢中的溶解与去除
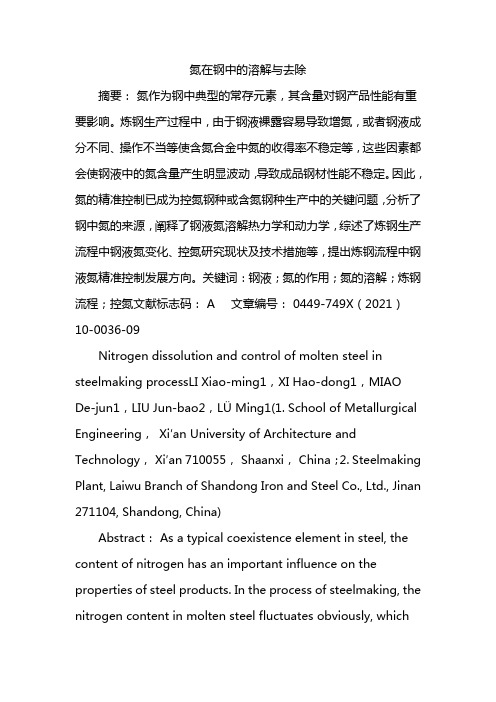
氮在钢中的溶解与去除摘要:氮作为钢中典型的常存元素,其含量对钢产品性能有重要影响。
炼钢生产过程中,由于钢液裸露容易导致增氮,或者钢液成分不同、操作不当等使含氮合金中氮的收得率不稳定等,这些因素都会使钢液中的氮含量产生明显波动,导致成品钢材性能不稳定。
因此,氮的精准控制已成为控氮钢种或含氮钢种生产中的关键问题,分析了钢中氮的来源,阐释了钢液氮溶解热力学和动力学,综述了炼钢生产流程中钢液氮变化、控氮研究现状及技术措施等,提出炼钢流程中钢液氮精准控制发展方向。
关键词:钢液;氮的作用;氮的溶解;炼钢流程;控氮文献标志码: A 文章编号: 0449-749X(2021)10-0036-09Nitrogen dissolution and control of molten steel in steelmaking processLI Xiao-ming1,XI Hao-dong1,MIAO De-jun1,LIU Jun-bao2,LÜ Ming1(1. School of Metallurgical Engineering,Xi′an University of Architecture and Technology,Xi′an 710055,Shaanxi,China;2. Steelmaking Plant, Laiwu Branch of Shandong Iron and Steel Co., Ltd., Jinan 271104, Shandong, China)Abstract: As a typical coexistence element in steel, the content of nitrogen has an important influence on the properties of steel products. In the process of steelmaking, the nitrogen content in molten steel fluctuates obviously, whichleads to unstable properties of finished steel, because the exposed molten steel easily leads to nitrogen increase, or the yield of nitrogen in nitrogen-containing alloy is unstable due to different compositions of molten steel and improper operation. Therefore, the precise control of nitrogen has become a key issue in the production of nitrogen-controlled steel or nitrogen-containing steel. The sources of nitrogen, the thermodynamics and kinetics of nitrogen dissolution in molten steel were analyzed, the changes of nitrogen in molten steel production process, the research status and technical measures of nitrogen control were summarized, and the development direction of precise control of nitrogen in steelmaking process puts forward.Key words:molten steel;effect of nitrogen;dissolution of nitrogen;steelmaking process;control of nitrogen氮作为钢中常存元素之一,对钢材性能有有利作用,如在奥氏体钢中可作为固溶强化元素,扩大并稳定形成奥氏体组织,提高钢材力学性能和耐腐蚀性能;或促进奥氏体区V(C,N)析出,为亚微米析出相提供非均匀形核中心。
金属冶炼中的脱硫和脱氮技术

总结词:利用微生物的代谢作用将氮从金属中去除。
脱硫和脱氮技术的比较与选择
脱硫技术
湿法脱硫:利用碱性溶液吸收烟气中的硫氧化物,生成亚硫酸盐或硫酸盐,再进一步处理。优点是脱硫效率高,但存在腐蚀、结垢和二次污染等问题。
干法脱硫:利用固体吸附剂或催化剂在干态下脱除烟气中的硫氧化物。优点是操作简单、无腐蚀,但脱硫效率相对较低。
脱氮技术
燃烧后脱氮:在燃烧后对烟气进行脱氮处理,通过化学或物理方法去除氮氧化物。优点是技术成熟,但投资和运行成本较高。
燃烧中脱氮:通过控制燃烧条件和加入还原剂,在燃烧过程中降低氮氧化物的生成。优点是成本较低,但技术难度较大。
根据当地环保法规和排放标准,选择满足要求的脱硫和脱氮技术。
环保要求
综合考虑初始投资、运行费用以及维护成本,选择经济可行的技术方案。
总结词
通过化学反应将氮从金属中去除。
要点一
要点二
详细描述
化学脱氮技术包括还原法和氧化法等。还原法是通过加入还原剂,将金属中的氮还原成更低价的氮化合物,如氨或氮气,从而将其从金属中去除。氧化法则是通过加入氧化剂,将金属中的氮氧化成高价的氮化合物,如硝酸盐或亚硝酸盐,然后将其从金属中分离出来。这些化学反应需要在特定的温度和压力条件下进行,以实现最佳的脱氮效果。
联合处理
将脱硫和脱氮技术进行联合处理,实现多种污染物的协同处理,提高处理效果。
资源化利用
将脱硫和脱氮过程中产生的副产物进行资源化利用,如生产化肥、建筑材料等,提高资源利用率。
智能化控制
利用物联网、大数据等技术手段,实现脱硫和脱氮过程的智能化控制,提高处理效率和稳定性。
法规推动
加强相关法规的制定和执行力度,推动企业采用先进的脱硫和脱氮技术,促进技术的普及和应用。
氮在钢水中的行为及工艺控制研究

山西冶金SHANXI METALLURGY Total 188No.6,2020DOI:10.16525/14-1167/tf.2020.06.17试(实)验研究总第188期2020年第6期氮在钢水中的行为及工艺控制研究晏武,付有彭,张忠福,王哲,任涛,孙海坤,李毅(日照钢铁控股集团有限公司,山东日照276800)摘要:氮元素在钢水中含量过高会导致钢材强度升高,降低钢材的韧性及塑性,严重时会影响钢材的时效性并引发“蓝脆”。
本文介绍了炼钢工序增氮及脱氮的机理,并制定了控氮措施,对转炉工序、精炼工序、RH 真空处理阶段做出了针对性的调整,钢水氮得到了有效控制。
关键词:炼钢增氮危害脱氮中图分类号:TF711文献标识码:A文章编号:1672-1152(2020)06-0041-04收稿日期:2020-07-22第一作者简介:晏武(1988—),男,硕士,毕业于安徽工业大学冶金工程专业,主要从事炼钢工艺技术相关工作。
钢中的氮是以氮化物的形式存在,它对钢质量的影响表现出双重性,氮含量高的钢种长时间放置将会变脆,这一现象称为“老化”或“时效”。
原因是钢中氮化物(Fe 4N )的析出速度很慢,逐渐改变着钢的性能。
钢中氮含量高时,会使钢发生第一类回火脆性,即在250~450℃温度范围内,其表面发蓝,钢的强度升高,冲击韧性降低,称为“蓝脆”。
氮的存在会使铸坯产生结疤和皮下气泡,在轧制过程中产生裂纹和发纹。
氮含量增加,钢的焊接性能变坏,造成焊接热影响区脆化,降低磁导率、电导率。
对于某些钢种氮的存在对其性能有一定的益处,氮可以起到细化晶粒的作用,但由于氮元素原子半径较大,即使在真空条件下扩散速率也不是很大[1],所以如何有效将钢水中氮去除仍是困扰炼钢工序的一个难题。
1氮对钢的影响在590℃时氮在α-Fe 中最高溶解度时约为0.1%,室温下降到0.001%以下。
对于游离氮含量高的钢,在高温下较快冷却时,铁素体将会被饱和,长时间放置,性能将变脆。
氮在钢中的溶解与去除
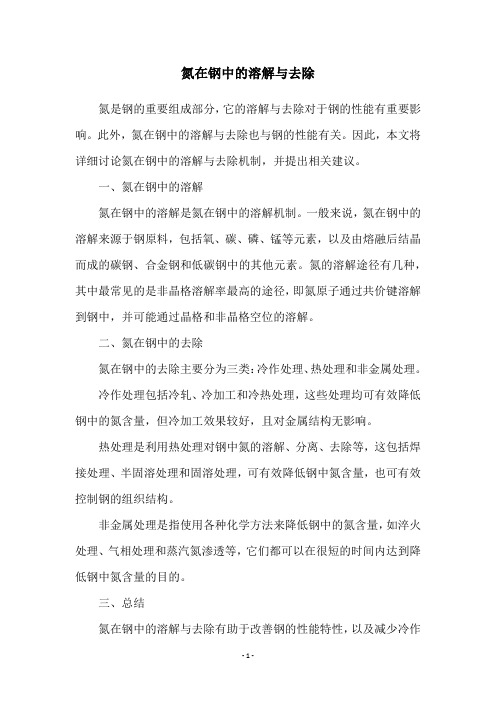
氮在钢中的溶解与去除
氮是钢的重要组成部分,它的溶解与去除对于钢的性能有重要影响。
此外,氮在钢中的溶解与去除也与钢的性能有关。
因此,本文将详细讨论氮在钢中的溶解与去除机制,并提出相关建议。
一、氮在钢中的溶解
氮在钢中的溶解是氮在钢中的溶解机制。
一般来说,氮在钢中的溶解来源于钢原料,包括氧、碳、磷、锰等元素,以及由熔融后结晶而成的碳钢、合金钢和低碳钢中的其他元素。
氮的溶解途径有几种,其中最常见的是非晶格溶解率最高的途径,即氮原子通过共价键溶解到钢中,并可能通过晶格和非晶格空位的溶解。
二、氮在钢中的去除
氮在钢中的去除主要分为三类:冷作处理、热处理和非金属处理。
冷作处理包括冷轧、冷加工和冷热处理,这些处理均可有效降低钢中的氮含量,但冷加工效果较好,且对金属结构无影响。
热处理是利用热处理对钢中氮的溶解、分离、去除等,这包括焊接处理、半固溶处理和固溶处理,可有效降低钢中氮含量,也可有效控制钢的组织结构。
非金属处理是指使用各种化学方法来降低钢中的氮含量,如淬火处理、气相处理和蒸汽氮渗透等,它们都可以在很短的时间内达到降低钢中氮含量的目的。
三、总结
氮在钢中的溶解与去除有助于改善钢的性能特性,以及减少冷作
处理成本。
上述溶解与去除机制均为降低钢中氮含量的可行手段,但要考虑到其处理条件和成本之间的平衡。
此外,钢的温度、时间和氧分也是影响氮在钢中溶解与去除的重要因素,应合理控制这些因素的大小,以保证溶解与去除的效率最大化。
底吹转炉钢中氮的含量与处理方法
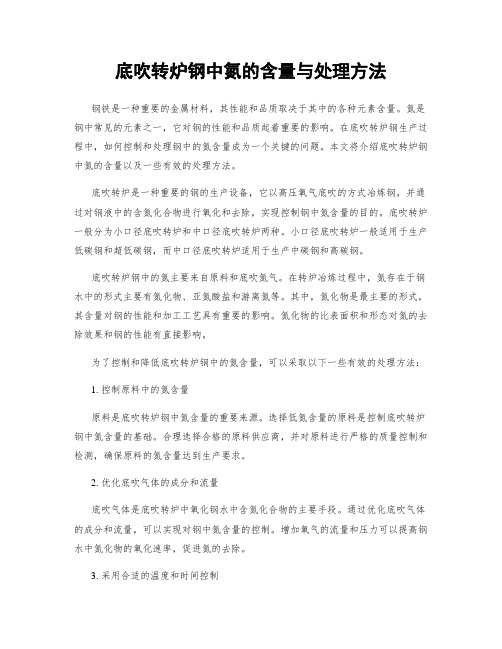
底吹转炉钢中氮的含量与处理方法钢铁是一种重要的金属材料,其性能和品质取决于其中的各种元素含量。
氮是钢中常见的元素之一,它对钢的性能和品质起着重要的影响。
在底吹转炉钢生产过程中,如何控制和处理钢中的氮含量成为一个关键的问题。
本文将介绍底吹转炉钢中氮的含量以及一些有效的处理方法。
底吹转炉是一种重要的钢的生产设备,它以高压氧气底吹的方式冶炼钢,并通过对钢液中的含氮化合物进行氧化和去除,实现控制钢中氮含量的目的。
底吹转炉一般分为小口径底吹转炉和中口径底吹转炉两种。
小口径底吹转炉一般适用于生产低碳钢和超低碳钢,而中口径底吹转炉适用于生产中碳钢和高碳钢。
底吹转炉钢中的氮主要来自原料和底吹氮气。
在转炉冶炼过程中,氮存在于钢水中的形式主要有氮化物、亚氮酸盐和游离氮等。
其中,氮化物是最主要的形式,其含量对钢的性能和加工工艺具有重要的影响。
氮化物的比表面积和形态对氮的去除效果和钢的性能有直接影响。
为了控制和降低底吹转炉钢中的氮含量,可以采取以下一些有效的处理方法:1. 控制原料中的氮含量原料是底吹转炉钢中氮含量的重要来源。
选择低氮含量的原料是控制底吹转炉钢中氮含量的基础。
合理选择合格的原料供应商,并对原料进行严格的质量控制和检测,确保原料的氮含量达到生产要求。
2. 优化底吹气体的成分和流量底吹气体是底吹转炉中氧化钢水中含氮化合物的主要手段。
通过优化底吹气体的成分和流量,可以实现对钢中氮含量的控制。
增加氧气的流量和压力可以提高钢水中氮化物的氧化速率,促进氮的去除。
3. 采用合适的温度和时间控制在底吹转炉钢的冶炼过程中,合适的温度和时间控制对氮的去除至关重要。
过高的温度可能导致氮的氮化物不完全分解,从而无法有效去除氮;而过低的温度可能会导致炉内化学反应不充分,同样达不到去除氮的效果。
根据具体的钢种和生产要求,选择合适的温度和时间控制条件,以获得更好的氮去除效果。
4. 增加钢水的搅拌和倾注方式通过增加钢水的搅拌和倾注方式,可以促进底吹转炉钢中的氮化物与氧气的接触和反应。
冶炼过程钢水氮的脱除与控制

造成火点区钢液的吸氮速度大于 C O气泡 的脱氮 速度 , 钢液在火点 区从气相 中吸氮造成钢中氮含 量升高 , 低碳钢补吹后增氮 6— 1 0 p p m。 吹炼过程中 , 反应 区元素氧化产生了极高 的 温度 , 碳氧化产生的 C O气泡降低 了氮分压, 同时 乳化的渣相和 C O气泡共同为脱氮反应提供了足 够大的反应界面积 , 这一时段脱氮强烈 , 适度提高 脱碳速率可以有效脱氮 , 如图 1 ; 吹炼末期 , 脱碳 速率减缓 , C O气体生成量大大降低 , 脱氮能力迅 速降低 , 空气进入炉 内的机率增加 , 氧气射流的强 烈 冲击 与搅 拌 作 用造 成 空 气 中 的氮被 钢 水 吸收 , 从而造 成钢水 中氮含量增加 , 这 时, 应该降低枪 位, 提高底吹搅拌强度 , 保证碳 氧反应速 度, 多产
豳{
如
磁 磐
嫡
脱 碳 速率 ( %/ ai r n)
3 冶炼 工序 氮的控制
3 . 1 转 炉 工序 的控 制
图 1 转炉脱 碳速 率对 氩 站氮的 影 响
转 炉终 点 碳 与 氮 含 量 的对 应 关 系 如 图 2所
示, 随着转炉终点碳含量下降 , 钢水中氮含量有增
・
l・
铸坯开裂及引起晶间腐蚀。针对 目前部分钢种氮 含量较 高 的这 一 情 况进 行分 析 , 找 到 控 制 钢 水 氮
含量 的措施 。
1 同类钢种氮 的水 平
钢水 中氮 的来 源 主要 是 铁水 中 的氮 , 转 炉 吹 炼 过程 中脱 除 大 部 分 氮 , 过 R H 炉 超 低碳 钢 氮 的
生 C O减少 钢水 吸氮 。
控制关键在转炉、 连铸减少增氮; 过L F炉的合 金
氮在钢中的溶解与去除

这是在未考虑合金之间相互影响的情况下
进行近似计算的结果, 即使考虑这个影响, 这个
值变化亦不大。
112 关于温度的影响
氮在铁液中的溶解 N 与温度的关系为:
Log[ N] = 26T3421106 对于含有大量合金的钢液有以下关系。[3]
Log[ N] = 210T002( 0186~ 0106) [ Si] 20124[ C] + 0115[ Mn]
合金元素含量对氮在钢中溶解度的影响, 是由于合金元素的加入, 改变了氮在钢中的活 度。如果合金元素与氮的亲合力强, 则使氮在 钢中的活泼程序下降, 即活度减少, 因而溶解度 增加。
氮在铁中的溶解度, 是遵守平方根定律的:
[ N] = KN PN2
( 1)
当氮气压力= 1 大气压时, 不同温度下氮
在铁中的溶解度如图 1。
中氮气析出引起的。
氮的溶解与温度, 溶解热有以下的关系:
[ N] = A/ fN#exp( -
Q RT
)
Q 为溶解热。在放热情况下, Q 为负值。
图 3 含氮钢锭的蜂窝状皮下气孔
溶解度随温 度的升高而减 少。在吸热 的情况
下, Q 为正值, 溶解度随温度的升高而增大。从
氮在铁中的溶解度来看, 在熔融状态下, 氮在钢 中的溶解度随温度而增大, 而合金的加入, 只能
联系人: 宫一衡 高级 工程 师 四川 江 油( 621701 ) 四 川川 投 长城 特殊 钢 股份 有 限公 司 第一 钢厂 技 术中 心 电 话: ( 0816 ) 3651926
# 6#
5 特 钢技 术6
国家
中
国
日本 意大利 西德
厂名 炉号
长钢 上五
一种降低钢中氮含量的冶炼方法

一种降低钢中氮含量的冶炼方法
钢材中含氮量的高低对其性能和质量有很大的影响,因此降低钢中氮含量是钢铁工业中非常重要的一项任务。
一种常见的降低钢中氮含量的方法是使用脱氮剂。
脱氮剂是一种能够与钢中的氮元素反应,形成氮化物而将其从钢中移除的化学物质。
常用的脱氮剂有钙、铝等,其中钙是最常用的一种。
在具体的生产过程中,通常会将脱氮剂加入到钢中,并在高温状态下进行混合,以促进氮元素与脱氮剂的反应。
经过反应后,脱氮剂与钢中的氮元素产生化学变化,形成不溶于钢中的氮化物,并在钢液表面上浮起,从而被倾倒或抛弃。
这样可以有效地降低钢中氮元素的含量,提高钢材的质量。
除了使用脱氮剂,钢铁工业还可以采用其他方法降低钢中氮含量,如通过改变合金配比、调整冶炼工艺等手段。
但在实际生产中,脱氮剂仍然是最常用的方法,其经济性和实用性得到工业界的广泛认可。
总之,降低钢中氮含量是钢铁工业中非常重要的一项任务,利用脱氮剂可以有效地达到降低钢中氮含量的目的。
电炉冶炼中测定钢液中氮含量原理是什么
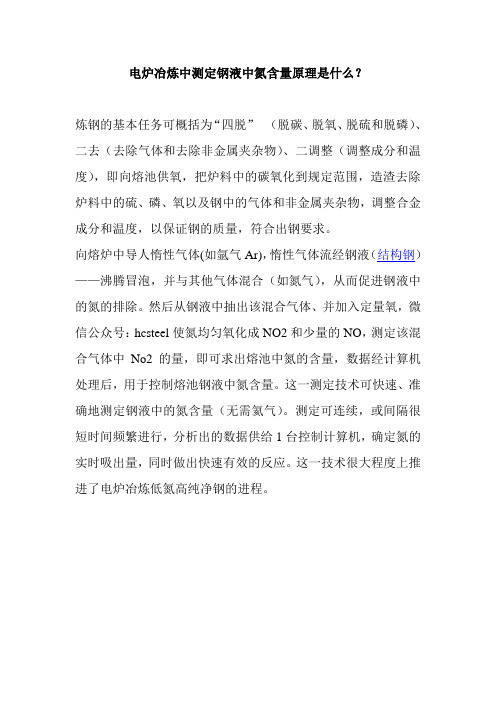
电炉冶炼中测定钢液中氮含量原理是什么?
炼钢的基本任务可概括为“四脱”(脱碳、脱氧、脱硫和脱磷)、二去(去除气体和去除非金属夹杂物)、二调整(调整成分和温度),即向熔池供氧,把炉料中的碳氧化到规定范围,造渣去除炉料中的硫、磷、氧以及钢中的气体和非金属夹杂物,调整合金成分和温度,以保证钢的质量,符合出钢要求。
向熔炉中导人惰性气体(如氩气Ar),惰性气体流经钢液(结构钢)——沸腾冒泡,并与其他气体混合(如氮气),从而促进钢液中的氮的排除。
然后从钢液中抽出该混合气体、并加入定量氧,微信公众号:hcsteel使氮均匀氧化成NO2和少量的NO,测定该混合气体中No2的量,即可求出熔池中氮的含量,数据经计算机处理后,用于控制熔池钢液中氮含量。
这一测定技术可快速、准确地测定钢液中的氮含量(无需氦气)。
测定可连续,或间隔很短时间频繁进行,分析出的数据供给1台控制计算机,确定氮的实时吸出量,同时做出快速有效的反应。
这一技术很大程度上推进了电炉冶炼低氮高纯净钢的进程。
钢包渣中V_2O_5和稀土氧化物在常压下对钢液脱氮的影响

钢包渣中V 2O 5和稀土氧化物在常压下对钢液脱氮的影响黄小东 王世俊 王海川 周 云(安徽工业大学)摘 要 为了研究熔渣中V 2O 5和R e x O y 对钢液氮含量的影响,选用CaO -Si O 2-A l 2O 3系碱性渣作为基础渣系。
通过对试验结果分析可知,熔渣中加入V 2O 5后,对钢液脱氮起了一定的作用,但效果不明显;渣中加入R e x O y 后,对钢液脱氮的影响不太明显,但是,它能够较好保护钢液,阻止钢液吸氮。
关键词 钢液 钢包顶渣 氮含量 V 2O 5 R e x O yI nf luence of Con ten t Change of V 2O 5and Re x O y i nthe M olten Slag on Rem oval of N itrogenunder the Con stan t A t m osphereH uang X iaodong ,W ang Sh ijun ,W ang H aichuan and Zhou Yun(A nhu i U n iversity of T echno logy )Abstract In o rder to study the influence ru les of V 2O 5and R e x O y in the ladle slag on n itrogen con ten t in liqu id steel ,the basic slag system of CaO -Si O 2-A l 2O 3w as cho sen as a basic ingredien t in the experi m en t .By analyzing experi m en t resu lts ,though V 2O 5in the mo lten slag has a defin ite effect on removal of n itrogen ,the functi on w as no t strong ;R e x O y in the flux has a little influence on removal of n itrogen from the liqu id steel ,bu t it can p ro tect mo lten steel from ab so rb ing n itrogen from the atmo sphere .Keywords L iqu id steel ,L adle slag ,N itrogen con ten t ,V 2O 5,R e x O y1 引言众所周知,氮在钢中一般被视为有害元素,它是产生屈服点现象的原因之一,由此造成深拉过程的拉伸变形,影响钢板的磁性、导电性和焊接性能;同时氮与钢中应变失效有密切的联系。
7超纯铁素体不锈钢的脱氮工艺及效果

1真空脱氮
1.1脱氮热力学 铁液中氮的溶解遵循西华特定律:
I N]=告N:IN]=争佤
(1)
由(1)式可以看出,随着氮分压的降低,铁液中 氮的溶解度下降,反之,氮溶解度升高。因此,要去 除钢液中氮,应设法降低氮分压。目前有两种降低 氮分压的方法,一是降低系统压力,比如VOD和RH 工艺;二是稀释法,比如AOD工艺。
氮在纯铁液中的溶解标准自由能采用Pehlke… 和Elliott[21推荐的数据,即:
En]:10一半“24新i∽:1)
(2)
由(2)式可知,氮在铁液中的溶解是吸热过程,
因而随温度升高,氮的溶解度增加,因此,降低温度 有利于降低铁液中的氮溶解度。
不锈钢中一般含有Cr、si、Ni、Mo、Mn及其它元 素,元素问相互影响作用不能忽略,Cr、Mo、Mn等元 素降低氮的活度,不利于氮的脱出;而c、Ni等元素 能提高氮的活度,对脱氮有好处。根据Chipman和 Corrigan的研究∞J,提高温度有利于降低钢液中的 氮溶解度。 1.2脱氮动力学
Material Index VOD。Ultra—pure Ferrite Staiuless Steel。Denitriding.Process
超纯铁素体不锈钢需极低的c、N含量,以获得 更加优良的性能,因此深度脱碳、脱氮成为超纯铁素 体不锈钢冶炼的核心技术。本文针对太钢85 t VOD 冶炼高铬超纯铁素体不锈钢生产实践,优化VOD降 氮工艺。
表1 00Crl8M02、00Crl7Mo超纯铁素体不锈钢化学成分/% Chemical compositions of ultra-pure ferrite stainless steel 00Crl8M02 and 00Crl7Mo,%
钢种 00Crl8M02
钢液的脱氮
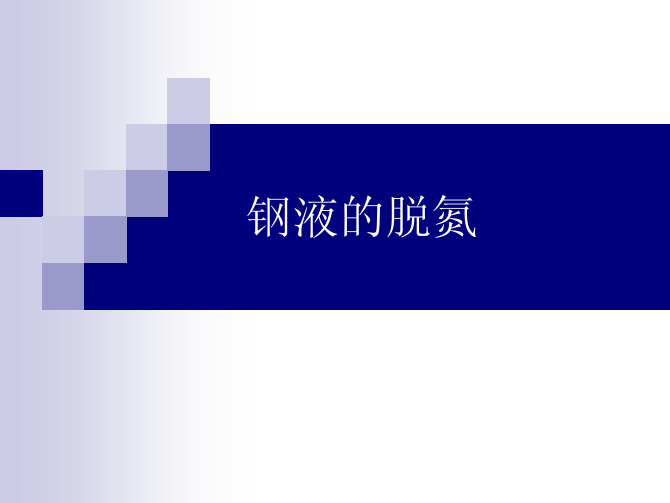
RT
<2>
<2>带入<1>式得:
dw[ N ] dw[C ] 2 = 572 × w[ N ]% × dt dt
dw[C ] = P ⋅
dw[ N ] ⋅ W M c ⋅ ' 2 PN 2 ⋅ M N W
dw[ N ] × 12 × 10 − 3 dw[ N ] = = 2 2 14 × 10 − 3 × 2 × 0 .5 × 490 .33 × w[ N ] % 572 w[ N ] %
−3
注: (1) 忽略钢液,炉渣表面的吸氮; (2) 脱氮反应未达平衡,不平衡常数a=0.5; (3) 已知
2 [ N ] = N 2( g ) , ΔGθ = −7190 − 47.77 J / mol
解:(1)脱N过程认为由三个步骤组成: 1)钢液中氮通过钢液边界层扩散到CO气泡表面; 2)在气泡/钢液界面上发生化学反应; 3)反应生成的氮分子扩散到气泡内部并随之上浮 排出。
当氮含量超过100ppm时,在铸铁和钢中会 产生气孔,在IN100高温合金中,当氮含量 超过15ppm时,就会造成大量显微缩孔。当 氮与Ti,V等生成脆性氮化物时,严重影响 钢的高温强度和高温塑性。 钢中氮含量控制理论及工艺十分重要。
1 氮的存在形式:自由状态的氮原子[N]和 结合状态的氮离子 2 影响因素:钢中表面活性元素氧、硫的阻 碍、真空度、气泡、熔渣的氮容量等 3 脱氮方式:真空脱氮、熔渣脱氮和气泡携带 法脱氮。 4 脱氮措施:对于生产工艺而言,主要是真空 和搅拌。
1.5 钢中氮的来源
铁水 炼钢用固体辅料 冶金工艺操作 底吹气体
1.6 氮的反应机理
2 钢液脱氮的影响因素及其脱氮方式
温度和表面活性物质对钢液脱氮吸氮的影 响:它们在表面富集占据了一部分可吸附 氮的表面位置,它们对脱氮、吸氮均有影 响,钢液最终N是吸N和脱N综合作用的结 果。
炼钢过程中钢水氮含量控制_李勇

第45卷 第10期 2010年10月钢铁Iron and SteelV ol.45,No.10O ctober 2010炼钢过程中钢水氮含量控制李 勇(济钢集团有限公司技术监督处,山东济南250101)摘 要:为控制钢中氮含量,提高产品的内在质量,通过对炼钢转炉)LF )连铸工艺的生产实践和研究,探讨影响钢中氮含量的因素和控制措施。
通过生产实践数据和研究得到,要满足钢水质量对降氮要求应采取如下措施:转炉底吹氮氩气体切换时间应控制在11min 左右,避免补吹操作,加强出钢口的维护并及时更换出钢口;L F 精炼时避免钢液裸露,采用大渣量埋弧操作;连铸采用保护浇注等。
关键词:复吹转炉;连铸;控制;氮含量中图分类号:T F 703 文献标志码:A 文章编号:0449-749X(2010)10-0052-05Control of Nitrogen Content in Liquid SteelsDuring Steelmaking ProcessLI Yong(T echnolo gy Superv isio n Department,Jinan Iro n and Steel Company ,Jinan 250101,Shandong,China)Abstract:In or der t o contro l the nitr og en co nt ent in liquid steel and impro ve the inher ent quality of the products,based on the pro ductio n practice during the process of BO F -L F -CC,the influence fact ors and contro lling techno lo gy of the nitro gen content in the liquid steel w ere studied.In o rder to meet the needs of steel quality for lo w nitro gen co ntent,the follow ing measur es have to be taken,such as an optimal changing -over t ime o f nitr og en and ar go n hold -ing abo ut 11m in,avo iding r eblow ing time,replacing tap ho le duly;avo iding steel being ex po sed to the atmospher e in LF fur nace,and int roducing the operatio n of lar ge amount slag embedding;adopting pro tected po ur ing process and so on.Key words:co mbined blow ing co nv erter;continuo us casting;contro l;nitro gen content作者简介:李 勇(1974)),男,大学本科,工程师; E -mail :jgliyon g@; 收稿日期:2009-10-15随着工业技术的发展,对钢材的质量要求越来越严格,特别是对钢质的纯净度要求越来越高。
氩直流辉光等离子体钢液脱氮的研究
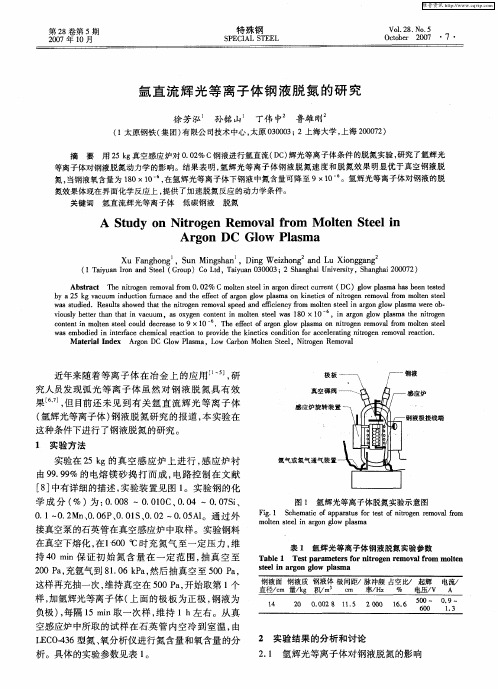
Ar o g n DC o Pls a Glw a m
Xu F n h n u n s a a g o g ,S n Mi g h n ,D n ez o g n u Xin g n i g W ih n a d L o g a g
( a unI nadSel G op oLd T iun00 0 ; hnh i nvr t, hn i 0 0 2 1T i a r n t ( ru )C t, aya 3 0 3 2S ag a U iesy Sa 曲a 20 7 ) y o e i
( 1太原钢铁 ( 集团 ) 限公 司技 术中心 , 有 太原 0 0 0 2上海大学 , 3 03; 上海 20 7 ) 0 0 2 摘 要 用 2 g真空感应 炉对 0 0 %C钢液进行氩直流 ( C 辉光等离子体条 件的脱氮实验 , 5k .2 D) 研究 了氩辉光
等离子体对钢液脱氮动力学 的影 响。结果表 明 , 辉光等 离子体 钢液脱 氮速 度 和脱 氮效果 明显 优于 真空钢液脱 氩 氮, 当钢液氧含量为 10×1 ~, 8 0 在氩 辉光等离子体下钢液 中氮含量可降 至 9×1 0~。氩 辉光等离子体对钢液 的脱
维普资讯
第2 8卷第 5期
20 07年 1 0月
特殊 钢
SPEC1 AL TEEL S
V0. 8 N . 12 . o 5
Oc0 e 2 o tb r 0 7 ・7 ・
氩 直 流 辉 光等 离子体 钢 液脱 氮 的研 究
徐芳泓 孙铭山 丁伟中 鲁雄 刚
b 5k au m id ci mae a dtee e t f ro O ls ao ie c f i o e mo a f m m l ns e ya gvc u u t nf c n f c o ag ng W p m n kn t s t g nr v o o e t l 2 n o u h l a i o nr e l r t e
钢液真空提升脱气法(DH法)
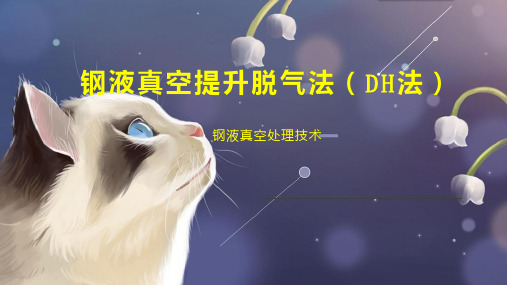
工艺流程和工艺特点
DH法的工艺流程可分8步:(1)处理前根据精炼钢种和出钢量确定需要配加的合金种类和数量,并将其装入料 罐内;(2)调整上下行程;(3)给吸嘴安装挡渣帽;(4)给真空室加热;(5)将装有钢液的钢包运至处理工位,取样、测 温、将吸嘴插入钢液内;(6)启动真空泵,使真空度达到13kPa左右,升降机构开始自动升降,使钢液进入真空室, 开始脱气反应,钢液产生沸腾和喷溅。处理后的钢液回流到钢包,产生搅拌和混匀。这样升降30次左右,钢液经 3次循环,真空度达极限值,脱气基本完成;(7)加入合金料再升降数次,使合金混匀;(8)破真空、测温取样、浇 铸。
钢液真空提升脱气法(DH法)
钢液真空处理技术
01 设备构成
目录
02 脱气原理
03 工艺参数
04 工艺流程和工艺特点
ቤተ መጻሕፍቲ ባይዱ
05 精炼效果及发展前景
钢液真空提升脱气法是早期出现的钢液真空处理技术之一。由联邦德国Dortmund Horder公司1956年设计制 造,取公司名称的头两个字母命名为DH真空脱气法,简称DH法。
设备构成
真空提升脱气设备主要由真空室、提升机构、加热装置、合金加入装置及真空抽气系统组成。(见下图1)钢 液的脱气反应在真空室内进行。主要设备参数有真空室内直径、真空室内高度、吸嘴长度等。真空室内直径与处 理量有关。真空室高度一般为3~5m。加热系统用以减少钢液在处理过程降温,防止钢液粘结在真空室上。可采 用电阻、煤气、重油等加热方式。真空抽气系统一般由多级蒸汽喷射泵组成。
图1
脱气原理
真空提升脱气法是根据压力平衡原理进行工作的。工作时首先将真空室下部的吸嘴插入钢包的钢液中。这种 插入过程可以是钢包台车将钢包抬高,也可以是真空室上部的铰链机构将真空室放下,也可以是二者兼而有之。 此时真空系统开始工作。随着真空度的提高,由于真空室内外压力差的作用,钢液进入真空室内。真空处理过程 中进入真空室的钢液表面压力大大降低,钢液中所溶解的气体的分压力也随之降低,脱气过程钢液中[C]+[O]=CO 反应也向着生成CO的方向进行。从而实现了脱氢、脱氮、真空碳脱氧。当钢包下降或真空室上升时,处理完的钢 液返回钢包,完成一次处理过程。钢包上升或真空室下降,又一个处理过程开始。这样周期性的处理直至达到所 要求的处理效果。
- 1、下载文档前请自行甄别文档内容的完整性,平台不提供额外的编辑、内容补充、找答案等附加服务。
- 2、"仅部分预览"的文档,不可在线预览部分如存在完整性等问题,可反馈申请退款(可完整预览的文档不适用该条件!)。
- 3、如文档侵犯您的权益,请联系客服反馈,我们会尽快为您处理(人工客服工作时间:9:00-18:30)。
图2 真空感应炉冶炼SAE4340钢时氮含 量与精炼时间的关系
2)氩气搅拌对脱氮的影 响。氩气搅拌的主要作 用是增大钢液与气相的 接触面积Ag,使脱氮速 度加快。吹氩搅拌还有 3点好处:a)用气泡不 断更新熔池表面;b) 金属液表面的湍流加速 了传质过程;c)吹氩 搅拌使温度均匀。
3)真空度对真空脱氮也有 较大影响。提高真空度, 钢液实际氮含量与该真空 度下平衡氮含量之差增 加,脱氮反应驱动力加 大。
RT
<2>
<2>带入<1>式得:
dw[ N ] dw[C ] 2 = 572 × w[ N ]% × dt dt
dw[C ] = P ⋅
dw[ N ] ⋅ W M c ⋅ ' 2 PN 2 ⋅ M N W
dw[ N ] × 12 × 10 − 3 dw[ N ] = = 2 2 14 × 10 − 3 × 2 × 0 .5 × 490 .33 × w[ N ] % 572 w[ N ] %
随着温度提高,吸氮速度提高,且吸氮几乎在30s内完成。 温度较低时,钢液氧含量对吸氮速度的影响显著。当温度 升高到2130º时,氧的影响消失。
钢液吸氮的实验研究
不脱氧钢对吸氮影响很小
பைடு நூலகம்
氧越低对吸氮的影响越明显
温度及硫含量对钢液脱氮吸氮的影响
温度升高脱氮速度常数增大,且温度对高硫试样脱氮速率常数的 影响大于对低硫试样的影响。 作者认为碳氧反应之所以能够对高硫、氧钢液有效脱氮,主要是 由于碳氧反应区钢液温度远高于熔池平均温度,氧、硫因表面活 性对钢液脱氮的阻碍作用减少甚至消失。
1.3 结合状态的氮原子
当钢液中氮含量达到饱和以后,并且有与 氮亲和力大的元素存在时,钢液中就会生 成氮化物。 [X]+[N]=XN 此时氮的溶解度由下式表示:
[% N ] = K ( XN ) f N a[ X ]
在氮化物形成的极限之前,[N]受氮的分压 决定,因而可以通过降低氮的分压来去 除。超过了这个极限,氮化物的平衡决定 了氮含量。因此在钢液中的氮与气相中的 氮分压相平衡后,氮化物的形成是一种进 一步脱氮的途径。
日本住友金属公司在VOD脱碳、脱氮的基础上, 开发了一种强化脱碳、脱氮的方法,即VOD-PB 法。这种方法是在常规的VOD生产铁素体不锈钢 时,吹氧脱碳到一定程度,然后改用氩气和氧气 作载气喷吹金属氧化物颗粒,使得脱碳、脱氮反 应同时都得以进一步强化。喷吹的金属氧化物粉 末主要是铁矿粉、锰矿粉及氧化锰(氧化脱碳), 粉末直径小于0.1mm。
−3
注: (1) 忽略钢液,炉渣表面的吸氮; (2) 脱氮反应未达平衡,不平衡常数a=0.5; (3) 已知
2 [ N ] = N 2( g ) , ΔGθ = −7190 − 47.77 J / mol
解:(1)脱N过程认为由三个步骤组成: 1)钢液中氮通过钢液边界层扩散到CO气泡表面; 2)在气泡/钢液界面上发生化学反应; 3)反应生成的氮分子扩散到气泡内部并随之上浮 排出。
θ 由 2 [ N ] = N 2( g ) , ΔG = −7190 − 47.77 J / mol 得
<1>
375.5 lg K = + 2.49 T
θ
1600℃时,N2的平衡压力为:
∗ 2 PN 2 = 490.33 × w[ N ]% × 1.013 × 10 5
Pa
由不平衡参数定义知:
' ∗ 2 PN 2 = α ⋅ PN 2 = 0.5 × 490.33 × w[ N ]% × 1.013 × 10 5
当氮在液相中的扩散为速度限制性环节 时,其脱氮的速度式如下
d [% N ] ' A = − k l ([% N ] − [% N ] e ) V dt
将上式积分得
ln [ N ]0 − K N [N ] − K N p N2 p N2 = km Ag VL t
可以看出,影响真空脱氮速度的因素主要有以下几个方面 1) 精炼时间对氮含量的影响
2.2.3.1 熔渣脱氮热力学
1)氮在钢-渣、渣-气中的反应 氮在钢-渣、渣-气中的反应与氮在 渣中的存在形式有关。普遍认为氮是 以离子的形式存在于渣中(或者以自 由离子存在,或以复杂离子存在)。
当使用CaO-CaF2等无酸性氧化物渣系进 行脱氮时,渣金界面反应如下: [N]+3/2(O2-)=(N3-)+3/2[O] 而在气相和熔渣界面则有 1/2N2+3/2(O2-)=(N3-)+3/4O2 用石墨坩埚进行试验反应如下: 1/2N2+C+1/2(O2-)=(CN-)+1/4O2
CO气泡上浮引起脱N量为:
' dn N = 2dn N 2 = 2 PN 2 ⋅
dV RT
mol
CO气泡上浮引起氮含量下降为
dw[ N ] = M N ⋅ dn N dV M N ' = 2 PN 2 ⋅ ⋅ W RT W
= dw[ N ] ⋅ W ' 2 PN 2 ⋅ M N
dw[N ]
则: dV
由于Al、Nb、V、Ti等元素与氮的亲和力 强,形成氮化物和碳氮化物,所以在生产含 Al、Nb、V、Ti钢种时,空气中的氮和原辅 料中的氮均易进入钢液中。
1.4 钢液脱氮困难的原因
(1) 钢液中,氮与多数元素反应生成的氮 化物处于溶解状态,故无法通过沉淀法去 除; (2) 氮原子的半径比氢大,扩散系数比氢 小得多(小两个数量级),故真空去氮的效 果比去氢差得多; (3) 氧、硫等表面活性元素阻碍钢液脱 氮。
1.1自由状态的氮原子
在钢液中氮含量没有饱和的情况下,自由 状态的氮原子[N]在液态钢水中溶解度遵循 西华特定律 1/2N2=[N]
KN = aN PN 2 = [% N ] f N PN 2
kN [% N ] = fN
p N2
氮含量与氮分压的平方根成正比。实际分压与平衡分 压差值越大,氮的传质速度越大。
2.2 脱氮方式 2.2.1真空脱氮
当钢液采用真空处理时,真空度67Pa,1600ºC条 件下,钢液中氮的平衡值为10ppm。但实际生产中 难以达到这种水平,主要原因是由于脱氮与钢液 中的氧、硫等表面活性元素的含量有密切关系, 当钢液中氧、硫含量较高时,真空处理的脱氮能 力受到很大的限制。
成国光等人在40kg 真空感应炉上进行表面活性元 素(氧、硫) 影响钢液脱氮动力学的研究, 实验采用 真空碳脱氧工艺, 研究了在不同的硫含量条件下, 钢中脱氧和脱氮的相互关系。 (1) 当钢中硫含量较低时, 脱氮速率很快, 随着硫含量 的逐步增加, 脱氮速率相应降低. (2)钢中硫含量较低时, 脱氮速率快于脱氧速率; 当硫 含量较高时, 脱氧速率大于脱氮速率. (3) 真空碳脱氧过程中, 脱碳、脱氧速率与硫含量关 系不大.
图4 钢液中氮分压与氮的平衡压力及气 泡中氮与氩气比随熔池深度变化图
h, m
2.2.3 熔渣脱氮
熔渣脱氮的研究目前进展缓慢。因为熔渣脱氮只 有在炉气气氛控制得较好的条件下才有良好的效 果。 熔渣脱氮有两种方式:一种是在钢液中生成氮化 物夹杂,这些夹杂物上浮到渣中后被去除。但这 种方法受到多种因素的制约,生产上很难实现; 另一种方法是造某种渣,钢液中的氮扩散到渣- 钢界面,与渣中某种化合物反应转入渣相,从而 达到去除的目的。
例题: 试讨论电炉炼钢氧化期脱氮的动力学。试 分析
(1)电炉炼钢氧化期脱氮的机理; (2)脱[N]速率与脱[C]速率的关系式; (3)试计算在1600℃时。脱[C]速率为0.6%/h, PCO=0.1Mpa条件下,钢液中原始含[N]量为 8.0 × 10 %,经10分钟后,钢液中的[N]含量为多少?
1.2各元素对[N]溶解度的影响
eN
>0,表示元素j使氮的活度系数增加,从 而降低了氮的溶解度
j
C、Mn、Si、P、S、Ni、Al、Cu的存在可降低氮在钢中的溶 解度, [C]、[Al]元素影响最大,所以低碳钢氮溶解度较高 氮在纯铁中的溶解度为0.044%(1600℃时),在铁水中由于受到 含碳量的影响氮的溶解度约为0.01%(PN2=0.1Kpa、1600℃时)
钢液的脱氮
❀ 钢中氮的溶解度
炼钢时 0.045% 室温时 0.001~0.002% ❀ 钢中氮的危害 时效硬化 蓝脆 皮下气泡 降低轴承钢的疲劳寿命
时 效 硬 化 : 钢 中 氮 以 Fe4N 氮 化 物 形 式 析 出,氮化物析出速度很慢,氮含量高的钢 种,长时间放置,钢的强度、硬度随时间 的推移而增大,而塑韧性则有所下降。 蓝脆:钢中氮含量高时,在250-450℃温度 范围,其表面发蓝,钢的强度升高、冲击 韧性降低,称之为“蓝脆”。由C和N间隙原 子的形变时效引起。
(2)脱[N]速率与脱[C]速率的关系式: 设脱[C]速率为 dw[C ] ,则:
dw[C ] =
W , ρ M 分别为钢液重量及钢液密度
dn ⋅ M C dc ⋅ V ⋅ M C dC[ c ] ⋅ M C ⎫ = = ⎪ W W ρM ⎪ ⎪ dn ⋅ RT P ⋅ dV M C dV = ⇒ dw[C ] = ⋅ ⎬ P RT W ⎪ W ⋅ dC[C ] ⎪ dn = ⎪ ρM ⎭
则: (3)当
dw[ N ] dw[C ] 2 = 572 × w[ N ]% × dt dt
dw[C ] = 0.6% / h = 0.01% / min dt
时:
dw[ N ] 2 = −572 × w[ N ]% × 0.01% dt dw[ N ]% ⇒ ∫ = − ∫ 572 × 0.01%dt 2 100w[ N ]% 0 8.0×10 −3 ⇒ 1 1 − = 57.2 −3 w[ N ]% 8 × 10
当氮含量超过100ppm时,在铸铁和钢中会 产生气孔,在IN100高温合金中,当氮含量 超过15ppm时,就会造成大量显微缩孔。当 氮与Ti,V等生成脆性氮化物时,严重影响 钢的高温强度和高温塑性。 钢中氮含量控制理论及工艺十分重要。