常减压装置扩量改造水力学计算书
常减压装置减压塔扩能改造
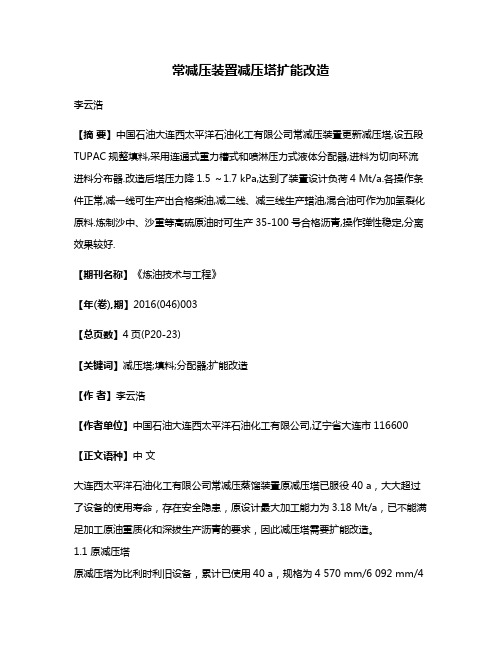
常减压装置减压塔扩能改造李云浩【摘要】中国石油大连西太平洋石油化工有限公司常减压装置更新减压塔,设五段TUPAC规整填料,采用连通式重力槽式和喷淋压力式液体分配器,进料为切向环流进料分布器.改造后塔压力降1.5 ~1.7 kPa,达到了装置设计负荷4 Mt/a.各操作条件正常,减一线可生产出合格柴油,减二线、减三线生产蜡油,混合油可作为加氢裂化原料.炼制沙中、沙重等高硫原油时可生产35-100号合格沥青,操作弹性稳定,分离效果较好.【期刊名称】《炼油技术与工程》【年(卷),期】2016(046)003【总页数】4页(P20-23)【关键词】减压塔;填料;分配器;扩能改造【作者】李云浩【作者单位】中国石油大连西太平洋石油化工有限公司,辽宁省大连市116600【正文语种】中文大连西太平洋石油化工有限公司常减压蒸馏装置原减压塔已服役40 a,大大超过了设备的使用寿命,存在安全隐患,原设计最大加工能力为3.18 Mt/a,已不能满足加工原油重质化和深拔生产沥青的要求,因此减压塔需要扩能改造。
1.1 原减压塔原减压塔为比利时利旧设备,累计已使用40 a,规格为4 570 mm/6 092 mm/4570 mm/2 000 mm×37 800 mm,内设四段ZUPAC型和TUPAC型规整填料、导板连通槽式液体分配器和双切向环流式进料分布器。
1.2 改造内容原减压塔进行更换,更新的减压塔规格为5 400 mm/7 800 mm/9 800 mm/5 000 mm ×48 000 mm(切),采用全填料减压塔技术,内设五段高效规整填料,减一中段为高2 m ZUPAC双向金属折峰式波纹规整填料、减一中内回流段高1.8 m规整填料、减二中段高1.4 m规整填料、减三中高1.4 m规整填料,洗涤段下部为高0.8 m垂直格栅填料,上部为高1.2 m规整填料;进料口设置进料分配器,使上升气体均匀分布,减少雾沫夹带。
玉门炼厂常减压装置减压系统深拔改造总结

2101 改造前存在问题由于炼化总厂加工方案改变和进厂原油重质化等原因,原常减压装置明显不能适应生产,开炼效果不理想,具体表现在三个方面。
1.1 总拔出率偏低尽管原设计加工原油为吐哈轻质原油,但随着近年进厂原油重质化和劣质化情况严重,原设计不能适应原料变化,总拔出率明显下降,仅约70%,远低于设计值70%。
1.2 换热终温较低鉴于常减压装置的加工量和掺炼原油性质与原设计时都有了较大的变化,但换热网络还是基本保持1997年装置新建时设计的结构。
原设计时的换热终温为288℃,现在实际换热终温最低为260℃左右,较设计时降低了近30℃左右。
由于换热终温较低,增加加热炉负荷,导致装置燃料消耗增加,装置能耗上升。
1.3 对下游装置运行产生不利影响玉门炼化总厂常减压装置加工原油持续重质化,导致常减压装置减压渣油产量逐步增加。
为平衡重油加工,催化裂化装置提高掺渣比例,使得原料性质进一步恶化,产品分布变差,液收下降。
另外,随着减压渣油收率越来越高,延迟焦化装置低附加值产品石油焦产量越来越大,对优化全厂产品结构、提高高效产品比例、增加经济效益带来不利影响。
2 改造内容为了解决常减压装置运行中存在的问题,经讨论研究后,决定对装置进行技术改造。
改造重点是减压系统,同时也对换热网络进行调整。
本次减压系统深拔改造项目工作主要包括以下内容:2.1 减压塔改造改造前,因需要生产润滑油原料,减压塔设计8段填料,设5个侧线抽出,3个中段回流取热。
为了适应当前只生产燃料油原料的生产方案,减压塔由8段填料改为5段填料,侧线抽出减少为3个。
2.2 减顶抽真空系统原减压塔设计中,塔顶残压45mmHg,塔顶为两级抽真空,塔顶油气先冷后抽。
本次改造中,为达到减压深拔目的,塔顶设计残压为15mmHg,设计三级抽空器,塔顶油气先抽后冷。
2.3 减压转油线原减压转油线为常规低压降转油线,本次减压深拔改造后炉出口气化率更高,转油线内介质超速,因此需对减压转油线进行改造。
常减压装置说明书

一、工艺流程1.1装置概况本装置为石油常减压蒸馏装置,原油经原油泵(P-1/1.2)送入装置,到装置内经两路换热器,换热至120℃,加入一定量的破乳剂和洗涤水,充分混合后进入电脱盐罐(V1)进行脱盐。
脱后原油经过两路换热器,换热至235℃进入初馏塔(T1)闪蒸。
闪蒸后的拔头原油经两路换热器,换热至310℃,分四股进入常压塔加热炉(F1)升至368℃进入常压塔(T2)。
常压塔塔底重组分经泵送到减压塔加热炉(F2)升温至395℃进入减压塔(T4)。
减压塔塔底渣油经两路换热器,送出装置。
1.2工艺原理1.2.1原油换热罐区原油(45℃)经原油泵P-1/1.2进入装置,分两路进行换热。
一路原油与E-1(常顶气)、E-2(常二线)、E-3(减一线)、E-4(减三线)、E-5(常一线)、E-6(减渣油)换热到120℃;二路原油与E-14(常顶气)、E-16(常二线)、E-17(减二线)换热到127.3℃。
两路原油混合换热后温度为120℃,注入冷凝水,经混合阀(PDIC-306)充分混合后,进入电脱盐罐(V-1)进行脱盐脱水。
脱后原油分成两路进行换热,一路脱后原油与E-7(常二线)、E-8(减二线)、E-9/1.2(减三线)、E-10/1~4(渣油)换热到239.8℃;二路脱后原油与E-11/1.2(减一中)、E-12/1.2(常二线)、E--13/1.2(减渣)换热到239.7℃。
两路脱后原油换热升温到230℃合为一路进入初馏塔(T-1)汽化段。
初馏塔塔顶油气经空冷气(KN-5/1~5)冷凝到77℃,进入初顶回流罐(V-2)。
油气经分离后,液相用初顶回流泵(P-4/1.2)打回初馏塔顶作回流,其余油气继续由初顶空冷器(KN-1/1~3)、初顶后冷器(N-1)冷却到40℃,进入初顶产品罐(V-3)。
初馏塔侧线油从初馏塔第10层用泵(P-6/1.2)抽出与常一中返塔线合并送到常压塔第33层塔盘上。
初馏塔底拔头油,经初底泵(P-2/1.2)抽出分两路换热。
【精品】辽河原油万吨常减压装置常压塔工艺计算

前言一、蒸馏过程的目的石油是极其复杂的混合物。
要从原油提炼出多种多样的燃料、润滑油和其他产品,基本的途径是:将原油分割为不同沸程的馏分,然后按照油品的使用要求,除去这些馏分中的非理想组分,或者是经由化学转化形成所需要的组成,进而获得合格的石油产品。
因此,炼油厂必须解决原油的分割和各种石油馏分在加工过程中的分离问题.蒸馏正是一种合适的手段,而且也是一种最经济、最容易实现的分离手段。
它能够将液体混合物按其所含组分的沸点或者蒸汽压的不同而分离为轻重不同的各种馏分。
几乎在所有的炼油厂中,第一个加工装置就是蒸馏装置.借助于蒸馏过程,可以按所制定的产品方案将原油分割成相应的直馏汽油、煤油、轻柴油或重柴油馏分及各种润滑油馏分;也可以按照不同的生产方案分割出一些二次加工所用的原料,进一步提高轻质油的产率或改善产品的质量。
二、装置生产方案的确定本设计所用原油为辽河油田欢喜岭地块原油。
辽河油田地质构造复杂,重质低凝环烷基原油储量较为丰富,这种重质低凝环烷基原油具有密度大、粘度高的特点,往往含有大量的胶质、沥青质,所以又称沥青基原油,可以生产各种优质沥青.通常还含有大量的环状烃和较多的芳烃,含蜡低,甚至不含蜡,是生产某些特种润滑油的良好原料,用它生产的低凝环烷基润滑油可以作为电气绝缘油、冷冻机油、橡胶工艺用油、润滑脂的基础油等.本设计为150万吨/年辽河原油加工方案,由于只对常压蒸馏部分进行工艺计算,故确定的方案如下:从初馏点至195℃可作为汽油的调合组分。
195℃~300℃可作为轻柴油的调合组分。
300℃~339℃可作为电气绝缘油的基础原料。
339℃~399℃可作为橡胶工艺用油的基础原料。
三、流程的确定及特点装置加工辽河低凝环烷基原油,生产润滑油基础原料和优质的道路沥青原料,流程的特点是燃料—润滑油型装置,工艺路线为原油进装置→换热→电脱盐→常压炉→常压塔→减压炉→减压塔。
装置未设初馏塔(闪蒸塔)是因为所加的原油属重质原油,轻组分较少的缘故。
常减压设计说明书计算部分.
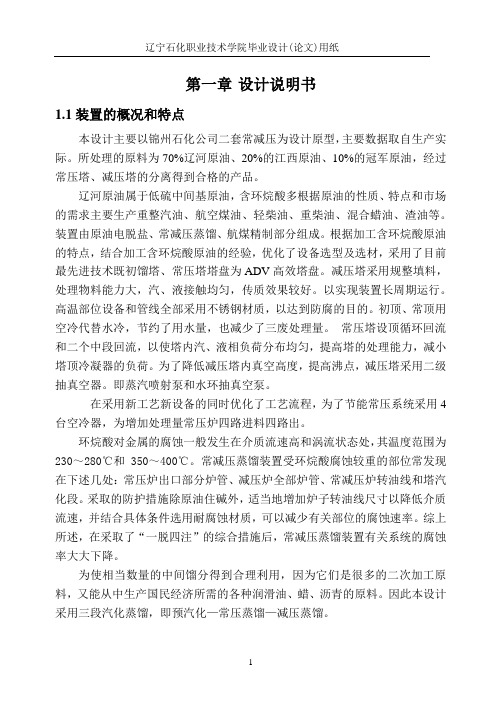
第一章设计说明书1.1装置的概况和特点本设计主要以锦州石化公司二套常减压为设计原型,主要数据取自生产实际。
所处理的原料为70%辽河原油、20%的江西原油、10%的冠军原油,经过常压塔、减压塔的分离得到合格的产品。
辽河原油属于低硫中间基原油,含环烷酸多根据原油的性质、特点和市场的需求主要生产重整汽油、航空煤油、轻柴油、重柴油、混合蜡油、渣油等。
装置由原油电脱盐、常减压蒸馏、航煤精制部分组成。
根据加工含环烷酸原油的特点,结合加工含环烷酸原油的经验,优化了设备选型及选材,采用了目前最先进技术既初馏塔、常压塔塔盘为ADV高效塔盘。
减压塔采用规整填料,处理物料能力大,汽、液接触均匀,传质效果较好。
以实现装置长周期运行。
高温部位设备和管线全部采用不锈钢材质,以达到防腐的目的。
初顶、常顶用空冷代替水冷,节约了用水量,也减少了三废处理量。
常压塔设顶循环回流和二个中段回流,以使塔内汽、液相负荷分布均匀,提高塔的处理能力,减小塔顶冷凝器的负荷。
为了降低减压塔内真空高度,提高沸点,减压塔采用二级抽真空器。
即蒸汽喷射泵和水环抽真空泵。
在采用新工艺新设备的同时优化了工艺流程,为了节能常压系统采用4台空冷器,为增加处理量常压炉四路进料四路出。
环烷酸对金属的腐蚀一般发生在介质流速高和涡流状态处,其温度范围为230~280℃和350~400℃。
常减压蒸馏装置受环烷酸腐蚀较重的部位常发现在下述几处:常压炉出口部分炉管、减压炉全部炉管、常减压炉转油线和塔汽化段。
采取的防护措施除原油住碱外,适当地增加炉子转油线尺寸以降低介质流速,并结合具体条件选用耐腐蚀材质,可以减少有关部位的腐蚀速率。
综上所述,在采取了“一脱四注”的综合措施后,常减压蒸馏装置有关系统的腐蚀率大大下降。
为使相当数量的中间馏分得到合理利用,因为它们是很多的二次加工原料,又能从中生产国民经济所需的各种润滑油、蜡、沥青的原料。
因此本设计采用三段汽化蒸馏,即预汽化—常压蒸馏—减压蒸馏。
常减压装置改扩建工程施工方案(DOC)

1.编制说明:1.1山东XXXX有限公司石油炼制装置改造扩建工程,是在原有减压装置基础上增加常压装置,主要增加的设备有常压塔、汽提塔,相关的冷换设备、空冷设备、机泵及管道、电气仪表和结构框架等。
1.2新增装置在原有装置的北侧,设置三层冷换框架,框架底部安装碱水罐和氨水罐,框架东侧布置泵区并和原有减压装置共用一部分框架、设备和公用工程。
1.3为了确保改造扩建工程施工的顺利进行,确保质量、进度、安全各项措施的落实,特编制本施工方案。
由于该改造扩建工程没有详细的施工图设计,根据建设方具体要求结合我方的施工经验,编制该施工方案。
2.编制依据:2.1建设方提供的施工简图和流程图。
2.2建设方提供的设备一览表。
3.主要工程实物量、工期要求及工程特点3.1主要实物工程量3.1.1塔设备2台、空冷2台、冷换设备12台、泵16台、另有瓦斯罐、氨水罐、碱性水罐等。
较大设备是减压塔30.9吨,其余设备重量均在7吨以下。
其中常压塔由发包方提供吊车和吊装机械,承包方安装就位。
3.1.2拆除检修原有装置的部分换热器和管线并重新安装。
3.2绝对工期90天。
3.3设备已基本到达安装现场,施工场地狭窄,设备安装难度较大,结构和管道预知应另行安排施工场地;原有装置仍在运行中,改扩建施工时原有装置必须全面停车比置换具备施工条件;施工场地西侧应由建设方采取防火隔离措施,应设置防火墙隔离燃料油罐和施工场地。
4.施工组织机构、指导思想和奋斗目标4.1组织机构4.2施工指导思想:保安全、高质量、高效率、工期短。
4.3奋斗目标:事故为零、质量优秀、工期提前。
5.施工部署和进度安排5.1提前进行钢结构和管道预制,将强预制深度,预制工期预计55天,安装工期35天6.主要施工措施6.1换热器检修措施6.1.1概述本次检修中,需检修换热器、空冷器(包括试压、抽芯、检修、回装、移位等),原有设备框架加固改造等,包括新加12台换热器,具有工程量大,时间紧、任务重的特点,因此施工中必须精心组织人力、物力,合理安排工期。
常减压蒸馏装置减压扩能改造

常减压蒸馏装置减压扩能改造大连西太平洋石油化工有限公司常减压蒸馏装置减压部分在原设计能力为318万吨/年的基础上,通过对装置的减压塔、换热流程及减顶抽真空系统的改造,使减压部分处理能力达到500万吨/年。
改造后装置运行效果良好,主要技术参数均达到或优于设计指标,并一次开车成功。
标签:常减压蒸馏装置;减压单元改造;处理量1 改造内容1.1 减压塔①采用全填料减压塔技术。
减压塔设置四个侧线。
为控制减一線产品质量,使其能够满足柴油的干点要求,设置减一线分馏段,这样减一线既可作为加氢裂化原料,亦可作为柴油加氢原料;减二线和减三线生产轻蜡油,作为加氢裂化原料;减四线生产重蜡油,作为渣油加氢原料;②设置分馏段。
在减一中和减二中之间设置一个分馏段控制减一线产品质量,使其满足柴油馏分的要求;③减压塔底注入适量蒸汽,采用微湿式带汽提操作,提高炉出口汽化量,提高产品质量;④设置净洗段。
良好的净洗段,是有效降低蜡油残碳、比色、重金属含量的重要措施;⑤进料口设置进料分配器,使上升气体均匀分布,减少雾沫夹带;⑥塔底设置急冷油控制塔底温度,防止塔底油大量裂化;⑦采用低速转油线、减压炉管逐级扩径、炉管吸收转油线热胀量技术。
1.2 抽真空系统由于减压处理能力增大,减压塔真空度提高,原减顶抽空系统不能满足减压深拔的设计需求,本次改造将原减顶抽空系统更换为蒸汽抽空+机械抽空组合工艺三级抽空系统,设两级蒸汽抽空器,第三级采用液环泵和蒸汽抽空器互为备用,抽空器后分别设冷凝器,节能效果较为理想。
增压器和一级抽空器按每级两组设计,一组按正常量的70%,另一组按正常量的40%;二级抽空器和液环真空泵按正常量的110%考虑;抽空器最后排出压力P=960mmHg(A);增压器后冷器出口温度不超过40℃,一、二级后冷器出口温度不超过45℃。
1.3 优化换热网络和采用强化传热设备换热网络部分减少换热台位4个,调整换热顺序4个台位。
有10个台位的换热器进行了面积调整,其中6个台位利旧现有换热器,3个台位换热器更换、1个台位在原有面积上新增。
常减压装置改扩建工程施工方案

常减压装置改扩建工程施工方案一、项目概况二、工程目标1.提高常减压装置的运行效率,减少能源消耗。
2.提高常减压装置的安全性,避免事故发生。
3.扩大常减压装置的产能,满足工业生产需求。
三、工程内容1.对现有常减压装置进行改造,包括提升设备的自动化程度,增加监控系统,改进设备结构。
2.对常减压装置进行扩建,增加容量,满足产能需求。
3.对现有设备进行维修和更换,确保设备的正常运行。
四、施工方案1.施工前准备1.1制定详细的施工计划,包括施工时间表、施工任务分配等。
1.2准备所需的施工材料和工具设备。
1.3做好安全措施,设置警示标志和隔离措施,确保施工安全。
2.改造工程2.1技术改造2.1.1提升设备的自动化程度,引入先进的控制系统。
2.1.2安装监控系统,实时监测设备运行状态。
2.1.3改进设备结构,提高运行效率和安全性。
2.2设备维修和更换2.2.1对现有设备进行全面维修,确保设备的正常运行。
2.2.2根据需要更换老化严重的设备部件,提高设备的稳定性和可靠性。
3.扩建工程3.1建筑扩建3.1.1根据设计方案进行基础工程施工,包括地基处理、基础混凝土浇筑等。
3.1.2按照设计要求进行钢结构搭建,确保建筑的稳定和安全。
3.2装备安装3.2.1根据设计图纸进行设备的安装,包括管道的布置和设备的组装。
3.2.2进行设备的调试和测试,确保设备的正常运行。
4.总结与验收4.1施工结束后,进行设备的运行测试和调试,确保设备的正常运行。
4.2进行施工质量验收,确保工程质量符合要求。
4.3进行工程结算和交接。
五、安全措施1.设置警示标志,明确施工现场的危险区域。
2.配备专业的施工人员,确保施工过程中的安全。
3.严格执行作业规程,加强对施工人员的安全教育和培训。
4.配备必要的安全设备,如安全帽、安全绳、救生器材等。
5.定期进行安全检查,及时发现和排除安全隐患。
六、工期和投资估算1.工期估算根据项目内容和工程量进行估算,包括改造工程和扩建工程的工期。
2014年常减压装置改造标定报告解读

中国化工集团油气公司昌邑石化分公司500万吨/年常减压蒸馏装置标定报告中国化工油气昌邑分公司生产技术部中国化工油气昌邑分公司运行一部2014年10月目录1. 概述 (1)1.1 装置概况 (1)1.2主要改造工作说明 (1)1.2.1初馏塔系统 (1)1.2.2常压塔系统 (2)1.2.3加热炉系统 (2)1.3本次改造核算 (2)1.4本装置主要组成 (2)2.工艺流程简述 (2)3 .装置开工运转与标定 (8)3.1 标定期间数据与分析 (8)3.2标定结果 (13)3.2.1 原油加工量 (13)3.2.2 轻收及总拔 (13)3.2.3 产品质量 (14)3.2.4 装置能耗 (15)3.2.5 塔系统 (15)3.2.6 换热网络 (16)3.2.7 机泵 (16)3.2.8 加热炉 (16)3.2.9装置防腐 (17)3.2.10 环境保护 (17)4.存在的问题及建议 (17)5.结论 (18)1. 概述1.1 装置概况山东昌邑石化有限公司500×104t/a 常减压蒸馏装置,系公司重交沥青装置能量系统优化改造项目核心装置,总投资7.6亿元,装置投资5.4亿元,占地15000m2。
由西安长庆科技工程有限责任公司设计,山东环海石化工程建设公司和山东宏扬石化工程公司等公司承建,于2008年5月开工建设,于2009年5月建成投产运行。
装置原设计加工混合重质含硫原料油,处理量为500万吨/年,设计年开工时间为8000小时,为燃料型装置。
但随着企业的持续性发展, 加工规模的继续扩大, 以及原油品种的日益多样化, 装置难以适应加工轻质原油的变化情况。
装置于2010年08月,在原装置的基础上,进行了第一次挖潜改造,充分利用已有设备和成熟的工艺,最大限度地减少改造工程量及投资,使其轻油加工能力提升至450万吨/年,尽可能降低生产成本,确保装置安全运行。
改造后的装置增加了初馏塔系统,旧闪蒸塔T1001改造成初馏塔,装填8.8m高的规整填料及气液分布器等塔内件;增加一台初馏塔回流罐V1026;新增初顶回流泵P1032AB 二台,初侧泵P1033AB二台;新增初顶油气后冷却器E1033一台。
压力式液体分布技术在350万t常减压装置的应用

压力式液体分布技术在350万t常减压装置的应用郝健勇【摘要】中石化沧州分公司常减压装置减压塔塔径较小,未设置洗涤段,不能满足350万 t/a 加工负荷下的产品质量要求,采用 LPEC 研发的新型压力式液体分布技术,在不增加塔高的情况下,增加洗涤段,使侧线产品残炭和重金属含量大幅降低,显著改善产品质量同时降低全塔压降,使减压渣油得以进一步深拔,处理能力也得到部分提高。
%Characteristics of atmospheric and vacuum distillation unit of Sinopec Cangzhou Company include relative short tower diameter of vacuum tower and without washing zone, it cannot meet the requirement to produce qualified products under 3.5 Mt/a processing load. Applying the new pressure liquid distribution technology developed by LPEC, and adding washing zones in the vacuum tower, sharply reduced carbon residue and heavy metal content in side-draw products, the quality of the product was significantly improved, and the pressure drop of the vacuum tower was reduced, vacuum residue was cut more deeply, the processing capacity was increased partially.【期刊名称】《当代化工》【年(卷),期】2015(000)005【总页数】4页(P1172-1175)【关键词】常减压蒸馏;压力式液体分布;加工负荷;产品质量【作者】郝健勇【作者单位】中石化沧州分公司,河北沧州 061000【正文语种】中文【中图分类】TE624.2中国石油化工股份公司沧州分公司常减压装置减压侧线蜡油现全部送去催化裂化作原料,因设计时没有设置洗涤段,同时减压塔塔径过小,中间部分塔径为5 m,造成汽、液相负荷过大,最下侧线减三线雾沫夹带严重。
常减压装置改扩建工程施工技术探讨

2019年10月员都能够迅速到达施工作业现场,以便工程施工可以有序进行。
当工程施工项目合同签订完成以后,施工方应该要安排专业的技术人员,认真仔细的对考察施工现场,科学的对施工计划进行制定,与当地的居民进行沟通和交流,从而有效提升施工进度管理以及控制水平。
3.3加大对施工进度管理以及控制的力度在实际的施工进度管理以及控制工作中,其进度计划涵盖的内容非常多,涉及的范围也比较广泛。
所以,编制可性较高的施工进度计划相对困难。
故此,为了能够最大程度降低施工期间管理问题的出现几率,一定要对施工计划进行科学编制,有效实施[5]。
同时,在实际的石油土建工程施工管理工作进行阶段,为了可以在规定的时间内完成施工工作,管理人员还需要对施工进度进行严格把控,强化对施工作业的监督力度,以便工程项目建设的顺利性。
针对施工阶段存在的各类影响因素,应该综合分析,合理考量,有效处理。
此外,管理人员可以合理对劳动组织进行改善,加大施工资源的投入力度,有效且科学的对施工次数进行更改,提升管理效果。
3.4做好信息管理以及调查工作在具体的石油土建工程进行阶段,应该对工程现场施工条件进行时刻关注,包括地理环境以及社会环境等。
比如在施工阶段,政府部门应该对施工工程进行严格要求,明确施工现场的交通运输条件等。
同时,在对施工进度进行规划之前,应该认真调查,获取施工现场的第一手信息,并将其合理的编制到计划中,确保可以为施工工作的进行提供更加精准的信息。
此外,还应该对已经完成的施工进度资料进行收集,仔细的对资料进行整理,有效的分析和研究,对施工进度管理以及控制的约束条件进行明确,进而从根本上提升石油土建工程施工质量。
4结语综合而言,针对石油工程项目来说,施工进度管理与控制是一个系统且复杂的工程,涉及到的内容以及方面也相对较多。
所以,在施工阶段,如果不能给予这一工作一定的关注,强化管理,那么不仅会出现施工问题,还会影响施工工作的顺利开展,对石油工程的未来发展非常不利。
常减压蒸馏装置常压塔工艺设计

化工专业课程设计常减压蒸馏装置常压塔工艺设计学校名称:广东石油化工学院专业名称:化学工程与工艺班别:姓名:学号:指导教师:完成时间:2012年02月01日至2012年10月日广东石油化工学院课程设计说明书设计名称:化工专业课程设计题目:530万吨/年原油常减压蒸馏装置设计常压分馏塔工艺设计学生:学号:班别:专业:化学工程与工艺指导教师:日期:2012 年02 月20 日广东石油化工学院化学工程与工艺专业设计任务书2012 年9 月30 日批准系主任谢颖发给学生1.设计题目: 原油常减压蒸馏装置工艺设计2. 学生完成全部设计之期限: 2013 年10 月20 日3. 设计之原始数据: (另给)4. 计算及说明部分内容: (设计应包括的项目)一、总论1.概述;2.文献综述;3.设计任务依据;4.主要原材料;5.其他二、工艺流程设计1. 原料油性质及产品性质;2. 生产方案;3.工艺流程;4. 蒸馏塔类型、塔器结构;5.环保措施三、常压蒸馏塔工艺计算1. 工艺参数计算;2. 物料平衡计算;3.操作条件的确定;4. 蒸馏塔各点温度核算;5. 蒸馏塔汽液负荷计算四、常压蒸馏塔尺寸计算1. 塔径计算;2. 塔高计算五、常压蒸馏塔水力学计算六、车间布置设计1. 车间平面布置方案;2. 车间平面布置图;3. 常压蒸馏塔装配图七、参考资料5. 绘图部分内容: (明确说明必绘之图)(1) 原油常减压蒸馏装置工艺流程图(2) 车间平面布置图(3) 常压蒸馏塔装配图插图: 主要塔器图, 蒸馏塔汽液负荷分布图, 计算草图等.6. 发出日期: 2013 年9 月30 日设计指导教师:完成任务日期: 2013 年10 月日学生签名:石油化工生产技术课程设计原油常减压蒸馏装置工艺设计基础数据1、原油的一般性质大庆原油,204d= 0.8587;特性因数K=12.32、原油实沸点蒸馏数据表1 大庆原油实沸点蒸馏及窄馏分性质数据馏分号沸点范围/℃占原油(质)/% 密度(20℃)/g·cm-3运动粘度/ mm2·s-1凝点/℃闪点(开)/℃折射率每馏分累计20℃50℃100℃20Dn70Dn1 初~112 2.98 2.98 0.7108 ————— 1.3995 —2 112~156 3.15 6.13 0.7461 0.89 0.64 ——— 1.4172 —3 156~195 3.22 9.35 0.7699 1.27 0.89 —-65 — 1.4350 —4 195~225 3.25 12.60 0.7958 2.03 1.26 —-41 78 1.4445 —5 225~257 3.40 16.00 0.8092 2.81 1.63 —-24 — 1.4502 —6 257~289 3.40 19.46 0.8161 4.14 2.26 —-9 125 1.4560 —7 289~313 3.44 22.90 0.8173 5.93 3.01 — 4 — 1.4565 —8 313~335 3.37 26.27 0.8264 8.33 3.84 1.73 13 157 1.4612 —9 335~355 3.45 29.72 0.8348 — 4.99 2.07 22 —— 1.445010 355~374 3.43 33.15 0.8363 — 6.24 2.61 29 184 — 1.445511 374~394 3.35 36.50 0.8396 —7.70 2.86 34 —— 1.447212 394~415 3.55 40.05 0.8479 —9.51 3.33 38 206 — 1.451513 415~435 3.39 43.44 0.8536 —13.3 4.22 43 —— 1.456014 435~456 3.88 47.32 0.8686 —21.9 5.86 45 238 — 1.464115 456~475 4.05 51.37 0.8732 ——7.05 48 —— 1.467516 475~500 4.52 55.89 0.8786 ——8.92 52 282 — 1.469717 500~525 4.15 60.04 0.8832 ——11.5 55 —— 1.4730 渣油>525 39.96 100.0 0.9375 ———41①———3、产品方案及产品性质4. 设计处理量: 250+学号×10万吨/年, 开工:8000小时/年。
常减压装置年产350万吨计算
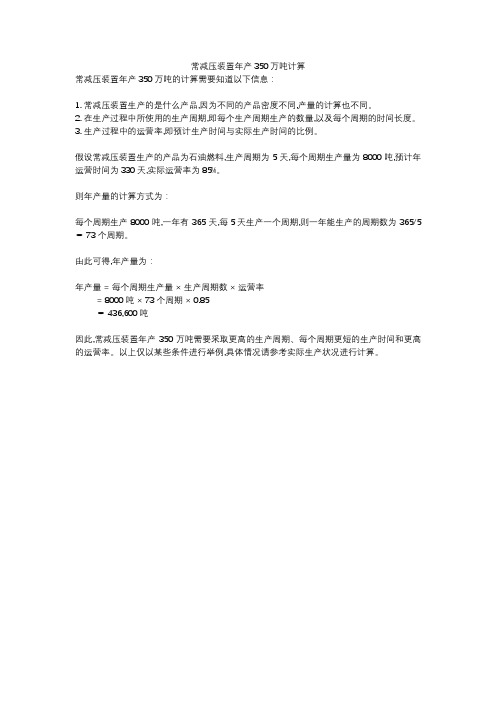
常减压装置年产350万吨计算
常减压装置年产350万吨的计算需要知道以下信息:
1. 常减压装置生产的是什么产品,因为不同的产品密度不同,产量的计算也不同。
2. 在生产过程中所使用的生产周期,即每个生产周期生产的数量,以及每个周期的时间长度。
3. 生产过程中的运营率,即预计生产时间与实际生产时间的比例。
假设常减压装置生产的产品为石油燃料,生产周期为5天,每个周期生产量为8000吨,预计年运营时间为330天,实际运营率为85%。
则年产量的计算方式为:
每个周期生产 8000 吨,一年有 365 天,每5天生产一个周期,则一年能生产的周期数为 365/5 ≈ 73 个周期。
由此可得,年产量为:
年产量 = 每个周期生产量× 生产周期数× 运营率
= 8000 吨× 73 个周期× 0.85
≈ 436,600 吨
因此,常减压装置年产 350 万吨需要采取更高的生产周期、每个周期更短的生产时间和更高的运营率。
以上仅以某些条件进行举例,具体情况请参考实际生产状况进行计算。
常减压设计说明与计算
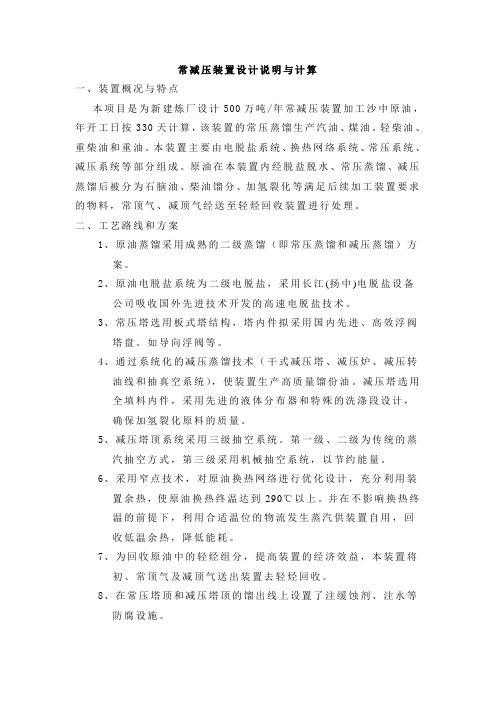
常减压装置设计说明与计算一、装置概况与特点本项目是为新建炼厂设计500万吨/年常减压装置加工沙中原油,年开工日按330天计算,该装置的常压蒸馏生产汽油、煤油。
轻柴油、重柴油和重油。
本装置主要由电脱盐系统、换热网络系统、常压系统、减压系统等部分组成。
原油在本装置内经脱盐脱水、常压蒸馏、减压蒸馏后被分为石脑油、柴油馏分、加氢裂化等满足后续加工装置要求的物料,常顶气、减顶气经送至轻烃回收装置进行处理。
二、工艺路线和方案1、原油蒸馏采用成熟的二级蒸馏(即常压蒸馏和减压蒸馏)方案。
2、原油电脱盐系统为二级电脱盐,采用长江(扬中)电脱盐设备公司吸收国外先进技术开发的高速电脱盐技术。
3、常压塔选用板式塔结构,塔内件拟采用国内先进、高效浮阀塔盘。
如导向浮阀等。
4、通过系统化的减压蒸馏技术(干式减压塔、减压炉、减压转油线和抽真空系统),使装置生产高质量馏份油。
减压塔选用全填料内件,采用先进的液体分布器和特殊的洗涤段设计,确保加氢裂化原料的质量。
5、减压塔顶系统采用三级抽空系统。
第一级、二级为传统的蒸汽抽空方式,第三级采用机械抽空系统,以节约能量。
6、采用窄点技术,对原油换热网络进行优化设计,充分利用装置余热,使原油换热终温达到290℃以上。
并在不影响换热终温的前提下,利用合适温位的物流发生蒸汽供装置自用,回收低温余热,降低能耗。
7、为回收原油中的轻烃组分,提高装置的经济效益,本装置将初、常顶气及减顶气送出装置去轻烃回收。
8、在常压塔顶和减压塔顶的馏出线上设置了注缓蚀剂、注水等防腐设施。
三、常压蒸馏塔的工艺计算1 原料性质2 产品实沸点蒸馏数据3 原油切割方案根据设计任务书及原油、产品性质数据,确定切割方案,见表3-2表3-2沙中原油常压切割方案产品实沸点沸程/℃实沸点切割温度/℃收率体积分数%质量分数%汽油~170169.822.4918.32煤油170~220218.37.77 6.98柴油220~350347.323.1522.24重油350~46.5952.464.产品性质见表以汽油为例列出详细的计算、换算过程其他产品仅将计算、换算结果列于上表(1)体积平均沸点t体t=(40.5+65.4+111.9+137.4+154.4)/5=101.92℃体(2)恩氏蒸馏90%~10%斜率90%~10%斜率=(154.4-40.5)/(90-10)=1.42℃/%(3)立方平均沸点由图查得校正值为-3.8℃T立=101.92-3.8=98.12℃(4)中平均沸点由图查得校正值为-9.5℃t中=101.92-9.5=92.42℃(5)比重指数API︒由汽油密度查表得:API︒=141.5/0.7926-131.5=47.03(6)特性因数K由图查得:K=1.216×(92.42+273)(1÷3)/0.7926=11.0 (7)相对分子质量: 查图的相对分子质量=90 (8)平衡汽化温度由图求得平衡汽化50%温度为89.9℃恩氏蒸馏/%·(体) 0 10 30 50 70 90 100 馏出温度/C ︒ 58 87 93 99 106 118 130恩氏蒸馏温差/C ︒ 29 6 6 7 12 12 因恩氏蒸馏10%~70%斜率=317.0107087106=--由图查得:平衡50%点-恩氏蒸馏50%点=C ︒-7平衡汽化50%点的温度/C ︒ C ︒=-92799平衡汽化温度/C ︒ 71 84 88 92 96 101 105 (9)临界温度由图查得:临界温度=295℃ (10)临界压力 由图查得:临界压力=2.26MPa(11)焦点压力由图查得:焦点压力=36.47MPa (12)焦点温度由图查得:焦点温度=82+295=377℃ 5 物料平衡由开工天数330天按8000小时计及各产品的收率,即可作出常压塔的物料平衡,如表3-3。
常减压装置塔内件改造技术方案

目录1. 技术方案 (1)2. 供货范围 (11)3. 设计资料交付 (12)4 技术特点 (13)5. 备品备件 (14)6. 检验和试验 (14)7. 技术服务 (14)1. 技术方案1.1 常压塔(T102)●该塔设计塔径为Φ1200mm。
该塔仅塔体利旧,更换衬里及全部塔内件。
●塔内共设置46层高效浮阀塔盘,从上至下依次为46#~1#,板间距为500mm,溢流形式为单溢流。
●46#塔盘上方设置回流挡板和顶循回流分布管,对顶回流及顶循环回流液相初始均匀分布。
●34#塔盘上方设置一中回流分布管,26#塔盘上方设置二中回流分布管,保证回流液相的均匀分布。
●43#、31#、23#塔盘受液盘分别设置顶循环抽出口、一中抽出口和二中抽出口。
●36#、28#、16#塔盘受液盘分别设置侧线抽出口,各抽出口下方两块塔盘处设置备用采出口(抽出口若和中段回流相混,会影响侧线产品质量,建议抽出口不下移)。
●39#、31#、19#塔盘上方分别设置侧线汽提返回口,30#塔盘上方设置闪蒸气入口挡板。
●5#塔盘下方设置低压降导流式气体分布器对进料均匀分布。
●1#塔盘下方设置汽提蒸汽分布管。
●该塔塔体利旧,拆除全部塔内件,包括与塔体焊接件。
●塔内壁内衬不锈钢,施工时需保证内衬光滑平整,由于原塔为碳钢结构,拆除与塔体焊接件时,需要对残留部分打磨平整,该工作量较大,请业主方考虑是否更换新塔。
●施工时建议打开全部人孔,拆除工作可以分几个工作面展开,每两个工作面之间保留1~2层塔盘,并加盖防火石棉布(浸湿)。
水力学计算结果:1.2 减压塔(T-104)●该塔设计塔径为Φ1800/1000mm。
该塔更换分布管,详见供货范围。
●塔内共设置4段规整填料,从上到下依次记为填料段BED1#~BED4#,填料段下方设置进料段与塔釜汽提段。
●塔内各段填料、主要塔内件排布见下表:2. 供货范围2.1 常压塔(T-102)材质仅为推荐材质,具体按业主要求。
360万吨原油常减压蒸馏装置工艺设计

*********课程设计说明书题目360万吨原油常减压蒸馏装置工艺设计学院:化工学院专业:化工专业班级:****学生:**** 指导教师****完成时间:20**年*月* 日至2***年* 月* 日目录第一章总论1.1概述 (3)1.1.1设计方案 (3)1.1.2 生产规模 (3)1.1.3 工艺技术路线 (4)1.1.4工艺技术特点 (4)1.2文献综述 (4)1.2.1常减压蒸馏技术现状 (4)1.3.设计任务依据 (5)1.4主要原材料 (5)1.5其他 (5)1.5.1交通运输 (5)1.5.2节能措施 (6)第二章工艺流程设计2.1原料油性质及产品性质 (7)2.1.1原料油性质 (7)2.1.2产品性质 (7)2.2. 工艺流程 (8)2.2.1工艺流程 (8)2.3 塔器结构 (9)2.4环保措施 (9)2.4.1污染源分析 (9)2.4.2废气处理 (10)2.4.3废水处理 (10)2.4.4噪声防护 (11)第三章工艺计算3.1 原料及产品的有关参数的计算 (13)3.2 工艺流程的确定根据与流程的叙述 (15)3.2.1 切割方案及性质 (15)3.2.2 物料平衡 (15)3.2.3 汽提蒸汽用量 (17)3.2.4 操作压力 (17)3.2.5 汽化段温度 (18)3.3蒸馏塔各点温度核算 (20)3.3.1塔底温度 (20)3.3.2塔顶及各侧线温度的假设与回流热分配 (20)3.3.3侧线及塔顶温度的校核 (21)3.4全塔汽、液负荷衡算 (23)第四章常压蒸馏塔尺寸计算4.1塔径的计算 (34)4.1.1塔径的初算 (34)4.1.2计算出Wmax后再计算适宜的气速Wa (34)4.1.3计算气相空间截面积 (35)4.1.4降液管内流体流速Vd (35)4.1.5计算降液管面积 (35)4.1.6塔横截面积Ft的计算 (35)4.1.7采用的塔径D及空塔气速W (35)4.2塔高的计算 (36)第五章水力学衡算5.1塔板布置,浮阀、溢流堰及降液管的计算 (37)5.2塔的水力学计算 (38)5.2.1塔板总压力降 (38)5.2.2雾沫夹带 (38)5.2.3泄漏 (39)5.2.4淹塔 (40)5.2.5降液管超负荷 (40)5.2.6适宜操作区和操作线 (40)5.2.7适宜操作区示意图 (42)第六章车间平面布置6.1 车间平面布置方案 (43)6.2 车间平面布置图 (43)6.2.1 CAD绘图(见附图) (43)6.2.2 工艺条件 (43)6.3 常压蒸馏塔装配图(见附图) (44)6.4 工艺流程图(见附图) (44)6.5 主要塔器图(见附图) (44)第七章结束语 (45)第八章参考文献 (45)第一章总论1.1概述石油是一种主要由碳氢化合物组成的复杂混合物。
- 1、下载文档前请自行甄别文档内容的完整性,平台不提供额外的编辑、内容补充、找答案等附加服务。
- 2、"仅部分预览"的文档,不可在线预览部分如存在完整性等问题,可反馈申请退款(可完整预览的文档不适用该条件!)。
- 3、如文档侵犯您的权益,请联系客服反馈,我们会尽快为您处理(人工客服工作时间:9:00-18:30)。
沥青装置技术改造项目
230万吨/年常减压装置
常压塔(C-1002)
常压汽提塔(C-1003)
塔内件改造利旧方案与水力学计算结果
1. 改造利旧方案
1.1 常压塔(C-1002)
利旧方案见下表:
1.2 常压汽提塔(C-1003)
利旧方案见下表:
注:最终参数以施工图为准。
2. 改造利旧部分的水力学计算结果
2.1 常压塔(C-1002)
厂名沥青装置改造日期2019年05月03日
塔名常压塔塔板号52
B5塔板流体力学考核结果
项目单位60%负荷100%负荷115%负荷空塔气速m/s 0.254 0.423 0.487 空塔动能因数(m/s)(kg/m3)0.5 0.465 0.776 0.892 阀孔气速m/s 2.885 4.809 5.530 阀孔动能因数(m/s)(kg/m3)0.5 5.289 8.815 10.137 液流强度m3/(m·h) 4.174 6.957 8.000 干板压降mm液柱32.546 41.783 44.739 湿板压降mm液柱37.849 49.771 53.645 塔板清液层高度mm 43.916 41.880 41.340 雾沫夹带量% 0.994 1.687 1.949 泄漏分率% 1.966 1.258 1.114 降液管液体停留时间sec 109.556 65.733 57.160 降液管液体流速m/s 0.005 0.009 0.010 降液管清液层高度mm 81.764 91.651 94.985 降液管清液层高度限制mm 325.000 325.000 325.000
负荷性能图 1--60%负荷图 2--100%负荷图 3--115%负荷图
厂名沥青装置改造日期2019年05月03日
塔名常压塔塔板号51
B5塔板流体力学考核结果
项目单位60%负荷100%负荷115%负荷空塔气速m/s 0.301 0.502 0.578 空塔动能因数(m/s)(kg/m3)0.5 0.565 0.941 1.082 阀孔气速m/s 3.348 5.580 6.417 阀孔动能因数(m/s)(kg/m3)0.5 6.272 10.454 12.022 液流强度m3/(m·h) 24.786 41.311 47.507 干板压降mm液柱35.370 45.409 48.622 湿板压降mm液柱63.221 83.381 89.944 塔板清液层高度mm 51.379 48.998 48.366 雾沫夹带量% 0.701 1.188 1.373 泄漏分率% 2.551 1.632 1.445 降液管液体停留时间sec 18.449 11.070 9.626 降液管液体流速m/s 0.033 0.054 0.062 降液管清液层高度mm 114.603 132.388 138.321 降液管清液层高度限制mm 325.000 325.000 325.000
负荷性能图 1--60%负荷图 2--100%负荷图 3--115%负荷图。