板材优化下料方案研究
板材下料优化方案
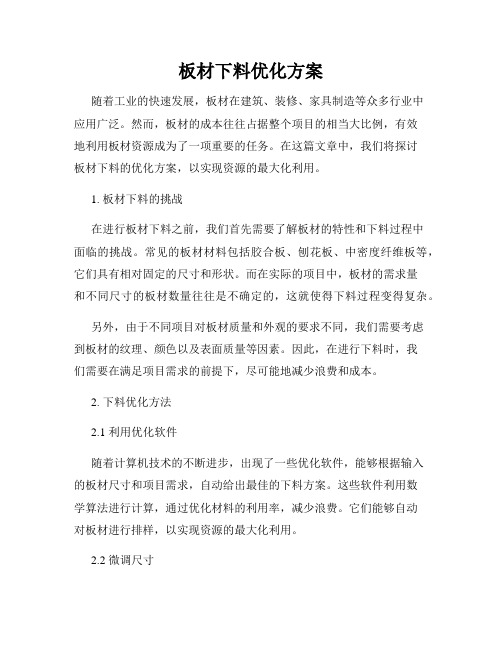
板材下料优化方案随着工业的快速发展,板材在建筑、装修、家具制造等众多行业中应用广泛。
然而,板材的成本往往占据整个项目的相当大比例,有效地利用板材资源成为了一项重要的任务。
在这篇文章中,我们将探讨板材下料的优化方案,以实现资源的最大化利用。
1. 板材下料的挑战在进行板材下料之前,我们首先需要了解板材的特性和下料过程中面临的挑战。
常见的板材材料包括胶合板、刨花板、中密度纤维板等,它们具有相对固定的尺寸和形状。
而在实际的项目中,板材的需求量和不同尺寸的板材数量往往是不确定的,这就使得下料过程变得复杂。
另外,由于不同项目对板材质量和外观的要求不同,我们需要考虑到板材的纹理、颜色以及表面质量等因素。
因此,在进行下料时,我们需要在满足项目需求的前提下,尽可能地减少浪费和成本。
2. 下料优化方法2.1 利用优化软件随着计算机技术的不断进步,出现了一些优化软件,能够根据输入的板材尺寸和项目需求,自动给出最佳的下料方案。
这些软件利用数学算法进行计算,通过优化材料的利用率,减少浪费。
它们能够自动对板材进行排样,以实现资源的最大化利用。
2.2 微调尺寸在进行下料时,我们可以根据板材的实际尺寸进行微调,以适应项目需求。
这种微调可以包括调整板材的宽度、长度以及厚度等方面。
通过合理的微调,我们可以尽量减少浪费,并满足项目对板材尺寸的要求。
2.3 考虑定制下料有些项目对板材的尺寸要求非常特殊,无法通过常规下料方案满足。
在这种情况下,我们可以考虑定制下料。
通过与板材供应商进行合作,我们可以获得符合项目需求的定制尺寸的板材,以提高资源的利用率。
3. 效果与案例分析对于以上提到的下料优化方法,我们可以通过实际案例来进行分析。
以某家具生产企业为例,他们利用优化软件进行下料,将浪费降低了20%以上。
同时,他们采用微调尺寸和定制下料相结合的方式,将板材利用率提高到了90%以上,大大降低了生产成本。
4. 结论综上所述,板材下料的优化方案是实现资源最大化利用的关键。
基于粒子群与模拟退火算法的板材优化下料

B O Q-i— a JA G J g qn IS N h - i LA G Y n cu A ij b o. N i — ig,O G C u y1 I N a ~ h n n I n ,
1 蒙古 民族 大学 数 学与计算机科学学院 , 内 内蒙古 通辽 0 84 203
2吉林大 学 计算机科 学与技术 学院 , . 长春 10 1 302
Ke o d :P rc w r pi zt n P 0)a oi m;i 1t n el g S y w r s atl S am 0 t a o ( S ie mi i 1 rh Smua d A n a n (A)印p0ce ;ut g s c rbe g t e i rah sc tn t k polm i o
1 引言
二维板材 下料问题可 以描 述为如何把事先 确定大 小的矩 形小块放置在大 的有 限的矩形板材上 。 或者说如何从大的矩形 板材 上切割出符 合要求 的小 的矩形块 。 非截断切割是不必从矩 形 的一条边直线切割到相对的边 。 板材 下料 问题 的 目标是最小 化 没有使 用的面积 。由于节省原材料和避免工业损失 的需要 , 下料问题 已经成为玻璃 、 钢铁 、 木材 、 张和纺织 等工 业生产过 纸 程 中一个 非常 重要 的研究课题 。这个 问题属于混合优化 问题 , 因此需要在所有可能解 中找到一个最优解 , 该解 使得有一系列 约束的 目标 函数达到最优或准最优 。
一种可变规格板材下料的优化方法

和 板 材 利 用 率 相 关 ,卵 越 大 利 用 率 越 高 ,所 用 板
材 相对越 少 ,材料 成本 相对 越低 。
2 优 化方法
可 变 规 格 板 材 下 料 一 般 流 程 如 图 1所 示 ,下
料 优化 需 要 确 定 使 用 何 种 板 材 、每 种 板 材 的 使 用
由于 该 类 组 合 优 化 问 题 属 于 NP 难 问题 ,不 一
存 在 多项 式 时 间 的算 法 ,但 遗 传 算 法 在 求 解 这 类
问题 上 效 果 突 出 。鉴 于 此 ,本 文 针 对 可 变 规 格板 材 下料 问题 ,以下 料方 案 对应 的 成本 最优 为 目标 ,
化 箱 子 的 序列 选 择 也 没 有协 调优 化 箱 子 之 间的 装 箱效果 。
率和 板 材 使 用 数 量 。本 文 以板 材 成本 统 一 考 虑 板 材 利 用 率 和 使 用数 量 。为 增 强 对板 材 使 用 数 量 的 控 制 ,引 进 板材 加 工 过 程 的 中 间成 本 。 中 间成 本
调 整 后 剩余 零 件 重 新 排 样 ,尺 个 零 件 加 入后 续 零 件序 列并 在后 续板 材上重 新排 样 。 如 果 调 整 效 果 不 优 , 以 当前 调 整 结 果 为 基 础 进 一 步 调 整存 在 更 优 的可 能 性 ,可 以按 概 率 接 收
21 板 材 序列优 化 _
搜 索 合 适 零 件 对 可 能 存 在 的 孔 洞 空 域 加 以填 充 。 排 样 受 零 件 面 积 的 影 响 ,排 样 后 期 随 小 型零 件 的
减 少 ,孔 洞 空域 逐 步 增 加 。一 张 板 材 完全 排 满 后 再 排 放 下 一 张 会使 后续 板 材 利 用 率 逐 渐 降 低 。如 果 在 当前 限 制 某 些后 续 搜 索零 件 的 插 入 ,后 续 的 排样 效果 可 以趋于 更优 。
板材下料优化方案

板材下料优化方案在木材加工行业中,如何最大程度地提高板材利用率和降低浪费是一个非常重要的问题。
传统的板材下料方式往往存在很大的浪费,而采用优化的板材下料方案可以有效地减少浪费,并提高生产效率。
本文将介绍一种常用的板材下料优化方案,通过优化下料方案来实现降低浪费,提高板材利用率。
一、了解板材规格和尺寸在制定下料优化方案之前,我们首先需要详细了解所使用的板材的规格和尺寸。
包括板材种类、厚度、长度、宽度等。
只有了解了板材的规格和尺寸,才能更好地制定下料方案,减少浪费。
二、利用计算软件进行优化可以借助计算机软件来进行板材下料的优化计算。
通过输入板材规格和需要裁剪的零件尺寸,计算软件可以自动生成最优的下料方案。
这些软件使用了高效的算法,可以快速且精准地进行优化计算。
例如,常用的下料软件有OptiCut、CutList Plus等。
三、合理设计零件尺寸在进行板材下料时,合理设计零件的尺寸也是非常重要的。
尽量避免设计过大或过小的零件,这样既可以减少浪费,又可以提高板材利用率。
同时,还可以考虑设计一些通用型的零件,以减少特定尺寸零件的数量,进一步降低浪费。
四、考虑边缘利用率和余料利用在进行板材下料时,除了面积利用率外,还要考虑板材的边缘利用率和余料利用。
通过合理规划下料方案,将板材边缘利用到最大化,并且合理利用余料,可以有效地减少浪费,提高板材利用率。
五、避免过多的切割在进行板材下料时,可以尽量避免过多的切割。
过多的切割不仅会增加加工的难度,还会增加浪费的可能性。
因此,在制定下料方案时,要避免过多的切割,尽量保持零件的形状和数量的简单性。
六、考虑批量生产的需求在制定板材下料方案时,还要考虑到批量生产的需求。
如果需要批量生产同样的零件,可以通过合理的下料方案来提高生产效率和板材利用率。
例如,可以将相同尺寸的零件集中进行下料切割,避免浪费和重复工作,提高生产效率。
七、严格控制切割误差和损耗在进行板材下料过程中,切割误差和材料损耗是无法完全避免的。
基于SigmaNest的板材下料问题研究
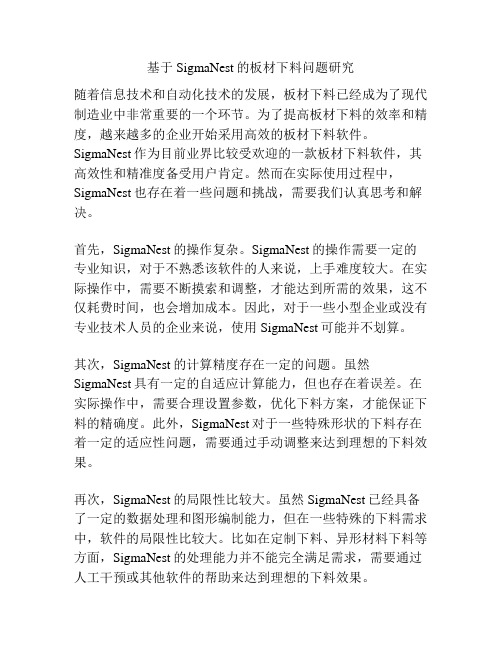
基于SigmaNest的板材下料问题研究随着信息技术和自动化技术的发展,板材下料已经成为了现代制造业中非常重要的一个环节。
为了提高板材下料的效率和精度,越来越多的企业开始采用高效的板材下料软件。
SigmaNest作为目前业界比较受欢迎的一款板材下料软件,其高效性和精准度备受用户肯定。
然而在实际使用过程中,SigmaNest也存在着一些问题和挑战,需要我们认真思考和解决。
首先,SigmaNest的操作复杂。
SigmaNest的操作需要一定的专业知识,对于不熟悉该软件的人来说,上手难度较大。
在实际操作中,需要不断摸索和调整,才能达到所需的效果,这不仅耗费时间,也会增加成本。
因此,对于一些小型企业或没有专业技术人员的企业来说,使用SigmaNest可能并不划算。
其次,SigmaNest的计算精度存在一定的问题。
虽然SigmaNest具有一定的自适应计算能力,但也存在着误差。
在实际操作中,需要合理设置参数,优化下料方案,才能保证下料的精确度。
此外,SigmaNest对于一些特殊形状的下料存在着一定的适应性问题,需要通过手动调整来达到理想的下料效果。
再次,SigmaNest的局限性比较大。
虽然SigmaNest已经具备了一定的数据处理和图形编制能力,但在一些特殊的下料需求中,软件的局限性比较大。
比如在定制下料、异形材料下料等方面,SigmaNest的处理能力并不能完全满足需求,需要通过人工干预或其他软件的帮助来达到理想的下料效果。
最后,SigmaNest的软件维护和更新费用较高。
由于SigmaNest是一款知名的软件产品,其对于软件维护、更新等方面的费用比较高。
对于一些规模较小的企业来说,成本较高可能会是不小的负担。
综上所述,尽管SigmaNest在板材下料方面具备高效和精准的优势,但也存在着一些问题和挑战,需要企业在选择时仔细衡量。
对于需要大量板材下料的企业来说,SigmaNest是一款值得推荐的软件产品,但在使用过程中需要注意操作指导书内容,优化下料方案,加强对软件进行维护和更新以及信任SigmaNest所提供的下料数据,从而达到最佳的下料效果。
板类零件优化排样及余料利用

— 152 —
生产。所以对回收的余料必须进行分割裁剪:板材按有用部分的最大
内接矩形裁剪。然后分规格、牌号、品种存放。为保证所存放的余料规
所示。
图 1 排样功能实现流程图 3.板材余料的利用及回收管理办法 板类零件制造企业使用的原材料主要是板材,占到原材料总量的 80%以上。在板材使用过程中,往往会产生许多余料,随着生产的进行 这样的余料越来越多。由于没有余料回收再利用的管理机制,造成的 余料浪费严重影响了企业的经济效益。板材余料的无管理状态阻碍了 企业的进一步发展。目前,企业基本上把余料板材作为废料处理,而作 为废料处理的价格仅为进货价的 1/6 左右,如果能把余料科学管理、合 理利用,可以显著提高企业的经济效益。 有时工人在加工时出现了差错,造成了材料浪费,害怕承担责任, 就自行找一块余料板材,重新加工零件,余料的这种自发式应用,给企 业的产品质量带来了安全隐患。 板材余料的随意堆积给企业的生产带来了不便和安全隐患。余料 由于没有清楚的标识,从而无法进行及时的清理,导致堆放在生产区 域,占据大量操作空间,给生产带来很大的不便和安全隐患。 余料管理方面的空白给企业全面实施信息化管理带来了极大的困 难。由于余料管理没有包含在企业信息化控制之内,成为企业信息化 的盲点。企业信息化是将企业的生产过程、物料移动、事务处理、现金 流动、客户交互等业务过程数字化,通过各种信息系统网络加工生成新 的信息资源,提供给各层次的人们洞悉、观察各类业务中的一切信息, 以作出有利于生产要素组合优化的决策,使企业资源合理配置,以使企 业能适应瞬息万变的市场经济竞争环境,求得最大利益。而余料板材 的管理是企业物流的重要组成部分。 提高材料的利用率,降低生产成本,已引起企业的高度重视,板材 余料的回收与再利用应规范管理,以省时省料,充分发挥余料的作用。[3] 由于搁置在车间的生产余料大多数为规格、牌号、品种混乱,长短、 大小、几何形状各异,若不进行一次切割裁剪、规范整理就难以再用于
优化下料流程提高下料效率和材料利用率
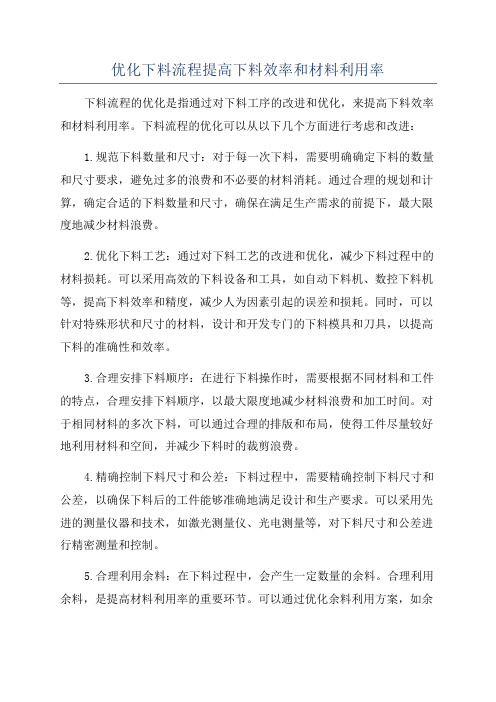
优化下料流程提高下料效率和材料利用率下料流程的优化是指通过对下料工序的改进和优化,来提高下料效率和材料利用率。
下料流程的优化可以从以下几个方面进行考虑和改进:1.规范下料数量和尺寸:对于每一次下料,需要明确确定下料的数量和尺寸要求,避免过多的浪费和不必要的材料消耗。
通过合理的规划和计算,确定合适的下料数量和尺寸,确保在满足生产需求的前提下,最大限度地减少材料浪费。
2.优化下料工艺:通过对下料工艺的改进和优化,减少下料过程中的材料损耗。
可以采用高效的下料设备和工具,如自动下料机、数控下料机等,提高下料效率和精度,减少人为因素引起的误差和损耗。
同时,可以针对特殊形状和尺寸的材料,设计和开发专门的下料模具和刀具,以提高下料的准确性和效率。
3.合理安排下料顺序:在进行下料操作时,需要根据不同材料和工件的特点,合理安排下料顺序,以最大限度地减少材料浪费和加工时间。
对于相同材料的多次下料,可以通过合理的排版和布局,使得工件尽量较好地利用材料和空间,并减少下料时的裁剪浪费。
4.精确控制下料尺寸和公差:下料过程中,需要精确控制下料尺寸和公差,以确保下料后的工件能够准确地满足设计和生产要求。
可以采用先进的测量仪器和技术,如激光测量仪、光电测量等,对下料尺寸和公差进行精密测量和控制。
5.合理利用余料:在下料过程中,会产生一定数量的余料。
合理利用余料,是提高材料利用率的重要环节。
可以通过优化余料利用方案,如余料利用方案的设计和规划,余料的再加工和利用等,有效地提高材料利用率,减少浪费。
6.加强质量管理:在下料生产过程中,加强质量管理是保证下料效率和材料利用率的关键。
通过建立和完善质量管理体系,加强对下料工艺和质量要求的控制和监督,及时发现和解决问题,以确保下料的质量和效率。
综上所述,通过规范下料数量和尺寸、优化下料工艺、合理安排下料顺序、精确控制下料尺寸和公差、合理利用余料和加强质量管理等措施,可以有效地提高下料效率和材料利用率,降低生产成本,提高企业竞争力。
板材下料问题
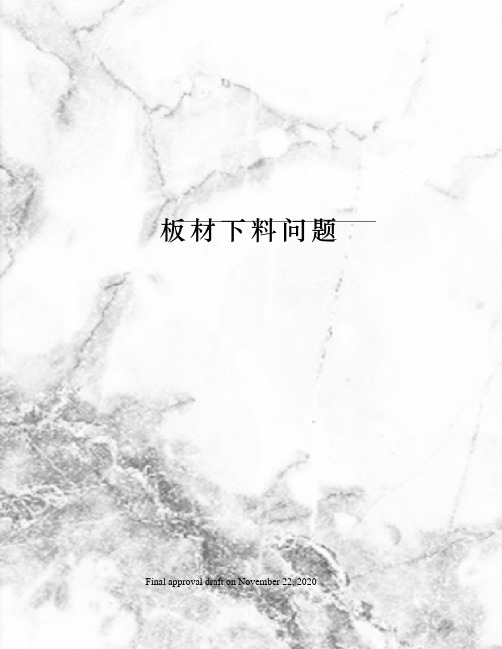
板材下料问题 Final approval draft on November 22, 2020板材玻璃的下料问题摘要“下料问题(cutting stock problem)”就是指在给定板材宽度和长度的情况下,如何将具有一定种类和数量的矩形件排放到板材上,使所需的板材数量最少的问题,该问题广泛存在于工业生产中。
本文运用优化理论,建立了矩形件优化排样数学模型,并提出了基于启发式算法的一刀切约束条件下二维板材下料算法。
关键词下料二维下料问题优化启发式算法矩形件排样一刀切一、问题的重述在大型建筑工程中,需要大量使用玻璃材料,如门窗等。
在作材料预算时,需要求出原材料的张数。
已知板材玻璃原材料和下料后的成品均为矩形。
由于玻璃材料的特点,切割玻璃时,刀具只能走直线,且中间不能拐弯或者停顿,即每切一刀均将玻璃板一分为二。
切割次序和方法的不同、各种规格搭配(即下料策略)不同,材料的消耗将不同。
工程实际需要解决如下问题,在给定一组材料规格尺寸后:(1)在原材料只有一种规格的情况下(例如长为2100cm,宽为1650㎝),给出最优下料策略,此时所需要材料张数最小。
(2)在原材料为两种规格的情况下(例如2100cm*1650cm和2000cm×1500cm),给出最优下料策略,使所需材料的张数最小,且利用率(实际使用总面积与原材料总面积之比)尽量高。
(3)下表是一些成品料及所需块数(长×宽×块数)分别以一种原材料2100cm×1650cm及两种原材料规格2100cm×1650cm,2000cm×1500cm为例,分别给出(1)和(2)的算法及数字结果,并给出两种情况下的利用率。
二、问题的分析本问题属于二维下料问题,该问题已被证明为是NP完全问题。
由于任何NP完全问题都不能用任何已知的多项式算法求解,所以我们建立一个排样的算法模型。
由题目要求该算法首先要满足生产工艺,即要满足“一刀切”,即从板材的一端,沿直线方向切割到另一端。
浅谈如何优化下料方法
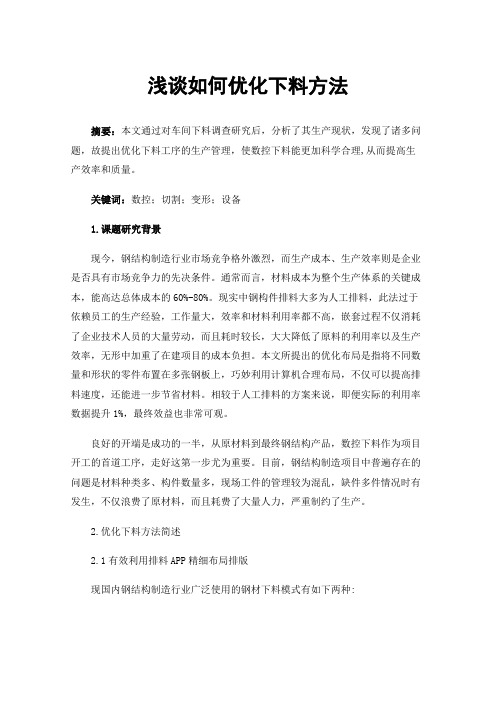
浅谈如何优化下料方法摘要:本文通过对车间下料调查研究后,分析了其生产现状,发现了诸多问题,故提出优化下料工序的生产管理,使数控下料能更加科学合理,从而提高生产效率和质量。
关键词:数控;切割;变形;设备1.课题研究背景现今,钢结构制造行业市场竞争格外激烈,而生产成本、生产效率则是企业是否具有市场竞争力的先决条件。
通常而言,材料成本为整个生产体系的关键成本,能高达总体成本的60%-80%。
现实中钢构件排料大多为人工排料,此法过于依赖员工的生产经验,工作量大,效率和材料利用率都不高,嵌套过程不仅消耗了企业技术人员的大量劳动,而且耗时较长,大大降低了原料的利用率以及生产效率,无形中加重了在建项目的成本负担。
本文所提出的优化布局是指将不同数量和形状的零件布置在多张钢板上,巧妙利用计算机合理布局,不仅可以提高排料速度,还能进一步节省材料。
相较于人工排料的方案来说,即便实际的利用率数据提升1%,最终效益也非常可观。
良好的开端是成功的一半,从原材料到最终钢结构产品,数控下料作为项目开工的首道工序,走好这第一步尤为重要。
目前,钢结构制造项目中普遍存在的问题是材料种类多、构件数量多,现场工件的管理较为混乱,缺件多件情况时有发生,不仅浪费了原材料,而且耗费了大量人力,严重制约了生产。
2.优化下料方法简述2.1有效利用排料APP精细布局排版现国内钢结构制造行业广泛使用的钢材下料模式有如下两种:(1)人工排料。
对特定项目而言,依据设计图开展细节的结构拆分,捕捉相应的下料信息,依托人工方法开展排料,再结合排料方案进行板材切割的处理。
若构件数量很少时,此法简单快捷。
但若某一类型的构件数量较多,外形较为复杂时,单靠员工凭经验完成下料工作,原材料利用率和工作效率都很低。
需求的材料以及工时,都很难精准把控,有碍材料的管理以及生产计划的调整。
(2)发展软件辅助排料。
将最优化理论应用于实践场景,配合计算机的辅助方案,进而取代人工排料。
关于板材优化下料方案研究
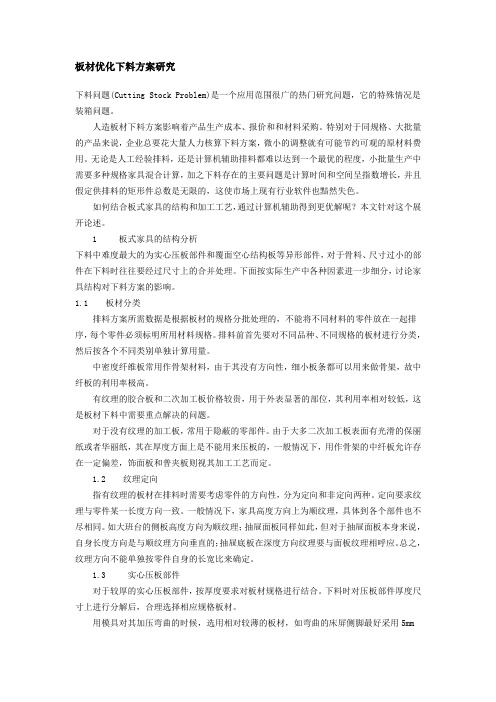
板材优化下料方案研究下料问题(Cutting Stock Problem)是一个应用范围很广的热门研究问题,它的特殊情况是装箱问题。
人造板材下料方案影响着产品生产成本、报价和和材料采购。
特别对于同规格、大批量的产品来说,企业总要花大量人力核算下料方案,微小的调整就有可能节约可观的原材料费用。
无论是人工经验排料,还是计算机辅助排料都难以达到一个最优的程度,小批量生产中需要多种规格家具混合计算,加之下料存在的主要问题是计算时间和空间呈指数增长,并且假定供排料的矩形件总数是无限的,这使市场上现有行业软件也黯然失色。
如何结合板式家具的结构和加工工艺,通过计算机辅助得到更优解呢?本文针对这个展开论述。
1 板式家具的结构分析下料中难度最大的为实心压板部件和覆面空心结构板等异形部件,对于骨料、尺寸过小的部件在下料时往往要经过尺寸上的合并处理。
下面按实际生产中各种因素进一步细分,讨论家具结构对下料方案的影响。
1.1 板材分类排料方案所需数据是根据板材的规格分批处理的,不能将不同材料的零件放在一起排序,每个零件必须标明所用材料规格。
排料前首先要对不同品种、不同规格的板材进行分类,然后按各个不同类别单独计算用量。
中密度纤维板常用作骨架材料,由于其没有方向性,细小板条都可以用来做骨架,故中纤板的利用率极高。
有纹理的胶合板和二次加工板价格较贵,用于外表显著的部位,其利用率相对较低,这是板材下料中需要重点解决的问题。
对于没有纹理的加工板,常用于隐蔽的零部件。
由于大多二次加工板表面有光滑的保丽纸或者华丽纸,其在厚度方面上是不能用来压板的,一般情况下,用作骨架的中纤板允许存在一定偏差,饰面板和普夹板则视其加工工艺而定。
1.2 纹理定向指有纹理的板材在排料时需要考虑零件的方向性,分为定向和非定向两种。
定向要求纹理与零件某一长度方向一致。
一般情况下,家具高度方向上为顺纹理,具体到各个部件也不尽相同。
如大班台的侧板高度方向为顺纹理;抽屉面板同样如此,但对于抽屉面板本身来说,自身长度方向是与顺纹理方向垂直的;抽屉底板在深度方向纹理要与面板纹理相呼应。
板材优化下料方案研究
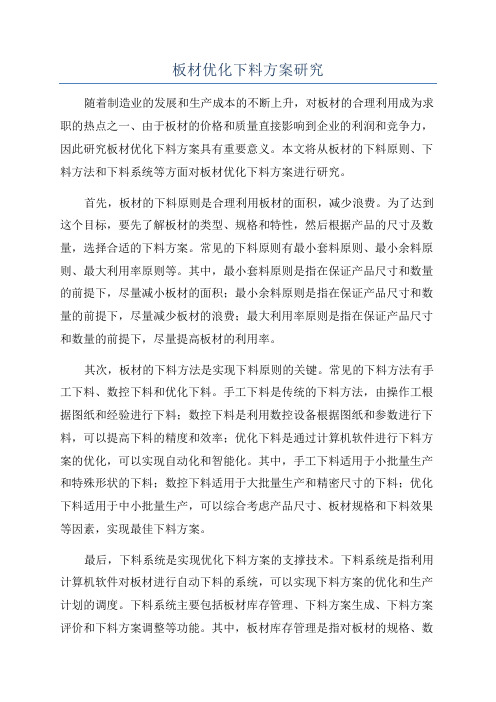
板材优化下料方案研究随着制造业的发展和生产成本的不断上升,对板材的合理利用成为求职的热点之一、由于板材的价格和质量直接影响到企业的利润和竞争力,因此研究板材优化下料方案具有重要意义。
本文将从板材的下料原则、下料方法和下料系统等方面对板材优化下料方案进行研究。
首先,板材的下料原则是合理利用板材的面积,减少浪费。
为了达到这个目标,要先了解板材的类型、规格和特性,然后根据产品的尺寸及数量,选择合适的下料方案。
常见的下料原则有最小套料原则、最小余料原则、最大利用率原则等。
其中,最小套料原则是指在保证产品尺寸和数量的前提下,尽量减小板材的面积;最小余料原则是指在保证产品尺寸和数量的前提下,尽量减少板材的浪费;最大利用率原则是指在保证产品尺寸和数量的前提下,尽量提高板材的利用率。
其次,板材的下料方法是实现下料原则的关键。
常见的下料方法有手工下料、数控下料和优化下料。
手工下料是传统的下料方法,由操作工根据图纸和经验进行下料;数控下料是利用数控设备根据图纸和参数进行下料,可以提高下料的精度和效率;优化下料是通过计算机软件进行下料方案的优化,可以实现自动化和智能化。
其中,手工下料适用于小批量生产和特殊形状的下料;数控下料适用于大批量生产和精密尺寸的下料;优化下料适用于中小批量生产,可以综合考虑产品尺寸、板材规格和下料效果等因素,实现最佳下料方案。
最后,下料系统是实现优化下料方案的支撑技术。
下料系统是指利用计算机软件对板材进行自动下料的系统,可以实现下料方案的优化和生产计划的调度。
下料系统主要包括板材库存管理、下料方案生成、下料方案评价和下料方案调整等功能。
其中,板材库存管理是指对板材的规格、数量和位置进行管理,通过对库存的分析和预测,实现下料方案的合理安排;下料方案生成是指根据产品的尺寸和数量,以及板材的规格和利用率等要求,生成符合要求的下料方案;下料方案评价是指对下料方案进行评价和分析,比较不同方案的优劣,提供合理的决策依据;下料方案调整是指根据实际生产情况,对下料方案进行调整和优化,及时地满足生产需求。
木材生产优化方案
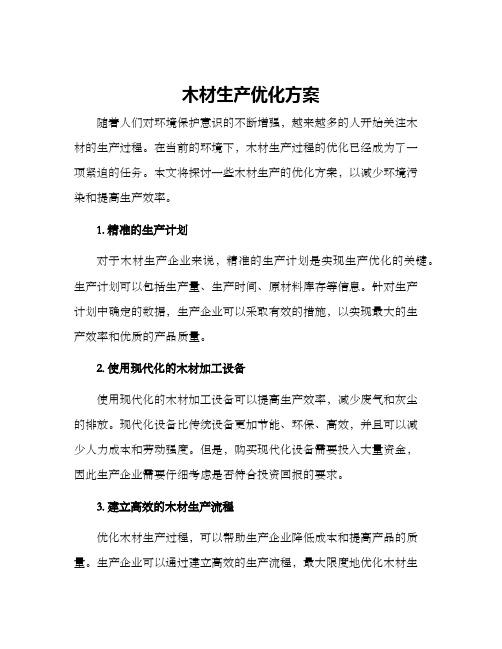
木材生产优化方案随着人们对环境保护意识的不断增强,越来越多的人开始关注木材的生产过程。
在当前的环境下,木材生产过程的优化已经成为了一项紧迫的任务。
本文将探讨一些木材生产的优化方案,以减少环境污染和提高生产效率。
1. 精准的生产计划对于木材生产企业来说,精准的生产计划是实现生产优化的关键。
生产计划可以包括生产量、生产时间、原材料库存等信息。
针对生产计划中确定的数据,生产企业可以采取有效的措施,以实现最大的生产效率和优质的产品质量。
2. 使用现代化的木材加工设备使用现代化的木材加工设备可以提高生产效率,减少废气和灰尘的排放。
现代化设备比传统设备更加节能、环保、高效,并且可以减少人力成本和劳动强度。
但是,购买现代化设备需要投入大量资金,因此生产企业需要仔细考虑是否符合投资回报的要求。
3. 建立高效的木材生产流程优化木材生产过程,可以帮助生产企业降低成本和提高产品的质量。
生产企业可以通过建立高效的生产流程,最大限度地优化木材生产。
高效生产流程可以减少无用的工作步骤,提高生产线的质量和效率。
4. 推广使用绿色材料绿色材料是一种更加环保、可持续的木材材料。
推广使用绿色材料可以减少砍伐原始森林,降低采伐和运输对环境的影响,同时,也可以提高产品的附加值。
5. 积极推动木材再利用和回收利用积极推动木材再利用和回收利用,可以减少对自然环境的损害,同时也可以提高生产企业的经济效益。
木材再利用和回收利用可以包括木材碎片、工业剩料、废木材、废旧木材等,这些都可以用来制造材料或用于其他生产行业。
结论木材生产过程的优化是一项长期而艰巨的任务,需要生产企业不断努力和改进。
此外,政府也应该积极推动木材生产优化的政策,通过鼓励和激励生产企业来达到减少环境污染、提高生产效益和保护自然环境的目的。
通过这些优化方案的实施,相信未来的木材生产过程将更加环保、高效、能源节省和经济可持续。
建筑板材下料方案
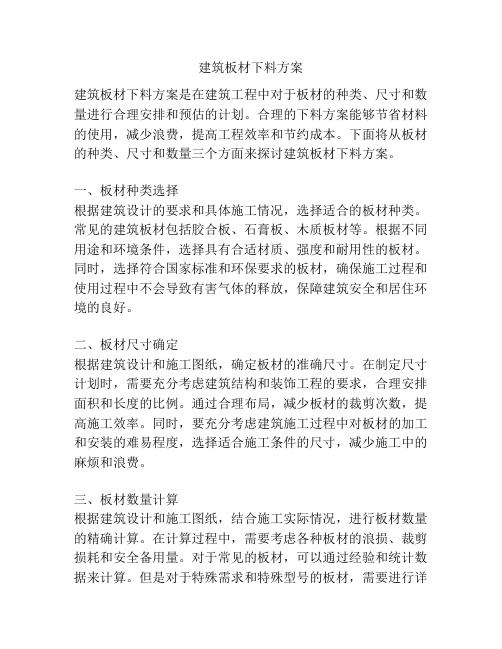
建筑板材下料方案建筑板材下料方案是在建筑工程中对于板材的种类、尺寸和数量进行合理安排和预估的计划。
合理的下料方案能够节省材料的使用,减少浪费,提高工程效率和节约成本。
下面将从板材的种类、尺寸和数量三个方面来探讨建筑板材下料方案。
一、板材种类选择根据建筑设计的要求和具体施工情况,选择适合的板材种类。
常见的建筑板材包括胶合板、石膏板、木质板材等。
根据不同用途和环境条件,选择具有合适材质、强度和耐用性的板材。
同时,选择符合国家标准和环保要求的板材,确保施工过程和使用过程中不会导致有害气体的释放,保障建筑安全和居住环境的良好。
二、板材尺寸确定根据建筑设计和施工图纸,确定板材的准确尺寸。
在制定尺寸计划时,需要充分考虑建筑结构和装饰工程的要求,合理安排面积和长度的比例。
通过合理布局,减少板材的裁剪次数,提高施工效率。
同时,要充分考虑建筑施工过程中对板材的加工和安装的难易程度,选择适合施工条件的尺寸,减少施工中的麻烦和浪费。
三、板材数量计算根据建筑设计和施工图纸,结合施工实际情况,进行板材数量的精确计算。
在计算过程中,需要考虑各种板材的浪损、裁剪损耗和安全备用量。
对于常见的板材,可以通过经验和统计数据来计算。
但是对于特殊需求和特殊型号的板材,需要进行详细的测量和统计,确保计算结果的准确性。
另外,要及时调整数量计算和采购计划,根据施工进度进行合理的调整和补充,避免材料的短缺或积压。
综上所述,建筑板材下料方案是建筑工程中一个重要的环节,通过合理选择板材种类、确定板材尺寸和精确计算板材数量,能够提高施工效率,减少浪费,节约成本。
因此,在建筑工程中,需要认真制定和执行合理的板材下料方案,确保建筑质量和工程进度的顺利进行。
板材下料算法

板材下料算法引言在制造业中,板材下料是一个重要的环节。
合理利用板材,减少浪费,不仅可以提高生产效率,降低成本,还可以减少对环境的影响。
因此,开发一种高效的板材下料算法是非常有必要的。
本文将就板材下料算法进行全面、详细、完整且深入地探讨。
传统的板材下料方法在传统的板材下料方法中,人工根据经验进行下料,这种方法的缺点非常明显:人工下料效率低下,容易出错且浪费材料。
由于人工下料的结果往往无法达到最佳利用率,因此需要一种自动化的下料算法来取代传统方法。
板材下料算法的意义与目标开发一种高效的板材下料算法,可以解决传统方法中存在的问题,提高下料效率,减少材料浪费,并确保产品质量。
其主要目标包括: 1. 最大限度地利用板材,减少浪费 2. 优化下料方案,提高下料效率 3. 确保下料后的板材尺寸满足要求板材下料算法的基本原理板材下料算法基于数学模型和优化算法,其基本原理如下: 1. 根据产品的尺寸要求和板材的规格,确定下料方案的约束条件 2. 将板材划分为若干个小块,每块的尺寸等于一个产品的尺寸 3. 使用优化算法搜索最优的下料方案,即使得浪费最小的方案 4. 对最优方案进行评估,判断是否满足规格要求 5. 若满足规格要求,则生成下料指令板材下料算法的常用优化算法在板材下料算法中,常用的优化算法有以下几种: 1. 贪心算法:从一个空白的板材开始,按照一定的策略依次放置产品,直到不能再放置为止。
该算法只考虑当前状态下的最佳选择,效率较高。
2. 回溯算法:在每一步都尝试所有可能的放置方式,并根据评估函数选择最优的放置方式。
由于需要尝试所有可能的情况,回溯算法效率较低,但能够找到最优解。
3. 遗传算法:将每个解视为一个个体,并通过基因交叉和变异操作来搜索最优解。
遗传算法适用于问题复杂、解空间巨大的情况。
板材下料算法的实现步骤1.输入产品的尺寸要求和板材的规格2.确定下料方案的约束条件,如最大浪费面积、最大下料时间等3.将板材划分为若干个小块,每块的尺寸等于一个产品的尺寸4.使用优化算法搜索最优的下料方案5.对最优方案进行评估,判断是否满足规格要求6.若满足规格要求,则生成下料指令板材下料算法的案例分析假设有一个产品A,尺寸为100mm×200mm,需要下料1000个。
钣金下料工艺的优化的思考
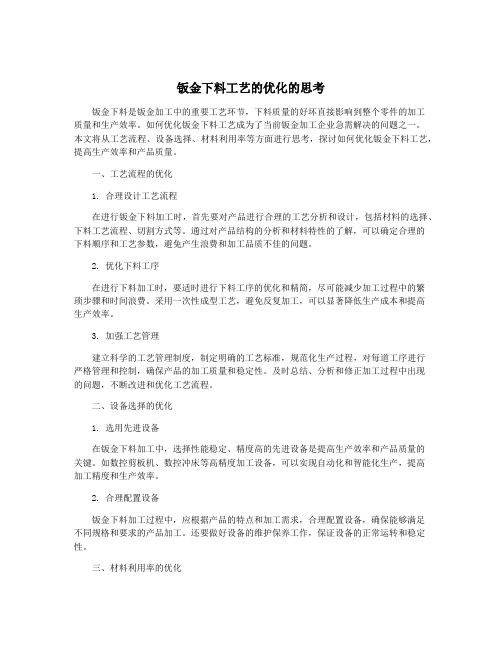
钣金下料工艺的优化的思考钣金下料是钣金加工中的重要工艺环节,下料质量的好坏直接影响到整个零件的加工质量和生产效率。
如何优化钣金下料工艺成为了当前钣金加工企业急需解决的问题之一。
本文将从工艺流程、设备选择、材料利用率等方面进行思考,探讨如何优化钣金下料工艺,提高生产效率和产品质量。
一、工艺流程的优化1. 合理设计工艺流程在进行钣金下料加工时,首先要对产品进行合理的工艺分析和设计,包括材料的选择、下料工艺流程、切割方式等。
通过对产品结构的分析和材料特性的了解,可以确定合理的下料顺序和工艺参数,避免产生浪费和加工品质不佳的问题。
2. 优化下料工序在进行下料加工时,要适时进行下料工序的优化和精简,尽可能减少加工过程中的繁琐步骤和时间浪费。
采用一次性成型工艺,避免反复加工,可以显著降低生产成本和提高生产效率。
3. 加强工艺管理建立科学的工艺管理制度,制定明确的工艺标准,规范化生产过程,对每道工序进行严格管理和控制,确保产品的加工质量和稳定性。
及时总结、分析和修正加工过程中出现的问题,不断改进和优化工艺流程。
二、设备选择的优化1. 选用先进设备在钣金下料加工中,选择性能稳定、精度高的先进设备是提高生产效率和产品质量的关键。
如数控剪板机、数控冲床等高精度加工设备,可以实现自动化和智能化生产,提高加工精度和生产效率。
2. 合理配置设备钣金下料加工过程中,应根据产品的特点和加工需求,合理配置设备,确保能够满足不同规格和要求的产品加工。
还要做好设备的维护保养工作,保证设备的正常运转和稳定性。
三、材料利用率的优化1. 合理采购材料钣金下料加工前,对材料进行合理的采购和管理是优化材料利用率的关键。
要根据产品的加工要求和规格,合理选择材料种类和规格,避免产生大量的浪费和材料报废。
2. 提高利用率在进行下料加工时,要充分利用原材料,尽可能减少废料和余料的产生。
通过合理的下料方案和工艺参数设置,最大限度地提高利用率,降低材料成本。
钣金下料工艺的优化的思考
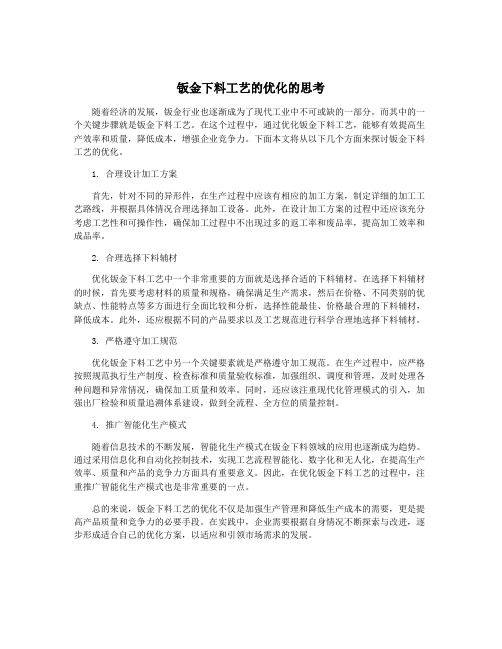
钣金下料工艺的优化的思考随着经济的发展,钣金行业也逐渐成为了现代工业中不可或缺的一部分。
而其中的一个关键步骤就是钣金下料工艺。
在这个过程中,通过优化钣金下料工艺,能够有效提高生产效率和质量,降低成本,增强企业竞争力。
下面本文将从以下几个方面来探讨钣金下料工艺的优化。
1. 合理设计加工方案首先,针对不同的异形件,在生产过程中应该有相应的加工方案,制定详细的加工工艺路线,并根据具体情况合理选择加工设备。
此外,在设计加工方案的过程中还应该充分考虑工艺性和可操作性,确保加工过程中不出现过多的返工率和废品率,提高加工效率和成品率。
2. 合理选择下料辅材优化钣金下料工艺中一个非常重要的方面就是选择合适的下料辅材。
在选择下料辅材的时候,首先要考虑材料的质量和规格,确保满足生产需求,然后在价格、不同类别的优缺点、性能特点等多方面进行全面比较和分析,选择性能最佳、价格最合理的下料辅材,降低成本。
此外,还应根据不同的产品要求以及工艺规范进行科学合理地选择下料辅材。
3. 严格遵守加工规范优化钣金下料工艺中另一个关键要素就是严格遵守加工规范。
在生产过程中,应严格按照规范执行生产制度、检查标准和质量验收标准,加强组织、调度和管理,及时处理各种问题和异常情况,确保加工质量和效率。
同时,还应该注重现代化管理模式的引入,加强出厂检验和质量追溯体系建设,做到全流程、全方位的质量控制。
4. 推广智能化生产模式随着信息技术的不断发展,智能化生产模式在钣金下料领域的应用也逐渐成为趋势。
通过采用信息化和自动化控制技术,实现工艺流程智能化、数字化和无人化,在提高生产效率、质量和产品的竞争力方面具有重要意义。
因此,在优化钣金下料工艺的过程中,注重推广智能化生产模式也是非常重要的一点。
总的来说,钣金下料工艺的优化不仅是加强生产管理和降低生产成本的需要,更是提高产品质量和竞争力的必要手段。
在实践中,企业需要根据自身情况不断探索与改进,逐步形成适合自己的优化方案,以适应和引领市场需求的发展。
优化板材开料办法
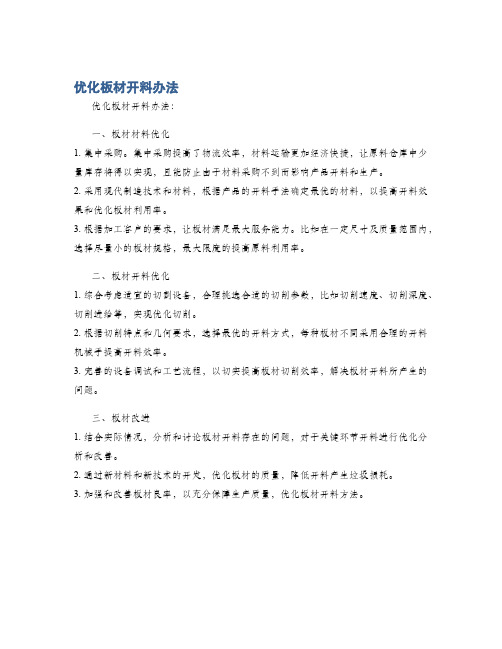
优化板材开料办法
优化板材开料办法:
一、板材材料优化
1. 集中采购。
集中采购提高了物流效率,材料运输更加经济快捷,让原料仓库中少量库存将得以实现,且能防止由于材料采购不到而影响产品开料和生产。
2. 采用现代制造技术和材料,根据产品的开料手法确定最优的材料,以提高开料效果和优化板材利用率。
3. 根据加工客户的要求,让板材满足最大服务能力。
比如在一定尺寸及质量范围内,选择尽量小的板材规格,最大限度的提高原料利用率。
二、板材开料优化
1. 综合考虑适宜的切割设备,合理挑选合适的切削参数,比如切削速度、切削深度、切削进给等,实现优化切削。
2. 根据切削特点和几何要求,选择最优的开料方式,每种板材不同采用合理的开料机械手提高开料效率。
3. 完善的设备调试和工艺流程,以切实提高板材切削效率,解决板材开料所产生的问题。
三、板材改进
1. 结合实际情况,分析和讨论板材开料存在的问题,对于关键环节开料进行优化分析和改善。
2. 通过新材料和新技术的开发,优化板材的质量,降低开料产生垃圾损耗。
3. 加强和改善板材良率,以充分保障生产质量,优化板材开料方法。
- 1、下载文档前请自行甄别文档内容的完整性,平台不提供额外的编辑、内容补充、找答案等附加服务。
- 2、"仅部分预览"的文档,不可在线预览部分如存在完整性等问题,可反馈申请退款(可完整预览的文档不适用该条件!)。
- 3、如文档侵犯您的权益,请联系客服反馈,我们会尽快为您处理(人工客服工作时间:9:00-18:30)。
板材优化下料方案研究
下料问题(Cutting Stock Problem)是一个应用范围很广的热门研究问题,它的特殊情况是装箱问题。
人造板材下料方案影响着产品生产成本、报价和和材料采购。
特别对于同规格、大批量的产品来说,企业总要花大量人力核算下料方案,微小的调整就有可能节约可观的原材料费用。
无论是人工经验排料,还是计算机辅助排料都难以达到一个最优的程度,小批量生产中需要多种规格家具混合计算,加之下料存在的主要问题是计算时间和空间呈指数增长,并且假定供排料的矩形件总数是无限的,这使市场上现有行业软件也黯然失色。
如何结合板式家具的结构和加工工艺,通过计算机辅助得到更优解呢?本文针对这个展开论述。
1.板式家具的结构分析
下料中难度最大的为实心压板部件和覆面空心结构板等异形部件,对于骨料、尺寸过小的部件在下料时往往要经过尺寸上的合并处理。
下面按实际生产中各种因素进一步细分,讨论家具结构对下料方案的影响。
1.1板材分类
排料方案所需数据是根据板材的规格分批处理的,不能将不同材料的零件放在一起排序,每个零件必须标明所用材料规格。
排料前首先要对不同品种、不同规格的板材进行分类,然后按各个不同类别单独计算用量。
中密度纤维板常用作骨架材料,由于其没有方向性,细小板条都可以用来做骨架,故中纤板的利用率极高。
有纹理的胶合板和二次加工板价格较贵,用于外表显著的部位,其利用率相对较低,这是板材下料中需要重点解决的问题。
对于没有纹理的加工板,常用于隐蔽的零部件。
由于大多二次加工板表面有光滑的保丽纸或者华丽纸,其在厚度方面上是不能用来压板的,一般情况下,用作骨架的中纤板允许存在一定偏差,饰面
板和普夹板则视其加工工艺而定。
1.2纹理定向
指有纹理的板材在排料时需要考虑零件的方向性,分为定向和非定向两种。
定向要求纹理与零件某一长度方向一致。
一般情况下,家具高度方向上为顺纹理,具体到各个部件也不尽相同。
如大班台的侧板高度方向为顺纹理;抽屉面板同样如此,但对于抽屉面板本身来说,自身长度方向是与顺纹理方向垂直的;抽屉底板在深度方向纹理要与面板纹理相呼应。
总之,纹理方向不能单独按零件自身的长宽比来确定。
1.3 实心压板部件
对于较厚的实心压板部件,按厚度要求对板材规格进行结合。
下料时对压板部件厚度尺寸上进行分解后,合理选择相应规格板材。
用模具对其加压弯曲的时候,选用相对较薄的板材,如弯曲的床屏侧脚最好采用5mm的中纤板来压板;若弯曲度较大,则芯部要采用狭长的板条;当然应该尽量减少胶合的层数,如对厚重的脚,25mm的中纤板是最佳选择。
1.4覆面空心结构板
表面常用加工板或胶合板,内部骨料用各种规格的中纤板。
对该结构板材的处理,中纤板的厚度选择则是一个相当复杂的过程,这也是下料软件的一个重要性能指标。
一方面骨料尺寸较小常常从余料中选择,另一方面其厚度尺寸可能利用本来宽度方向的尺寸。
1.5连开处理
连开处理常常用于下面两种情形:
1. 面积较小零件:这是因为较小的零件在较小的板材尺寸允许范围就可以产生太多的组合,若不处理则大幅降低开料速度。
2. 封边尺寸较小的方向:后序工艺要对其进行封边,若该尺寸较小,不处理则降低了封边效率。
这样,开料时可对一定数量组合的零件整体参与排料,包括锯路宽度和边工余量。
2 针对板式家具下料软件的开发思路
和常规软件一样,要有完善的功能体系,如下料清单生成、库存处理、局部调整、图纸打印、产品数据库等。
下面仅对其核心技术模块的开发进行讨论。
2.1 数据初始化
主要对其基本工艺参数进行确定,基本要点如下:
1. 项目分解
将各部件按组合方式和板材规格分解为单个零件,并生成净尺寸的清单,重新编号。
2. 板材选择
选用各零件所用板材种类、规格和余料情况。
排料时将按不同规格的板材分类优化。
3. 尺寸确定
结合各个零件的结构和加工工艺,确定其净尺寸、毛料尺寸。
4. 纹理定向
选择纹理是否需要定向。
若定向,是否允许一定比例或数量内的零件可以不定向。
5. 锯路宽度
精确到0.5mm,亦可据刀片寿命和板材类别略作调整。
6. 批量
上面分析仅仅是对单件而言,成本预算时批量将影响成本,此项单列可用于不同批量下的快速报价。
2.2数据库建立
能够兼容Excel,Access,DBF等格式的文档,并可以相互导入和导出。
对常用设计图纸的软件可以进行智能选择。
2.3算法设计
下料属于装箱问题的特殊情况,目前实际应用中常用的求解方法有:
1. 近似圆整法。
即不作整数规划,在得出实数最优解后就终止最优解搜索,然后进行近似取整,这种方法在下料数量大时还可以,但数量少时,误差较大。
2. 人工整数规划。
这种方法的优化效果比近似圆整好,但这种方法对人的知识要求增高,操作复杂,同时所得解并非是理想的最优解。
3. 采取时间判别终止法,即在整数规划允许到一定时间后仍不收敛,程序自动终止。
算法设计中,并非一味追求高利用率,还要考虑工艺上的现实性,这样才有实际意义。
例如,一般情况下,一块完整的板材允许有两到三块的零件参与排料,其锯路也要规整,过多的零件组合和繁琐锯路降低了开料的速度,生产中往往是不可行的,这也是目前市场上软件最为欠缺的。
2.4数据重组
一个下料任务中,可能包括多个家具产品,并且每个产品的数量不同。
好的开料软件可以方便快捷的对数据进行重组,不需要直接修改原数据。
这是一些CAD二次开发软件需要进一步突破的。
2.5辅助功能
在满足下料任务的前提下,为尽量提供生产效率,降低成本,有如下需求:
1. 基于标准零件库,自动生成下料清单,进行利用率和利用量的计算,并对相关信息进行计算。
2. 对应于自动生成下料清单,同时也应具有手工输入下料数据的功能。
以适应小批量临时性的加工任务。
3. 下料时充分利用现有余料,达到减少废料,节约成本的目的。
4. 根据排料结果,确定板材原材料的需求,由库房根据需求定制采购计划。
避免库存资金的占用。
5. 根据下料清单和单位加工工时定额,估算加工工时,制定详细的生产计划下发车间,严格控制生产周期,保证按合同期限交货。
6. 预备下料任务的安排。
生产较空闲时,安排常用标准板材零件的加工。
2.6拓展功能
主要是通过允许存在偏差进行合理优化。
对机械加工来说,对板材的下料要求极为严格,可以说是分毫不差。
但在家具设计中,允许板材尺寸存在偏差,且不影响整体结构和力学性能。
如文件柜的活动搁板,若假设宽度允许存在1~2mm 的偏差,完全不影响文件柜的结构性能。
其实在实际生产中,假设的偏差范围往往在允许的误差范围之内,但正是这个假定,借助计算机就有可能算出更优的排料方案。
进一步讲,若家具各部件尺寸已定,在已得较优方案下,能否计算出某个零件若允许存在一定偏差时能使整体用料显著下降,再回头设计图纸,将与此相关的尺寸下调1~2mm,可能降低几个百分点的板材利用率,这也是快速报价必须考虑的问题;另一方面,在不影响板材有效利用率时权衡边料回收与锯路工序成本,必要时增加毛边尺寸,来提高生产效率,这是生产管理所要考虑的问题。
更多的情况是下料方案设计中,零件尺寸多为含有加工余量的毛料尺寸。
其加工余量在一定范围内如何确定,可以有效通过计算机辅助得到更优解。
大批量生产的情况下,下料方案的优化对节约成本有极其重要的意义,目前靠人工和计算机交互计算难以达到最优。
通过讨论,将家具方面相关的专业知识,同数学建模和计算机辅助计算结合起来,为计算机辅助工艺设计软件的开发成为一种可能。
相信在不久的将来,智能的下料软件将更好的服务于家具设计,为节约型社会的建设贡献力量。