模架设计
移动模架施工设计方案
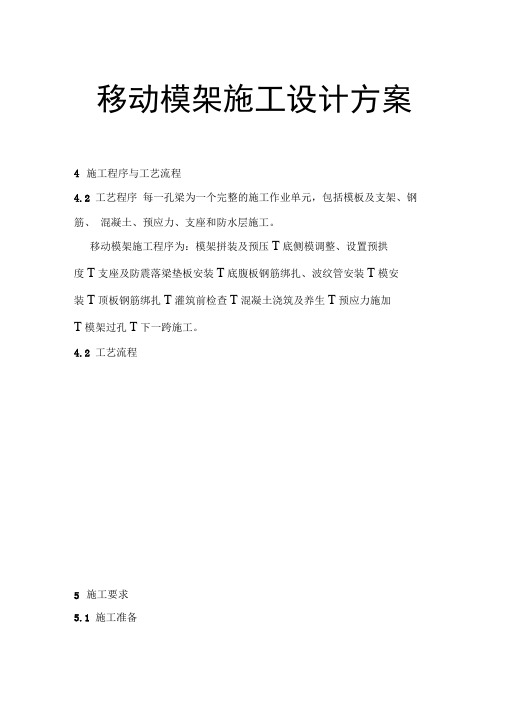
移动模架施工设计方案4施工程序与工艺流程4.2 工艺程序每一孔梁为一个完整的施工作业单元,包括模板及支架、钢筋、混凝土、预应力、支座和防水层施工。
移动模架施工程序为:模架拼装及预压T底侧模调整、设置预拱度T支座及防震落梁垫板安装T底腹板钢筋绑扎、波纹管安装T模安装T顶板钢筋绑扎T灌筑前检查T混凝土浇筑及养生T预应力施加T模架过孔T下一跨施工。
4.2 工艺流程5施工要求5.1 施工准备5.1.1 墩柱施工时做好预埋件或预留孔的埋设作业。
对于墩身上安装牛腿支架临时支撑点和锚固点的位置安装方式,在收到施工图纸后做出详细的施工设计方案报审以确保结构物安全。
墩身施工时,在其两侧立面中心处按照设计要求预留孔洞。
施工时采取措施确保预埋位置、尺寸准确。
支撑托架转运后,模架过孔前根据要求封口,施工时通过主梁设置挂篮,凿毛预留孔表面混凝土,剔除松散颗粒,喷水润湿,采用半干硬性微膨胀混凝土土人工浇筑,分层砸实,收面平整。
5.1.2 场地平整,并确保临时拼装支架基础稳定。
5.2 施工工艺5.2.1 模架构造下承式移动模架由主框架(含纵梁、导梁、横梁)、外模板、模板、主支腿(前后两个)、前辅助支腿、中辅助支腿、后辅助支腿、电气及液压系统等八部分组成。
模架整体结构如图5.2.1 所示。
1 主框架总成主框架由两根平行的箱形断面纵梁及桁架式导梁组成,全长69m,高2.8m,宽1.5m (腹板中心距)。
两根纵梁中心距11m采用8根横梁连成框架结构,横梁中心分开,以便横向开合,纵向移动时通过墩台。
横梁、纵梁、导梁各节点板采用高强螺栓连接。
2 外模及支撑系统外模包括底模、侧模及翼模,由6mmi冈板和角钢焊接而成。
通过可调支承系统支撑于主框架之上。
底模从中间以螺栓连接,分开后可连同主框架一起横向开合。
3 模系统32m箱梁模纵向分为7块,模板由顶模和侧模组成,侧模与顶模铰接,可旋转收。
通过水平和斜向丝杆支撑。
模通过液压移动车下降收后,在箱梁室纵向移动。
CAD第四章EMX模架设计

二、 EMX4.1模架设计过程
三、 EMX4.1----建立及修改项目
步骤:EXM4.1
项目
新建/修改
组件(ASM)模式:在这种模式下,成型零件需要事先设计好,然后通 过装配的方法加载到EMX模块中。 制造(MFG)模式:这种模式中的大多数功能均与组件模式下的相同, 但参照模型与成型零件的制作都在EMX中进行。
其他------其它
六、 EMX4.1----组件定义
步骤: EMX4.1
模具基体 组件定义 改变模架X、Y的大小
供应商
类型 B板 厚度
右视图(沿Y-Y剖视图)
主视图
A板
七、 EMX4.1----组件定义---添加标准模架
步骤: 组件定义 载入/保存组件 选择类型 载入 确定
选择类型
八、 EMX4.1----组件定义---识别模架组件
四、 EMX4.1----导入模具装配模型(.asm)
步骤:
选择要装配的模型(.asm)
用坐标系对齐方式装配模型
五、 EMX4.1----准备项目并对元件分类
步骤:EMX4.1
项目
准备
参考模型(_REF)------REF_MODEL 凸模------动模侧的抽模 凹模------定模侧的抽模
工件(_WRK)--------工件
选取被切除的组件 确定 确定
A板、推件板、 B板需要切除
推件板切除后
B板切除后 A板切除前 A板切除后
十五、 EMX4.1----添加顶杆
步骤:
选择顶出点所在的面 草绘基准点 绘制基准点 定义 顶杆 EMX4.1 在现有点上
推件板的下 表面为草绘 平面
草 绘 基 准 点
设置参数
移动模架施工组织设计

移动模架施工组织设计一、施工前准备1.确定工程范围和时间计划:根据建筑设计方案确定需要使用移动模架的区域,然后根据工程时间计划确定模架的使用时间。
2.编制施工组织设计方案:制定移动模架的使用计划和施工流程。
包括模架的购置和运输、搭建和拆除等工作的时间节点和工作内容。
3.确定施工人员和机械设备:根据工程的规模和施工要求,确定所需的施工人员和机械设备。
包括模架搭建人员、搬运工、起重机械等。
4.购置和运输模架材料:根据设计要求购买所需的模架材料,并安排运输到工地。
二、模架搭建施工流程1.施工现场布置:根据移动模架的使用要求,确定施工区域,并进行清理和平整。
2.安装固定基础:根据模架的使用需求,在施工区域内安装固定基础,确保模架的稳定性和安全性。
3.运输模架材料:根据施工计划,将模架材料从仓库运输到施工现场。
4.搭建模架:根据模架图纸和搭建要求,进行模架的组装和搭建工作。
在搭建过程中,需要注意模架的连接牢固和平整度。
5.安装扶手和防护措施:在搭建完成后,安装扶手和防护措施,确保作业人员的安全。
6.检验和修整:在搭建完成后,进行模架的检验和修整工作,确保模架的稳定性和安全性。
三、工程管理1.安全管理:设置警示标志、安全警告等安全措施,加强工人的安全教育和培训。
2.施工进度管理:根据施工组织设计方案,编制移动模架施工进度计划,监督施工进展,并及时调整施工计划。
3.资料管理:做好移动模架施工的各种记录和资料,包括材料验收、施工现场照片、施工进度等。
4.质量管理:制定模架施工质量验收标准,对施工质量进行抽查和验收。
四、其他事项1.施工现场环境保护:确保施工现场干净整洁,合理利用资源,减少噪音和空气污染。
2.管理沟通协调:加强施工人员之间的沟通和协调,确保施工过程顺利进行。
3.施工风险控制:针对搭建模架可能存在的风险,制定相应的措施进行风险控制。
以上是移动模架施工组织设计的大致内容,施工组织设计的具体内容和步骤可以根据实际情况进行调整和详细化。
sw冲压模具第二讲—模架的设计

SOLIDWORKS模具设计第二讲—模架的设计上节我们讲解了如何利用logopress进行钣金展开,并且进行排样和冲头的设置,这节课我来大概说一下模架的设计,模架设计一直也是冲压模具设计的重难点。
(1),首先我们打开上节保存的料带;(2),我们点击模具设计,出现如下图所示保存装配体选项,我们输入文件名然后点击保存,在这里请输入文件名称,不要去覆盖求前一个额装配体文件,具体原因在以后章节会谈到,计算机经过一段时间运算出现如下界面,我们点击下面箭头所指的按钮,增添一块儿模板,然后再模板下拉菜单选择下模,再选择合适的板型,点击z位置,同时单击料带下表面,如图所示,弹出如下提示窗,我们选择是,计算机短暂运算以后在图形区生成如下,以下箭头所指都是可以调节的,对参照面进行重新选取,参数进行设置,完成结果如下,此处我们发现这儿折弯工位和冲孔太近需要调节以后再阐述怎么调节,我们继续选择添加一块板,关数值选择合适的参照定位平面,我们对于外置以及需要的参数进行设置,调整后的位置和尺寸如图所示,用同样的操作添加下模座,(3),下面我们还是在下模部分添加模板,只是这个模板比较特殊我们来重点学习一下,选择导向板,设置材料等参数,这次定位请选择两个方向,z和x,完成以后确定,结果如下,不难发现位置是不合理的需要我们调整,怎么调节呢,首先我们点击x方向,把导向板的参考基准选为图示的面,完成结果如下同样的操作步骤对z方向进行重新设置,做好这些设置只是完成了对于导向件的定位,对于外形尺寸我们还没有定义,我们下拉菜单,看到外形尺寸设置选项,根据别的模板以及料带尺寸进行设置,生成结果如图;(4),这次我们添加一块儿卸料板,选择料带上表面作为定位参照,对模板位置进行调节,并设置合适的外形尺寸,(5),上模部分步骤原理同下模,我们直接给出结果。
注:西北狼(164874561)专注于全3D,参数化自上而下设计理论的研究及运用,目前涉及领域结构,机构,钣金,模具,管道以及钢结构等,欢迎广大同学老师以及业界工程师批评教导,初出茅庐,菜鸟一枚,欢迎老鸟蹂躏教导。
模具设计 模架介绍

模具设计-模架介绍1. 引言在模具设计中,模架作为模具的支撑结构,起到固定模具零部件的作用。
模架的设计质量直接影响着模具的性能和使用寿命。
本文将介绍模架的定义、分类、设计原则和常见材料等内容,以帮助读者更好地理解和应用模架设计。
2. 模架定义模架是模具的支撑结构,包括模架板和模架柱两部分。
模架板一般由钢板或铸铁制成,用于固定模具的零部件;模架柱则用来支撑和固定模架板。
模架的主要功能是承受模具零部件的压力,为模具提供稳定的支撑。
根据不同的应用场景和结构特点,模架可以分为以下几种类型:3.1 单层模架单层模架是最基本的模架形式,由一块模架板和若干根模架柱构成。
它适用于一些结构简单且要求不高的模具,成本较低。
然而,单层模架不适合承受较大的压力,对于一些复杂的模具来说可能会不够稳定。
3.2 分层模架分层模架相对于单层模架来说,多了一层模架板和中间支撑柱。
分层模架的结构更加稳定,可以承受更大的压力。
它适用于一些复杂的模具,如多腔模具和多层结构模具。
拉杆模架是一种特殊的模架结构,它使用拉杆代替模架柱,提高了支撑的稳定性。
拉杆模架适用于承受大的压力和冲击的模具,如冲压模具和注塑模具。
4. 模架设计原则在进行模架设计时,需要遵循以下原则:4.1 强度和刚度要求模架应具备足够的强度和刚度,能够承受模具零部件的压力和重量。
同时,模架还要保持稳定,不产生明显的变形,以确保模具的精度。
4.2 可调性和可拆卸性模架的设计应该考虑到模具零部件的可调性和可拆卸性。
模架板和支撑柱应该能够进行调整,以适应不同尺寸和形状的模具。
此外,模架还应容易拆卸,以便于修理和更换模具零部件。
4.3 实用性和经济性模架的设计应该尽量简洁实用,不做过度的加工和装饰。
同时,要充分考虑到材料成本和加工成本,追求经济性。
5. 模架常用材料常用的模架材料包括钢板、铸铁和铝合金等。
选择合适的材料取决于模具的具体要求和使用环境。
钢板是最常见的模架材料,它具有良好的强度和刚度,并且易于加工。
模架工程专项方案设计要点

模架工程专项方案设计要点一、工程概述1.1 项目名称:模架工程专项方案设计1.2 项目地址:XX省XX市XX区1.3 项目规模:建筑面积XXX平方米1.4 项目概况:本项目是为了满足生产需要,对新建或现有建筑进行模架工程设计,并确定施工工艺和流程以及施工方案。
二、设计依据2.1 相关标准:根据《建筑模板模架工程施工质量验收规范》(GB 50203-2011)、《建筑施工模模板工程验收规程》(JGJ 57-2010)等国家标准进行设计。
2.2 法律法规:按照《建筑法》、《建筑工程安全生产管理条例》等相关法律法规进行设计。
2.3 技术要求:充分考虑设计的技术可行性和经济合理性,确保设计的施工方案可以高效、安全地进行施工。
三、设计内容3.1 摸底调研:对现有建筑进行摸底调研,包括建筑结构、承重能力、现有模架工程施工情况等。
3.2 设计方案:根据调研结果,设计合理的模架工程方案,包括模板、模架的选型和搭设,模板支撑体系的设计等。
3.3 施工工艺:制定详细的施工工艺流程,包括模架搭设、调整、加固等具体施工步骤。
3.4 施工方案:拟定施工方案,包括工程组织设计、施工单位的技术能力、施工进度计划等。
四、设计注意事项4.1 安全施工:设计要充分考虑施工安全问题,在模架工程设计中应注重施工操作的安全性和稳定性。
4.2 质量控制:在设计过程中,要注意控制施工材料的质量,确保模板、模架等材料符合国家标准。
4.3 施工环境:设计要充分考虑施工环境的影响,包括气候、地质等因素对施工的影响,并提出相应的解决方案。
4.4 经济合理:设计要考虑经济合理性,力求在满足工程质量要求的前提下,尽可能降低施工成本。
五、设计成果5.1 设计图纸:出具模架工程设计图纸,包括平面布置图、结构图、剖面图等。
5.2 设计报告:编写模架工程专项方案设计报告,详细说明设计依据、设计内容、设计要点等。
5.3 审图意见:提交设计图纸和设计报告,获得相关专业审核意见。
注塑模具UG模架设计具体步骤2

注塑模具UG模架设计具体步骤2
PPT文档演模板
注塑模具UG模架设计具体步骤2
PPT文档演模板
注塑模具UG模架设计具体步骤2
3rew
演讲完毕,谢谢听讲!
再见,see you again
PPT文档演模板
2020/11/24
注塑模具UG模架设计具体步骤2
PPT文档演模板
注塑模具UG模架设计具体步骤2
1 Injection(浇注系统标准件)
标准件库中多家世界著名厂商提供了模具 系列标准件,在浇注系统标准件里就包括 有定位环和浇口套。 1) 定位环 2) 浇口套
PPT文档演模板
注塑模具UG模架设计具体步骤2
PPT文档演模板
注塑模具UG模架设计具体步骤2
MW模架库管理
UG MW专家模架库中提 供了面向中国地区用户 使用的龙记模架,英文 缩写LKM。 在“注塑模向导”工具 条上单击“模架”按钮 ,程序弹出“模架管理 ”对话框,如图所示。
PPT文档演模板
注塑模具UG模架设计具体步骤2
MW模式下的模架加载
在MW模式下,模架的加载变得很简便,初始化后的模 型设置了模具坐标系,模架则以模具坐标系为参照 基准来进行加载、装配。同样以一个实例例来说明 初始化项目的模架加载过程。操作步骤如下:
•定位 环 •工字板(前盖板) •A板(前模板) •B板(后模板)
•方铁(模脚) •面针板/底针 •板(顶针板/顶针盖板)
•底板/后盖板
PPT文档演模板
注塑模具UG模架设计具体步骤2
•工子板(前盖板) •水口板
•A板(前模板) •B板(后模板)
•方铁(模脚) •顶针板/顶针盖板
•底板(后盖板)
PPT文档演模板
中国注塑模架标准最新规范

中国注塑模架标准最新规范一、概述注塑模具是塑料加工行业的关键组成部分,其标准化对于提高生产效率、降低成本、保证产品质量具有重要意义。
本规范旨在为模具设计、制造和使用提供统一的技术要求。
二、适用范围本规范适用于各类塑料注射成型模具的设计和制造,包括但不限于单色、双色、多色及特殊成型工艺的模具。
三、材料要求1. 模具材料应具有良好的硬度、耐磨性和抗腐蚀性,以适应不同的工作环境和成型要求。
2. 模具钢材应符合国家标准或行业标准,确保材料的一致性和可靠性。
四、设计要求1. 模具设计应考虑塑料流动性、冷却速度和收缩率等因素,确保成型件的尺寸精度和表面质量。
2. 模具结构应简洁合理,便于拆卸、清洗和维护。
五、制造工艺1. 模具制造应采用精密加工技术,确保模具的尺寸精度和表面光洁度。
2. 模具的关键部件应进行热处理,以提高其硬度和耐磨性。
六、装配与调试1. 模具装配应严格按照设计图纸进行,确保各部件的配合精度。
2. 模具调试应在实际生产条件下进行,以验证模具的成型能力和稳定性。
七、质量检验1. 模具在出厂前应进行全面的质量检验,包括尺寸精度、表面质量、材料性能等。
2. 检验结果应符合本规范的要求,并附有相应的检验报告。
八、维护与保养1. 模具在使用过程中应定期进行清洁和维护,以延长模具的使用寿命。
2. 发现模具有损坏或磨损时,应及时进行修复或更换。
九、安全与环保1. 模具设计和制造过程中应严格遵守国家安全生产法规,确保操作人员的安全。
2. 模具材料和制造过程中产生的废弃物应符合环保要求,进行妥善处理。
十、附录本规范附录包含模具设计和制造过程中常用的参考数据、计算公式和图例,供设计和制造人员参考。
以上规范为注塑模架设计和制造提供了一套完整的技术指导,有助于提升模具行业的整体水平和竞争力。
现行规范高大模架构造设计参数的探讨与选用

( 北京六建集 团有限责任公司 , 1 0 0 1 4 3 , 北京)
摘
要 :现行规范对高大模架 的设计 与构造要求存在较多不一致 , 研究与分析相关规范 中的控制参数有必
要性 , 通过对比得 出 : 应将 立杆间距及 水平杆步距布置合理使之能尽量充分承载 ; 高大模架的剪刀撑 间距按《 混 凝 土结构 工程施 工规 范》 ( G B 5 0 6 6 6 -2 0 1 1 )选取 ,并应符 合 《 建 筑施工 扣件式钢 管脚手 架安全技 术规范 》 ( J G J 1 3 0 - - 2 0 1 1 ) 中加强型剪刀撑 的间距规定 ; 连墙件 、 抱柱及顶墙等措施 应尽量加强 。 关键词 :规范 ;高大模架 ;稳 固性 ;设计参数
l a r g e f o r m w o r k s u p p o r t s h a l l b e d e t e r m i n e d a c c o r d i n g t o c 0 d e r C o n s t r u c t i o n o f C o n c r e t e S t r u c t u r e s( G B 5 0 6 6 6 -2 0 1 1 )a nd s h l a l c o m p l y w i t h t h e s p a c i n g a m o n g s t r e n g t h e n e d b r i d g i n g s s p e c i f i e d i n T e c h n i c a l c o d e厂 0 r S a f e t y f o S t e e l T u b u l a r S c a fo l d w i t h C o u p l e r s i n C o st n r u c t i o n ( J G J 1 3 0 —2 0 1 1 ) ;w a l l — c o n n e c t i n g m e m b e r s ,
无梁顶板模架支撑体系设计与技术措施
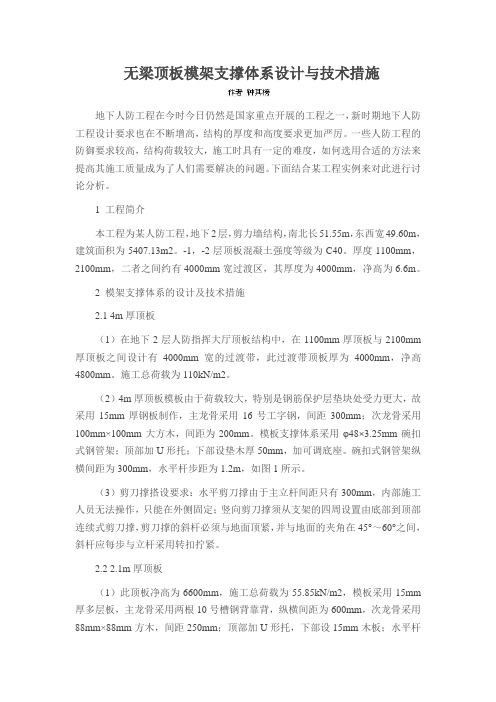
无梁顶板模架支撑体系设计与技术措施地下人防工程在今时今日仍然是国家重点开展的工程之一,新时期地下人防工程设计要求也在不断增高,结构的厚度和高度要求更加严厉。
一些人防工程的防御要求较高,结构荷载较大,施工时具有一定的难度,如何选用合适的方法来提高其施工质量成为了人们需要解决的问题。
下面结合某工程实例来对此进行讨论分析。
1 工程简介本工程为某人防工程,地下2层,剪力墙结构,南北长51.55m,东西宽49.60m,建筑面积为5407.13m2。
-1,-2层顶板混凝土强度等级为C40。
厚度1100mm,2100mm,二者之间约有4000mm宽过渡区,其厚度为4000mm,净高为6.6m。
2 模架支撑体系的设计及技术措施2.1 4m厚顶板(1)在地下2层人防指挥大厅顶板结构中,在1100mm厚顶板与2100mm 厚顶板之间设计有4000mm宽的过渡带,此过渡带顶板厚为4000mm,净高4800mm。
施工总荷载为110kN/m2。
(2)4m厚顶板模板由于荷载较大,特别是钢筋保护层垫块处受力更大,故采用15mm厚钢板制作,主龙骨采用16号工字钢,间距300mm;次龙骨采用100mm×100mm大方木,间距为200mm。
模板支撑体系采用φ48×3.25mm碗扣式钢管架;顶部加U形托;下部设垫木厚50mm,加可调底座。
碗扣式钢管架纵横间距为300mm,水平杆步距为1.2m,如图1所示。
(3)剪刀撑搭设要求:水平剪刀撑由于主立杆间距只有300mm,内部施工人员无法操作,只能在外侧固定;竖向剪刀撑须从支架的四周设置由底部到顶部连续式剪刀撑,剪刀撑的斜杆必须与地面顶紧,并与地面的夹角在45°~60°之间,斜杆应每步与立杆采用转扣拧紧。
2.2 2.1m厚顶板(1)此顶板净高为6600mm,施工总荷载为55.85kN/m2,模板采用15mm 厚多层板,主龙骨采用两根10号槽钢背靠背,纵横间距为600mm,次龙骨采用88mm×88mm方木,间距250mm;顶部加U形托,下部设15mm木板;水平杆步距为1.2m。
模架设计知识点归纳
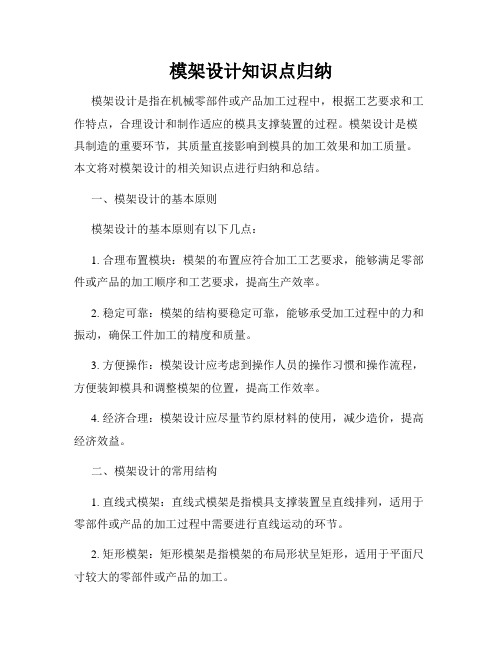
模架设计知识点归纳模架设计是指在机械零部件或产品加工过程中,根据工艺要求和工作特点,合理设计和制作适应的模具支撑装置的过程。
模架设计是模具制造的重要环节,其质量直接影响到模具的加工效果和加工质量。
本文将对模架设计的相关知识点进行归纳和总结。
一、模架设计的基本原则模架设计的基本原则有以下几点:1. 合理布置模块:模架的布置应符合加工工艺要求,能够满足零部件或产品的加工顺序和工艺要求,提高生产效率。
2. 稳定可靠:模架的结构要稳定可靠,能够承受加工过程中的力和振动,确保工件加工的精度和质量。
3. 方便操作:模架设计应考虑到操作人员的操作习惯和操作流程,方便装卸模具和调整模架的位置,提高工作效率。
4. 经济合理:模架设计应尽量节约原材料的使用,减少造价,提高经济效益。
二、模架设计的常用结构1. 直线式模架:直线式模架是指模具支撑装置呈直线排列,适用于零部件或产品的加工过程中需要进行直线运动的环节。
2. 矩形模架:矩形模架是指模架的布局形状呈矩形,适用于平面尺寸较大的零部件或产品的加工。
3. 正交模架:正交模架是指模具支撑装置的结构按照直角坐标系布置,适用于需要在多个方向上进行加工的零部件或产品。
4. 圆环式模架:圆环式模架是指模架的布置形状呈圆环,适用于需要进行环状加工的零部件或产品。
三、模架设计的关键要点1. 模架强度:模架设计时,要根据加工过程中的力和振动情况,保证模架具有足够的强度和刚度,以确保模架在工作过程中不会发生变形和断裂。
2. 模架尺寸:模架设计时,要根据加工工艺要求和零部件或产品的尺寸,确定模架的尺寸和布局,以保证零部件或产品能够顺利进行加工。
3. 模架位置:模架设计时,要考虑到操作人员的操作习惯和工作流程,合理安排模架的位置和高度,以方便操作和调整模具。
4. 模架装卸:模架设计时,要考虑到模具的装卸过程,设计合适的装卸方式和装卸装置,以提高工作效率和安全性。
四、模架设计的常见问题及解决方法1. 模架刚度不足:解决方法可以是增加支撑点或加强模架的结构,以提高模架的刚度。
模架设计教学

模架设计教学一、引言模架设计是工程领域中常见的设计任务之一。
模架是指用于支撑和定位工件或部件的具有特定形状和尺寸的支撑结构。
模架设计的质量直接影响到工件的加工精度和生产效率。
本文将介绍模架设计的基本原则和步骤,帮助读者更好地掌握模架设计技术。
二、模架设计的基本原则1. 稳定性原则:模架设计应保证模架的稳定性,以确保工件在加工过程中不会出现晃动或倾斜的情况。
稳定性可以通过增加支撑点、加大支撑面积等方式来实现。
2. 刚性原则:模架设计应保证模架具有足够的刚性,以便能够承受工件加工过程中的力和振动。
刚性可以通过增加模架的横截面尺寸、选择适当的材料等方式来提高。
3. 精度原则:模架设计应考虑工件加工过程中的精度要求,以确保模架的精度与工件的精度要求匹配。
精度可以通过精确的定位装置、精细的加工工艺等方式来保证。
4. 经济原则:模架设计应追求经济性,即在满足工件加工要求的前提下,尽量降低成本和材料消耗。
经济性可以通过合理的结构设计、优化的材料选择等方式来实现。
三、模架设计的步骤1. 确定工件加工要求:首先需要明确工件的加工要求,包括尺寸精度、加工工艺等。
这将有助于确定模架的支撑方式和定位要求。
2. 设计模架结构:根据工件的形状和特点,设计模架的整体结构。
可以采用三维建模软件来进行模架的设计,以便更好地进行模拟和分析。
3. 确定支撑点和面:根据工件的形状和加工需求,确定模架的支撑点和支撑面。
支撑点应尽量均匀分布在工件上,支撑面应覆盖工件的关键部位。
4. 确定定位装置:根据工件加工要求,确定模架的定位装置。
定位装置应具有良好的定位精度,以确保工件在加工过程中保持正确的位置和姿态。
5. 优化设计:对已完成的模架设计进行优化,以提高模架的稳定性、刚性和精度。
可以利用有限元分析软件对模架进行强度和刚度分析,进一步完善模架设计。
6. 确定材料和加工工艺:根据模架的设计要求,选择合适的材料和加工工艺。
材料应具有足够的强度和刚度,同时考虑生产成本和可加工性。
6000kN热模锻压力机模架结构设计

加
9
图1 模架结构
1 8
最大合模高/ mm
能力发生点/ mm
60 5
5
滑块面积 ( . . ) LR XFB/ Xml mm T l
6 0X6 0 9 3
工作台面积 ( - FB / m X m LRX - ) m m
侧 窗 口尺 寸/ Xmm mm 上 顶 料 能 力一 程/ m n 行 t l - 下 顶 料 能 力一 程/ ml 行 t n —
,
m et M ol o w r
n O. m fl S co g
热 碧 置 蕉 参 .热。 倦 锈 ’ 一 … 工 磊 … 加 一
上 下 模 板 是 上 模 架 的主 体 ,必 须 能 经 受 长 期 使 用 而 不 失 效 ,即具 有 一 定 的 抗 冲 击性 、较 高 强 度 及 耐 磨 性 。 因此 模板 材 质不 宜 选 用铸 钢 ,此 模 架 模板 采 用4 CMo 钢 ,热 处理 后 硬 度 3~ 6 R 2r 锻 2 3 H C。
定位 ,所 以其硬度 尽量高 点 ,在 锻打过 程 中不易
变 形 。 材 质 选 用 4 C M o 钢 ,热 处理 后 硬 度4 ~ 2r 锻 0
4 HRC 。 4
要有好的冲击韧度 ,材质选 用H1 ,热处理后硬度 3
60k 热模锻压力机模架结构设计 00 N
浙江德美轴 承有限公 司 ( 嵊州 32 0 ) 董 1 5 0 雷
1 设计 要求 .
— —
模架是热模锻压力机上锻模 的通用部分 ,不 同 锻件按工序单独设计的模块安装在模架上。模架作 为紧固锻模和传力构件 ,设计时必须考虑模 架的强
度及 生 产过 程 中的 安 全性 ,并 且 在保 证 锻 件生 产 效
第十章 模具模架设计—EMX ProE模具设计基础教程(课件)PPT
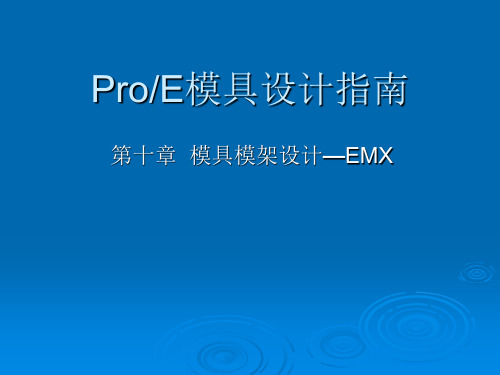
第十章 模具模架设计—EMX
10.1 EMX安装及设置
EMX有两种工作模式:
➢ 组件(ASM)模式:在这种模式下,成型零件需要事 先设计好,然后通过装配的方法加载到EMX模块中。
➢ 制造(MFG)模式:这种模式中的大多数功能均与组 件模式下的相同,但参照模型与成型零件的制作都 在EMX中进行。
10.1 EMX安装及设置
10.1.1 安装EMXຫໍສະໝຸດ 10.1 EMX安装及设置
10.1.2 设置EMX
10.2 EMX设计模架
如图所示是食品盒盖的实体模型,它在内侧有卡钩,要成型 它必须采用内侧抽芯机构,塑件的总体尺寸大小适中,比较 适合于模具生产。 食品盒盖的技术参数及设计要求为:材料为ABS,中小批量 生产,未注公差等级为MT5级精度。由于食品盒盖是中小 批量生产,一模一件方式生产能适应需求,点浇口上端进料, 料流比较顺畅,流程较短,零件质量较好,且塑件脱模后不 需去除浇口。 模具的基准与分型面位置有关,根据侧型芯和凹凸模的位置, 可以确定分型面位于零件的底部,产生的飞边容易去除,不 影响塑件外观。 本例采用EMX的组件模式设计模具,首先在Pro/E模具模块 中设计参照零件,然后导入到EMX中进行模架设计。
10.2 EMX设计模架
模架中可供设计参考的值

模架中可供设计参考的值以下内容,为素彦平常设计中常用的方法,如有雷同,不胜荣幸,若转载,请注明出处。
一:回针大小(中托司,弹簧,垃圾钉,可参考)用法:1:中托司设计时,回针大小的值可做为(中托司)的参考尺寸,正常情况下,25以下的回针,中托司做到跟回针同样大小。
25以上的回针,中托司可做到跟回针同样大,或者小一号。
2:顶针板弹簧顶针板加弹簧时,要求严格的公司,我们应该去计算弹簧的力(不知道有没有人不会?),对于一般要求不太严格的公司,顶针板弹簧内孔大小,以回针大小为标准。
比如:回针直径为20,那么直径35的黄弹簧内径就是20,我们的选择尺寸就出来了。
3:垃圾钉对于20以下回针的模具,垃圾钉做到大一号,对于20-30的,做到相等比较合适。
35以上的做到小一号的比较合适二:导柱大小(撬模坑可参考)用法:1:撬模坑有些公司规定了规格,不过,这个东西大点小点无妨,只是看起来好不好看的问题,一般来说,撬模坑的长宽的值,做到导柱直径大小比较合理,比如:导柱直径是35,那么,撬模坑就做到C35就OK了。
三:顶针板螺丝(模仁螺丝可参考)用法:1:模仁螺丝网上有资料统计,长宽为多大范围的模仁用多大的螺丝,用几个。
实际上,你按那个大小去画个模仁出来看看,你会觉得很奇怪。
我比较推荐的用法是,参考模架的顶针板螺丝,比如:顶针板螺丝是M8。
那么,模仁螺丝做M8绝对不会小。
对于稍微大点的模架,模仁螺丝比顶针板螺丝大一个规格。
四:顶针板宽度(模仁宽度)确定模架大小时,有些人说模仁大小确定的情况下,单边加50,有滑块加80-100,就是模架的尺寸。
个人认为,这样的尺寸带给刚入行的人很多的误导,你说到底是加70对,还是80呢?我常用的方法是,以顶针板宽度为准,有滑块的,得保证铲基面足够强度为宜。
如下图,图中,第一种情况,模架显得大了,第二种较合适,第三种有点紧凑。
这几种做法,设计中都会碰到,一般来说,有滑块等结构的模具或小模具,第一种常见,显得大点,也不离谱,小模具10mm都觉得很多了。
注塑模具模架设计具体步骤

实例:MW模式下模架与标准件的加载
自动中心
(6)型芯安装形式。
直接浇口 推件板 台肩安装
(7)确定型腔结构形式
整体镶嵌式
(8)确定型腔壁厚和底板厚度
查表
S=19+70=89mm 取90mm
确定型腔壁厚取90mm 底板厚取30mm
(9)确定模板尺寸( 一模一腔)
L=S+A+S L=90+220+90=400mm N=S+B+S N=90+140+90=320mm
1 标准模架 2 定位环、浇口套 3 浇注系统 4 冷却系统 5 滑动机构
一、模架
T板 A板 B板 U板
E板
C 板
F板
L板
S板:推件板
动、定模座板 固定板 支承板 垫块
模架具体由四部分组成:
1. 定 模 部 分 2. 动 模 部 分 3. 导 向 部 分 4. 连 接 固 定 部 分
定模座板
定模部分
要有足够的强度:小型模具H>13mm, 大型模具H可达75mm以上
连接方式:用螺栓压板与机床相连 材料:中碳钢 45钢
2.固定板 作用:固定凸模、型芯、凹模、导柱、导套、推杆等零件:台阶、沉孔、平面连接
3.支承板
作用:垫在固定板背面,防止成型零件和导向 零件的轴向移动并承受一定的成型压力。
有托导套 直导套 导柱 回针
面针板
5、模架选择步骤实例
塑料:ABS
步骤:
(1)根据软件测出塑件体积 V1=211cm3 (2)估算出一模1腔加浇注系统体积 V=211(1+0.25)=263cm3
(3)初选注塑机
263/0.8=328.75cm3
通用模架设计规范要求有哪些

通用模架设计规范要求有哪些通用模架设计规范是为了确保模架的设计、制造和应用过程中的安全性、可靠性和可维护性而制定的一系列要求。
下面是一些通用模架设计规范的要求:1. 结构强度:模架应能承受各种工况下的荷载,如自重、操作荷载等。
其结构强度要满足相关的标准和规范。
2. 模架材料:模架的材料应具有足够的强度和刚度,能够承受工作环境中的腐蚀、磨损和冲击等。
常用的材料包括钢、铁、铝合金等。
3. 尺寸和几何精度:模架的尺寸和几何精度应符合设计要求,以保证模具部件的装配精度和工作性能。
4. 模具安装和调试:模架应设计方便快捷的安装和调试方式,使模具能够快速调整和适应工作要求。
5. 模具稳定性:模架应具有稳定的结构,能够保证模具在运行过程中的稳定性和可靠性,避免因模具晃动而导致的加工误差或故障。
6. 模具附件:模架设计应考虑到模具所需的各类附件,如导向装置、顶出装置等,并保证其良好的运行状态和可靠性。
7. 模具保护:模架应具有必要的保护措施,如抗震、防腐蚀、耐磨损等,以延长模具的使用寿命。
8. 模架刚性:模架应具备足够的刚性,以抵抗加工过程中的加工力和振动等,确保模具的精度和工作性能。
9. 模架的可维护性:模架应设计方便维护和修复的结构,使操作者能够快速进行维护和修复工作,减少停机时间。
10. 安全性:模架设计应考虑操作者的安全,在设计中要遵循相关的安全规范,采取适当的措施保障操作者的人身安全。
总之,通用模架设计规范要求以上述要素为基础,以确保模架的结构强度、材料选择、尺寸和几何精度、安装和调试、稳定性、附件、保护、刚性、可维护性和安全等方面都能满足相关的标准和规范,以确保模架的安全、可靠和长期稳定的运行。
模架体系施工方案
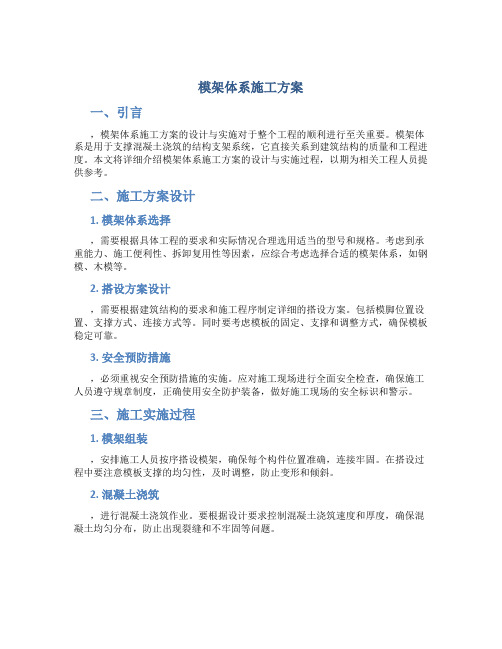
模架体系施工方案一、引言,模架体系施工方案的设计与实施对于整个工程的顺利进行至关重要。
模架体系是用于支撑混凝土浇筑的结构支架系统,它直接关系到建筑结构的质量和工程进度。
本文将详细介绍模架体系施工方案的设计与实施过程,以期为相关工程人员提供参考。
二、施工方案设计1. 模架体系选择,需要根据具体工程的要求和实际情况合理选用适当的型号和规格。
考虑到承重能力、施工便利性、拆卸复用性等因素,应综合考虑选择合适的模架体系,如钢模、木模等。
2. 搭设方案设计,需要根据建筑结构的要求和施工程序制定详细的搭设方案。
包括模脚位置设置、支撑方式、连接方式等。
同时要考虑模板的固定、支撑和调整方式,确保模板稳定可靠。
3. 安全预防措施,必须重视安全预防措施的实施。
应对施工现场进行全面安全检查,确保施工人员遵守规章制度,正确使用安全防护装备,做好施工现场的安全标识和警示。
三、施工实施过程1. 模架组装,安排施工人员按序搭设模架,确保每个构件位置准确,连接牢固。
在搭设过程中要注意模板支撑的均匀性,及时调整,防止变形和倾斜。
2. 混凝土浇筑,进行混凝土浇筑作业。
要根据设计要求控制混凝土浇筑速度和厚度,确保混凝土均匀分布,防止出现裂缝和不牢固等问题。
3. 拆除模架,可以开始拆除模架。
拆除过程中应注意避免对混凝土结构造成影响,采取逐级拆除、有序进行的方式,确保拆除作业的安全和效率。
四、总结,直接关系到工程质量和进度。
通过合理的设计与施工方案,可以提高施工效率,保障施工安全,为工程的顺利进行奠定基础。
在实际施工中,要严格按照设计方案和安全规定进行操作,确保施工质量和安全。
模架设计知识点

模架设计知识点模架设计是制造和工程领域中的重要环节,用于支撑和定位工件、夹具、模具等。
本文将从模架设计的概念、设计原则、材料选择、组装方式等方面进行探讨。
1. 概念说明模架设计是指在制造过程中,为了满足工件定位、支撑和加工需求而设计的支撑架构。
良好的模架设计能够提高加工精度、降低生产成本和缩短加工周期。
2. 设计原则(1)稳定性原则:模架设计应确保结构的稳定性,防止工件在加工过程中出现偏移或倾斜。
(2)刚性原则:模架应具备足够的刚性,以保证工件的加工精度和质量。
(3)合理性原则:模架设计应符合工艺要求,便于加工操作和工件装夹。
(4)经济性原则:模架应尽可能简化结构,减少材料和成本的消耗。
3. 材料选择(1)铸铁:铸铁具有良好的刚性和稳定性,适用于承载较重工件的模架设计。
(2)铝合金:铝合金具有较低的密度和良好的加工性能,适用于小型模架的设计。
(3)钢材:钢材具有高强度和优良的刚性,适用于高负荷和高精度要求的模架设计。
4. 组装方式(1)焊接:焊接是常见的模架组装方式,能够提供较高的结构刚性和稳定性。
但是焊接过程中可能会产生变形和残余应力,需要合理控制焊接工艺。
(2)螺栓连接:螺栓连接方便拆卸和调整,适用于需要频繁更换工件或调整间距的模架设计。
(3)插接连接:插接连接简单快捷,适用于较轻型的模架设计,并能够减少结构变形的风险。
5. 其他注意事项(1)模架设计时应考虑工件的形状、尺寸和重量,合理安排支撑点和支撑面积,以确保工件的稳定性和加工精度。
(2)模架的设计应尽量减少干涉,并留出足够的空间进行加工。
(3)在实际操作中,应根据具体工艺要求和加工条件进行模架设计的优化和改进。
结语:模架设计是制造和工程领域中的重要环节,能够决定工件加工的精度和质量。
本文从概念、设计原则、材料选择、组装方式等方面介绍了模架设计的知识点,希望能对读者在实际操作中的模架设计起到一定的指导作用。
- 1、下载文档前请自行甄别文档内容的完整性,平台不提供额外的编辑、内容补充、找答案等附加服务。
- 2、"仅部分预览"的文档,不可在线预览部分如存在完整性等问题,可反馈申请退款(可完整预览的文档不适用该条件!)。
- 3、如文档侵犯您的权益,请联系客服反馈,我们会尽快为您处理(人工客服工作时间:9:00-18:30)。
3.模架设计
模架一般采用外购标准件。
要求较高的0级和1级模具模架要从HASCO 、DME 等外购买或自制,2、3级的模具从FUTABA 或龙记购买。
3.1模架规格的选用
3.1.1塑件结构和注塑机规格决定。
①
模架宽度应小于注塑机两条导柱间距,一般情况在选定注塑机后模架应尽量大些。
②
模架厚度要保证: a) 在注塑机前后墙板极限开合范围内 b) 模具结构的要求
c) 模具强度和刚性方面的要求 ③
三板模的拉杆长度的确定: 拉杆长度=A+6+B+水口长+(20~25)+C ④
拉板长度: a) 50吨以下机:D1=120-150
80吨以上机:D1=30+D
=30+(2.5-3)h+(120-150)
b) 当分模采用尼龙塞扣紧而为防止上模板回弹而设置的拉板只须对角、两副,此时拉板介子不必藏入模架;当不用尼龙塞而用拉板拉开上模板时,宜用4根拉板并且拉板介子要藏入模板。
⑤
限位螺丝。
2020以下模架D=10,3030以下D=12,4040 以下D=16,4040以上D=20
⑥
水口螺丝组(自制标准件) ⑦
弹簧选用TF 型黄色弹簧(压缩量50%) ⑧ 模架(间隔板高度=H+顶出距离,顶出距离≥需顶出高度+10mm 3.1.2模架板强度校核
在注射成形过程中,型腔承受塑料熔体的高压作用,因此模具型腔应该有足够
的强度,型腔强度不足将发生塑性变形,甚至破裂;刚度不足将产生过大弹性变形,导致型腔向外膨胀,并引致塑件卡在前模或产生分模面披锋。
1) 强度计算条件
在各种受力形式下,型腔产生的应力不应超过材料的许用应力。
通常许用应力
为[σ]= σς (σς—材料的屈服极限)
2) 刚度计算条件。
刚度计算主要依据是:
a) 型腔变形量不能产生分模面披锋,此时把塑料不产生披锋的最大间隙作为型腔允许变形量[δ]
b) 保证塑件尺寸精度。
此时型腔允许变形量[δ],由塑件的尺寸及其公差值决定,可由下表
2
1
c) 保证塑件顺利脱模,型腔允许变形量[δ]应小于塑件壁厚的收缩值以免脱模时擦伤塑件
3)
型腔计算
刚度计算: P=内模所受压强2/cm kg
δ=允许变形量mm
E=弹性系数=26/10*1.2cm kg h L b B 单位取mm
F=锁模力kg
P 胶—成形压力=222/65.44.25/3000/3mm kg kg in T ==
S —塑件投影面积2m m
3.2模架开框的规定:
3.2.1 2020以上模架的开框工作,建议在模架厂进行,4040以上一定要在模架厂开框。
3.2.2 中托司套的加工。
标示参见下列表格及简图
34
325δ
EB PbL = L
b S P F P
*)*(胶+=()()33
8
36
365.410*44.710*1.2*32*5δδ
B L S F B L S P F +=+=-胶
说明:a 对4040以下模架采用2支中托司 B 1=回针之间距离 d >回针直径
3.3模架板吊环螺丝孔的规定
3.3.1 模架A.B 板都必须要钻吊环螺丝孔(至少上下2个),规格按标准模架螺丝孔加工 3.3.2对于30kg 以上的每块模架板都须加上上、下吊环螺丝孔,100kg 以上模板四边都须有螺
3.3.3留意为防止特别场合下螺丝孔与方定位块、行位运水等相干涉,螺丝孔须偏移模板
中
心,此时螺丝孔须成双加工。
3.4关于模架的刻印
3.4.1模架回厂后要先在各模架板上刻上钢印,如上码模板定为GM2000-1,以此类推,其
序号与装配图所示零件图号相合。
3.4.2刻字位置及大小,无论模架大小用8#钢印刻8mm 高字于模板基准角对角位如图示:
每个字间隔1mm ,要求刻印前先轻划一条线,保证刻字平整、清晰
3.4.3运水进出孔要标注“IN1”、“OUT1”、“IN2”、“OUT2”等字样字高同上。
3.4.4对于顶针等易装错的零件,要在模架相应位置刻上相同记号:1、2、3……
3.5模架其他辅助装置
3.5.1撑头
1)为防止锁模力或在注塑时注塑压力将模板弯曲变形而造成成型塑件成品及品质不能达到要求,要在码模板和下模间加撑头。
2)要求+0.05(3030以下)
①
撑头应按标准选用。
撑头直径尽量选大,撑头高度=模具间隔板高 ②
撑头位置应放在下模板所受注塑压力集中处,且尽量往间隔板中间 +0.1(3030以上) 3.5.2定位块(INTERLOCK )
定位块能保证上下模精确对位,并承受模具受塑胶侧向力。
定位块分三种:方定位块、圆定位锥、模具原身定位块
自制标准件。
①
、定位块 保护插位,承受侧向力―
选用件。
②
、定位锥 保证模具精确定位―自制标准件。
③
、模架原身定位块大模具要承受较大的侧向力,一般采用模架原身定位 3.5.3
3.5.4锁模扣(用光扁料发黑)
为防止模具搬运及运输过程中分离而导致事故,要在模架表面加锁模扣。
3.5.5法兰
法兰是注塑机与模具连接定位的部分。
法兰采用自制标准件。
当有5mm 隔热板时,选用20厚法兰。
15吨机用φ50的法兰(20吨机用φ60法兰)。