陶瓷烧成工艺技术手册
范文陶瓷工艺技术手册

范文陶瓷工艺技术手册章一:引言陶瓷工艺是一门古老而精湛的手工艺术,它使用陶土、瓷石等原材料并通过特定工艺加工而成。
范文陶瓷作为一家专业制造陶瓷产品的企业,我们致力于传承和创新陶瓷工艺技术,并将其运用于产品设计与制造中。
本手册将详细介绍范文陶瓷的工艺技术和制作流程。
章二:材料准备2.1 陶土选择与配比陶土是制作陶瓷的重要原材料,我们选择高质量的陶土,根据不同产品的需求进行配比。
配比要保证陶瓷的强度和质地,使其适应不同的工艺要求。
2.2 瓷石的使用瓷石是另一个重要的原材料,具有高温煅烧后形成瓷质的特点。
瓷石的选择和研磨工艺对产品的质量有重要影响,我们会谨慎选择瓷石,并使用先进的研磨工艺。
章三:成型工艺3.1 手工成型手工成型是一种传统的陶瓷制作工艺,我们的熟练工匠使用手工技术将陶土塑造成各种形状。
手工成型注重工匠对细节的把握和对产品整体比例的掌控,使产品更具艺术性。
3.2 注浆成型注浆成型是一种辅助成型的工艺,通过将稀浆状的陶浆注入模具中,使其形成预定的形状,然后经过烘干和烧结工艺变成实心的陶瓷产品。
我们的注浆成型工艺流程严格,确保产品的准确度和稳定性。
章四:装饰工艺4.1 釉料选择与调配釉料决定了陶瓷表面的质感和颜色。
我们根据设计要求选择合适的釉料,并使用专业的调配技术进行配比,以确保产品的视觉效果与设计意图一致。
4.2 施釉工艺施釉是将釉料均匀地涂抹在陶瓷表面的过程,我们使用先进的喷涂或浸漆工艺,确保釉料能够完整地附着在陶瓷表面,并避免釉料的流淌与渗透。
章五:烧制工艺5.1 烘干工艺成型和装饰后的陶瓷产品需要经过烘干工艺,我们会将产品放置在恰当的环境条件下,控制温度和湿度,以确保产品在烘干过程中不会出现开裂或变形等问题。
5.2 烧结工艺烧结是将陶瓷产品置于高温窑炉中,使其达到熔化程度,形成致密的瓷质结晶体。
我们的烧结工艺严密控制炉温和烧结时间,确保产品的质量稳定和瓷质的均匀性。
章六:后处理工艺6.1 晾晒与检查烧制完成后的陶瓷产品需要进行晾晒,以保证产品内部的温度均衡。
陶瓷烧制安全操作手册
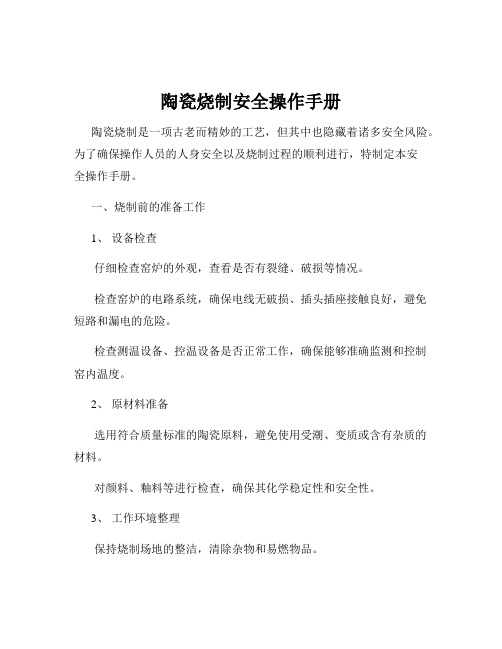
陶瓷烧制安全操作手册陶瓷烧制是一项古老而精妙的工艺,但其中也隐藏着诸多安全风险。
为了确保操作人员的人身安全以及烧制过程的顺利进行,特制定本安全操作手册。
一、烧制前的准备工作1、设备检查仔细检查窑炉的外观,查看是否有裂缝、破损等情况。
检查窑炉的电路系统,确保电线无破损、插头插座接触良好,避免短路和漏电的危险。
检查测温设备、控温设备是否正常工作,确保能够准确监测和控制窑内温度。
2、原材料准备选用符合质量标准的陶瓷原料,避免使用受潮、变质或含有杂质的材料。
对颜料、釉料等进行检查,确保其化学稳定性和安全性。
3、工作环境整理保持烧制场地的整洁,清除杂物和易燃物品。
确保通风良好,安装有效的通风设备,排除烧制过程中产生的有害气体。
4、个人防护装备操作人员应佩戴耐高温手套、防护眼镜、口罩等防护用品。
穿着防火阻燃的工作服,避免衣物被火星引燃。
二、烧制过程中的安全操作1、装窑装窑时要轻拿轻放,避免陶瓷制品相互碰撞而损坏。
合理安排摆放位置,确保制品之间有足够的空间,便于热气流通。
2、点火与升温按照窑炉的操作规程进行点火,先进行小火预热,逐渐升温。
密切关注温度上升速度,避免升温过快导致陶瓷制品破裂。
3、温度控制严格按照烧制工艺要求控制温度,不得随意更改温度设定。
定时检查温度显示,如发现异常应及时调整或停止烧制。
4、观察与监控在烧制过程中,通过观察孔定期观察窑内情况,但要注意避免高温热气灼伤。
利用监控设备,实时了解窑内的工作状态。
5、气体排放关注窑炉排放的气体,确保其通过有效的净化处理,符合环保要求。
如发现有害气体泄漏,应立即停止烧制,疏散人员,并采取通风措施。
三、烧制完成后的安全操作1、冷却烧制结束后,让窑炉自然冷却,切勿急于打开窑门,以免因温度骤变造成陶瓷制品开裂和操作人员烫伤。
2、出窑待窑内温度降至安全范围后,方可进行出窑操作。
出窑时仍需佩戴防护手套,小心取出陶瓷制品,防止烫伤和碰伤。
3、设备清理与维护清理窑炉内的残渣和灰尘,为下次烧制做好准备。
陶瓷一次烧成的工艺流程
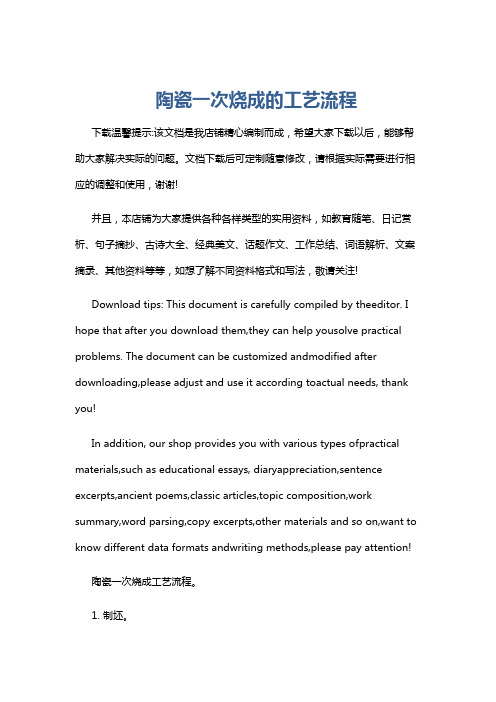
陶瓷一次烧成的工艺流程下载温馨提示:该文档是我店铺精心编制而成,希望大家下载以后,能够帮助大家解决实际的问题。
文档下载后可定制随意修改,请根据实际需要进行相应的调整和使用,谢谢!并且,本店铺为大家提供各种各样类型的实用资料,如教育随笔、日记赏析、句子摘抄、古诗大全、经典美文、话题作文、工作总结、词语解析、文案摘录、其他资料等等,如想了解不同资料格式和写法,敬请关注!Download tips: This document is carefully compiled by theeditor. I hope that after you download them,they can help yousolve practical problems. The document can be customized andmodified after downloading,please adjust and use it according toactual needs, thank you!In addition, our shop provides you with various types ofpractical materials,such as educational essays, diaryappreciation,sentence excerpts,ancient poems,classic articles,topic composition,work summary,word parsing,copy excerpts,other materials and so on,want to know different data formats andwriting methods,please pay attention!陶瓷一次烧成工艺流程。
1. 制坯。
根据产品形状和尺寸设计模具。
陶瓷烧制作业安全操作手册
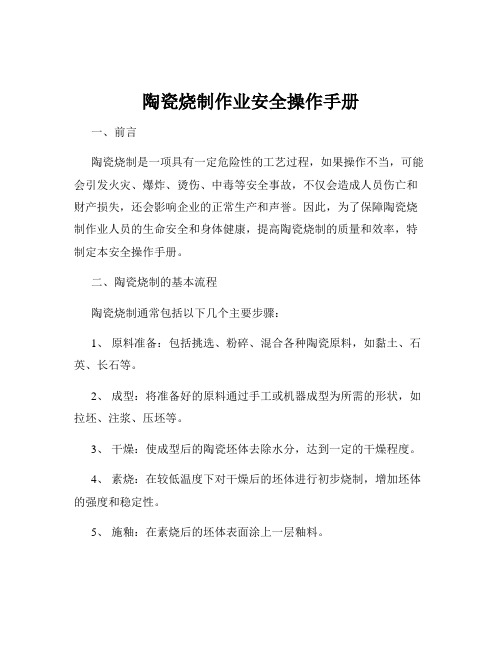
陶瓷烧制作业安全操作手册一、前言陶瓷烧制是一项具有一定危险性的工艺过程,如果操作不当,可能会引发火灾、爆炸、烫伤、中毒等安全事故,不仅会造成人员伤亡和财产损失,还会影响企业的正常生产和声誉。
因此,为了保障陶瓷烧制作业人员的生命安全和身体健康,提高陶瓷烧制的质量和效率,特制定本安全操作手册。
二、陶瓷烧制的基本流程陶瓷烧制通常包括以下几个主要步骤:1、原料准备:包括挑选、粉碎、混合各种陶瓷原料,如黏土、石英、长石等。
2、成型:将准备好的原料通过手工或机器成型为所需的形状,如拉坯、注浆、压坯等。
3、干燥:使成型后的陶瓷坯体去除水分,达到一定的干燥程度。
4、素烧:在较低温度下对干燥后的坯体进行初步烧制,增加坯体的强度和稳定性。
5、施釉:在素烧后的坯体表面涂上一层釉料。
6、釉烧:在较高温度下对施釉后的坯体进行烧制,使釉料熔融并与坯体结合,形成光滑、美观的表面。
三、安全操作要点(一)设备安全1、定期检查和维护烧制设备,如窑炉、电气设备、通风设备等,确保其正常运行和安全性。
2、窑炉在使用前,要检查炉体、炉门、热电偶、加热元件等是否完好,有无损坏或松动现象。
3、电气设备要接地良好,电线电缆无破损、老化现象,开关、插座等要安装牢固,防止触电事故。
4、通风设备要保持畅通,能够有效地排除窑炉内的废气和粉尘,防止中毒和爆炸事故。
(二)原料处理安全1、搬运和储存陶瓷原料时,要防止原料散落、飞扬,造成环境污染和人员伤害。
2、原料粉碎和混合过程中,要佩戴好防护眼镜、口罩、耳塞等防护用品,防止粉尘、噪音对人体造成伤害。
3、对于有毒、有害的原料,如铅、镉等,要严格按照操作规程进行处理,防止中毒事故。
(三)成型安全1、操作成型设备时,要严格按照设备的操作规程进行,避免违规操作导致设备故障和人员伤害。
2、手工成型时,要注意工具的使用安全,防止刺伤、割伤手指。
3、成型后的坯体要放置平稳,防止倾倒伤人。
(四)干燥安全1、干燥设备要安装在通风良好的地方,防止火灾和爆炸事故。
第七章陶艺制品的烧成

(3) 保温时间:根据具体泥料而定,一般细瓷为l~2小时。 (4) 冷却速度:以关闭火门、自然冷却为佳。
第三节 陶艺的烧制
2.陶质还原焰烧成曲线。陶质材料的还原焰烧成曲线与瓷匝材料的烧成曲线相比 要简单得多,它是通过还原焰烧制使陶质坯体中渗入二氧化碳,在作品表面形成深沉、 厚重和质朴的特殊效果.强还原烧制产生过浓的二氧化碳有时还会使作品表面出现铁 质般的金属感。由于陶泥的产地不同,烧制还原焰的曲线控制也不一样,在这里我们 按照普通烧制细陶的方法作介绍。
第一节 坯体的干燥与收缩
二、坯体的体积收缩 陶艺坯体经干燥和烧成后,体积会发生收缩变化。这是由于泥料中的水分排除,
经一系列物理变化所产生的玻璃态物质填充于颗粒之间,使之相互拉紧靠拢所致。 影响收缩的主要因索有矿物种类、配方组成、泥料粗细,含水量、烧成温度等。
可塑泥料所含水分,称为可塑水分,一般占总可塑泥料的10-20%。泥土经过干 燥和烧成二次收缩后体积约为原来的5/6。在自然干燥和人工干燥及烧成过程中,泥 料中的水分会自然排出,水分排出的过程就是泥料收缩的过程。
(1) 升温曲线:常温至300℃;每分钟约2℃,为加热蒸发期;3013℃~950℃,每 分钟约4℃,为氧化分解及晶体转化期;950℃~1150℃,每分钟约6℃,为玻化成陶 期。
(2) 还原曲线:950℃时封闭烟道1/3进行还原,约0.5小时;1050℃对封闭烟道2/3进 行强还原,约0.5小时;1150℃时开肩烟道,还原结束。
第二节 现代陶艺的装窑技术
图154 氧化焰烧制,花盆的装窑
第三节 陶艺的烧制
低温共烧陶瓷工艺技术手册

低温共烧陶瓷工艺技术手册
1. 原料选择,介绍了用于低温共烧陶瓷制作的各种原料,包括
粘土、矿物、釉料等,以及它们的特性和选择标准。
2. 工艺流程,详细描述了低温共烧陶瓷制作的工艺流程,包括
制胚、干燥、装饰、烧制等各个环节的具体操作步骤和注意事项。
3. 设备工具,介绍了用于低温共烧陶瓷制作的各种设备和工具,例如制胚机、干燥设备、窑炉等,以及它们的使用方法和维护保养。
4. 工艺参数,对于每个制作环节的工艺参数进行了详细的介绍
和说明,包括温度、湿度、时间等关键参数的控制要点。
5. 质量控制,介绍了低温共烧陶瓷制作过程中的质量控制方法
和标准,以及常见的质量缺陷及其预防和改进措施。
6. 安全环保,对于低温共烧陶瓷制作过程中的安全生产和环境
保护进行了相关的介绍和要求,确保生产过程安全、环保。
综上所述,低温共烧陶瓷工艺技术手册是一本全面介绍低温共
烧陶瓷制作工艺的指导手册,对于从事陶瓷制作的人员具有很高的参考价值,能够帮助他们更好地掌握低温共烧陶瓷的制作技术,提高产品质量,确保生产安全。
陶瓷烧成工艺技术

陶瓷烧成工艺技术陶瓷烧成工艺技术是指将陶瓷原料经过成型、干燥等工序后,通过高温烧制,使其变为坚硬、致密、具有一定物理和化学性能的制品的过程和技术。
陶瓷烧成工艺技术主要包括烧成温度控制、烧成周期设计以及烧成气氛控制等方面。
首先,烧成温度控制是陶瓷烧成工艺中非常重要的一环。
陶瓷材料的烧成温度直接影响着制品的物理和化学性能。
过低的烧成温度无法使陶瓷材料充分熔化,从而导致制品的容易破碎和抗压强度低等问题。
而过高的烧成温度则会导致陶瓷制品变形、烧裂等问题。
因此,在烧成过程中,必须严格控制烧成温度,以确保陶瓷制品的质量。
其次,烧成周期的合理设计也对陶瓷制品的质量有着重要的影响。
烧成周期包括加热阶段、保温阶段和冷却阶段。
加热阶段是指将陶瓷原料从室温加热到烧成温度的过程。
在这一过程中,需要适当控制加热速率,避免因温度变化过快而导致制品破裂。
保温阶段是指将陶瓷制品在烧成温度下保持一定时间以使其均匀烧结的过程。
而冷却阶段则是将烧成完的陶瓷制品从高温环境中冷却下来的过程。
在这一过程中,需要逐渐降温,避免因温度变化过快而导致制品破裂。
最后,烧成气氛的控制也是影响陶瓷制品质量的重要因素之一。
烧成气氛是指在烧成过程中制造的气氛,包括氧气浓度、气氛性质等。
不同的陶瓷制品对烧成气氛有不同的要求。
例如,釉上瓷需要弱还原性的气氛,而瓷砖则需要强氧化性的气氛。
因此,在烧成过程中,需要控制燃烧炉内的气氛,并根据不同的陶瓷制品要求做出相应的调整。
综上所述,陶瓷烧成工艺技术是一门研究如何控制陶瓷材料在高温下进行烧结的技术。
通过合理设计烧成温度,烧成周期和烧成气氛,可以得到质量更加优良的陶瓷制品。
在实践中,还需要结合不同的陶瓷材料以及制品的特点,对烧成工艺技术进行进一步的优化和改进,以满足不断变化的市场需求。
陶瓷高温烧成

实验5.5 陶瓷高温烧成1 目的意义1.1 意义烧成是通过高温处理,使坯体发生一系列物理化学变化形成预期的矿物组成和显微结构,从而达到固定外形并获得所要求性能的工序。
陶瓷烧成是制备陶瓷材料最重要的工艺步骤之一。
1.2 目的① 进一步了解陶瓷烧成温度和温度制度对材料性能的影响;② 掌握实验室常用高温实验仪器、设备的使用方法;③ 通过实验学会分析材料的烧成缺陷,制定材料合理的烧成温度制度。
2 基本原理陶瓷材料在烧成过程中,随着温度的升高,将发生一系列的物理化学变化。
例如,原料的脱水和分解,原料之间新化合物的生成,易熔物的熔融等。
随着温度的逐步升高,新生成的化合物量不断变化,液相的组成、数量及粘度也不断变化,坯体的气孔率逐渐降低,坯体逐渐致密,直至密度达到最大值,此种状态称为“烧结”。
坯体在烧结时的温度称为“烧结温度”。
陶瓷材料的烧结过程将成型后的可密实化的粉末,转化为一种通过晶界相互联系的致密晶体结构。
陶瓷生坯经过烧结后,其烧结物往往就是最终产品。
陶瓷材料的质量与其原料、配方以及成型工艺、陶瓷制品的性能、烧结过程等有很大关系。
因此,一般建筑卫生瓷的烧结除了要通过控制烧结条件,以形成所需要的物相和防止晶粒异常长大外,还要严格控制高温下生成的液相量。
液相量过少,制品难以密实;液相量过多,则易引起制品变形,甚至产生废品。
烧结后若继续加热,温度升高,坯体会逐渐软化(烧成工艺上称为过烧),甚至局部熔融,这时的温度称为“软化温度”。
烧结温度和软化温度之间的温度范围称为“烧结温度范围”。
3 实验器材①坩埚钳,石棉手套、护目镜;②高温电阻炉(最高温度1350℃±);③垫砂(煅烧SiO2或A12O3粉)。
④坯料:高岭土、滑石、长石、化学试剂等4 实验步骤① 试样制备:参见实验九;② 按编号将试样置人高温炉内。
装炉时,试样与炉底间以煅烧过的石英粉或A12O3粉隔离。
试样之间的距离为10mm。
③ 检查电炉正常后,开始按设定的升温曲线加热(烧结温度按照实验五计算结果),按预定的温度保温后取样。
陶瓷艺术的烧成方法

陶瓷艺术的烧成方法陶瓷品制作完成后,还要经过烧制才能最终成为成品。
那么,你知道陶艺的烧成方法有哪些吗?以下是有我为大家整理的,希望能帮到你。
陶瓷的烧成方法1、素烧法:表面不上釉的作品,直接烧成称为素烧。
素烧可以保留陶瓷作品上的手工痕迹,显现材质的自然和本质的美。
陶的素烧温度为900~1150℃。
瓷的素烧温度为1100~1310℃。
2、本烧法:陶瓷作品坯体表面上釉后,用高温一次性烧成,使坯体完全烧结,釉料完全融化,称为本烧。
烧成温度为1100~1350℃。
3、釉烧法:釉烧分两次烧成,陶瓷坯体经过一次素烧后再上釉,用低温二次烧成,使釉完全融化,烧成温度为900~1000℃。
4、氧化焰法:调整烟道阀门,保证窑内空气充足,定时添加燃料,使燃料在空气中彻底烧尽,由于窑炉氧气充足,则形成氧化焰气氛5、还原焰法:当温度加速升温至高温阶段,放低烟道阀门,使窑炉供养不足,炉内碳素增加,形成还原焰气氛。
6、乐烧法:乐烧采用二次烧成的工艺技术。
第一次素烧,温度为700~900℃。
再上釉,用低温二次烧成。
7、盐烧法:坯体在高温时,将氯化钠直接撒入在燃烧的窑炉中,氯化钠开始挥发,产生纳蒸气,这种纳蒸汽同陶瓷坯体表面的铝与硅产生反应,熔融成釉形成带有肌理的透明釉。
8、熏烧法:熏烧采用素烧和烟熏二次完成的工艺技术。
在素烧完成后再选用木屑、树枝、报纸等作燃料产生浓烟,通过坯体表面的缝隙使碳素附着于作品表面,形成自然的斑迹效果。
9、柴烧法:一种用木柴直接烧陶的方法。
因柴火直接在体坯上留下自然的“火痕”和木柴燃烧后的灰烬落在作品表面形成的“落灰釉”,使得作品色泽温润且有变化。
烧制陶瓷工艺流程烧制陶瓷的关键因素是:泥、釉、火。
为什么有些陶、瓷器会莫明其妙的出现裂纹呢?为什么有时甚至会掉皮釉呢?这不外是在一定温度条件下泥和釉的收缩系数又称膨胀系数不相一致的结果。
有时人们亦会对这种缺陷特意加以利用,传统的开片釉及现代陶艺的一些肌理追求就是利用釉和泥收缩系数不相一致的原理配制出来的。
烧窑大师手册
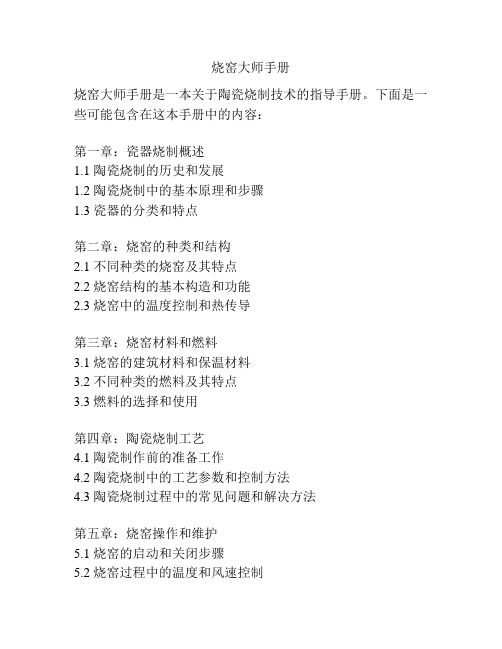
烧窑大师手册
烧窑大师手册是一本关于陶瓷烧制技术的指导手册。
下面是一些可能包含在这本手册中的内容:
第一章:瓷器烧制概述
1.1 陶瓷烧制的历史和发展
1.2 陶瓷烧制中的基本原理和步骤
1.3 瓷器的分类和特点
第二章:烧窑的种类和结构
2.1 不同种类的烧窑及其特点
2.2 烧窑结构的基本构造和功能
2.3 烧窑中的温度控制和热传导
第三章:烧窑材料和燃料
3.1 烧窑的建筑材料和保温材料
3.2 不同种类的燃料及其特点
3.3 燃料的选择和使用
第四章:陶瓷烧制工艺
4.1 陶瓷制作前的准备工作
4.2 陶瓷烧制中的工艺参数和控制方法
4.3 陶瓷烧制过程中的常见问题和解决方法
第五章:烧窑操作和维护
5.1 烧窑的启动和关闭步骤
5.2 烧窑过程中的温度和风速控制
5.3 烧窑维护和保养的方法和注意事项
第六章:安全和环保
6.1 安全操作规程和注意事项
6.2 烧窑过程中的环境保护措施
6.3 废气排放和废弃物处理的方法
第七章:烧窑技术进展和发展趋势
7.1 烧窑技术的新发展和创新
7.2 先进的烧窑设备和控制系统
7.3 陶瓷制作技术和装饰工艺的发展动向
烧窑大师手册提供了从烧窑基础知识到高级技术的全面指导,适合陶瓷爱好者、陶艺学习者和专业陶艺师使用。
它是陶瓷制作过程中的重要参考书籍,可以帮助人们更好地理解和掌握烧制技术,提高作品的质量和艺术价值。
陶瓷烧制工艺说明书
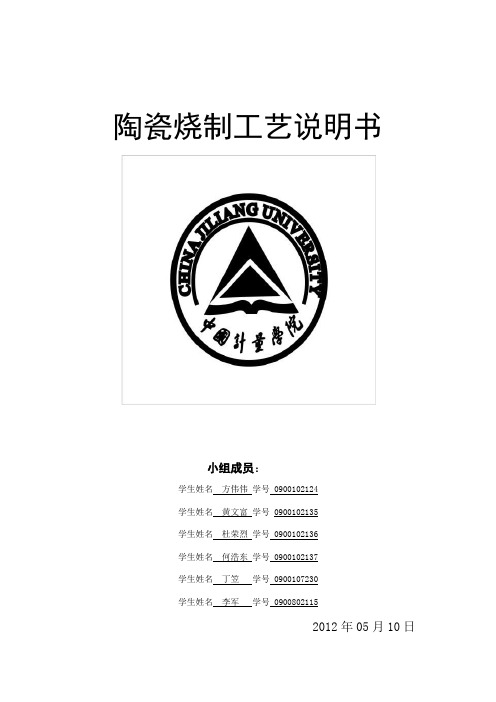
陶瓷烧制工艺说明书小组成员:学生姓名方伟伟学号 0900102124学生姓名黄文富学号 0900102135学生姓名杜荣烈学号 0900102136学生姓名何浩东学号 0900102137学生姓名丁笠学号 0900107230学生姓名李军学号 09008021152012年05月10日目录引言 (1)2陶瓷的传统烧制工艺 (2)3陶瓷的现代烧制工艺3.1陶瓷粉体的制备3.2 陶瓷的烧结3.3 陶瓷的成型3.3.1 注浆成型3.3.2 注浆成型操作注意事项3.4 陶瓷的精加工3.4.1界面反应抛光4结语5参考资料1引言中国是瓷器的故乡,瓷器的发明是中华民族对世界文明的伟大贡献,在英文中“瓷器(china)”与中国(China)同为一词。
大约在公元前16世纪的商代中期,中国就出现了早期的瓷器,经过发展形成了“定,邢,哥,汝,钧”等名噪一时的各类瓷器,其中有些直至今日仍旧享有盛誉。
在物质文明高度发达的现代,瓷器也已经越来越多的朝功能性方面发展,在瓷器的制造过程中,现代机械及工艺也占着越来越重要的戏份。
故而,笔者将秉着传承与发展中华优秀文明的原则,对陶瓷烧制的传统工艺与现代工艺做一简要的论述,以弘扬古朴、典雅的华夏美德。
以下对陶瓷传统与现代制作工艺加以介绍:2 陶瓷的传统烧制工艺传统的陶瓷烧制分工极其细致,最核心的包括拉坯、利坯、画坯、施釉和烧窑等五项工序。
如下:为了能让读者真正了解陶瓷的传统烧制工艺,笔者将从陶瓷原材料的采集到陶瓷成品的整个烧制工艺做简一介绍。
(一)采集瓷石瓷土:瓷器都是以瓷石和瓷土(高岭土)为基本原料烧制而成的。
《天工开物·陶埏篇》说:“土出婺源、祁门两山:一名高梁山,出粳米土,其性坚硬;一名开化山,出糯米土。
其性粢软。
两土相合,瓷器即成。
”所谓糯米土即指高岭土。
高岭土是陶瓷制品的坯体和釉料以及粘土质耐火材料的重要原料。
它是我国瓷都景德镇古代瓷工首先发现并应用的瓷器原料,因为最早发现其产地是江西景德镇以东四十五公里处的高岭村而得名。
陶瓷窑炉烧成技术

陶瓷窑炉烧成技术1、烧成气氛的概念陶瓷产品的烧成气氛是指在烧制的过程中,窑炉内的燃烧产物中所含的游离氧与还原成分的百分比。
一般将烧成气氛分为氧化气氛和还原气氛两种。
游离氧含量在8%以上的称为强氧化气氛,游离氧含量在4%~5%的称为普通氧化气氛,游离氧含量1%~1.5%的称为中性气氛当游离氧的含量小于1%,并且co含量在3%以下时,称为弱还原气氛,co含量在5%以上的称为强还原气氛。
在实际生产中,采用何种气氛制度来烧制陶瓷产品,要根据产品配方中原料的组成以及烧制过程中各阶段的物化反映情况来确定。
当原料中所含有机物和碳较少,且粘性低、吸附性弱、含铁量较高时,适合与还原气氛烧成反之,则适合与氧化气氛烧成。
2、烧成气氛对产品性能的影响众所周知,气氛会影响陶瓷坯体在高温下的物化反应速度、体积变化、晶粒尺寸与气孔大小等,尤其对陶瓷坯的颜色、透光度和釉面质量的影响,更显突出。
①影响铁和钛的化合价在实际生产中,当氧化气氛烧成时,坯料中的fe2o3在含碱量较低的玻璃相中熔解度很低,可析出胶态的fe2o3使坯显黄色当还原气氛烧成时,形成的feo熔化在玻璃相中呈淡青色。
另外,当坯体中的氧化铁含量一定时,若用氧化气氛烧成,被釉层所封闭的fe2o3将有一部分与sio2反应生成铁橄榄石并放出氧,其反应如下:(2fe2o3+2 sio2→2(2feo·sio2)+o2↑)反应生成的氧会使釉面形成气泡与孔洞,而残留的fe2o3会使坯体呈黄色。
对含钛较高的坯料应避免用还原气氛烧成,否则部分tio2会变成蓝至紫色ti2o3,还可能形成黑色2feo·ti2o3尖晶石和一系列铁钛混合晶体,从而呈色加深。
②使sio2还原和co分解在一定的温度下,还原气氛可使sio2还原为气态的sio,在较低的温度下它将按2s io→sio2+si 分解,因而在制品表面形成si的黑斑。
还原气氛中的co在一定的温度下会按2co→co2+c 分解。
陶瓷烧制技术的基本步骤和流程解析

陶瓷烧制技术的基本步骤和流程解析陶瓷是一种古老而重要的工艺品,它在人类历史上扮演着重要的角色。
陶瓷制作的核心是烧制技术,通过高温烧制,将陶土转化为坚硬的陶瓷器物。
本文将介绍陶瓷烧制的基本步骤和流程。
第一步:原料准备陶瓷的原料主要是陶土,陶土的选择对陶瓷的质量和特性有着重要的影响。
不同种类的陶土具有不同的特性,如黏土、瓷土、赤陶土等。
制作陶瓷还需要添加一些辅助材料,如石英、长石等,以改善陶土的塑性和烧制性能。
第二步:成型成型是将陶土按照设计要求塑造成所需的形状的过程。
常见的成型方法有手工成型、轮盘成型和模具成型。
手工成型是最传统的方法,通过手工捏制、揉捏和拉制等方式制作陶瓷器物。
轮盘成型是利用陶轮将陶土旋转成型,可以制作出圆形和对称的器物。
模具成型是利用模具将陶土压制成所需形状。
第三步:干燥成型后的陶瓷器物需要进行干燥处理,以去除其中的水分。
干燥是一个重要的环节,也是制作陶瓷的关键步骤之一。
陶瓷在干燥过程中会发生收缩,如果干燥过快或不均匀,容易导致陶瓷出现开裂等问题。
因此,干燥需要控制得当,通常会分为自然干燥和人工干燥两个阶段。
第四步:修整和装饰干燥后的陶瓷器物需要进行修整和装饰。
修整是指对陶瓷器物表面进行打磨和修整,使其更加光滑和均匀。
装饰是给陶瓷器物添加图案、花纹或采用彩绘等方式进行装饰,以增加陶瓷的观赏性和艺术性。
第五步:烧制烧制是陶瓷制作的核心过程,通过高温烧制,使陶土发生化学和物理变化,形成坚硬的陶瓷。
烧制的温度和时间是关键因素,不同类型的陶瓷需要不同的烧制条件。
常见的烧制方式有电窑烧制、气窑烧制和木炭烧制等。
在烧制过程中,陶瓷器物会经历干燥、失水、胚瓷、成熟等阶段,最终形成成品。
第六步:上釉和再烧烧制完成后,陶瓷器物可以选择进行上釉。
釉料可以改善陶瓷的光泽、强度和耐磨性,同时也可以增加陶瓷的装饰效果。
上釉后的陶瓷器物需要再次进行烧制,以使釉料与陶瓷器物相融合,形成一层坚硬的釉面。
陶瓷烧制技术是一门复杂而精细的工艺,需要经过多个步骤和流程才能完成。
陶瓷坯体的烧成工艺
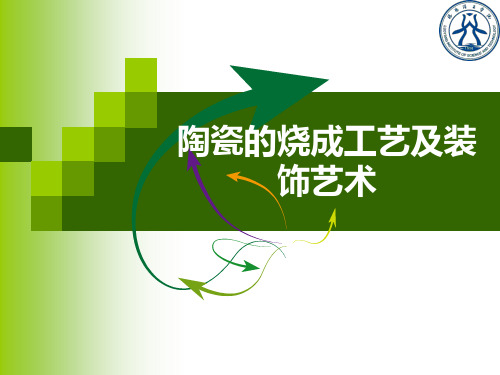
窑具的材质及破坏分析
3)碳化硅质(粘土结合、氧化铝结合、氮化硅结合、再 结晶)
碳化硅导热系数大、热膨胀系数小,使用温度高,可达 1400℃以上
500℃ 时 λ=15.12W/m·K;α=5.57-5.59×10-6/℃ 随着结合方式的优化各种性能进一步提高。 4)熔融石英质 含SiO2 99.5% 时α=0.54×10-6/℃,而且高温粘度大, 高温荷重软化温度也比硅铝质及硅铝镁质窑具高,抗热震 性好, 使用温度可达1380℃。使用过程中转变为方石英,膨 胀破坏。
装钵 坯体装窑时,由于生坯强度低,不能直接堆叠,
而且坯上有釉,如果相互堆叠则烧后会黏在一起。 同时为避免坯体受窑内火焰、灰尘、烟气的污染, 需将坯体装于匣钵内进行烧成。
装窑要求 1、根据窑内温差情况,确定各部位的装窑密度 或产品种类。
高火位密装,低火位稀装;色釉产品根据颜料 耐火情况装。 2、窑具之间、窑具与窑体之间产品之间保持一 定的距离,保证烟气合理流动,传热均匀。窑具 与窑底、窑车面之间有垫砂(垫饼、垫泥、涂层 )防止粘结。 3、叠装牢固平稳,保证在高温下或受到震动等 作用下能够安全运行。 4、在保证安全和产品质量的前提下,减轻窑具 质量,减少窑具用量,提高经济效益。
缓冷 终冷
850~400℃;注意石英相变,冷
却速率不宜过大, 速率为40~
70℃/h; 400℃~室温; 可以快冷,含有大量 方石英的坯体应缓冷,速率可大于 100℃/h;
气氛制度
由烟气中游离氧和还原成分的含量确定
空气过剩系数 a 1/(1 3.76 O2 0.5CO ) N2
强氧化气氛: O2=8~10%, a=1.6~2.5 氧化气氛: O2=2~5%, a=1.2~1.5 中性气氛: O2=1~5%, CO=1~2%, a=0.99~1.05 弱还原气氛: O2<1%, CO=1.5~2.5%, a=0.95 强还原气氛: O2<1%, CO=3~7%, a=0.90
陶瓷工艺学烧成
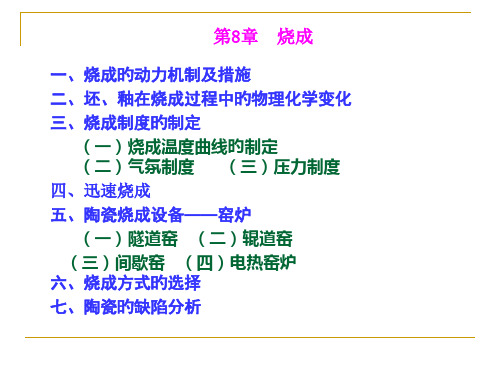
防止了析氧发泡。
(2)FeO与SiO2等形成亚铁硅酸盐,呈淡青旳色调,使瓷器具 有白如玉旳特点。
(3)影响还原气氛旳主要介质是O2,其次是CO和CO2。 还原阶段应尽量使O2旳百分浓度不大于1%或接近零,空
第8章 烧成
一、烧成旳动力机制及措施 二、坯、釉在烧成过程中旳物理化学变化 三、烧成制度旳制定
(一)烧成温度曲线旳制定 (二)气氛制度 (三)压力制度 四、迅速烧成 五、陶瓷烧成设备——窑炉 (一)隧道窑 (二)辊道窑 (三)间歇窑 (四)电热窑炉 六、烧成方式旳选择 七、陶瓷旳缺陷分析
一、烧成旳动力机制及措施 从热力学观点来看,烧成(firing)是系统总能量降低旳过程。 任何体系都有向最低能量状态转变旳趋势,这就是烧成
(二)氧化分解阶段(300~950℃)
其主要反应是有机物及碳素旳氧化、碳酸盐分 解、结晶水排除及晶型转变。坯、釉在这一阶段, 伴随物理化学变化会出现吸热及放热反应。 1. 碳素和有机物旳氧化
坯体中旳碳素和有机物起源于结合粘土。在低 温阶段,因为坯体中碳素和有机物不能充分燃烧, 火焰中往往也具有一定数量旳碳素和一氧化碳。
(一)烧成温度曲线旳制定
烧成温度曲线表达由室温加热到烧成温度,再 由烧成温度冷却至室温旳烧成过程全部旳温度-时间 变化情况。烧成温度曲线旳性质决定于下列原因:
(1)烧成时坯体中旳反应速度。坯体旳构成、原料性 质以及高温中发生旳化学变化均影响反应旳速度。
(2)坯体旳厚度、大小及坯体旳热传导能力。 (3)窑炉旳构造、型式和热容,以及窑具旳性质和装
FeS2+O2 350~ 450ºC
陶瓷加工中的烧成工艺和控制

陶瓷加工中的烧成工艺和控制陶瓷作为一种材料,因其优异的性能而被广泛应用于各种领域。
而在陶瓷加工中,烧成工艺和控制是非常重要的环节。
本文将围绕这一主题展开,从烧成工艺的流程和烧成控制的重要性两个方面进行讨论。
一、烧成工艺的流程烧成工艺是指将制作好的陶瓷制品置于窑炉中进行高温加热,以使其形成一定的结晶和化学反应,从而使其具有硬度、密度、抗压强度等特性。
下面是烧成工艺的详细流程:(1)装罐:陶瓷物品在烧成前需要进行装罐操作,即将其放置于陶瓷器皿中。
装罐的目的在于保护陶瓷物品,以防止其在烧成过程中受到损坏。
(2)上炉:将装罐好的陶瓷物品放入窑炉中,开始进行高温加热。
在上炉之前,需要仔细检查窑炉和陶瓷物品是否满足烧成条件。
(3)烧成:在高温环境下,陶瓷物品进行化学反应和结晶,形成其各种特性。
烧成温度和时间通常是根据陶瓷物品的材质、大小、形状等因素来决定的。
(4)降温:在烧成结束后,需要将陶瓷物品缓慢冷却,使其稳定下来并防止烧裂。
降温过程通常是比较缓慢的。
(5)出窑:陶瓷物品冷却后,可以从窑炉中取出,完成整个烧成工艺。
二、烧成控制的重要性烧成控制是指在整个烧成过程中对温度、气氛、时间等参数进行控制,以保证陶瓷物品的质量和性能。
下面是烧成控制的重要性的几个方面:(1)控制物品颜色:烧成控制可以保证陶瓷物品的颜色一致性和稳定性,避免出现不同批次或不同位置的物品颜色有明显差异的情况。
(2)控制物品尺寸和形状:烧成控制可以确保陶瓷物品尺寸和形状的稳定,避免出现变形或碎裂的情况。
在控制温度和时间时,需要考虑陶瓷物品内外温度差异的影响,同时控制热胀冷缩的效应。
(3)控制物品密度:烧成控制可以在保证物品质量的基础上,控制物品密度的稳定性。
这对于一些特殊应用场合而言尤为重要。
(4)控制烧结和晶化:在烧成过程中,陶瓷物品会发生烧结和晶化过程,而烧成控制可以确保这些过程的均匀性和完整性。
这对于提高陶瓷物品的抗压强度等性能有着非常重要的影响。
瓷砖烧成工艺技术
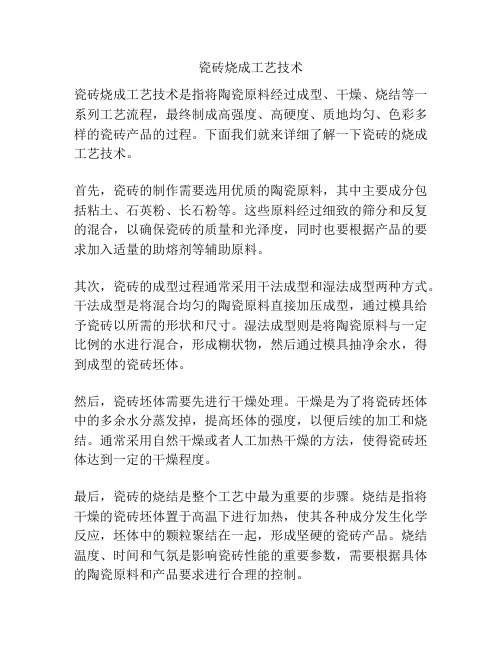
瓷砖烧成工艺技术瓷砖烧成工艺技术是指将陶瓷原料经过成型、干燥、烧结等一系列工艺流程,最终制成高强度、高硬度、质地均匀、色彩多样的瓷砖产品的过程。
下面我们就来详细了解一下瓷砖的烧成工艺技术。
首先,瓷砖的制作需要选用优质的陶瓷原料,其中主要成分包括粘土、石英粉、长石粉等。
这些原料经过细致的筛分和反复的混合,以确保瓷砖的质量和光泽度,同时也要根据产品的要求加入适量的助熔剂等辅助原料。
其次,瓷砖的成型过程通常采用干法成型和湿法成型两种方式。
干法成型是将混合均匀的陶瓷原料直接加压成型,通过模具给予瓷砖以所需的形状和尺寸。
湿法成型则是将陶瓷原料与一定比例的水进行混合,形成糊状物,然后通过模具抽净余水,得到成型的瓷砖坯体。
然后,瓷砖坯体需要先进行干燥处理。
干燥是为了将瓷砖坯体中的多余水分蒸发掉,提高坯体的强度,以便后续的加工和烧结。
通常采用自然干燥或者人工加热干燥的方法,使得瓷砖坯体达到一定的干燥程度。
最后,瓷砖的烧结是整个工艺中最为重要的步骤。
烧结是指将干燥的瓷砖坯体置于高温下进行加热,使其各种成分发生化学反应,坯体中的颗粒聚结在一起,形成坚硬的瓷砖产品。
烧结温度、时间和气氛是影响瓷砖性能的重要参数,需要根据具体的陶瓷原料和产品要求进行合理的控制。
在烧结过程中,还需要注意避免坯体的变形和开裂。
为了降低应力和消除坯体中的内部空隙,可以选择适当的烧结曲线和增加保温时间。
此外,还需要密切关注瓷砖产品的色彩和光泽度,通过合理的材料配比和工艺参数调控,以满足市场需求。
总之,瓷砖烧成工艺技术是一个复杂而精细的过程,需要在原料选用、成型、干燥和烧结等多个环节中进行细致的调控和处理。
只有掌握了瓷砖烧成工艺技术,才能制作出高质量的瓷砖产品,满足人们对建筑装饰材料的要求。
- 1、下载文档前请自行甄别文档内容的完整性,平台不提供额外的编辑、内容补充、找答案等附加服务。
- 2、"仅部分预览"的文档,不可在线预览部分如存在完整性等问题,可反馈申请退款(可完整预览的文档不适用该条件!)。
- 3、如文档侵犯您的权益,请联系客服反馈,我们会尽快为您处理(人工客服工作时间:9:00-18:30)。
江西烧成工艺技术手册目录第一节干燥基础知识在斯米克实际生产过程中,玻化砖使用卧干器等设备对坯体进行烘干,卧干器,通称五层卧干器,每层全长23米,有的企业称之为多层烘道窑一、干燥的作用在斯米克内部,不管是玻化砖还是釉面砖,均采用干压(等静压)成型而成,其坯体所含的水分跟粉料水分基本一致,一般在5~6.5%。
该状态下坯体的强度整体偏低,一般在3~5kg/cm2,不利于长距离的输送,也不利于后续的施釉和直接烧成。
因此干燥的作用就是将坯体中所含的大部分结合水(通俗说,该水不参与粉料内部的结构组成)排出,赋予坯体一定的干坯强度,确保后续的走线传送、修坯及施釉等加工工序要求,也能避免在烧成时由于水分大量汽化膨胀导致砖坯炸裂等缺陷出现。
二、干燥过程如上面所述,干燥过程就是排出坯体内部结合水的过程。
在实际的干燥过程中,一般包含以下四个阶段:1.升速干燥阶段:在该阶段坯体表面首先被加热,外表水分开始逐步的向外排出;2.等速干燥阶段:随着干燥的逐步深入,坯体内部的水分在此阶段顺着坯体内部的毛细孔不断向外排出,程度也较为剧烈,坯体开始出现一定程度的收缩;3.降速干燥阶段:随着干燥的不断进行,坯体内部的水分不断外排,经历过前期的等速干燥阶段后,干燥的速度逐步下降,毛细孔的排水动力逐步减弱,进入降速干燥阶段;4.平衡干燥阶段:此阶段坯体表面排出和吸附处于动态平衡过程,坯体水分不再发生变化,坯体的表面湿度和烘干介质湿度基本一致。
三、干燥收缩与变形随着坯体内部水分的排出,坯体也发生一定的体积变化——收缩。
在整个坯体收缩过程中,因坯料的颗粒具有一定的取向性,导致了干燥收缩的各向异性,这种各向异性导致了坯体内外层及各部分收缩的差异,从而产生内应力。
当这种内应力大于塑性状态坯体的屈服值时,坯体发生变形,若内应力过大,超过其弹性状态的坯体强度,会导致开裂。
影响坯体干燥收缩与变形的主要因素有以下几个方面:1、坯体含水率:含水率越大,干燥后排出的水分越多,收缩越大,容易产生内部应力而导致变形和开裂;2、坯体粉料的级配:由于粉料颗粒级配的不同,粉料的堆积密度就有所差异。
一般说,当坯体粉料的堆积密度越高时,烘干收缩越小,反之,收缩越大3、成型压力:在一定体积内,成型压力越大,坯体致密度越高,收缩越小,当然烘干的速率也会有所下降;反之,坯体收缩越大,烘干速率会有所提高;4、坯体形状:形状越复杂,各向收缩更不均与,内部应力会比较容易集中,更容易产生变形等问题;5、在目前陶瓷墙地砖生产过程中,一般均采用水分在5~8%的粉料进行高压压制工艺,坯体的致密程度都很高,粉料的颗粒大小(级配)也有针对性的控制,堆积密度相对高且稳定,所以在干燥过程中,整体的收缩比较小。
根据斯米克的实际的生产情况,坯体干燥收缩一般在0.1~0.3%。
同时,针对公司部分两次布料的产品,因为工艺的差异,面料和底料的水分存在一定的差异,导致在烘干过程中上下两层粉料之间的收缩存在一定的差异,内部的应力整体相对较大,容易产生开裂和变形(如平整度中凸或中凹现象)四、干燥中容易出现的问题1、开裂:开裂是烘干过程中(尤其是大规格产品,如600*600mm以上)比较容易出现的问题。
针对我们平板砖而言,该问题的产生根源是烘干制度的不合理,特别是在升速干燥和等速干燥阶段,由于表面水分挥发太快,外表面的毛气孔通道容易被堵住,造成内部的水分不易排出,内外应力加大,超过其弹性形变值后,导致开裂发生。
为解决该问题,必须确保在烘干前期,升温速率适当放慢,并保持烘干的环境一定湿度,以平衡表面水平急速排出的情况,确保毛气孔通道的畅通;2、平整度中凸或中凹:该问题在两次布料的产品中较为多见,主要原因面料和底料的水分差异较大,烘干过程中收缩不一致,导致砖坯变形而出现中凸或中凹现象。
在实际操作中,可适当放慢烘干速度,能改善该现象。
最根本的解决方法是要减少面料和基料水分的差异,同时对于可调整上下进风量的卧干器而言,可有差异地对上下进风量进行调整。
3、干坯强度偏低或干坯水分偏高:一般情况下,该问题主要是干坯含水率偏高所致。
按照我们常规的工艺控制,主要干坯水分控制小于0.5%,干坯强度都能维持在13kg/cm2,若水分上升,强度会明显下降,走线过程中容易产生开裂。
4、水滴印:该现象主要发生在冬季。
主要是因为卧干器内部的湿度偏大,外界的冷空气温度偏低,内部的热空气冷却后,凝成水滴粘附与卧干器夹层顶部后成股滴到砖坯表面造成水滴印。
通过调整加大抽湿开度,关闭循环风机冷风口,都能有效改善。
5、其他问题:如大颗粒G系列产品的颗粒边缘开裂,撞角或缺角,表面棍棒印划伤等。
以G系列产品为例。
主要是颗粒料和粉料之间的水分差异,致密度差异、烘干效率差异叠加引发,通常情况下适当放慢烘干速度,有条件时把砖坯反烘,都能有效改善边缘开裂的效果。
五、玻化砖干燥工艺的确定1、卧干器速度的确定:目前,玻化砖卧干器传动都采用变频器控制的方式,速度设置范围在0.37~0.76m/min。
一般情况下,卧干器的速度设置遵循压机产能的原则,满足窑炉产能需求。
根据产品规格、系列和进砖方式等不同,速度设置可有一定的变化2、进砖方式的确定:因设备配置的差异,各个卧干器的进砖方式有所不同。
具体情形见下表(未考虑正烘和反烘);3、温度曲线的确定:与干燥过程四个阶段的基础理论相对应,在温度曲线设置方面,遵循先缓后高最后低的思路,即开始的时候温度设置稍低,中间略高,最后略低的过程,如以下曲线110,130,160,160,130就遵循该过程。
同时从内部环境控制上,确保先高湿度再低湿度的原则,即在干燥的前、中期阶段,卧干器的抽湿开度要尽量小,减少水汽外排,确保干燥介质环境的高温高湿状态,有利于水分的均匀外排,最后在开大开度排湿。
4、风机的设置:除P6窑炉的卧干器外,玻化厂其他窑线的卧干器都采用双流控制的方式,即风机能单独控制,而点烧嘴时必须启用风机。
在生产施釉类产品时,因对坯体温度的特殊要求,一般情况下,夏天时,8#烧嘴启用风机,而在冬天时,8#烧嘴启用燃烧器,以确保各层之间坯温的稳定,满足工艺要求;5、附表:卧干器进砖方式汇总备注:4*2表示每排4片,一次进2排六、卧干器设备基本状态表2第二节烧成基础知识当前,在陶瓷墙地砖生产中,绝大多数企业都采用辊道窑进行烧成。
斯米克集团是国内较早引进全自动进口辊道窑进行生产的企业,有SITI公司,SACMI公司,NERO公司等众多知名品牌。
进几年,随着国内陶机设备制造能力的升级,研发能力的提升,部分品牌达到国外的质量水平,如KEDA,MODENA等一线企业,也被国内众多的陶瓷企业使用。
一、烧成作用烧成是陶瓷产品制造工艺过程中最重要的工序之一。
从广泛的角度来说,烧成过程就是将成形或其表面改良装饰后的坯体在一定条件下进行热处理,经过一系列的物理化学变化,得到具有一定矿物组成和显微结构,达到所要求的理化性能指标的产品。
针对墙地砖生产而言,烧成就是将含有多种天然或合成的矿物原料组成(如粘土,长石、石英等)的坯体,利用特定的窑具(如辊道窑),以天然气、液化气、水煤气或重油等为燃料,在一定的烧成条件下(温度、压力、周期、气氛),经过一系列的物理化学反应,得到具有一定矿物组成、显微结构(如莫来石晶相,微气孔)、特定的理化性能(强度、光泽度、耐磨性、吸水率等)和表面成色效果产品的过程。
二、烧成的主要过程根据窑炉结构和实际生产中曲线设置,以及结合坯体在烧成中经历的各个阶段反应,一般情况下,烧成可分为以下几个过程:1、预热阶段(预热排水阶段):一般在700以下温度进行,该阶段处于强负压状态(相对外界大气压而言),主要是预热坯体,并将坯体内部的结构水进行排除,整个过程属于吸热过程。
一般情况下,该区域的烧嘴不启用,而是通过排烟机的作用,把高温区的温度带过来就能满足要求。
2、预烧阶段(也称氧化分解阶段):一般在800~1100度进行,该阶段仍处于弱负压阶段,原料内部的盐类矿物质(如碳酸盐、硫酸盐)、有机物、络合物开始分解,分解出的二氧化碳,氮气等通过排烟机排出。
该阶段吸热明显,随着矿物质的分解,坯体开始出现一定程度的收缩,在分解后续,部分温度较低的物质(如长石类的助溶剂等原料)开始融化,出现液相。
3、烧成阶段(也称反应烧结阶段):随着液相的不断增多,不同物质成分之间开始反应,并伴随着时间的继续进一步加剧,坯体收缩明显,并呈高温软化状态。
坯体内部的晶相结构逐步形成,内部气孔和间隙不断被填充,直至达到完全玻化状态。
该阶段一般在1200左右完成,根据配方和产品特性的不同,烧成温度和持续时间也有所差异。
就斯米克多数配方和产品而言,该过程一般在8~10分钟。
4、冷却阶段:该阶段包含两个过程,即高温快速冷却过程和低温慢速冷却过程。
快速冷却又称直接冷却,通过风机和管道直接将冷空气吹到坯体表面,坯体温度从最高烧成温度快速下降到570左右,坯体从高温软化状态直接固化,并伴随一定的体积变化。
在实际的控制中,该过程一般在3~4分钟完成。
而慢速冷却又称间接冷却,通过窑炉的抽热风机向外抽热和循环风机热交换实现坯体的缓慢冷却,该过程一般经历20~25分钟结束。
冷却过程对坯体的显微结构和内部应力有巨大的影响。
如果控制不当,坯体容易出现诸如冷裂、变形、脆性大等缺陷,影响正常生产。
三、烧成中容易出现的问题(窑炉本身造成)1、阴阳面:专指窑炉产生的阴阳面。
该问题主要是在烧成过程中,窑内气氛和温度不均匀,温差大,导致坯体反应不同而出现不同成色所致。
多数情况下,窑炉左右边阴阳面较为多见。
根据阴阳面的实际情况,可通过调整窑炉左右两边的空气压力进行调整2、冷裂:冷裂主要是坯体在烧成和冷却过程中,因坯体内部应力过大,超过坯体的极限值后,出现的开裂现象。
根据冷裂产生的情况不同,又分毛口冷裂和光口冷裂。
毛口冷裂主要是坯体在进窑前,表面有隐伤,烧成和冷却后,由于收缩和应力集中的左右,导致出窑后开裂的情况,断面能清楚看到粗糙的状态。
光口冷裂主要发生在慢速冷却过程中。
因窑炉冷却曲线设置的不合理,或窑炉内部实际温差大,导致砖坯在冷却过程中,因坯体内部石英的晶型转化导致内部应力集中,超过坯体的极限值后出现的开裂现象。
该情况一般发生在更换产品砖坯刚出窑阶段,解决办法可提前对慢速冷却区域进行预热处理,减少冷却过程中的温差;或是通过调整冷却曲线,调整抽热的开度等进行处理。
3、翘角和塌角:此处暂不考虑因粉料收缩差异产生的塌角和翘角情况。
就窑炉方面而言,该问题主要由以下两种情况有直接关系:一是砖坯在烧成过程中的走砖不平整。
因陶瓷辊的水平高低差异以及瓷辊在高温状态下的弯曲程度,走砖过程中,砖坯变斜,个边边向靠前或滞后而引发;二是窑内上下温差较大,特别是预烧和烧成区,由于烧嘴熄火或煤空气压力不匹配导致上下温差大,坯体上下收缩差异造成。