OEE-产能分析-培训教程
合集下载
OEE培训资料
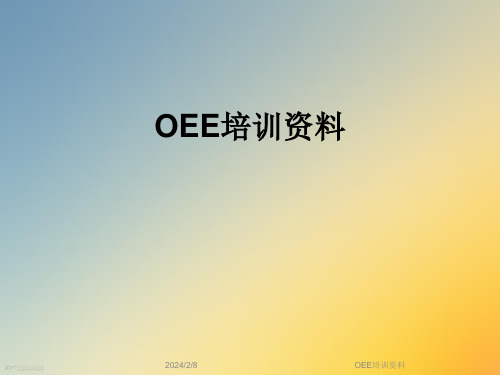
PPT文档演模板
6. 启动稳定的损失 设备从启动到正常工作所需要的时间。
其原因有:
–设备要平缓加速到标准速度 –料筒需升温到设定温度 –去除多余的材料 –处理相关原料O的EE短培缺训资料
重庆光能荣能汽车配件有限公司
3. 设备综合效率的计算
稼动=开动=运转
工作时间 Total operating time A 负荷时间 Loading time
OEE培训资料
重庆光能荣能汽车配件有限公司
设
备
6大损失
设备综合效率的计算公式
工作时间
计
负荷时间
划 损
失
停
稼动时间
止 损
失
性
实 际能
稼动时间 损
失
不
价值稼 良
动时间 损
失
PPT文档演模板
0-1 计 划 停 机 0-2 教育、 早会
① 停工、故障 ② 换装、调整 ③ 空转、瞬停 ④ 速 度 降低 ⑤ 废品、返工 ⑥ 启 动 稳定
2. 设备效率损失的分类
大分类 计划损失 停止损失 性能损失 不良损失
中分类 交班时间/就餐/休息/生产中断/预防维修 设备故障/动力事故/换产/流量不足 流量调节/资材短缺/品质问题
瞬间停止/速度降低/空转
不良/再作业
公司认可的损失
影响OEE 的损失
PPT文档演模板
OEE培训资料
重庆光能荣能汽车配件有限公司
OEE就是用来表现实际的生产能力相对于理论产能的比率,它 是一个独立的测量工具 。
OEE也是一种简单实用的生产管理工具,设备效率指数已成为 衡量企业生产效率的重要标准,也是TPM实施的重要手法之一。
设备综合效率(OEE)是衡量一台设备按计划速度生产出合格产品 的时间占全部时间的百分比.
6. 启动稳定的损失 设备从启动到正常工作所需要的时间。
其原因有:
–设备要平缓加速到标准速度 –料筒需升温到设定温度 –去除多余的材料 –处理相关原料O的EE短培缺训资料
重庆光能荣能汽车配件有限公司
3. 设备综合效率的计算
稼动=开动=运转
工作时间 Total operating time A 负荷时间 Loading time
OEE培训资料
重庆光能荣能汽车配件有限公司
设
备
6大损失
设备综合效率的计算公式
工作时间
计
负荷时间
划 损
失
停
稼动时间
止 损
失
性
实 际能
稼动时间 损
失
不
价值稼 良
动时间 损
失
PPT文档演模板
0-1 计 划 停 机 0-2 教育、 早会
① 停工、故障 ② 换装、调整 ③ 空转、瞬停 ④ 速 度 降低 ⑤ 废品、返工 ⑥ 启 动 稳定
2. 设备效率损失的分类
大分类 计划损失 停止损失 性能损失 不良损失
中分类 交班时间/就餐/休息/生产中断/预防维修 设备故障/动力事故/换产/流量不足 流量调节/资材短缺/品质问题
瞬间停止/速度降低/空转
不良/再作业
公司认可的损失
影响OEE 的损失
PPT文档演模板
OEE培训资料
重庆光能荣能汽车配件有限公司
OEE就是用来表现实际的生产能力相对于理论产能的比率,它 是一个独立的测量工具 。
OEE也是一种简单实用的生产管理工具,设备效率指数已成为 衡量企业生产效率的重要标准,也是TPM实施的重要手法之一。
设备综合效率(OEE)是衡量一台设备按计划速度生产出合格产品 的时间占全部时间的百分比.
生产设备OEE、TEEP培训教材

Effectiveness)设备综合利用率, 用来监控设备在需要它运行时运行
效率如何。
▪ TEEP (Total Effective Equipment Performance) ▪ 设备总生产率
▪ 监控是否最大化的榨取了固定资产的价值
GSE 工厂设备的5类损失
关机损失 未排产时间– (如国家法定节假日, 周六或周日, 无客
GSE 目录
• 什么是OEE、TEEP? • 工厂设备的5类损失 • OEE、TEEP的关系图 • GPC目前对OEE的定义详解 • OEE损失分析步骤 • OEE和Hourly Counts的关联 • OEE使用中的困惑 • OEE的积极性和局限性
GSE 什么是OEE、OPR、TEEP?
▪ OEE (Overall Equipment
净生产时间 完全的生 产时间
GSE OEE、OPR、TEEP关系图
设备总生产率
设备综合利用率
OEE 3类损失 TEEP 5类损失
GSE 如何 计算OEE, OPR and TEEP
计算公式:
ABCD E F
OEE = F / C TEEP = F / A
GSE
GPC目前对OEE定义的详解
GSE GPC目前对OEE的定义详解
ST
Q
RT
AT
AT =
Qty st
Q
RT
AT
= Qt(良品数量) St(标准时间)
RT(计划运行时间)
GSE OEE 的损失分析步骤
Level 1
各线停机的帕拉图
Level 2
分解的帕拉图
按机器分解(如果是一条线) 按原因分解(如果是单机)
Level 3
细节的分解
效率如何。
▪ TEEP (Total Effective Equipment Performance) ▪ 设备总生产率
▪ 监控是否最大化的榨取了固定资产的价值
GSE 工厂设备的5类损失
关机损失 未排产时间– (如国家法定节假日, 周六或周日, 无客
GSE 目录
• 什么是OEE、TEEP? • 工厂设备的5类损失 • OEE、TEEP的关系图 • GPC目前对OEE的定义详解 • OEE损失分析步骤 • OEE和Hourly Counts的关联 • OEE使用中的困惑 • OEE的积极性和局限性
GSE 什么是OEE、OPR、TEEP?
▪ OEE (Overall Equipment
净生产时间 完全的生 产时间
GSE OEE、OPR、TEEP关系图
设备总生产率
设备综合利用率
OEE 3类损失 TEEP 5类损失
GSE 如何 计算OEE, OPR and TEEP
计算公式:
ABCD E F
OEE = F / C TEEP = F / A
GSE
GPC目前对OEE定义的详解
GSE GPC目前对OEE的定义详解
ST
Q
RT
AT
AT =
Qty st
Q
RT
AT
= Qt(良品数量) St(标准时间)
RT(计划运行时间)
GSE OEE 的损失分析步骤
Level 1
各线停机的帕拉图
Level 2
分解的帕拉图
按机器分解(如果是一条线) 按原因分解(如果是单机)
Level 3
细节的分解
OEE产能分析课件(PPT 36张)

14000*12=168000
满足
案例B
生产能力分析报告
供应商:XX公司
产品名称及图号:XX轴
项
目
工
序
磨外径
该工序加工
设备
时间(分钟,计划月 含辅助时间)台套② 次数/月
①
磨床
2件/分钟 24000
月调机时间③
时间/每次 (分钟)
总计时间分 钟(品种*次 数/月*时间/
次)
月设备维 修及停工 待料时间 (分钟)
专线和共线的产能分析,区别在于“产能分配百分比”的计 算,其它分析方法一致
28
产能分析问题交流
对以上内容有任何问题 或您在这方面有更深的体会请提出
共同参与交流
29
钓鱼
1、钓鱼方式 2、赢
30
分享共赢 钓鱼方式
传统钓
矶钓
海钓
冰钓
路亚钓
31
分享共赢 鱼竿种类
•
15、只有登上山顶,才能看到那边的风光。
•
16只会幻想而不行动的人,永远也体会不到收获果实时的喜悦。
•
17、勤奋是你生命的密码,能译出你一部壮丽的史诗。
•
1 8.成功,往往住在失败的隔壁!
•
1 9 生命不是要超越别人,而是要超越自己.
•
2 0.命运是那些懦弱和认命的人发明的!
•
21.人生最大的喜悦是每个人都说你做不到,你却完成它了!
•
3、当你还不能对自己说今天学到了什么东西时,你就不要去睡觉。 ——利希顿堡
•
4、人天天都学到一点东西,而往往所学到的是发现昨日学到的是错的。 ——B.V
•
5、学到很多东西的诀窍,就是一下子不要学很多。 ——洛 克
经典OEE培训教材

• 应对措施
– 了解损坏的原因及发生的时间和地点,然后运用根源问题解决 办法来解决
– 使用SMED技术来减少甚至消除设置调整的必要,并实现标准 化的第一轮通过流程
– 如果因为进线部件和原材料的变化而导致损坏,从而需要进行
调整来补偿就要建立部件质量拒收的限制,并使供应商质量管
理也参与到此管理流程
12
6. 质量缺陷
16
质量缺陷
计划外停 机
机器故障
速度下降
换线
损坏
4
OEE计算 – 模型
可编辑
六种重大损失降低机器效能说明
一班总工作时
可使用总工时
操作时间(停工时间 损失)
机器运转时间 (速度损失)
增值 (缺陷损失)
* 计划内停工排除在OEE计算之外
计划内停工*
机器故障 换线 计划外停工 速度降低 损坏 质量缺陷
可用时间 = (可使用总工时) - (窝工时间损失) (可使用总工时)
• 由PLC控制器衡量
• 应对措施 – 明确实际设计速度,最大速度,以及造成速度受限的物理原因 – 请工程人员进行程序检查并进行修改 – 应用Machine Kaizen来查找低速的原因并对设计速度提出质 疑
11
5. 损坏
可编辑
• 定义:工艺处理流程中,即“线上”即被查出的部件
• 由手写废品记录登记测量(注:假设每个部件的损坏造成生产该 部件全部时间的损失,从而将损坏部件数量转化为时间损失)
• 除机器故障或换线的所有计划 管理 外的停产 • 问题根源解决方法
• 由于机器运行速度较设计速度 慢而造成的时间损失 • 问题根源解决方法
• 在组装或调整中的损坏部件 • 问题根源解决方法
oee培训ppt课件
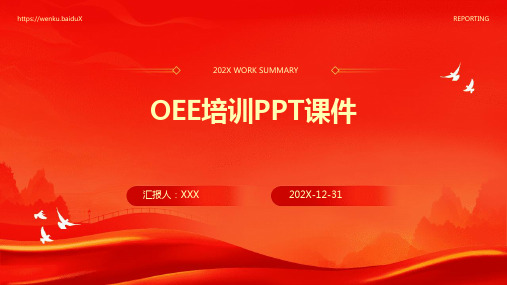
RY
OEE培训PPT课件
汇报人:XXX
202X-12-31
REPORTING
目录
• OEE基本概念 • OEE的重要性和影响 • 如何提高OEE • OEE的监控与改进 • OEE的未来人和时间节点,确保措施的 有效执行。
对改进措施进行风险评估和经 济效益分析,确保措施的公道 性和可行性。
跟踪改进效果
实施改进措施后,持 续监测OEE数据的变 化情况,评估改进效 果。
根据跟踪结果,及时 调整和优化改进措施 ,持续提高OEE水平 。
对改进效果进行统计 分析和可视化展示, 便于团队成员了解改 进成果。
下落生产成本
提高装备效率可以下落生产成本,因为装备效率的提高意味 着生产进程中所需的人力和物力资源更少,能源消耗更低, 从而下落了生产成本。
OEE培训可以帮助员工更好地掌握成本控制的方法和技能, 通过优化生产流程、减少浪费等措施,进一步下落生产成本 。
提升产品质量
01
装备效率的提高可以提升产品质 量,因为装备的稳定高效运行可 以减少产品缺陷和不良品率。
PART 04
OEE的监控与改进
OEE数据收集与整理
确定数据收集的指标
根据装备特点和生产要求,确定需要收集的OEE指标,如开机率 、故障率、准备时间等。
制定数据收集计划
确定数据收集的时间间隔、采集人员和采集方式,确保数据的准确 性和实时性。
数据整理与存储
对收集到的数据进行整理、分类和存储,便于后续的分析和查询。
备用装备
配备备用装备,在主装备故障时,能 够迅速切换到备用装备,保证生产连 续性。
提高操作员技能
培训教育
定期对操作员进行技能培训和安 全教育,提高操作员的专业素养
OEE培训PPT课件
汇报人:XXX
202X-12-31
REPORTING
目录
• OEE基本概念 • OEE的重要性和影响 • 如何提高OEE • OEE的监控与改进 • OEE的未来人和时间节点,确保措施的 有效执行。
对改进措施进行风险评估和经 济效益分析,确保措施的公道 性和可行性。
跟踪改进效果
实施改进措施后,持 续监测OEE数据的变 化情况,评估改进效 果。
根据跟踪结果,及时 调整和优化改进措施 ,持续提高OEE水平 。
对改进效果进行统计 分析和可视化展示, 便于团队成员了解改 进成果。
下落生产成本
提高装备效率可以下落生产成本,因为装备效率的提高意味 着生产进程中所需的人力和物力资源更少,能源消耗更低, 从而下落了生产成本。
OEE培训可以帮助员工更好地掌握成本控制的方法和技能, 通过优化生产流程、减少浪费等措施,进一步下落生产成本 。
提升产品质量
01
装备效率的提高可以提升产品质 量,因为装备的稳定高效运行可 以减少产品缺陷和不良品率。
PART 04
OEE的监控与改进
OEE数据收集与整理
确定数据收集的指标
根据装备特点和生产要求,确定需要收集的OEE指标,如开机率 、故障率、准备时间等。
制定数据收集计划
确定数据收集的时间间隔、采集人员和采集方式,确保数据的准确 性和实时性。
数据整理与存储
对收集到的数据进行整理、分类和存储,便于后续的分析和查询。
备用装备
配备备用装备,在主装备故障时,能 够迅速切换到备用装备,保证生产连 续性。
提高操作员技能
培训教育
定期对操作员进行技能培训和安 全教育,提高操作员的专业素养
OEE培训讲义PPT课件

花了30分钟,设备中途故障与修复总时间为15分钟。(B=A-30-15=460-3015=415) • 请计算这一班的Availability.(Availability=415/460=0.90)
第10页/共16页
的计算---Performance性能稼动率
第11页/共16页
Performance的计算练习C
OEE
第2页/共16页
1.设备关连损失
• Availability (时间) • Performance (性能) • Quality (品质)
• Availability: Downtime Losses – 停机损失 • Breakdowns – 故障 • Setup Time – 工程变换与调整 • Performance: Speed Losses – 速度损失 • Minor Stoppages – 小停止 • Reduced Operating Speed – 速度低下 • Quality: Defect Losses – 不良损失
• Scrap and Rework – 报第废3页与/共重1工6页
的定义
第4页/共16页
的组成及其计算
第5页/共16页
I.OEE 的组成
第6页/共16页
挂图
第7页/共16页
的损失结构图
第8页/共16页
的计算---Availability时间稼动率
第9页/共16页
Availability的计算练习
第14页/共16页
结束语:
谢谢大家
第15页/共16页
感谢您的观看!
第16页/共16页
• Availability = B / A • [练习] • 某公司每班上班总时间为540分钟,其中用餐时间与休息为60分钟,上班前的交
第10页/共16页
的计算---Performance性能稼动率
第11页/共16页
Performance的计算练习C
OEE
第2页/共16页
1.设备关连损失
• Availability (时间) • Performance (性能) • Quality (品质)
• Availability: Downtime Losses – 停机损失 • Breakdowns – 故障 • Setup Time – 工程变换与调整 • Performance: Speed Losses – 速度损失 • Minor Stoppages – 小停止 • Reduced Operating Speed – 速度低下 • Quality: Defect Losses – 不良损失
• Scrap and Rework – 报第废3页与/共重1工6页
的定义
第4页/共16页
的组成及其计算
第5页/共16页
I.OEE 的组成
第6页/共16页
挂图
第7页/共16页
的损失结构图
第8页/共16页
的计算---Availability时间稼动率
第9页/共16页
Availability的计算练习
第14页/共16页
结束语:
谢谢大家
第15页/共16页
感谢您的观看!
第16页/共16页
• Availability = B / A • [练习] • 某公司每班上班总时间为540分钟,其中用餐时间与休息为60分钟,上班前的交
OEE培训PPT课件
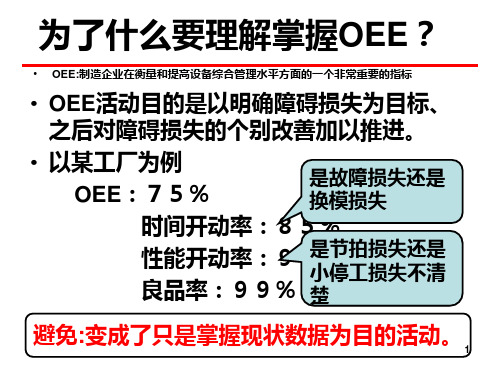
O P3
所有设备的加工没有完成、
O P2
零件不会移动到下一个设备
瓶颈工序决定节拍
O P1
加工時間 待ち 搬送
例)把多台机械加工设备用传送带来连接的生产线
OP3
B
OP2
OP1
A
应该主要针对瓶颈工序 进行OEE管理。
OP1 OP2 OP3
生产线全体
更换零件
14秒 14秒 18秒
加工时间 计划节拍 停工待料
分
时间开动率
分
性能开动率
分
生产外时间
分
良品率
100% 分
计划停止
分
OEE
分 停止损失
%
分速度损失
%
分 分
1.故障停止损失 2.工艺调整损失 3.模具交换损失
不良损失
分
4.小停工损失
5.速度低下损失
6.不良・返修损失
7.启动的损失
% % % %
分
%
分
%
分
%
分
%
分
%
分
%
分 14 %
六大损失分析(详解)
负荷时间-停止时间
*时间开动率=
负荷时间
理论周期×产量 *性能开动率= 生产时间
O 生产时间为实际生产时间
产量-不良数
*良品率=
产量
负荷时间・停止时间・理论周期・产量・不良数知道的话就能够计算3
OEE?(来看看损失的构成!)
上班时间
负荷时间 开动时间
计划停止(计划保养・生产停止・
早晚班会・吃饭休息・)
零件A (孔大)
零件B (孔小)
<夹紧装置的触动调整化>由Biblioteka 是长形孔位置不易确定触 动 化
OEE培训教材资料
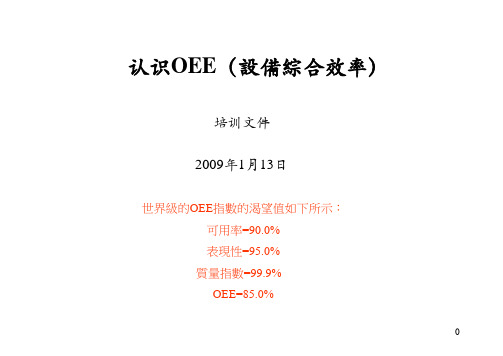
2、分析說明
根據OEE系統所提供的資料,你可以方便的知道自己工廠存在什麼問題,例如, 如果你的可用率在某一個時間段很低,說明在六大損失中和OEE可用率損失有關的 故障太多,那麼,顯而易見,你應該把改善重點放在這些方面了!同樣,如果質量 指數或者生產率導致你的OEE水準降低,那麼你就應該把目光放在和它們有關的問 題點上。在表一中,我們只列舉了一些事件原因,其實它可以包括和生產有關的任 何方面,因此,你可以對生產做到全面的管理和改善。
設備預熱,調試等生產正式運行之前產 • 问题根源解决方法 生的次品 生產穩定進行時產生的次品
■
• 问题根源解决方法
十三、使用OEE时的注意事项
!
!
• OEE要应用在一台机器上(可视为一台机器的生产线) 而不能应用在整个生产线或全厂上,这样才有意义
• OEE要作为一系列一体化的综合关键业绩指标中的一部 分来运用而不能孤立使用,否则将造成生产批次规模加大 或有质量缺陷的产品 • OEE必须与精益原则相符,要确保对OEE的计算不会导 致浪费合理化、制度化,例如,绝不要允许给换线留出 时间
理系統。
2、能分析/跟蹤生產線設備的有效利用情況,以便最大
化挖掘設備生產潛力。
3、能分析/跟蹤產線上的潛在風險和六大損失,以便降
低生產成本、提高生產力。
4、能為企業精益生產管理提供可視化的生產報告。 設備:降低設備的故障以及維修成本,加強設備管理以延長設備 的使用壽命。 員工:通過明確操作程式和SOP,提高勞動者的熟練程度和有效 工作業績,從而 提高生產效率。 工藝:通過解決工藝上的瓶頸問題,提高生產力。 質量:提高產品直通率(FTT),降低返修率,減少質量成本,
认识OEE(設備綜合效率)
培训文件 2009年1月13日
设备管理OEE培训课件

是用停机时间反映设备的运行状态。统计时间开动率主要是严格区分设备计 划内停机时间与设备计划外停机时间,并通过减少和控制设备计划停机时间 来提高设备利用率,通过减少和控制设备计划外停机时间来提高时间开动率。
计划停机时间
=日常维护保养时间+交接班时间+一级保养时间+换模试模时间+计划维修时 间+达产的停机时间+其它计划中规定的时间
负荷时间
用餐 时间
(有效)利用时间
停机损失
净利用时间ຫໍສະໝຸດ 表现损失创造价值 缺陷 的时间 损失
1.故障 2.更换品种 / 清洁
/ 调节 3.启动 / 停机(故障、 调整)
时间利用率
4.小停机 / 空转 5.速度损失
6.质量缺陷返工
设备性能率
产品合格率 3
OEE计算模型
六种重大损失降低机器效能说明
每周总工作时间 7*24 hours = 168
空闲和暂停损失(Idling and Minor Stoppage Losses)
- 误操作而停顿或机器空闲时发生短暂停顿而产生这种损失。例如,有 些工件阻塞了滑槽顶端,导致了设备空闲,很明显,这种停顿有别于 故障停工,因为除去阻塞的工件和重新启动设备即可恢复生产。
7
异常停机-2
质量缺陷和返工(Quality Defects and Rework)
15
感谢大家的参与,谢谢!
THANK YOU !
16
中国员工有几个不好的习惯; 一、做事随意,没有规矩; 二、有了规矩,弄虚作假,不守规矩; 三、遵守规矩,却总是做不到位。
12
希望你关注OEE
做好记录,查找/整改出现问题 统计OEE 每天自动生成三率 每月我们将集中反馈
计划停机时间
=日常维护保养时间+交接班时间+一级保养时间+换模试模时间+计划维修时 间+达产的停机时间+其它计划中规定的时间
负荷时间
用餐 时间
(有效)利用时间
停机损失
净利用时间ຫໍສະໝຸດ 表现损失创造价值 缺陷 的时间 损失
1.故障 2.更换品种 / 清洁
/ 调节 3.启动 / 停机(故障、 调整)
时间利用率
4.小停机 / 空转 5.速度损失
6.质量缺陷返工
设备性能率
产品合格率 3
OEE计算模型
六种重大损失降低机器效能说明
每周总工作时间 7*24 hours = 168
空闲和暂停损失(Idling and Minor Stoppage Losses)
- 误操作而停顿或机器空闲时发生短暂停顿而产生这种损失。例如,有 些工件阻塞了滑槽顶端,导致了设备空闲,很明显,这种停顿有别于 故障停工,因为除去阻塞的工件和重新启动设备即可恢复生产。
7
异常停机-2
质量缺陷和返工(Quality Defects and Rework)
15
感谢大家的参与,谢谢!
THANK YOU !
16
中国员工有几个不好的习惯; 一、做事随意,没有规矩; 二、有了规矩,弄虚作假,不守规矩; 三、遵守规矩,却总是做不到位。
12
希望你关注OEE
做好记录,查找/整改出现问题 统计OEE 每天自动生成三率 每月我们将集中反馈
OEE培训教材(ppt44张)

时
间
5大人力损失
11 12 13 14
3大原材料与能源损失
成
15 16
本
我们的近邻联合利华世界500强在经过近10年的OE 的管理,2010年才从12大损失向16大损失迈进。
其中它是先做6大损失到9大损失到12大损失不断的摸索 才有今天的成绩。数据显示联合利华洗衣粉的产量从2004 日产260T/D到2010年日产近1000T/D。其中生产机器只增 了50%。在OEE的数据支撑下结合一些优良的管理方法再 加上公司员工的群策群力下设备的效率平均提高了48.6%
…
OEE 表格
原来 修改制作 在修改的
你会选择那种表?
中国员工的画像
海尔总裁张瑞敏关于人的品质有一段精彩的论述; “如果训练一个日本人,让他每天擦六遍桌子,他一定 会这样做;而一个中国人开始会擦六遍,慢慢觉得五遍 四遍也可以,最后索性不擦了”,“中国人坐事最大毛 是不认真,做事不到位,每天工作欠缺一点,天长地久 成为落后的顽症”。
OEE表的填写标准
上班第一时间填写OEE表上的日期、班次 、机器号、包装机、设定速度 开班清理、点检、润滑后填写开停车时间 开机至机器正常运行时填写试车时间 运行过程中出现如故障、小停机调整等填 写相应项,吃饭停机后要填写吃饭时间 不得提前填写或推迟填写
【OEE】要注意的问题
设备综合效率 = 时间利用率 * 设备性能率 * 产品合格率
1. 时间利用率 = (负荷时间 - 停机损失) / 负荷时间 * 100%
2. 设备性能率 = 生产产品数 / (利用时间 * 设计速度) * 100
3. 质量缺陷率 = (生产产品数 - 不合格品) / 生产产品数 * 1
TPM与PAMCO OEE的差别
OEE、MTBF--MTTR培训ppt课件

OEE= 0.87 X 0.6 X 0.98
理论周期时间为0.6分/个, OEE= 51.2%
实际周期时间为0.8分/个, 分析:
一天的产量是400个,
透过OEE看企业的浪费与改善潜力
其中废品有8个,
1,主要损失在哪里?
请计算出设备的综合效率
2,各是多少 ? OEE、MTBF--MTTR培训
2
世界级设备维护管理水平标杆
生产运 行情况
运行时间 3 个月
维修时 间1天
运行时间 5 个月
运行时间
运行时间
维修时 2个月 维修时 2个月
间½ 天
间¼ 天
时间
术语
MTBF MTTR
定义 -故障间隔平均时间,设备在发 生故障前正常运行的平均时间 -平均维修时间,维修某设备平
均所需时间
示例 (3 + 5 + 2 + 2) / 3= 4个月 (1 + ½ + ¼) / 3 = 0.6 天
OEE、MTBF--MTTR培训
5
7-1 设备维护活动的考核评价指标
◆ 信赖性:平均故障间隔时间(MTBF) ◆ 保全性:平均修理时间( MTTR)
OEE、MTBF--MTTR培训
6
表示设备信赖性的指标
① MTBF (Mean Time Between Failure) : 平均故障间隔时间
驱动时间的合计 = 停止回数 (件数) =
2.平均修理时间分析
35+40+42+46+36+30+32+28+25+26+22+23 385
MTTR=
=
生产管理中的OEETEEP培训讲课文档

第七页,共20页。
GPC目前对OEE定义的详解
第八页,共20页。
GPC目前对OEE的定义详解
设备综合效率 OEE (Overall Equipment Effectiveness) 是基于设备来衡量人机系统
及其运行结果的综合绩效指标。
OEE = 时间利用率(A) 生产效率(P) 产品合格率(Q)
产品合格率 (Quality factor - Q) 如果50件产品中,有2个废品,则:
产品合格率 Q = (50-2)/50 = 96.0%
设备综合效率:
OEE = 85.7% * 83.3% * 96.0%
= 68.5%
设备总生产率: TEEP = 68.5% * 87.5%
= 59.9%
第十三页,共20页。
…
速度损失 小停顿, 速度减慢,
…
质量损失 报废 – 返工 …
操作时间
净生产时间
完全的生 产时间
第五页,共20页。
OEE、OPR、TEEP关系图
设备总生产率
第六页,共20页。
设备综合利用率
OEE 3类损失
TEEP 5类损失
如何 计算OEE, OPR and TEEP
计算公式:
AB CD E F
OEE = F / C TEEP = F / A
各线停机的帕拉图
Level 2
分解的帕拉图
按机器分解(如果是一条线) 按原因分解(如果是单机)
(Perf Loss)
产品合格率 Quality Factor (Q) 质量损失
(Quality Loss)
第十一页,共20页。
GPC目前对OEE的定义详解
计划率 (Planning Factor - PF)
设备OEE培训PPT课件
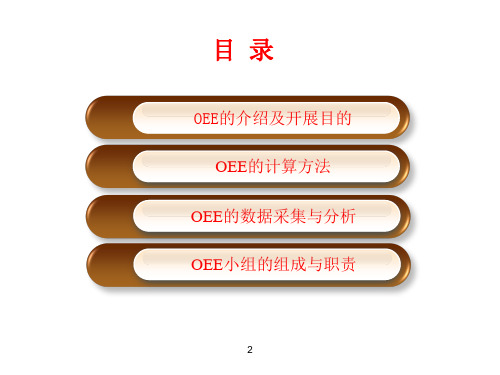
一工厂金工 OEE组长:黄元林
项目责任人 胡楚平
二工厂金工 OEE组长:宋秋阳
一工厂检包 OEE组长:金钱有
19
二工厂检包 OEE组长:刘银火
OEE车间小组结构图
OEE副组长 车间副主任
OEE专员
OEE组员 工程师、领班
1.组长负责整个OEE工作落 实
2.副组长、主管工程师负责 工艺分析与改进方案实施
2.每周进行数据汇总, 分析时间利用率、设 备性能率、产品合格 率指数,找出对应设 备损失
提升步骤
3.针对各项损失做出 改进方案,及时落实 工作
17
四、OEE小组的组成与职责
万丰摩轮设备OEE项目组织结构图
一工厂综合 OEE组长:徐亚忠
一工厂熔铸 OEE组长:张剑辉
二工厂熔铸 OEE组长:陈国云
时间开动率=
* 100%
负荷时间
停
可利用时间
止 损
失 2.空转、间
速
歇停顿
真正利用时间
度 损
失
1.废品、返工
创造价值的
不 良
2.启动、开机
运转时间 损
失
理论循环时间*加工数量
性能开动率=
利用时间
* 100%
加工数量-不合格数量
合格率 =
* 100%
加工数量
10
OEE案例
设某设备某天工作时间为8h, 班前计划停机15min, 故 障停机30min,工装调整25min, 产品的理论加工周期 为0.6 min/件, 一天共加工产品450件, 有20件不合格, 求这台设备的OEE? 根据上面可知: 计划运行时间 =8 x 60 -15 =465 (min) 实际运行时间 =465-30-25=410 (min) 时间开动率 =(410/465)*100%=88.1% 性能开动率 =(450*0.6)/410*100%=65.8% 合格品率 =(450—20)/450*100%=95.5% OEE = 时间开动率x性能开动率x合格品率=55.4%
OEE培训[1]
![OEE培训[1]](https://img.taocdn.com/s3/m/a6d1d39948649b6648d7c1c708a1284ac85005cc.png)
损失
解决方案
处理6大OEE损失
废品
产品或服务未达到制定的生产规范或客户要求
通过防误措施消除问题源 人工自动化(停止生产线,辨识和呼叫)-授权工人在发生意外情况或发现问题时,停止生产线
返工
产品需要非标准操作,以满足客户的规范要求(例如,产品在生产过程中损坏,需要维修)
损失
解决方案
OEE用作测量能力的方法
OEE
0.78
0.70
0.45
0.48
0.77
0.75
有效生产交期* (秒) (秒)
观测的 周期 生产交期
由于OEE损失导致生产交期调整
日程
整体设备效率(OEE) 什么是OEE? OEE计算 OEE的优点 结论 附录:OEE练习
主要着重点
OEE是一种监控和改进生产流程的有效性的有用的方法* OEE使我们可以清楚地看见六大主要生产能力损失: 停机 换模 轻微停机 速度降低 废品 返工 多个TEOA工具用作OEE的改进杠杆
OEE培训
学习目标
本课程结束时,您将学会: 解释确定整体设备效率(OEE)的目的 描述计算OEE时的步骤 理解OEE如何作为TEOA的一部分帮助推动绩效
日程
整体设备效率(OEE) 什么是OEE? 计算OEE 将OEE与绩效联系起来 结论 附录:OEE练习
什么是OEE?
定义:一种车间的工具,用于测量生产设备的运行状况,并与理论目标进行对比。
基于时间OEE =部件的理论生产数量部件的实际生产数量
基于部件
* 取决于时间和(或)部件数据的可用性
计算OEE – 范例
可用性 =
预计的 生产时间 生产时间
操作时间
480分钟
360分钟
解决方案
处理6大OEE损失
废品
产品或服务未达到制定的生产规范或客户要求
通过防误措施消除问题源 人工自动化(停止生产线,辨识和呼叫)-授权工人在发生意外情况或发现问题时,停止生产线
返工
产品需要非标准操作,以满足客户的规范要求(例如,产品在生产过程中损坏,需要维修)
损失
解决方案
OEE用作测量能力的方法
OEE
0.78
0.70
0.45
0.48
0.77
0.75
有效生产交期* (秒) (秒)
观测的 周期 生产交期
由于OEE损失导致生产交期调整
日程
整体设备效率(OEE) 什么是OEE? OEE计算 OEE的优点 结论 附录:OEE练习
主要着重点
OEE是一种监控和改进生产流程的有效性的有用的方法* OEE使我们可以清楚地看见六大主要生产能力损失: 停机 换模 轻微停机 速度降低 废品 返工 多个TEOA工具用作OEE的改进杠杆
OEE培训
学习目标
本课程结束时,您将学会: 解释确定整体设备效率(OEE)的目的 描述计算OEE时的步骤 理解OEE如何作为TEOA的一部分帮助推动绩效
日程
整体设备效率(OEE) 什么是OEE? 计算OEE 将OEE与绩效联系起来 结论 附录:OEE练习
什么是OEE?
定义:一种车间的工具,用于测量生产设备的运行状况,并与理论目标进行对比。
基于时间OEE =部件的理论生产数量部件的实际生产数量
基于部件
* 取决于时间和(或)部件数据的可用性
计算OEE – 范例
可用性 =
预计的 生产时间 生产时间
操作时间
480分钟
360分钟
OEE内训教材

10
OEE定义
公式推导
数据收集
数据分析
案例分析
§造成设备速度降低的时间类别
瞬间停止、空转:传送装置上的产品阻塞或者工作台上的加工品挂住的情况,或 检查装置自动停止的时间(故障和导致问题发生原因的清除、插入、开关ON等简 单操作初始化的恢复)
生产线不均衡:前、后生产(或者前、后设备)中由于别的因素引起的作业停止 或者担当设备后加工的生产数量或者目标量已达成而停止情况的时间
17
§八大损失的改善目标
OEE定义
公式推导
数据收集
数据分析
案例分析
§第一大损失:计划性停机损失 ※此类停机包括节假日、会议、年修、定修等,并且 很多企业对 在保证设备正常运转的前提下,如何缩短甚至取消部分项目缺少 足够的重视和研究. 应对措施: (1)充分认识大修等项目一样导致生产停机损失,逐步采用项修和 局部维修代替大修; (2)过多的大修降低了设备可靠性,增加故障隐患.
数据收集
数据分析
案例分析
§哪些应归类于休止时间? (6)休止时间:作业时间中由于设备的非开动而引发的损失时间(与设备的机能无关 停止的时间) 年修、定修计划:年度的维修计划而设备停机时间 假日、会议、早会:作业中因假日或必需的会议及早会而使设备停止的时间 (例:节日、月例早会、参加活动、车间、班长早会、小组)
高损坏率
产品生产线换线时间长
频繁故障
计划外停机
产品质量低下
运行缓慢
6
OEE定义
公式推导
数据收集
数据分析
案例分析
OEE定义
公式推导
数据收集
数据分析
案例分析
output 产出工时
合格品数×标准工时
OEE Training分析PPT课件

设备负荷时间 设备开动时间
Planned Production Time(计划生产时间)(ex: 2x8shifts/230 days per year)
Not working hours 非工作时间
Operating Time(操作时间) (计划生产时间—计划测试及欠单停班时间)
清洁,点检 - -预防性维护- -周期性维护 - -会议,休息,培训
12
OEE定义
1,Overall Equipment Effectiveness (设备综合效率)的缩写,
2,由 时间开动率 、性能开动率 以及合格品率 三个关键要素组成
11/14/2020 Title of presentation
13
休息时间
11/14/2020 Title of presentation
生产出的2个 1个合格,一个不良
时间开动率=50%
性能开动率=50% 合格品率=50%
OEE = 50% X 50% X 50% = 12.5%
1 / 8 = 12.5 %
假设效率全部为1,实际开动2小时,4/小时,全部是合格品 合格品=?
11/14/2020 Title of presentation
时间损失
3. 空转和瞬间停机的损失 由于小问题引起的短暂中断。其原因有: -零件卡在滑道里 -清除碎屑 -感应器不工作 -软件程序出错
性能损失
11/14/2020 Title of presentation
4. 降低速度的损失 设备在低于其标准设计速度运行导致的损失。其原
因有: –机器磨损 –人为干扰 –工具磨损 –机器过载
14
OEE定义
1,Overall Equipment Effectiveness (设备综合效率)的缩写,
相关主题
- 1、下载文档前请自行甄别文档内容的完整性,平台不提供额外的编辑、内容补充、找答案等附加服务。
- 2、"仅部分预览"的文档,不可在线预览部分如存在完整性等问题,可反馈申请退款(可完整预览的文档不适用该条件!)。
- 3、如文档侵犯您的权益,请联系客服反馈,我们会尽快为您处理(人工客服工作时间:9:00-18:30)。
33
分享共赢
钓鱼的好处
1、钓鱼可以修心养性,陶冶情操; 2、钓鱼时水面开阔,空气清新,有益身体健康; 3、钓鱼可以缓解情绪,适于放松工作压力。 4、可以锻炼自己的耐心。 5、鱼儿上钩时的兴奋,可以使自己有一个好心情。 6、享受新鲜的美味。
34
考试
填写一份产能分析报告(阶段3)
解答: 1、请验证各工序实际OEE? 2、产能是否满足客户要求? 3、如果不满足,您是公司总经理,你会如何改善?
10
11
世界制造业OEE指数
12
13
OEE六大损失 机器故障 速度损失 开停机 切换 小停机
14
质量缺陷
什么是六大损失
15
你不可能在设备故障停机时生产出产品
16
设置和调整占用了太多的时间
17
一个微小的问题就会造成设备的停机
18
设备运转过快容易造成故障
19
您是不是正在制造一个不合格产品
PPAP阶段3(产能验证) --完成时机:量产爬坡阶段。固定时间,计算产出,满足客 户订单为目的
27
产能分析两种因素
专线设备生产 共线设备生产
专用设备: 指该设备仅用于本工作表中分析的那个零件。 共享设备: 指在该设备上会制造很多不同的零件,且具有更长的工具切换时间 举例: · 冲压设备 · 压铸机 · 热处理设备 专线和共线的产能分析,区别在于“产能分配百分比”的计 算,其它分析方法一致
100%
负荷时间 价值开动时间 多少%
OEE是什么?(来看看组成!)
7
OEE如何计算?
OEE(设备综合效率) =时间开动率×性能开动率×良品率
时间开动效率= 负荷时间-停止时间 负荷时间
*负荷时间=日历工作时间-计划停机时间
计划节拍×产量 性能开动效率= 开动时间 产量-不良数 产量
*开动时间=负荷时间-停止时间
生产能力分析报告
案例B
生产能力分析报告
供应商:XX公司
项 工
产品名称及图号:XX轴
月设备维 需设备 总计时间分 修及停工 数(台 时间/每次 钟(品种*次 待料时间 /月) (分钟) 数/月*时间/ (分钟) ⑤ ④ 次) 月调机时间③ 生产其 他产品 占用该 设备台 数⑥ 现有该 设备富 工序加 有台数 瓶颈工序 工设备 ⑧=⑦数⑦ ⑤-⑥
35
Thank you for your attention!
谢谢!
20
早晨机器的启动需要花去一定的时间
21
22
23
产能分析最佳时机
工装样件节拍生产时 PSW产能验证时
工艺、设备改进后
24
您可能见过的产能分析报告
案例A
供应商:XX有限公司
产品图号名称 AA 年需求量 150000 瓶颈工序 磨外圆 班产量 500 月产量 500*28=14000 年需求量 14000*12=168000 结论 满足
OEE-产能分析-培训教程
2014-12-26
手机请打到静音 会议上不要接电话
培训前确认事项
您清楚供应商的生产过程 您准备了笔记本电脑
3
OEE的定义 _
设备综合效率
4
OEE是什么?(看看来源!)
5
OEE是什么?(来看看损失的构成!)
在负荷时间中多大程度 上尽可能没有浪费、而 生产出好产品呢?
5
目 序
该工序加工 时间(分钟,计划月 设备 含辅助时间)台套② 次数/月 ①
磨床 2件/分钟 24000
磨外径
推荐使用的产能分析表
26
产能分析的三个阶段
产能规划阶段 --完成时机:报价阶段。零件未生产,处于规划阶段
PPAP阶段0(节拍生产) --完成时机:CP/IPSW阶段。固定数量,以计算节拍为目的
28
产能分析问题交流
对以上内容有任何问题 或您在这方面有更深的体会请提出
共同参与交流
29
分享共赢
钓鱼 1、钓鱼方式 2、鱼竿种类 3、鱼竿的组成 4、钓鱼的好处
30
分享共赢 钓鱼方式
传统钓
矶钓
海钓冰钓路亚钓来自31分享共赢鱼竿种类
手竿
抛竿
矶竿
路亚竿
32
分享共赢
鱼竿的组成:鱼竿、鱼线、鱼钩、鱼坠、鱼漂、钓饵、钓线
良品率=
*不良数=废品+返修数
名词:开动率=稼动率=运行效率=Run
OEE计算案例
9
案例:5分钟测试题 工作时间:8h, 班前计划停机:20min, 故障停机:20min, 安装工夹时间:20min, 调整设备时间:20min。
零件加工总数:400件, 单件 理论加工周期为0.5min, 单件实际加工周期为0.8min, 合格品率为98% ;