什么是精益生产
精益生产的实施步骤是什么
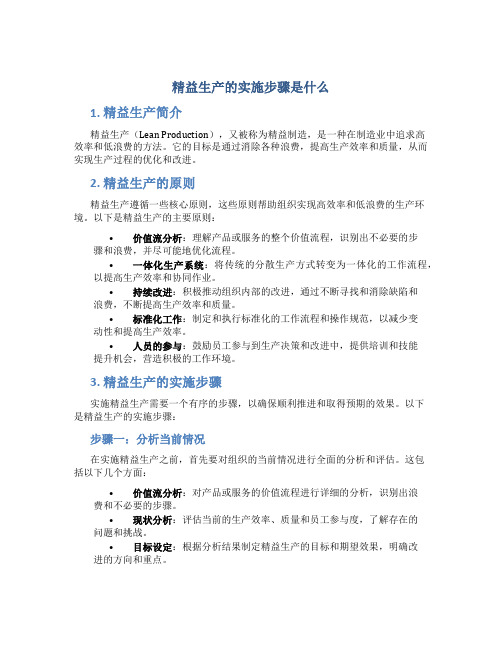
精益生产的实施步骤是什么1. 精益生产简介精益生产(Lean Production),又被称为精益制造,是一种在制造业中追求高效率和低浪费的方法。
它的目标是通过消除各种浪费,提高生产效率和质量,从而实现生产过程的优化和改进。
2. 精益生产的原则精益生产遵循一些核心原则,这些原则帮助组织实现高效率和低浪费的生产环境。
以下是精益生产的主要原则:•价值流分析:理解产品或服务的整个价值流程,识别出不必要的步骤和浪费,并尽可能地优化流程。
•一体化生产系统:将传统的分散生产方式转变为一体化的工作流程,以提高生产效率和协同作业。
•持续改进:积极推动组织内部的改进,通过不断寻找和消除缺陷和浪费,不断提高生产效率和质量。
•标准化工作:制定和执行标准化的工作流程和操作规范,以减少变动性和提高生产效率。
•人员的参与:鼓励员工参与到生产决策和改进中,提供培训和技能提升机会,营造积极的工作环境。
3. 精益生产的实施步骤实施精益生产需要一个有序的步骤,以确保顺利推进和取得预期的效果。
以下是精益生产的实施步骤:步骤一:分析当前情况在实施精益生产之前,首先要对组织的当前情况进行全面的分析和评估。
这包括以下几个方面:•价值流分析:对产品或服务的价值流程进行详细的分析,识别出浪费和不必要的步骤。
•现状分析:评估当前的生产效率、质量和员工参与度,了解存在的问题和挑战。
•目标设定:根据分析结果制定精益生产的目标和期望效果,明确改进的方向和重点。
步骤二:制定改进计划在分析了当前情况之后,制定一个详细的改进计划是非常重要的。
改进计划应包括以下内容:•具体目标:明确改进的具体目标和期望效果,例如提高生产效率、降低成本、提高质量等。
•重点领域:确定改进的重点领域,可以是特定的生产环节、工作流程或者产品线。
•资源分配:确定改进所需的资源,包括人力、物力和时间等,并合理分配到各个环节和任务上。
•时间计划:制定具体的时间计划,明确改进工作的时间节点和里程碑,以确保按计划推进。
精益生产推行步骤
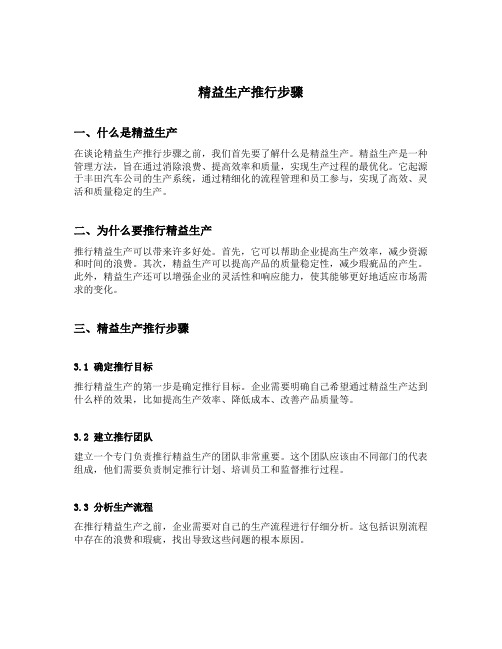
精益生产推行步骤一、什么是精益生产在谈论精益生产推行步骤之前,我们首先要了解什么是精益生产。
精益生产是一种管理方法,旨在通过消除浪费、提高效率和质量,实现生产过程的最优化。
它起源于丰田汽车公司的生产系统,通过精细化的流程管理和员工参与,实现了高效、灵活和质量稳定的生产。
二、为什么要推行精益生产推行精益生产可以带来许多好处。
首先,它可以帮助企业提高生产效率,减少资源和时间的浪费。
其次,精益生产可以提高产品的质量稳定性,减少瑕疵品的产生。
此外,精益生产还可以增强企业的灵活性和响应能力,使其能够更好地适应市场需求的变化。
三、精益生产推行步骤3.1 确定推行目标推行精益生产的第一步是确定推行目标。
企业需要明确自己希望通过精益生产达到什么样的效果,比如提高生产效率、降低成本、改善产品质量等。
3.2 建立推行团队建立一个专门负责推行精益生产的团队非常重要。
这个团队应该由不同部门的代表组成,他们需要负责制定推行计划、培训员工和监督推行过程。
3.3 分析生产流程在推行精益生产之前,企业需要对自己的生产流程进行仔细分析。
这包括识别流程中存在的浪费和瑕疵,找出导致这些问题的根本原因。
3.4 制定改进计划基于对生产流程的分析,企业需要制定改进计划。
这个计划应该明确具体的改进目标和实施步骤,并制定相应的时间表和责任人。
3.5 培训员工推行精益生产需要员工的积极参与和支持。
因此,企业需要对员工进行培训,使他们能够理解精益生产的原理和方法,并掌握相应的工具和技巧。
3.6 实施改进措施一旦培训完成,企业就可以开始实施改进措施了。
这包括消除生产过程中的浪费、改善工作流程、提高产品质量等。
3.7 监督和评估推行精益生产并不是一次性的任务,而是一个持续改进的过程。
因此,企业需要建立相应的监督和评估机制,定期检查和评估改进效果,并根据评估结果进行调整和改进。
3.8 持续改进精益生产的推行永远不会结束,企业应该将其作为一种持续改进的理念贯穿于整个组织。
jit生产的理解
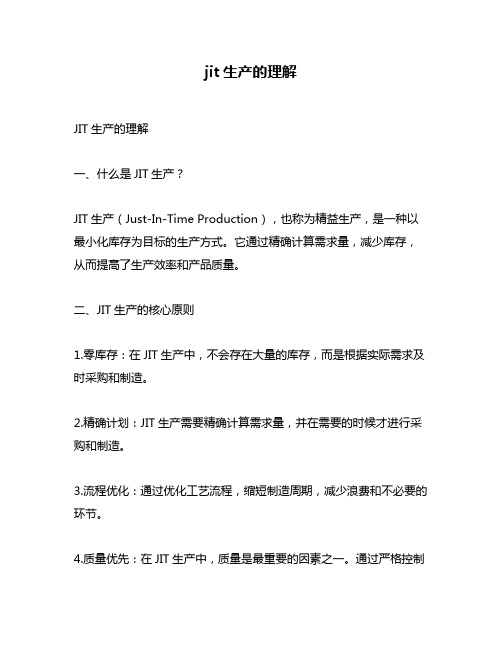
jit生产的理解JIT生产的理解一、什么是JIT生产?JIT生产(Just-In-Time Production),也称为精益生产,是一种以最小化库存为目标的生产方式。
它通过精确计算需求量,减少库存,从而提高了生产效率和产品质量。
二、JIT生产的核心原则1.零库存:在JIT生产中,不会存在大量的库存,而是根据实际需求及时采购和制造。
2.精确计划:JIT生产需要精确计算需求量,并在需要的时候才进行采购和制造。
3.流程优化:通过优化工艺流程,缩短制造周期,减少浪费和不必要的环节。
4.质量优先:在JIT生产中,质量是最重要的因素之一。
通过严格控制每一个环节来保证产品质量。
三、JIT生产的优点1.降低成本:由于不需要大量储备原材料或成品,在物流、仓储等方面可以节省成本。
2.提高效率:通过减少库存、优化流程等方式,可以提高整个供应链的效率。
3.增强竞争力:由于能够更快地响应市场需求并保持良好的产品质量,JIT生产可以提高企业的竞争力。
4.减少浪费:通过减少库存、优化流程等方式,可以减少浪费,提高资源利用率。
四、JIT生产的缺点1.对供应链要求高:由于JIT生产需要精确计算需求量并及时采购和制造,因此对供应链的要求较高。
2.风险较大:在JIT生产中,由于库存较少,一旦出现问题可能会导致生产中断或者无法满足市场需求。
3.需要投入大量资源:为了实现JIT生产,企业需要投入大量的人力、物力和财力进行流程优化和技术改进等工作。
五、JIT生产在实践中的应用1.汽车制造业:汽车制造业是最早采用JIT生产的行业之一。
通过精确计算零部件需求量,并及时采购和制造,可以提高整个供应链的效率和产品质量。
2.电子制造业:电子产品更新换代快,在这个领域采用JIT生产可以更快地响应市场需求,并保持良好的产品质量。
3.医药制造业:医药行业需要严格控制产品质量,采用JIT生产可以保证产品质量,并减少废品和浪费。
六、JIT生产的未来发展随着信息技术的不断发展,JIT生产将会变得更加智能化和自动化。
精益生产是什么?

精益生产是什么?什么是精益生产?精益生产(Lean Manufacturing)是一套管理原则和方法,旨在通过最大限度地减少浪费和提高生产效率,以实现高质量、低成本和可持续发展的生产。
精益生产最初由丰田汽车公司在上世纪50年代发展起来,并随后被广泛推广和应用于制造业和服务业。
精益生产的核心理念是围绕客户需求来优化生产流程,增加产品价值,提高生产效率,并通过减少浪费和消除不必要的活动来降低成本。
精益生产强调团队合作、持续改进和全员参与,以实现高品质、灵活性和交付速度的提升。
精益生产的原则和方法1. 价值流分析(Value Stream Mapping)价值流分析是精益生产中的一项重要工具,用于识别和分析产品或服务的价值流程。
通过绘制价值流程图,识别出每个环节的价值和非价值活动,有助于发现浪费和瓶颈,并制定改进方案。
价值流分析可以帮助企业了解整个生产过程,并找到提高效率和降低成本的方法。
2. 连续流(Continuous Flow)连续流是指在生产过程中将产品或服务的价值流动起来,使每个步骤都能够无间断地连接在一起。
通过优化物料流动和信息传递,最大限度地减少停顿和等待时间,从而加快生产速度和交付周期。
连续流的目标是实现高效率的生产,减少库存和运营成本。
3. 花式柔制生产(Flexible Manufacturing)花式柔制生产是指通过改变生产线的配置和组织方式,使其具备灵活性和快速响应客户需求的能力。
通过引入标准化工艺和模块化设计,可以快速切换生产任务,避免浪费和错误。
花式柔制生产的目标是实现高品质、高效率和高灵活性的生产。
4. 数字化管理(Digital Management)数字化管理是指通过使用先进的信息技术和数据分析方法,实现生产过程的可视化和追踪。
通过实时监控和分析生产数据,可以快速识别问题和改进机会,并及时采取措施。
数字化管理可以帮助企业实现生产过程的优化和精细化管理。
5. 持续改进(Continuous Improvement)持续改进是精益生产的核心思想之一,强调通过小步改进和一直向前的态度来不断提高效率和质量。
精益生产是什么?精益生产具有哪些特点

精益生产是什么?精益生产具有哪些特点一、什么是精益生产?精益生产(LeanProduction)又称精良生产,其中“精”表示精良、精确、精美;“益”表示利益、效益等等。
精益生产就是及时制造,消灭故障,消除一切浪费,向零缺陷、零库存进军。
它是美国麻省理工学院在一项名为“国际汽车计划”的研究项目中提出来的。
它们在做了大量的调查和对比后,认为日本丰田汽车公司的生产方式是最适用于现代制造企业的一种生产组织管理方式,称之为精益生产,以针对美国大量生产方式过于臃肿的弊病。
精益生产综合了大量生产与单件生产方式的优点,力求在大量生产中实现多品种和高质量产品的低成本生产。
丰田生产方式又称精细生产方式,或精益生产方式。
二、精益生产的特点2-1、拉动式准时化生产A、以最终用户的需求为生产起点,强调物流平衡,追求零库存,要求上一道工序加工完的零件立即可以进入下一道工序。
B、组织生产线依靠一种称为看板(Kanban)的形式。
2-2、全面质量管理A、强调质量是生产出来而非检验出来的,由生产中的质量管理来保证最终质量。
B、对于出现的质量问题,一般是组织相关的技术与生产人员作为一个小组,一起协作,尽快解决。
2-3、团队工作法团队工作法(Teamwork)。
每位员工在工作中不仅是执行上级的命令。
更重要的是积极地参与,起到决策与辅助决策的作用。
组织团队的原则并不完全按行政组织来划分,而主要根据业务的关系来划分。
团队成员强调一专多能,要求能够比较熟悉团队内其他工作人员的工作,保证工作协调的顺利进行。
团队的组织是变动的,针对不同的事物,建立不同的团队,同一个人可能属于不同的团队。
2-4、并行工程并行工程(ConcurrentEngineering)。
在产品的设计开发期间,将概念设计、结构设计、工艺设计、最终需求等结合起来,保证以最快的速度按要求的质量完成。
精益生产的实施步骤是啥
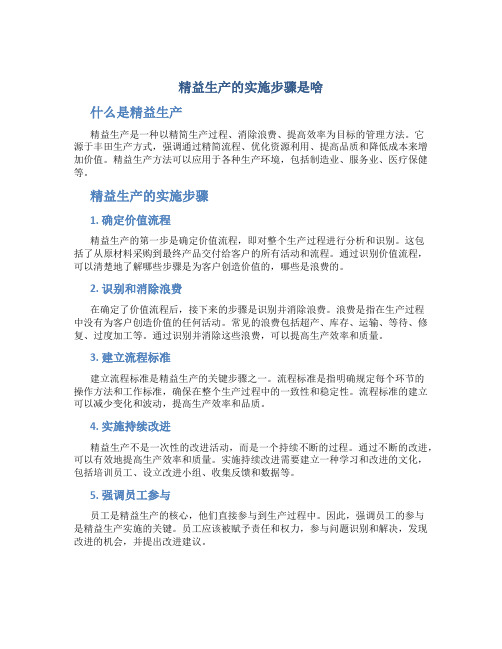
精益生产的实施步骤是啥什么是精益生产精益生产是一种以精简生产过程、消除浪费、提高效率为目标的管理方法。
它源于丰田生产方式,强调通过精简流程、优化资源利用、提高品质和降低成本来增加价值。
精益生产方法可以应用于各种生产环境,包括制造业、服务业、医疗保健等。
精益生产的实施步骤1. 确定价值流程精益生产的第一步是确定价值流程,即对整个生产过程进行分析和识别。
这包括了从原材料采购到最终产品交付给客户的所有活动和流程。
通过识别价值流程,可以清楚地了解哪些步骤是为客户创造价值的,哪些是浪费的。
2. 识别和消除浪费在确定了价值流程后,接下来的步骤是识别并消除浪费。
浪费是指在生产过程中没有为客户创造价值的任何活动。
常见的浪费包括超产、库存、运输、等待、修复、过度加工等。
通过识别并消除这些浪费,可以提高生产效率和质量。
3. 建立流程标准建立流程标准是精益生产的关键步骤之一。
流程标准是指明确规定每个环节的操作方法和工作标准,确保在整个生产过程中的一致性和稳定性。
流程标准的建立可以减少变化和波动,提高生产效率和品质。
4. 实施持续改进精益生产不是一次性的改进活动,而是一个持续不断的过程。
通过不断的改进,可以有效地提高生产效率和质量。
实施持续改进需要建立一种学习和改进的文化,包括培训员工、设立改进小组、收集反馈和数据等。
5. 强调员工参与员工是精益生产的核心,他们直接参与到生产过程中。
因此,强调员工的参与是精益生产实施的关键。
员工应该被赋予责任和权力,参与问题识别和解决,发现改进的机会,并提出改进建议。
6. 进行定期审核和评估为了确保精益生产的持续有效,定期的审核和评估是必要的。
通过定期审核,可以识别问题并及时进行纠正措施。
评估可以评估改进效果,了解精益生产的实施状况,并提出进一步的改进建议。
总结精益生产是一种管理方法,通过精简生产过程、消除浪费、提高效率来增加价值。
它的实施步骤包括确定价值流程、识别和消除浪费、建立流程标准、实施持续改进、强调员工参与以及进行定期审核和评估。
对于精益生产的理解

对于精益生产的理解一、什么是精益生产精益生产是一种以客户需求为导向,通过优化流程、降低浪费和提高效率来实现生产过程的最大化价值的方法。
它通过消除不必要的浪费和缩短流程时间,实现了资源的最大化利用和成本的最小化。
二、精益生产的原则1.价值定义:明确产品或服务对客户有什么价值,并根据客户需求进行设计和开发。
2.流程分析:对整个生产过程进行分析,找出其中存在的浪费和不必要的环节,并消除它们。
3.流程优化:通过改进流程,使其更加高效、简单、快速,减少浪费并提高质量。
4.拉动式生产:根据客户需求,以拉动方式进行生产,避免过度生产和库存积压。
5.持续改进:不断地寻找问题并改进解决方案,使得整个生产过程不断地完善和提升。
三、精益生产与传统生产模式的区别1.价值观念不同:传统模式注重规模经济和成本控制,而精益模式注重客户价值和持续改进。
2.流程设计不同:传统模式中,流程是基于生产能力和设备的,而精益模式中,流程是基于客户需求和价值的。
3.生产方式不同:传统模式采用推动式生产,即按计划进行生产并将产品推向市场,而精益模式采用拉动式生产,即根据客户需求进行生产。
4.质量控制方式不同:传统模式注重检验和纠错,而精益模式注重预防和持续改进。
四、精益生产的优势1.提高效率:通过消除浪费和优化流程,提高了整个生产过程的效率。
2.降低成本:通过减少浪费和提高效率,降低了整个生产过程的成本。
3.提高质量:通过持续改进和预防控制,提高了产品或服务的质量。
4.增强竞争力:通过提高效率、降低成本、提高质量等方面的优化,增强了企业的竞争力。
5.改善员工满意度:通过减少浪费和优化工作流程,员工可以更加轻松地完成工作任务,并获得更多的自豪感和成就感。
五、实施精益生产的步骤1.明确价值:确定客户需求和产品或服务的价值。
2.流程分析:对整个生产过程进行分析,找出其中存在的浪费和不必要的环节,并消除它们。
3.流程优化:通过改进流程,使其更加高效、简单、快速,减少浪费并提高质量。
精益知识点总结归纳
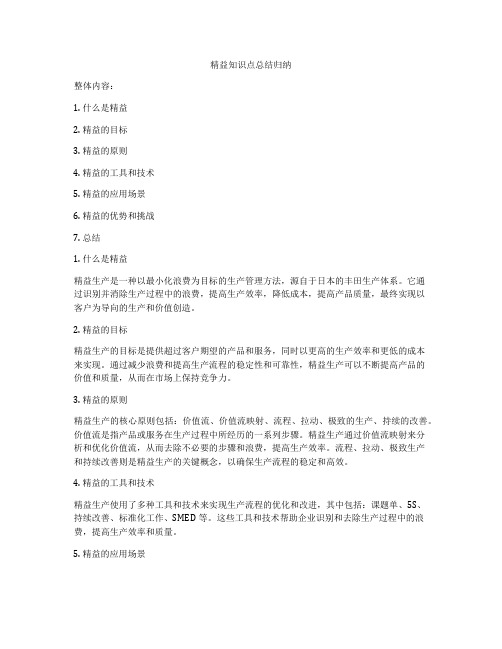
精益知识点总结归纳整体内容:1. 什么是精益2. 精益的目标3. 精益的原则4. 精益的工具和技术5. 精益的应用场景6. 精益的优势和挑战7. 总结1. 什么是精益精益生产是一种以最小化浪费为目标的生产管理方法,源自于日本的丰田生产体系。
它通过识别并消除生产过程中的浪费,提高生产效率,降低成本,提高产品质量,最终实现以客户为导向的生产和价值创造。
2. 精益的目标精益生产的目标是提供超过客户期望的产品和服务,同时以更高的生产效率和更低的成本来实现。
通过减少浪费和提高生产流程的稳定性和可靠性,精益生产可以不断提高产品的价值和质量,从而在市场上保持竞争力。
3. 精益的原则精益生产的核心原则包括:价值流、价值流映射、流程、拉动、极致的生产、持续的改善。
价值流是指产品或服务在生产过程中所经历的一系列步骤。
精益生产通过价值流映射来分析和优化价值流,从而去除不必要的步骤和浪费,提高生产效率。
流程、拉动、极致生产和持续改善则是精益生产的关键概念,以确保生产流程的稳定和高效。
4. 精益的工具和技术精益生产使用了多种工具和技术来实现生产流程的优化和改进,其中包括:课题单、5S、持续改善、标准化工作、SMED等。
这些工具和技术帮助企业识别和去除生产过程中的浪费,提高生产效率和质量。
5. 精益的应用场景精益生产可以应用于任何生产性质的企业和组织,尤其适用于制造业和服务业。
在制造业中,精益生产可以帮助企业提高生产效率和减少成本;在服务业中,精益生产可以帮助企业提高服务质量和客户满意度。
6. 精益的优势和挑战精益生产的优势在于它能够提高生产效率和质量,降低成本,提高客户满意度,增强企业竞争力。
然而,精益生产也面临着一些挑战,如对组织文化和管理理念的挑战,应用工具和技术的难度等。
7. 总结精益生产是一种以最小化浪费为目标的生产管理方法,它通过去除不必要的步骤和浪费,提高生产效率和质量,从而为企业创造更大的价值。
精益生产的核心原则包括价值流、价值流映射、流程、拉动、极致的生产、持续的改善。
精益生产的定义

精益生产的定义什么是精益生产?精益生产是一种管理理念和生产方法,旨在通过最大程度地减少资源浪费,以实现高效生产和提供价值给客户。
精益生产的核心原则是通过不断改善流程,消除浪费,提高生产效率和质量。
这一理念最初起源于丰田汽车公司的生产体系,后来被广泛应用于其他行业和领域。
精益生产的目标精益生产的主要目标是实现以下几点:1.提高生产效率:通过消除浪费,优化流程,提高生产效率和生产率。
2.降低成本:通过减少废品和不必要的生产成本,实现成本的最小化。
3.提高产品质量:通过改进生产过程和流程控制,提高产品质量和稳定性。
4.提高客户满意度:通过及时交付高质量的产品,提高客户满意度和忠诚度。
精益生产的原则精益生产遵循一些核心原则,其中包括:1.价值:专注于为客户创造价值,只集中精力和资源在对客户有意义的活动上。
2.价流:优化价值流动,消除所有形式的浪费,确保产品/服务按需求流动。
3.拉动:基于客户需求拉动生产,避免过度生产和库存积压。
4.流程改进:不断改进生产过程,强调团队合作和持续学习。
5.标准化:建立标准化工作流程和操作规程,确保质量和稳定性。
精益生产的实践精益生产的实践方法包括:1.价值流分析:分析整个价值流,识别不必要的步骤和浪费。
2.5S整理法:通过整理、整顿、清扫、清洁、标准化等步骤,改善工作环境和效率。
3.持续改进:建立改进文化和机制,鼓励员工提出改进建议和参与改进活动。
4.精益供应链管理:与供应商建立紧密合作关系,实现供应链的高效协同和配合。
精益生产的应用范围精益生产不仅适用于制造业,也适用于服务业和其他领域。
在制造业中,精益生产可以帮助企业提高生产效率、降低成本、改善质量;在服务业中,精益生产可以帮助企业提高服务效率、提升客户体验、降低服务成本。
总结精益生产是一种重要的管理理念和生产方法,其核心目标是通过最大程度地减少浪费,实现高效生产和提供价值给客户。
精益生产的原则和实践方法可以帮助企业提高生产效率、降低成本、改善质量,从而获得持续竞争优势。
精益生产知识题库-简答题

1.什么是精益生产?答:精益生产(Lean Production,简称LP).精,即少而精,不投入多余的生产要素,只是在适当的时间生产必要数量的市场急需产品(或下道工序急需的产品);益,即所有的经营活动都要有益有效,具有经济性。
精益生产的特点是消除一切浪费、追求精益求精和不断改善,去掉生产环节中一切无用的东西,每个工人及其岗位的安排原则是必须增值,撤除一切不增值的岗位。
2.什么是生产均衡化?答:所谓生产均衡化,是指总装配线在向前工序领取零部件时,应均衡的使用各种零部件,混合生产各种产品。
3.“六零”管理指的是哪六零?答:所谓“六零”管理,主要是指:产品质量“零缺陷”、作业手段“零故障”、物资周转“零库存”、员工行为“零差错”、降低成本“零浪费”、现场管理“零松弛”等。
通过对“六零”管理的追求,促进整个企业的各项工作向“尽善尽美”的最高境界迈进,形成最科学、最完善的管理体系。
4.精益管理的基本方法有?答:(1)预防型的质量控制;(2)价值创造链的集成(3)模块化的组织结构;(4)团队工作;(5)反求工程;(6)相互对话;(7)可视化的通讯。
5.6S及6S之间的关系?答:整理、整顿、清洁、清扫、素养、安全关系:整理是整顿的基础,整顿是对整理的巩固,清扫是显现整理整顿的效果,而通过清洁对前三项进行约束。
工作的展开关键是人员,只有人员素养的提高才能把4S做实,安全是对人的保护。
6.精益生产的特点答:(1)拉动式准时化生产(2)全面质量管理(3)团队工作法(4)并行工程7.什么是JIT生产?答:只在需要时,按需要的量,生产所需的产品”。
(这种生产方式的核心是追求一种零库存、零浪费、零不良、零故障、零灾害、零停滞的较为完美的生产系统。
)8.精益思想有哪5项原则?答:价值、价值流、流动、拉动和尽善尽美。
9.什么是看板管理?答:JIT生产方式是以降低成本为基本目的,在生产系统的各个环节全面展开的一种使生产有效进行的新型生产方式。
JIT精益生产的基本知识

JIT精益生产的基本知识一、什么是JIT精益生产?JIT(Just-in-Time)精益生产是一种生产管理方法,旨在实现以最少的库存、最小的费用和最高的效率来满足客户需求。
其核心思想是在生产的每一步都不浪费时间、劳力和资源,以实现高效的生产流程。
二、JIT精益生产的原理1.零库存原则:JIT强调减少库存量,只在需要的时候才进行生产,有效降低库存成本和过剩库存的风险。
2.及时生产:产品在需要的时候才开始生产,以减少库存积压和生产周期,提高生产效率。
3.拉动生产:JIT通过“拉动式生产”,以客户需求为导向,根据实际订单推动生产,避免过度生产和浪费。
4.持续改进:JIT倡导持续改进和优化生产流程,促进团队协作和精益生产文化的建设。
三、JIT精益生产的优势1.降低成本:减少库存和废料,提高生产效率,降低生产成本。
2.提高质量:通过减少浪费和优化生产流程,提高产品质量和客户满意度。
3.提升交付速度:JIT生产方式能够更快速地响应客户需求,提高交付速度和服务水平。
4.增强竞争力:JIT可以帮助企业提升竞争力,降低生产周期,适应市场变化,实现持续发展。
四、如何实施JIT精益生产1.建立稳定的供应链:与供应商建立稳定的合作关系,确保物料供应的稳定和及时。
2.实施流程再造:对生产流程进行优化和改进,消除浪费,提高生产效率。
3.培训员工:向员工提供JIT精益生产的培训,增强他们的生产技能和质量意识。
4.持续改进:制定并实施持续改进计划,对生产流程和产品质量进行不断改进。
五、JIT精益生产的案例分析1. 丰田汽车丰田汽车采用JIT精益生产方式,通过精细的供应链管理和及时生产,实现了高效的制造和交付,提高了产品质量和客户满意度。
2. 联想集团联想集团在生产管理中推行JIT精益生产,通过优化生产流程和降低库存,提高了生产效率和竞争力,实现了持续发展。
六、结语JIT精益生产是一种重要的生产管理方法,对企业提高效率、降低成本、提高竞争力具有重要意义。
精益生产宣传文案

精益生产宣传文案范文
精益生产:创造卓越,减少浪费
什么是精益生产?
精益生产是一种以最大程度减少浪费为目标的生产方法。
它的核心理念是通过不断优化流程,减少资源浪费,提高生产效率,提供更高质量的产品或服务。
精益生产不仅仅适用于制造业,也可以在各种领域中得以应用,包括服务业、医疗保健、教育等。
核心原则
1. 价值观念:了解客户的需求,将重点放在创造客户价值的活动上。
2. 价值流:分析生产过程,识别非价值增加的步骤和浪费。
3. 流程改进:优化生产流程,减少浪费,提高效率。
4. 拉动生产:根据需求启动生产,以避免库存浪费。
5. 追求卓越:不断改进,追求卓越,提供更高质量的产品和服务。
精益生产的好处
-成本降低:减少浪费,降低成本,提高盈利能力。
-交付时间缩短:优化流程,加速生产,更快地满足客户需求。
-产品质量提高:减少错误和缺陷,提供更可靠的产品。
-员工参与:鼓励员工提出改进建议,提高员工满意度。
-环保:减少资源浪费,降低对环境的影响。
我们的承诺
作为精益生产的倡导者,我们致力于帮助您优化生产过程,提高竞争力,同时降低成本。
我们的专家团队将与您合作,定制适合您业务的精益生产解决方案,帮助您实现更高质量、更高效率的生产。
让我们一起迈向卓越,减少浪费,提高竞争力!联系我们,了解如何在精益生产的指导下,提升您的业务表现。
联系方式:[您的联系信息]
不要等待,开始精益生产之旅,创造卓越,减少浪费!。
精益生产是什么

精益生产是什么精益生产(Lean Manufacturing),又称为精益生产管理或精益制造,是一种强调生产过程中消除浪费、提高效率和质量的管理方式。
它起源于丰田汽车公司,通过优化生产流程和资源利用,帮助企业实现高效、高质量的生产。
本文将介绍精益生产的定义、原则、特点以及实施步骤。
1. 定义精益生产是一种基于消除浪费和提高价值增长的生产方法。
它从资源和生产流程的角度出发,通过减少无效活动和资源浪费,以最少的资源创造出最大的价值。
精益生产强调持续改进和员工参与,旨在提高效率、降低成本、提高质量和满足客户需求。
2. 原则精益生产依据一系列原则进行实施,这些原则有助于指导企业在生产过程中消除浪费和提高效率。
以下是精益生产的主要原则:2.1 价值定义精益生产强调以客户需求为导向,确定什么是对客户有价值的。
通过仔细分析价值流,企业可以识别出哪些步骤和活动是为客户创造价值的,从而优化生产流程。
2.2 流程优化流程优化是精益生产的核心原则之一。
通过分析和优化生产流程,消除不必要的步骤和环节,减少产出的浪费和资源的浪费。
2.3 拉动生产拉动生产是指根据内部和外部需求进行生产,而不是根据预测的需求。
这种方式可以避免过度生产和库存积压,提高生产响应速度。
2.4 持续改进持续改进是精益生产的重要原则之一。
通过不断地改进生产流程和方法,寻求效率和质量的提升,并培养员工参与改进的习惯。
2.5 资源最优化精益生产强调尽可能最大化资源的利用效率。
通过避免不必要的浪费和合理分配资源,提高效率和质量。
3. 特点精益生产具有以下几个特点:3.1 去除浪费精益生产通过消除生产过程中的各种浪费,例如等待时间、运输时间、制造缺陷等,实现资源的最优利用。
3.2 质量优先精益生产强调短期和长期的质量目标。
通过提升质量控制和员工参与,减少缺陷和重新制造,提高质量水平。
3.3 灵活性精益生产追求产品和生产流程的灵活性,以便根据市场需求进行调整和改变。
什么是精益生产

什么是精益生产精益生产是一种管理理念,旨在通过提高生产效率、降低浪费以及优化价值流程,帮助组织实现更高的生产质量和更低的成本。
本文将对精益生产进行详细阐述,介绍其背景、原则以及应用情况。
精益生产源于日本的丰田生产方式(Toyota Production System),起源于上世纪50年代,是一种以消除浪费为核心目标的生产管理系统。
它的提出是为了应对日本汽车产业在战后初期的困境,通过改善生产流程和管理方式来提高效率、质量和竞争力。
随着时间的推移,精益生产逐渐得到了其他行业和组织的认可和应用。
精益生产的核心原则是以价值流为导向,即从顾客的角度出发,识别出实际为顾客创造价值的流程和活动,并通过精确定义价值、价值流和流程、以及强调团队协作、连续改进等手段,优化整个价值流程。
精益生产通过剔除不必要或无价值的环节、降低库存和减少时间浪费,实现有效地生产,从而降低成本并提高生产质量。
精益生产的核心原则包括以下几个方面:1. 价值流映射(Value Stream Mapping):通过绘制价值流图,将整个价值流程可视化,识别出存在的浪费环节和不必要的活动,从而为改进提供依据。
2. 流程改进(Process Improvement):通过不断分析和改进流程,优化价值流程,提高效率和质量。
这包括去除浪费、标准化工作程序、实施自动化等措施。
3. 丰田生产方式中的“拉动”(Pull)生产模式:顾客需求是生产的驱动力,根据订单和需求进行生产,避免过度生产和库存过剩。
4. 尊重员工(Respect for People):重视员工并赋予他们更多的职责和决策权,鼓励员工参与团队协作,以提高生产效率和质量。
5. 持续改进(Continuous Improvement):精益生产的最终目标是实现持续改进,通过小步快走的方式不断寻找问题和解决问题,以达到更高效的生产方式。
精益生产的应用范围广泛。
除了制造业,像服务业、医疗卫生、建筑业和金融业等各个行业都可以借鉴精益生产的原则和方法。
什么是精益生产

什么是精益生产精益生产是一种管理方法,通过减少浪费和提高效率来优化生产流程。
它起源于日本的丰田生产系统,现已广泛应用于各行各业。
本文将深入探讨精益生产的原理和实施步骤。
精益生产的核心原理是以客户为导向,并将价值定义为顾客所需的产品或服务。
它的目标是消除不必要的浪费和减少生产时间,以提高产品质量并降低成本。
为了实现这个目标,精益生产强调对流程的持续改进和最大化价值流动。
精益生产方法中的关键概念之一是价值流映射。
价值流是指为生产产品或提供服务所需的所有活动。
通过绘制价值流地图,生产者可以清楚地看到从供应商到客户的整个流程,并识别出浪费和不必要的环节。
这样,他们可以集中精力改进这些环节,以提高生产效率。
其次,精益生产强调持续的改进和团队合作。
所有员工都应积极参与,发现问题并提出解决方案。
精益生产需要建立一个开放的沟通环境,使每个人都能贡献自己的想法和建议。
通过共同努力,团队可以发现和解决潜在问题,并实现更高的生产效率和质量标准。
此外,精益生产着重于减少库存和降低工作中的过程时间。
它通过实施“拉动制造”原则,即根据顾客需求,按需生产产品,避免过剩的库存。
这不仅减少了浪费,还提高了生产的灵活性和响应能力。
实施精益生产需要一系列的步骤和方法。
首先,需要进行价值流映射,分析整个流程,并确定哪些环节是无价值的,可以被取消或改进。
然后,制定改进计划,并设立目标。
团队成员应该共同努力,积极参与改进过程,并定期回顾和评估改进效果。
此外,培训和教育也是至关重要的。
精益生产需要员工具备必要的知识和技能,以便他们能够更好地理解和应用精益生产方法。
公司应该为员工提供培训机会,并鼓励他们不断学习和成长。
总结起来,精益生产是一种通过消除浪费和提高效率来优化生产流程的管理方法。
它以客户为导向,强调通过价值流映射和团队合作来改进生产流程。
精益生产的实施需要一系列的步骤和方法,以及员工的培训和教育。
通过精益生产,企业可以提高生产效率和质量,实现可持续的发展。
什么是精益生产

什么是精益生产精益生产是一种被广泛应用于制造业的管理方法论。
它主要源于丰田生产系统(TPS),由日本企业家和学者丰田麻省理工学院栗田惠顿和詹姆斯·韦姆克共同发展而成。
精益生产不仅仅是一种生产方法,更是一种管理哲学,它以“最小浪费,最大价值”为核心思想,旨在优化生产流程,提高企业效率和竞争力。
精益生产的核心概念是价值流和浪费。
价值流是一系列、一件物品或服务在其整个生命周期内所需的流程和步骤,最终使产品或服务创造价值。
而浪费是指生产过程中不必要的消耗和不必要的步骤,它们使得企业的生产效率降低。
精益生产的目的就是减少浪费,优化价值流。
在精益生产中,有7种浪费。
它们分别是:等待、过剩产能、运输、抽检、过度处理、库存以及人员移动和失误。
这些浪费会降低企业的生产效率,导致不必要的成本和时间浪费。
精益生产的目的就是避免这些浪费,从而提高生产效率。
为了实现精益生产,企业可以采用一系列的工具和技术。
其中最著名的是“KAIZEN”(改进)。
它是一种持续不断地改善的方法,旨在逐步优化和提高生产流程。
除此之外,企业可以使用“5S”管理方法(整理、整顿、清洁、清理和标准化)来提高生产现场的效率和品质。
此外还有“JIT”(Just in Time)库存管理法,可以有效减少库存,避免浪费。
在精益生产中,还有一种很重要的概念叫“ANDON”(安灯)。
它是一种生产线条上的一种设备,随时显示生产情况和异常情况。
如果发现生产中的问题,员工可以按下安灯按钮,生产线停止运行。
这允许制造商及时响应问题,防止浪费但不牺牲质量。
总的来说,精益生产是一个有效提高企业效率和竞争力的方法。
它通过重新思考和优化生产流程,减少浪费,优化价值流,使企业在降低成本和提高质量方面具有显著的优势。
在当代企业管理中,精益生产已经成为一种被广泛应用的管理方法。
精益生产基本知识点

精益生产基本知识问与答1、什么事精益生产?p9精益生产,又称精良生产,其中“精”表示精良、精确、精美,即少而精,更少的投入,只是在适当的时间生产必要数量的市场急需产品(或下道工序急需的产品);“益”表示利益、效率,即所有经营活动都要有益、有效,并具有经济性。
精益生产就是及时制造,消灭故障,消除一切浪费,向零缺陷、零库存进军。
2、精益生产主要特点有哪些?p9(1)一切为用户着想,产品直接面向用户,将用户纳入产品开发过程,以适应产品小批量、多元化、尽可能短的交货期生产,最大限度地满足用户需求,真正体现用户是“上帝”的精神。
(2)实施一个流,采用准时生产方式和看板管理,即只在需要的时候,按必需的量生产所需的商品,能够最大限度减少闲置时间、作业交换时间、库存、劣质品、不合格的供应商,缩短产品开发设计周期,使得导致成本提高的零部件库存减少直至接近于零,加快产品周期、减少规模效益影响;寻找、纠正和解决质量问题,提高生产率,减少浪费。
(3)以“人”为中心,部分权力下放,员工参与管理,充分发挥一线员工的积极性和创造性,从而降低产品返修率。
此外,还须满足员工学习新知识和实现自我价值的愿望,形成独特和谐的企业文化。
(4)以“精简”为手段,实现组织机构精简化,去掉一切多余的环节和人员。
强调团队工作组方式,集成各方面人才进行产品的并行设计,对产品的开发和生产具有很强的指导和集成能力。
(5)实现准时供货方式,保证最小的库存和最少的在制品数,与供货商建立良好的合作关系,相互信任、相互支持,利益共享。
(6)追求的目标是精益求精、尽善尽美、不断降低成本,做到零废品、零库存和产品品种的多样化。
3、精益思想的五大原则是什么?p121.精益思想第一大原则:价值站在客户立场上来审视企业的产品设计、制造过程、服务项目,就会发现太多的浪费,从而不满足客户需求到过多功能和多余的非增值消耗。
因此企业在制造过程中应实现增值活动,即实现增值动作和时间,如改变形状,改变性能、组装、包装等,已达到产品增值的目的,提供给用户真正需要的价值。
- 1、下载文档前请自行甄别文档内容的完整性,平台不提供额外的编辑、内容补充、找答案等附加服务。
- 2、"仅部分预览"的文档,不可在线预览部分如存在完整性等问题,可反馈申请退款(可完整预览的文档不适用该条件!)。
- 3、如文档侵犯您的权益,请联系客服反馈,我们会尽快为您处理(人工客服工作时间:9:00-18:30)。
精益手册什么是精益生产通过消除企业所有不值活动,来达到降低成本、缩短生产周期和改善质量的目的。
区别精益生产方式与传统生产方式的区别主要表现为:改变了品质控制手段;消灭(减少)了各种缓冲区;增加了职工的参与感和责任感;培训职工并与职工交流;仅在需要的地方采用自动化;精益组织结构。
精益生产方式的主要特征表现为(1)品质——寻找、纠正和解决问题;(2)柔性——小批量、一个流;(3)投放市场时间——把开发时间减至最小;(4)产品多元化——缩短产品周期、减小规模效益影响;(5)效率——提高生产率、减少浪费;(6)适应性——标准尺寸总成、协调合作;(7)学习——不断改善。
精益生产的核心精益生产的核心是通过持续不断滴排除浪费来赢得利润、创造价值。
精益思想五个原则1. 价值——精确地确定特定产品的价值。
2. 价值流——识别出每种产品的价值流。
3. 流动——使价值不间断地流动。
4. 拉动——让用户从生产者方面拉动价值。
5. 尽善尽美——永远追求尽善尽美。
浪费什么是浪费浪费是指生产过程中用户不愿意支付的那部分企业活动。
浪费的种类1、生产过剩:是最坏的浪费,直接导致其他6种浪费。
是指生产出尚未有订单的产品,造成过早的占用资源,同时导致生产部均衡和各工序排队等待,生产周期长。
2、等待:因作业不平衡、安排作业不当、停工待料、品质不良、监看机器而造成的等待的浪费。
3、不必要的加工:加工质量或精度超过了客户的要求而造成的资源浪费,包括浪费了过多的工时、能源,增加了设备损耗,占用了作业空间等。
在制造过程中,为了达到作业的目的,有一些加工程序是可以省略、合并、重排或简化的。
4、搬运:长距离搬运在制品,缺乏效率的运输,进出仓库或在流程之间搬运原材料、零部件或最终成品5、库存过高:因为大量的库存会产生不必要的搬运、堆积、放置、防护、找寻等浪费,日常管理、领用、甚至盘点等也需要增加额外的时间。
既占用生产空间、浪费人力物力,又占用运营资金、损失管理费用。
随着存储时间增长,物品价值往往会降低,变成呆料废料,甚至被遗忘。
6、不合理的动作:任何对生产制造不增值的人员或机器的动作、行为。
7、不良品:在生产过程中,任何不良品的产生,都会造成人力、物力和时间方面的浪费,如产品报废返工、材料和人工损失、订单和市场信誉损失等。
准时生产准时生产定义准时生产是指在正确的时间生产正确数量的正确产品,否则就会导致浪费。
准时生产的基本原则1.不加工任何东西,除非顾客下订单。
2.令需求平稳,以使在整个工厂内工作可以顺利地进行。
3.使用简单的可视化工具(看板)将所有流程与顾客需求连接在一起。
4.最大化人力和设备弹性。
目标准时化生产的目标是产生一个连续的价值流,以便于顾客拉动。
彻底消除无效劳动造成的浪费。
1. 废品量最低2. 准备时间最低3. 库存量最低4. 搬运量最低5. 机器损坏率低6. 生产提前期短7. 批量小看板看板是一个用来实现准时生产的可视工具。
看板的特点:1. 看板制定了规则,告诉线上的作业员,当生产出现问题时,他们采取何种步骤,应该向谁申请帮助。
2. 看板系统具有良好的可视性。
3. 看板是一种由客户需求驱动的计划微调与进度控制方法,必须遵守两点:a. 只生产客户(后道工序)需要的产品,绝不能超出客户的需求。
b. 只根据客户发生的生产指标进行生产,绝不自行组织生产。
看板的功能:1. 做为生产和领料的指示2. 控制库存数量3. 防止生产过多/早4. 掌握异常生产进度5. 简化物管工作6. 防止缺料停线6条有效使用看板的规则:1. 永远不要装运次品2. 下道工序只取走他们需要的产品3. 只生产下道工序取货的数量4. 均衡化生产5. 使用看板微调生产6. 稳定流程和加强流程生产均衡化均衡化是指在固定的生产周期内,平衡产品的类型与数量。
这样可以在避免大量生产的同时,有效地满足顾客的需求,最终带来整条价值流中的最大化的库存、投资成本、人力资源以及产品交付期。
连续流通过一系列的工序,在生产和运输产品的时候,尽可能地使工序连续化,即每个步骤只执行下一步骤所必须的工作。
目的:最大限度地排除搬运、在制品多以及可能出现大量不良等无价值的现象。
拉式生产方式拉式生产意味着,除非下游工序要求,否则上游的工人就不生产产品或提供服务。
节拍时间(Takt Time)可用的生产时间除以顾客需求量。
节拍时间对生产的作用:对生产的调节控制、防止浪费和分段供应不连续、使生产现场作业规律化节拍时间等于有效的作业时间除以顾客需求量周期时间(Cycle Time)是指制造一件产品需要的时间通常由观察得出。
这个时间等于操作时间加上必要的准备、装载及卸载的时间之和。
自働化自働化的定义当品质或设备有异常发生时,设备或生产线具有自动停止或作业员主动使之停止的能力,在这里强调自働化是带人字旁的动。
[自动化]和[自働化]之相异点:[自働化]如有异常发生,因其设备的关系会停止运转,故容易找出异常的原因,也容易防止再发。
但是[自働化]不要特意投资设备,增加保修和监视机械的人员。
自働化的目的总体:保证设备安定运转及良好的维持1. 确保100%的良品制造。
2. 防止由于错误操作或材料不良造成机器设备损坏。
3. 事前预防设备故障,即不需要对每台设备进行看护。
4. 不良品发生时要明确设备上异常的问题并防止再发。
自働化运用的几种方式1. 可视化管理2. 定位停止系统(安灯板和呼叫灯)3. 防呆工装设计4. 误动作防止系统和安全装置5. 全数自检机制和全员质量意识的提升5S1.整理(seiri):从必要的项目——工具,零件,材料,文件中分离,并丢弃那些不必要的东西。
2.整顿(seiton):整洁地布置工作区域,把所有东西放到它们应该在的位置上。
3.清扫(seiso):打扫与清洗。
4.清洁(seiketsu):将上面的3S实施的做法制度化、规范化、并贯彻执行及维持结果。
5.自律(shitsuke):养成良好的的工作习惯,遵守纪律,努力提高人员素质,养成严格遵守规章制度的习惯和作风,营造团队精神。
目视化管理目视化管理:1.用眼睛即时发现异常的重要手段。
2.管理者意志通过管理板让全员知晓,进而达成一致目标的手段。
3.让全员知晓责任区域主要问题和解决方法的手段。
4.让监督者和作业者清楚地知晓基本规则的手段。
5.发现浪费的手段6.生产线发出指令,相关人员接收信息的手段。
7.改善的依据。
8.快速找到需求的物或者场所的手段。
目视化管理的形式:1.安灯(电子装置):传达工程异常或零件供应,刀具交换指令等讯息的装置。
2.生产管理板:用较小的时间段(如:5分钟)显示生产计划与实绩进行状态对比,将影响生产进度的设备停机与原因、品质问题停机与原因、物料问题停机原因、人员问题停机与原因、计划性停机等数据进行写实用的管理板(放在生产线后)。
3.KANBAN(看板):领取物品情报、搬运指示情报和生产指示情报。
作为不能生产比需求量多的管理手段,我们可以通过KANBAN来了解需求信息,只生产需求的量。
4.现场立式管理板:部门、班组等用于揭示公司方针、目标指示、现场管理7大任务等信息的揭示板。
5.管理基准线:设备压力范围、物料最大和最小在库标准等指导员工点检和遵守的规则等。
6.其他:颜色线条的标准、空间地名的标准、地面通道的标准、设备电器的标准、物品材料的标准、工具器具的标准、安全警示的标准外围环境的标准、办公室的标准等一切可以让人立即明白的标识。
TPMTPM英文Total Productive Maintenance的缩略语,中文译名叫全面生产维护。
是以提高设备综合效率为目标,以全系统的预防维护为国程,全体人员参与为基础的设备保养和维护管理体系。
TPM强调五大要素:1.TPM致力于设备综合效率最大化的目标;2.TPM在设备一生建立彻底的预防维修体制;3.TPM由各个部门共同推行;4.TPM涉及每个雇员,从最高管理者到现场工人;5.TPM通过动机管理,即自主的小组活动来推进。
标准作业标准作业是为了将作业人员、设备布置及物流过程作最适当的组合,以有效地达成生产目标而设立的标准化文件。
PDCA循环PDCA是一个以科学方法为基础的改善循环。
对一个过程提出改善方案,实施这个方案,评测结果,然后再采取适当的行动。
Plan(计划):确定一个过程的目标,以及实现目标所需要采取的改革方案。
Do(执行):实施这些方案。
Check(检验):根据执行效果来评价改进结果。
Action(行动):将改革后的程序更标准化,然后再次开始这个循环。
标准化是管理成果的积累,它遵循PDCA的原则,将经过检验的实践成果固化,促进组织的共同学习和进步。
标准化是一个过程,而非一个结果,它不是来束缚我们前进的障碍。
而是改进的基石,可以帮助我们获得必要的稳定和一致。
快速换模换模:任何因产品更换,而必须使机器或生产线停止生产,以从事更换动作皆是。
换模时间:因从事换模动作,而使机器或生产线停止生产的时间,即在前一批次最后一个合格零件与下一批次第一个合格零件之间的间隔时间.线内换模(内作业):指必须在机器停止生产状态下,才能进行的换模动作。
又称为"内作业"或者是"内部准备".线外作业(外作业):指机器在生产运转中,而仍然可以进行的换模动作,又称为"外作业"或者是"外部准备".快速换模法的三个基本要点:(1)区分“内变换操作”和“外变换操作”。
(2)减少“内变换操作”。
(3)缩短“内变换操作” 时间。
原则:一旦设备停止运转,作业人员绝对不要离开设备参与外部作业转换的操作。
在外部作业转换中,模具、工具以及材料必须事前整整齐齐地准备到设备旁边,而且模具必须事前修理好。
在内部作业转换中,必须只拆卸和安装模具。
11。