螺栓断裂分析报告
螺栓断口失效分析

1、解理断裂(大多数情况下为脆性断裂)2、剪切断裂1、静载断裂(拉伸断裂、扭转断裂)2、冲击断裂3、疲劳断裂1、低温冷脆断裂2、静载延滞断裂(静载断裂)3、应力腐蚀断裂4、氢脆断裂断口微观形貌(图3/4/5/6),断口呈脆性特征,表面微观形貌为冰糖状沿晶断裂,芯部为沿晶+准解理断裂,在断裂的晶面上有细小的发纹状形貌。
结论:零件为沿晶断裂的脆性断口。
断口呈脆性特征,表面微观形貌沿晶断裂,芯部为准解理断裂;终断区(图4)微观为丝状韧窝形貌,为最终撕裂区结论:断口为脆性断裂宏观断口无缩颈现象且微观组织多处存在剪切韧窝形貌,为剪切过载断裂断口。
综上分析:零件为氢脆导致的断裂,氢进入钢后常沿晶界处聚集,导致晶界催化,形成沿晶裂纹并扩展,导致断面承载能力较弱,最终超过其承载极限导致断裂典型氢脆断口的宏观形貌如右图所示:氢脆又称氢致断裂失效是由于氢渗入金属内部导致损伤,从而使金属零件在低于材料屈服极限的静应力持续作用下导致的失效。
氢脆多发生于螺纹牙底或头部与杆部过渡位置等应力集中处。
断口附近无明显塑性变形,断口平齐,结构粗糙,氢脆断裂区呈结晶颗粒状,一般可见放射棱线。
色泽亮灰,断面干净,无腐蚀产物。
应力腐蚀也属于静载延滞断裂,其断口宏观形貌与一般的脆性断口相似,断口平齐而光亮,且与正应力相垂直,断口上常有人字纹或放射花样。
裂纹源区、扩展区通常色泽暗灰,伴有腐蚀产物或点蚀坑,离裂纹源区越近,腐蚀产物越多。
应力腐蚀断面最显著宏观形貌特征是裂纹源表面存在腐蚀介质成分贝纹线是疲劳断口最突出的宏观形貌特征,是鉴别疲劳断口的重要宏观依据。
如果在宏观上观察到贝壳状条纹时,在微观上观察到疲劳辉纹,可以判别这个断口属于疲劳断口。
螺栓断裂分析报告

螺栓断裂分析报告1. 引言螺栓是一种常见的连接元件,广泛应用于工程领域。
然而,在使用过程中,螺栓的断裂可能会导致严重的安全事故和设备损坏。
因此,对螺栓的断裂原因进行分析非常重要。
本文将介绍螺栓断裂的分析步骤,以帮助读者更好地了解螺栓断裂的原因,并提供相应的解决方案。
2. 分析步骤螺栓断裂分析通常可以按照以下步骤进行:2.1 收集断裂螺栓样本首先,需要收集断裂的螺栓样本。
这些样本应来自不同的工程项目,并涵盖不同的工作条件。
收集足够数量的样本有助于得出准确的结论。
2.2 观察断口形貌通过对断裂螺栓的断口形貌进行观察可以初步判断断裂的原因。
断口形貌可以分为韧性断口、脆性断口等。
韧性断口常常表明螺栓断裂是由于受到超负荷载荷所致,而脆性断口则意味着存在其他问题。
2.3 进行金相分析金相分析是一种常用的分析方法,通过对螺栓样本进行金相薄片制备和观察,可以获得螺栓的组织结构信息。
通过金相分析,可以检测到螺栓材料中的缺陷、夹杂物、氧化层等问题。
2.4 进行力学性能测试力学性能测试是评估螺栓质量的重要手段。
通过对螺栓样本进行拉伸试验、硬度测试等,可以了解螺栓的强度、韧性等性能参数。
与标准数值进行对比,可以判断螺栓是否达到设计要求。
2.5 考虑工况因素分析断裂螺栓时,还需要考虑螺栓所处的工作条件。
例如,工作温度、湿度、振动等因素都可能对螺栓的性能产生影响。
通过分析工况因素,可以找到与断裂相关的潜在问题。
2.6 结果分析与解决方案综合以上分析结果,可以得出螺栓断裂的原因。
根据不同的原因,提出相应的解决方案。
例如,如果断裂原因是由于材料质量问题,可以优化材料制备过程;如果是由于超负荷导致断裂,则需要对工作负荷进行合理评估等。
3. 结论螺栓断裂分析是一项复杂的工作,需要综合考虑多个因素。
通过对断裂螺栓样本的观察、金相分析、力学性能测试以及考虑工况因素,可以准确判断螺栓断裂的原因,并提出相应的解决方案。
对螺栓断裂问题的分析与解决不仅可以提高工程项目的安全性,还能为相关领域的研究提供参考。
车桥螺栓断裂分析报告

车桥螺栓断裂分析报告某厂生产的重型机械在行进途中,所用车桥轮毂的紧固螺栓断裂,螺栓规格:M22×1.5,形状如图1所示。
断口形貌见图2。
螺栓材质为40Cr,螺栓所要达到的性能指标和具体工艺不详,应企业要求,现对其进行断裂失效分析。
1、化学成分分析经线切割后,在螺栓断面接近中心处取样,按照40Cr主要成分先进行了常规5元素(C,Si,Mn,S,P)及Cr,Mo两元素的化学分析,结果(质量分数) 及标准成分(GB/T3077-1999)对照表见表1。
40Cr为低合金调质钢,淬透性高于碳钢,油淬临界直径达17-30mm,水淬临界直径30mm以上。
经调质处理后具有良好的综合力学性能,常用于在交变载荷作用下工作的重要零件。
成分分析结果显示,该螺栓的化学成分符合40Cr钢标准成分要求。
2、断口宏观形貌分析螺栓断面与螺栓轴线垂直,断口表面经过清洗后发现(如图2所示),中间部分区域已经发生氧化,在断口上不能找到明显的放射线的汇集区域。
在断口的右侧存在明显的剪切唇,所以应该属于最后的断裂区域。
在断口左下侧存在平坦区域,因此判断此处为裂纹源的位置。
3、金相组织分析图3、图4为螺栓的金相照片,其组织为回火索氏体+铁素体,铁素体呈游离块状,分布不均。
组织中块状游离态铁素体的出现,主要是由于热处理加热过程中加热温度偏低或保温时间不足,也即热处理不充分,造成部分铁素体未能完全溶解于奥氏体,并在随后的冷却过程中保留下来。
这种游离态铁素体组织属淬火欠热组织,其硬度低,强度也低,大大降低了钢的使用性能,尤其是显著降低钢的冲击韧性。
另外,金相照片还发现不少黑点存在,初步判定为夹杂或者热处理过程中脱碳造成,确切的构成可以通过区域能谱分析进行进一步的确认。
但是不管是夹杂还是石墨,都会在一定程度上割裂基体,减少承载面,降低材料力学性能,有时甚至会成为裂纹萌生源,继而不断扩展而最终完全断裂。
平均312/30.3315/30.7335/32.7344/34.0根据“GB/T 3098.1-2010紧固件机械性能螺栓、螺钉和螺柱”要求,M22×1.5对应于10.9级规定,维氏硬度在HV320-380之间,最小拉力载荷346000N,保证载荷376000N,国标规定表面硬度允许高于芯部硬度,其最大差值为30个维氏硬度值(螺栓表面没有渗碳处理的情况)。
M20轮胎螺栓断裂分析报告

[1] 赵东标,朱剑英.智能制造技术与系统的发展与研究 [J].中国机械工程,1999,10(8):927-931.
[2] 邵立,严隽琪,马登哲,等.生产线的虚拟集成设计[J]. 工业工程与管理,2000,5(6):1-4.
(上接第34页)
进而产生疲劳断裂,从而导致整个轮毂上的螺栓松 导致螺栓在实际装配中出现假拧紧状态,未充分利
1 概述 委托方提供规格为M20×1.5-M20×1.5×83的
10.9级后右车轮螺栓断裂部件五件(两件短件断口 与其余三件断口不能完好连接,故为五件),材质 为40Cr。 该款产品在实际使用过程中断裂,通过委 托方描述,汽车在正常运输过程中出现后右轮胎脱 出现象,造成外车轮总成脱落飞出,内车轮轮胎、 钢圈破裂报废。
2 宏观分析 根据委托方提供样品可见螺栓断裂发生在螺纹
部位,在最终断裂时,断裂部位未发生明显塑性变 形,说明螺栓断裂时承受较小的轴向拉伸力。外部 断口整齐,内部呈现波浪状,说明螺栓在断裂前承 受横向弯曲力,可初步判定为疲劳剪切断裂。
3 化学成分分析 采用直读光谱法对螺栓进行化学成分分析,结
果如下表所示,其化学成分符合40Cr钢的要求。
标准 实测
C% 0.37-0.44
0.38
Si% 0.17-0.37
0.18
Mn% 0.50-0.80
0.67
P% ≤ 0.025
0.012Sຫໍສະໝຸດ ≤ 0.0250.025
Cr% 0.80-1.10
0.96
4 摩擦系数分析
预紧力下扭矩 T(Nm) 330 380 330 380 330 380
动或断裂。
用螺栓性能。
6 结论 送检螺栓出现断裂的主要原因是螺栓在实际装
30CrMnSiNi2A螺栓断裂分析
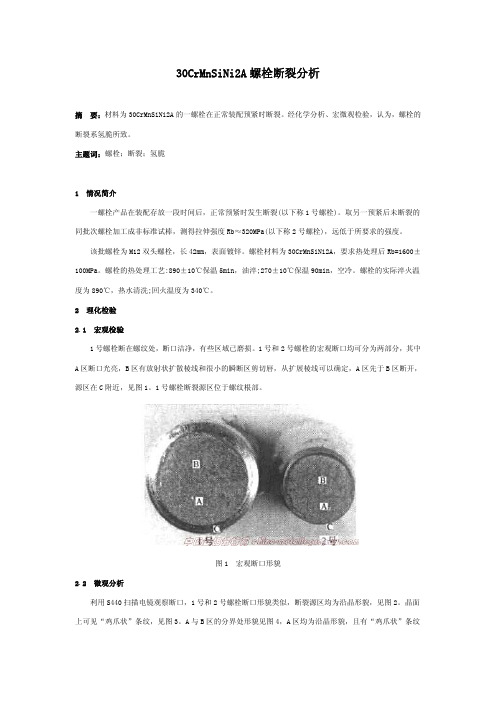
30CrMnSiNi2A螺栓断裂分析摘 要:材料为30CrMnSiNi2A的一螺栓在正常装配预紧时断裂。
经化学分析、宏微观检验,认为,螺栓的断裂系氢脆所致。
主题词:螺栓;断裂;氢脆1 情况简介一螺栓产品在装配存放一段时间后,正常预紧时发生断裂(以下称1号螺栓)。
取另一预紧后未断裂的同批次螺栓加工成非标准试棒,测得拉伸强度Rb≈320MPa(以下称2号螺栓),远低于所要求的强度。
该批螺栓为M12双头螺栓,长42mm,表面镀锌。
螺栓材料为30CrMnSiNi2A,要求热处理后Rb=1600±100MPa。
螺栓的热处理工艺:890±10℃保温5min,油淬;270±10℃保温90min,空冷。
螺栓的实际淬火温度为890℃,热水清洗;回火温度为340℃。
2 理化检验2.1 宏观检验1号螺栓断在螺纹处,断口洁净,有些区域已磨损。
1号和2号螺栓的宏观断口均可分为两部分,其中A区断口光亮,B区有放射状扩散棱线和很小的瞬断区剪切唇,从扩展棱线可以确定,A区先于B区断开,源区在C附近,见图1。
1号螺栓断裂源区位于螺纹根部。
图1 宏观断口形貌2.2 微观分析利用S440扫描电镜观察断口,1号和2号螺栓断口形貌类似,断裂源区均为沿晶形貌,见图2。
晶面上可见“鸡爪状”条纹,见图3。
A与B区的分界处形貌见图4,A区均为沿晶形貌,且有“鸡爪状”条纹和二次裂纹;B区为脆性沿晶和韧窝的混合断裂形貌,沿晶形貌的晶面也可见“鸡爪状”条纹和二次裂纹;剪切唇区为细小韧窝,见图5。
图2 源区形貌 图3 晶面“鸡爪状”条纹形貌图4 A与B两区交界处形貌 图5 剪切唇区韧窝形貌利用Link能谱分析仪测试源区和沿晶形貌区域,未发现金属基体元素以外的其它腐蚀产物或杂质元素。
断口形貌表明螺栓断裂为氢脆所致。
2.3 显微硬度测试用MVK2H11显微硬度测试仪,测试两螺栓的显微硬度,结果见表1。
可见,同批次两螺栓及螺栓的沿晶断裂区和混合断裂区的硬度无甚差别。
六角头螺栓断裂分析

六角头螺栓断裂分析接到客户的质量反馈,重载矿山机械车辆轴承包紧固螺栓断裂导致轴承包脱落,现场反馈如下:是什么原因导致的螺栓断裂?是螺栓本身存在质量缺陷还是其他原因引起的连锁反应呢?我们一起探讨下...一、理化检验◆ 宏观检测a. 失效螺栓断裂形态见下图:观察图片,可见失效螺栓锈蚀严重,断裂位置存在明显的缩颈变形(红色虚线区域)。
失效螺栓断裂位置存在缩颈,说明螺栓在断裂之前承受了较大的拉应力而不是突然出现的脆性断裂。
b. 失效螺栓断面形态见下图:观察失效螺栓断口宏观形貌,断口较平整,存在明显的剪切唇,部分区域呈波纹状花纹,将断口分为源裂纹区(红色虚线区域)、裂纹扩展区(波纹状花纹)、最后断裂区(绿色虚线区域)。
源裂纹区位于螺纹根部表面,锈蚀严重且锈迹向螺栓中心位置扩散,存在较大剪切唇。
结合螺栓实际安装位置,分析该区域在断裂之前,承受了一定的剪切力导致此位置出现裂纹,在使用过程中裂纹逐渐扩散,最终发生断裂。
◆ 化学成分分析使用光谱仪对失效样品进行化学成分检测,检测结果见下表:比照GB/T 3077-2015标准,该物料材质应该为40Cr合金钢,该材质满足标准ISO 898-1中规定的10.9级螺栓材质要求以及热处理性能要求。
◆维氏硬度检测使用HV30硬度仪对失效样品进行检测,并与发货时原始数据比对,ISO 898-1标准要求10.9级螺栓维氏硬度(≥HV10)为320HV-380HV,检测结果见下表:拉伸实验检测取同批次未断裂螺栓一支进行拉伸实验,检测结果为1136.8Mpa,大于标准ISO 898-1要求的1040Mpa,抗拉强度合格。
-20℃冲击试验检测取同批次未断裂螺栓一支进行-20℃冲击试验,检测结果为58.75J,大于标准ISO 898-1要求的27J,-20℃冲击合格。
金相检测使用金相显微镜对失效件样品金相组织进行检测(500X),检测结果见下图:可见螺栓金相组织为典型的回火屈氏体组织,碳化物分布均匀,组织无明显异常。
40Cr高强螺栓断裂分析

螺栓材料的化学成分符合规定要求,螺栓的组织不是正常的调质组织,材料的硬度也偏
低。
主要分析人员及单位
朱衍勇 教授级高工 钢铁研究总院
董毅 工程师
钢铁研究总院
资料整理人:王冬梅 国家钢铁材料测试中心 审核人: 吴伯群 国家钢铁材料测试中心
网 理断口呈片层状、羽毛状和细条状,在高倍下看出,微观断面上的片层撕裂棱边缘发生轻微
的圆钝化,具有开裂后又受到热影响的痕迹,这是钢中白点缺陷的断口微观特征。
2
中
国
缺陷区断口形态
应
急
分 缺陷区混合断口
析
网
断口受到热影响表面轻微的圆钝化 图 2 断裂源区微观形态
在裂纹源区的边缘断口中可以观察到有韧窝状断口,如图 3,这是在被钝化的初始裂纹 的基础上发生裂纹扩展形成的伸张区断口特征。伸张区断口的外侧为裂纹快速扩展形成的解 理断口,如图 4,解理断裂是一种穿晶脆性断裂。与裂纹源与扩展区之间过渡观察到伸张区 韧窝断口带形成鲜明的对比。断口上也没有看到疲劳的痕迹。由此可以断定,螺栓断口是在
记录号:JS-AL-紧固件-015
40Cr 高强螺栓断裂原因分析
摘要:某螺栓设计安装公称预紧拉力 450 吨,在安装过程中拉力达到 120 吨左右时突然断裂。
中对断裂螺栓试样进行化学成分分析、断口分析、无损检测、金相组织分析及硬度测试,结果 表明:该螺栓属于一次性正应力载荷作用下的脆性断裂,螺栓材料内部存在较大尺寸的具有 裂纹性质的白点缺陷是造成螺栓在远未达到设计要求的载荷下发生脆性断裂的主要原因。
断裂源位置和裂纹扩展的方向如图中箭头所示。断裂源位于偏离中心约 1/3 半径的位置,源
螺栓断裂原因分析及预防

螺栓断裂原因分析及预防摘要:本文通过对失效螺栓及同批次的零件进行理化分析和无损检测。
对断裂件进行了宏观、微观断口观察、金相组织检查、硬度、化学成分、破坏拉力等一系列试验,经分析找出螺栓失效原因,并提出预防措施。
关键词:螺栓断裂回火脆化螺栓作为飞机上重要的紧固件,其发生断裂危害较大。
我厂修理过程中使用的螺栓主要为M4、M5、M6、M8和M10等规格,然而在某产品装配和停放过程中,某批次30CrMnSiA M8的螺栓先后发生脆性断裂。
引起工厂高度重视,因为螺栓发生脆断,不论是氢脆断裂,还是热处理造成的脆性断裂大都与“批次性”问题有关,涉及数量多,危害大,组织专业人员对螺栓在装配过程中及装配一段时间后发生断裂的原因进行了分析,并对后续的预防工作,提出了建议和方案。
1 宏观、微观检查对断裂螺栓进行宏观观察:发现断裂位置接近于第一扣螺纹处见(图1)。
断裂处螺纹表面未发现有明显的机械接触痕迹,如压坑、啃刀、划伤等表面缺陷,也未发现热处理表面烧蚀痕迹、螺纹变形等现象,没有局部麻点、剥蚀等缺陷。
断裂螺栓螺纹牙底呈线性起源,放射棱线粗大,断口附近无明显宏观塑性变形,断口齐平,呈暗灰色,断面粗糙,具有金属光泽(图2)。
图1断裂螺栓图2螺栓断口图3 螺栓整体形貌对裂纹断口进行观察,断口特征呈现以沿晶为主+韧窝的混合断裂形貌,且断口源区未见冶金和加工等产生的缺陷。
对同批次的螺栓抽样进行了磁粉检测,在螺纹的根部没有发现表面或近表面裂纹,对螺栓进行X射线检测,也没有发现内部缺陷。
同批螺栓见图3。
2 材质检验2.1成份分析抽取同批次的螺栓去掉镀层后制取化学粉末,采用碳、硫联合测定仪对碳、硫含量进行了检测,利用QSN750光谱仪对其它元素进行了检测,结果见(表1),螺栓的化学成分符合技术要求,但含碳量较高。
表1 化学成份检测结果表2.2 金相分析在靠近断口位置切取金相试样,镶嵌、磨抛、腐蚀后,显微镜对试样进行组织观察,螺栓显微组织为较粗大的回火马氏体(图4)。
- 1、下载文档前请自行甄别文档内容的完整性,平台不提供额外的编辑、内容补充、找答案等附加服务。
- 2、"仅部分预览"的文档,不可在线预览部分如存在完整性等问题,可反馈申请退款(可完整预览的文档不适用该条件!)。
- 3、如文档侵犯您的权益,请联系客服反馈,我们会尽快为您处理(人工客服工作时间:9:00-18:30)。
高强度螺栓断裂分析曾振鹏(上海交通大学高温材料及高温测试教育部重点实验室,上海200030)摘要:采用断口分析、金相检验和硬度测定等方法,对高强度螺栓断裂原因进行了分析。
断口分析结果表明,断口平坦,呈放射状花样,微观形态主要为准解理花样,表明螺栓的断裂是脆性断裂;同时发现,在断口附近还存在横向内裂纹,内裂纹的断口形态与断裂断口一样。
金相分析表明,材料棒中存在严重的中心碳偏析,而中心碳偏析是引起断裂的主要原因。
关键词:高强度螺栓;准解理;横向内裂纹;中心碳偏析某厂生产的一批规格为M30×160mm的高强度大六角头螺栓,在进行验收试验时发生断裂。
螺栓材料为35CrMoA,采用常规工艺生产,硬度要求为35~39HRC。
1 检验1.1 材料的化学成分用VD25直读光谱仪进行了材料化学成分分析,分析结果(质量分数)列于表1。
从表1可以看出,材料的化学成分符合标准要求。
1.2 硬度测定硬度测定结果列于表2。
由表可见,螺栓材料硬度虽符合技术要求,但已接近上限。
1.3 材料的显微组织(1)在抛光态下,可见材料中含有较严重的夹杂物,其形态、分布见图1。
对照标准[2],夹杂物级别为3~4级。
图1 夹杂物形态及分布状况100×图2 螺栓的显微组织280×4%硝酸酒精溶液侵蚀(2)显微组织见图2。
组织为回火马氏体+粒状贝氏体,并有少量铁素体。
从图2可明显看出,组织中存在严重偏析,出现回火马氏体和粒状贝氏体带,致使显微组织不均匀,而且在回火马氏体带中存在MnS夹杂。
对样品螺纹根部附近的组织进行了观察,未发现脱碳现象。
1.4 断口分析(1)图3a为断口的宏观形貌,断口较平坦,表面呈灰色,有明显的撕裂脊,呈放射状花样,放射线从中心向四周发射。
表明裂纹先在中心形成,然后向外扩展。
当裂纹扩展至整个横截面时,螺栓断裂。
图3 断口的宏观形貌图4 断口微观形貌(2)断口的微观形态基本上以准解理花样为主,还有一些二次裂纹,如图4所示。
从断口的宏观和微观分析可知,断裂断口为脆性断口,裂纹起源于中心部位。
裂纹产生后向四周扩展,直至螺栓断裂。
1.5 螺纹部位横向内裂纹(1)在制取金相试样时,发现试样螺纹部分至少还有1~2个垂直轴线的横向内裂纹,其纵截面形态见图5,似人的嘴形。
打开内裂纹,发现其面积已基本占据了整个横截面,其形态与断裂断口十分相似。
图3b为它的宏观形貌。
从断口的宏观形态上可以看出,裂纹面较平坦,呈灰色,有明显的呈放射花样的撕裂脊,放射线是从中心向四周放射的。
比较图3a 和图3b可以看出,它们的形貌是相同的。
裂纹断口的微观形态也是以准解理花样为主加二次裂纹。
断口的宏观、微观分析表明,该内裂纹断口与断裂断口本质上是一样的。
(2)将剩余部分的螺栓沿中心纵向剖开,用10%硝酸溶液侵蚀,发现材料心部有严重的碳偏析,存在明显的流线,见图6。
这与金相观察结果是一致的。
对存在偏析的显微组织进行显微硬度测定,发现偏析中的回火马氏体区域的硬度为48.2HRC,大大高于粒状贝氏体区域的硬度(35.5HRC)。
图5 螺纹部位的横向内裂纹纵截面形态图6 螺栓材料内部的碳偏析2 分析与讨论2.1 螺栓的横向内裂纹化学成分分析表明,螺栓材料的化学成分符合35CrMoA钢的标准成分,其硬度也在技术要求范围内(但已接近上限)。
但是从金相分析结果可以看出,材料的内在质量较差,心部存在碳偏析,不仅降低了材料的韧性和塑性,而且由于组织不均匀,引起心部硬度不均匀,最高硬度已达48HRC。
同时,材料中存在严重的夹杂物,致使螺栓心部材料硬而脆,因此施加载荷后首先在心部产生裂纹,而后形成横向内裂纹。
所谓钢材的碳偏析是指钢材内各部位含碳量的不均匀性。
碳偏析是树枝状偏析的结果,而树枝状偏析又是选择结晶的结果。
钢在结晶时,先形成枝干,然后形成枝间,先结晶的枝干比较纯,碳浓度较低,而迟结晶的枝间碳浓度较高,形成碳分布不均。
若钢材或锻件树枝晶发达,则钢的塑性和韧性降低,这种情况尤以中碳铬钼钢最为普遍,在压力加工时会形成流线,树枝晶偏析严重时还可使锻件破裂[3]。
碳偏析是在冶金过程中由于种种原因造成的。
紧固件原材料中的严重碳偏析会造成紧固件经热处理后各部位力学性能的显著差异。
文献[4]报道,有一批某型汽车上的45钢螺栓,在使用中连续发生断裂事故,经检查发现,断裂是由心部开始,整个断口呈放射状脆断形貌,将这批螺栓所用钢材沿其轧制方向剖开,发现在试样中心存在着内部裂纹,经酸蚀后可看出严重的中心碳偏析。
所以,可以认为,本例螺栓受载荷后产生脆性断裂和存在横向内裂纹是与螺栓材料内存在中心碳偏析有关。
2.2 内裂纹为什么内裂纹不象断口裂纹那样使螺栓断裂呢?这是因为拧紧螺母后,在螺杆上产生的轴向拉力分布是不均匀的,轴向力在旋合各圈罗纹牙间的分布呈双曲余弦函数关系,第一圈罗纹牙承受的轴向力最大,然后依次减小[5]。
因为与横向内裂纹相对应的螺纹处的轴向应力小,所以螺栓没有断裂。
2.3 材质虽然螺栓材料的化学成分符合35CrMoA钢标准,但其夹杂物含量较高(3~4级),且存在中心碳偏析,因此认为,该批螺栓的材质是不合格的。
3 结论(1)螺栓的断裂为脆性断裂。
(2)断裂的原因是因为螺栓材质不良———原材料棒中存在中心碳偏析以及严重的夹杂物。
4 建议(1)加强对原材料的质量检查。
(2)为了提高螺栓材料的综合力学性能,硬度控制在技术要求的中限附近。
40Cr钢螺栓断裂分析刘泽坤(湖北江山机械厂,襄樊441003)摘要:采用金相检验、硬度测试及化学成分分析等方法对变速箱制动鼓定位螺栓断裂的原因进行了分析。
结果表明,由于零件在热加工后未按要求进行热处理,导致出现非正常组织,降低了零件的硬度和强韧性,加上零件肩胛根部没有过渡圆弧易造成应力集中,因此在装车使用后不久便发生了螺栓断裂失效。
关键词:螺栓;断裂;显微组织;应力集中;铁素体1 情况简介我厂生产的某型号的变速箱在装车使用后不久,即发生了一批变速箱制动鼓定位螺栓断裂事故,断裂部位均发生在截面急剧变化的肩胛处。
由于该批螺栓系外购件,其热处理工艺尚不十分清楚。
按设计要求,该批螺栓为M14螺栓,其长度为55mm,材料为40Cr,热处理后调质硬度为255~321HBS,表面经软氮化处理,要求氮化层深度为0.05~012mm,硬度为35~50HRC,相当于329~509HV。
2 理化检验2.1 化学成分分析从螺栓上取样进行化学成分分析,结果列于表1。
可见螺栓的化学成分符合GB/T3077-1999的要求。
2.2 宏观断口分析断裂发生在螺栓肩部与杆部连接处,见图1。
按设计要求,杆部与肩部连接端应有滚花,长约10mm,其连接处应留R为0.5mm的过渡圆弧。
从断裂零件的肩部可见到明显的因滚花留下的挤压痕迹,说明滚花时已滚到零件的肩胛部,在连接处没有过渡圆弧。
断口表面较平整,无肉眼可见的宏观塑性变形,断裂零件表面亦未见明显的机械损伤痕迹,属一次性脆性断裂。
2.3 硬度测试将断裂螺栓两端磨平后进行硬度测试,测得心部硬度为235~250HBS,硬度偏低。
表面硬度为465~485HV,属于正常的软氮化硬度。
图1 螺栓断裂部位示意图(mm)2.4 金相检验从螺栓断裂部位取样进行金相检验,心部组织为网状铁素体+珠光体,并有少量呈针状的铁素体,由晶界向晶内延伸,呈现轻微的魏氏组织状态,见图2。
图2 断裂螺栓心部组织照片400×图3 正常调质螺栓心部组织照片400×4%硝酸酒精溶液侵蚀 4%硝酸酒精溶液侵蚀在R和滚花交界处沿纵向制样观察,基体材料中非金属夹杂物含量较少,符合国家标准要求,其近表面组织与心部组织基本相同,为珠光体+少量网状铁素体。
从使用正常未曾断裂的另一批螺栓上取样进行金相检验,在光学显微镜下,螺栓的显微组织为均匀回火索氏体,见图3。
3 结果分析由于该批零件是制动鼓定位螺栓,使用时承受较大的交变载荷,故要求零件应具有较高的强度和较好的冲击韧性。
根据成分分析可知,该零件所用材料的化学成分符合GB/T3077-1999中40Cr钢的要求,可排除因材料错用而造成的断裂。
从金相组织上看,由于该批零件心部组织是珠光体及少量铁素体,且铁素体呈网状分布,部分呈针状分布,这种组织同一般40Cr钢锻造正火组织极为相似[1]。
说明该批零件并未按要求进行调质处理,可能只是头部镦成型后进行正火处理。
由于这种网状铁素体的存在,破坏了组织的连续性,导致基体强度明显降低,塑、韧性下降。
有资料表明[2],钢件中魏氏组织的存在,使材料的力学性能明显下降,尤其是冲击韧性下降很多。
这种组织的形成是由于零件在热加工过程中的终锻温度过高而冷却又过缓,导致了铁素体沿晶界呈网状析出。
这种不良组织状态是造成零件断裂的根本原因。
从零件断裂的部位上看,断裂发生在肩胛的根部,由于该处没有过渡圆弧,容易形成应力集中,变速箱制动时,必然会加大对螺栓施加各方向应力,当应力超过其断裂强度时,造成在应力集中的薄弱处断裂。
4 结论螺栓断裂的根本原因是由于零件在热加工后,未按热处理工艺要求进行处理,造成零件组织状态不良,硬度偏低,强韧性较差。
加之零件机加工时,肩胛根部没有过渡圆弧,造成应力集中,一但受力较大必将导致沿圆周倒角处断裂。
日本爱信用高强度螺栓材质SCM440(主减齿圈连接螺栓)40Cr钢的最大屈服强度:试样毛坯尺寸(mm):25热处理:第一次淬火加热温度(℃):850;冷却剂:油第二次淬火加热温度(℃):-回火加热温度(℃):520;冷却剂:水、油抗拉强度(σb/MPa):≥980屈服点(σs/MPa):≥785断后伸长率(δ5/%):≥9断面收缩率(ψ/%):≥45冲击吸收功(Aku2/J):≥47布氏硬度(HBS100/3000)(退火或高温回火状态):≤42CrMo钢的机械性能●特性及适用范围:强度、淬透性高,韧性好,淬火时变形小,高温时有高的蠕变强度和持久强度。
用于制造要求较35CrMo钢强度更高和调质截面更大的锻件,如机车牵引用的大齿轮、增压器传动齿轮、后轴、受载荷极大的连杆及弹簧夹,也可用于 2000m以下石油深井钻杆接头与打捞工具等。
●化学成份:碳 C :0.38~0.45硅 Si:0.17~0.37锰 Mn:0.50~0.80硫 S :允许残余含量≤0.035磷 P :允许残余含量≤0.035铬 Cr:0.90~1.20镍 Ni:允许残余含量≤0.030铜 Cu:允许残余含量≤0.030钼 Mo:0.15~0.25●力学性能:抗拉强度σb (MPa):≥1080(110)屈服强度σs (MPa):≥930(95)伸长率δ5 (%):≥12断面收缩率ψ (%):≥45冲击功 Akv (J):≥63冲击韧性值αkv (J/cm2):≥78(8)硬度:≤217HB试样尺寸:试样毛坯尺寸为25mm最明显的区别,二次回火脆性倾向,42CrMo优于40Cr;再次,由于碳含量和合金元素总量,也高于后者,耐回火性好42CrMo淬透性优于40Cr,热处理工艺性能好。