高强度螺栓断裂失效分析
12.9级高强度螺栓断裂原因分析

~测试与分析-12. 9级高强度螺栓断裂原因分析焦丽1,赵英军1,张伟民2,孙晓东1,周兰梅1(1.河北华北柴油机有限责任公司,河北石家庄050081;2.陆军装备部驻北京地区军事代表局驻石家庄地区第三军事代表室,河北石家庄050081 )摘要:柴油机12.9级高强度螺栓材料为42C r M 〇钢,在紧固过程中发生断裂。
对断裂的螺栓进行了宏观 检验、化学成分分析、锻造纤维流线检验和金相检验,并检查了螺栓的加工工艺,以揭示其断裂的原 因。
结果表明:螺栓在镦锻过程中,头-杆结合部产生了裂纹,大大减小了螺栓的有效承载面积,在 紧固力的作用下发生断裂。
检查发现,螺栓有因热处理不当而产生的脱碳,但这不是造成螺栓断裂 的原因。
关键词:高强度螺栓;镦锻;断裂中图分类号:T G 157文献标志码:A文章编号:1008-丨690(2020)04-0042-04Analysis on Fracturing of 12.9 Grade High-strength BoltJIAO Li' , ZHAO Yingjun 1 , ZHANG Weimin2, SUN Xiaodong' , ZHOU Lanmei 1(1. H e b e i H u a b e i Diesel E n g i n e Co., Ltd., Shijiazhuang 050081 , H e b e i C h i n a ;2. 3th Military Representative Office in Shijiazhuang Reg io n of Military Representative B u r e a uof the A r m y A r m a m e n t D ep a r t m e n t in Beijing, Shijiazhuang 050081 , H e b e i China)Abstract : T h e 12.9 grade high-strength bolts of diesel engine, m a d e from 42C r M o steel, fractured in the processof fastening. T h e fractured bolt w a s tested for macroscopic a p p e a r a n c e , chemical c omposition, forged fibre flow a n d microstructure, a n d its work i ng process also w a s c h e c k e d , to discover the reason w h y i t fracturing. T h e results s h o w e d that crack e m a n a t e d from head-rod joint of the bolt during upsetting. A s a result, effective load-bearing area of the bolt w a s considerably reduced, thus fracturing under the action of fastening force. It w a s revealed from the examination that the bolt exhibited decarburization du e to the fault in heat treatment but this is not the cause of the bolt fracturing.Key words : high-strength bolt ; upsetting ; fracturing〇引言螺栓是普遍使用的紧固件,常被称为工业之 米[|]。
高强度螺栓断裂金相分析
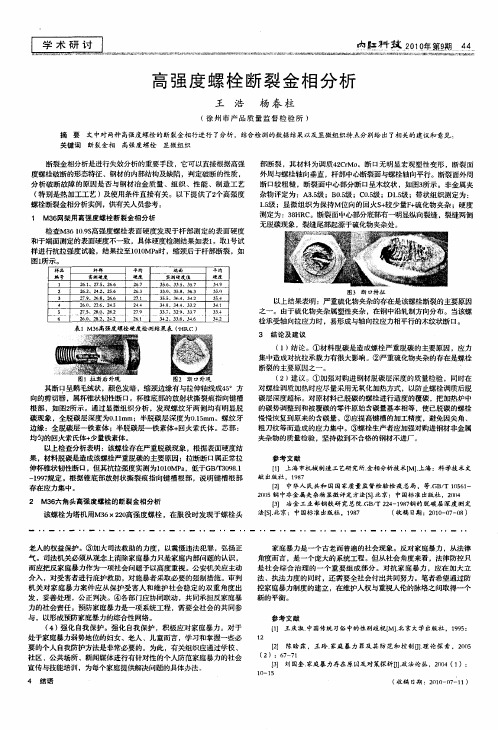
4 结 语
控 家庭暴力制度的建立 ,在维护人权与重视人伦 的脉络之间取得一个 新的平衡 。
参 考 文 献
【 王 庆淑 中国传统 习俗 中的性 别歧视 【 . 1 】 M】 北京 大学 出版社 ,19 : 95
1 2
【】 陈 晗 霖 ,王玲 . 2 家庭 暴 力 罪 及 其 防 范 和控 制 卟 理 论 探 索 ,2 0 05
老人的权益保护 。 加大司法救助的力度 ,以震慑违法犯罪 ,弘扬正 ③ 气 。司法机关 必须从 观念上 消除家庭暴力只是家庭 内部问题的认识 , 而应把反 家庭暴 力作 为一项社 会问题予以高度重视 。公安机关应主动 介入 ,对受 害者进行庇护救助 , 对施暴者 采取必 要的强制措施。审判
测定 为 : 8 R 3 H C。断裂面 中心部分底部有一明显纵向裂缝 ,裂缝两 侧 无脱碳现象 , 裂缝尾 部起 源于硫化物夹杂处 。
检 查M3 . 高强 度螺栓表面 硬度 发现于杆 部测 定的表面硬度 61 9 0S 和予端面测定 的表面硬度不一致 ,具体硬度检测结果如表 1 。取 l 号试 样进行抗拉强度 试验 ,结果拉至 1 1MP 时 ,缩 颈后于杆部断裂 ,如 00 a 图l 所示 。
家庭暴力是 一个古 老而普遍的社会现 象。反对 家庭暴 力 ,从 法律 角度 而言 。是一个庞 大的系统工程 。但从社会 角度来看 ,法律 防控 只 是社会 综合 治理的 一个重要 组成 部分 。对抗 家庭暴 力 ,应在 加大立 法 、执法力度的 同时 ,还需要全社会付 出共 同努力 。笔者希望通过防
12.9级高强度螺栓断裂失效分析
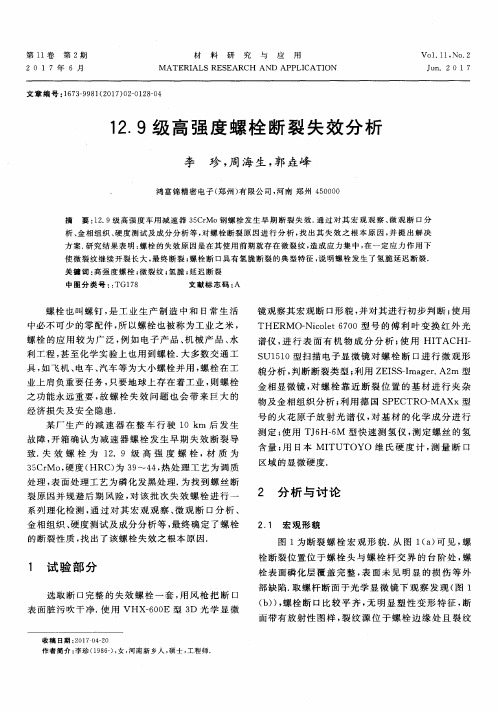
图 1 断 裂螺 宏 观 形 貌 ( a ) 断裂螺栓照 片 . 6 X: ( h )断 【 I 宏观彤批 . : ( 1
Fi g 1 A pp c a r  ̄ L I ] C L o 1 ) 、 r va t { o 1 1 of f ai l L I F t b ol t ( 1 ) p i c I L I F ( ,o f f a i l u r e l } o l t . 6X : ( 1 1 )ap p 4 J ar  ̄ t i 1 “- o1 ) S U I + V  ̄ t t i on of f r a  ̄ ’ t ur e S uI - f  ̄ t c c. 9 o X
貌 分析 , 判 断断 裂类 型 ; 利用 Z E I S S - I ma g e r . A2 m 型 金 相显 微镜 , 对 螺 栓 靠 近 断 裂 位 置 的 基 材 进 行 夹 杂
物 及金 相组 织 分析 ; 利用德国 S P E C TR O- MAX x型
业 上肩 负 重要任 务 , 只要 地球 上存 在着 工业 , 则 螺 栓
表 面脏 污吹 干 净. 使 用 VHX - 6 0 0 E型 3 D光 学 显 微
( b ) ) , 螺栓 断 口比较 平 齐 , 无 明显 塑 性 变 形 特 征 , 断 面 带有 放射 性 图样 , 裂 纹 源 位 于 螺栓 边缘 处 且 裂 纹
收 稿 日期 : 2 0 1 7 - 0 4 — 2 0
Байду номын сангаас
作者简介 : 李珍( 1 9 8 6 - ) , 女, 河 南 新 乡人 , 硕士 , 工 程 师
源 与扩 展 【 x 均仃 褐 的 物 仔 . 这 足f } r r 减 速
20MnTiB钢螺栓断裂失效分析

王 弘等 : 20M nT iB 钢螺栓断裂失效分析
门槛应力 , 不足以发生应力腐蚀开裂[ 3] 。 ( 3) X 射线微区元素定性分析结果显示腐蚀物 为铁的氧化物, 表明上述应力腐蚀的机理是阳极溶 解型
[ 3]
保证结构的使用安全。
5
Байду номын сангаас结论
。 由于受测试性能的限制 , 电子探针仪仅能分析
螺栓断裂失效的主要原因是由于螺栓根部存在 着初始裂纹, 初始裂纹尖端的应力集中和露天工作 环境的共同作用使螺栓产生应力腐蚀开裂。应力腐 蚀开裂的方式是阳极溶解型。 参考文献 :
收稿日期 : 2002 10 21 作者简介 : 王 弘 ( 1960 ) , 男 , 副教授 , 硕士。
M22( GB1228- 1984) , 螺栓材料为 20MnT iB 钢, 这是 国标推荐的高强度螺栓用钢 , 在相同硬度下, 与中碳 合金钢比较, 具有更加良好的韧性和可锻性, 较好的 强韧性, 还 可避免脱 碳现象[ 1] 。其 化学成 分 ( 质量 分数) 为: C 0. 17% ~ 0. 24% , Si 0. 17% ~ 0 37% , Mn 1 30% ~ 1. 60% , T i 0. 04% ~ 0. 1% , P< 0. 035% , S< 0. 035% , B 0. 0005% ~ 0. 0035% 。 螺栓材料在加工前经过严格的化学成分检验, 符合标准要求。加工螺栓用毛坯为热轧圆钢。加工 前毛坯全样经超声波无损探伤检验合格。螺纹采用 滚丝工艺加工。其热处理工艺为 880 400 中温 回火, 组 织为回火屈氏 体
500 #
T he corrosive on fracture surface
M icrostructure of failed bolt
高强度螺栓断裂分析-扭矩过大

记录号:JS-AL-紧固件-023
高强度螺栓断裂分析
摘要:由 30CrMnSi 制造的高强度螺栓,经调质处理,在安装时发生断裂。分析结果表明: 螺栓断裂是由于外应力过载引起的超载断裂。
中关键词:高强度螺栓;超载断裂 材料种类/牌号:合金结构钢/30CrMnSi 概述 国由30CrMnSi制造的高强度螺栓,经调质处理,在安装时发生断裂。 测试过程与结果 断口分析 应 断口宏观形貌属纤维状断口,如图1所示,由纤维状分布形态可判断螺栓为扭力作用下 引起的断裂。
急 分 析 网
图1 螺栓断口宏观形貌,纤维状条纹由螺纹根部区发散,条纹呈弧形弯曲, 说明主要是在超载扭转应力作用下引起的断裂。
扫描电镜观察断口属韧窝型断裂,如图2所示。由于材料强度较高,断裂时速度较快, 在某些部位出现准解理断裂,如图3 所示。
1
中 国 应 急 图2 螺栓断口扫描电镜形貌,略带方向性的韧窝,由于螺栓材料强度较高,
故韧窝较小。
分 析 网
图3 螺栓断口微观形貌以韧窝为主,局部有少量的准解理断裂,这是由于螺栓材 料强度较高及断裂时外应力较高所致。这些特征均为外应力过载造成的断裂 特征。
金相检验 金相检验显微组织为回火索氏体,组织正常。
结论
2
分析结果表明螺栓断裂是由于外应力过载引起的超载断裂。
参考文献
[1]黄振东.钢铁金相图谱.北京:中国科技文化出版社,2005,1258-1259 页.
中资料整理人:王冬梅 审核人: 吴伯群
国家钢铁材料测试中心 国家钢铁材料测试中心
国
应急分析网 Nhomakorabea3
大型起重机高强度螺栓的断裂失效分析

大型起重机高强度螺栓的断裂失效分析摘要:本文通过对一台大型起重机高强度螺栓断裂失效的分析,探究其原因和解决方法。
初步分析结果表明,螺栓断裂的主要原因是材料强度不足、应力过大和使用环境恶劣等因素导致的。
针对这些问题,本文提出了一系列改进措施,包括选用高强度材料、降低应力和改善使用环境等方面。
通过实验验证和理论计算,改进后的螺栓具备更高的强度和耐用性,可以有效地提高装置的稳定性和安全性。
关键词:起重机;高强度螺栓;断裂失效;强度分析;改进措施正文:1. 背景介绍大型起重机是现代工业中不可或缺的设备之一。
在使用过程中,螺栓作为连接装置的重要组成部分,在保证装置的稳定性和安全性方面起着至关重要的作用。
然而,螺栓也是易受力集中的零部件,容易出现断裂失效的情况。
因此,对螺栓失效进行分析和解决具有重要的理论和实践意义。
2. 断裂失效分析2.1 断裂形态分析通过对失效螺栓的断口形态进行分析,可以初步了解其失效原因。
观察失效螺栓的断口,发现其呈现出典型的断裂韧突混合断口。
2.2 强度分析对失效螺栓的材料进行强度测试,发现其强度值低于设计要求。
在使用过程中,由于受到集中载荷的作用,应力过大导致螺栓逐渐疲劳并最终断裂。
2.3 环境分析失效螺栓所处的使用环境恶劣,存在高温、湿润等不利因素。
因此,失效的螺栓容易受到腐蚀和氧化等影响,导致其材料性能和强度下降。
3. 改进措施针对分析结果,本文提出了一系列改进措施:3.1 选用高强度材料为了提高螺栓的强度,可以选用高强度材料来替代原有的材料,例如S45C、SCM43等。
这样既可以提高螺栓的耐久性,也可以在承受大载荷时发挥更好的作用。
3.2 降低应力在设计过程中,应尽可能减小螺栓所承受的载荷和应力,从而减少螺栓的疲劳损伤和断裂的可能性。
可以通过优化结构、增加支撑和缓冲措施等方法实现此目的。
3.3 改善使用环境在实际使用中,应注意维护和保养,防止螺栓受到腐蚀和氧化的影响。
可以采用表面防护涂层、常规保养和定期更换等措施,延长螺栓的使用寿命。
20MnTiB螺栓失效分析

20MnTiB螺栓失效分析1 概述高强度螺栓是继铆接、焊接之后发展起来的一种钢结构连接型式。
它具有施工简单、可拆卸、承载大、耐疲劳、较安全等优点。
因此, 高强度螺栓连接已发展成为钢结构工程安装的主要手段。
20MnTiB钢高强度螺栓用于航天发射塔架斜支梁、悬臂梁及主梁联结板的连接。
在进行服役过程中,发现有少量连接螺栓断裂的现象。
本文通过断裂螺栓的断口、显微组织、显微硬度和微区成分进行了分析。
查找螺栓失效原因,制定改进措施,以防止同类失效再度发生。
2 螺栓的材料及技术条件螺栓型号为M22(GB1228-1984),螺栓材料为20MnTiB钢,这是国标推荐的高强度螺栓用钢,在相同硬度下,与中碳合金钢比较,具有更加良好的韧性和可锻性,较好的强韧性,还可避免脱碳现象。
其化学成分如表1表1 螺栓化学成分(W B)C Mn Si P S Cu Cr TI B 样品0.22 1.38 0.99 0.006 0.023 0.15 0.07 0.07 0.0018该批螺栓所用钢材化学成分符合标准要求,P、S、Cu等残余元素也控制在合理范围之内。
加工螺栓用毛坯为热轧圆钢。
制造工艺流程如下:20MnTiB圆钢(盘条)酸洗拉拔冷镦成型搓丝热处理发黑包装入库其热处理工艺为880℃油淬,380~400℃中温回火,组织为回火屈氏体。
每批成品均抽样作静拉伸实验,力学性能达到GB1231-1984标准中10.9S的螺栓性能等级要求,σb为1040~1240MPa,σs≥940MPa,δ5≥10%,ψ≥42%,A k≥58.8N·m,维氏硬度为312~367HV30,洛氏硬度为33~39HRC。
3断裂螺栓失效分析3.1断口宏观形貌分析宏观下,断裂螺栓断口具有脆性特征,如图1。
断口面位于螺栓的第五个螺纹处。
断口可分为三个区域:裂纹源区、裂纹扩展区和最终瞬断区。
未观察到疲劳断裂特征。
裂纹源区位于螺纹根部,其放大形貌,如图2。
在裂纹源区可观察到一扁长形状的原始裂纹,长约 5.5mm,深约0.8mm,在其旁有一半月形的锈蚀区。
螺栓断裂分析报告

螺栓断裂分析报告一、引言螺栓是一种常见的连接元件,在机械设备和结构工程中得到广泛应用。
然而,螺栓在使用中可能会发生断裂,给机械设备和结构的安全运行带来隐患。
本报告旨在对螺栓断裂进行分析,并提供解决方案,以确保设备和结构的安全性。
二、螺栓断裂原因分析1.质量问题:螺栓断裂可能是由于螺栓本身存在质量问题所致,如材料强度不符合标准、制造工艺不良等。
为此,应关注螺栓的采购渠道和制造工艺,并严格按照相关标准进行选择和检测。
3.腐蚀问题:腐蚀是导致螺栓断裂的常见原因之一、在潮湿、酸性或碱性环境中,螺栓易受到腐蚀,使其材料的强度降低。
因此,在腐蚀环境中应选择抗腐蚀性能良好的螺栓材料,并进行定期维护保养。
4.紧固力不均匀:不正确的紧固力分布可能导致螺栓在负载过程中承受不均匀的力,从而引发断裂。
在安装过程中,应根据设备或结构的要求,采用正确的紧固力分布方案,并进行定期检查和调整。
三、螺栓断裂的解决方案1.优化选材:根据设备或结构的负荷、工作环境等要求,选择合适的螺栓材料。
关注材料的强度、韧性、抗腐蚀性等指标,并遵循标准进行选材。
2.合理设计螺栓连接:根据实际负荷情况和工作要求,合理选用螺栓的规格、数量和布置方式,并确保紧固力的均匀分布。
在设计过程中,可以借助有限元分析等工具来验证螺栓连接的安全性。
3.定期检查和维护:对于暴露在恶劣环境中的螺栓,应定期进行检查和维护,特别是针对腐蚀环境。
清洁螺栓表面,涂覆抗腐蚀涂层,必要时更换受损螺栓,以延长其使用寿命。
4.强化管理和培训:通过建立规范的螺栓管理制度和培训机制,提高操作人员的专业水平,加强螺栓使用和维护的知识宣传,以减少螺栓断裂的发生。
四、结论螺栓断裂是机械设备和结构工程中常见的问题,但可以通过合理选材、优化设计、定期维护和加强管理来减少其发生。
对于已经断裂的螺栓,应及时进行更换,并对其断裂原因进行调查分析,以避免类似问题再次发生。
通过以上措施的综合应用,能够提高螺栓连接的安全性和可靠性,保证设备和结构的正常运行。
- 1、下载文档前请自行甄别文档内容的完整性,平台不提供额外的编辑、内容补充、找答案等附加服务。
- 2、"仅部分预览"的文档,不可在线预览部分如存在完整性等问题,可反馈申请退款(可完整预览的文档不适用该条件!)。
- 3、如文档侵犯您的权益,请联系客服反馈,我们会尽快为您处理(人工客服工作时间:9:00-18:30)。
高强度螺栓断裂失效分析韩志良(常州机电职业技术学院机械系,常州213012)马红卫,丁燕君(常柴股份有限公司理化室,常州213002)摘要:针对装配现场发生的几起高强度螺栓断裂失效事故,采用金相分析、化学成分分析和力学性能测试等方法进行检测。
分析结果认为螺栓失效的原因有:(1)螺纹成形时产生裂纹,螺栓因之而脆断;(2)杆部与头部交接处表面脱碳、使局部强度降低而断裂;(3)装配时扭矩过大,螺栓明显缩颈而断裂;(4)原材料中心存在裂纹。
关键词:螺栓;裂纹;扭转;脱碳高强度螺栓是发动机紧固件中最重要的零件之一,如连杆螺栓、缸盖螺栓、主轴承盖螺栓,要求强度等级为10.9级,有的甚至达12.9级。
但在实际使用中,高强度螺栓(简称螺栓)断裂失效也时有发生。
笔者就发生在装配过程中的四起高强度螺栓断裂失效逐一进行分析。
1 195连杆螺栓断裂失效分析195连杆螺栓装配时断裂于螺纹处。
从断口上看,断口平直,无缩颈,几乎没有裂纹萌生区,全部为最后瞬断区。
零件供应商进行了失效分析,认为装配时连杆螺纹内夹入异物,阻碍了螺纹的拧紧,导致装配扭矩过大而断裂。
1.1 断口分析由于断口表现出极大的脆性,如果是基于扭紧力矩过大而断裂,断口应表现出良好的塑性,因为拧紧时螺栓主要受扭转应力,而扭转试验的应力状态的柔性系数较大(大于拉伸试验),材料易于塑性变形,而失效的螺栓并未表现出塑性。
另外,断裂源也不在齿根部,而是有所偏离。
1.2 化学成分和显微组织分析螺栓材料牌号为40Cr钢,强度等级10.9级,硬度要求32~38HRC,金相组织要求1~3级(JB/T8837-2000)。
经检验,螺栓化学成分(质量分数)符合GB/T3077-1988之规定,见表1。
显微组织为细的回火索氏体,按JB/T8837-2000评定为1级,其硬度值为34HRC和35HRC,硬度和显微组织均符合技术条件规定。
经磁粉探伤未发现磁痕。
将螺栓从杆部与头部交接处纵向剖开,经金相制样、观察,结果在大部分螺纹的根部均有裂纹,即在断口附近和远离断口的螺纹处均存在裂纹,裂纹位置偏离“真正的”齿根部,裂纹的两侧无贫碳和脱碳,说明裂纹的形成与调质处理无关,见图1和图2。
由于裂纹细小且位于螺纹根部,常规磁粉探伤未发现磁痕。
1 螺纹根部之裂纹(未侵蚀) 20×图2 螺纹根部组织400×4%硝酸酒精溶液侵蚀1.3 试验与讨论为判定裂纹的形成原因,另取同批量、同型号但未使用过的连杆螺栓进行纵剖面金相分析,结果在部分螺纹根部也存在裂纹,因此判定此裂纹系滚齿成型时造成的。
这与滚轮使用次数过多,滚齿加工能力下降有关,经查该批滚轮已超期服役。
由于螺纹根部存在裂纹,因此在装配拧紧时螺栓表现出较大的脆性,发生脆性断裂,而滚轮超期服役,其滚齿加工能力下降则是失效的主要因素。
2 缸盖螺栓断裂失效分析某单位生产的强度等级为10.9级的缸盖螺栓,在装配时发生断裂,送样要求分析原因。
2.1 断口分析两缸盖螺栓(分别编1号和2号)断裂位置均在杆部和头部交接处,装配拧紧时螺栓主要受扭转载荷,此时,主应力与轴线成45°,而切应力则与轴线垂直。
从断口看,裂纹开始区与轴线成45°角,表现为扭转时的正断断口,是正应力作用的结果。
而瞬断区与轴线垂直,瞬断区面积占总断口面积的绝大部分,说明断裂时应力较大或材料强度不足。
2.2 化学成分和显微组织分析螺栓材料牌号为40Cr钢,硬度要求32~38HRC,金相组织要求1~3级(JB/T8837-2000)。
经检验,1号缸盖螺栓化学成分(质量分数)符合GB/T3077-1988之规定,见表1。
两螺栓基体组织均为细的回火索氏体,按JB/T8837-2000评定,组织为1级,符合其1~3级之技术条件规定。
边缘组织中晶界清晰可见,但其颜色明显比其它部位浅,估计表面存在脱碳层,其中2号螺栓更为明显,见图3。
两螺栓均残留带状组织,带状组织中还有非金属夹杂物,1号螺栓的带状组织见图4,其间的硫化物类夹杂物清晰可见,但均在规定范围之内。
2.3 显微硬度测试经磁粉探伤,未发现磁痕。
经测定,1号螺栓硬度值为34HRC,2号螺栓硬度值为36HRC和37HRC,符合32~38HRC技术条件规定。
由于螺栓已经过调质处理,所以仅根据金相组织来判定边缘是否存在脱碳层似乎尚缺证据。
为证实边缘是否存在脱碳层,对边缘和中心部位进行了显微硬度测试,结果见表2。
图3 2号螺栓组织,边缘颜色较浅65×图4 1号螺栓的带状组织130×4%硝酸酒精溶液浸蚀表2 螺栓边缘及中心处显微硬度值从表中可见,边缘硬度低于中心硬度,进一步证实了边缘存在脱碳层。
边缘碳含量的降低,使侵蚀程度下降,因而颜色较浅且晶界清晰可见。
虽然螺栓在调质后对其表面进行了机加工,以去除热加工所产生的脱碳层,但在杆部与头部交接处往往难以用机械加工去除脱碳层,结果在杆和头部的交接处保留了脱碳层。
2.4 分析与讨论由于最大应力位于螺栓边缘,而边缘存在脱碳,降低了边缘的强度。
虽然螺栓允许存在一定量的脱碳层,但脱碳层的存在对螺栓服役总是不利的。
由于裂纹源于脱碳处,那么脱碳则成为该螺栓断裂失效的主要因素之一。
3 主轴承盖螺栓断裂失效分析发动机主轴承盖螺栓,在装配拧紧时断裂失效。
螺栓材料牌号为40Cr钢,硬度要求30~35HRC,金相组织要求1~3级(JB/T8837-2000)。
3.1 理化分析观察三支断裂螺栓的断口,均存在回旋状塑性变形痕迹,为扭转断口,是以扭转为主的扭转和拉伸之混合断口。
裂纹起源于螺纹齿根处,断口处均有明显的缩颈。
而缩颈的产生,表明试样的载荷达到最大值(抗拉强度)后,在试样的某一部位截面开始急剧缩小,随后变形主要集中于缩颈附近。
所以缩颈的存在,一方面说明螺栓有良好的塑性和韧性,另一方面说明服役载荷很大,已超过试样的抗拉强度。
主轴承盖螺栓化学成分分析结果见表1,符合GB/T3077-1988之规定。
杆部硬度值为32HRC和33HRC,符合30~35HRC技术条件规定。
金相组织为细而均匀的回火索氏体,按JB/T8837-2000,组织级别为1级,符合其1~3级之技术条件规定。
经磁粉探伤未发现磁痕。
将三支断裂螺栓纵向剖开进行金相观察,螺纹表面无脱碳,但螺纹齿根处均存在微裂纹,长约0.05~0.10mm,裂纹均存在于距断口3~4个螺距范围的缩颈区,缩颈区以外的齿根处则无裂纹。
3.2 拉伸试验取与断裂螺栓同批供货的两支未使用的螺栓进行拉伸试验,其抗拉强度分别为1103MPa和1126MPa,符合10.9级的强度等级要求。
将试样纵向剖开进行金相分析,在距断口3~5个螺距范围内的缩颈区,其齿根处存在裂纹,而缩颈区以外的齿根处则无裂纹,可见该裂纹是拉伸时形成的。
取三支未使用的同批螺栓,也取其纵剖面进行金相分析,在螺纹齿根处均未发现裂纹。
3.3 分析与讨论断裂试样的硬度和强度均符合螺栓10.9级的强度等级要求,金相组织也正常,所以螺栓材质正常。
从拉伸试验和未使用的同批螺栓的金相分析结果看,缩颈不是由于材料强度不足而产生的。
由于裂纹均产生于断裂试样的缩颈处,缩颈以外的螺纹处无裂纹,则该裂纹是螺栓拧紧时载荷过大(超过材料的抗拉强度)所致。
经查,断裂螺栓的装配扭矩达146N·m,超过了120N·m的极限规定。
综上所述,螺栓断裂失效的原因是螺栓服役载荷(扭矩)过大,已超过其抗拉强度。
4 1110连杆螺栓断裂失效分析螺栓于装配时断裂,材料为35CrMo钢,强度等级10.9级,硬度要求30~35HRC,金相组织要求1~3级(JB/T8837-2000)。
经检验,1110连杆螺栓化学成分(质量分数)符合GB/T3077-1988之规定,见表1。
硬度为35HRC,符合32~38HRC技术条件规定。
经磁粉探伤,在螺栓表面发现细小裂纹。
将试样纵向剖开(0.5R处),显微镜下观察发现螺栓齿根部无脱碳,显微组织为细而均匀的回火索氏体,按JB/T8837-2000,组织级别为1级,符合其1~3级之技术条件规定。
但是,在纵剖面上有许多沿晶裂纹,裂纹两侧无脱碳。
绝大多数裂纹位于试样中心区域,断口处的数条裂纹也位于中心区域,估计螺栓中央存在裂纹。
对螺栓横向间隔取样进行金相分析,在数个磨面上均有裂纹,且裂纹存在于螺栓中央见图5。
由于裂纹位于螺栓的中央,较为封闭,虽经淬火、回火,但裂纹两侧无贫碳或脱碳。
图5 试样横截面裂纹形貌(未蚀,负片) 3×由于试样的回火索氏体组织细小,裂纹趋向很“柔”,且裂纹源于试样中心,可确定裂纹的产生与调质处理无关。
裂纹周围未发现夹杂类缺陷,裂纹存在位置和趋向确与“轴向晶间裂纹”类同,故该裂纹属原材料缺陷。
5 结论(1)所分析的螺栓的成分、牌号均符合GB/T3077-1988之规定,硬度、金相组织也符合技术条件要求,说明热处理工艺及其操作合理。
(2)螺栓失效原因:①195连杆螺栓断裂的直接原因是滚轮的滚齿能力下降导致产生裂纹,而滚轮超期服役则是关健因素;②缸盖螺栓断裂原因是其杆部和头部交接处的贫脱碳所致;③主轴承盖螺栓的断裂则是拧紧时扭矩过大造成;④1110连杆螺栓断裂是原材料存在裂纹所致。
(3)上述螺栓失效,很大程度上是源于质量管理的疏忽,如滚轮的超期服役、装配扭矩过大,理化检验的欠认真、细致等。
(4)连杆螺栓的金相检验按JB/T8837-2000进行,其它高强度螺栓也可参照进行。
虽然JB/T8837-2000对脱碳层未作规定,但在螺栓的技术条件中对脱碳层有明确规定。
因此,可根据要求在试样纵面上进行脱碳检验,方法有金相法和显微硬度法。
如果195连杆累栓按要求进行脱碳层的检验,其裂纹和缸盖螺栓的贫、脱碳则可检验出来。