化工行业十大类常见安全隐患300项
化工企业常见安全隐患300项
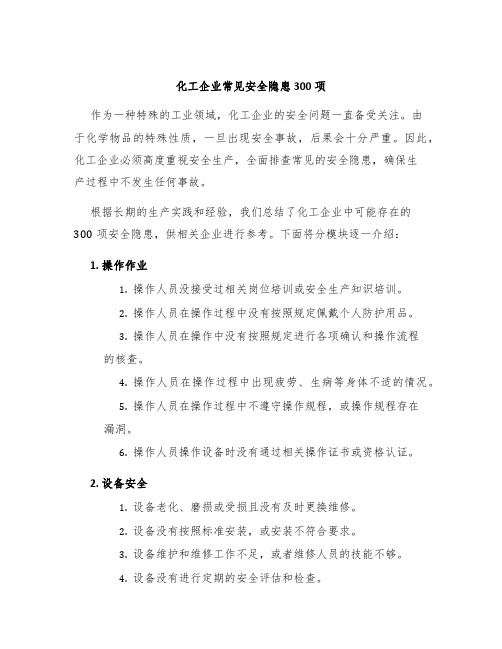
化工企业常见安全隐患300项作为一种特殊的工业领域,化工企业的安全问题一直备受关注。
由于化学物品的特殊性质,一旦出现安全事故,后果会十分严重。
因此,化工企业必须高度重视安全生产,全面排查常见的安全隐患,确保生产过程中不发生任何事故。
根据长期的生产实践和经验,我们总结了化工企业中可能存在的300项安全隐患,供相关企业进行参考。
下面将分模块逐一介绍:1. 操作作业1.操作人员没接受过相关岗位培训或安全生产知识培训。
2.操作人员在操作过程中没有按照规定佩戴个人防护用品。
3.操作人员在操作中没有按照规定进行各项确认和操作流程的核查。
4.操作人员在操作过程中出现疲劳、生病等身体不适的情况。
5.操作人员在操作过程中不遵守操作规程,或操作规程存在漏洞。
6.操作人员操作设备时没有通过相关操作证书或资格认证。
2. 设备安全1.设备老化、磨损或受损且没有及时更换维修。
2.设备没有按照标准安装,或安装不符合要求。
3.设备维护和维修工作不足,或者维修人员的技能不够。
4.设备没有进行定期的安全评估和检查。
5.设备在操作过程中没有按照规定的参数进行调节。
6.设备安装的防护设备不符合要求或没有按照规范使用。
7.设备出现意外故障时没有得到及时维修。
3. 危险化学品1.危险化学品没有按照规定的存储条件存放,或者存放区域没有明确的标识。
2.危险化学品容器的泄露或漏气现象。
3.危险化学品在运输过程中,没有得到有效的保护措施,或者没有按照规定的运输方式。
4.危险化学品倾倒、泄漏或扩散,造成环境污染.5.危险化学品没有进行及时的检测或者没有检测记录。
4. 电气安全1.电气设备在没有通过专业的电气检测和验收前投入使用。
2.对电气设备及线路没有进行定期的维护或检查。
3.电气设备未按照规定安装接地装置。
4.对于电气设备及线路的保护措施不足,可能导致电击事故。
5.没有制定相关的紧急救援措施。
5. 安全管理1.安全管理制度不完善,或者制度已过时。
常见安全隐患300项
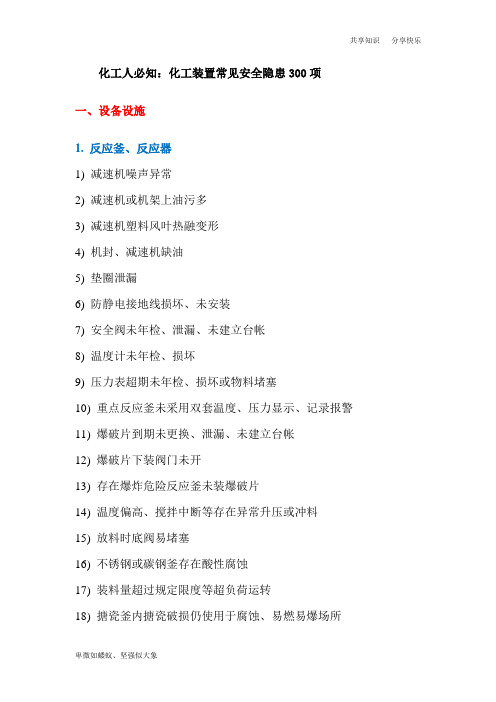
化工人必知:化工装置常见安全隐患300项一、设备设施1. 反应釜、反应器1) 减速机噪声异常2) 减速机或机架上油污多3) 减速机塑料风叶热融变形4) 机封、减速机缺油5) 垫圈泄漏6) 防静电接地线损坏、未安装7) 安全阀未年检、泄漏、未建立台帐8) 温度计未年检、损坏9) 压力表超期未年检、损坏或物料堵塞10) 重点反应釜未采用双套温度、压力显示、记录报警11) 爆破片到期未更换、泄漏、未建立台帐12) 爆破片下装阀门未开13) 存在爆炸危险反应釜未装爆破片14) 温度偏高、搅拌中断等存在异常升压或冲料15) 放料时底阀易堵塞16) 不锈钢或碳钢釜存在酸性腐蚀17) 装料量超过规定限度等超负荷运转18) 搪瓷釜内搪瓷破损仍使用于腐蚀、易燃易爆场所19) 反应釜内胆于夹套蒸汽进口处冲蚀破损20) 压力容器超过使用年限、制造质量差,多次修理后仍泄漏21) 压力容器没有铭牌22) 缺位号标识或不清23) 对有爆炸敏感性的反应釜未能有效隔离24) 重要设备未制订安全检查表25) 重要设备缺备件或备机2. 贮槽、罐区、槽车1) 液位计模糊或损坏、堵塞2) 静电接地线松动或未连接3) 法兰垫片处泄漏4) 小平台等高位贮槽未能有效固定5) 安全液封液位未达到要求6) 常压贮槽带压使用7) 装料量超过规定限度8) 非常温贮槽未装温度计9) 容器出现裂缝,仍在使用10) 频繁受真空、氮气交变载荷使贮罐破损11) 低沸点溶剂或液化气贮槽受阳光直射12) 室外贮罐等存在运输车辆等撞击危险13) 危险品罐区围堰孔洞未封堵14) 危化品罐区防护堤封堵不严密,任意开设排雨水孔15) 通向排水管的截止阀处于常开等不安全状态16) 危化品罐区的可燃或腐蚀性物料出口管线,其支架未设置吊式压式弹簧补偿措施,或直接采用挠性连接短管17) 危化品罐区未设禁打手机、禁带火源、限高限速等各种警示牌18) 危险品罐区无泄漏、送料操作记录及日常巡查19) 拖拉机随意进入危险品罐区20) 危险品罐区周边有明火或山林火灾21) 危险品罐区操作室使用电炉、电茶壶、电热板等违章用电22) 槽车在装卸地点没有接地装置23) 没有防止操作人员从罐车上坠落的措施24) 未装配有效的阻火器和车况不合格(照明灯损坏或刹车失灵)槽车进入罐区25) 槽车贮罐的安全附件(压力表、温度计、安全阀)无检验日期或存在失效26) 槽车罐体未标明压力容器下次检验日期27) 罐体上无静电拖链、防毒器材或阀门泄漏28) 卸料前和卸料后接地未静置10分钟以上29) 槽车卸料时,司机、押运员离开卸料现场,没有现场监护人员30) 采用敞开式和喷溅式卸料31) 卸料时使贮罐超标准液位或满料溢出32) 氯乙烯槽车卸料时,软管或法兰处泄漏33) 氯乙烯运输送料时,满槽34) 槽车装量不满时多次在厂内运输和卸料35) 卸料车辆为熄火及手闸制动或卸料中途启动车辆36) 在高强闪电、雷击频繁时,从事卸料操作37) 油罐接地点没有2处38) 装卸汽油、甲苯时,操作人员未穿戴防静电工作服和防静电的鞋子39) 液氨等贮槽贮存区域未设置事故围堰和应急喷淋稀释设施40) 现场未设置应急喷淋和洗眼设施41) 没有防止物料错装措施如乙酸乙酯装入汽油槽罐42) 站在汽油桶上电焊43) 未经清洗,切割汽油桶或焊接贮槽44) 液氨、氯乙烯贮罐超装45) 槽车卸料时,堵塞消防通道及侵占通行道路46) 收料员离开卸料现场47) 装卸现场使用铁制、塑料等易产生火花的工具48) 由罐区送入车间的物料贮槽没有操作记录3. 冷凝器、再沸器1) 腐蚀、垫圈老化等引起泄漏2) 冷凝后物料温度过高3) 换热介质层被淤泥、微生物堵塞4) 高温表面没有防护5) 冷却高温液体(如150℃)时,冷却水进出阀未开,或冷却水量不够6) 蒸发器等在初次使用时,急速升温7) 换热器未考虑防震措施,使与其连接管道因震动造成松动泄漏4. 管道及管件1) 管道安装完毕,内部的焊渣、其他异物未清理2) 视镜玻璃不清洁或损坏3) 选用视筒材质耐压、耐温性能不妥,视筒安装不当4) 视筒破裂或长时间带压使用5) 防静电接地线损坏6) 管道、法兰或螺栓严重腐蚀、破裂7) 高温管道未保温8) 泄爆管制作成弯管9) 管道物料及流向标识不清10) 管道色标不清11) 调试时不同物料串接阀门未盲死12) 废弃管道未及时清理13) 管阀安装位置低,易撞头或操作困难14) 腐蚀性物料管线、法兰等易泄漏处未采取防护措施15) 存在水、氮气、空气、蒸汽等进入物料管线的可能16) 高温管道边放置易燃易爆物料的铁桶或塑料桶17) 管道或管件材料选材不合理,易腐蚀18) 玻璃管液位计没有防护措施19) 在可能爆炸的视镜玻璃处,未安装防护金属网20) 止回阀不能灵活动作或失效21) 电动阀停电、气动阀停气22) 使用氢气等压力管道没有定期维护保养或带病运行23) 使用压力管道时,操作人员未经培训或无证上岗24) 维护人员没有资质修理、改造压力管道25) 压力管道焊接质量低劣,有咬边、气孔、夹渣、未焊透等焊接缺陷26) 压力管道未按照规定设安全附件或安全附件超期未校验27) 压力管道未建立档案、操作规程28) 搪玻璃管道受钢管等撞击29) 生产工艺介质改变后仍使用现有管线阀门未考虑材料适应性30) 氮气管与空气管串接31) 盐水管与冷却水管串接5. 输送泵、真空泵1) 泵泄漏2) 异常噪声3) 联轴器没有防护罩4) 泵出口未装压力表或止回阀5) 长期停用时,未放净泵和管道中液体,造成腐蚀或冻结6) 容积泵在运行时,将出口阀关闭或未装安全回流阀7) 泵进口管径小或管路长或拐弯多8) 离心泵安装高度高于吸入高度9) 未使用防静电皮带6. 离心机1) 甩滤溶剂,未充氮气或氮气管道堵塞或现场无流量计可显示2) 精烘包内需用离心机甩滤溶剂时,未装测氧仪及报警装置3) 快速刹车或用辅助工具(如铁棒等)刹车4) 离心机未有效接地5) 防爆区内未使用防静电皮带6) 离心机运行时,震动异常7. 双锥(双锥回转真空干燥机)1) 无防护栏及安全连锁装置2) 人员爬入双锥内更换真空袋3) 传动皮带无防护4) 轴封泄漏5) 真空管路堵塞或使用时真空阀未开启8. 气瓶1) 气瓶没有配瓶帽、防震圈2) 氢气钢瓶夏季运输、存放时,没有遮阳措施,导致曝晒3) 部分气瓶超过年检期限4) 乙炔瓶与氧气瓶同时使用时,安全间距未超过五米5) 用带催化剂手套关氢气瓶阀6) 敲击碰撞气瓶7) 气瓶使用后,气压小于0.05Mpa8) 气瓶组及管路连接、阀门损坏9) 氢气瓶使用时,未采用防静电装置或已坏10) 气体钢瓶没有防倒措施11) 储存场所存在地沟、暗道12) 贮存场所不通风或通风不畅或有腐蚀性气体进入13) 缺灭火器材14) 乙炔气瓶放倒使用15) 气瓶颜色模糊不清二、电器仪表1. 防爆区内设置非防爆电器或控制柜非防爆2. 配电室窗户玻璃破损3. 配电室内杂物较多4. 配电室内有蒸汽水、物料管、粉尘、腐蚀性物质,致使电柜内的电气设备老化,导致短路事故5. 变压器室外有酸雾腐蚀或溶剂渗入或粉尘多6. 控制柜或变电柜后有衣服等杂物7. 配电柜过于陈旧,易产生短路8. 电缆靠近高温管道9. 架空电缆周边物料管道、污水管道等泄漏,使腐蚀性物料流入电缆桥架内10. 埋地电缆受到地下水腐蚀11. 电缆井、沟内污水严重渗入12. 电缆桥架严重腐蚀13. 电缆线保护套管老化断裂14. 铺设电气线路的电缆或钢管在穿过不同场所之间的墙或楼板处孔洞时,未采用非燃烧性材料严格堵塞15. 乱拉活动排风,导致电缆接头脱落、漏电16. 开关按钮对应设备位号标识不清17. 车间内有零乱不明电缆18. 应急照明灯未装或已坏19. 露天电动机无防护罩20. 操作现场照明度不够21. 设备与电气不配套(小牛拖大车、老牛拖大车)形成电气设备发热损坏、起火22. 电气设备、电缆桥架上冲水23. 防爆视镜灯、照明灯元宝螺丝松动,漏光三、静电24. 在易燃易爆场所,反应釜、管道、贮槽、冷凝器、输送泵、法兰、阀门未接地或接地不不良25. 在易燃易爆场所,投粉体料斗未接地,充氮气26. 超过安全流速(v2<0.64/d)输送汽油、甲苯、环己烷等液体27. 氢气流速总管超过12m/s,支管超过8m/s28. 将汽油等从高位喷入贮罐底或地面29. 在未充氮气时,异丙醇铝、镁粉等由敞口漏斗投入含汽油、甲苯等反应釜中30. 在易燃易爆场所,穿脱衣服、鞋帽及剧烈活动31. 在易燃易爆场所,用化纤材料的拖布或抹布擦洗设备或地面32. 向塑料桶中灌装汽油33. 用汽油等溶剂洗工作服或拖地或钢平台、地面34. 不锈钢、碳钢贮罐罐壁未用焊接钢筋或扁钢接地,超过50m2未有两处接地35. 存在散发易燃易爆气体的场所,未采用增湿等消除静电危害的措施36. 用塑料管吸料或装甲苯或回收甲苯37. 用压缩空气输送或搅拌汽油38. 防爆洁净区未使用防静电拖鞋39. 接地扁钢、屋顶防雷带生锈、腐蚀严重40. 高出屋面的金属设备未焊接钢筋并入避雷带四、生产现场41. 贮存原料或废料较多42. 现场“跑、冒、滴、漏”多43. 保温层损坏44. 缺有效防护栏45. 常闭式防火门常开46. 存有粉尘(镁粉、锌粉等)的操作岗位,未及时清理47. 金属钠、钠氢存放,没有防雨措施或废桶、废袋随意存放48. 消防通道堵塞或各种管线及其支架妨碍通行49. 灭火器缺少或已过期锈蚀或消防带、消防栓不符合消防要求50. 废料桶有多张标签51. 强氧化剂(双氧水、高锰酸钾等)堆放在木架上52. 钢平台晃动幅度过大53. 钢平台或钢柱腐蚀严重54. 局部区域溶剂浓度超标55. 高处阀门手柄、铁棒等易跌落56. 混凝土楼面震动大57. 室外钢棚或屋顶杂物多58. 防毒器材过期或失效59. 生产现场存放有非生产用具(食品、报纸、小说)60. 缺乏夏季的防暑降温设施61. 室外小管径水管冬季未保温62. 车间内没有紧急淋浴、洗眼等卫生设施或已损坏63. 车辆未装阻火器进入生产现场64. 易燃易爆场所没有安装可燃气体报警仪或失灵65. 反应釜、贮罐、泵等未标注设备位号和名称66. 大铁门没有固定插销,一旦风大就可能使铁门擦出火花,导致危险67. 库房门槛偏低,一旦发生意外,危险品将外溢68. 生产现场地面存放铁板、钢管五、人员、现场操作69. 没有岗位操作记录或操作记录不完整70. 吸料、灌装、搬运腐蚀性物品未戴防护用品71. 存在操作人员脱岗、离岗、睡岗等现象72. 粉体等投料岗位未戴防尘口罩73. 快速开关阀门74. 分层釜、槽底阀分层后未关75. 分层釜、槽分水阀开太大,造成水中夹油排入污水池或排水时间过长忘记关阀而跑料76. 高温釜、塔内放入空气77. 提取催化剂(如钯碳、活性镍等)现场散落较多78. 用铁棒捅管道、釜内堵塞的物料或使用不防爆器械产生火花79. 噪声环境未戴防耳器或耳塞80. 贮槽超压使用81. 使用汽油、甲苯等易燃易爆溶剂处,釜、槽未采用氮气置换82. 烟尘弥漫、通风不良或缺氧83. 带压开启反应釜盖84. 员工有职业禁忌或过敏症或接触毒物时间过长85. 紧急阀门或紧急开关不易操作86. 在易燃易爆场所,穿带钉子鞋或高跟鞋、凉鞋六、土建87. 可能发生火势蔓延的上下楼层管道井没有预防措施(如阻燃材料封堵)88. 有爆炸危险的工艺未采用防爆墙及轻质屋顶或未考虑足够的泄爆面89. 出入口和紧急通道设计数量不够或堵塞或无明显标志90. 厂房基础已受酸、碱类物质腐蚀,立柱、梁已受损严重91. 有大风时,钢窗玻璃易脱落92. 楼梯太窄或较陡93. 室内排水不畅或低洼处长期积水、积油94. 通道或作业处,头顶与顶棚没有足够的空间95. 在不明地下管线(水管、电缆等)情况下,随意开挖路面96. 使用大型机械在接近地下电缆、管道等附近挖土97. 在禁火区域内动火时,生产车间未派人监护98. 施工中出现异常情况(管道断裂、泄漏等),未立即停工进行应急处理99. 挖掘的沟、坑、池等和破坏的管道,未设置围栏和标志,夜间未设置照明100. 发现土壤有可能坍塌或滑动时,未停止作业101. 没有防止地下空罐、空池上浮的措施102. 在下罐、下池作业时,未办理相应审批手续或未遵照审批要求实施(如劳保用品、监护人落实等),防范措施未到位的情况下作业103. 在非土建作业时,未办理“非基建用工手续“或作业前不了解相应可能风险,在安全措施不到位情况下开工七、生产检修104. 在容器内进行清扫和检修时,遇到危险情况,没有紧急逃出设施或措施105. 动火作业无监护人或监护人由新近员工担任或违章动火106. 超负荷吊装107. 工具或吊物未合理固定108. 未配备或未穿戴防护用品(安全帽、安全带等)109. 无警示标志或标志已模糊不清(如防止触电、防止坠物等)110. 检修时踏在悬空管路或小管径塑料管道和搪玻璃管道上或使用不安全登高设施111. 电焊机、手动电动工具等电缆破损引起漏电,零线破损或跨接112. 盲目进入污水池、深沟、深池作业113. 冬季管架结冰滑,无防滑措施114. 安装公司电焊工无电焊证或检修工未经过相关培训115. 直接站在石棉瓦、油毡等易碎材料的屋顶上作业116. 高处作业时,未采取防范措施进行交叉作业117. 高处作业时,电焊机的零线未接到所焊位置118. 有异味或可能产生有毒气体的区域作业未佩带防毒面具119. 高处补、挖墙洞时,未设安全围栏或安全网等120. 清理出的危险物料由高层向下层散落121. 用吊装机械载人122. 夜间作业无足够照明123. 遇有六级以上强风或其他恶劣天气时,仍在露天高空作业124. 釜内作业时,釜外无两人以上监护125. 釜内检修时,没有切断电源并挂“有人检修、禁止合闸”的牌子126. 进罐作业前,未对釜进行有效清洗127. 进罐作业前,未分析可燃气体浓度、氧含量、有毒气体(CO、H2S)浓度128. 进罐作业前,未对物料管线如原料、溶剂、蒸汽、水、氮气等管线可靠隔离129. 检修过程中,未对釜内定期取样分析130. 釜外明显位置未挂上“罐内有人”的牌子131. 进罐作业时,没有执行“双检制”132. 釜内照明不符合安全电压标准,干燥情况下电压大于24V,潮湿情况下电压大于12V133. 检修完毕,未检查、清理杂物就开机使用134. 长时间在釜内作业未轮换135. 检修时,釜内缺必要的通风设施136. 在搪玻璃罐外壁表面或内壁施焊137. 进入搪玻璃釜、槽内未铺设软垫138. 快速升温或急速冷却搪玻璃釜139. 使用搪玻璃罐时,罐口或人孔螺栓、卡子掉入釜内140. 使用搪玻璃釜、不锈钢釜、碳钢釜时,酸液进入釜夹套141. 选用材料未经温度、PH、腐蚀溶解性审核,可能存有压力的场合未经受压专项审核142. 检修完毕,釜内、检修现场高低位等全部空间未经全面清场、复核,既开始试运行143. 检修完毕,相关事项未做全面沟通,变更未经确认审批,相关人员未全面培训并了解就接手144. 检修未经运行确认即投料生产八、生产工艺145. 存在突发反应,缺乏应对措施及培训146. 随意改变投料量或投料配比147. 改进工艺或新工艺,未进行安全评估148. 工艺变更未经过严格审订、批准149. 工艺过程在可燃气体爆炸极限内操作150. 使用高毒物料时,采用敞口操作151. 未编写工艺操作规程进行试生产152. 未编写所用物料的物性资料及安全使用注意事项153. 所用材料分解时,产生的热量未经详细核算154. 存在粉尘爆炸的潜在危险性155. 某种原辅料不能及时投入时,釜内物料暂存时存在危险156. 原料或中间体在贮存中会发生自燃或聚合或分解危险157. 工艺中各种参数(温度、压力等)接近危险界限158. 发生异常状况时,没有将反应物迅速排放的措施159. 没有防止急剧反应和制止急剧反应的措施盛年不重来,一日难再晨。
化工生产中常见安全生产隐患300项
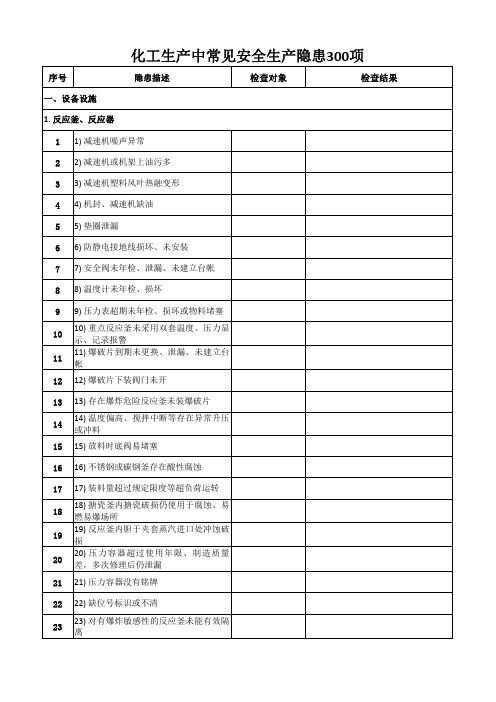
序号隐患描述检查对象检查结果11) 减速机噪声异常22) 减速机或机架上油污多33) 减速机塑料风叶热融变形44) 机封、减速机缺油55) 垫圈泄漏66) 防静电接地线损坏、未安装77) 安全阀未年检、泄漏、未建立台帐88) 温度计未年检、损坏99) 压力表超期未年检、损坏或物料堵塞1010)重点反应釜未采用双套温度、压力显示、记录报警1111)爆破片到期未更换、泄漏、未建立台帐1212) 爆破片下装阀门未开1313) 存在爆炸危险反应釜未装爆破片1414)温度偏高、搅拌中断等存在异常升压或冲料1515) 放料时底阀易堵塞1616) 不锈钢或碳钢釜存在酸性腐蚀1717) 装料量超过规定限度等超负荷运转1818)搪瓷釜内搪瓷破损仍使用于腐蚀、易燃易爆场所1919)反应釜内胆于夹套蒸汽进口处冲蚀破损2020)压力容器超过使用年限、制造质量差,多次修理后仍泄漏2121) 压力容器没有铭牌2222) 缺位号标识或不清2323)对有爆炸敏感性的反应釜未能有效隔离一、设备设施1. 反应釜、反应器化工生产中常见安全生产隐患300项2424) 重要设备未制订安全检查表2525) 重要设备缺备件或备机261) 液位计模糊或损坏、堵塞272) 静电接地线松动或未连接283) 法兰垫片处泄漏294) 小平台等高位贮槽未能有效固定305) 安全液封液位未达到要求316) 常压贮槽带压使用327) 装料量超过规定限度338) 非常温贮槽未装温度计349) 容器出现裂缝,仍在使用3510)频繁受真空、氮气交变载荷使贮罐破损3611) 低沸点溶剂或液化气贮槽受阳光直射3712) 室外贮罐等存在运输车辆等撞击危险3813) 危险品罐区围堰孔洞未封堵3914)危化品罐区防护堤封堵不严密,任意开设排雨水孔4015)通向排水管的截止阀处于常开等不安全状态4116)危化品罐区的可燃或腐蚀性物料出口管线,其支架未设置吊式压式弹簧补偿措施,或直接采用挠性连接短管4217)危化品罐区未设禁打手机、禁带火源、限高限速等各种警示牌4318)危险品罐区无泄漏、送料操作记录及日常巡查4419) 拖拉机随意进入危险品罐区4520) 危险品罐区周边有明火或山林火灾4621)危险品罐区操作室使用电炉、电茶壶、电热板等违章用电4722) 槽车在装卸地点没有接地装置4823)没有防止操作人员从罐车上坠落的措施2. 贮槽、罐区、槽车4924)未装配有效的阻火器和车况不合格(照明灯损坏或刹车失灵)槽车进入罐5025)槽车贮罐的安全附件(压力表、温度计、安全阀)无检验日期或存在失效5126)槽车罐体未标明压力容器下次检验日期5227)罐体上无静电拖链、防毒器材或阀门泄漏5328)卸料前和卸料后接地未静置10分钟以上5429)槽车卸料时,司机、押运员离开卸料现场,没有现场监护人员5530) 采用敞开式和喷溅式卸料5631) 卸料时使贮罐超标准液位或满料溢出5732)氯乙烯槽车卸料时,软管或法兰处泄漏5833) 氯乙烯运输送料时,满槽5934)槽车装量不满时多次在厂内运输和卸料6035)卸料车辆为熄火及手闸制动或卸料中途启动车辆6136)在高强闪电、雷击频繁时,从事卸料操作6237) 油罐接地点没有2处6338)装卸汽油、甲苯时,操作人员未穿戴防静电工作服和防静电的鞋子6439)液氨等贮槽贮存区域未设置事故围堰和应急喷淋稀释设施6540) 现场未设置应急喷淋和洗眼设施6641)没有防止物料错装措施如乙酸乙酯装入汽油槽罐6742) 站在汽油桶上电焊6843) 未经清洗,切割汽油桶或焊接贮槽6944) 液氨、氯乙烯贮罐超装7045)槽车卸料时,堵塞消防通道及侵占通行道路7146) 收料员离开卸料现场7247)装卸现场使用铁制、塑料等易产生火花的工具7348)由罐区送入车间的物料贮槽没有操作记录3. 冷凝器、再沸器741) 腐蚀、垫圈老化等引起泄漏752) 冷凝后物料温度过高763) 换热介质层被淤泥、微生物堵塞774) 高温表面没有防护785)冷却高温液体(如150℃)时,冷却水进出阀未开,或冷却水量不够796) 蒸发器等在初次使用时,急速升温807)换热器未考虑防震措施,使与其连接管道因震动造成松动泄漏811)管道安装完毕,内部的焊渣、其他异物未清理822) 视镜玻璃不清洁或损坏833)选用视筒材质耐压、耐温性能不妥,视筒安装不当844) 视筒破裂或长时间带压使用855) 防静电接地线损坏866) 管道、法兰或螺栓严重腐蚀、破裂877) 高温管道未保温888) 泄爆管制作成弯管899) 管道物料及流向标识不清9010) 管道色标不清9111) 调试时不同物料串接阀门未盲死9212) 废弃管道未及时清理9313) 管阀安装位置低,易撞头或操作困难9414)腐蚀性物料管线、法兰等易泄漏处未采取防护措施9515)存在水、氮气、空气、蒸汽等进入物料管线的可能9616)高温管道边放置易燃易爆物料的铁桶或塑料桶9717) 管道或管件材料选材不合理,易腐蚀9818) 玻璃管液位计没有防护措施9919)在可能爆炸的视镜玻璃处,未安装防护金属网4. 管道及管件10020) 止回阀不能灵活动作或失效10121) 电动阀停电、气动阀停气10222)使用氢气等压力管道没有定期维护保养或带病运行10323)使用压力管道时,操作人员未经培训或无证上岗10424)维护人员没有资质修理、改造压力管道10525)压力管道焊接质量低劣,有咬边、气孔、夹渣、未焊透等焊接缺陷10626)压力管道未按照规定设安全附件或安全附件超期未校验10727) 压力管道未建立档案、操作规程10828) 搪玻璃管道受钢管等撞击10929)生产工艺介质改变后仍使用现有管线阀门未考虑材料适应性11030) 氮气管与空气管串接11131) 盐水管与冷却水管串接1121) 泵泄漏1132) 异常噪声1143) 联轴器没有防护罩1154) 泵出口未装压力表或止回阀1165)长期停用时,未放净泵和管道中液体,造成腐蚀或冻结1176)容积泵在运行时,将出口阀关闭或未装安全回流阀1187) 泵进口管径小或管路长或拐弯多1198) 离心泵安装高度高于吸入高度1209) 未使用防静电皮带1211)甩滤溶剂,未充氮气或氮气管道堵塞或现场无流量计可显示1222)精烘包内需用离心机甩滤溶剂时,未装测氧仪及报警装置1233)快速刹车或用辅助工具(如铁棒等)刹车5. 输送泵、真空泵6. 离心机1244) 离心机未有效接地1255) 防爆区内未使用防静电皮带1266) 离心机运行时,震动异常1271) 无防护栏及安全连锁装置1282) 人员爬入双锥内更换真空袋1293) 传动皮带无防护1304) 轴封泄漏1315) 真空管路堵塞或使用时真空阀未开启1321) 气瓶没有配瓶帽、防震圈1332)氢气钢瓶夏季运输、存放时,没有遮阳措施,导致曝晒1343) 部分气瓶超过年检期限1354)乙炔瓶与氧气瓶同时使用时,安全间距未超过五米1365) 用带催化剂手套关氢气瓶阀1376) 敲击碰撞气瓶1387) 气瓶使用后,气压小于0.05Mpa 1398) 气瓶组及管路连接、阀门损坏1409)氢气瓶使用时,未采用防静电装置或已坏14110) 气体钢瓶没有防倒措施14211) 储存场所存在地沟、暗道14312)贮存场所不通风或通风不畅或有腐蚀性气体进入14413) 缺灭火器材14514) 乙炔气瓶放倒使用14615) 气瓶颜色模糊不清1471.防爆区内设置非防爆电器或控制柜非防爆7. 双锥8. 气瓶二、电器仪表148 2. 配电室窗户玻璃破损149 3. 配电室内杂物较多1504.配电室内有蒸汽水、物料管、粉尘、腐蚀性物质,致使电柜内的电气设备老化,导致短路事故1515.变压器室外有酸雾腐蚀或溶剂渗入或粉尘多152 6. 控制柜或变电柜后有衣服等杂物1537. 配电柜过于陈旧,易产生短路1548. 电缆靠近高温管道1559.架空电缆周边物料管道、污水管道等泄漏,使腐蚀性物料流入电缆桥架内15610. 埋地电缆受到地下水腐蚀15711. 电缆井、沟内污水严重渗入15812. 电缆桥架严重腐蚀15913. 电缆线保护套管老化断裂16014.铺设电气线路的电缆或钢管在穿过不同场所之间的墙或楼板处孔洞时,未采用非燃烧性材料严格堵塞16115.乱拉活动排风,导致电缆接头脱落、漏电16216. 开关按钮对应设备位号标识不清16317. 车间内有零乱不明电缆16418. 应急照明灯未装或已坏16519. 露天电动机无防护罩16620. 操作现场照明度不够16721.设备与电气不配套(小牛拖大车、老牛拖大车)形成电气设备发热损坏、起火16822. 电气设备、电缆桥架上冲水16923.防爆视镜灯、照明灯元宝螺丝松动,漏光17024.在易燃易爆场所,反应釜、管道、贮槽、冷凝器、输送泵、法兰、阀门未接地或接地不不良17125.在易燃易爆场所,投粉体料斗未接地,充氮气三、静电17226.超过安全流速(v2<0.64/d)输送汽油、甲苯、环己烷等液体17327.氢气流速总管超过12m/s,支管超过8m/s17428. 将汽油等从高位喷入贮罐底或地面17529.在未充氮气时,异丙醇铝、镁粉等由敞口漏斗投入含汽油、甲苯等反应釜中17630.在易燃易爆场所,穿脱衣服、鞋帽及剧烈活动17731.在易燃易爆场所,用化纤材料的拖布或抹布擦洗设备或地面17832. 向塑料桶中灌装汽油17933.用汽油等溶剂洗工作服或拖地或钢平台、地面18034.不锈钢、碳钢贮罐罐壁未用焊接钢筋或扁钢接地,超过50m2未有两处接地18135.存在散发易燃易爆气体的场所,未采用增湿等消除静电危害的措施18236. 用塑料管吸料或装甲苯或回收甲苯18337. 用压缩空气输送或搅拌汽油18438. 防爆洁净区未使用防静电拖鞋18539.接地扁钢、屋顶防雷带生锈、腐蚀严重18640.高出屋面的金属设备未焊接钢筋并入避雷带18741. 贮存原料或废料较多18842. 现场“跑、冒、滴、漏”多18943. 保温层损坏19044. 缺有效防护栏19145. 常闭式防火门常开19246.存有粉尘(镁粉、锌粉等)的操作岗位,未及时清理19347.金属钠、钠氢存放,没有防雨措施或废桶、废袋随意存放19448.消防通道堵塞或各种管线及其支架妨碍通行19549.灭火器缺少或已过期锈蚀或消防带、消防栓不符合消防要求四、生产现场19650. 废料桶有多张标签19751.强氧化剂(双氧水、高锰酸钾等)堆放在木架上19852. 钢平台晃动幅度过大19953. 钢平台或钢柱腐蚀严重20054. 局部区域溶剂浓度超标20155. 高处阀门手柄、铁棒等易跌落20256. 混凝土楼面震动大20357. 室外钢棚或屋顶杂物多20458. 防毒器材过期或失效20559.生产现场存放有非生产用具(食品、报纸、小说)20660. 缺乏夏季的防暑降温设施20761. 室外小管径水管冬季未保温20862.车间内没有紧急淋浴、洗眼等卫生设施或已损坏20963. 车辆未装阻火器进入生产现场21064.易燃易爆场所没有安装可燃气体报警仪或失灵21165.反应釜、贮罐、泵等未标注设备位号和名称21266.大铁门没有固定插销,一旦风大就可能使铁门擦出火花,导致危险21367.库房门槛偏低,一旦发生意外,危险品将外溢21468. 生产现场地面存放铁板、钢管21569. 没有岗位操作记录或操作记录不完整21670.吸料、灌装、搬运腐蚀性物品未戴防护用品21771.存在操作人员脱岗、离岗、睡岗等现象21872. 粉体等投料岗位未戴防尘口罩21973. 快速开关阀门22074. 分层釜、槽底阀分层后未关五、人员、现场操作22175.分层釜、槽分水阀开太大,造成水中夹油排入污水池或排水时间过长忘记关阀而跑料22276. 高温釜、塔内放入空气22377.提取催化剂(如钯碳、活性镍等)现场散落较多22478.用铁棒捅管道、釜内堵塞的物料或使用不防爆器械产生火花22579. 噪声环境未戴防耳器或耳塞22680. 贮槽超压使用22781.使用汽油、甲苯等易燃易爆溶剂处,釜、槽未采用氮气置换22882. 烟尘弥漫、通风不良或缺氧22983. 带压开启反应釜盖23084.员工有职业禁忌或过敏症或接触毒物时间过长23185. 紧急阀门或紧急开关不易操作23286.在易燃易爆场所,穿带钉子鞋或高跟鞋、凉鞋23387.可能发生火势蔓延的上下楼层管道井没有预防措施(如阻燃材料封堵)23488.有爆炸危险的工艺未采用防爆墙及轻质屋顶或未考虑足够的泄爆面23589.出入口和紧急通道设计数量不够或堵塞或无明显标志23690.厂房基础已受酸、碱类物质腐蚀,立柱、梁已受损严重23791. 有大风时,钢窗玻璃易脱落23892. 楼梯太窄或较陡23993.室内排水不畅或低洼处长期积水、积油24094.通道或作业处,头顶与顶棚没有足够的空间24195.在不明地下管线(水管、电缆等)情况下,随意开挖路面24296.使用大型机械在接近地下电缆、管道等附近挖土24397.在禁火区域内动火时,生产车间未派人监护六、土建24498.施工中出现异常情况(管道断裂、泄漏等),未立即停工进行应急处理24599.挖掘的沟、坑、池等和破坏的管道,未设置围栏和标志,夜间未设置照明246100.发现土壤有可能坍塌或滑动时,未停止作业247101.没有防止地下空罐、空池上浮的措施248102.在下罐、下池作业时,未办理相应审批手续或未遵照审批要求实施(如劳保用品、监护人落实等),防范措施未到位的情况下作业249103.在非土建作业时,未办理“非基建用工手续“或作业前不了解相应可能风险,在安全措施不到位情况下开工250104.在容器内进行清扫和检修时,遇到危险情况,没有紧急逃出设施或措施251105.动火作业无监护人或监护人由新近员工担任或违章动火252106. 超负荷吊装253107. 工具或吊物未合理固定254108.未配备或未穿戴防护用品(安全帽、安全带等)255109.无警示标志或标志已模糊不清(如防止触电、防止坠物等)256110.检修时踏在悬空管路或小管径塑料管道和搪玻璃管道上或使用不安全登高设施257111.电焊机、手动电动工具等电缆破损引起漏电,零线破损或跨接258112. 盲目进入污水池、深沟、深池作业259113. 冬季管架结冰滑,无防滑措施260114.安装公司电焊工无电焊证或检修工未经过相关培训261115.直接站在石棉瓦、油毡等易碎材料的屋顶上作业262116.高处作业时,未采取防范措施进行交叉作业263117.高处作业时,电焊机的零线未接到所焊位置七、生产检修264118.有异味或可能产生有毒气体的区域作业未佩带防毒面具265119.高处补、挖墙洞时,未设安全围栏或安全网等266120.清理出的危险物料由高层向下层散落267121. 用吊装机械载人268122. 夜间作业无足够照明269123.遇有六级以上强风或其他恶劣天气时,仍在露天高空作业270124. 釜内作业时,釜外无两人以上监护271125.釜内检修时,没有切断电源并挂“有人检修、禁止合闸”的牌子272126. 进罐作业前,未对釜进行有效清洗273127.进罐作业前,未分析可燃气体浓度、氧含量、有毒气体(CO、H2S)浓度274128.进罐作业前,未对物料管线如原料、溶剂、蒸汽、水、氮气等管线可靠隔离275129.检修过程中,未对釜内定期取样分析276130.釜外明显位置未挂上“罐内有人”的牌子277131. 进罐作业时,没有执行“双检制”278132.釜内照明不符合安全电压标准,干燥情况下电压大于24V,潮湿情况下电压大于12V279133.检修完毕,未检查、清理杂物就开机使用280134. 长时间在釜内作业未轮换281135. 检修时,釜内缺必要的通风设施282136. 在搪玻璃罐外壁表面或内壁施焊283137. 进入搪玻璃釜、槽内未铺设软垫284138. 快速升温或急速冷却搪玻璃釜285139.使用搪玻璃罐时,罐口或人孔螺栓、卡子掉入釜内286140.使用搪玻璃釜、不锈钢釜、碳钢釜时,酸液进入釜夹套287141.选用材料未经温度、PH、腐蚀溶解性审核,可能存有压力的场合未经受压专项审核288142.检修完毕,釜内、检修现场高低位等全部空间未经全面清场、复核,既开始试运行289143.检修完毕,相关事项未做全面沟通,变更未经确认审批,相关人员未全面培训并了解就接手290144. 检修未经运行确认即投料生产291145.存在突发反应,缺乏应对措施及培训292146. 随意改变投料量或投料配比293147.改进工艺或新工艺,未进行安全评估294148. 工艺变更未经过严格审订、批准295149.工艺过程在可燃气体爆炸极限内操作296150. 使用高毒物料时,采用敞口操作297151. 未编写工艺操作规程进行试生产298152.未编写所用物料的物性资料及安全使用注意事项299153.所用材料分解时,产生的热量未经详细核算300154. 存在粉尘爆炸的潜在危险性301155.某种原辅料不能及时投入时,釜内物料暂存时存在危险302156.原料或中间体在贮存中会发生自燃或聚合或分解危险303157.工艺中各种参数(温度、压力等)接近危险界限304158.发生异常状况时,没有将反应物迅速排放的措施305159.没有防止急剧反应和制止急剧反应的措施八、生产工艺。
化工常见隐患300项剖析
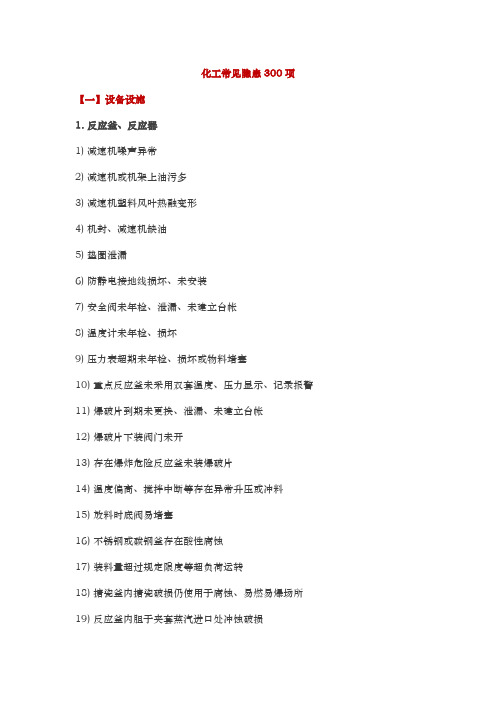
化工常见隐患300项【一】设备设施1.反应釜、反应器1)减速机噪声异常2)减速机或机架上油污多3)减速机塑料风叶热融变形4)机封、减速机缺油5)垫圈泄漏6)防静电接地线损坏、未安装7)安全阀未年检、泄漏、未建立台帐8)温度计未年检、损坏9)压力表超期未年检、损坏或物料堵塞10)重点反应釜未采用双套温度、压力显示、记录报警11)爆破片到期未更换、泄漏、未建立台帐12)爆破片下装阀门未开13)存在爆炸危险反应釜未装爆破片14)温度偏高、搅拌中断等存在异常升压或冲料15)放料时底阀易堵塞16)不锈钢或碳钢釜存在酸性腐蚀17)装料量超过规定限度等超负荷运转18)搪瓷釜内搪瓷破损仍使用于腐蚀、易燃易爆场所19)反应釜内胆于夹套蒸汽进口处冲蚀破损20)压力容器超过使用年限、制造质量差,多次修理后仍泄漏21)压力容器没有铭牌22)缺位号标识或不清23)对有爆炸敏感性的反应釜未能有效隔离24)重要设备未制订安全检查表25)重要设备缺备件或备机2.贮槽、罐区、槽车1)液位计模糊或损坏、堵塞2)静电接地线松动或未连接3)法兰垫片处泄漏4)小平台等高位贮槽未能有效固定5)安全液封液位未达到要求6)常压贮槽带压使用7)装料量超过规定限度8)非常温贮槽未装温度计9)容器出现裂缝,仍在使用10)频繁受真空、氮气交变载荷使贮罐破损11)低沸点溶剂或液化气贮槽受阳光直射12)室外贮罐等存在运输车辆等撞击危险13)危险品罐区围堰孔洞未封堵14)危化品罐区防护堤封堵不严密,任意开设排雨水孔15)通向排水管的截止阀处于常开等不安全状态16)危化品罐区的可燃或腐蚀性物料出口管线,其支架未设置吊式压式弹簧补偿措施,或直接采用挠性连接短管17)危化品罐区未设禁打手机、禁带火源、限高限速等各种警示牌18)危险品罐区无泄漏、送料操作记录及日常巡查19)拖拉机随意进入危险品罐区20)危险品罐区周边有明火或山林火灾21)危险品罐区操作室使用电炉、电茶壶、电热板等违章用电22)槽车在装卸地点没有接地装置23)没有防止操作人员从罐车上坠落的措施24)未装配有效的阻火器和车况不合格(照明灯损坏或刹车失灵)槽车进入罐区25)槽车贮罐的安全附件(压力表、温度计、安全阀)无检验日期或存在失效26)槽车罐体未标明压力容器下次检验日期27)罐体上无静电拖链、防毒器材或阀门泄漏28)卸料前和卸料后接地未静置10分钟以上29)槽车卸料时,司机、押运员离开卸料现场,没有现场监护人员30)采用敞开式和喷溅式卸料31)卸料时使贮罐超标准液位或满料溢出32)氯乙烯槽车卸料时,软管或法兰处泄漏33)氯乙烯运输送料时,满槽34)槽车装量不满时多次在厂内运输和卸料35)卸料车辆为熄火及手闸制动或卸料中途启动车辆36)在高强闪电、雷击频繁时,从事卸料操作37)油罐接地点没有2处(微信号:hse123_com)38)装卸汽油、甲苯时,操作人员未穿戴防静电工作服和防静电的鞋子39)液氨等贮槽贮存区域未设置事故围堰和应急喷淋稀释设施40)现场未设置应急喷淋和洗眼设施41)没有防止物料错装措施如乙酸乙酯装入汽油槽罐42)站在汽油桶上电焊43)未经清洗,切割汽油桶或焊接贮槽44)液氨、氯乙烯贮罐超装45)槽车卸料时,堵塞消防通道及侵占通行道路46)收料员离开卸料现场47)装卸现场使用铁制、塑料等易产生火花的工具48)由罐区送入车间的物料贮槽没有操作记录3.冷凝器、再沸器1)腐蚀、垫圈老化等引起泄漏2)冷凝后物料温度过高3)换热介质层被淤泥、微生物堵塞4)高温表面没有防护5)冷却高温液体(如150℃)时,冷却水进出阀未开,或冷却水量不够6)蒸发器等在初次使用时,急速升温7)换热器未考虑防震措施,使与其连接管道因震动造成松动泄漏4.管道及管件1)管道安装完毕,内部的焊渣、其他异物未清理2)视镜玻璃不清洁或损坏3)选用视筒材质耐压、耐温性能不妥,视筒安装不当4)视筒破裂或长时间带压使用5)防静电接地线损坏6)管道、法兰或螺栓严重腐蚀、破裂7)高温管道未保温8)泄爆管制作成弯管9)管道物料及流向标识不清10)管道色标不清11)调试时不同物料串接阀门未盲死12)废弃管道未及时清理13)管阀安装位置低,易撞头或操作困难14)腐蚀性物料管线、法兰等易泄漏处未采取防护措施15)存在水、氮气、空气、蒸汽等进入物料管线的可能16)高温管道边放置易燃易爆物料的铁桶或塑料桶17)管道或管件材料选材不合理,易腐蚀18)玻璃管液位计没有防护措施19)在可能爆炸的视镜玻璃处,未安装防护金属网20)止回阀不能灵活动作或失效21)电动阀停电、气动阀停气22)使用氢气等压力管道没有定期维护保养或带病运行23)使用压力管道时,操作人员未经培训或无证上岗24)维护人员没有资质修理、改造压力管道25)压力管道焊接质量低劣,有咬边、气孔、夹渣、未焊透等焊接缺陷(微信号:hse123_com)26)压力管道未按照规定设安全附件或安全附件超期未校验27)压力管道未建立档案、操作规程28)搪玻璃管道受钢管等撞击29)生产工艺介质改变后仍使用现有管线阀门未考虑材料适应性30)氮气管与空气管串接31)盐水管与冷却水管串接5.输送泵、真空泵1)泵泄漏2)异常噪声3)联轴器没有防护罩4)泵出口未装压力表或止回阀5)长期停用时,未放净泵和管道中液体,造成腐蚀或冻结6)容积泵在运行时,将出口阀关闭或未装安全回流阀7)泵进口管径小或管路长或拐弯多8)离心泵安装高度高于吸入高度9)未使用防静电皮带6.离心机1)甩滤溶剂,未充氮气或氮气管道堵塞或现场无流量计可显示2)精烘包内需用离心机甩滤溶剂时,未装测氧仪及报警装置3)快速刹车或用辅助工具(如铁棒等)刹车4)离心机未有效接地5)防爆区内未使用防静电皮带6)离心机运行时,震动异常7.双锥1)无防护栏及安全连锁装置2)人员爬入双锥内更换真空袋3)传动皮带无防护4)轴封泄漏5)真空管路堵塞或使用时真空阀未开启8.气瓶1)气瓶没有配瓶帽、防震圈2)氢气钢瓶夏季运输、存放时,没有遮阳措施,导致曝晒3)部分气瓶超过年检期限4)乙炔瓶与氧气瓶同时使用时,安全间距未超过五米5)用带催化剂手套关氢气瓶阀6)敲击碰撞气瓶(微信号:hse123_com)7)气瓶使用后,气压小于0.05Mpa8)气瓶组及管路连接、阀门损坏9)氢气瓶使用时,未采用防静电装置或已坏10)气体钢瓶没有防倒措施11)储存场所存在地沟、暗道12)贮存场所不通风或通风不畅或有腐蚀性气体进入13)缺灭火器材14)乙炔气瓶放倒使用15)气瓶颜色模糊不清【二】电器仪表1.防爆区内设置非防爆电器或控制柜非防爆2.配电室窗户玻璃破损3.配电室内杂物较多4.配电室内有蒸汽水、物料管、粉尘、腐蚀性物质,致使电柜内的电气设备老化,导致短路事故5.变压器室外有酸雾腐蚀或溶剂渗入或粉尘多6.控制柜或变电柜后有衣服等杂物7.配电柜过于陈旧,易产生短路8.电缆靠近高温管道9.架空电缆周边物料管道、污水管道等泄漏,使腐蚀性物料流入电缆桥架内10.埋地电缆受到地下水腐蚀11.电缆井、沟内污水严重渗入12.电缆桥架严重腐蚀13.电缆线保护套管老化断裂14.铺设电气线路的电缆或钢管在穿过不同场所之间的墙或楼板处孔洞时,未采用非燃烧性材料严格堵塞15.乱拉活动排风,导致电缆接头脱落、漏电16.开关按钮对应设备位号标识不清17.车间内有零乱不明电缆18.应急照明灯未装或已坏19.露天电动机无防护罩20.操作现场照明度不够21.设备与电气不配套(小牛拖大车、老牛拖大车)形成电气设备发热损坏、起火22.电气设备、电缆桥架上冲水23.防爆视镜灯、照明灯元宝螺丝松动,漏光【三】静电24.在易燃易爆场所,反应釜、管道、贮槽、冷凝器、输送泵、法兰、阀门未接地或接地不不良25.在易燃易爆场所,投粉体料斗未接地,充氮气26.超过安全流速(v2<0.64/d)输送汽油、甲苯、环己烷等液体27.氢气流速总管超过12m/s,支管超过8m/s28.将汽油等从高位喷入贮罐底或地面29.在未充氮气时,异丙醇铝、镁粉等由敞口漏斗投入含汽油、甲苯等反应釜中30.在易燃易爆场所,穿脱衣服、鞋帽及剧烈活动31.在易燃易爆场所,用化纤材料的拖布或抹布擦洗设备或地面32.向塑料桶中灌装汽油33.用汽油等溶剂洗工作服或拖地或钢平台、地面34.不锈钢、碳钢贮罐罐壁未用焊接钢筋或扁钢接地,超过50m2未有两处接地35.存在散发易燃易爆气体的场所,未采用增湿等消除静电危害的措施36.用塑料管吸料或装甲苯或回收甲苯37.用压缩空气输送或搅拌汽油38.防爆洁净区未使用防静电拖鞋39.接地扁钢、屋顶防雷带生锈、腐蚀严重40.高出屋面的金属设备未焊接钢筋并入避雷带【四】生产现场41.贮存原料或废料较多42.现场“跑、冒、滴、漏”多43.保温层损坏44.缺有效防护栏45.常闭式防火门常开46.存有粉尘(镁粉、锌粉等)的操作岗位,未及时清理47.金属钠、钠氢存放,没有防雨措施或废桶、废袋随意存放48.消防通道堵塞或各种管线及其支架妨碍通行49.灭火器缺少或已过期锈蚀或消防带、消防栓不符合消防要求50.废料桶有多张标签(微信号:hse123_com)51.强氧化剂(双氧水、高锰酸钾等)堆放在木架上52.钢平台晃动幅度过大53.钢平台或钢柱腐蚀严重54.局部区域溶剂浓度超标55.高处阀门手柄、铁棒等易跌落56.混凝土楼面震动大57.室外钢棚或屋顶杂物多58.防毒器材过期或失效59.生产现场存放有非生产用具(食品、报纸、小说)60.缺乏夏季的防暑降温设施61.室外小管径水管冬季未保温62.车间内没有紧急淋浴、洗眼等卫生设施或已损坏63.车辆未装阻火器进入生产现场64.易燃易爆场所没有安装可燃气体报警仪或失灵65.反应釜、贮罐、泵等未标注设备位号和名称66.大铁门没有固定插销,一旦风大就可能使铁门擦出火花,导致危险67.库房门槛偏低,一旦发生意外,危险品将外溢68.生产现场地面存放铁板、钢管【五】人员、现场操作69.没有岗位操作记录或操作记录不完整70.吸料、灌装、搬运腐蚀性物品未戴防护用品71.存在操作人员脱岗、离岗、睡岗等现象72.粉体等投料岗位未戴防尘口罩73.快速开关阀门(微信号:hse123_com)74.分层釜、槽底阀分层后未关75.分层釜、槽分水阀开太大,造成水中夹油排入污水池或排水时间过长忘记关阀而跑料76.高温釜、塔内放入空气77.提取催化剂(如钯碳、活性镍等)现场散落较多78.用铁棒捅管道、釜内堵塞的物料或使用不防爆器械产生火花79.噪声环境未戴防耳器或耳塞80.贮槽超压使用81.使用汽油、甲苯等易燃易爆溶剂处,釜、槽未采用氮气置换82.烟尘弥漫、通风不良或缺氧83.带压开启反应釜盖84.员工有职业禁忌或过敏症或接触毒物时间过长85.紧急阀门或紧急开关不易操作86.在易燃易爆场所,穿带钉子鞋或高跟鞋、凉鞋【六】土建87.可能发生火势蔓延的上下楼层管道井没有预防措施(如阻燃材料封堵)88.有爆炸危险的工艺未采用防爆墙及轻质屋顶或未考虑足够的泄爆面89.出入口和紧急通道设计数量不够或堵塞或无明显标志90.厂房基础已受酸、碱类物质腐蚀,立柱、梁已受损严重91.有大风时,钢窗玻璃易脱落92.楼梯太窄或较陡(微信号:hse123_com)93.室内排水不畅或低洼处长期积水、积油94.通道或作业处,头顶与顶棚没有足够的空间95.在不明地下管线(水管、电缆等)情况下,随意开挖路面96.使用大型机械在接近地下电缆、管道等附近挖土97.在禁火区域内动火时,生产车间未派人监护98.施工中出现异常情况(管道断裂、泄漏等),未立即停工进行应急处理99.挖掘的沟、坑、池等和破坏的管道,未设置围栏和标志,夜间未设置照明100.发现土壤有可能坍塌或滑动时,未停止作业101.没有防止地下空罐、空池上浮的措施102.在下罐、下池作业时,未办理相应审批手续或未遵照审批要求实施(如劳保用品、监护人落实等),防范措施未到位的情况下作业103.在非土建作业时,未办理“非基建用工手续“或作业前不了解相应可能风险,在安全措施不到位情况下开工【七】生产检修104.在容器内进行清扫和检修时,遇到危险情况,没有紧急逃出设施或措施105.动火作业无监护人或监护人由新近员工担任或违章动火106.超负荷吊装(微信号:hse123_com)107.工具或吊物未合理固定108.未配备或未穿戴防护用品(安全帽、安全带等)109.无警示标志或标志已模糊不清(如防止触电、防止坠物等)110.检修时踏在悬空管路或小管径塑料管道和搪玻璃管道上或使用不安全登高设施111.电焊机、手动电动工具等电缆破损引起漏电,零线破损或跨接112.盲目进入污水池、深沟、深池作业113.冬季管架结冰滑,无防滑措施114.安装公司电焊工无电焊证或检修工未经过相关培训115.直接站在石棉瓦、油毡等易碎材料的屋顶上作业116.高处作业时,未采取防范措施进行交叉作业117.高处作业时,电焊机的零线未接到所焊位置118.有异味或可能产生有毒气体的区域作业未佩带防毒面具119.高处补、挖墙洞时,未设安全围栏或安全网等120.清理出的危险物料由高层向下层散落121.用吊装机械载人122.夜间作业无足够照明123.遇有六级以上强风或其他恶劣天气时,仍在露天高空作业124.釜内作业时,釜外无两人以上监护125.釜内检修时,没有切断电源并挂“有人检修、禁止合闸”的牌子126.进罐作业前,未对釜进行有效清洗S)浓度127.进罐作业前,未分析可燃气体浓度、氧含量、有毒气体(CO、H2128.进罐作业前,未对物料管线如原料、溶剂、蒸汽、水、氮气等管线可靠隔离129.检修过程中,未对釜内定期取样分析130.釜外明显位置未挂上“罐内有人”的牌子131.进罐作业时,没有执行“双检制”132.釜内照明不符合安全电压标准,干燥情况下电压大于24V,潮湿情况下电压大于12V133.检修完毕,未检查、清理杂物就开机使用134.长时间在釜内作业未轮换135.检修时,釜内缺必要的通风设施136.在搪玻璃罐外壁表面或内壁施焊137.进入搪玻璃釜、槽内未铺设软垫138.快速升温或急速冷却搪玻璃釜139.使用搪玻璃罐时,罐口或人孔螺栓、卡子掉入釜内140.使用搪玻璃釜、不锈钢釜、碳钢釜时,酸液进入釜夹套141.选用材料未经温度、PH、腐蚀溶解性审核,可能存有压力的场合未经受压专项审核(微信号:hse123_com)142.检修完毕,釜内、检修现场高低位等全部空间未经全面清场、复核,既开始试运行143.检修完毕,相关事项未做全面沟通,变更未经确认审批,相关人员未全面培训并了解就接手144.检修未经运行确认即投料生产【八】生产工艺145.存在突发反应,缺乏应对措施及培训146.随意改变投料量或投料配比(微信号:hse123_com)147.改进工艺或新工艺,未进行安全评估148.工艺变更未经过严格审订、批准149.工艺过程在可燃气体爆炸极限内操作150.使用高毒物料时,采用敞口操作151.未编写工艺操作规程进行试生产152.未编写所用物料的物性资料及安全使用注意事项153.所用材料分解时,产生的热量未经详细核算154.存在粉尘爆炸的潜在危险性155.某种原辅料不能及时投入时,釜内物料暂存时存在危险156.原料或中间体在贮存中会发生自燃或聚合或分解危险157.工艺中各种参数(温度、压力等)接近危险界限158.发生异常状况时,没有将反应物迅速排放的措施159.没有防止急剧反应和制止急剧反应的措施。
常见安全隐患300项资料

常见安全隐患300项化工人必知:化工装置常见安全隐患300项一、设备设施1. 反应釜、反应器1) 减速机噪声异常2) 减速机或机架上油污多3) 减速机塑料风叶热融变形4) 机封、减速机缺油5) 垫圈泄漏6) 防静电接地线损坏、未安装7) 安全阀未年检、泄漏、未建立台帐8) 温度计未年检、损坏9) 压力表超期未年检、损坏或物料堵塞10) 重点反应釜未采用双套温度、压力显示、记录报警11) 爆破片到期未更换、泄漏、未建立台帐12) 爆破片下装阀门未开13) 存在爆炸危险反应釜未装爆破片14) 温度偏高、搅拌中断等存在异常升压或冲料15) 放料时底阀易堵塞16) 不锈钢或碳钢釜存在酸性腐蚀17) 装料量超过规定限度等超负荷运转18) 搪瓷釜内搪瓷破损仍使用于腐蚀、易燃易爆场所19) 反应釜内胆于夹套蒸汽进口处冲蚀破损20) 压力容器超过使用年限、制造质量差,多次修理后仍泄漏21) 压力容器没有铭牌22) 缺位号标识或不清23) 对有爆炸敏感性的反应釜未能有效隔离24) 重要设备未制订安全检查表25) 重要设备缺备件或备机2. 贮槽、罐区、槽车1) 液位计模糊或损坏、堵塞2) 静电接地线松动或未连接3) 法兰垫片处泄漏4) 小平台等高位贮槽未能有效固定5) 安全液封液位未达到要求6) 常压贮槽带压使用7) 装料量超过规定限度8) 非常温贮槽未装温度计9) 容器出现裂缝,仍在使用10) 频繁受真空、氮气交变载荷使贮罐破损11) 低沸点溶剂或液化气贮槽受阳光直射12) 室外贮罐等存在运输车辆等撞击危险13) 危险品罐区围堰孔洞未封堵14) 危化品罐区防护堤封堵不严密,任意开设排雨水孔15) 通向排水管的截止阀处于常开等不安全状态16) 危化品罐区的可燃或腐蚀性物料出口管线,其支架未设置吊式压式弹簧补偿措施,或直接采用挠性连接短管17) 危化品罐区未设禁打手机、禁带火源、限高限速等各种警示牌18) 危险品罐区无泄漏、送料操作记录及日常巡查19) 拖拉机随意进入危险品罐区20) 危险品罐区周边有明火或山林火灾21) 危险品罐区操作室使用电炉、电茶壶、电热板等违章用电22) 槽车在装卸地点没有接地装置23) 没有防止操作人员从罐车上坠落的措施24) 未装配有效的阻火器和车况不合格(照明灯损坏或刹车失灵)槽车进入罐区25) 槽车贮罐的安全附件(压力表、温度计、安全阀)无检验日期或存在失效26) 槽车罐体未标明压力容器下次检验日期27) 罐体上无静电拖链、防毒器材或阀门泄漏28) 卸料前和卸料后接地未静置10分钟以上29) 槽车卸料时,司机、押运员离开卸料现场,没有现场监护人员30) 采用敞开式和喷溅式卸料31) 卸料时使贮罐超标准液位或满料溢出32) 氯乙烯槽车卸料时,软管或法兰处泄漏33) 氯乙烯运输送料时,满槽34) 槽车装量不满时多次在厂内运输和卸料35) 卸料车辆为熄火及手闸制动或卸料中途启动车辆36) 在高强闪电、雷击频繁时,从事卸料操作37) 油罐接地点没有2处38) 装卸汽油、甲苯时,操作人员未穿戴防静电工作服和防静电的鞋子39) 液氨等贮槽贮存区域未设置事故围堰和应急喷淋稀释设施40) 现场未设置应急喷淋和洗眼设施41) 没有防止物料错装措施如乙酸乙酯装入汽油槽罐42) 站在汽油桶上电焊43) 未经清洗,切割汽油桶或焊接贮槽44) 液氨、氯乙烯贮罐超装45) 槽车卸料时,堵塞消防通道及侵占通行道路46) 收料员离开卸料现场47) 装卸现场使用铁制、塑料等易产生火花的工具48) 由罐区送入车间的物料贮槽没有操作记录3. 冷凝器、再沸器1) 腐蚀、垫圈老化等引起泄漏2) 冷凝后物料温度过高3) 换热介质层被淤泥、微生物堵塞4) 高温表面没有防护5) 冷却高温液体(如150℃)时,冷却水进出阀未开,或冷却水量不够6) 蒸发器等在初次使用时,急速升温7) 换热器未考虑防震措施,使与其连接管道因震动造成松动泄漏4. 管道及管件1) 管道安装完毕,内部的焊渣、其他异物未清理2) 视镜玻璃不清洁或损坏3) 选用视筒材质耐压、耐温性能不妥,视筒安装不当4) 视筒破裂或长时间带压使用5) 防静电接地线损坏6) 管道、法兰或螺栓严重腐蚀、破裂7) 高温管道未保温8) 泄爆管制作成弯管9) 管道物料及流向标识不清10) 管道色标不清11) 调试时不同物料串接阀门未盲死12) 废弃管道未及时清理13) 管阀安装位置低,易撞头或操作困难14) 腐蚀性物料管线、法兰等易泄漏处未采取防护措施15) 存在水、氮气、空气、蒸汽等进入物料管线的可能16) 高温管道边放置易燃易爆物料的铁桶或塑料桶17) 管道或管件材料选材不合理,易腐蚀18) 玻璃管液位计没有防护措施19) 在可能爆炸的视镜玻璃处,未安装防护金属网20) 止回阀不能灵活动作或失效21) 电动阀停电、气动阀停气22) 使用氢气等压力管道没有定期维护保养或带病运行23) 使用压力管道时,操作人员未经培训或无证上岗24) 维护人员没有资质修理、改造压力管道25) 压力管道焊接质量低劣,有咬边、气孔、夹渣、未焊透等焊接缺陷26) 压力管道未按照规定设安全附件或安全附件超期未校验27) 压力管道未建立档案、操作规程28) 搪玻璃管道受钢管等撞击29) 生产工艺介质改变后仍使用现有管线阀门未考虑材料适应性30) 氮气管与空气管串接31) 盐水管与冷却水管串接5. 输送泵、真空泵1) 泵泄漏2) 异常噪声3) 联轴器没有防护罩4) 泵出口未装压力表或止回阀5) 长期停用时,未放净泵和管道中液体,造成腐蚀或冻结6) 容积泵在运行时,将出口阀关闭或未装安全回流阀7) 泵进口管径小或管路长或拐弯多8) 离心泵安装高度高于吸入高度9) 未使用防静电皮带6. 离心机1) 甩滤溶剂,未充氮气或氮气管道堵塞或现场无流量计可显示2) 精烘包内需用离心机甩滤溶剂时,未装测氧仪及报警装置3) 快速刹车或用辅助工具(如铁棒等)刹车4) 离心机未有效接地5) 防爆区内未使用防静电皮带6) 离心机运行时,震动异常7. 双锥(双锥回转真空干燥机)1) 无防护栏及安全连锁装置2) 人员爬入双锥内更换真空袋3) 传动皮带无防护4) 轴封泄漏5) 真空管路堵塞或使用时真空阀未开启8. 气瓶1) 气瓶没有配瓶帽、防震圈2) 氢气钢瓶夏季运输、存放时,没有遮阳措施,导致曝晒3) 部分气瓶超过年检期限4) 乙炔瓶与氧气瓶同时使用时,安全间距未超过五米5) 用带催化剂手套关氢气瓶阀6) 敲击碰撞气瓶7) 气瓶使用后,气压小于0.05Mpa8) 气瓶组及管路连接、阀门损坏9) 氢气瓶使用时,未采用防静电装置或已坏10) 气体钢瓶没有防倒措施11) 储存场所存在地沟、暗道12) 贮存场所不通风或通风不畅或有腐蚀性气体进入13) 缺灭火器材14) 乙炔气瓶放倒使用15) 气瓶颜色模糊不清二、电器仪表1. 防爆区内设置非防爆电器或控制柜非防爆2. 配电室窗户玻璃破损3. 配电室内杂物较多4. 配电室内有蒸汽水、物料管、粉尘、腐蚀性物质,致使电柜内的电气设备老化,导致短路事故5. 变压器室外有酸雾腐蚀或溶剂渗入或粉尘多6. 控制柜或变电柜后有衣服等杂物7. 配电柜过于陈旧,易产生短路8. 电缆靠近高温管道9. 架空电缆周边物料管道、污水管道等泄漏,使腐蚀性物料流入电缆桥架内10. 埋地电缆受到地下水腐蚀11. 电缆井、沟内污水严重渗入12. 电缆桥架严重腐蚀13. 电缆线保护套管老化断裂14. 铺设电气线路的电缆或钢管在穿过不同场所之间的墙或楼板处孔洞时,未采用非燃烧性材料严格堵塞15. 乱拉活动排风,导致电缆接头脱落、漏电16. 开关按钮对应设备位号标识不清17. 车间内有零乱不明电缆18. 应急照明灯未装或已坏19. 露天电动机无防护罩20. 操作现场照明度不够21. 设备与电气不配套(小牛拖大车、老牛拖大车)形成电气设备发热损坏、起火22. 电气设备、电缆桥架上冲水23. 防爆视镜灯、照明灯元宝螺丝松动,漏光三、静电24. 在易燃易爆场所,反应釜、管道、贮槽、冷凝器、输送泵、法兰、阀门未接地或接地不不良25. 在易燃易爆场所,投粉体料斗未接地,充氮气26. 超过安全流速(v2<0.64/d)输送汽油、甲苯、环己烷等液体27. 氢气流速总管超过12m/s,支管超过8m/s28. 将汽油等从高位喷入贮罐底或地面29. 在未充氮气时,异丙醇铝、镁粉等由敞口漏斗投入含汽油、甲苯等反应釜中30. 在易燃易爆场所,穿脱衣服、鞋帽及剧烈活动31. 在易燃易爆场所,用化纤材料的拖布或抹布擦洗设备或地面32. 向塑料桶中灌装汽油33. 用汽油等溶剂洗工作服或拖地或钢平台、地面34. 不锈钢、碳钢贮罐罐壁未用焊接钢筋或扁钢接地,超过50m2未有两处接地35. 存在散发易燃易爆气体的场所,未采用增湿等消除静电危害的措施36. 用塑料管吸料或装甲苯或回收甲苯37. 用压缩空气输送或搅拌汽油38. 防爆洁净区未使用防静电拖鞋39. 接地扁钢、屋顶防雷带生锈、腐蚀严重40. 高出屋面的金属设备未焊接钢筋并入避雷带四、生产现场41. 贮存原料或废料较多42. 现场“跑、冒、滴、漏”多43. 保温层损坏44. 缺有效防护栏45. 常闭式防火门常开46. 存有粉尘(镁粉、锌粉等)的操作岗位,未及时清理47. 金属钠、钠氢存放,没有防雨措施或废桶、废袋随意存放48. 消防通道堵塞或各种管线及其支架妨碍通行49. 灭火器缺少或已过期锈蚀或消防带、消防栓不符合消防要求50. 废料桶有多张标签51. 强氧化剂(双氧水、高锰酸钾等)堆放在木架上52. 钢平台晃动幅度过大53. 钢平台或钢柱腐蚀严重54. 局部区域溶剂浓度超标55. 高处阀门手柄、铁棒等易跌落56. 混凝土楼面震动大57. 室外钢棚或屋顶杂物多58. 防毒器材过期或失效59. 生产现场存放有非生产用具(食品、报纸、小说)60. 缺乏夏季的防暑降温设施61. 室外小管径水管冬季未保温62. 车间内没有紧急淋浴、洗眼等卫生设施或已损坏63. 车辆未装阻火器进入生产现场64. 易燃易爆场所没有安装可燃气体报警仪或失灵65. 反应釜、贮罐、泵等未标注设备位号和名称66. 大铁门没有固定插销,一旦风大就可能使铁门擦出火花,导致危险67. 库房门槛偏低,一旦发生意外,危险品将外溢68. 生产现场地面存放铁板、钢管五、人员、现场操作69. 没有岗位操作记录或操作记录不完整70. 吸料、灌装、搬运腐蚀性物品未戴防护用品71. 存在操作人员脱岗、离岗、睡岗等现象72. 粉体等投料岗位未戴防尘口罩73. 快速开关阀门74. 分层釜、槽底阀分层后未关75. 分层釜、槽分水阀开太大,造成水中夹油排入污水池或排水时间过长忘记关阀而跑料76. 高温釜、塔内放入空气77. 提取催化剂(如钯碳、活性镍等)现场散落较多78. 用铁棒捅管道、釜内堵塞的物料或使用不防爆器械产生火花79. 噪声环境未戴防耳器或耳塞80. 贮槽超压使用81. 使用汽油、甲苯等易燃易爆溶剂处,釜、槽未采用氮气置换82. 烟尘弥漫、通风不良或缺氧83. 带压开启反应釜盖84. 员工有职业禁忌或过敏症或接触毒物时间过长85. 紧急阀门或紧急开关不易操作86. 在易燃易爆场所,穿带钉子鞋或高跟鞋、凉鞋六、土建87. 可能发生火势蔓延的上下楼层管道井没有预防措施(如阻燃材料封堵)88. 有爆炸危险的工艺未采用防爆墙及轻质屋顶或未考虑足够的泄爆面89. 出入口和紧急通道设计数量不够或堵塞或无明显标志90. 厂房基础已受酸、碱类物质腐蚀,立柱、梁已受损严重91. 有大风时,钢窗玻璃易脱落92. 楼梯太窄或较陡93. 室内排水不畅或低洼处长期积水、积油94. 通道或作业处,头顶与顶棚没有足够的空间95. 在不明地下管线(水管、电缆等)情况下,随意开挖路面96. 使用大型机械在接近地下电缆、管道等附近挖土97. 在禁火区域内动火时,生产车间未派人监护98. 施工中出现异常情况(管道断裂、泄漏等),未立即停工进行应急处理99. 挖掘的沟、坑、池等和破坏的管道,未设置围栏和标志,夜间未设置照明100. 发现土壤有可能坍塌或滑动时,未停止作业101. 没有防止地下空罐、空池上浮的措施102. 在下罐、下池作业时,未办理相应审批手续或未遵照审批要求实施(如劳保用品、监护人落实等),防范措施未到位的情况下作业103. 在非土建作业时,未办理“非基建用工手续“或作业前不了解相应可能风险,在安全措施不到位情况下开工七、生产检修104. 在容器内进行清扫和检修时,遇到危险情况,没有紧急逃出设施或措施105. 动火作业无监护人或监护人由新近员工担任或违章动火106. 超负荷吊装107. 工具或吊物未合理固定108. 未配备或未穿戴防护用品(安全帽、安全带等)109. 无警示标志或标志已模糊不清(如防止触电、防止坠物等)110. 检修时踏在悬空管路或小管径塑料管道和搪玻璃管道上或使用不安全登高设施111. 电焊机、手动电动工具等电缆破损引起漏电,零线破损或跨接112. 盲目进入污水池、深沟、深池作业113. 冬季管架结冰滑,无防滑措施114. 安装公司电焊工无电焊证或检修工未经过相关培训115. 直接站在石棉瓦、油毡等易碎材料的屋顶上作业116. 高处作业时,未采取防范措施进行交叉作业117. 高处作业时,电焊机的零线未接到所焊位置118. 有异味或可能产生有毒气体的区域作业未佩带防毒面具119. 高处补、挖墙洞时,未设安全围栏或安全网等120. 清理出的危险物料由高层向下层散落121. 用吊装机械载人122. 夜间作业无足够照明123. 遇有六级以上强风或其他恶劣天气时,仍在露天高空作业124. 釜内作业时,釜外无两人以上监护125. 釜内检修时,没有切断电源并挂“有人检修、禁止合闸”的牌子126. 进罐作业前,未对釜进行有效清洗127. 进罐作业前,未分析可燃气体浓度、氧含量、有毒气体(CO、H2S)浓度128. 进罐作业前,未对物料管线如原料、溶剂、蒸汽、水、氮气等管线可靠隔离129. 检修过程中,未对釜内定期取样分析130. 釜外明显位置未挂上“罐内有人”的牌子131. 进罐作业时,没有执行“双检制”132. 釜内照明不符合安全电压标准,干燥情况下电压大于24V,潮湿情况下电压大于12V133. 检修完毕,未检查、清理杂物就开机使用134. 长时间在釜内作业未轮换135. 检修时,釜内缺必要的通风设施136. 在搪玻璃罐外壁表面或内壁施焊137. 进入搪玻璃釜、槽内未铺设软垫138. 快速升温或急速冷却搪玻璃釜139. 使用搪玻璃罐时,罐口或人孔螺栓、卡子掉入釜内140. 使用搪玻璃釜、不锈钢釜、碳钢釜时,酸液进入釜夹套141. 选用材料未经温度、PH、腐蚀溶解性审核,可能存有压力的场合未经受压专项审核142. 检修完毕,釜内、检修现场高低位等全部空间未经全面清场、复核,既开始试运行143. 检修完毕,相关事项未做全面沟通,变更未经确认审批,相关人员未全面培训并了解就接手144. 检修未经运行确认即投料生产八、生产工艺145. 存在突发反应,缺乏应对措施及培训146. 随意改变投料量或投料配比147. 改进工艺或新工艺,未进行安全评估148. 工艺变更未经过严格审订、批准149. 工艺过程在可燃气体爆炸极限内操作150. 使用高毒物料时,采用敞口操作151. 未编写工艺操作规程进行试生产152. 未编写所用物料的物性资料及安全使用注意事项153. 所用材料分解时,产生的热量未经详细核算154. 存在粉尘爆炸的潜在危险性155. 某种原辅料不能及时投入时,釜内物料暂存时存在危险156. 原料或中间体在贮存中会发生自燃或聚合或分解危险157. 工艺中各种参数(温度、压力等)接近危险界限158. 发生异常状况时,没有将反应物迅速排放的措施159. 没有防止急剧反应和制止急剧反应的措施。
安全生产隐患三百项

《化工人必知的化工装置常见安全隐患300项》一、设备设施1. 反应釜、反应器1) 减速机噪声异常2) 减速机或机架上油污多3) 减速机塑料风叶热融变形4) 机封、减速机缺油5) 垫圈泄漏6) 防静电接地线损坏、未安装7) 安全阀未年检、泄漏、未建立台帐8) 温度计未年检、损坏9) 压力表超期未年检、损坏或物料堵塞10) 重点反应釜未采用双套温度、压力显示、记录报警11) 爆破片到期未更换、泄漏、未建立台帐12) 爆破片下装阀门未开13) 存在爆炸危险反应釜未装爆破片14) 温度偏高、搅拌中断等存在异常升压或冲料15) 放料时底阀易堵塞16) 不锈钢或碳钢釜存在酸性腐蚀17) 装料量超过规定限度等超负荷运转18) 搪瓷釜内搪瓷破损仍使用于腐蚀、易燃易爆场所19) 反应釜内胆于夹套蒸汽进口处冲蚀破损20) 压力容器超过使用年限、制造质量差,多次修理后仍泄漏21) 压力容器没有铭牌22) 缺位号标识或不清23) 对有爆炸敏感性的反应釜未能有效隔离24) 重要设备未制订安全检查表25) 重要设备缺备件或备机2. 贮槽、罐区、槽车1) 液位计模糊或损坏、堵塞2) 静电接地线松动或未连接3) 法兰垫片处泄漏4) 小平台等高位贮槽未能有效固定5) 安全液封液位未达到要求6) 常压贮槽带压使用7) 装料量超过规定限度8) 非常温贮槽未装温度计9) 容器出现裂缝,仍在使用10) 频繁受真空、氮气交变载荷使贮罐破损11) 低沸点溶剂或液化气贮槽受阳光直射12) 室外贮罐等存在运输车辆等撞击危险13) 危险品罐区围堰孔洞未封堵14) 危化品罐区防护堤封堵不严密,任意开设排雨水孔15) 通向排水管的截止阀处于常开等不安全状态16) 危化品罐区的可燃或腐蚀性物料出口管线,其支架未设置吊式压式弹簧补偿措施,或直接采用挠性连接短管17) 危化品罐区未设禁打手机、禁带火源、限高限速等各种警示牌18) 危险品罐区无泄漏、送料操作记录及日常巡查19) 拖拉机随意进入危险品罐区20) 危险品罐区周边有明火或山林火灾21) 危险品罐区操作室使用电炉、电茶壶、电热板等违章用电22) 槽车在装卸地点没有接地装置23) 没有防止操作人员从罐车上坠落的措施24) 未装配有效的阻火器和车况不合格(照明灯损坏或刹车失灵)槽车进入罐区25) 槽车贮罐的安全附件(压力表、温度计、安全阀)无检验日期或存在失效26) 槽车罐体未标明压力容器下次检验日期27) 罐体上无静电拖链、防毒器材或阀门泄漏28) 卸料前和卸料后接地未静置10分钟以上29) 槽车卸料时,司机、押运员离开卸料现场,没有现场监护人员30) 采用敞开式和喷溅式卸料31) 卸料时使贮罐超标准液位或满料溢出32)槽车卸料时,软管或法兰处泄漏33)运输送料时,满槽34) 槽车装量不满时多次在厂内运输和卸料35) 卸料车辆为熄火及手闸制动或卸料中途启动车辆36) 在高强闪电、雷击频繁时,从事卸料操作37) 油罐接地点没有2处38) 装卸汽油、甲苯时,操作人员未穿戴防静电工作服和防静电的鞋子39) 液氨等贮槽贮存区域未设置事故围堰和应急喷淋稀释设施40) 现场未设置应急喷淋和洗眼设施41) 没有防止物料错装措施如乙酸乙酯装入汽油槽罐42) 站在汽油桶上电焊43) 未经清洗,切割汽油桶或焊接贮槽44) 液氨贮罐超装45) 槽车卸料时,堵塞消防通道及侵占通行道路46) 收料员离开卸料现场47) 装卸现场使用铁制、塑料等易产生火花的工具48) 由罐区送入车间的物料贮槽没有操作记录3. 冷凝器、再沸器1) 腐蚀、垫圈老化等引起泄漏2) 冷凝后物料温度过高3) 换热介质层被淤泥、微生物堵塞4) 高温表面没有防护5) 冷却高温液体(如150℃)时,冷却水进出阀未开,或冷却水量不够6) 蒸发器等在初次使用时,急速升温7) 换热器未考虑防震措施,使与其连接管道因震动造成松动泄漏4. 管道及管件1) 管道安装完毕,内部的焊渣、其他异物未清理2) 视镜玻璃不清洁或损坏3) 选用视筒材质耐压、耐温性能不妥,视筒安装不当4) 视筒破裂或长时间带压使用5) 防静电接地线损坏6) 管道、法兰或螺栓严重腐蚀、破裂7) 高温管道未保温8) 泄爆管制作成弯管9) 管道物料及流向标识不清10) 管道色标不清11) 调试时不同物料串接阀门未盲死12) 废弃管道未及时清理13) 管阀安装位置低,易撞头或操作困难14) 腐蚀性物料管线、法兰等易泄漏处未采取防护措施15) 存在水、氮气、空气、蒸汽等进入物料管线的可能16) 高温管道边放置易燃易爆物料的铁桶或塑料桶17) 管道或管件材料选材不合理,易腐蚀18) 玻璃管液位计没有防护措施19) 在可能爆炸的视镜玻璃处,未安装防护金属网20) 止回阀不能灵活动作或失效21) 电动阀停电、气动阀停气22) 使用氢气等压力管道没有定期维护保养或带病运行23) 使用压力管道时,操作人员未经培训或无证上岗24) 维护人员没有资质修理、改造压力管道25) 压力管道焊接质量低劣,有咬边、气孔、夹渣、未焊透等焊接缺陷26) 压力管道未按照规定设安全附件或安全附件超期未校验27) 压力管道未建立档案、操作规程28) 搪玻璃管道受钢管等撞击29) 生产工艺介质改变后仍使用现有管线阀门未考虑材料适应性30) 氮气管与空气管串接31) 盐水管与冷却水管串接5. 输送泵、真空泵1) 泵泄漏2) 异常噪声3) 联轴器没有防护罩4) 泵出口未装压力表或止回阀5) 长期停用时,未放净泵和管道中液体,造成腐蚀或冻结6) 容积泵在运行时,将出口阀关闭或未装安全回流阀7) 泵进口管径小或管路长或拐弯多8) 离心泵安装高度高于吸入高度9) 未使用防静电皮带6. 离心机1) 甩滤溶剂,未充氮气或氮气管道堵塞或现场无流量计可显示2) 精烘包内需用离心机甩滤溶剂时,未装测氧仪及报警装置3) 快速刹车或用辅助工具(如铁棒等)刹车4) 离心机未有效接地5) 防爆区内未使用防静电皮带6) 离心机运行时,震动异常7. 双锥(双锥回转真空干燥机)1) 无防护栏及安全连锁装置2) 人员爬入双锥内更换真空袋3) 传动皮带无防护4) 轴封泄漏5) 真空管路堵塞或使用时真空阀未开启8. 气瓶1) 气瓶没有配瓶帽、防震圈2) 氢气钢瓶夏季运输、存放时,没有遮阳措施,导致曝晒3) 部分气瓶超过年检期限4) 乙炔瓶与氧气瓶同时使用时,安全间距未超过五米5) 用带催化剂手套关氢气瓶阀6) 敲击碰撞气瓶7) 气瓶使用后,气压小于0.05Mpa8) 气瓶组及管路连接、阀门损坏9) 氢气瓶使用时,未采用防静电装置或已坏10) 气体钢瓶没有防倒措施11) 储存场所存在地沟、暗道12) 贮存场所不通风或通风不畅或有腐蚀性气体进入13) 缺灭火器材14) 乙炔气瓶放倒使用15) 气瓶颜色模糊不清二、电器仪表1. 防爆区内设置非防爆电器或控制柜非防爆2. 配电室窗户玻璃破损3. 配电室内杂物较多4. 配电室内有蒸汽水、物料管、粉尘、腐蚀性物质,致使电柜内的电气设备老化,导致短路事故5. 变压器室外有酸雾腐蚀或溶剂渗入或粉尘多6. 控制柜或变电柜后有衣服等杂物7. 配电柜过于陈旧,易产生短路8. 电缆靠近高温管道9. 架空电缆周边物料管道、污水管道等泄漏,使腐蚀性物料流入电缆桥架内10. 埋地电缆受到地下水腐蚀11. 电缆井、沟内污水严重渗入12. 电缆桥架严重腐蚀13. 电缆线保护套管老化断裂14. 铺设电气线路的电缆或钢管在穿过不同场所之间的墙或楼板处孔洞时,未采用非燃烧性材料严格堵塞15. 乱拉活动排风,导致电缆接头脱落、漏电16. 开关按钮对应设备位号标识不清17. 车间内有零乱不明电缆18. 应急照明灯未装或已坏19. 露天电动机无防护罩20. 操作现场照明度不够21. 设备与电气不配套(小牛拖大车、老牛拖大车)形成电气设备发热损坏、起火22. 电气设备、电缆桥架上冲水23. 防爆视镜灯、照明灯元宝螺丝松动,漏光三、静电24. 在易燃易爆场所,反应釜、管道、贮槽、冷凝器、输送泵、法兰、阀门未接地或接地不不良25. 在易燃易爆场所,投粉体料斗未接地,充氮气26. 超过安全流速(v2<0.64/d)输送汽油、甲苯、环己烷等液体27. 氢气流速总管超过12m/s,支管超过8m/s28. 将汽油等从高位喷入贮罐底或地面29. 在未充氮气时,异丙醇铝、镁粉等由敞口漏斗投入含汽油、甲苯等反应釜中30. 在易燃易爆场所,穿脱衣服、鞋帽及剧烈活动31. 在易燃易爆场所,用化纤材料的拖布或抹布擦洗设备或地面32. 向塑料桶中灌装汽油33. 用汽油等溶剂洗工作服或拖地或钢平台、地面34. 不锈钢、碳钢贮罐罐壁未用焊接钢筋或扁钢接地,超过50m2未有两处接地35. 存在散发易燃易爆气体的场所,未采用增湿等消除静电危害的措施36. 用塑料管吸料或装甲苯或回收甲苯37. 用压缩空气输送或搅拌汽油38. 防爆洁净区未使用防静电拖鞋39. 接地扁钢、屋顶防雷带生锈、腐蚀严重40. 高出屋面的金属设备未焊接钢筋并入避雷带四、生产现场41. 贮存原料或废料较多42. 现场“跑、冒、滴、漏”多43. 保温层损坏44. 缺有效防护栏45. 常闭式防火门常开46. 存有粉尘(镁粉、锌粉等)的操作岗位,未及时清理47. 金属钠、钠氢存放,没有防雨措施或废桶、废袋随意存放48. 消防通道堵塞或各种管线及其支架妨碍通行49. 灭火器缺少或已过期锈蚀或消防带、消防栓不符合消防要求50. 废料桶有多张标签51. 强氧化剂(双氧水、高锰酸钾等)堆放在木架上52. 钢平台晃动幅度过大53. 钢平台或钢柱腐蚀严重54. 局部区域溶剂浓度超标55. 高处阀门手柄、铁棒等易跌落56. 混凝土楼面震动大57. 室外钢棚或屋顶杂物多58. 防毒器材过期或失效59. 生产现场存放有非生产用具(食品、报纸、小说)60. 缺乏夏季的防暑降温设施61. 室外小管径水管冬季未保温62. 车间内没有紧急淋浴、洗眼等卫生设施或已损坏63. 车辆未装阻火器进入生产现场64. 易燃易爆场所没有安装可燃气体报警仪或失灵65. 反应釜、贮罐、泵等未标注设备位号和名称66. 大铁门没有固定插销,一旦风大就可能使铁门擦出火花,导致危险67. 库房门槛偏低,一旦发生意外,危险品将外溢68. 生产现场地面存放铁板、钢管五、人员、现场操作69. 没有岗位操作记录或操作记录不完整70. 吸料、灌装、搬运腐蚀性物品未戴防护用品71. 存在操作人员脱岗、离岗、睡岗等现象72. 粉体等投料岗位未戴防尘口罩73. 快速开关阀门74. 分层釜、槽底阀分层后未关75. 分层釜、槽分水阀开太大,造成水中夹油排入污水池或排水时间过长忘记关阀而跑料76. 高温釜、塔内放入空气77. 提取催化剂(如钯碳、活性镍等)现场散落较多78. 用铁棒捅管道、釜内堵塞的物料或使用不防爆器械产生火花79. 噪声环境未戴防耳器或耳塞80. 贮槽超压使用81. 使用汽油、甲苯等易燃易爆溶剂处,釜、槽未采用氮气置换82. 烟尘弥漫、通风不良或缺氧83. 带压开启反应釜盖84. 员工有职业禁忌或过敏症或接触毒物时间过长85. 紧急阀门或紧急开关不易操作86. 在易燃易爆场所,穿带钉子鞋或高跟鞋、凉鞋六、土建87. 可能发生火势蔓延的上下楼层管道井没有预防措施(如阻燃材料封堵)88. 有爆炸危险的工艺未采用防爆墙及轻质屋顶或未考虑足够的泄爆面89. 出入口和紧急通道设计数量不够或堵塞或无明显标志90. 厂房基础已受酸、碱类物质腐蚀,立柱、梁已受损严重91. 有大风时,钢窗玻璃易脱落92. 楼梯太窄或较陡93. 室内排水不畅或低洼处长期积水、积油94. 通道或作业处,头顶与顶棚没有足够的空间95. 在不明地下管线(水管、电缆等)情况下,随意开挖路面96. 使用大型机械在接近地下电缆、管道等附近挖土97. 在禁火区域内动火时,生产车间未派人监护98. 施工中出现异常情况(管道断裂、泄漏等),未立即停工进行应急处理99. 挖掘的沟、坑、池等和破坏的管道,未设置围栏和标志,夜间未设置照明100. 发现土壤有可能坍塌或滑动时,未停止作业101. 没有防止地下空罐、空池上浮的措施102. 在下罐、下池作业时,未办理相应审批手续或未遵照审批要求实施(如劳保用品、监护人落实等),防范措施未到位的情况下作业103. 在非土建作业时,未办理“非基建用工手续“或作业前不了解相应可能风险,在安全措施不到位情况下开工七、生产检修104. 在容器内进行清扫和检修时,遇到危险情况,没有紧急逃出设施或措施105. 动火作业无监护人或监护人由新近员工担任或违章动火106. 超负荷吊装107. 工具或吊物未合理固定108. 未配备或未穿戴防护用品(安全帽、安全带等)109. 无警示标志或标志已模糊不清(如防止触电、防止坠物等)110. 检修时踏在悬空管路或小管径塑料管道和搪玻璃管道上或使用不安全登高设施111. 电焊机、手动电动工具等电缆破损引起漏电,零线破损或跨接112. 盲目进入污水池、深沟、深池作业113. 冬季管架结冰滑,无防滑措施114. 安装公司电焊工无电焊证或检修工未经过相关培训115. 直接站在石棉瓦、油毡等易碎材料的屋顶上作业116. 高处作业时,未采取防范措施进行交叉作业117. 高处作业时,电焊机的零线未接到所焊位置118. 有异味或可能产生有毒气体的区域作业未佩带防毒面具119. 高处补、挖墙洞时,未设安全围栏或安全网等120. 清理出的危险物料由高层向下层散落121. 用吊装机械载人122. 夜间作业无足够照明123. 遇有六级以上强风或其他恶劣天气时,仍在露天高空作业124. 釜内作业时,釜外无两人以上监护125. 釜内检修时,没有切断电源并挂“有人检修、禁止合闸”的牌子126. 进罐作业前,未对釜进行有效清洗127. 进罐作业前,未分析可燃气体浓度、氧含量、有毒气体(CO、H2S)浓度128. 进罐作业前,未对物料管线如原料、溶剂、蒸汽、水、氮气等管线可靠隔离129. 检修过程中,未对釜内定期取样分析130. 釜外明显位置未挂上“罐内有人”的牌子131. 进罐作业时,没有执行“双检制”132. 釜内照明不符合安全电压标准,干燥情况下电压大于24V,潮湿情况下电压大于12V133. 检修完毕,未检查、清理杂物就开机使用134. 长时间在釜内作业未轮换135. 检修时,釜内缺必要的通风设施136. 在搪玻璃罐外壁表面或内壁施焊137. 进入搪玻璃釜、槽内未铺设软垫138. 快速升温或急速冷却搪玻璃釜139. 使用搪玻璃罐时,罐口或人孔螺栓、卡子掉入釜内140. 使用搪玻璃釜、不锈钢釜、碳钢釜时,酸液进入釜夹套141. 选用材料未经温度、PH、腐蚀溶解性审核,可能存有压力的场合未经受压专项审核142. 检修完毕,釜内、检修现场高低位等全部空间未经全面清场、复核,既开始试运行143. 检修完毕,相关事项未做全面沟通,变更未经确认审批,相关人员未全面培训并了解就接手144. 检修未经运行确认即投料生产八、生产工艺145. 存在突发反应,缺乏应对措施及培训146. 随意改变投料量或投料配比147. 改进工艺或新工艺,未进行安全评估148. 工艺变更未经过严格审订、批准149. 工艺过程在可燃气体爆炸极限内操作150. 使用高毒物料时,采用敞口操作151. 未编写工艺操作规程进行试生产152. 未编写所用物料的物性资料及安全使用注意事项153. 所用材料分解时,产生的热量未经详细核算154. 存在粉尘爆炸的潜在危险性155. 某种原辅料不能及时投入时,釜内物料暂存时存在危险156. 原料或中间体在贮存中会发生自燃或聚合或分解危险157. 工艺中各种参数(温度、压力等)接近危险界限158. 发生异常状况时,没有将反应物迅速排放的措施159. 没有防止急剧反应和制止急剧反应的措施。
化工行业常见安全生产隐患有哪些
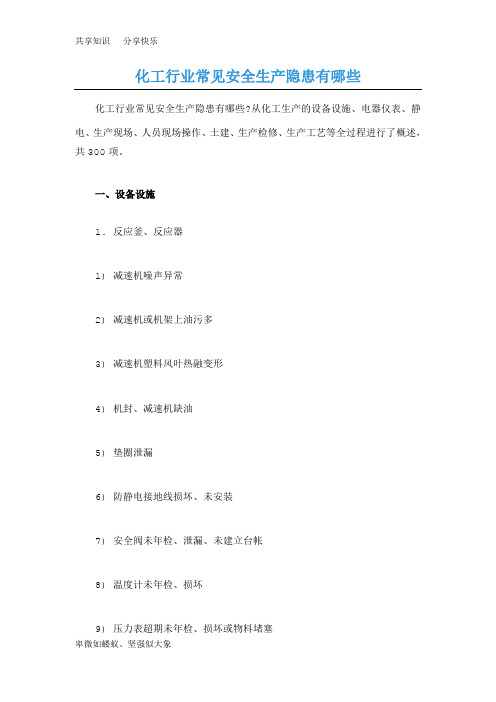
化工行业常见安全生产隐患有哪些化工行业常见安全生产隐患有哪些?从化工生产的设备设施、电器仪表、静电、生产现场、人员现场操作、土建、生产检修、生产工艺等全过程进行了概述,共300项。
一、设备设施1. 反应釜、反应器1) 减速机噪声异常2) 减速机或机架上油污多3) 减速机塑料风叶热融变形4) 机封、减速机缺油5) 垫圈泄漏6) 防静电接地线损坏、未安装7) 安全阀未年检、泄漏、未建立台帐8) 温度计未年检、损坏9) 压力表超期未年检、损坏或物料堵塞10) 重点反应釜未采用双套温度、压力显示、记录报警11) 爆破片到期未更换、泄漏、未建立台帐12) 爆破片下装阀门未开13) 存在爆炸危险反应釜未装爆破片14) 温度偏高、搅拌中断等存在异常升压或冲料15) 放料时底阀易堵塞16) 不锈钢或碳钢釜存在酸性腐蚀17) 装料量超过规定限度等超负荷运转18) 搪瓷釜内搪瓷破损仍使用于腐蚀、易燃易爆场所19) 反应釜内胆于夹套蒸汽进口处冲蚀破损20) 压力容器超过使用年限、制造质量差,多次修理后仍泄漏21) 压力容器没有铭牌22) 缺位号标识或不清23) 对有爆炸敏感性的反应釜未能有效隔离24) 重要设备未制订安全检查表25) 重要设备缺备件或备机2. 贮槽、罐区、槽车1) 液位计模糊或损坏、堵塞2) 静电接地线松动或未连接3) 法兰垫片处泄漏4) 小平台等高位贮槽未能有效固定5) 安全液封液位未达到要求6) 常压贮槽带压使用7) 装料量超过规定限度8) 非常温贮槽未装温度计9) 容器出现裂缝,仍在使用10) 频繁受真空、氮气交变载荷使贮罐破损11) 低沸点溶剂或液化气贮槽受阳光直射12) 室外贮罐等存在运输车辆等撞击危险13) 危险品罐区围堰孔洞未封堵14) 危化品罐区防护堤封堵不严密,任意开设排雨水孔15) 通向排水管的截止阀处于常开等不安全状态16) 危化品罐区的可燃或腐蚀性物料出口管线,其支架未设置吊式压式弹簧补偿措施,或直接采用挠性连接短管17) 危化品罐区未设禁打手机、禁带火源、限高限速等各种警示牌18) 危险品罐区无泄漏、送料操作记录及日常巡查19) 拖拉机随意进入危险品罐区20) 危险品罐区周边有明火或山林火灾21) 危险品罐区操作室使用电炉、电茶壶、电热板等违章用电22) 槽车在装卸地点没有接地装置23) 没有防止操作人员从罐车上坠落的措施24) 未装配有效的阻火器和车况不合格(照明灯损坏或刹车失灵)槽车进入罐区25) 槽车贮罐的安全附件(压力表、温度计、安全阀)无检验日期或存在失效26) 槽车罐体未标明压力容器下次检验日期27) 罐体上无静电拖链、防毒器材或阀门泄漏28) 卸料前和卸料后接地未静置10分钟以上29) 槽车卸料时,司机、押运员离开卸料现场,没有现场监护人员30) 采用敞开式和喷溅式卸料31) 卸料时使贮罐超标准液位或满料溢出32) 氯乙烯槽车卸料时,软管或法兰处泄漏33) 氯乙烯运输送料时,满槽34) 槽车装量不满时多次在厂内运输和卸料35) 卸料车辆为熄火及手闸制动或卸料中途启动车辆36) 在高强闪电、雷击频繁时,从事卸料操作37) 油罐接地点没有2处38) 装卸汽油、甲苯时,操作人员未穿戴防静电工作服和防静电的鞋子39) 液氨等贮槽贮存区域未设置事故围堰和应急喷淋稀释设施40) 现场未设置应急喷淋和洗眼设施41) 没有防止物料错装措施如乙酸乙酯装入汽油槽罐42) 站在汽油桶上电焊43) 未经清洗,切割汽油桶或焊接贮槽44) 液氨、氯乙烯贮罐超装45) 槽车卸料时,堵塞消防通道及侵占通行道路46) 收料员离开卸料现场47) 装卸现场使用铁制、塑料等易产生火花的工具48) 由罐区送入车间的物料贮槽没有操作记录3. 冷凝器、再沸器1) 腐蚀、垫圈老化等引起泄漏2) 冷凝后物料温度过高3) 换热介质层被淤泥、微生物堵塞4) 高温表面没有防护5) 冷却高温液体(如150℃)时,冷却水进出阀未开,或冷却水量不够6) 蒸发器等在初次使用时,急速升温7) 换热器未考虑防震措施,使与其连接管道因震动造成松动泄漏4. 管道及管件1) 管道安装完毕,内部的焊渣、其他异物未清理2) 视镜玻璃不清洁或损坏3) 选用视筒材质耐压、耐温性能不妥,视筒安装不当4) 视筒破裂或长时间带压使用5) 防静电接地线损坏6) 管道、法兰或螺栓严重腐蚀、破裂7) 高温管道未保温8) 泄爆管制作成弯管9) 管道物料及流向标识不清10) 管道色标不清11) 调试时不同物料串接阀门未盲死12) 废弃管道未及时清理13) 管阀安装位置低,易撞头或操作困难14) 腐蚀性物料管线、法兰等易泄漏处未采取防护措施15) 存在水、氮气、空气、蒸汽等进入物料管线的可能16) 高温管道边放置易燃易爆物料的铁桶或塑料桶17) 管道或管件材料选材不合理,易腐蚀18) 玻璃管液位计没有防护措施19) 在可能爆炸的视镜玻璃处,未安装防护金属网20) 止回阀不能灵活动作或失效21) 电动阀停电、气动阀停气22) 使用氢气等压力管道没有定期维护保养或带病运行23) 使用压力管道时,操作人员未经培训或无证上岗24) 维护人员没有资质修理、改造压力管道25) 压力管道焊接质量低劣,有咬边、气孔、夹渣、未焊透等焊接缺陷26) 压力管道未按照规定设安全附件或安全附件超期未校验27) 压力管道未建立档案、操作规程28) 搪玻璃管道受钢管等撞击29) 生产工艺介质改变后仍使用现有管线阀门未考虑材料适应性30) 氮气管与空气管串接31) 盐水管与冷却水管串接5. 输送泵、真空泵1) 泵泄漏2) 异常噪声3) 联轴器没有防护罩4) 泵出口未装压力表或止回阀5) 长期停用时,未放净泵和管道中液体,造成腐蚀或冻结6) 容积泵在运行时,将出口阀关闭或未装安全回流阀7) 泵进口管径小或管路长或拐弯多8) 离心泵安装高度高于吸入高度9) 未使用防静电皮带6. 离心机1) 甩滤溶剂,未充氮气或氮气管道堵塞或现场无流量计可显示2) 精烘包内需用离心机甩滤溶剂时,未装测氧仪及报警装置3) 快速刹车或用辅助工具(如铁棒等)刹车4) 离心机未有效接地5) 防爆区内未使用防静电皮带6) 离心机运行时,震动异常7. 双锥1) 无防护栏及安全连锁装置2) 人员爬入双锥内更换真空袋3) 传动皮带无防护4) 轴封泄漏5) 真空管路堵塞或使用时真空阀未开启8. 气瓶1) 气瓶没有配瓶帽、防震圈2) 氢气钢瓶夏季运输、存放时,没有遮阳措施,导致曝晒3) 部分气瓶超过年检期限4) 乙炔瓶与氧气瓶同时使用时,安全间距未超过五米5) 用带催化剂手套关氢气瓶阀6) 敲击碰撞气瓶7) 气瓶使用后,气压小于0.05Mpa8) 气瓶组及管路连接、阀门损坏9) 氢气瓶使用时,未采用防静电装置或已坏10) 气体钢瓶没有防倒措施11) 储存场所存在地沟、暗道12) 贮存场所不通风或通风不畅或有腐蚀性气体进入13) 缺灭火器材14) 乙炔气瓶放倒使用15) 气瓶颜色模糊不清二、电器仪表1. 防爆区内设置非防爆电器或控制柜非防爆2. 配电室窗户玻璃破损3. 配电室内杂物较多4. 配电室内有蒸汽水、物料管、粉尘、腐蚀性物质,致使电柜内的电气设备老化,导致短路事故5. 变压器室外有酸雾腐蚀或溶剂渗入或粉尘多6. 控制柜或变电柜后有衣服等杂物7. 配电柜过于陈旧,易产生短路8. 电缆靠近高温管道9. 架空电缆周边物料管道、污水管道等泄漏,使腐蚀性物料流入电缆桥架内10. 埋地电缆受到地下水腐蚀11. 电缆井、沟内污水严重渗入12. 电缆桥架严重腐蚀13. 电缆线保护套管老化断裂14. 铺设电气线路的电缆或钢管在穿过不同场所之间的墙或楼板处孔洞时,未采用非燃烧性材料严格堵塞15. 乱拉活动排风,导致电缆接头脱落、漏电16. 开关按钮对应设备位号标识不清17. 车间内有零乱不明电缆18. 应急照明灯未装或已坏19. 露天电动机无防护罩20. 操作现场照明度不够21. 设备与电气不配套(小牛拖大车、老牛拖大车)形成电气设备发热损坏、起火22. 电气设备、电缆桥架上冲水23. 防爆视镜灯、照明灯元宝螺丝松动,漏光三、静电24. 在易燃易爆场所,反应釜、管道、贮槽、冷凝器、输送泵、法兰、阀门未接地或接地不不良25. 在易燃易爆场所,投粉体料斗未接地,充氮气26. 超过安全流速(v2<0.64/d)输送汽油、甲苯、环己烷等液体27. 氢气流速总管超过12m/s,支管超过8m/s28. 将汽油等从高位喷入贮罐底或地面29. 在未充氮气时,异丙醇铝、镁粉等由敞口漏斗投入含汽油、甲苯等反应釜中30. 在易燃易爆场所,穿脱衣服、鞋帽及剧烈活动31. 在易燃易爆场所,用化纤材料的拖布或抹布擦洗设备或地面32. 向塑料桶中灌装汽油33. 用汽油等溶剂洗工作服或拖地或钢平台、地面34. 不锈钢、碳钢贮罐罐壁未用焊接钢筋或扁钢接地,超过50m2未有两处接地35. 存在散发易燃易爆气体的场所,未采用增湿等消除静电危害的措施36. 用塑料管吸料或装甲苯或回收甲苯37. 用压缩空气输送或搅拌汽油38. 防爆洁净区未使用防静电拖鞋39. 接地扁钢、屋顶防雷带生锈、腐蚀严重40. 高出屋面的金属设备未焊接钢筋并入避雷带四、生产现场41. 贮存原料或废料较多42. 现场“跑、冒、滴、漏”多43. 保温层损坏44. 缺有效防护栏45. 常闭式防火门常开46. 存有粉尘(镁粉、锌粉等)的操作岗位,未及时清理47. 金属钠、钠氢存放,没有防雨措施或废桶、废袋随意存放48. 消防通道堵塞或各种管线及其支架妨碍通行49. 灭火器缺少或已过期锈蚀或消防带、消防栓不符合消防要求50. 废料桶有多张标签51. 强氧化剂(双氧水、高锰酸钾等)堆放在木架上52. 钢平台晃动幅度过大53. 钢平台或钢柱腐蚀严重54. 局部区域溶剂浓度超标55. 高处阀门手柄、铁棒等易跌落56. 混凝土楼面震动大57. 室外钢棚或屋顶杂物多58. 防毒器材过期或失效59. 生产现场存放有非生产用具(食品、报纸、小说)60. 缺乏夏季的防暑降温设施61. 室外小管径水管冬季未保温62. 车间内没有紧急淋浴、洗眼等卫生设施或已损坏63. 车辆未装阻火器进入生产现场64. 易燃易爆场所没有安装可燃气体报警仪或失灵65. 反应釜、贮罐、泵等未标注设备位号和名称66. 大铁门没有固定插销,一旦风大就可能使铁门擦出火花,导致危险67. 库房门槛偏低,一旦发生意外,危险品将外溢68. 生产现场地面存放铁板、钢管五、人员、现场操作69. 没有岗位操作记录或操作记录不完整70. 吸料、灌装、搬运腐蚀性物品未戴防护用品71. 存在操作人员脱岗、离岗、睡岗等现象72. 粉体等投料岗位未戴防尘口罩73. 快速开关阀门74. 分层釜、槽底阀分层后未关75. 分层釜、槽分水阀开太大,造成水中夹油排入污水池或排水时间过长忘记关阀而跑料76. 高温釜、塔内放入空气77. 提取催化剂(如钯碳、活性镍等)现场散落较多78. 用铁棒捅管道、釜内堵塞的物料或使用不防爆器械产生火花79. 噪声环境未戴防耳器或耳塞80. 贮槽超压使用81. 使用汽油、甲苯等易燃易爆溶剂处,釜、槽未采用氮气置换82. 烟尘弥漫、通风不良或缺氧83. 带压开启反应釜盖84. 员工有职业禁忌或过敏症或接触毒物时间过长85. 紧急阀门或紧急开关不易操作86. 在易燃易爆场所,穿带钉子鞋或高跟鞋、凉鞋六、土建87. 可能发生火势蔓延的上下楼层管道井没有预防措施(如阻燃材料封堵)88. 有爆炸危险的工艺未采用防爆墙及轻质屋顶或未考虑足够的泄爆面89. 出入口和紧急通道设计数量不够或堵塞或无明显标志90. 厂房基础已受酸、碱类物质腐蚀,立柱、梁已受损严重91. 有大风时,钢窗玻璃易脱落92. 楼梯太窄或较陡93. 室内排水不畅或低洼处长期积水、积油94. 通道或作业处,头顶与顶棚没有足够的空间95. 在不明地下管线(水管、电缆等)情况下,随意开挖路面96. 使用大型机械在接近地下电缆、管道等附近挖土97. 在禁火区域内动火时,生产车间未派人监护98. 施工中出现异常情况(管道断裂、泄漏等),未立即停工进行应急处理99. 挖掘的沟、坑、池等和破坏的管道,未设置围栏和标志,夜间未设置照明100. 发现土壤有可能坍塌或滑动时,未停止作业101. 没有防止地下空罐、空池上浮的措施102. 在下罐、下池作业时,未办理相应审批手续或未遵照审批要求实施(如劳保用品、监护人落实等),防范措施未到位的情况下作业103. 在非土建作业时,未办理“非基建用工手续“或作业前不了解相应可能风险,在安全措施不到位情况下开工七、生产检修104. 在容器内进行清扫和检修时,遇到危险情况,没有紧急逃出设施或措施105. 动火作业无监护人或监护人由新近员工担任或违章动火106. 超负荷吊装107. 工具或吊物未合理固定108. 未配备或未穿戴防护用品(安全帽、安全带等)109. 无警示标志或标志已模糊不清(如防止触电、防止坠物等)110. 检修时踏在悬空管路或小管径塑料管道和搪玻璃管道上或使用不安全登高设施111. 电焊机、手动电动工具等电缆破损引起漏电,零线破损或跨接112. 盲目进入污水池、深沟、深池作业113. 冬季管架结冰滑,无防滑措施114. 安装公司电焊工无电焊证或检修工未经过相关培训115. 直接站在石棉瓦、油毡等易碎材料的屋顶上作业116. 高处作业时,未采取防范措施进行交叉作业117. 高处作业时,电焊机的零线未接到所焊位置118. 有异味或可能产生有毒气体的区域作业未佩带防毒面具119. 高处补、挖墙洞时,未设安全围栏或安全网等120. 清理出的危险物料由高层向下层散落121. 用吊装机械载人122. 夜间作业无足够照明123. 遇有六级以上强风或其他恶劣天气时,仍在露天高空作业124. 釜内作业时,釜外无两人以上监护125. 釜内检修时,没有切断电源并挂“有人检修、禁止合闸”的牌子126. 进罐作业前,未对釜进行有效清洗127. 进罐作业前,未分析可燃气体浓度、氧含量、有毒气体(CO、H2S)浓度128. 进罐作业前,未对物料管线如原料、溶剂、蒸汽、水、氮气等管线可靠隔离129. 检修过程中,未对釜内定期取样分析130. 釜外明显位置未挂上“罐内有人”的牌子131. 进罐作业时,没有执行“双检制”132. 釜内照明不符合安全电压标准,干燥情况下电压大于24V,潮湿情况下电压大于12V133. 检修完毕,未检查、清理杂物就开机使用134. 长时间在釜内作业未轮换135. 检修时,釜内缺必要的通风设施136. 在搪玻璃罐外壁表面或内壁施焊137. 进入搪玻璃釜、槽内未铺设软垫138. 快速升温或急速冷却搪玻璃釜139. 使用搪玻璃罐时,罐口或人孔螺栓、卡子掉入釜内140. 使用搪玻璃釜、不锈钢釜、碳钢釜时,酸液进入釜夹套141. 选用材料未经温度、PH、腐蚀溶解性审核,可能存有压力的场合未经受压专项审核142. 检修完毕,釜内、检修现场高低位等全部空间未经全面清场、复核,既开始试运行143. 检修完毕,相关事项未做全面沟通,变更未经确认审批,相关人员未全面培训并了解就接手144. 检修未经运行确认即投料生产八、生产工艺145. 存在突发反应,缺乏应对措施及培训146. 随意改变投料量或投料配比147. 改进工艺或新工艺,未进行安全评估148. 工艺变更未经过严格审订、批准149. 工艺过程在可燃气体爆炸极限内操作150. 使用高毒物料时,采用敞口操作151. 未编写工艺操作规程进行试生产152. 未编写所用物料的物性资料及安全使用注意事项153. 所用材料分解时,产生的热量未经详细核算154. 存在粉尘爆炸的潜在危险性155. 某种原辅料不能及时投入时,釜内物料暂存时存在危险156. 原料或中间体在贮存中会发生自燃或聚合或分解危险157. 工艺中各种参数(温度、压力等)接近危险界限158. 发生异常状况时,没有将反应物迅速排放的措施159. 没有防止急剧反应和制止急剧反应的措施。
常见安全隐患300项
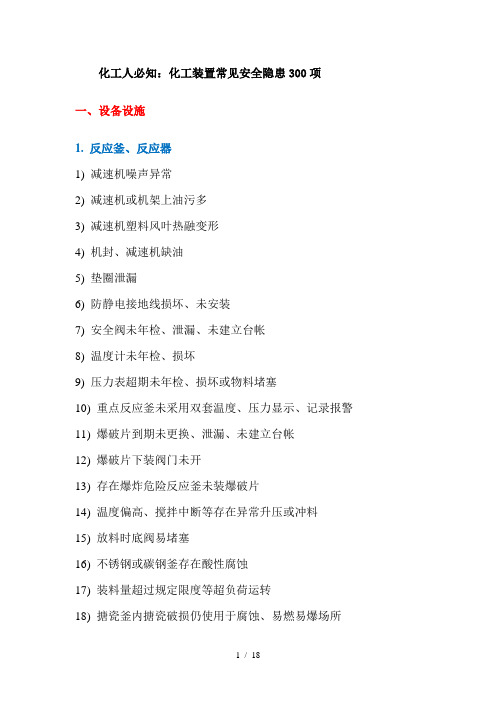
化工人必知:化工装置常见安全隐患300项一、设备设施1. 反应釜、反应器1) 减速机噪声异常2) 减速机或机架上油污多3) 减速机塑料风叶热融变形4) 机封、减速机缺油5) 垫圈泄漏6) 防静电接地线损坏、未安装7) 安全阀未年检、泄漏、未建立台帐8) 温度计未年检、损坏9) 压力表超期未年检、损坏或物料堵塞10) 重点反应釜未采用双套温度、压力显示、记录报警11) 爆破片到期未更换、泄漏、未建立台帐12) 爆破片下装阀门未开13) 存在爆炸危险反应釜未装爆破片14) 温度偏高、搅拌中断等存在异常升压或冲料15) 放料时底阀易堵塞16) 不锈钢或碳钢釜存在酸性腐蚀17) 装料量超过规定限度等超负荷运转18) 搪瓷釜内搪瓷破损仍使用于腐蚀、易燃易爆场所19) 反应釜内胆于夹套蒸汽进口处冲蚀破损20) 压力容器超过使用年限、制造质量差,多次修理后仍泄漏21) 压力容器没有铭牌22) 缺位号标识或不清23) 对有爆炸敏感性的反应釜未能有效隔离24) 重要设备未制订安全检查表25) 重要设备缺备件或备机2. 贮槽、罐区、槽车1) 液位计模糊或损坏、堵塞2) 静电接地线松动或未连接3) 法兰垫片处泄漏4) 小平台等高位贮槽未能有效固定5) 安全液封液位未达到要求6) 常压贮槽带压使用7) 装料量超过规定限度8) 非常温贮槽未装温度计9) 容器出现裂缝,仍在使用10) 频繁受真空、氮气交变载荷使贮罐破损11) 低沸点溶剂或液化气贮槽受阳光直射12) 室外贮罐等存在运输车辆等撞击危险13) 危险品罐区围堰孔洞未封堵14) 危化品罐区防护堤封堵不严密,任意开设排雨水孔15) 通向排水管的截止阀处于常开等不安全状态16) 危化品罐区的可燃或腐蚀性物料出口管线,其支架未设置吊式压式弹簧补偿措施,或直接采用挠性连接短管17) 危化品罐区未设禁打手机、禁带火源、限高限速等各种警示牌18) 危险品罐区无泄漏、送料操作记录及日常巡查19) 拖拉机随意进入危险品罐区20) 危险品罐区周边有明火或山林火灾21) 危险品罐区操作室使用电炉、电茶壶、电热板等违章用电22) 槽车在装卸地点没有接地装置23) 没有防止操作人员从罐车上坠落的措施24) 未装配有效的阻火器和车况不合格(照明灯损坏或刹车失灵)槽车进入罐区25) 槽车贮罐的安全附件(压力表、温度计、安全阀)无检验日期或存在失效26) 槽车罐体未标明压力容器下次检验日期27) 罐体上无静电拖链、防毒器材或阀门泄漏28) 卸料前和卸料后接地未静置10分钟以上29) 槽车卸料时,司机、押运员离开卸料现场,没有现场监护人员30) 采用敞开式和喷溅式卸料31) 卸料时使贮罐超标准液位或满料溢出32) 氯乙烯槽车卸料时,软管或法兰处泄漏33) 氯乙烯运输送料时,满槽34) 槽车装量不满时多次在厂内运输和卸料35) 卸料车辆为熄火及手闸制动或卸料中途启动车辆36) 在高强闪电、雷击频繁时,从事卸料操作37) 油罐接地点没有2处38) 装卸汽油、甲苯时,操作人员未穿戴防静电工作服和防静电的鞋子39) 液氨等贮槽贮存区域未设置事故围堰和应急喷淋稀释设施40) 现场未设置应急喷淋和洗眼设施41) 没有防止物料错装措施如乙酸乙酯装入汽油槽罐42) 站在汽油桶上电焊43) 未经清洗,切割汽油桶或焊接贮槽44) 液氨、氯乙烯贮罐超装45) 槽车卸料时,堵塞消防通道及侵占通行道路46) 收料员离开卸料现场47) 装卸现场使用铁制、塑料等易产生火花的工具48) 由罐区送入车间的物料贮槽没有操作记录3. 冷凝器、再沸器1) 腐蚀、垫圈老化等引起泄漏2) 冷凝后物料温度过高3) 换热介质层被淤泥、微生物堵塞4) 高温表面没有防护5) 冷却高温液体(如150℃)时,冷却水进出阀未开,或冷却水量不够6) 蒸发器等在初次使用时,急速升温7) 换热器未考虑防震措施,使与其连接管道因震动造成松动泄漏4. 管道及管件1) 管道安装完毕,内部的焊渣、其他异物未清理2) 视镜玻璃不清洁或损坏3) 选用视筒材质耐压、耐温性能不妥,视筒安装不当4) 视筒破裂或长时间带压使用5) 防静电接地线损坏6) 管道、法兰或螺栓严重腐蚀、破裂7) 高温管道未保温8) 泄爆管制作成弯管9) 管道物料及流向标识不清10) 管道色标不清11) 调试时不同物料串接阀门未盲死12) 废弃管道未及时清理13) 管阀安装位置低,易撞头或操作困难14) 腐蚀性物料管线、法兰等易泄漏处未采取防护措施15) 存在水、氮气、空气、蒸汽等进入物料管线的可能16) 高温管道边放置易燃易爆物料的铁桶或塑料桶17) 管道或管件材料选材不合理,易腐蚀18) 玻璃管液位计没有防护措施19) 在可能爆炸的视镜玻璃处,未安装防护金属网20) 止回阀不能灵活动作或失效21) 电动阀停电、气动阀停气22) 使用氢气等压力管道没有定期维护保养或带病运行23) 使用压力管道时,操作人员未经培训或无证上岗24) 维护人员没有资质修理、改造压力管道25) 压力管道焊接质量低劣,有咬边、气孔、夹渣、未焊透等焊接缺陷26) 压力管道未按照规定设安全附件或安全附件超期未校验27) 压力管道未建立档案、操作规程28) 搪玻璃管道受钢管等撞击29) 生产工艺介质改变后仍使用现有管线阀门未考虑材料适应性30) 氮气管与空气管串接31) 盐水管与冷却水管串接5. 输送泵、真空泵1) 泵泄漏2) 异常噪声3) 联轴器没有防护罩4) 泵出口未装压力表或止回阀5) 长期停用时,未放净泵和管道中液体,造成腐蚀或冻结6) 容积泵在运行时,将出口阀关闭或未装安全回流阀7) 泵进口管径小或管路长或拐弯多8) 离心泵安装高度高于吸入高度9) 未使用防静电皮带6. 离心机1) 甩滤溶剂,未充氮气或氮气管道堵塞或现场无流量计可显示2) 精烘包内需用离心机甩滤溶剂时,未装测氧仪及报警装置3) 快速刹车或用辅助工具(如铁棒等)刹车4) 离心机未有效接地5) 防爆区内未使用防静电皮带6) 离心机运行时,震动异常7. 双锥(双锥回转真空干燥机)1) 无防护栏及安全连锁装置2) 人员爬入双锥内更换真空袋3) 传动皮带无防护4) 轴封泄漏5) 真空管路堵塞或使用时真空阀未开启8. 气瓶1) 气瓶没有配瓶帽、防震圈2) 氢气钢瓶夏季运输、存放时,没有遮阳措施,导致曝晒3) 部分气瓶超过年检期限4) 乙炔瓶与氧气瓶同时使用时,安全间距未超过五米5) 用带催化剂手套关氢气瓶阀6) 敲击碰撞气瓶7) 气瓶使用后,气压小于0.05Mpa8) 气瓶组及管路连接、阀门损坏9) 氢气瓶使用时,未采用防静电装置或已坏10) 气体钢瓶没有防倒措施11) 储存场所存在地沟、暗道12) 贮存场所不通风或通风不畅或有腐蚀性气体进入13) 缺灭火器材14) 乙炔气瓶放倒使用15) 气瓶颜色模糊不清二、电器仪表1. 防爆区内设置非防爆电器或控制柜非防爆2. 配电室窗户玻璃破损3. 配电室内杂物较多4. 配电室内有蒸汽水、物料管、粉尘、腐蚀性物质,致使电柜内的电气设备老化,导致短路事故5. 变压器室外有酸雾腐蚀或溶剂渗入或粉尘多6. 控制柜或变电柜后有衣服等杂物7. 配电柜过于陈旧,易产生短路8. 电缆靠近高温管道9. 架空电缆周边物料管道、污水管道等泄漏,使腐蚀性物料流入电缆桥架内10. 埋地电缆受到地下水腐蚀11. 电缆井、沟内污水严重渗入12. 电缆桥架严重腐蚀13. 电缆线保护套管老化断裂14. 铺设电气线路的电缆或钢管在穿过不同场所之间的墙或楼板处孔洞时,未采用非燃烧性材料严格堵塞15. 乱拉活动排风,导致电缆接头脱落、漏电16. 开关按钮对应设备位号标识不清17. 车间内有零乱不明电缆18. 应急照明灯未装或已坏19. 露天电动机无防护罩20. 操作现场照明度不够21. 设备与电气不配套(小牛拖大车、老牛拖大车)形成电气设备发热损坏、起火22. 电气设备、电缆桥架上冲水23. 防爆视镜灯、照明灯元宝螺丝松动,漏光三、静电24. 在易燃易爆场所,反应釜、管道、贮槽、冷凝器、输送泵、法兰、阀门未接地或接地不不良25. 在易燃易爆场所,投粉体料斗未接地,充氮气26. 超过安全流速(v2<0.64/d)输送汽油、甲苯、环己烷等液体27. 氢气流速总管超过12m/s,支管超过8m/s28. 将汽油等从高位喷入贮罐底或地面29. 在未充氮气时,异丙醇铝、镁粉等由敞口漏斗投入含汽油、甲苯等反应釜中30. 在易燃易爆场所,穿脱衣服、鞋帽及剧烈活动31. 在易燃易爆场所,用化纤材料的拖布或抹布擦洗设备或地面32. 向塑料桶中灌装汽油33. 用汽油等溶剂洗工作服或拖地或钢平台、地面34. 不锈钢、碳钢贮罐罐壁未用焊接钢筋或扁钢接地,超过50m2未有两处接地35. 存在散发易燃易爆气体的场所,未采用增湿等消除静电危害的措施36. 用塑料管吸料或装甲苯或回收甲苯37. 用压缩空气输送或搅拌汽油38. 防爆洁净区未使用防静电拖鞋39. 接地扁钢、屋顶防雷带生锈、腐蚀严重40. 高出屋面的金属设备未焊接钢筋并入避雷带四、生产现场41. 贮存原料或废料较多42. 现场“跑、冒、滴、漏”多43. 保温层损坏44. 缺有效防护栏45. 常闭式防火门常开46. 存有粉尘(镁粉、锌粉等)的操作岗位,未及时清理47. 金属钠、钠氢存放,没有防雨措施或废桶、废袋随意存放48. 消防通道堵塞或各种管线及其支架妨碍通行49. 灭火器缺少或已过期锈蚀或消防带、消防栓不符合消防要求50. 废料桶有多张标签51. 强氧化剂(双氧水、高锰酸钾等)堆放在木架上52. 钢平台晃动幅度过大53. 钢平台或钢柱腐蚀严重54. 局部区域溶剂浓度超标55. 高处阀门手柄、铁棒等易跌落56. 混凝土楼面震动大57. 室外钢棚或屋顶杂物多58. 防毒器材过期或失效59. 生产现场存放有非生产用具(食品、报纸、小说)60. 缺乏夏季的防暑降温设施61. 室外小管径水管冬季未保温62. 车间内没有紧急淋浴、洗眼等卫生设施或已损坏63. 车辆未装阻火器进入生产现场64. 易燃易爆场所没有安装可燃气体报警仪或失灵65. 反应釜、贮罐、泵等未标注设备位号和名称66. 大铁门没有固定插销,一旦风大就可能使铁门擦出火花,导致危险67. 库房门槛偏低,一旦发生意外,危险品将外溢68. 生产现场地面存放铁板、钢管五、人员、现场操作69. 没有岗位操作记录或操作记录不完整70. 吸料、灌装、搬运腐蚀性物品未戴防护用品71. 存在操作人员脱岗、离岗、睡岗等现象72. 粉体等投料岗位未戴防尘口罩73. 快速开关阀门74. 分层釜、槽底阀分层后未关75. 分层釜、槽分水阀开太大,造成水中夹油排入污水池或排水时间过长忘记关阀而跑料76. 高温釜、塔内放入空气77. 提取催化剂(如钯碳、活性镍等)现场散落较多78. 用铁棒捅管道、釜内堵塞的物料或使用不防爆器械产生火花79. 噪声环境未戴防耳器或耳塞80. 贮槽超压使用81. 使用汽油、甲苯等易燃易爆溶剂处,釜、槽未采用氮气置换82. 烟尘弥漫、通风不良或缺氧83. 带压开启反应釜盖84. 员工有职业禁忌或过敏症或接触毒物时间过长85. 紧急阀门或紧急开关不易操作86. 在易燃易爆场所,穿带钉子鞋或高跟鞋、凉鞋六、土建87. 可能发生火势蔓延的上下楼层管道井没有预防措施(如阻燃材料封堵)88. 有爆炸危险的工艺未采用防爆墙及轻质屋顶或未考虑足够的泄爆面89. 出入口和紧急通道设计数量不够或堵塞或无明显标志90. 厂房基础已受酸、碱类物质腐蚀,立柱、梁已受损严重91. 有大风时,钢窗玻璃易脱落92. 楼梯太窄或较陡93. 室内排水不畅或低洼处长期积水、积油94. 通道或作业处,头顶与顶棚没有足够的空间95. 在不明地下管线(水管、电缆等)情况下,随意开挖路面96. 使用大型机械在接近地下电缆、管道等附近挖土97. 在禁火区域内动火时,生产车间未派人监护98. 施工中出现异常情况(管道断裂、泄漏等),未立即停工进行应急处理99. 挖掘的沟、坑、池等和破坏的管道,未设置围栏和标志,夜间未设置照明100. 发现土壤有可能坍塌或滑动时,未停止作业101. 没有防止地下空罐、空池上浮的措施102. 在下罐、下池作业时,未办理相应审批手续或未遵照审批要求实施(如劳保用品、监护人落实等),防范措施未到位的情况下作业103. 在非土建作业时,未办理“非基建用工手续“或作业前不了解相应可能风险,在安全措施不到位情况下开工七、生产检修104. 在容器内进行清扫和检修时,遇到危险情况,没有紧急逃出设施或措施105. 动火作业无监护人或监护人由新近员工担任或违章动火106. 超负荷吊装107. 工具或吊物未合理固定108. 未配备或未穿戴防护用品(安全帽、安全带等)109. 无警示标志或标志已模糊不清(如防止触电、防止坠物等)110. 检修时踏在悬空管路或小管径塑料管道和搪玻璃管道上或使用不安全登高设施111. 电焊机、手动电动工具等电缆破损引起漏电,零线破损或跨接112. 盲目进入污水池、深沟、深池作业113. 冬季管架结冰滑,无防滑措施114. 安装公司电焊工无电焊证或检修工未经过相关培训115. 直接站在石棉瓦、油毡等易碎材料的屋顶上作业116. 高处作业时,未采取防范措施进行交叉作业117. 高处作业时,电焊机的零线未接到所焊位置118. 有异味或可能产生有毒气体的区域作业未佩带防毒面具119. 高处补、挖墙洞时,未设安全围栏或安全网等120. 清理出的危险物料由高层向下层散落121. 用吊装机械载人122. 夜间作业无足够照明123. 遇有六级以上强风或其他恶劣天气时,仍在露天高空作业124. 釜内作业时,釜外无两人以上监护125. 釜内检修时,没有切断电源并挂“有人检修、禁止合闸”的牌子126. 进罐作业前,未对釜进行有效清洗127. 进罐作业前,未分析可燃气体浓度、氧含量、有毒气体(CO、H2S)浓度128. 进罐作业前,未对物料管线如原料、溶剂、蒸汽、水、氮气等管线可靠隔离129. 检修过程中,未对釜内定期取样分析130. 釜外明显位置未挂上“罐内有人”的牌子131. 进罐作业时,没有执行“双检制”132. 釜内照明不符合安全电压标准,干燥情况下电压大于24V,潮湿情况下电压大于12V133. 检修完毕,未检查、清理杂物就开机使用134. 长时间在釜内作业未轮换135. 检修时,釜内缺必要的通风设施136. 在搪玻璃罐外壁表面或内壁施焊137. 进入搪玻璃釜、槽内未铺设软垫138. 快速升温或急速冷却搪玻璃釜139. 使用搪玻璃罐时,罐口或人孔螺栓、卡子掉入釜内140. 使用搪玻璃釜、不锈钢釜、碳钢釜时,酸液进入釜夹套141. 选用材料未经温度、PH、腐蚀溶解性审核,可能存有压力的场合未经受压专项审核142. 检修完毕,釜内、检修现场高低位等全部空间未经全面清场、复核,既开始试运行143. 检修完毕,相关事项未做全面沟通,变更未经确认审批,相关人员未全面培训并了解就接手144. 检修未经运行确认即投料生产八、生产工艺145. 存在突发反应,缺乏应对措施及培训146. 随意改变投料量或投料配比147. 改进工艺或新工艺,未进行安全评估148. 工艺变更未经过严格审订、批准149. 工艺过程在可燃气体爆炸极限内操作150. 使用高毒物料时,采用敞口操作151. 未编写工艺操作规程进行试生产152. 未编写所用物料的物性资料及安全使用注意事项153. 所用材料分解时,产生的热量未经详细核算154. 存在粉尘爆炸的潜在危险性155. 某种原辅料不能及时投入时,釜内物料暂存时存在危险156. 原料或中间体在贮存中会发生自燃或聚合或分解危险157. 工艺中各种参数(温度、压力等)接近危险界限158. 发生异常状况时,没有将反应物迅速排放的措施159. 没有防止急剧反应和制止急剧反应的措施最新文件仅供参考已改成word文本。
化工行业常见安全生产隐患300项

化工行业常见安全生产隐患300项、设备设施1. 反应釜、反应器1)减速机噪声异常2)减速机或机架上油污多3)减速机塑料风叶热融变形4)机封、减速机缺油5)垫圈泄漏6)防静电接地线损坏、未安装7)安全阀未年检、泄漏、未建立台帐8)温度计未年检、损坏9)压力表超期未年检、损坏或物料堵塞10)重点反应釜未采用双套温度、压力显示、记录报警11)爆破片到期未更换、泄漏、未建立台帐12)爆破片下装阀门未开13)存在爆炸危险反应釜未装爆破片|14)温度偏高、搅拌中断等存在异常升压或冲料15)放料时底阀易堵塞16)不锈钢或碳钢釜存在酸性腐蚀17)装料量超过规定限度等超负荷运转18)搪瓷釜内搪瓷破损仍使用于腐蚀、易燃易爆场所19)反应釜内胆于夹套蒸汽进口处冲蚀破损21)压力容器没有铭牌22)缺位号标识或不清23)对有爆炸敏感性的反应釜未能有效隔离24)重要设备未制订安全检查表或直 25)重要设备缺备件或备机2. 贮槽、罐区、槽车1) 液位计模糊或损坏、堵塞2) 静电接地线松动或未连接3) 法兰垫片处泄漏4) 小平台等高位贮槽未能有效固定5) 安全液圭寸液位未达到要求6) 常压贮槽带压使用7) 装料量超过规定限度8) 非常温贮槽未装温度计9) 容器出现裂缝,仍在使用10) 频繁受真空、氮气交变载荷使贮罐破损11) 低沸点溶剂或液化气贮槽受阳光直射12) 室外贮罐等存在运输车辆等撞击危险13) 危险品罐区围堰孔洞未封堵14)危化品罐区防护堤封堵不严密,任意开设排雨水孔 15) 通向排水管的截止阀处于常开等不安全状态16)危化品罐区的可燃或腐蚀性物料出口管线, 其支架未设置吊式压式弹簧补偿措施, 接采用挠性连接短管17) 危化品罐区未设禁打手机、禁带火源、限高限速等各种警示牌18) 危险品罐区无泄漏、送料操作记录及日常巡查19)拖拉机随意进入危险品罐区 20) 危险品罐区周边有明火或山林火灾22) 槽车在装卸地点没有接地装置23) 没有防止操作人员从罐车上坠落的措施24)未装配有效的阻火器和车况不合格(照明灯损坏或刹车失灵)槽车进入罐区 25) 槽车贮罐的安全附件(压力表、温度计、安全阀)无检验日期或存在失效26) 槽车罐体未标明压力容器下次检验日期27) 罐体上无静电拖链、防毒器材或阀门泄漏28) 卸料前和卸料后接地未静置10分钟以上 29) 槽车卸料时,司机、押运员离开卸料现场,没有现场监护人员30)采用敞开式和喷溅式卸料 31) 卸料时使贮罐超标准液位或满料溢出32) 氯乙烯槽车卸料时,软管或法兰处泄漏33)氯乙烯运输送料时,满槽 34) 槽车装量不满时多次在厂内运输和卸料35) 卸料车辆为熄火及手闸制动或卸料中途启动车辆36)在高强闪电、雷击频繁时,从事卸料操作37)油罐接地点没有2处38)装卸汽油、甲苯时,操作人员未穿戴防静电工作服和防静电的鞋子39)液氨等贮槽贮存区域未设置事故围堰和应急喷淋稀释设施40)现场未设置应急喷淋和洗眼设施41)没有防止物料错装措施如乙酸乙酯装入汽油槽罐42)站在汽油桶上电焊43)未经清洗,切割汽油桶或焊接贮槽45)槽车卸料时,堵塞消防通道及侵占通行道路46)收料员离开卸料现场47)装卸现场使用铁制、塑料等易产生火花的工具48)由罐区送入车间的物料贮槽没有操作记录3. 冷凝器、再沸器1)腐蚀、垫圈老化等引起泄漏2)冷凝后物料温度过高3)换热介质层被淤泥、微生物堵塞4)高温表面没有防护5)冷却高温液体(如150 C)时,冷却水进出阀未开,或冷却水量不够6)蒸发器等在初次使用时,急速升温7)换热器未考虑防震措施,使与其连接管道因震动造成松动泄漏4. 管道及管件1)管道安装完毕,内部的焊渣、其他异物未清理2)视镜玻璃不清洁或损坏3)选用视筒材质耐压、耐温性能不妥,视筒安装不当4)视筒破裂或长时间带压使用5)防静电接地线损坏6)管道、法兰或螺栓严重腐蚀、破裂7)高温管道未保温8)泄爆管制作成弯管9)管道物料及流向标识不清10)管道色标不清11)调试时不同物料串接阀门未盲死12)废弃管道未及时清理13)管阀安装位置低,易撞头或操作困难14)腐蚀性物料管线、法兰等易泄漏处未采取防护措施15)存在水、氮气、空气、蒸汽等进入物料管线的可能16)高温管道边放置易燃易爆物料的铁桶或塑料桶17)管道或管件材料选材不合理,易腐蚀18)玻璃管液位计没有防护措施19)在可能爆炸的视镜玻璃处,未安装防护金属网20)止回阀不能灵活动作或失效21)电动阀停电、气动阀停气22)使用氢气等压力管道没有定期维护保养或带病运行23)使用压力管道时,操作人员未经培训或无证上岗24)维护人员没有资质修理、改造压力管道25)压力管道焊接质量低劣,有咬边、气孔、夹渣、未焊透等焊接缺陷26)压力管道未按照规定设安全附件或安全附件超期未校验27)压力管道未建立档案、操作规程28)搪玻璃管道受钢管等撞击29)生产工艺介质改变后仍使用现有管线阀门未考虑材料适应性30)氮气管与空气管串接31)盐水管与冷却水管串接5. 输送泵、真空泵1)泵泄漏2)异常噪声3)联轴器没有防护罩4)泵出口未装压力表或止回阀5)长期停用时,未放净泵和管道中液体,造成腐蚀或冻结6)容积泵在运行时,将出口阀关闭或未装安全回流阀7)泵进口管径小或管路长或拐弯多8)离心泵安装高度高于吸入高度9)未使用防静电皮带6. 离心机1)甩滤溶剂,未充氮气或氮气管道堵塞或现场无流量计可显示2)精烘包内需用离心机甩滤溶剂时,未装测氧仪及报警装置3)快速刹车或用辅助工具(如铁棒等)刹车4)离心机未有效接地5)防爆区内未使用防静电皮带6)离心机运行时,震动异常7. 双锥(双锥回转真空干燥机)1)无防护栏及安全连锁装置2)人员爬入双锥内更换真空袋3)传动皮带无防护4)轴封泄漏5)真空管路堵塞或使用时真空阀未开启8. 气瓶1)气瓶没有配瓶帽、防震圈2)氢气钢瓶夏季运输、存放时,没有遮阳措施,导致曝晒3)部分气瓶超过年检期限|5)用带催化剂手套关氢气瓶阀6)敲击碰撞气瓶7)气瓶使用后,气压小于0.05Mpa8)气瓶组及管路连接、阀门损坏9)氢气瓶使用时,未采用防静电装置或已坏10)气体钢瓶没有防倒措施11)储存场所存在地沟、暗道12)贮存场所不通风或通风不畅或有腐蚀性气体进入13)缺灭火器材14)乙炔气瓶放倒使用15)气瓶颜色模糊不清二、电器仪表1.防爆区内设置非防爆电器或控制柜非防爆2.配电室窗户玻璃破损3.配电室内杂物较多5. 变压器室外有酸雾腐蚀或溶剂渗入或粉尘多4.配电室内有蒸汽水、物料管、粉尘、腐蚀性物质,致使电柜内的电气设备老化,导致短路事故6.控制柜或变电柜后有衣服等杂物7.配电柜过于陈旧,易产生短路8.电缆靠近高温管道9.架空电缆周边物料管道、污水管道等泄漏,使腐蚀性物料流入电缆桥架内10.埋地电缆受到地下水腐蚀11.电缆井、沟内污水严重渗入12.电缆桥架严重腐蚀13.电缆线保护套管老化断裂14.铺设电气线路的电缆或钢管在穿过不同场所之间的墙或楼板处孔洞时,未采用非燃烧性材料严格堵塞15.乱拉活动排风,导致电缆接头脱落、漏电16.开关按钮对应设备位号标识不清17.车间内有零乱不明电缆18.应急照明灯未装或已坏19.露天电动机无防护罩20.操作现场照明度不够21.设备与电气不配套(小牛拖大车、老牛拖大车)形成电气设备发热损坏、起火22.电气设备、电缆桥架上冲水23.防爆视镜灯、照明灯元宝螺丝松动,漏光三、静电24.在易燃易爆场所,反应釜、管道、贮槽、冷凝器、输送泵、法兰、阀门未接地或接地不不良25.在易燃易爆场所,投粉体料斗未接地,充氮气26.超过安全流速(v2<0.64/d )输送汽油、甲苯、环己烷等液体28.将汽油等从高位喷入贮罐底或地面29.在未充氮气时,异丙醇铝、镁粉等由敞口漏斗投入含汽油、甲苯等反应釜中30.在易燃易爆场所,穿脱衣服、鞋帽及剧烈活动31.在易燃易爆场所,用化纤材料的拖布或抹布擦洗设备或地面32.向塑料桶中灌装汽油33.用汽油等溶剂洗工作服或拖地或钢平台、地面34.不锈钢、碳钢贮罐罐壁未用焊接钢筋或扁钢接地,超过50m2未有两处接地35.存在散发易燃易爆气体的场所,未采用增湿等消除静电危害的措施36.用塑料管吸料或装甲苯或回收甲苯37.用压缩空气输送或搅拌汽油38.防爆洁净区未使用防静电拖鞋39.接地扁钢、屋顶防雷带生锈、腐蚀严重40.高出屋面的金属设备未焊接钢筋并入避雷带四、生产现场41.贮存原料或废料较多42.现场跑、冒、滴、漏”多43.保温层损坏44.缺有效防护栏45.常闭式防火门常开46.存有粉尘(镁粉、锌粉等)的操作岗位,未及时清理47.金属钠、钠氢存放,没有防雨措施或废桶、废袋随意存放48.消防通道堵塞或各种管线及其支架妨碍通行49.灭火器缺少或已过期锈蚀或消防带、消防栓不符合消防要求50.废料桶有多张标签51.强氧化剂(双氧水、高锰酸钾等)堆放在木架上52.钢平台晃动幅度过大53.钢平台或钢柱腐蚀严重54.局部区域溶剂浓度超标55.高处阀门手柄、铁棒等易跌落56.混凝土楼面震动大57.室外钢棚或屋顶杂物多58.防毒器材过期或失效59.生产现场存放有非生产用具(食品、报纸、小说)60.缺乏夏季的防暑降温设施61.室外小管径水管冬季未保温62.车间内没有紧急淋浴、洗眼等卫生设施或已损坏63.车辆未装阻火器进入生产现场64.易燃易爆场所没有安装可燃气体报警仪或失灵65.反应釜、贮罐、泵等未标注设备位号和名称66.大铁门没有固定插销,一旦风大就可能使铁门擦出火花,导致危险67.库房门槛偏低,一旦发生意外,危险品将外溢68.生产现场地面存放铁板、钢管五、人员、现场操作69.没有岗位操作记录或操作记录不完整70.吸料、灌装、搬运腐蚀性物品未戴防护用品71.存在操作人员脱岗、离岗、睡岗等现象72.粉体等投料岗位未戴防尘口罩73.快速开关阀门74.分层釜、槽底阀分层后未关75.分层釜、槽分水阀开太大,造成水中夹油排入污水池或排水时间过长忘记关阀而跑料76.高温釜、塔内放入空气77.提取催化剂(如钯碳、活性镍等)现场散落较多78.用铁棒捅管道、釜内堵塞的物料或使用不防爆器械产生火花79.噪声环境未戴防耳器或耳塞80.贮槽超压使用81.使用汽油、甲苯等易燃易爆溶剂处,釜、槽未采用氮气置换82.烟尘弥漫、通风不良或缺氧83.带压开启反应釜盖84.员工有职业禁忌或过敏症或接触毒物时间过长85.紧急阀门或紧急开关不易操作86.在易燃易爆场所,穿带钉子鞋或高跟鞋、凉鞋六、土建87.可能发生火势蔓延的上下楼层管道井没有预防措施(如阻燃材料封堵)88.有爆炸危险的工艺未采用防爆墙及轻质屋顶或未考虑足够的泄爆面89.出入口和紧急通道设计数量不够或堵塞或无明显标志90.厂房基础已受酸、碱类物质腐蚀,立柱、梁已受损严重91.有大风时,钢窗玻璃易脱落92.楼梯太窄或较陡93.室内排水不畅或低洼处长期积水、积油94.通道或作业处,头顶与顶棚没有足够的空间95.在不明地下管线(水管、电缆等)情况下,随意开挖路面96.使用大型机械在接近地下电缆、管道等附近挖土97.在禁火区域内动火时,生产车间未派人监护98.施工中出现异常情况(管道断裂、泄漏等),未立即停工进行应急处理99.挖掘的沟、坑、池等和破坏的管道,未设置围栏和标志,夜间未设置照明100.发现土壤有可能坍塌或滑动时,未停止作业101.没有防止地下空罐、空池上浮的措施102.在下罐、下池作业时,未办理相应审批手续或未遵照审批要求实施(如劳保用品、监护人落实等),防范措施未到位的情况下作业103.在非土建作业时,未办理非基建用工手续或作业前不了解相应可能风险,在安全措施不到位情况下开工12V 七、 生产检修104.在容器内进行清扫和检修时,遇到危险情况,没有紧急逃出设施或措施 105.动火作业无监护人或监护人由新近员工担任或违章动火 106.超负荷吊装 107.工具或吊物未合理固定 108.未配备或未穿戴防护用品(安全帽、安全带等) 109.无警示标志或标志已模糊不清(如防止触电、防止坠物等) 110.检修时踏在悬空管路或小管径塑料管道和搪玻璃管道上或使用不安全登高设施 111.电焊机、手动电动工具等电缆破损引起漏电,零线破损或跨接 112.盲目进入污水池、深沟、深池作业 113.冬季管架结冰滑,无防滑措施 114.安装公司电焊工无电焊证或检修工未经过相关培训 115.直接站在石棉瓦、油毡等易碎材料的屋顶上作业 116.高处作业时,未采取防范措施进行交叉作业 117.高处作业时,电焊机的零线未接到所焊位置 118.有异味或可能产生有毒气体的区域作业未佩带防毒面具 119.高处补、挖墙洞时,未设安全围栏或安全网等 120.清理出的危险物料由高层向下层散落 121.用吊装机械载人 122.夜间作业无足够照明 123.遇有六级以上强风或其他恶劣天气时,仍在露天高空作业 124.釜内作业时,釜外无两人以上监护 125. 釜内检修时,没有切断电源并挂 有人检修、禁止合闸”的牌子 126. 进罐作业前,未对釜进行有效清洗127.进罐作业前,未分析可燃气体浓度、氧含量、有毒气体( CO 、H2S )浓度 128.进罐作业前,未对物料管线如原料、溶剂、蒸汽、水、氮气等管线可靠隔离 129.检修过程中,未对釜内定期取样分析 130.釜外明显位置未挂上 罐内有人”的牌子 131.进罐作业时,没有执行 双检制” 132. 釜内照明不符合安全电压标准,干燥情况下电压大于24V,潮湿情况下电压大于 133.检修完毕,未检查、清理杂物就开机使用 134. 长时间在釜内作业未轮换135 .检修时,釜内缺必要的通风设施136. 在搪玻璃罐外壁表面或内壁施焊137. 进入搪玻璃釜、槽内未铺设软垫138 .快速升温或急速冷却搪玻璃釜139.使用搪玻璃罐时,罐口或人孔螺栓、卡子掉入釜内140.使用搪玻璃釜、不锈钢釜、碳钢釜时,酸液进入釜夹套141.选用材料未经温度、PH、腐蚀溶解性审核,可能存有压力的场合未经受压专项审核142.检修完毕,釜内、检修现场高低位等全部空间未经全面清场、复核,既开始试运行143.检修完毕,相关事项未做全面沟通,变更未经确认审批,相关人员未全面培训并了解就接手144 .检修未经运行确认即投料生产八、生产工艺145. 存在突发反应,缺乏应对措施及培训146. 随意改变投料量或投料配比147. 改进工艺或新工艺,未进行安全评估148. 工艺变更未经过严格审订、批准149. 工艺过程在可燃气体爆炸极限内操作150. 使用高毒物料时,采用敞口操作151. 未编写工艺操作规程进行试生产152. 未编写所用物料的物性资料及安全使用注意事项153. 所用材料分解时,产生的热量未经详细核算154. 存在粉尘爆炸的潜在危险性155. 某种原辅料不能及时投入时,釜内物料暂存时存在危险156. 原料或中间体在贮存中会发生自燃或聚合或分解危险157. 工艺中各种参数(温度、压力等)接近危险界限158. 发生异常状况时,没有将反应物迅速排放的措施159. 没有防止急剧反应和制止急剧反应的措施。
化工企业日常安全隐患300项
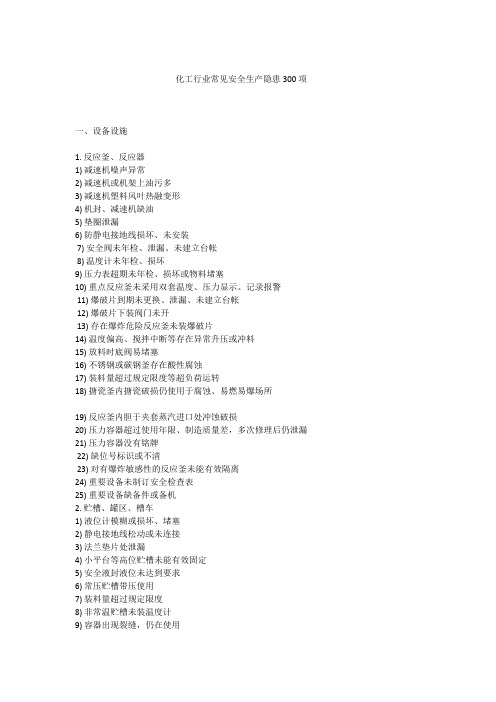
化工行业常见安全生产隐患300项一、设备设施1. 反应釜、反应器1) 减速机噪声异常2) 减速机或机架上油污多3) 减速机塑料风叶热融变形4) 机封、减速机缺油5) 垫圈泄漏6) 防静电接地线损坏、未安装7) 安全阀未年检、泄漏、未建立台帐8) 温度计未年检、损坏9) 压力表超期未年检、损坏或物料堵塞10) 重点反应釜未采用双套温度、压力显示、记录报警11) 爆破片到期未更换、泄漏、未建立台帐12) 爆破片下装阀门未开13) 存在爆炸危险反应釜未装爆破片14) 温度偏高、搅拌中断等存在异常升压或冲料15) 放料时底阀易堵塞16) 不锈钢或碳钢釜存在酸性腐蚀17) 装料量超过规定限度等超负荷运转18) 搪瓷釜内搪瓷破损仍使用于腐蚀、易燃易爆场所19) 反应釜内胆于夹套蒸汽进口处冲蚀破损20) 压力容器超过使用年限、制造质量差,多次修理后仍泄漏21) 压力容器没有铭牌22) 缺位号标识或不清23) 对有爆炸敏感性的反应釜未能有效隔离24) 重要设备未制订安全检查表25) 重要设备缺备件或备机2. 贮槽、罐区、槽车1) 液位计模糊或损坏、堵塞2) 静电接地线松动或未连接3) 法兰垫片处泄漏4) 小平台等高位贮槽未能有效固定5) 安全液封液位未达到要求6) 常压贮槽带压使用7) 装料量超过规定限度8) 非常温贮槽未装温度计9) 容器出现裂缝,仍在使用10) 频繁受真空、氮气交变载荷使贮罐破损11) 低沸点溶剂或液化气贮槽受阳光直射12) 室外贮罐等存在运输车辆等撞击危险13) 危险品罐区围堰孔洞未封堵14) 危化品罐区防护堤封堵不严密,任意开设排雨水孔15) 通向排水管的截止阀处于常开等不安全状态16) 危化品罐区的可燃或腐蚀性物料出口管线,其支架未设置吊式压式弹簧补偿措施,或直接采用挠性连接短管17) 危化品罐区未设禁打手机、禁带火源、限高限速等各种警示牌18) 危险品罐区无泄漏、送料操作记录及日常巡查19) 拖拉机随意进入危险品罐区20) 危险品罐区周边有明火或山林火灾21) 危险品罐区操作室使用电炉、电茶壶、电热板等违章用电22) 槽车在装卸地点没有接地装置23) 没有防止操作人员从罐车上坠落的措施24) 未装配有效的阻火器和车况不合格(照明灯损坏或刹车失灵)槽车进入罐区25) 槽车贮罐的安全附件(压力表、温度计、安全阀)无检验日期或存在失效26) 槽车罐体未标明压力容器下次检验日期27) 罐体上无静电拖链、防毒器材或阀门泄漏28) 卸料前和卸料后接地未静置10分钟以上29) 槽车卸料时,司机、押运员离开卸料现场,没有现场监护人员30) 采用敞开式和喷溅式卸料31) 卸料时使贮罐超标准液位或满料溢出32) 氯乙烯槽车卸料时,软管或法兰处泄漏33) 氯乙烯运输送料时,满槽34) 槽车装量不满时多次在厂内运输和卸料35) 卸料车辆为熄火及手闸制动或卸料中途启动车辆36) 在高强闪电、雷击频繁时,从事卸料操作37) 油罐接地点没有2处38) 装卸汽油、甲苯时,操作人员未穿戴防静电工作服和防静电的鞋子39) 液氨等贮槽贮存区域未设置事故围堰和应急喷淋稀释设施40) 现场未设置应急喷淋和洗眼设施41) 没有防止物料错装措施如乙酸乙酯装入汽油槽罐42) 站在汽油桶上电焊43) 未经清洗,切割汽油桶或焊接贮槽44) 液氨、氯乙烯贮罐超装45) 槽车卸料时,堵塞消防通道及侵占通行道路46) 收料员离开卸料现场47) 装卸现场使用铁制、塑料等易产生火花的工具48) 由罐区送入车间的物料贮槽没有操作记录3. 冷凝器、再沸器1) 腐蚀、垫圈老化等引起泄漏2) 冷凝后物料温度过高3) 换热介质层被淤泥、微生物堵塞4) 高温表面没有防护5) 冷却高温液体(如150℃)时,冷却水进出阀未开,或冷却水量不够6) 蒸发器等在初次使用时,急速升温7) 换热器未考虑防震措施,使与其连接管道因震动造成松动泄漏4. 管道及管件1) 管道安装完毕,内部的焊渣、其他异物未清理2) 视镜玻璃不清洁或损坏3) 选用视筒材质耐压、耐温性能不妥,视筒安装不当4) 视筒破裂或长时间带压使用5) 防静电接地线损坏6) 管道、法兰或螺栓严重腐蚀、破裂7) 高温管道未保温8) 泄爆管制作成弯管9) 管道物料及流向标识不清10) 管道色标不清11) 调试时不同物料串接阀门未盲死12) 废弃管道未及时清理13) 管阀安装位置低,易撞头或操作困难14) 腐蚀性物料管线、法兰等易泄漏处未采取防护措施15) 存在水、氮气、空气、蒸汽等进入物料管线的可能16) 高温管道边放置易燃易爆物料的铁桶或塑料桶17) 管道或管件材料选材不合理,易腐蚀18) 玻璃管液位计没有防护措施19) 在可能爆炸的视镜玻璃处,未安装防护金属网20) 止回阀不能灵活动作或失效21) 电动阀停电、气动阀停气22) 使用氢气等压力管道没有定期维护保养或带病运行23) 使用压力管道时,操作人员未经培训或无证上岗24) 维护人员没有资质修理、改造压力管道25) 压力管道焊接质量低劣,有咬边、气孔、夹渣、未焊透等焊接缺陷26) 压力管道未按照规定设安全附件或安全附件超期未校验27) 压力管道未建立档案、操作规程28) 搪玻璃管道受钢管等撞击29) 生产工艺介质改变后仍使用现有管线阀门未考虑材料适应性30) 氮气管与空气管串接31) 盐水管与冷却水管串接5. 输送泵、真空泵1) 泵泄漏2) 异常噪声3) 联轴器没有防护罩4) 泵出口未装压力表或止回阀5) 长期停用时,未放净泵和管道中液体,造成腐蚀或冻结6) 容积泵在运行时,将出口阀关闭或未装安全回流阀7) 泵进口管径小或管路长或拐弯多8) 离心泵安装高度高于吸入高度9) 未使用防静电皮带6. 离心机1) 甩滤溶剂,未充氮气或氮气管道堵塞或现场无流量计可显示2) 精烘包内需用离心机甩滤溶剂时,未装测氧仪及报警装置3) 快速刹车或用辅助工具(如铁棒等)刹车4) 离心机未有效接地5) 防爆区内未使用防静电皮带6) 离心机运行时,震动异常7. 双锥(双锥回转真空干燥机)1) 无防护栏及安全连锁装置2) 人员爬入双锥内更换真空袋3) 传动皮带无防护4) 轴封泄漏5) 真空管路堵塞或使用时真空阀未开启8. 气瓶1) 气瓶没有配瓶帽、防震圈2) 氢气钢瓶夏季运输、存放时,没有遮阳措施,导致曝晒3) 部分气瓶超过年检期限4) 乙炔瓶与氧气瓶同时使用时,安全间距未超过五米5) 用带催化剂手套关氢气瓶阀6) 敲击碰撞气瓶7) 气瓶使用后,气压小于0.05Mpa8) 气瓶组及管路连接、阀门损坏9) 氢气瓶使用时,未采用防静电装置或已坏10) 气体钢瓶没有防倒措施11) 储存场所存在地沟、暗道12) 贮存场所不通风或通风不畅或有腐蚀性气体进入13) 缺灭火器材14) 乙炔气瓶放倒使用15) 气瓶颜色模糊不清二、电器仪表1. 防爆区内设置非防爆电器或控制柜非防爆2. 配电室窗户玻璃破损3. 配电室内杂物较多4. 配电室内有蒸汽水、物料管、粉尘、腐蚀性物质,致使电柜内的电气设备老化,导致短路事故5. 变压器室外有酸雾腐蚀或溶剂渗入或粉尘多6. 控制柜或变电柜后有衣服等杂物7. 配电柜过于陈旧,易产生短路8. 电缆靠近高温管道9. 架空电缆周边物料管道、污水管道等泄漏,使腐蚀性物料流入电缆桥架内10. 埋地电缆受到地下水腐蚀11. 电缆井、沟内污水严重渗入12. 电缆桥架严重腐蚀13. 电缆线保护套管老化断裂14. 铺设电气线路的电缆或钢管在穿过不同场所之间的墙或楼板处孔洞时,未采用非燃烧性材料严格堵塞15. 乱拉活动排风,导致电缆接头脱落、漏电16. 开关按钮对应设备位号标识不清17. 车间内有零乱不明电缆18. 应急照明灯未装或已坏19. 露天电动机无防护罩20. 操作现场照明度不够21. 设备与电气不配套(小牛拖大车、老牛拖大车)形成电气设备发热损坏、起火22. 电气设备、电缆桥架上冲水23. 防爆视镜灯、照明灯元宝螺丝松动,漏光三、静电24. 在易燃易爆场所,反应釜、管道、贮槽、冷凝器、输送泵、法兰、阀门未接地或接地不不良25. 在易燃易爆场所,投粉体料斗未接地,充氮气26. 超过安全流速(v2<0.64/d)输送汽油、甲苯、环己烷等液体27. 氢气流速总管超过12m/s,支管超过8m/s28. 将汽油等从高位喷入贮罐底或地面29. 在未充氮气时,异丙醇铝、镁粉等由敞口漏斗投入含汽油、甲苯等反应釜中30. 在易燃易爆场所,穿脱衣服、鞋帽及剧烈活动31. 在易燃易爆场所,用化纤材料的拖布或抹布擦洗设备或地面32. 向塑料桶中灌装汽油33. 用汽油等溶剂洗工作服或拖地或钢平台、地面34. 不锈钢、碳钢贮罐罐壁未用焊接钢筋或扁钢接地,超过50m2未有两处接地35. 存在散发易燃易爆气体的场所,未采用增湿等消除静电危害的措施36. 用塑料管吸料或装甲苯或回收甲苯37. 用压缩空气输送或搅拌汽油38. 防爆洁净区未使用防静电拖鞋39. 接地扁钢、屋顶防雷带生锈、腐蚀严重40. 高出屋面的金属设备未焊接钢筋并入避雷带四、生产现场41. 贮存原料或废料较多42. 现场跑、冒、滴、漏多43. 保温层损坏44. 缺有效防护栏45. 常闭式防火门常开46. 存有粉尘(镁粉、锌粉等)的操作岗位,未及时清理47. 金属钠、钠氢存放,没有防雨措施或废桶、废袋随意存放48. 消防通道堵塞或各种管线及其支架妨碍通行49. 灭火器缺少或已过期锈蚀或消防带、消防栓不符合消防要求50. 废料桶有多张标签51. 强氧化剂(双氧水、高锰酸钾等)堆放在木架上52. 钢平台晃动幅度过大53. 钢平台或钢柱腐蚀严重54. 局部区域溶剂浓度超标55. 高处阀门手柄、铁棒等易跌落56. 混凝土楼面震动大57. 室外钢棚或屋顶杂物多58. 防毒器材过期或失效59. 生产现场存放有非生产用具(食品、报纸、小说)60. 缺乏夏季的防暑降温设施61. 室外小管径水管冬季未保温62. 车间内没有紧急淋浴、洗眼等卫生设施或已损坏63. 车辆未装阻火器进入生产现场64. 易燃易爆场所没有安装可燃气体报警仪或失灵65. 反应釜、贮罐、泵等未标注设备位号和名称66. 大铁门没有固定插销,一旦风大就可能使铁门擦出火花,导致危险67. 库房门槛偏低,一旦发生意外,危险品将外溢68. 生产现场地面存放铁板、钢管五、人员、现场操作69. 没有岗位操作记录或操作记录不完整70. 吸料、灌装、搬运腐蚀性物品未戴防护用品71. 存在操作人员脱岗、离岗、睡岗等现象72. 粉体等投料岗位未戴防尘口罩73. 快速开关阀门74. 分层釜、槽底阀分层后未关75. 分层釜、槽分水阀开太大,造成水中夹油排入污水池或排水时间过长忘记关阀而跑料76. 高温釜、塔内放入空气77. 提取催化剂(如钯碳、活性镍等)现场散落较多78. 用铁棒捅管道、釜内堵塞的物料或使用不防爆器械产生火花79. 噪声环境未戴防耳器或耳塞80. 贮槽超压使用81. 使用汽油、甲苯等易燃易爆溶剂处,釜、槽未采用氮气置换82. 烟尘弥漫、通风不良或缺氧83. 带压开启反应釜盖84. 员工有职业禁忌或过敏症或接触毒物时间过长85. 紧急阀门或紧急开关不易操作86. 在易燃易爆场所,穿带钉子鞋或高跟鞋、凉鞋六、土建87. 可能发生火势蔓延的上下楼层管道井没有预防措施(如阻燃材料封堵)88. 有爆炸危险的工艺未采用防爆墙及轻质屋顶或未考虑足够的泄爆面89. 出入口和紧急通道设计数量不够或堵塞或无明显标志90. 厂房基础已受酸、碱类物质腐蚀,立柱、梁已受损严重91. 有大风时,钢窗玻璃易脱落92. 楼梯太窄或较陡93. 室内排水不畅或低洼处长期积水、积油94. 通道或作业处,头顶与顶棚没有足够的空间95. 在不明地下管线(水管、电缆等)情况下,随意开挖路面96. 使用大型机械在接近地下电缆、管道等附近挖土97. 在禁火区域内动火时,生产车间未派人监护98. 施工中出现异常情况(管道断裂、泄漏等),未立即停工进行应急处理99. 挖掘的沟、坑、池等和破坏的管道,未设置围栏和标志,夜间未设置照明100. 发现土壤有可能坍塌或滑动时,未停止作业101. 没有防止地下空罐、空池上浮的措施102. 在下罐、下池作业时,未办理相应审批手续或未遵照审批要求实施(如劳保用品、监护人落实等)防范措施未到位的情况下作业103. 在非土建作业时,未办理“非基建用工手续“或作业前不了解相应可能风险,在安全措施不到位情况下工七、生产检修104. 在容器内进行清扫和检修时,遇到危险情况,没有紧急逃出设施或措施105. 动火作业无监护人或监护人由新近员工担任或违章动火106. 超负荷吊装107. 工具或吊物未合理固定108. 未配备或未穿戴防护用品(安全帽、安全带等)109. 无警示标志或标志已模糊不清(如防止触电、防止坠物等)110. 检修时踏在悬空管路或小管径塑料管道和搪玻璃管道上或使用不安全登高设施111. 电焊机、手动电动工具等电缆破损引起漏电,零线破损或跨接112. 盲目进入污水池、深沟、深池作业113. 冬季管架结冰滑,无防滑措施114. 安装公司电焊工无电焊证或检修工未经过相关培训115. 直接站在石棉瓦、油毡等易碎材料的屋顶上作业116. 高处作业时,未采取防范措施进行交叉作业117. 高处作业时,电焊机的零线未接到所焊位置118. 有异味或可能产生有毒气体的区域作业未佩带防毒面具119. 高处补、挖墙洞时,未设安全围栏或安全网等120. 清理出的危险物料由高层向下层散落121. 用吊装机械载人122. 夜间作业无足够照明123. 遇有六级以上强风或其他恶劣天气时,仍在露天高空作业124. 釜内作业时,釜外无两人以上监护125. 釜内检修时,没有切断电源并挂“有人检修、禁止合闸”的牌子126. 进罐作业前,未对釜进行有效清洗127. 进罐作业前,未分析可燃气体浓度、氧含量、有毒气体(CO、H2S)浓度128. 进罐作业前,未对物料管线如原料、溶剂、蒸汽、水、氮气等管线可靠隔离129. 检修过程中,未对釜内定期取样分析130. 釜外明显位置未挂上“罐内有人”的牌子131. 进罐作业时,没有执行“双检制”132. 釜内照明不符合安全电压标准,干燥情况下电压大于24V,潮湿情况下电压大于12V 133. 检修完毕,未检查、清理杂物就开机使用134. 长时间在釜内作业未轮换135. 检修时,釜内缺必要的通风设施136. 在搪玻璃罐外壁表面或内壁施焊137. 进入搪玻璃釜、槽内未铺设软垫138. 快速升温或急速冷却搪玻璃釜139. 使用搪玻璃罐时,罐口或人孔螺栓、卡子掉入釜内140. 使用搪玻璃釜、不锈钢釜、碳钢釜时,酸液进入釜夹套141. 选用材料未经温度、PH、腐蚀溶解性审核,可能存有压力的场合未经受压专项审核142. 检修完毕,釜内、检修现场高低位等全部空间未经全面清场、复核,既开始试运行143. 检修完毕,相关事项未做全面沟通,变更未经确认审批,相关人员未全面培训并了解就接手144. 检修未经运行确认即投料生产八、生产工艺145. 存在突发反应,缺乏应对措施及培训146. 随意改变投料量或投料配比147. 改进工艺或新工艺,未进行安全评估148. 工艺变更未经过严格审订、批准149. 工艺过程在可燃气体爆炸极限内操作150. 使用高毒物料时,采用敞口操作151. 未编写工艺操作规程进行试生产152. 未编写所用物料的物性资料及安全使用注意事项153. 所用材料分解时,产生的热量未经详细核算154. 存在粉尘爆炸的潜在危险性155. 某种原辅料不能及时投入时,釜内物料暂存时存在危险156. 原料或中间体在贮存中会发生自燃或聚合或分解危险157. 工艺中各种参数(温度、压力等)接近危险界158. 发生异常状况时,没有将反应物迅速排放的措施159. 没有防止急剧反应和制止急剧反应的措施。
常见安全隐患300项
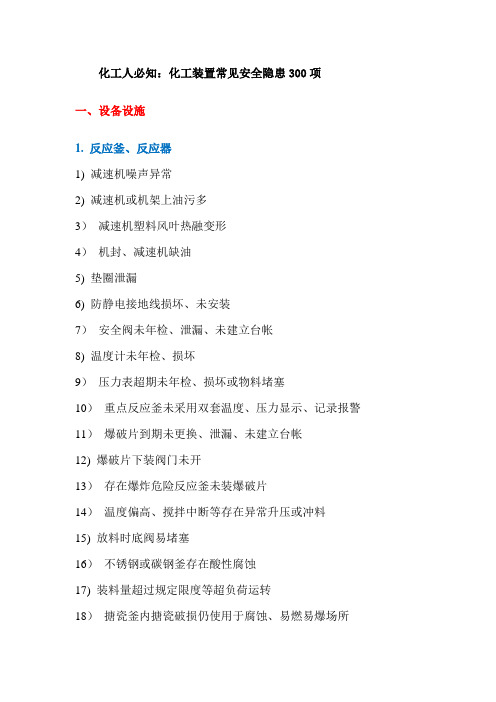
化工人必知:化工装置常见安全隐患300项一、设备设施1. 反应釜、反应器1) 减速机噪声异常2) 减速机或机架上油污多3)减速机塑料风叶热融变形4)机封、减速机缺油5) 垫圈泄漏6) 防静电接地线损坏、未安装7)安全阀未年检、泄漏、未建立台帐8) 温度计未年检、损坏9)压力表超期未年检、损坏或物料堵塞10)重点反应釜未采用双套温度、压力显示、记录报警11)爆破片到期未更换、泄漏、未建立台帐12) 爆破片下装阀门未开13)存在爆炸危险反应釜未装爆破片14)温度偏高、搅拌中断等存在异常升压或冲料15) 放料时底阀易堵塞16)不锈钢或碳钢釜存在酸性腐蚀17) 装料量超过规定限度等超负荷运转18)搪瓷釜内搪瓷破损仍使用于腐蚀、易燃易爆场所19) 反应釜内胆于夹套蒸汽进口处冲蚀破损20)压力容器超过使用年限、制造质量差,多次修理后仍泄漏21)压力容器没有铭牌22)缺位号标识或不清23) 对有爆炸敏感性的反应釜未能有效隔离24) 重要设备未制订安全检查表25) 重要设备缺备件或备机2。
贮槽、罐区、槽车1) 液位计模糊或损坏、堵塞2)静电接地线松动或未连接3) 法兰垫片处泄漏4) 小平台等高位贮槽未能有效固定5) 安全液封液位未达到要求6)常压贮槽带压使用7)装料量超过规定限度8) 非常温贮槽未装温度计9) 容器出现裂缝,仍在使用10)频繁受真空、氮气交变载荷使贮罐破损11)低沸点溶剂或液化气贮槽受阳光直射12)室外贮罐等存在运输车辆等撞击危险13)危险品罐区围堰孔洞未封堵14) 危化品罐区防护堤封堵不严密,任意开设排雨水孔15)通向排水管的截止阀处于常开等不安全状态16)危化品罐区的可燃或腐蚀性物料出口管线,其支架未设置吊式压式弹簧补偿措施,或直接采用挠性连接短管17)危化品罐区未设禁打手机、禁带火源、限高限速等各种警示牌18)危险品罐区无泄漏、送料操作记录及日常巡查19) 拖拉机随意进入危险品罐区20)危险品罐区周边有明火或山林火灾21) 危险品罐区操作室使用电炉、电茶壶、电热板等违章用电22)槽车在装卸地点没有接地装置23) 没有防止操作人员从罐车上坠落的措施24) 未装配有效的阻火器和车况不合格(照明灯损坏或刹车失灵)槽车进入罐区25) 槽车贮罐的安全附件(压力表、温度计、安全阀)无检验日期或存在失效26) 槽车罐体未标明压力容器下次检验日期27) 罐体上无静电拖链、防毒器材或阀门泄漏28) 卸料前和卸料后接地未静置10分钟以上29)槽车卸料时,司机、押运员离开卸料现场,没有现场监护人员30)采用敞开式和喷溅式卸料31)卸料时使贮罐超标准液位或满料溢出32)氯乙烯槽车卸料时,软管或法兰处泄漏33)氯乙烯运输送料时,满槽34) 槽车装量不满时多次在厂内运输和卸料35)卸料车辆为熄火及手闸制动或卸料中途启动车辆36)在高强闪电、雷击频繁时,从事卸料操作37)油罐接地点没有2处38) 装卸汽油、甲苯时,操作人员未穿戴防静电工作服和防静电的鞋子39) 液氨等贮槽贮存区域未设置事故围堰和应急喷淋稀释设施40)现场未设置应急喷淋和洗眼设施41)没有防止物料错装措施如乙酸乙酯装入汽油槽罐42)站在汽油桶上电焊43)未经清洗,切割汽油桶或焊接贮槽44)液氨、氯乙烯贮罐超装45)槽车卸料时,堵塞消防通道及侵占通行道路46)收料员离开卸料现场47) 装卸现场使用铁制、塑料等易产生火花的工具48)由罐区送入车间的物料贮槽没有操作记录3。
化工企业日常安全隐患项

化工行业常见安全生产隐患 300 项一、设备设施反应釜、反应器 减速机噪声异常 减速机或机架上油污多 减速机塑料风叶热融变形 机封、减速机缺油 垫圈泄漏 防静电接地线损坏、未安装7) 安全阀未年检、泄漏、未建立台帐 8) 温度计未年检、损坏9) 压力表超期未年检、损坏或物料堵塞10) 重点反应釜未采用双套温度、压力显示、记录报警11) 爆破片到期未更换、泄漏、未建立台帐12) 爆破片下装阀门未开13) 存在爆炸危险反应釜未装爆破片14)15)16)17)18)反应釜内胆于夹套蒸汽进口处冲蚀破损 压力容器超过使用年限、制造质量差,多次修理后仍泄漏 压力容器没有铭牌22) 缺位号标识或不清 23) 对有爆炸敏感性的反应釜未能有效隔离 24) 25) 2. 1) 2) 3) 4) 5) 6) 7)8)1. 1) 2)3) 4) 5) 6) 温度偏高、搅拌中断等存在异常升压或冲料 放料时底阀易堵塞 不锈钢或碳钢釜存在酸性腐蚀装料量超过规定限度等超负荷运转 搪瓷釜内搪瓷破损仍使用于腐蚀、易燃易爆场所19) 20) 21)重要设备未制订安全检查表 重要设备缺备件或备机 贮槽、罐区、槽车 液位计模糊或损坏、堵塞 静电接地线松动或未连接 法兰垫片处泄漏 小平台等高位贮槽未能有效固定 安全液封液位未达到要求 常压贮槽带压使用装料量超过规定限度 非常温贮槽未装温度计14)15) 通向排水管的截止阀处于常开等不安全状态16)危化品罐区的可燃或腐蚀性物料出口管线,其支架未设置吊式压式弹簧补偿措施,或 直接采用挠性连接短管17)18)19)20)21)22)23)24)25)26) 9) 容器出现裂缝,仍在使用10) 频繁受真空、氮气交变载荷使贮罐破损11) 低沸点溶剂或液化气贮槽受阳光直射12) 室外贮罐等存在运输车辆等撞击危险13) 危险品罐区围堰孔洞未封堵危化品罐区防护堤封堵不严密,任意开设排雨水孔危化品罐区未设禁打手机、禁带火源、限高限速等各种警示牌 危险品罐区无泄漏、送料操作记录及日常巡查 拖拉机随意进入危险品罐区 危险品罐区周边有明火或山林火灾 危险品罐区操作室使用电炉、电茶壶、电热板等违章用电 槽车在装卸地点没有接地装置 没有防止操作人员从罐车上坠落的措施 未装配有效的阻火器和车况不合格(照明灯损坏或刹车失灵)槽车进入罐区 槽车贮罐的安全附件(压力表、温度计、安全阀)无检验日期或存在失效 槽车罐体未标明压力容器下次检验日期 罐体上无静电拖链、防毒器材或阀门泄漏 卸料前和卸料后接地未静置 10 分钟以上 槽车卸料时,司机、押运员离开卸料现场,没有现场监护人员 采用敞开式和喷溅式卸料 卸料时使贮罐超标准液位或满料溢出 氯乙烯槽车卸料时,软管或法兰处泄漏 氯乙烯运输送料时,满槽 槽车装量不满时多次在厂内运输和卸料 卸料车辆为熄火及手闸制动或卸料中途启动车辆 在高强闪电、雷击频繁时,从事卸料操作 油罐接地点没有 2 处 装卸汽油、甲苯时,操作人员未穿戴防静电工作服和防静电的鞋子 液氨等贮槽贮存区域未设置事故围堰和应急喷淋稀释设施 现场未设置应急喷淋和洗眼设施 没有防止物料错装措施如乙酸乙酯装入汽油槽罐 站在汽油桶上电焊 未经清洗,切割汽油桶或焊接贮槽 液氨、氯乙烯贮罐超装 槽车卸料时,堵塞消防通道及侵占通行道路 收料员离开卸料现场 装卸现场使用铁制、塑料等易产生火花的工具 由罐区送入车间的物料贮槽没有操作记录 冷凝器、再沸器 腐蚀、垫圈老化等引起泄漏 冷凝后物料温度过高27)28)29)30)31)32)33)34)35)36)37)38)39)40)41)42)43)44)45)46)47)48) 3.1)2)换热介质层被淤泥、微生物堵塞 高温表面没有防护冷却高温液体(如150 C )时,冷却水进出阀未开,或冷却水量不够 蒸发器等在初次使用时,急速升温 换热器未考虑防震措施,使与其连接管道因震动造成松动泄漏 管道及管件管道安装完毕,内部的焊渣、其他异物未清理 视镜玻璃不清洁或损坏 选用视筒材质耐压、耐温性能不妥,视筒安装不当 视筒破裂或长时间带压使用防静电接地线损坏 管道、法兰或螺栓严重腐蚀、破裂高温管道未保温 泄爆管制作成弯管 管道物料及流向标识不清 管道色标不清 调试时不同物料串接阀门未盲死 废弃管道未及时清理 管阀安装位置低,易撞头或操作困难 腐蚀性物料管线、法兰等易泄漏处未采取防护措施 存在水、氮气、空气、蒸汽等进入物料管线的可能 高温管道边放置易燃易爆物料的铁桶或塑料桶 管道或管件材料选材不合理,易腐蚀 玻璃管液位计没有防护措施 在可能爆炸的视镜玻璃处,未安装防护金属网 止回阀不能灵活动作或失效 电动阀停电、气动阀停气 使用氢气等压力管道没有定期维护保养或带病运行 使用压力管道时,操作人员未经培训或无证上岗 维护人员没有资质修理、改造压力管道 压力管道焊接质量低劣,有咬边、气孔、夹渣、未焊透等焊接缺陷 压力管道未按照规定设安全附件或安全附件超期未校验 压力管道未建立档案、操作规程 搪玻璃管道受钢管等撞击 生产工艺介质改变后仍使用现有管线阀门未考虑材料适应性 氮气管与空气管串接 盐水管与冷却水管串接输送泵、真空泵 泵泄漏 异常噪声 联轴器没有防护罩 泵出口未装压力表或止回阀 长期停用时,未放净泵和管道中液体,造成腐蚀或冻结 容积泵在运行时,将出口阀关闭或未装安全回流阀3) 4) 5) 6) 7) 4. 1) 2) 3) 4) 5) 6) 7) 8)9)10)11)12)13) 14) 15) 16) 17)18)19)20)21)22)23)24)25)26)27)28)29)30)31)5.1)2)3)4)5)6)泵进口管径小或管路长或拐弯多 离心泵安装高度高于吸入高度 未使用防静电皮带 离心机 甩滤溶剂,未充氮气或氮气管道堵塞或现场无流量计可显示 精烘包内需用离心机甩滤溶剂时,未装测氧仪及报警装置 快速刹车或用辅助工具(如铁棒等)刹车 离心机未有效接地防爆区内未使用防静电皮带 离心机运行时,震动异常 双锥(双锥回转真空干燥机) 无防护栏及安全连锁装置 人员爬入双锥内更换真空袋 传动皮带无防护 轴封泄漏 真空管路堵塞或使用时真空阀未开启 气瓶气瓶没有配瓶帽、防震圈 氢气钢瓶夏季运输、存放时,没有遮阳措施,导致曝晒 部分气瓶超过年检期限 乙炔瓶与氧气瓶同时使用时,安全间距未超过五米 用带催化剂手套关氢气瓶阀敲击碰撞气瓶 气瓶使用后,气压小于 0.05Mpa 气瓶组及管路连接、阀门损坏 氢气瓶使用时,未采用防静电装置或已坏 气体钢瓶没有防倒措施 储存场所存在地沟、暗道 贮存场所不通风或通风不畅或有腐蚀性气体进入 缺灭火器材14) 乙炔气瓶放倒使用 15) 气瓶颜色模糊不清二、电器仪表7) 8) 9) 6. 1) 2) 3) 4)5)6)7. 1) 2) 3)4)5)8. 1)2)3)4)5)6)7)8)9)10)11)12)13) 1. 防爆区内设置非防爆电器或控制柜非防爆2. 配电室窗户玻璃破损3. 配电室内杂物较多4. 配电室内有蒸汽水、物料管、粉尘、腐蚀性物质,致使电柜内的电气设备老化,导致短 路事故5. 变压器室外有酸雾腐蚀或溶剂渗入或粉尘多6. 控制柜或变电柜后有衣服等杂物7. 配电柜过于陈旧,易产生短路8. 电缆靠近高温管道9. 架空电缆周边物料管道、污水管道等泄漏,使腐蚀性物料流入电缆桥架内 埋地电缆受到地下水腐蚀电缆井、沟内污水严重渗入 19.露天电动机无防护罩三、静电24. 在易易爆场所反应釜 管道贮槽冷凝器输送泵法兰阀门未接地或接不不良25. 在易燃易爆场所,投粉体料斗未接地,充氮气26.超过安全流速(v2v0.64/d )输送汽油、甲苯、环己烷等液体27. 氢气流速总管超过12m/s ,支管超过8m/s28. 将汽油等从高位喷入贮罐底或地面在未充氮气时,异丙醇铝、镁粉等由敞口漏斗投入含汽油、甲苯等反应釜中在易燃易爆场所,用化纤材料的拖布或抹布擦洗设备或地面10. 11.12. 电缆桥架严重腐蚀13.14.15.16.17.18.电缆线保护套管老化断裂 铺设电气线路的电缆或钢管在穿过不同场所之间的墙或楼板处孔洞时, 乱拉活动排风,导致电缆接头脱落、漏电 开关按钮对应设备位号标识不清 车间内有零乱不明电缆 应急照明灯未装或已坏 未采用非燃烧性材料严格堵塞20. 21. 22. 操作现场照明度不够 设备与电气不配套(小牛拖大车、老牛拖大车)形成电气设备发热损坏、起火电气设备、电缆桥架上冲水23. 防爆视镜灯、照明灯元宝螺丝松动,漏光29. 30. 在易燃易爆场所,穿脱衣服、鞋帽及剧烈活动31.32.向塑料桶中灌装汽油33.用汽油等溶剂洗工作服或拖地或钢平台、地面34.不锈钢、碳钢贮罐罐壁未用焊接钢筋或扁钢接地,超过50m2未有两处接地35.存在散发易燃易爆气体的场所,未采用增湿等消除静电危害的措施36.用塑料管吸料或装甲苯或回收甲苯37.用压缩空气输送或搅拌汽油38.防爆洁净区未使用防静电拖鞋39.接地扁钢、屋顶防雷带生锈、腐蚀严重40.高出屋面的金属设备未焊接钢筋并入避雷带四、生产现场41.贮存原料或废料较多42.现场跑、冒、滴、漏多43.保温层损坏44.缺有效防护栏45.常闭式防火门常开46.存有粉尘(镁粉、锌粉等)的操作岗位,未及时清理47.金属钠、钠氢存放,没有防雨措施或废桶、废袋随意存放48.消防通道堵塞或各种管线及其支架妨碍通行49.灭火器缺少或已过期锈蚀或消防带、消防栓不符合消防要求50.废料桶有多张标签51.强氧化剂(双氧水、高锰酸钾等)堆放在木架上52.钢平台晃动幅度过大53.钢平台或钢柱腐蚀严重54.局部区域溶剂浓度超标55.高处阀门手柄、铁棒等易跌落56.混凝土楼面震动大57.室外钢棚或屋顶杂物多58.防毒器材过期或失效59.生产现场存放有非生产用具(食品、报纸、小说)60.缺乏夏季的防暑降温设施61.室外小管径水管冬季未保温62.车间内没有紧急淋浴、洗眼等卫生设施或已损坏63.车辆未装阻火器进入生产现场64.易燃易爆场所没有安装可燃气体报警仪或失灵65.反应釜、贮罐、泵等未标注设备位号和名称66.大铁门没有固定插销,一旦风大就可能使铁门擦出火花,导致危险67.库房门槛偏低,一旦发生意外,危险品将外溢68.生产现场地面存放铁板、钢管五、人员、现场操作69.没有岗位操作记录或操作记录不完整70.吸料、灌装、搬运腐蚀性物品未戴防护用品71.存在操作人员脱岗、离岗、睡岗等现象72.粉体等投料岗位未戴防尘口罩73.快速开关阀门74.分层釜、槽底阀分层后未关75.分层釜、槽分水阀开太大,造成水中夹油排入污水池或排水时间过长忘记关阀而跑料76.高温釜、塔内放入空气77.提取催化剂(如钯碳、活性镍等)现场散落较多78.用铁棒捅管道、釜内堵塞的物料或使用不防爆器械产生火花79.噪声环境未戴防耳器或耳塞80.贮槽超压使用81.使用汽油、甲苯等易燃易爆溶剂处,釜、槽未采用氮气置换82.烟尘弥漫、通风不良或缺氧83.带压开启反应釜盖84.员工有职业禁忌或过敏症或接触毒物时间过长85.紧急阀门或紧急开关不易操作86.在易燃易爆场所,穿带钉子鞋或高跟鞋、凉鞋六、土建87.可能发生火势蔓延的上下楼层管道井没有预防措施(如阻燃材料封堵)88.有爆炸危险的工艺未采用防爆墙及轻质屋顶或未考虑足够的泄爆面89.出入口和紧急通道设计数量不够或堵塞或无明显标志90.厂房基础已受酸、碱类物质腐蚀,立柱、梁已受损严重91.有大风时,钢窗玻璃易脱落92.楼梯太窄或较陡93.室内排水不畅或低洼处长期积水、积油94.通道或作业处,头顶与顶棚没有足够的空间95.在不明地下管线(水管、电缆等)情况下,随意开挖路面96.使用大型机械在接近地下电缆、管道等附近挖土97.在禁火区域内动火时,生产车间未派人监护98.施工中出现异常情况(管道断裂、泄漏等),未立即停工进行应急处理99.挖掘的沟、坑、池等和破坏的管道,未设置围栏和标志,夜间未设置照明100.发现土壤有可能坍塌或滑动时,未停止作业101.没有防止地下空罐、空池上浮的措施102.在下罐、下池作业时,未办理相应审批手续或未遵照审批要求实施(如劳保用品、监护人落实等)防范措施未到位的情况下作业103.在非土建作业时,未办理非基建用工手续或作业前不了解相应可能风险,在安全措施不到位情况下工七、生产检修104.在容器内进行清扫和检修时,遇到危险情况,没有紧急逃出设施或措施105.动火作业无监护人或监护人由新近员工担任或违章动火106.超负荷吊装107.工具或吊物未合理固定108.未配备或未穿戴防护用品(安全帽、安全带等)109.无警示标志或标志已模糊不清(如防止触电、防止坠物等)110.检修时踏在悬空管路或小管径塑料管道和搪玻璃管道上或使用不安全登高设施111.电焊机、手动电动工具等电缆破损引起漏电,零线破损或跨接112.盲目进入污水池、深沟、深池作业113.冬季管架结冰滑,无防滑措施114.安装公司电焊工无电焊证或检修工未经过相关培训115.直接站在石棉瓦、油毡等易碎材料的屋顶上作业116.高处作业时,未采取防范措施进行交叉作业117.高处作业时,电焊机的零线未接到所焊位置118.有异味或可能产生有毒气体的区域作业未佩带防毒面具119.高处补、挖墙洞时,未设安全围栏或安全网等120.清理出的危险物料由高层向下层散落121.用吊装机械载人122.夜间作业无足够照明123. 遇有六级以上强风或其他恶劣天气时,仍在露天高空作业124. 釜内作业时,釜外无两人以上监护125.釜内检修时,没有切断电源并挂 有人检修、禁止合闸”的牌子 126.进罐作业前,未对釜进行有效清洗127.进罐作业前,未分析可燃气体浓度、氧含量、有毒气体( CO 、H2S )浓度进罐作业前,未对物料管线如原料、溶剂、蒸汽、水、氮气等管线可靠隔离132.釜内照明不符合安全电压标准,干燥情况下电压大于 24V,潮湿情况下电压大于12V 133. 检修完毕,未检查、清理杂物就开机使用134. 长时间在釜内作业未轮换135. 检修时,釜内缺必要的通风设施136. 在搪玻璃罐外壁表面或内壁施焊137. 进入搪玻璃釜、槽内未铺设软垫138. 快速升温或急速冷却搪玻璃釜139. 使用搪玻璃罐时,罐口或人孔螺栓、卡子掉入釜内140. 使用搪玻璃釜、不锈钢釜、碳钢釜时,酸液进入釜夹套141. 选用材料未经温度、PH 、腐蚀溶解性审核,可能存有压力的场合未经受压专项审核 142. 检修完毕,釜内、检修现场高低位等全部空间未经全面清场、复核,既开始试运行 143. 检修完毕,相关事项未做全面沟通,变更未经确认审批,相关人员未全面培训并了解就接手 144. 检修未经运行确认即投料生产八、生产工艺145. 存在突发反应,缺乏应对措施及培训129. 检修过程中,未对釜内定期取样分析 130. 釜外明显位置未挂上 罐内有人”的牌子 131. 进罐作业时,没有执行双检制”128.146.随意改变投料量或投料配比147.改进工艺或新工艺,未进行安全评估148.工艺变更未经过严格审订、批准149.工艺过程在可燃气体爆炸极限内操作150.使用高毒物料时,采用敞口操作151.未编写工艺操作规程进行试生产152.未编写所用物料的物性资料及安全使用注意事项153.所用材料分解时,产生的热量未经详细核算154.存在粉尘爆炸的潜在危险性155.某种原辅料不能及时投入时,釜内物料暂存时存在危险156.原料或中间体在贮存中会发生自燃或聚合或分解危险157.工艺中各种参数(温度、压力等)接近危险界158.发生异常状况时,没有将反应物迅速排放的措施159.没有防止急剧反应和制止急剧反应的措施。
常见安全隐患300项
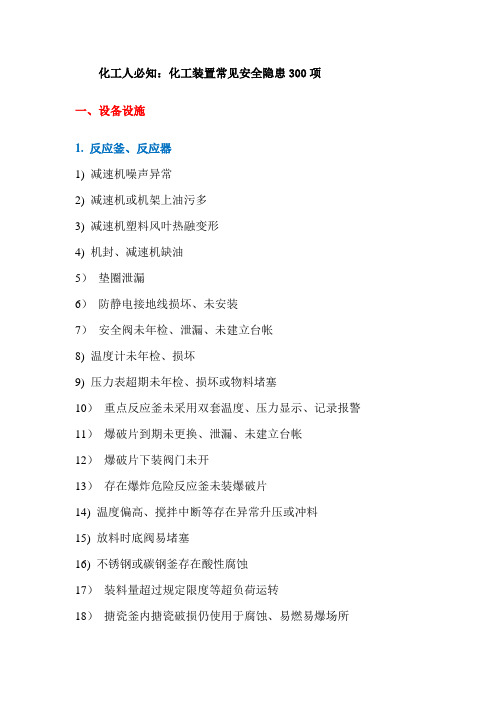
化工人必知:化工装置常见安全隐患300项一、设备设施1. 反应釜、反应器1) 减速机噪声异常2) 减速机或机架上油污多3) 减速机塑料风叶热融变形4) 机封、减速机缺油5)垫圈泄漏6)防静电接地线损坏、未安装7)安全阀未年检、泄漏、未建立台帐8) 温度计未年检、损坏9) 压力表超期未年检、损坏或物料堵塞10)重点反应釜未采用双套温度、压力显示、记录报警11)爆破片到期未更换、泄漏、未建立台帐12)爆破片下装阀门未开13)存在爆炸危险反应釜未装爆破片14) 温度偏高、搅拌中断等存在异常升压或冲料15) 放料时底阀易堵塞16) 不锈钢或碳钢釜存在酸性腐蚀17)装料量超过规定限度等超负荷运转18)搪瓷釜内搪瓷破损仍使用于腐蚀、易燃易爆场所19) 反应釜内胆于夹套蒸汽进口处冲蚀破损20)压力容器超过使用年限、制造质量差,多次修理后仍泄漏21)压力容器没有铭牌22)缺位号标识或不清23) 对有爆炸敏感性的反应釜未能有效隔离24)重要设备未制订安全检查表25)重要设备缺备件或备机2. 贮槽、罐区、槽车1)液位计模糊或损坏、堵塞2) 静电接地线松动或未连接3)法兰垫片处泄漏4) 小平台等高位贮槽未能有效固定5) 安全液封液位未达到要求6)常压贮槽带压使用7) 装料量超过规定限度8) 非常温贮槽未装温度计9)容器出现裂缝,仍在使用10)频繁受真空、氮气交变载荷使贮罐破损11)低沸点溶剂或液化气贮槽受阳光直射12)室外贮罐等存在运输车辆等撞击危险13)危险品罐区围堰孔洞未封堵14)危化品罐区防护堤封堵不严密,任意开设排雨水孔15)通向排水管的截止阀处于常开等不安全状态16)危化品罐区的可燃或腐蚀性物料出口管线,其支架未设置吊式压式弹簧补偿措施,或直接采用挠性连接短管17) 危化品罐区未设禁打手机、禁带火源、限高限速等各种警示牌18)危险品罐区无泄漏、送料操作记录及日常巡查19) 拖拉机随意进入危险品罐区20) 危险品罐区周边有明火或山林火灾21)危险品罐区操作室使用电炉、电茶壶、电热板等违章用电22) 槽车在装卸地点没有接地装置23) 没有防止操作人员从罐车上坠落的措施24)未装配有效的阻火器和车况不合格(照明灯损坏或刹车失灵)槽车进入罐区25)槽车贮罐的安全附件(压力表、温度计、安全阀)无检验日期或存在失效26)槽车罐体未标明压力容器下次检验日期27) 罐体上无静电拖链、防毒器材或阀门泄漏28) 卸料前和卸料后接地未静置10分钟以上29) 槽车卸料时,司机、押运员离开卸料现场,没有现场监护人员30)采用敞开式和喷溅式卸料31)卸料时使贮罐超标准液位或满料溢出32) 氯乙烯槽车卸料时,软管或法兰处泄漏33) 氯乙烯运输送料时,满槽34) 槽车装量不满时多次在厂内运输和卸料35)卸料车辆为熄火及手闸制动或卸料中途启动车辆36) 在高强闪电、雷击频繁时,从事卸料操作37)油罐接地点没有2处38) 装卸汽油、甲苯时,操作人员未穿戴防静电工作服和防静电的鞋子39) 液氨等贮槽贮存区域未设置事故围堰和应急喷淋稀释设施40) 现场未设置应急喷淋和洗眼设施41) 没有防止物料错装措施如乙酸乙酯装入汽油槽罐42) 站在汽油桶上电焊43)未经清洗,切割汽油桶或焊接贮槽44) 液氨、氯乙烯贮罐超装45) 槽车卸料时,堵塞消防通道及侵占通行道路46) 收料员离开卸料现场47) 装卸现场使用铁制、塑料等易产生火花的工具48) 由罐区送入车间的物料贮槽没有操作记录3. 冷凝器、再沸器1) 腐蚀、垫圈老化等引起泄漏2)冷凝后物料温度过高3) 换热介质层被淤泥、微生物堵塞4)高温表面没有防护5) 冷却高温液体(如150℃)时,冷却水进出阀未开,或冷却水量不够6) 蒸发器等在初次使用时,急速升温7)换热器未考虑防震措施,使与其连接管道因震动造成松动泄漏4. 管道及管件1)管道安装完毕,内部的焊渣、其他异物未清理2) 视镜玻璃不清洁或损坏3) 选用视筒材质耐压、耐温性能不妥,视筒安装不当4) 视筒破裂或长时间带压使用5)防静电接地线损坏6)管道、法兰或螺栓严重腐蚀、破裂7)高温管道未保温8)泄爆管制作成弯管9) 管道物料及流向标识不清10)管道色标不清11)调试时不同物料串接阀门未盲死12)废弃管道未及时清理13)管阀安装位置低,易撞头或操作困难14)腐蚀性物料管线、法兰等易泄漏处未采取防护措施15)存在水、氮气、空气、蒸汽等进入物料管线的可能16)高温管道边放置易燃易爆物料的铁桶或塑料桶17)管道或管件材料选材不合理,易腐蚀18)玻璃管液位计没有防护措施19)在可能爆炸的视镜玻璃处,未安装防护金属网20)止回阀不能灵活动作或失效21)电动阀停电、气动阀停气22)使用氢气等压力管道没有定期维护保养或带病运行23) 使用压力管道时,操作人员未经培训或无证上岗24) 维护人员没有资质修理、改造压力管道25)压力管道焊接质量低劣,有咬边、气孔、夹渣、未焊透等焊接缺陷26)压力管道未按照规定设安全附件或安全附件超期未校验27) 压力管道未建立档案、操作规程28) 搪玻璃管道受钢管等撞击29)生产工艺介质改变后仍使用现有管线阀门未考虑材料适应性30) 氮气管与空气管串接31)盐水管与冷却水管串接5. 输送泵、真空泵1) 泵泄漏2)异常噪声3)联轴器没有防护罩4) 泵出口未装压力表或止回阀5)长期停用时,未放净泵和管道中液体,造成腐蚀或冻结6) 容积泵在运行时,将出口阀关闭或未装安全回流阀7)泵进口管径小或管路长或拐弯多8) 离心泵安装高度高于吸入高度9)未使用防静电皮带6. 离心机1)甩滤溶剂,未充氮气或氮气管道堵塞或现场无流量计可显示2) 精烘包内需用离心机甩滤溶剂时,未装测氧仪及报警装置3)快速刹车或用辅助工具(如铁棒等)刹车4)离心机未有效接地5)防爆区内未使用防静电皮带6)离心机运行时,震动异常7。
化工企业日常安全隐患300项

化工行业常见安全生产隐患300项一、设备设施1. 反应釜、反应器1) 减速机噪声异常2) 减速机或机架上油污多3) 减速机塑料风叶热融变形4) 机封、减速机缺油5) 垫圈泄漏6) 防静电接地线损坏、未安装7) 安全阀未年检、泄漏、未建立台帐8) 温度计未年检、损坏9) 压力表超期未年检、损坏或物料堵塞10) 重点反应釜未采用双套温度、压力显示、记录报警11) 爆破片到期未更换、泄漏、未建立台帐12) 爆破片下装阀门未开13) 存在爆炸危险反应釜未装爆破片14) 温度偏高、搅拌中断等存在异常升压或冲料15) 放料时底阀易堵塞16) 不锈钢或碳钢釜存在酸性腐蚀17) 装料量超过规定限度等超负荷运转18) 搪瓷釜内搪瓷破损仍使用于腐蚀、易燃易爆场所19) 反应釜内胆于夹套蒸汽进口处冲蚀破损20) 压力容器超过使用年限、制造质量差,多次修理后仍泄漏21) 压力容器没有铭牌22) 缺位号标识或不清23) 对有爆炸敏感性的反应釜未能有效隔离24) 重要设备未制订安全检查表25) 重要设备缺备件或备机2. 贮槽、罐区、槽车1) 液位计模糊或损坏、堵塞2) 静电接地线松动或未连接3) 法兰垫片处泄漏4) 小平台等高位贮槽未能有效固定5) 安全液封液位未达到要求6) 常压贮槽带压使用7) 装料量超过规定限度8) 非常温贮槽未装温度计9) 容器出现裂缝,仍在使用10) 频繁受真空、氮气交变载荷使贮罐破损11) 低沸点溶剂或液化气贮槽受阳光直射12) 室外贮罐等存在运输车辆等撞击危险13) 危险品罐区围堰孔洞未封堵14) 危化品罐区防护堤封堵不严密,任意开设排雨水孔15) 通向排水管的截止阀处于常开等不安全状态16) 危化品罐区的可燃或腐蚀性物料出口管线,其支架未设置吊式压式弹簧补偿措施,或直接采用挠性连接短管17) 危化品罐区未设禁打手机、禁带火源、限高限速等各种警示牌18) 危险品罐区无泄漏、送料操作记录及日常巡查19) 拖拉机随意进入危险品罐区20) 危险品罐区周边有明火或山林火灾21) 危险品罐区操作室使用电炉、电茶壶、电热板等违章用电22) 槽车在装卸地点没有接地装置23) 没有防止操作人员从罐车上坠落的措施24) 未装配有效的阻火器和车况不合格(照明灯损坏或刹车失灵)槽车进入罐区25) 槽车贮罐的安全附件(压力表、温度计、安全阀)无检验日期或存在失效26) 槽车罐体未标明压力容器下次检验日期27) 罐体上无静电拖链、防毒器材或阀门泄漏28) 卸料前和卸料后接地未静置10分钟以上29) 槽车卸料时,司机、押运员离开卸料现场,没有现场监护人员30) 采用敞开式和喷溅式卸料31) 卸料时使贮罐超标准液位或满料溢出32) 氯乙烯槽车卸料时,软管或法兰处泄漏33) 氯乙烯运输送料时,满槽34) 槽车装量不满时多次在厂内运输和卸料35) 卸料车辆为熄火及手闸制动或卸料中途启动车辆36) 在高强闪电、雷击频繁时,从事卸料操作37) 油罐接地点没有2处38) 装卸汽油、甲苯时,操作人员未穿戴防静电工作服和防静电的鞋子39) 液氨等贮槽贮存区域未设置事故围堰和应急喷淋稀释设施40) 现场未设置应急喷淋和洗眼设施41) 没有防止物料错装措施如乙酸乙酯装入汽油槽罐42) 站在汽油桶上电焊43) 未经清洗,切割汽油桶或焊接贮槽44) 液氨、氯乙烯贮罐超装45) 槽车卸料时,堵塞消防通道及侵占通行道路46) 收料员离开卸料现场47) 装卸现场使用铁制、塑料等易产生火花的工具48) 由罐区送入车间的物料贮槽没有操作记录3. 冷凝器、再沸器1) 腐蚀、垫圈老化等引起泄漏2) 冷凝后物料温度过高3) 换热介质层被淤泥、微生物堵塞4) 高温表面没有防护5) 冷却高温液体(如150℃)时,冷却水进出阀未开,或冷却水量不够6) 蒸发器等在初次使用时,急速升温7) 换热器未考虑防震措施,使与其连接管道因震动造成松动泄漏4. 管道及管件1) 管道安装完毕,内部的焊渣、其他异物未清理2) 视镜玻璃不清洁或损坏3) 选用视筒材质耐压、耐温性能不妥,视筒安装不当4) 视筒破裂或长时间带压使用5) 防静电接地线损坏6) 管道、法兰或螺栓严重腐蚀、破裂7) 高温管道未保温8) 泄爆管制作成弯管9) 管道物料及流向标识不清10) 管道色标不清11) 调试时不同物料串接阀门未盲死12) 废弃管道未及时清理13) 管阀安装位置低,易撞头或操作困难14) 腐蚀性物料管线、法兰等易泄漏处未采取防护措施15) 存在水、氮气、空气、蒸汽等进入物料管线的可能16) 高温管道边放置易燃易爆物料的铁桶或塑料桶17) 管道或管件材料选材不合理,易腐蚀18) 玻璃管液位计没有防护措施19) 在可能爆炸的视镜玻璃处,未安装防护金属网20) 止回阀不能灵活动作或失效21) 电动阀停电、气动阀停气22) 使用氢气等压力管道没有定期维护保养或带病运行23) 使用压力管道时,操作人员未经培训或无证上岗24) 维护人员没有资质修理、改造压力管道25) 压力管道焊接质量低劣,有咬边、气孔、夹渣、未焊透等焊接缺陷26) 压力管道未按照规定设安全附件或安全附件超期未校验27) 压力管道未建立档案、操作规程28) 搪玻璃管道受钢管等撞击29) 生产工艺介质改变后仍使用现有管线阀门未考虑材料适应性30) 氮气管与空气管串接31) 盐水管与冷却水管串接5. 输送泵、真空泵1) 泵泄漏2) 异常噪声3) 联轴器没有防护罩4) 泵出口未装压力表或止回阀5) 长期停用时,未放净泵和管道中液体,造成腐蚀或冻结6) 容积泵在运行时,将出口阀关闭或未装安全回流阀7) 泵进口管径小或管路长或拐弯多8) 离心泵安装高度高于吸入高度9) 未使用防静电皮带6. 离心机1) 甩滤溶剂,未充氮气或氮气管道堵塞或现场无流量计可显示2) 精烘包内需用离心机甩滤溶剂时,未装测氧仪及报警装置3) 快速刹车或用辅助工具(如铁棒等)刹车4) 离心机未有效接地5) 防爆区内未使用防静电皮带6) 离心机运行时,震动异常7. 双锥(双锥回转真空干燥机)1) 无防护栏及安全连锁装置2) 人员爬入双锥内更换真空袋3) 传动皮带无防护4) 轴封泄漏5) 真空管路堵塞或使用时真空阀未开启8. 气瓶1) 气瓶没有配瓶帽、防震圈2) 氢气钢瓶夏季运输、存放时,没有遮阳措施,导致曝晒3) 部分气瓶超过年检期限4) 乙炔瓶与氧气瓶同时使用时,安全间距未超过五米5) 用带催化剂手套关氢气瓶阀6) 敲击碰撞气瓶7) 气瓶使用后,气压小于0.05Mpa8) 气瓶组及管路连接、阀门损坏9) 氢气瓶使用时,未采用防静电装置或已坏10) 气体钢瓶没有防倒措施11) 储存场所存在地沟、暗道12) 贮存场所不通风或通风不畅或有腐蚀性气体进入13) 缺灭火器材14) 乙炔气瓶放倒使用15) 气瓶颜色模糊不清二、电器仪表1. 防爆区内设置非防爆电器或控制柜非防爆2. 配电室窗户玻璃破损3. 配电室内杂物较多4. 配电室内有蒸汽水、物料管、粉尘、腐蚀性物质,致使电柜内的电气设备老化,导致短路事故5. 变压器室外有酸雾腐蚀或溶剂渗入或粉尘多6. 控制柜或变电柜后有衣服等杂物7. 配电柜过于陈旧,易产生短路8. 电缆靠近高温管道9. 架空电缆周边物料管道、污水管道等泄漏,使腐蚀性物料流入电缆桥架内10. 埋地电缆受到地下水腐蚀11. 电缆井、沟内污水严重渗入12. 电缆桥架严重腐蚀13. 电缆线保护套管老化断裂14. 铺设电气线路的电缆或钢管在穿过不同场所之间的墙或楼板处孔洞时,未采用非燃烧性材料严格堵塞15. 乱拉活动排风,导致电缆接头脱落、漏电16. 开关按钮对应设备位号标识不清17. 车间内有零乱不明电缆18. 应急照明灯未装或已坏19. 露天电动机无防护罩20. 操作现场照明度不够21. 设备与电气不配套(小牛拖大车、老牛拖大车)形成电气设备发热损坏、起火22. 电气设备、电缆桥架上冲水23. 防爆视镜灯、照明灯元宝螺丝松动,漏光三、静电24. 在易燃易爆场所,反应釜、管道、贮槽、冷凝器、输送泵、法兰、阀门未接地或接地不不良25. 在易燃易爆场所,投粉体料斗未接地,充氮气26. 超过安全流速(v2<0.64/d)输送汽油、甲苯、环己烷等液体27. 氢气流速总管超过12m/s,支管超过8m/s28. 将汽油等从高位喷入贮罐底或地面29. 在未充氮气时,异丙醇铝、镁粉等由敞口漏斗投入含汽油、甲苯等反应釜中30. 在易燃易爆场所,穿脱衣服、鞋帽及剧烈活动31. 在易燃易爆场所,用化纤材料的拖布或抹布擦洗设备或地面32. 向塑料桶中灌装汽油33. 用汽油等溶剂洗工作服或拖地或钢平台、地面34. 不锈钢、碳钢贮罐罐壁未用焊接钢筋或扁钢接地,超过50m2未有两处接地35. 存在散发易燃易爆气体的场所,未采用增湿等消除静电危害的措施36. 用塑料管吸料或装甲苯或回收甲苯37. 用压缩空气输送或搅拌汽油38. 防爆洁净区未使用防静电拖鞋39. 接地扁钢、屋顶防雷带生锈、腐蚀严重40. 高出屋面的金属设备未焊接钢筋并入避雷带四、生产现场41. 贮存原料或废料较多42. 现场跑、冒、滴、漏多43. 保温层损坏44. 缺有效防护栏45. 常闭式防火门常开46. 存有粉尘(镁粉、锌粉等)的操作岗位,未及时清理47. 金属钠、钠氢存放,没有防雨措施或废桶、废袋随意存放48. 消防通道堵塞或各种管线及其支架妨碍通行49. 灭火器缺少或已过期锈蚀或消防带、消防栓不符合消防要求50. 废料桶有多张标签51. 强氧化剂(双氧水、高锰酸钾等)堆放在木架上52. 钢平台晃动幅度过大53. 钢平台或钢柱腐蚀严重54. 局部区域溶剂浓度超标55. 高处阀门手柄、铁棒等易跌落56. 混凝土楼面震动大57. 室外钢棚或屋顶杂物多58. 防毒器材过期或失效59. 生产现场存放有非生产用具(食品、报纸、小说)60. 缺乏夏季的防暑降温设施61. 室外小管径水管冬季未保温62. 车间内没有紧急淋浴、洗眼等卫生设施或已损坏63. 车辆未装阻火器进入生产现场64. 易燃易爆场所没有安装可燃气体报警仪或失灵65. 反应釜、贮罐、泵等未标注设备位号和名称66. 大铁门没有固定插销,一旦风大就可能使铁门擦出火花,导致危险67. 库房门槛偏低,一旦发生意外,危险品将外溢68. 生产现场地面存放铁板、钢管五、人员、现场操作69. 没有岗位操作记录或操作记录不完整70. 吸料、灌装、搬运腐蚀性物品未戴防护用品71. 存在操作人员脱岗、离岗、睡岗等现象72. 粉体等投料岗位未戴防尘口罩73. 快速开关阀门74. 分层釜、槽底阀分层后未关75. 分层釜、槽分水阀开太大,造成水中夹油排入污水池或排水时间过长忘记关阀而跑料76. 高温釜、塔内放入空气77. 提取催化剂(如钯碳、活性镍等)现场散落较多78. 用铁棒捅管道、釜内堵塞的物料或使用不防爆器械产生火花79. 噪声环境未戴防耳器或耳塞80. 贮槽超压使用81. 使用汽油、甲苯等易燃易爆溶剂处,釜、槽未采用氮气置换82. 烟尘弥漫、通风不良或缺氧83. 带压开启反应釜盖84. 员工有职业禁忌或过敏症或接触毒物时间过长85. 紧急阀门或紧急开关不易操作86. 在易燃易爆场所,穿带钉子鞋或高跟鞋、凉鞋六、土建87. 可能发生火势蔓延的上下楼层管道井没有预防措施(如阻燃材料封堵)88. 有爆炸危险的工艺未采用防爆墙及轻质屋顶或未考虑足够的泄爆面89. 出入口和紧急通道设计数量不够或堵塞或无明显标志90. 厂房基础已受酸、碱类物质腐蚀,立柱、梁已受损严重91. 有大风时,钢窗玻璃易脱落92. 楼梯太窄或较陡93. 室内排水不畅或低洼处长期积水、积油94. 通道或作业处,头顶与顶棚没有足够的空间95. 在不明地下管线(水管、电缆等)情况下,随意开挖路面96. 使用大型机械在接近地下电缆、管道等附近挖土97. 在禁火区域内动火时,生产车间未派人监护98. 施工中出现异常情况(管道断裂、泄漏等),未立即停工进行应急处理99. 挖掘的沟、坑、池等和破坏的管道,未设置围栏和标志,夜间未设置照明100. 发现土壤有可能坍塌或滑动时,未停止作业101. 没有防止地下空罐、空池上浮的措施102. 在下罐、下池作业时,未办理相应审批手续或未遵照审批要求实施(如劳保用品、监护人落实等)防范措施未到位的情况下作业103. 在非土建作业时,未办理“非基建用工手续“或作业前不了解相应可能风险,在安全措施不到位情况下工七、生产检修104. 在容器内进行清扫和检修时,遇到危险情况,没有紧急逃出设施或措施105. 动火作业无监护人或监护人由新近员工担任或违章动火106. 超负荷吊装107. 工具或吊物未合理固定108. 未配备或未穿戴防护用品(安全帽、安全带等)109. 无警示标志或标志已模糊不清(如防止触电、防止坠物等)110. 检修时踏在悬空管路或小管径塑料管道和搪玻璃管道上或使用不安全登高设施111. 电焊机、手动电动工具等电缆破损引起漏电,零线破损或跨接112. 盲目进入污水池、深沟、深池作业113. 冬季管架结冰滑,无防滑措施114. 安装公司电焊工无电焊证或检修工未经过相关培训115. 直接站在石棉瓦、油毡等易碎材料的屋顶上作业116. 高处作业时,未采取防范措施进行交叉作业117. 高处作业时,电焊机的零线未接到所焊位置118. 有异味或可能产生有毒气体的区域作业未佩带防毒面具119. 高处补、挖墙洞时,未设安全围栏或安全网等120. 清理出的危险物料由高层向下层散落121. 用吊装机械载人122. 夜间作业无足够照明123. 遇有六级以上强风或其他恶劣天气时,仍在露天高空作业124. 釜内作业时,釜外无两人以上监护125. 釜内检修时,没有切断电源并挂“有人检修、禁止合闸”的牌子126. 进罐作业前,未对釜进行有效清洗127. 进罐作业前,未分析可燃气体浓度、氧含量、有毒气体(CO、H2S)浓度128. 进罐作业前,未对物料管线如原料、溶剂、蒸汽、水、氮气等管线可靠隔离129. 检修过程中,未对釜内定期取样分析130. 釜外明显位置未挂上“罐内有人”的牌子131. 进罐作业时,没有执行“双检制”132. 釜内照明不符合安全电压标准,干燥情况下电压大于24V,潮湿情况下电压大于12V 133. 检修完毕,未检查、清理杂物就开机使用134. 长时间在釜内作业未轮换135. 检修时,釜内缺必要的通风设施136. 在搪玻璃罐外壁表面或内壁施焊137. 进入搪玻璃釜、槽内未铺设软垫138. 快速升温或急速冷却搪玻璃釜139. 使用搪玻璃罐时,罐口或人孔螺栓、卡子掉入釜内140. 使用搪玻璃釜、不锈钢釜、碳钢釜时,酸液进入釜夹套141. 选用材料未经温度、PH、腐蚀溶解性审核,可能存有压力的场合未经受压专项审核142. 检修完毕,釜内、检修现场高低位等全部空间未经全面清场、复核,既开始试运行143. 检修完毕,相关事项未做全面沟通,变更未经确认审批,相关人员未全面培训并了解就接手144. 检修未经运行确认即投料生产八、生产工艺145. 存在突发反应,缺乏应对措施及培训146. 随意改变投料量或投料配比147. 改进工艺或新工艺,未进行安全评估148. 工艺变更未经过严格审订、批准149. 工艺过程在可燃气体爆炸极限内操作150. 使用高毒物料时,采用敞口操作151. 未编写工艺操作规程进行试生产152. 未编写所用物料的物性资料及安全使用注意事项153. 所用材料分解时,产生的热量未经详细核算154. 存在粉尘爆炸的潜在危险性155. 某种原辅料不能及时投入时,釜内物料暂存时存在危险156. 原料或中间体在贮存中会发生自燃或聚合或分解危险157. 工艺中各种参数(温度、压力等)接近危险界158. 发生异常状况时,没有将反应物迅速排放的措施159. 没有防止急剧反应和制止急剧反应的措施。
化工设备常见安全隐患300项,纯干货!

化工设备常见安全隐患300项,纯干货!【化工设备常见安全隐患300项,纯干货!】化工行业是一个高风险行业,安全隐患众多。
为了确保工作人员的生命安全和生产设备的正常运行,化工企业有责任对常见安全隐患进行全面排查并采取相应的预防措施。
本文将围绕化工设备的常见安全隐患,分析其中的各种安全风险,并提供纯干货的解决办法。
一、设备层面1. 机械故障化工设备中的机械故障往往会导致设备的停机和生产线的中断,甚至造成人员伤亡。
常见的机械故障有轴承失效、齿轮断齿、高温螺栓松动等。
解决办法是定期进行设备维修、更换关键零部件,并加强设备运行的监测和维护。
2. 设备老化随着使用时间的延长,化工设备容易出现老化和腐蚀,从而导致设备的结构松散、功能失效等问题。
解决办法是进行设备的定期维护和检修,并注意防止腐蚀介质的侵蚀。
3. 高温和高压在化工生产过程中,高温和高压是常见的安全隐患,特别是对于压力容器和高温反应釜。
解决办法是加强设备的温度和压力监控,设立相应的安全阀和爆破片,并定期进行设备的检测和维护。
4. 静电静电是化工设备中的一个常见隐患,它会引起火灾和爆炸。
为了解决这个问题,可以采用防静电地板、导电材料等措施,并定期对设备进行防静电处理。
5. 泄漏化工设备的泄漏会导致有害物质的泄露和环境污染,从而危害工作人员的健康和生命安全。
解决办法是加强设备的密封性能,设立泄漏监测装置,并定期进行泄漏检测和维修。
二、操作层面1. 无证操作无证操作是化工企业中普遍存在的问题,它会给人员安全和生产设备的正常运行带来隐患。
解决办法是加强操作人员的培训和管理,确保其具备相应的证书和操作技能。
2. 操作失误化工设备需要人员按照相应的工艺操作,一旦操作失误,就会引发安全事故。
解决办法是加强对操作人员的培训和考核,制定明确的操作规程,并加强对操作过程的监督和管理。
3. 过度疲劳长时间的工作和高强度的操作容易造成人员的过度疲劳,从而增加安全事故的发生概率。
常见安全隐患300项

化工人必知:化工装置常见安全隐患300项一、设备设施1. 反应釜、反应器1)减速机噪声异常2)减速机或机架上油污多3) 减速机塑料风叶热融变形4) 机封、减速机缺油5)垫圈泄漏6) 防静电接地线损坏、未安装7)安全阀未年检、泄漏、未建立台帐8) 温度计未年检、损坏9)压力表超期未年检、损坏或物料堵塞10)重点反应釜未采用双套温度、压力显示、记录报警11)爆破片到期未更换、泄漏、未建立台帐12) 爆破片下装阀门未开13)存在爆炸危险反应釜未装爆破片14)温度偏高、搅拌中断等存在异常升压或冲料15) 放料时底阀易堵塞16) 不锈钢或碳钢釜存在酸性腐蚀17)装料量超过规定限度等超负荷运转18) 搪瓷釜内搪瓷破损仍使用于腐蚀、易燃易爆场所19)反应釜内胆于夹套蒸汽进口处冲蚀破损20)压力容器超过使用年限、制造质量差,多次修理后仍泄漏21) 压力容器没有铭牌22) 缺位号标识或不清23) 对有爆炸敏感性的反应釜未能有效隔离24) 重要设备未制订安全检查表25) 重要设备缺备件或备机2. 贮槽、罐区、槽车1)液位计模糊或损坏、堵塞2)静电接地线松动或未连接3) 法兰垫片处泄漏4)小平台等高位贮槽未能有效固定5)安全液封液位未达到要求6) 常压贮槽带压使用7) 装料量超过规定限度8)非常温贮槽未装温度计9)容器出现裂缝,仍在使用10) 频繁受真空、氮气交变载荷使贮罐破损11) 低沸点溶剂或液化气贮槽受阳光直射12)室外贮罐等存在运输车辆等撞击危险13) 危险品罐区围堰孔洞未封堵14)危化品罐区防护堤封堵不严密,任意开设排雨水孔15)通向排水管的截止阀处于常开等不安全状态16) 危化品罐区的可燃或腐蚀性物料出口管线,其支架未设置吊式压式弹簧补偿措施,或直接采用挠性连接短管17) 危化品罐区未设禁打手机、禁带火源、限高限速等各种警示牌18) 危险品罐区无泄漏、送料操作记录及日常巡查19)拖拉机随意进入危险品罐区20) 危险品罐区周边有明火或山林火灾21)危险品罐区操作室使用电炉、电茶壶、电热板等违章用电22) 槽车在装卸地点没有接地装置23) 没有防止操作人员从罐车上坠落的措施24)未装配有效的阻火器和车况不合格(照明灯损坏或刹车失灵)槽车进入罐区25)槽车贮罐的安全附件(压力表、温度计、安全阀)无检验日期或存在失效26)槽车罐体未标明压力容器下次检验日期27) 罐体上无静电拖链、防毒器材或阀门泄漏28) 卸料前和卸料后接地未静置10分钟以上29) 槽车卸料时,司机、押运员离开卸料现场,没有现场监护人员30) 采用敞开式和喷溅式卸料31) 卸料时使贮罐超标准液位或满料溢出32)氯乙烯槽车卸料时,软管或法兰处泄漏33) 氯乙烯运输送料时,满槽34)槽车装量不满时多次在厂内运输和卸料35)卸料车辆为熄火及手闸制动或卸料中途启动车辆36)在高强闪电、雷击频繁时,从事卸料操作37)油罐接地点没有2处38) 装卸汽油、甲苯时,操作人员未穿戴防静电工作服和防静电的鞋子39)液氨等贮槽贮存区域未设置事故围堰和应急喷淋稀释设施40) 现场未设置应急喷淋和洗眼设施41) 没有防止物料错装措施如乙酸乙酯装入汽油槽罐42) 站在汽油桶上电焊43)未经清洗,切割汽油桶或焊接贮槽44) 液氨、氯乙烯贮罐超装45) 槽车卸料时,堵塞消防通道及侵占通行道路46)收料员离开卸料现场47)装卸现场使用铁制、塑料等易产生火花的工具48) 由罐区送入车间的物料贮槽没有操作记录3。
- 1、下载文档前请自行甄别文档内容的完整性,平台不提供额外的编辑、内容补充、找答案等附加服务。
- 2、"仅部分预览"的文档,不可在线预览部分如存在完整性等问题,可反馈申请退款(可完整预览的文档不适用该条件!)。
- 3、如文档侵犯您的权益,请联系客服反馈,我们会尽快为您处理(人工客服工作时间:9:00-18:30)。
01 作业类隐患
02 装置类隐患
03 管理类隐患
目
录
04 “两票三制”隐患
05 触电及机械伤害
06 高处作业类隐患 07 交通运输类隐患 08 消防及环保类隐患 09 设备及PPE类隐患 10 其他类综合隐患
01 作业类隐患
LOO
的安全隐患
9、电火焊线、电源线不集中布置、走向混乱,过通道无保护措施; 10、现场低压配电开关护盖不全或导电部分裸露,电气安全工器具、绝 缘工具未按规定定期试验; 11、一个电气开关控制两台及以上电动设备; 12、流动电源箱无漏电保护器或漏电保护器失灵; 13、现场使用不规范的流动电源箱、开关、电源板; 14、电动工具、电动机械不符合国家有关安全标准; 15、脚手架搭设后未经使用部门验收合格并挂牌后就投入使用; 16、脚手板未按标准敷设或有探头板未绑扎牢固;
LOO
作业过程中可能存在的安全隐患
51、在机械的转动、传动部分的防护罩上坐、立、行走或用手触摸运转中机 械的转动、传动、滑动部分及旋转中的工件; 52、使用卷板机卷板时,板上站人; 53、工作电梯运行时电梯门或层间门关闭不严; 54、敲打电梯层间联络的电信器材或强制解锁运行; 55、电梯超载运行或货用电梯人货混载; 56、进入易燃、易爆区的机动车辆排气管未加设防火罩; 57、在易燃、易爆或禁火区域携带火种、吸烟、动用明火、穿带铁钉的鞋;
LOO
作业过程中可能存在的安全隐患
64、工作现场用明火取暖; 65、对有压力、带电、充油的容器施焊或未采取措施对盛过油的容器施 焊; 66、焊接、切割工作前未清理周围的易燃物,工作结束后未检查清理遗 留物,留下火种; 67、打锤时戴手套或挥动方向正对人; 68、高处清理垃圾时抛掷或堵塞通道; 69、掉在安全网或防护棚内的杂物,在收工前未及时清理; 70、未经有关部门同意,在厂房内任意打孔。
LOO
作业过程中可能存在的安全隐患
58、不及时关闭氧气、乙炔阀门就离开工作场所; 59、乙炔、氧气管混用,氧气、乙炔瓶混放在一起; 60、高处电、火焊作业,对下方的设备不采用防火隔离措施;61、随意 损坏消防器材或移作他用; 62、随意堵塞消防通道或取用消防水; 63、压力容器、锅炉水压试验升压过程中,在承压部件上作业;
LOO
作业过程中可能存在的安全隐患
43、操作链条、电动葫芦时,站在葫芦正下方; 44、无证操作、驾驶各种机动车辆; 45、厂内机动车辆行驶时违章带人; 46、施工机械、机动车辆超铭牌使用; 47、现场车辆运输装运设备不封车; 48、转动机械的操作人员在工作时戴手套作业; 49、使用砂轮机、车、钳、钻等切割机械不戴防护眼镜; 50、运行中将转动设备的防护罩打开或将手伸入遮拦内,戴手套或用布、 棉纱对转动部位进行清扫或检查维修等;
1、随意移动、损坏、拆除安全设施或移作他用; 2、非电工私接电源或拆装电气设备; 3、闸刀式电源开关带负荷拉闸,造成闸刀受损; 4、将电源线钩挂在闸刀上或直接插入插座内使用; 5、使用手持电动工具或建筑电动机械未经漏电保护器; 6、潜水泵在工作时,在潜水泵排水的坑、池内工作或在周围进行清淤、 挖土等工作; 7、使用金属丝代替熔丝或使用没有达到规范要求的熔丝; 8、流动电源箱盘至固定配电盘之间的电源线长度大于40米;
LOO
作业过程中可能存在的安全隐患
35、无安全措施起吊氧气、乙炔瓶等易燃易爆危险品; 36、带棱角、刃口的物件为包、垫起吊; 37、起吊埋在地下的不明物件; 38、起吊大件或不规则组件时,未拴以牢固的溜绳; 39、起吊钢板、管子、毛竹、钢材等较长易滑构件时采用兜吊的方式; 40、起重机工作完毕后,未及时摘除吊钩上的钢丝绳并将吊钩升起,或未切 断电源; 41、跨越或手扶在运行的卷扬机及设备钢丝绳上; 42、将双链条葫芦拆成单链条使用;
LOO
作业过程中可能存在的安全隐患
9、在金属容器内或井坑内工作时,金属容器没有可靠接地,或将行灯变 压器带入金属容器内或井坑内; 10、在电源盘、电缆周围2米范围内进行焊、割等高温作业; 11、电焊机二次接线头铜芯裸露,未包扎绝缘; 12、酒后登高作业; 13、高处作业时随手抛掷工器具及材料等物品; 14、高处作业时工器具不系保险绳,无防坠落的措施; 15、高处作业时,工作材料、工器具等放在临空面或孔洞附近; 16、高处作业切割、焊接的下角料不及时清理,有可能造成高空坠物;
02 装置类隐患
LOO
装置中可能存在的安全隐患
1、配电盘、电源箱非防雨型临时开关箱等配电设施无可靠的防雨设施; 2、电焊机、卷扬机等小型工作机械无可靠的防雨措施; 3、在电缆沟、隧道、夹层、锅炉烟道内工作不使用安全电压行灯照明或行 灯电压超过36伏; 4、在金属容器内、管道内、潮湿的地方使用的行灯电压大于12伏; 5、使用220伏及以上电源作照明电源,无可靠安全措施; 6、在金属容器内施焊时,容器外围设专人监护; 7、焊把或电焊机二次接线绝缘不良,有破损; 8、电焊机外壳无接地保护;
LOO
作业过程中可能存在的安全隐患
17、搭建脚手架无验收牌,无定期检验签名; 18、在高处平台、孔洞边缘、安全网内休息或倚坐栏杆; 19、擅自穿越安全警戒区; 20、上下爬梯或特殊脚手架时,未仔细检查是否牢固就盲目攀爬; 21、不按规程规定拆除脚手架,拆除时上下同时作业或将脚手架整体推倒; 22、擅自拆除上下爬梯、孔洞盖板、栏杆、隔离层,或拆除上述设施后不 设明显警告标志,未及时恢复; 23、使用不规范的梯子或损坏严重的梯子,或梯脚无防滑措施; 24、两人站在同一梯子上工作,或站在最高两档上;
LOO
作业过程中可能存在的安全隐患
25、站在石棉瓦、油毡、苇席等轻型简易结构的屋面上工作; 26、凭借栏杆、脚手架、瓷件起吊重物; 27、非操作工操作起重机; 28、非起重人员指挥起吊及非特种作业人员从事特种作业; 29、吊物捆扎、吊装方法不当,在吊物上堆放、悬挂零星物件; 30、起吊超过额定负荷的物件且无措施; 31、指挥信号不明,重量不明起吊; 32、吊车吊重物直接进行加工作业; 33、起吊时歪拉、斜吊; 34、工件上站人或工件上附有悬浮物时起吊;